Interflex IF-4735 User manual



Copyright
The information contained in this document is accurate and reliable to the best of our
knowledge. Nevertheless, mistakes cannot be excluded. Interflex Datensysteme GmbH &
Co. KG assumes no responsibility for the information in this manual, which is subject to
change without prior notice.
Copyright © 2019
Version Date: April 9, 2019
Interflex Datensysteme GmbH
Allegion
Zettachring 16
D-70567 Stuttgart, Germany
Phone: +49 (0711) 1322 0
Internet e-mail: interflex.info@allegion.com
Website: http://www.interflex.de
Interflex operates as part of Allegion plc.
For more information on Allegion, please visit
www.allegion.com.


Contents i
Contents
1General Information 1
1.1 Scope of delivery..................................................................................................................1
1.2 Target group.........................................................................................................................1
1.3 Symbols used in this document...........................................................................................1
1.4 Intended use ........................................................................................................................1
1.5 General safety instructions ..................................................................................................2
1.6 All specifications are subject to change without notice........................................................2
1.7 List of abbreviations.............................................................................................................2
2System Overview 3
2.1 Cable lengths and cable types.............................................................................................3
2.2 Shielded cables....................................................................................................................3
2.3 Online/offline mode..............................................................................................................3
2.4 Encryption of data transfer...................................................................................................4
3Mounting the Device 5
4Connecting the Device 6
4.1 Risk of electric shock ...........................................................................................................6
4.2 Electrostatic discharge (ESD)..............................................................................................6
4.3 Voltage supply......................................................................................................................7
4.4 Power supply setting............................................................................................................8
4.5 Redundant power supply.....................................................................................................8
5Interfaces 9
5.1 Bus data cables with slave terminals...................................................................................9
5.2 Additional RS232 interface ..................................................................................................9
5.3 Connecting a barcode reader ............................................................................................10
5.4 Connecting an RS232 service device................................................................................10
6Configuring the Device 11
6.1 Switching on the Power Supply .........................................................................................11
6.2 SSH connection and login..................................................................................................11
6.3 How to apply the configuration...........................................................................................15
6.4 Preparing to update software.............................................................................................15
6.5 Updating software..............................................................................................................16
6.6 Performing device license upgrade....................................................................................17
7Maintenance and Service 17
8Technical Specifications 18
8.1 EU Declaration of Conformity ............................................................................................19
8.2 Open source program packages........................................................................................19

1
1 General Information
1.1 Scope of delivery
The following is included in the package:
▪Master terminal with ordered reading technology and options.
▪Accessory bag containing:
▪Screws
▪Dowels
▪Mortise lock
Please check the completeness and condition of the shipment upon receipt.
Report any damages caused during transport immediately.
1.2 Target group
This document is directed primarily to readers, who - based on their education, their training, or both -
are able to install these devices properly and put them into operation.
Only perform the actions described in this document if you belong to this target group.
1.3 Symbols used in this document
Warnings warn against hazards that may arise when using the devices described in this document. The
hazard levels can be identified by the signal word:
Indicates a hazard that may result in severe personal injury or even death if proper precautions are
not taken.
Indicates a hazard that may lead to actual damages if proper precautions are not taken.
1.4 Intended use
Master terminals are used for recording time and access data, controlling access, and monitoring locking
devices (optional).
The device is designed for fixed installation in dry rooms. Any other use is not in accordance with the
intended purpose and is therefore not permitted.
Modifications to the device are not permitted.

