Jema Autolifte DWC-8-E User manual

Computer wheel balancer
DWC-8-E
Operation and Maintenance Manual
Jema Autolifte A/S
Industrihegnet 2
4030 Tune, Denmark

2
Operation and Maintenance Manual
Passenger car and light truck wheel balancer
MODEL DWC-8-E
Serial number

3
CONTENTS
I. PACKAGING, TRANSPORTATION AND STORAGE
II.INTRODUCTION
Chapter 1 DESCRIPTION OF THE MACHINE
Chapter 2 TECHNICAL SPECIFICATIONS
Chapter 3 SAFETY
Chapter 4 INSTALLATION
Chapter 5 DESCRIPTION OF SUBPROGRAMMES
Chapter 6 NOTES ON OPERATION
Chapter 7 MAINTENANCE
Chapter 8 MACHINE SCRAPPING
Chapter 9 TROUBLESHOOTING
III. SPARE PARTS CATALOGUE

4
JEMA AUTOLIFTE RESERVES THE RIGHT TO MAKE MODERNIZATION CHANGES TO ITS
PRODUCT WITHOUT ANY OBLIGATION TO MAKE SUCH CHANGES IN THIS MANUAL.
I. PACKAGING, TRANSPORTATION AND STORAGE
CAUTION
Any operations related to packaging, lifting, moving, transportation and unpacking must be
performed only by qualified staff.
Packaging
The wheel balancer is dispatched as a complete machine (quick adapter, casing, wheel
balancer). Rubber pads, calibration device and the manual.
The wheel balancer may be packaged in several ways:
- Pallet + stretch film +cardboard box
- Pallet + stretch film
- Pallet + cardboard box
-Stretch film
Transportation
The packaging must be lifted or moved by means of forklift or pallet trucks. Upon delivery of
the load to the place of destination it is required to check if it has not been damaged during
transportation. It is also necessary to check completeness of the delivery against the
waybill. If the shipment is found to be short or damaged during transportation, it is
necessary to immediately report the fact to the person responsible or carrier.
Furthermore, special care must be taken when unloading the shipment.
Storage
The machine should be stored in a dry and dust-free place.

5
II. INTRODUCTION
WARNING
This manual is addressed to workshop staff who are authorised to operate a wheel balancer (an
operator) as well as to workers performing on-going maintenance; read this manual thoroughly
before starting unpacking and operation of the wheel balancer. The manual contains important
information pertaining to:
PERSONAL SAFETY of operators and maintenance workers,
OPERATION OF THE WHEEL BALANCER,
Storage of the manual
The manual constitutes an integral part of the wheel balancer and should be kept near it at all
times, even if the machine is sold.
The manual must be kept near the machine in a readily and immediately accessible location. The
Operators and maintenance staff must have an immediate access to the manual at all time.
CAUTION
IT IS PARTICULARLY RECOMMENDED TO READ THOROUGHLY AND REPEATEDLY
CHAPTER 3 WHICH CONTAINS IMPORTANT INFORMATION AND WARNINGS RELATED TO
SAFETY.
The machine was designed and created according to the following documents:
Directives 2006/42/CE, 2006/95/CE, 2004/108/CE and
Polish standards adequate European regulations:
- PN-EN ISO 12100-1:2005 Safety of machinery. Basic concepts, general principles for design. Part 1: Basic
terminology, methodology
- PN-EN ISO 12100-2:2005 Safety of machinery.. Basic concepts, general principles for design. Part 2: Technical
principles (orig.)
- PN-EN 61000-6-3:2002 Electromagnetic compatibility (EMC). Part 6-3: Generic standards. Emission standard for
residential, commercial and light industrial (orig.)
- PN-EN 61000-6-4:2002 Electromagnetic compatibility (EMC). Part 6-4: Generic standards. Emission standard for
industrial environments (orig.)
- PN-EN ISO 13857:2008 Safety of machinery. Safety distances to prevent reaching the upper limbs and lower the
danger zones (orig.)
- PN-EN 349+A1:2008 Safety of machinery. Minimum gaps to avoid crushing of parts of human body.
- PN-EN 60204-1:2006 Safety of machinery. Electrical equipment of machines. Part 1:General requirement(orig.)
- PN - EN 61293 / 2000 Marking of electrical equipment with ratings related to electrical supply - Safety
requirements;
- PN-EN 983+A1:2008 Safety of machinery - Safety requirements for hydraulic and pneumatic systems and their
components-Pneumatics (orig.)
- PN - EN 61204 / 2001 Low voltage DC - Properties and safety requirements;
- PN-EN ISO 11201:1999 Acoustics - Noise emitted by machinery and equipment - Measurement levels of sound
pressure emission at a work station and other specified positions by engineering method .
- PN-EN 50419 -1:2008 Marking of electrical and electronic equipment in accordance with Article 11 (2) of
Directive 2002/96/CE (WEEE)
- PN-EN 61190-1 -3:2008 Materials for connecting electronic components - Part 1-3: Particular requirements for
solders for electronic applications and solders with fluxes or without fluxes for soldering
electronic components .
- PN-EN 61760-1 :2006 Surface mounting technology - Part 1: Method qualification standard components for
surface mount (SMD)

