Huck 2012 Series User manual

03-07-2013
HK969
INSTRUCTION MANUAL
2012 ALL MODELS
PNEUDRAULIC INSTALLATION TOOL

2012 series Tooling (HK969) Alcoa Fastening Systems
2

January 29, 2014
PB618
THREADLOCKER RECOMMENDATION
Loctite®243 THREADLOCKER
TO REPLACE Vibra-Tite®IN
HUCK PNEUDRAULIC INSTALLATION TOOLS
Page 1 of 1
In order to ensure ease of assembly of back caps
and air pistons, among other components of HUCK
installation equipment, it is recommended that
wherever Vibra-Tite
®
has been mentioned in a HUCK
instruction manual or product bulletin procedure, the
product Loctite
®
243 Threadlocker be used instead.
This oil-tolerant, removable, medium-strength blue
threadlocker is designed for locking and sealing
threaded components. It can be applied smoothly
and will now be the HUCK recommended standard
for these applications. For best results, follow
manufacturer’s recommendations for use.
Loctite
®
243 Threadlocker is available for purchase
from HUCK in a .5 mL tube as part number 508567.
Locite is a registered trademark of Henkel Corporation, U.S.A.
Vibra-Tite is a registered trademark of ND Industries, Inc. USA.
For more informaƟon or to order, please contact your local distributor or call direct:
Alcoa Fastening Systems
1 Corporate Drive
Kingston, NY 12401
800-278-4825
PKG: 8452
GRP: 01 through 12, 15 through 19, & 21-22

This page is intentionally blank.

2012 series Tooling (HK969) Alcoa Fastening Systems
3
EU DECLARATION OF CONFORMITY . . . . . . . . . . . . . . . . . . . . . . . . . . . . .2
SAFETY . . . . . . . . . . . . . . . . . . . . . . . . . . . . . . . . . . . . . . . . . . . . . . . . . . .4
DESCRIPTION . . . . . . . . . . . . . . . . . . . . . . . . . . . . . . . . . . . . . . . . . . . . . . .5
SPECIFICATIONS . . . . . . . . . . . . . . . . . . . . . . . . . . . . . . . . . . . . . . . . . . .5-6
PRINCIPLE OF OPERATION . . . . . . . . . . . . . . . . . . . . . . . . . . . . . . . . . . . .7
PREPARATION FOR USE . . . . . . . . . . . . . . . . . . . . . . . . . . . . . . . . . . . . . .8
OPERATING INSTRUCTIONS . . . . . . . . . . . . . . . . . . . . . . . . . . . . . . . . . . . .8
MAINTENANCE . . . . . . . . . . . . . . . . . . . . . . . . . . . . . . . . . . . . . . . . . . . . . .9
DISASSEMBLY . . . . . . . . . . . . . . . . . . . . . . . . . . . . . . . . . . . . . . . . . . .10-11
ASSEMBLY . . . . . . . . . . . . . . . . . . . . . . . . . . . . . . . . . . . . . . . . . . . . . . . .12
FILL AND BLEED PROCEDURE . . . . . . . . . . . . . . . . . . . . . . . . . . . . .13-14
HOW TO MEASURE STROKE . . . . . . . . . . . . . . . . . . . . . . . . . . . . . . . . . .15
TOOL ASSEMBLY PARTS DRAWINGS . . . . . . . . . . . . . . . . . . . . . . . .16-22
ACCESSORIES . . . . . . . . . . . . . . . . . . . . . . . . . . . . . . . . . . . . . . . . . . . . .23
STICKER LOCATIONSS . . . . . . . . . . . . . . . . . . . . . . . . . . . . . . . . . . . . . . .23
TROUBLESHOOTING . . . . . . . . . . . . . . . . . . . . . . . . . . . . . . . . . . . . . . . . .24
C
CONTENTS
ONTENTS