2 General Information
1.5 General safety instructions
For the safety of you and others, please observe the following safety instructions:
Danger to life due to electric shock
People can be seriously hurt or killed through physical contact with live
parts (e.g. 230 V~). Make sure that you cannot touch live lines during
installation. Disconnect devices from the mains power supply.
Please observe the accident prevention regulations and take all precautionary
measures to ensure the safe installation of the devices.
Danger to life through explosion
Do not use this device in environments exposed to explosion hazards!
1.6 All specifications are subject to change without notice
All information contained in this documentation is accurate at the time of printing. All specifications are
subject to change without notice. The product brand names and trademarks specified in this
documentation are protected by commercial and patent laws.
1.7 List of abbreviations
Designation
Description
ESD
Electrostatic discharge
IEEE
Institute of Electrical and Electronics Engineers
PoE
Power over Ethernet
RFID
Radio frequency identification
Switch
Network distributor
UL
Underwriters Laboratories

System Overview 3
2 System Overview
2.1 Cable lengths and cable types
Cable Function
Max. Length
Recommended Cable
Type
230 V AC voltage supply to power supply unit
(if not pre-installed)
-
NYM 3 1.5 mm²
Network cabling: RJ45 patch cable, preferably shield
braiding
25 m
As of cat. 5
Cable to floating status contacts, control cable
100 m
J-Y(St) Y 2 2 0.6 mm²
RS485 bus cable to parent or child devices
1200 m
J-Y(St) Y 2 2 0.6 mm²
RS485 branch cable to bus cable
100 m
J-Y(St) Y 2 2 0.6 mm²
▪Cable lengths: The specifications indicate the maximum permitted cable lengths that guarantee
reliable function.
▪Cable types: Install only data and control cables with cable shielding, e.g. cable type J-Y(St) Y.
▪Voltage losses in long cables may impair the function of the connected device. We recommend
connecting the "+5 V" and "GND” lines with two wires each if the cable lengths exceed 50 meters.
2.2 Shielded cables
To ensure malfunction-free operation, we recommend the use of shielded cables.
Operation is also possible with unshielded cables. In case of transmission problems, you will have to
examine the reasons in each individual case. If necessary, equip the corresponding device with shielded
cables.
2.3 Online/offline mode
Online mode
In this operating mode, data is continuously exchanged between the IF-4735 device and the parent host
system (e.g. the IF-60x0 system). In the process, the host system causes the status of the IF-4735 device
to be cyclically queried. The IF-4735 device acknowledges the query either by sending a “sign of life” or
status messages or booking data from the terminals.

4 System Overview
After receiving the data, the host system evaluates it and reacts depending on the data received. For
booking data, the IF-60x0 system sends back a positive or negative booking response, for example.
Depending on the booking response, access is either permitted or denied.
The IF-60x0 system can also actuate relays or trigger an alarm if certain events occur. All booking data
and events of the connected terminals are stored in the memory of the IF-4735 device.
Offline mode
If there is no transfer of data between the IF-4735 device and the parent host system (e.g. the IF-60x0
system), the device will automatically switch to offline mode. There, it records all bookings and events
and autonomously makes decisions based on configured conditions.
In the event of a positive decision, a booking response and/or a signal for activating an output relay, for
example, are transmitted to the booking location. If the decision is negative, the reason for the booking
rejection is transmitted.
All bookings and status changes recorded in offline mode are stored in the device, together with a special
remark. The IF-4735 device transmits this data to the parent host system once an online connection has
been established again.
2.4 Encryption of data transfer
Transmission, credential <-> reader/terminal
The transmission of data between the credential and the reader/terminal is subject to requirements which
are constantly changing. Interflex is always always up-to-date in supporting the current credential and
reader technologies.
Transmission, reader/terminal <-> controller
The data transmission between terminal and controller takes place via an RS485 two-wire line, which is
installed in the secured area. You can encrypt the data transmission, by using the terminal controllers of
the IF-4xxx series, the master terminals of the IF-5xxx series and the slave terminals of the IF-8xx series.
The controllers are equipped with up to 3 bus systems that can be used to connect several slave
terminals. Data encryption can be activated or deactivated for each connected slave terminal individually.
You can configure this setting when starting up the controller. Mixed operation of encrypted and
non-encrypted transmission on the same bus is possible.
For this purpose, the devices must be equipped with a minimum software version:
▪Controller: Version V7.13.05 or higher.
▪IF-8xx slave terminals: Version 7.ba or higher.
Transmission, controller <-> host system
You can activate and deactivate the encryption for this data link in the host system. You will find details in
the documentation of the host system.
See also
Setting interfaces, booking memory and encryption ..............................................................13

Mounting the Device 5
3 Mounting the Device
1
Housing back panel
2
Wall
1a
3 drilled holes for screw mounting
3
Installed cable (in-wall)
1b
Cutout for installed cables (in-wall)
4
Cable feed for surface-mounted installation
Installation Site
The device is designed for fixed installation in dry rooms. Operation in humid environments is not
permitted.
Maintain a distance of 30 cm to other devices with RFID readers.
Mounting
Use the screws and screw anchors included in delivery to mount the device.
Fasten the master terminal with 3 screws as shown in the figure.