6
CAUTION
Lifting, transportation, unpacking, assembly, installation, start-up, preliminary adjustment, testing,
maintenance do not require presence of service workers, but must be performed with special
care.
Jema Autolifte shall not be liable for any personal injuries or damages of vehicles or any
other objects, if any of the aforementioned operations have been performed in a manner
non-compliant with this manual, or if the wheel balancer has been used improperly.
The manual includes only these maintenance and safety aspects which may help an operator or
maintenance worker to understand better the construction and operation of the wheel balancer as
well as to use it most efficiently.
In order to understand the terminology used in the manual, the operator must have specific
experience in workshop, service, maintenance and repair works, ability to interpret correctly the
drawings and descriptions included herein and knowledge of general and specific safety
regulations applicable in the country of installation.
The word “operator” used in this manual should be understood as follows: OPERATOR: a person
authorised to operate the wheel balancer.

7
1
CHAPTER 1 DESCRIPTION OF THE MACHINE
The wheel balancer DWC-8-E is intended to be used to balance dynamically passenger car and
light truck wheels within one measuring run.
1.power switch
2.distance gauge
3. rubber pads
4. feeder
5. quick adapter
6. keyboard
7.foot brake pedal
8. calibration device
Indicator screen
Fig. 1

8
Description of keyboard (fig. 1 and 2)
Verbal messages generated by the wheel balancer upon pressing a button
are provided in square brackets.
Button setting the width of a wheel to be balanced [WIDTH]
Button setting diameter and distance of a wheel to be balanced
[DIAMETER] or [DISTANCE]
Button of selection of weights mounting manner with diode
signalisation [RIM TYPE CHANGE]
Memory button M1 –M3 [MEMORY READOUT]
Button changing parameters of distance, diameter, distance of a wheel to be balanced
(decreasing the values)
Button changing parameters of distance, diameter, distance of a wheel to be balanced
(increasing the values)
Button deleting the result of the last measurement [NEW MEASUREMENT]
Button of the wheel balancer calibration [CALIBRATION]
Button starting the “hidden weight” programme
Button of calculation of imbalances [CALCULATION OF IMBALANCES]
Button of selection of the cut-off threshold [THRESHOLD CHANGE] —with diode
signalisation
Function button
CAUTION:
Every instance of pressing any of the buttons is confirmed by a sound
signal.
programme 1:
both weights clipped to the rim edge
programme 2:
both stick-on weights
programme 3:
one weight clipped on the inner correction plane; the other weight
stuck to the outer correction plane
programme 4:
static balancing (for thin rims, with one weight), not recommended
for car wheels
programme 5:
both weights stuck to inner side of the rim
programme 6:
one weight attached on the inner correction plane; the other weight
stuck to the inner side of the rim

9
WARNING
The wheel balancer was designed and manufactured to be used to dynamically balance
passenger car and light truck wheels. It is prohibited to use it in any other way. The wheel
balancer should not be used to wash wheels.
CHAPTER 2 TECHNICAL SPECIFICATIONS
Technical data
-max. tyre diameter 0.9 m
-rim diameter capacity 10” – 30”
-rim width capacity 2” –15”
-weight imbalance volume indications accuracy 1g
-weight imbalance placement signalisation accuracy 3 degrees
-measurement time 6–7 sec.
-weight of the machine ca. 50 kg
-machine dimensions: with adapter 77x60x33 cm
-wheel weight capacity up to 60 kg
-shaft rotational speed (during measurement) 95–130 rpm
-shaft rotational speed (calibration with a wheel) 115 rpm
-shaft rotational speed (calibration with device) 125 rpm
-power supply 230 V / 50 Hz

