ORTEC DSPEC User manual

69;,*
®
DSPEC®
Digital Gamma-Ray Spectrometer
Hardware Manual
Printed in U.S.A. ORTEC Part No. 761560 0303
Manual Revision G

$GYDQFHG0HDVXUHPHQW7HFKQRORJ\,QF
a/k/a/ ORTEC®, a subsidiary of AMETEK®, Inc.
WARRANTY
ORTEC* warrants that the items will be delivered free from defects in material or workmanship. ORTEC makes no other
warranties, express or implied, and specifically NO WARRANTY OF MERCHANTABILITY OR FITNESS FOR A
PARTICULAR PURPOSE.
ORTEC’s exclusive liability is limited to repairing or replacing at ORTEC’s option, items found by ORTEC to be defective
in workmanshipor materials withinone year fromthe date of delivery. ORTEC’s liability on anyclaim of anykind, including
negligence, loss, or damages arising out of, connected with, or from the performance or breach thereof, or from the
manufacture, sale, delivery, resale, repair, or use of any item or services covered by this agreement or purchase order, shall in
no case exceed the price allocable to the item or service furnished or any part thereof that gives rise to the claim. In the event
ORTEC fails to manufacture or deliver items called for in this agreement or purchase order, ORTEC’s exclusive liability and
buyer’s exclusive remedyshall be release of the buyer from the obligation to paythe purchase price. In no event shall ORTEC
be liable for special or consequential damages.
Quality Control
Before being approved for shipment, each ORTEC instrument must pass a stringent set of quality control tests designed to
expose any flaws in materials or workmanship. Permanent records of these tests are maintained for use in warranty repair and
as a source of statistical information for design improvements.
Repair Service
If it becomes necessary to return this instrument for repair, it is essential that Customer Services be contacted in advance of
its return sothataReturn Authorization Number can be assigned to the unit. Also, ORTEC must be informed, eitherinwriting,
by telephone [(865) 482-4411] or by facsimile transmission [(865) 483-2133], of the nature ofthefault of the instrument being
returned and of the model, serial, and revision ("Rev" on rear panel) numbers. Failure to do so may cause unnecessary delays
in gettingthe unit repaired. The ORTEC standard procedure requires that instruments returned for repair pass the same quality
control tests that are used for new-production instruments. Instruments that are returned should be packed so that they will
withstandnormaltransithandlingandmustbeshippedPREPAIDviaAirParcelPostorUnitedParcelServicetothedesignated
ORTEC repair center. The address label and the package should include the Return Authorization Number assigned.
Instruments being returned that are damaged in transit due to inadequate packing will be repaired at the sender's expense, and
it will be the sender's responsibility to make claim with the shipper. Instruments not in warranty should follow the same
procedure and ORTEC will provide a quotation.
Damage in Transit
Shipments should be examined immediately upon receipt for evidence of external or concealed damage. The carrier making
delivery should be notified immediately of any such damage, since the carrier is normally liable for damage in shipment.
Packing materials, waybills, and other such documentation should be preserved in order to establish claims. After such
notification to the carrier, please notify ORTEC of the circumstances so that assistance can be provided in making damage
claims and in providing replacement equipment, if necessary.
Copyright © 2003, Advanced Measurement Technology, Inc. All rights reserved.
*ORTEC®is a registered trademark of Advanced Measurement Technology, Inc. All other trademarks used herein are the
property of their respective owners.

iii
TABLE OF CONTENTS
SafetyInstructionsandSymbols.................................................. v
CleaningInstructions........................................................... v
1. INTRODUCTION .......................................................... 1
1.1. WhatisDSPEC? ....................................................... 2
1.2. About this Manual ...................................................... 2
2. GETTING STARTED ....................................................... 3
2.1. What You Will Learn in this Chapter ....................................... 3
2.2. TheFrontPanel ........................................................ 3
2.3. TheRearPanel......................................................... 4
2.4. InternalSwitches ....................................................... 5
2.5. InternalBattery ........................................................ 8
3. SYSTEM CONNECTION .................................................... 9
3.1. What You Will Learn in this Chapter ....................................... 9
3.2. BuildingaSystem ...................................................... 9
3.2.1. Single-DetectorNon-NetworkedSystem............................... 9
3.2.2. Multiple Detectors ............................................... 10
3.2.3. Multiple Computers .............................................. 10
4. THEORYOFOPERATION ................................................. 11
4.1. What You Will Learn in this Chapter: ...................................... 11
4.2. ReviewoftheHPGeSystem ............................................. 11
4.3. TheShapingAmplifier ................................................. 11
4.4. Analogvs.Digital ..................................................... 12
5. SPECIFICATIONS......................................................... 15
5.1. SystemPerformance.................................................... 15
5.1.1. Indicators ...................................................... 17
5.1.2. Inputs and Outputs ............................................... 18
5.1.3. Controls ....................................................... 19
5.1.4. Interface Connectors .............................................. 19
5.2. ElectricalandMechanical ............................................... 19
5.3. Prerequisites.......................................................... 20
5.3.1. Hardware....................................................... 20
5.3.2. Software ....................................................... 20

DSPEC®Digital Gamma-Ray Spectrometer
iv
6. COMMANDS AND RESPONSES ............................................ 21
6.1. CommandRecords..................................................... 21
6.2. Percent Response Records ............................................... 22
6.3. Dollar Response Records ................................................ 24
6.4. CommandCatalog ..................................................... 24
INDEX..................................................................... 65

v
CAUTION To prevent moisture inside of the instrument during external cleaning, use
only enough liquid to dampen the cloth or applicator.
Safety Instructions and Symbols
This manual contains up to three levels of safety instructions that must be observed in order to
avoid personal injury and/or damage to equipment or other property. These are:
DANGER Indicates a hazard that could result in death or serious bodily harm if the safety
instruction is not observed.
WARNING Indicates a hazard that could result in bodily harm if the safety instruction is not
observed.
CAUTION Indicates a hazard that could result in property damage if the safety instruction is
not observed.
In addition, the following symbols may appear on the product:
DANGER–High Voltage
ATTENTION–Refer to Manual
Please read all safety instructions carefully and make sure you understand them fully before
attempting to use this product.
Cleaning Instructions
To clean the instrument exterior:
Disconnect the instrument from the power source.
Remove loose dust on the outside of the instrument with a lint-free cloth.
Remove remaining dirt with a lint-free cloth dampened in a general-purpose detergent and
water solution. Do not use abrasive cleaners.
Allow the instrument to dry completely before reconnecting it to the power source.