2012 series Tooling (HK969) Alcoa Fastening Systems
4
I. GENERAL SAFETY RULES:
1. A half hour long hands-on training session with qualified personnel is rec-
ommended before using Huck equipment.
2. Huck equipment must be maintained in a safe working condition at all
times. Tools and hoses should be inspected at the beginning of each
shift/day for damage or wear. Any repair should be done by a qualified
repairman trained on Huck procedures.
3. For multiple hazards, read and understand the safety instructions before
installing, operating, repairing, maintaining, changing accessories on, or
working near the assembly power tool. Failure to do so can result in seri-
ous bodily injury.
4. Only qualified and trained operators should install, adjust or use the
assembly power tool.
5. Do not modify this assembly power tool. This can reduce effectiveness of
safety measures and increase operator risk.
6. Do not discard safety instructions; give them to the operator.
7. Do not use assembly power tool if it has been damaged.
8. Tools shall be inspected periodically to verify all ratings and markings
required, and listed in the manual, are legibly marked on the tool. The
employer/operator shall contact the manufacturer to obtain replacement
marking labels when necessary. Refer to assembly drawing and parts list
for replacement.
9. Tool is only to be used as stated in this manual. Any other use is prohibit-
ed.
10. Read MSDS Specifications before servicing the tool. MSDS specifica-
tions are available from the product manufacturer or your Huck represen-
tative.
11.Only genuine Huck parts shall be used for replacements or spares. Use
of any other parts can result in tooling damage or personal injury.
12.Never remove any safety guards or pintail deflectors.
13.Never install a fastener in free air. Personal injury from fastener ejecting
may occur.
14.Where applicable, always clear spent pintail out of nose assembly before
installing the next fastener.
15.Check clearance between trigger and work piece to ensure there is no
pinch point when tool is activated. Remote triggers are available for
hydraulic tooling if pinch point is unavoidable.
16.Do not abuse tool by dropping or using it as a hammer. Never use
hydraulic or air lines as a handle or to bend or pry the tool. Reasonable
care of installation tools by operators is an important factor in maintaining
tool efficiency, eliminating downtime, and preventing an accident which
may cause severe personal injury.
17.Never place hands between nose assembly and work piece. Keep hands
clear from front of tool.
18.Tools with ejector rods should never be cycled with out nose assembly
installed.
19.When two piece lock bolts are being used always make sure the collar ori-
entation is correct. See fastener data sheet for correct positioning.
II. PROJECTILE HAZARDS:
1. Risk of whipping compressed air hose if tool is pneudraulic or pneumatic.
2. Disconnect the assembly power tool from energy source when changing
inserted tools or accessories.
3. Be aware that failure of the workpiece, accessories, or the inserted tool
itself can generate high velocity projectiles.
4. Always wear impact resistant eye protection during tool operation. The
grade of protection required should be assessed for each use.
5. The risk of others should also be assessed at this time.
6. Ensure that the workpiece is securely fixed.
7. Check that the means of protection from ejection of fastener or pintail is in
place and operative.
8. There is possibility of forcible ejection of pintails or spent mandrels from
front of tool.
III. OPERATING HAZARDS:
1. Use of tool can expose the operator’s hands to hazards including: crush-
ing, impacts, cuts, abrasions and heat. Wear suitable gloves to protect
hands.
2. Operators and maintenance personnel shall be physically able to handle
the bulk, weight and power of the tool.
3. Hold the tool correctly and be ready to counteract normal or sudden
movements with both hands available.
4. Maintain a balanced body position and secure footing.
5. Release trigger or stop start device in case of interruption of energy sup-
ply.
6. Use only fluids and lubricants recommended by the manufacturer.
7. Avoid unsuitable postures, as it is likely for these not to allow counteract-
ing of normal or unexpected tool movement.
8. If the assembly power tool is fixed to a suspension device, make sure that
fixation is secure.
9. Beware of the risk of crushing or pinching if nose equipment is not fitted.
IV. REPETITIVE MOTION HAZARDS:
1. When using assembly power tool, the operator can experience discomfort
in the hands, arms, shoulders, neck or other parts of the body.
2. When using tool, the operator should adopt a comfortable posture while
maintaining a secure footing and avoid awkward or off balanced postures.
3. The operator should change posture during extended tasks to help avoid
discomfort and fatigue.
4. If the operator experiences symptoms such as persistent or recurring dis-
comfort, pain, throbbing, aching, tingling, numbness, burning sensations
or stiffness, these warnings should not be ignored. The operator should
tell the employer and consult a qualified health professional.
V. ACCESSORIES HAZARDS:
1. Disconnect tool from energy supply before changing inserted tool or
accessory.
2. Use only sizes and types of accessories and consumables that are rec-
ommended. Do not use other types or sizes of accessories or consum-
ables.
VI. WORKPLACE HAZARDS:
1. Be aware of slippery surfaces caused by use of the tool and of trip haz-
ards caused by the air line or hydraulic hose.
2. Proceed with caution while in unfamiliar surroundings; there could be hid-
den hazards such as electricity or other utility lines.
3. The assembly power tool is not intended for use in potentially explosive
environments.
4. Tool is not insulated against contact with electrical power.
5. Ensure there are no electrical cables, gas pipes, etc., which can cause a
hazard if damaged by use of the tool.
VII. NOISE HAZARDS:
1. Exposure to high noise levels can cause permanent, disabling hearing
loss and other problems such as tinnitus, therefore risk assessment and
the implementation of proper controls is essential.
2. Appropriate controls to reduce the risk may include actions such as damp-
ing materials to prevent workpiece from ‘ringing’.
3. Use hearing protection in accordance with employer’s instructions and as
required by occupational health and safety regulations.
4. Operate and maintain tool as recommended in the instruction handbook
to prevent an unnecessary increase in the noise level.
5. Select, maintain and replace the consumable / inserted tool as recom-
mended to prevent an unnecessary increase in noise.
6. If the power tool has a silencer, always ensure that it is in place and in
good working order when the tool is being operated.
VIII. VIBRATION HAZARDS:
1. Exposure to vibration can cause disabling damage to the nerves and
blood supply to the hands and arms.
2. Wear warm clothing when working in cold conditions and keep hands
warm and dry.
3. If numbness, tingling, pain or whitening of the skin in the fingers or hands,
stop using the tool, tell your employer and consult a physician.
4. Support the weight of the tool in a stand, tensioner or balancer in order to
have a lighter grip on the tool.
IX. PNEUMATIC / PNEUDRAULIC TOOL SAFETY INSTRUCTIONS:
1. Air under pressure can cause severe injury.
2. Always shut off air supply, drain hose of air pressure and disconnect tool
from air supply when not in use, before changing accessories or when
making repairs.
3. Never direct air at yourself or anyone else.
4. Whipping hoses can cause severe injury, always check for damaged or
loose hoses and fittings.
5. Cold air should be directed away from hands.
6. Whenever universal twist couplings (claw couplings) are used, lock pins
shall be installed and whipcheck safety cables shall be used to safeguard
against possible hose to hose or hose to tool connection failure.
7. Do not exceed maximum air pressure stated on tool.
8. Never carry an air tool by the hose.
GLOSSARY OF TERMS AND SYMBOLS:
- Product complies with requirements set forth by the rele-
vant European directives.
-READ MANUAL prior to using this equipment.
-EYE PROTECTION IS REQUIRED while using this equip-
ment.
-HEARING PROTECTION IS REQUIRED while using this
equipment.
Notes: are reminders of required procedures.
Bold, Italic type and underlining: emphasizes a specific instruction.
S
SAFETY
AFETY I
INSTRUCTIONS
NSTRUCTIONS
CAUTIONS: show conditions that will
damage equipment and or structure.
WARNINGS: Must be understood to avoid
severe personal injury.

