Leuze electronic MLC 520 User manual

S A F E I M P L E M E N T A T I O N A N D O P E R A T I O N
Original operating instructions
EN 2015/12 - 700191
We reserve the right to
make technical changes
MLC 520
Safety Light Curtains

© 2015
Leuze electronic GmbH & Co. KG
In der Braike 1
D-73277 Owen / Germany
Phone: +49 7021 573-0
Fax: +49 7021 573-199
http://www.leuze.com
Leuze electronic MLC 520 2

Table of contents
Leuze electronic MLC 520 3
Table of contents
1 About this document ............................................................................................5
1.1 Used symbols and signal words .............................................................................................5
1.2 Checklists................................................................................................................................ 6
2 Safety .....................................................................................................................7
2.1 Approved purpose and foreseeable improper operation ........................................................ 7
2.1.1 Proper use ..............................................................................................................................7
2.1.2 Foreseeable misuse ............................................................................................................... 8
2.2 Competent persons ................................................................................................................ 8
2.3 Responsibility for safety.......................................................................................................... 8
2.4 Disclaimer ............................................................................................................................... 8
3 Device description ................................................................................................9
3.1 Device overview......................................................................................................................9
3.2 Connection technology .........................................................................................................10
3.3 Display elements .................................................................................................................. 11
3.3.1 Operating indicators on the MLC500 transmitter ................................................................. 11
3.3.2 Operating indicators on the MLC520 receiver .....................................................................11
3.3.3 Alignment display..................................................................................................................13
4 Functions.............................................................................................................14
4.1 Start/restart interlock RES ....................................................................................................14
4.2 EDM contactor monitoring ....................................................................................................15
4.3 Transmission channel changeover ....................................................................................... 15
4.4 Range reduction ................................................................................................................... 16
5 Applications ........................................................................................................17
5.1 Point of operation guarding...................................................................................................17
5.2 Access guarding ...................................................................................................................18
5.3 Danger zone guarding ..........................................................................................................18
6 Mounting..............................................................................................................19
6.1 Arrangement of transmitter and receiver ..............................................................................19
6.1.1 Calculation of safety distanceS............................................................................................19
6.1.2 Calculation of safety distance if protective fields act orthogonally to the approach direction. 20
6.1.3 Calculation of safety distanceS for parallel approach to the protective field........................ 24
6.1.4 Minimum distance to reflective surfaces............................................................................... 25
6.1.5 Preventing mutual interference between adjacent devices .................................................. 26
6.2 Mounting the safety sensor................................................................................................... 28
6.2.1 Suitable mounting locations.................................................................................................. 28
6.2.2 Definition of directions of movement..................................................................................... 29
6.2.3 Fastening via BT-NC60 sliding blocks .................................................................................. 29
6.2.4 Fastening with BT-R swivel mount ....................................................................................... 29
6.2.5 Fastening via swiveling mounting brackets .......................................................................... 30
6.2.6 One-sided mounting on the machine table ........................................................................... 30
6.3 Mounting accessories ........................................................................................................... 31
6.3.1 Deflecting mirror for multiple-side guarding .......................................................................... 31
6.3.2 MLC-PS protective screen.................................................................................................... 33
7 Electrical connection..........................................................................................34
7.1 Pin assignment transmitter and receiver .............................................................................. 34
7.1.1 MLC500 transmitter .............................................................................................................34
7.1.2 MLC520 receiver ................................................................................................................. 36
7.2 Circuit diagram examples .....................................................................................................37

Table of contents
Leuze electronic MLC 520 4
7.2.1 MLC520 circuit diagram example ........................................................................................37
8 Starting up the device ........................................................................................38
8.1 Switching on ......................................................................................................................... 38
8.2 Aligning the sensor ...............................................................................................................38
8.3 Aligning of deflecting mirrors with the laser alignment aid.................................................... 39
8.4 Unlocking start/restart interlock ............................................................................................ 40
9 Testing .................................................................................................................41
9.1 Before the initial start-up and following modifications........................................................... 41
9.1.1 Checklist for integrator – to be performed prior to the initial start-up and following modifica-
tions ...................................................................................................................................... 41
9.2 To be performed periodically by competent persons............................................................ 43
9.3 Periodically by the operator ..................................................................................................43
9.3.1 Checklist – periodically by the operator ................................................................................ 43
10 Maintenance ........................................................................................................45
11 Troubleshooting..................................................................................................46
11.1 What to do in case of failure? ...............................................................................................46
11.2 Operating displays of the LEDs ............................................................................................46
11.3 Error messages 7-segment display ......................................................................................47
12 Disposing.............................................................................................................50
13 Service and support ...........................................................................................51
14 Technical data .....................................................................................................52
14.1 General specifications .......................................................................................................... 52
14.2 Dimensions, weight, response time ...................................................................................... 54
14.3 Dimensional drawings: Accessories .....................................................................................56
15 Ordering information and accessories .............................................................59
16 EC Declaration of Conformity............................................................................65

