INIM Electronics Praesidia Instruction sheet

Configuration manual
1
EN 54-2
EN 54-4
EN 54-21
EN 12094-1 0832
0832-CPR-F1342
cert. N.991K
FIRE DETECTION AND EXTINGUISHANT SYSTEM
PRAESIDIA
Configuration manual

2Warranty
Fire detection and extinguishant system
Warranty
INIM Electronics s.r.l. (Seller, Our, Us) warrants the original purchaser that this product shall be free from defects in
materials and workmanship under normal use for a period of 24 months. As INIM Electronics s.r.l. does not install this
product directly, and due to the possibility that it may be used with other equipment not approved by Us; INIM
Electronics s.r.l. does not warrant against loss of quality, degradation of performance of this product or actual damage
that results from the use of products, parts or other replaceable items (such as consumables) that are neither made nor
recommended by INIM Electronics. Seller obligation and liability under this warranty is expressly limited to repairing or
replacing, at Seller's option, any product not meeting the specifications. In no event shall INIM Electronics s.r.l. be liable
to the purchaser or any other person for any loss or damage whether direct of indirect or consequential or incidental,
including without limitation, any damages for lost profits, stolen goods, or claims by any other party caused by defective
products or otherwise arising from the incorrect or otherwise improper installation or use of this product.
This warranty applies only to defects in parts and workmanship relating to normal use. It does not cover:
• damage arising from improper maintenance or negligence
• damage caused by fire, flood, wind or lightning
•vandalism
• fair wear and tear
IINIM Electronics s.r.l. shall, at its option, repair or replace any defective products. Improper use, that is, use for purposes
other than those mentioned in this manual will void the warranty. Contact Our authorized dealer, or visit our website for
further information regarding this warranty.
Limited warranty
INIM Electronics s.r.l. shall not be liable to the purchaser or any other person for damage arising from improper storage,
handling or use of this product.
Installation of this Product must be carried out by qualified persons appointed by INIM Electronics. Installation of this
Product must be carried out in accordance with Our instructions in the product manual.
Copyright
The information contained in this document is the sole property of INIM Electronics s.r.l.
No part may be copied without written authorization from INIM Electronics s.r.l.
All rights reserved.
European directive compliance
This control panel has been designed and developed to the highest standards of quality and performance implemented
by INIM Electronics s.r.l.
This control panel must be installed in accordance with the instructions described in this manual and in compliance with
the laws in force.
All control panels from the PRAESIDIA series are EN54-2, EN54-4, EN54-21 and EN12094-1. compliant.
All control panels from the PRAESIDIA series, and all accessory items and special functions have LPCB certification,
unless otherwise stated.
Declarations of performance, declarations of compliance and certificates relating to the products mentioned in this
manual can be downloaded from the following website:
www.inim.biz/certifications

Configuration manual
Table of contents 3
Table of contents
Warranty.......................................................................................................................... 2
Limited warranty........................................................................................................... 2
Copyright........................................................................................................................ 2
European directive compliance ............................................................................... 2
Table of contents ......................................................................................................... 3
General information .................................................................................................... 5
1.1 Details of Manufacturer ..................................................................................................................5
1.2 Supplied Documentation ...............................................................................................................5
1.3 About this manual ............................................................................................................................5
1.4 Description of the configuration and programming procedures .......................................6
Configuration ................................................................................................................ 7
2.1 Access to programming.................................................................................................................8
2.2 Setting the IP network address.....................................................................................................8
2.3 Accessing the configuration menu .............................................................................................8
2.4 Addressing IFM and FPM modules ..............................................................................................9
2.5 Setting the Hornet+ network address (IFMNET) ....................................................................10
2.6 Addressing the repeaters..............................................................................................................10
2.7 Enrolling loop devices (IFM2L).................................................................................................... 11
2.8 Acquiring the configuration.........................................................................................................13
2.9 Signal check and fault search .....................................................................................................13
2.10 Reset Factory data .........................................................................................................................13
2.11 Setting the date and time.............................................................................................................13
Commissioning........................................................................................................... 14
3.1 Testing the Control panel ............................................................................................................14
3.2 Testing to detectors and manual activations..........................................................................15
3.3 Testing signalling and activations ..............................................................................................15
3.4 Testing the extinguishment system...........................................................................................15
Maintenance................................................................................................................ 16
4.1 Testing the control panel.............................................................................................................16
4.2 Testing the detectors ....................................................................................................................16
4.3 Manual activation test ...................................................................................................................16
4.4 Testing signalling and activations ..............................................................................................16

