Makita DTD148 User manual














Other manuals for DTD148
1
Other Makita Impact Driver manuals
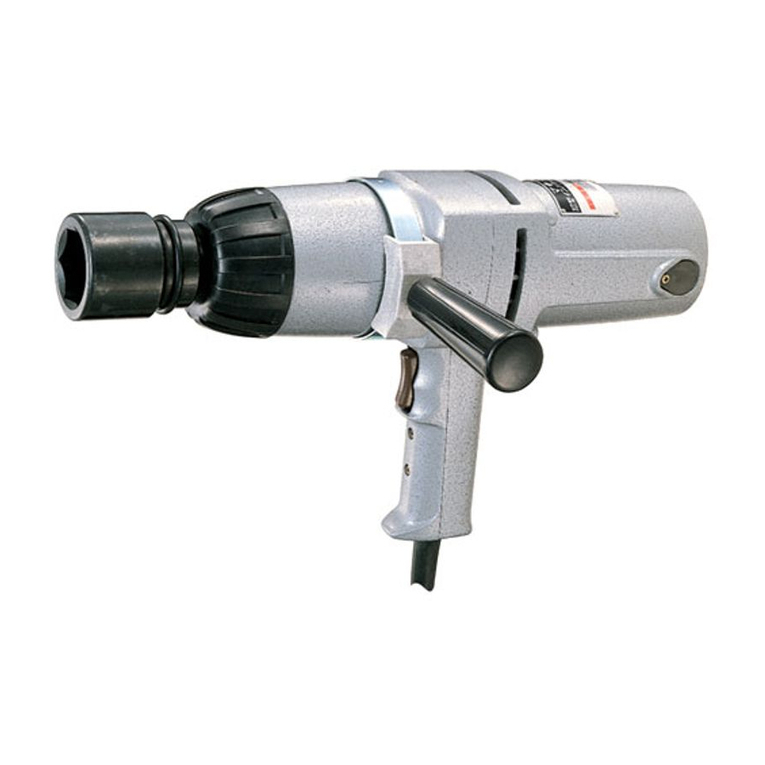
Makita
Makita 6910 User manual
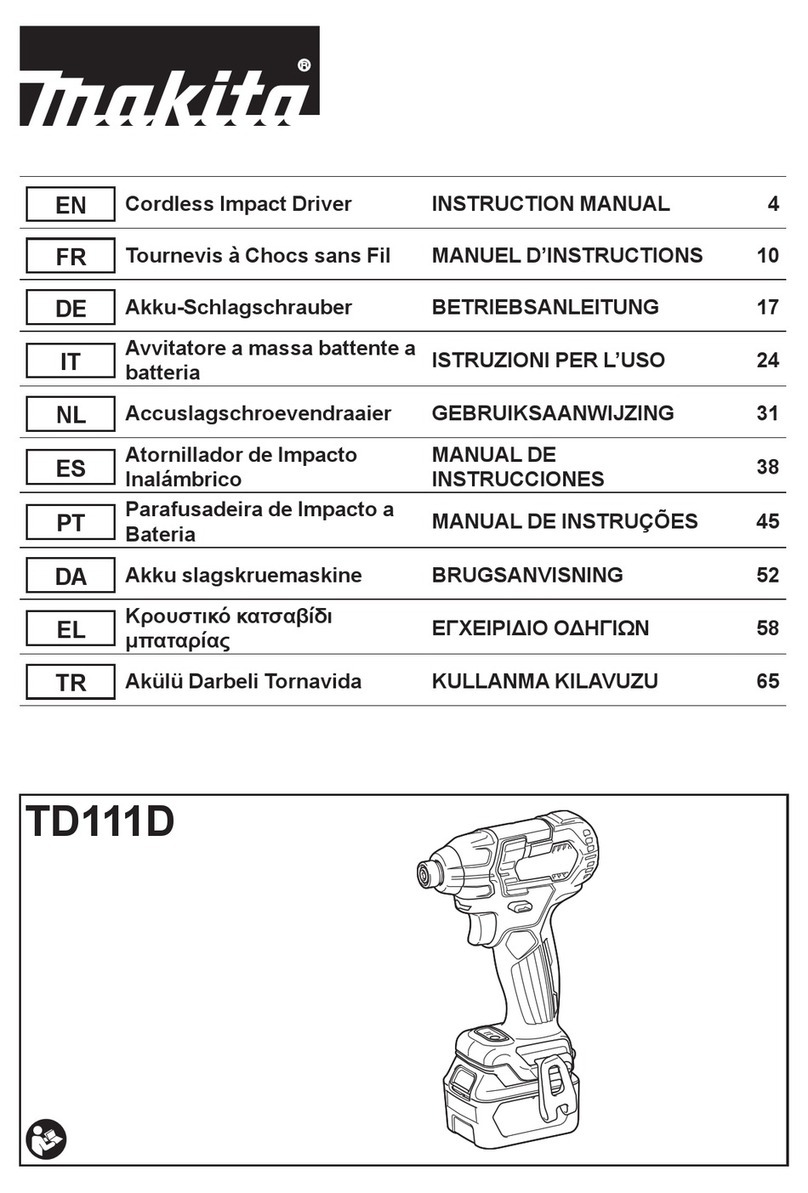
Makita
Makita TD111DY1J User manual
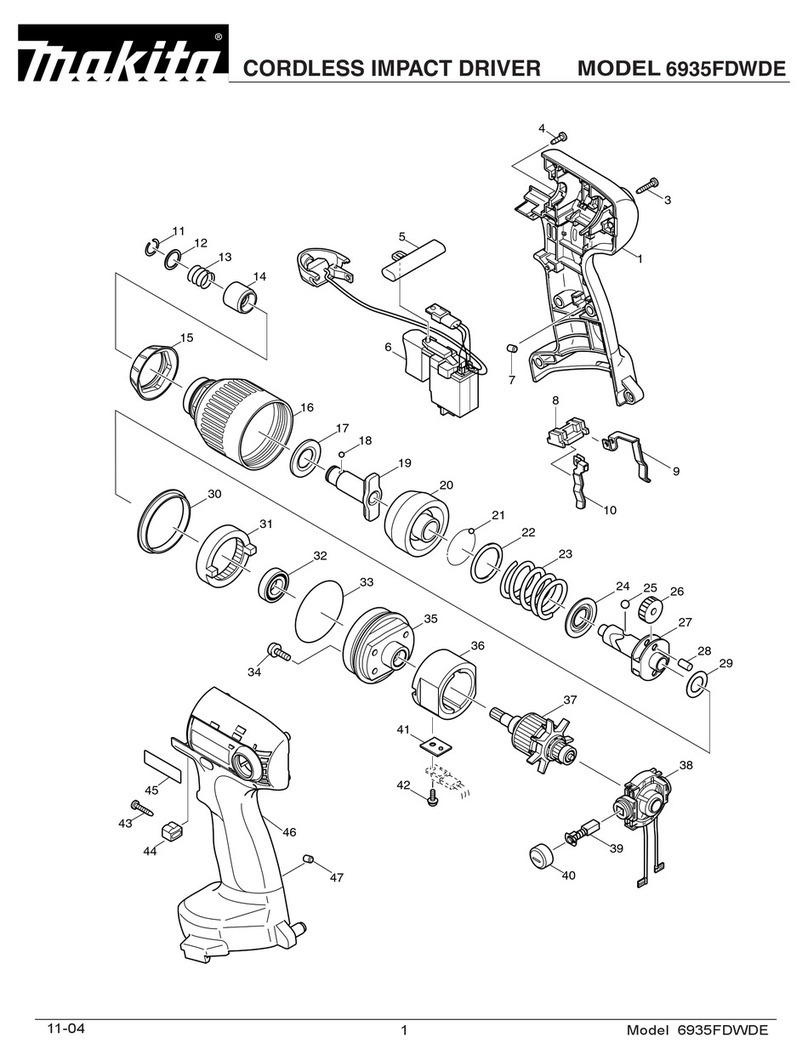