About this document
Leuze electronic MLC 520 5
1 About this document
1.1 Used symbols and signal words
Tab.1.1: Warning symbols and signal words
Symbol indicating dangers to persons
Symbol indicating possible property damage
NOTICE Signal word for property damage
Indicates dangers that may result in property damage if the measures for dan-
ger avoidance are not followed.
CAUTION Signal word for minor injury
Indicates dangers that may result in minor injury if the measures for danger
avoidance are not followed.
WARNING Signal word for serious injury
Indicates dangers that may result in severe or fatal injury if the measures for
danger avoidance are not followed.
DANGER Signal word for life-threatening danger
Indicates dangers with which serious or fatal injury is imminent if the measures
for danger avoidance are not followed.
Tab.1.2: Other symbols
Symbol for tips
Text passages with this symbol provide you with further information.
Symbols for action steps
Text passages with this symbol instruct you to perform actions.
Symbol for action results
Text passages with this symbol describe the result of the preceding action.
Tab.1.3: Terms and abbreviations
AOPD Active Optoelectronic Protective Device
(Active Optoelectronic Protective Device)
EDM Contactor monitoring
(External Device Monitoring)
LED LED, display element in transmitter and receiver
MLC Brief description of the safety sensor, consisting of transmitter and receiver
MTTFdMean time to dangerous failure
(Mean Time To dangerous Failure)
OSSD Safety-related switching output
(Output Signal Switching Device)
PFHdProbability of a dangerous failure per hour
(Probability of dangerous Failure per Hour)
PL Performance Level

About this document
Leuze electronic MLC 520 6
RES Start/restart interlock
(Start/REStart interlock)
Scan Consecutive scans of the protective field from the first to the last beam
Safety sensor System consisting of transmitter and receiver
SIL Safety Integrity Level
State ON: device intact, OSSD switched on
OFF: device intact, OSSD switched off
Locking: device, connection or control / operation faulty, OSSD switched off
(lock-out)
1.2 Checklists
The checklists (see chapter 9 "Testing") serve as a reference for the machine manufacturer or supplier.
They replace neither testing of the complete machine or system prior to the initial start-up nor their periodic
testing by a competent person. The checklists contain minimum testing requirements. Depending on the
application, other tests may be necessary.

Safety
Leuze electronic MLC 520 7
2 Safety
Before using the safety sensor, a risk assessment must be performed according to valid standards (e.g.
ENISO12100, ENISO13849‑1, IEC61508, ENIEC62061). The result of the risk assessment determines
the required safety level of the safety sensor (see chapter 14.1 "Safety-relevant technical data").
For mounting, operating and testing, this document as well as all applicable national and international stan-
dards, regulations, rules and directives must be observed. Relevant and supplied documents must be ob-
served, printed out and handed to affected persons.
ÄBefore working with the safety sensor, completely read and observe the documents applicable to your
task.
In particular, the following national and international legal regulations apply for the start-up, technical in-
spections and work with safety sensors:
• Machinery directive 2006/42/EC
• Low voltage directive 2006/95/EC
• EMC directive 2004/108/EC
• Use of work equipment directive 89/655/EEC supplemented by directive 95/63EC
• OSHA 1910 Subpart O
• Safety regulations
• Accident-prevention regulations and safety rules
• Industrial safety regulation and employment protection act
• Product Safety Law (ProdSG)
NOTICE
For safety-related information you may also contact the local authorities (e.g., industrial inspec-
torate, employer's liability insurance association, labor inspectorate, occupational safety and
health authority).
2.1 Approved purpose and foreseeable improper operation
WARNING
A running machine may result in serious injury!
ÄMake certain that the safety sensor is correctly connected and that the protective function of
the protective device is ensured.
ÄMake certain that, during all conversions, maintenance work and inspections, the system is
securely shut down and protected against being restarted.
2.1.1 Proper use
• The safety sensor may only be used after it has been selected in accordance with the respectively ap-
plicable instructions and relevant standards, rules and regulations regarding labor protection and safety
at work, and after it has been installed on the machine, connected, commissioned, and checked by a
competent person (see chapter 2.2 "Competent persons").
• When selecting the safety sensor it must be ensured that its safety-related capability meets or exceeds
the required performance level PLr ascertained in the risk assessment (see chapter 14.1 "General
specifications").
• The safety sensor protects persons or body parts at points of operation, danger zones or access points
of machines and systems.
• With the “access guarding” function, the safety sensor detects persons only when they enter the danger
zone but cannot tell whether there are any persons inside the danger zone. For this reason, a start/
restart interlock in the safety chain is essential in this case.
• The construction of the safety sensor must not be altered. When manipulating the safety sensor, the
protective function is no longer guaranteed. Manipulating the safety sensor also voids all warranty
claims against the manufacturer of the safety sensor.

Safety
Leuze electronic MLC 520 8
• The safety sensor must be inspected regularly by a competent person to ensure proper integration and
mounting (see chapter 2.2 "Competent persons").
• The safety sensor must be exchanged after a maximum of 20 years. Repairs or exchange of wear parts
do not lengthen the service life.
2.1.2 Foreseeable misuse
Any use other than that defined under the “Approved purpose” or which goes beyond that use is consid-
ered improper use.
In principle, the safety sensor is not suitable as a protective device for use in the following cases:
• Danger posed by ejected objects or the spraying of hot or hazardous liquids from within the danger
zone
• Applications in explosive or easily flammable atmospheres
2.2 Competent persons
Prerequisites for competent persons:
• They have a suitable technical education.
• They know the rules and regulations for labor protection, safety at work and safety technology and can
assess the safety of the machine.
• They know the instructions for the safety sensor and the machine.
• You have been instructed by the responsible person on the mounting and operation of the machine and
of the safety sensor and you perform a task related to the subject matter shortly thereafter and keep
your knowledge up to date through continuous further training.
2.3 Responsibility for safety
Manufacturer and operating company must ensure that the machine and implemented safety sensor func-
tion properly and that all affected persons are adequately informed and trained.
The type and content of all imparted information must not lead to unsafe actions by users.
The manufacturer of the machine is responsible for:
• Safe machine construction
• Safe implementation of the safety sensor, verified by the initial test performed by a competent person
• Imparting all relevant information to the operator
• Adhering to all regulations and directives for the safe commissioning of the machine
The operator of the machine is responsible for:
• Instructing the operator
• Maintaining the safe operation of the machine
• Adhering to all regulations and directives for labor protection and safety at work
• Regular testing by competent persons
2.4 Disclaimer
LeuzeelectronicGmbH+Co.KG is not liable in the following cases:
• Safety sensor is not used as intended.
• Safety notices are not adhered to.
• Reasonably foreseeable misuse is not taken into account.
• Mounting and electrical connection are not properly performed.
• Proper function is not tested (see chapter 9 "Testing").
• Changes (e.g., constructional) are made to the safety sensor.

