iAIRE ultraDRY User manual

O/M manual
PD 02/22/2020 - v 5.71
ultraDRY
outside air solutions

iAIRE, LLC iAIRE OM manual
2
Table of Contents
PART NUMBER AND DESCRIPTIONS............................................................................................. 3-4
START UP REQUIREMENTS............................................................................................................... 5
START UP PROCEDURE.................................................................................................................. 6-9
SEQUENCE OF OPERATIONS..................................................................................................... 10-11
WIRING AND ELECTRICAL................................................................................................................11
CONTROLLER NAVIGATION ....................................................................................................... 12-21
WIRING DIAGRAMS...................................................................................................................... 22-49
PLUMBING/PIPING DIAGRAM..................................................................................................... 50-51
OPTIONS WIRING DIAGRAMS .................................................................................................... 52-74
REFRIGERANT PIPING GUIDELINES .............................................................................................. 76
TROUBLESHOOTING........................................................................................................................ 77
APPENDIX A (CAPACITY CONTROL DEVICE) ........................................................................... 78-83
APPENDIX B (VFD)..................................................................................................................... 84-128
APPENDIX C (LOW-AMBIENT CONTROL) ............................................................................. 129-130
APPENDIX D (SPACE SENSOR).............................................................................................. 131-137
APPENDIX E (SPLIT SYSTEM PIPING REQUIREMENTS) ..................................................... 138-155
APPENDIX F (SPLIT SYSTEM DAT SENSOR INSTALLATION) ............................................. 156-157
APPENDIX G (MODULATING GAS VALVE)............................................................................. 158-164
APPENDIX H (SMOKE SENSOR)............................................................................................. 165-171
APPENDIX J (24/7 TIMER)........................................................................................................ 172-182
APPENDIX K (HIGH HEAT BOX).............................................................................................. 183-214
APPENDIX L (UPC BACNET INSTALLATION) ........................................................................ 215-235
APPENDIX M (BACNET TROUBLESHOOTING) ..................................................................... 236-237
Contact iAIRE At:
www.myiaire.com
Email: [email protected]
Phone: 844-348-9168

iAIRE OM manualiAIRE, LLC
3
ultraDRY PART NUMBERING SCHEME
08/30/2019v2.02
COOLING
AZ07RA07*
AZ08RA08*
AZ12RA12*
AZ14RA14*
AZ16RA16*
AZ25RA25*
AD12RA12**
AD14RA14**
AD16RA16**
AD25RA25**
HEAT PUMP
AQ07RQ07*
AQ08RQ08*
AQ12RQ12*
AQ16RQ16**
AQ25RQ25**
L - LOW/STD STATIC
M - MED STATIC
H - HIGH STATIC
G - 230VAC 1Φ
H - 230VAC 3Φ
K - 460VAC 3Φ
L - 575VAC 3Φ
0 - NO CONTROLS
A - DAT w/ VAV DUCT
B - DAT w/ VAV BLDG
C - UD3 w/ VAV DUCT
D - DAT CONTROL
E - SPACE w/ VAV DUCT
F - SPACE w/ VAV BLDG
G - ultraGROW CTRL
H - UD3 w/ VAV BDLG
S - SPACE CTRL
3 - ultraDRY 3 TEMP CTL
TC07
TC08
TC09
TC12
TC14
TC16
TC17
TC20
TC24
TC28
TC30
A30
A35
A40
A50
A60
GC04
GC05
GC06
HC04
HC05
HC06
HC07
HC08
HC09
HC11
HC12
HC14
HC17
HC20
HC24
HC28
12C - 3 4 5 6 7 8 9 10 11 12 13 - 14
configuration (13)
DOWN SUPPLY
DOWN RETURN
HORIZONTAL SUPPLY
DOWN RETURN
DOWN SUPPLY
HORIZONTAL RETURN
HORIZONTAL SUPPLY
HORIZONTAL RETURN
WTR SRC CONFIG ONLY
TOP DISCHARGE
REAR RETURN
TOP DISCHARGE
FRONT RETURN
FRONT DISCHARGE
REAR RETURN
REAR DISCHARGE
FRONT RETURN
RIGHT DISCHARGE
LEFT RETURN
BACK DISCHARGE
LEFT RETURN
LEFT DISCHARGE
RIGHT RETURN
A -
B -
C -
D -
E -
F -
G -
H -
I -
J -
K -
disconnect (11,12)
00 - NO DISCONNECT
(if requested, size will be
determined by factory)
heat stages
(10)
A - NO CONTROLS
B - 1 STAGE
C - 2 STAGE
D - 3 STAGE
E - 4 STAGE
M - MODULATING
electric &
gas heat (7,8,9)
XXX - ELECTRIC (kW)
XXX - GAS (mBH)
options (14)
0 - NO OPTIONS
A - IONIZATION
B - WHOLE UNIT (UG)
C - ALL COILS (UG)
D - CONDENSER COIL (UG)
E - ERV
F - MERV 13 4” FILTER
G - 2 POS. OA DAMPER
H - BACNET
J - HINGED ACCESS DOORS
K - DW W/ POLY INSUL.
L - SS DRIP PAN
M - SS GAS HEAT EXCHANGER
N - DIRTY FILTER SWITCH
P - SERV. OUTLET (NON PWR)
Q - SERV. OUTLET (PWR)
R - SPLIT PWR FUSE DISC.
S - SPLIT PWR SWT DISC.
T - SMOKE SA
U - SMOKE RA
V - LOW AMBIENT BYPASS
W - MANUAL OA DAMPER
X - INTERTWINED EVAP. COIL
Y - START UP
1 - 365 DAY ANNUAL TIMER
2 - DUEL FUEL UNIT
3 - CONDEN. FLOW SWITCH
4 - AIRFLOW MONITORING
5 - HAIL GUARD
6 - REMOTE READOUT
7 - PHASE MONITOR
8 - POWERED EXHAUST
type (1,2)
fan (4)
voltage (5)
control (6)
Rooftop Units (3) Comm. Split (3) Res. Split (3)
01 - 240V - 30A FUSE
02 - 240V - 60A FUSE
03 - 240V - 100A FUSE
04 - 240V - 150A FUSE
05 - 240V - 200A FUSE
06 - 240V - 300A FUSE
11 - 240V - 30A SWITCH
12 - 240V - 60A SWITCH
13 - 240V - 100A SWITCH
14 - 240V - 150A SWITCH
15 - 240V - 200A SWITCH
16 - 240V - 300A SWITCH
21 - 600V - 30A FUSE
22 - 600V - 60A FUSE
23 - 600V - 100A FUSE
24 - 600V - 150A FUSE
31 - 600V - 30A SWITCH
32 - 600V - 60A SWITCH
33 - 600V - 100A SWITCH
34 - 600V - 150A SWITCH
COOLING
AC36FV3
AC42FV6
AC48FV6
AC60FV6
HEAT PUMP
HC36FV3
HC42FV6
HC48FV6
HC60FV6
* one circuit
**two circuit
* one circuit
**two circuit
VQP72
VQP96
VQP120
VQP151
VQP181
VQP210
VQP240
VQP300
VQP360
HQP72
HQP96
HQP120
HQP150
HQP180
HQP242
UD - COOLING ONLY
UG - WITH GAS HEAT
UH - DX Cooling w/ H.W. Coils
UP - WITH HEAT PUMP
UW - WSHP
P70
P100
N150
N75
N90
N105
N120
N130
FC05
FC04
FC06
FC07
AP27RA30**
AP25RA30**
P90
P75
P60
P55
P50
P40
P35
P30
AB36FV3
AB42FV6
AB48FV6
AB60FV6
AP30RA30**
TC18
TC21
TC25
TC29

iAIRE, LLC iAIRE OM manual
4
How to Translate ultraDRY Part Numbering Schemes
ultraDRY’s part numbering scheme is composed of similar product identication, when compared to Carrier, in order to
easily provide common options and features. Using the comparison below, an excerpt is provided from Carrier’s technical
guide to illustrate how a common unit can be traced from ultraDRY to Carrier.
For more information about Carrier Residential Units go to: For more information about Carrier Commercial Units go to:
http://www.carrier.com/homecomfort/en/us/products/ http://www.commercial.carrier.com/commercial/hvac/
heating-and-cooling/packaged-product/ homepage/1,3052,CLI1_DIV12_ETI372,00.html
To determine the specic Carrier unit you need, see below for how to determine which Carrier manual you will need.
iAIRE Model # UDC-TC04-LH*
Carrier Model #
ADDITIONAL OPTIONSPACKAGE UNIT
COOLING ONLY LOW STATIC FAN

iAIRE OM manualiAIRE, LLC
5
START-UP REQUIREMENTS
! IMPORTANT !
To maintain factory warranty, all units
must have an authorized factory start-up
and the start-up paperwork on le.
For Questions, Contact iAIRE At:
www.myiaire.com
Email: [email protected]
Phone: 844-348-9168

