ICD PFC9055 User manual

1
POWER FACTOR CONTROLLER
MODEL - PFC9055
INDUSTRIAL CONTROLS & DRIVES (INDIA) PVT. LIMITED
New No: 33 Old No:10, Mettukuppam Road, (via) Alapakkam Road,
Maduravoyal, Chennai - 600 095.

2
INDEX
1. GENERAL FEATURE
2. ALARM FUNCTIONS
3. WIRING DIAGRAM
4. FRONT PANEL FEATURE
5. CONTROL OPERATIONS
6. PROGRAMMING INSTRUCTIONS
7. HEADING DISPLAY FORMATS
8. TECHNICAL SPECIFICATION

3
POWER FACTOR CONTROLLER
1.General Features
The Power Factor Controller PFC 9055 measures the power
factor (cosφφ
φφ
φ) and reactive power (kVAr) of power system and displays
them on a digital display. The power factor controller performs the
automaticconnectionanddisconnectionofcapacitorsinfunctionofthepower
factor and set point programmed.
Designed with latest state of art technology using micro controller, the
power factor controller becomes an intelligent equipment, able to
accurately measure the power factor and to take complex decisions for
switching on/off the capacitors.
The power factor controller performs the true R.M.S measurement of
reactive power and power factor including harmonics. The power
measurement is done for the full four quadrants. The power factor is
displayed on a 12.5 mm high visibility red LED display. Four keys are
provided on the front panel for programming purpose.
The power factor controller is provided with 12 output relays with the
possibilityof an additional alarm relay. Thepower factor controller is housed
in a PVC enclosure with the dimension of 144(H)x144(W)x150(D) mm
Installation
General consideration
The meter is panel mountable and fits into a cut out of 138 X 138 mm
dimension. Place the meter through the panel cut out and fix the mounting
clamps provided with the meter on each side of the meter. Tighten the fixing
clamps with limit amount of force so as to hold the meter firmly.
The power factor controller is used to measure power factor, when
mounted in instrument panels and is to be installed only by trained
electricians and technicians. The PT’s and CT’s used for measurement
should be of instrument class 1 or better for accurate measurement
results. Also PT’s and CT’s should have adequate VA rating to support the
burden on the secondaries.

4
The power factor controller must be protected by the fuses in each
voltage circuits. The current circuits must be provided with CT shorting
blocks to reduce the possibility of accidental disconnection. The CT
connections of the meter must not be disconnected while current is flowing
in the primary of the CT.
2. ALARMFUNCTIONS
ALARM - 01 = UNDER COMPENSATION
After all outputs are ON, required kVAr(Lag) >>
>>
> 70% of 1st
capacitorvalue, thealarm LEDwill beON andthe displayshows ALr01
ALARM - 02 = OVER COMPENSATION
After all outputs are OFF, required kVAr(Lead) >>
>>
> 70% of 1st
capacitorvalue, thealarm relaywill beON andthedisplay showsALr 02
ALARM-03=OVERVOLTAGEPROTECTION
Phase voltage >>
>>
> 115%of rated voltage,the alarmLED willbe ON
& step output are switched OFF and the display shows ALr 3r / y/ b
R,Y, B.
ALARM-04 = OVER CURRENT PROTECTION
Phase current >>
>>
> 110%of ratedcurrent, the alarmrelay willbe ON,
step relays are switched OFF and the display showsALr 4r/y / b.
Note
Index(#) keyis used toacknowledge thealarm relay.

5
NO 1 Output Relay - 1 NO 7 Output Relay 7
NO 2 Output Relay – 2 NO 8 Output Relay 8
NO 3 Output Relay – 3 NO 9 Output Relay 9
NO 4 Output Relay – 4 NO 10 Output Relay 10
NO 5 Output Relay – 5 NO 11 Output Relay 11
NO 6 Output Relay – 6 NO 12 Output Relay 12
COM - Relay common for 1 to 6 COM- relay common for 7 to 12
NC P NO relay contacts for Alarm
UPPER TERMINALS
R Three phase voltage input
Y 415 VAC For LT meters
B 110 VAC For HT meters
N
MIR
L
M Three phase current input
IY from external CT’s (1/5 A)
L
MIB
L
Voltage Signal connections
The power factor controller can accept voltages upto 415 VAC R.M.S
+10% to – 20% in case of LT meters and 110 VAC R.M.S +10% to – 20%
in case of HT meters. The voltage input terminals has a burden on auxiliary
power supply less than 10VA.