10
CHAPTER 3 SAFETY
WARNING
The following chapter must be read in its entirety, since it provides important information
concerning danger for the operator and other people in the case of improper use of the
machine.
Explanations concerning threats and hazards that may occur during operation and
maintenance of the wheel balancer as well as general and specific precautions intended to
eliminate the potential dangers are provided below.
Before starting work with DWC-8-E, it is necessary to read carefully and understand these
instructions.
WARNING
The wheel balancer DWC-8-E is intended to be used to balance passenger car and light truck
wheels within one measuring run.
It is prohibited to use it in any other way. In particular, the wheel balancer is not suitable for:
-using for purposes other than balancing
- balancing heavy truck wheels
CAUTION
Jema Autolifte and vendor shall not be liable for any personal injuries or damages to
vehicles or any other objects caused by improper or unauthorised use of the wheel
balancer.
CAUTION
IT IS NOT RECOMMENDED TO USE THE WHEEL BALANCER WITHOUT PRIOR
CLOSURE OF THE WHEEL GUARD.
FAILURE TO MEET THE AFOREMENTIONED REQUIREMENTS MAY RESULT IN
SERIOUS PERSONAL INJURIES AND IRREPARABLE DAMAGE TO THE WHEEL
BALANCER AND THE WHEEL. ______________________________________________
General precautions
The operator and maintenance worker are required to follow the safety regulations applicable
in the country of the machine installation.

11
The manual contains the following captions concerning safety:
Danger —indicates a possibility of danger which may lead to serious injuries
Warning —indicates dangerous situations and/or types of manoeuvres which may lead to
major or minor injuries
Caution —indicates dangerous situations and/or types of manoeuvres which may lead to
minor injuries and/or damage to the wheel balancer, wheel or any other objects
Electric shock risk —a specific caption placed on the machine where there is particularly
high risk of electric shock.
Hazards for staff
The paragraph describes possible threats for the operator or any other people present near
the wheel balancer caused by its improper use.
Risk of hitting
There is a risk of hitting the component of the machine.
In the event when the guard is opened, the staff must take special care not to hit themselves
at the components of the machine.
Risk of wheel getting loose
Before starting any balancing procedure, it is very important that the wheel is mounted on the
adapter.
CAUTION!
NEVER REMOVE THE WHEEL DURING OPERATION OF THE MACHINE.
NEVER LEAVE THE MACHINE UNATTENDED WHILE IT IS IN OPERATION.
Risk of slipping
Danger caused by contamination of the floor around the machine with lubricants.

12
AREA UNDER THE WHEEL BALANCER AND IN ITS DIRECT
SURROUNDING AS WELL AS THE ADAPTERS MUST BE KEPT CLEAN AT
ALL TIMES.
Immediately remove any oil stains.___________________________________
Risk of electric shock
Danger of electric shock in the areas where electric wiring is routed.
It is forbidden to use water or vapour atomizers (high pressure washing equipment),
solvents or paints near the machine. These substances must not be allowed to spread to
the control panel.
Dangers caused by inadequate lighting
The operator and maintenance worker must be able to inspect if all the areas of the
machine are correctly and evenly lit, in accordance with the regulations applicable in the
country of installation.
Risk of damaging a component of the wheel balancer while it is in operation
In order to manufacture a reliable and safe wheel balancer, Jema Autolifte used appropriate
materials and manufacturing techniques adopted to the specified application of the
machine. However, it should be noted that the wheel balancer must be operated in
compliance with Jema Autolifte’s recommendations. It is required to perform technical
inspections with a specified frequency (upon expiry of the warranty period) and
maintenance works described in Chapter 7 “MAINTENANCE”.
Never exceed admissible weight capacity of the balancer —i.e. 60 kg.
IMPORTANT
Every use of the wheel balancer in a manner contrary to its intended purpose shall
entail the danger of causing serious injuries and accidents.
Therefore, it is particularly significant to strictly apply any and all recommendations
concerning operation, maintenance and safety, stipulated in this manual.