Makita
Makita 6935FDWDE User manual
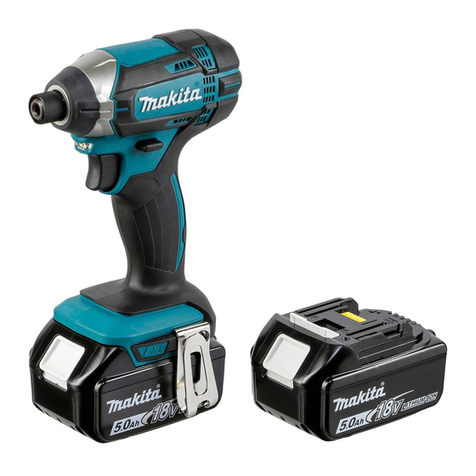
Makita
Makita DTD152 User manual
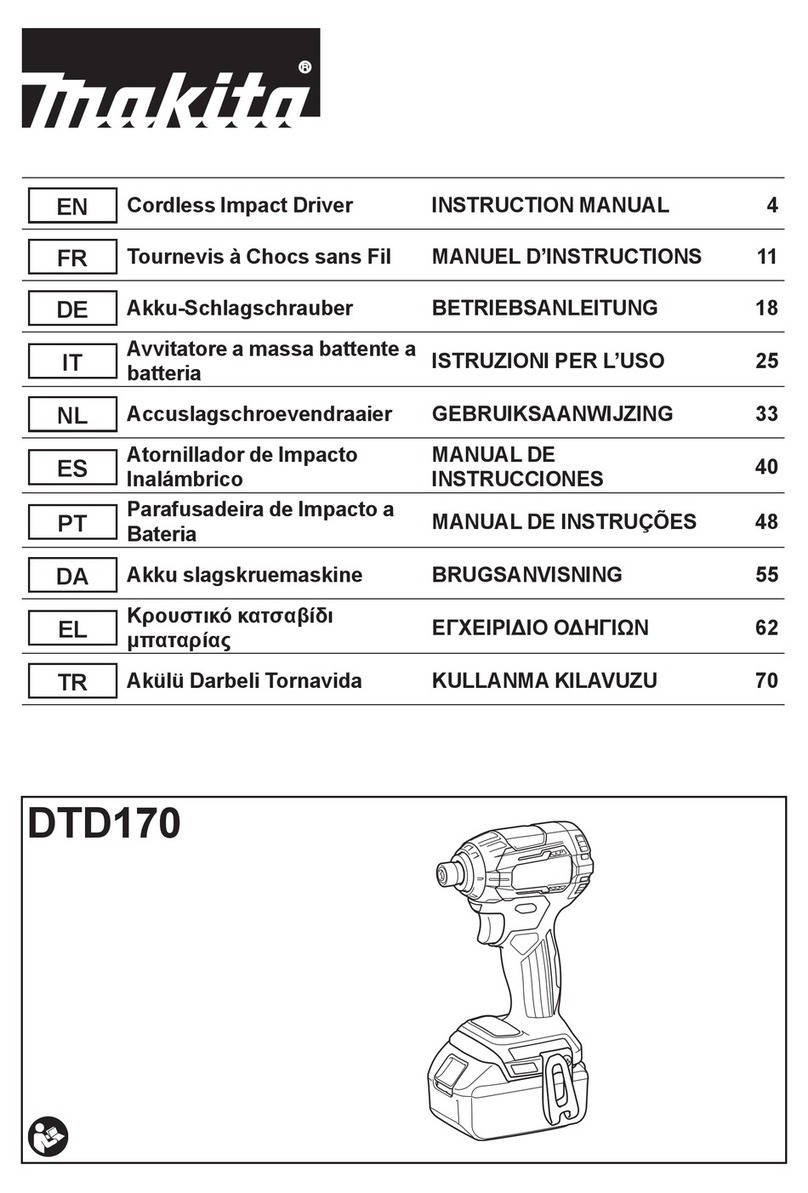
Makita
Makita DTD170 User manual
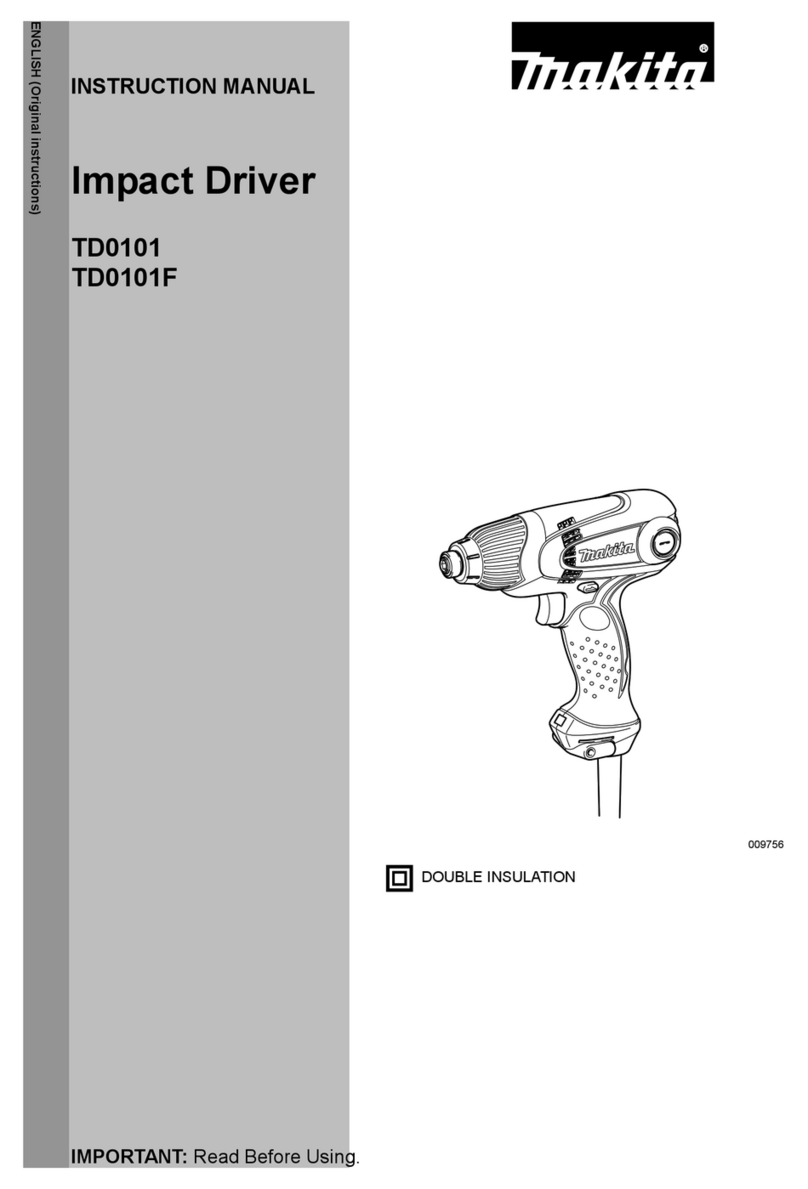
Makita
Makita TD0101 User manual