Device description
Leuze electronic MLC 520 9
3 Device description
The safety sensors from the MLC500 series are active opto-electronic protective devices. They satisfy the
following standards:
MLC500
Type in accordance with ENIEC61496 4
Category in accordance with ENISO13849 4
Performance Level (PL) in accordance with ENISO13849‑1 e
Safety Integrity Level (SIL) in accordance with IEC61508 and SILCL in ac-
cordance with ENIEC62061
3
The safety sensor consists of a transmitter and a receiver (see chapter 3.1 "Device overview"). It is pro-
tected against overvoltage and overcurrent acc. to IEC60204-1 (safety class3). Its infrared beams are not
influenced by ambient light (e.g. welding sparks, warning lights).
3.1 Device overview
The series is characterized by three different receiver classes (Basic, Standard, Extended) with specific
features and properties (see table below).
Tab.3.1: Device models in the series with specific features and functions
Transmitter Receiver
Basic Standard Ex-
tended
MLC500
MLC501
MLC500/A MLC502 MLC510
MLC511
MLC510/A MLC520 MLC530
OSSDs (2x) ■ ■ ■
AS-i ■ ■
Transmission chan-
nel changeover
■ ■ ■ ■ ■
LED indicator ■ ■ ■ ■ ■ ■ ■
7‑segment display ■ ■
Automatic start/
restart
■ ■ ■
RES ■ ■
EDM ■
Linkage ■
Blanking ■
Muting ■
Scan mode ■
Range reduction ■
Test input ■
Protective field properties
The beam distance and the number of beams are dependent on the resolution and protective field height.
NOTICE
Depending on the resolution, the effective protective field height can be larger than the optically
active area of the safety sensor housed in yellow (see chapter 3.1 "Device overview" and see
chapter 14.1 "General specifications").

Device description
Leuze electronic MLC 520 10
Device synchronization
The synchronization of receiver and transmitter for creating a functioning protective field is done optically,
i.e. without cables, via two specially coded synchronization beams. A cycle (i.e. a pass from the first to the
last beam) is called a scan. The length of a scan determines the length of the response time and affects the
calculation of the safety distance (see chapter 6.1.1 "Calculation of safety distanceS").
NOTICE
For the correct synchronization and function of the safety sensor, at least one of the two syn-
chronization beams must be free during synchronization and operation.
a
b
b
a Optically active area, housed in yellow
b Synchronization beams
Fig.3.1: Transmitter-receiver system
QR code
A QR code as well as the corresponding web address are located on the safety sensor.
At the web address, you will find device information and error messages (see chapter 11.3 "Error mes-
sages 7-segment display") after scanning the QR code with a mobile end device or after entering the web
address.
When using mobile end devices, mobile service charges can accrue.
Fig.3.2: QR code with corresponding web address (URL) on the safety sensor
3.2 Connection technology
The transmitter and receiver feature an M12 connector as an interface to the machine control with the fol-
lowing number of pins:

Device description
Leuze electronic MLC 520 11
Device model Device type Device plug
MLC500 Transmitter 5-pin
MLC520 Standard receiver 8-pin
3.3 Display elements
The display elements of the safety sensors simplify start-up and fault analysis.
3.3.1 Operating indicators on the MLC500 transmitter
Located in the connection cap on the transmitter are two LEDs which serve as function indicators:
1
2
1 LED1, green/red
2 LED2, green
Fig.3.3: Indicators on the MLC500 transmitter
Tab.3.2: Meaning of the LEDs on the transmitter
LED Color State Description
1 Green/red OFF Device switched off
Red Device error
Green Normal operation
2 Green Flashing For 10s after switch-on: reduced
range selected by the wiring of
pin4
OFF Transmission channel C1
ON Transmission channel C2
3.3.2 Operating indicators on the MLC520 receiver
Two LEDs and a 7-segment display for showing the operating state are located on the receiver:

Device description
Leuze electronic MLC 520 12
13
4
2
5
1 LED1, red/green
2 LED2, yellow
3 OSSD icon
4 RES icon
5 7‑segment display
Fig.3.4: Indicators on the MLC520 receiver
Tab.3.3: Meaning of the LEDs on the receiver
LED Color State Description
1 Red/green OFF Device switched off
Red OSSD off
red slowly flashing (approx.1Hz) External fault
red flashing fast (approx.10Hz) Internal fault
Green slowly flashing (approx.1Hz) OSSD on, weak signal
Green OSSD on
2 Yellow OFF • RES deactivated
• or RES activated and enabled
• or RES blocked and protective
field interrupted
ON RES activated and blocked but
ready to be unlocked - protective
field free
7-segment display at the MLC520 receiver
In normal operation, the 7-segment display shows the number of the selected transmission channel. In ad-
dition, it helps during the detailed error diagnostics (see chapter 11 "Troubleshooting") and serves as an
alignment aid (see chapter 8.2 "Aligning the sensor").
Tab.3.4: Meaning of the 7-segment display
Display Description
After switching on
8 Self test
tnn Response time (t) of the receiver in milliseconds (nn)
In normal operation
C1 Transmission channel C1
C2 Transmission channel C2

