Kemper KHS 686 02 008 User manual

Installation and operating instructions
KEMPER KHS Mini System Control
KEMPER KHS Mini System Control MASTER 2.0 Figure 686 02 008
KHS Mini System Control SLAVE Figure 686 02 006

Manual KHS Mini System Control
TABLE OF CONTENTS
1.
GENERAL INSTRUCTIONS: .................................................................................. 1
2.
AREA OF APPLICATION ....................................................................................... 2
2.1
Operating modes for the water exchange .................................................................................................. 2
2.2
KHS MASTER/SLAVE technology............................................................................................................. 2
2.3
Water exchange groups............................................................................................................................. 2
3.
SAFETY .................................................................................................................. 3
3.1
Safety Instructions ..................................................................................................................................... 3
3.2 Hazards if the safety instructions are not complied with ............................................................................ 3
3.3
Unauthorized alteration and spare part fabrication .................................................................................... 3
3.4
Unauthorised modes of operation.............................................................................................................. 3
4.
TECHNICAL DATA ................................................................................................. 4
5.
CAN BUS SYSTEM OVERVIEW............................................................................. 5
5.1
Layout variants .......................................................................................................................................... 5
5.2
Terminal resistance.................................................................................................................................... 6
5.3 Connection of terminal resistor .................................................................................................................. 6
6.
ASSEMBLY ............................................................................................................ 7
6.1.
Wall mounting ............................................................................................................................................ 7
6.2
Electrical installation KHS Mini System Control ......................................................................................... 8
6.2.1Terminal description -MASTER 2.0- and -SLAVE-8
6.2.2Detailed illustration of the terminals for cable entry9
6.2.2.1Power supply connection9
6.2.2.2
Connection of KHS-VAV Maximum flow isolating ball valve with servo-drive
(Figure 686 00)
9
6.2.2.3
Connection of KHS-VAV Maximum flow isolating ball valve with spring reset servo-drive
(Figure 686 01)
10
6.2.2.4CAN bus connection10
6.2.2.5Connection of external switch
11
6.2.2.6Connection of KHS-CONTROL-PLUS flow measurement valve (Figure 638 4G)
12
6.2.2.7Connection of KHS Temperature sensor Pt 1000 (Figure 628 0G)13
6.2.2.8Connection of KHS drain with overflow monitor (Figure 688 00)
13
6.2.2.9Connection of water sensor (Figure 620 00)14
6.2.2.10Connection of floating alarm relay14
6.3
Installation of network cable..................................................................................................................... 15
7.
COMMISSIONING................................................................................................. 16

Manual KHS Mini System Control
8.
CONFIGURATION ................................................................................................ 17
8.1
Manual configuration................................................................................................................................ 18
8.1.1Basic menu operation and functions18
8.1.2General plan19
8.1.3Detailed overview20
8.1.4Main menu21
8.1.4.1System settings.....................................................................................................................................22
8.1.4.2CAN BUS setup....................................................................................................................................25
8.1.4.3Device settings......................................................................................................................................26
8.1.4.4Operating modes..................................................................................................................................31
8.1.4.5Journal....................................................................................................................................................37
8.1.4.6Switching programs..............................................................................................................................38
8.1.4.7Valve manual mode.............................................................................................................................39
8.1.4.8Network setup.......................................................................................................................................40
8.1.4.9Error handling........................................................................................................................................42
8.1.5Using the USB interface......................................................................................................................43
8.2
Configuration of the WEB browser........................................................................................................... 44
8.2.1Basic menu operation and functions.................................................................................................45
8.2.2SYSTEM SETTINGS...........................................................................................................................46
8.2.3DEVICE SETTINGS.............................................................................................................................48
8.2.4OPERATING MODES..........................................................................................................................63
8.2.5OVERVIEW...........................................................................................................................................70
8.2.6CURRENT VALUES............................................................................................................................71
8.2.7DATA TRANSFER................................................................................................................................72
8.2.8EMAIL ADMINISTRATION..................................................................................................................77
9.
DESCRIPTION OF MALFUNCTIONS AND MALFUNCTION REPAIR.................. 79
10.
DIMENSIONS, ATTACHMENT DIMENSIONS ...................................................... 81
11.
ACCESSORIES .................................................................................................... 82
12.
WIRING INSTRUCTIONS FOR COMPONENTS WITH ELECTRICAL
CONNECTION ...................................................................................................... 82
13.
APPENDIX ............................................................................................................ 83
13.1
Valve technologies................................................................................................................................... 83
13.1.1A/B valve technology...........................................................................................................................83
13.1.2C-valve technology...............................................................................................................................84
13.2
Overview for the system commissioning of the KHS Mini System Control............................................... 84

