Hypertherm HRT User manual

Duramax™ Retrofit Torch
HRT, HRTs, MRT
Operator Manual – 807190
Revision 1


Operator Manual
(P/N 807190)
Revision 1 – May 2011
Hypertherm, Inc.
Hanover, NH USA
www.hypertherm.com
email: [email protected]
© 2011 Hypertherm, Inc.
All Rights Reserved
Hypertherm, Powermax, and Duramax are trademarks of Hypertherm, Inc.
and may be registered in the United States and/or other countries.
Duramax™ Retrofit Torch
HRT, HRTs, MRT

Hypertherm, Inc.
Etna Road, P.O. Box 5010
Hanover, NH 03755 USA
603-643-3441 Tel (Main Office)
603-643-5352 Fax (All Departments)
[email protected] (Main Office Email)
800-643-9878 Tel (Technical Service)
[email protected] (Technical Service Email)
800-737-2978 Tel (Customer Service)
customer.ser[email protected] (Customer Service Email)
Hypertherm Automation
5 Technology Drive, Suite 300
West Lebanon, NH 03784 USA
603-298-7970 Tel
603-298-7977 Fax
Hypertherm Plasmatechnik GmbH
Technologiepark Hanau
Rodenbacher Chaussee 6
D-63457 Hanau-Wolfgang, Deutschland
49 6181 58 2100 Tel
49 6181 58 2134 Fax
49 6181 58 2123 (Technical Service)
Hypertherm (S) Pte Ltd.
82 Genting Lane
Media Centre
Annexe Block #A01-01
Singapore 349567, Republic of Singapore
65 6841 2489 Tel
65 6841 2490 Fax
65 6841 2489 (Technical Service)
Hypertherm (Shanghai) Trading Co., Ltd.
Unit A, 5th Floor, Careri Building
432 West Huai Hai Road
Shanghai, 200052
PR China
86-21 5258 3330/1 Tel
86-21 5258 3332 Fax
Hypertherm Europe B.V.
Vaartveld 9
4704 SE
Roosendaal, Nederland
31 165 596907 Tel
31 165 596901 Fax
31 165 596908 Tel (Marketing)
31 165 596900 Tel (Technical Service)
00 800 4973 7843 Tel (Technical Service)
Hypertherm Japan Ltd.
Level 9, Edobori Center Building
2-1-1 Edobori, Nishi-ku
Osaka 550-0002 Japan
81 6 6225 1183 Tel
81 6 6225 1184 Fax
Hypertherm Brasil Ltda.
Avenida Doutor Renato de
Andrade Maia 350
Parque Renato Maia
CEP 07114-000
Guarulhos, SP Brasil
55 11 2409 2636 Tel
55 11 2408 0462 Fax
Hypertherm México, S.A. de C.V.
Avenida Toluca No. 444, Anexo 1,
Colonia Olivar de los Padres
Delegación Álvaro Obregón
México, D.F. C.P. 01780
52 55 5681 8109 Tel
52 55 5683 2127 Fax
Hypertherm Korea Branch
#3904 Centum Leaders Mark B/D,
1514 Woo-dong, Haeundae-gu, Busan
Korea, 612-889
82 51 747 0358 Tel
82 51 701 0358 Fax
03/08/11

9/10
Compliance Information EMC-1
Introduction
Hypertherm’s CE-marked equipment is built
in compliance with standard EN60974-10.
The equipment should be in stalled and used
in accordance with the information be low to
achieve elec tro mag net ic com pat i bil i ty.
The limits required by EN60974-10 may
not beadequate to com plete ly eliminate
interference whenthe affected equip ment
is in close proximity orhas a high degree of
sen sitivity. Insuch cases itmay be nec essary
to use other mea sures to furtherre duce
interference.
This cutting equipment is designed for use
onlyin an in dus tri al environment.
Installation and use
The user is responsible for installing and
usingtheplasma equipment according to the
manufacturer’s instructions. If elec tromagnet ic
disturbances are de tect ed then it shall be
the respon si bil i ty of the user to re solve the
situation withthe technical as sis tance of the
man u fac tur er. Insome cases this remedial
action may be as sim ple as earthing the
cuttingcircuit, see Earthingof Workpiece.
Inother cas es it could involve constructing an
electromag net ic screen enclosing the pow er
source and the work complete with associated
input filters. In all cases elec tro mag net ic
disturbanc es must be reduced to the point
where they are no longer trou ble some.
Assessment of area
Before installing the equipment the user
shall make an assessment of po ten tial
electromagnet ic problems in the sur round ing
area. The following shall be taken into account:
a. Other supply cables, control cables,
signalling and telephone ca bles; above,
below and adjacent to the cutting equipment.
b. Radio and television transmitters and
receivers.
c. Computer and other control equip ment.
d. Safety critical equipment, for example
guarding of industrial equipment.
e. Health of the people around, for example the
use of pacemakers and hear ing aids.
f. Equipment used for calibration or
measurement.
g. Immunity of other equipment in the
environment. User shall ensure that other
equipment being used in the environment
is com pat i ble. This may require ad di tion al
protection measures.
h. Time of day that cutting or other ac tiv i ties
are to be carried out.
The size of the sur round ing area to be
considered will depend on the structure of
the building and other activities that are taking
place. The surrounding area may ex tend
beyond the bound aries of the pre mises.
Methods of reducing
emissions
Mains supply
Cutting equipment must be con nect ed to the
mains supply according to the man u fac tur er’s
recom men da tions. If in ter fer ence occurs, it may
ELECTROMAGNETIC COMPATIBILITY EMC