6 Connecting the Device
4 Connecting the Device
4.1 Risk of electric shock
Danger to life due to electric shock
People can be seriously hurt or killed through physical contact with live
parts (e.g. 230 V~). Make sure that you cannot touch live lines during
installation. Disconnect devices from the mains power supply.
Please observe the accident prevention regulations and take all precautionary
measures to ensure the safe installation of the devices.
▪Connection to power supply voltage and initial operation may only be carried out by qualified persons
trained in electrical engineering.
▪The electrical installation, in which the device is to be operated, must comply with national standards.
To guarantee trouble-free operation, we recommend carrying out the electrical installation according
to the principles of a TN-S system, which means using separate neutral and grounding conductors.
▪Secure the power cable with a strain relief, if necessary.
▪The device must be connected via an all-pole separator to ensure that it can be disconnected
completely from the mains power supply, if required (service, maintenance).
▪The device must be equipped with an external fuse protection with a maximum nominal current of
16 A.
4.2 Electrostatic discharge (ESD)
Electrical components and modules can be damaged by only slight, hardly
noticeable electrostatic discharge (ESD) without this becoming immediately
obvious. ESD damages result in malfunctions and even failure of the product.
Therefore, make sure that effective protective measures against electrostatic
discharge are in place when working on the open device.
Protective measures
Therefore, it is best to carry out maintenance work in an ESD-protected environment:
▪ESD-compliant shoes, protective gloves and outerwear.
▪ESD-compliant work surfaces with conductive mats as surfaces (if possible).
▪ESD-compliant tools.
▪ESD-compliant personal protective grounding, e.g. wrist grounding strap.
▪Where this is not possible (e.g. product already installed), at least touch a grounded item in order to
conduct electrostatic charge away from your body.

Connecting the Device 7
4.3 Voltage supply
1
Screw terminal strip 1 (10-pin)
5
Optional: 12 V battery for emergency power
supply (order no.: 75-1735-0002)
2
Optional: 230 V AC power board
6
Power supply unit for DIN rail mounting or
pluggable power supply
3
Low-voltage cable
7
230 VAC
4
Power cable
8
250 mA slow-blow fuse
Power supply is possible with:
▪A power supply unit (mounting rail or pluggable power supply) 18 to 24 VAC/DC
▪A PoE device IEE 802.3 of power class 3 (up to 13 W).
▪230 V AC (optional). The device is equipped with a transformer and a power board (2) for connection
to 230 V AC.
The type of power supply is set by the position of the jumper.
To comply with the required EMC limit values, the device requires protective grounding.
Connect the PE conductor to the protective earth terminal.

8 Connecting the Device
4.4 Power supplysetting
The setting power supply via power supply unit (A) is preset by default.
Insert the jumper according to the type of power supply you have selected.
▪Power supply via power supply unit: Jumper on pin 1 and pin 2
▪Power supply via Ethernet (PoE): Jumper on pin 2 and pin 3
A
Power supply via power supply unit
2
Pin 2
B
Power supply via Ethernet (PoE)
3
Pin 3
1
Pin 1
Check the setting of the jumper, in order to counteract a redundant power
supply.
4.5 Redundant power supply
To provide a redundant power supply for the device, you need an 18 V DC; 1 A power supply unit (order
number: 41-10063). If power supply via Ethernet (PoE) fails, the device automatically switches to voltage
supply via power supply unit.
Set the jumper to power supply via Ethernet (PoE).

