LinMot E1100-GP User manual

Documentation of the MasterSlave Application of the
following Controllers:
- E1100-GP (-HC)
- E1130-DP (-HC, -XC)
- E1100-RS (-HC, -XC)
- E1100-DN (-HC, -XC)
- E1100-CO (-HC, -XC)
MasterSlave V3.7
User Manual

L
i
n
M
o
t
®
MasterSlave Application
Page 2/8 User Manual MasterSlave Application / 13.12.2007 NTI AG / LinMot
© 2007NTI AG
This work is protected by copyright.
Under the copyright laws, this publication may not be reproduced or transmitted in any form, electronic or mechanical, including
photocopying,
recording, microfilm, storing in an information retrieval system, not even for didactical use, or translating, in whole or in
part, without the prior written consent of NTI AG.
LinMot® is a registered trademark of NTI AG.
Note
The information in this documentation reflects the stage of development at the time of press and is therefore without obligation.
NTI AG. reserves itself the right to make changes at any time and without notice to reflect further technical advance or product
improvement. Please refer to the latest edition of our "General business terms"
Document version 3.7 / December 2007

MasterSlave Application
L
i
n
M
o
t
®
NTI AG / LinMot User Manual MasterSlave Application / 13.12.2007 Page 3/8
Table of Content
1. SYSTEM OVERVIEW.........................................................................................................4
2. CONNECTING THE CAN BUS ...........................................................................................4
Pin Assignment of the COM Connector:............................................................................4
Pin Assignment of the CMD Connectors X7/X8 :..............................................................4
Pin Assignment of the Master Encoder Connectors X10/X11 for the GP servos:.............5
CAN/RS 485 Termination...................................................................................................5
3. USING THE MASTER/SLAVE SW......................................................................................6
4. MASTER SLAVE PARAMETERS.........................................................................................7
5. CONTACT ADDRESSES.....................................................................................................8

L
i
n
M
o
t
®
MasterSlave Application
Page 4/8 User Manual MasterSlave Application / 13.12.2007 NTI AG / LinMot
1. System Overview
The MasterSlave Application SW is an easy to use SW for following applications:
• Current master motor with one current slave motor to double force
• Gantry master motor with one gantry slave motor which has the same position setpoint
The MasterSlave Application SW supports the Master/Slave linked either Over the CAN-Bus
(X7/X8 or X10/X11) or over the RS485 (only X7/X8). For the CAN-Bus interfaces like
CAN-Open or DeviceNet the RS485 based linked has to be used for all other interfaces the
CAN-Bus linked mode should be used, the RS232-maintenance link on X5 Connector is still
available.
2. Connecting the CAN bus
Pin Assignment of the COM Connector:
DSBU 9 male:
Pin 1 RS-485 Y Pin 6 RS-485 B
Pin 2 RS-232 TX Pin 7 RS-485 Z
Pin 3 RS-232 RX Pin 8 CAN L
Pin 4 RS-485 A Pin 9 CAN H
Pin 5 GND
Pin Assignment of the CMD Connectors X7/X8 :
The CMD connector exists only at the E1100-DP(-HC) and E1100-RS(-HC) controllers,
2xRJ45 with 1:1 connected signals. Standard twisted pairs: 1/2, 3/6, 4/5, 7/8. Use Ethernet
cables according the EIA / TIA 568A standard (Art. Nr. 0150-1853). Over the X7/X8 the
CAN-Bus linked or the RS485 linked Master/Slave mode could be used.
1
8
1
8
Pin 1 RS485 A
Pin 2 RS485 B
Pin 3 RS485 Y
Pin 4/5 Ground
Pin 6 RS485 Z
Pin 7 CAN H
Pin 8 CAN L

MasterSlave Application
L
i
n
M
o
t
®
NTI AG / LinMot User Manual MasterSlave Application / 13.12.2007 Page 5/8
Pin Assignment of the Master Encoder Connectors X10/X11 for the GP
servos:
With the E1100-GP(-HC) controllers, the CAN bus is also available on the two RJ45
connectors X10 (ME IN) and X11 (ME OUT) with 1:1 connected signals. Standard twisted
pairs: 1/2, 3/6, 4/5, 7/8. Use Ethernet cables according the EIA / TIA 568A standard to loop
through the CAN bus over this connector (Art. Nr. 0150-1852). Over the X10/X11 connection
only the CAN-Bus linked Master/Slave mode could be used!