ELECTROMAGNETIC COMPATIBILITY EMC
9/10
EMC-2 Compliance Information
be necessary to take addi tional precautions
such as fil ter ing of the mains supply.
Consideration should be given to shield ing the
supply cable of per ma nent ly installed cutting
equip ment, in metallic conduit or equiv a lent.
Shielding should beelec tri cal ly continuous
through out its length. The shielding should
becon nect ed to the cutting mains supply
so that good electrical contact is maintained
between the conduit and the cutting pow er
source enclosure.
Maintenance of cutting equipment
The cutting equipment must be rou tine ly
maintained according to the man u fac tur er’s
recom men da tions. All ac cess and service doors
and covers should be closed and properly
fastened when the cutting equip ment is in
operation. The cutting equipment should not be
modified in any way except as set forth in and
in accordance with the manufacturer’s written
instructions. For example, the spark gaps of
arc striking and sta bi liz ing devices should be
adjusted and maintained according to the
manu fac tur er’s recommendations.
Cutting cables
The cutting cables should be kept as short
aspossible and should be po si tioned close
together, running at or close to the floor level.
Equipotential bonding
Bonding of all metallic components in the
cutting installation and adjacent to it should
be considered. However, metallic com po nents
bonded to the workpiece will increase the risk
that the op er a tor could receive a shock by
touch ing these metallic compo nents and the
electrode (nozzle for laser heads) at the same
time. The op er a tor should be in su lat ed from all
such bonded metallic components.
Earthing of workpiece
Where the workpiece is not bonded to earth
for electrical safety, nor connected to earth
because of its size and position, for ex-
ample, ship’s hull or building steel work, a
con nec tion bonding the work piece to earth
may reduce emis sions in some, but not all
instances. Careshould be takento prevent the
earthing ofthe work piece increasing the risk
of injury to users, or damage to other elec tri cal
equipment. Where necessary, the con nec tion
of the workpiece to earth should be made by
a direct connection to the work piece, but in
some countries where direct connection is not
permitted, the bonding should be achieved by
suit able capacitances se lect ed according to
national regulations.
Note: the cutting circuit may or may not
be earthed for safety reasons. Changing
the earthing arrangements should only be
authorized by a person who is com pe tent to
assess whether the chang es will in crease the
risk of injury, for example, by al low ing parallel
cutting cur rent return paths which may damage
the earth cir cuits of other equipment. Further
guid ance is provided in IEC 60974-9, Arc
Welding Equip ment, Part 9: Installation and
Use.
Screening and shielding
Selective screening and shielding of other
cables and equipment in the surrounding
area may alleviate problems of in ter ference.
Screening of the entire plas ma cutting
installation may be con sid ered for special
applications.

9/10
Compliance Information W-1
Attention
Genuine Hypertherm parts are the factory-
recommended replacement parts for your
Hypertherm system. Any damage or injury
caused by the use of other than genuine
Hypertherm parts may not be covered by the
Hypertherm warranty, and will constitute misuse
of the Hypertherm Product.
You are solely responsible for the safe use of
the Product. Hypertherm does not and cannot
make any guarantee or warranty regarding the
safe use of the product in your environment.
General
Hypertherm, Inc. warrants that its Products
shall be free from defects in materials and
workmanship for the specific periods of time
set forth herein and as follows: if Hypertherm
is notified of a defect (i) with respect to the
power supply within a period of two (2) years
from the date of its delivery to you, with the
exception of Powermax brand power supplies,
which shall be within a period of three (3) years
from the date of delivery to you, and (ii) with
respect to the torch and leads within a period
of one (1) year from its date of delivery to you,
and with respect to torch lifter assemblies
within a period of one (1) year from its date of
delivery to you, and with respect to laser heads
within a period of one (1) year from its date of
delivery to you, and with respect to Automation
products one (1) year from its date of delivery
to you, with the exception of the EDGE Pro
CNC and ArcGlide THC, which shall be within
a period of two (2) years from the date of
delivery to you.
This warranty shall not apply to any Powermax
brand power supplies that have been used with
phase converters. In addition, Hypertherm does
not warranty systems that have been damaged
as a result of poor power quality, whether from
phase converters or incoming line power. This
warranty shall not apply to any Product which
has been incorrectly installed, modified, or
otherwise damaged.
Hypertherm provides repair, replacement or
adjustment of the Product as the sole and
exclusive remedy, if and only if the warranty
set forth herein properly is invoked and
applies. Hypertherm, at its sole option, shall
repair, replace, or adjust, free of charge, any
defective Products covered by this warranty
which shall be returned with Hypertherm’s prior
authorization (which shall not be unreasonably
withheld), properly packed, to Hypertherm’s
place of business in Hanover, New Hampshire,
or to an authorized Hypertherm repair facility,
all costs, insurance and freight pre paid by
the customer. Hypertherm shall not be liable
for any repairs, replacement, or adjustments
of Products covered by this warranty, except
those made pursuant to this paragraph and
with Hypertherm’s prior written consent.
The warranty set forth above is exclusive and is
in lieu of all other warranties, express, implied,
statutory, or otherwise with respect to the
Products or as to the results which may be
obtained therefrom, and all implied warranties
or conditions of quality or of merchantability
or fitness for a particular purpose or against
infringement. The foregoing shall constitute the
sole and exclusive remedy for any breach by
Hypertherm of its warranty.
WARRANTY