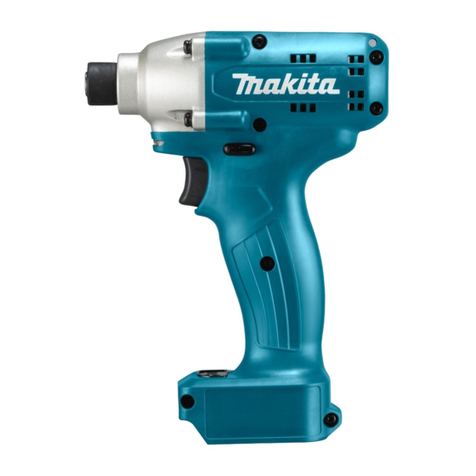
Makita
Makita TD112D User manual
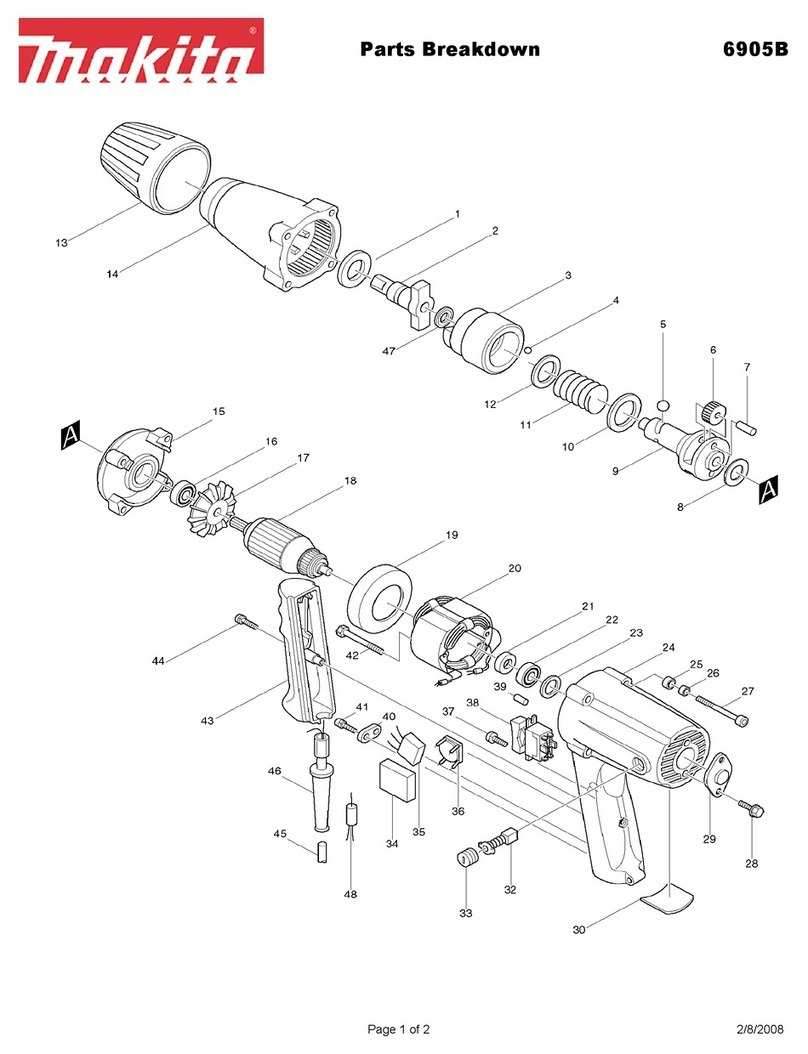
Makita
Makita 6905B Quick start guide
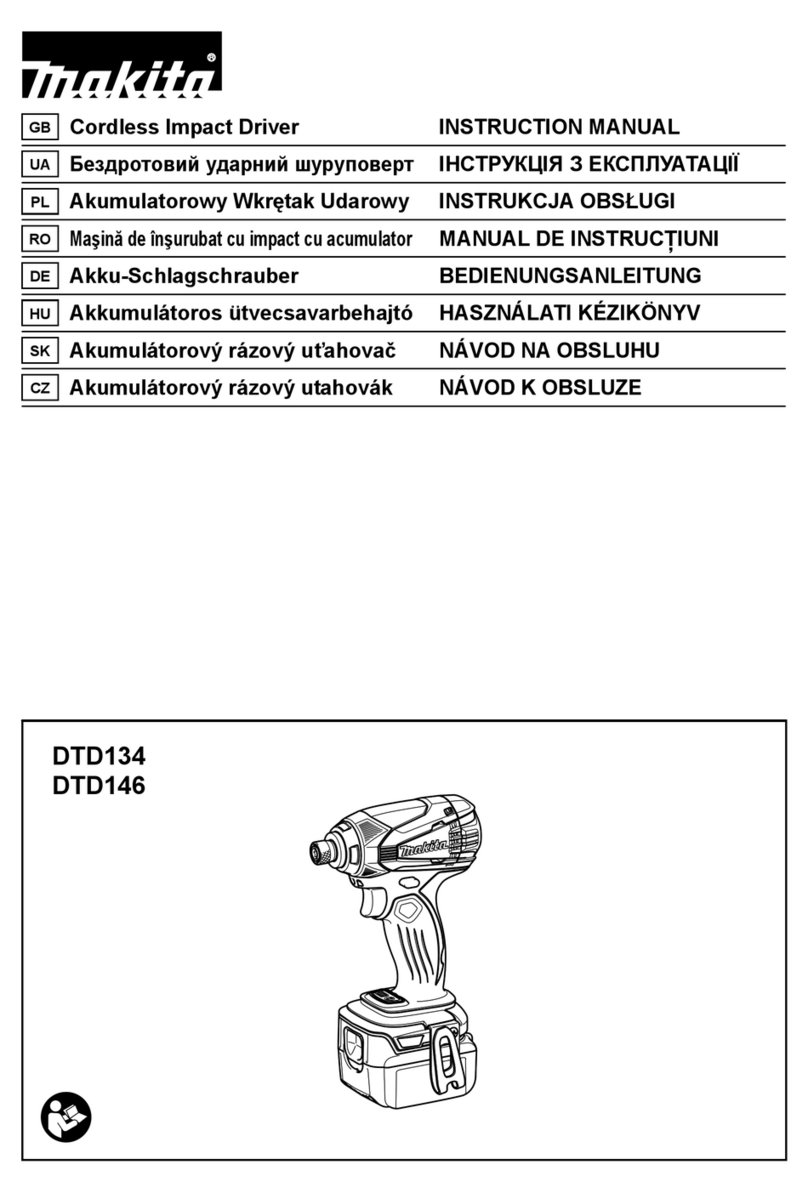
Makita
Makita DTD134 User manual
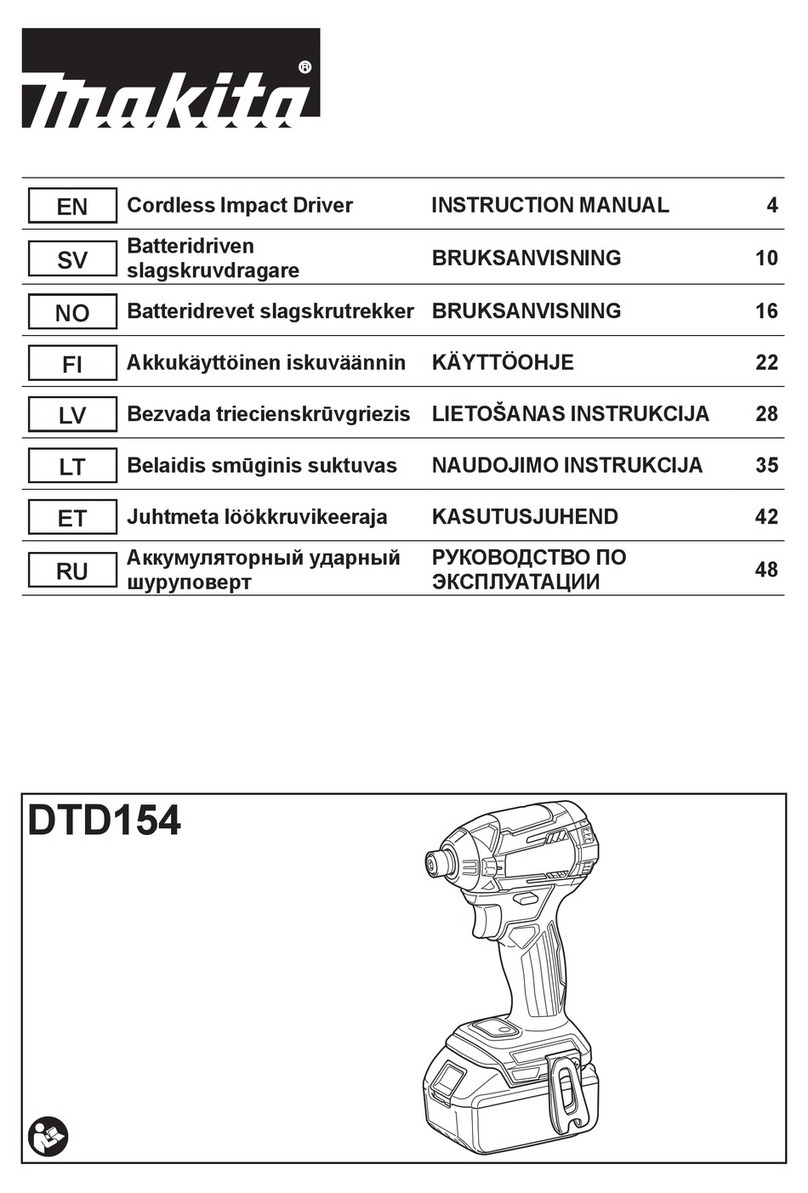
Makita
Makita DTD154 User manual

