ITOH DENKI CBM-103FN User manual

SPECIFICATIONS SUBJECT TO CHANGE WITHOUT NOTICE Page 1 of 10
www.itohdenki.com
ITOH DENKI, USA, INC.
Ph: 570.820.8811 Hanover Industrial Estates
Fx: 570.820.8838 Hanover Township, PA 18706 rev13-0514
CBM-103FN/FP Circuit Board
Features
•New driver card specifically designed for the new KE series Power
Moller® family
•Adjustable acceleration and deceleration time (0 to 2.5s)
•Stable speed operation
•Manual or automatic recovery from thermal overload and low voltage
•One (1) rotary switch to select up to 10 different fixed speeds
•Two (2) LEDs (green & red) to identify error type
•Pulse signal output to indicate motor revolution (2 pulses/motor
revolution)
•RoHS and EMC conformity
•Low Voltage Protection
•External Direction control

SPECIFICATIONS SUBJECT TO CHANGE WITHOUT NOTICE Page 2 of 10
www.itohdenki.com
ITOH DENKI, USA, INC.
Ph: 570.820.8811 Hanover Industrial Estates
Fx: 570.820.8838 Hanover Township, PA 18706 rev13-0514
SPECIFICATIONS
Electrical
24V DC ±10% input
- Battery
- Power Supply: fullwave rectified, smooth current <10% Ripple
Power ON delay < 1s
10A locking current
Input signals (minimum 2.2mA, maximum 7.3mA)
- NPN (0V)
- PNP (+24V DC)
Output signals (open collector 24V, 25mA or less)
- NPN (0V)
- PNP (+24V DC; selectable for Error only)
Applicable PM
Models
PM635KE
Brake
Dynamic (electric)
Protection
Motor control thermal protection
- 95°C (203°F) on the PCB
- 105°C (221°F) in the motor
Built-in diode for incorrect wiring protection
Built-in 18A in-line fuse for supply protection
Built-in thermal fuse to prevent overheating
- 139°C (282°F)
Applicable
Environment
Temperature 0~40°C (32~104°F)
<90% Relative Humidity (No condensation)
No corrosive gas
Vibration <0.5G
Dimensions
VR1
VR2 SW1 SW2
LED1
LED2
3mm
[0.12"]
143.5mm
[5.65"]
27mm
[1.07"]
151.5mm
[5.96"]
64mm
[2.51"]
4mm
[0.16"]
5mm
[0.20"]
3mm
[0.12"]
4.5mm (x2)
[0.18"]

SPECIFICATIONS SUBJECT TO CHANGE WITHOUT NOTICE Page 3 of 10
www.itohdenki.com
ITOH DENKI, USA, INC.
Ph: 570.820.8811 Hanover Industrial Estates
Fx: 570.820.8838 Hanover Township, PA 18706 rev13-0514
SPECIFICATIONS
Connections
CN1 2 PIN connector
POWER
Connector on Card
WAGO #231-432/001-000
Connector for Wiring
WAGO #231-102/026-000
PIN Description
1 +24V DC
2 0V Wire size
28~14 AWG
CN3 7 PIN connector
MOTOR
Connector on Card
JST #S7B-XH-A
Connector for Wiring
JST #XHP-7
PIN Description
1 GND – Grey
2 +12V DC – Blue
3 Hall sensor U - Violet
4 Hall sensor V – Orange
5 Hall sensor W – Green
6 Thermistor – Light Blue
7 Not used
Wire size:
28~22 AWG
Terminal pins:
JST #SXH-001T-P0.6
CN4 3 PIN connector
MOTOR
Connector on Card
JST #S3P-VH Connector for Wiring
JST #VHR-3N
PIN Description
1 Motor phase U – Red
2 Motor phase V – White
3 Motor phase W – Black
Wire size:
20~16 AWG
Terminal pins:
JST SVH-41T-P1.1
KE Motor Cable
17 13

