ORTEC 420 User manual

INSTRUCTION
MANUAL
MODEL
420
TIMING
SINGLE
CHANNEL
ANALYZER
Serial
No.
Purchaser.
Date
Issued
OAK
RIDGE
TECHNICAL
ENTERPRISES
CORPORATION
p.
O.
BOX
C
OAK
RIDGE,
TENNESSEE
Telephone
(615)
483-8451
TWX
810-572-1078
)
Osk
Ridge
Technical
Enterprises
Corporation
1966
Printed
In
U.S.A.

TABLE
OF
CONTENTS
Page
WARRANTY
PHOTOGRAPH
FORWARD:
Introduction
To
Fast
Timing
With
Linear
Signals
1
.
DESCRIPTION
1-1
2.
SPECIFICATIONS
2-1
3.
INSTALLATION
INSTRUCTIONS
3-1
3.1
General
3-1
3.2
Connection
To
Power
-
Nuclear
Standard
Bin,
ORTEC
Model
3-1
401/402
3.3
Connection
To
A
Linear
Amplifier
3-1
3.4
Linear
Output
Signal
Connections
And
Terminating
Impedance
3-2
Considerations
4.
OPERATING
INSTRUCTIONS
4-1
4.1
Front
Panel
Control
Functions
4-1
4.2
Initial
Testing
And
Observation
Of
Waveforms
4-2
4.3
Connector
Data
4-3
4.4
Typical
Operating
Conditions
4-3
5.
CIRCUIT
DESCRIPTION
5-1
6.
MAINTENANCE
INSTRUCTIONS
6-1
6.1
Testing
Performance
6-1
6.2
Calibration
Adjustment
6-3
6.3
Troubleshooting
Suggestions
6-3
6.4
Tabulated
Test
Point
Voltages
on
Etched
Boards
6-3

STANDARD
WARRANTY
FOR
ORTEC
ELECTRONIC
INSTRUMENTS
DAMAGE
IN
TRANSIT
Shipments
should
be
examined
immediately
upon
receipt
for
evidence
of
external
or
con
cealed
damage.
The
carrier
making
delivery
should
be
notified
immediately
of
any
such
damage,
since
the
carrier
is
normally
liable
for
damage
in
shipment.
Packing
materials,
waybills,
and
other
such
documentation
should
be
preserved
in
order
to
establish
claims.
After
such
notification
to
the
carrier,
notify
ORTEC
of
the
circumstances
so
that
we
may
assist
in
damage
claims
and
in
providing
replacement
equipment
when
necessary.
WARRANTY
ORTEC
warrants
its
electronic
products
to
be
free
from
defects
in
workmanship
and
materials,
other
than
vacuum
tubes
and
semiconductors,
for
a
period
of
twelve
months
from
date
of
ship
ment,
provided
that
the
equipment
has
been
used
in
a
proper
manner
and
not
subjected
to
abuse.
Repairs
or
replacement,
at
ORTEC
option,
will
be
made
without
charge
at
the
ORTEC
factory.
Shipping
expense
will
be
to
the
account
of
the
customer
except
in
cases
of
defects
discovered
upon
initial
operation.
Warranties
of
vacuum
tubes
and
semiconductors,
as
made
by
their
manufacturers,
will
be
extended
to
our
customers
only
to
the
extent
of
the
manufacturers'
liability
to
ORTEC.
Specially
selected
vacuum
tubes
or
semiconductors
cannot
be
warranted.
ORTEC
reserves
the
right
to
modify
the
design
of
its
products
without
incurring
responsibility
for
modification
of
previously
manufactured
units.
Since
instal
lation
conditions
are
beyond
our
control,
ORTEC
does
not
assume
any
risks
or
liabilities
associated
with
the
methods
of
installation,
or
installation
results.
QUALITY
CONTROL
Before
being
approved
for
shipment,
each
ORTEC
instrument
must
pass
a
stringent
set
of
quality
control
tests
designed
to
expose
any
flaws
in
materials
or
workmanship.
Permanent
records
of
these
tests
are
maintained
for
use
in
warranty
repair
and
as
a
source
of
statistical
information
for
design
improvements.
REPAIR
SERVICE
ORTEC
instruments
not
in
warranty
may
be
returned
to
the
factory
for
repairs
or
checkout
at
modest
expense
to
the
customer.
Standard
procedure
requires
that
returned
instruments
pass
the
same
quality
control
tests
as
those
used
for
new
production
instruments.
Please
contact
the
factory
for
instructions
before
shipping
equipment.