2012 series Tooling (HK969) Alcoa Fastening Systems
5
The Model 2012 series tools are lightweight,
high speed production tools designed to install:
● -04 through -06 diameter HUCK-
KLINCH®fasteners (including oversize
HUCK-KLINCH)
● -04 through -06 UNIMATIC®blind rivets
● Any other
The 2012V, with vacuum boost selector switch
ON, has two functions:
1. With tool in any position, vacuum holds
fastener firmly in nose assembly.
2. Vacuum expels broken pintail into pintail
collector.
Pulling action of the pull piston is provided by
a pneumatic-hydraulic (pneudraulic) intensifier
system powered by 90 psi air pressure. The air
inlet is equipped with a connector with 1/4-18
female pipe threads to accept your air hose or
quick connect fitting. The piston return stroke is
spring actuated.
POWER SOURCE:
90psi MAX shop air
HOSE KITS:
Use only genuine HUCK Hose Kits rated @ 10,000
psi working pressure.
HYDRAULIC FLUID:
ATF meeting DEXRON III, DEXRON IV, MERCON,
Allison C‐4 or equivalent specifications.
Fire resistant hydraulic fluid may also be used,
and is required to comply with OSHA regulation
1926.302 paragraph (d): "the fluid used in
hydraulic power tools shall be fire resistant fluid
approved under schedule 30 of the US Bureau of
Mines, Department of Interior, and shall retain its
operating characteristics at the most extreme
temperatures to which it will be exposed."
MAX OPERATING TEMP:
125°F (51.7°C)
MAX FLOW RATE:
2.9 scfm (170 l/m)
MAX INLET PRESSURE:
90 psi (6.2 bar)
MIN PULL CAPACITY:
2670 lbs (11.88 kN) @ 90 psi
MIN STROKE:
.650 inches (1.65 cm)
SPEED/CYCLES:
20 per minute
WEIGHT:
2012: 4.4 lbs (1.99 kg)
2012B & 2012V: 4.7 lbs (2.13 kg)
D
DESCRIPTION
ESCRIPTION
S
SPECIFICATIONS
PECIFICATIONS

2012 series Tooling (HK969) Alcoa Fastening Systems
6
S
SPECIFICATIONS
PECIFICATIONS continued
8.77
222.9
9.53
242
10.29
261.3 2012V
2012B
2012
4.88
124
12
305
10°
3.41
86.6
.79
20
1.10
27.9
2012
2012B & 2012V

2012 series Tooling (HK969) Alcoa Fastening Systems
7
P
PRINCIPLE
RINCIPLE
OF
OF O
OPERATION
PERATION
PULL Piston Spring
Damper
Val e
Exhaust
Muffler Air
Piston
Hydraulic Oil
Air Pressure
Exhaust Air
Hydraulic
Piston Rod
Throttle Val e
(PULL position)
Hydraulic
Piston Rod
Throttle Val e
(RETURN position)
Fig. 2
When the tool is connected to the air supply, air
pressure holds the Throttle Valve in the UP
position, and air pressure is directed to the top of
the Air Piston keeping it down.
When the trigger is depressed, the Throttle
Valve moves to the DOWN position, and pres-
surized air is directed to the bottom of the Air
Piston, causing the it to move upward (Fig.2a).
The air above the piston is exhausted and direct-
ed through the center of the Throttle Valve and
out the bottom of the tool through the Muffler.
As the Hydraulic Piston Rod moves upward, a
column of fluid is forced into the tool head,
which moves the PULL Piston rearward. The
attached nose assembly moves with the PULL
Piston to start fastener installation.
When fastener installation is completed, and
upon trigger release, air pressure with the assis-
tance of a spring causes the Throttle Valve to
return to its UP position.
Pressurized air is re-directed to the top of the
Air Piston (Fig.2b), causing the Air Piston and
Hydraulic Piston Rod to move downward. The
air from below the piston is exhausted through
the Muffler at the bottom of the tool.
As the Hydraulic Piston Rod moves downward
and hydraulic pressure is released from the
PULL Piston, a Spring behind the PULL
Piston returns it to its forward position. The
Damper Valve impedes oil flow at pinbreak
helping prevent “Tool Kick”.
Fig. 2a Fig. 2b

2012 series Tooling (HK969) Alcoa Fastening Systems
8
The 2012 is shipped with a plastic plug in the
air inlet connector. Connector has 1/4-18 female
pipe threads to accept the hose fitting. Quick con-
nect fittings and 1/4 inch inside diameter air hose
are recommended. An air supply of 90-100 psi,
capable of 2.9 CFM, must be available. Air supply
should be equipped with a filter-regulator-lubricator
unit.
1. Remove plastic plug from air inlet connector and
drop in a few drops of Automatic Transmission
Fluid, DEXRON Ill, or equivalent.
2. Screw quick-connect fitting into air inlet connec-
tor.
3. Set air pressure on regulator to 90-100 psi.
4. Attach optional air hose, part number 115436
(supplied with tool), to air inlet connector.
5. Connect air hose to tool.
6. Cycle tool a few times by depressing and releas-
ing trigger.
7. Disconnect air hose from tool.
8. Remove retaining nut.
9. Select correct nose assembly from the available
SELECTION CHARTS or speak with your Huck
representative.
NOTE: Quick disconnect fittings and air hoses
are not available from Huck.
NOTE: 2O12V is sold with the ribbed vacuum control
ON/OFF slide in the forward or OFF position. See
FIGURE 6 for slides location which is shown in the
ON (rear) position. While Tool is not being used,
move slide to the OFF (forward) position to prevent
unnecessary air loss.
Blind Fastener Installation:
The Fastener may be placed either in the work hole
or in the end of the Nose Assembly. In either case,
Tool and Nose Assembly must be held against work
and at right angles to it. Depress Trigger and hold it
depressed until Fastener is installed and Pintail
breaks. Release Trigger.
WARNING
As applicable, do not use without deflectors
or pintail bottles. If deflectors are removed or
damaged, separated pintails may eject forcibly
from rear of tool. Unshielded eyes, especially,
may be permanently injured. Other severe
injuries can be caused by flying pintails. If
there is any chance of a projectile-like ejec-
tion, always point rear of tool in a safe direc-
tion, or be sure there is some structure that
will stop ejecting pintails.
CAUTION: Insert Pintail Tube 124448-2 into
tool ONLY when using a Nose Assembly
that installs either -04 or -05 size fasteners.
Jammed pintails and damage may result if
Pintail Tube and fastener size do not corre-
spond correctly.
WARNING
To avoid pinch points, be sure there is
adequate clearance for tool and operator’s
hands before proceeding. Tool moving toward
structure may crush hands or fingers between
tool and structure if clearance is limited.
WARNING
Inspect tool for damage before each use. Do not
operate if damaged as severe personal injury
may occur.
Broken pintails eject from deflector with speed
and force. Be sure pintail deflector is directed
safely away from operator or other personnel in
the area. Ejecting pintails striking anyone may
cause serious personal injury. For Models
2012B and 2012V, pintail bottles must always be
used. Replace damaged pintail deflectors and
bottles as serious personal injury may occur
from pintails when using these defective parts.
P
PREPARATION
REPARATION
FOR
FOR U
USE
SE
O
OPERATING
PERATING I
INSTRUCTIONS
NSTRUCTIONS

