Murphy Lube Level Maintainer LM2000 User manual
Other Murphy Automobile Part manuals
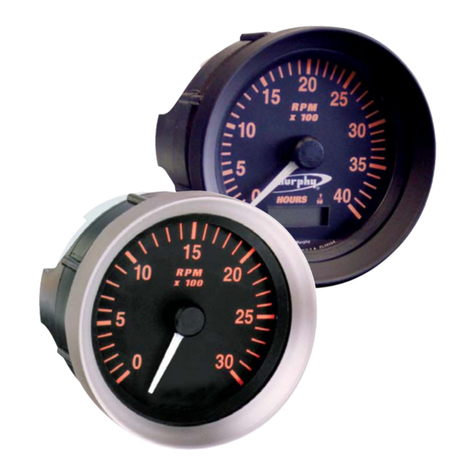
Murphy
Murphy TAH-97026B User manual
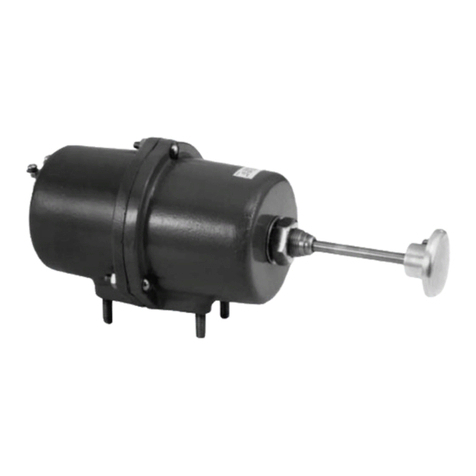
Murphy
Murphy Rack Puller RP75 User manual
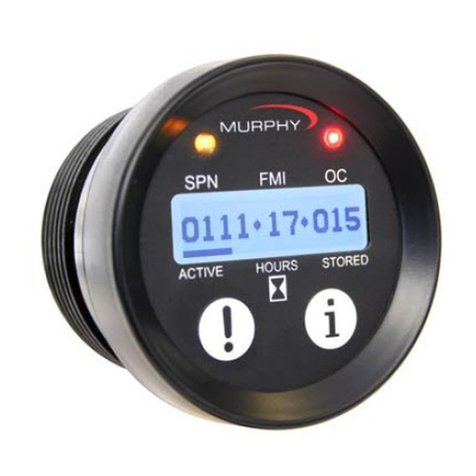
Murphy
Murphy Diagnostic Display PV10 User manual