Makita
Makita TD110D User manual
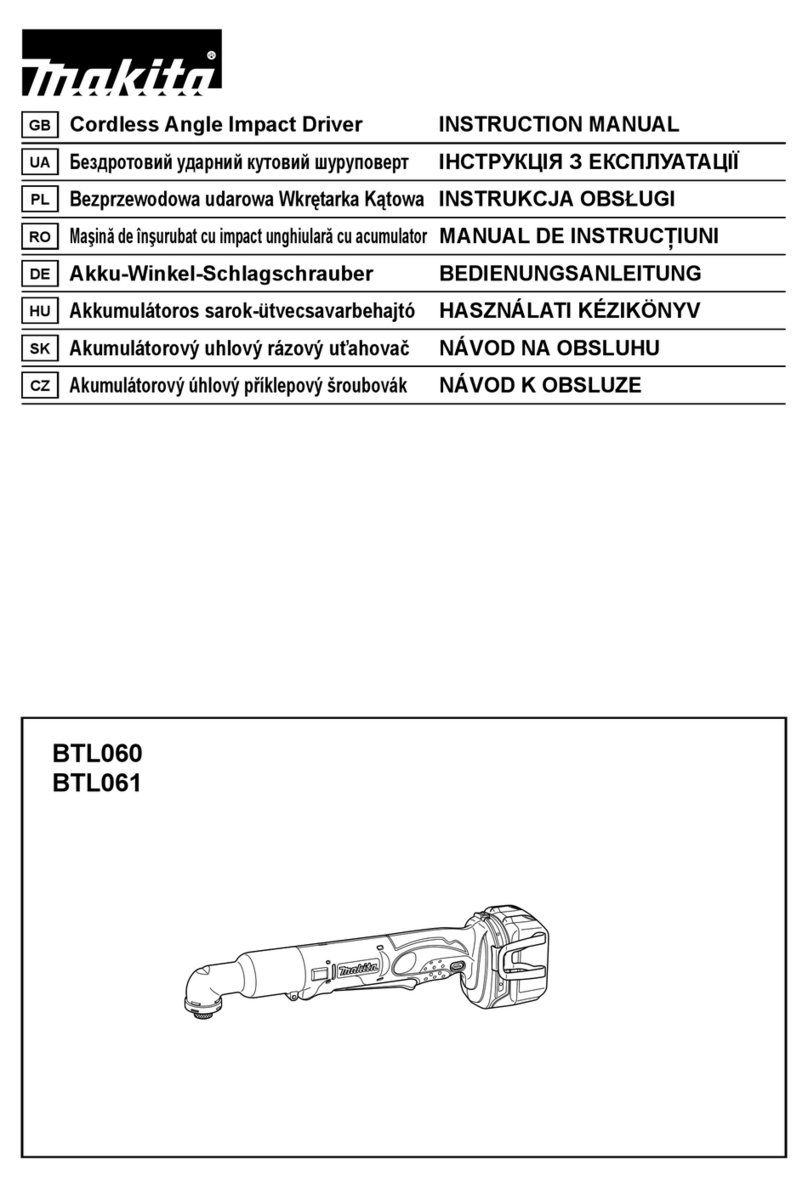
Makita
Makita BTL060 User manual
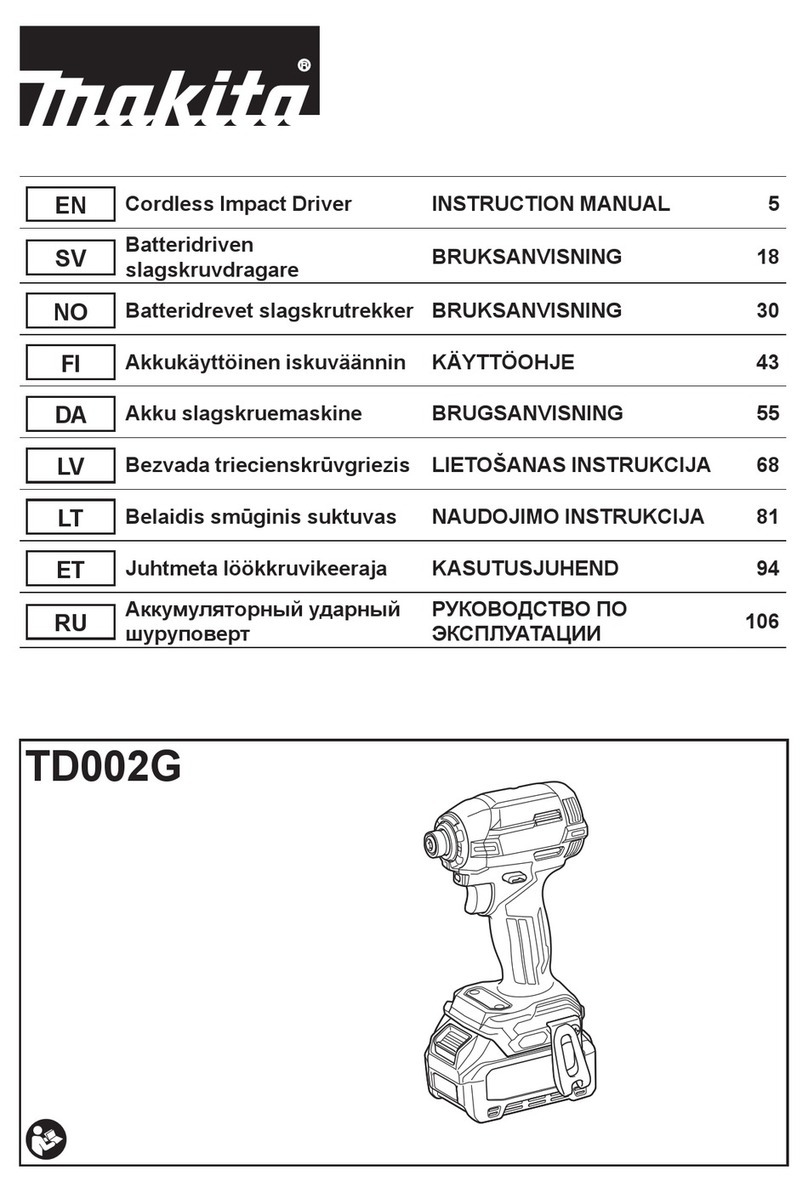
Makita
Makita TD002G User manual