SPECIFICATIONS SUBJECT TO CHANGE WITHOUT NOTICE Page 4 of 10
www.itohdenki.com
ITOH DENKI, USA, INC.
Ph: 570.820.8811 Hanover Industrial Estates
Fx: 570.820.8838 Hanover Township, PA 18706 rev13-0514
OPERATION
Control Connection
CN2 5 PIN connector
CONTROL
Connector on Card
WAGO #733-365 Connector for Wiring
WAGO #733-105
PIN Description
1 +24V DC (PNP) or 0V (NPN) input – RUN
2 +24V DC (PNP) or 0V (NPN) input – DIR
3 0 ~ +10V DC input – V-IN (speed variation)
4 +24V DC or 0V output – ERR
5 0V (NPN) output – PLS (pulse)
Wire size:
28~20 AWG
Control Wiring
Power to CN1 (24V DC) remains ON, control motor Run/Stop through CN2
NPN Input
Control
PNP Input
Control
Press down spring clamp in connector
with a small screwdriver.
Insert leads in proper order.
Lead should be stripped approx:
0.31~0.35”
WAGO connector (included) must be
inserted and/or pulled out carefully, so
as not to damage other parts.

SPECIFICATIONS SUBJECT TO CHANGE WITHOUT NOTICE Page 5 of 10
www.itohdenki.com
ITOH DENKI, USA, INC.
Ph: 570.820.8811 Hanover Industrial Estates
Fx: 570.820.8838 Hanover Township, PA 18706 rev13-0514
OPERATION
Switch
Position
Switch Function Up Down Initial Setting
SW3 ERR
Output NPN PNP NPN
DIP Switches – User Settings
DIP
Switch Function ON OFF Initial
Setting
Manual
Reset
Auto-
matic
Reset
1
Error recovery:
Thermal;
Low voltage;
Induced voltage See Page 8
ON
External
Voltage
Input
Internal
Rotary
Switch
2 Speed change
selection See Page 6
OFF
3
Motor Direction
(no external DIR
signal; viewed
from cable side)
CW CCW OFF
4 ERR output Normal,
ON Error,
ON OFF
OPERATION
Potentiometers
Potentiometer Function Description
VR1 Acceleration RUN signal ON
0~2.5s until set speed
VR2 Deceleration RUN signal OFF
0~2.5s until stop
VRs turn 270°

SPECIFICATIONS SUBJECT TO CHANGE WITHOUT NOTICE Page 6 of 10
www.itohdenki.com
ITOH DENKI, USA, INC.
Ph: 570.820.8811 Hanover Industrial Estates
Fx: 570.820.8838 Hanover Township, PA 18706 rev13-0514
Speed Change Table
Rotary V-IN Speed (ft/min) ± 5%
Switch (V) 1-stage 2-stage 3-stage
9
9.69 ± 0.25 758.0 199.5 52.5
8
9.06 ± 0.25 710.6 187.0 49.2
7
8.44 ± 0.25 663.3 174.5 45.9
n/a 7.81 ± 0.25 615.9 162.1 42.7
6
7.19 ± 0.25 568.5 149.6 39.4
n/a 6.56 ± 0.25 521.1 137.1 36.1
5
5.94 ± 0.25 473.8 124.7 32.8
n/a 5.31 ± 0.25 426.4 112.2 29.5
4
4.69 ± 0.25 379.0 99.7 26.2
n/a 4.06 ± 0.25 331.6 87.3 23.0
3
3.44 ± 0.25 284.3 74.8 19.7
n/a 2.81 ± 0.25 236.9 62.3 16.4
2
2.19 ± 0.25 189.5 49.9 13.1
1
1.56 ± 0.25 142.1 37.4 9.8
0
0.94 ± 0.25 94.8 24.9 6.6
10 speed steps available
through on-board
rotary switch
16 speed steps available
through external voltage
input (V-IN)
n/a 0.31 ± 0.25 47.4 12.5 3.3
Motor Pulse Output Signal
•0V (NPN) output from CN2-5
•Two (2) pulses per motor revolution
•Maximum speed pulse frequency approximately 147Hz
LEDs
LED 1 – Green (power)
LED 2 – Red (error condition)
NPN / PNP inputs
The card(s) are ordered with the inputs preset from the factory – ALL NPN or ALL PNP. The
model designation will show the factory preset.
•CBM-103FN – NPN input type (Default)
•CBM-103FP – PNP input type
Note – the output can be manually switched in the field by DIP switch SW-3 – Output signal type
for both CN2-4