vi

1
1. INTRODUCTION
ORTEC’s DSPEC (pronounced D–Spec) is an industry first —the first integrated, digital-
signal-processor-based, digital gamma-ray spectrometer for use with all types of germanium
detectors, including super-large detectors.
DSPEC combines all the best features of low- and high-rate analog systems in a single, PC-
based package that is easily connected to local area networks (LANs). This highly automated,
yet flexible, hardware and software combination is suitable for most spectroscopy applications.
From all sides, environmental measurement through physics research to on-line industrial
measurements, the question has often been posed: “Why can’t one system provide the best in
resolution, throughput, and stability simultaneously? Why do we always have to make a less-
than-ideal compromise when the detector itself is capable of more performance?”Until now,
these questions have remained unanswered. Now DSPEC provides those answers:
In Environmental Counting, DSPEC provides extremely high stability over long counting
times. DSPEC solves the ballistic deficit problem that often degrades the resolution of large
HPGe detectors. It delivers the best resolution of which any detector is capable. A statistical
preset optimizes sample throughput, and delivers lower cost per sample.
DSPEC is highly automated, ending forever the need to use screwdriver or oscilloscope to
achieve the best performance.
Recognizing that not all counting rooms provide “laboratory conditions,”DSPEC also
provides unprecedented temperature stability for varying ambient temperature.
For applications involving high or widely varying count rates —such as intermediate-level
waste measurement or post accident sampling —DSPEC has unmatched count-rate stability
in both peak position and resolution.
For industrial applications and when LANs are a requirement, DSPEC’s built-in Ethernet
port allows direct connection to the network. No other integrated instrument can do this.
Those wanting to wring the last drop of resolution performance from their detector will
appreciate the built-in InSight™“Virtual Oscilloscope.”
DSPEC is a truly unique package, providing real benefits “where it counts,”for all gamma
spectroscopy operations: STABILITY, RESOLUTION, and AUTOMATION.

DSPEC®Digital Gamma-Ray Spectrometer
2
1.1. What is DSPEC?
One germanium or silicon gamma or x-ray detector, one PC, and one DSPEC comprise a
complete spectroscopy system. The detector provides a signal proportional to the gamma-ray
energy; the PC provides the user interface, data display, and storage; and the DSPEC provides
everything else.
DSPEC includes an analog prefilter, fast digitizing circuits, and digital signal processing to
optimize energy resolution and data rate, via variable rate baseline restoration, automatic pulse
pile-up rejection, automatic pole-zero cancellation, ballistic deficit correction and zero effective-
conversion-time peak detection, measurement, and storage. Spectral data is maintained in the
DSPEC battery-backed data memory until transferred to the PC by the user. DSPEC also
includes the high-speed data link to the PC, with a choice of ORTEC’s ultra-fast, direct Dual-
Port Memory interface or standard Ethernet interface. You can even connect multiple DSPEC
units into networks and control them all from anywhere on the network!
1.2. About this Manual
This manual describes the ORTEC DSPEC Digital Gamma-Ray Spectrometer, and provides all
the information necessary to prepare the DSPEC for use and connect it into a complete
spectroscopy system. Because the DSPEC is almost completely computer controlled, this manual
is short. Details on running the control software are contained in the MAESTRO™and
GammaVision™software manuals. A condensed version of some key MAESTRO and
GammaVision information is provided in the ORTEC publication entitled “DSPEC Digital
Gamma-Ray Spectrometer and Its Use with MAESTRO™or GammaVision™.”

3
Fig. 1. DSPEC Front Panel.
2. GETTING STARTED
2.1. What You Will Learn in this Chapter
In this chapter you will:
Become acquainted with the DSPEC front- and rear-panel indicators and controls.
Set the electrical power input for your local conditions.
Learn whether you need to change the factory settings of the internal switches.
2.2. The Front Panel
Figure 1 shows the DSPEC front panel.
Starting from the left, there are four LEDs indicating the status of the detector bias supply.
Illumination of the HV ON light indicates that the rear-panel high voltage connector is powered.
Either the HV POS or HV NEG light will be illuminated to show the internal setting of the
detector bias polarity switch.
The OVERLOAD light indicates that the power supply is overloaded and shut down. (This
condition usually indicates a shorted output due to a faulty cable or improper connection.)
The PROCESSOR BUSY light flashes to indicate functions of the internal microprocessor.

DSPEC®Digital Gamma-Ray Spectrometer
4
Fig. 2. DSPEC Rear Panel.
The STABILIZER GAIN and OFFSET numeric displays indicate the settings of the internal
digital spectrum stabilizer. If the stabilizer is not being used, the displays indicate “off.”
The SPECTROMETER ACCEPT and REJECT lights indicate the operation of the internal
pulse pile-up rejector. If pulses from the detector are too close together in time to be accurately
measured, they are rejected and the REJECT light flashes. Each measured pulse causes the
ACCEPT light to flash.
Additional information on the rate of data acquisition is available from the SPECTROMETER
DEADTIME numeric display. The dead time of the system is the fraction of time that the
system is busy and unavailable to process pulses. As the count rate increases, the number of
events rejected by the pile-up rejector increases and the dead time increases. At 50% dead time,
half of the pulses occur so closely together that they are rejected.
The POWER switch turns the instrument on or off and indicates its status with a lighted
indicator.
2.3. The Rear Panel
Figure 2 shows the DSPEC rear panel.

2. GETTING STARTED
5
Under the cooling fan is the power input block, into which is plugged an international standard
AC power cord suitable for local power distribution. A small printed circuit board can be
accessed behind a sliding plastic window. This board can be inserted in four different ways,
allowing you to select 100, 120, 220, or 240 volts. The selected voltage is the only one that can
be read through the window. The correct fuse size, power cord, and voltage setting are supplied
with the instrument.
PREAMP POWER, both ±12 and ±24 volts DC, is provided via a standard 9-pin D-type
connector.
The HIGH VOLTAGE section has three components. A 10-turn potentiometer sets the value of
the detector bias. A BNC connector receives the signal indicating a warmed-up detector,
requiring removal of detector bias. The OUTPUT connector is an SHV-type connector carrying
the detector bias voltage.
The next section has three BNC connectors. The INPUT connector receives the low-level
analog signal from the preamplifier. The ADC GATE connector is an input which can be used
to cause the system to accept or reject a pulse under the control of external electronics. The TRP
INHIBIT is an input used to reject pulses during the reset period of detectors with transistor-
reset preamplifiers.
CHANGE SAMPLE is a logic output used to control sample changers. SAMPLE READY is a
logic input used to report that the sample changer has completed changing the sample. (Use of
these features requires software support discussed in the software manuals.)
Connection to the computer is by means of either the DUAL-PORT MEMORY 37-pin D-Type
connector or the ETHERNET BNC connector. Most new systems will use the more convenient
Ethernet connection; the Dual-Port Memory method is provided for compatibility with existing
systems. The RS-232-C connector provides a low-speed serial link to the PC and is normally not
used.
2.4. Internal Switches
NOTE If you are using P-type detectors, such as ORTEC’s GEM Series, or if you have
purchased a complete system, you may skip the remainder of this section.
There are two internal settings which must be correctly set for your particular type of detector.
Changing these settings requires removal of the DSPEC cover:

DSPEC®Digital Gamma-Ray Spectrometer
6
DANGER Turn off the DSPEC, remove its power cord, and wait several minutes for the
power supply to discharge before performing this operation!
CAUTION The cover is not secured to the chassis; therefore, if the chassis is supported
only by the cover and tilted with the back panel downward, the chassis can
slide free and fall!
1. Place the DSPEC upside down on a clean workbench, preferably covered with cloth or clean
paper to prevent scratching the cover.
2. Remove the four Phillips-head screws that secure the cover. There is one screw at each
corner, just outside the rubber feet.
3. Carefully place the DSPEC back on its rubber feet.
4. Slide the cover forward to free it from the chassis. Figure 3 shows the internal details of the
DSPEC.
Note the amplifier input polarity switch (note the pointer slightly right of bottom center). This
switch must be set to match the output polarity of your detector’s preamplifier. The factory
setting is positive, which is appropriate for ORTEC GEM detectors and most other P-type
detectors. For those ordering a complete system, the setting will be set correctly during system
checkout.
Changing the detector bias supply polarity is easy to do but not easy to explain:
1. Remove the cover as described above.
2. Turn the DSPEC so that its right side (opposite the power supply and fan) faces you.
3. The high-voltage power supply board is the bottom board in the stack of four boards.
4. Locate the bias selector board (BSB), shown in Fig. 4. The BSB is a printed circuit board
approximately 180 mm ×15 mm. It has eight pairs of jumper pins that plug into the high-
voltage power supply board.
The BSB moves one jumper location left or right to select between HPGe detectors or NaI
detectors. The leftmost position is correct for HPGe detectors.

2. GETTING STARTED
7
Fig. 3. Internal Details and Amplifier Input Polarity Switch.
Moving one jumper location from the edge of the board toward the center selects negative or
positive bias. The jumpers closest to the edge of the high-voltage power supply board select
positive voltage; the jumpers toward the center select negative voltage.
5. There are two ways to move the BSB. The easiest way for most people is to place the index
finger of each hand on the ends of the BSB and lift up about one centimeter until the jumpers
clear the board. Move the BSB to the correct set of jumpers and position the jumpers into the
high-voltage power supply board. The BSB can then be completely reseated by pressing
down from the top with your fingertips.
Alternatively, the BSB can be lifted and moved using tools. Two electronics-type needlenose
pliers, one held in each hand, can be used to grip the BSB near each end. Lift and move to
the required jumper position, then position the jumpers with a gentle downward pressure.
Press the BSB completely into place using either the pliers or your fingertips, as above.

DSPEC®Digital Gamma-Ray Spectrometer
8
Fig. 4. Bias Selector Board (BSB).
2.5. Internal Battery
An internal lithium battery provides backup of settings when the power to the unit is off. Should
the battery become depleted, replace it with ORTEC Part Number 739460.

9
CAUTION Detectors can be seriously damaged if this protection is ignored.
3. SYSTEM CONNECTION
3.1. What You Will Learn in this Chapter
In this chapter you will learn how to:
Connect a single-detector/single-computer spectroscopy system.
Add multiple detectors to the basic system.
3.2. Building a System
3.2.1. Single-Detector,Non-Networked System
1. Connect the detector preamplifier power, using the 9-pin D-type connector and the supplied
power cable. The DSPEC provides this power from its rear-panel PREAMP POWER
connector.
2. Connect the detector high-voltage bias. This is usually an SHV-type high-voltage coaxial
connector on the detector preamplifier. The DSPEC supplies this bias voltage from its rear-
panel 0–5 kV OUTPUT connector.
3. Connect the bias voltage shutdown circuit. Most cryogenic detectors signal if they are
warming up and should have the bias removed.
4. Connect the Preamplifier Energy Output to the DSPEC rear-panel INPUT connector. The
cable used is normally 100-coaxial cable with BNC type connectors.
5. Connect the data link from the DSPEC to the computer. The normal connection is Ethernet
standard 50-cable with BNC type connectors. Alternatively, the ORTEC Dual-Port
Memory connection can be used. This connection requires that the ORTEC interface card be
installed in your computer. ORTEC can supply the special cable, with 37-pin D-type
connections.
6. Plug in the power and you are ready to take data!
If your detector has a pulsed-reset type preamplifier (ORTEC’s “PLUS”Series), use BNC
coaxial cable to connect the detector’s INHIBIT or RESET output to the DSPEC rear-panel
INHIBIT input.

DSPEC®Digital Gamma-Ray Spectrometer
10
3.2.2. Multiple Detectors
Each DSPEC processes the output of a single detector. If your lab has more than one detector,
multiple systems can be set up as described above. It is usually far more convenient to control all
the detectors from a single computer. This is easy to do with DSPEC-based systems. Using the
Ethernet data link connection method, it is only necessary to chain all DSPECs together into a
single LAN using BNC T-connectors at each DSPEC. (Don’t forget the 50-terminator
required at the last DSPEC in the chain.) ORTEC software handles all the details of finding the
detectors and allowing them to be named individually.
If the Dual-Port Memory data link has been chosen, it is still convenient to connect up to eight
DSPEC controlled detectors (or many other combinations of ORTEC MCBs) to one computer.
The only requirement is a special cable available from ORTEC, plus the standard software.
When more than one ORTEC MCB is connected to a single computer via the Dual-Port Memory
Interface, each MCB in the system must have a unique MCB address. The MCB address for a
DSPEC is set with a jumper inside the unit. To change the jumper setting do the following:
1. Remove the cover of the DSPEC as outlined above.
2. On the inside of the DSPEC, follow the ribbon cable connected to the Dual-Port Memory
connector to the location at which it plugs into the circuit board. The DPM address jumper is
located just behind the ribbon-cable connection point toward the rear of the DSPEC. The
jumper consists of two parallel rows of eight right-angle pins.
3. Move the jumper to the desired address. Address 1 is represented by the two pins closest to
the outside edge of the DSPEC. Address 8 is represented by the two pins closest to the center
of the DSPEC. Figure ? shows the appropriate jumper location for each address.
4. Replace the DSPEC cover.
3.2.3. Multiple Computers
Adding multiple computers is as easy as adding multiple detectors. Using the LAN described
above, multiple computers can control single or multiple detectors using standard Microsoft®
operating systems and ORTEC software. Such systems are cost-effective, redundant, reliable,
and easy to use.