2012 series Tooling (HK969) Alcoa Fastening Systems
9
GOOD SERVICE PRACTICES
Service Kits 2012KIT and 2012VKIT include perishable
parts and should be kept on hand at all times. Other
components, as experience dictates, should also be kept
for replacements. Always replace O-Rings and Back-
up Rings when tool is disassembled for any rea-
son.
The efficiency and life of any tool depends upon proper
maintenance and good service practices. Tool should
be serviced by personnel who are thoroughly familiar
with it and how it operates.
A clean, well-lit area should be available for servicing
the tool. Special care must be taken to prevent contam-
ination of pneumatic and hydraulic systems. Proper
hand tools and soft materials to protect tools must be
available. Use only standard hand tools, brass drift and
wood block. Vise with soft jaws should be available.
Unsuitable hand tools will cause installation tool dam-
age. All parts must be handled carefully and examined
for damage and/or wear. Components should be disas-
sembled and assembled in a straight line without bend-
ing, cocking or undue force. Disassembly and assem-
bly procedures outlined in this manual should be fol-
lowed. If Huck recommended procedures are not fol-
lowed, the tool may be damaged.
Rub Slic-tite®* with PTFE thread compound, or equiva-
lent, on pipe plug threads and quick connect fitting.
Smear LUBRIPLATE®13OAA*, or equivalent lubricant,
on O-Rings and mating surfaces to aid assembly and
to prevent damage to O-Rings. (LUBRIPLATE 13O-AA
is available in a tube as Huck P/N 502723.)
Use Never-Seez®* Lubricating Compound (Huck P/N
508183), or equivalent anti-seize compound, on Gland
Housing Assy, Huck P/N 116134-1, threads. Torque to
50 ft. lbs.
Apply Loctite®* #271 Adhesive/sealant to Locknut
505420. (Loctite is available from Huck in a tube as
P/N 503657.) Torque to 25-30 ft. lbs.
STANDARD TOOLS AVAILABLE FROM HUCK
1/8 hex key 502294 used on button head screw
504127.
5/32 hex key 502295 used on socket cap screw
123756.
(0400) TRUARC®* pliers 502866 used on (N5100-l00)
retaining ring.
TOOL MAINTENANCE
The 2012 series require a minimum amount of mainte-
nance. Regular inspection and correction of minor prob-
lems will keep the tool operating efficiently and prevent
downtime.
Using filter-regulator-lubricator unit is highly recom-
mended for safe and reliable tool operation. If a filter-reg-
ulator-lubricator unit is not being used in the air supply:
(1) Remove hose fitting from air inlet connector and drop
in a few drops of automatic transmission fluid or light oil.
(2) Blow out air line to remove dirt and water before con-
necting air hose to tool. At regular intervals, depending
upon use, replace all seals in tool. Service Kits should be
kept on hand. Inspect both hydraulic pistons, and their
piston rods for scored surfaces, excessive wear or dam-
age, and replace as necessary.
Always replace seals and back-up rings when tool is
disassembled for any reason to assure proper sealing
and tool function.
NOSE ASSEMBLY MAINTENANCE
Frequently cleaning the nose assembly is recomended.
Remove nose assembly from tool and disassemble.
See D
DISSASSEMBLY
ISSASSEMBLY section. Check components for any
signs of damage, e.g. cracks, scores and spring dam-
age. Check gripper teeth for damage. Remove any
debris packed between teeth with a sharp pointed
‘pick’. Periodically dip nose, while cycling tool, in miner-
al spirits, isopropyl alcohol or other suitable solvent, to
clean jaws and wash away metal chips and dirt.
*
Slic‐tite is a registered trademark of LA‐CO Industries, Inc.
TEFLON is a registered trademark of E. I. du Pont de
Nemours and Company
Loctite is a registered trademark of Henkel Corporation,
U.S.A.
TRUARC is a trademark of TRUARC Co. LLC
Never‐Seez is a registered trademark of Bostik, Inc.
LUBRIPLATE is a registered trademark of Fiske Brothers
Refining Co.
CAUTION: Damaged jaw teeth, or debris
packed between teeth, will result in failure
to install fastener or improperly installed
fastener.
M
MAINTENANCE
AINTENANCE
CAUTION: Do not use TEFLON®* tape on
pipe threads. Pipe threads may cause tape
to shred resulting in tool malfunction.
(Slic-tite is available in stick form, as part
number 503237, from Huck.)