I
'4^
ortec*
MODEL
420
TIMING
SINGLE
CHANNEL
ANALYZER
"E"
DISC
0-1
DELAY
DIFF.
WALK
BIPOLAR
4:
-0,
INT.
Adj.
UNIPOLAR
■■
NEG.
INPUT
IT
n
POS.
OUTPUT
Model
420
Timing
Single
Channel
Analyzer

MODEL
420
TIMING
SINGLE
CHANNEL
ANALYZER
Foreword
Introduction
to
Fast
Timing
With
Linear
Signals
Precise
determination
of
the
time
of
occurrence
of
nuclear
events
is
often
compli
cated.
Detection
of
these
events
usually
results
in
a
voltage
pulse
whose
amplitude
is
a
function
of
the
energy
loss
in
the
detector,
and
whose
rise
time
is
a
function
of
the
conversion
process
from
detector
energy
to
charge.
When
time
determination
is
derived
from
the
leading
edge
of
such
a
pulse
(by
means
of
a
discriminator,
e.g., a
Schmitt
trigger),
there
is
a
time
shift
of
the
discriminator
output
that
depends
on
the
pulse
rise
time
and
the
range
of
pulse
amplitudes
involved.
(See
Figure
1(a).)
The
rise
time
of
these
pulses
is
usual
ly
limited
by
the
linear
amplifier
which
is
necessary
for
pulse
height
analysis;
such
amplifiers
are
the
Models
410,
and
the
older
versions
OS
the
Model
203,
A-8
and
DD2,
etc.
For
those
amplifiers
which
have
variable
RC
shaping,
e.g.,
the
Model
410,
the
rise
time
and
fall
time
will
vary
directly
with
the
integration
and
differentiation
time
constants
chosen;
therefore,
the
zero
crossing
time
will
vary
in
real
time.
The
time
of
zero
crossing
in
real
time
is
approximately
2
time
constants
after
the
detector
event
when
the
double
RC
differentiation
is
used.
Figure
1(b)
shows
a
series
of
idealized
output
pulses
from
a
double
delay
line
clipped
amplifier,
superimposed
upon
each
other.
All
of
the
pulses
pass
through
the
baseline
at
the
same
time;
this
is
true
because
in
the
amplifier
clipping
process,
the
voltage
which
is
forming
the
pulse
shape
goes
from
a
positive
value
(+E)
to
on
equal
negative
value
(—E)
in
the
same
time
that
wasrequired
forthe
voltage
to
go
from
0
to
+E,
i.e.,
one
rise
time.
The
pulses,
therefore,
pass
through
the
baseline
(zero
volts)at
a
time
Tr
r
-01
DISC.
TRIGGER
LEVEL
Tr/i
—
DISC.
TRIGGER
LEVEL
DISC.
\i,
OUTPUTS
h
J
TIME
SHIFT
WITH
LEADING
EDGE
TRIGGER
(6)
TIME
SHIFT
WITH
CROSSOVER
PICKOFF
Figure
1.
Timing
From
Linear
Amplifier
Output
Pulses

