Hussmann RBB Operating instructions

RBB
UPRIGHT BACK BAR DELI CASE
P/N IGUP-RBB-0608
INSTALLATION & OPERATION GUIDE
/CHINO
RBB
UPRIGHT BACK BAR DELI CASE REV. 0608
Installation
& Operation
Manual

IGUP-RBB-0608
2
/CHINO
A publication of HUSSMANN®Chino
13770 Ramona Avenue • Chino, California 91710
(909) 628-8942 FAX
(909) 590-4910
(800) 395-9229
Keep this booklet with the case at all times for future reference.
General Instructions
Table of Contents
General Instructions.....................................................2
Cut and Plan Views ......................................................3
Installation.....................................................................3
Location ..................................................................................... 3
Uncrating the Stand................................................................... 3
Exterior Loading......................................................................... 3
Setting and Joining .................................................................... 3
Leveling ..................................................................................... 3
Joint Trim ................................................................................... 4
Plumbing .......................................................................4
Waste Outlet and P-TRAP......................................................... 4
Installing Condensate Drain - Remote....................................... 4
Refrigeration .................................................................5
Refrigerant Type ........................................................................ 5
Piping......................................................................................... 5
Refrigeration Lines..................................................................... 5
Control Settings ......................................................................... 5
Access to TX Valves and Drain Lines........................................ 5
Electronic Expansion Valve (Optional)....................................... 5
Thermostatic Expansion Valve Location.................................... 5
Expansion Valve Adjustment ..................................................... 5
Measuring the Operating Superheat.......................................... 5
T-STAT Location ........................................................................ 5
Electrical........................................................................6
Wiring Color Code ..................................................................... 6
Electrical Circuit Identication.................................................... 6
Field Wiring and Serial Plate Amperage.................................... 6
Ballast Location ......................................................................... 6
User Information...........................................................6
Stocking..................................................................................... 6
Important Steps ......................................................................... 6
Case Cleaning ........................................................................... 7
Cleaning Glass and Mirrors ....................................................... 7
Plexiglass and Acrylic Care ....................................................... 7
Waxing....................................................................................... 7
Antistatic Coatings..................................................................... 7
Maintenance..................................................................8
Replacing Fluorescent Lamps ................................................... 8
Evaporator Fans ........................................................................ 8
Coil Access ................................................................................ 8
Compressor Access................................................................... 8
Tips and Troubleshooting .......................................................... 8
Electrical Wiring Diagrams..........................................8
Wiring Diagrams ........................................................... 9
Appendices .................................................................21
Appendix A. - Temperature Guidelines .................................... 21
Appendix B. - Application Recommendations.......................... 21
Appendix C. - Field Recommendations ................................... 21
Appendix D. - Recommendations to User ............................... 22
This Booklet Contains Information on:
The RBB this case is a narrow 23" depth multi deck
air curtain case designed to display pre-packaged Deli
products. It is constructed with a lower storage area which
provides a counter-top prep area. This lower storage is
non-refrigerated as a standard with the option to refrigerate
if desired.
Shipping Damage
All equipment should be thoroughly examined for shipping
damage before and during unloading.
This equipment has been carefully inspected at our factory
and the carrier has assumed responsibility for safe arrival.
If damaged, either apparent or concealed, claim must be
made to the carrier.
Apparent Loss or Damage
If there is an obvious loss or damage, it must be noted on
the freight bill or express receipt and signed by the carrier’s
agent; otherwise, carrier may refuse claim. The carrier will
supply necessary claim forms.
Concealed Loss or Damage
When loss or damage is not apparent until after equipment
is uncrated, a claim for concealed damage is made. Make
request in writing to carrier for inspection within 15 days,
and retain all packaging. The carrier will supply inspection
report and required claim forms.
Shortages
Check your shipment for any possible shortages of
material. If a shortage should exist and is found to be the
responsibility of Hussmann Chino, notify Hussmann Chino.
If such a shortage involves the carrier, notify the carrier
immediately, and request an inspection. Hussmann Chino
will acknowledge shortages within ten days from receipt
of equipment.
Hussmann Chino Product Control
The serial number and shipping date of all equipment
has been recorded in Hussmann’s les for warranty and
replacement part purposes. All correspondence pertaining
to warranty or parts ordering must include the serial number
of each piece of equipment involved, in order to provide
the customer with the correct parts.
This equipment is to be installed
to comply with the applicable
NEC, Federal, State , and Local
Plumbing and Construction
Code having jurisdiction.

Rev. 0608
3
Cut and Plan Views
RBB
Adj. Shelves
Display Area
32"
78"
12"
Optional
Shelves
24"
36"
54"
12"
Condiment
Shelf
Pan
Light
21"
8"
24"
4
1
/
2
"
1" 1"
C
L
FRONT
RBB
PLAN VIEW SINGLE CASE
36"
VARIABLE LENGTHS
18"
Electrical
8"
4"
Drain
Refrigeration
8"
4"
Installation
Location
The refrigerated merchandisers have been designed for
use only in air conditioned stores where temperature and
humidity are maintained at or below 75°F and 55% relative
humidity. DO NOT allow air conditioning, electric fans, ovens,
open doors or windows (etc.) to create air currents around
the merchandiser, as this will impair its correct operation.
Product temperature should always be maintained at a
constant and proper temperature. This means that from the
time the product is received, through storage, preparation
and display, the temperature of the product must be
controlled to maximize life of the product.
Uncrating the Stand
Place the xture as close to its permanent position as
possible. Remove the top of the crate. Detach the walls
from each other and remove from the skid. Unbolt the case
from the skid. The xture can now be lifted off the crate
skid. Lift only at base of stand!
Exterior Loading
These models have not been structurally designed to
support excessive external loading. Do not walk on their
tops; This could cause serious personal injury and damage
to the xture.
Setting and Joining
The sectional construction of these models enable them to
be joined in line to give the effect of one continuous display.
A joint trim kit is supplied with each case.
Leveling
IMPORTANT! IT IS IMPERATIVE THAT CASES BE
LEVELED FROM FRONT TO BACK AND SIDE TO SIDE
PRIOR TO JOINING. A LEVEL CASE IS NECESSARY
TO INSURE PROPER OPERATION, WATER DRAINAGE,
GLASSALIGNMENT, AND OPERATION OF THE HINGES
SUPPORTING THE GLASS. LEVELING THE CASE
CORRECTLY WILL SOLVE MOST HINGE OPERATION
PROBLEMS.
NOTE: A. To avoid removing concrete ooring, begin lineup
leveling from the highest point of the store oor.
B. When wedges are involved in a lineup, set them rst.
All cases were leveled and joined prior to shipment to
insure the closest possible t when cases are joined in
the eld. When joining, use a carpenters level and shim
legs accordingly. Case must be raised correctly, under legs
where support is best, to prevent damage to case.
1. Check level of oor where cases are to be set.
Determine the highest point of the oor; cases will
be set off this point.
2. Set rst case, and adjust legs over the highest part of
the oor so that case is level. Prevent damage - case
must be raised under leg or by use of 2x6 or 2x4 leg
brace. Remove side and back leg braces after case
is set.
3. Set second case as close as possible to the
rst case, and level case to the rst using the
instructions in step one.
4. Apply liberal bead of case joint sealant (butyl) to
dotted area shown in (Figure on page 4) of rst
case. Apply heavy amount to cover entire shaded
area.

IGUP-RBB-0608
4
DO NOT USE PERMAGUM!
It is the contractor’s responsibility to install
case(s) according to local construction and
health codes.
5. Slide second case up to rst case snugly. Then level
second case to the rst case so glass front, bumper
and top are ush.
6. Attach sections together via a bolt located in top of
case (see diagram and lock camlock in place).
Plumbing
Waste Outlet and P-TRAP
The waste outlet is located off the center of the case, 8"
from the front.
A 3/4" P-TRAP and threaded adapter are supplied with
each xture. The P-TRAP must be installed to prevent air
leakage and insect entrance into the xture.
NOTE: PVC-DWV solvent cement is recommended.
Follow the Hussmann’s instructions.
Installing Condensate Drain - Remote
Poorly or improperly installed condensate drains can
seriously interfere with the operation of this refrigerator, and
result in costly maintenance and product losses. Please
follow the recommendations listed below when installing
condensate drains to insure a proper installation:
1. Never use pipe for condensate drains smaller
than the nominal diameter of the pipe or P-TRAP
supplied with the case.
2. When connecting condensate drains, the P-TRAP
must be used as part of the condensate drain
to prevent air leakage or insect entrance. Store
plumbing system oor drains should be at least 14"
off the center of the case to allow use of the P-TRAP
pipe section. Never use two water seals in series in
any one line. Double P-TRAPS in series will cause a
lock and prevent draining.
3. Always provide as much down hill slope ("fall") as
possible; 1/8" per foot is the preferred minimum.
PVC pipe, when used, must be supported to
maintain the 1/8" pitch and to prevent warping.
4. Avoid long runs of condensate drains. Long runs
make it impossible to provide the "fall" necessary for
good drainage.
5. Provide a suitable air break between the ood rim of
the oor drain and outlet of condensate drain. 1" is
ideal.
6. Prevent condensate drains from freezing:
a. Do not install condensate drains in contact with
non-insulated suction lines. Suction lines should
be insulated with a nonabsorbent insulation
material such as Armstrong's Armaex.
b. Where condensate drains are located in dead
air spaces (between refrigerators or between a
refrigerator and a wall), provide means to prevent
freezing. The water seal should be insulated to
prevent condensation.
Installation (Cont'd)
Bolt
Silicone
Camlock
Joint Trim
After cases have been leveled and joined and refrigeration,
electrical and wasted piping work completed, install the
splashguards. Fasten along the top edge, or center, with
#10 X 3/3" sheet metal screws.
DO NOT SEAL JOINT TRIM TO FLOOR!

