MGM BAH 80-112 Series User guide

Page 1 of 36 A80H0321
Manuale d’uso e manutenzione
Serie BAH 80-112
I T A L I A N O
Vi ringraziamo per la fiducia accordataci acquistando questo prodotto.
Prima di mettere in funzione il motore Vi raccomandiamo di leggere attentamente queste istruzioni per
assicurarVi di utilizzare il motore M.G.M. in condizioni di sicurezza e al massimo delle sue prestazioni.
Per le varie tipologie di motori MGM si raccomanda di prendere visione delle istruzioni d’uso e
manutenzione nella versione più completa e aggiornata sul nostro sito web (www.mgmrestop.com). Per
qualsiasi chiarimento Vi preghiamo di contattare l’organizzazione della M.G.M. specificando tipo di
prodotto e numero di matricola.
La lingua originaria in cui il documento è stato redatto è l’ITALIANO; in caso di dubbi o incongruenze richiedere
delucidazioni al costruttore.
Queste istruzioni sono valide per i motori elettrici M.G.M. della serie BAH e serie derivate.
Per motori con esecuzioni o applicazioni specifiche possono essere necessarie delle istruzioni apposite.
La serie BAH è costituita da motori elettrici autofrenanti asincroni trifase o monofase con costruzione
chiusa e ventilazione esterna. Il freno interviene in assenza di alimentazione. I motori della serie BAH sono destinati ad
essere utilizzati come componenti in applicazioni industriali.
Le prestazioni e le caratteristiche riportate sulla targa del motore sono garantite per installazioni in ambienti con
temperatura compresa tra –15°C a +40°C e altitudine inferiore a 1000 metri s.l.m.
Per ogni chiarimento contattare l’organizzazione della M.G.M. motori elettrici S.p.A.
Il manuale d’uso e manutenzione è disponibile in varie lingue sul nostro sito web (www.mgmrestop.com).
Targa
Ogni motore è provvisto di una targa di identificazione dove sono riportate le informazioni relative al prodotto. Di
seguito sono presentate le targhe utilizzate sui motori MGM, con le relative note esplicative, per una corretta
comprensione dei dati su di esse riportate. La targa posta a sinistra è utilizzata sui motori a singola velocità, quella a
destra sui motori a doppia velocità.
Note:
Il disegno della targa a sinistra rappresenta la targa relativa ai motori con collegamento / . Per i motori
con collegamento / , le indicazioni di tensione e intensità di corrente riferiti a questo collegamento
sono rappresentati con V , V , I , I .

Page 2 of 36 A80H0321
Nei motori con esecuzione speciale oppure per il Nord America possono essere presenti informazioni
aggiuntive (ad esempio Code letter, CC number, Service Factor, etc.) e alcune informazioni possono essere
collocate in campi diversi rispetto a quanto indicato.
1 tipo di servizio
2 grado di protezione
3 classe di isolamento; la dicitura TR dopo la lettera che specifica la classe di isolamento, indica il trattamento di
tropicalizzazione
4 peso (Kg)
5 designazione tipo motore
6 numero di matricola
7 coppia frenante statica massima ottenibile attraverso opportuna regolazione delle molle (Nm)
8 intensità di corrente assorbita dal freno (Ampere)
9 tensione di alimentazione del freno (Volt). Sui motori con freno in corrente trifase alternata il simbolo Vb=Vm indica
che motore e freno hanno la medesima tensione di alimentazione. Per motori con freno DC, l’indicazione 1~230V
oppure 1~400V rappresenta la tensione di alimentazione monofase (230V oppure 400V) in ingresso al raddrizzatore
10 potenza nominale (kW) a 50 Hz
11 fattore di potenza
12 velocità angolare dell’albero (giri al minuto) a 50 Hz
13 tensione di alimentazione del motore collegato a triangolo a 50 Hz (Volt)
14 intensità di corrente assorbita dal motore collegato a triangolo a 50 Hz (Ampere)
15 tensione di alimentazione del motore collegato a stella a 50 Hz (Volt)
16 intensità di corrente assorbita dal motore collegato a stella a 50 Hz (Ampere)
17 potenza nominale (kW) a 60 Hz
18 fattore di potenza
19 velocità angolare dell’albero (giri al minuto) a 60 Hz
20 tensione di alimentazione del motore collegato a triangolo a 60 Hz (Volt)
21 intensità di corrente assorbita dal motore collegato a triangolo a 60 Hz (Ampere)
22 tensione di alimentazione del motore collegato a stella a 60 Hz (Volt)
23 intensità di corrente assorbita dal motore collegato a stella a 60 Hz (Ampere)
24 tensione di alimentazione del motore a 50 Hz (Volt)
25 intensità di corrente assorbita dal motore a 50 Hz (Ampere)
26 tensione di alimentazione del motore a 60 Hz (Volt)
27 intensità di corrente assorbita dal motore a 60 Hz (Ampere)
28 forma costruttiva
29 Identificazione esecuzione speciale. Per motori con ventilazione ausiliaria, all’interno di tale spazio viene riportata
la tensione di alimentazione dei ventilatori preceduta dalla sigla VENT. La presenza di termoprotettori bimetallici
è indicata con TP, dei termistori con TM, delle scaldiglie anti condensa con SCALD seguita dalla tensione di
alimentazione.
30 rendimento e classe di efficienza (IE) a 50 Hz
31 rendimento e classe di efficienza (IE) a 60 Hz
32 marchi certificazioni (cCSAus, CSA Energy efficiency, CCC, etc.)
33 se è presente la dicitura ‘DM’ indica la doppia morsettiera
34 numero di fasi motore ( 3 = trifase, 1= monofase)

Page 3 of 36 A80H0321
Informazioni generali sulla sicurezza
Durante il funzionamento i motori presentano parti sotto tensione o in movimento. La rimozione delle
necessarie protezioni elettriche e meccaniche, l'uso improprio o la non adeguata manutenzione possono
causare gravi danni a persone e cose.
Le operazioni di installazione, manutenzione, regolazione, sostituzione di componenti devono essere fatte
da personale qualificato utilizzando strumenti di lavoro adeguati. E’ necessario leggere attentamente
queste istruzioni per assicurare di utilizzare il motore M.G.M. in condizioni di sicurezza. Il personale che
interagisce con il motore deve utilizzare sempre i mezzi personali di protezione previsti dalle leggi del paese
di destinazione.
Le operazioni di installazione, manutenzione, regolazione, sostituzione di componenti devono essere fatte
avendo preventivamente verificato che il motore o l'impianto sia scollegato dalla rete di alimentazione e
che sui terminali in morsettiera non sia presente tensione residua.
Durante il funzionamento la temperatura sulla superficie del motore può superare i 50° C. Fare raffreddare
il motore prima di qualsiasi intervento.
Per la possibile mancanza di efficienza del freno durante le operazioni di regolazione,
manutenzione o sostituzione di componenti, verificare che all'albero motore non sia applicato
nessun carico prima di ogni intervento.
Ricevimento e magazzinaggio
All'atto del ricevimento verificare che le caratteristiche riportate sulla targa del motore coincidano con
quanto richiesto e che il motore non abbia subito danni durante il trasporto; eventuali danni dovranno
essere immediatamente segnalati al trasportatore.
I golfari se presenti servono al sollevamento del solo motore e non di altre macchine ad esso accoppiate. I
golfari danneggiati non devono essere utilizzati. Prima di sollevare il motore assicurarsi che i golfari di
sollevamento siano serrati ( per golfari avvitati) e non siano danneggiati.
Immagazzinare i motori in luogo asciutto e privo di polvere. Per immagazzinamenti prolungati le superfici
lavorate non protette (flange ed estremità dell'albero) devono essere trattate con prodotti anticorrosivi.
Gli elementi dell’imballo possono generare pericolo. Essi vanno rimossi con opportuni mezzi, non lasciati in
balia di persone non responsabili (es. bambini) e vanno smaltiti secondo le norme vigenti nel paese di
installazione.
Installazione
L’installazione del motore deve essere fatta da personale qualificato utilizzando strumenti e mezzi di lavoro
adeguati.
All’atto dell’installazione verificare che le caratteristiche richieste dal motore coincidano con quanto
riportato sulla targa con particolare riguardo alla tensione di alimentazione del motore e alla coppia
frenante massima.
La serie BAH (e serie derivate) non comprende motori idonei ad essere utilizzati in ambienti con pericolo di
esplosione. L'uso di un motore non idoneo in un ambiente con pericolo di esplosione può causare gravi
danni a persone e cose.