iAIRE, LLC iAIRE OM manual
6
© 2019 iAIRE, LLC
www.myiaire.com
Page 1
Factory Start-up Request
HVAC Contractor: _________________________________________________________________
Date: __________________ Requested Start-up Date: ______________________
Project: ___________________________ Qualified Technician: __________________________
iAIRE Model #: ___________________________________________________________________
iAIRE Serial #: ____________________________________________________________________
Project Address: __________________________________________________________________
________________________________________________________________________________
Site Customer Contact: _________________________
Phone: _________________
Email: ________________________
Note: The above start-up date needs to be scheduled with our office immediately. Allow three
weeks lead time to schedule start-up. The items on both pages must be completed, signed-off &
faxed/emailed to our office prior to the start-up date. Please fill out completely.
Proper equipment start-up is critical to customer comfort and equipment longevity. Utilize the
following form to ensure that all the PRE-start-up procedures have been completed. The
technician should initial each step as it has been completed and fill out the required start-up
values. This form will provide the technician confidence that the system was thoroughly evaluated
and installed properly. A separate checklist must be prepared and signed for all units to be started
on the same date. Additional P.O. amount may be necessary for separate start-up dates. Please
contact your Sales Engineer.
Note: The installing contractor’s start-up technician must be present when iAIRE’s start-up
technician arrives on site for proper coordination and instructions on proper unit operation. The
installing contractor is responsible for properly operating the unit after iAIRE’s start-up technician
leaves the job site.
Startup services require the installer to complete the manufacturers’ PRE-start-up checklist on the
next page prior to requesting startup.
Aer completeing this checklist, please scan and email back to iAIRE.
sales@myiaire.com
PD 3/30/19 - v 1.61
ultraDR
Y
outside air solutions

iAIRE OM manualiAIRE, LLC
7
© 2019 iAIRE, LLC
www.myiaire.com
Page 2
Factory Pre-Startup Request
Item General Inspecon Completed
Inspect unit for shipping and/or rigging damage.
Is unit installed with proper clearances?
Is unit installed within slope limitaons?
Check terminal screws and wiring connecons for ghtness.
Are lters installed correctly and clean?
Check Outdoor Air dampers if installed are in operang posion.
(When G terminal is shorted to R, 24V)
Have Refrigeraon circuits been checked for leaks?
Is condensate drain trapped properly?
Is all eld wiring (power and control) complete and sized accurately?
Is unit power correct voltage?
Mated ERV’s that ship seperatly have power & comm wires connected to RTU?
Is space thermostat run with twisted shielded wire?
Are split systems completely wired? (Is twisted, shielded cable used?)
If G/E, is building natural gas available and piped to the unit?
Is there refrigerant in the unit / line set?
Item Air Moving Inspecon Completed
Check alignment of drive components.
Check Supply Air fan belt tension.
Check blower pulley’s and wheel’s ght on sha.
Check fan operates with proper rotaon/direcon.
Check VFD set for proper supply air CFM. (keypad display) cfm
VAV Duct or Building Pressure tube installed?
Notes:________________________________________________________________________
_____________________________________________________________________________
_____________________________________________________________________________
Installing Contractor Signature: _____________________________________
Printed Name: _____________________________ Date: _________
ultraDR
Y
outside air solutions
NOTE: If start up technician shows up and the above tasks are not complete, an additional charge will be incurred.

iAIRE, LLC iAIRE OM manual
8
CONTROLS DESCRIPTIONS
DAT CONTROL
Designed to temper the air supplied to other HVAC equipment
by supplying neutral air.
SPACE CONTROL
Designed to condition the air to provide cooling or heating to
the building space so only (1) piece of equipment is needed
to both treat outside air and maintain space temperatures.
ultraDRY 3 CONTROL
Uses a standard thermostat with a humidistat, a call for
cooling turns on Y1, a call for heating turns on W1, a call
for fan turns on fan. A humidity call (when there is no call for
cooling) will turn on Y1 and also engage the modulating hot
gas reheat valves.
GENERAL INSTRUCTIONS
An iAIRE’s operation is a function of the options and control
packages that the iAIRE unit is equipped with.
RECEIVING / INSPECTION
Check part # of iAIRE unit to ensure it is what was ordered.
Verify voltage/phases match.
At the time of delivery the iAIRE unit should be visually
inspected for possible damage. If any damage is found it
should be reported immediately to the last courier company,
preferably in writing. iAIRE recommends leaving the iAIRE
unit in its shipping packaging until the time of installation.
RIGGING
Utilize the Carrier factory information on rigging these units.
If you need help accessing this information, please contact
iAIRE customer service at:
SAFETY CONSIDERATIONS
Installation and servicing of the iAIRE units can be hazardous
due to system, pressure, electrical components and moving
parts. Only trained and qualied service personnel should
install, repair or service these units.
When working on iAIRE or other HVAC units observe
precautions in the literature, tags and labels attached to the
units, and any other safety precautions that may apply.
Follow all local, national and industry electrical codes when
installing these units and accessories.
START-UP
SPACE / DISCHARGE AIR TEMP CONTROL PACKAGE
START-UP
Physical Inspection (pre power-up)
Check part # of iAIRE unit to ensure it is what was ordered.
Verify voltage/phases match.
1. Verify condition of unit and note any installation or shipping
damage to coils or cabinets.
2. Verify installation of condensate drain trap.
3. Verify power is available at disconnect and fuses are
installed if required. Check incoming power to make sure it
is within tolerance.
4. Verify that all airways are open. (Fire dampers and supply
air registers.)
5. Check blower belt tension. (if available)
6. Conrm that the space sensor is installed. (Space
Control units only, see wiring in gure “B” on installatoin
wiring diagram pages. Space Sensors must be wired using
shielded wire.
After power-up
1. Check incoming 3-phase power for a stinger leg if voltage is
208/230VAC. If so ensure that stinger leg (high voltage phase to
ground) is the center leg.
2. Go to iAIRE controller and set both the heat and cool CFM. The
heat CFM is the VFD % in the heat mode that the AHU fan will run.
The cool CFM is the VFD % the AHU fan will run in all other modes.
3. Remove panel from outside air section and verify outside air damper
is fully open. Set adjustment thumbwheel on damper motor for full
opening. Check crank arms and balljoints on damper mechanism
allow damper to open fully.
Charging
1. Locate Rawal device in condenser section. Locate the Rawal
Device and close the ball valve. This will stop ow to the Rawal Device
2. Disconnect 2-pin signal plug from Sporlan IB circuit board. This will
close the modulating hot gas valve to allow correct charging.
3. Invert refrigerant jug to provide liquid charge into suction line and
proceed to charge unit for 10 degrees of subcooling and 20 degrees
superheat. Depending on ambient conditions, evaporator leaving air
temperature should be between 48-58 F.
4. When charge is complete return signal connector to Sporlan IB
board and re-open Rawal ball valve.

iAIRE OM manualiAIRE, LLC
9
h) Record sub cooling temperature _____ Record evap
saturation temperature ______
i) Open Rawal valve.
j) If Low Ambient is installed, open valve to low ambient
and close valve to bypass Low Ambient.
k) Record sub cooling temperature ______ Record evap
saturation temperature ______
l) Note: You can leave the TEST menu and enter the
STATUS menu to check system temperatures at any time.
TEST mode will remain active until it is manually disabled.
m) When charging and checks are complete, disable the
TEST mode and open the Rawal valve.
n) Allow system to stabilize and check sub cooling again.
o) Add/Remove refrigerant as necessary to maintain
about 4 degree of sub cooling.
p) Remove gauges and replace service port covers.
q) If charging for the rst time note all required conditions
in startup sheets and record weight of all refrigerant added.
Record Keeping
1. Record all readings and conditions in startup sheets and
add notes to call attention to any issues for the unit installing
contractor to attend to.
2. Have the startup documents signed by supervising
foreman for mechanical contractor.
MODULATING GAS SETUP:
1: SEE APPENDIX “G” (pg.157) for standard carrier heat
2: SEE APPENDIX “K” (pg. 182) for High Heat Box.
5. Disconnect jumper from terminal strip input to allow the iAIRE
controller to take over machine.
6. Adjust sensor setpoint to a low setpoint to bring all cooling stages
on and check if hot gas line warms up.
TEST PROCEDURE
Verify operation as described above by monitoring liquid line
temperature and observing motor speed.
Heater check
1. Verify Kw of installed electric heaters.
2. Disconnect white space temperature sensor wire from
terminal strip. (This will make the iAIRE controller see a
space temperature of -40 degrees and start heaters) There is
a ve minute delay at start of heat cycle. With heater running
check amperage and verify discharge air temperature.
3. Return white space temperature sensor wire to terminal
strip.
Checking and adjusting system refrigerant charge.
Before connecting gauges to the systems suction and
discharge service ports, make the following adjustments.
1. Before running blower and compressors, close the manual
ball valve on the discharge of the #1 compressor Rawal valve
to eliminate Hot Gas Bypass during the charging process.
2. If Low Ambient is installed, shut o ball valve to low
ambient and open bypass around low ambient to isolate L.A.
valve.
3. Before running blower and compressors, put iAIRE
controller in TEST mode and manually set Hot Gas Valve %
to 0.0% to direct all refrigerant to DX cooling.
a) Connect gauges. (Pre-load evacuated split systems
with nominal weight of refrigerant)
b) Enable FAN and then Cool Stage 1 in TEST mode and
allow several minutes for system to stabilize.
c) Note, high pressure saturation Temperature on
gauge and the temperature of the Liquid Line leaving the
condenser. (Condensing temperature should be 100-110
degrees minimum)
d) Calculate Sub cooling (Saturation Temp – Liquid line
Temp = Sub cooling)
e) Charge systems for 12-15 degrees of sub cooling. Add
refrigerant if sub cooling is low and remove if high. With all
cooling stages enabled system should deliver 55 degree air,
or less depending on ambient conditions.
f) Record sub cooling temperature __________ degrees
g) With controller still in TEST mode, increase the Hot
gas valve position in increments until discharge air, (DAT) is
raised to 70 - 72 degrees.