Device description
Leuze electronic MLC 520 13
Display Description
For alignment
Alignment display (see chapter 3.3.3 "Alignment display")
• Segment1: beam area in upper third of the protective field
• Segment2: beam area in middle third of the protective field
• Segment3: beam area in lower third of the protective field
For error diagnostics
F… Failure, internal device error
E… Error, external error
U… Usage info, application error
For error diagnostics, the error's respective letter is displayed first followed by the number code. The dis-
play is repeated cyclically. An AutoReset is carried out after 10s for errors that do not cause locking, with
an unauthorized restart being impossible. In the case of blocking errors, the voltage supply must be sepa-
rated and the cause of the error must be eliminated. Before switching on again, the steps taken before ini-
tial commissioning must be repeated (see chapter 9.1 "Before the initial start-up and following modifica-
tions").
The 7-segment display switches to alignment mode when the device has not yet been aligned or when the
protective field has been interrupted (after 5s). In this case, a fixed beam area from the protective field is
assigned to every segment.
3.3.3 Alignment display
Approximately 5s after a protective-field interruption, the 7-segment display switches to alignment mode.
In this mode, one third of the total protective field (top, middle, bottom) is assigned to one of the three hori-
zontal segments and the state of this sub-protective field displayed as follows:
Tab.3.5: Function of alignment display
Segment Description
On All beams in the beam area are uninterrupted.
Flashing At least one, but not all beams in the beam area are uninterrupted.
Switched off All beams in the beam area are interrupted.
When the protective field has been free for about 5s, the device switches back to the display of the operat-
ing mode.

Functions
Leuze electronic MLC 520 14
4 Functions
An overview of features and functions of the safety sensor can be found in chapter “Device descrip-
tion” (see chapter 3.1 "Device overview").
Overview of functions
• Start/restart interlock (RES)
• EDM
• Range reduction
• Transmission channel changeover
4.1 Start/restart interlock RES
After accessing the protective field, the start/restart interlock ensures that the safety sensor remains in the
OFF state after the protective field has been cleared. It prevents automatic release of the safety circuits
and automatic start-up of the system, e.g. if the protective field is again clear or if an interruption in the volt-
age supply is restored.
NOTICE
For access guarding, the start/restart interlock function is mandatory. The protective device may
only be operated without start/restart interlock in certain exceptional cases and under certain
conditions acc. to ENISO12100.
WARNING
Deactivation of the start/restart interlock may result in serious injury!
ÄImplement the start/restart interlock on the machine or in a downstream safety circuit.
Using start/restart interlock
ÄWire the MLC520 receiver appropriately for the desired operating mode (see chapter 7 "Electrical con-
nection")
The start/restart interlock function is automatically activated.
Switching the safety sensor back on after shutting down (OFF state):
ÄPress the reset button (press/release between 0.1s and 4s)
NOTICE
The reset button must be located outside the danger zone in a safe place and give the operator
a good view of the danger zone so that he/she can check whether anyone is located in it before
pressing the reset button.
DANGER
Risk of death if start/restart is operated unintentionally!
ÄEnsure that the reset button for unlocking the start/restart interlock cannot be reached from
the danger zone.
ÄBefore unlocking the start/restart interlock, make certain that no people are in the danger
zone.
After the reset button has been actuated, the safety sensor switches to the ON state.

Functions
Leuze electronic MLC 520 15
4.2 EDM contactor monitoring
NOTICE
The contactor monitoring of the MLC520 safety sensors can be activated through appropriate
wiring (see chapter 7.1.1 "MLC500 transmitter")!
The “contactor monitoring” function monitors the contactors, relays or valves connected downstream of the
safety sensor. Prerequisites for this are switching elements with positive-guided feedback contacts (nor-
mally closed contact).
Implement the contactor monitoring function:
• through appropriate wiring of the MLC520 safety sensors (see chapter 7.1.1 "MLC500 transmitter").
• through the external contactor monitoring of the downstream safety relay, (e.g. MSI series from Leuze
electronic)
• or through contactor monitoring of the downstream safety PLC (optional, integrated via a safety bus)
If contactor monitoring is activated (see chapter 7 "Electrical connection"), it operates dynamically, i.e., in
addition to monitoring the closed feedback circuit every time before the OSSDs are switched on, it also
checks whether the release of the feedback circuit opened within 500 ms and, after the OSSDs are
switched off, whether it has closed again within 500 ms. If this is not the case, the OSSDs return to the
OFF state after being switched on briefly. An error message appears on the 7-segment display (E30, E31)
and the receiver switches to the fault interlock state from which it can only be returned to normal operation
by switching the supply voltage off and back on again.
4.3 Transmission channel changeover
Transmission channels are used to prevent mutual interference of safety sensors which are located close
to each other.
NOTICE
To guarantee reliable operation, the infrared beams are modulated so they can be discerned
from the ambient light. Welding sparks or warning lights, e.g. from passing high-lift trucks,
thereby do not influence the protective field.
With the factory setting, the safety sensor works in all operating modes with transmission channelC1.
The transmission channel of the transmitter can be switched by changing the supply voltage polarity (see
chapter 7.1.1 "MLC500 transmitter").
The transmission channel of the receiver can be switched by changing the supply voltage polarity (see
chapter 7.1.2 "MLC520 receiver").
NOTICE
Faulty function due to incorrect transmission channel!
Select the same transmission channel on the transmitter and corresponding receiver.

