Jafar 8890 Manual

OPERATION AND MAINTENANCE MANUAL 01-2016
Operation
& Maintenance Manual
INSPECTION COUPLING WITH
HYDRANT AL E
P/N
8890
Approved for use by
President of Factory, JAFAR S.A.
Failure to comply with the guidelines and instructions in this Operation and
Maintenance Manual releases the manufacturer from all obligations, liability and guarantee.
Due to continuous business development, we reserve the right to introduce
modifications and structural changes to the presented product.

OPERATION AND MAINTENANCE MANUAL 01-2016
2
TABLE OF CONTENTS
1 TECHNICAL DESCRIPTION............................................................................................................................ 3
1.1 PRODUCT NAME AND FEATURES......................................................................................................... 3
1.2 PURPOSE..................................................................................................................................................... 3
1.3 TECHNICAL SPECIFICATION.................................................................................................................. 3
2 STRUCTURE...................................................................................................................................................... 3
2.1 FITTING DESIGN DESCRIPTION............................................................................................................. 3
2.2 MATERIALS................................................................................................................................................ 4
2.3 DIMENSIONS.............................................................................................................................................. 4
2.4 STANDARDS............................................................................................................................................... 5
2.5 ORDERING REGULATIONS ..................................................................................................................... 5
2.6 MANUFACTURE AND ACCEPTANCE.................................................................................................... 6
2.7 MARKINGS ................................................................................................................................................. 6
3 PROTECTION, STORAGE & TRANSPORT.................................................................................................... 6
3.1 PROTECTIVE COATINGS......................................................................................................................... 6
3.2 PACKAGING............................................................................................................................................... 6
3.3 STORAGE.................................................................................................................................................... 6
3.4 TRANSPORT ............................................................................................................................................... 7
4. ASSEMBLY AND INSTALLATION................................................................................................................ 7
4.1. INSTALLATION GUIDELINES................................................................................................................ 7
4.2 INSTALLATION INSTRUCTIONS............................................................................................................ 7
4.3 OPERATION................................................................................................................................................ 8
4.4 OH&S REGULATIONS............................................................................................................................... 8
5 GUARANTEE CONDITIONS............................................................................................................................ 8

OPERATION AND MAINTENANCE MANUAL 01-2016
3
1 TECHNICAL DESCRIPTION
1.1 PRODUCT NAME AND FEATURES
The subject of this O&MM is:
Inspection coupling with hydrant valve Type 8890:
- Cast-iron body prepared for removing impurities (e.g. sand, gravel)
- Aluminium saddle tee C52 per DIN 14317.
1.2 PURPOSE
The inspection coupling type 8890 with hydrant valve for water supply systems for chemically neutral pure
water, containing solid impurities and for industrial systems. Recommended for use on above-ground installations
on pipelines laid horizontally or vertically below the freezing zone.
The coupling design enables introducing cleaning devices, monitoring and flow measurement devices
(probes) into the pipeline.
For transferring water in water supply systems, for pressures up to 1.6 MPa and temperatures from +1ºC to
+70ºC.
1.3 TECHNICAL SPECIFICATION
The inspection coupling with hydrant valve for cleaning and transferring potable water, for industrial water
at temperatures from +1°C to +70°C.
- Available diameters DN50 –DN250 — for flanged versions;
- Installation length PN-EN 558:2012;
- Maximum medium flow rate: 4m/s;
- Max working pressure (PS): 1.6 MPa — for flanged version;
- Max. working temperature (TS): 70ºC
Connecting flanges for inspection couplings type 8890
according to PN-EN 1092-2: 1999 with the dimensions
adequate to the relevant nominal pressure values.