6
φ
M
L
φ
M
L
φ
M
L
CT
CT CT
Systemworks
normally
Load
Capacitor
Capacitor
Load
Load
Capacitor
All the capacitors are
connected. The power
system may be over
compensated
None of the capacitors
are connected - No
compensationforPF
Rightconnection Wrongconnection Wrongconnection
Current signal connections
The power factor controller is provided with current input terminals to ac-
cept 1/5 A R.M.S from external CT’s. The CT secondary value is not field
programmable and has to be specified at the time of ordering. The current
inputs has a overload capability of 120% and has a burden on less than
0.5VA per phase.
The CT must be placed at any point on the entrance of the power system
where the whole current consumed by both load and capacitors can be
measured.

7
3. Wiring diagram for various
types of systems
a) Three phase four wire LTsystems (3 watt meter measurement)
Voltage Input : 415V AC RMS (L-L) (-20% to +10%)
Current Input : 5/1A provide through 3 CT’s
CT’s
R
Y
B
N
ML
246 8
ML
ML
124578
TOLoad
1/5Amp
110/415VAC
789
C C 10 11 12
C C NC P NO
ALARM
123456
NO NO NO NO NO NO
NO NO NONO NO NO
IR
IY
IB

8
WiringDiagram
b) Three phase four wire HT systems (3 watt meter measurement)
Voltage Input : 110VAC RMS (L-L) (-20% to +10%)
Current Input : 5/1A provided through 3 CT’s
CT’s
R
Y
B
N
ML
2468
ML
ML
124578
1/5Amp
110/415VAC
789
C C 10 11 12
C C NC P NO
ALARM
1234 56
NO NO NONO NO NO
NO NO NO NO NO NO
IR
IY
IB

9
WiringDiagram
C) TThreephasethree wire HT systems (2watt meter measurement)
Voltage Input : 110VAC (L-L)(ThroughPT)
Currentinput :5/1Aprovidedthrough2 CT’sWir
CT’s
R
Y
B
ML
2468
ML
12 78
1/5Amp
110/415VAC
789
C C 10 11 12
C C NC P NO
ALARM
1234 56
NO NO NONO NO NO
NO NO NO NO NO NO
45
IR
IB
IY

10
Cross checking the wiring
The three phase voltage wiring and current wiring are to be properly done
for the correct measurement. Any wrong connections done either during
installation or rewiring can produce wrong measurement.
The reverse condition occurs when the voltages R,Y & B are not con-
nected in proper sequence and also when the respective current is not given
according to its respective voltage.
To avoid any accidental wrong connections the PFC 9055 is provided
with a connection diagnostic page of display. If the display shows Ct niL
then there is no reverse flow otherwise the reversed phase is shown. While
checking the reverse condition, make sure that the load current is more than
5% of full load current.
Relay Output Connections
The power factor controller connects/disconnects the capacitors through
output relays. The relays are rated for 3Aat 240 VAC. So proper contactors
are to be used for switching the capacitors.