4Table of contents
Fire detection and extinguishant system

Configuration manual
General information 5
Chapter 1
General information
1.1 Details of Manufacturer
Manufacturer: INIM ELECTRONICS s.r.l
Production plant: Via Fosso Antico snc - Centobuchi
63076, Monteprandone (AP) - Italy
Tel.: +39 0735 705007
Fax: +39 0735 704912
E-mail: [email protected]
Web: www.inim.biz
The persons authorized by the manufacturer to repair or replace the parts of this system have authorization to work on
INIM Electronics brand devices only.
1.2 Supplied Documentation
Praesidia User's Manual: contains the identification of the parts on the front plate and the end-user operating
instructions for use.
Praesidia216 Istallation Manual: contains the technical specifications of the Praesidia216 and the mounting, installation
and wiring instructions.
Presidia Installation Manual: contains the technical specifications of the system components, the description of the
system applications and use, instructions for the installation of the system components with wiring instructions complete
with wiring diagrams for the various modules. contains the instructions for system commissioning.
Manual for system configuration, commissioning and maintenance: contains the instructions for system
commissioning and the operations to be carried out during commissioning, maintenance and troubleshooting sessions.
Manual for system programming: contains the control panel configuration guide and a detailed description of the
various options contained in the programming software.
Installation manual for IFM modules: contains instructions for installation and the wiring diagrams for the various
internal modules (IFM2L, IFMNET, IFM4R, IFM4IO, IFMDIAL, IFM16IO, IFMLAN, IFMEXT)
Installation manual for FPM modules: contains instructions for installation and the wiring diagrams for the various
internal modules (FPMCPU, FPMLED, FPMLEDPRN, FPMEXT, FPMNUL)
Instructions for the installation of accessory components: contains instructions for mounting accessory components
(PRCAB, PRREP, PRCABSP, PRCABRK)
Guide to Networking: contains instructions for the connection of control panels in a Hornet network or via IP, with the
description of the system limits and responsibilities relating to network use.
Guide for MODBUS usage: register map and MODBUS RTU and IP specifications.
The manuals which are not normally supplied with the apparatus can be ordered using the codes found in Appendix -
Order Codes, or downloaded from www.inim.biz.
1.3 About this manual
Manual code: DCMCINE0PRAESIDIA
Version: 100
This manual describes the procedures for the configuration, commissioning and maintenance of the Praesidia fire-
detection system.

6General information
Fire detection and extinguishant system
1.3.1 Terminology
Control panel, System, Device: The main supervisory unit or any constituent part of the fire detection system.
Left, Right, Behind, Above, Below: Directions as seen by the operator when directly in front of the mounted device.
Qualified personnel: Persons whose training, expertise and knowledge of the products and laws regarding security
systems, are able to create, in accordance with the requirements of the purchaser, the most suitable solution for the
protected premises.
Select: Click on a specific item on the interface (drop-down menu, options box, graphic object, etc.).
Press: Push a button/key or tap on a video button on a touchscreen or display.
1.3.2 Graphic conventions
Following are the graphic conventions used in this manual.
Note: The notes contain important information relating to the text.
Attention:
The “Attention” prompts indicate that total or partial disregard of the procedure could damage the
device or its peripherals.
1.4 Description of the configuration and programming procedures
Following is a flow chart which summarizes the operations to be carried out during the installation and commissioning
phases of the Praesidia system and indications regarding the manuals to refer to for each operation.
1. Installation and cabling (refer to the Installation Manual)
2. Initializing (refer to the Installation Manual)
3. Configuration from the front plate (operations described in this manual)
4. Troubleshooting (operations described in this manual)
5. Connection to a PC and reading (refer to the Programming Manual)
6. Configuring the parameters (editing data, refer to the Programming Manual)
7. Writing data on the control panel and test (refer to the Programming Manual)
8. Commissioning (operations described in this manual)
9. System handover
10. Maintenance (operations described in this manual)
Conventions Example Description
Text in Italics
Refer to paragraph
1.3.2 Graphic
conventions
Directs you to the title of a chapter, section,
paragraph, table or figure in this manual or
other published reference.
<text> <AccountCode> Editable field
[Uppercase letter] or
[number] [A] or [1] Reference relating to a part of the system
or video object.