11
4. THEORY OF OPERATION
4.1. What You Will Learn in this Chapter:
Briefly review a high purity germanium (HPGe) gamma-ray spectroscopy system.
Learn how a shaping amplifier controls the tradeoffs between energy resolution and data rate
in an HPGe system.
Compare analog and digital spectroscopy systems.
4.2. Review of the HPGe System
An HPGe detector is a semiconductor diode. Its operation is similar to that of a photodiode
except that it is a few thousand times larger. The detector is operated under reverse bias
(typically a few thousand volts) and at about the temperature of liquid nitrogen. An evacuated
cryostat provides the clean vacuum and low temperature needed by the detector.
When the detector absorbs a gamma-ray photon, electron-hole pairs are created. The resulting
charge pulse is integrated by a charge-sensitive preamplifier to produce a voltage step
proportional to the energy of the gamma ray.
The signal produced by the HPGe detector is very small. A 1-MeV gamma-ray photon produces
a signal of about one-tenth of a volt out of the preamplifier. This small signal must be amplified,
filtered to produce the best signal-to-noise ratio, and measured to a precision of one part in
16,000 in a few microseconds. The amplitude measurement is used to increment the appropriate
element (channel) of an array in data memory. The result of many such measurements is the
spectrum of gamma-ray energies seen by the detector.
4.3. The Shaping Amplifier
The signal produced by the preamplifier must be further processed before being digitized. Three
problems must be addressed:
1. The signals are not referenced to any particular voltage level (such as the system ground) but
instead have a random DC component.
2. Improvements in signal-to-noise ratio can be made by appropriate filtering.
3. The signals are not matched to the range of typical analog-to-digital circuits (ADCs).
The classic solution to these problems is performed by a device called the Shaping Amplifier.
The dc component is removed and low-frequency noise reduced by electronically differentiating
(high-pass filtering) the signal. High-frequency noise is reduced by multiple integrations (low-

DSPEC®Digital Gamma-Ray Spectrometer
12
pass filtering). Variable gain allows matching the range of gamma-ray signals to the range of the
ADC.
The shape and time duration of the shaping amplifier output pulse determine the electronic noise
and maximum data rate of the system. Analog systems typically use a Gaussian shape (like the
standard probability curve) or a modified triangular shape. These perform well, but the optimum
shape has an exponential rising edge, a flattop of duration about equal to the detector rise time,