11
240VAC
L
L
L
L
240VAC
C6
Neutral
C12
N
C1 C2 C3
C1 - C12 are the coils of the contactors to which the capacitors are
connected. Thecoilsare energisedthrough240VAC supplyvia theoutput
relays.
It is recommended to connect the common supply for the output relays
through four individual wires and also from a separate power source
especiallynotfrom‘ R’phaseand alsonotfromthe terminalblocksof PFC
9055.
789
C
10 11 12
C C NC P NO
ALARM
123456
C
NO NO NO NO NO NO
NO NO NO NO NO NO

12
PF CONTROLLER
8. 8. 8. 8. 8. 8. 8
AUTO 1 23456
MAN 7 89101112
44
44
455
55
5↵↵
↵↵
↵
0.5 “ 7
segment
redLED
Status
LED’s
The display is a 0.5” 7 segment red LED. The LED display shows
powerfactor,ActualkVAr,Target kVAr,Alarmstatus (Alr01/Alr 02/Alr
3r/y/b/Alr4r/y/b)and CTpolarity status.
Thekeypadconsists offourkeynamelyindex,shift,incrementandenter
key. Thesekeysareusedtoprogramvariouscontrolparametersandswitch
on/offthecapacitorsinmanual mode.
TheAUTO/MANUAL LED is illuminated according to the mode of
controlselected. The relay onLED 1 to12 are illuminatedwhenever the
correspondingrelayisswitched on.
PFC9055
ALARM
#AUTO
MAN
ICD CHENNAI-95
4.FRONTPANELFEAUTURE

13
.
5. Controloperations
The power factor controller is provided with two type of control modes
namely Auto mode and Manual mode. The control mode is selected by
pressing key in run mode. The AUTO or MAN LED illuminates
according to the mode of control selected.
Auto mode
The power factor controller calculates the reactive power (kVAr)
and power factor (cosφ) from the voltage and current inputs. It also
computes the reactive power necessary for the target PF. When required
reactive power exceeds the 70% of kVAr (lag) value of the smallest ca-
pacitor in the network, the capacitor stages are automatically connected.
Similarly when the required reactive power exceeds the 70% of kVAr
(lead) value of the smallest capacitor in the network, the capacitor stages
are automatically disconnected.
The capacitor connection/reconnection delay time of 5 to 240 seconds is
provided to allow sufficient time delay for switching on/off the capacitors in
the compensation network. This feature avoids hunting especially in highly
fluctuating loads and also allow the capacitors to discharge properly before
connecting them again in the network. The delay time has to be properly
chosen according to the load and design of capacitor network.
↵↵
↵↵
↵
Auto/man

14
Manual mode
In manual operation, the capacitor banks can be connected/disconnected
irrespective of system power factor and setting. The capacitors are discon-
nected by pressing key. The capacitors are connected by pressing
key. A delay time of 5 seconds is permanently provided for the
connection/disconnection of the capacitors.
6. Programming Instructions
The power factor controller is provided with four keys for program-
ming purpose. The various functions of the keys are given below
Program mode Automode Manual mode
Index key To select P.F, kVar,
Target kVAr,
CT, Alarm status &
Alarm acknowledge
Shiftkey Not applicable Switch off
capactors ( )
Increment key Notapplicable Switch on
capacitors ( )
Enter key To Select Auto mode To select manual
mode
All power factor controllers are to be programmed properly to work in a
particular installation. The various items that are to be programmed are
shown in the table below.
44
44
4
44
44
4
↵
AUTO
-DO-
4
#
44
44
4
44
44
4
MAN

15
The powerfactor controlleris provided withpass word facilityto
preventalterationofconfigurationitemsby unauthorisedpersons. The
configurationitemscanbechangedbyfollowingthesequencegiven
below.
With power applied to the meter, press & keys together
for three seconds. The display indicates enter pass word as EP- - - -
Thevalid password setin configurationitem newpass wordhas to
beenteredbyusing shift,incrementand enterkeys(referchanging the
configurationitemsforusingshift,incrementandenterkeys). Aftervalid
password isentered themeter entersinto programmode byshowing it in
display as P r o g
Note:Ifthe user enters theenter pass word for the first time, or ifthe user
fails to remember the pass word set in new pass word, the default pass
word ‘0386’can be entered.
Inprogram mode,the configuration itemscan beselected by pressing
theindex(#)key. Theheadingdisplaysareused todifferentiatethe various
configurationitems.
44
44
4
44
44
4
Runmodedisplaypages
Press # key one by one, run mode display pages as follows:
Page 1 - Ld 0.51 Powerfactor
Page 2 - q.692.4 ActualtotalkVAr
Page 3 - r.832.4 Target/requiredkVAr
Page 5 -Alr 01 Alarmstatus
Page 4 - CT nil CT/PT polaritystatus