Makita
Makita TW0200 User manual
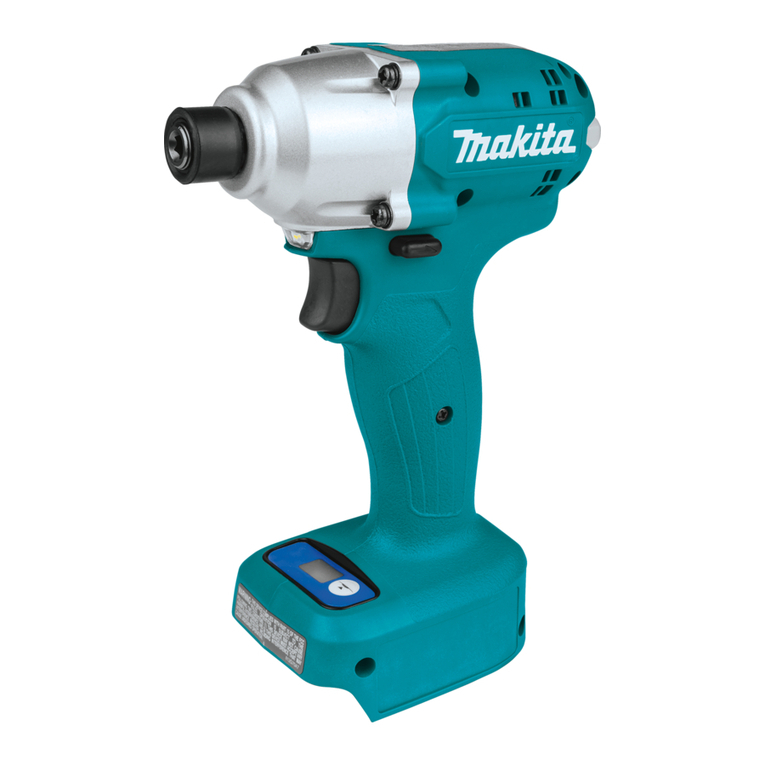
Makita
Makita DTDA040 Series User manual