WARRANTY
9/10
W-2 Compliance Information
WARRANTY
Distributors/OEMs may offer different or
additional warranties, but Distributors/OEMs
are not authorized to give any additional
warranty protection to you or make any
representation to you purporting to be binding
upon Hypertherm.
Distributors/OEMs may offer different or
additional warranties, but Distributors/OEMs
are not authorized to give any additional
warranty protection to you or make any
representation to you purporting to be binding
upon Hypertherm.
Patent indemnity
Except only in cases of products not
manufactured by Hypertherm or manufactured
by a person other than Hypertherm not in strict
conformity with Hypertherm’s specifications
and in cases of designs, processes, formulae,
or combinations not developed or purported
to be developed by Hypertherm, Hypertherm
will have the right to defend or settle, at
its own expense, any suit or proceeding
brought against you alleging that the use
of the Hypertherm product, alone and not
in combination with any other product not
supplied by Hypertherm, infringes any patent
of any third party. You shall notify Hypertherm
promptly upon learning of any action or
threatened action in connection with any
such alleged infringement (and in any event
no longer than fourteen (14) days after
learning of any action or threat of action), and
Hypertherm’s obligation to defend shall be
conditioned upon Hypertherm’s sole control
of, and the indemnified party’s cooperation and
assistance in, the defense of the claim.
Limitation of liability
In no event shall Hypertherm be liable to
any person or entity for any incidental,
consequential direct, indirect, punitive
or exemplary damages (including but
not limited to lost profits) regardless of
whether such liability is based on breach
of contract, tort, strict liability, breach of
warranty, failure of essential purpose,
or otherwise, and even if advised of the
possibility of such damages.
National and local codes
National and local codes governing plumbing
and electrical installation shall take precedence
over any instructions contained in this manual.
In no event shall Hypertherm be liable for injury
to persons or property damage by reason of
any code violation or poor work practices.
Liability cap
In no event shall Hypertherm’s liability,
if any, whether such liability is based on
breach of contract, tort, strict liability,
breach of warranties, failure of essential
purpose or otherwise, for any claim,
action, suit or proceeding (whether in
court, arbitration, regulatory proceeding
or otherwise) arising out of or relating
to the use of the Products exceed in
the aggregate the amount paid for the
Products that gave rise to such claim.
Insurance
At all times you will have and maintain
insurance in such quantities and types, and
with coverage sufficient and appropriate to
defend and to hold Hypertherm harmless in the
event of any cause of action arising from the
use of the products.

WARRANTY
9/10
Compliance Information W-3
Transfer of rights
You may transfer any remaining rights you may
have hereunder only in connection with the
sale of all or substantially all of your assets or
capital stock to a successor in interest who
agrees to be bound by all of the terms and
conditions of this Warranty. Within thirty (30)
days before any such transfer occurs, you
agree to notify in writing Hypertherm, which
reserves the right of approval. Should you
fail timely to notify Hypertherm and seek its
approval as set forth herein, the Warranty set
forth herein shall be null and void and you will
have no further recourse against Hypertherm
under the Warranty or otherwise.

WARRANTY
9/10
W-4 Compliance Information

TABLE OF CONTENTS
Duramax Retrofit Torch Operator Manual xi
Electromagnetic compatibility .................................................................................................................. EMC-1
Warranty............................................................................................................................................................. W-1
Section 1
Specifications
Component weights .......................................................................................................................................... 1-2
Duramax HRT hand torch dimensions .......................................................................................................... 1-2
Duramax HRTs hand torch dimensions ........................................................................................................ 1-2
Duramax MRT full-length machine torch dimensions ................................................................................ 1-3
Duramax MRT without positioning sleeve (mini torch) .............................................................................. 1-3
Section 2
Torch Setup
Introduction ......................................................................................................................................................... 2-2
Consumable life .................................................................................................................................................. 2-2
Hand torch setup ............................................................................................................................................... 2-3
Choose the hand torch consumables ................................................................................................ 2-3
Hand torch consumables ...................................................................................................................... 2-4
Install the hand torch consumables ..................................................................................................... 2-5
Machine torch setup.......................................................................................................................................... 2-6
Converting a Duramax retrofit machine torch into a mini torch .................................................... 2-7
Mount the torch ........................................................................................................................................ 2-9
Choose the machine torch consumables ........................................................................................2-12
Machine torch consumables ...............................................................................................................2-12
Install the machine torch consumables ............................................................................................2-15
Aligning the torch ..................................................................................................................................2-15
Torch installation ..............................................................................................................................................2-16
Section 3
Operation
Using the cut charts .......................................................................................................................................... 3-3
Estimated kerf-width compensation .................................................................................................... 3-3
100 amp mechanized shielded cutting for Powermax1650.......................................................... 3-6
85 amp mechanized shielded cutting for Powermax1650 ............................................................ 3-8
80 amp mechanized shielded cutting for Powermax1250/1650 ..............................................3-12
65 amp mechanized shielded cutting for Powermax1250/1650 ..............................................3-14
60 amp mechanized shielded cutting for Powermax1000/1250/1650 ...................................3-18