Page 4 of 36 A80H0321
Verificare che il tipo di freno installato sul motore sia idoneo per l'applicazione prevista e che sia
conforme a eventuali norme e prescrizioni vigenti. Verificare che per il tipo di applicazione previsto sia
necessario utilizzare un motore della serie -K o -PK (ad esempio sollevamenti, impieghi di sicurezza,
carroponte, etc).
Per eventuali chiarimenti contattare la MGM motori elettrici Spa.
Prima di collegare il motore alla rete di alimentazione, deve essere effettuato il collegamento verso terra
mediante i morsetti posti all’interno della scatola morsettiera e, se presenti, sulla carcassa del motore.
Nei motori con forma costruttiva B14 occorre fare attenzione a non superare con le viti di fissaggio la
profondità di avvitamento consentita per non danneggiare l'avvolgimento.
Verificare che le guarnizioni siano in perfette condizioni e perfettamente alloggiate nelle loro sedi e che le
aperture d’ingresso cavo siano ben chiuse in modo che sia garantito il grado di protezione indicato in targa.
Per installazioni all’aperto, si raccomanda di proteggere opportunamente il motore dall’irraggiamento e
dalle intemperie. E’ opportuno evitare che i bocchettoni per l’ingresso dei cavi siano posizionati verso l'alto.
Si consiglia inoltre che i cavi di collegamento arrivino dal basso verso l’alto, per evitare fenomeni di
gocciolamento o ristagno dell’acqua. Nel caso di montaggio verticale con lato comando in basso è
necessario l'uso della specifica cuffia anti pioggia. Nel caso in cui siano rimossi i golfari, se presenti, è
necessario per garantire il grado di protezione IP, che siano sostituiti con viti di medesimo passo e
lunghezza.
Verificare prima della messa in servizio o dopo lunghi periodi di inattività o giacenza in magazzino oppure
quando si sospetti formazione di umidità negli avvolgimenti che la resistenza di isolamento verso massa non
sia inferiore a 75MΩ (valore riferito alla temperatura di 25°C). Se questo valore della resistenza di
isolamento non viene raggiunto, l'avvolgimento è troppo umido e deve essere asciugato in forno. Per
maggiori informazioni contattare MGM.
La misura deve essere fatta con strumento per la misurazione dell’isolamento a 500V DC. Durante ed
immediatamente dopo la misurazione sui morsetti si presentano delle tensioni pericolose, non toccare i
morsetti per nessun motivo e osservare scrupolosamente le istruzioni per l’uso dello strumento di misura.
Il motore deve essere installato in un locale aerato lontano da fonti di calore e in posizione tale da consentire la libera
aspirazione dell’aria per una corretta ventilazione. Il motore deve essere collocato in modo da consentire agevoli
operazioni di ispezione e manutenzione tenendo conto di eventuali pericoli derivanti dal contatto con parti in
movimento o con parti del motore che possono superare i 50°C.
L'equilibratura dei motori è stata realizzata con mezza chiavetta applicata all'estremità d'albero (EN60034-14).
All’atto del montaggio verificare che il motore e la macchina accoppiate siano allineate accuratamente in quanto un
allineamento impreciso può causare vibrazioni, danneggiamento dei cuscinetti e rottura dell’estremità d’albero.
In particolare all’atto del montaggio verificare, nel caso di motori con forma costruttiva IMB5 e IMB14, che le superfici
di accoppiamento siano ben pulite.
Per motori IMB3 verificare, nel caso di accoppiamento con giunti, che l’asse del motore e della macchina condotta
coincidano e, che, nel caso in cui si effettui l’accoppiamento con pulegge, la tensione delle cinghie non sia eccessiva.
Per la regolazione delle cinghie attenersi alle indicazioni del fornitore della macchina azionata. Un’ eccesiva
tensione della cinghia può causare il danneggiamento dei cuscinetti e la rottura dell’albero.
La superficie alla quale viene fissato il motore deve garantire stabilità di fissaggio e assenza di vibrazioni indotte sul
motore stesso. Le fondazioni devono essere dimensionate in modo da evitare il trasferimento di vibrazioni al motore e
l'insorgere di vibrazioni dovute a risonanza. E’ necessario provvedere affinché sia minimizzata la trasmissione di
vibrazioni al motore.
Verificare inoltre che la superficie su cui il motore si appoggia sia piana. Il non rispetto di questa condizione può
determinare la rottura dei piedi del motore.

Page 5 of 36 A80H0321
Collegamento Elettrico
Prima di collegare il motore alla rete di alimentazione, deve essere effettuato il collegamento verso terra
mediante i morsetti posti all’interno della scatola morsettiera e, se presenti, sulla carcassa del motore. Tali
morsetti devono essere puliti e protetti dalla corrosione.
Verificare che le specifiche della rete (tensione e frequenza) siano congruenti con quanto indicato sulla targa per il
motore e il freno ed eventuali dispositivi ausiliari.
Per il collegamento del motore alla rete di alimentazione e per il collegamento verso terra utilizzare conduttori di
sezione adeguata e in accordo alle norme vigenti nel paese d’utilizzo del motore.
E’ inoltre necessario prevedere dei dispositivi di protezione contro le sovracorrenti regolati opportunamente in base
alla corrente nominale del motore. Si raccomanda di seguire le indicazioni contenute nella norma EN 60204-1 o della
norma vigente nel paese d’utilizzo del motore.
Verificare che il senso di rotazione del motore sia quello desiderato. Per cambiare il senso di rotazione invertire due
fasi dell'alimentazione.
È opportuno adottare adeguati accorgimenti allo scopo di limitare gli eventuali disturbi generati dai dispositivi di
inserzione. Nel caso di alimentazione separata del freno si consiglia di tenere insieme i cavi del freno con altri cavi solo
se schermati.
Per il collegamento alla rete attenersi agli schemi illustrati qui di seguito.
La tensione e la frequenza di alimentazione previste sono indicate sulla targa del motore.
Dopo aver effettuato il collegamento verificare accuratamente il serraggio dei dadi dei morsetti.
Per informazioni sulla coppia di serraggio richiesta contattare MGM.
Verificare che la corrente assorbita dal motore a carico sia congruente con i dati di targa.
Per i motori comandati da inverter per il cablaggio attenersi alle indicazioni fornite dal costruttore di inverter. Per
alimentazione superiore a 500V o in caso siano usati dei lunghi cavi di collegamento inverter – motore ( > 50 metri) si
consiglia di utilizzare motori con isolamento rinforzato o appostiti filtri.
Sui motori destinati a funzionare con inverter, si deve provvedere ad alimentare separatamente il freno rispetto al
motore per garantire il corretto funzionamento dell’elettromagnete.
Qualora siano previsti cicli di funzionamento prolungato a bassa velocità verificare la necessità della servoventilazione.
Per maggiori informazioni contattare MGM.
L’alimentazione dell’elettromagnete del freno DC avviene attraverso un raddrizzatore alloggiato all’interno della
morsettiera (eccetto che per il freno a 24V DC). La tensione di alimentazione del raddrizzatore lato corrente alternata
è indicata sulla targhetta del motore.
Per l’eventuale collegamento degli ausiliari (protezioni termiche, scaldiglie anticondensa, ventilazione ausiliaria) si
consideri l’identificazione dei cavi all’interno della scatola morsettiera secondo quanto descritto nel relativo paragrafo.
Nota: a secondo del tipo di motore e degli eventuali dispositivi ausiliari presenti, la forma della scatola
morsettiera potrebbe essere diversa da quella indicata nelle figure.

