John Bean VPI System User manual

FOR:
PASSENGER CAR & LIGHT TRUCK WHEELS
OPERATION INSTRUCTIONS
Form 5787-1
Rev 04/19/2001
VPI SYSTEM I
COMPUTER WHEEL BALANCER


SAFETY INFORMATION
For your safety, read this manual thoroughly
before operating the JBC VPI System I Wheel Balancer
The JBC VPI System I Wheel Balancer is intended for use by properly trained automo-
tive technicians. The safety messages presented in this section and throughout the
manual are reminders to the operator to exercise extreme caution when servicing tires
with these products.
There are many variations in procedures, techniques, tools, and parts for balancing
tires, as well as the skill of the individual doing the work. Because of the vast number
of wheel and tire applications and potential uses of the product, the manufacturer can-
not possibly anticipate or provide advice or safety messages to cover every situation.
It is the automotive technician's responsibility to be knowledgeable of the wheels and
tires being serviced. It is essential to use proper service methods in an appropriate and
acceptable manner that does not endanger your safety, the safety of others in the work
area or the equipment or vehicle being serviced.
It is assumed that, prior to using the Model VPI System I Wheel Balancer, the
operator
has a thorough understanding of the wheels and tires being serviced. In addition, it is
assumed he has a thorough knowledge of the operation and safety features of the
rack, lift, or floor jack being utilized, and has the proper hand and power tools neces-
sary to service the vehicle in a safe manner.
Before using the Model VPI System I Wheel Balancer, always refer to and follow the
safety messages and service procedures provided by the manufacturers of the equip-
ment being used and the vehicle being serviced.
IMPORTANT !! SAVE THESE INSTRUCTIONS -- DO NOT DISCARD !!

Page 2
IMPORTANT SAFETY INSTRUCTIONS
When using this equipment, basic safety precautions should always be followed,
including the following:
1. Read all instructions.
2. Donotoperateequipmentwithadamagedpowercordoriftheequipmenthasbeen
damaged - until it has been examined by a qualified authorized service technician.
3. If an extension cord is used, a cord with a current rating equal to or more than that
of the machine should be used. Cords rated for less current than the equipment
mayoverheat. Careshouldbetakentoarrangethecordsothatitwillnotbetripped
over or pulled.
4. Always unplug equipment from electrical outlet when not in use. Never use the
cord to pull the plug from the outlet. Grasp plug and pull to disconnect.
5. To reduce the risk of fire, do not operate equipment in the vicinity of open
containers of flammable liquids (gasoline).
6. Keephair,loosefittingclothing,fingersandallpartsofthebodyawayfrommoving
parts.
7. Adequate ventilation should be provided when working on operating internal
combustion engines.
8. To reduce the risk of electric shock, do not use on wet surfaces or expose to rain.
9. Do not hammer on or hit any part of the control panel with weight pliers.
10. Do not allow unauthorized personnel to operate the equipment.
11. Do not disable the hood safety interlock system or bypass the intended operation.
12. Use only as described in this manual. Use only manufacturer’s recommended
attachments.
13. Always securely tighten the wing nut before spinning the shaft.
14. ALWAYS WEAR SAFETY GLASSES. Everyday eyeglasses only have impact
resistant lenses, they are NOT safety glasses.
15. Balancer is for indoor use only.
SAVE THESE INSTRUCTIONS

Page 3
John Bean VPI System I Operators Manual
TABLE OF CONTENTS
General Safety Instructions Pages 1 & 2
1.0 Introduction Page 4
1.1 Safety Notice Page 4
1.2 Balancer Application Page 4
1.3 Specifications Page 5
1.4 Balancer Features Page 5
1.5 Standard Accessories Page 6
1.6 Optional Accessories Page 6
1.7 Dimensions Of The Machine Page 7
1.8 Installation Area Page 7
1.9 Installation Instructions Page 7
2.0 Shaft Adapter Installation Page 7
2.1 Wheel Guard Installation Page 8
2.2 Electrical Installation Page 8
2.3 Perform a User Calibration Page 8
3.0 Terminology Page 9
4.0 Balancer Operation Page 10
4.1 Inspection Check list Page 10
4.2 Wheel Mounting Page 10
4.2.1 Mounting of Standard Wheels Page 10
4.2.2 Mounting of Light Truck Wheels Page 11
4.3 Mode Selection Page 11
4.3.1 Weight Placement Modes Page 11
4.4 Selecting Operator Preferences Page 12
4.4.1 Fine Balance Mode Page 12
4.4.2 Ounce /Grams Conversion Page 12
4.4.3 Inch/Millimeter Conversion Page 12
4.4.4 Selection of Operator A/B Page 12
4.5 Entering Rim Parameters Page 13
4.5.1 Entering Distance (offset) with SAPE Page 13
4.5.2 Entering Rim Diameter Page 13
4.5.3 Entering Rim Width Page 13
4.5.3.1 Manual Distance Entry Page 13
4.6 Correcting the Imbalance Page 14
4.7 Verifying Results Page 14
4.8 Vibration Problems Page 14
5.0 Matching Program Page 15
6.0 Optimization Program Page 17
7.0 Alu-S Program Page 18
8.0 Spoke Mode Page 19
9.0 Split Weight Mode Page 20
10.0 User Shaft Calibration Page 21
11.0 Distance Gauge Calibration Page 22
11.0 Explanation of "F" Codes Page 23
12.0 Maintenance Page 23
13.0 Trouble Shooting Page 23

Page 4
1.0 INTRODUCTION
Congratulations on purchasing the VPI System I computer wheel balancer. This wheel balancer is
designed for ease of operation, accuracy, reliability and speed. With a minimum of maintenance and
care your wheel balancer will provide many years of trouble-free operation.
Instructions on use, maintenance and operational requirements of the machine are covered in this
manual.
STORE THIS MANUAL IN A SAFE PLACE FOR FUTURE REFERENCE.
READ THIS MANUAL THOROUGHLY BEFORE USING THE MACHINE.
1.1 SAFETY NOTICE
This manual is a part of the balancer product.
Read carefully all warnings and instructions of this manual since they provide important information
concerning safety and maintenance.
1.2 BALANCER APPLICATION
The John Bean wheel balancer model VPI System I is intended to be used as a device to balance car,
and light truck wheels within the following range:
Maximum wheel diameter : 44” (1117mm)
Maximum wheel width : 16” (530mm)
Maximum wheel weight : 120lbs (54 kg)
This device is to be only used in the application for which it is specifically designed.
Any other use shall be considered as improper and thus not reasonable.
The manufacturer shall not be considered liable for possible damages caused by improper, wrong or
non reasonable use.