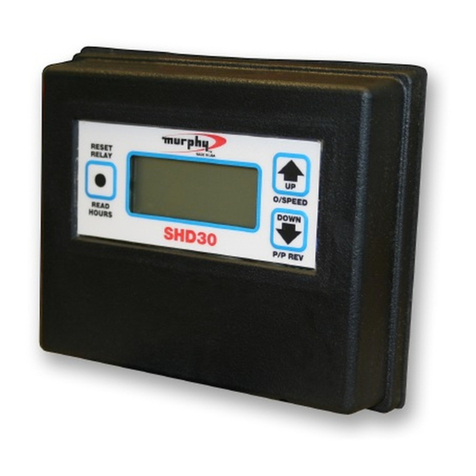
Murphy
Murphy Digital Tach/Hourmeter with Overspeed Trip Point... User manual

Murphy
Murphy Exhaust Pyrometers 10705146 User manual
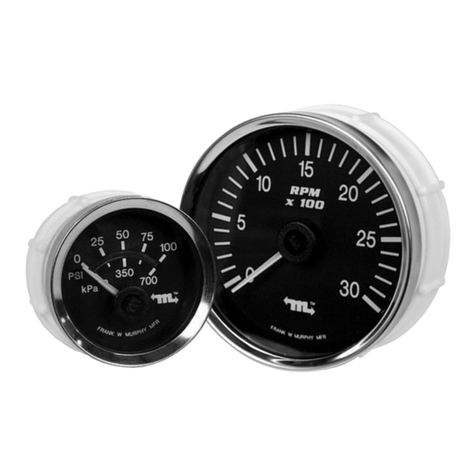
Murphy
Murphy MLA20 User manual

Murphy
Murphy Diesel-Fuel Shutoff Valve SV-Series User manual
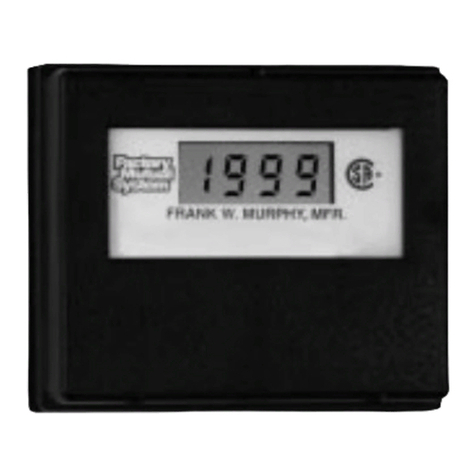