13
CHAPTER 4 INSTALLATION
WARNING
The following operations may be performed only by persons who were previously trained to
operate the machine to which this manual pertains.
In order to prevent potential damage to the balancer or hazard of causing personal injuries, it
is necessary to carefully follow the instructions below. It must be ensured that no people are
present within the working field.
Requirements regarding installation
The wheel balancer must be installed in the safe distance from walls, columns and other
devices.
The site must be equipped in advance with the power supply source and compressed air
system. The wheel balancer may be placed on any even, stable and dry floor.
All the parts must be uniformly lit with the light sufficient to safely perform all the operational,
adjustment and maintenance operations mentioned in this manual. Presence of any shaded
areas, light reflections and blinding light is inadmissible; any situations which may cause eye
strain should be avoided.
Lighting must be installed in accordance with the regulations applicable in the place of
installation (the lighting contractor shall bear this liability).
Prior to installing, all the parts must be unpacked and inspected for any signs of damage.
Issues regarding manoeuvring and lifting are discussed in the chapter “Packaging,
transportation and storage”.

14
Place of installation
The wheel balancer DWC-8-E must be installed in a closed and dry place which will be heated in
the autumn and winter period. The machine should be installed on a stable level floor. The wheel
balancer should be installed on four rubber pads enclosed which should be placed under the flat
legs welded to the machine base. The machine should not be screwed to the floor.
Assembly of the adapter
Before mounting the adapter, it is necessary to clean thoroughly the cone areas of shaft “1” and
adapter “2” with an oil-wetted cloth. Mount the adapter onto the shaft so as to maintain the
position of markers “3” on the shaft rod and adapter as in fig. 3. Tighten up the adapter to the
shaft with the use of screw “4”.
CAUTION:
Careful cleaning of the cone areas and maintenance of the adapter position against the
shaft (overlapped markers) is one of the conditions for proper wheel balancing.
Wheels with a centre hole should be mounted in the standard adapter of the balancer.
Fig. 3 Adapter of the balancer, without the nut, cones and clamping sleeves

15
1
b
1
0
9
Components of the adapter set
1 –
adapter; a –stud, b –flange
2 –screw for mounting the adapter on the shaft
3 –spring
4 –clamp nut
5 –centring cone No 2 1 43–82 mm 06.04.046 —W-St-6
6 –centring cone No 2 65–111 mm 06.04.047 —W-St-7
7 –nut clamp
8 –centring disc No 1 (with double cone)** 125–145 mm 06.04.017 W-St-5
9 –centring disc No 2 (with double cone)** 145–165 mm 06.04.009 W-St-2
10 –centring cone No 3** 40–57 mm 06.04.046 W-St-3
11 –reduction ring of the adapter**
12 –centring disc No 4 (with double cone)** 110–125 mm 06.04.008 W-St-4
** additional accessories

Clamp nut
16
POSITION L (LOOSE) POSITION D (CLAMP)
Fig. 5
Lever of the clamp nut revolves against the nut body within the limits indicated by a notch in the
body (positions L and D).
In the L position (LOOSE) the nut may be freely moved along the threaded stud of the adapter.
In the D position (CLAMP) the nut may be screwed onto the threaded stud.

17
Mounting the wheel on the adapter
Slide the wheel onto the adapter stud and position it with the edges of centre hole on the
centring cone catch. Set the nut lug in the position LOOSE and screw the nut to the wheel until
stop. Placing one’s thumbs on the nut rod (as in fig. 6) move lugs to the right to the position
CLAMP and tighten up the nut, pressing the wheel towards the faceplate.
Tightening up the nut
In order to remove the wheel from the adapter, it is necessary (as in fig. 7) to move lugs to the
left to the position LOOSE and loosen the nut halfway. It will get loosened and may be removed
from the stud and the wheel may be removed from the adapter.
Fig. 7
Loosening the nut

18
Adapter structure and equipment enabling to mount wheels with various rim shapes and centre
hole diameters.
1 - use of cone 5 or 6 with centring from the inner side of the rim:
- nut of adapter “4” should be with a clamp “7” (see fig. 4 and 11)
- the spring of the cone should be placed in such a way so that the smaller diameter of the
springs supported against the cone base (fig. 10)
2- - use of cone 5, 6, 8, 9, 10 with centring from the outer side of the rim (as in fig. 8 and fig. 9)
- nut without clamp
-adapter without spring