Manual KHS Mini System Control 1
1. General instructions:
Assemble and commission the KEMPER KTS Mini System Control only after reading these assembly
and operating instructions. It informs you in detail about the assembly, commissioning, operating
principles and operation of the Kemper KHS Mini System Control. If you cannot find the information
and instructions you need in these operating instructions, ask the manufacturer, Gebr. Kemper (please
refer to last page for the address). Keep the mounting and operating instructions with the device or file
it with the other technical documentation in the system documentation.
Symbols used
The symbols used in the text are explained below.
List of symbols
Note:
Useful information
Warning notice:
Danger electric shock
Attention:
Imminent danger
Maintenance:
Maintenance/Repair

Manual KHS Mini System Control 2
2. Area of application
The KEMPER KHS Mini System Control can be used for monitoring and water exchange in drinking
water systems. The water exchanges can be generated and documented as flushing logs with the
MASTER 2.0 control. The dedicated water exchanges prevent stagnation in the drinking water with the
aim of maintaining the drinking water hygiene in the drinking water systems. Based on the KHS Mini
System Control MASTER, the MASTER 2.0 is a web-based further development that no longer
requires configuration and readout software. The system works entirely independent of the operating
system. On top of that, some new functions have been added that make the device also interesting for
large buildings.
NOTICE:
If two or more valves are simultaneously opened in a drinking water system,
under certain circumstances pressure fluctuations or a large pressure drop can
occur in the system. For that reason, make sure beforehand that the required flow
pressure is continuously guaranteed at all tapping points. It is recommended to
not make simultaneous water exchanges.
2.1 Operating modes for the water exchange
Time controlled water exchange
Temperature controlled water exchange
Volume controlled water exchange
2.2 KHS MASTER/SLAVE technology
The MASTER/SLAVE technology can be used to trigger flushing measures for maintaining the
drinking water hygiene for the drinking water system. The corresponding operating modes can be
individually configured for each individual water-exchange group. Positioning the individual MASTER
or SLAVE controls directly on the water exchange groups ensures short wiring distances for
interconnection.
2.3 Water exchange groups
Shown in Ill. 2.1 as an example is a KHS Mini
System Control -SLAVE- (2) in connection with a
water exchange group which comprises a KHS-
VAV Maximum flow isolating ball valves (4),
Temperature sensor (1), Volume flow sensor (3)
and a KHS Drain (5). The components of the water
exchange group are only listed as examples here.
The operating mode depends on the components
and the valve technology (for valve technology
please refer to Chapter 13.1). In the example
illustrated, the -SLAVE-(2) controls the specified
water exchange groups. It is connected with the
MASTER 2.0- through a CAN bus cable.
(5)
Note:
Maintenance cut-offs are re-
commended in front of the
Volume flow sensor (3).
Ill. 2.1 Illustration of a water exchange
group
(1)
(2)
(3)
(4)

Manual KHS Mini System Control 3
3. Safety
The descriptions and instructions in these
operating instructions concern the KHS Mini
System Control -MASTER 2.0- and KHS
Mini System Control -SLAVE-. The
prerequisite for handling the controller is the
deployment of professionally trained
personnel as per DIN EN 50110-1.
3.1 Safety Instructions
Before commissioning, make sure the connections have been made properly and professionally and
that the system is properly protected. Comply with the pertinent regulations (EN, VDE, etc.) and the
regulations of the local energy utility.
3.2 Hazards if the safety instructions are not complied with
Non-compliance with the safety instructions can result in both hazards to people and hazards to the
environment and the system. Non-compliance with the safety instructions leads to the loss of rights to
any compensation claims. In some cases, non-compliance can, for example, result in the following
hazards:
Failure of important functions in the device
Hazards to people through electrical and mechanical effects
3.3 Unauthorized alteration and spare part fabrication
Alternations and modifications to the device are only permissible after agreement with the
manufacturer. Original spare parts and manufacturer authorised accessories serve the purpose of
safety. The use of any other parts may annul the liability for any resultant consequences.
Attention:
Use only original/approved spare parts otherwise no warranty claims will be
recognized.
3.4 Unauthorised modes of operation
The reliability of the supplied unit is only ensured when used as intended. Never exceed the limits
stated in this documentation under any circumstances.
Note:
If the operating instructions are not followed, the manufacturer of this controller
does not assume any responsibility. These operating instructions contain basic
instructions that must be complied with during set-up, commissioning and
maintenance. Therefore, the plumber/mechanic and the responsible
specialists/operators must read these operating instructions before assembly and
commissioning. Comply not only with the general safety instructions listed in this
main point; also follow the specific safety instructions listed under the other main
points.
Warning notice:
During assembly and
maintenance, make sure that
the control is not switched on.
Only skilled professional
personnel are permitted to
operate electrical systems.
Danger of fatal electric shock.