SPECIFICATIONS SUBJECT TO CHANGE WITHOUT NOTICE Page 7 of 10
www.itohdenki.com
ITOH DENKI, USA, INC.
Ph: 570.820.8811 Hanover Industrial Estates
Fx: 570.820.8838 Hanover Township, PA 18706 rev13-0514
OPERATION
LED and ERROR Indications
ERR Output
(DIP-SW4 setting)
LED 1
(Green) LED 2
(Red) OFF ON Condition Result
○○○○
No power Supply power
(24V DC)
○
●●
Flashes two
times with a
1.5s pause
●○
Fuse or temperature
fuse, blown Card must be
replaced
●○○●
Normal
-
●●●
Flashes
Slowly
●○
Stalled motor Motor shuts off
●●●
Flashes
Slowly
●○
Motor is
disconnected at CN4 Motor does not run
●
●●●●
Flashes
Quickly
○●
Current limit, active
May indicate
overload during
operation
●●●○
Thermal error in
motor or on PCB Motor stops after 4s
●●●○
Motor is
disconnected at CN3 Motor does not run
●
●●
Flashes two
times with a
1.5s pause
●○
Low voltage Motor shuts off
●
●●●
Flashes three
times with a
1.5s pause
●○
Induced voltage Motor shuts off

SPECIFICATIONS SUBJECT TO CHANGE WITHOUT NOTICE Page 8 of 10
www.itohdenki.com
ITOH DENKI, USA, INC.
Ph: 570.820.8811 Hanover Industrial Estates
Fx: 570.820.8838 Hanover Township, PA 18706 rev13-0514
OPERATION
Error List
Error Description Solution
Fuse or
temperature
fuse, blown
> 18A through circuit or
> 139°C (282°F) Replace card
Motor
disconnected
(CN3 or CN4) Motor connector(s) unplugged Plug in appropriate connectors
Stalled motor RUN signal turns ON, but motor
does not turn for 1s After motor
shuts off
Thermal error
(PCB or motor)
Motor control circuit has reached
95°C (203°F) on the PCB or
105°C (221°F) in the motor
After operating
temperature is
restored
Low voltage
Supply voltage has
dropped < 15V for at least 1s
or dropped < 15V five times
within 0.5s
After supply voltage
rises > 18V
Induced voltage
(overspeeding) Voltage from motor
rises > 40V
After induced
voltage
drops < 30V
Turn OFF RUN
signal, then turn
back ON
Automatic Recovery
DIP switch 1 – OFF
•Toggling the run signal (OFF/ON) is not necessary
Thermal error resets 60s AFTER operating temperature is restored
Low voltage error resets as soon as the supply voltage rises above 18V
Induced voltage error resets 1s AFTER induced voltage drops and stays below 30V