19
Disassembly of the nut clamp
Fig. 11
If in order to mount the wheel using centring discs and
cones in the centring system from the outer side of the
rim, it is required to remove the clamp from the nut.
To remove the clamp, it should be pulled axially so that it
is removed from the catch; it may be carefully levered
with a flathead screwdriver.
To place the clamp back, it should be pushed onto the nut
catch.
Electrical connection of the wheel balancer
CAUTION:
Plug the feeder cable into the socket 230V/50Hz.
CAUTION:
SINCE UNEXPECTED WARMING OF FROZEN METAL AND PLASTIC SOLID GENERATES
CONSIDERABLE QUANTITIES OF WATER VAPOUR CONDENSATE, IT IS FORBIDDEN TO
PLUG IN COOLED WHEEL BALANCER TO THE POWER NETWORK BEFORE THE LAPSE
OF 2 TO 3 HOURS REQUIRED TO DRY THE ELECTRONIC ELEMENTS AND THEIR
REACHING THE WORKSHOP TEMPERATURE. FAILURE TO COMPLY WITH THIS
REQUIREMENT MAY CAUSE DAMAGE TO THE WHEEL BALANCER. And with faulty
electrical installation it may cause electric shock.

20
CHAPTER 5 DESCRIPTION OF SUBPROGRAMMES
5.1 PROGRAMMING THE WHEEL BALANCER COMPUTER
Operation of the wheel balancer computer
The inspection shall be performed with the wheel mounted (tolerably only the rim) on the shaft.
Connection of the wheel balancer computer
Press power switch “1” on the wheel balancer Fig. 2 After completing the control testing, which is
signalled with a sound, the measuring indicator screen shall display the icons as in Fig. 1.
5.1.1 Entry of WIDTH parameter
Press the button on the keyboard. The indicator screen displays symbol and
the value of width recently entered to the memory. By pressing button and it
is possible to adjust this parameter, every half an inch in a range between 2 and15 inches.
5.1.2 Entry of DIAMETER parameter
Press the button on the keyboard. The indicator screen displays symbol and
the value of diameter recently entered to the memory. By pressing button or it is
possible to adjust this parameter, every inch in a range between 10 and 30 inches.
5.1.3 Entry of DISTANCE parameter
Press the button on the keyboard. The indicator screen displays symbol and the
value of distance recently entered to the memory. Move controller “1” closer to rim “2” Fig. 12.
Read the value of distance and enter it to the memory by pressing or
Table of contents
Other Jema Autolifte Wheel Balancer manuals
Popular Wheel Balancer manuals by other brands

Sun Microsystems
Sun Microsystems SWB 300 Operator's manual

Bosch
Bosch FWA 4630 Original instructions
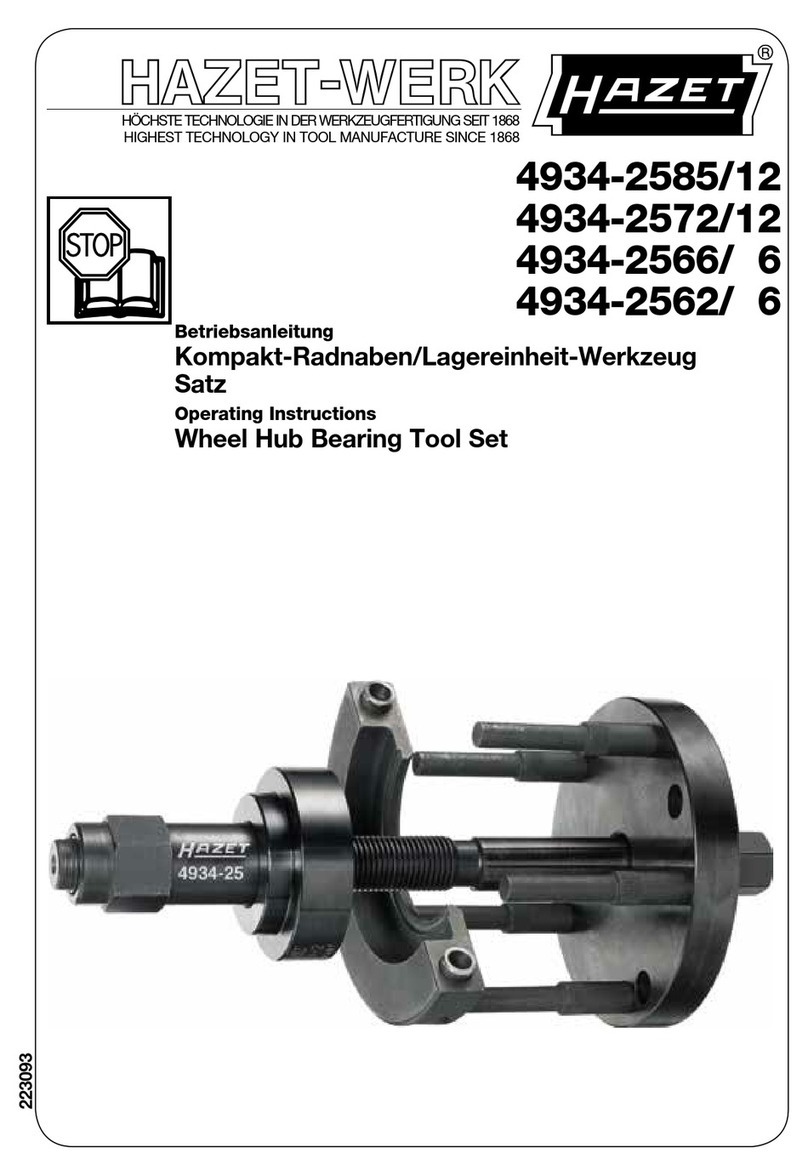
HAZET-WERK
HAZET-WERK HAZET 4934-2585/12 operating instructions