Configuration manual
Configuration 7
Chapter 2
Configuration
Once the installation and cabling procedures have been completed (refer to the Installation Manual of the Praesidia
system) the system is ready for the initializing phase.
On first startup it will be necessary to select the system language (see paragraph 2.10).
The control panel screen will be as follows:
In this condition the control panel has no acquired configuration, all the modules connected to the CAN drive bar or
front plate have the same address and are not included in the configuration.
The configuration status icon on the status bar indicates a fault condition, due to the fact that modules have been
detected but are not present in the configuration saved in the memory.
In order to configure the Praesidia control panel it is necessary to work through the following procedure:
1. Access programming (paragraph 2.1)
2. Set the IP network address (paragraph 2.2)
3. Access the configuration menu (paragraph 2.3)
4. Assign addresses to the system modules (paragraph 2.4)
5. Enroll loop devices on IFM2L modules and respective troubleshooting procedure (paragraph 2.7)
6. Set the defined configuration (paragraph 2.8)
7. Check eventual signalling and search for faults (paragraph 2.9)
8. Set the date and time (paragraph 2.11)
Note: Once the configuration operations have been completed correctly, the control panel will be ready to
operate.
The control panel is configured to consider each input point (detector, module, terminal) as a fire-alarm
point. Therefore, in the event of a fire alarm it will activate all the outputs available on its loops or
terminals.
At this point it is necessary to proceed with eventual changes to the configuration data for the
distribution of points in zones, edit descriptions of the various system elements, define specific
activation sequences, etc.
Refer to the Programming manual.
[A]
Buttons to access the
events logs, system
status and
programming.
[B]
Status bar (always
present) shows
essential information
regarding the system.
[C]
Configuration status
icon (system
configuration and
faults)
/RJ
6\VWHPVWDWXV
3URJUDPPLQJ
$FFHVVOHYHO
B
A
C

8Configuration
Fire detection and extinguishant system
2.1 Access to programming
In order to access the programming session of the Praesidia control
panel, it is necessary to work through the following procedure:
1. Insert the programming jumper on the back of the FPMCPU module
(see opposite, [D]).
2. Tap on the Programming button on the screen (see above, [A]).
3. A keypad will appear (see opposite, [E]) for the entry of a code with
installation privileges.
Note: The default access code to level 3 is “00004”.
4. The accessed programming menu will provide the following options:
-Configuration
-Network
- Factory data
2.2 Setting the IP network address
If an Ethernet network connection is used, it will be necessary to set up the IP address and parameters of the network.
This operation must be done for anyone of the following devices:
• the Praesidia control panel, via the main FPMCPU module
• the backup FPMCPU module, via the FPMCPU module itself
• the FPMCPU repeater module, when connected to an Ethernet network, via the FPMCPU module itself
In order to set the network parameters, it is first necessary to access the
programming phase of the control panel (paragraph 2.1) and then tap on the
Network button which appears on the screen.
The network parameters template will be shown [F].
Beside these there is the Backup panel option [G]. If enabled, the FPMCPU
module you are using will be set as control panel backup CPU unit. In this
case, the network parameters must be the same as the parameters set for
the main FPMCPU module.
Once set, it will be necessary to tap on the Ok button and save the data.
Once the module is set as backup CPU unit, the will show the template you
see beside [H].
2.3 Accessing the configuration menu
To access the configuration menu it is necessary to first access the programming phase of the control panel (paragraph
2.1) and then tap on the Configure button which appears on the screen.
Alternatively, it is possible to tap directly on the configuration status icon (see above, [C]).
Entry of a valid access code is necessary In both cases.
Once the configuration menu has been accessed, the control panel screen will provide a layout of the control panel and
its parts.
D
$ %
& '
( )
& 2.
E
1HWZRUN ,3
%DFNXSSDQHO
1HWPDVN
*DWHZD\
(VF3RUW
2N
$FFHVV
OHYHO
G
F
,QEDFNXS
H