TABLE OF CONTENTS
xii Duramax Retrofit Torch Operator Manual
45 amp mechanized shielded cutting for Powermax1000/1250/1650 ...................................3-20
100 amp mechanized unshielded cutting for Powermax1650 ...................................................3-24
85 amp mechanized unshielded cutting for Powermax1650......................................................3-26
65 amp mechanized unshielded cutting for Powermax1250/1650 ..........................................3-30
45 amp mechanized unshielded cutting for Powermax1000/1250/1650 ..............................3-34
FineCut® consumables for Powermax1000/1250/1650 ............................................................3-38
Using the hand torch .......................................................................................................................................3-41
Operate the safety trigger ...................................................................................................................3-41
Hand torch cutting hints ......................................................................................................................3-42
Start a cut from the edge of the workpiece.....................................................................................3-43
Pierce a workpiece ................................................................................................................................3-44
Gouge a workpiece ..............................................................................................................................3-45
Common hand-cutting faults ..............................................................................................................3-48
Using the machine torch ................................................................................................................................3-49
Ensure the torch and table are set up correctly .............................................................................3-49
Understand and optimize cut quality .................................................................................................3-49
To pierce a workpiece using the machine torch ............................................................................3-52
Common machine-cutting faults ........................................................................................................3-52
Section 4
Maintenance and parts
Perform routine maintenance .......................................................................................................................... 4-2
Inspect the consumables ................................................................................................................................. 4-3
Hand torch replacement parts ........................................................................................................................ 4-4
Machine torch replacement parts .................................................................................................................. 4-6
Accessory parts.................................................................................................................................................. 4-7

Duramax Retrofit Torch Operator Manual 1-1
Section 1
SPECIFICATIONS
In this section:
Component weights .......................................................................................................................................... 1-2
Duramax HRT hand torch dimensions .......................................................................................................... 1-2
Duramax HRTs hand torch dimensions ........................................................................................................ 1-2
Duramax MRT full-length machine torch dimensions ................................................................................ 1-3
Duramax MRT without positioning sleeve (mini torch) .............................................................................. 1-3

SPECIFICATIONS
1-2 Duramax Retrofit Torch Operator Manual
Duramax HRT hand torch dimensions
Duramax HRTs hand torch dimensions
9.9 in (25.2 cm)
3.8 in
(9.8 cm)
75°
angle 2.6 in
(6.6 cm)
1.0 in
(2.5 cm)
Component weights
Torch type Weight – lbs (kg)
Hand torch 25 ft (7.6 m) 7.1 (3.2)
Hand torch 50 ft (15 m) 12.5 (5.7)
Machine torch 25 ft (7.6 m) 7.6 (3.4)
Machine torch 50 ft (15 m) 13.2 (6.0)
10.2 in (25.9 cm)
1.9 in
(4.7 cm)
15°
angle 2.6 in
(6.6 cm)
1.0 in
(2.5 cm)

SPECIFICATIONS
Duramax Retrofit Torch Operator Manual 1-3
Duramax MRT full-length machine torch dimensions
15.6 in
(39.6 cm)
1.0 in
(2.5 cm)
1.4 in (3.6 cm) outer
dimension, 1.3 in
(3.3cm) flat sides
12.3 in
(31.3 cm)
8.1 in
(20.6 cm)
1.4 in
(3.5 cm)
1.0 in
(2.5 cm)
1.4 in (3.6 cm) outer
dimension, 1.3 in
(3.3cm) flat sides
1.4 in
(3.5 cm)
Duramax MRT without positioning sleeve (mini torch)
6.6 in
(16.8 cm)
3.3 in
(8.4 cm)

SPECIFICATIONS
1-4 Duramax Retrofit Torch Operator Manual

Duramax Retrofit Torch Operator Manual 2-1
Section 2
TORCH SETUP
In this section:
Introduction ......................................................................................................................................................... 2-2
Consumable life .................................................................................................................................................. 2-2
Hand torch setup ............................................................................................................................................... 2-3
Choose the hand torch consumables ................................................................................................ 2-3
Hand torch consumables ...................................................................................................................... 2-4
Install the hand torch consumables ..................................................................................................... 2-5
Machine torch setup.......................................................................................................................................... 2-6
Converting a Duramax retrofit machine torch into a mini torch .................................................... 2-7
Mount the torch ........................................................................................................................................ 2-9
Choose the machine torch consumables ........................................................................................2-12
Machine torch consumables ...............................................................................................................2-12
Install the machine torch consumables ............................................................................................2-15
Aligning the torch ..................................................................................................................................2-15
Torch installation ..............................................................................................................................................2-16

TORCH SETUP
2-2 Duramax Retrofit Torch Operator Manual
Introduction
Duramax™ series handheld and machine retrofit torches are available for the Powermax1000,
Powermax1250, and Powermax1650 systems. The ETR (Easy Torch Removal)™ quick-disconnect
system makes it easy to remove the torch for transport or to switch from one torch to the other if
your applications require the use of different torches. The torches are cooled by ambient air and do
not require special cooling procedures.
This section explains how to setup your torch and choose the appropriate consumables for the job.
Consumable life
How often you need to change the consumables on your retrofit torch will depend on a number of
factors:
• Thickness of the material – the thicker the material being cut, the more often consumables
need to be changed.
• Average length of cut – the longer the average cut, the more often consumables need to
be changed.
• Type of cutting – handheld cutting will require more consumable changes than machine
cutting.
• Air quality – the presence of oil, moisture, or other contaminants will reduce consumable
life.
• Piercing / edge starting – piercing the metal causes more consumable wear then starting
cuts from the edge of the metal.
• Proper torch-to-work distance – when gouging or cutting with unshielded consumables,
maintaining proper torch-to-work distance will result in better consumable life.
• Proper pierce height – maintaining proper pierce height will result in better consumable
life.
• Cutting in “continuous pilot arc” mode or normal cutting mode – cutting with a continuous
pilot arc causes more consumable wear than cutting in normal cutting mode.
You will find more information about proper cutting techniques in Section 3, Operation.