1
8
1
8
CAN/RS 485 Termination
The CAN bus must be terminated by two 120 Ohm resistors at both ends of the bus line,
according the following scheme:
For easy installation, the LinMot E1100 controllers have built in termination resistors, which
have to be activated on both the master and the slave servo, using the Master/Slave
application SW over CAN bus and the RS 485 link.
The built in termination resistor for the CAN bus can be
activated by setting the dip switch “CAN Term” to “ON”.
The built in termination resistor for the RS 485 bus can be
activated by setting the dip switch “RS485 Term” to
“ON”.
Interface
CAN Term
RS485 Term
RS485/232
4
3
2
1
S3
On-Off
Pin 1 A
Pin 2 /A
Pin 3 B
Pin 4 Z
PIN 5 /Z
Pin 6 /B
Pin 7 CAN H
Pin 8 CAN L

L
i
n
M
o
t
®
MasterSlave Application
Page 6/8 User Manual MasterSlave Application / 13.12.2007 NTI AG / LinMot
3. Using the Master/Slave SW
To install the Master/Slave Application SW start the LinMot-Talk1100 SW, or if already
started and logged in logout, then push the Install Firmware button, select the installation
script under:
//Firmware/Applications/MasterSlave/MasterSlave_V3Sxxyy.sct
The same Master/Slave application SW has to be loaded to both the master servo controller
and the slave servo controller.
Select the needed serial link CAN or RS 485 (UPID3100).
After the Master/Slave application SW is installed log in the Servo and Select the correct
Master Slave Mode (UPID 30D4h) on both servo controllers. The rest could be leave as
configured as default.
After power up the master servo controller try to connect to its slave controller, when it
succeed to connect to the slave, the application Warn Flag bit 15 vanish ant the connection
state (UPID 3A98h or 3A99h) changes to 1 which means ‘Data Exchange’.
The state of the slave servo controller could be monitored over the variable Slave State Var
(UPID 3B70h).
Though the slave servo is in a streaming mode (current or position) in state 8 ‘Operation
Enabled’ the bit 5 ‘Motion Active’ normally is set and bit 6 ‘In Target Position’ is cleared in
the Slave State Var. But bit 8 ‘Homed ‘ indicates if the slave servo has correctly homed or
not.
The slave state machine is controlled from the master, so if connecting a serial fieldbus link to
the slave servo for monitoring reasons, take care to not write to the control word of the
slave. So with Profibus DP interface do not configure the control status module, the status
word could be monitored word over a monitoring channel with UPID 1D51h.

MasterSlave Application
L
i
n
M
o
t
®
NTI AG / LinMot User Manual MasterSlave Application / 13.12.2007 Page 7/8
4. Master Slave Parameters
The Master/Slave Servo Controllers have an additional parameter tree branch, which can be
configured with the distributed LinMot-Talk1100 software. With these parameters, the
Master/Slave behaviour can be configured. The software LinMot-Talk1100 can be
downloaded from http://www.linmot.com under the section download, software & manuals.
Master Slave Mode defines the master/slave behaviour of the controller.
Master Slave Appl\ Serial Link Selection
CAN [0] MasterSlave communication over CAN bus
1Mbaud.
RS485[1] MasterSlave communication over RS485.
Master Slave Mode defines the master/slave behaviour of the controller.
Master Slave Appl\ Master Slave Mode
Disable [0] Servo controller runs without Master Slave
behaviour.
Current Master[1] Servo controller acts as current master
Current Slave [2] Servo controller acts as current slave
Gantry Master [3] Servo controller acts as gantry master
Gantry Slave [4] Servo controller acts as gantry slave
Master Config In this section the further master configurations are done.