Page 6 of 36 A80H0321
BAH
Motore trifase a singola velocità
FRENO A.C.
BAH
Motore trifase a singola velocità
FRENO D.C.

Page 7 of 36 A80H0321
BAHD
Motore trifase a due velocità – Dahlander
FRENO A.C.
ALTA VELOCITA’ BAHSSA VELOCITA’
BAHD
Motore trifase a due velocità – Dahlander
FRENO D.C.
ALTA VELOCITA’ BAHSSA VELOCITA’

Page 8 of 36 A80H0321
BAHDA
Motore trifase a due velocità – Due avvolgimenti
FRENO A.C.
ALTA VELOCITA’ BAHSSA VELOCITA’
.
BAHDA
Motore trifase a due velocità – Due avvolgimenti
FRENO D.C.
ALTA VELOCITA’ BAHSSA VELOCITA’

Page 9 of 36 A80H0321
Raddrizzatore M
Raddrizzatore Q

Page 10 of 36 A80H0321
Identificazione dei cavi dei dispositivi ausiliari
Nella tabella sottostante sono indicati i simboli utilizzati all’interno della scatola morsettiera (vedere foto a lato come
esempio) per l’identificazione dei cavi dei dispositivi ausiliari. La tensione di alimentazione delle eventuali scaldiglie o
dei servoventilatori è indicata sulla targa del motore. Per qualsiasi dubbio sul collegamento dei dispositivi ausiliari vi
preghiamo di contattarci.
Nota: a secondo del tipo di motore e degli eventuali dispositivi ausiliari presenti, il tipo di morsettiera e la
posizione dei terminali dei dispositivi ausiliari sulla morsettiera potrebbero essere diversi da quanto
indicato nella fotografia scelta come esempio.
La scaldiglia anticondensa può essere alimentata solo dopo avere spento il motore. Non deve essere
alimentata durante il funzionamento del motore.
L’eventuale servoventilazione assicura, durante il funzionamento del motore principale, la sottrazione del
calore di dissipazione. Verificare una volta spento il motore, in base alla temperatura raggiunta, l’eventuale
necessità di prevedere il proseguimento della ventilazione per un periodo aggiuntivo. Nelle unità di
ventilazione forzata in cui il funzionamento dipende dal senso di rotazione occorre assolutamente rispettare
il senso di rotazione (vedi freccia indicatrice del senso di rotazione).
Dispositivo Identificazione cavi
Scaldiglie motore HT
Termoprotettori (PTO) TP
Termistori (PTC) TM
Servoventilazione SV
Microswitch sblocco freno MS
Scaldiflie freno HB
Microswitch usura disco freno MB

Page 11 of 36 A80H0321
Manutenzione
La carenza di ispezioni e manutenzione può causare gravi danni a persone o cose. Le attività di ispezione e
manutenzione di seguito descritte sono indispensabili comunque, ma diventano particolarmente importanti
per tutte le applicazioni gravose o nelle quali il motore riveste una funzione di sicurezza (ad esempio
sollevamenti, impieghi di sicurezza, carroponte, etc.).
Le attività di manutenzione devono essere eseguite da personale qualificato e solo dopo aver
preventivamente scollegato l'impianto o il motore dalla rete di alimentazione elettrica (compreso eventuali
ausiliari e in particolare le scaldiglie anticondensa). Per i motori monofase attendere che i condensatori si
siano scaricati.
Per la possibile mancanza di efficienza del freno durante le operazioni di regolazione,
manutenzione o sostituzione di componenti, verificare che all'albero motore non sia applicato
nessun carico prima di ogni intervento.
Nel caso di motori con protezione termica dell’avvolgimento occorre prendere delle precauzioni, in modo
che non possano sorgere pericoli a causa di una riaccensione automatica accidentale.
Evitare qualunque riparazione precaria, le riparazioni vanno effettuate esclusivamente con ricambi
originali. Il manutentore ha l’obbligo di segnalare tempestivamente qualunque anomalia.
NON consentire l’uso del motore qualora si riscontrino problemi di qualsiasi natura e provvedere al
corretto ripristino delle normali condizioni.
Per motivi di sicurezza la chiave a "T", se disponibili, non devono essere mai lasciate inserite sul motore ma
rimosse e custodite dal responsabile della manutenzione dell'impianto dopo ogni intervento. La chiave a
“T“deve essere utilizzata soltanto quando il motore è scollegato dalla rete di alimentazione e solo dopo
aver verificato che all’albero motore non risulti applicato nessun carico.
Dopo ogni intervento sul gruppo freno verificare sempre la chiusura della cuffia (26) attraverso un adeguato
serraggio della vite di fissaggio (117).
Di seguito sono elencate le attività che devono essere svolte periodicamente per assicurare il corretto funzionamento
del motore MGM. La frequenza delle ispezioni dipende dalla particolare applicazione del motore (ad esempio dal
numero di avviamenti, dal momento inerzia applicato, dalle condizioni ambientali, presenza di polvere, vibrazioni,
etc.). Si consiglia di effettuare la prima ispezione dopo circa 2-3 settimane di funzionamento e di redigere
conseguentemente un programma di manutenzione periodica. E’ necessario comunque programmare le ispezioni
successive con frequenza di almeno 2 volte all'anno. Per eventuali informazioni contattare l'organizzazione della
M.G.M. motori elettrici S.p.A.
Verificare periodicamente che il motore funzioni correttamente senza rumori o vibrazioni anomale. In particolare
verificare l’eventuale rumorosità dei cuscinetti. I cuscinetti normalmente utilizzati sono lubrificati a vita e quindi
non necessitano l’aggiunta di lubrificante. Se necessario sostituire i cuscinetti con altri dello stesso tipo di quelli
montati originariamente.
Verificare che le aperture per il passaggio dell'aria per la ventilazione non siano ostruite. Soprattutto quando il
motore lavora in un ambiente polveroso le verifica e la pulizia è molto importante e deve avvenire con una
frequenza maggiore.
Verificare che la corrente assorbita dal motore a carico sia congruente con i dati di targa.
Verificare il corretto serraggio dei cavi di alimentazione del motore e del conduttore di terra.
Verificare lo stato di conservazione e l’integrità dei cavi di alimentazione del motore e del cavo di terra.