Rev. 0608
5
Refrigeration
Refrigerant Type
The standard refrigerant will be R-22 unless otherwise
specied on the customer order. Check the serial plate on
the case for information.
Piping
The refrigerant line outlets are located under the case.
Locate rst the electrical box, the outlets are then on the
same side of the case, but at the opposite end. Insulate
suction lines to prevent condensation drippage.
Refrigeration Lines
Liquid Suction
3/8” O.D. 5/8” O.D.
NOTE: The standard coil is piped at 5/8" (suction); however,
the store tie-in may vary depending on the number of
coils and the draw the case has. Depending on the case
setup, the connecting point in the store may be 5/8”, 7/8”,
or 11/8”. Refer to the particular case you are hooking up.
Refrigerant lines should be sized as shown on the
refrigeration legend furnished by the store. Install P-TRAPS
(oil traps) at the base of all suction line vertical risers.
Pressure drop can rob the system of capacity. To keep the
pressure drop to a minimum, keep refrigerant line run as
short as possible, using the minimum number of elbows.
Where elbows are required, use long radius elbows only.
Control Settings
See RBB technical data sheet for the appropriate settings
for your merchandiser. Maintain these parameters to
achieve near constant product temperatures. Product
temperature should rst be measured in the morning, after
having been refrigerated overnight. For all multiplexing,
defrost should be time terminated. Defrost length and
frequency should be as directed in the RBB technical
data sheet. The number of defrosts per day should never
change. The duration of the defrost cycle may be adjusted
to meet conditions present at your location.
Access to TX Valves and Drain Lines
MECHANICAL - Remove product from end of case.
Remove product racks. Remove refrigeration and drain
access panels (labeled). TX valve (mechanical only) and
drain are located under the pans within the case.
ELECTRONIC - The electronic expansion valve master and
slave cylinder(s) are located within the electrical access
panel(s) in the rear of case. Rear panels lift up and out.
Electronic Expansion Valve (Optional)
A wide variety of electronic expansion valves and case
controllers can be utilized. Please refer to EEV and
controller Hussmann’s information sheet. Sensors for
electronic expansion valves will be installed on the coil inlet,
coil outlet, and in the discharge air. (Some supermarkets
require a 4th sensor in the return air). Case controllers will
be located in the electrical raceway or under the case.
Thermostatic Expansion Valve Location
This device is located on the same side as the refrigeration
stub. A Sporlan balanced port expansion valve model
is furnished as standard equipment, unless otherwise
specied by customer.
Expansion Valve Adjustment
Expansion valves must be adjusted to fully feed the
evaporator. Before attempting any adjustments, make
sure the evaporator is either clear or very lightly covered
with frost, and that the xture is within 10°F of its expected
operating temperature.
After case has been brought to running temperature
verify screws along glass clamp aluminum
extrusion are tight.
Measuring the Operating Superheat
1. Determine the suction pressure with an accurate
pressure gauge at the evaporator outlet.
2. From a refrigerant pressure temperature chart,
determine the saturation temperature at the
observed suction pressure.
3. Measure the temperature of the suction gas at the
thermostatic remote bulb location.
4. Subtract the saturation temperature obtained in step
No. 2 from the temperature measured in step No. 3.
5. The difference is superheat.
6. Set the superheat for 5°F - 7°F.
T-STAT Location
The T-STAT is located on the upper right hand side, inside
the light can. It's adjustment is accessible through a
pop-out chrome plug (1" round).

IGUP-RBB-0608
6
Electrical
Wiring Color Code
CASE MUST BE GROUNDED
NOTE: Refer to label afxed to case to determine the actual
conguration as checked in the “TYPE INSTALLED”
boxes.
Electrical Circuit Identication
Standard lighting for all models will be full length uorescent
lamps located within the case at the top. The switch
controlling the lights and the thermometer are located at
the rear of the case mullion.
BEFORE SERVICING
ALWAYS DISCONNECT ELECTRICAL
POWER AT THE MAIN DISCONNECT
WHEN SERVICING OR REPLACING ANY
ELECTRICAL COMPONENT.
This includes (but not limited to) Fans, Heaters
Thermostats, and Lights.
Field Wiring and Serial Plate Amperage
Field Wiring must be sized for component amperes printed
on the serial plate. Actual ampere draw may be less than
specied. Field wiring from the refrigeration control panel to
the merchandisers is required for refrigeration thermostats.
Case amperes are listed on the wiring diagram, but always
check the serial plate.
Ballast Location
Ballasts are located within top canopy of the case near the
top lights.
User Information
Stocking
Improper temperature and lighting will cause serious
product loss. Discoloration, dehydration and spoilage
can be controlled with proper use of the equipment and
handling of product. Product temperature should always
be maintained at a constant and proper temperature.
This means that from the time the product is received,
through storage, preparation and display, the temperature
of the product must be controlled to maximize life of the
product. Hussmann cases were not designed to “heat up”
or “cool down” product - but rather to maintain an item’s
proper temperature for maximum shelf life. To achieve the
protection required always:
1. Minimize processing time to avoid damaging
temperature rise to the product. Product should be
at proper temperature.
2. Keep the air in and around the case area free
of foreign gasses and fumes or food will rapidly
deteriorate.
3. Maintain the display merchandisers temperature
controls as outlined in the refrigerator section of this
manual.
4. Do not place any product into these refrigerators
until all controls have been adjusted and they
are operating at the proper temperature. Allow
merchandiser to operate a minimum of 6 hours
before stocking with any product.
5. When stocking, never allow the product to extend
beyond the recommended load limit. Air discharge
and return air ue must be unobstructed at all times
to provide proper refrigeration.
6. Avoid the use of supplemental ood or spot lighting.
Display light intensity has been designed for
maximum visibility and product life at the factory.
The use of higher output uorescent lamps (H.O.
and V.H.O.), will shorten the shelf life of the product.
Important Steps
1. Do not set temperature too cold, as this causes
product dehydration. Set thermostat per Case specs
section. Process the meat to enter case at 40°F or
below. Product deterioration is very rapid above
40°F.
2. Discharge air temperature should be set per case
specication section.

Rev. 0608
7
Case Cleaning
Long life and satisfactory performance of any equipment
are dependent upon the care given to it. To insure long
life, proper sanitation and minimum maintenance costs,
the refrigerator should be thoroughly cleaned frequently.
SHUT OFF FAN DURING CLEANING PROCESS. It can
be unplugged within the case, or shut off entire case at
the source. The interior bottom may be cleaned with any
domestic soap or detergent based cleaners. Sanitizing
solutions will not harm the interior bottom, however,
these solutions should always be used according to the
Hussmann’s directions. It is essential to establish and
regulate cleaning procedures. This will minimize bacteria
causing discoloration which leads to degraded product
appearance and signicantly shortening product shelf
life.
Soap and hot water are not enough to kill this bacteria. A
sanitizing solution must be included with each cleaning
process to eliminate this bacteria.
1. Scrub thoroughly, cleaning all surfaces, with soap
and hot water.
2. Rinse with hot water, but do not ood.
3. Apply the sanitizing solution according to
Hussmann’s directions.
4. Rinse thoroughly.
5. Dry completely before resuming operation.
Cleaning Glass and Mirrors
Only use a soft cloth and mild glass cleaner for cleaning
any glass or mirrored components. Be sure to rinse and/or
dry completely.
Never use hot water on cold glass surfaces! It may
shatter and cause serious injury! Allow glass surfaces
to warm rst.
CLEANING PRECAUTIONS
When cleaning:
• Do not use high pressure water hoses
• Do not introduce water faster than waste outlet can drain
• NEVER USE A CLEANING OR SANITIZING SOLUTION THAT HAS AN OIL
BASE (these will dissolve the butyl sealants) or an AMMONIA BASE
(this will corrode the copper componets of the case)
TO PRESERVE THE ATTRACTIVE FINISH:
• DO USE WATER AND A MILD DETERGENT FOR THE EXTERIOR ONLY
• DO NOT USE ABRASIVES OR STEEL WOOL PADS AS THESE
WILL MAR THE FINISH
Plexiglass and Acrylic Care
Cleaning
Clean with plenty of nonabrasive soap (or detergent) and
luke warm water, using the bare hand to feel and dislodge
any caked-on dirt.A soft, grit-free cloth, sponge or chamois
may be used, but only as a means of carrying the water to
the plastic. Dry with a clean damp chamois or clean soft
cloth such as cotton annel. Hard, rough cloths or paper
towels will scratch the acrylic and should not be used.
Waxing
If after removing dirt and grease, the acrylic can be waxed
with a good grade commercial wax.This will improve the
appearance of the surface by lling in most minor scratches.
Wax should be applied in a thin even coat and brought to
a high polish by rubbing lightly with a dry clean soft cloth,
such as a cotton annel. Excessive rubbing may cause
scratching and/or buildup an electrostatic charge which
attracts dust and dirt to the surface. Blotting with a clean
damp cloth is recommended to remove charge.
Antistatic Coatings
For acrylic used indoors, antistatic coatings successfully
prevent the accumulation of an electrostatic charge for
periods of several months - if the surface is not washed
or wiped down with a wet cloth. Between applications of
the antistatic coatings, the parts need only be dusted with
a soft clean cloth to maintain a good appearance. In use,
liquid antistatic coatings should be applied in a very thin
even coat. If beads appear as it is applied, the coat is too
thick and the excess should be removed with another
cloth. Allow the coating to dry, then bring to a high gloss
with a soft cloth.
User Information (Cont'd)