Manual KHS Mini System Control 4
4. Technical Data
Technical Data
Power supply 230 V AC 50/60Hz
Display Graphic display with background lighting
Operation with 4 buttons: Up | Down | Enter | Esc
Relay flush valve switching capacity 230 V, 2 A
Floating alarm relay, max. 230 V, 2 A
16 memory locations for the operating modes:
Time controlled water exchange
Temperature controlled water exchange
Volume controlled water exchange
Routine-time, routine-duration and routine-volume
Data logging
Release
For connecting:
1 ea. KHS-VAV-plus or KHS-VAV
1 ea. KHS-Temperature sensor Pt 1000
1 ea. KHS-Control Plus volume flow measurement valve
1 ea. KHS overflow monitor
1 detector circuit with up to 25 water sensors
Acoustic alarm signal in case of faults
Alarm acknowledgement on device
System is expandable: 1 -MASTER- with max. 62 - SLAVEs- via CAN bus
Leak safeguard through water sensor
Bus system connection per direction: CAN installation cable, max. 1000m total length
WEB-based PC-link for configuration and for reading out the flush log
Can save 50,000 journal entries
Datalogging up to 12 million entries
External switch | Switchover:
Program 1 (e.g. school-holidays program)
Program 2 (e.g. school program)
Maintenance mode (system is blocked)
Menu driven operation in German, English or Dutch
Internal consumption 10 VA
Manual operation of the valves on the MASTER or via WEB browser
Ambient temperature range from 0 °C to 50 °C
Protection class IP 54
Surface mounted housing for wall installation
USB interface for updating the firmware, reading out the journal and data logging and
for downloading and uploading the configuration file
Network link through network cable (accessory)
Email in case of malfunctions possible

Manual KHS Mini System Control 5
CAN bus
A
CAN bus
B
CAN bus
A
5. CAN bus system overview
The basic version of the -MASTER/SLAVE- technology includes as the smallest solution the
-MASTER 2.0- System Control for water exchanging measures in the sector of drinking water and
for signal evaluation.
Furthermore, the -MASTER 2.0- System Control, using two integrated CAN bus connections, can
trigger up to 62 -SLAVE- controls and one directly-connected KHS water exchange group. Up to a
maximum of 31 -SLAVE- controls per CAN-BUS connection of the -MASTER 2.0- can be controlled
per CAN bus connection.
That means up to 63 KHS water exchange groups can be connected and operated through
the -MASTER/SLAVE- technology. The accumulated total length of one CAN bus connection
can amount to a maximum of 1000 m (total length is thus 2000m).
5.1 Layout variants
Note:
The controllers must be connected in series, as can be seen in Example 1.
During this, the -MASTER 2.0- System Control can be connected within the
series (Variant 2) or as a final subscriber (Variant 1). Branches or start
connections, as can be seen in Example 2, are not possible. Furthermore, shorter
cable distances are recommended.
Example 1: Layout variant, KHS-Mini System Control -MASTER 2.0-
Variant 1
Variant 2
Ill. 5.1 Illustration of a layout variant, KHS Mini System Control -MASTER- system control

Manual KHS Mini System Control 6
CAN bus
A
CAN bus
A
CAN bus
B
CAN bus
A
Example 2: Incorrect layout
Ill. 5.2 View of an impermissible layout variant, KHS Mini System Control -Master 2.0-
5.2 Terminal resistance
Variant 1
Note:
The 120 Ωterminal resistance
must be installed only in the last
control component (-SLAVE-) of
a CAN bus cable line. The -
MASTER control does not
require a terminal resistance.
Variant 2
Ill. 5.3 Illustration of a CAN bus line with terminal resistor
5.3 Connection of terminal resistor
Attention:
All KHS Mini controls -SLAVE-
are supplied with a 120 Ω
terminal resistor.
For non-terminal -SLAVE-
controls, the resistor must be
removed!
120
Ω
Note:
Incorrect layout
Ill. 5.4 Illustration of the terminal resistor

Manual KHS Mini System Control 7
6.
Assembly
Warning notice:
Allow only certified electricians to assemble and install electrical equipment.
Danger of fatal electric shock.
Very strong magnetic fields can impair the functioning. Interferences can be prevented by following the
installation rules below:
Do not mount the controller and the sensors near inductive loads (motors, transformers,
contactors, etc.).
Feed through a separate mains voltage circuit (if necessary, with an a.c. mains filter).
Inductive loads must be equipped with safeguards to reduce overvoltages (varistors, RC-
filter).
Attention:
When using the controller together with other devices in one system, check to
see if that causes interference signals to be emitted.
6.1. Wall mounting
The KHS Mini System Control is intended for wall installation. The housing has 4 each ø 4mm
mounting holes in a clearance of w = 188mm and h = 88mm. Additional dimensions are listed in
Chapter 10. To mount, open the cover and screw the device tightly to the wall. After mounting the
housing, make the required electrical connections.
Ill. 6.1 Illustration of the mounting holes for wall installation