16
7. The heading display pages for various
configuration items are given below.
Password toprevent unauthorisedpersons entry
Ct 1000
PRESS # KEY
Primarycurrentsetting
L005.0
PRESS # KEY
Kvarvalueof thesmallest capacitorinthe compensation-
network
U
SP-0.99
PRESS # KEY
Target power factorsetting (Lag 0.80 to lead0.95)
nC 12
PRESS # KEY
Totalnumberofcapacitorsin thecompensationnetwork
Enterpass word
EP - - -
PRESS 4& 5KEYS TOGETHER
Prog Programmode
nP0000
Cd 008
PRESS # KEY
Timedelayfor connection/disconnectionof capacitors
(Range : 5 - 240 secs.)
OP1.1.1.1.1
Changingtheconfigurationitems
After selecting the configuration item through index key, they can be altered by
using shift, increment and enter keys.
The shift key is is used to select the digit one by one. The selected
digit is shown by flashing that digit. In set point and number of capacitors mode
the shift key is used to decrement the value by one.
The incrementkey is used to increment the selected digit.
rCd 010 Time delay for reconnection (Range :5 - 240 secs.)
PRESS # KEY
PRESS # KEY
C
1.2.4.8.8)
55
55
5
44
44
4

17
Theincrementkey incrementsthe digitfrom 0to9 andthen wraps
downto 0 onceagain. In setpoint and numberof capacitors mode, the
incrementkey isused toincrement thevalues byone. Once therequired
valuesare setinthe configurationitems pressthe enterkey tostore itin the
memory. Ifthechange isaccepted the display indicatesE otherwisean error
messageis displayedas Err. When numberof capacitorsand oprating
sequenceare altered,the controllerrestarts again.
Oncetheconfiguration itemsareprogrammed holdin the4&5keys
togetherfor 3 seconds tocome back tonormal operating mode.
8. TECHINICAL SPECIFICATION
Type : ICD MAKE MICROCONTROLLER
BASED POWER FACTOR CONTROLLER
Model : PFC 9055
Voltage Circuit
Rated voltage : 415 V AC 3 phase R, Y & B phase for LT
110 VAC 3 phase R, Y & B phase for HT
Tolerance : -20% to 10%
Frequency : 40.00 to 60.00 Hz
Current Circuit
Rated current : 1A/5A 3phase, R,Y & B
Burden : Less than 0.5VA
Isolation :available through CT
Power Factor Measurement
1) Un- balanced load : From a 3phase voltage & 3 phase current
PF is computed
2) Balanced load : Using line to line voltage and current, PF is
computed
Indicating accuracy (PF) : ±1% of reading + 2 least digit
Display parameter : Average P.F, Total kVAr, kVar required to
reach target P.F, CT NIL & Alarm status

18
IndicatingResolution : 0.01PF
Lead&lagindication : Available - shown on display
Reversepolarityindication : Shown on the display to correct
voltage and current polarity
ControlPFsetting : 0.80Lag to0.95 Lead
OutputRelays : 4/6/8/12 steps
CapacitorConnectiondelay : 5 - 240 seconds (adjustable)
Capacitorreconnectiondelay : 5 - 240 seconds (adjustable)
ControlSensitivity : The step output added when required
kVAr in lag more than 70%of the
first capacitor bank, to attain preset
COS∅∅
∅∅
∅ and is removed when
required kVAr in lead more then 70%
of first capactitor bank
Keypadfor settingsandselections : Index, increment, shift & Enter keys
for P.F setttings, delay setting and
auto manual operation.
Protection : Available against
a) Over voltage 115% of the rated
voltage (Alr 3r/y/b)
b) Over current 110 % of the rated
current (Alr 4r/y/b)
c) Over compensation (Alr 02)
d) Under compensation (Alr 01)