Configuration manual
Configuration 9
Selection of one of the cabinets from the control panel layout ([E]) will show it both on the left ([A]), where the installed
IFM modules with their addresses are shown, and on the right ([F]), where the installed FPM external modules are shown.
From this section you can access the configuration phase of each module by tapping on the icon which represents it.
2.4 Addressing IFM and FPM modules
In order for the control panel to identify each module individually, it is
necessary to assign an address to each one. It is possible to assign the same
address to modules of different types, however, modules of the same type
must have different addresses.
To assign an address to a module, it is necessary to tap on the module
shown in the section it belongs to (internal IFM modules on the left [A]; FPM
front-plate modules on the right [F]).
A window will open ([H]), select the desired address in the programming
field, then tap on Set.
Note: Addresses which exceed the maximum number of modules supported by the control panel will not be
considered valid.
Following is a table containing the addresses allowed for each type:
[A] Internal layout of the
selected cabinet
[B] Internal module
detected
[C] Position empty
[D] Address of detected
module
[E] Layout of the entire
control panel
[F] Layout of the selected
cabinet
[G]
Buttons to carry out
setting changes or to
exit without saving
FPM Module Maximum
number
Address
IFM Module Maximum
number
Address
from to from to
FPMLED 7 1 7 IFM24160 4 1 4
FPMLEDPRN 1 / IFM2L 8 1 8
FPMEXT 5 1 5 IFM4R 16 1 16
IFM4IO 16 1 16
IFMDIAL 1 /
IFM16IO 4 1 4
IFMNET 1 /
IFMLAN 1 /
IFMEXT 24 1 24
6HW
(VF
$FFHVVOHYHO
B
A
C
D
E
F
G
C
C
C
C
B
B
D
D
0RGXOH[[[
$GGUHVV
(VF 6HW
H

10 Configuration
Fire detection and extinguishant system
Due to the fact that each FPMEXT front plate module is associated automatically with 5 internal IFMEXT modules at
precise addresses, the FPMEXT modules must have an address which respects the IFMEXT - FPMEXT module association
table which follows:
On returning to the control-panel configuration section, the assigned address ([D]) will be shown at the side of the
previously selected internal module.
2.5 Setting the Hornet+ network address (IFMNET)
If the installation has control panels connected in a Hornet+ network, it will be necessary to assign the network address
to each control panel.
Select the IFMNET module in the section on the left containing the internal layout of the cabinet ([A]). In the section
which appears, enter the network address and the bit rate.
Note: Each control panel in the same Hornet+ network must be set with the same bit rate and univocal
address.
2.6 Addressing the repeaters
The procedure to configure the FPMCPU modules as repeaters depends on the type of connection between the
modules and the control panel.
Connection via Ethernet network
The Ethernet connection needs network parameters setting. The procedure must be done via the display of the module
itself, following the indications described in the paragraph 2.2 Setting the IP network address.
Connection via RS485 BUS
The BUS connection needs the addressing of any repeater in configuration,
in order for the control panel to identify each module individually.
To assign an address to a repeater, it is necessary to enter the configuration
procedure starting from the display of the module itself, as described in the
paragraph 2.3.
A window will open, select the desired address in the programming field,
then tap on Set. The available addresses are from 1 to 14.
Attention:
The “0” address is reserved to the main FPMCPU module.
Do not use.
Addressing the Extinguishment module
IFMEXT FPMEXT IFMEXT FPMEXT IFMEXT FPMEXT
11 113 215
21 123 225
31 133 235
41 143 245
51 153
62 164
72 174
82 184
92 194
10 2 20 4
$GGUHVV
(VF 6HW