iAIRE, LLC iAIRE OM manual
10
SPACE
In the UNOCCUPIED mode, the outside air unit will be
o and the outside air damper, if supplied, will be closed.
Occupied or Unoccupied is signaled to the IAIRE controller
via a normally open or normally closed contact on the
OCCUPIED input with a clock or switch. An open contact
on the input indicates OCCUPIED, a closed contact
indicates UNOCCUPIED.
In the OCCUPIED mode, the outside air damper will
open and the supply fan will start. When equipped with
a Variable-Frequency Drive (VFD), the fan will ramp up
to the congured fan speed (dependent on whether the
unit is heating or cooling). ). The Fan input is monitored
to determine if fan is operating or not. If not operating, the
IAIRE controller will enter into an alarm state, start staging
o compressors, and attempt to cycle the fan until it starts.
There is a congurable EAT Heat Lockout (default 58F).
If the EAT is < or = to this temperature, the electric heat
stages will cycle to maintain the room air temperature
setpoint.
There is a congurable EAT Cool Lockout (default 61F). If
the EAT is > or = to this temperature than Y1 is always on
and Y2-Y4 (if enabled) along with the modulated hot gas
valve will be used to maintain the room air temperature.
If the EAT is > the EAT Heat Lockout (default 58F) and <
the EAT Cool Lockout (default 61F) The modulated hot gas
valve is used to maintain room air temperature (Y1 will turn
on as necessary). While in this mode, if humidity is > 50%
then Y1 will stage on and if humidity is > 70% then Y2 will
stage on as well. Y2 will stage o, once on, if necessary to
help maintain room air temperature.
SEQUENCE OF OPERATIONS
DAT
In the UNOCCUPIED mode, the outside air unit will be
o and the outside air damper, if supplied, will be closed.
Occupied or Unoccupied is signaled to the IAIRE controller
via a normally open or normally closed contact on the
OCCUPIED input with a clock or switch. An open contact
on the input indicates OCCUPIED, a closed contact
indicates UNOCCUPIED.
In the OCCUPIED mode, the outside air damper will open
and the supply fan will ramp up to the congured fan speed
(dependent on whether the unit is heating or cooling). The
Fan input is monitored to determine if fan is operating or
not. If not operating, the IAIRE controller will enter into an
alarm state, start staging o compressors, and attempt to
cycle the fan until it starts.
There is a congurable EAT Heat Lockout (default 58F). If
the entering air temperature (EAT) is < or = to the lockout,
then the heat stages will cycle to maintain the discharge air
temperature DAT setpoint.
There is a congurable EAT Cool Lockout (default 61F). If
the EAT is > or = to this lockout than Y1 is always on and
Y2-Y4 is staged on depending on demand (if enabled),
along with the modulated hot gas valve will be used to
maintain the DAT.
If the EAT is > the EAT Heat Lockout (default 58F) and
< the EAT Cool Lockout (default 61F), Y1 will stage on
and the modulated hot gas will maintain DAT unless DAT
setpoint = EAT then free-cooling will engage and Y1 will be
o. While in this mode, if discharge humidity is > 50% then
Y1 will stage on and if its >70% then Y2 will stage on as
well.
SEQUENCE OF OPERATIONS NOTES
All forms of temperature control (SPACE / DAT / ultraDRY3) can come with the ability to control the supply fan with VAV
control.
VAV control can be set up for either duct static pressure control or building pressure control. In either of these cases,
there is a min CFM setting to maintain minimum airow to keep the evaporator coil from freezing and a max CFM setting
to make sure you cannot run more air than the unit can heat or cool.
Duct static control tries to maintain a user set constant pressure in the discharge duct of the equipment.
Building static control tries to maintain a user set constant pressure in the building space.

iAIRE OM manualiAIRE, LLC
11
WIRING AND ELECTRICAL
DAT default variables
EAT cool lockout (61 degrees)
EAT heat lockout (58 degrees)
DAT setpoint (70 degrees)
EAT cool 2 lockout (72 degrees)
LAT setpoint (55 degrees) DX
EAH humidity lockout (55% RH)
Space default variables
EAT cool lockout (61 degrees)
Room setpoint (60-80 degrees)
EAT cool 2 lockout (72 degrees)
EAH humidity lockout (55% RH)
SEQUENCE OF OPERATIONS (cont’d)
ultraDRY3
FAN SPEED CONTROL
These units are equipped with variable speed supply fan
control. There is a cooling and heating fan speed set
point. In this application, both the cooling and heating fan
speed set point should be the same. This should be set by
the test and balance contractor to provide and correct CFM
for the unit. Once the supply fan speed is initially set, it will
not modulate.
NORMAL HOURS (not night set back)
Cooling Mode(humidistat on cooling) –When the
temperature gets above the set point temperature by more
than 2 degrees, the compressor will come on and start
cooling the air. Once the temperature reaches the set-
point, the compressor will turn o and the air will continue
to circulate in the space without heating or cooling.
Heating Mode (humidistat on heating) – When the
temperature gets below the set point temperature by
more than 2 degrees, the heat pump will come and begin
heating the air. Once the temperature reaches the set
point temperature, the heat pump will turn o and the air
will continue to circulate in the space without heating or
cooling.
Humidity mode – When the unit is not running in cooling
or heating and the humidity sensor on the humidistat
registers a humidity higher than the set point humidity, the
compressor will come on for cooling and the hot gas on/o
valves will open to raise the discharge temperature of the
air entering the building after cooling. This will help reduce
the humidity without cooling the building o too much.
Once the humidity is below the set point humidity, the unit
compressor and hot gas on/o valves will shut o and the
air will continue to circulate in the space without heating or
cooling.
NIGHT SET BACK HOURS
Allows the occupant to set a schedule across the 7 day, 24
hour week to schedule set back temperatures at night to
conserve energy.
UNOCCUPIED HOURS
Allows the occupant to set a schedule across the 7 day, 24
hour week to schedule the unit o to conserve energy.

iAIRE, LLC iAIRE OM manual
12
NAVIGATE BACK
NAVIGATE FORWARD
SCROLL PREVIOUS OPTION/MENU
SCROLL NEXT OPTION/MENU
NAVIGATING ON AN iAIRE CONTROLLER
POWER ON THE CONTROLLER AND THE FIRST MENU IS STATUS MENU. TO NAVIGATE THROUGH THE OPTIONS,
PRESS THE UP ARROW KEY. PRESS ENTER TO MAKE CHANGES IN ANY SUB MENU. TO GO BACK TO THE MAIN
STATUS MENU, PRESS THE ESC BUTTON.
MENU SCREENS BEGIN ON THE FOLLOWING PAGE.

iAIRE OM manualiAIRE, LLC
13
STATUS MENU
fan status
RANGE:
On/Off
startup status
RANGE:
Started_Off
Entering Air
Temp Status
RANGE:
- 058 F_132 F
NOTE: View Entering (OA) Air Temp. Sensor
failures register as -58F.
leaving Air
humidity
RANGE:
000_100
NOTE: DAT mode only.
Room Air
Humidity Status
RANGE:
000_100
NOTE: View Room Humidity %.
Room SP and
Temp Status
RANGE:
032 F_085 F
NOTE: View Room Temp Setpoint and Actual
Temp.
DAT/LAT Status
RANGE:
- 058 F_132 F
NOTE:
"Discharge Air Temp. of Unit / Leaving
Air Temp. of Evaporator Sensor failures
register as -58F."
Dehumidification
Status
RANGE:
Disabled/Enabled
NOTE:
Enabled because of Dehumidification
call.
NOTE: Controller is enabled or disabled.
RANGE:
On/Off
NOTE: BAS Switch.
NOTE: Supply Fan Status.
cool mode status
RANGE:
Disabled/Enabled
hot Gas status
RANGE:
000_100
Heating Stages
Status
RANGE:
W1 W2 W3
NOTE:
View Number of Heating Stages
called.
Cooling Stages
Status
RANGE:
Y1 Y2 Y3 Y4
NOTE:
View Number of Cooling Stages
called.
Modulating heat
Status
RANGE:
000_100
NOTE:
View % of Modulating Gas or Electric
Heat.
NOTE:
View % of Modulating Hot Gas
Reheat.
heat mode status
RANGE:
Disabled/Enabled
NOTE:
DAT mode only
NOTE:
Enabled because of Cooling call.
RANGE:
On/Off
NOTE: Test Mode.
VAV
STATUS MENU
duct pressure
DEFAULT:
[enabled]
DEFAULT:
[enabled]
NOTE:
Duct pressure 00.00 IN H2O. Fan
speed (FAST) 100.
buliding
pressure
NOTE:
Building pressure -00.50 IN H2O. Fan
speed (FAST) 100.