- Nominal pressure values PN: 1,6 MPa
- Connection: - Saddle tees C 52 per DIN 14317: 1985
2 STRUCTURE
2.1 FITTING DESIGN DESCRIPTION
Inspection couplings with hydrant valves supplied by F.A. JAFAR S.A. are supplied in flanged design. A
coupling is made up of pipe-shaped body and a bonnet with screwed in hydrant valve (saddle tee C52). There
are threaded inspection openings in the coupling body. The couplings feature a cleanout opening in the lower part
of the body to enable drainage of liquid left in the pipeline or to flush a valve after completion of service
procedures.
All internal and external surfaces made of cast-iron on the coupling have corrosion protection in the form
powder epoxy coat.

OPERATION AND MAINTENANCE MANUAL 01-2016
4
2.2 MATERIALS
List of materials used in the inspection couplings:
Item Part name Material Reference standard
1 Body EN-GJL-250
EN-GJS-400-15 PN-EN1561: 2012
PN-EN1563: 2012
2 Cover EN-GJL-250
EN-GJS-400-15 PN-EN1561: 2012
PN-EN1563: 2012
3 Cleanout opening CuZn39Pb1Al-B PN-EN1982: 2010
4 Cleanout opening seal Technical fibre
5 Bonnet gasket EPDM/NBR PN-EN1629: 2005
6 Bolt Steel Fe/Zn5 or stainless steel PN-EN ISO 4762: 2006
7 Bolt plug Paraffin
8 Valve seal EPDM/NBR PN-EN1629: 2005
9 Hydrant valve AlSi
Stainless steel 1.4401 PN-EN1706: 2011
PN-EN 10088-2: 2014
2.3 DIMENSIONS

OPERATION AND MAINTENANCE MANUAL 01-2016
5
DN L D
K
PN16 (PN10)
d h H L
x
n
PN16 (PN10)
Weight
[kg]
50 200 165 125 102 185 307 18x4 11
80 260 200 160 138 185 329 18x8(4) 18
100 300 220 180 158 185 351 18x8 23
150 400 285 240 212 185 384 22x8 39
200 500 340 295 268 185 420 22x12(8) 58
250 700 405 355 (350) 320 185 390 26(22)x12 106
[mm]
2.4 STANDARDS
PN-EN 1074-1: 2002 Valves for water supply. Fitness for purpose requirements and appropriate
verification tests. General requirements
PN-EN 1074-2: 2002 Valves for water supply. Fitness for purpose requirements and appropriate
verification tests. Isolating valves.
PN-89/H-02650 Fittings and pipelines. Pressures and temperatures.
PN-EN 19: 2005 Industrial valves. Marking of metallic valves.
PN-EN558: 2012 Industrial valves. Face-to-face and centre-to-face dimensions of metal valves
for use in flanged pipe systems. PN-designated valves.
PN-EN 12266-1: 2012 Industrial valves. Testing of metallic valves. Pressure tests, test procedures
and acceptance criteria. Mandatory requirements.
PN-EN 1092-2: 1999 Flanges and their connections. Circular flanges for pipes, valves, fittings and
accessories, PN designated. Cast iron flanges.
PN-EN ISO 6708: 1998 Definition and selection of DN (nominal size).
PN-EN1561: 2012 Founding. Grey cast irons.
PN-EN1563: 2012 Founding. Spheroidal graphite cast irons.
PN-EN 10088-1: 2014 Stainless steels. List of stainless steels.
PN-EN 1706 2011 Aluminium and aluminium alloys. Foundings.
Chemical composition and mechanical properties.
PN-EN12420: 2002 Copper and copper alloys. Forgings.
PN-EN 1982:2008 Copper and copper alloys. Ingots and castings.
PN-EN ISO 228-1: 2005 Pipe threads where pressure tight joints are made on the threads.
Dimensions, tolerances and designation
PN-EN ISO 4762:2006 Hexagon socket headcap screws.
PN-EN ISO 4017:2011 Hexagon head screws.
Product grades A and B.
PN-EN ISO 4014:2011 Hex head bolt. Product grades A and B.
PN-EN ISO 4032:2013 Hexagon regular nuts (style 1). Product grades A and B.