Page 12 of 36 A80H0321
Verificare che, per effetto dell'usura della guarnizione di attrito del disco freno, il traferro non sia al di fuori dei
valori indicati nella tabella 1. Si consideri che l'usura è maggiore durante la fase di rodaggio. Per la regolazione del
traferro seguire le indicazioni riportate nel paragrafo "Regolazione del Traferro".
Verificare lo stato di usura della superficie di attrito da entrambe le parti del disco freno assicurandosi che lo
spessore non scenda al di sotto di 2 mm.
Verificare inoltre l'assenza di danneggiamenti sulla superficie del disco ed in particolare nella dentatura del mozzo.
(Per l'eventuale sostituzione consultare il paragrafo "Sostituzione del Disco Freno").
Verificare inoltre che non ci sia gioco tra il mozzo e il disco in corrispondenza dei chiodi.
Verificare periodicamente lo stato di usura della dentatura dell'albero dove scorre il disco freno. Se la dentatura
presenta un'usura visibile è necessario provvedere alla sostituzione dell'albero rotore (1)
Verificare periodicamente che la coppia frenante sia adeguata. Se necessario procedere alla regolazione secondo
quanto indicato nel paragrafo 'Regolazione coppia frenante '.
Verificare periodicamente lo stato di usura delle colonnette di guida (19-42) e il loro saldo ancoraggio sul
convogliatore (17).
Tutti i componenti del gruppo freno e in particolare il disco freno (23) e le colonnette di guida (19) sono
componenti soggetti ad usura. In considerazione della funzione di sicurezza svolta è necessario effettuare, come
manutenzione preventiva, la sostituzione periodica. La frequenza dipende dal tipo di lavoro svolto dal motore
(numero di avviamenti, momento di inerzia applicato, condizioni ambientali etc.); si raccomanda comunque di
provvedere alla sostituzione con una frequenza non superiore ai 18 mesi.
Verificare il corretto fissaggio del motore attraverso i piedini o la flangia. Verificare il serraggio delle viti di
fissaggio. Verificare che l’eventuale basamento su cui il motore è fissato non presenti crepe né danni di altra
natura quali abbassamenti o simili.
Verificare periodicamente che la guarnizione della scatola morsettiera sia in buone condizioni. Si raccomanda di
effettuare una verifica almeno una volta all’anno. Se la guarnizione è deteriorata deve essere sostituita.
In generale le varie guarnizioni utilizzate per la chiusura del motore e del freno devono essere in buone condizioni
per garantire il grado di protezione dell’involucro. Se una guarnizione è deteriorata deve essere sostituita.
Si raccomanda di realizzare un programma di manutenzione periodico della verniciatura allo scopo di proteggere
il motore dalla corrosione.
Gruppo freno serie BAH
17 - Convogliatore con pista d’attrito
18 - Molla freno
19 - Colonnetta di guida
20 - Dado autobloccante registro molla
21 - Dado blocco interno elettromagnete
22 - Dado blocco esterno elettromagnete
23 - Disco freno
24 - Ancora mobile con triangolo di guida
25 - Elettromagnete
26 - Cuffia protezione freno BAH
60 - Traferro
117 -Vite di fissaggio cuffia BAH
119 - Tappo di chiusura cuffia BAH

Page 13 of 36 A80H0321
Smontaggio cuffia protezione freno
Svitare il tappo di chiusura cuffia (119) e poi la vite di fissaggio cuffia (117). Rimuovere la cuffia protezione freno (26).
Per rimontare la cuffia protezione freno (26) procedure a ritroso.
Per I motori serie BAHE-BAHXE, prima di rimuovere protezione freno (26), è necessario rimuovere la calotta di
protezione dell’encoder (103) e l’encoder (102).
Regolazione Coppia Frenante
La coppia frenante è proporzionale alla compressione delle molle (18) che può essere variata agendo sui
dadi (20).
Nella tabella 2 e 3 sono riportati i valori di compressione standard (H std) delle molle. La coppia frenante
corrispondente alla regolazione standard della compressione delle molle riportata in tabella, è solitamente
inferiore a quella massima riportata sulla targa del motore, soprattutto per i gruppi freno con
elettromagnete AC.
Dopo aver effettuato la registrazione verificare sempre che la coppia frenante sia idonea per l'utilizzo
previsto.
Se alimentando il freno l'elettromagnete non riuscisse a richiamare l'ancora mobile (24) con un colpo
secco e a tenerla attratta senza vibrazioni, verificare l'esatta regolazione del traferro (60) e, se
l'inconveniente persiste, allentare i dadi (20) e riprovare sino ad ottenere il funzionamento corretto.
Verificare sempre a fine intervento che la coppia frenante registrata sia adeguata.
Non superare mai il valore di coppia frenante massimo riportato in targa.
Si consiglia di evitare di regolare la coppia frenante a valori inferiori al 40% del valore massimo.
Per eventuali informazioni contattare l'organizzazione della M.G.M. motori elettrici S.p.A.
Elettromagnete AC trifase
Altezza d’asse motore 80 90 100 112
H std (mm) 12.0 16.0 15.0 16.5
Tabella 2
Elettromagnete DC
Altezza d’asse motore 80 90 100 112
H std (mm) 12.5 16.0 15.0 16.5
Tabella 3

Page 14 of 36 A80H0321
Sostituzione disco freno
Verificare che il disco freno sia del tipo idoneo per l'applicazione prevista e in particolare verificare se sia
necessario utilizzare un disco freno K (ad esempio sollevamenti, impieghi di sicurezza, carroponte etc.). Per
eventuali chiarimenti contattare la MGM motori elettrici Spa.
Prima di procedere alla sostituzione del disco verificare sempre lo stato di usura della dentatura dell'albero
dove scorre il disco freno. Se la dentatura presenta un'usura visibile è necessario provvedere alla sostituzione
dell'albero rotore (1).
Rimuovere la cuffia protezione freno (26) secondo quanto indicato nel relativo paragrafo.
Svitare i dadi (22), sfilare l’elettromagnete (25) dalle colonnette (19), togliere i dadi (20-21) e le molle (18). Estrarre
l’ancora mobile (24) dalle colonnette (19), togliere il disco freno (23) vecchio ed inserire il disco nuovo.
Porre attenzione che il disco sia inserito nel verso corretto.
Per i dischi K la faccia del disco che ha il mozzo che sporge o comunque maggiormente sporgente deve essere
rivolta verso il convogliatore
Procedere a ritroso per il successivo montaggio.
Si raccomanda di maneggiare il disco freno con le mani pulite perché ogni traccia di grasso diminuisce la
capacità frenante e aumenta la rumorosità.
Sostituzione elettromagnete
Rimuovere la cuffia protezione freno (26) secondo quanto indicato nel relativo paragrafo.
Scollegare i connettori dell’elettromagnete (25), svitare i dadi (22) e sfilare dalle colonnette (19) l’elettromagnete (25).
Ricollocare sulle colonnette il nuovo elettromagnete e i dadi ed effettuare il collegamento elettrico avendo cura di
disporre i connettori nella posizione che rende possibile l’innesto. Prima di rimontare la cuffia di protezione freno (26)
verificare che i connettori e i relativi cavi siano ben ancorati. Procedere con la regolazione del traferro (vedere relativo
paragrafo). Verificare che l’elettromagnete funzioni regolarmente; alimentando il freno l’elettromagnete (25) deve
richiamare l’ancora mobile (24) con un colpo secco e tenerla attratta senza alcuna vibrazione o rumorosità. Se l’ancora
mobile (24) tendesse a vibrare occorre verificare che i terminali siano accoppiati correttamente.
Sostituzione colonnette
Rimuovere la cuffia protezione freno (26) secondo quanto indicato nel relativo paragrafo.
Svitare i dadi (22), sfilare l’elettromagnete (25) dalle colonnette (19 o 42), togliere i dadi (20-21) e le molle (18).
Estrarre l’ancora mobile (24) dalle colonnette (19 o 42), svitare le colonnette vecchie e avvitare le nuove verificando
che siano saldamente ancorate al convogliatore (17). Dopo avere avvitato ciascuna colonnetta (19 o 42) verificare che
la base di appoggio della stessa sia completamente a contatto con la superficie del convogliatore (17).