Murphy
Murphy SELECTRONIC TACHSWICH DT9803 User manual
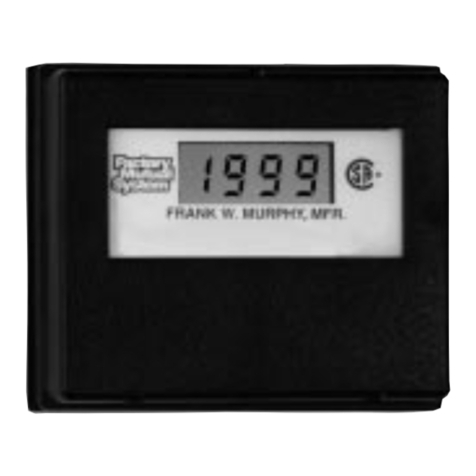
Murphy
Murphy Selectronic DT9800 User manual

Murphy
Murphy Diesel Fuel Check Valves CKV1WPS User manual
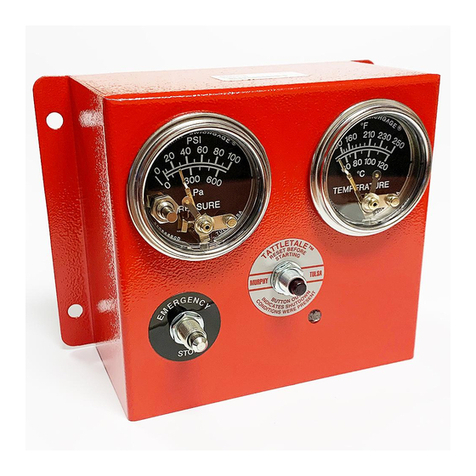
Murphy
Murphy Engine Panels WD300-LV User manual

Murphy
Murphy Gear Oil Pressure Sender EGPK-95083N User manual