Configuration manual
Configuration 11
2.7 Enrolling loop devices (IFM2L)
The operations required for the configuration of the IFM2L network modules involve the configuration of the devices
connected to the loops.
The selection of the module from the internal layout section of the cabinet (paragraph 2.1 Access to programming,[A])
will access the configuration section which, in addition to providing the change address button (at the top) also provides
two identical sections for each of the two loops (connected to the Loop-A and Loop-B terminals). The present
document describes the operations necessary for the configuration of a single loop, however, it is implicit that the
operations be repeated for each of the two loop.
[A] Button to access the section for IFM2L module address assignment (paragraph 2.4 Addressing IFM
and FPM modules).
[B] Sections containing the configuration menu of individual loops
Section on the left for the loop connected to the Loop-A terminals, on the right for the Loop-B terminals.
[C] Button to access the section for loop diagnosis.
8SGDWH (VF
$FFHVV
OHYHO
K
/RRS/RRS
/RRS27HUPLQDO2.
/RRS7HUPLQDO2.
/RRSFRQVXPSWLRQP$
/223&/26('
*HQHULF
'HWHFWRUV
,10RGXOHV
2870RGXOHV
,12870RGXOHV
6RXQGHUV
&DOOSRLQWV
/RRSUHVHW 6FDQ 6KRZOD\RXW (VF
$FFHVV
OHYHO
/RRSPRGXOH &KDQJHDGGUHVV
/RRS /RRS
'LDJQRVWLFV 'LDJQRVWLFV
3DUDPHWHUV 3DUDPHWHUV
$XWRFRQILJXUH $XWRFRQILJXUH
'LVDEOH
$FFHVV
OHYHO
A
B
C
D
B
E
FG
IH J
J
C
D
E
C
$FTXLUH
5HDGGUHVV
8SGDWH
$GG5HSODFH
(VF
E
L
M
N
O
3URFHGXUHLQSURJUHVV
3URFHGXUHFRPSOHWHG
)RXQG
*HQHULF
'HWHFWRUV
,1PRGXOHV
287PRGXOHV
,1287PRGXOHV
'HWHFWRUV
&DOOSRLQWV 'LDJQRVWLFV
(VF
$FFHVV
OHYHO
)RXQG
1 61 7\SH 'HVFULSWLRQ 61 7\S H
((' 2SWGHW 2SWGHW ((' 2SWGHW
((( 2SWGHW 2SWGHW ((( 2SWGHW
(($% ,10RG ,QSXWPRGXOH (($% 2SWGHW
&&$& &DOOSRLQW %XWWRQ
(&( 2SWGHW 2SWGHW (&( 2SWGHW
(() 2SWGHW 2SWGHW (() 2SWGHW
(VF
(&& 2SWGHW 2SWGHW (&& 2SWGHW
()) ,10RG
2N
(& ,10RG ,QSXWPRGXOH (& ,10RG
$FFHVV
OHYHO
'HOHWH
1 61 7\SH 'HVFULSWLRQ
((' 2SWGHW 2SWGHW
$GG&KDQJH
((( 2SWGHW 2SWGHW
(($% ,10RG ,QSXWPRGXOH
3URJUDP
&&$& &DOOSRLQW %XWWRQ
(&( 2SWGHW 2SWGHW
(() 2SWGHW 2SWGHW
(&& 2SWGHW 2SWGHW
(VF
()) ,10RG ,QSXWPRGXOH
$FFHVV
OHYHO
O
L
M
N
C
&KDQJHDGGUHVV
'LDJQRVWLFV

12 Configuration
Fire detection and extinguishant system
[D]
Button to access the section for the selection of the type of devices installed on the loop.
It provides a check box for option selection “4 wires” (if the cabling has been completed as a ring
circuit, as required by the fire control standards).
Tap on Ok to confirm and exit.
[E] Button to access the automatic loop-configuration procedure.
[F]
Section which provides data regarding the electrical status of the loop circuit:
-Loop status: indicates whether the loop is a closed ring circuit or open
-Loop O Terminal: indicates eventual short-circuits or anomalies immediately on the “OUT” terminals
-Loop I Terminal: indicates eventual short-circuits or anomalies immediately on the “IN” terminals
-Loop Consumption: indicates the voltage draw of the loop
-Cable resistance: indicates the cable resistance value
[G] Section which provides the number and type of devices currently in the configuration.
[H]
Button to rearm the loop and reassess the status.
In the event of a “Loop open” fault, it will be necessary to tap on this button in order to check
whether or not the interruption has been cleared.
[I]
Button to start a check on an already enrolled loop.
The procedure verifies whether there are any connected devices which are not in the configuration,
if devices have been lost or if there are any other anomalies.
The result of the scan can be viewed in the section on the right ([G]).
[J]
Button which passes to the layout of the devices in the configuration of the enrolled loop.
The layout shows all the devices which are connected to the loop and how they are connected to
one another. Any devices in alarm or fault status will be outlined in red or yellow.
The selection of a device will access its management page (refer to the Device management section
in the Installation manual).
[K] Button to refresh the screen by updating the alarm and fault indications of the devices shown
(restored fault events will not be shown).
[L]
Button to perform a scan which will search the loop for devices and their serial numbers and place
those found in the configuration.
A report of the devices will be shown when the scan terminates. The “Diagnostics” button will allow
you to pass to the technical report, as shown in the previously ([C]).
For loops operating with Inim or Argus protocol, it is possible to use this procedure only after
completion of an automatic or manual addressing procedure by means of a programmer
(EDRV1000 for Inim loops and VPU100 for Argus).
[M]
Button to perform a scan which will search the loop for devices and their serial numbers and assign
automatically an address to each of those found in order of their connection to the loop. This
operation may take some minutes depending on the size and composition of the loop.
A report of the devices will be shown when the scan terminates. The “Diagnostics” button will allow
you to pass to the technical report, as shown in the previously ([C]).
For Apollo devices, where the address is assigned by means of the microswitch on the device, these
operations coincide with those previously described (“Acquire”).
[N]
Button to start the procedure which is to be performed after changes have been carried out on a
previously configured loop (add, remove or replace devices).
The control panel will provide a table with the previously acquired configuration in the columns on
the left, and the newly detected configuration in the columns on the right. Positions in which
changes have not been detected will be outlined in green. Changes will be indicated in white. This
operation may take some minutes depending on the size and composition of the loop.
The OK button will allow you to accept the new configuration which will become the configuration
saved to the memory.
Procedure available for loops with Inim protocol only.
3DUDPHWHUV
$XWRFRQILJXUH
/RRSUHVHW
6FDQ
6KRZOD\RXW
8SGDWH
$FTXLUH
5HDGGUHVV
8SGDWH