Page 15 of 36 A80H0321
Regolazione traferro
Il traferro (60), ossia la distanza tra i due nuclei elettromagnetici dell'elettromagnete (25) e dell'ancora mobile (24),
deve rimanere entro i valori indicati nella tabella 1. E'necessario non oltrepassare tali valori, per evitare vibrazioni
dell'ancora mobile, rumorosità eccessiva, l'eventuale bruciatura delle bobine dell'elettromagnete o il danneggiamento
del gruppo freno.
Il traferro tende ad aumentare per effetto dell‘usura del disco freno. Si consideri che l'usura del disco freno è
maggiore durante la fase di rodaggio (alcune migliaia di frenate).
Rimuovere la cuffia protezione freno (26) secondo quanto indicato nel relativo paragrafo.
Per riportare il traferro al valore richiesto occorre agire sulle coppie di dadi (21-22) che fermano l'elettromagnete (25)
facendolo avanzare verso l'ancora mobile (24).
Non è corretto serrare i dadi (22) di blocco dell'elettromagnete su una delle colonnette prima di aver ultimato la
regolazione della posizione dell'elettromagnete su tutte le colonnette. Non si deve pertanto modificare la posizione
dell'elettromagnete agendo su un dado interno (21), per fare una regolazione in corrispondenza di una colonnetta, se
non sono stati allentati precedentemente i dadi esterni (22) su tutte le colonnette.
Il traferro deve essere uniforme allo scopo di garantire il corretto funzionamento ed evitare sollecitazioni meccaniche
dovute al cattivo allineamento.
Per gruppi freno con 6 colonnette (19-42) effettuare inizialmente la regolazione della posizione dell'elettromagnete
(agendo sui dadi 21-22) solo su 3 colonnette poste a 120°. Dopo aver registrato il traferro sulle prime 3 colonnette
completare l'operazione sulle rimanenti 3 colonnette accostando prima i 3 dadi (21) a contatto con l'elettromagnete e
serrando quindi i 3 dadi (22).
Ad operazione conclusa verificare l'uniformità del traferro e il serraggio dei dadi (21-22).
Altezza d’asse motore 80 90-100 112
Intervallo traferro (mm) 0.25÷0.6 0.3÷0.7 0.35÷0.8
Tabella 1
Il traferro deve rimanere entro i valori indicati in tabella per evitare possibili danneggiamenti del gruppo
freno

Page 16 of 36 A80H0321
Ricambi
Per eventuali richieste di ricambi indicare il numero del pezzo, il tipo del motore, e il numero di matricola.
Descrizione componenti
1 - Gruppo albero motore
2 - Chiavetta
3 - Cuscinetto lato comando
4 - Scudo lato comando (B3)
6 - Tirante con dadi esagoni
7 - Carcassa motore
8 - Anello elastico
9 - Scudo lato freno
11 - Ventola
12 - Accessori blocca ventola
15 - Cuscinetto lato freno
17 - Convogliatore con pista di attrito
18 - Molla freno
19 - Colonnetta di guida
20 - Dado autobloccante registro molla
21 - Dado blocco interno elettromagnete
22 - Dado blocco esterno elettromagnete
23 - Disco freno
24 - Ancora mobile con triangolo di guida
25 - Elettromagnete
26 - Cuffia protezione treno BAH
28 - Viti coperchio morsettiera
29 - Scatola morsettiera (singola o doppia)
30 - Morsettiera
32 - Bocchettone pressa cavo
34 - Collegamento morsettiera/elettromagnete
36 - Scudo flangia (B5)
37 - Scudo flangia (B14)
38 - Rosetta elastica compensatrice
49 - Vite di sblocco manuale del freno
55 - Anello O-R Gruppo Freno
56 - Lamina inox
102 - Encoder
103 - Calotta di protezione encoder
117 -Vite di fissaggio cuffia BAH
118 - Vite di sblocco BAH
119 - Tappo di chiusura cuffia BAH

Page 17 of 36 A80H0321
Recupero/Smaltimento
Lo smaltimento del motore deve avvenire nel rispetto delle normative vigenti nel paese d'installazione.
Il simbolo del cassonetto barrato, riportato sulla targa, indica che il prodotto alla fine della propria vita
utile, non deve essere smaltito come rifiuto urbano misto ma deve essere raccolto separatamente dagli
altri rifiuti ed avviato a recupero o eventuale smaltimento secondo specifiche modalità per contribuire
ad evitare possibili effetti negativi sull'ambiente e sulla salute e per favorire il reimpiego e/o riciclo dei
materiali di cui è composto il motore.
La maggior parte dei componenti del motore è realizzata con materiali (acciaio, rame, alluminio, etc..)
che possono essere riutilizzati/riciclati contribuendo in questo modo alla tutela dell’ambiente.
Per ricevere maggiori informazioni sulle modalità di smaltimento/recupero o informazioni specifiche sui vari materiali
delle parti che costituiscono il motore visitare il nostro sito web (www.mgmrestop.com) oppure contattare MGM
Italia.

Page 18 of 36 A80H0321
ITALIA
STABILIMENTO DI PRODUZIONE E UFFICI:
S.R. 435 LUCCHESE KM. 31 (nr.439)
51034 - SERRAVALLE PISTOIESE (PT)-ITALY
TEL. +39 0573 91511 R.A. - FAX +39 0573 518138
email: [email protected]
http://www.mgmrestop.com
DEPOSITO NORD-ITALIA - NORTH ITALY BRANCH OFFICE:
VIA FERMI, 44 - 20090 ASSAGO – MILANO-ITALY
TEL. +39 02 48843593 - FAX +39 02 48842837
CANADA
STABILIMENTO DI PRODUZIONE E UFFICI:
3600 F.X. Tessier, Suite 140
Vaudreuil, Quebec
J7V 5V5 Canada
TEL. +1 (514) 355-4343 - FAX +1 (514) 355-5199
email: [email protected]
http://www.mgmelectricmotors.com
USA
UFFICI E DEPOSITO
269 Executive Drive
Troy, MI 48083
USA
Phone: 1 (248) 987-6572 - Fax: 1 (248) 987-6569
email: [email protected]
http://www.mgmelectricmotors.com
INDIA
STABILIMENTO DI PRODUZIONE E UFFICI:
Door No. 68, Indus Valley’s Logistic Park
Unit 3, Mel AyanamBAHkkam, Vellala Street
Chennai 600 095, Tamil Nadu - INDIA
Tel. +91 44 64627008
Web www.mgmvarvelindia.com
E-mail [email protected]
TURKEY
STABILIMENTO DI PRODUZIONE E UFFICI:
Ekrem Demirtas Ave. No. 28 ITOB OSB
Menderes/IZMIR - TURKEY
Tel. +90 232 7990347
Fax +90 232 7990348
Web www.mgmmotor.com.tr
E-mail [email protected]

Page 19 of 36 A80H0321
Use and maintenance
Series BAH 80-112
E N G L I S H
We would like to thank you for trusting us and for buying our product.
Before starting the motor, we advise you to read these instructions carefully, to be sure that the M.G.M.
motor is used in safe conditions and to obtain its highest performance. For the different MGM motors
types we suggest to download the “Use and maintenance” in its last and complete version directly from
our web site: www.mgmrestop.com. Should any difficulty arise, please contact the M.G.M. organization,
specifying the type of product and its serial number.
This document is originally drawn in ITALIAN language; in case of hesitation in understanding the text please ask the
manufacturer for further clarifications.
These instructions are valid for all M.G.M. electric motors belonging to BAH 80-112 series and to the derived series.
Please require a specific instruction manual for special execution motors as it might differ from this one.
BAH series (and the derived series) includes asynchronous three-phase enclosed fan cooled brake motors. The BAH
and derived series motors are used as components in industrial applications. Performance and characteristics shown
on the motor nameplate are guaranteed for installations with ambient temperature ranging from –15°C to +40°C and
an altitude less than 1000 meters above sea level.
For any clarifications, please contact the M.G.M. motori elettrici S.p.A. organization.
The Use and Maintenance manual is available in several languages on our website (www.mgmrestop.com)
Targa
Every motor is provided with an identifying nameplate, on which specific motor information is given. Motor
nameplates are shown below with motor data and explanatory notes. The nameplate shown on the left is used for
single speed motors while the nameplate on the right is used for two speed motors.
Note:
The picture on the left represents the nameplate of a / connected motor. For those motors
connected for / , have the voltage and current indication reported as V , V , I , I .
Special execution motors or motors for North America might be provided with additional nameplate
information (i.e. Code Letter, CC number, Service Factor etc.) and some information might be displayed in a
different position from what indicated.