Interfaces 9
5 Interfaces
5.1 Bus data cables with slave terminals
1
Screw terminal strip 1
3
Stub line to RS485 data cable (max. length: 100 m)
2
RS485 data cable (max. length:
1200 m)
4
Slave terminal (up to 7 slave terminals)
Connect the RS485 data cables from the slave terminals to screw terminal strip 1.
5.2 Additional RS232 interface
Connect devices with an RS232 interface as follows. Observe the recommended line length of max.
15 m.
Once configured, the standard software supports communication with external devices.
A
RS232 interface (screw terminal strip 2)
The connection is set to 1,200 baud, 7 bits, even parity and no handshake.

10 Interfaces
5.3 Connecting a barcode reader
At the factory, the ribbon cable (A) is routed along the bottom of the device (B) and fastened to the
housing via a 9-pin socket. Thus, the barcode reader with its 9-pin plug can be plugged in directly on the
bottom of the housing.
5.4 Connecting an RS232 service device
Dialog devices with RS232 interfaces can be connected as shown in the figure below.
The following settings are required for an RS232 connection:
▪Baud rate: 115200
▪Data bits: 8 data bits, no parity, 1 stop bit
▪Flow control: None
1
Screw terminal strip 5
2
RS232 service cable
Connect the device using the RS232 service cable (order number: 75-4070-0001).

Configuring the Device 11
6 Configuring the Device
Once the connection has been established, the device must be configured. Configuration requires
extensive system knowledge and may be carried out only by authorized personnel.
6.1 Switching on the Power Supply
After the power supply has been switched on, the device executes the following functions:
▪The operating system is booted.
▪The applications are started.
▪The connected slave terminals are connected to each other.
The start-up procedure lasts up to 30 seconds. When the RUN LED lights up, a SSH connection is
possible.
6.2 SSH connection and login
Establish an SSH connection via the factory-set IP address. After the connection is established, you can
log in.
First, you will be asked to enter the system password you received from your Interflex system consultant.
Then, the system prompts you to change the password.
iftc-8D4E56 login: root
Password:
You are required to change your password immediately (root enforced)
Changing password for root.
(current) UNIX password:
New password:
Retype new password:
root@iftc-8D:4E:56:~
6.2.1 Creating a password
The following criteria must be met to create a new password:
▪The password has 8 digits and requires the following 3 security features:
▪Uppercase letters
▪Lowercase letters
▪Digits
▪If one of the security features is missing, the password is extended by 2 digits each. This means that
the password must have 8-12 digits, depending on the number of security features.
▪The password must not contain any mutated vowels or special characters.
▪The password must not contain any sequences (e.g. 111 or aaa).
▪Furthermore, the system password or the previous password must not be used.
▪If an incorrect entry is made four times in a row, a further entry is blocked for 25 seconds.

12 Configuring the Device
Recommendation:
Choose an encrypted password.
Please keep the new password in a safe place.
After you have created a new system password, you can access the controller commands.
6.2.2 Changing a password
Change the password with the command passwd.
Recommendation: Choose an encrypted password and keep it in a safe place.
root@IF-xxxx:~ passwd
New password:
Retype new password:
passwd: password updated successfully
Once you have changed the password, you have to log in again for it to take effect.
6.2.3 Configuring the Device
Once the connection is established, the device must be configured. Configuration requires extensive
system knowledge and may be carried out only by authorized personnel.
This document only describes the most important steps. Please refer to the system manual for detailed
information.
Configuring the device using "OC Task"
The software for configuring the device and displaying device functions is called OC Task and is available
on the device. OC Task contains a number of commands that are used for administrative purposes.
To access OC task, the device must be connected to a computer. This can take place:
▪via network (TCP/IP) using SSH connection. Use the factory-set IP address (see label on housing) or
the IP address 172.18.70.52.
▪via the RS232 service interface with a terminal emulation program that supports SSH.
Access to the console and Linux commands is granted after you login with root and enter the password.
The root@ prompt signals readiness to receive commands and data.
The following input syntax must be observed:
▪Commands are written in lowercase letters.
▪Options are separated from the command by a blank and the minus sign.
▪An overview of the command options can be retrieved with -?.
▪Press the "ENTER" key to confirm command lines and data.
▪To save new data, you must confirm the prompt Write to EEPROM (y/n)? with y.
▪Modified data only becomes effective after a "Restart", e.g. after a cold boot.
▪SSH connections must be properly terminated after configuration.