TORCH SETUP
Duramax Retrofit Torch Operator Manual 2-3
Choose the hand torch consumables
Duramax retrofit torches are shipped with a full set of cutting consumables pre-installed.
Hypertherm also includes spare cutting electrodes, nozzles, and gouging consumables in the
consumables box, for handheld torches.
Consumables for handheld cutting are shown on the next page. Notice that the retaining cap and
electrode are the same for cutting, gouging, and FineCut® applications. Only the shield, nozzle,
and swirl ring are different.
For the best cut quality on thin materials, you may prefer to use FineCut consumables, or use a
45A nozzle and reduce the current setting to 45 amps.
Consumables
Consumables
Safety trigger
Safety trigger
Hand torch setup
Duramax HRT
Duramax HRTs

TORCH SETUP
2-4 Duramax Retrofit Torch Operator Manual
6
5
A
4
5
A
8
5
A
1
0
0
A
Hand torch consumables
Drag-cutting consumables: Powermax1000/1250/1650
Gouging consumables: Powermax1000/1250/1650
FineCut® consumables: Powermax1000/1250/1650
220854
Retaining cap
220947
Swirl ring
220842
Electrode
220931
Shield
220930
Nozzle
Powermax1000 – Use 45-65 A consumables
Powermax1250 – Use 45-85 A consumables
Powermax1650 – Use 45-100 A consumables
220857
Swirl ring
220994
Swirl ring
220842
Electrode
220941
Nozzle
220819
Nozzle
220816
Nozzle
220990
Nozzle
220854
Retaining cap
220818
Shield
220992
Shield
1
0
0
A
6
5
A
8
5
A
220857
Swirl ring
220994
Swirl ring
220842
Electrode
220797
Nozzle
220991
Nozzle
220854
Retaining cap
220798
Shield
This manual suits for next models
2
Table of contents
Other Hypertherm Flashlight manuals
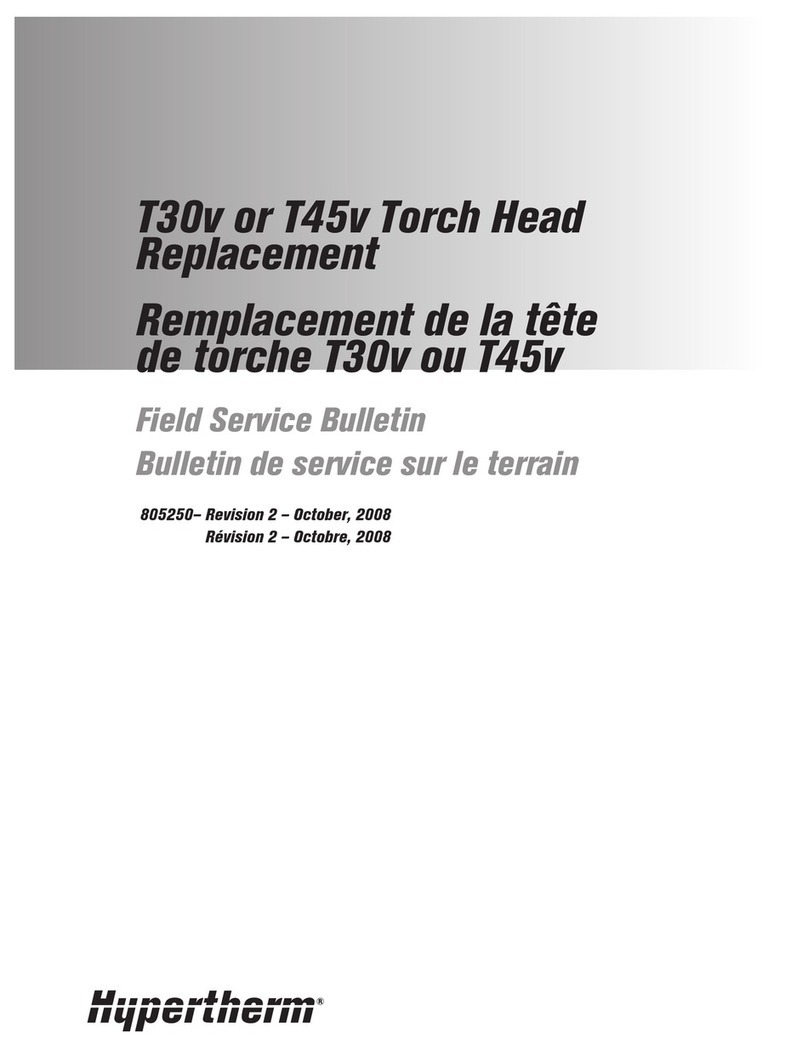
Hypertherm
Hypertherm T30v Use and care manual
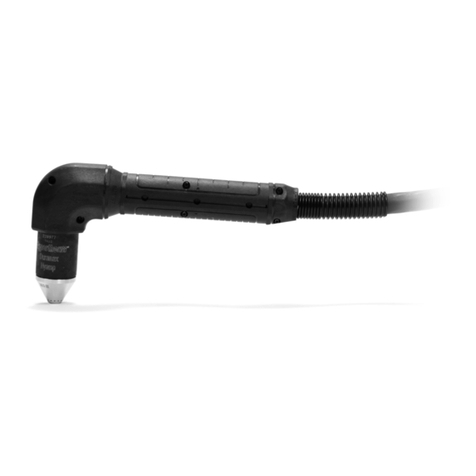
Hypertherm
Hypertherm Duramax User manual