Page 20 of 36 A80H0321
1 Duty type
2 Protection degree
3 Insulation Class, the letters TR following the insulation class means tropicalized treatment
4 Weight (Kg)
5 Motor type designation
6 Serial Number
7 Maximum Static Brake Torque obtainable with proper regulation of the springs (Nm)
8 Brake current (A)
9 Brake Voltage Supply (V). On brake motors with AC brake, the symbol “Vb = Vm” indicates that the motor and brake
have the same voltage supply. For the motor with DC brake the indication 1~230V or 1~400V represent the AC side
single phase input voltage to the rectifier (230V or 400V)
10 Rated Power (kW) at 50 Hz
11 Power Factor at 50 Hz
12 Motor Speed (RPM) at 50 Hz
13 Motor Voltage Supply at 50 Hz in Delta configuration (V)
14 Motor Amps at 50 Hz in Delta configuration (A)
15 Motor Voltage Supply at 50 Hz in Star configuration (V)
16 Motor Amps at 50 Hz in Star configuration (A)
17 Rated Power (kW) at 60 Hz
18 Power Factor at 60 Hz
19 Motor Speed (RPM) at 60 Hz
20 Motor Voltage Supply at 60 Hz in Delta configuration (V)
21 Motor Amps at 60 Hz in Delta configuration (A)
22 Motor Voltage Supply at 60 Hz in Star configuration (V)
23 Motor Amps at 60 Hz in Star configuration (A)
24 Motor voltage supply at 50 Hz (V)
25 Motor Amps at 50 Hz (A)
26 Motor voltage supply at 60 Hz (V)
27 Motor Amps at 60 Hz (A)
28 Mounting position
29 Motor special execution identification. For motors with additional cooling fans, the fan voltage supply is shown in
this location, preceded by the letters “VENT”. The letters “TP” indicate the presence of bimetallic thermal
protectors, “TM” indicate thermistors and “SCALD” indicates anti-condensation heaters followed by their voltage
supply.
30 Efficiency and efficiency class (IE) at 50Hz
31 Efficiency and efficiency class (IE) at 60Hz
32 Certification marks (cCSAus, CCC , etc.)
33 DM, if present, means double terminal board.
34 Number of the motor winding phases ( 3= three phase, 1=single phase)
Table of contents
Languages:
Other MGM Control System manuals
Popular Control System manuals by other brands
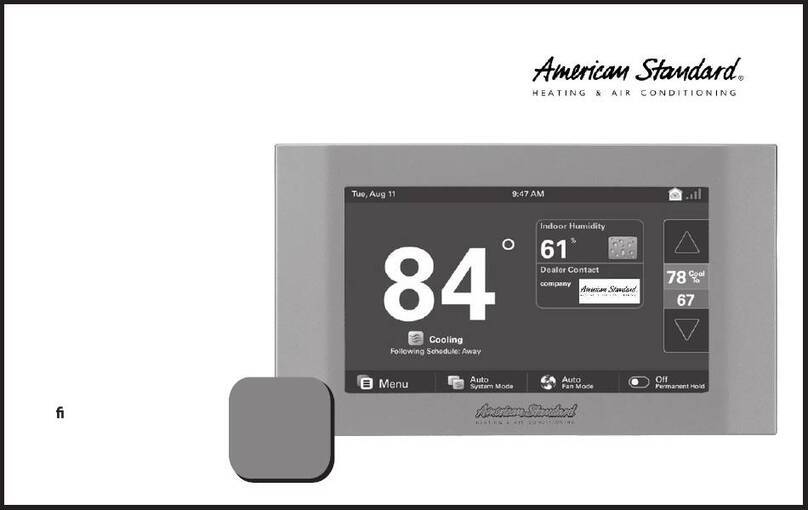
American Standard
American Standard Gold 824 user guide
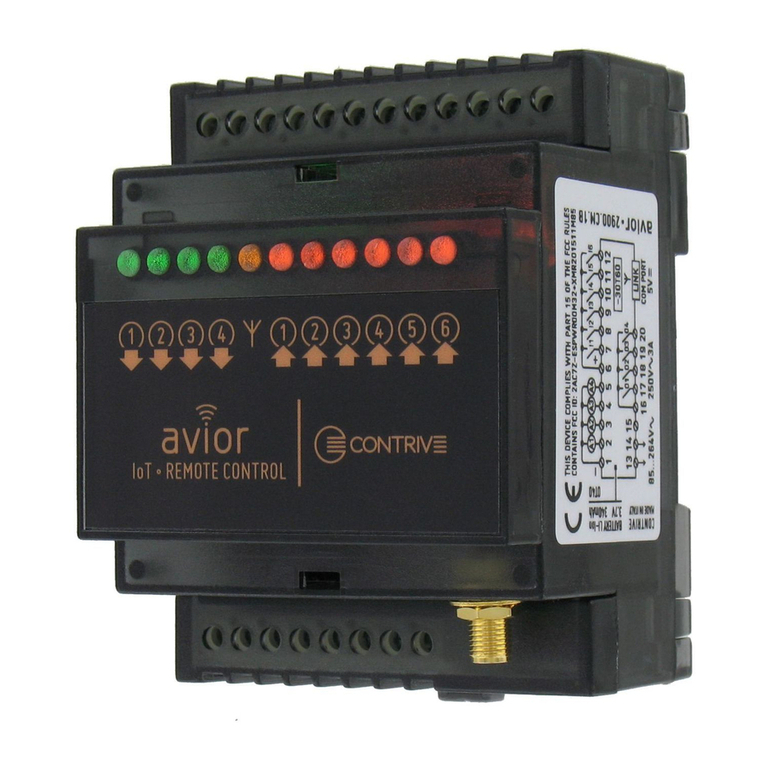
Contrive
Contrive avior quick start guide