IGUP-RBB-0608
8
Maintenance
Electrical Wiring Diagrams
RBB Standard Case 4' W1900001
6' W1900002
8' W1900003
12' W1900004
7' W1900015
Self Contained Cases 4' W1900005
6' W1900006
Single S/C ? 8' W1900009
8' W1900007
12' W1900008
RBB 8' REM With Einstein Control 8' W1900016
FOR PROMPT
SERVICEHave case Model and
Serial Numberready!
This information is located on
thenameplate of the unit.
BEFORE SERVICING
ALWAYS DISCONNECT ELECTRICAL
POWER AT THE MAIN DISCONNECT
WHEN SERVICING OR REPLACING ANY
ELECTRICAL COMPONENT.
This includes (but not limited to) Fans, Heaters
Thermostats, and Lights.
Replacing Fluorescent Lamps
The lamps supplied are single slim-line or bi-pan type with
or without starters.To remove, push in the one side and
pull the other end out of the socket. One end has a spring
loaded socket.
Evaporator Fans
The evaporator fans are located at the center front of these
merchandisers directly beneath the display pans. Should
fans or blades need servicing, always replace fan blades
with the raised embossed side of the blade TOWARD THE
MOTOR.
Coil Access
The access panel to the coil is through the back wall.
Remove shelves and unscrew the panel.
The coil can be accessed through the storage area.
Compressor Access
The compressor may be accessed by reaching over the
front fascia. If desired, the fascia can be removed by lifting
it up and out.
Tips and Troubleshooting
Before calling for service, check the following:
1. Check electrical power supply to the equipment for
connection.
2. Check xture loading. Overstocking case will affect
its proper operation.
3. If frost is collecting on xture and/or product, check
that Humidity Control is working properly, and that
no outside doors or windows are open - allowing
moisture to enter store.
FOR PROMPT SERVICE
When Contacting the Factory regarding problems.
Be sure to have the Case MODEL and
SERIAL NUMBER Handy. This Information
is on a plate located on the case itself.

Rev. 0608
9
Wiring Diagrams
DATE:
PROJECT TITLE: DRAWING #:
DRAWN BY:
PRODUCTION ORDER #: DRAWING TITLE:
DATE:
Hussmann Corporation, Int'l.
13770 Ramona Avenue
Chino, CA. 91710
(909)-590-4910 Lic.#: 644406
REVISIONS:
#: DESCRIPTION: CHECKED BY:
BY:
FILE LOCATION:
ADRIAN E. CRISCI
AEC
PAGE OF
?
11
06/08/01
A Updated dwg; revised load ratings 10/22/07 JR
RBB CASES W1900001
4' CASE - REMOTE WIRING DIAGRAM
LIGHT SWITCH
125-01-0307
BUNDLE COLOR
ORANGE
BALLAST 125-01-3266
FULHAM LH3-120-L
BALLAST 125-01-0681
MAGNETEK B260I120HP
BUNDLE COLOR
BROWN
BUNDLE COLOR
BLACK & WHITE
CANOPY LIGHT
(1) F48T12/830
SHELF LIGHTING
(3) FP28T5/830
MAIN CASE SUCTION
SOLENOID
225-01-3206
RBB REFRIGERATED BASE (OPTIONAL)
LOWER BASE SUCTION
SOLENOID
225-01-3206
MAIN CASE
T-STAT
225-01-0707
RBB MAIN CASE
LOWER BASE
T-STAT
225-01-0707
CAP UNUSED
BLUE LEAD
BALLAST 125-01-3266
FULHAM LH3-120-L
CAP UNUSED
RED LEAD
BLK # 14
WHT # 14
~120 VAC - 60 Hz.
MCA= 1.53A
MOP= 15A
L1 N
M
LIGHT CIRCUIT= 1.22A 132W
BLK # 14
WHT # 14
~120 VAC - 60 Hz.
MCA= 1.6A
MOP= 15A
L1 N
BLK # 14
WHT # 14
~120 VAC - 60 Hz.
L1 N
EVAP FAN MOTOR
125-01-0615A
0.6A 49W@ 120VAC
BOHN COIL ASSY
U-09 115V 0.45A
225-02-0515
CIRCUIT #1
NOTE: CASE MUST
BE GROUNDED
2.3
L1
120 V
LOADING

IGUP-RBB-0608
10
DATE:
PROJECT TITLE: DRAWING #:
DRAWN BY:
PRODUCTION ORDER #: DRAWING TITLE:
DATE:
Hussmann Corporation, Int'l.
13770 Ramona Avenue
Chino, CA. 91710
(909)-590-4910 Lic.#: 644406
REVISIONS:
#: DESCRIPTION: CHECKED BY:
BY:
FILE LOCATION:
ADRIAN E. CRISCI
AEC
PAGE OF
?
11
06/08/01
A Updated dwg; revised load ratings 10/22/07 JR
RBB CASES W1900002
6' CASE - REMOTE WIRING DIAGRAM
LIGHT SWITCH
125-01-0307
BUNDLE COLOR
ORANGE
BALLAST 125-01-3266
FULHAM LH3-120-L
BALLAST 125-01-3266
FULHAM LH3-120-L
BALLAST 125-01-3266
FULHAM LH3-120-L
BALLAST 125-01-0681
MAGNETEK B260I120HP
BUNDLE COLOR
BROWN
BUNDLE COLOR
BLACK & WHITE
CANOPY LIGHTS
(2) F36T12/830
SHELF LIGHTING
(6) FP21T5/830
2ND. ROW
3RD. ROW
1ST. ROW
RBB REFRIGERATED BASE (OPTIONAL)
RBB MAIN CASE
M
BLK # 14
WHT # 14
~120 VAC - 60 Hz.
MCA= 2.29A
MOP= 15A
L1 N
BLK # 14
WHT # 14
~120 VAC - 60 Hz.
MCA= 1.6A
MOP= 15A
L1 N
BLK # 14
WHT # 14
~120 VAC - 60 Hz.
L1 N
LIGHT CIRCUIT= 1.83A 198W
MAIN CASE SUCTION
SOLENOID
225-01-3206
LOWER BASE SUCTION
SOLENOID
225-01-3206
MAIN CASE
T-STAT
225-01-0707
LOWER BASE
T-STAT
225-01-0707
EVAP FAN MOTOR
125-01-0615A
0.6A 49W@ 120VAC
BOHN COIL ASY
U-015-0
1.1 AMP @115VAC
225-02-0517
CIRCUIT #1 277W
NOTE: CASE MUST
BE GROUNDED
3.5
L1
120 V
LOADING
Wiring Diagrams (Cont'd)

Rev. 0608
11
DATE:
PROJECT TITLE: DRAWING #:
DRAWN BY:
PRODUCTION ORDER #: DRAWING TITLE:
DATE:
Hussmann Corporation, Int'l.
13770 Ramona Avenue
Chino, CA. 91710
(909)-590-4910 Lic.#: 644406
REVISIONS:
#: DESCRIPTION: CHECKED BY:
BY:
FILE LOCATION:
ADRIAN E. CRISCI
AEC
PAGE OF
?
11
06/08/01
A Updated dwg; revised load ratings 10/22/07 JR
RBB CASES W1900003
8' CASE - REMOTE WIRING DIAGRAM
LIGHT SWITCH
125-01-0307
BUNDLE COLOR
ORANGE
BALLAST 125-01-3266
FULHAM LH3-120-L
BALLAST 125-01-3266
FULHAM LH3-120-L
BALLAST 125-01-3266
FULHAM LH3-120-L
BALLAST 125-01-0681
MAGNETEK B260I120HP
BUNDLE COLOR
BROWN
BUNDLE COLOR
BLACK & WHITE
CANOPY LIGHTS
(2) F48T12/830
SHELF LIGHTING
(6) FP28T5/830
2ND. ROW
3RD. ROW
1ST. ROW
RBB REFRIGERATED BASE (OPTIONAL)
RBB MAIN CASE
M
M
BOHN COIL ASY
U-015-0
1.1 AMP @115VAC
225-02-0517
BLK # 14
WHT # 14
~120 VAC - 60 Hz.
MCA= 2.6A
MOP= 15A
L1 N
BLK # 14
WHT # 14
~120 VAC - 60 Hz.
L1 N
MAIN CASE SUCTION
SOLENOID
225-01-3206
LOWER BASE SUCTION
SOLENOID
225-01-3206
MAIN CASE
T-STAT
225-01-0707
LOWER BASE
T-STAT
225-01-0707
EVAP FAN MOTOR
125-01-0615A
0.6A 49W@ 120VAC
BLK # 14
WHT # 14
~120 VAC - 60 Hz.
MCA= 3.13A
MOP= 15A
L1 N
LIGHT CIRCUIT= 2.5A 264W
CIRCUIT #1
NOTE: CASE MUST
BE GROUNDED
4.8
L1
120 V
LOADING
Wiring Diagrams (Cont'd)