Page 5
John Bean VPI System I Operators Manual
1.3 VPI System I SPECIFICATIONS
Computerized digital wheel balancer for car, light truck
wheels.
Weight Imbalance Accuracy .1 oz / 2 grams
Weight Placement Resolution ± .7 degrees
Weight Imbalance Resolution:
Roundoff Mode .25 oz / 5 grams
Non-Roundoff Mode .05 oz / 1 gram
Max. Shaft Weight Capacity 120 lbs / 54 kg
Max.Tire Diameter 44" / 1117 mm
Rim Width Capacity 1.5"-15" / 76 mm - 406 mm
Max. Tire Width 19” / 482 mm
Rim Diameter Capacity 8"-20" / 152 mm-660 mm
Balancing Cycle Time. 7 seconds or less
Shaft Speed at calculation >100 RPM
Electrical 115vac, 1ph, 50-60Hz, 8A
Required Work Area 54” x 52” (1372 x 1321 mm)
Shipping Weight, complete 325 lbs/147kg
ShippingDimensions 52.75”h 41.5”w 37”d
Machine Dimensions 54”h 45”w 48.5”d
Actual Weight with Accessories 309 lbs / 140 kg
Operating Temperature Range 32-122F / 0-50C
1.4 FEATURES
ACCURACY
• Weight placement accuracy to as low as ± .7°
• Weight imbalance accuracy to 2 grams.
• Self test check with every power up cycle.
• Fast operator calibration.
• Pre-programmed Error Codes indicate procedural
errors or safety concerns.
SPEED and DURABILITY
• Automatic distance entry. Simply touch the distance
arm to the wheel, the distance parameter is auto-
matically entered.
• Quickclamp speednut reduceswheel mountingtime.
• Capturedback springeliminateshaving tohandle the
backing spring.
• Quick cycle time.
• Automatic recalculation if weight positions are
changed. No need for re-spinning the wheel.
• Common 40 mm diameter mounting shaft.
• Weight pocket storage tray.
• Easy-to-Read Data display.
• Easy weight tray access.
SOFTWARE VERSATILITY
• Both dual weight Dynamic and single weight Static
capability.
• MatchBalance programfor reducingweightrequired.
• Built-in spin counter for monitoring balancer
productivity.
• Service code access to all Balancer electronic func-
tions for fast, easy diagnosis.
• Operator selectable roundoff mode.
• 5 Aluminum Modes
• Alu-S mode
• Hidden Weight (Spoke) mode
• Split Weight mode

Page 6
1.5 STANDARD ACCESSORIES
Standard accessories included with the VPI System I
are:
1 EAM0003J08A Cone, 85-132 mm / 3.3”-5.2”
2 EAM0003J07A Cone, 71-99 mm / 2.8”-3.9”
3 EAM0003J06A Cone, 56-84 mm / 2.2”-3.3”
4 EAM0003J05A Cone, 43-63 mm / 1.7” - 2.5”
5 8 - 02040A2 Cup - Pressure
6 8 - 02040A1 Disk - Pressure
7 8 - 02140A Quick Nut
8 EAM0005D40A Weight - Calibration
9 EAM0005D15A Stub Shaft
10 EAA0247G21A Caliper - Rim Width
11 EAC0060G02A Flange - Cover, Hook
12 EAM0006G01A Pin - Accessory
Figure 1
Figure 2
1.6 OPTIONAL ACCESSORIES
Weight Pliers P/N 26 (Figure3).
Versatile weight hammer/plier. In addition to ham-
meringon weightand usedweightremoval, the
model
26
hammer/plier can beused to reshapewornweight
clips and trim weight to size.
Figure 3

Page 7
John Bean VPI System I Operators Manual
PRE-INSTALLATION CONSIDERATIONS
1.7 DIMENSIONS OF THE MACHINE
Figure 4 - Actual Footprint Dimensions.
1.8 REQUIRED INSTALLATION AREA
Makesure that fromthe operating position theuser can
see all of the machine and the surrounding area.
The operator should prevent non authorized persons
and/or objects from entering the area which may cre-
ate potential hazards.
Themachine should be installed on astable level floor.
Do not install the machine on a uneven floor.
If the balancer is to be installed on a raised floor, the
floor must have a capacity of at least 110lbs per sq ft.
(5000 N/m² - 500 kg/m²).
It is not required to secure the machine to the floor.
Install the machine in a dry, covered area.
Theinstallation of the machine requiresaworking area
of at least 54” x 52” (1372 x 1321 mm) (Figure5).
1.9 INSTALLATION INSTRUCTIONS
CAUTION! CAREFULLY REMOVE THE BALANCER
FROM THE PALLET.
Remove the hardware that secures the machine to
thepallet andslide thebalancer ontothe floorwhere
it is to be installed.
THE UNIT IS HEAVY AND THE WEIGHT IS NOT
EVENLY DISTRIBUTED.
DO NOT LIFT THE BALANCER BY THE SHAFT.
DROPPING THE UNIT MAY CAUSE PERSONAL IN-
JURY OR EQUIPMENT DAMAGE.
2.0 BALANCER INSTALLATION
Mounting the Shaft Adapter
IMPORTANT!
CHECK THAT THE SURFACES ARE PERFECTLY
CLEAN AND NOT DAMAGED. AN INCORRECT
MOUNTING MAY RESULT IN SIGNIFICANT IMBAL-
ANCE.
A. Mount the threaded shaft onto the arbor of the bal-
ancer. Tighten firmly using a screwdriver. (Figure 6).
Figure 6
Figure 5 - Recommended Work Area

Page 8
B. Install the accessory pins (Figure 7). Tighten firmly.
Figure 7
C. Place cones and other accessories onto the acces-
sory pins.
2.1 HOOD GUARD INSTALLATION
The safety hood guard is standard equipment and
must be installed prior to use.
Refer to Figure 8 for hood guard installation.
Parts Required:
(1) Hood Guard Assembly
(1) 3/8” - 16 x 2” HHCS
(1) 3/8” x 16 Keps
Position the hood guard in the raised (up) position.
Slide the hood guard support tube over the frame pivot
shaftprotruding from theright side ofthe balancer cabi-
net.
Line up the mounting holes in both the pivot shaft and
theguardsupport tube.Secure theguard with3/8”hard-
ware.
Figure 8
2.2 ELECTRIC INSTALLATION
ANY ELECTRICAL WIRING MUST BE PER-
FORMED BY LICENSED PERSONNEL.
ALL SERVICE MUST BE PERFORMED BY AN
AUTHORIZED SERVICE TECHNICIAN.
Check on the plate of the machine that the electrical
specifications of the power source are the same as the
machine. The machine uses 115VAC, 50-60Hz, 1Ph,
8.0 Ampere. 230VAC units are available if required.
NOTE:
Any electrical outlet installation must be verified
by a licensed electrician before connecting the bal-
ancer.
NOTE:
This machine performs a self-test routine on start-
up. There will be a delay of several seconds before
the display is activated.
2.3 USER CALIBRATION
Perform the user calibration procedures as instructed
on page 21 and 22 of this manual before placing the
machine in service.