Hypertherm
Hypertherm T30v Reference manual
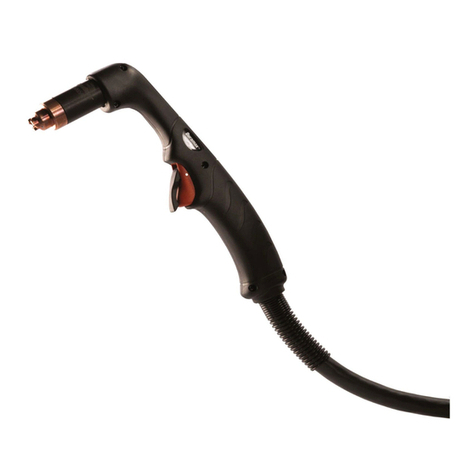
Hypertherm
Hypertherm Duramax 75 Degrees Reference manual

Hypertherm
Hypertherm powermax65 User manual
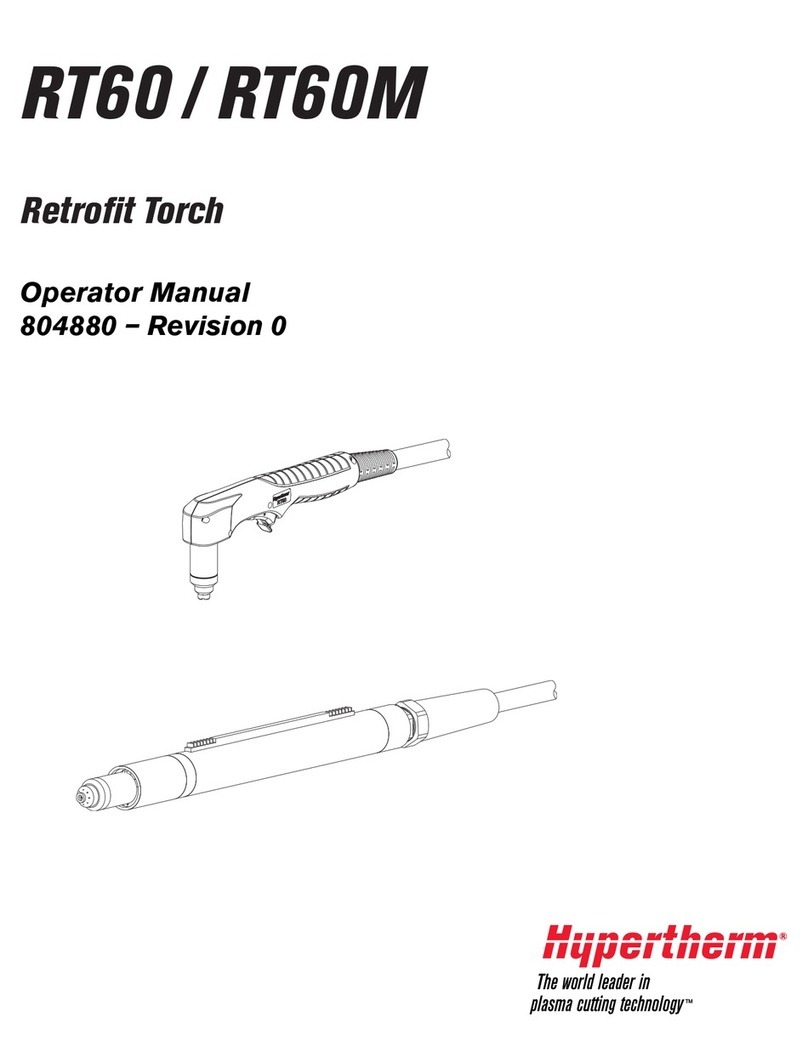