t
1-1
corresponding
to
1/2,
but
displaced
along
the
time
axis
by
the
one
clipping
time,'".
Thus,
it
is
evident
that
the
time
1/2
corresponds
to
the
point
at
which
the
pulses
attain
half-height.
Since
in
linear
amplifiers
the
rise
time
is
constant
and
therefore
inde
pendent
of
pulse
height,
the
time
at
which
the
pulses
reach
half-height
is
also
con
stant
and
independent
of
pulse
height.
The
discriminator
in
the
Model
420
is
designed
to
trigger
on
the
leading
edge
of
the
pulse,
at
a
selected
voltage,
and
is
forced
to
reset
when
the
pulse
passes
through
zero
volts.
The
discriminator
output
pulse
is
then
differ
entiated,
and
the
reset
edge
is
used
to
furnish
an
output
pulse
that
is
relatively
jitter-free
for
timing.
Time
resolution
in
the
order
of
5
to
10
nanoseconds
independent
of
discrimi
nator
level
is
typical
for
this
circuit.
1.
DESCRIPTION
The
Model
420
Timing
Single
Channel
Analyzer,
as
indicated
by
its
title,
performs
two
functions.
First,
it
is
a
single
channel
analyzer,
with,both
the
lower
level
and
the
window
width
variable
over
the
pulse
height
range.
For
input
signals
which
are
doubly
differ
entiated,
it
furnishes
an
output
which
occurs
at
the
time
these
signals
go
through
zero.
This
time,
as
explained
in
the
preceding
introduction,
is
a
precisely
known
time
and
there
fore
the
output
time
from
the
Model
420
is
a
precise
time.
The
unit
will
accept
single
or
double
delay
line
differentiated
signals
or
single
or
double
RC
differentiated
signals
with
pulse
widths
from
200
nanoseconds
to
20
microseconds.
When
the
unit
is
fed
a
unipolar
pulse,
the
crossover
time
is
not
fixed
in
time
and
therefore
the
input
selector
switch
should
be
set
to
the
unipolar
position.
This
will
cause
the
discriminator
to
reset
at
the
same
pulse
height
at
which
it
was
triggered,
and
therefore
the
time
of
output
pulse
will
depend
upon
the
fall
time
of
the
signal
input.
The
unit
is
provided
with
a
variable
delay,
selectable
by
a
front
panel
control,
of
approximately
1000
nanoseconds
to
allow
time
balance
in
coincidence
circuitry
and
analyzer
gating.
The
unit
provides
two
outputs
whose
leading
edges
contain
the
same
timing
information.
One
is
a
negative
spike
used
for
very
fast
timing
such
as
time
to
pulse
height
converters,
etc.,
and
the
other
is
a
positive
5-volt,
500-nanosecond-wide
pulse
for
slower
applications
such
as
coincidence
circuits
and
analyzer
gating.
These
output
pulses
are
the
two
standard
forms
of
logic
pulses
in
the
ORTEC
400
Series
modular
instruments,
and
are
compatible
with
all
related
input
signal
requirements.

2-1
2.
SPECIFICATIONS
INPUT
SIGNAL
REQUIREMENTS:
Amplitude
Range
100
mV
to
10
V
Pulse
Width
Range
200
nsec
to
20
(xsec
Polarity
Positive
(Unipolar)
or
Positive
Portion
leading
(Bipolar)
CONTROLS:
Lower
Level
("E")
100
mV
to
10
V,
10-turn
control
Window
Width
("AE")
100
mV
to
10
V,
10-turn
control
Delay
0
to
1000
nsec,
10-turn
control
DiflFerentiol-integrol
Mode
Switch,
integral
position
disables
"AE"
Discriminator
Unipolar-Bipolar
Mode
Switch
LINEARITY
(as
percent
of
full
span):
"E"
<±0.25%
"AE"
<±0.25%
Delay
<
±
2
%
TEMPERATURE
STABILITY
(as
percent
of
full
span):
"E"
."
..
.<
±
0.015%/C°
"AE"
<±0.015%/C°
Delay
<
±
0.4
nsec/C°
TIME
SHIFT
VS.
PULSE
HEIGHT*
<
±2
nsec
for
a
factor
of
(XI0)
or
±
10
nsec
for
(X50)
*Specified
withiORTEC
Model
410
Amplifier,
Double-Delay-Line
Mode,
Integrate
0.2
/xsec
OUTPUT
SIGNALS
Both
occur
simultaneously
and
may
be
delayed
0
to
1.0
/xsec
by
means
of
a
10-turn
DELAY
control
Fast
Negative,
0.6
V
(min),
T,.
<
5
nsec.
Width
<
20
nsec
Slow
Positive,
5
V,
Tr
<
20
nsec.
Width
~
500
nsec
POWER
REQUIRED
30
mA
at
+
24
V,
30
mA
at
—
24
V
50
mA
at
+
1
2
V,
40
mA
at
—1
2
V
WEIGHT
~
2.5
pounds
net
SIZE
Standard
double
width
module
(2.70
inches
wide)
per
TID-20893
_J