Page 9
John Bean VPI System I Operators Manual
3.0 TERMINOLOGY
Figure 9
Before using the wheel balancer it is suggested that
you become familiar with the terminology and features
of the machine’s components. Refer to Figures 9 and
10 for identification and location.
1. Inside Weight Amount and Function Display
Window - Shows inside or left weight amount and
various operation messages.
2. Position Indicator LEDs - Displays the location
for wheel weight placement.
3. Outside Weight Amount and Function Display
Window Showsoutside orright weightamount and
various operation messages.
4. Weight Mode and Placement Display - Displays
a pictorial reference of the chosen balance mode.
5. Function Button - Used to activate the various
functions. Press this button followed by pressing
the
up
or
down
arrowbuttons untilthe desired num-
ber is displayed. Press the “Enter” button to active
the function.
6. Enter - This key activates whatever selection has
been requested, it also spins the wheel if guard
frame is down.
7. Up and Down Value - Buttons are used to raise or
lowerdisplayed values for parameterentry or func-
tion code activation.
NOTE: Rotating the shaft in either direction will
also vary displayed values.
8. Cancel - Pressing this key interrupts any process.
9. Mode Selection - A series of placement locations
for custom weight location. Useful for the wide va-
riety of custom wheels on today's market.
10. Rim Width - Press this key to enter the rim width.
Use the rim width calipers for measurement.
11. Rim Diameter - Enter the rimdiameterafter press-
ingthiskey.Readthesizestatedonthetiresidewall.
12. ALU-S and Spoke Mode - Activates the ALU-S or
Spoke Mode. Each time this button is pressed pro-
gramming toggles between the two.
13. Rim Offset -This key is usedtoenter the rim offset
positionusingthenumbersfromthedistancegauge.
14. Multi-Operator Selection - This key toggles be-
tween four operators designated as a, b, c, and d.
Wheel parameters are recalled upon command.
15. Display - Easy to read, user friendly display fea-
turing large LEDs and one button functions.
16. Weight Storage Tray - Generous storage for a
variety of weight profiles and sizes as well as built
instoragepockets forthe standardcenteringcones.
17. Accessory Storage - Four sturdy side mounted
pegs are supplied for storage of additional acces-
sories.
18. Foot Operated Shaft Lock - A foot operated shaft
lock is used to stabilize the shaft during the weight
placement process.
19. Shaft Adapter - A common 40 mm size shaft is
used. The easily removable shaft can be replaced
forservice or during use of certainwheeladapters.
20. Wheel Guard - The standard wheel guard is a
safety feature for prevention of operator injury in
the event of loose weights, debris or wheel mount-
ingfailure. The balanceris programed tospin upon
guard closure as well as brake when the guard is
raised.
21. Semi-Automatic Parameter Arm - Rim distance
is automatically input with the SAPE. The SAPE is
also used in several procedures for determining
accurate rim profiles.
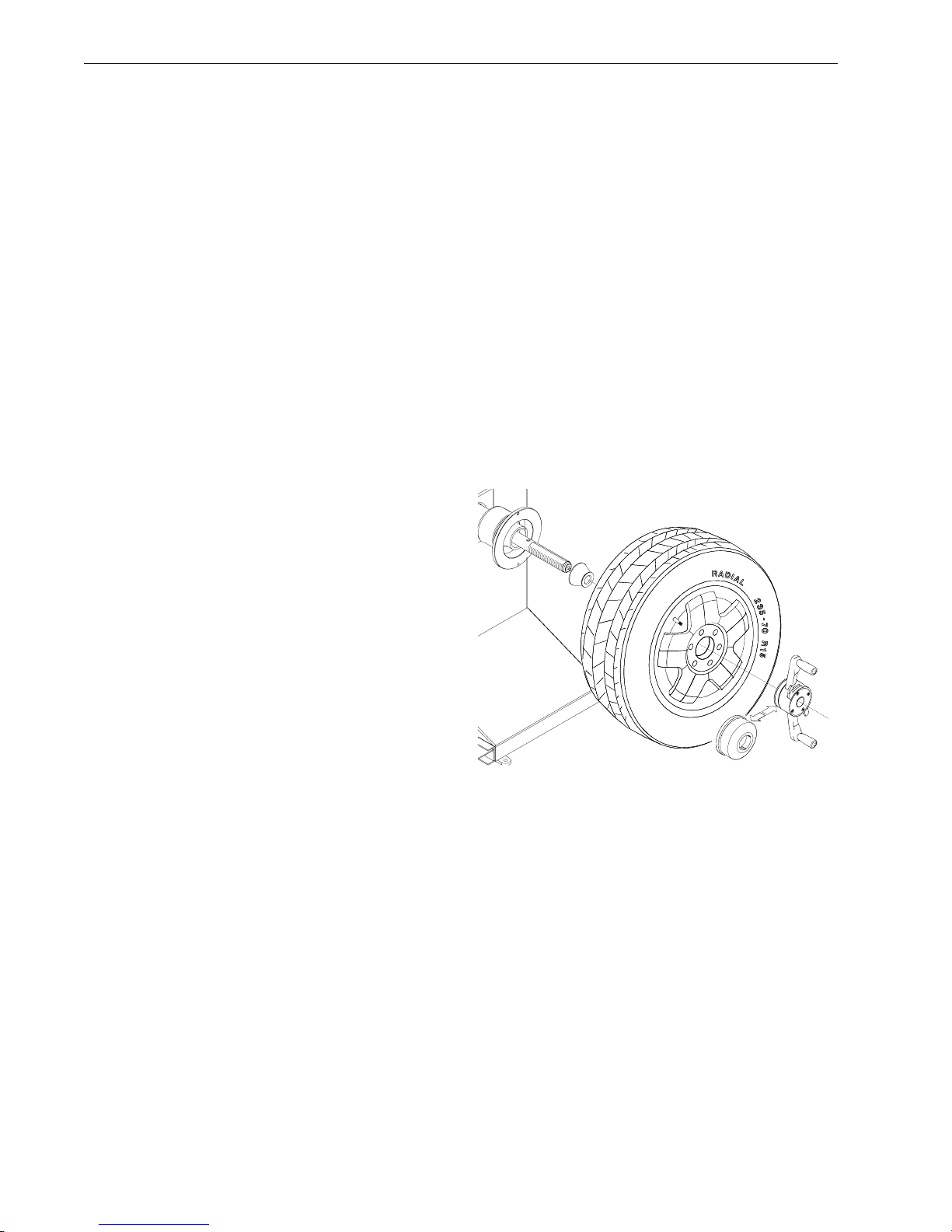
Page 10
4.0 OPERATION OF THE BALANCER
WARNING: Foroperator safety please read
and follow the precautions outlined on
pages 1 and 2 of this manual.
NOTE: Read all instructions before pro-
ceeding with operation of the balancer.
All balancer functions are input into the main computer
through the large easy to read touch panel. Although
each wheel tire assembly differ in some ways all bal-
ancingjobs require basically the sameprocedure. The
order of events to take place are:
1. Inspection of the wheel/tire assembly
2. Mounting wheel onto shaft or adapter
3. Selection of Balancing Mode and Preferences
4. Entry of wheel parameters
5. Spinning the wheel
6. Applying the recommended weight
7. Check spin if desired
8. Dismounting the wheel
The following operation instructions will follow the ba-
sic outline above.
4.1 CHECK LIST - INSPECTION
Observe Before Balancing Wheel
1.Checkforproperairpressure. Ifnotcorrect,inflateto
correct pressure.
2. Check for any foreign material inside tire. If present,
remove before balancing tire.
WATER IS FOREIGN MATERIAL!
3.Removeold weights—old weightsmaybe improper
value or in wrong location.
4.Be sure tire and wheel are freeofexcessive dirt, rust
andlargestones.Usewire brushon backside ofwheel
if necessary.
4.2 WHEEL MOUNTING
Nearlyallstandardwheelsandmanyalloywheelshave
accurately machined center holes, and they should be
mounted with center cones. Accurate balancing de-
pends on accurate mounting of the wheel and correct
seatingoftheconeinthepilothole.Insurethatthewheel
is centered on the shaft exactly as it will be mounted to
the vehicle.
Before starting any balancing procedure it is very im-
portant that the wheel is mounted on the machine with
theproper adaptors.An incorrectcentering of thewheel
will result in considerable imbalance.
There are many types of wheels and John Bean sup-
pliesadaptors ofgood qualityand durabilityfor thelarge
majority.Howeverif youmeetspecial wheelswhichmay
require a specific adaptor, call your authorized John
Bean distributor.
Rims may be divided into these major groups:
1. Car rims with a true center hole.
2. Car rims without a center hole.
3. Car rims with an untrue center hole.
4. Light truck rims.
4.2.1 Standard Wheels (back cone mount)
Mount the wheel as detailed below in Figure 11:
1. Mount proper cone against spring plate.
2. Mount wheel on shaft in the same manner as you
would on the car.
3. Mount pressure cup on shaft and place against
outside of wheel, follow with the Quick-nut.
4. Tighten Quick-nut securely with both hands. To
operate the Quick-nut pull the lock-unlock lever
(Figure 12). Slide the Quick-nut on the threaded
shaft. When in contact with the rim, release the
unlock lever and tighten firmly. To assist in
centering the wheel properly, rotate the wheel on
the shaft while tightening the quick nut.
Figure 11

