Jafar 4493 User manual

OPERATING MANUAL 07-2022 1/14
OPERATING MANUAL
Double eccentric
flanged butterfly valve
Part No. 4493 4493SQ 4493SA

OPERATING MANUAL 07-2022 2/14
TABLE OF CONTENTS
1. INTENDED USE.......................................................................................................................................... 3
2. TECHNICAL DESCRIPTION................................................................................................................... 3
3. PRODUCT IDENTIFICATION................................................................................................................. 6
4. STORAGE AND TRANSPORT ................................................................................................................. 8
5. INSTALLATION ......................................................................................................................................... 8
5.1. GENERAL REQUIREMENTS.............................................................................................................. 8
5.2. INSTALLATION ISNTRUCTIONS.................................................................................................... 11
6. OPERATION.............................................................................................................................................. 13
4. SAFETY...................................................................................................................................................... 14
5. WARRANTY.............................................................................................................................................. 14

OPERATING MANUAL 07-2022 3/14
1. INTENDED USE
Product Number 4493, 4493SA eccentric butterfly valves are intended for potable water supply systems, sanitary
sewage systems and (if approved by the manufacturer) industrial media systems. Each valve can be installed in
overground and underground pipelines as an integral in-line part of the piping. The butterfly valves are used to
shut off and regulate the flow of the medium using a part-turn gearbox, electric actuator or a multi-turn actuator
unit with a part-turn gearbox. They are recommended as shut-off valves for open or closed position. Additionally
they can be used as flow control valves for opening angle range 15°÷90°. The selected actuator unit must ensure
a stable closure actuation angle within 0° - 90° and the correct operating torque value, see Table 1.
2. TECHNICAL DESCRIPTION
•Production and acceptance according to EN 1074-2 (Valves for water supply. Fitness for purpose
requirements and appropriate verification tests. Isolating valves) and EN 12266-1 (Industrial valves.Testing
of valves).
•100% of each valve is leak tested.
•4493, 4493SA butterfly valves are tight in both directions.
•The temperature range of the valve application is from 0C to 70C (they can be used in other temperatures
as agreed with the manufacturer).
•Nominal pressure ratings: 1.0 MPa; 1.6 MPa.
•Nominal diameter range offered: DN200÷ DN2000 [mm].
•Hydraulic performance: maximum liquid medium flow rate: PS10 max. 3[m/s]; PS16 max. 4[m/s];
•Minimum driving torques necessary to operate the valve (without actuator element) are given below:
DN
[mm]
ISO
5211
Torque value on valve shaft required for
closing or opening (Nm)
Δp
Pa
6 Pa
200
F10
430
970
250
F10
500
1,100
300
F10
860
1,200
350
F14
1,300
1,891
400
F14
1,400
2,400
450
F14
2,300
3,300
500
F16
2,600
3,800
600
F16
3,700
6,300
700
F25
5,500
8,700
800
F25
7,600
11,300
900
F25
9,600
14,400
1000
F25
14,500
20,200
1200
F30
22,900
37,200
1400
F35
42,500
67,800
1600
F40
54,600
118,400
1800
F40
135,000
202,500
2000
F48
150,000
225,000
Table 1. Driving torque