and an exponentially falling edge with the same time constant as the rising edge. This shape is
referred to as a flattop cusp. Obtaining this shape is very difficult with analog electronics.
There is no advantage to adjusting the time duration of the output pulse to a value longer than
the minimum required. If the optimum duration is too long for the existing count rate, shorter
values are used to allow higher rates accompanied by somewhat degraded energy resolution.
Analog amplifiers typically allow two shapes and 5–10 durations (shaping times).
These systems have been in continuous development for over 30 years. Modern analog systems
include special circuits called baseline restorers to maintain the reference voltage level, and
pile-up rejectors that reject signals that occur so close to another signal that they are distorted.
4.4. Analog vs. Digital
If the output of the preamplifier is sampled at a very high rate by a fast ADC, digital signal
processing can be used to perform all the functions performed by the analog shaping amplifier.
The output of the “shaping amplifier”exists as a sequence of numbers instead of a voltage
signal, but there is an exact equivalence to the analog system. The optimum shape and time
duration are the same. The tradeoff of noise and data rate are the same. The differences,
however, are many:
The digital system can generate the ideal flattop cusp. The shape of the rising and falling
edges (the “cuspiness”) are adjustable to match the detector’s noise characteristics or
improve data rate. The width of the flattop is adjustable to match the rise time.
Changing the shaping time in the analog system involves mechanical switches changing
several components. Consequently, the number of shaping times available is limited. The
shaping time in the digital system is determined by constants in the DSPEC computer code
and can be changed at will. Many more values are available.
The gain in analog systems depends on the value of electronic components and drifts with
temperature and time. Digital systems do not exhibit such changes. As the DSPEC is almost
totally digital, it drifts much less than analog systems.

4. THEORY OF OPERATION
13
The reference baseline in analog systems varies with count rate. This causes peaks in the
spectrum to shift and broaden. Digital systems have no such effects. Again, as most of the
DSPEC is digital, such problems are vastly reduced.

DSPEC®Digital Gamma-Ray Spectrometer
14
Table of contents
Other ORTEC Measuring Instrument manuals
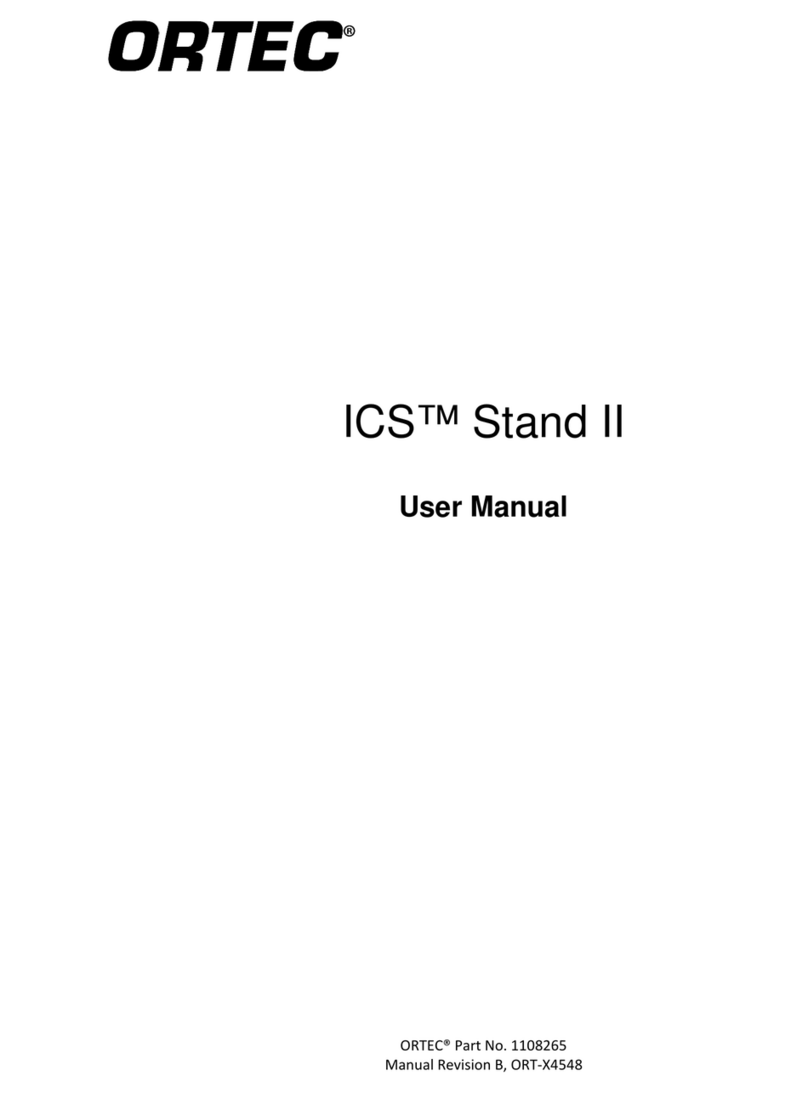
ORTEC
ORTEC ICS Stand II User manual
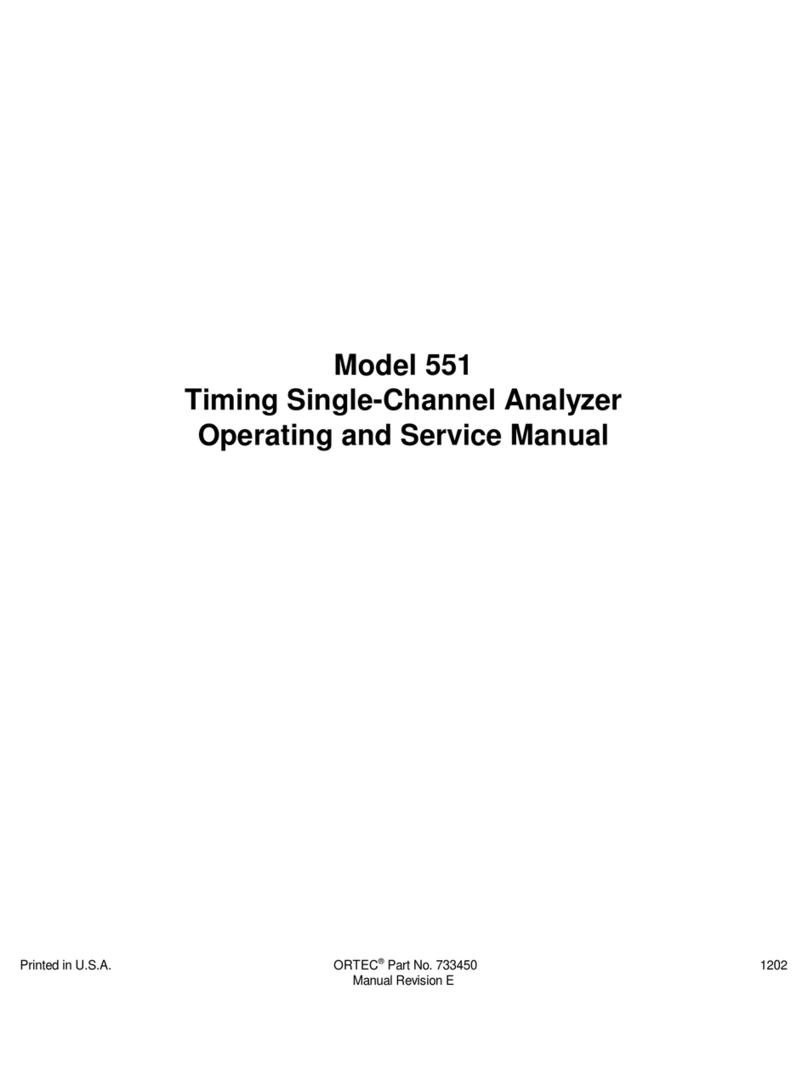
ORTEC
ORTEC 551 Service manual