Carrier
Carrier AQUASNAP 30RA/RH Operation & maintenance instructions
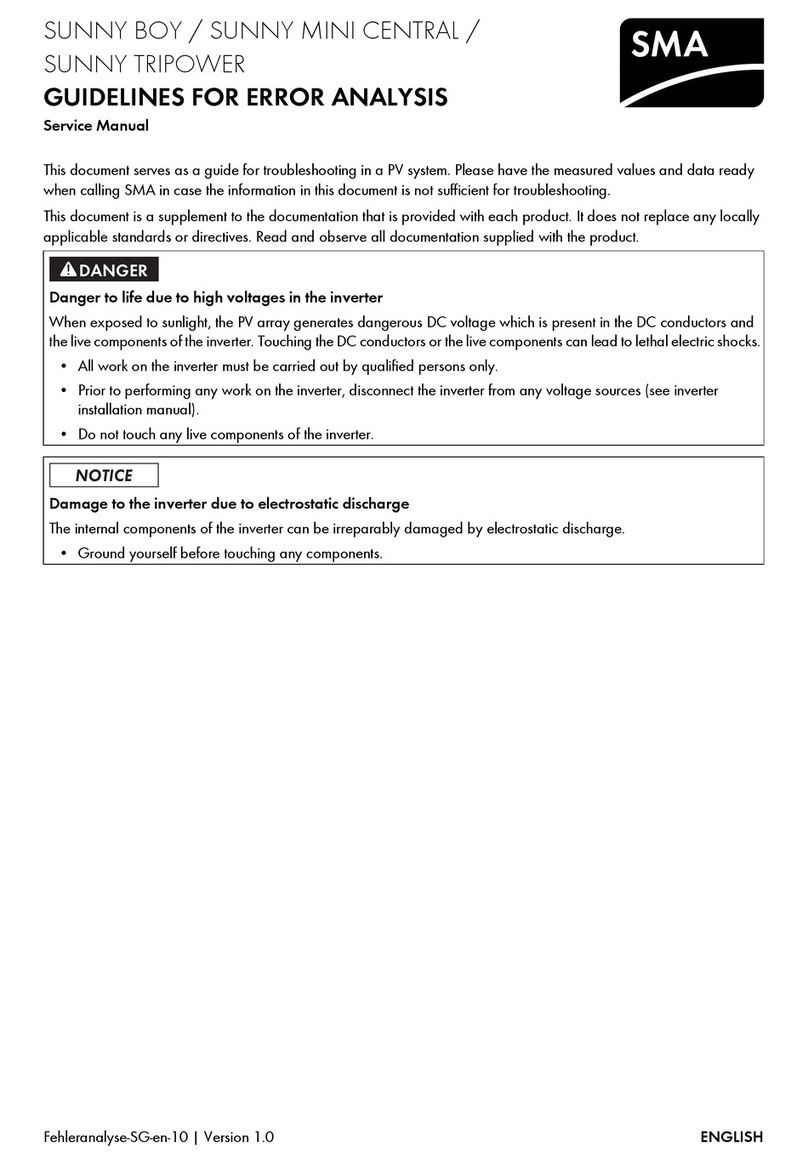
SMA
SMA SUNNY BOYSTORAGE Service manual
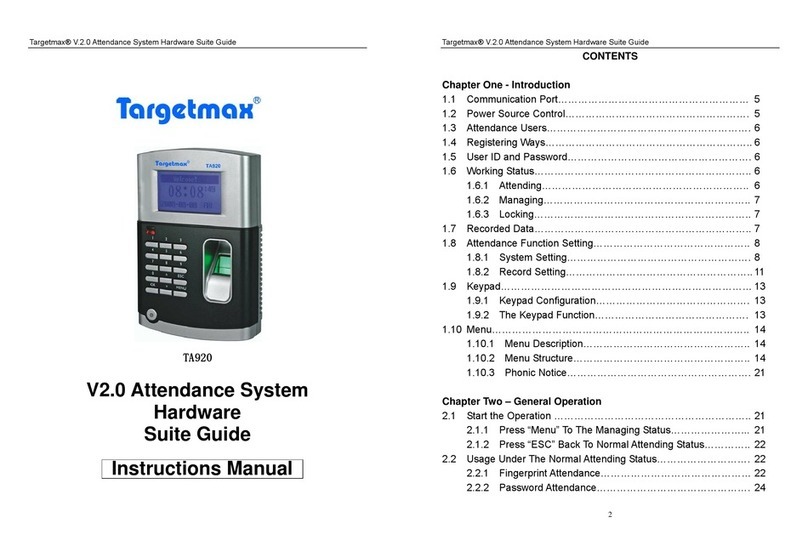
Targetmax
Targetmax TA920 instruction manual