Hypertherm
Hypertherm RT60 User manual
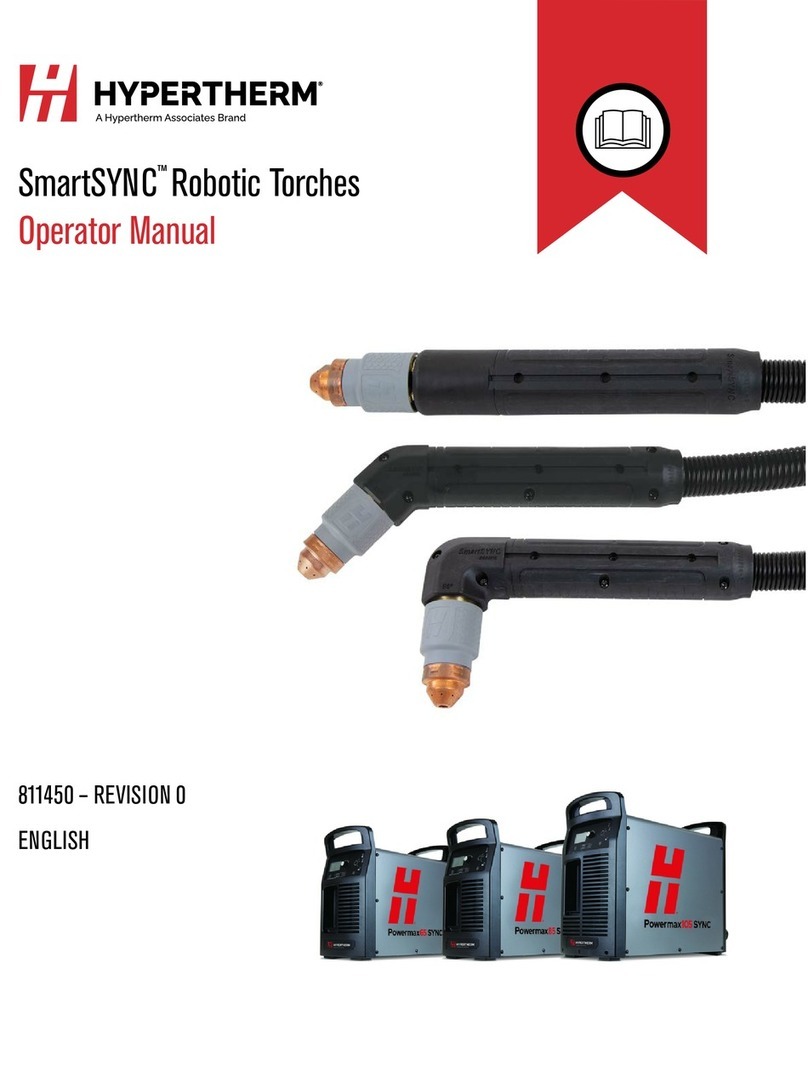
Hypertherm
Hypertherm SmartSYNC Robotic Torch User manual
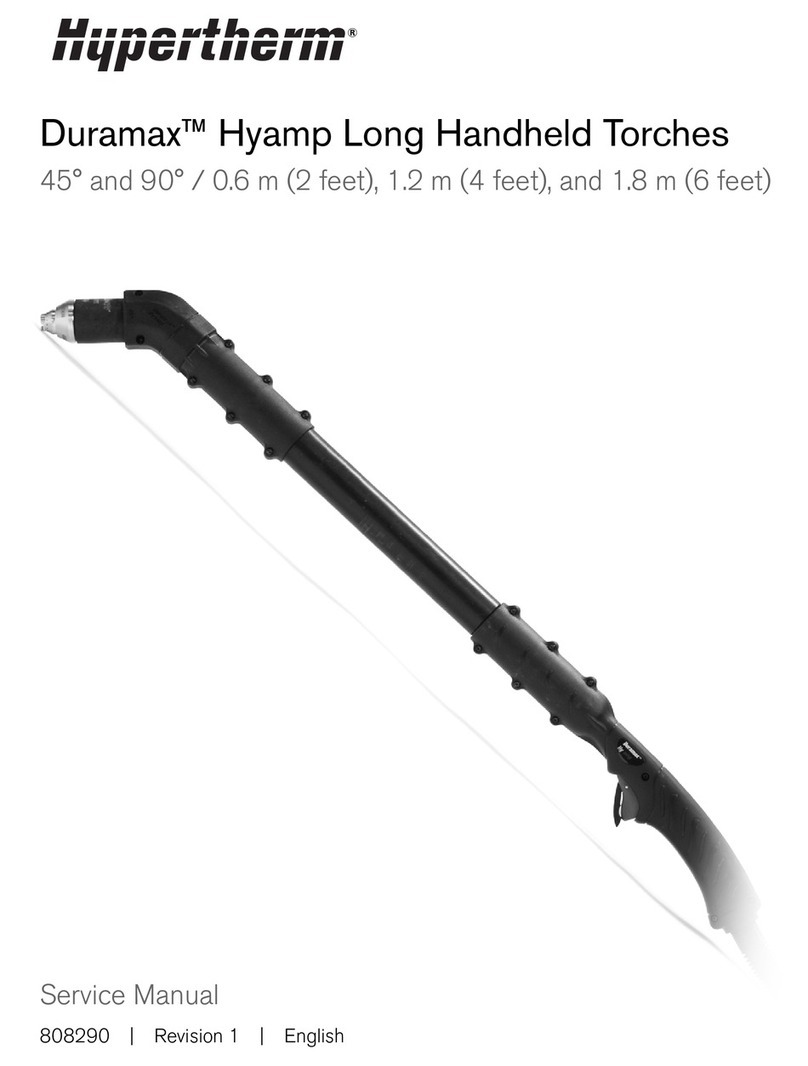
Hypertherm