2012 series Tooling (HK969) Alcoa Fastening Systems
10
The following procedure is for complete disassembly.
Disassemble only subassemblies necessary to check
and replace damaged or worn seals, wipers, back-up
rings and other components.
Always replace seals, wipers, and back-up rings of
disassembled sub-assemblies.
1. Disconnect tool from air source.
2. Unscrew Retaining Nut and remove nose assem-
bly.
3. Unscrew Bleed Plug (Figure 7), including O-ring,
from top of Handle/head. Turn tool over and allow
fluid to drain into container. Tool may be cycled to
clear tool more completely. Discard fluid.
4. Pull Pintail Deflector off End Cap.
5. Remove Throttle Arm Pivot Screw and lift out throt-
tle arm. Disconnect ball end of Cable Assembly
from throttle arm. (Figures 8 & 9)
6. Hold tool in vise with bottom up. Remove Button
Head Screws (3) with 1/8 hex key. Remove End
Cap and Gasket. Remove Muffler from end cap.
Remove Spring from Throttle Valve.
7. To loosen Cylinder Head Retaining Ring in
Cylinder, tap Cylinder Head with mallet. Remove
Retaining Ring.
8. Screw Button Head Screws back into Cylinder
Head, and carefully pull or pry on screws to
remove head.
9. To remove air piston from cylinder, pull on Locknut
with vise-grip pliers. Note: Air piston and rod
should not be disassembled. If Locknut
loosens, apply LOCTITE #271 and tighten to 25-
30 ft. lbs.
10. Remove Bumper from Gland Assembly. Unscrew
gland with 1 3/8 socket wrench and extension bar.
11. Remove Retaining Ring from Gland. Pull out
Spacer and Polyseal.
12. Lift Cylinder from Handle/head.
13. Turn Handle/head over and drain fluid into contain-
er. Discard fluid.
14. Pull Throttle Valve out of Cylinder. Note: Service on
Throttle Valve Bushings is not normally required.
15. Press out Lower Bushing and Upper Bushing. Use
square ended brass rods at least six inches long.
With proper diameter rod, press out lower bushing
first, and then press out upper bushing using a
larger size rod.
16. 2012: Place handle/head securely in vise. Remove
End Cap with 15/16” open end wrench. Extract
Spring, Washer and Wiper Seal.
2012B or 2012V: See Special Disassembly
Instructions in Figure 3 for 2012B and 2012V on
next page.
REMOVAL OF PISTON AND FRONT GLAND (Figure 10)
17. Thread Polyseal Insertion/removal Tool, 121694-
202, into Handle/head.
18. Slide Spacer, 123112-2, onto piston. Thread Piston
Assembly (bullet) Tool, 123111-2 onto piston.
continued
CAUTION:Do not scratch, nick or ding
Piston Rod. This will cause permanent
hydraulic leakage.
WARNING
Air hose must be disconnected before:
• Removing or attaching nose assembly.
• Cleaning tool and/or nose assembly.
• Replacing worn or damaged tool
components.
Tool may be activated if not disconnected
and cylinder is under pressure. Fingers
may be severely pinched/lacerated. Other
severe personal injury may result.
CAUTION:Only if air leakage is not cor-
rectable with new Throttle Valve Seals,
Bushings should be replaced in Cylinder.
CAUTION: If Piston Seals and Gland Seals
must be reused, help prevent damaging
them by installing optional Polyseal
Insertion/removal Tool (121694-202) in rear
of Handle/head.
D
DISASSEMBLY
ISASSEMBLY

2012 series Tooling (HK969) Alcoa Fastening Systems
11
67
8
5
3
4
2
1
19. Push complete piston from front using brass drift.
Allow clearance, with stand-off, for piston as it
leaves tool.
20. Remove Piston Assembly Bullet, Spacer and
Polyseal Insertion/removal Tool. NOTE: Inspect
hydraulic piston for wear, scoring or damage.
Replace when necessary.
21. Unscrew Adapter, 123761, with wrench.
22. Inspect all seals and parts.
23. Remove trigger cable assembly by removing pin
with parallel punch. Remove dowel pin to discon-
nect cable from trigger.
1. Remove Vacuum Tube from
Cylinder.
(2012V only)
2. Place handle/head securely in
vise.Use 0100 TRUARC pliers,
502857, to remove retaining
ring. Reach through window
of pintail bottle. Remove
washer.
3. Remove pintail bottle.
4. Remove bottle adapter and vac-
uum ON/OFF slide.
5. Remove end cap assembly
and spring.
6. Remove washer and O-ring
from spring side of end cap.
7. Remove retaining ring on bottle
side of end cap. Remove
spacer, wiper seal, washer
and O-ring.
8. Remove O-rings from ON/OFF
slide.
Special Disassembly Instructions
for 2012B and 2012V
Figure 3
D
DISASSEMBLY
ISASSEMBLY continued

2012 series Tooling (HK969) Alcoa Fastening Systems
12
See MAINTENANCE: GOOD SERVICE PRACTICE.
Clean all components with mineral spirits, and
inspect for wear or damage. Replace as necessary.
Use seals, wipers and back-up rings supplied in
SERVICE KIT, 2012KIT and 2012VKIT -see NOTES.
Smear LUBRIPLATE 130AA or PARKER-O-LUBE on
seals.
Figures 3 through 12.
1. If Bushings have been removed from cylin-
der:
Use an arbor press and apply LOCTITE #609,
(503377) on bushings before being pressed into
cylinder. Place chamfered end of Upper Bushing
In top of Cylinder. Carefully press bushing
squarely into cylinder. Repeat procedure for
Lower Bushing.
2. Assemble Gland Assembly after replacing
Polyseal, Spacer and Retaining Ring. Figure 8.
NOTE: Cup of POLYSEAL must face toward
top of tool when installed in Gland.
3. Install Adapter into cylinder handle/head.
4. Thread Polyseal insertion/removal tool, 121694-
202 into handle/head.
5. Thread Piston Assembly Tool 123111-4, onto
Piston Assembly.
6. Push front gland assembly onto piston, as
shown.
7. Slide wiper onto piston, as shown.
8. Push assembled components in gently from rear
of tool using a press or soft mallet and wood or
brass drift.
9. Remove Piston Assembly Tool and Polyseal
Insertion/removal Tool.
10. For 2012: Assemble Spring, Spacer, Rear Wiper
Seal and End Cap into handle/head.
For 2012B or 2012V: Reverse the disassembly
instructions in the Special Disassembly
Instructions for 2012B and 2012V in the
Disassembly section.
11. Position Cable Assembly in Trigger slot and push
Dowel Pin through holes in trigger and cable
assembly. Position assembled trigger in handle
and drive Pin through holes in handle and trig-
ger.
12. Hold handle/head in vise with lower end pointing
up. Turn cylinder bottom up, and position on han-
dle by lining up cylinder pin with handle hole.
13. Apply Never-Seez or equivalent to threads of
Gland Assembly. Screw gland into head/handle.
Using a 1 3/8 socket wrench, tighten gland to
75-80 ft. lbs.
14. Push Bumper firmly over gland, slots must face
toward bottom of tool.
15. Lubricate piston rod. Press assembled air pis-
ton/piston rod into cylinder just enough to allow
installation of cylinder head.
16. Push Cylinder Head squarely into cylinder taking
care not to damage O-ring. Install Retaining
Ring. Align screw holes with muffler end cap.
17. Position Muffler in center of cylinder head.
Position Gasket on cylinder.
18. Carefully position Muffler End Cap on cylinder.
Be certain that muffler is properly positioned
in recess of muffler end cap.
19. Muffler end cap is secured with three Button
Head Screws. Tighten with 1/8 hex key.
20. Place tool upright on level surface. Drop Spring
into throttle valve bore in cylinder. Push Throttle
Valve into cylinder.
21. Place ball end of Throttle Cable in end of Throttle
Arm.
22. Slide Throttle Arm into slot on Cylinder.
23. Install Pivot Screw in cylinder to retain Throttle
Arm.
24. Follow FILLING AND BLEEDING PROCEDURE of this
manual to fill tool.
25. Install Bleed Screw afte filling and bleeding pro-
cedure.
CAUTION: Always replace all seals, wipers
and back-up rings on/in disassembled
components. These parts wear from fric-
tion and deteriorate with age. Replacement
prevents potential leakage.
A
ASSEMBLY
SSEMBLY