Manual KHS Mini System Control 8
6.2 Electrical installation KHS Mini System Control
The following chapter explains the electrical installation. The electrical connections are made through
screwless-type terminals.
6.2.1 Terminal description -MASTER 2.0- and -SLAVE-
Ill. 6.2 Cut-out view of the -MASTER 2.0- and -SLAVE- controller board with terminals
Illustration: Control board with terminals
1. Flushing valve switching output 230
_
_______________________
2. Flushing valve voltage output 230 V (only on 68654) ___________
3. Flushing valve N _______________________________________
4. Power supply - LI 230V__________________________________
5. Power supply – N ______________________________________
6. External input 230 V (Function only with -MASTER-) ___________
7. Grounded conductor PE _________________________________
8. CAN-Bus HIGH 1 ______________________________________
9. CAN-Bus LOW 1_______________________________________
10. CAN-Bus GND 1 ______________________________________
11. CAN-Bus HIGH 2 _____________________________________
12. CAN-Bus LOW 2______________________________________
13. CAN-Bus GND 2 ______________________________________
14 Flow measurement valve - Voltage output 5V ________________
15 Flow measurement valve - Flow input ______________________
16 Flow measurement valve - no function _____________________
17. Flow measurement valve GND ___________________________
18. Pt 1000 Input 1 _______________________________________
19. Pt 1000 Input 2 _______________________________________
20. Pt 1000 Input 3 _______________________________________
21. Pt 1000 Input 4 _______________________________________
22. Drain floating switch (strands interchangeable) ______________
23. Drain floating switch (strands interchangeable)
[Terminals 22 and 23 can also be used to connect
the water sensor]
24. Alarm relay voltage input external ________________________
25. External monitor voltage error ___________________________
26. External monitor voltage operation ________________________

Manual KHS Mini System Control 9
6.2.2 Detailed illustration of the terminals for cable entry
Note:
The following illustrations apply to the KHS Mini System Control -MASTER 2.0-
and the KHS Mini System Control -SLAVE-. Please note the preceding warning
notices:
6.2.2.1 Power supply connection
Power supply: 230 V +/- 15% AC 50/60Hz
Connection: Terminals, L, N, PE
Line fuse max. 16A
BN = brown = L
BU = blue = N
GR = green = PE
Ill. 6.3: Schematic representation of the power supply connection
6.2.2.2 Connection of KHS-VAV Maximum flow isolating ball valve with servo-drive (Figure 686 00)
BN = brown = 1
BK = black = 2
BU = blue = 3
Ill. 6.4: Schematic representation of the connection of the KHS-VAV Maximum flow isolating ball valve
BN BK

Manual KHS Mini System Control 10
6.2.2.3
Connection of KHS-VAV Maximum flow isolating ball valve with spring reset servo-drive (Figure
686 01)
BN = brown = 1
BU = blue = 3
Ill. 6.5: Schematic representation of the connection of the KHS-VAV Maximum flow isolating ball
valve with spring reset servo-drive
6.2.2.4 CAN bus connection
Attention:
Follow the notices and instructions in Chapter
5. The twisted pair of the CAN bus cable
should be separated and the shielding
removed only as far as necessary to assign
the maximum terminals (recommendation:
max. 4cm).
The shielding must be properly bundled with a
heat shrink tube or insulating tape to prevent
contact of the individual wires of the shielding
to the other potentials.
Ill. 6.6: Schematic diagram of the twisted pair

Manual KHS Mini System Control 11
Ill. 6.7: Exemplary illustration of a CAN bus installation from a -MASTER 2.0- and three -SLAVE-
controls
6.2.2.5 Connection of external switch
Attention:
The external connection can only be used
with the KHS Mini System Control -MASTER
2.0-.
Power supply: 230V +/- 15% AC 50/60Hz
Line fuse max. 16A
BK = black = L
Ill. 6.8: Schematic diagram of connection of external switch
Note:
Through the trigger on Terminal 6 you have a facility to switch the KHS Mini
System Control program with external switching processes through a 230V
input. The program switching of the external connection is discussed in Chapter
8.
230V
L (external voltage)
S
wi
tc
h
CAN bus H and L = 1
Twisted-Pair
H: Strand 1
L: Strand 2
Put on GND cable
shielding
The terminal groups 8/9/10 and 11/12/13
are of equal value. For instance the wire
end a can also be connected to
Terminals 11/12/13 and the wired end b
to Terminals 8/9/10.