Configuration manual
Configuration 13
2.8 Acquiring the configuration
Once the previously described operations have been completed, it will be necessary to save the defined configuration to
the control panel memory. This operation can be done via the configuration template, by means of the “Set” button
(paragraph 2.3 - [G]).
A progress bar will confirm data saving in course.
Once this operation has been completed and valid addresses have been assigned to all the devices, the
configuration status icon will turn green. Any successive changes to the hardware configuration (for example,
the loss of a module or addition of a new module) will turn the icon yellow to signal that the control panel
configuration is different to the one saved to the memory.
2.9 Signal check and fault search
Once the configuration setup has been completed, the control panel will check the status of the devices and input/
output terminals.
Eventual faults on these elements will be shown on the screen. In the event of faults or anomalies, it is necessary to find
and remove the cause. Once any problems have been solved the screen will return to the homepage (refer to the
Installation manual of the Praesidia system).
2.10 Reset Factory data
The Factory data button from the programming menu (paragraph 2.1)
deletes all the configuration data and resets the control panel to the
factory default settings.
As an alternative to using the Factory data button, it is possible to reset
the factory default settings by means of the buttons on the back of the
FPMCPU front-plate module. Press and hold the “Factory data” button [A]
and press and release the “Reset” button [B].
After a request of confirmation, a template will be shown where you can
choose the control panel language.
A progress bar will confirm factory data resetting in course.
2.11 Setting the date and time
When setting this parameter, it is necessary to tap on the respective field in the bottom right-hand corner of the
template, enter an access code with either supervisor or installer capabilities then, by means of the scroll keys, navigate
through the programming fields and set the desired date and time.
[O]
Button to access a section which will allow you to select a specific address and change, remove or
add a device manually.
At the side of the loop device list are a series of buttons which will allow you to work on the device
selected by a screen tap gesture, as follows:
-Delete: button to delete the selected device.
-Add/Change: button to change or add a device manually.
After completing the connection of a new device or replacing an old device, it is necessary to
select the address involved then tap on the Add/Replace button.
When using Inim protocol, it is necessary to enter the serial number of the new device.
-Program: button to access a section where it is possible to change some of the device
parameters.
Once this operation has been completed the control panel will communicate with the new device.
The appearance of the type of device detected is the confirmation of its acquisition.
Arrow buttons
Button to step back
$GG&KDQJH
(VF
B
A

14 Commissioning
Fire detection and extinguishant system
Chapter 3
Commissioning
The commissioning phase is a set of tests and verifications which are necessary to ensure the full efficiency and proper
functioning of the system as specified in the executive project. This phase is essential and must be performed in a
scrupulously in accordance the regulatory requirements of the country where the system is installed and in full respect of
the recommendations herein.
Ensure the test and verification procedures are performed only after securing the system and after having verified that
any device activations controlled by the system will not cause any conditions of danger, and that all the building
occupants who can be reached by the audible and visual signalling have been preventively informed.
Ensure that the person who is responsible for the security of the building where the tests and inspections are being
carried out has taken countermeasures to avoid any situations of panic or distress for the building occupants.
3.1 Testing the Control panel
It is necessary to check the functionality status of the front plate by first checking the information supplied on the screen
and LEDs and then by inspecting the efficiency of the command devices (user-interface buttons, access keys, etc.):
• Check the functionality status of the screen and ensure that the information provided is clear.
• Ensure that the descriptions of the various zones, points and system elements entered during the data-entry phase are
correct, and that the information provided on the screen clearly indicates any detectable conditions of danger.
• Check that there are no indications present of faults, alarms or anomalies of any type whatsoever. In the event of such
indications, proceed with the removal of the causes of faults and anomalies.
• Check the status the functionality of the LEDs and buzzer. The front panel provides a button for the simultaneous
activation of all the LEDs and buzzer thus allowing evaluation of their efficiency (refer to the description of the User
Interface).
• Check the efficiency of the front-plate buttons and keys.
• Check the status of the power-supply sources (mains and batteries) and the control panel current draw. The power-
supply parameters can be checked by accessing the configuration menu (refer to paragraph 2.3 Accessing the
configuration menu) and selecting the configured IFM24160 modules.
The sections show the voltages, currents and temperatures of the various elements:
[A] Button for addressing the
module
[B] Section containing a list of
current faults
[C] Voltage and output current
of the IFM24160 module
[D]
Battery parameters (internal
resistance, voltage, status
and current)
[E] Internal temperature and
battery charge voltages
/RZEDWWHU\YROWDJH
0DLQVIDXOW
3680RGXOH
&KDQJHDGGUHVV
([LW
9
$
P2KP
9
&
&KDUJLQJ
$
&
&
9 (VF
$FFHVV
OHYHO
B
A
C
E
D