19
Alaramrelayoutput : For the above protection
conditions aralmrelay isON
OutputRelay : NO contact for each step
Contactrating : 3Aat230VAC
RelayONindication : ByLEDlamps
Auto/manualselection : Available
Auto/manualindication : ByLED
Manualselectionofcap.banks : Through keypad
Ratinghumidity&temperature : 90% Rh at 25deg. &
55deg.celcius
Enclosuredimension : 144(H) x144(W)x 150(D)
mm
Table of contents
Other ICD Controllers manuals
Popular Controllers manuals by other brands
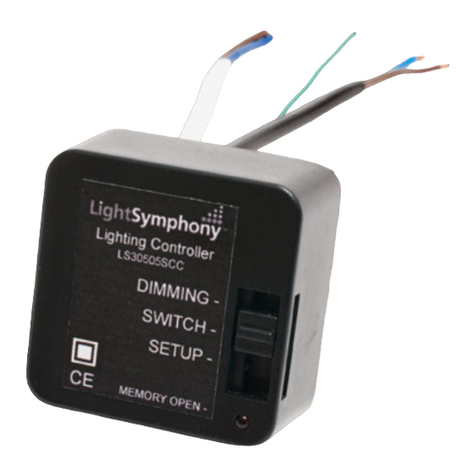
Light Symphony
Light Symphony LS30505SCC instructions