Makita
Makita 6980FD User manual

Makita
Makita 6904VH User manual

Makita
Makita 6904VH User manual

Makita
Makita BTL062 User manual

Makita
Makita DTP141Z User manual
Popular Impact Driver manuals by other brands

Chicago Pneumatic
Chicago Pneumatic CP772H-6 Operator's manual
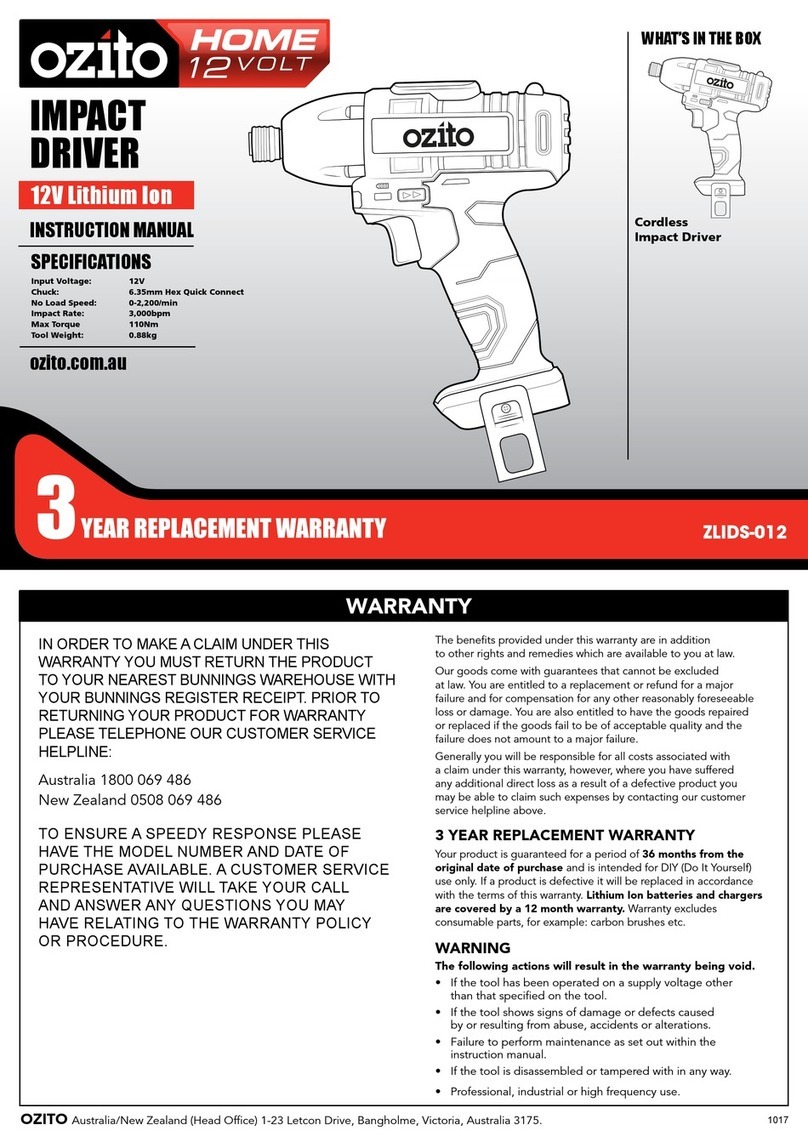
Ozito
Ozito ZLIDS-012 instruction manual
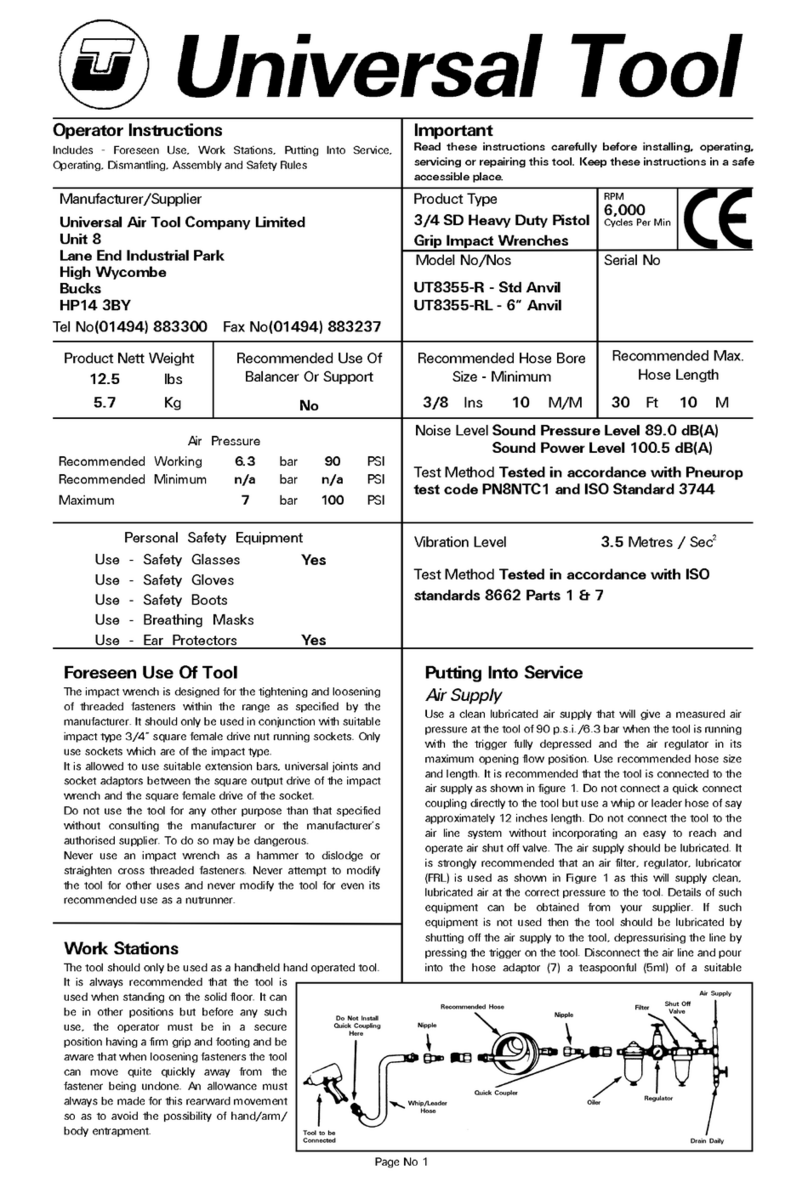
Universal Tool
Universal Tool UT8355-R Operator instructions