Configuring the Device 13
6.2.4 Checking and setting network parameters
The command netpar shows you the current network parameters, which you can then change. The
following options are available:
login as: root
root@IF-xxxx:~ netpar
displays or changes network parameters
usage:
netpar -i show network settings
netpar -x change IP addr., gateway, netmask and port no
netpar -s reboot system
netpar -y enable DHCP
netpar -y print this screen
6.2.5 Setting network parameters (netpar -x)
With the netpar-x command, you can retrieve information on the current network parameters (e.g. the IP
address and port), which you can then change.
root@IF-xxxx:~ netpar -x
IP address [172.18.20.110] :
Gateway [172.18.70.1] :
Netmask [255.255.0.0] :
Port number [2001] :
hostname [IF-xxxx] :
Confirm other settings (e.g. Gateway, Netmask, etc.) that are not to be changed by pressing the "Enter"
key.
Please note: A connection to the controller (SSH) is terminated immediately after the network
parameters have been changed.
6.2.6 Setting interfaces, booking memory and encryption
With the command oc -h, you can:
▪Change interface settings
▪Encrypt data transmission
▪Adjust the size of the booking memory
root@IF-xxxx:~ oc -h
base address : 1
No. of term. bus 1 : 6
bus 2 : 4
bus 3 : 6
IF-LT64 at bus 2 : 0
Protocol bus 1 : 0
bus 2 : 0
bus 3 : 0
KryptAddrbus 1 : 0
bus 2 : 0
bus 3 : 0
Baudrate host : 3
Baudrate bus 1 : 2
bus 2 : 2
bus 3 : 2
Number of bookings (1000) : 50
Notice: Baudrate terminalbus: 2 (9600, 8, ep), 3 (19200 , 8, ep) appropr. terminals only
Your license allows 8 terminals as maximum