Functions
Leuze electronic MLC 520 16
4.4 Range reduction
In addition to selecting the suitable transmission channels (see chapter 4.3 "Transmission channel
changeover"), the range reduction also serves to prevent mutual interference of adjacent safety sensors.
Activating the function reduces the light power of the transmitter so that around half of the nominal range is
reached.
Reducing range:
ÄWire pin4 (see chapter 7.1 "Pin assignment transmitter and receiver").
ðThe wiring of pin4 determines the transmitting power and thereby the range.
WARNING
Impairment of the protective function due to incorrect transmitting power!
The light power emitted from the transmitter is reduced through a single channel and without
safety-relevant monitoring.
ÄDo not use this configuration option for safety purposes.
ÄNote that the distance to reflective surfaces must always be selected so that no reflection
bypass can occur even at maximum transmitting power (see chapter 6.1.4 "Minimum dis-
tance to reflective surfaces").

Applications
Leuze electronic MLC 520 17
5 Applications
The safety sensor only creates square protective fields.
NOTICE
For applications with increased mechanical requirements, device models are available in ver-
sion MLC…/V (see chapter 15 "Ordering information and accessories").
5.1 Point of operation guarding
Point of operation guarding for hand and finger protection is typically the most common application for this
safety sensor. In accordance with ENISO13855, resolutions from 14to40mm make sense here. This
yields the necessary safety distance, among others (see chapter 6.1.1 "Calculation of safety distanceS").
Fig.5.1: Point of operation guarding protects reaching into the danger zone, e.g. for cartoners or filling systems
Fig.5.2: Point of operation guarding protects reaching into the danger zone, e.g. for a pick&place robot applica-
tion

Applications
Leuze electronic MLC 520 18
5.2 Access guarding
Safety sensors with up to 90mm resolution are used for access guarding into danger zones. They detect
people only upon entry into the danger zone, i.e., they do not detect parts of a person or whether a person
is present in the danger zone.
Fig.5.3: Access guarding on a transfer path
5.3 Danger zone guarding
Safety light curtains can be used in horizontal arrangement for danger zone guarding - either as stand-
alone device for presence monitoring or as stepping behind protection for presence monitoring e.g. in com-
bination with a vertically-arranged safety sensor. Depending on the mounting height, resolutions of
40or90mm are used (see chapter 15 "Ordering information and accessories").
Fig.5.4: Danger zone guarding on a robot

Mounting
Leuze electronic MLC 520 19
6 Mounting
WARNING
Improper mounting may result in serious injury!
The protective function of the safety sensor is only ensured if appropriately and professionally
mounted for the respective, intended area of application.
ÄOnly allow competent persons to install the safety sensor.
ÄMaintain the necessary safety distances (see chapter 6.1.1 "Calculation of safety dis-
tanceS").
ÄMake sure that stepping behind, crawling under or stepping over the protective device is reli-
ably ruled out and reaching under, over or around is taken into account in the safety dis-
tance, if applicable with additional distanceCRO corresponding to ENISO13855.
ÄTake measures to prevent that the safety sensor can be used to gain access to the danger
zone, e.g. by stepping or climbing into it.
ÄObserve the relevant standards, regulations and these instructions.
ÄClean the transmitter and receiver at regular intervals: environmental conditions (see chap-
ter 14 "Technical data"), care (see chapter 10 "Maintenance").
ÄAfter mounting, check the safety sensor for proper function.
6.1 Arrangement of transmitter and receiver
Optical protective devices can only perform their protective function if they are mounted with adequate
safety distance. When mounting, all delay times must be taken into account, such as the response times of
the safety sensor and control elements as well as the stopping time of the machine, among others.
The following standards specify calculation formulas:
• prENIEC61496-2, "Active Optoelectronic Protective Devices": distance of the reflecting surfaces/de-
flecting mirrors
• EN13855, "Safety of machines - The positioning of protective equipment in respect of approach
speeds of parts of the human body": mounting situation and safety distances
NOTICE
In accordance with ISO13855, with a vertical protective field, it is possible to pass under beams
over 300mm or pass over beams under 900mm. If the protective field is horizontal, climbing on
the safety sensor must be prevented through suitable installation or with covers and the like.
6.1.1 Calculation of safety distanceS
General formula for calculating the safety distanceS of an Optoelectronic Protective Device acc. to
ENISO13855
S [mm] = Safety distance
K [mm/s] = Approach speed
T [s] = Total time of the delay, sum from (ta+ti+tm)
ta[s] = Response time of the protective device
ti[s] = Response time of the safety relay
tm[s] = Stopping time of the machine
C [mm] = Additional distance to the safety distance

Mounting
Leuze electronic MLC 520 20
NOTICE
If longer stopping times are determined during regular inspections, an appropriate additional
time must be added to tm.
6.1.2 Calculation of safety distance if protective fields act orthogonally to the approach direction
With vertical protective fields, ENISO13855 differentiates between
• SRT: safety distance concerning access through the protective field
• SRO: safety distance concerning access over the protective field
The two values are distinguished by the way additional distanceC is determined:
• CRT: from a calculation formula or as a constant (see chapter 6.1.1 "Calculation of safety distanceS")
• CRO: from the following table “Reaching over the vertical protective field of electro-sensitive protective
equipment (excerpt from ENISO13855)”
The larger of the two values SRT and SRO is to be used.
Calculation of safety distanceSRT acc. to ENISO13855 when access occurs through the protective
field:
Calculation of safety distanceSRT for point of operation guarding
SRT [mm] = Safety distance
K [mm/s] = Approach speed for point of operation guarding with approach reaction and normal approach di-
rection to the protective field (resolution 14to40mm): 2000mm/s or 1600mm/s, when
SRT>500mm
T [s] = Total time of the delay, sum from (ta+ti+tm)
ta[s] = Response time of the protective device
ti[s] = Response time of the safety relay
tm[s] = Stopping time of the machine
CRT [mm] = Additional distance for point of operation guarding with approach reaction with resolutions of
14to40mm, d=resolution of protective device CRT=8×(d-14)mm
Calculation example
The feeding-in area in a press with a stopping time (including press Safety PLC) of 190ms is to be safe-
guarded with a safety light curtain with 20mm of resolution and 1200mm of protective field height. The
safety light curtain has a response time of 22ms.
ÄCalculate safety distanceSRT using the formula acc. to ENISO13855.
K [mm/s] = 2000
T [s] = (0.022+0.190)
CRT [mm] = 8×(20-14)
SRT [mm] = 2000mm/s×0.212s+48mm
SRT [mm] = 472
SRT is smaller than 500mm; this is why the calculation may not be repeated with 1600mm/s.
NOTICE
Implement the stepping behind protection required here, e.g., through the use of an additional or
cascaded safety sensor for area protection.
Table of contents
Other Leuze electronic Security Sensor manuals