Configuration manual
Commissioning 15
3.2 Testing to detectors and manual activations
All the installed detectors must be tested during the commissioning phase. It is necessary to check the capacity of each
detector to react to a simulated condition of fire, and to check the precision of the signals transmitted to the control
panel in response to its activation (description of the point and zone).
For this purpose it is possible to use the Test button of the control panel ([A])
on the “Zone status” template, accessible via the “System status” menu on
the homepage.
By tapping this button it is possible to place one or more zones in test status.
The activation of a detector which belongs to a zone in test status will not
generate any alarm signalling or activate the outputs or signalling devices.
However, the control panel will activate the signalling LEDs on the detectors
and will perform automatic reset after a few seconds without any need of
further intervention by the operator on the control panel.
The activation of a point which belongs to a zone in test status will be recorded in the events log. Therefore, on
completion of the test on all the zone devices, the operator can check the congruence of the various indications by
means of the log.
The activation of all the manual call points (alarm buttons) must be tested in the same way as described for the detectors.
3.3 Testing signalling and activations
The functionality and efficiency of all the signalling devices must be checked thoroughly.
It is possible to test such devices by activating the relative LEDs and outputs
manually at the control panel via the respective management page ([B]).
To reach this page you must access the “Points” section via the “System
status” menu on the homepage. Select the desired loop and point to be
tested from the lists shown then, by means of the relative View buttons go to
the respective management template where you will find the Turn On
output and Turn On LED buttons.
Note: Testing devices by means of manual activation does not test functionality and efficiency of the cause/
effect association which determines their activation (programming coherence of groups), therefore, it is
necessary to perform real functionality tests.
3.4 Testing the extinguishment system
Particular attention must be paid to the testing of eventual fire extinguishment systems.
Special attention must be paid to the functionality and safety of the extinguishing-agent release devices before
proceeding with the testing of all activation and stop-extinguishment procedures in accordance with the requirements of
the executive project.
=RQHVWDWXV
1 'HVFULSWLRQ 6WDWXV
=RQH 6WDQGE\
=RQH )DXOW
=RQH 6WDQGE\
=RQH 6WDQGE\
=RQH $ODUP
=RQH 6WDQGE\
'LVDEOH 7H V W (VF
$FFHVV
OHYHO
A
/RRSPRGXOH3RLQW6161616161
2SWLFDOWKHUPDOGHWHFWRU
=RQH
'HWHFWRUORVW
5HSODFH ,QIR
7XUQ2QRXWSXW 5HDOWLPH
7XUQ2Q/(' &DPHUD
'LVDEOHSRLQW 0DS
'LVDEOH]RQH (VF
$FFHVV
OHYHO
B

16 Maintenance
Fire detection and extinguishant system
Chapter 4
Maintenance
For correct and efficient management of the system it is necessary to carry out periodic maintenance in accordance
with the regulatory requirements of the country where the system is installed and in full respect of the recommendations
herein.
For the frequency of the maintenance operations it is necessary to adhere to the applicable regulations. However, the
manufacturer recommends that tests are performed on each point, component and element of the system at least once
a year.
4.1 Testing the control panel
Work through the steps for control-panel test procedure as described in the commissioning section (paragraph 3.1
Testing the Control panel).
Additionally, consult the events log and check for the presence of fault or alarm conditions which must be investigated.
4.2 Testing the detectors
As well as the tests which must be performed during the commissioning phase (paragraph 3.2 Testing to detectors and
manual activations), it is also necessary to check the contamination level in smoke detectors.
The management and configuration software provides a loop diagnostic function which allows you to gather the
contamination values of the various devices in such a way to decide when cleaning is necessary.
Refer to the Programming manual for details regarding the diagnostic function and the detector manual for the
instructions regarding cleaning operations.
4.3 Manual activation test
Work through the same tests as recommended in the commissioning section (paragraph 3.2 Testing to detectors and
manual activations).
4.4 Testing signalling and activations
Work through the same tests as indicated in the commissioning section (paragraph 3.3 Testing signalling and activations).