Master MACID The ID of the master servo, default = 1, should not be changed
Slave Config In this section the further master configurations are done.
Slave MACID The ID of the slave servo, default = 2, should not be changed
Direction Coose ‘Normal’ if the slave is mounted in the same way like the master
and moves in the same direction as the master, otherwise ‘Inverted’.
CAN Baud Rate In this section the CAN baud rate is configured.
Baud Rate Parameter Definition
The CAN Baud rate is fixed to 1M baud by this parameter.

L
i
n
M
o
t
®
MasterSlave Application
Page 8/8 User Manual MasterSlave Application / 13.12.2007 NTI AG / LinMot
5. Contact Addresses
-----------------------------------------------------------------------------------------------------------------------------
SWITZERLAND NTI AG
Haerdlistr. 15
CH-8957 Spreitenbach
Sales and Administration: +41-(0)56-419 91 91
office@linmot.com
Tech. Support: +41-(0)56-544 71 00
Fax: +41-(0)56-419 91 92
Web: http://www.linmot.com/
-----------------------------------------------------------------------------------------------------------------------------
USA LinMot, Inc.
5750 Townline Road
Elkhorn, WI 53121
Sales and Administration: 877-546-3270
262-743-2555
Tech. Support: 877-804-0718
262-743-1284
Fax: 800-463-8708
262-723-6688
Web: http://www.linmot-usa.com/
-----------------------------------------------------------------------------------------------------------------------------
Please visit http://www.linmot.com/ to find the distribution near you.
Smart solutions are…
Other manuals for E1100-GP
1
This manual suits for next models
8
Table of contents
Other LinMot Controllers manuals
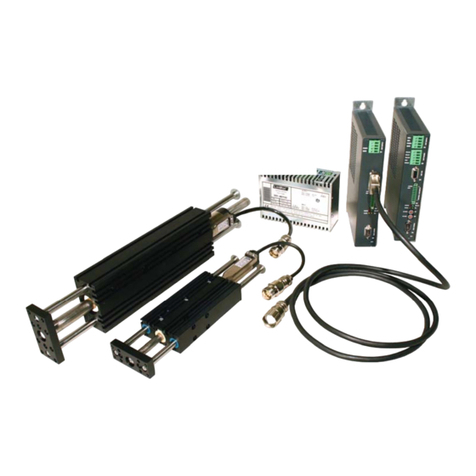
LinMot
LinMot E1200-GP-UC User manual
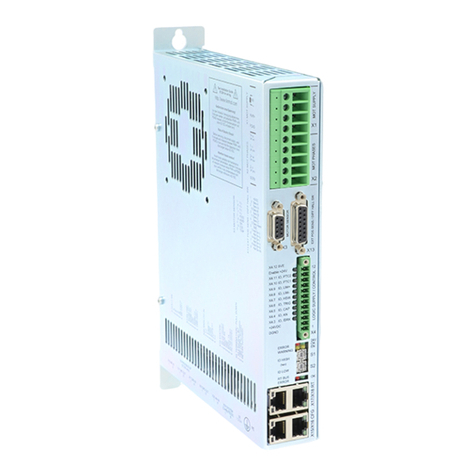
LinMot
LinMot E1250-EC-UC User manual