2012 series Tooling (HK969) Alcoa Fastening Systems
13
Equipment Required:
• Shop airline with 90 - 100 psi max.
• Air regulator
• Fill Bottle 120337 (supplied with tool).
• Large flat blade screwdriver
• Nose assembly or optional Stall Nut
• Fasteners (optional)
• Optional Stall Nut, part no. 124090. (Stall nut is
used to load tool during bleeding and for meas-
uring stroke.)
Preparation:
1. Install air regulator in
air line and set pres-
sure to 20-40 psi.
2. Fill bleed bottle
almost full of
DEXRON III ATF
(automatic transmis-
sion fluid). Figure 4
.
Procedure to Fill Empty Tool (new or
rebuilt):
1. Attach the tool air source momentarily to seat air
piston at bottom of cylinder and disconnect tool.
With fill port facing up, lay tool on its side.
2. With a screwdriver, remove bleed plug from fill
port.
3. Screw fill bottle into fill port in the head.
4. Set air line pressure to 20-40 psi and connect air
line to tool.
5. Stand tool upright on bench. While triggering tool
slowly (20-30 cycles), bend fill bottle at right
angles to tool. Figure 4.2. Air bubbles will
emerge from tool. When bubbles stop, cycling
may be discontinued.
6. When trigger is released, pull piston returns to
idle position (full forward). Disconnect tool from
air line.
7. Lay tool on its side. Remove fill bottle. Top off
fluid in fill port. Install bleed plug and tighten.
8. Connect air line to tool. There is a choice of two
procedures for measuring the stroke: with and
without a stall nut. See SEE HOW TOMEASURE
STROKE section and follow the selected proce-
dure. If stroke is less than specified, remove
bleed plug and top off fluid. Reinstall bleed plug.
9. Increase air pressure to specification. Install two
fasteners to check function and installation in a
single stroke, or cycle tool with stall-nut fully
threaded onto piston to load up tool. Measure
stroke again. Remove plug and top off fluid.
Reinstall plug and cycle again. Measure again.
Continue this process until stroke meets mini-
mum requirements. continued
Fill
Point
Fill Bottle
Assembly
CONTAINER
(Discard Fluid)
Fig. 4
Fig. 4.1
Fig. 4.2
WARNING
Air pressure MUST be set to 20-40 psi to
prevent possible injurious high pressure
spray.
NEVER CYCLE TOOL WITHOUT:
BLEED PLUG TIGHTENED
FILL BOTTLE TIGHTENED IN TOOL, or
FILLPORT HELD OVER A RECEPTACLE Figure 4.1
When not properly contained any fluid pres-
ent in tool will spray out. Severe injury may
result.
F
FILLING
ILLING
AND
AND B
BLEEDING
LEEDING P
PROCEDURE
ROCEDURE

2012 series Tooling (HK969) Alcoa Fastening Systems
14
Bleed Procedure for Partially Filled Tool
in Field Use:
1. Disconnect tool from airline. With fillport facing
up, lay tool on its side.
2. Remove bleed plug from bleed port.
3. Hold tool over suitable container with fillport fac-
ing into container.
4. Connect tool to air line. Cycle tool several times
to drain the old fluid, air and foam.
5. Screw fill bottle into fillport.
6. See WARNING above. With air pressure set at
20-40 psi, connect airline to tool.
7. Stand tool upright on bench. While actuating the
trigger slowly (20-30 cycles), bend fill bottle at
right angles to tool. Figure 4.2. Observe that air
bubbles emerge from tool. When bubbles are no
longer observed, cycling may be discontinued.
8. When trigger is released, pull piston returns to
idle position (full forward). Disconnect tool from
airline with piston full forward.
9. Lay tool on its side. Remove fill bottle. Top off
fluid in fillport. Install bleed plug and tighten with
screwdriver.
10. Connect air line to tool. There is a choice of two
procedures for measuring the stroke: With and
without a stall-nut. SEE HOW TOMEASURE STROKE
section and follow the selected procedure. If
stroke is less than specified, remove bleed plug
and top off fluid. Reinstall bleed plug.
11. Install two fasteners to check function and instal-
lation in a single stroke, or cycle tool with stall
nut fully threaded onto piston. Measure stroke
again. Remove plug and top off fluid. Reinstall
plug and cycle again. Measure again. Continue
this process until stroke meets minimum require-
ments.
F
FILLING
ILLING
AND
AND B
BLEEDING
LEEDING P
PROCEDURE
ROCEDURE (continued)
WARNING
Air pressure MUST be set to 20-40 psi to
prevent possible injurious high pressure
spray.
NEVER CYCLE TOOL WITHOUT:
BLEED PLUG TIGHTENED
FILL BOTTLE TIGHTENED IN TOOL, or
FILLPORT HELD OVER A RECEPTACLE Figure 4.1
When not properly contained any fluid pres-
ent in tool will spray out. Severe injury may
result.