OPERATING MANUAL 07-2022 4/14
•The minimum valve switch-over time (to close or open) dependent on the DN size (nominal diameter) is listed
in Table 2:
DN (mm)
Switch-over time (s)
40÷350
10
400÷600
16
700÷800
40
900÷1200
50
Table 2. Minimum valve switch-over time
The valve switch-over time is the minimum time to close or open the valve connected to a pump which delivers
a medium. The time values listed in Table 2 are calculated with the following formula:
𝑇 = 𝐿 ∙ 𝑉
𝑔 ∙ ℎ ∙ (𝑘 − 1) ∙ √𝑘
T –> switch-over time (s)
L –> piping length (m)
g –> 9.81(m/s2),
h –> nominal pressure in metres of sweet water
column
V –> flow rate (m/s)
k –> shock wave pressure rise factor, calculated
in relation to the nominal pressure (1-1.25)
The listed time values from Table 2 are calculated for: L=500(m), V= 4(m/s), k= 1.25. If the closing time is shorter,
it is mandatory to install water hammer dampers (and standard safety valves are unfit for this application).
•Valve control mode: the standard version of the valve has the clockwise closing sense of rotation. The closing
sense of rotation can be opposite on special order. The standard valve version control is operated with a self-
retarding worm gearbox. It is possible to control the valves with electric actuators. The following is the
standard for the version with electric actuator:
➢Product 4493SQ: applies to DN200 - DN400; control is carried out by the SQ electromechanical
part-turn actuator from AUMA,
➢Product 4493SA: applies to DN500 - DN2000; the control is carried out by the SA
electromechanical multi-turn actuator and a GS part-turn gearbox from AUMA.
•Connection flanges are manufactured in accordance with EN 1092-2 (Flanges and their joints.Circular
flanges for pipes, valves, fittings and accessories, PN. Cast iron flanges) and in sizes suitable for nominal
pressure ratings.
•The installation (face to face) length and its tolerance are per EN 558 (Industrial valves. Face-to-face and
centre-to-face dimensions of metal valves for use in flanged pipe systems. Valves with PN and class marking);
Series 14.
•Butterfly valves with a soft seal (4493, 4493SQ, 4493SA) in diameters DN200 ÷ DN2000 have a double-
seated cover (disk). The valve pivot shafts are held by the necks, mounted on additional bearing sleeves. The
pivot shafts are sealed by the packing gland assembly, comprising an arrangement of o-rings. The butterfly
valve is closed with a cast iron disc fitted with an elastomer seal. One of the shafts is used to control the valves.
The second shaft is enclosed and is used to evenly distribute the moments acting on the butterfly valve disk.
In the case of underground installations, the valve must have a part-turn gearbox connected to the fixed
housing Product Number 9025. Such a configured valve can be controlled with: T key - Product Number
9015,
➢
➢Stand with opening indicator - Product Number 9113,
➢Stand for actuator - Product Number 9114.
➢Stand for actuator - Product Number 9114 + additional equipment ( electromechanical actuator)
For more information on installation of valves in underground pipework, see point 5.2. Installation
instructions).

OPERATING MANUAL 07-2022 5/14
The following figures (fig.1) show the position of the eccentrics for double eccentric butterfly valves.
Fig. 1. Disk positions depending on the butterfly valve opening angle.
The first eccentric (a) causes the disc rotation axis to be outside of the sealing surface axis. Such construction
ensures full sealing around the entire circumference between the body welded seat and the rubber sealing ring.
The second eccentric (b) is an offset of the butterfly valve disc axis in relation to the butterfly valve axis (body
axis).
It serves to minimise the compressive stress of the sealing ring when the butterfly valve is opened.
•The valve without a gearbox forms an assembly that can be adapted to various control devices (gearboxes,
actuators). To ensure proper leak-tightness of the valve, an operator can only be installed by an
authorized service of Fabryka Armatur JAFAR. The operator must ensure a stable closure actuation angle
within:
➢0 - 90for the fully open and fully closed motion;
➢15- 90for flow control (damping);
and the proper operating torque (see Table 1). Long-term operation of the valve with an operator as a flow
damping valve may cause wear of the sealing insert and result in leaks through the closed valve.

OPERATING MANUAL 07-2022 6/14
3. PRODUCT IDENTIFICATION
The valve marking meets the following standards: EN 19 (Industrial valves. Marking of metallic valves), EN 1074-
1 (Valves for water supply. Fitness for purpose requirements and appropriate verification tests. Part 1: General
requirements). The permanent identification markings are on the front and back walls of the body chamber and on
the cylindrical closure plate. The marking contains the following data:
- manufacturer's trade mark,
- arrow; direction of the recommended
media flow,
- identification sticker,
- nominal diameter,
- nominal pressure,
- body material type,
- closure plate material type,
- nominal diameter;
The location on the valve specified in the documentation features the identification stickers (nameplates) which
contains the following data (Fig.2):
Fig.2 Plate identifying the valve
1. Manufacturer's company and country of origin.
2. Manufacturer's company logo.
3. Polish construction mark (for the full range of diameter values).
4. Alphanumerical reference designation for the combination of mechanical properties and sizing of the
mating piping ends (PN).
5. CE marking
6. Maximum permitted pressure (PS).
7. Barcode.
8. Maximum / minimum permissible temperature (TS).
9. Production serial no. in the calendar year.
10. Year of manufacture of the product.
11. Sealing material specification (where the operating temperature shall not exceed 70°C for EPDM).
12. Reference standard the product is compliant with.
13. Nominal diameter (DN).