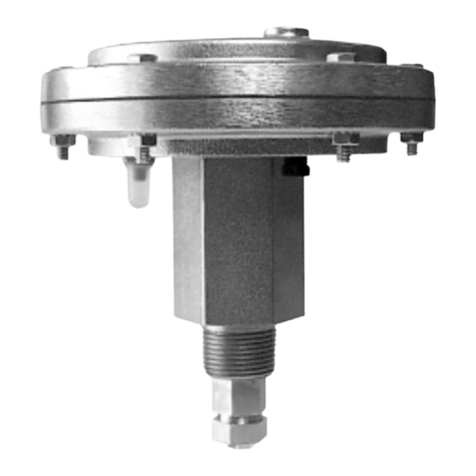
Murphy
Murphy Dump Valves DV Series User manual
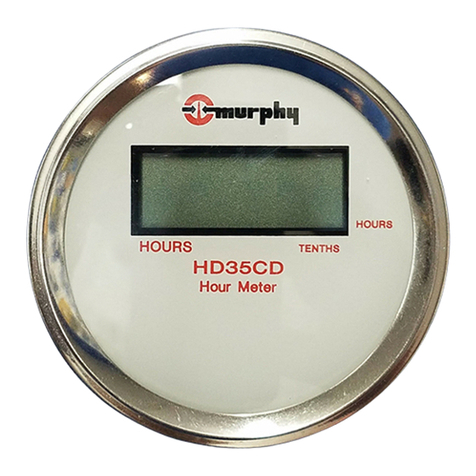
Murphy
Murphy Digital Time Meters HD35-CD User manual
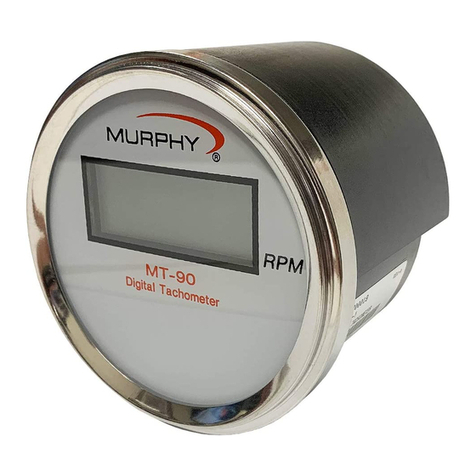
Murphy
Murphy Selectronic MT90 User manual
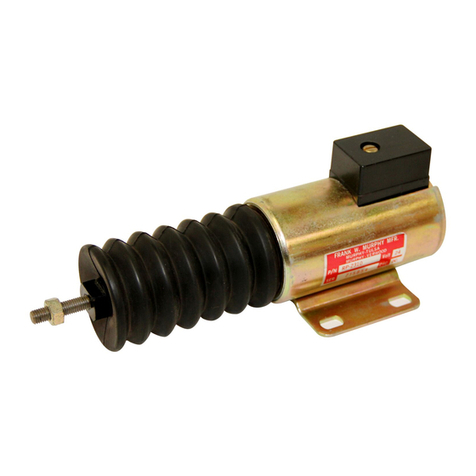
Murphy