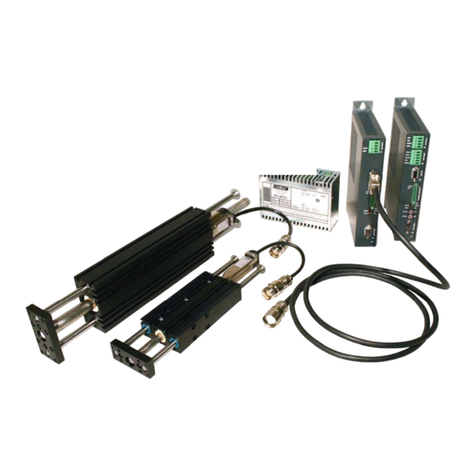
LinMot
LinMot E1200-GP-UC Instruction Manual
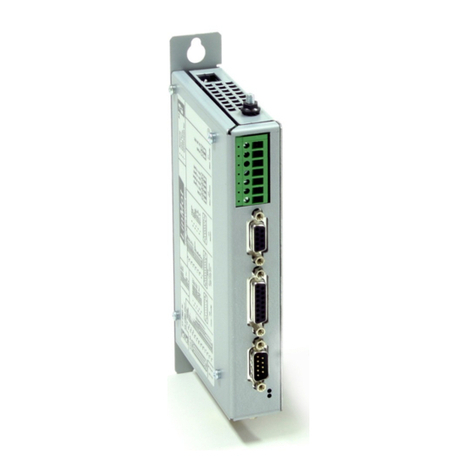
LinMot
LinMot B1100-PP User manual
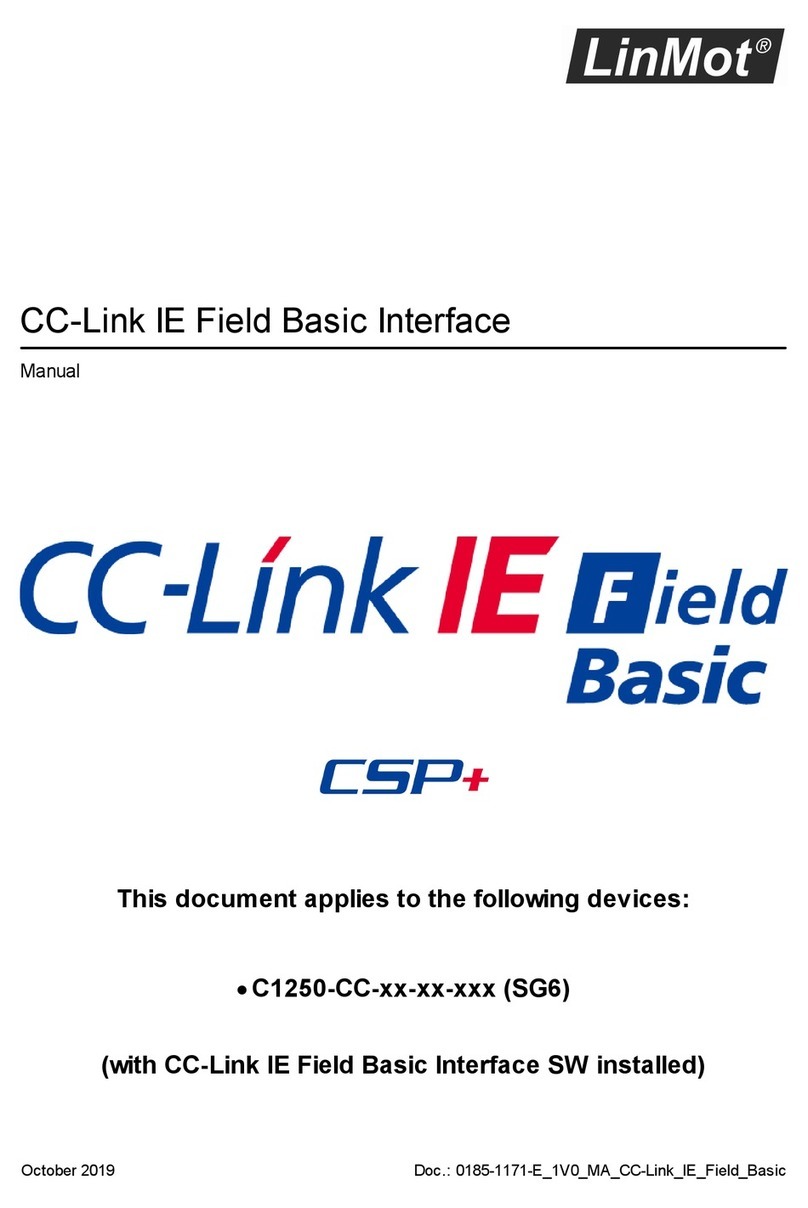
LinMot
LinMot CC-Link IE Field Basic C1250-CC Series User manual
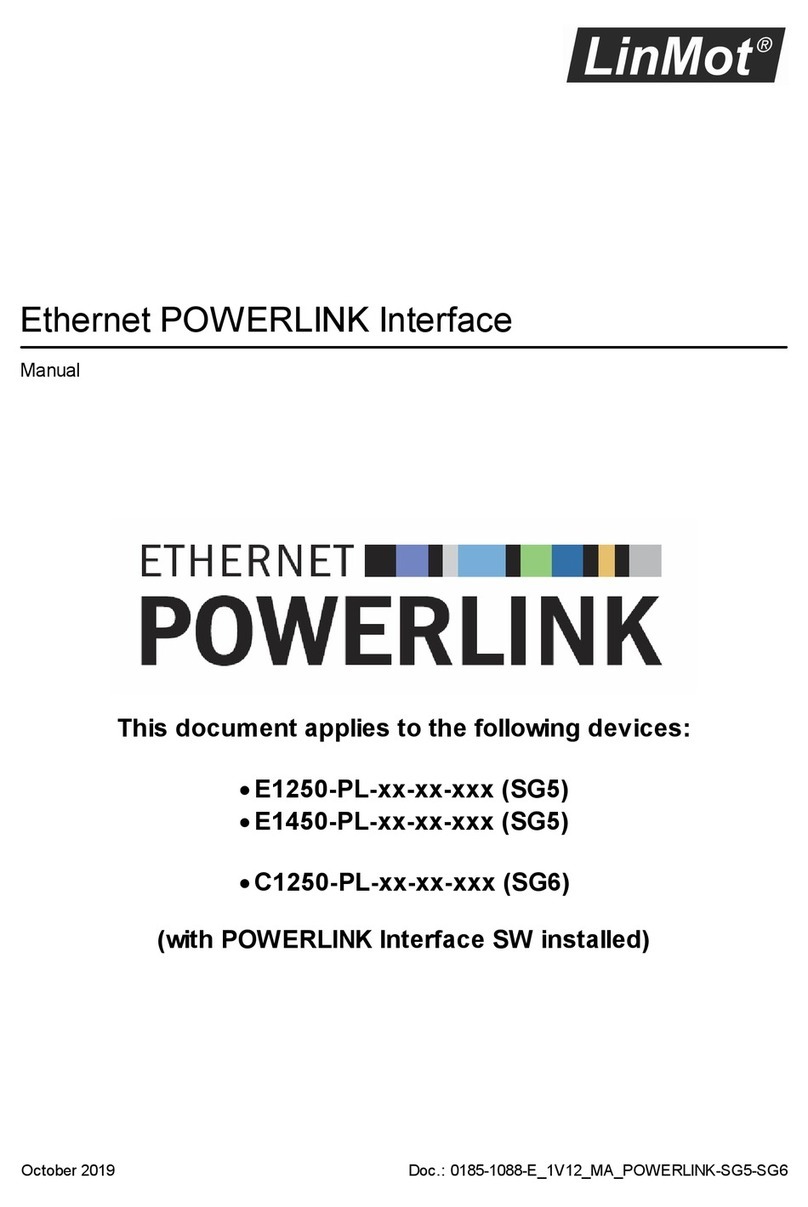
LinMot
LinMot E1250-PL Series User manual
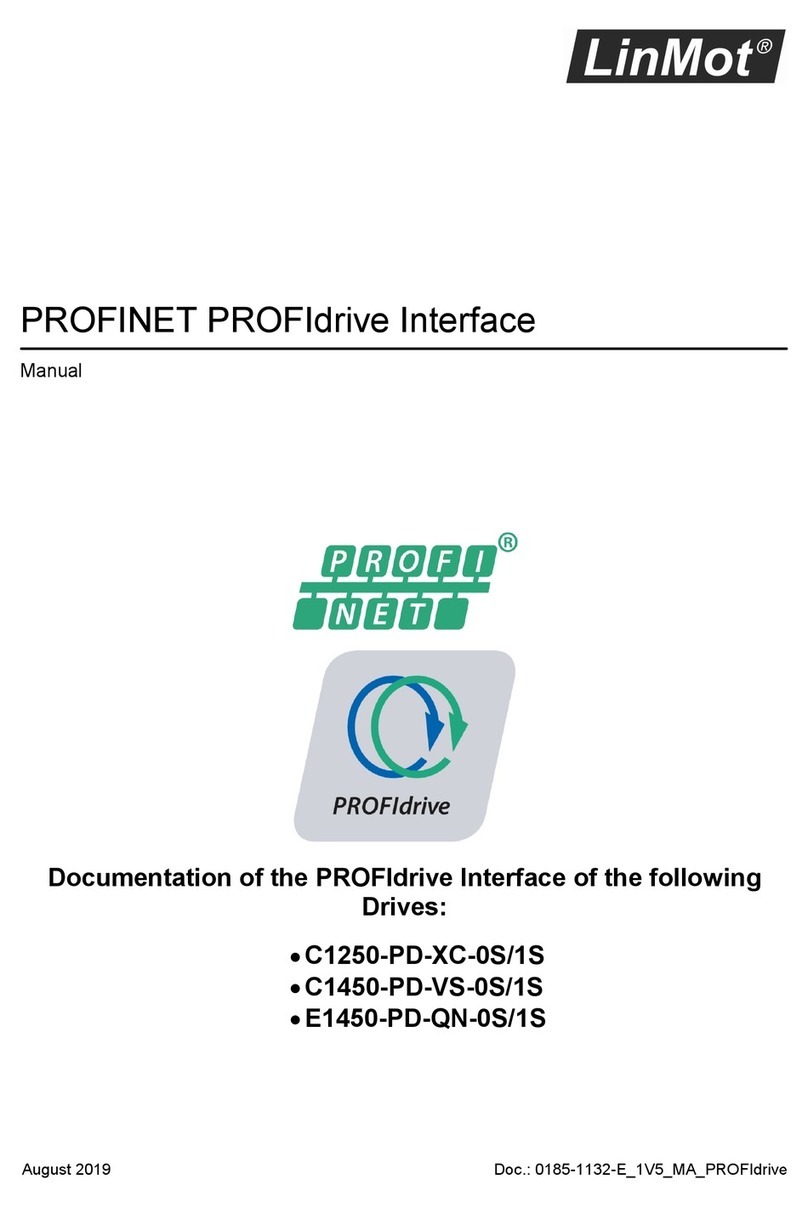
LinMot
LinMot C1250-PD-XC-0S/1S User manual

LinMot
LinMot Series E1400-GP User manual
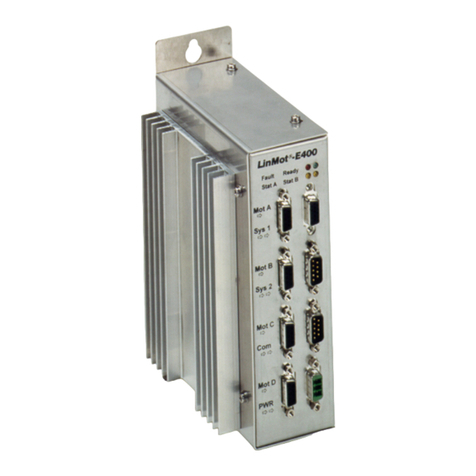
LinMot
LinMot E100 Series User manual
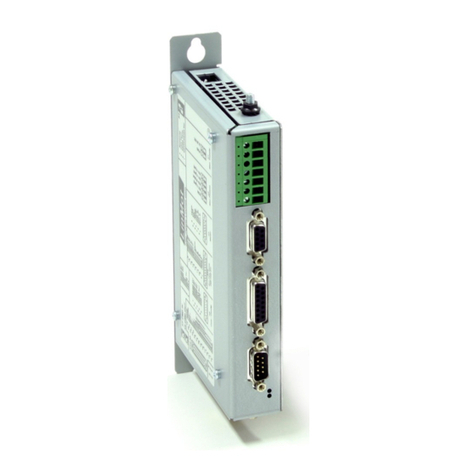
LinMot
LinMot B1100-PP User manual