Page 11
John Bean VPI System I Operators Manual
FAILURE TO TIGHTEN WING NUT SECURELY
MAYRESULTINSERIOUSPERSONALINJURY.
DO NOT USE A HAMMER TO TIGHTEN THE
QUICK NUT.
TO RELEASE THE QUICK NUT, UNSCREW A
FEW TURNS TO REDUCE THE AXIAL PRES-
SURE,THEN PRESSTHE UNLOCKLEVER AND
SLIDE AWAY FROM THE SHAFT.
5.Checkthat thewheel rotatestrue byturning thewheel
several revolutions while noting any excessive runout.
4.2.2 CENTERING LIGHT-TRUCK WHEELS
Anoptional offsetspacer maybe requiredfor somelight
truck wheels and reverse-offset wheels that must be
moved away from the balancer mounting flange. The
extension adaptor is often used with the 5-1/4 inch di-
ameter light truck cone.
Install the spacer on the mounting flange, then mount
the wheel, using the front cone method (Figure 13)
Figure 13
4.3 MODE SELECTION
The majority of balancing takes place in the default 2-
plane dynamic mode which is displayed as "2 PL"
(location 1). Hammer-on clip weights will be placed on
both inside and outside of the rim edge. If required,
select an optional weight placement mode by pressing
the
Mode
button until the appropriate placement mode
is displayed.
4.3.1 WEIGHT PLACEMENT MODES
Before spinning the wheel (although it may be done af-
terwards) choose the appropriate balancing mode for
thewheel.To selectthevarious placementmodespress
theMode button untilplacement LEDs indicate desired
placementposition.
The balancing modes available are:
A. DYNAMIC (twoplanes), suggested for allsteelrims.
Inthis case the wheel weightsmust be clipped onto the
rim edges. This function is selected as a default and
the LEDs corresponding to the wheel weight location
are lit on (Figure15).
B. STATIC(singleplane-Figure16). Suggestedfor nar-
row rims (3" or less). Use a single corrective weight
placed in the center of rim as illustrated in Figure 16.
Figure 14
Figure 15
Figure 16
!
Figure 12
Mode Button
Indicator LEDs

Page 12
C. ALUMINUM MODES. Balancing using a combina-
tion of hammer-on and adhesive weights as shown in
Figures 17 thru 21.
Figure 17 ALU 1
Figure 18 ALU 2
Figure 19 ALU 3
Figure 20 ALU 4
Figure 21 ALU 5
TO RETURN TO THE
DYNAMIC
PROGRAM FROM
ANY OF THE
ALU
PROGRAMS, JUST PRESS Can-
cel/Stop.
4.4 SELECTING OPERATOR PREFERENCES
4.4.1 FINE BALANCING MODE
This balancer measures with the maximum precision
available all the time, 1g / 0.05 oz, however values be-
low 5g / 0.25 oz are shown as zero while in the normal
operating mode. Values exceeding 5g / 0.25 oz are
roundedto theamount ofthe nearestcommercial wheel
weight.
Press the
F
button followed by the
UP
or
Down
arrow
button to toggle the display resolution between 5g /
0.25 oz and 1g / 0.05 oz.
4.4.2 OUNCE/GRAMS CONVERSION
When the machine is first turned on it is preset to dis-
play the imbalance in ounces.
If the display in grams is desired, press the
F
button
followed by the
UP
or
Down
arrow button until “P 3”is
displayed”.
Repeat the procedure for converting back to ounces.
4.4.3 RIM DIAMETER IN MILLIMETERS
The rim diameter is normally displayed in inches, how-
ever if the value in millimeters is desired, press the
F
button followed by the
UP
or
Down
arrow button until
“P 7”is displayed”.
Repeat the above operation to convert back to inches.
Example: “dIA ICH”= inches
“dIA ---”= millimeters
4.4.4 OPERATOR SELECTION
SelectthedesiredoperatordesignatedA,B,C,orD. The
EEWB304A Balancer can store wheel parameters of
four operators. The Operator button toggles between
the four operators with each depression.