iAIRE, LLC iAIRE OM manual
14
TEST MODE MENU
hot gas test
RANGE:
0_100%
DEFAULT:
000
NOTE:
Allows test of modulating gas reheat
valves. Must have Cool 1 Test stage enable to
create any reheat.
vfd speed test
RANGE:
0_100%
DEFAULT:
050
NOTE:
Allows test of fan speed. Fan will not
engage until Fan Test is Enabled.
cool 1 test
RANGE:
Enabled/Disabled
DEFAULT:
N/A
NOTE:
Turns on relay to turn Compressor 1
on.
fan test
RANGE:
Enabled/Disabled
DEFAULT:
N/A
NOTE:
Turns on supply fan contactor. Fan
runs at VFD Speed Test %.
heat 1 test
RANGE:
Enabled/Disabled
DEFAULT:
N/A
NOTE:
Turns on relay to turn W1 on.
heat 2 test
RANGE:
Enabled/Disabled
DEFAULT:
N/A
NOTE:
Turns on relay to turn W2 on.
heat 3 test
RANGE:
Enabled/Disabled
DEFAULT:
N/A
NOTE:
Turns on relay to turn W3 on.
cool 2 test
RANGE:
Enabled/Disabled
DEFAULT:
N/A
NOTE:
Turns on relay to turn Compressor 2
on.
erv wheel test
RANGE:
On/Off
DEFAULT:
N/A
NOTE:
cool 3 test
RANGE:
Enabled/Disabled
DEFAULT:
N/A
NOTE:
Turns on relay to turn Compressor 3
on.
cool 4 test
RANGE:
Enabled/Disabled
DEFAULT:
N/A
NOTE:
Turns on relay to turn Compressor 4
on.
mod heat test
RANGE:
0_100%
DEFAULT:
000
NOTE:
Allows test of modulating gas heat
valve. Must have W1 Test stages enabled to
create any heat.
damper test
RANGE:
0_100%
DEFAULT:
000
NOTE:
Allows test of damper air flow.
oa test
RANGE:
0_100%
DEFAULT:
000
NOTE:
Allows test of outside air flow.
ea test
RANGE:
0_100%
DEFAULT:
000
NOTE:
Allows test of exhaust air flow.

iAIRE OM manualiAIRE, LLC
15
SETPOINTS MENU
VFD SPEED COOL %
RANGE:
0_100% (100% = 60 Hz)
DEFAULT:
060
VFD SPEED heat %
RANGE:
0_100% (100% = 60 Hz)
DEFAULT:
050
EAT Heat Lockout
RANGE:
32 F_100 F
DEFAULT:
61 F
NOTE: Heating disabled until Outside Air
Temp is at this setpoint or below. When
enabled, Y1 will not come on.
lat setpoint
RANGE:
39 F_ 58 F
DEFAULT:
55 F
NOTE:
Temperature unit is trying to control
leaving air temperature off of evaporator coil
when LAT overide is enabled.
SET DUCT
PRESSURE
RANGE:
0.00 _ 5.00 IN H2O
DEFAULT:
1.00
NOTE:
Allows the change in pressure inside
the duct.
NOTE:
Allows the change in pressure inside
the building.
RANGE:
0.00 _ 5.00 IN H2O
DEFAULT:
1.00
Set Building
pressure
Humidity Stage 1
Setpoint %
RANGE:
000_100
DEFAULT:
050
NOTE: Space or DAT humidity in which unit
will force Y1 on to dehumify in dead band.
Humidity Stage 2
Setpoint %
RANGE:
000_100
DEFAULT:
055
NOTE: Space or DAT humidity in which unit
will force Y2 on to dehumify in cooling mode or
dead band.
EAT Cool LckOut
RANGE:
000 F_100 F
DEFAULT:
061 F
NOTE: Cooling Disabled until Outside Air
Temp is at this setpoint or above. When
enabled, Y1 is always on.
DAT setpoint
RANGE:
000 F_100 F
DEFAULT:
070 F
NOTE: (DAT MODE ONLY) Temperature
unit is trying to control to when in Discharge air
mode (DAT).
NOTE: Supply fan speed in heating mode.
NOTE: Supply fan speed in cooling mode.
ROOM TEMP
SETPOINT
RANGE:
1. N/A
2. [enabled]
3. N/A
4. 60 F_90 F
DEFAULT:
1. SPACE MODE
2. Set Via I/O
3. Set Remotely
4. User Interface
NOTE:
1. Temperature unit is trying to control to when
in SPACE MODE.
2. When this is enabled, unit is getting room
setpoint temperature for iAIRE provided space
sensor.
3. When this is enabled, unit is getting room
setpoint temperature from BAS system.
4. When this is enabled, unit is getting room
setpoint temperature from iAIRE controller in
unit.
lockout deadband
RANGE:
01 F_ 60 F | 30 F_ 31 F
DEFAULT:
03_58 F
NOTE: Deadband/HeatLOCK

iAIRE, LLC iAIRE OM manual
16
CONFIGURATION MENUS
Config Heat
and Cool Offsets
OPTION: Cool Stage 2 On Offset
RANGE:
-10F SP to +10F SP
DEFAULT:
+1F SP
NOTE: Allows user to set temp difference
from setpoint that Y2 is enabled.
OPTION: Cool Stage 2 Off Offset
RANGE:
-10F SP to +10F SP
DEFAULT:
-2F SP
NOTE: Allows user to set temp difference
from setpoint that Y2 is disabled.
OPTION: Cool Stage 3 On Offset
RANGE:
-10F SP to +10F SP
DEFAULT:
+3F SP
NOTE: Allows user to set temp difference
from setpoint that Y3 is enabled.
OPTION: Cool Stage 3 Off Offset
RANGE:
-10F SP to +10F SP
DEFAULT:
-1F SP
NOTE: Allows user to set temp difference
from setpoint that Y3 is disabled.
OPTION: Cool Stage 4 On Offset
RANGE:
-10F SP to +10F SP
DEFAULT:
+4F SP
NOTE: Allows user to set temp difference
from setpoint that Y4 is enabled.
OPTION: Cool Stage 4 Off Offset
RANGE:
-10F SP to +10F SP
DEFAULT:
0F SP
NOTE: Allows user to set temp difference
from setpoint that Y4 is disabled.
OPTION: Heat Stage 1 On Offset
RANGE:
-10F SP to +10F SP
DEFAULT:
0F SP
NOTE: Allows user to set temp difference
from setpoint that W1 is enabled.
OPTION: Heat Stage 1 Off Offset
RANGE:
-10F SP to +10F SP
DEFAULT:
+4F SP
NOTE: Allows user to set temp difference
from setpoint that W1 is disabled.
OPTION: Heat Stage 2 On Offset
RANGE:
-10F SP to +10F SP
DEFAULT:
-2F SP
NOTE: Allows user to set temp difference
from setpoint that W2 is enabled.
OPTION: Heat Stage 2 Off Offset
RANGE:
-10F SP to +10F SP
DEFAULT:
+2F SP
NOTE: Allows user to set temp difference
from setpoint that W2 is disabled.
OPTION: Heat Stage 3 On Offset
RANGE:
-10F SP to +10F SP
DEFAULT:
-3F S
P
NOTE: Allows user to set temp difference
from setpoint that W3 is enabled.
OPTION: Heat Stage 3 Off Offset
RANGE:
-10F SP to +10F SP
DEFAULT:
+1F SP
NOTE: Allows user to set temp difference
from setpoint that W3 is disabled.
Config Heat
and Cool timers
OPTION: Cool 1 On Delay
RANGE:
000S _ 600S
DEFAULT:
120S
NOTE: Allows user to set delay before Y1
comes on after controller deems Y1 is
required.
OPTION: Cool 1 Off Delay
RANGE:
000S _ 600S
DEFAULT:
060S
NOTE: Allows user to set delay before Y1
goes off after controller deems Y1 isn’t
required.
OPTION: DeHumidify Off (Y1 Off) Offset
RANGE:
-10F SP to +10F SP
DEFAULT:
Off 02F Below S
P
OPTION: Cool 2 On Delay
RANGE:
000S _ 600S
DEFAULT:
120S
NOTE: Allows user to set delay before Y2
comes on after controller deems Y2 is
required.
OPTION: Cool 2 Off Delay
RANGE:
000S _ 600S
DEFAULT:
060S
NOTE: Allows user to set delay before Y2
goes off after controller deems Y2 isn’t
required.
OPTION: Cool 3 On Delay
RANGE:
000S _ 600S
DEFAULT:
180S
NOTE: Allows user to set delay before Y3
comes on after controller deems Y3 is
required.
OPTION: Cool 3 Off Delay
RANGE:
000S _ 600S
DEFAULT:
030S
NOTE: Allows user to set delay before Y3
goes off after controller deems Y3 isn’t
required.
OPTION: Heat 1 On Delay
RANGE:
000S _ 600S
DEFAULT:
030S
NOTE: Allows user to set delay before W1
comes on after controller deems W1 is
required.
OPTION: Heat 1 Off Delay
RANGE:
000S _ 600S
DEFAULT:
005S
NOTE: Allows user to set delay before W1
goes off after controller deems W1 isn’t
required.
OPTION: Heat 2 On Delay
RANGE:
000S _ 600S
DEFAULT:
005S
NOTE: Allows user to set delay before W2
comes on after controller deems W2 is
required.
OPTION: Heat 2 Off Delay
RANGE:
000S _ 600S
DEFAULT:
000S
NOTE: Allows user to set delay before W2
goes off after controller deems W2 isn’t
required.
OPTION: Heat 3 On Delay
RANGE:
000S _ 600S
DEFAULT:
005S
NOTE: Allows user to set delay before W3
comes on after controller deems W3 is
required.
OPTION: Heat 3 Off Delay
RANGE:
000S _ 600S
DEFAULT:
000S
NOTE: Allows user to set delay before W3
goes off after controller deems W3 isn’t
required.
OPTION: Cool 4 On Delay
RANGE:
000S _ 600S
DEFAULT:
180S
NOTE: Allows user to set delay before Y4
comes on after controller deems Y4 is
required.
OPTION: Cool 4 Off Delay
RANGE:
000S _ 600S
DEFAULT:
030S
NOTE: Allows user to set delay before Y4
goes off after controller deems Y4 isn’t
required.