OPERATING MANUAL 07-2022 7/14
Butterfly valves with anti-corrosion protection in accordance with GSK RAL certificate have an appropriate
label (this applies to valves in the range DN200 - DN1200) (Fig. 3):
1. GSK logo.
2. Certificate title.
3. Certificate reference number.
Fig. 3 The sticker specifying the RAL mark of the GSK company
Additionally, each valve has a sticker with information on how to contact the JAFAR service (Fig. 4).
Fig. 4 Sticker specifying contact with JAFAR service
A sticker identifying part-turn gearboxes Type JFR IP68 (GRAY) is used for standard valves:
Fig. 5. Plate identifying JFR gearboxes
1. Manufacturer's company logo.
2. Shaft size used for the gearbox unit.
3. A constant ratio of the number of sprockets between the worm screw crescent and the worm screw shaft
of the gearbox.
4. Conversion ratio of the maximum output torque from the gearbox to the input torque. This value may
increase to 20% during operation.
5. Maximum input torque which can be used to operate a valve using, for example, a drive wheel.
6. Maximum gearbox torque that can be transmitted to the valve shaft.
7. Accessory type.
8. Gearbox type JFR IP68
9. Production serial no. in the calendar year.
10. Year of manufacture of the product.

OPERATING MANUAL 07-2022 8/14
4. STORAGE AND TRANSPORT
The products are packed on EURO pallets (1200x800) or in dedicated packaging. The valves should be stored in
clean rooms, free from bacteriological and chemical contamination, at temperatures from -20°C to 70°C. The paint
coating and rubber elements must be protected against long-term exposure to UV radiation. The stored valves are
protected against mechanical damage.
Do not compress any rubber parts. The valve flap should be left in an intermediate position - so that the flap does
not exceed the installation length of the valve (this position is shown in Figs. 6 and 7). Secure the products against
shifting during shipping and handling. Heavy valves (DN500 and larger) shall be handled with dedicated eye bolts;
valve sizes from DN200 to DN400 shall be handled on slings and secured from rotating. Do not handle by the
lever, the gearbox handwheel, or the operator/gearbox housing.
Table 3 below lists the transport holes on the flange projections for the range DN500 - DN900 - Fig. 3. For DN1000
and DN1200, the transport holes are located on the cylindrical surface of the body (between the connection flanges
to the pipeline) - Fig. 4.
DN500
DN600
DN700
DN800
DN900
DN1000
DN1200
PN10
4𝑥𝜙28
4𝑥𝜙31
4𝑥𝜙31
4𝑥𝜙34
4𝑥𝜙34
4xM27
4xM36
PN16
4𝑥𝜙34
4𝑥𝜙37
4𝑥𝜙37
4𝑥𝜙41
Table 3. Sizes of transport holes
Fig. 6. Butterfly valve part no. 4493SA DN800
Fig.7. Butterfly valve part no. 4493 DN1200
5. INSTALLATION
5.1. GENERAL REQUIREMENTS
Flanged butterfly valves: TYPE 4493, TYPE 4493SQ and TYPE 4493SA can be installed in underground or
overground pipelines on horizontal or vertical installations. The listed products are suitable for joining with the
flanged ends of pipelines with the size equal to that of the valve flanges. The valves are bi-directional tight. The
valves are to be installed in the pipeline so that the flow direction of the medium is in accordance with the flow
direction indicated on the body. This is due to the increased service life of the sealing elements and the reliability
of operation in such a configuration. At the moment of valve opening the stream coming out through the slit in the
lower part of the body has the maximum speed, which consequently results in tearing off the embedded
contamination (this applies to the situation when solid contaminants get with the medium and they settle at the
bottom of the pipeline and in the body of the butterfly valve). It is possible to mount the valve in the opposite
direction to the arrow on the body, bearing in mind the increased wear and tear of the sealing elements compared
to the standard configuration described above.