Page 13
John Bean VPI System I Operators Manual
4.5 ENTER RIM PARAMETERS
4.5.1 Rim Distance (offset) - Move the rim off-
set arm to the edge of the rim, touch the pointer to
the rim edge as illustrated in Figure 22 and hold
steady for about a second. The beeper will sound
when the distance values are calculated and en-
tered automatically. Return the arm to its fully in
and down position on the balancer. Do not allow
the measurement arm to "dangle" down in front of
the balancer.
Figure 22
4.5.2 Rim Diameter Entry - Select the Manual
Diameter button (#11 page 9). Read the rim di-
ameter marked on the sidewall of the tire (Figure
23). Enter the measured rim diameter by pressing
the
Diameter
button followed by the
UP
or
Down
ar-
row button until the desired value appears in the
right display.
Figure 23
4.5.3 Measure Rim Width using rim width
calipers. Measure wheel where corrective clip-on
weight would be applied, Figure 24. Enter the
measured width by pressing the
UP
or
Down
arrowbutton until thedesired valueappears inthe
center display.
4.5.3 Manual Parameter Entry
In the event of automatic gauge failure, the dis-
tance values can be input manually.
4.5.3.1 Manual Distance Entry - Move the dis-
tance gauge arm to touch the inner edge of the
wheelwhereweightsaretobeplacedandobserve
the reading on the scale of the distance gauge.
Press manual Wheel
Offset
button (#13 page 9)
followed by pressing the
UP
or
Down
arrow button
until value is displayed in the left display window.
NOTE: For a more precise balancing of perfor-
mance wheels, an “ALU-S”Mode is available for
precisiondeterminationofwheelparameters. This
feature allows exacting placement of corrective
weights as well. See
Page 18
for detailed instruc-
tions.
NOTE: The parameter arm must be in the Home
rest position when the balancer is powered up.
Thisestablishes the arm starting position.
Figure 24

Page 14
4.6 CORRECTION OF THE IMBALANCE
NOTE: Before spinning the wheel make sure proper
eye protection is worn by all personnel in the vicinity of
the balancer.
A. Spin the wheel by lowering the wheel guard or by
pressing the
Enter
button. When the balancing cycle
is completed the wheel will stop automatically and the
imbalance values will appear on the LED’s.
NOTE: Do not use the foot operated shaft lock as a
brake, it is intended to be used only to prevent shaft
rotation while placing corrective weights.
B. Read the imbalance value on the outer display. Val-
ues are displayed in ounces but can be displayed in
grams if required and are automatically rounded to the
nearest commercial wheel weight.
4.6.1PLACING THE CORRECTIVE WEIGHT
Raise the wheel guard and turn the wheel until the dis-
plays of the outer plane imbalance position indicator
areilluminated green. Applythewheel weightattwelve
o’clockposition.Usethe footoperatedshaft locktopre-
vent shaft rotation while placing weights.
C.Correct theimbalance onthe innerplanein thesame
manner.
4.7 VERIFICATION OF THE RESULTS
Lower the wheel guard to spin the wheel again and
check that the readout is “0.00”“0.00”If a residual
imbalance is displayed:
A. Check the rim parameters, if entered value is incor-
rect, correct as needed. Imbalance values will be re-
computed after re-spinning wheel.
B. Check if the balancing mode selected is the most
appropriate. If not, choose the right mode and respin.
C.Thewheelweight couldhave beenplaced ata wrong
position. To check this, position the wheel at the cor-
rection position for the outer plane. If the wheel weight
previously attached is in sector ‘L’or ‘R’( Figure25),
move the wheel weight up about 1”(2.54cm).
If the wheel weight is in sector ‘D’cut a piece of the
wheel weight of an approximate value corresponding
to the value shown on the right display, or replace the
wheel weight with a lighter one.
Ifthewheelweightisinsector‘U’add a weight of value
indicated by the display or replace the wheel weight
with a heavier one. Repeat the same operation for the
inner plane.
NOTE: If this situation is repeated, your machine may
be out of calibration and a calibration operation might
be required as instructed on page 21.
D.Ifan
ALU
functionwas selectedensurethat thewheel
weights have been placed in accordance to the pro-
gram chosen.
E. Checkthat the quick nut istightand that the wheel is
not slipping against the backing collar.
F. Check that the wheel and adaptors are clean.
Figure 25
4.8 VIBRATION PROBLEMS
If vibration is still present after balancing, check the fol-
lowing possible sources of vibration:
1. Stones caught in the tire tread.
2. Tire slippage on the wheel.
3. Incorrectly mounted wheel.
4. Imbalanced wheel covers.
5. Excessive radial or lateral runout in the tire or
wheel.
6. Damaged wheel bolt holes.
7. Worn universal joints.
8. Imbalanced brake rotors or drums.
9. Worn or damaged balancer accessories.

Page 15
John Bean VPI System I Operators Manual
5.0 TIRE MATCHING PROGRAM - F90
Tire matching assists the user in determining the best
possible mating of the tire and rim. The mating of tire
and wheel normally allows the least amount of addi-
tional weight required for balancing and total runout.
The matching program is helpful when:
•Excessive radial runout is noticed.
•The balancer calls for weights in excess of 2 oz. on
either plane in the
Dynamic
mode.
TheVPI System I computer wheel balancerfeatures a
matching program capable of two levels of resolution:
Dynamic
, to rotate
and
reverse the tire on the rim
for optimum rim and tire matching.
Static
, when the tire has an ornate sidewall or di-
rectional tread and cannot be reversed on the rim.
INSTRUCTIONS:
1.Press the "F" button dollowedby pressing the
UP
or
Down
arrow button until the display reads "F" “90”,
release the "F"
button.
Whenactivated the machine displays"--- ACH"forone
second followed by "VAL tOP". This instructs the op-
erator to rotate the wheel so the inflation valve is at 12
o'clock. See
Figure
26. Press "F" to store the valve
position, the display will then read "SPN 1 ".
NOTE: The F button can be pressed more than once,
every time the F button is pressed, the valve position is
remembered by machine as a reference point.
2. Lower the wheel guard to spin the wheel, when the
shaft reaches the balancing speed, the display reads
"ACH 1" accompanied with a short beep.
3. After spinning the shaft brake engages and the dis-
play reads "tur tir" and "CrS tOP" alternatively.
(1) The operator should turn the wheel and mark an X
atthe12 o'clock when the valve is at the 6 o'clock posi-
tion.
Figure
27
(2)Remove the wheel assembly fromthebalancer and
deflate and rotate the tire on the rim so the valve points
to the cross mark on tire as shown in
Figure
28
4.After inflating the tire and remountingon shaft, press
F Button. The machine displays "VAL tOP" again. Op-
eratorshouldturn thewheel sothe valveis at12 o'clock.
Press the "F" button to program the valve position.
Figure 26 - Step 1, valve top, press "F"
Figure 27 - Step 2, valve at bottom,
mark top of tire with X, press "F"
Figure 28 - Step 3, rotate tire on wheel so the valve and
X mark line up. Rotate assembly to TDC, press "F".