Eagle
Eagle EB-1200 Instruction & maintenance manual
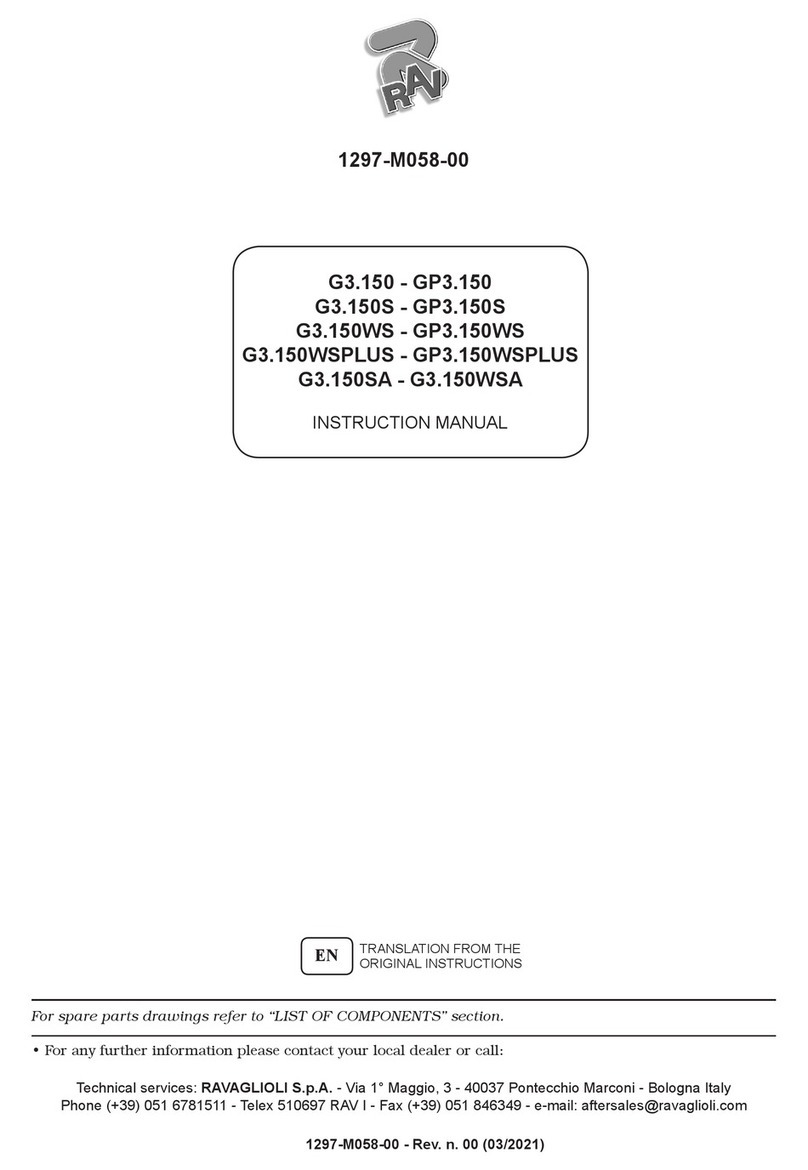
rav
rav G3.150 Translation from the original instructions

Hunter
Hunter HD Elite Operation instructions