Murphy Pull/Push DC Solenoids RP2307B User manual

Murphy
Murphy M5081 Series User manual

Murphy
Murphy MURPHYMATIC AT03069 User manual
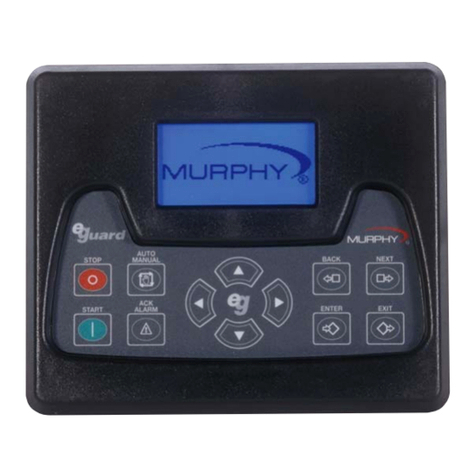
Murphy
Murphy EG-05012B User manual
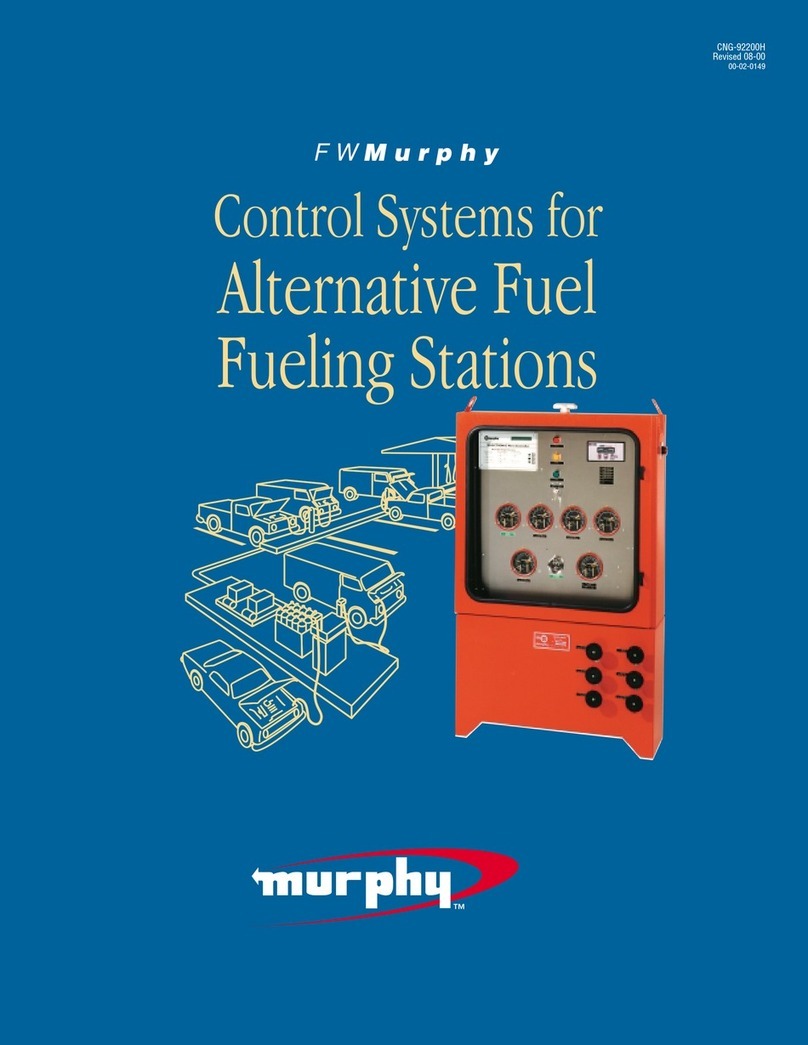
Murphy
Murphy CNG-92200H User manual
Popular Automobile Part manuals by other brands

Ridewell Suspensions