Page 16
NOTE: The "F" button can be pressed as often as nec-
essary, with every press the machine updates the
memory of the valve position.
5. The machine displays "SPN 2 ". Lower the wheel
guard to spin the wheel, when the shaft reaches the
balancingspeed, machinedisplays"ACH 2" alongwith
a beep.
6. Once the spin cycle is complete, the display reads
"CAL CUL" for one second. Machine calculates the
results based on the previous two spins.
From this point, there are three possible procedures to
conclude the match balance routine. These 3 proce-
dures are quite different depending on the results of
calculation.
Procedure 1
The imbalance measured in spin 2 has been reduced
to an acceptable amount, less than 2 oz, and it will not
be necessary to continue match balance. The display
reads "ACH FIN" for one second, and then proceeds
to the normal two-plane balancing mode and displays
the weight imbalance amount and its position for both
planes.
Procedure 2
Due to a large amount of remaining imbalance the op-
erator can continue match mount. Machine displays
"CrS”“r" and"tur”“tir" alternatively. Thisinstructs the
operator to turn the wheel and make a double cross
mark(XX) on the right sideof the tire at 12o'clockposi-
tion when the right center position LED turns to green.
See Figure 29.
NOTE: If you do not intend to continue minimization,
you can press the Cancel/Stop Button
Ifthe Cancel/Stop Button is pressednow,machine dis-
plays "Qit Qit" for one and half second to remind op-
erator whether he wants to quit optimization or not. If
one presses Cancel/Stop Button immediately, the pro-
gram goes to procedure 1. If not, after one and half
second,machine returnstothe optimizationprocedure.
Tocontinue with optimization: Deflate the tireand then
turnthe valve topoint the XXmarkon the tire.Remount
tire/wheelonto shaft, press"F" when ready tocontinue.
1. The machine displays "VAL tOP". Turn the wheel
so the valve is at top position. (12 o'clock) and then
press F Button. The machine stores the valve position.
See Figure 30.
2.The machine displays "SPN 3 ". Lower wheelguard
to spin shaft. Machine displays "ACH 3 ".
Figure 29
Figure 30

Page 17
John Bean VPI System I Operators Manual
3. Display will read "ACH CHC" for one second. Bal-
ancing results are checked whether or not the match-
ing balancing has been achieved.
4. There are two results that could been given by the
previous step:
1 -
Match Balance failure
. Machine displays:
"FAI L " foronesecond and thengoes to idlestate.
2 -
Match Balance is successful
. Machine displays:
"ACH FIN"for one secondandthen goes tonormal
two plane balancing mode. Machine displays the
recalculated weights and their position taking the
matching results into account.
Procedure 3
1. Machine displays "CrS L" and "FLP tir" alterna-
tively. When the left center position LED turns to green
this instructs the operator to turn the wheel and mark a
XX on the left side of the tire at 12 o'clock position.
2. If the tire cannot be flipped, press the Cancel/Stop
Button to force machine to procedure 2.
Calculations may not allow continuation of the match-
ing process. If this is the case, machine displays "NO
NO " for one and half second. If the operator does not
respond the machine returns to above state after one
and half second.
Ifthe Cancel/Stop Buttonis pressed withinone and half
second, machine will display "Qit Qit" for one and half
seconds indicating cancelation of optimization return-
ing the machine to normal balancing modes.
If optimization is to be continued with flipping tire, pro-
ceed as described below.
3.Deflate the tire then flip,turningthe valve to point the
XX mark on the tire (as in procedure 2).
4. Inflate the tire and mount it to shaft again. Press the
“F”Button.
5.Themachine displays "VAL tOP". Turn the wheel to
make valve at top position. (12 o'clock) and then press
"F" button. The machine will store the valve position.
6. The machine displays "SPN 3 ".
NOTE: The F Button can be pressed as often as nec-
essary, with every press the machine updates the
memory of the valve position.
7. Lower the wheel guard to spin the shaft. Machine
displays "ACH 3 " while collecting data. Do not disturb
the machine while it is acquiring data.
8. When balancing is complete, the machine displays
"ACH CHC" for one second. Machine processes the
balancing results to check whether or not the matching
balancing has been achieved.
9. There are two results could been given by the previ-
ous step.
1.
Matching balancing failure
. Machine displays:
"FAI L " for one second andthen goes to idle state.
2 -
Match Balance is successful
. Machine displays:
"ACH FIN"for one second andthen goes to normal
two plane balancing mode. Machine displays the
recalculated weights and their position taking the
matching results into account.
6.0 OPTIMIZATION ROUTINE- F91
The Optimization Routine is very similar to that of the
Match Mount Program (F90). The main difference is
that operation begins with a bare rim instead of a rim-
tireassembly.Follow instructionsasdetailed forinchap-
ter 5.0 for F90.