14 Configuring the Device
Explanation for devices of the IF-1xxx series
Term
Description
host baud rate
▪1 = 1,200
▪2 = 9,600
▪3 = 19,200
Token ring baud rate
Baud rate, TCP/IP network:
▪0 = 4 MB
▪1 = 16 MB
Baud rate
terminal bus 'n'
▪2 = 9,600
▪3 = 19,200)
▪
See also
Performing device license upgrade ........................................................................................16
6.2.7 Listing slave terminals
With the cfg command, you can list the configuration data of slave terminals.
Terminal configuration IF-xxxx V7.xx
--------------------------------------------------------------------
No B A HA TNo type HWU SWU display keys read.1 read.2 In/Out I/O
-- - - -- --- ---- --- --- ------- ---- ------ ------ ------ ----
1 1 A 1 0 IFx 2.04 6.b OL/2x20 ..NF PSCR/P ...... ...... --
2 1 B 2 0
............
16 3 F 15 0 IFx 2.04 6.b ../.... ..NF PSCR/P ...... ...... -+
Column
List of
B
3 bus interfaces with the terminal distribution, e.g. the factory-configured default
distribution of 6, 4 and 6 slave terminals
TNo
Host administration number. The numbers are configured in the time recording/access
control program and are only displayed after the data has been loaded.
type
Device type, e.g. the slave terminal IFxx
HWU
Hardware status, e.g. 2.04 for MPU hardware HCS12
SWU
Software status, e.g. version 6.b
read.1
First reader type, e.g. PSCR/P for MIFARE readers
read.2
Second reader type, e.g. FIP for slave terminals with fingerprint
In/Out
Configured RS232 interface, e.g. >RKASS< for a cashbox
This manual suits for next models
1
Table of contents
Other Interflex Touch Terminal manuals
Popular Touch Terminal manuals by other brands
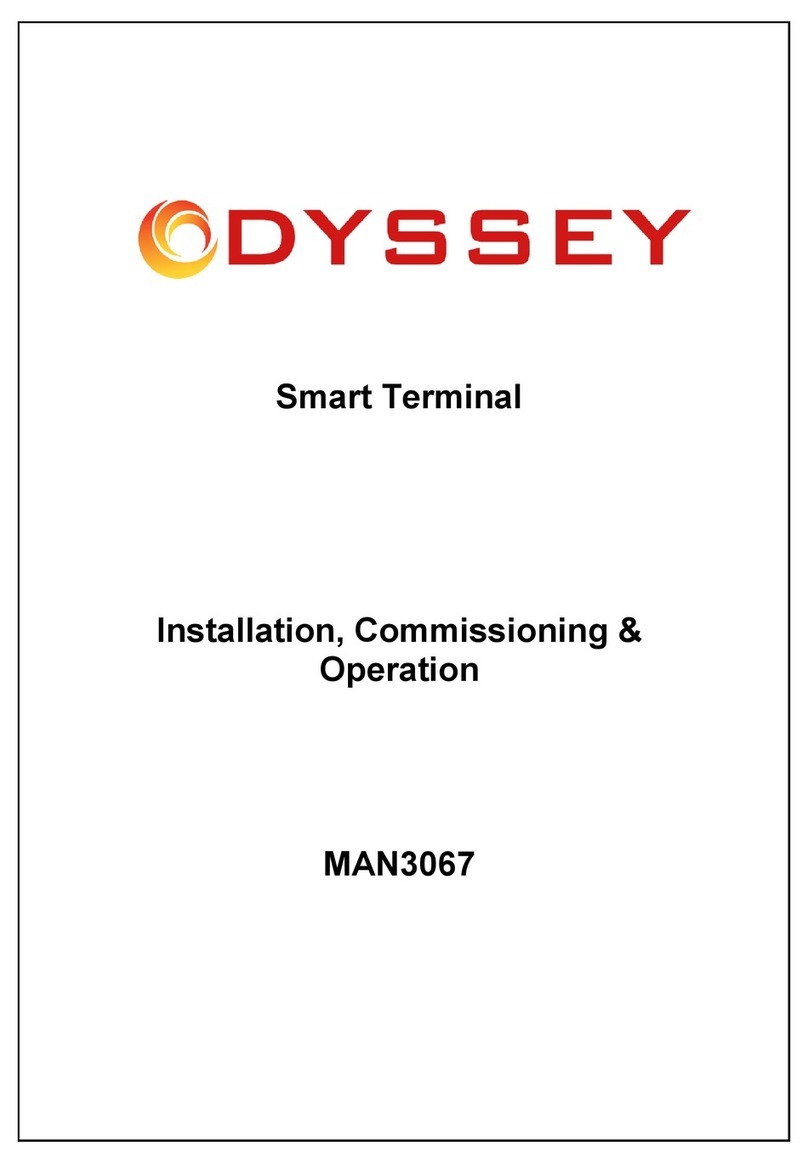
Odyssey
Odyssey MAN3067 Installation, commissioning & operation