IGUP-RBB-0608
12
DATE:
PROJECT TITLE: DRAWING #:
DRAWN BY:
PRODUCTION ORDER #: DRAWING TITLE:
DATE:
Hussmann Corporation, Int'l.
13770 Ramona Avenue
Chino, CA. 91710
(909)-590-4910 Lic.#: 644406
REVISIONS:
#: DESCRIPTION: CHECKED BY:
BY:
FILE LOCATION:
ADRIAN E. CRISCI
AEC
PAGE OF
?
11
06/08/01
A Updated dwg; revised load ratings 10/29/07 JR
RBB CASES W1900004
12' CASE - REMOTE WIRING DIAGRAM
LIGHT SWITCH
125-01-0307
BUNDLE COLOR
ORANGE
BALLAST 125-01-3266
FULHAM LH3-120-L
BALLAST 125-01-3266
FULHAM LH3-120-L
BALLAST 125-01-3266
FULHAM LH3-120-L
BALLAST 125-01-3266
FULHAM LH3-120-L
BALLAST 125-01-3266
FULHAM LH3-120-L CAP UNUSED
RED LEAD
BALLAST 125-01-0681
MAGNETEK B260I120HP
BUNDLE COLOR
BROWN
BUNDLE COLOR
BLACK & WHITE
CANOPY LIGHTS
(2) F72T12/830
SHELF LIGHTING
(9) FP28T5/830
2ND. ROW 3RD. ROW1ST. ROW
RBB REFRIGERATED BASE (OPTIONAL)
RBB MAIN CASE
M
M
M
BOHN COIL ASY
U-015-0
1.1 AMP @115VAC
(2) 225-02-0517
MAIN CASE SUCTION
SOLENOID
225-01-3206
MAIN CASE
T-STAT
225-01-0707
LOWER BASE SUCTION
SOLENOID
225-01-3206
LOWER BASE
T-STAT
225-01-0707
BLK # 14
WHT # 14
~120 VAC - 60 Hz.
MCA= 4.2A
MOP= 15A
L1 N
BLK # 14
WHT # 14
~120 VAC - 60 Hz.
L1 N
LIGHT CIRCUIT= 3.67A 396W
BLK # 14
WHT # 14
~120 VAC - 60 Hz.
MCA= 4.6A
MOP= 15A
L1 N
EVAP FAN MOTOR
(3)125-01-0615A
0.6A 49W@ 120VAC
CIRCUIT #1
NOTE: CASE MUST
BE GROUNDED
7.7
L1
120 V
LOADING
Wiring Diagrams (Cont'd)

Rev. 0608
13
DATE:
PROJECT TITLE: DRAWING #:
DRAWN BY:
PRODUCTION ORDER #: DRAWING TITLE:
DATE:
Hussmann Corporation, Int'l.
13770 Ramona Avenue
Chino, CA. 91710
(909)-590-4910 Lic.#: 644406
REVISIONS:
#: DESCRIPTION: CHECKED BY:
BY:
FILE LOCATION:
JESSE RIOS
PAGE OF
?
11
885699
11
5/10/07 RBB CASES W1900015
7' CASE - REMOTE WIRING DIAGRAM
BUNDLE COLOR
ORANGE
LABELED LIGHT
CIRCUIT
BUNDLE COLOR
BROWN
LABELED FAN
CIRCUIT
BUNDLE COLOR
BLACK & WHITE
LABELED 120V
THERMOSTAT/
SOLENOID
LIGHT
F30/T12/SPX30
125-03-0012B
(2) EVAPORATOR
FANS
GE 9W - 120V 0.60A
125-01-0615A
SUCTION
SOLENOID
225-01-3206
T-STAT
225-01-0707
L N
L N L N
MM
~120 VAC - 60 Hz.
MCA= .81A
MOP= 15A
LIGHT CIRCUIT= .65A
~120 VAC - 60 Hz.
MCA= 1.4A
MOP= 15A
~120 VAC - 60 Hz.
LIGHT
F48/T12/SPX30
125-03-0120C
BALLAST 125-01-0681
MAGNETEK B260I120HP
BALLAST 125-01-0642
MAGNETEK B140R120HP
CAP UNUSED
BLUE LEAD
CAP UNUSED
BLUE LEAD
L
LIGHT SWITCH
TIPPETTE
125-01-0311
BLACK # 14
WHITE # 14
BLACK # 14
WHITE # 14
BLK # 14
WHT # 14
1.9
L1
L2
L3
LOADING
L1
L2
L3
LOADING
L1
L2
L3
LOADING
L1
L2
L3
LOADING
L1
L2
L3
LOADING
L1
L2
L3
LOADING
L1
L2
L3
LOADING
L1
L2
L3
LOADING
120 V
CIRCUIT #1
NOTE: CASE MUST
BE GROUNDED
Wiring Diagrams (Cont'd)

IGUP-RBB-0608
14
DATE:
PROJECT TITLE: DRAWING #:
DRAWN BY:
PRODUCTION ORDER #: DRAWING TITLE:
DATE:
Hussmann Corporation, Int'l.
13770 Ramona Avenue
Chino, CA. 91710
(909)-590-4910 Lic.#: 644406
REVISIONS:
#: DESCRIPTION: CHECKED BY:
BY:
FILE LOCATION:
ADRIAN E. CRISCI
AEC
PAGE OF
?
11
06/12/01
A Updated dwg; revised load ratings 12/3/07 JR
RBB CASES W1900005
4' CASE - SELF CONTAINED DIAGRAM
LIGHT SWITCH
125-01-0307
BUNDLE COLOR
ORANGE
BALLAST 125-01-3266
FULHAM LH3-120-L
BALLAST 125-01-0681
MAGNETEK B260I120HP
BUNDLE COLOR
BROWN
BUNDLE COLOR
BLACK & WHITE
CANOPY LIGHT
(1) F48T12/830
SHELF LIGHTING
(3) FP28T5/830
RBB REFRIGERATED BASE (OPTIONAL)
LOWER BASE LIQUID
SOLENOID
RBB MAIN CASE
LOWER BASE
T-STAT
CAP UNUSED
BLUE LEAD
BALLAST 125-01-3266
FULHAM LH3-120-L CAP UNUSED
RED LEAD
TX
4
N
3
1
2
CONDENSER FAN
~208 VAC
DEFROST TIMER
PARAGON 8045-20
~208 V - 60 Hz.
125-01-0715
NOTE:
LOWER SECTION IS
GREATLY REDUCED
IN SIZE BY THE CON-
DENSING UNIT.
M
M
CONDENSING UNIT - COPELAND®
F9AM-A103-CFV-140
RLA= 9.5A 1857W
MCC= 13.3
LRA= 43.3A
225-03-0121
CONDENSING UNIT
C
R
EVAP FAN MOTOR
125-01-0615A
0.6A 49W@ 120VAC
BOHN COIL ASSY
U-09 115V 0.45A
225-02-0515
LIGHT CIRCUIT= 1.22A 132W
L1
L2
N
G
~208 / 240 VAC - 50/60 Hz.
RED # 14
GREEN # 14
WHT # 14
BLK # 14
WHT # 14
BLK # 14
SWITCH
MOTOR START
SQ "D"
125-01-0271
PRESSURE
SAFETY
225-01-0706B
T-STAT
225-01-2010
CIRCUIT #1
NOTE: CASE MUST
BE GROUNDED
11.8
9.5
11.8
9.5
L1
L2
208 V 240 V
LOADING
Wiring Diagrams (Cont'd)