Page 18
7.0 ALU-S MODE
Thisis a modesimilarto ALU mode2 and 3. The differ-
ence is that the distance and width parameters are ac-
curatelydefined for a moreexacting weight placement,
therefore improving the likelihood of a single spin bal-
ance. Follow the procedures below:
1. Press the Alu-s/Spoke button to activate the ALU-S
mode, the display will read " ALU - S".
2. Extendthe rim offset gaugearm and touch theposi-
tion of the left weight position. See Figure 31. The
display will read “d - I”. The high tone will sound when
dimension is entered. Return the gauge arm to the rest
position, a low pitch tone will indicate when it is OK to
proceed.
3. Move the parameter arm to the right weight posi-
tion, the machine displays “d - 2”as the arm is moved.
See Figure 32. The high tone will sound when dimen-
sions are entered. Return the gauge arm to the rest
position, a low pitch tone will indicate when it is OK to
proceed.
4. Enter the measured rim diameter by pressing the
Diameter
button followed by the
UP
or
Down
arrow
button or by rotating the shaft until the desired value
appears in the right display.
5. Lower the wheel guard or press “Enter”to spin the
wheel.Thedisplaywillread “ALU”duringthespincycle.
6. After spinning, the machine displays both the left
and right plane imbalance weight and position with its
color LEDs.
Rotatethe wheel until the leftGreen LED indicates cor-
rect position for the left correction weight.
7. Extend the gauge arm. The left display shows the
weight amount to be applied, the right display shows
the distance the gauge arm has to travel to get to the
correction plane. A high beep will sound when the cor-
rect position is reached, at the same time the right dis-
play will read “0“when the proper position is attained.
A reading of “- - -“in the distance window means the
gauge arm is over extended. Apply the weight amount
indicatedin the left window usingthe tape weight appli-
cator mounted on the SAPE extension.
Return the gauge arm to its home position.
8. Therightplane correctionweightwill beappliednext
as in step 7 above. The steps outlines are:
- Extend the arm until “0”is indicated in left window.
- Position the wheel in the weight application position
- Apply the displayed weight.
NOTE: Returning the gauge arm to the “Home”posi-
tiontoggles between the left andrightcorrection plane.
NOTE: To exit ALU-S mode and return to two plane
DYN (dynamic) mode press “Mode”button. The ma-
chine displays "ALU OFF" for one second and then
enters idle state in the 2-pl DYN mode
NOTE: Inspect the rim and available weights and use
good judgement in your selection. Weights should not
interfere with any suspension parts or make contact
during rotation. If a weight does make contact, use an
alternate location and select an appropriate mode.
Figure 31
Figure 32
This manual suits for next models
1
Table of contents
Other John Bean Wheel Balancer manuals
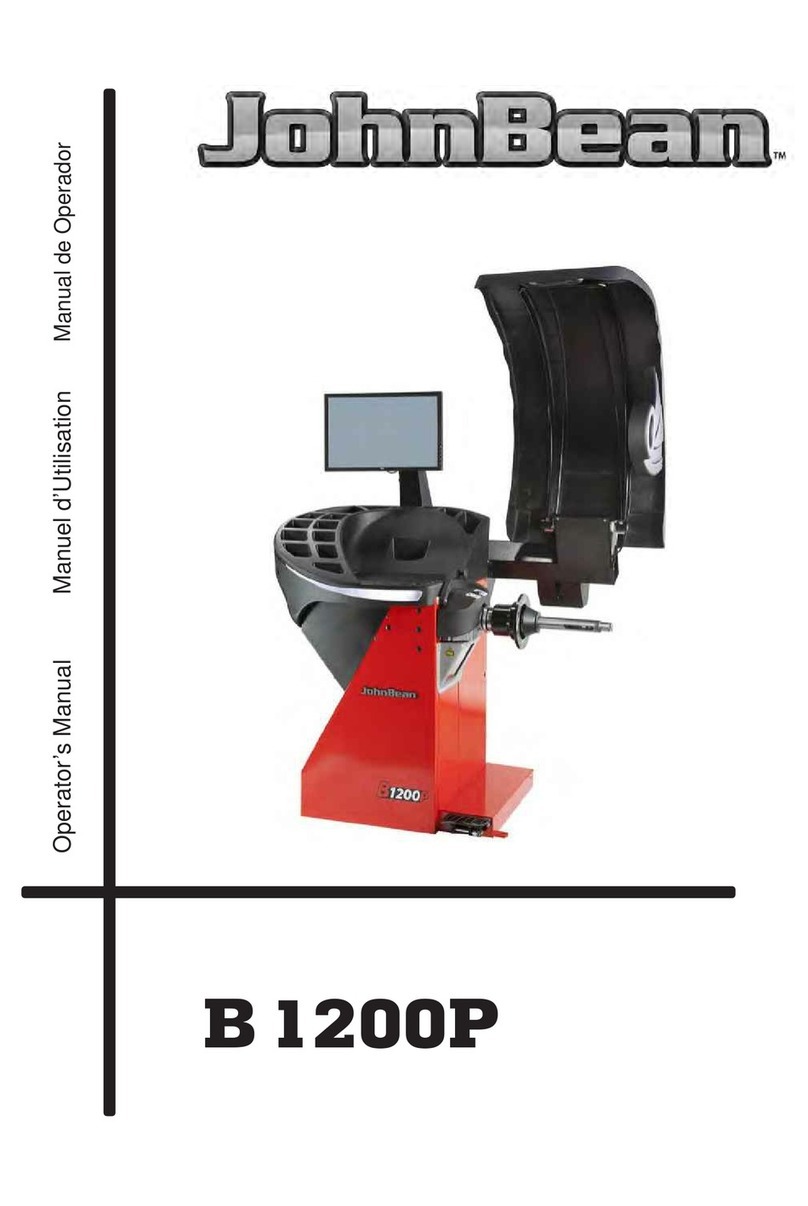
John Bean
John Bean B 1200P User manual