iAIRE OM manualiAIRE, LLC
17
CONFIGURATION MENUS
(cont.)
controller mode
configuration
OPTION: DAT MODE
RANGE:
N/A
DEFAULT:
[enabled]
NOTE: Discharge Air Temp Controlled.
OPTION: SPACE MODE
RANGE:
N/A
DEFAULT:
[disabled]
NOTE: 0-10vdc Space Sensor Controlled.
configure # of
control boards
OPTION: 1 CONTROL BOARD
RANGE:
N/A
DEFAULT:
[enabled]
NOTE: Main Controller basic I/O.
OPTION: 2 CONTROL BOARDS
RANGE:
N/A
DEFAULT:
[disabled]
NOTE: Accessory Controller additional I/O.
configure # of
HEAT STAGES
OPTION: # of Heat Stages 1
RANGE:
N/A
DEFAULT:
[enabled]
NOTE: Set number of heat stages in unit. If
no heat stages select 1 stage.
OPTION: # of Heat Stages 2
RANGE:
N/A
DEFAULT:
[disabled]
NOTE:
max reheat
requirement
OPTION: Yes, Max Needed
RANGE:
N/A
DEFAULT:
[enabled]
NOTE:
OPTION: No Max Needed
RANGE:
N/A
DEFAULT:
[disabled]
NOTE: If No max is needed is selected, HGR
valve will go from 0-100%.
OPTION: # of Heat Stages 3
RANGE:
N/A
DEFAULT:
[disabled]
NOTE:
configure
Heat Pump
OPTION: No Heat Pump
RANGE:
N/A
DEFAULT:
[enabled]
NOTE:
This is selected for even heat pump if
the heat pump logic turns on Y1 & O on W1
command.
OPTION: Yes, Heat Pump
RANGE:
N/A
DEFAULT:
[disabled]
NOTE:
This is selected if the heat pump
requires both Y1 & W1(O) signal to run.
BAS config
OPTION: No BAS
RANGE:
N/A
DEFAULT:
[enabled]
NOTE:
Unit Operates as Standalone.
OPTION: Yes, BAS Active
RANGE:
N/A
DEFAULT:
[disabled]
NOTE:
Unit is Operated by Building
Automation System.
comm setup
OPTION: Cks Only
RANGE:
N/A
DEFAULT:
[enabled]
NOTE:
Default V.4+.
OPTION: Repeating
RANGE:
N/A
DEFAULT:
[disabled]
NOTE:
Used when V3 Main Board is
replaced w/ V4 Board.
fan input
OPTION: Fan is Enabled
RANGE:
N/A
DEFAULT:
[selected]
NOTE:
Unit has a feedback to ensure supply
fan is on. If not unit will not run and go into
alarm.
OPTION: Fan is Disabled
RANGE:
N/A
DEFAULT:
N/A
NOTE:
If this is selected, it ignores the
feedback from fan and runs unit
regardless of feedback.
LAT Override
OPTION: LAT Override OFF
RANGE:
N/A
DEFAULT:
[enabled]
NOTE:
When enabled, forces the unit to run
to try and maintain LAT temperature over other
commands.
OPTION: LAT Override ON
RANGE:
N/A
DEFAULT:
[disabled]
NOTE:
reheat min
RANGE:
001_100
DEFAULT:
002
NOTE:
If Reheat min is set to 0%, the unit
can vapor lock due to lack of fluid flow through
reheat coil.
reheat max
RANGE:
001_100
DEFAULT:
075
NOTE:
If Reheat max is more that 75%, many
times the unit will loose ability to cool.
reheat
multiplier
RANGE:
.1_1
DEFAULT:
.8
NOTE:
% Modulating reheat signal = (((Act
temp - setpoint temp)+ Reheat Offset)/Reheat
Gain) * Reheat Multiplier.
reheat gain
RANGE:
-20_20
DEFAULT:
03
NOTE:
% Modulating reheat signal = (((Act
temp - setpoint temp)+ Reheat Offset)/Reheat
Gain) * Reheat Multiplier.
reheat offset
RANGE:
-10_10
DEFAULT:
01
NOTE:
% Modulating reheat signal = (((Act
temp - setpoint temp)+ Reheat Offset)/Reheat
Gain) * Reheat Multiplier.
humidity mode
config
OPTION: 0-10V/0-100%
RANGE:
N/A
DEFAULT:
[enabled]
NOTE:
OPTION: 0-10V/20-80%
RANGE:
N/A
DEFAULT:
[disabled]
NOTE:
OPTION: User Defined
RANGE:
N/A
DEFAULT:
[disabled]
NOTE:
Allows user to set up different humidity
sensors if required.
humidity low sp
RANGE:
001 _ 080
DEFAULT:
020
NOTE:
USER DEFINED

iAIRE, LLC iAIRE OM manual
18
CONFIGURATION MENUS
cont.)
humidity high sp
RANGE:
020 _ 100
DEFAULT:
080
NOTE: USER DEFINED
freeze
protection
RANGE:
Off < 33_45 F
DEFAULT:
039
NOTE:
On at 39 F.
freeze timer
RANGE:
000S_600S
DEFAULT:
300S
NOTE:
Freeze time 300 seconds.
water guard
config
RANGE:
Disabled/Enabled
DEFAULT:
Disabled
NOTE:
Supplemental
heat
OPTION: No Supp Heat
RANGE:
N/A
DEFAULT:
[enabled]
NOTE: Allows unit to bring on stages of heat
if HGR does not have enough heat to get unit
to Space or DAT set point temperature.
OPTION: W1 Supp. Heat
RANGE:
N/A
DEFAULT:
[disabled]
NOTE: W1 will be supplemental heat.
OPTION: W2 Supp. Heat
RANGE:
N/A
DEFAULT:
[disabled]
NOTE: W2 will be supplemental heat - This
would be selected if unit has a heat pump
since W1 is Y1 & O.
OPTION: W3 Supp. Heat
RANGE:
N/A
DEFAULT:
[disabled]
NOTE: W3 will be supplemental heat.
hum override on
delay
RANGE:
000S _ 600S
DEFAULT:
180S
NOTE: When Y2 is called on because of
humidity, this is the delay the unit will keep Y2
off before it turns on.
hum override off
delay
RANGE:
000S _ 600S
DEFAULT:
120S
NOTE: When Y2 is on because of humidity
and is no longer needed, this is the delay the
unit will keep Y2 on before it shuts it off.
allow hum off
override delay
RANGE:
000S _ 600S
DEFAULT:
300S
NOTE: When Y2 is on because of humidity
and the space temperature is below set point,
this is the delay the unit will keep Y2 on before
it shuts it off.
CONFIGURATION MENU
(SPACE ONLY)
room temp type
OPTION: GreyStone
RANGE:
N/A
DEFAULT:
[enabled]
NOTE:
Allows user to select what type of
space sensor is being used.
OPTION: User Defined
RANGE:
N/A
DEFAULT:
[disabled]
NOTE:
Allows user to create custom curve to
utilize their own space sensor. Signal is 0-10V.
OPTION: Tongdy 32F-122F
RANGE:
N/A
DEFAULT:
[disabled]
NOTE:
OPTION: Tongdy 32F-140F
RANGE:
N/A
DEFAULT:
[disabled]
NOTE:
ROOM TEMP LOW
RANGE:
-040 _ 080
DEFAULT:
032
ROOM TEMP HIGH
RANGE:
000 _ 140
DEFAULT:
095
ROOM setpoint
LOW
RANGE:
050 _ 082
DEFAULT:
062
ROOM setpoint
HIGH
RANGE:
062 _ 130
DEFAULT:
082
ROOM SETPOINT
SOURCE
OPTION: I/O
RANGE:
60 F_90 F
DEFAULT:
[enabled]
NOTE:
When this is enabled, unit is getting
room setpoint temperature for iAIRE provided
space sensor.
OPTION: User Interface
RANGE:
60 F_90 F
DEFAULT:
[enabled]
NOTE:
When this is enabled, unit is getting
room setpoint temperature from iAIRE
controller in unit.
OPTION: Remotely
RANGE:
BAS Controlled
DEFAULT:
[disabled]
NOTE:
When this is enabled, unit is getting
room setpoint temperature from BAS system.

iAIRE OM manualiAIRE, LLC
19
CONFIGURATION MENUS
(2 Control Boards Only)
mod heat config
OPTION: Electric
RANGE:
N/A
DEFAULT:
[enabled]
NOTE: This is selected if unit is all electric
unit.
OPTION: Gas 1
RANGE:
N/A
DEFAULT:
[disabled]
NOTE: This is selected if unit is a 1 stage gas
heat unit or a unit with a high high heat unit.
OPTION: Gas 2
RANGE:
N/A
DEFAULT:
[disabled]
NOTE: This is selected if the unit has a 2
stage gas heat unit.
configure # of
cooling stages
OPTION: 1
RANGE:
N/A
DEFAULT:
[enabled]
NOTE: Select # of cooling stages the unit
has.
OPTION: 2
RANGE:
N/A
DEFAULT:
[disabled]
NOTE:
OPTION: 3
RANGE:
N/A
DEFAULT:
[disabled]
NOTE:
OPTION: 4
RANGE:
N/A
DEFAULT:
[disabled]
NOTE:
configure heat
type
OPTION: Non-Mod Heat
RANGE:
N/A
DEFAULT:
[enabled]
NOTE: Select if the unit has modulating heat
or not.
OPTION: Mod Heat
RANGE:
N/A
DEFAULT:
[disabled]
NOTE:
modulated
heat min
RANGE:
000 _ 100
DEFAULT:
000
NOTE: Sets minimum % output from contoller
to modulating heat valve.
modulated
heat max
RANGE:
000 _ 100
DEFAULT:
100
NOTE: Sets minimum % output from contoller
to modulating heat valve - This will limit max
firing of heater.
modulated
heat gain
RANGE:
-20 _ 20
DEFAULT:
04
NOTE: % Modulating heat signal = (((Act
temp - setpoint temp)+ Mod Heat Offset)/Mou-
lated Heat Gain) * Mod Heat Multiplier.
modulated
heat offset
RANGE:
-10 _ 10
DEFAULT:
00
NOTE: % Modulating heat signal = (((Act
temp - setpoint temp)+ Mod Heat Offset)/Mou-
lated Heat Gain) * Mod Heat Multiplier.
modulated heat
multiplier
RANGE:
.1 _ 1
DEFAULT:
1
NOTE: % Modulating heat signal = (((Act
temp - setpoint temp)+ Mod Heat Offset)/Mou-
lated Heat Gain) * Mod Heat Multiplier.