Leuze electronic
Leuze electronic MLD 300 User manual
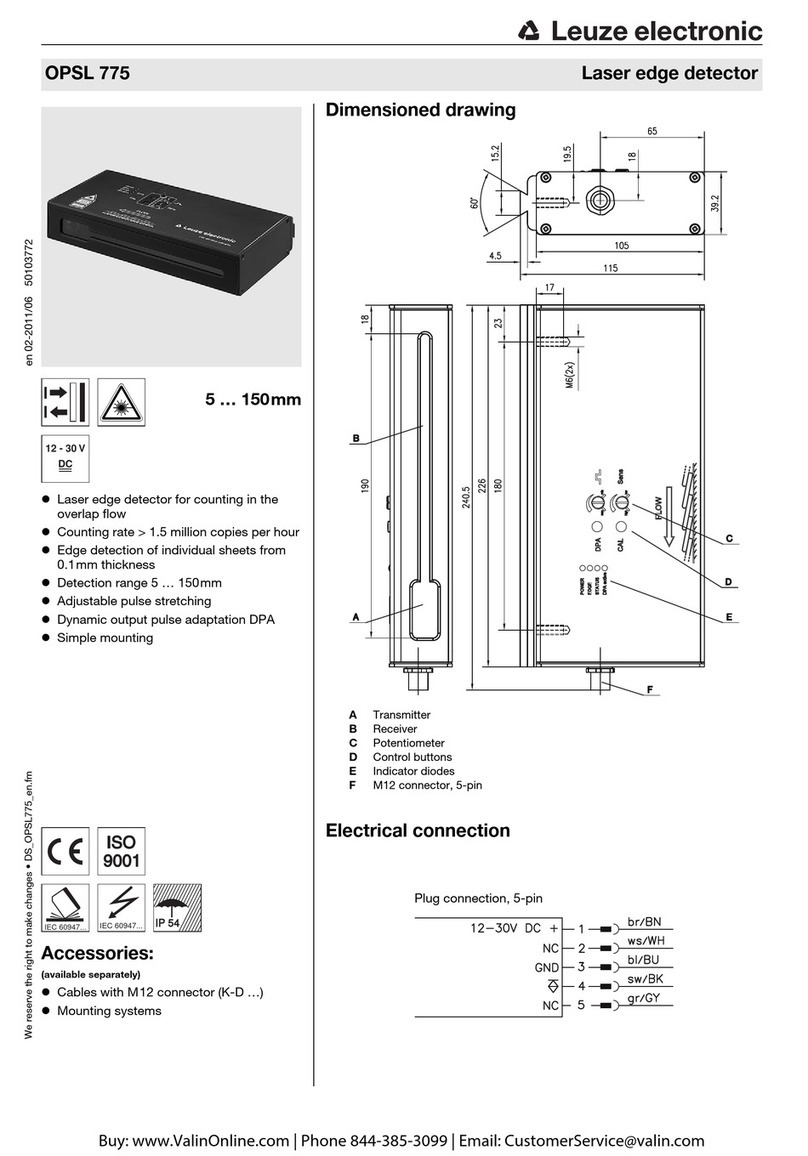
Leuze electronic
Leuze electronic OPSL 775 User manual
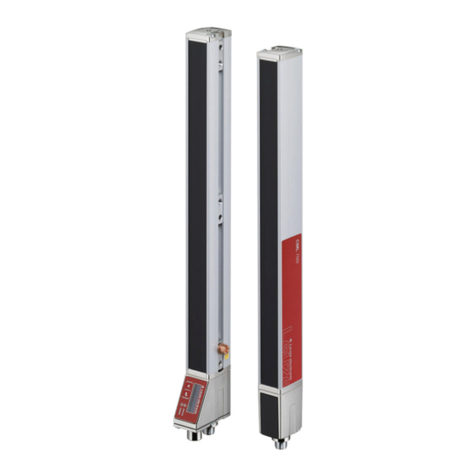
Leuze electronic
Leuze electronic CML 720i Ex User manual