SPECIFICATIONS SUBJECT TO CHANGE WITHOUT NOTICE Page 9 of 10
www.itohdenki.com
ITOH DENKI, USA, INC.
Ph: 570.820.8811 Hanover Industrial Estates
Fx: 570.820.8838 Hanover Township, PA 18706 rev13-0514
Installation Precautions –
IMPORTANT, PLEASE READ BEFORE INSTALLATION
Precaution Action Reason
Power supply
If the power supply is not sized
appropriately for the number of
cards/rollers it provides power to, then
a low voltage condition may occur.
•If the voltage drops below 15V DC and
remains low for 1s, then the low voltage
error will appear
•If the voltage drops below 15V DC five
times in 0.5s, then the low voltage error
will appear
•If the voltage drops below 15V DC less
than five times in 0.5s or does not
remain low for 1s, the roller may stutter
– quickly turning off then on
Multiple power
supplies
0V line of the power supply for the
card must be common to the 0V line of
the power supply for the controls
(RUN, DIR, etc.).
This completes the signal path from the
controller (PLC, etc.) to the motor driver card.
Voltage drop
across the
power bus
Use suitable gauge wire in relation to
distance and current draw to prevent
voltage drop.
Operating DC voltage is 24V ±10%
When running long distances from a DC
power supply, the voltage drop during motor
operation across the power bus may be
significant (may drop below 15V!). If there is
a large enough drop in voltage, the roller(s)
may behave in a strange manner. In order to
prevent this, a larger gauge wire must be
used.
Grounding
Ensure the control card is securely
grounded to the conveyor frame. The
conveyor frame should also be at the
same potential reference as earth
ground. Standard grounding practices
should be followed.
Static discharge may interfere and damage
internal components.
Electrical
24V DC ±10%
10A maximum current limiter
(motor lock is 10A)
Diode protection for mis-wiring
Sensor power short circuit protection
18A fuse for power supply protection
Auto-sensing inputs for PNP or NPN
Improper power will damage the card.
The motor/card should not be subject to
locked conditions repeatedly.
Internal fuse is not replaceable. If the fuse
has blown, more serious damage has
occurred within the card/motor.
If inputs are subjected to a low potential the
card may see this as a signal, use of a diode
inline is recommended to prevent this.
Environment Ambient temperature is 32~104°F
Ambient humidity is < 90%RH
Atmosphere has no corrosive gas
Vibration is < 0.5G
Indoor use only
Extreme environmental variables may
cause poor or no performance and
damage the card.
Over-speeding Over-speeding of the roller’s no-
load speed by more than 50% may
cause damage.
Back EMF will be generated.

SPECIFICATIONS SUBJECT TO CHANGE WITHOUT NOTICE Page 10 of 10
www.itohdenki.com
ITOH DENKI, USA, INC.
Ph: 570.820.8811 Hanover Industrial Estates
Fx: 570.820.8838 Hanover Township, PA 18706 rev13-0514
Revision History
Revision Number Change
11-0914 Initial document
12-1226 Added autosensing inputs and precautions for electrical potential
13-0314 Added diode recommendation and wiring diagram
13-0514 Removed auto-sensing feature
This manual suits for next models
1
Table of contents
Other ITOH DENKI Controllers manuals