OPERATING MANUAL 07-2022 9/14
When installing eccentric butterfly valves downstream of the control valves (e.g. Product Number 6800)
and shut-off valves (e.g. needle, ball or poppet valves), a minimum distance of 10xDN of the valve must be
kept between them.
Due to the non-uniformity of the speed and pressure fields near piping elbows and tees, it is recommended
to maintain a straight piping run at least 3×DN long between the valve outer flange face and the piping bend
or tee (see picture below). The manufacturer allows for a distance less than 3xDN, but this may result in
noisy operation and faster wear of the butterfly valve.
Fig. 8. Recommended distances from the piping bends
The general rule is not to install the valve near any bend or tee or any piping bends (elbows / tees), especially with
the valve on the high-pressure side of the piping (in the pump to valve to piping curve system)
The normal flow deflection over a piping bend will be aggravated by the low-pressure area of the valve (where a
risk of flow interruption exists). Installation directly behind pumps, behind elbows or tees is not permitted due to
the possibility of cavitation on the flap surface, vibration or disc oscillation and faster wear of bearings and sealing
elements. The dimensions of the valve must also be taken into account in the technical design so that the valve can
be operated freely.
The butterfly valve can be installed in any orientation and in either direction of flow, provided that the butterfly
valve closure pivot shafts are aligned horizontally. Correct installation of the valve on vertical and horizontal
pipelines is given below - Fig. 9. The permissible deviation from the horizontal location of the shafts in relation
to the horizontal axis of the pipeline is from 2 to 5 degrees.
Fig. 9. Orientation of the valve closure pivot shaft relative to the piping plane shown for Product Number
4493 DN500
a) Vertical piping
b) Horizontal pipeline

OPERATING MANUAL 07-2022 10/14
Fig.10 The movement of the valve flap in the standard version
The above Fig.10 shows the standard version of eccentric butterfly valves with the JFR GRAY gearbox. The
standard movement that opens the flap is clockwise. In contrast, the permanently marked arrow on the valve flap
pivots shows the movement that closes the flap (counter clockwise). This is the optimal movement that increases
the service life of the valve components. Irrespective of the requirement for a straight piping run at least 3×DN
long between the valve outer flange face and the piping bend (alternatively, the designed valve can be replaced
with one of a higher pressure rating), to minimise the localised flow acceleration and interruption by the piping
bend. The valve shall be installed with the centreline of the valve closure pivot shaft perpendicular to the vertical
line of the piping bend so that the valve closure drive shaft centreline is aligned with the piping bend plane. While
the valve is being closed or opened, the medium is at its maximum flow rate and entrains the contamination settled
in the neighbouring part of the pipeline. The valve installation shown in Fig. 10 additionally extends the service
life and operating reliability even with media loaded with contaminants which by their weight tend to settle down
in the piping. A consequence of this is that the deposits can be entrained from the upstream of the valve by the
maximum possible flow passing the bottom part of the valve closure during the opening operation (Fig. 11). Apart
from normal flow deflection by the piping bend, the liquid flow applies a high strain in the low-pressure valve
area. This in turn causes the valve to operate with difficulties.
Fig. 11. Correct valve flap orientation
When designing the installation, consider that the horizontal orientation of the valve closure pivot shafts is the best
for operating performance and reliability:
1. the weight of the pivot shafts and the closure rests on both bearings;
2. the load at the bearing of the face end of the shaft is decreased,
3. valve life is increased, particularly when the liquid contains solids the particles of which tend to settle at
the bottom of the pipe.