Leuze electronic
Leuze electronic MLC 500 Series User manual
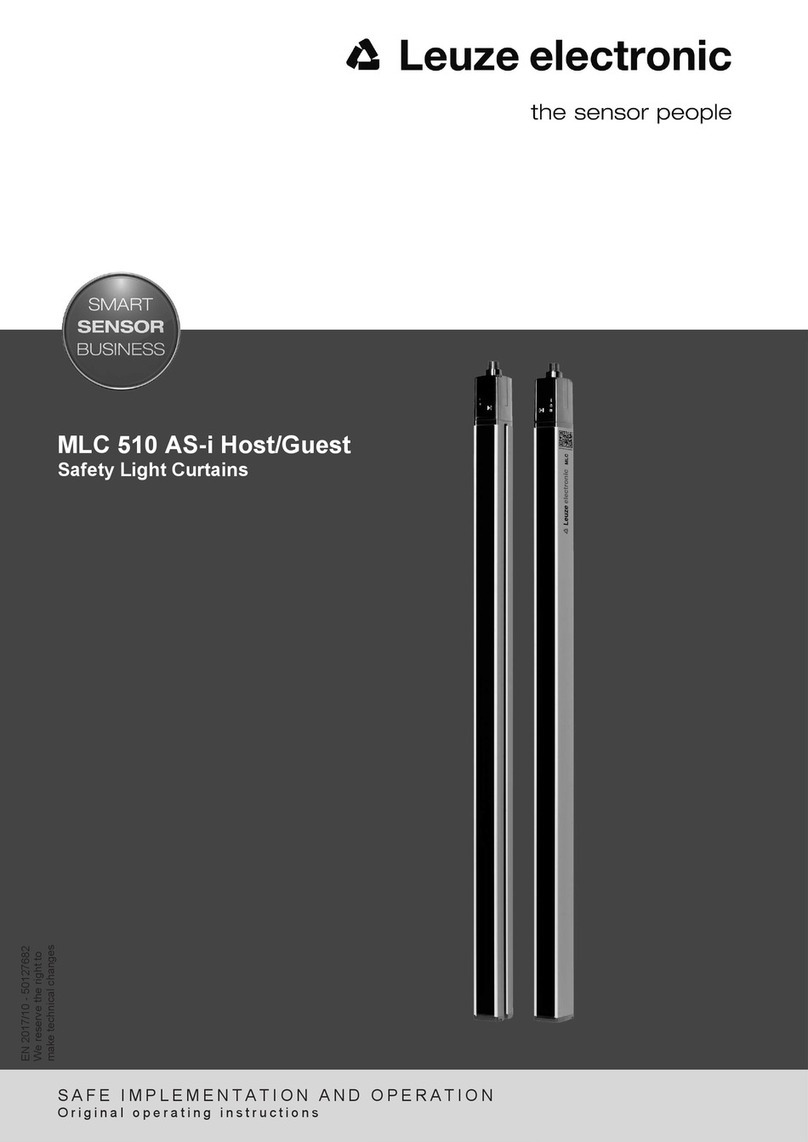
Leuze electronic
Leuze electronic MLC 510 AS-i Host/Guest User manual
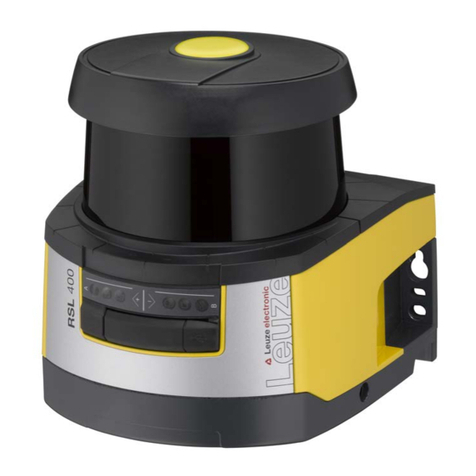
Leuze electronic
Leuze electronic RSL 430 User manual
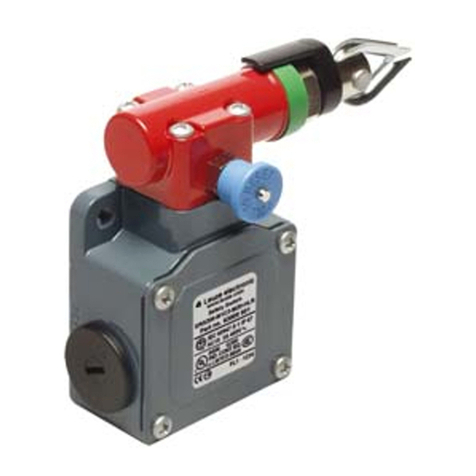
Leuze electronic