ITOH DENKI
ITOH DENKI CB016 User manual

ITOH DENKI
ITOH DENKI POWER MOLLER HBM-604BN Technical manual
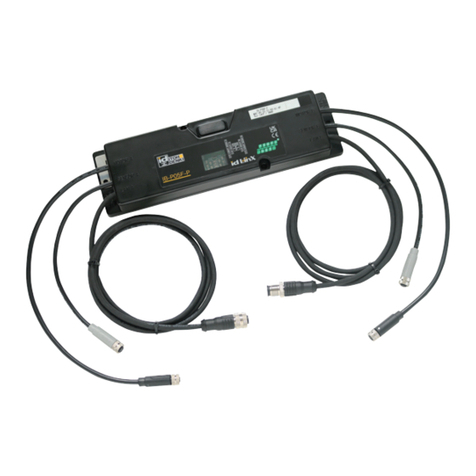
ITOH DENKI
ITOH DENKI IB-P05F-P Guide
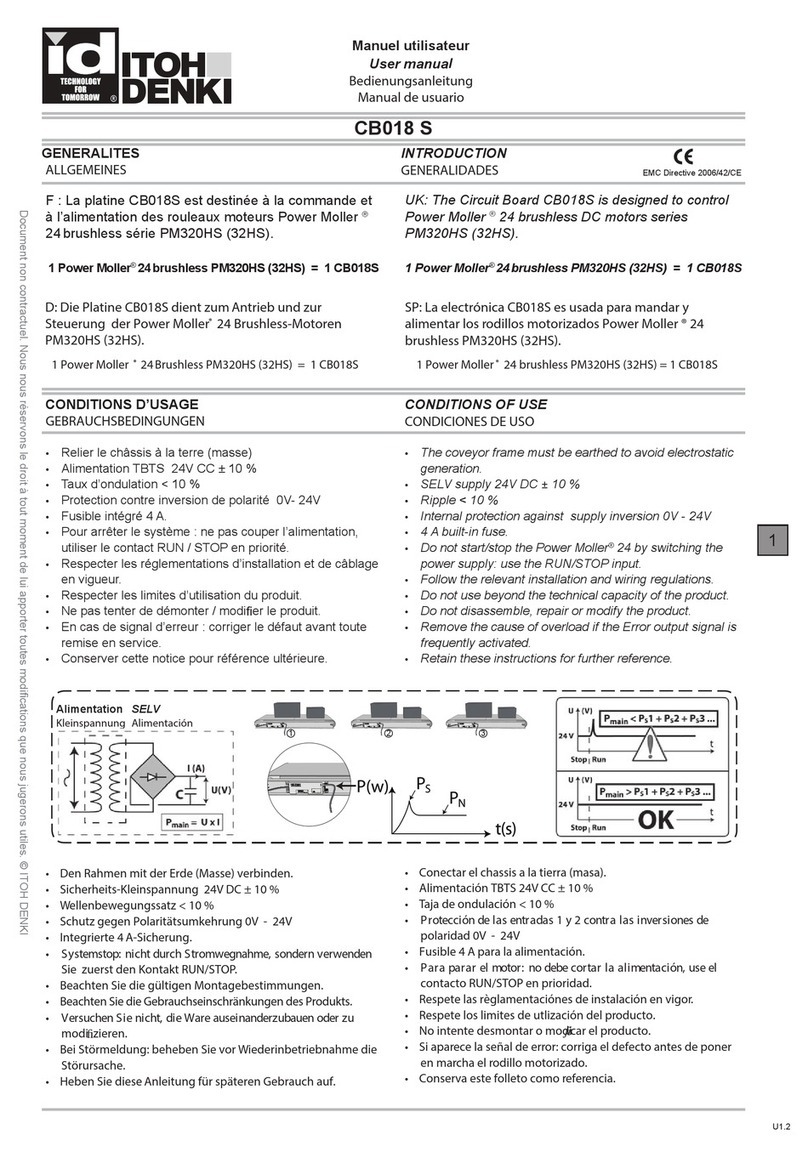
ITOH DENKI
ITOH DENKI CB018 S User manual
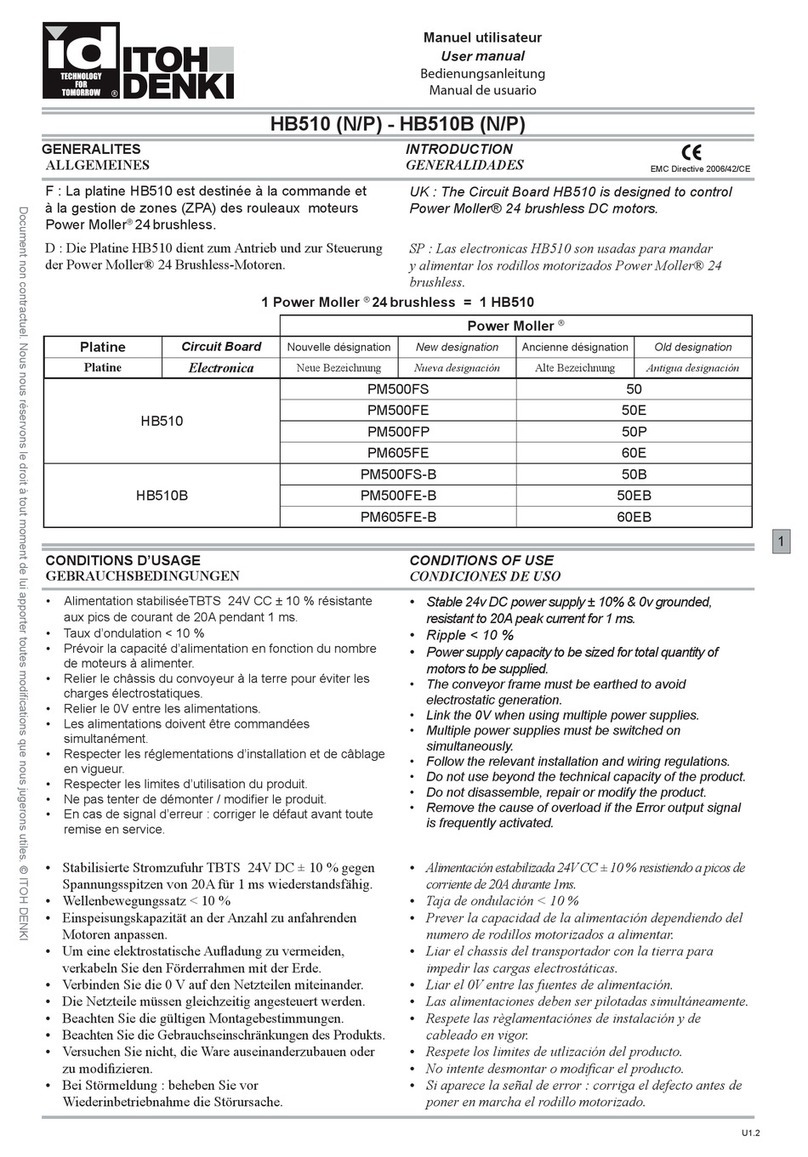
ITOH DENKI