OPERATING MANUAL 07-2022 11/14
5.2. INSTALLATION INSTRUCTIONS
Before installation, the condition of the internal surfaces of the butterfly valve and the surfaces to which the seals
working with the pipeline will be fitted should be checked and, if necessary, thoroughly washed with water. When
mounting butterfly valves between pipeline flanges, first remove any preservatives which may have been used to
protect the surfaces during transport, clean thoroughly the side surfaces of the butterfly valve to which the seal is
to be mounted, install previously prepared seals and fasten the whole assembly with appropriately long bolts or
pins connecting two adjacent flanges. For proper installation, the flange thickness for the selected DN of the
pipeline must be taken into account. When opening the butterfly valve flap it extends beyond the installation
length, therefore it is necessary to remember about free space in the pipeline for proper operation of the flap by
using the appropriate fittings e.g. cast iron stub pipe, assembly insert. The minimum distance from the valve flange
to the end of the gasket dimension is given in the following Table 4 and Fig. 12:
DN
DN200
DN250
DN300
DN350
DN400
DN450
DN500
DN600
DN700
x [mm]
0
0
8
24
33
48
63
93
124
DN
DN800
DN900
DN1000
DN1100
DN1200
DN1400
DN1600
DN1800
DN2000
x [mm]
154
184
214
199
274
334
394
454
514
Table 4. Dimension "x"
Fig. 12. Preview drawing of a fully open valve 4493 DN1200 PN10
Tighten the connection flange bolts crosswise to ensure a proper seal pressure. Start from the bolt holes near the
valve pivot shaft. The tightening torque of the bolt nuts is specified in the standard PN-63/M-82056. During
mounting, it is necessary to consider making bases or supports for butterfly valves, which must be adapted to the
size and weight of the valve in order to avoid transferring the load into the pipeline. Installed fittings are an integral
part of the pipeline.

OPERATING MANUAL 07-2022 12/14
As standard, the manufacturer offers fittings for dry chambers and directly for installation in the ground. The IP68
protection class (part turn gearbox) does not define the exact operating ranges of the products, such as: immersion
depth (a value is specified; at least 1m), the pressure value acting on the product and the valve immersion time.
The fittings may be used in chambers (tanks) only after prior agreement between the customer and Fabryka
Armatur Jafar. - special realization. As stated in point 2, the control is carried out by a T- key, stands or an
electromechanical actuators including fixed casing Product Number 9025. When mounted in the ground, the
manufacturer recommends the use of a street box Product Number 9501 mounted on a base plate Product Number
9521 or an equivalent product ensuring rigid foundation of the box. More information on the use of street boxes
for underground installations is described in the "Operating Manual for PE-HD street boxes Product Number
95xx”.
In case of installing butterfly valve housings in chambers, it is forbidden to transfer the weight of the housing
to the valve gearbox. It is absolutely necessary to use stabilizers or other relieving elements, which are
mounted to the walls of chambers. Exceeding the limit moments given in Table 4 in point 6 may result in
mechanical damage to the JFR GRAY part-turn gearbox.
Note that the completed installation must not expose the valve to bending or tensile stress from loading with the
unsupported pipeline sections. Install the product properly aligned with the piping centreline and with proper
parallelism and flatness of the mating connection flanges, with prevention of hydraulic shock, and with due
compensation of the pipeline dimensional changes from temperature and pressure. A valve assembled and adjusted
by the manufacturer is ready for installation in the system. Any dismantling of the valve components (e.g. the
shaft, the closure panel, or sleeves) may result in loss of seal.
The requirements for correct quality of the mating flanges have to be satisfied, that is flatness and parallelism,
during the installation process. During the installation process, do not leave any installation tools, bolts, nuts, or
welding wire inside of the piping or they can stop in the sealing seat of the butterfly valve or on the flap (disc).
This may lead to damage of the seat during closing of the valve and loss of seal across the valve. The outer diameter
of the flat seals installed the pipeline and butterfly valve flange faces must be equal to or higher than the outer
diameter of the face. It must never less than the outer diameter of the face. Place the flat seals aligned with the
centreline of the flap sealing ring (the outer diameter of the flat seal must be equal to the nominal diameter of the
piping). The tightness is ensured by an elastomeric seal in the disc groove, attached with a clamping ring to the
valve flap.
The manufacturing tolerance of the valves and their components are large enough to ensure full interchangeability.
The user carries out the installation of the valve in the pipeline on his or her own accord.
Use proper intrinsically safe tools and avoid all actions which may lead to fire during all repair and maintenance
work.
Before attempting to install the valve, check the technical and commercial documents delivered with the product
to verify that your media and pipeline operating parameters comply with the manufacturer's declaration.
If the butterfly valve is installed at the end of piping, mount a steel or cast-iron stub pipe on the free end of the
butterfly valve to guard the disc during opening.
Any change in the operating conditions must be consulted with the valve manufacturer beforehand.
Before attempting to assemble the valve, remove the main bore plugs, check the inner surfaces of the valve and
thoroughly flush with water, if necessary. When installing butterfly valves between the pipeline flanges, first
remove all transport preservation from the surfaces, thoroughly clean the flange faces, install the seals, and screw
down with screws long enough to tighten the adjacent flanges of the pipeline together. The valve and piping flange
holes must be aligned.
Having completed the installation, perform a pressure test at a maximum test pressure equal to 1.5 times
the nominal pressure in the fully open or 1.1 times the nominal pressure in fully closed position.
Caution! If the product has mechanical damage, do not install it in the pipeline.
The pipe inner diameter shall be equal to the nominal diameter (DN) of the valve plus the tolerance for the
deviations provided for by the foundry industry for the given pipe I.D.
If the valve is installed with an operator or an operator and gearbox unit, check the electrical wiring and fire-proof
protection features (also during coupling and adjustment of the operator) for conformity with the respective
operating manuals from the operator drive unit manufacturer.