Chicago Pneumatic
Chicago Pneumatic CP9540-B Series Operator's manual

Clarke
Clarke CAT117 Operating & maintenance instructions
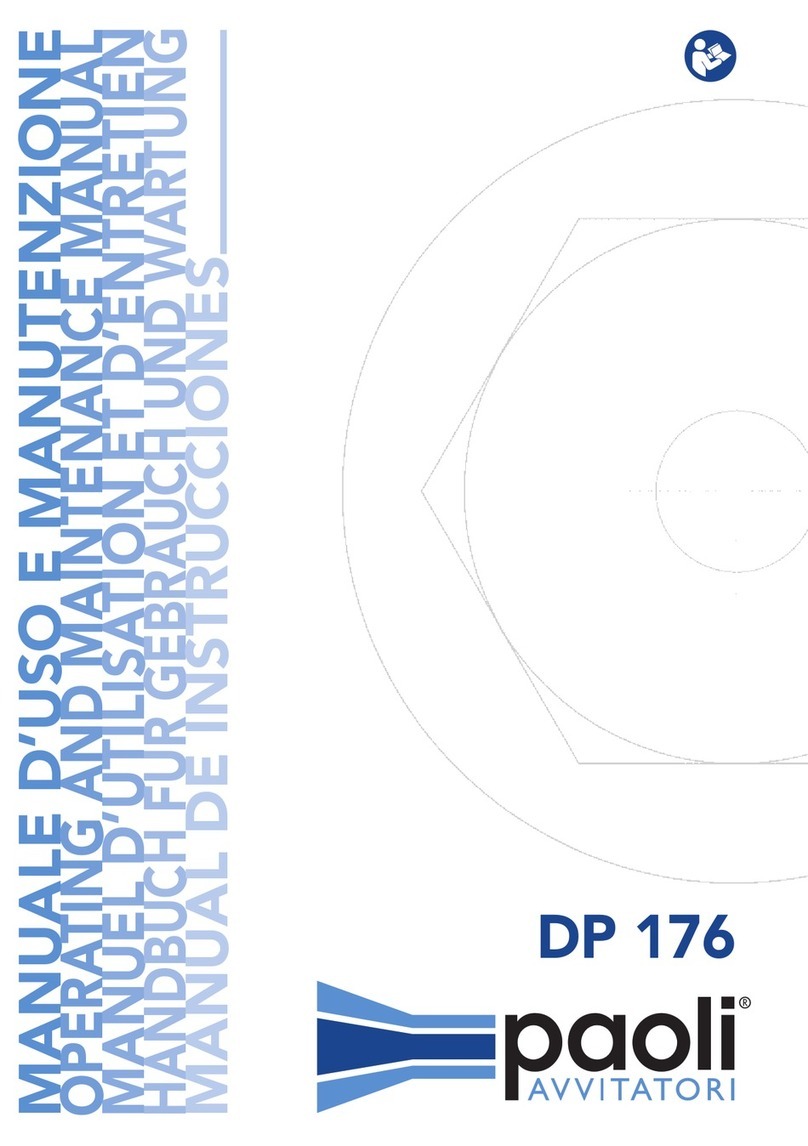
Paoli Avvitatori
Paoli Avvitatori DP 176 Operating and maintenance manual