Configuration manual
Maintenance 17

18 Maintenance
Fire detection and extinguishant system
DCMCINE0PRAESIDIA-100-20160415

Configuration manual
19

20
Fire detection and extinguishant system
via Fosso Antico Loc. Centobuchi
63076 Monteprandone (AP) IT
Tel. +39 0735 705007
Fax +39 0735 70491
inim.biz
ISO 9001 Quality Management
certified by BSI with certificate number FM530352
Table of contents
Other INIM Electronics Security System manuals
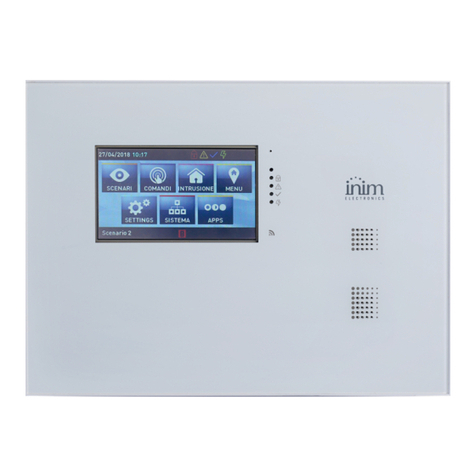
INIM Electronics
INIM Electronics Sol-P User manual
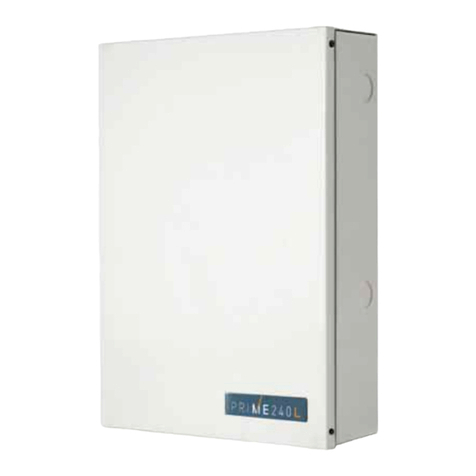
INIM Electronics
INIM Electronics Prime Owner's manual

INIM Electronics
INIM Electronics enea ES1050 User manual
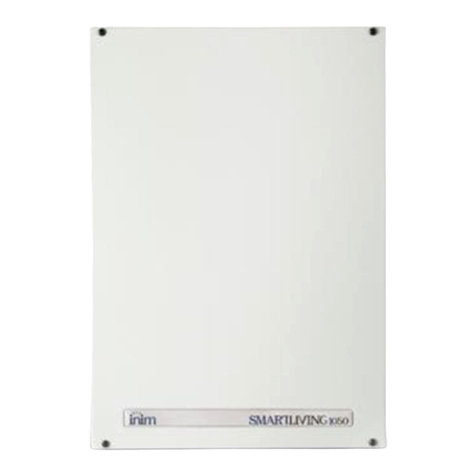
INIM Electronics
INIM Electronics SmartLiving 505 User manual
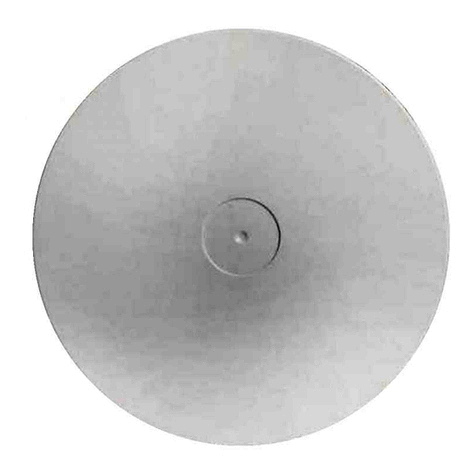
INIM Electronics
INIM Electronics IS1030 User manual

INIM Electronics
INIM Electronics SmartLiving 505 Assembly instructions