iAIRE, LLC iAIRE OM manual
20
CONFIGURATION MENUS
(Config VAV)
(if duct or build pressure
is [enabled])
VAV MODE
CONFIGURATION
OPTION: VAV mode off
RANGE:
N/A
DEFAULT:
[enabled]
NOTE:
set min
fan speed
RANGE:
000_100
DEFAULT:
40
NOTE:
set max
fan speed
RANGE:
000_100
DEFAULT:
100
NOTE:
(if ERV mode is [enabled])
set oa
fan speed
RANGE:
000_100
DEFAULT:
50
NOTE:
set ea
fan speed
RANGE:
000_100
DEFAULT:
50
NOTE:
set damper
position
RANGE:
000_100
DEFAULT:
100
NOTE:
select damper/
fan control
adjust fast rate
RANGE:
000_100
DEFAULT:
001
NOTE: X * 0.5 seconds
adjust slow rate
RANGE:
000_050
DEFAULT:
005
NOTE: X * 0.5 seconds
select
slow point
RANGE:
000_100
DEFAULT:
013
NOTE:
OPTION: Duct Pressure
RANGE:
N/A
DEFAULT:
[disabled]
NOTE:
OPTION: Build. Pressure
RANGE:
N/A
DEFAULT:
[disabled]
NOTE:
CONFIGURATION MENUS
(Config ERV)
ERV MODE
CONFIGURATION
OPTION: ERV mode off
RANGE:
N/A
DEFAULT:
[enabled]
NOTE:
OPTION: ERV mode
RANGE:
N/A
DEFAULT:
[disabled]
NOTE:
select
transducer type
RANGE:
0in to +1in_-5in to 5in
DEFAULT:
0in to +2in
NOTE:
OPTION: Fan Control
RANGE:
N/A
DEFAULT:
[enabled]
NOTE:
OPTION: Damper Control
RANGE:
N/A
DEFAULT:
[disabled]
NOTE:
Table of contents
Other iAIRE Control System manuals
Popular Control System manuals by other brands
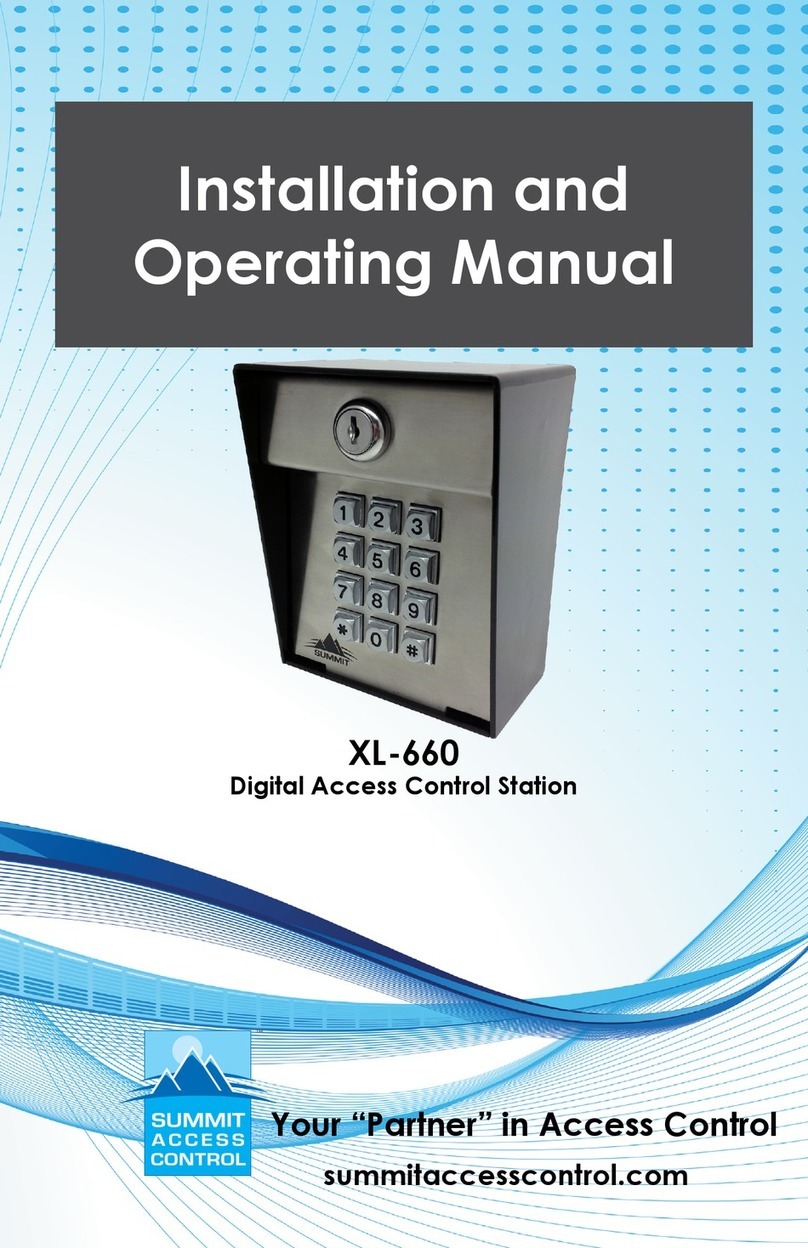
Security Brands
Security Brands XL-660 Installation and operating manual
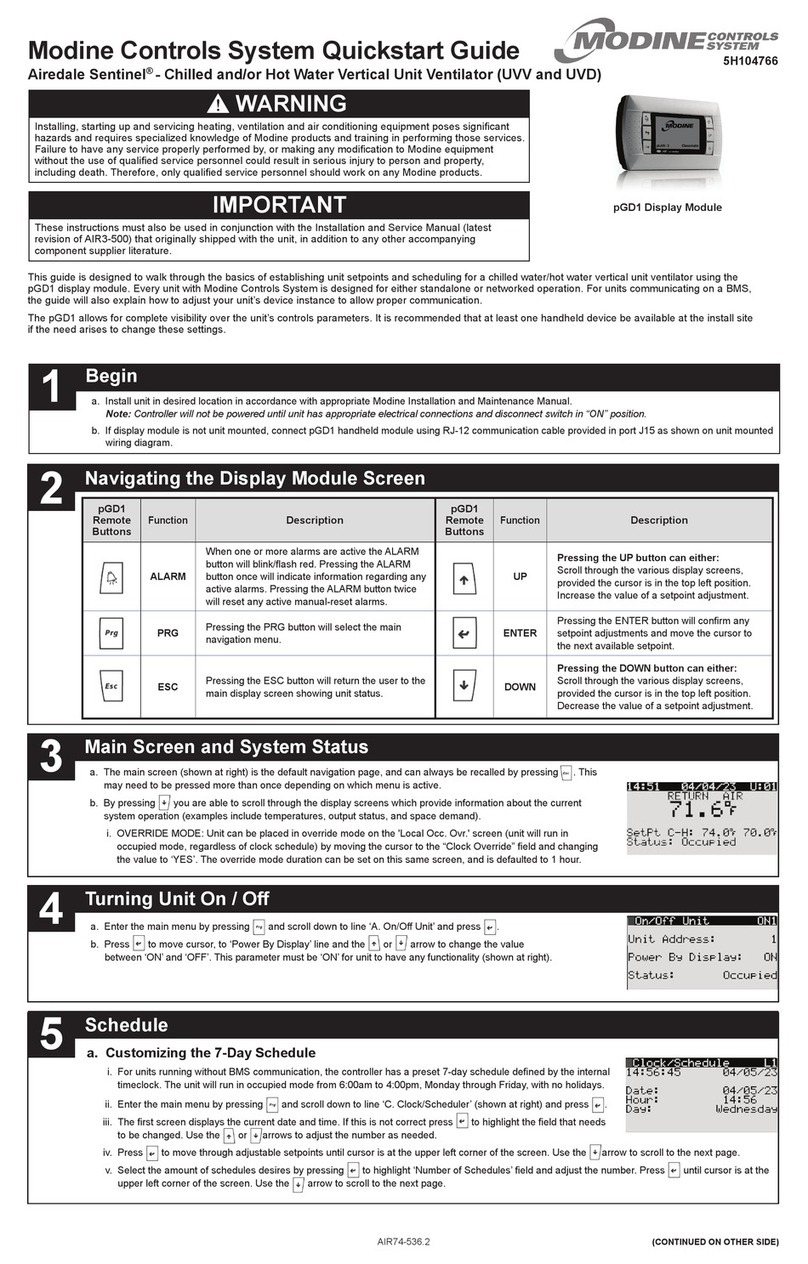
Modine Manufacturing
Modine Manufacturing 5H104766 quick start guide
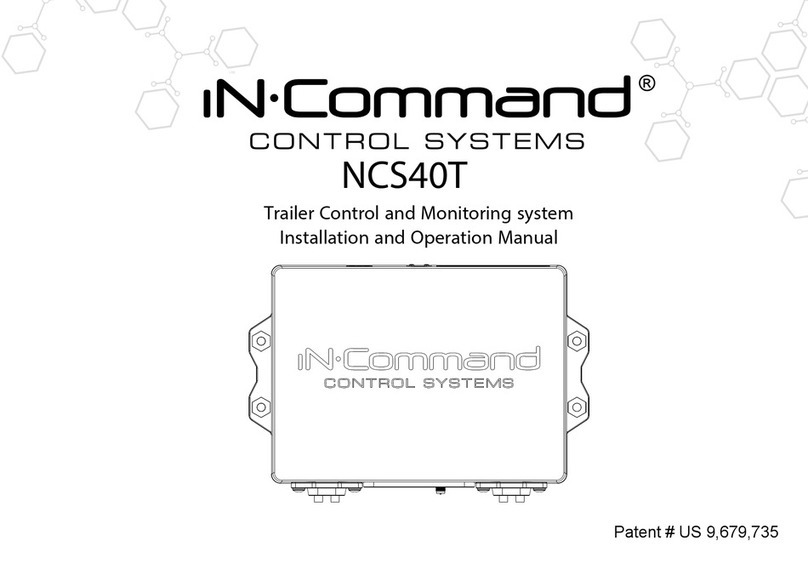
IN-COMMAND
IN-COMMAND NCS40T Installation and operation manual
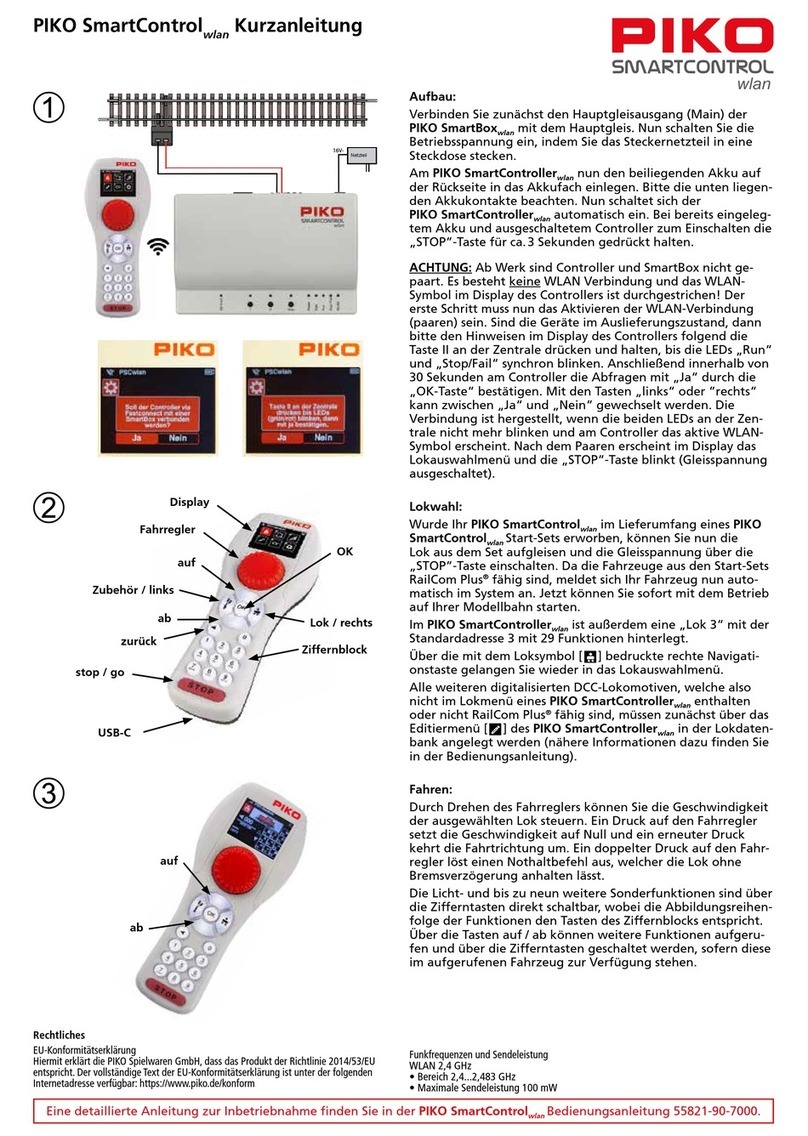
PIKO
PIKO SmartControl WLAN Quick manual
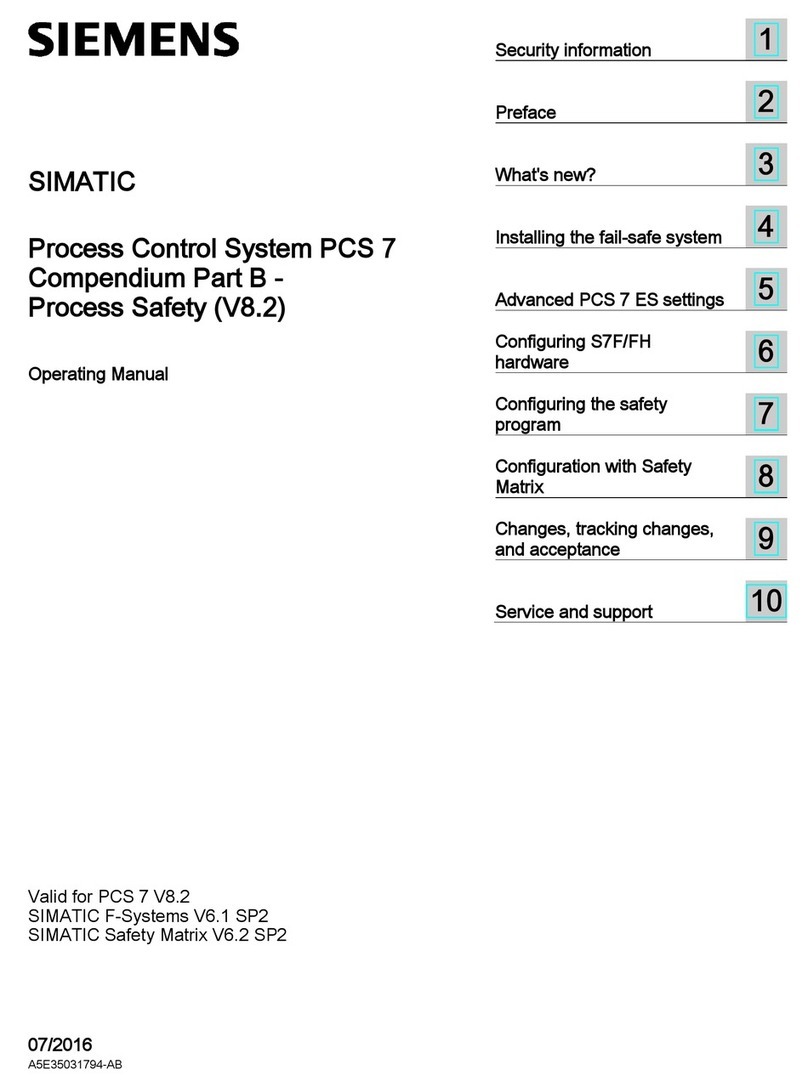
Siemens
Siemens SIMATIC PCS 7 operating manual
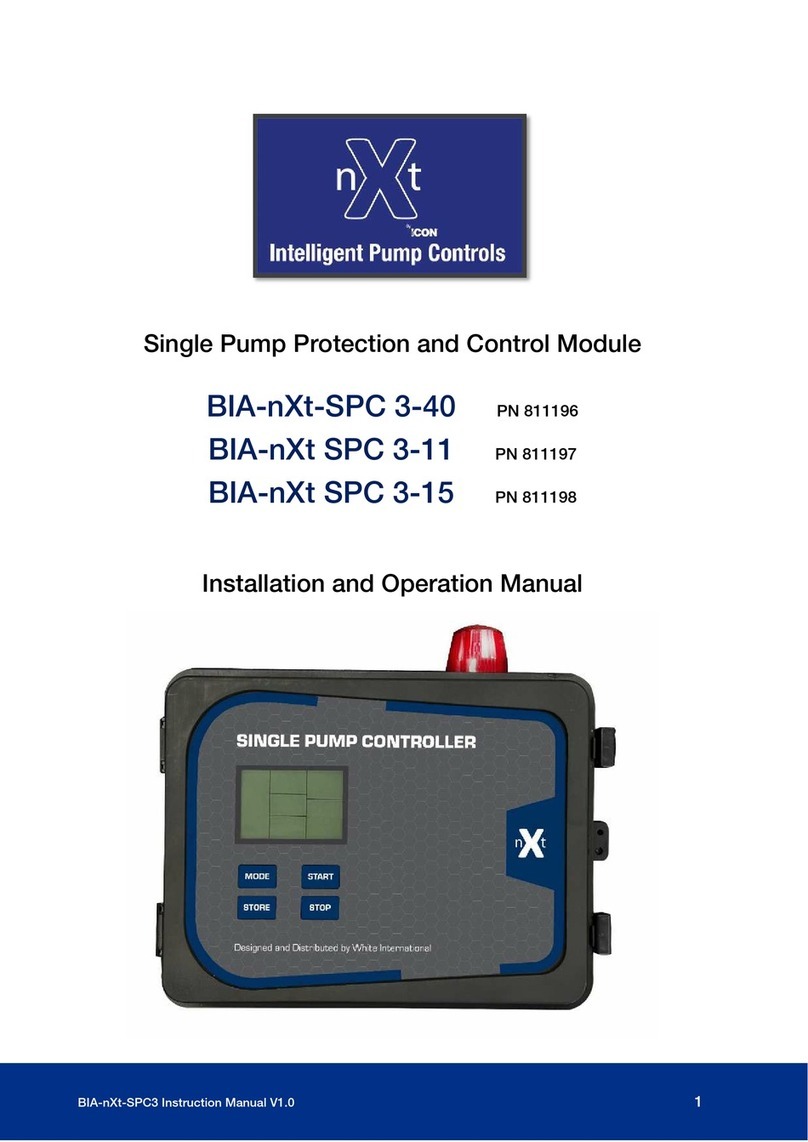
nxt
nxt BIA-nXt-SPC 3-40 Installation and operation manual
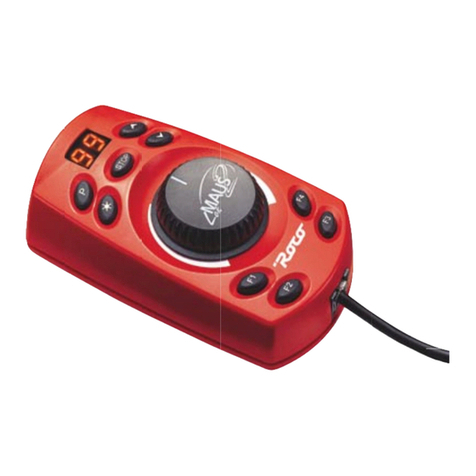
roco
roco LOKMAUS 2 manual