Manual KHS Mini System Control 12
6.2.2.6 Connection of KHS-CONTROL-PLUS flow measurement valve (Figure 638 4G)
Connection of KHS-CONTROL-PLUS volume flow measurement valve
BR = +5V DC = 14
BU = Flow = 15
BK = GND = 17
Ill. 6.9: Schematic diagram of connection of KHS-CONTROL-PLUS flow measurement valve
Connection of KHS-CONTROL-PLUS temperature sensor
Attention:
The KHS-CONTROL-PLUS has an internal
Pt 1000, enabling an additional temperature
measurement. If no temperature
measurement is needed, insulate and
protect the strands from contact with the
board.
GY = grey (green/yellow) = 19
W = white = 20
Ill. 6.10: Schematic diagram of connection of KHS-CONTROL-PLUS volume flow sensor
Note
Attention:
To perform the temperature measurement
through the KHS-CONTROL-PLUS, the
jumper on the board must be changed from
4-wire to 2-wire, see Photo 6.11.
Important comment:
During this measurement, the temperature
measurement is falsified through the line
resistance. For 10m line-length with
0.34mm² cross-section, the measurement
falsification can amount to approx. + 0.5°C.
Ill. 6.11: Schematic diagram of connection of KHS-CONTROL-PLUS temperature sensor
14 15 17

Manual KHS Mini System Control 13
Connection of KHS-CONTROL-PLUS cable-plug connector
Ill. 6.12: Schematic diagram of the preparation of the sensor top to make cable-plug connection of
the KHS-CONTROL-PLUS
6.2.2.7 Connection of KHS Temperature sensor Pt 1000 (Figure 628 0G)
RD = red = 18
RD = red = 19
W = white = 20
W = white = 21
Ill. 6.13: Schematic diagram of connection of KHS Temperature Measurement Valve Pt1000
6.2.2.8 Connection of KHS drain with overflow monitor (Figure 688 00)
Note:
In the as delivered state, a bridge strand is
plugged between Terminals 22 and 23. It
must be removed before connecting the
KHS drain.
W = white = 22
BN = brown = 23
Ill. 6.14: Schematic diagram of connection of the KHS drain with overflow monitor
1. Cut off top of cap 2. Route cable through 3. Screw cable to sensor 4. Put on the cap

Manual KHS Mini System Control 14
6.2.2.9 Connection of water sensor (Figure 620 00)
Note:
It is possible to link up to 25 water sensors in
parallel in the detection circuit.
Max. cable length water sensor: < 50m
with standard cable
Max. cable length water sensor: > 50m to
500m as shielded cable, 2x 0.75 mm²,
(e.g. UL-LIYCY)
W = white = 22
BN = brown = 23
Ill. 6.15: Exemplary diagram of the water sensor connection
6.2.2.10 Connection of floating alarm relay
Monitoring example: Errors and mains voltage
failures are reported with external voltage to the
warning lamp, the warning horn or to the BMS.
Ill. 6.16: Exemplary diagram of the alarm relay
III. 6.16: Exemplary diagram of the alarm relay
Warning light
A
larm horn
e.g input BMS or
alarm relay
External voltage max.
230V, 2A or 24V input

Manual KHS Mini System Control 15
6.3 Installation of network cable
Note:
The supplied network cable has a total length of 2.5m!
Step 1. Open the housing Step 2. Route the cable through bottom
left into the housing
Step 3. Secure cable Step 4. Connect cable to the board

Manual KHS Mini System Control 16
7. Commissioning
After finishing the wall installation and the electrical installation in accordance with Chapter 5, apply
the mains voltage of 230V.
Warning notice:
Allow only certified electricians to assemble and install electrical equipment.
Danger of fatal electric shock.
ATTENTION!
Note:
To simplify the control system and to guarantee flawless installation, fill in the
overview of the system commissioning of the KHS Mini System Control (see
supply pressure, Chapter 13.2) before making the settings. It is mandatory to fill
in the supply pressure to be able to take advantage of the optional factory
support.