ORTEC
ORTEC DSPEC Pro Instructions for use

ORTEC
ORTEC 418A Service manual
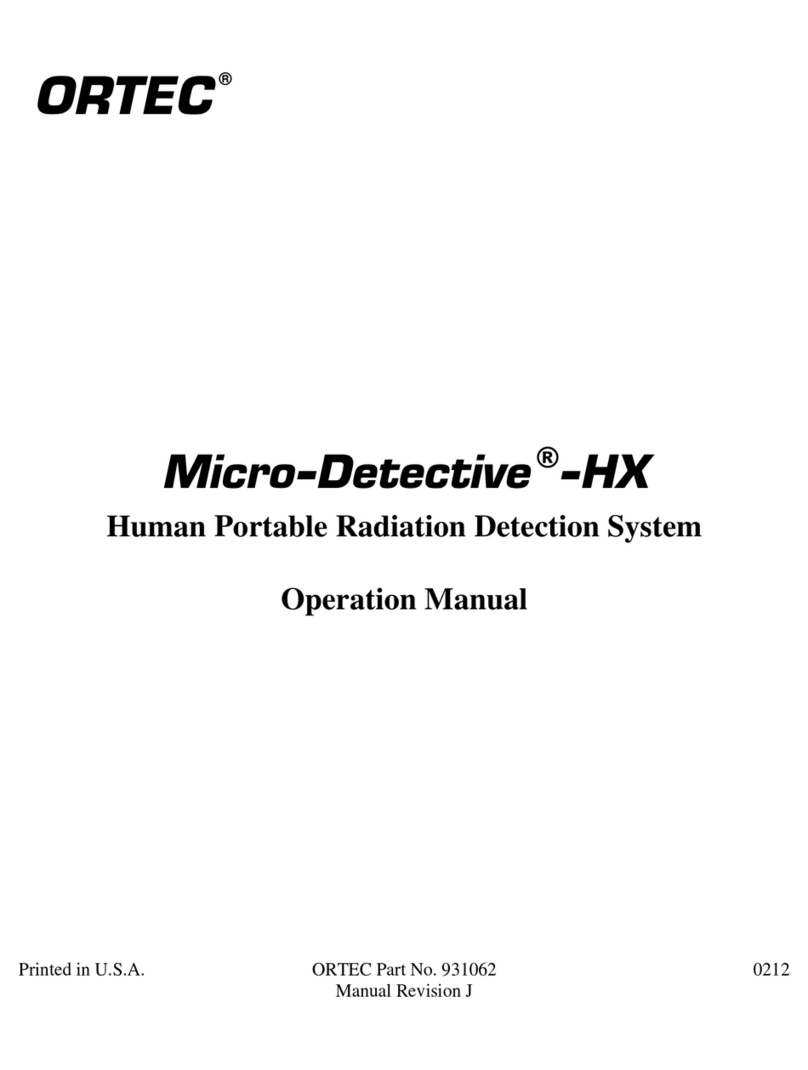
ORTEC
ORTEC Micro-Detective-HX User manual
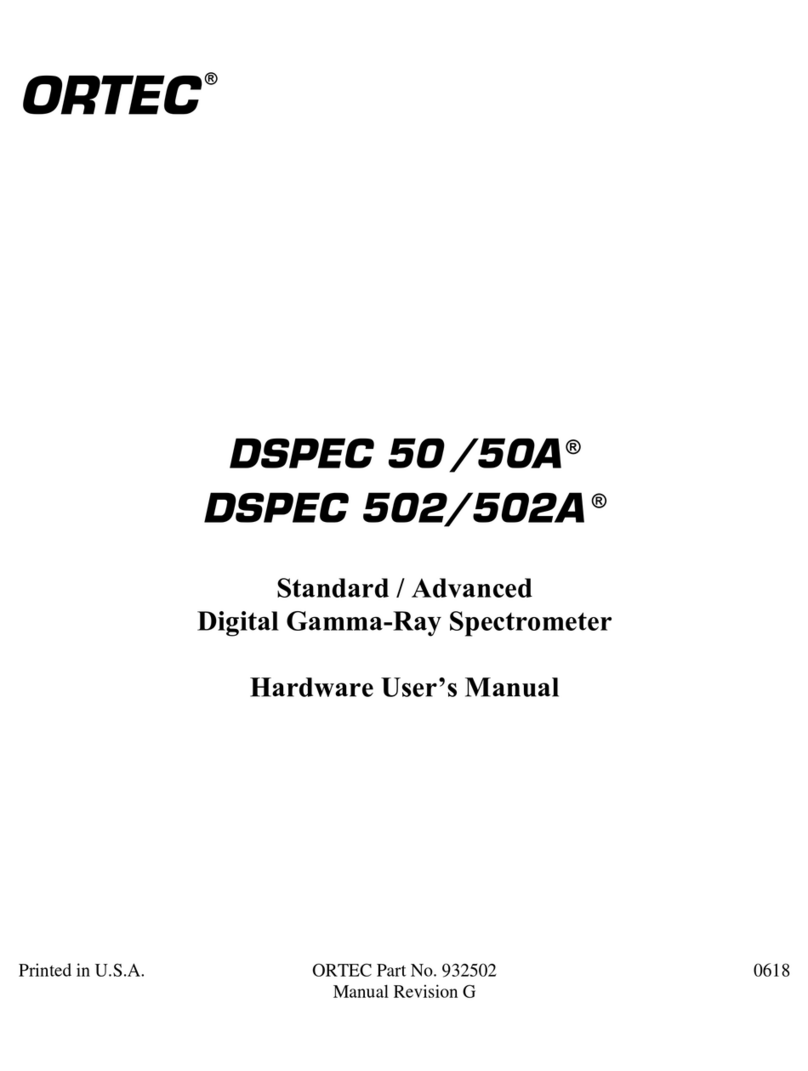
ORTEC
ORTEC DSPEC 50 Instructions for use
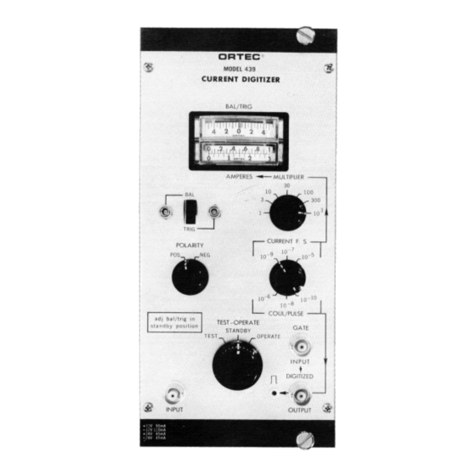
ORTEC
ORTEC 439 User manual
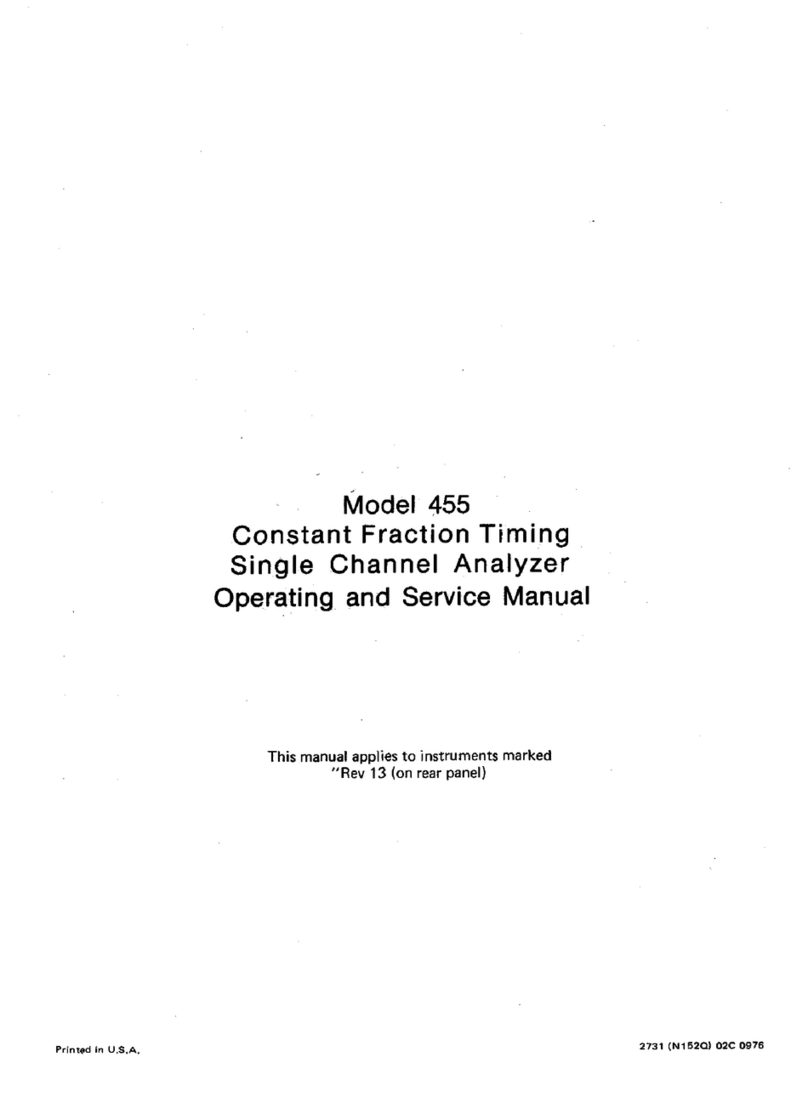
ORTEC
ORTEC 455 User manual