Leuze electronic ERS200-M0C3-M20-HLR User manual
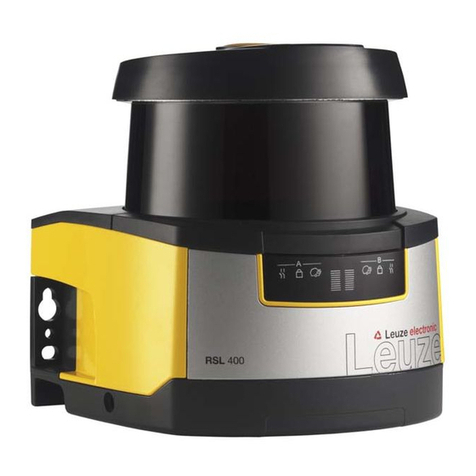
Leuze electronic
Leuze electronic CU411-RS4 User manual
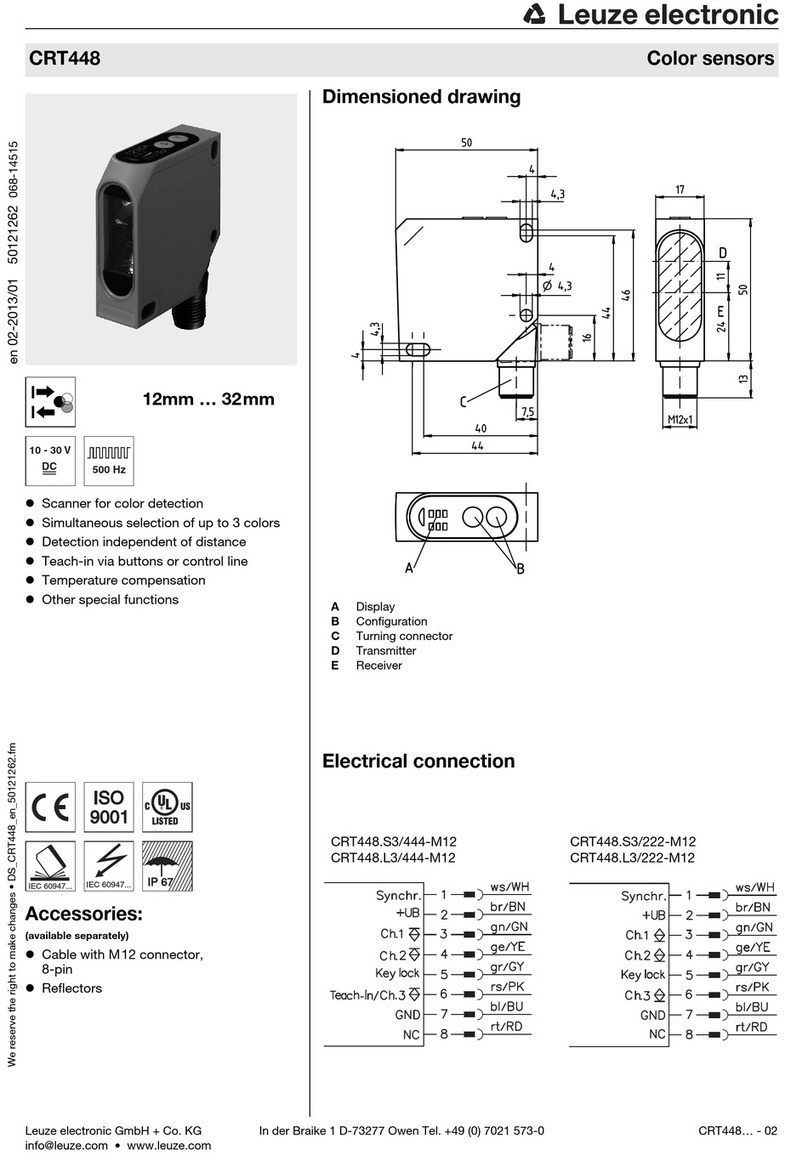
Leuze electronic
Leuze electronic CRT448 User manual
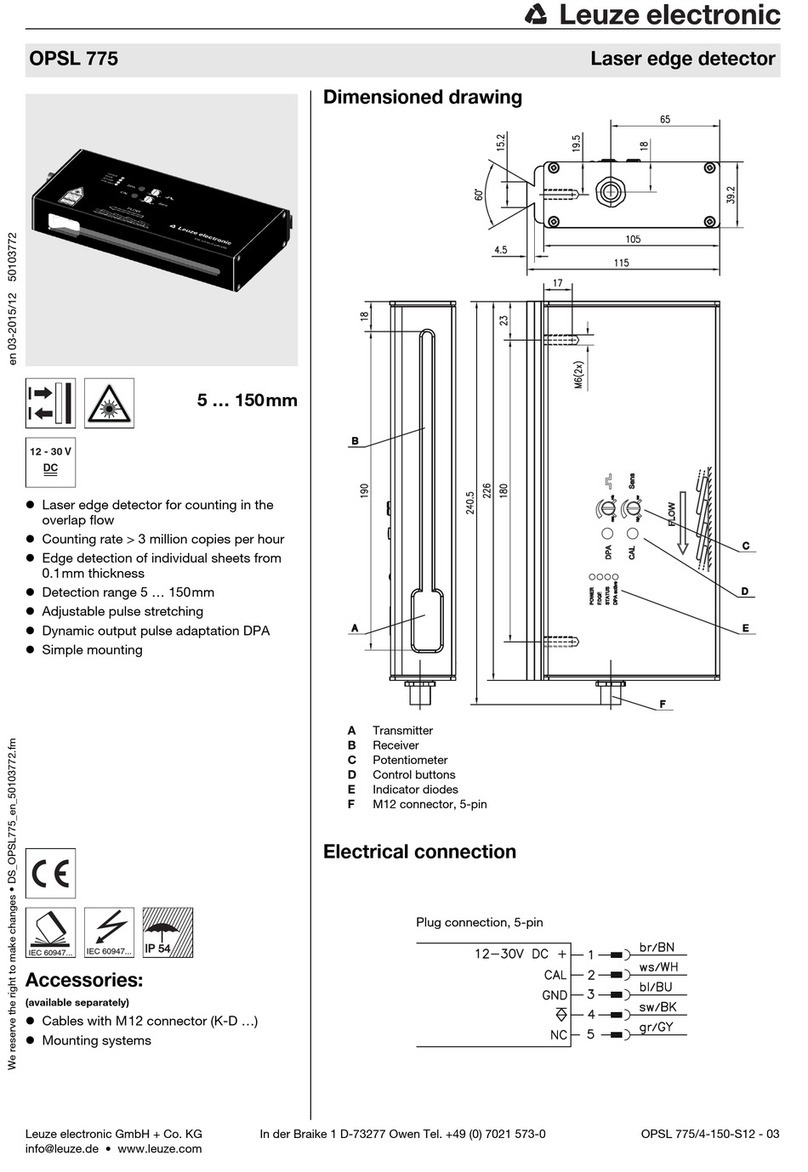
Leuze electronic
Leuze electronic OPSL 775 User manual