Rev. 0608
15
DATE:
PROJECT TITLE: DRAWING #:
DRAWN BY:
PRODUCTION ORDER #: DRAWING TITLE:
DATE:
Hussmann Corporation, Int'l.
13770 Ramona Avenue
Chino, CA. 91710
(909)-590-4910 Lic.#: 644406
REVISIONS:
#: DESCRIPTION: CHECKED BY:
BY:
FILE LOCATION:
ADRIAN E. CRISCI
AEC
PAGE OF
1 1
06/14/01
H:\WIRESCHEMATICS\NEWWIRE
RBB CASES W1900006
6' CASE - SELF CONTAINED DIAGRAM
LIGHT SWITCH
125-01-0307
BUNDLE COLOR
ORANGE
BALLAST 125-01-3266
FULHAM LH3-120-L
BALLAST 125-01-3266
FULHAM LH3-120-L
BALLAST 125-01-3266
FULHAM LH3-120-L
BALLAST 125-01-0681
MAGNETEK B260I120HP
BUNDLE COLOR
BROWN
BUNDLE COLOR
BLACK & WHITE
M
CANOPY LIGHTS
(2) F36T12/830
SHELF LIGHTING
(6) FP21T5/830
2ND. ROW
3RD. ROW
1ST. ROW
EVAPORATOR FANS
GE 9W - 115V
RBB REFRIGERATED BASE (OPTIONAL)
EVAPORATOR FANS
BOHN COIL UNIT
LOWER BASE LIQUID
SOLENOID
LOWER BASE
T-STAT
RBB MAIN CASE
L N POWER: ~115 VAC - 50/60 Hz. - 3 WIRE POWER: ~115 VAC - 50/60 Hz. - 3 WIRE
L N L N
M
S
C
R
M
C
2
1
3
RS
TX
4
N
3
1
2
L1 L2 N COMPRESSOR
MOTOR
CONDENSER FAN
~208 VAC
START
CAPACITOR
EXTERNAL
PROTECTOR
T-STAT
PRESSURE
SAFETY
POWER
SWITCH
DEFROST TIMER
PARAGON 8045-20
~208 V - 60 Hz.
125-01-0715
5
2
1
POTENCIAL
RELAY
RED
YELLOW
BLUE
BLACK
RUN CAPACITOR
POWER: ~208 / ~230 VAC - 60 Hz. - 4 WIRE
CONTACTOR
SQUARE -D
8910DPA43V02
125-01-0002
1½ HP CONDENSING
UNIT CIRCUIT
NOTE: CASE MUST BE GROUNDED
NOTE:
LOWER SECTION IS
GREATLY REDUCED
IN SIZE BY THE CON-
DENSING UNIT.
Wiring Diagrams (Cont'd)

IGUP-RBB-0608
16
DATE:
PROJECT TITLE: DRAWING #:
DRAWN BY:
PRODUCTION ORDER #: DRAWING TITLE:
DATE:
Hussmann Corporation, Int'l.
13770 Ramona Avenue
Chino, CA. 91710
(909)-590-4910 Lic.#: 644406
REVISIONS:
#: DESCRIPTION: CHECKED BY:
BY:
FILE LOCATION:
ADRIAN E. CRISCI
AEC
PAGE OF
1 1
06/14/01
H:\WIRESCHEMATICS\NEWWIRE
RBB CASES W1900007
8' CASE - SELF CONTAINED DIAGRAM
M
LIGHT SWITCH
125-01-0307
BUNDLE COLOR
ORANGE
BALLAST 125-01-3266
FULHAM LH3-120-L
BALLAST 125-01-3266
FULHAM LH3-120-L
BALLAST 125-01-3266
FULHAM LH3-120-L
BALLAST 125-01-0681
MAGNETEK B260I120HP
BUNDLE COLOR
BROWN
BUNDLE COLOR
BLACK & WHITE
CANOPY LIGHTS
(2) F48T12/830
SHELF LIGHTING
(6) FP28T5/830
2ND. ROW
3RD. ROW
1ST. ROW
EVAPORATOR FANS
(2) GE 9W - 115V
RBB REFRIGERATED BASE
(OPTIONAL)
EVAPORATOR FAN
(1) BOHN COIL UNIT
LOWER BASE LIQUID
SOLENOID
RBB MAIN CASE
L N POWER: ~115 VAC - 50/60 Hz. - 3 WIRE POWER: ~115 VAC - 50/60 Hz. - 3 WIRENL
N
L
M
M
LOWER BASE
T-STAT
S
C
R
M
C
2
1
3
RS
TX
4
N
3
1
2
L1 L2 N COMPRESSOR
MOTOR
CONDENSER FAN
~208 VAC
START
CAPACITOR
EXTERNAL
PROTECTOR
T-STAT
PRESSURE
SAFETY
POWER
SWITCH
DEFROST TIMER
PARAGON 8045-20
~208 V - 60 Hz.
125-01-0715
5
21
POTENCIAL
RELAY
RED
YELLOW
BLUE
BLACK
RUN CAPACITOR
POWER: ~208 / ~230 VAC
- 60 Hz. - 4 WIRE
S
C
R
C
2
1
3
RS
COMPRESSOR
MOTOR
START
CAPACITOR
EXTERNAL
PROTECTOR
5
21
POTENCIAL
RELAY
RED
YELLOW
BLUE
BLACK
RUN CAPACITOR
T-STAT
PRESSURE
SAFETY
MCONDENSER
FAN ~208 VAC
CONTACTOR
SQUARE -D
8910DPA43V02
125-01-0002
RIGHT COIL
LEFT COIL
(2) 1 HP CONDENSING
UNIT CIRCUITS
NOTE: CASE MUST BE GROUNDED
NOTE:
LOWER SECTION IS
GREATLY REDUCED
IN SIZE BY THE CON-
DENSING UNIT.
Wiring Diagrams (Cont'd)

Rev. 0608
17
DATE:
PROJECT TITLE: DRAWING #:
DRAWN BY:
PRODUCTION ORDER #: DRAWING TITLE:
DATE:
Hussmann Corporation, Int'l.
13770 Ramona Avenue
Chino, CA. 91710
(909)-590-4910 Lic.#: 644406
REVISIONS:
#: DESCRIPTION: CHECKED BY:
BY:
FILE LOCATION:
ADRIAN E. CRISCI
AEC
PAGE OF
1 1
06/18/01
H:\WIRESCHEMATICS\NEWWIRE
RBB CASES W1900008
12' CASE - SELF CONTAINED DIAGRAM
M
LIGHT SWITCH
125-01-0307
BUNDLE COLOR
ORANGE
BALLAST 125-01-3266
FULHAM LH3-120-L
BALLAST 125-01-3266
FULHAM LH3-120-L
BALLAST 125-01-3266
FULHAM LH3-120-L
BALLAST 125-01-3266
FULHAM LH3-120-L
BALLAST 125-01-3266
FULHAM LH3-120-L
CAP UNUSED
RED LEAD
BALLAST 125-01-0681
MAGNETEK B260I120HP
M
M
M
BUNDLE COLOR
BROWN
BUNDLE COLOR
BLACK & WHITE
M
CANOPY LIGHTS
(2) F72T12/830
SHELF LIGHTING
(9) FP28T5/830
2ND. ROW 3RD. ROW
1ST. ROW
EVAPORATOR FANS
(3) GE 9W - 115V
RBB REFRIGERATED
BASE (OPTIONAL)
EVAPORATOR FANS
(2) BOHN COIL
UNITS
LOWER BASE LIQUID
SOLENOID
RBB MAIN CASE
L N POWER: ~115 VAC - 50/60 Hz. - 3 WIRE POWER: ~115 VAC - 50/60 Hz. - 3 WIRE N
L
N
L
LOWER BASE
T-STAT
S
C
R
M
C
2
1
3
RS
TX
4
N
3
1
2
L1 L2 N COMPRESSOR
MOTOR
CONDENSER FAN
~208 VAC
START
CAPACITOR
EXTERNAL
PROTECTOR
T-STAT
PRESSURE
SAFETY
POWER
SWITCH
DEFROST TIMER
PARAGON 8045-20
~208 V - 60 Hz.
125-01-0715
5
21
POTENCIAL
RELAY
RED
YELLOW
BLUE
BLACK
RUN CAPACITOR
POWER: ~208 / ~230 VAC
- 60 Hz. - 4 WIRE
CONTACTOR
SQUARE -D
8910DPA43V02
125-01-0002
C
2
1
3
RSSTART
CAPACITOR
EXTERNAL
PROTECTOR
5
2
1
POTENCIAL
RELAY
RED
YELLOW
BLUE
BLACK
RUN CAPACITOR
T-STAT
PRESSURE
SAFETY
MCONDENSER
FAN ~208 VAC
CONTACTOR
SQUARE -D
8910DPA43V02
125-01-0002
CONTACTOR
SQUARE -D
8910DPA43V02
125-01-0002
RIGHT COIL
LEFT COIL
(2) 1½ HP CONDENSING
UNIT CIRCUITS
S
C
R
COMPRESSOR
MOTOR
NOTE: CASE MUST BE GROUNDED
NOTE:
LOWER SECTION IS
GREATLY REDUCED
IN SIZE BY THE CON-
DENSING UNIT.
Wiring Diagrams (Cont'd)