ORTEC
ORTEC 935 Service manual
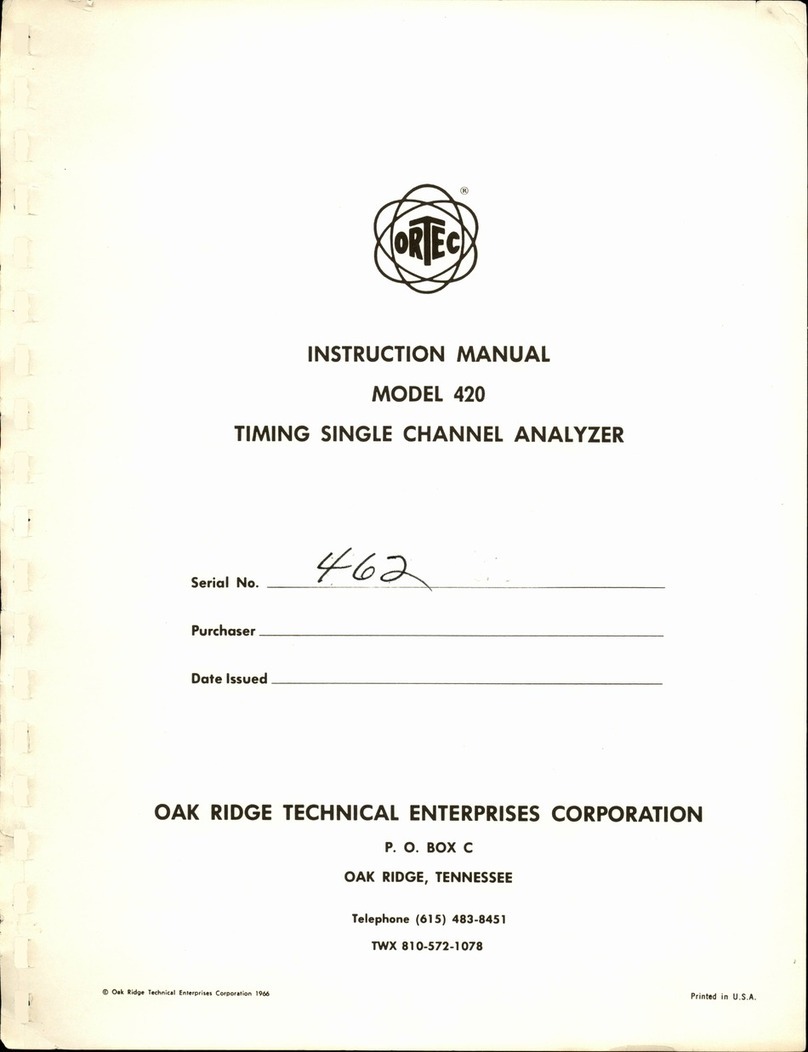
ORTEC
ORTEC 420 User manual
Popular Measuring Instrument manuals by other brands
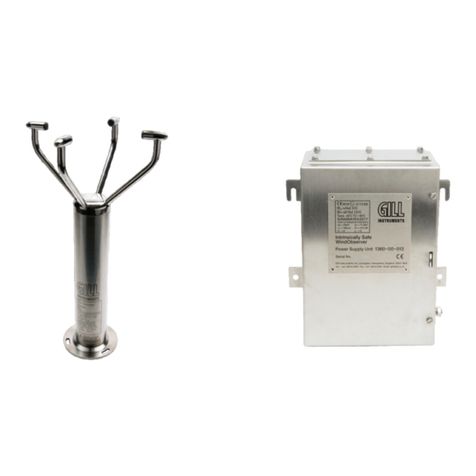
Gill Instruments
Gill Instruments 1360-PK-022 user manual
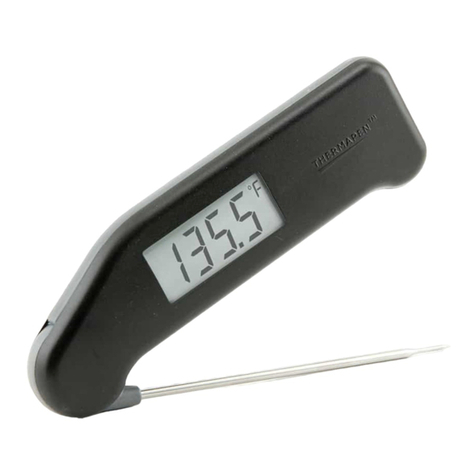
ThermoWorks
ThermoWorks Classic Thermapen operating instructions