Hypertherm Duramax Hyamp Series User manual
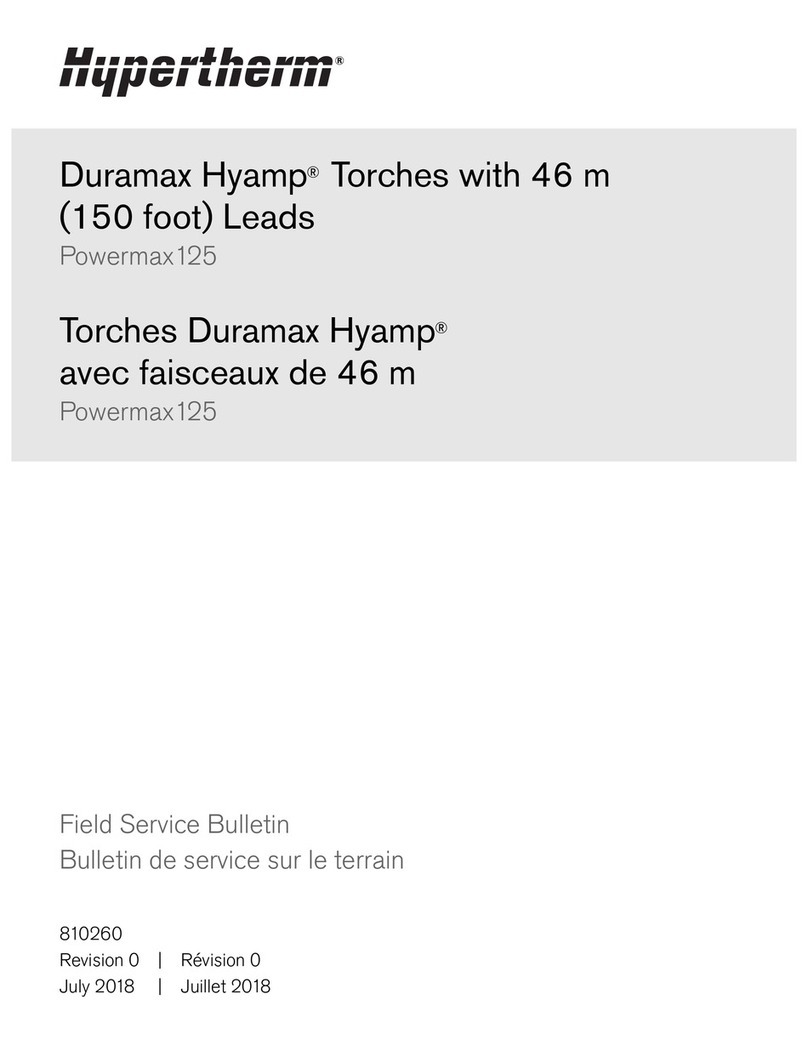
Hypertherm
Hypertherm 059664 Reference manual
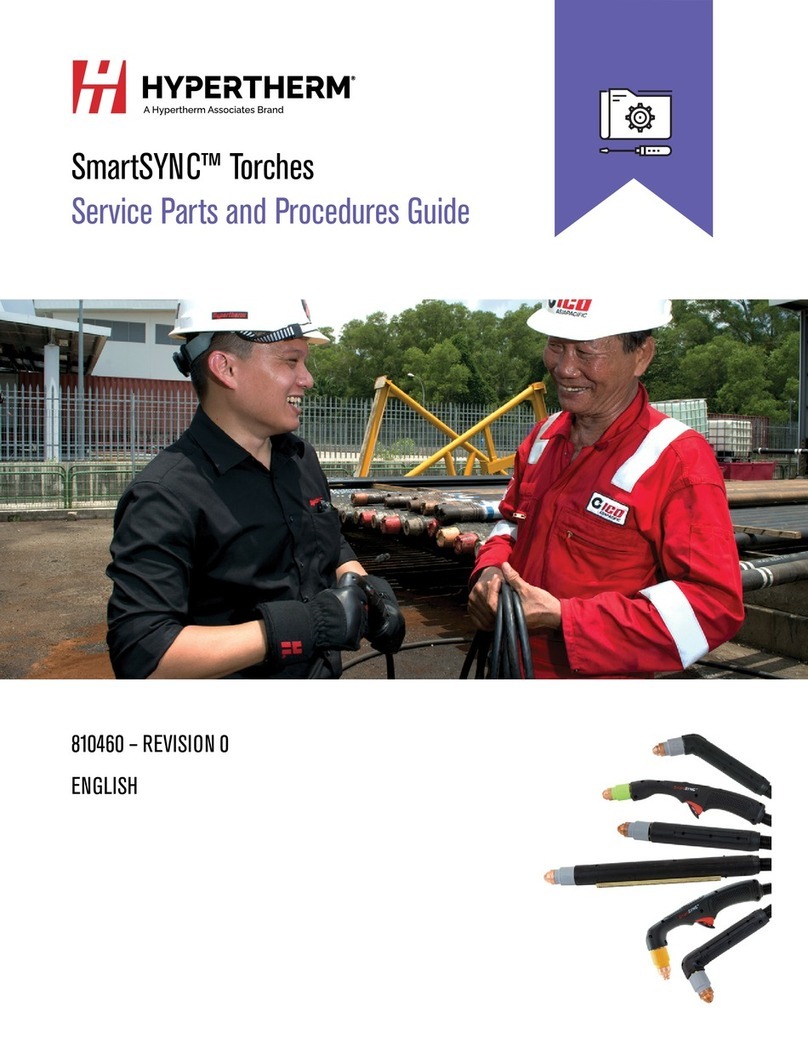
Hypertherm
Hypertherm SmartSYNC 059719 Manual