Manual KHS Mini System Control 17
8. Configuration
The KHS Mini System Control -MASTER 2.0- can be configured through the internal menu driven
operation or through a web server. Furthermore, the saved configurations can be uploaded through a
USB interface to the KHS Mini System Control -MASTER 2.0-.
The sample project shown below shows the basic controller types of the KHS Mini System Control -
MASTER 2.0-. The individual configuration facilities of the KHS Mini System Control -MASTER 2.0- is
elucidated using exemplary configurations of the sample project in the following chapters (8.1 and
8.2).
After all units, as described in Chapter 6, have been mounted and electrically connected and a
network connection has been successfully established, the actual configuration of the individual KHS
Mini System Controls starts.
The sample project has one KHS Mini System Control -MASTER 2.0- and six KHS Mini System
Controls -SLAVE-. The system controls shown in Illustration 8.1 are intended to secure the cold-water
line against stagnation and leaks in a fictitious building.
Ill. 8.1 Sample project
Consumers
Sensor cable
230V cable
CAN bus cable
SLAVE 1.6
SLAVE 1.4
SLAVE 1.3 SLAVE 1.5
SLAVE 1.2 SLAVE 1.1 MASTER
Valve A3; 1st
UF;
temperature
controlled
Valve
cellar
Volume flow sensor 1;
GF
Temperature sensor 1;
GF
Temperature sensor
3; 1st UF
Volume flow sensor 2;
Cellar
Water sensor 1-4; Cellar
Drain + overflow
monitor 1-2; Cellar
Valve B1;
Cellar
Valve C1;
Cellar,
time
controlled
1st UF
GF
Cellar