flakt woods
flakt woods STRA-24 Installation and commissioning manual
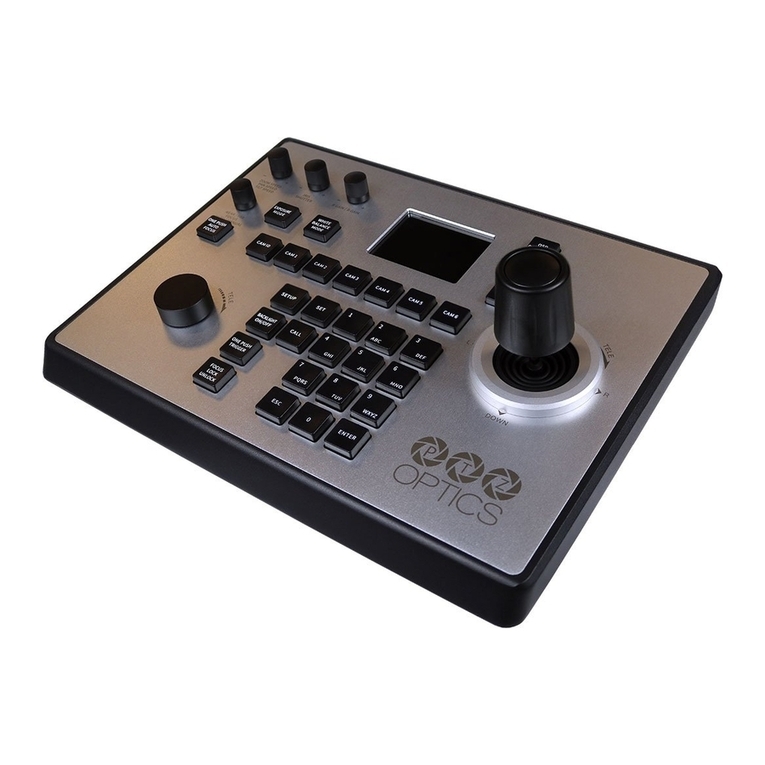
PTZOptics
PTZOptics PT-JOY-G4 user guide
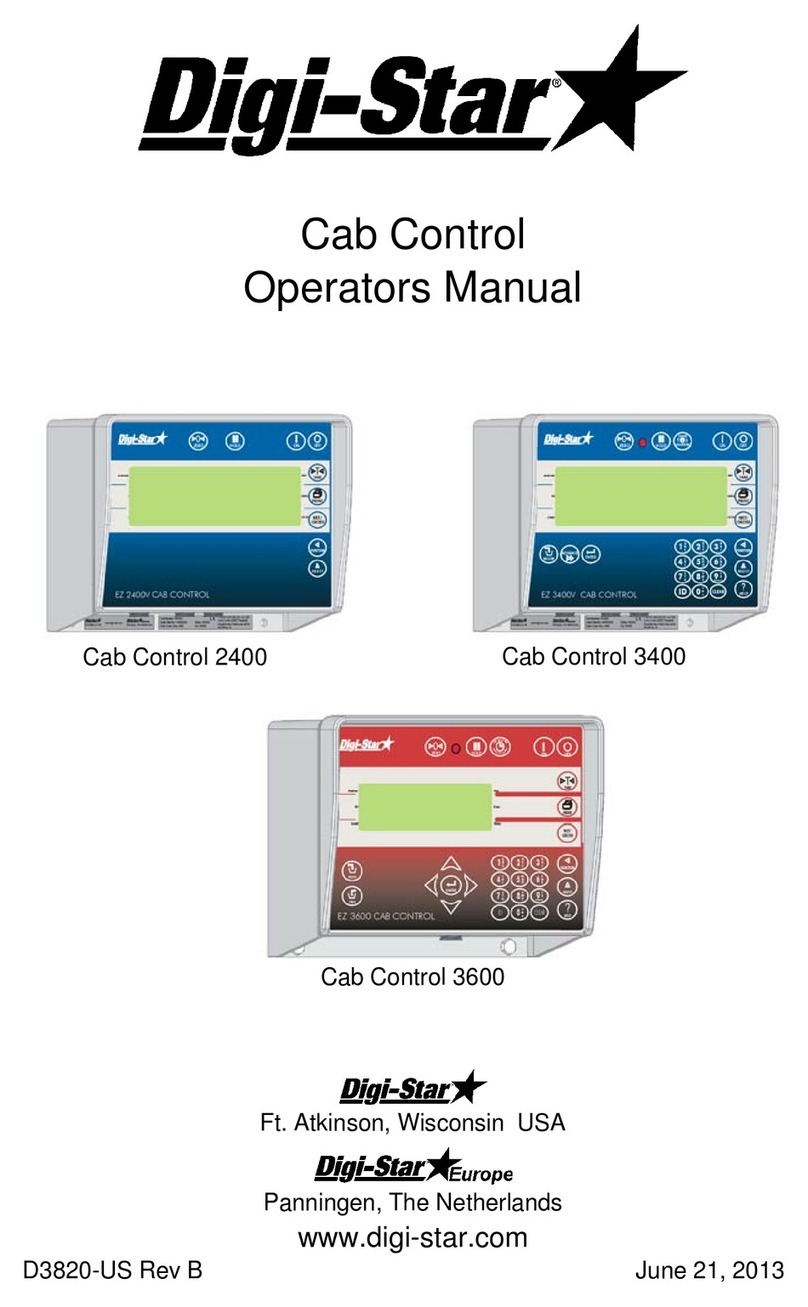
Digistar
Digistar Cab Control 2400 operating manual

Inter link
Inter link EC Series Installation and operation manual
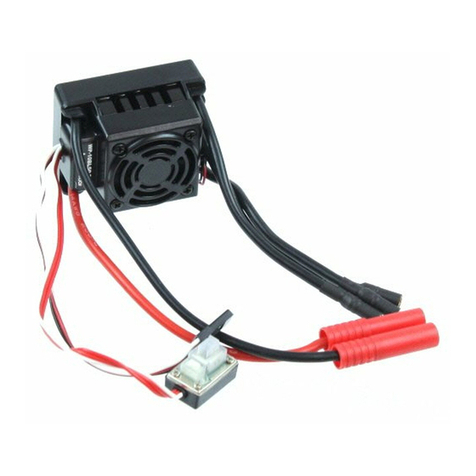
Hobby-Wing
Hobby-Wing WP-10BL50-RTR user manual