OPERATING MANUAL 07-2022 13/14
6. OPERATION
The valve shall be operated in accordance with all relevant requirements for stop valves.
To ensure full operational efficiency, carry out a technical inspection and maintenance at least once a year as
follows:
•Operate the valve from the fully open position to the fully closed position, or vice versa.
•If the valve operation is difficult, i.e. the valve reaches the maximum driving torque before either of its
limit positions, repeat the full operation three times (by opening and closing the valve repeatedly).
•Check the tightness of all connections and seals with the valve closed.
If all the actions above have been completed with a good result, visually inspect the corrosion protection. If the
paint coat is damaged, rebuild it with the paint kits available from JAFAR.
Exceeding the operating limits of the valve may result in damage that will not covered by the warranty or the
statutory warranty granted by the manufacturer. When controlling butterfly valves 4493 fitted with a JFR part-turn
gearboxes, the torque limits given in Table 5 below must be strictly adhered to:
DN
200
250
300
350
400
500
600
700
800
900
1000
1200
Mmaks [Nm]
46
46
109
175
175
197
134
123
123
151
151
153
Number of turns
10
10
9
10
10
14
55
93
93
117
117
218
Table 5. Maximum torque on the gearbox shaft and the total number of rotations to the open-close position.
Replacing the seal in the flap.
In order to replace the sealing ring of the flap, it is recommended to remove the butterfly valve from the pipeline,
while observing the relevant health and safety regulations.
Before replacing the seal (4), the product must be fully closed. This will make it easier to dismantle the
compression ring (5).
In the first stage, the transmission
control element (wheel or drive)
must be removed to avoid
accidental damage when
changing the butterfly valve
position to horizontal. Then place
the butterfly valve body (2) on a
solid surface, e.g. a pallet (1) as
presented in the drawing (with the
compression ring facing
upwards). The next step is to clean
the seat of the welded body, the
flap (3), the compression ring
from any dirt and contaminants.
Remove the retaining screws (7),
then alternately remove the
retaining screws with the spring
washers (6) from the flap (3).
6
4
5
7
2
1
3