2012 series Tooling (HK969) Alcoa Fastening Systems
15
1. Disconnect tool from airline and remove nose
from tool.
2. Reconnect tool to airline, with piston fully for-
ward (end of RETURN stroke), measure and
record “X” dimension. Figure 6.
3. Hold trigger depressed. Piston is now fully to
the rear and at end of PULL stroke. Measure
and record “Y” dimension.
4. Subtract “X” dimension from “Y” dimension.
5. If stroke is less than .650, refer to appropriate
previous section. Follow filling and topping off
instructions.
Fig. 6
Fig. 5
1. Disconnect tool from airline and remove
nose from tool.
2. Reconnect tool to airline. Cycle tool and
hold trigger depressed. This keeps pis-
ton fully to the rear and at end of PULL
stroke. Thread stall-nut back onto pis-
ton until it contacts stop.
3. Release trigger. Stall-nut will move for-
ward with piston. Figure 5 and measure
‘X” dimension. This is the tool’s stroke.
4. If stroke is less than .650, refer to
appropriate previous section. Follow fill-
ing and topping off instructions.
TO MEASURE STROKE OF TOOL WITH STALL-NUT THREADED ONTO PISTON:
H
HOW
OW
TO
TO M
MEASURE
EASURE S
STROKE
TROKE
TO MEASURE STROKE OF TOOL WITHOUT STALL-NUT:

2012 series Tooling (HK969) Alcoa Fastening Systems
16
Pivot
Screw
123754-1
Throttle Arm
125467-2
Throttle Val e
507396
O-Ring (3)
116272
Spring
Throttle
Cable
AA
116134-1 Gland Assembly
Notes:
Piston and Rod Assy 123777-3 includes:
123776-2 Piston Assy (including:)
123753-1 Air Piston
501 51 Quad-Ring
111803-1 Piston Rod
506 93 Washer
505 20 Self-locking Nut
Cylinder Head Assy 123778-1 includes:
111959-2 Cylinder Head (not sold separately)
50086 O-Ring
Throttle Valve Assy 125472-2 includes:
125 67-2 Throttle Valve (not sold separately)
507396 O-Ring (qty. 3)
2
3
1
1
1
1
1
1
2
2
3
3
Se tion A-A
500778
O-ring
500779
O-ring
(2)
507164
Swi el
Assembly
123753-1
Air Piston
111959-2
Cylinder
Head
506493
Washer
505420
Locknut
115554-2
Muffler
128791
Bottom
Plate 504127
Screw (3)
506878
Retaining Ring
500864
O-Ring
501451
QUAD Ring
126941 Gasket
125118
Pi ot
Screw
111803-1
Piston Rod
125471
Cylinder
Assy
116408
Bumper
125139 Gland
Housing
500786 O-ring
506566 Polyseal
123906 Spacer
506565
Retaining Ring
500784
O-ring
501090
Back-up
Ring
501414
QUAD-Ring
Figure 7
*
*When replacing Cylinder Assembly Stickers (590350, 590351,
and 590347) MUST be ordered and placed in the location shown
in Figure 15.
T
TOOL
OOL A
ASSEMBLY
SSEMBLY D
DRAWINGS
RAWINGS
(pages 16-22)

2012 series Tooling (HK969) Alcoa Fastening Systems
17
125150
End Cap
506488
Wiper*
124828
Washer
123774
Piston
Assy
500621 Pin
124333-1
Trigger
505496
Dowel Pin
116404-1
Cable
Assembly
123766
Handle
Assembly
2012 Head / Handle
506492
Spring
2
124211
Pintail
Deflector
*Note orientation of
Wipers and
Polyseals.
** WARNING Sticker
MUST be p rchased
and placed as shown
any time it becomes
worn, lost, or
damaged or if
Handle/Head is
replaced.
505817
Wiper*
122432
Gland Cap
505818
Polyseal*
501110
Back-up
Ring 500816
O-ring
123775 Front
Gland Assy
506160
Polyseal*
506654
Washer
506653
Retaining
Ring
124448-2
Pintail Tube
3
1
1
1
1
2
2
2
2
2
123770 End Cap &
Adapter Assembly
123772
Pintail Bottle
123771
Washer
501007
Retaining
Ring
506488
Wiper*
124828
Washer
2012B Head / Handle
All components same as
2012 except as shown here.
111795
Retaining Nut
120588 Stop
Notes:
Piston Assembly 123774 includes:
12 258 Piston (not sold separately)
506160 Polyseal
506653 Retaining Ring
50665 Washer
Front Gland Assembly 123775 includes:
123757 Front Gland (not sold separately)
122 32 Gland Cap
505818 Polyseal
500816 O-Ring
501110 Back-up Ring
505817 Wiper
Pintail to be used ONLY for -0 and
-05 size fasteners.
2
3
1
123761
Adapter
590517
Sticker
590240-1
WARNING
Sticker
Figure 8
**
T
TOOL
OOL A
ASSEMBLY
SSEMBLY D
DRAWINGS
RAWINGS
(pages 16-22)
**