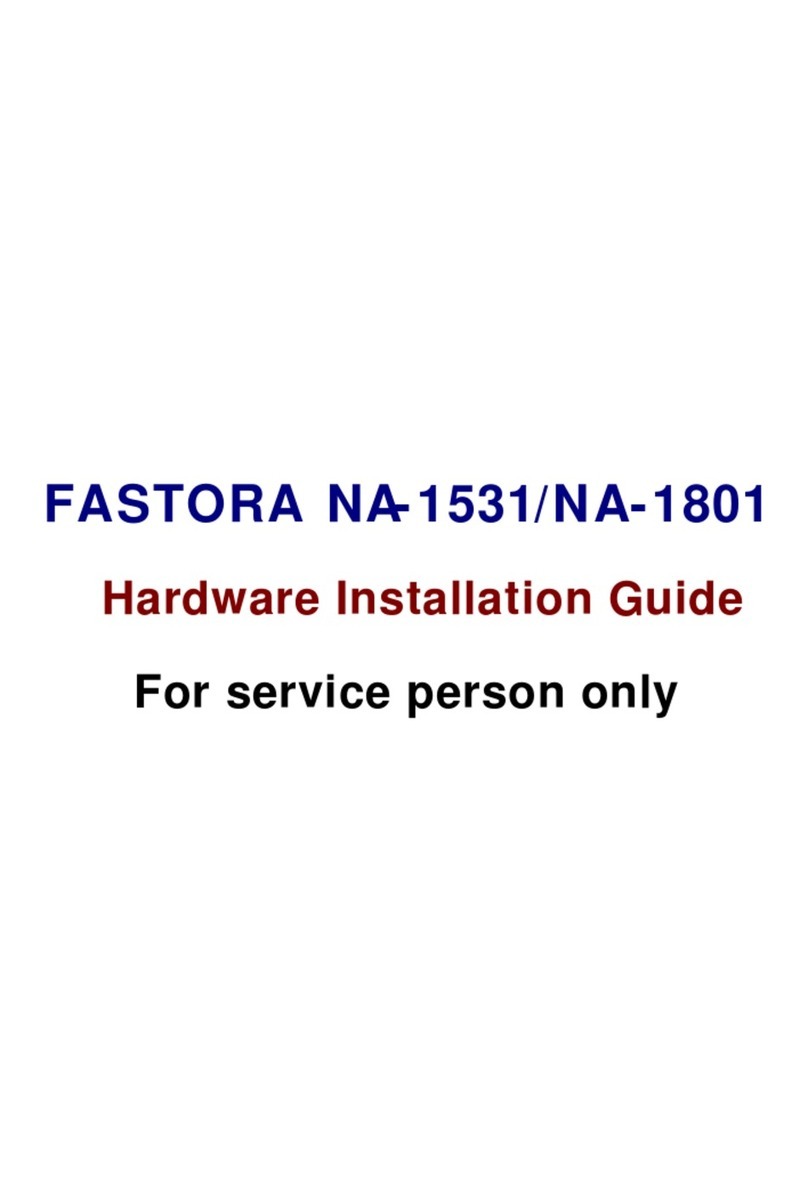
Fastora
Fastora NA-1531 Hardware installation guide
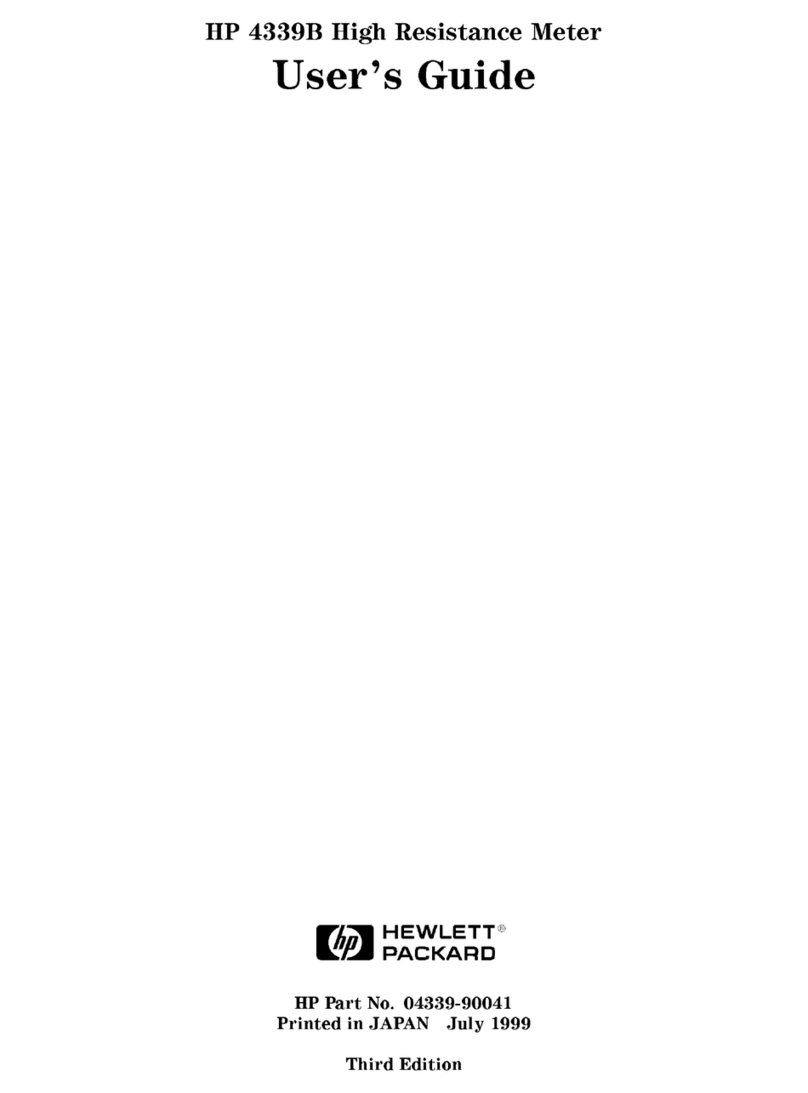
Helwett Packard
Helwett Packard 4339B user guide
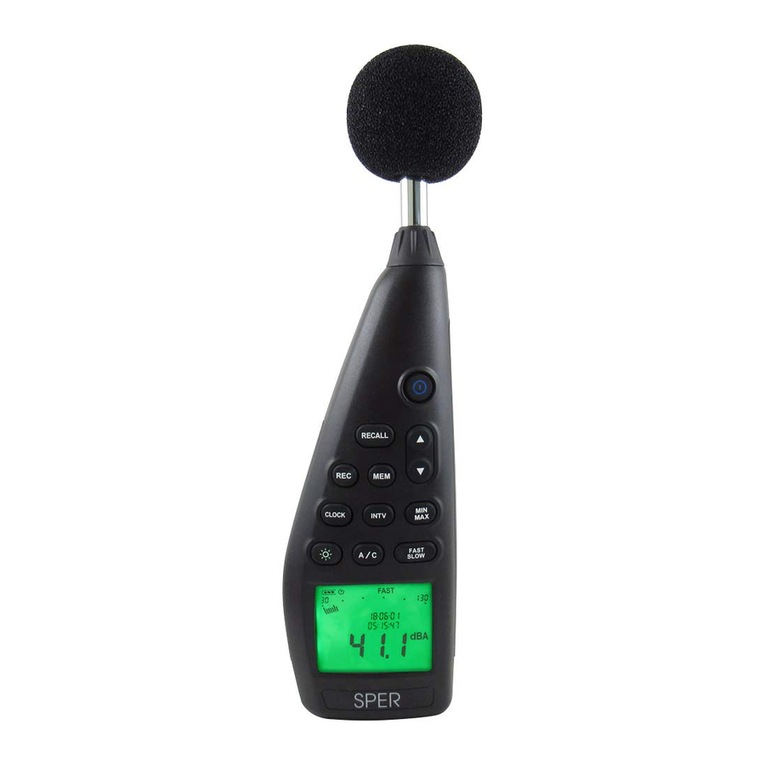
Sper scientific
Sper scientific 850013 instruction manual
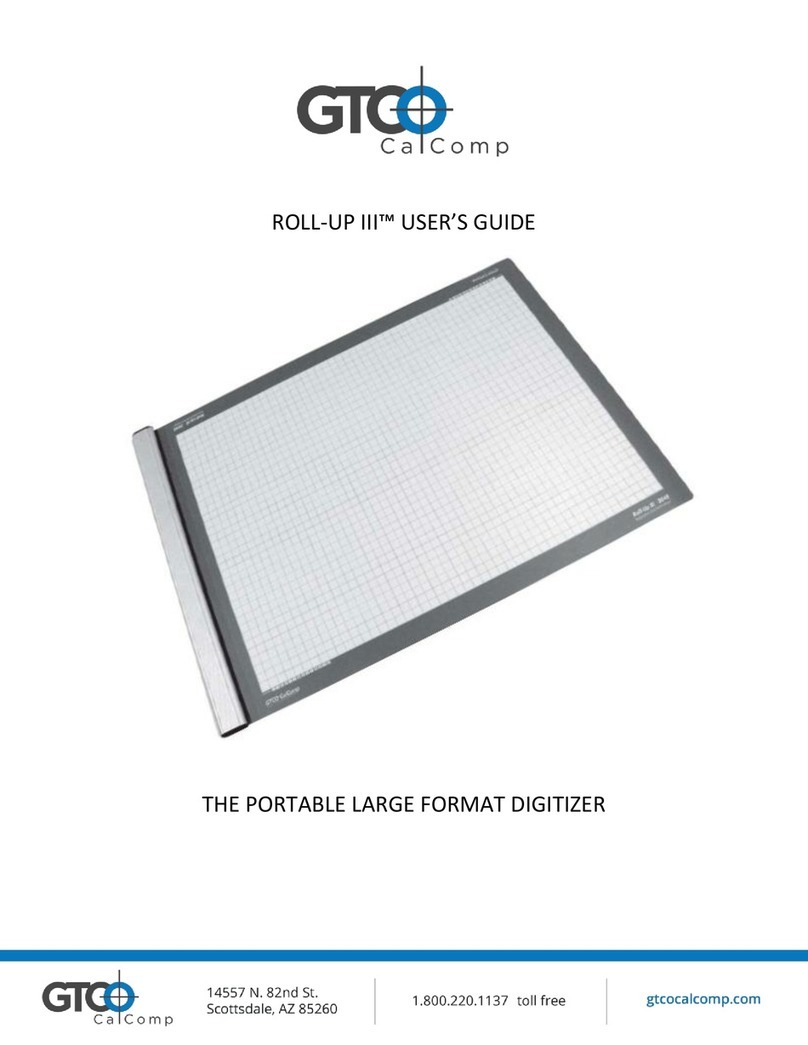
GTCO CalComp
GTCO CalComp Roll-Up III user guide