OPERATING MANUAL 07-2022 14/14
Remove the compression ring (5). Open the flap (3)
with the seal (4) so that the seal is completely
relieved. Carefully clean the flap where the seal is
installed. In addition, the welded seat and the
compression ring must be cleaned. The flap seal
should be lubricated with a grease approved for
contact with drinking water and certified by the
National Institute of Hygiene (PZH). Install the seal
in the place provided for it in the flap, then install the
compression ring starting from the initial centring of
the ring with the screws (7). Tighten the screws and
washers alternately to the torque listed in the table
below. Tighten screws (7) in the butterfly valve flap.
Butterfly valve DN
Screw thread
Screw tightening torque
DN200 –DN250
M8
20 Nm
DN300 –DN350
M10
35 Nm
DN400 –DN1200
M12
60 Nm
4. SAFETY
All installation and operation tasks related to the product shall be only be done by qualified professionals with
sufficient training and experience to assess the current situation and identify and avoid hazards. Failure to follow
this warning or this Operating Manual may cause death, severe bodily injury or substantial property damage.
Fabryka Armatur Jafar S.A. shall not be liable for any accidents or emergencies related to incorrect installation or
operation of the product. Note that the valve installation could be pressurized or contain various type of stray gas
or aggressive liquids. If the installation is operated explosion hazard zones, ATEX requirements may apply; this
will require suitably trained professionals (according to ATEX requirements). Do not use tools which may
generate electrostatic discharge in the ATEX zone.
Do not use the product without thorough knowledge and understanding of this Operating Manual. Follow the
general health and safety rules. Keep this Operating Manual throughout the service life of the product to ensure a
safe operation of the latter.
5. WARRANTY
The product assembled, installed and operated in conformity with this Operating Manual and the data sheet is
covered by a guarantee from the manufacturer. The warranty terms, conditions and period are given on the website
http://www.jafar-valves.com/en/obsluga-gwarancyjna-i-pogwarancyjna. The tab can only be accessed after
creating an account in Customer area and then logging in.
The manufacturer may provide this product with custom materials and modifications on order. The final selection
of the product which meets the optimum criteria for the installation project in question is made by the installation
designer, who should consider this Operating Manual along with other data and information of significance for the
correct operation of the product.
Failure to comply with the guidelines and instructions in this Operation and Maintenance Manual releases the
manufacturer from all obligations, liability and warranty. Due to constant development of our company, we reserve
the right to introduce modifications and structural alterations to the product presented in this document.
3
4
This manual suits for next models
2
Table of contents
Other Jafar Control Unit manuals
Popular Control Unit manuals by other brands