Teton Grill
Teton Grill Fuel Manager Product installation manual
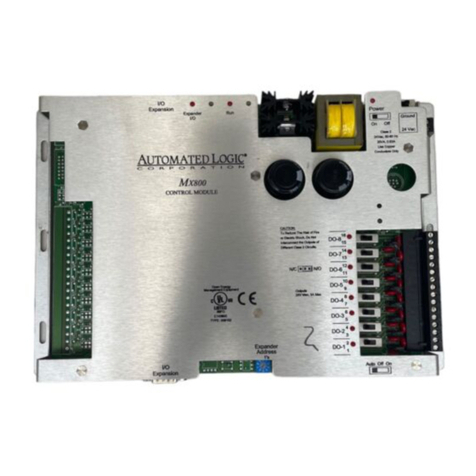
Automated Logic
Automated Logic MX800 Technical instructions
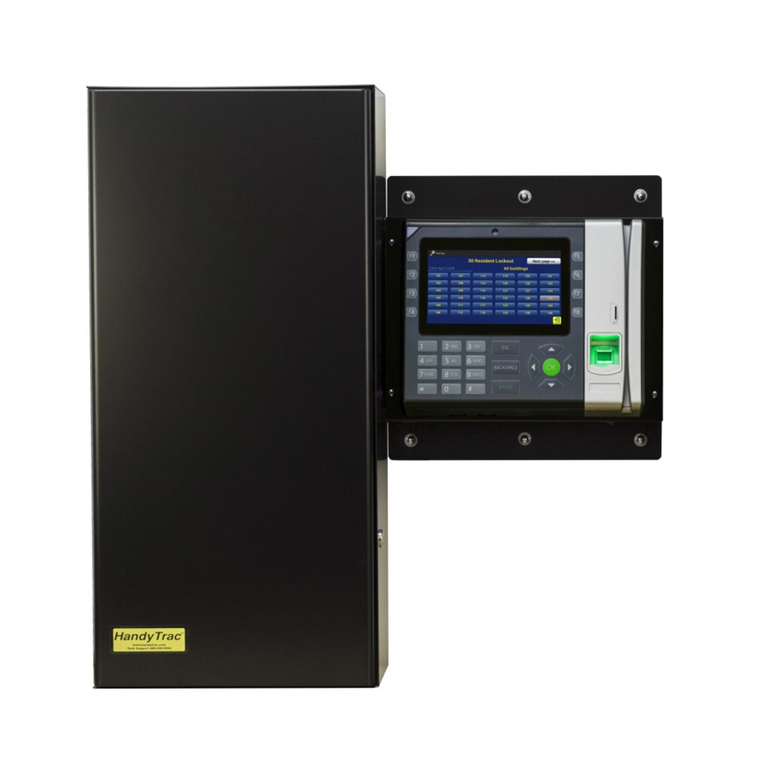
HandyTrac
HandyTrac Key Control System installation & operating manual
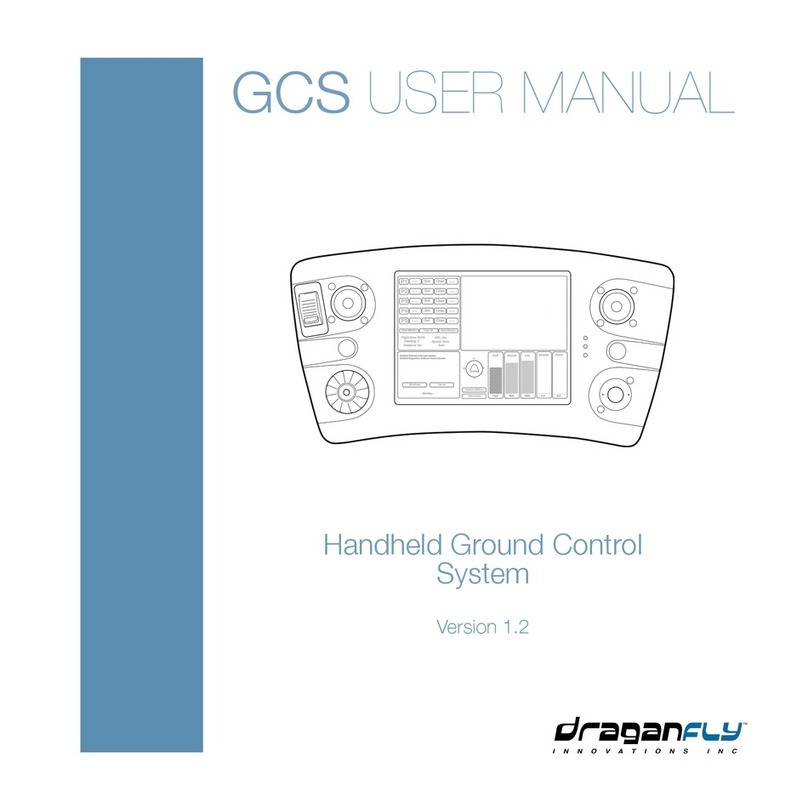
Draganfly
Draganfly GCS user manual
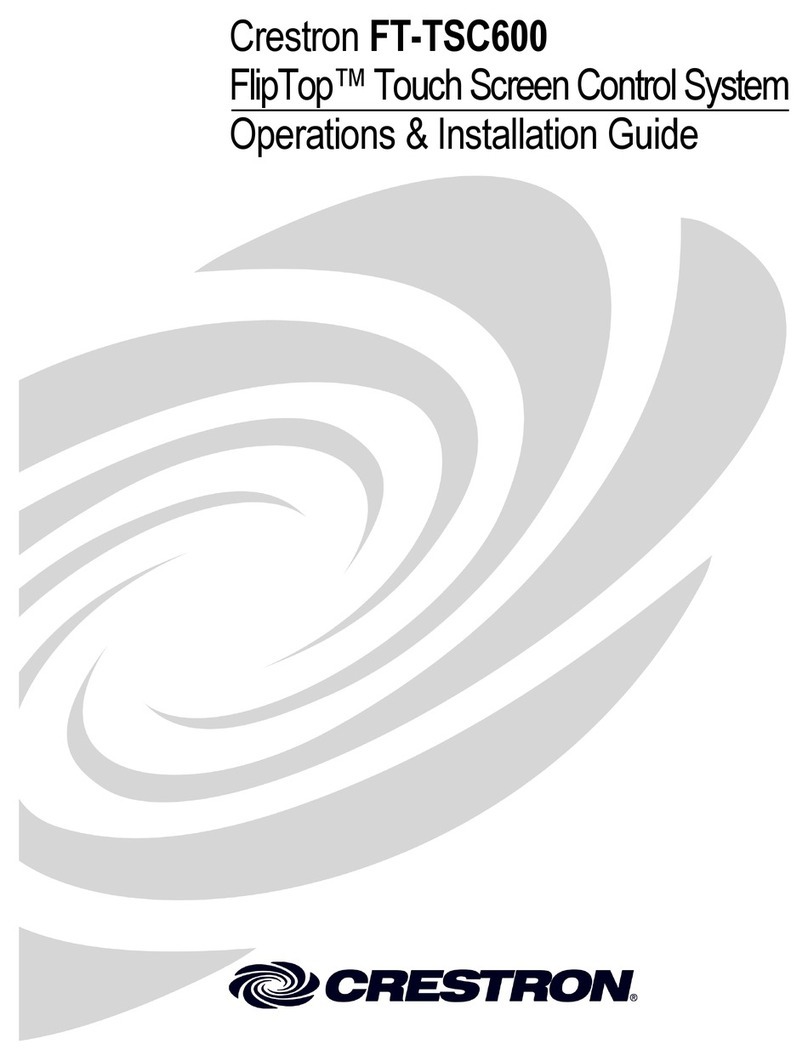
Crestron
Crestron FT-TSC600 FlipTop Operations & installation guide