PN-EN ISO 7091:2003 Plain washers. Normal series. Product grade C
PN-ISO 1629: 2005 Rubbers and lattices. Nomenclature.
PN-EN ISO 1873-1: 2000 Plastic materials. Polypropylene (PP) moulding and extrusion materials.
Designation system and basis for specifications.
PN-EN ISO 1872-1:2000 Plastic materials. Polyethylene (PE) moulding and extrusion materials.
Designation system and basis for specifications.
PN-EN ISO 12944-5: 2009 Paints and varnishes. Anti-corrosion protection of steel structures by means of
protective painting systems. Protective paint systems.
2.5 ORDERING REGULATIONS
The inspection coupling is a specific purpose industrial valve, therefore orders must include:
- Part Number (P/N)
- intended use, e.g. for water supply systems;
furthermore:
- nominal diameter — acc. to PN-EN ISO 6708: 1998;

OPERATION AND MAINTENANCE MANUAL 01-2016
6
- nominal pressure, acc. to PN-89/H-02650;
- type of body material — acc. to PN-EN 1561: 2012, ( PN-EN 1563) or PN-EN 1982: 2008
- max. operating temperature — acc. to PN-89/H — 02650.
2.6 MANUFACTURE AND ACCEPTANCE
Inspection couplings with hydrant valve type 8890 are accepted and produced in accordance with: PN-EN
1074-2:2002 (Valves for water supply. Fitness for purpose requirements and appropriate verification tests.
Isolating valves) and PN-EN 12266-1:2012 (Industrial valves. Testing of metallic valves). All valves are leak
tested (100%). The tests include external body tightness and closing tightness.
2.7 MARKINGS
The marking of inspection couplings is defined by the following standards: PN-EN-19: 2005; PN-EN-1074-1:
2002.
The bodies feature markings on the front and back walls of the body chamber. The marking contains the
following data:
- nominal diameter;
- nominal pressure;
- type of body material;
- manufacturer trade mark;
- an arrow showing flow direction.
The location on the valve specified in the documentation features the nameplate which contains the
following data: - manufacturer's company name and logo
- product serial number
- sealing temperature grade
- the Polish Building Mark "B" and/or the CE mark (as applicable)
- product type
3 PROTECTION, STORAGE & TRANSPORT
3.1 PROTECTIVE COATINGS
All inner and outer cast-iron surfaces are protected with electro-deposited epoxy coat. The coat has been
approved for contact with foodstuffs.
The anti-corrosion coating layer minimum thickness is 250µm.
The casting surface is pre-treated for epoxy coating in accordance with the relevant technical documentation and
standard PN-EN ISO 12944-5: 2009.
3.2 PACKAGING
Inspection couplings are placed on pallets and protected with stretch wrap.
3.3 STORAGE
Store the inspection couplings in sheltered rooms.

OPERATION AND MAINTENANCE MANUAL 01-2016
7
3.4 TRANSPORT
Transport the couplings on sheltered vehicles.
Use slings sized from DN80 to DN250 for transport and installation of couplings.
4. ASSEMBLY AND INSTALLATION
4.1. INSTALLATION GUIDELINES
Inspection couplings with hydrant valves type 8890 can be installed in above-ground pipelines in horizontal
orientation, configured as shown in the following figure. The couplings are suitable for joining with the flanged
ends of pipelines with the size equal to that of the valve flanges. Note that the system must not expose the
coupling to bending or tensile stress from loading with the unsupported pipeline sections. It is recommended to
perform installation works considering pipeline compensation due to temperature and pressure. A coupling
assembled and delivered by the manufacturer is ready for installation in the system. Disassembly of the coupling
components without proper care may result in loss of tightness.
4.2 INSTALLATION INSTRUCTIONS
Before installing the fittings, check the technical and commercial documentation, i.e. application for media
and operation parameters of the pipeline, in which they are to be installed. Any change in the operating
conditions must be consulted with the fitting's manufacturer beforehand.