schmersal
schmersal SRB 211LT/CC operating instructions
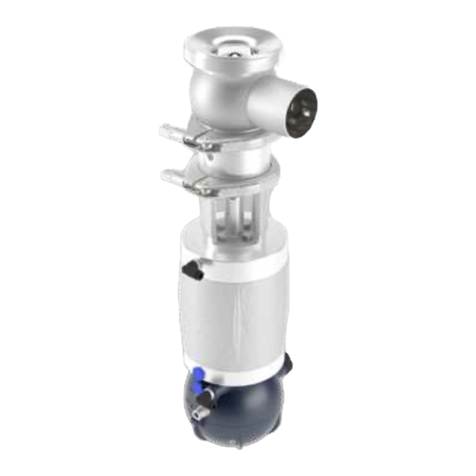
Bardiani Valvole
Bardiani Valvole BBZO Instruction, use and maintenance manual
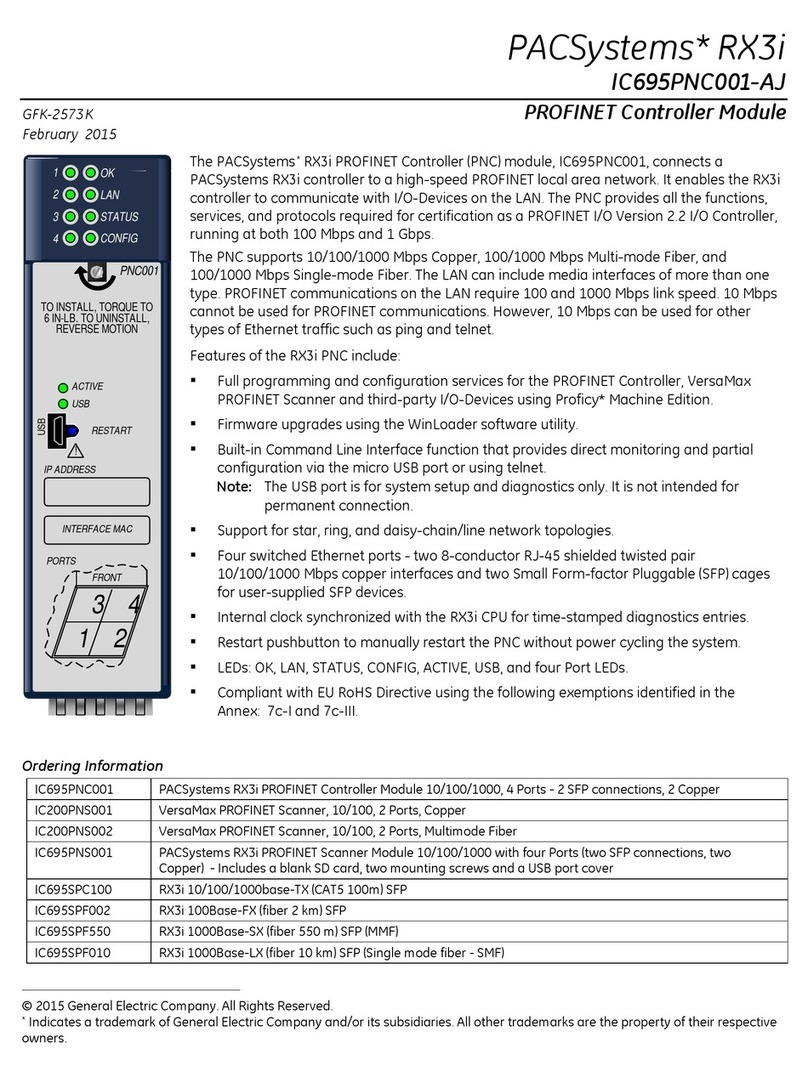
GE
GE RX3i PROFINET quick start guide
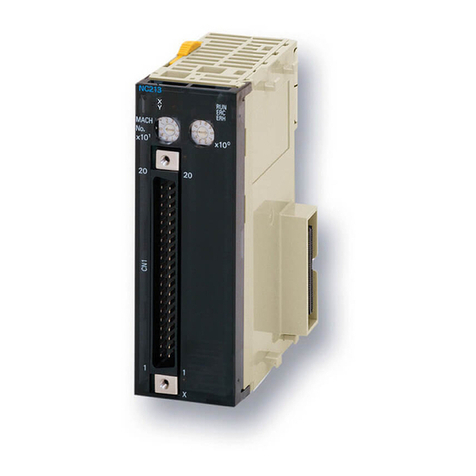
Omron
Omron CS1W-213 - REV 02-2008 Operation manual
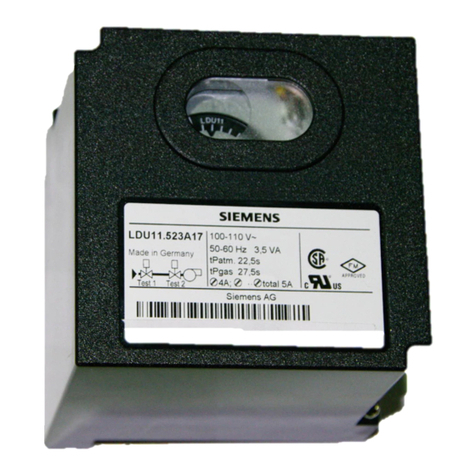
Siemens
Siemens VALVEGYR LDU11.323A17 user manual
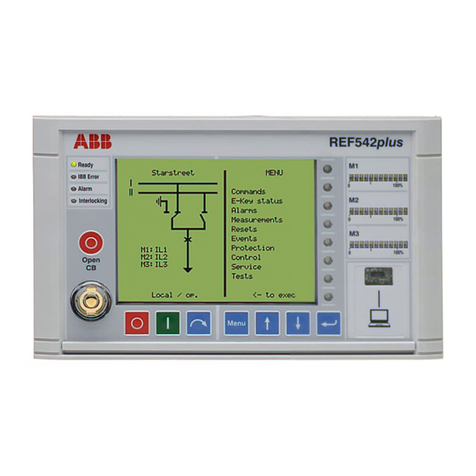
ABB
ABB REF 542plus installation manual