Valve A2; GF;
time
controlled
C1 B1
Temperature sensor
2;
GF
This manual suits for next models
1
Table of contents
Other Kemper Control System manuals
Popular Control System manuals by other brands
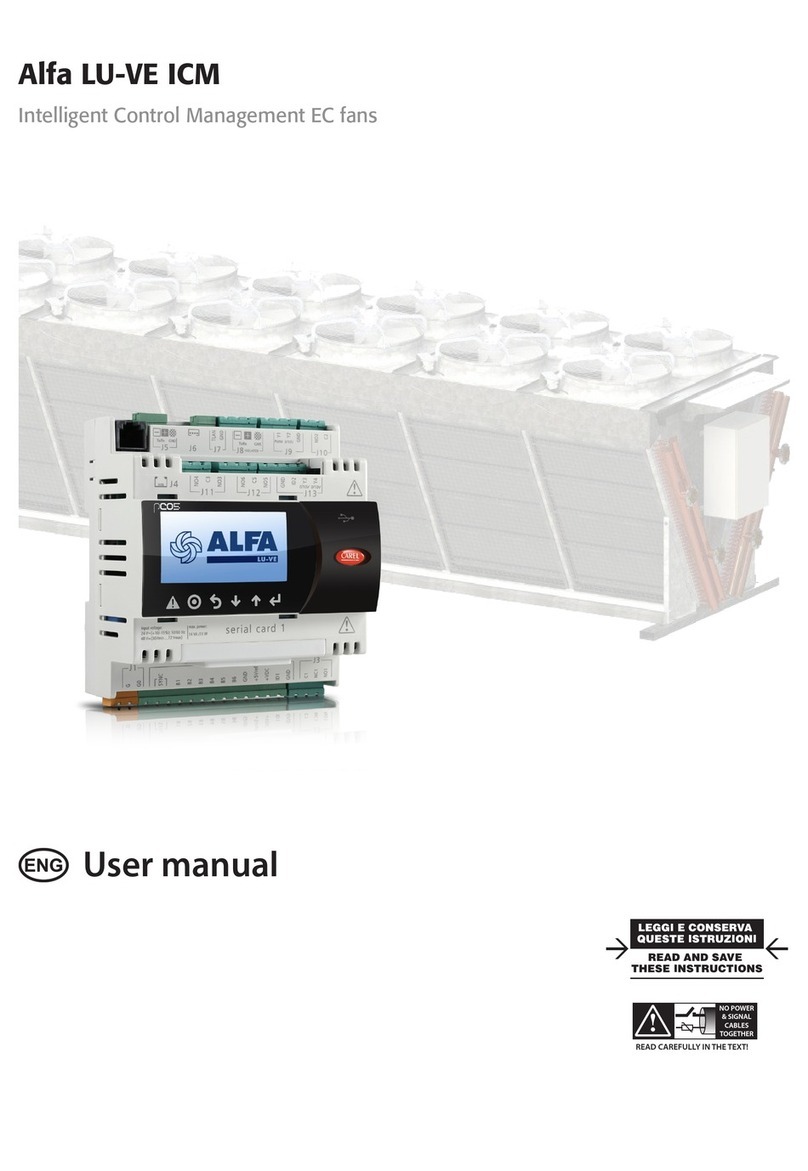
Alfa Network
Alfa Network LU-VE ICM user manual
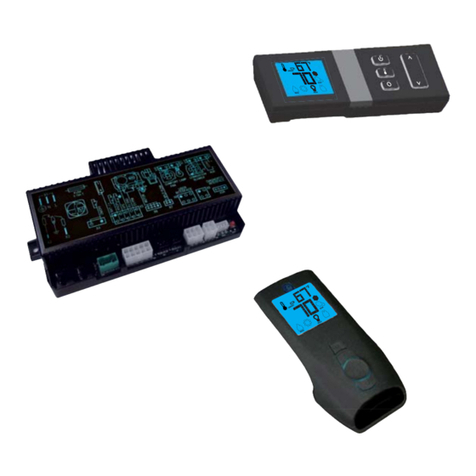
SITGroup
SITGroup PROFLAME 2 Basic Installation and operating instructions
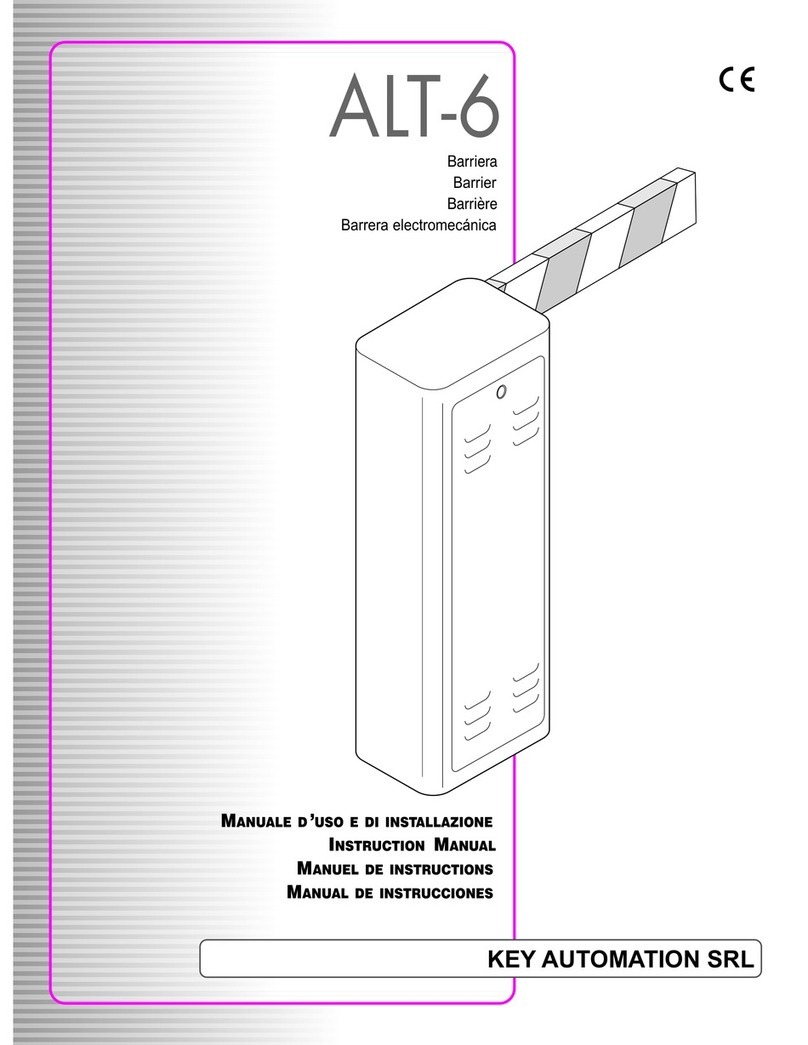
Keyautomation
Keyautomation ALT-6 instruction manual
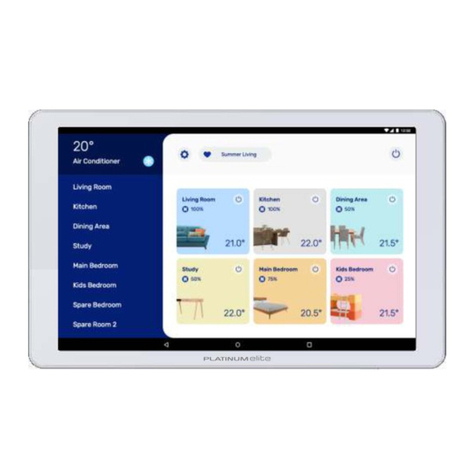
A/DA
A/DA Platinum Elite installation manual
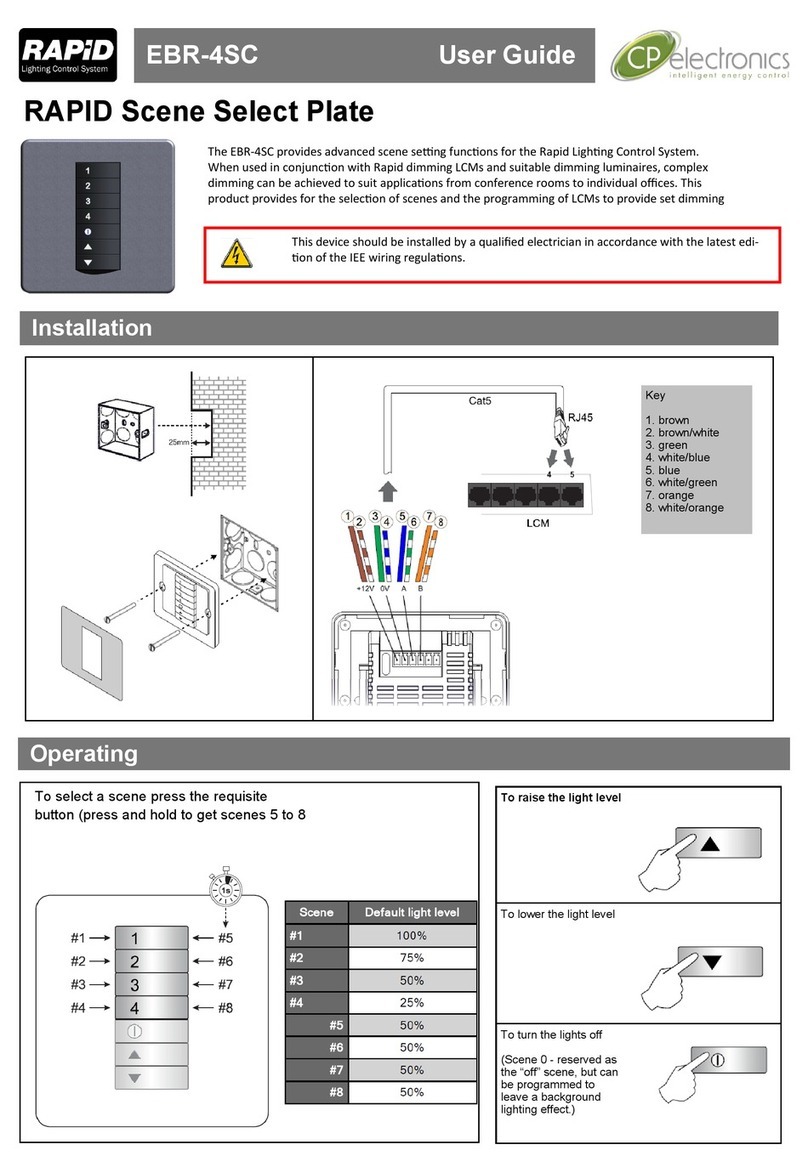
C.P. Electronics
C.P. Electronics Rapid EBR-4SC user guide
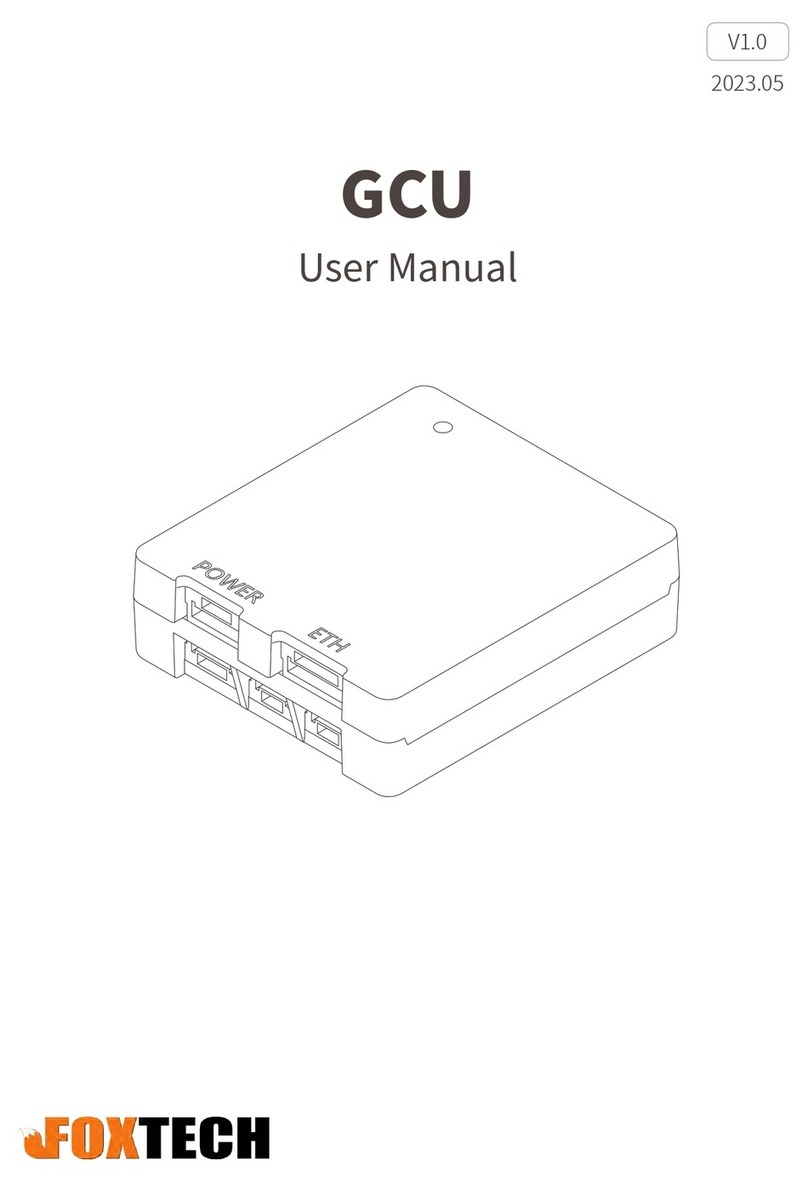
Foxtech
Foxtech GCU user manual