Before attempting to assemble the valve, remove the main bore plugs, check the inner surfaces of the valve
and thoroughly flush with water, if necessary.
Note! If the product is damaged mechanically, do not install it in the pipeline.
The assembly method is shown in the following figure:

OPERATION AND MAINTENANCE MANUAL 01-2016
8
1. Coupling, 2. Pipeline flange, 3. Seal, 4. Fastening bolt, 5. Nut, 6. Washer
4.3 OPERATION
Inspection couplings with hydrant valve type 8890 shall be used in accordance with the requirements for
isolating valves. It is recommended to periodically purge the coupling with fresh water (once a year) to assure
full performance.
For servicing, shutoff valves shall be installed upstream and downstream the coupling. The installation
location shall enable free access to the coupling for servicing and maintenance on the system.
The coupling cannot be situated in a location subject to flooding. The device shall not be subject to
temperatures exceeding the allowable scope of work.
Exceeding the operating limits of the fitting may result in damage that will not be covered by the
suretyship granted by the manufacturer.
4.4 OH&S REGULATIONS
The inspection couplings are eligible for the OHS guidelines and recommendation concerning installation of
pipelines and devices for: water supply stations, heat power plants, water treatment plants, sewage treatment
plants, pumping stations and other facilities, and eligible for the Polish Regulation concerning general OHS laws
(use of personal protective equipment for hands, legs and head, and safety garment), especially at work with low
or high temperature hazard.
Misuse of this product is prohibited.
5 GUARANTEE CONDITIONS
The manufacturer grants guarantee for the product being installed and operated according to this O&MM.
The conditions and period of the guarantee is specified in the guarantee sheet.
Table of contents
Other Jafar Control Unit manuals