Fujitsu
Fujitsu TeamPoS 3000 XL Installation & maintenance manual

Opticon
Opticon PHL 2700 user manual
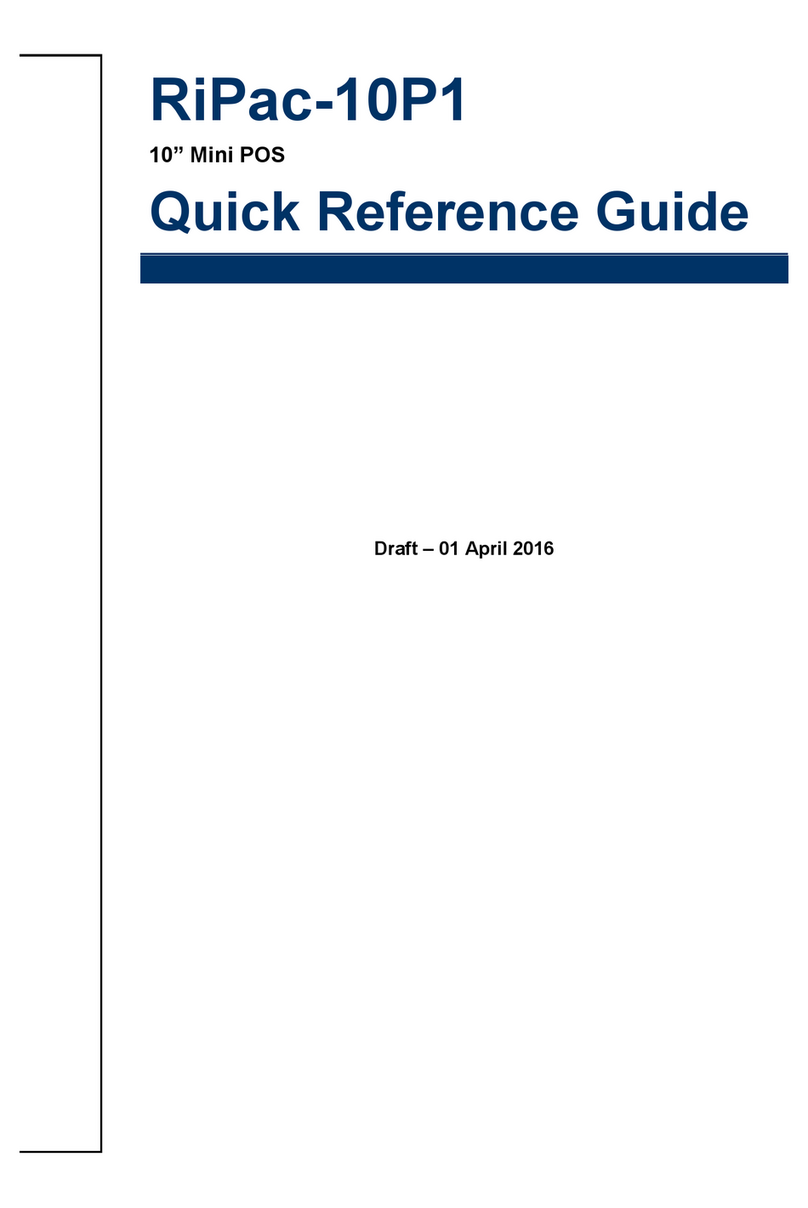
Avalue Technology
Avalue Technology RiPac-10P1 Quick reference guide

Telular
Telular Phonecell SX3i AMPS user manual
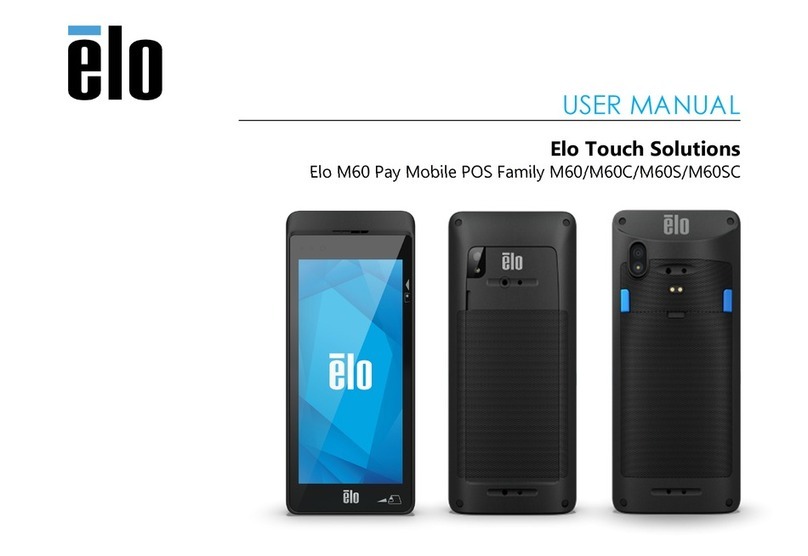
Elo TouchSystems
Elo TouchSystems M60 Pay user manual