ITOH DENKI HB510 User manual
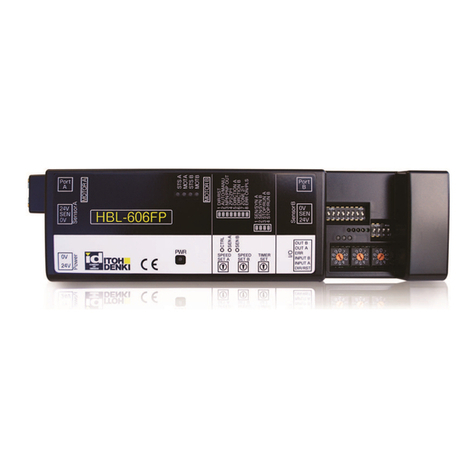
ITOH DENKI
ITOH DENKI POWER MOLLER HBL-606FN Technical manual
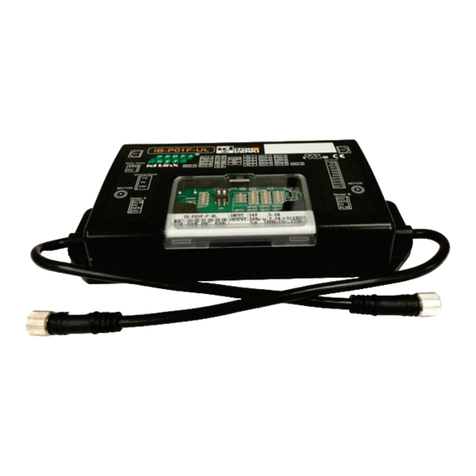
ITOH DENKI
ITOH DENKI POWER MOLLER IB-P01 Guide
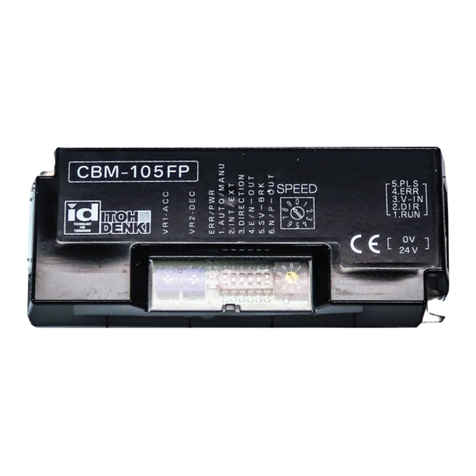
ITOH DENKI
ITOH DENKI Power Moller CBM-105FP1-EU1 Guide