Ridewell Suspensions RAR-251 Installation and service manual
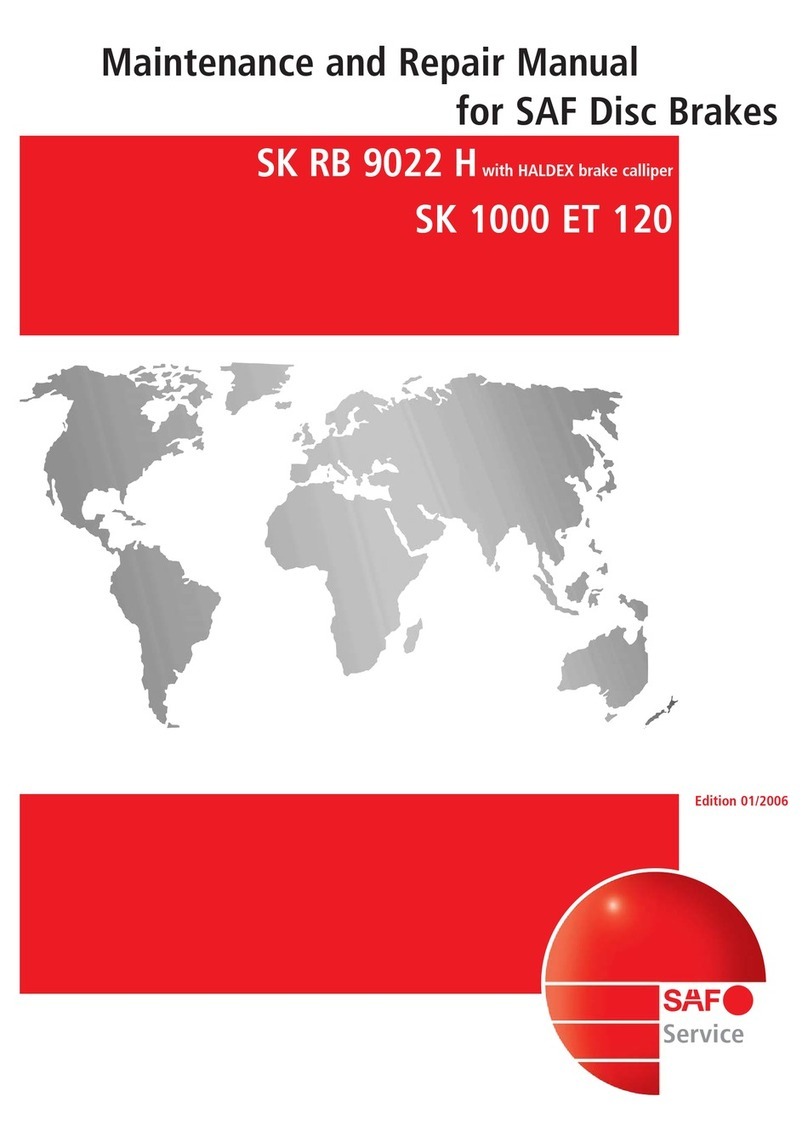
SAF-HOLLAND
SAF-HOLLAND SK RB 9022 H Maintenance and Repair Manual
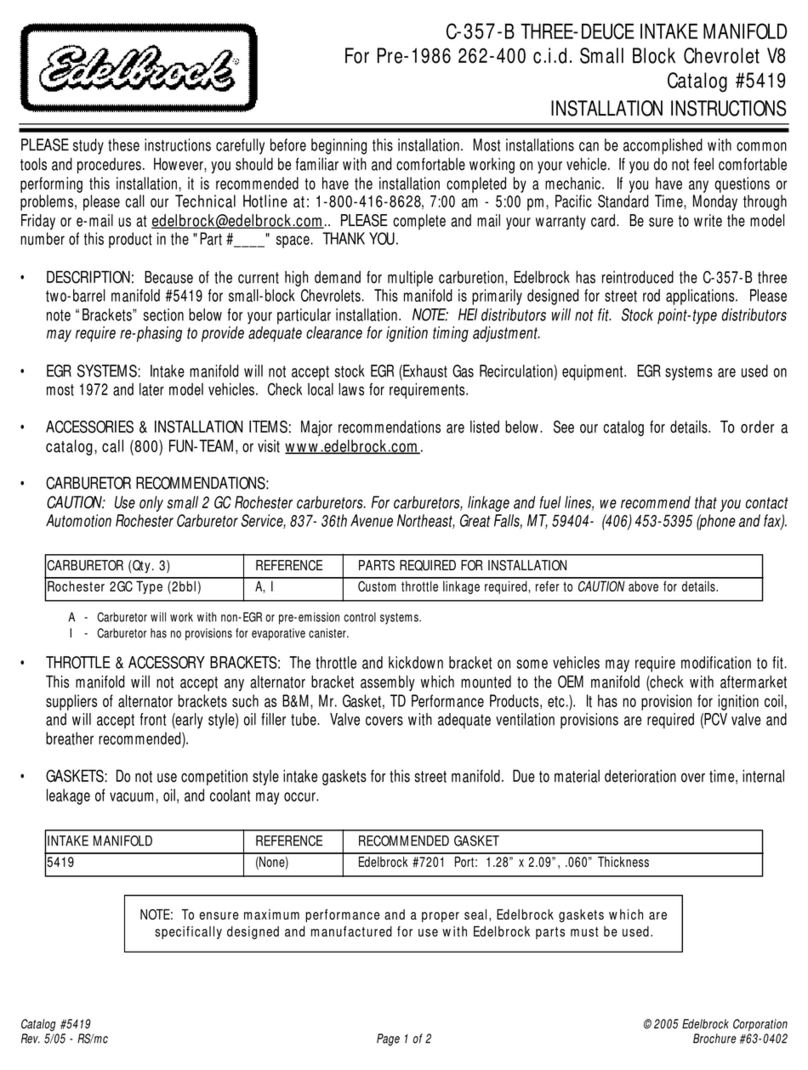
Edelbrock
Edelbrock 5419 installation instructions
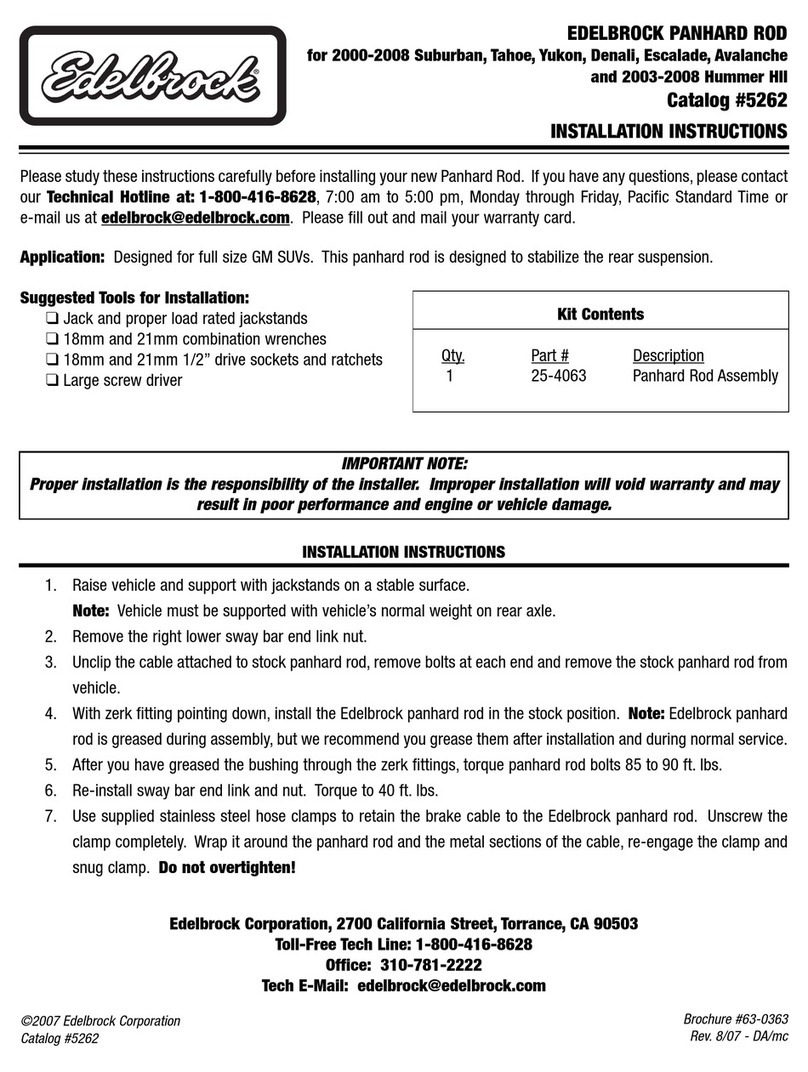
Edelbrock
Edelbrock 5262 installation instructions