IGUP-RBB-0608
18
DATE:
:
#
GW
D
:EL
T
IT
TC
E
J
ORPDRAWN BY:
PRODUCTION ORDER #: DRAWING TITLE:
DATE:
REVISIONS:
:YB
DEK
CEH
C
:
N
O
I
TP
IRCSE
D:
# BY:
FILE LOCATION:
ADRIAN E. CRISCI
AEC
PAGE OF
HUSSMANN® CORPORATION
13770 RAMONA AVENUE
CHINO, CA.91710
(909) 590-4910 LIC.#: 644406
1
2
31 1
11/05/02
H:\WIRESCHEMATICS\NEW-WIRING
RBB CASES W1900009
RBB-8' S/C - SINGLE C-UNIT BASE MOUNTED
932289
M
LIGHT SWITCH
125-01-0307
BUNDLE COLOR
ORANGE
BALLAST 125-01-3266
FULHAM LH3-120-L
BALLAST 125-01-3266
FULHAM LH3-120-L
BALLAST 125-01-3266
FULHAM LH3-120-L
BALLAST 125-01-0681
MAGNETEK B260I120HP
BUNDLE COLOR
BROWN
BUNDLE COLOR
BLACK & WHITE
CANOPY LIGHTS
(2) F48T12/830
SHELF LIGHTING
(6) FP28T5/830
2ND. ROW
3RD. ROW
1ST. ROW
EVAPORATOR FANS
(2) GE 9W - 115V
RBB REFRIGERATED BASE
(OPTIONAL)
EVAPORATOR FAN
(1) BOHN COIL UNIT
LOWER BASE LIQUID
SOLENOID
RBB MAIN CASE
L N POWER: ~115 VAC - 50/60 Hz. - 3 WIRE POWER: ~115 VAC - 50/60 Hz. - 3 WIRENLN
L
M
M
LOWER BASE
T-STAT
S
C
R
M
C
2
1
3
RS
TX
4
N
3
1
2
L1 L2 N COMPRESSOR
MOTOR
CONDENSER FAN
~208 VAC
START
CAPACITOR
EXTERNAL
PROTECTOR
T-STAT
PRESSURE
SAFETY
POWER
SWITCH
DEFROST TIMER
PARAGON 8045-20
~208 V - 60 Hz.
125-01-0715
5
2
1
POTENCIAL
RELAY
RED
YELLOW
BLUE
BLACK
RUN CAPACITOR
POWER: ~208 / ~230 VAC
- 60 Hz. - 4 WIRE
CONTACTOR
SQUARE -D
8910DPA43V02
125-01-0002
RIGHT COIL
(1) 1½ HP CONDENSING
UNIT CIRCUIT
CONDENSING UNIT - COPELAND® MODEL F9AM-0175-CFV-140
225-03-0102 - 1½ HP- 12.9RLA - 54.0 LRA - 19.0 MCA @208VAC
Wiring Diagrams (Cont'd)

Rev. 0608
19
DATE:
PROJECT TITLE: DRAWING #:
DRAWN BY:
PRODUCTION ORDER #: DRAWING TITLE:
DATE:
Hussmann Corporation, Int'l.
13770 Ramona Avenue
Chino, CA. 91710
(909)-590-4910 Lic.#: 644406
REVISIONS:
#: DESCRIPTION: CHECKED BY:
BY:
FILE LOCATION:
JESSE RIOS
PAGE OF
?
12
6/1/07 RBB W1900016
RBB 8' REM
914357
BALLAST 125-01-3266
FULHAM LH3-120-L
BALLAST 125-01-3266
FULHAM LH3-120-L
CANOPY LIGHT
F96T12
125-03-0064C
2ND. ROW
3RD. ROW
1ST. ROW
EEPR ESR-12-T-7-S/T 12V
225-01-3165
RBB MAIN CASE
BALLAST 125-01-3266
FULHAM LH3-120-L
M
M
SHELF LIGHTING
(6) FP28T5 48"
125-03-1131
BLACK # 14
WHITE # 14
TO EINSTEIN POWER MODULE
CPC CS-100 CONTROLLER
CONNECTION 1 AND 2
LIGHT CIRCUIT= 2.2A
EVAPORATOR FAN
0.60 A
(2)125-01-0615A
BLACK # 14
WHITE # 14
TO EINSTEIN POWER MODULE
CPC CS-100 CONTROLLER
CONNECTION 3 AND 4
BLACK # 14
RED # 14
12VDC
- +
OPTIONAL
SENSOR
SENSOR
CPC
225-01-3260
BALLAST 125-01-0681
MAGNETEK B260I120HP
CAP UNUSED
BLUE LEAD
T-STAT
(1) 225-01-0710
SUCTION SOLENOID
(1) 225-01-3206
BUNDLE
WHITE/BLACK
BOHN COIL
CIRCUIT
~120 VAC - 60 Hz
L1 N
BLACK #14
WHITE #14
BOHN COIL ASSY
(1) U-015-0 120V 1.1A
225-02-0517
MCA= 1.4A
MOP= 15A
TO EINSTEIN POWER MODULE
CPC CS-100 CONTROLLER
STEPPER VALVE CABLE
NOTE: CASE MUST
BE GROUNDED
4.5L1
L2
L3
120 V
LOADING
Wiring Diagrams (Cont'd)