SGS
SGS SAT110K owner's manual
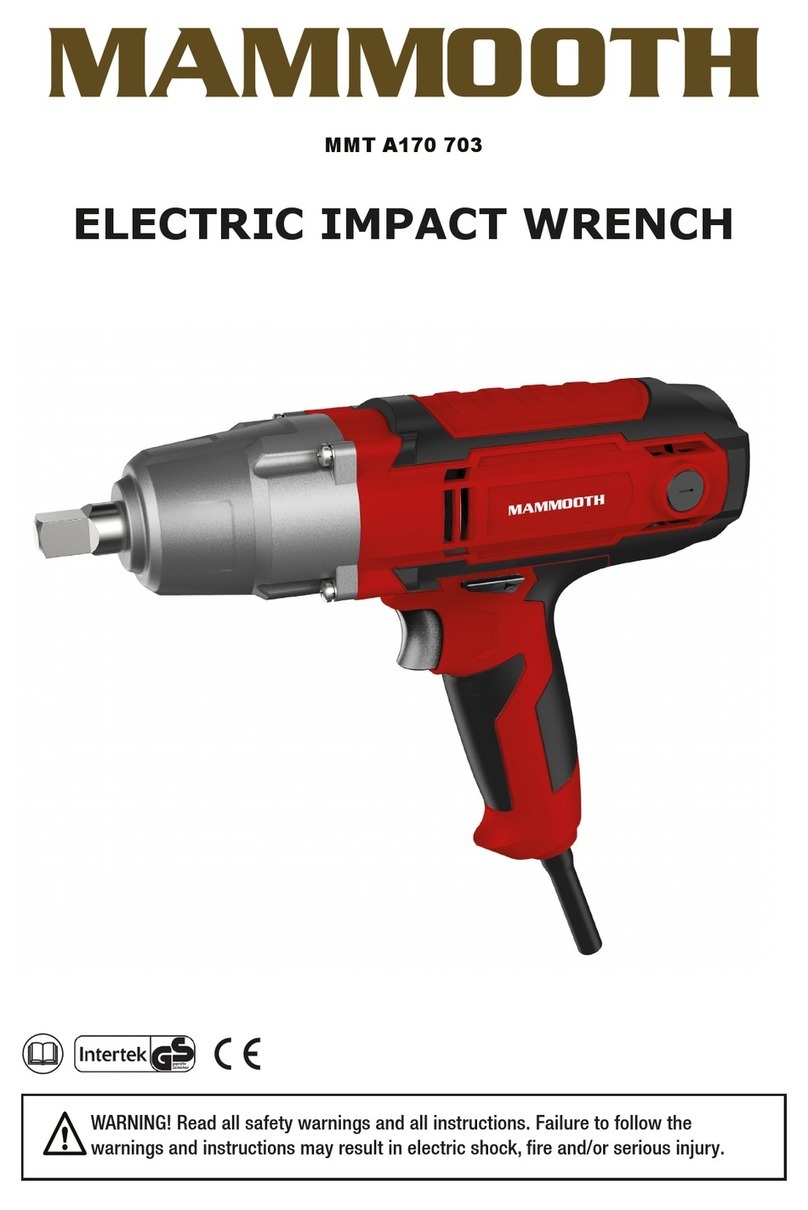
Mammooth
Mammooth MMT A170 703 manual

Milwaukee
Milwaukee M18 FMTIW2P12 Original instructions
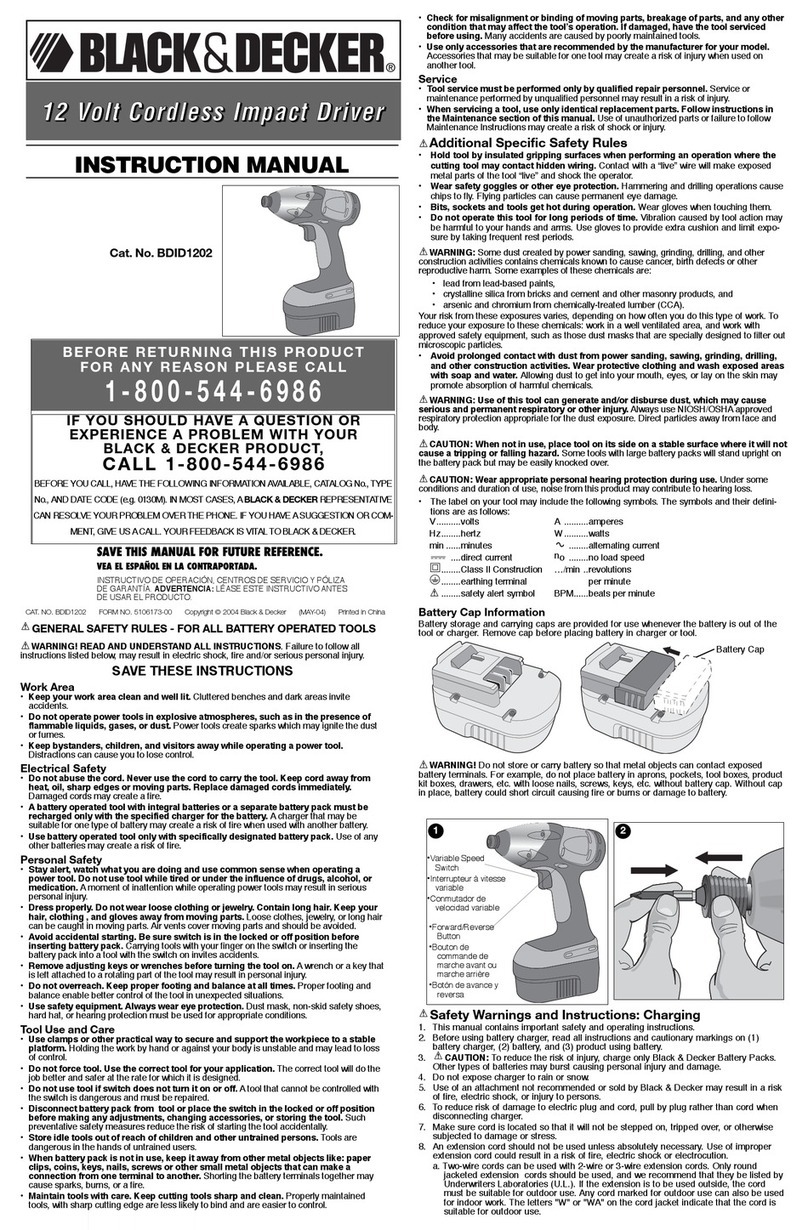
Black & Decker
Black & Decker 5106173-00 instruction manual

Cornwell Tools
Cornwell Tools bluePOWER CAT4282 operating manual

Black & Decker
Black & Decker Fire Storm FS1202ID instruction manual