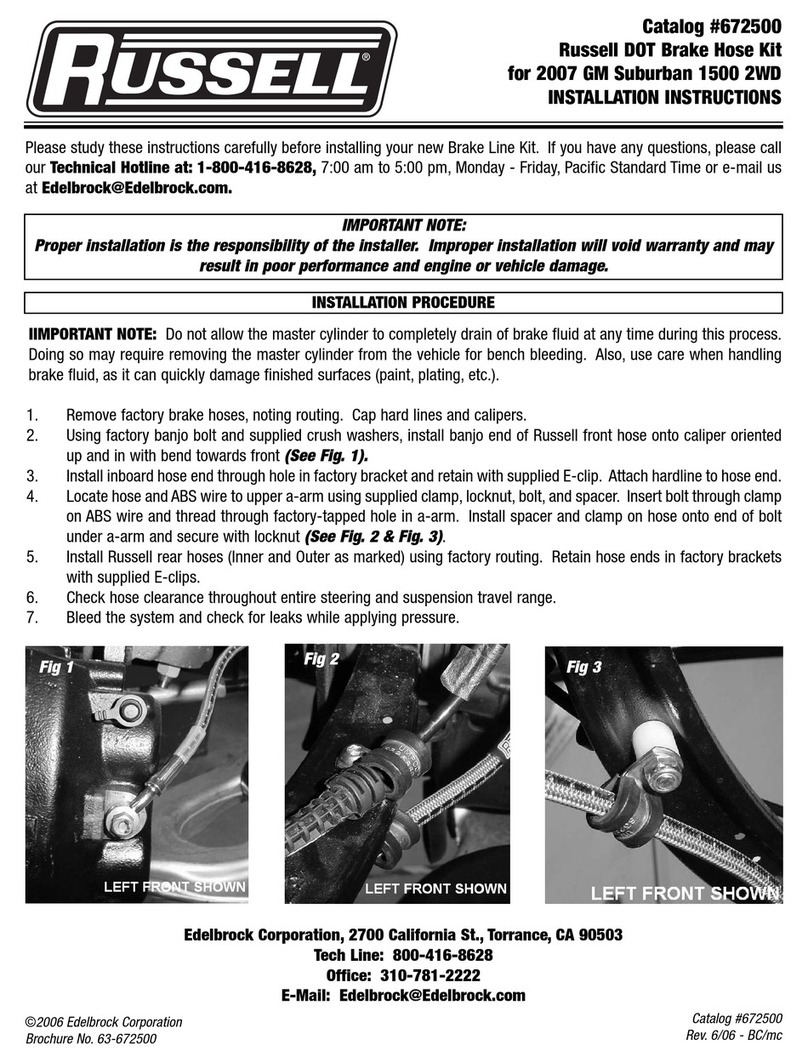
Edelbrock
Edelbrock Russell 672500 installation instructions
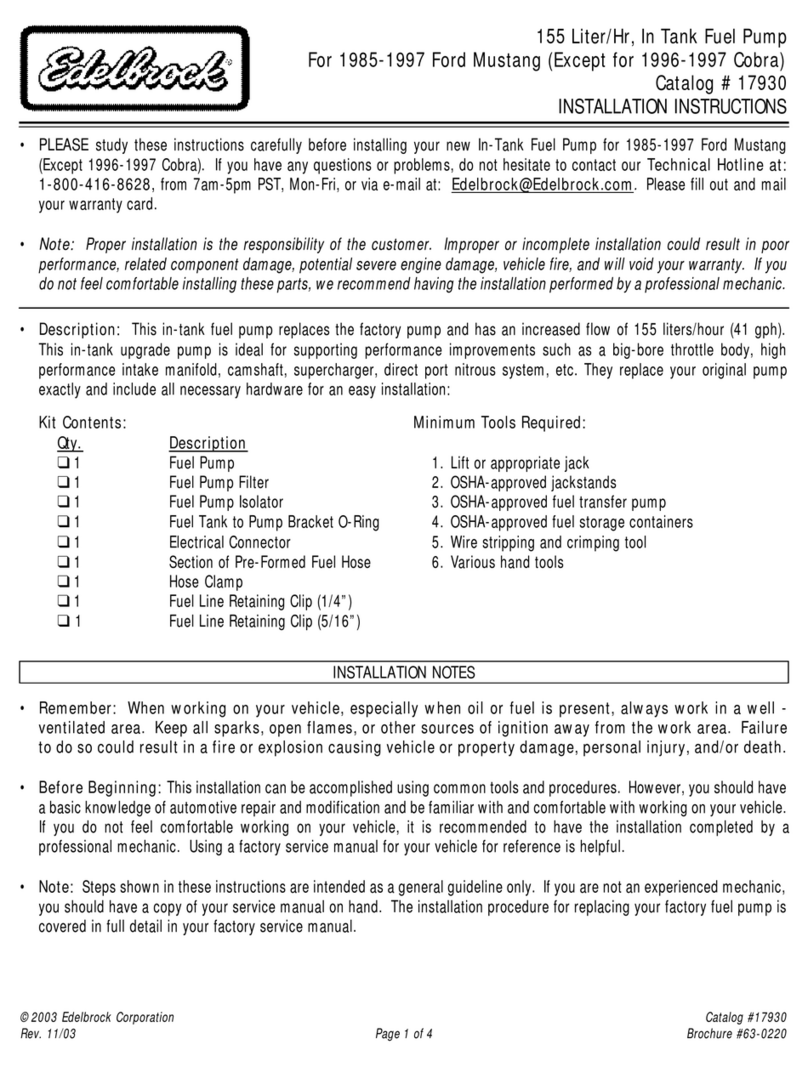
Edelbrock
Edelbrock 17930 installation instructions

Edelbrock
Edelbrock Honda TRX450R Instruction supplement
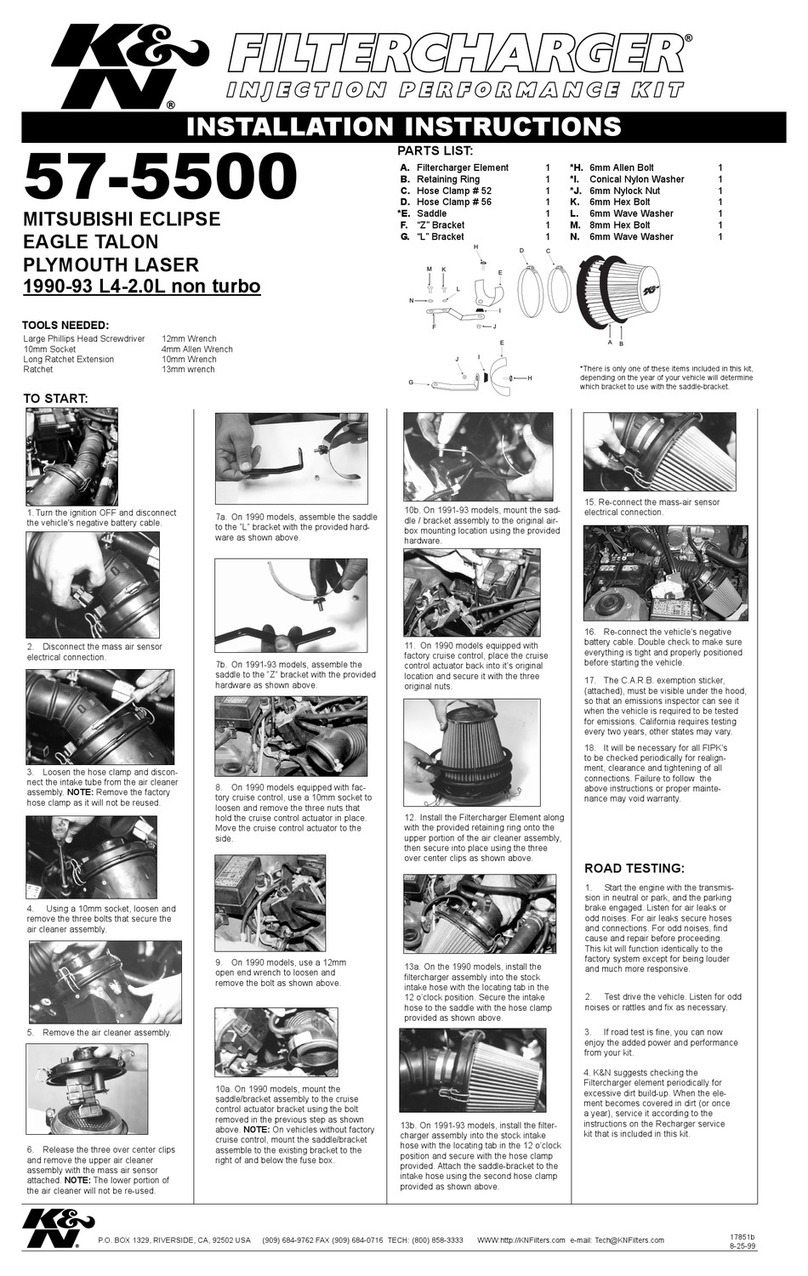
K&N Engineering