John Bean
John Bean B 100 User manual
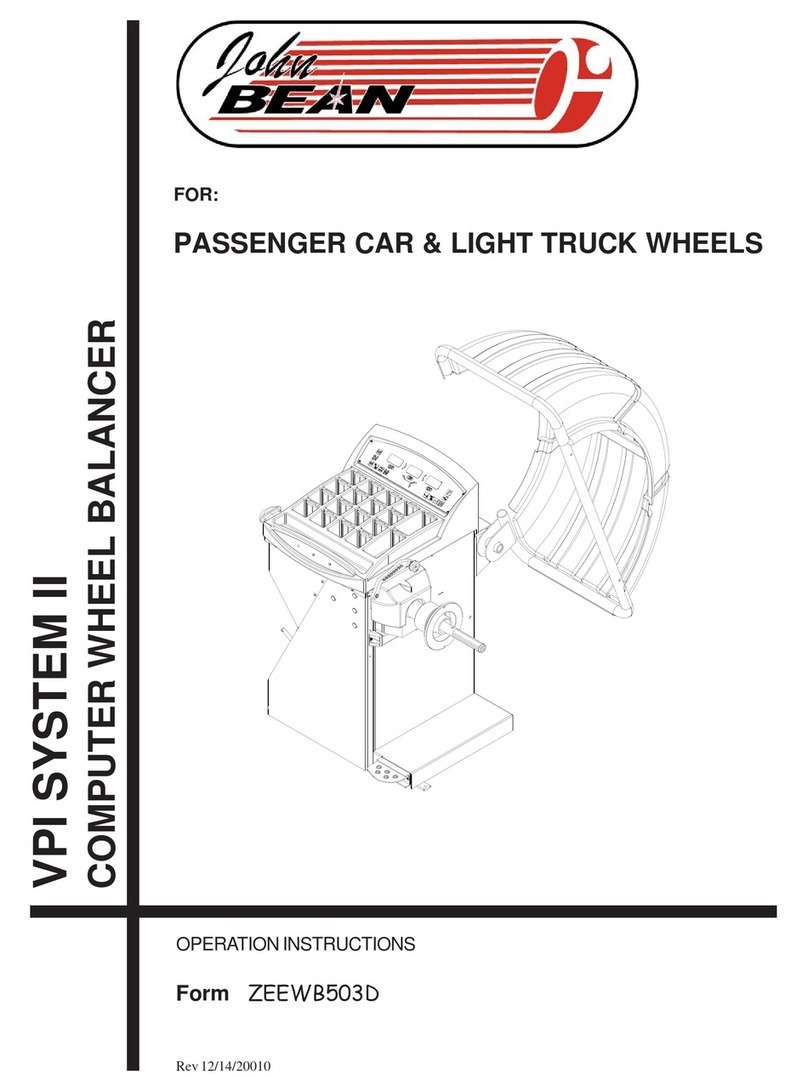
John Bean
John Bean VPI SYSTEM II User manual
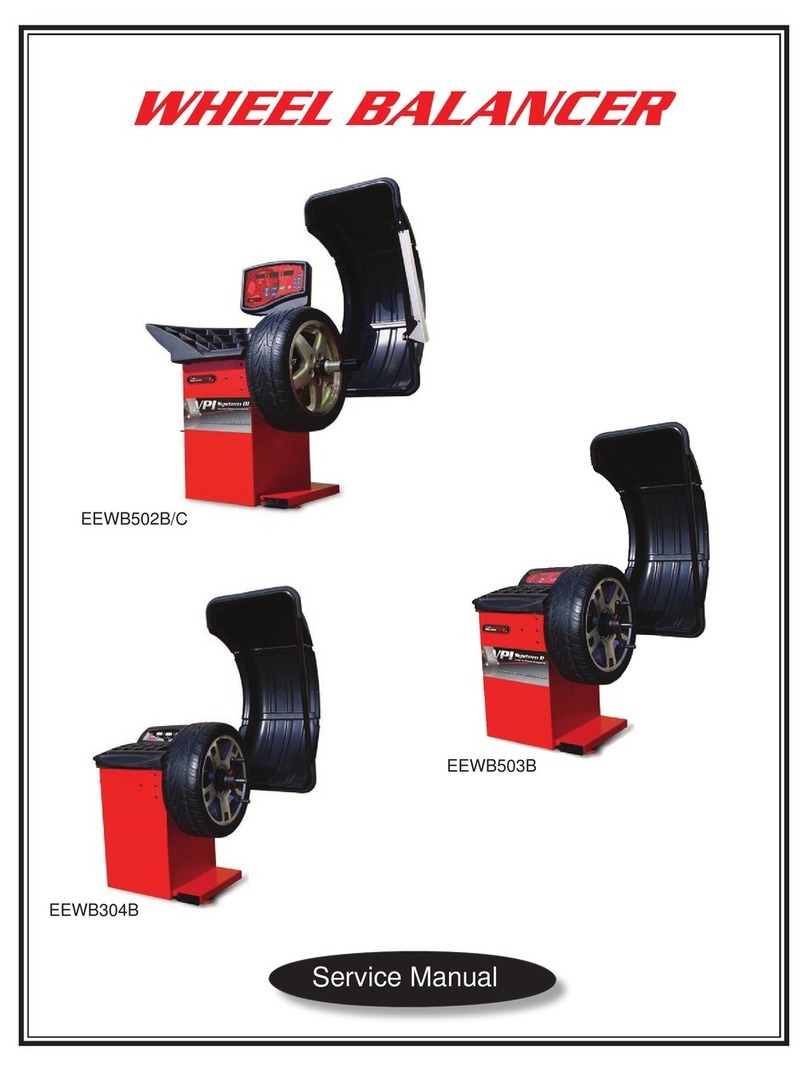
John Bean
John Bean EEWB502B User manual
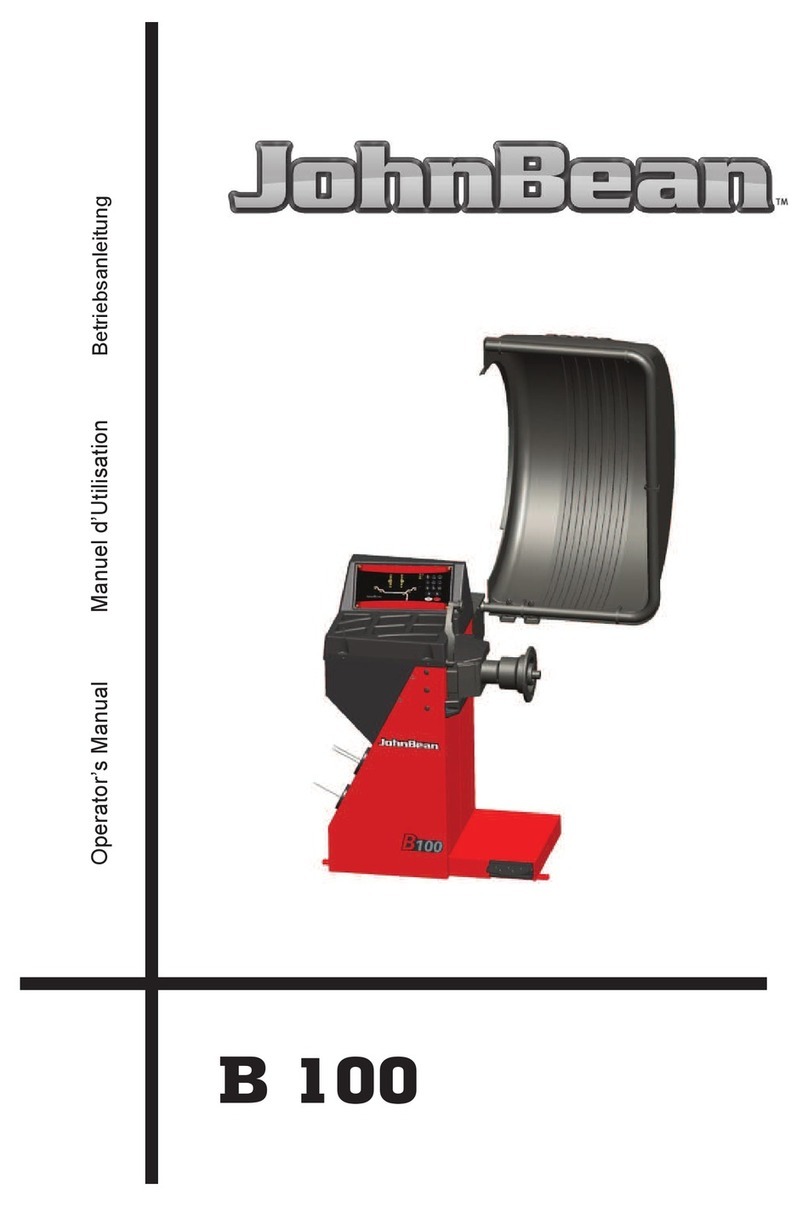
John Bean
John Bean B 100 User manual
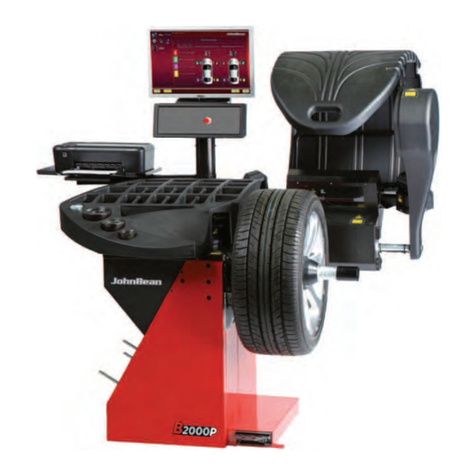
John Bean
John Bean B 2000P User manual

John Bean
John Bean B 200 User manual
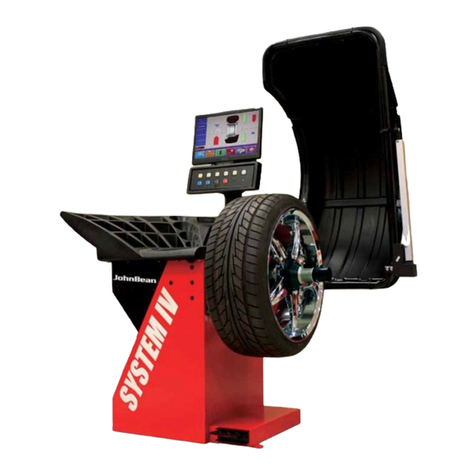
John Bean
John Bean VPI System IV User manual

John Bean
John Bean B400 User manual