OPTICLIMATE
OPTICLIMATE REVOMAX II Installation & user guide
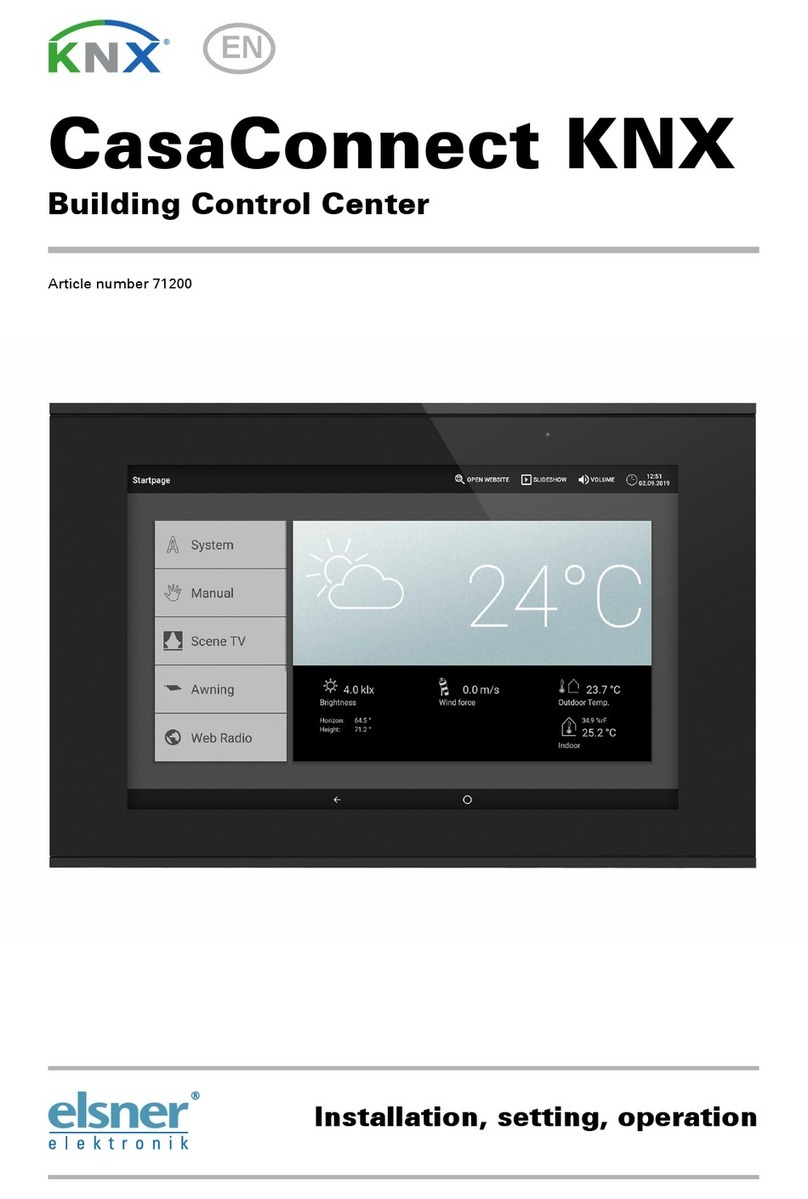
Elsner
Elsner KNX CasaConnect KNX Installation, setting, operation
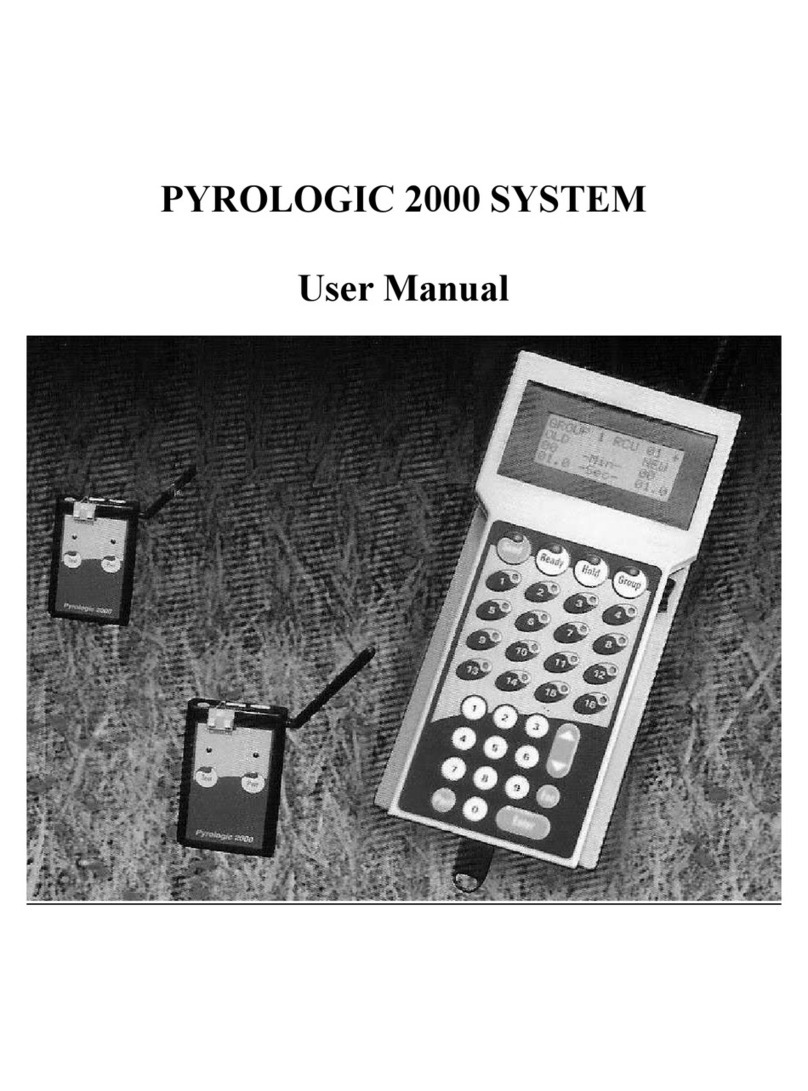
PYROLOGIC
PYROLOGIC 2000 SYSTEM user manual
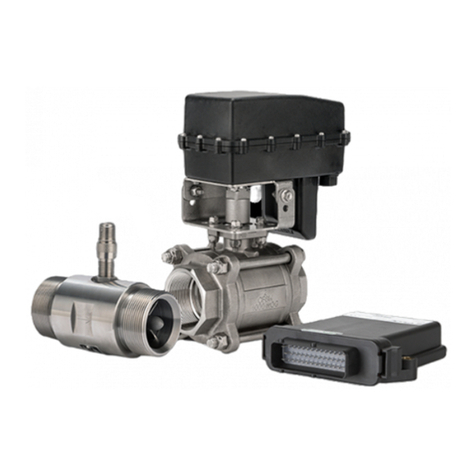
Satloc
Satloc IntelliFlow 2 installation guide
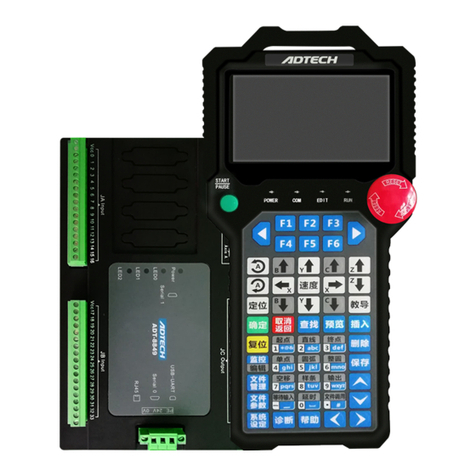
Adtech
Adtech TV5600-B01 Series user manual
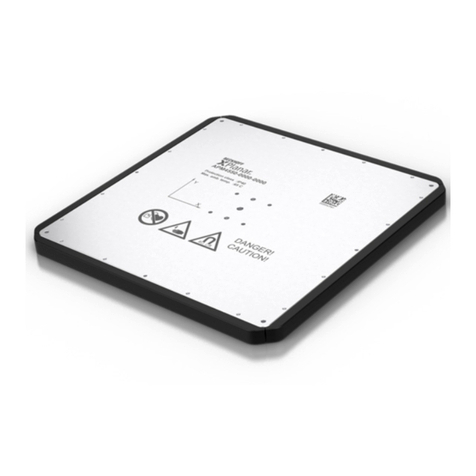
Beckhoff
Beckhoff XPlanar operating instructions
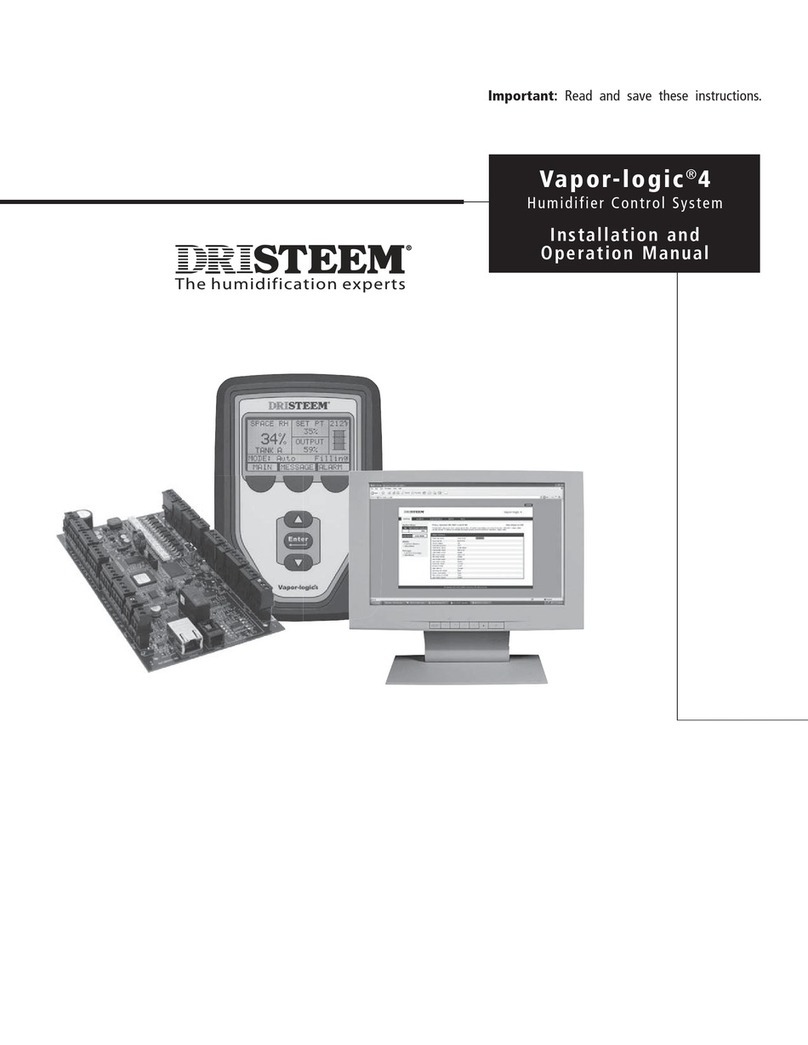
DriSteem
DriSteem Vapor-logic 4 Installation and operation manual