IGUP-RBB-0608
20
DATE:
PROJECT TITLE: DRAWING #:
DRAWN BY:
PRODUCTION ORDER #: DRAWING TITLE:
DATE:
Hussmann Corporation, Int'l.
13770 Ramona Avenue
Chino, CA. 91710
(909)-590-4910 Lic.#: 644406
REVISIONS:
#: DESCRIPTION: CHECKED BY:
BY:
FILE LOCATION:
JESSE RIOS
PAGE OF
?
1
2
3
4
5
6
LIGHT - LINE
LIGHT - NEUTRAL
FAN - LINE
FAN - NEUTRAL
ANTI-SWEAT-LINE
ANTI-SWEAT-COMMON
EINSTEIN POWER MODULE
CPC CS-100 CONTROLLER
0381785
1
2
3
4
5
6
TO +24VAC CLASS 2 50VA SOURCE
GROUND
NONE
NONE
AUX GROUND
AUX GROUIND
EINSTEIN
CPC CC-100 CONTROLLER
225-01-3540A
7
8
9
10
11
12
NONE
TO +24VAC CLASS 2 50 VA SOURCE
FANS
LIGHTS
ANTI-SWEAT
DEFROST
13
14
AUXILIARY 1
AUXILIARY 2
1
2
3
4
5
6
TO +24VAC CLASS 2 50VA SOURCE
GROUND
NONE
NONE
AUX GROUND
AUX GROUIND
7
8
9
10
11
12
NONE
TO +24VAC CLASS 2 50 VA SOURCE
FANS
LIGHTS
ANTI-SWEAT
DEFROST
13
14
AUXILIARY 1
AUXILIARY 2
1
2
3
4
5
6
STEPPER 2
STEPPER 1
STEPPER 3
STEPPER 4
+12V DC
GROUND
POWER CONTROLLER
STEPPER VALVE CABLE
TO LIGHT
TO FAN
TO ANTI-SWEAT
TO STEPPER
TO +12V DC
EINSTEIN P/N 335-3260
STEPPER VALVE CABLE