K&N Engineering KS-F160 instruction manual
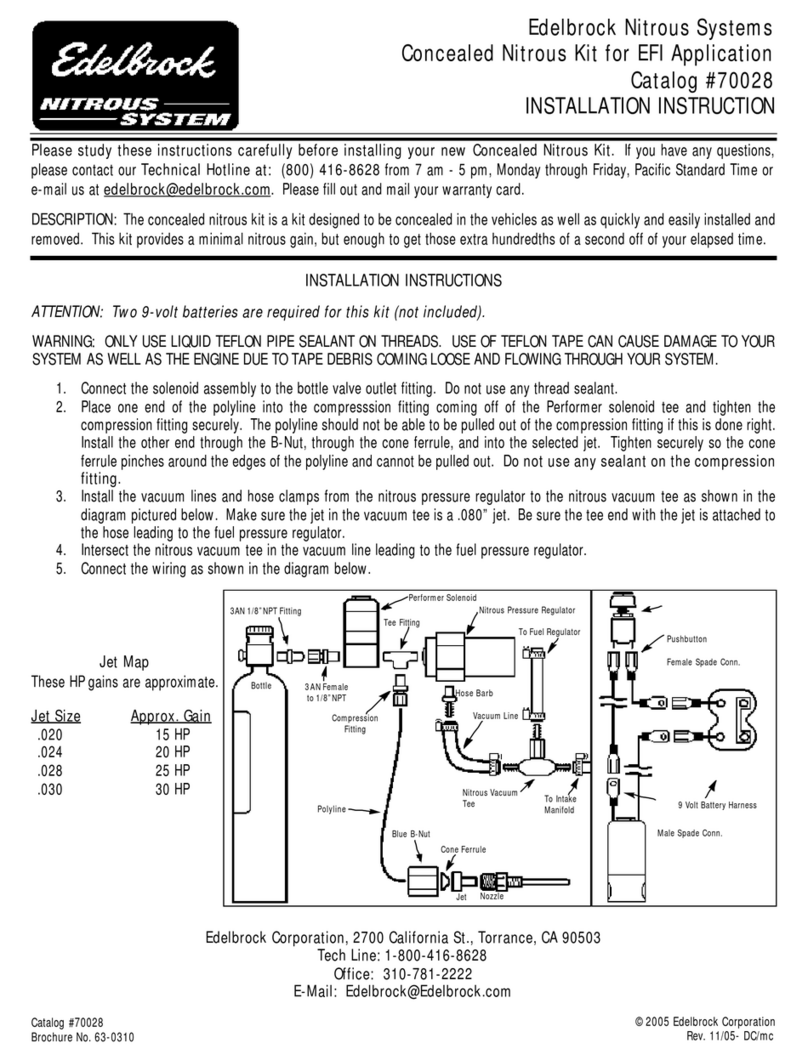
Edelbrock
Edelbrock 70028 installation instructions
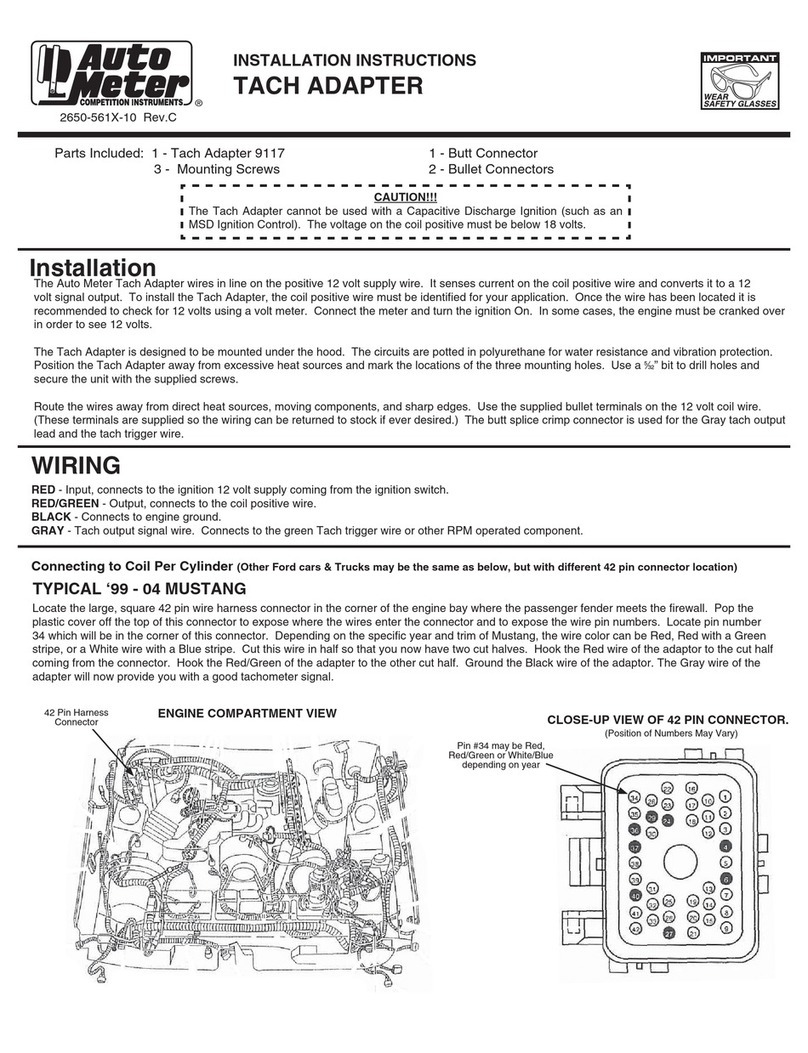
AutoMeter
AutoMeter 9117 installation instructions
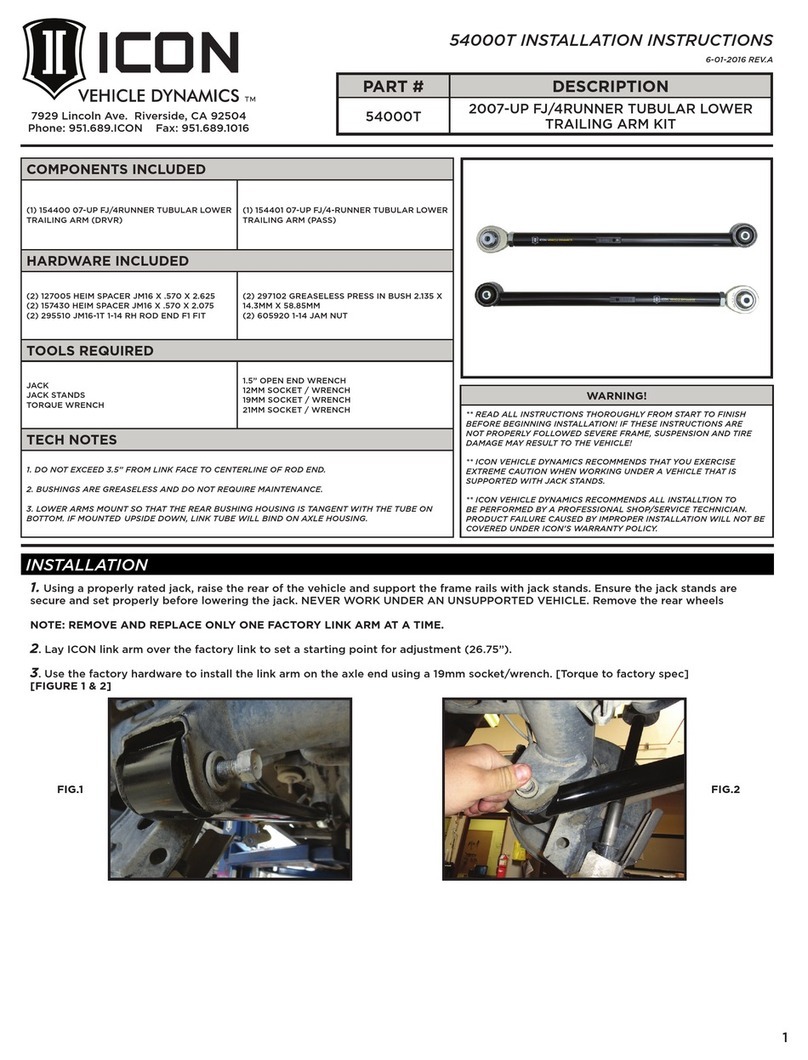
ICON
ICON 54000T installation instructions

Air Lift
Air Lift AirCell 52202 installation guide