2012 series Tooling (HK969) Alcoa Fastening Systems
18
506648
Washer
124245 Slide &
Tube Assembly
(shown in N
position)
123577
End Cap
500790
O-ring
500778
O-ring
500790
O-ring 500807
O-ring
506628
Washer
501007
Retaining
Ring
502310
Retaining
Ring
123578 Spacer
506488
Wiper*
124828
Washer
123784
Adapter
123761
Adapter
500621 Pin
124333-1 Trigger
505496 Dowel Pin
116404-1 Cable Assembly 123766
Handle Assembly
123772
Pintail Bottle
2012V Head / Handle
506492
Spring
505817
Wiper*
122432
Gland
Cap
505818
Polyseal*
501110
Back-up
Ring 500816
O-ring
123757
Front
Gland
506160
Polyseal*
506654
Washer
506653
Retaining
Ring
*Note orientation
of Wipers and
Polyseals.
123774-1
Piston Assy
Notes:
Piston Assembly 123774-1 includes:
12 258-1 Piston (not sold separately)
506160 Polyseal
506653 Retaining Ring
50665 Washer
Front Gland Assembly 123775 includes:
123757 Front Gland (not sold separately)
122 32 Gland Cap
505818 Polyseal
500816 O-Ring
501110 Back-up Ring
505817 Wiper
Pintail to be used ONLY for -0 and
-05 size fasteners.
2
3
1
2
124448-2
Pintail Tube
3
1
1
1
1
2
2
2
2
2
111795
Retaining Nut
120588 Stop
Figure 9
*
T
TOOL
OOL A
ASSEMBLY
SSEMBLY D
DRAWINGS
RAWINGS
(pages 16-22)
This manual suits for next models
3
Table of contents
Other Huck Power Tools manuals
Popular Power Tools manuals by other brands
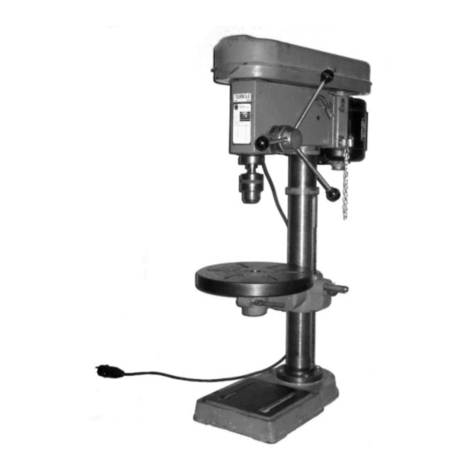
Tournevie BXL
Tournevie BXL Shin Li SLM5S user manual

Hilti
Hilti DD 120 operating instructions

Parkside
Parkside PDRD 13 A1 Operation and safety notes
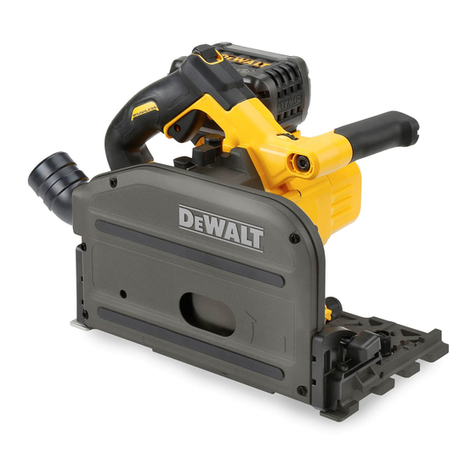
DeWalt
DeWalt XR FLEX VOLT DCS520 quick start guide
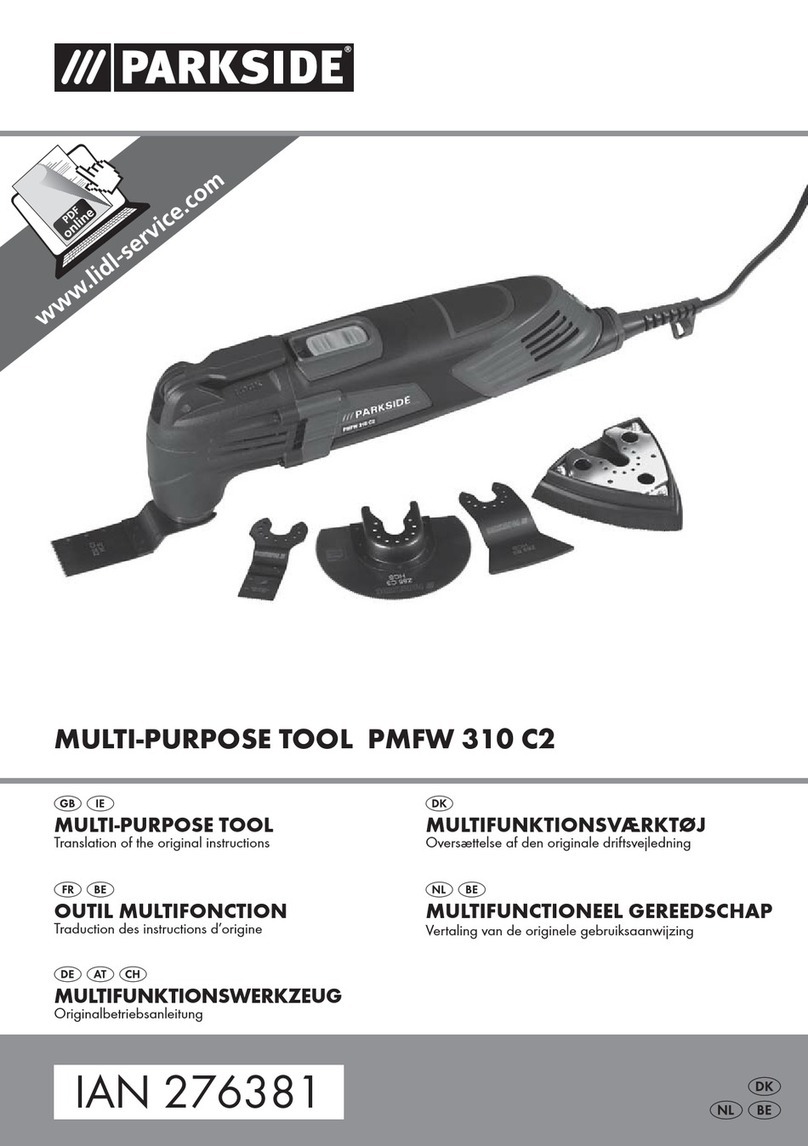
Parkside
Parkside PMFW 310 C2 Translation of the original instructions

Avdel
Avdel 74101 instruction manual