Popular Control Unit manuals by other brands
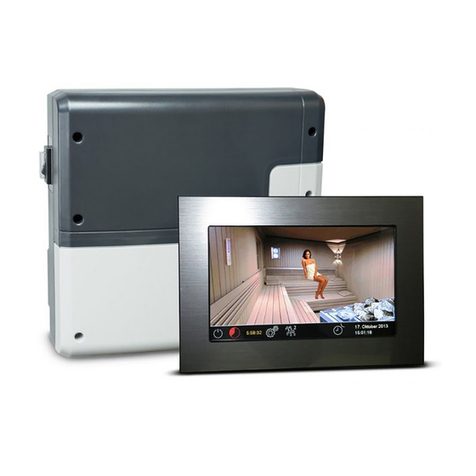
EOS
EOS EmoTouch II + User guide and operating manual
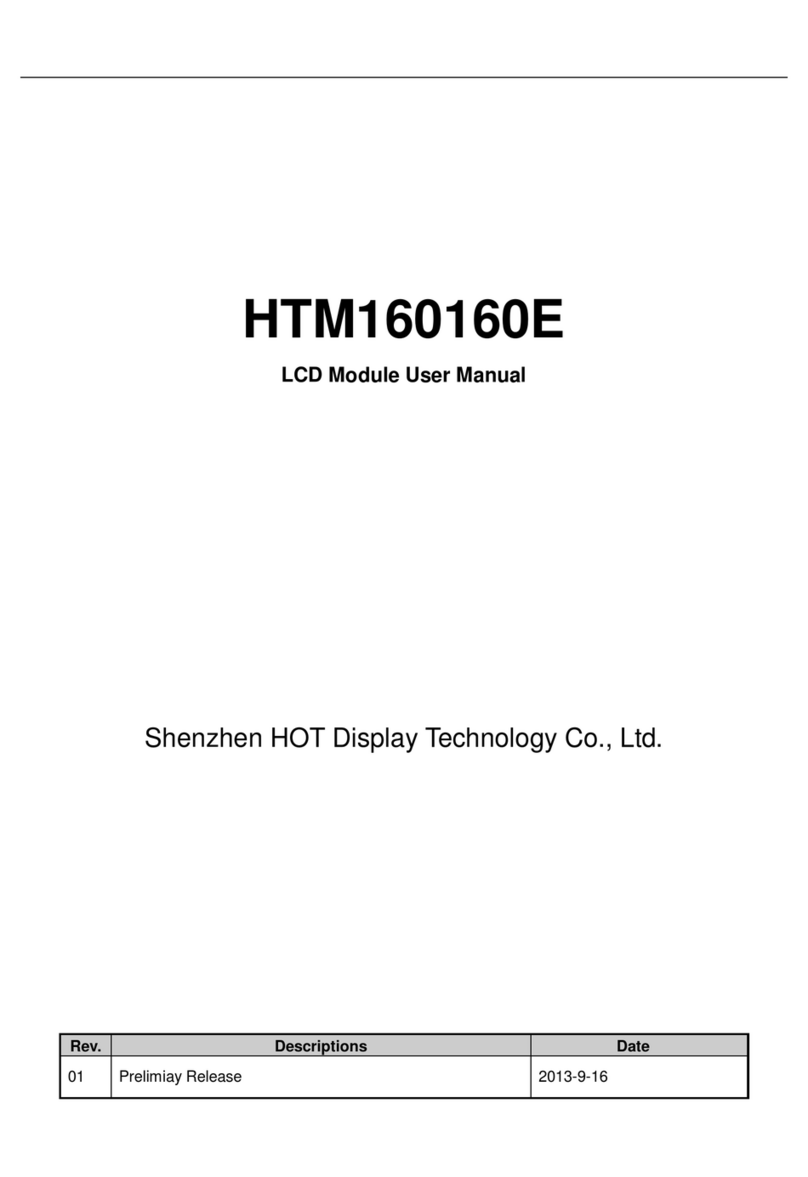
HOT Display Technology
HOT Display Technology HTM160160E user manual
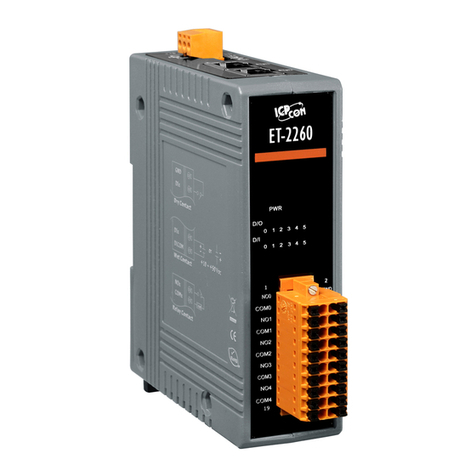
ICP DAS USA
ICP DAS USA ET-2200 Series quick start
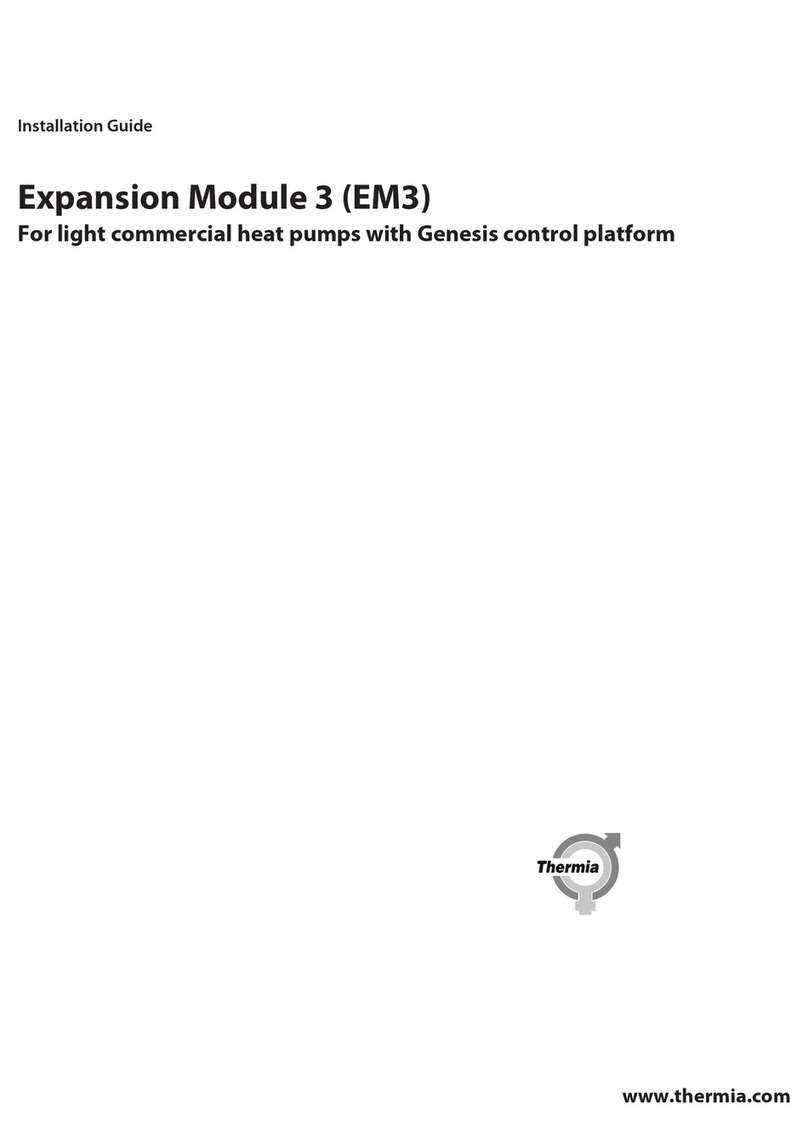
Thermia
Thermia EM3 installation guide
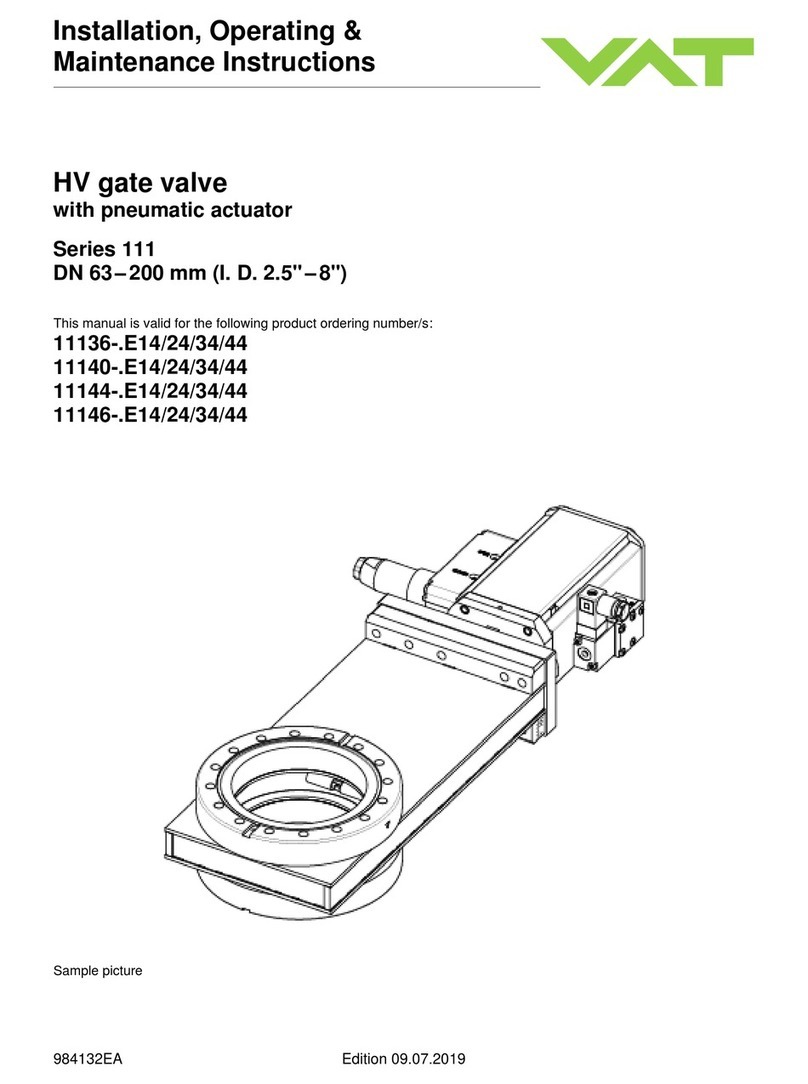
VAT
VAT 111 Series Installation, operating, & maintenance instructions
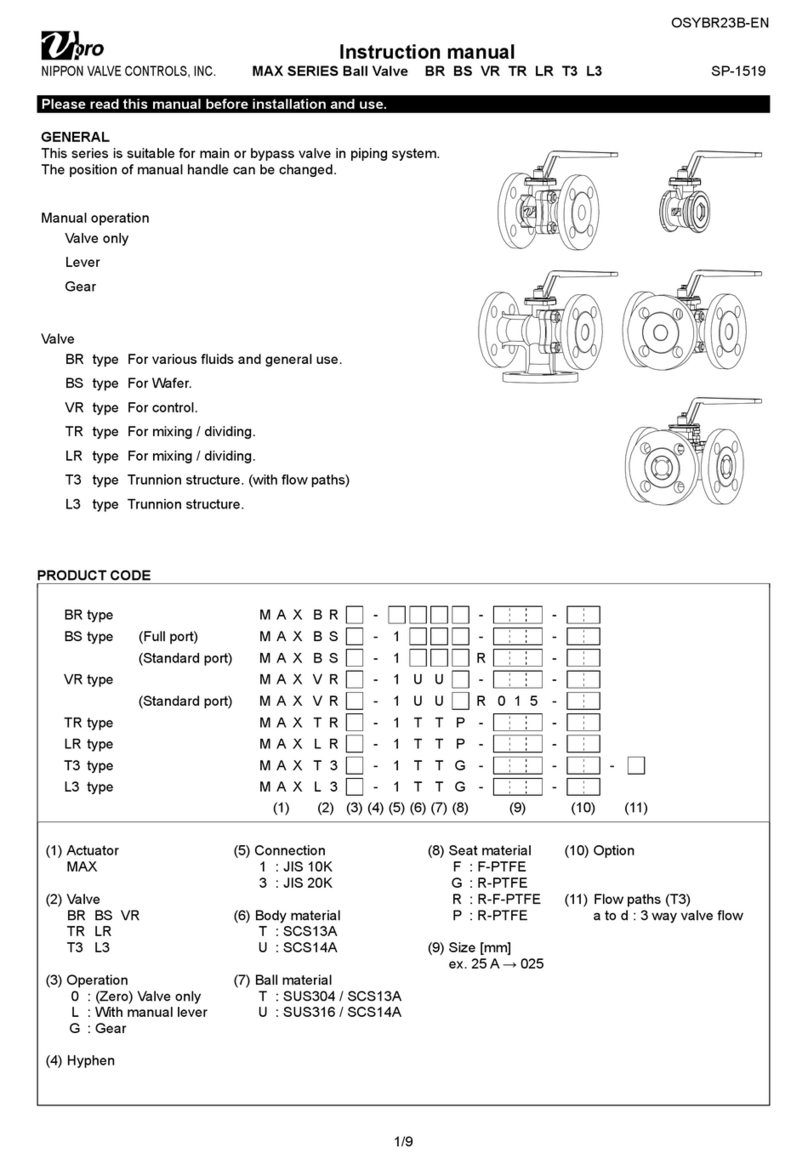
NIPPON VALVE CONTROLS
NIPPON VALVE CONTROLS Vpro MAX Series instruction manual