EINSTEIN P/N 335-3258
STEPPER OUTPUT CABLE
OPTIONS
22
6/1/07 RBB W1900016
RBB 8' REM
914357
Wiring Diagrams (Cont'd)
Other manuals for RBB
1
This manual suits for next models
1
Table of contents
Other Hussmann Display Case manuals
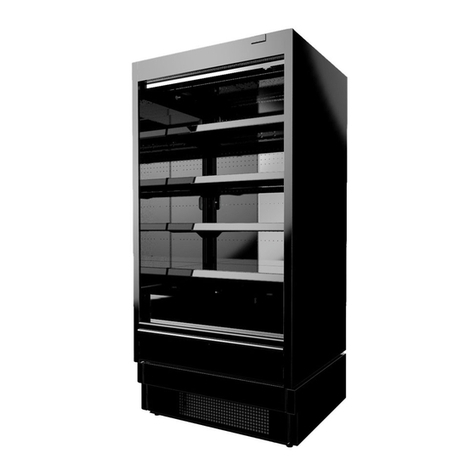
Hussmann
Hussmann Austral H1 User manual
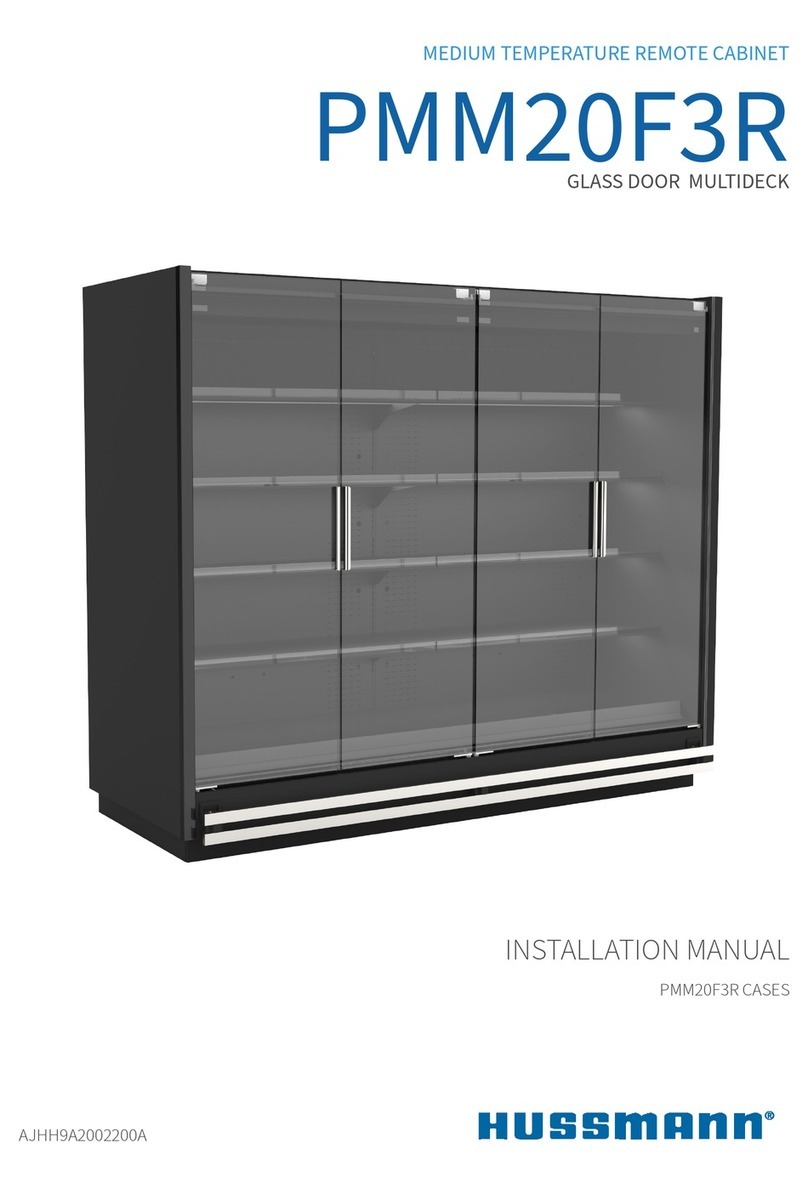
Hussmann
Hussmann PMM20F3R User manual
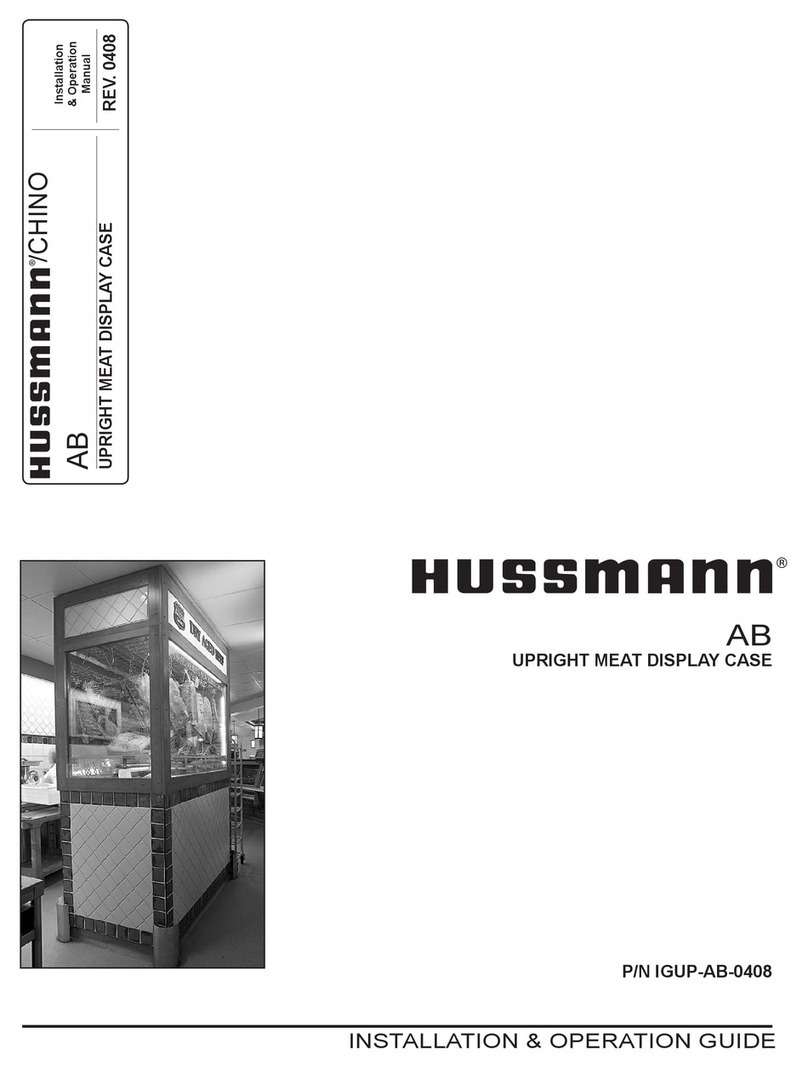
Hussmann
Hussmann AB Operating instructions
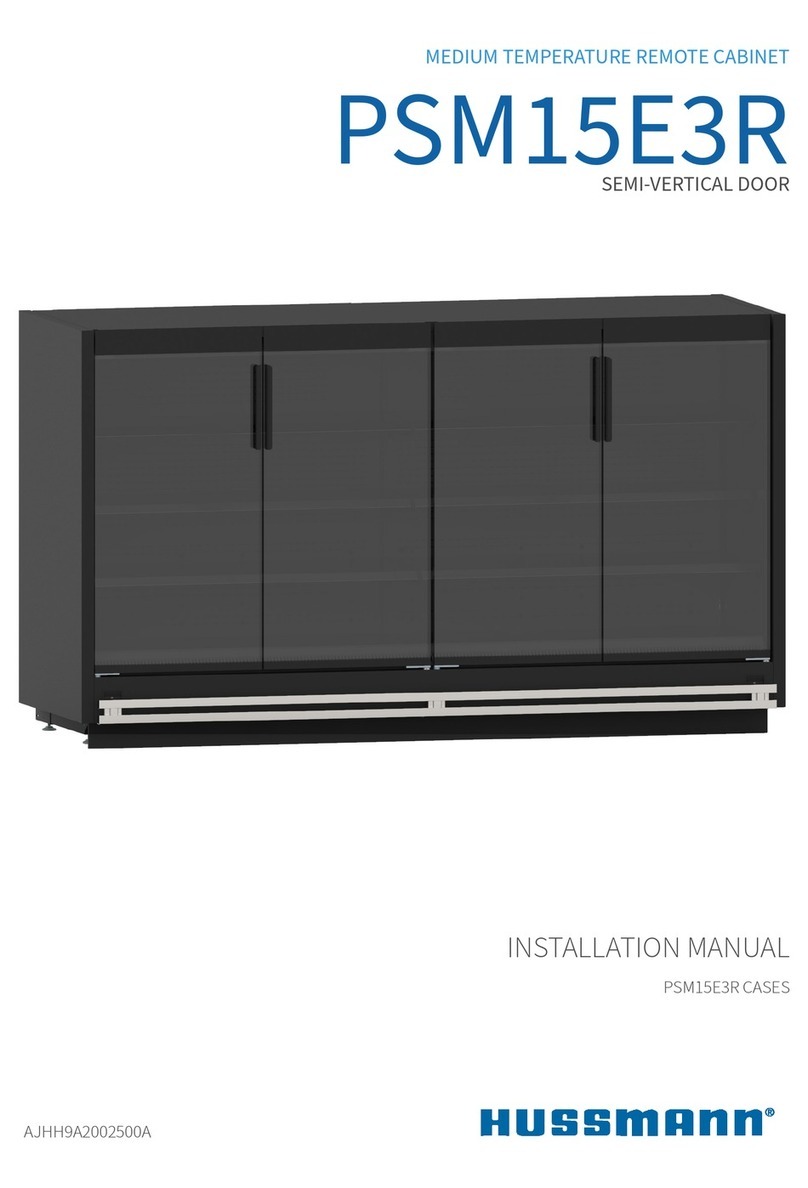
Hussmann
Hussmann PSM15E3R User manual
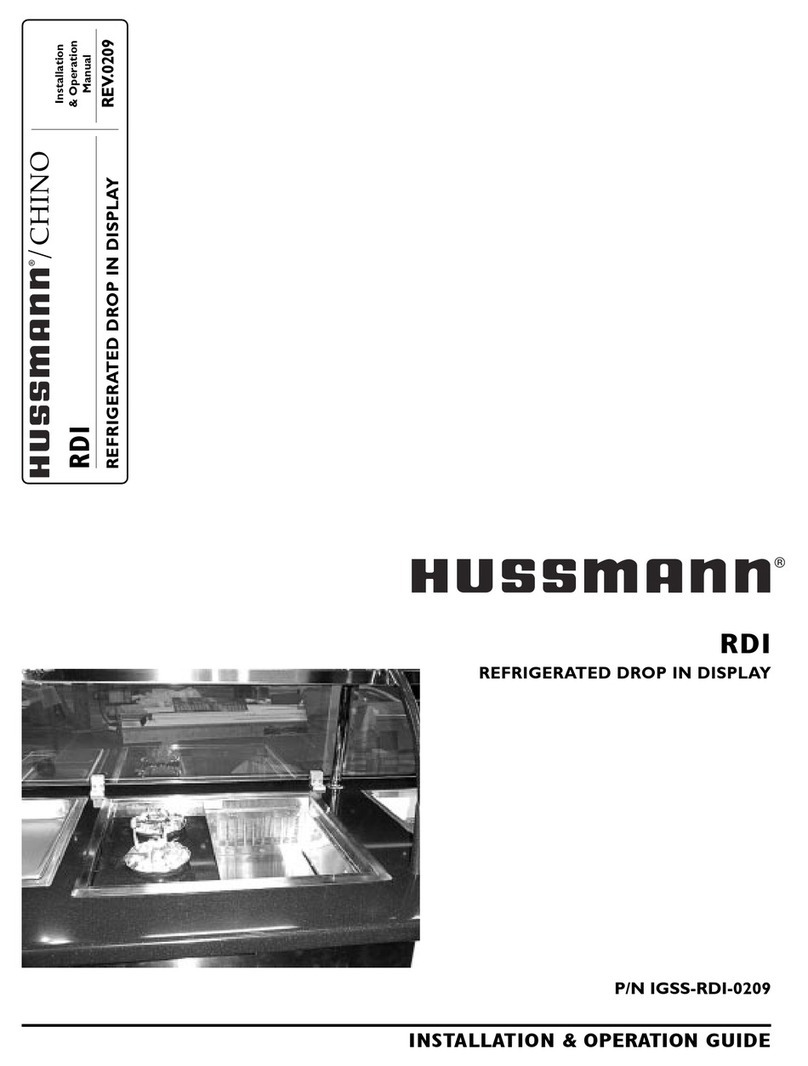
Hussmann
Hussmann RDI Operating instructions
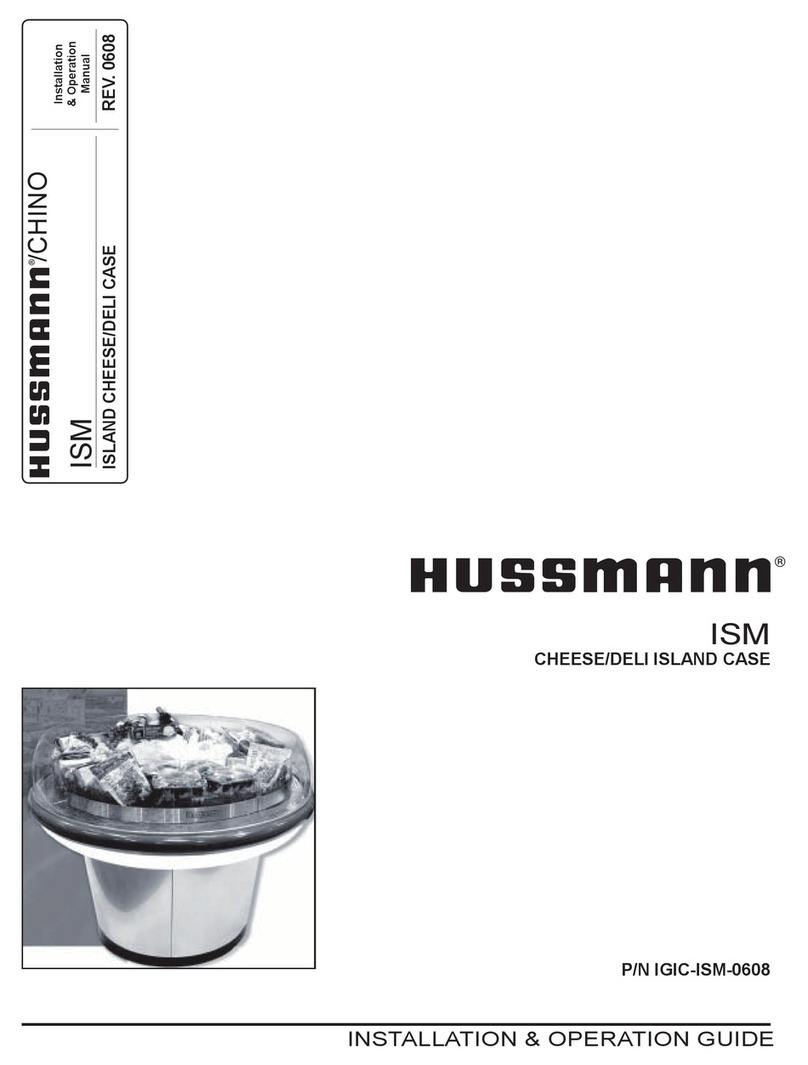
Hussmann
Hussmann ISM Operating instructions
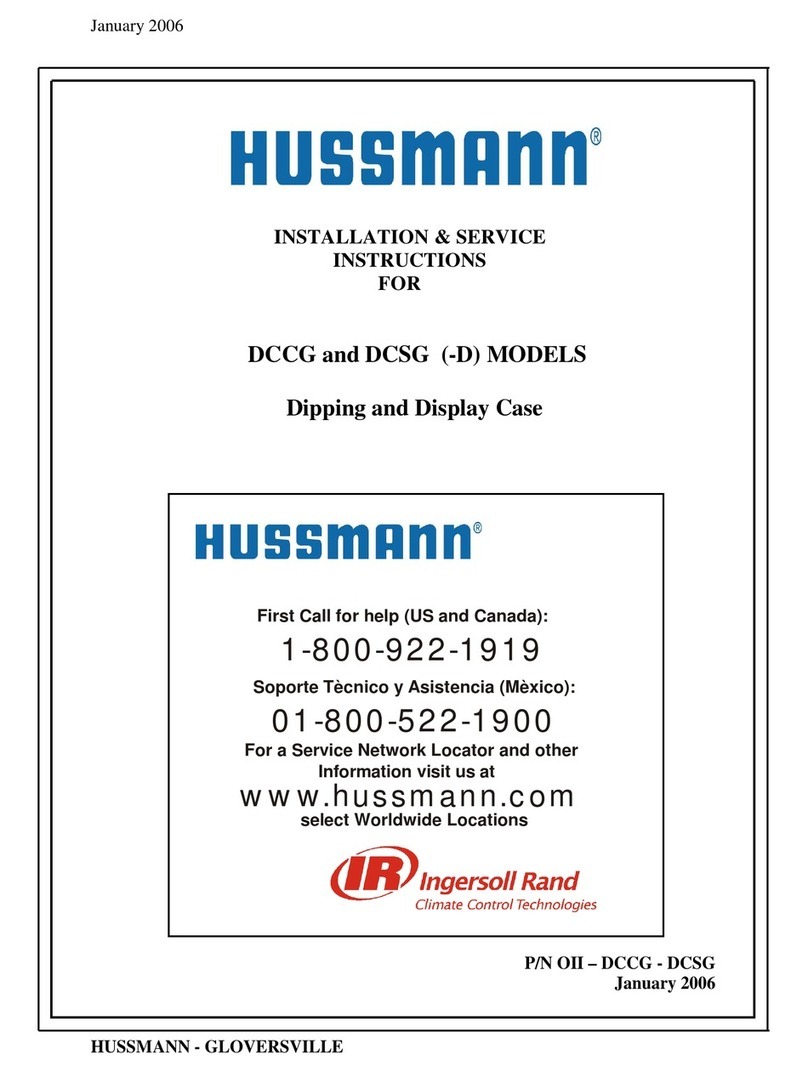
Hussmann
Hussmann DCCG-8 Quick guide
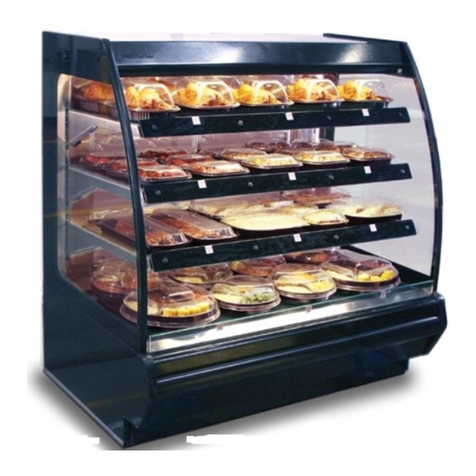
Hussmann
Hussmann ISLA Original operating instructions

Hussmann
Hussmann Q3-DV Original operating instructions
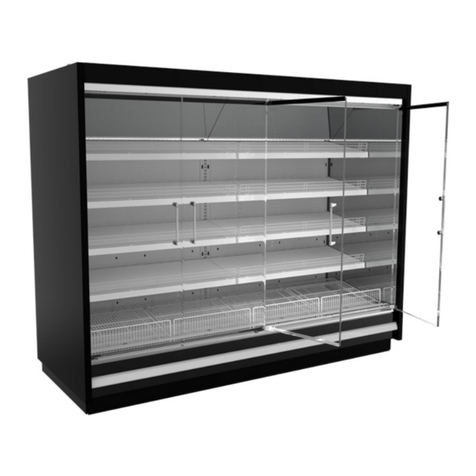
Hussmann
Hussmann MPD116 User manual