3-1
3.
INSTALLATION
INSTRUCTIONS
3.1
General
Model
420,
used
in
conjunction
with
Model
401/402
Bin
and
Power
Supply,
is
intended
for
rock
mounting,
and
therefore
it
is
necessary
to
ensure
that
vacuum
tube
equipment
operating
in
the
some
rock
has
sufficient
cooling
air
circulating
to
prevent
any
localized
heating
of
the
all-transistor
circuitry
used
throughout
the
Model
420.
The
temperature
of
equipment
mounted
in
racks
can
easily
exceed
the
recommended
maximum
unless
precautions
are
taken;
Model
420
should
not
be
subjected
to
temperatures
in
excess
of
120''F
(50°
C).
^
3.2
Connecton
to
Power—Nuclear
Standard.Bin,
ORTEC
Model
401/402
Model
420
contains
no
internal
power
supply,
and
therefore
must
obtain
power
f
from
a
Nuclear
Standard
Bin
and
Power
Supply
such
as
ORTEC
Model
401/402.
I
It
is
recommended
that
the
Bin
power
supply
be
turned
off
when
inserting
or
'
removing
modules.
The
ORTEC
400
Series
is
designed
so
that
it
is
not
possible
to
overload
the
Bin
power
supply
with
a
full
complement
of
modules
in
the
Bin;
however,
this
may
not
be
true
when
the
Bin
contains
modules
other
than
those
of
ORTEC
design.
In
this
case,
power
supply
voltages
should
be
checked
after
the
'
insertion
of
modules.
Model
401
/402
has
test
points
on
the
power
supply
control
panel
to
monitor
the
dc
voltages.
3.3
Connection
to
a
Linear
Amplifier
The
input
to
the
Model
420
is
via
a
front
panel
BNC
connector
and
is
compatible
with
all
linear
amplifiers
capable
of
producing
10-volt
unipolar
or
bipolar
output
signals
onto
a
2000-ohm
load,
with
the
positive
excursion
of
a
bipolar
signal
leading
the
negative
excursion
in
real
time.
The
input
operating
range
is
from
threshold,
typically
100
millivolts,
to
10
volts,
This
unit
may
be
used
with
vacuum
tube
amplifiers
which
are
capable
of
output
signals
of
100
volts,
if
the
output
signal
from
the
amplifier
is
attentuated
so
that
it
cannot
exceed
10
volts.
Simple
resistive
attenuators
installed
in
the
vacuum
tube
amplifiers
will
make
them
com
patible
with
related
transistor
equipment.

3-2
3.4
Linear
Output
Signal
Connections
and
Terminating
impedance
Considerations
The
source
impedance
of
the
0-10
volt
standard
linear
outputs
of
most
400
Series
modules
is
approximately
1
ohm.
Interconnection
of
linear
signals
is,
thus,
non-critical
since
the
input
impedance
of
circuits
to
be
driven
is
not
important
in
determining
the
actual
signal
span,
e.g.,
0-10
volts,
de
livered
to
the
fol
lowing
circuit.
Paralleling
several
loads
on
a
single
out
put
is
therefore
permissible
while
preserving
the
0-10
volt
signal
span.
Short
lengths
of
interconnecting
coaxial
cable
(up
to
approximately
4
feet)
need
not
be
terminated.
However,
if
a
cable
longer
than
approximately
4
feet
is
necessary
on
a
linear
output,
it
should
be
terminated
in
a
resistive
load
equal
to
the
cable
impedance.
Since
the
output
impedance
is
not
purely
resistive,
and
is
slightly
different
for
each
individual
module,
when
a
certain
given
length
of
coaxial
cable
is
connected
and
is
not
terminated
in
the
characteristic
impedance
of
the
cable,
oscil
lations
wil
l
generally
be
observed.
These
oscillations
can
be
suppressed
for
any
length
of
cable
by
properly
terminating
the
cable
either
in
series
at
the
sending
end
or
in
shunt
at
the
receiving
end
of
the
line.
To
properly
terminate
the
cable
at
the
receiving
end,
it
maybe
necessary
to
consider
the
input
impedance
of
the
driven
circuit,
choosing
on
additional
paral
lel
resistor
to
make
the
combination
produce
the
desired
termination
resistance.
Series
terminating
the
cable
at
the
sending
end
may
be
preferable
in
some
coses
where
re
ceiving
and
terminating
is
notdesirable
or
possible.
When
series
terminat
ing
at
the
sending
end,
ful
l
signal
span,
i.e.,
amplitude,
isobtainedat
the
receiving
end
only
when
it
is
essential
ly
unloaded
or
loaded
with
an
impedance
many
times
that
of
the
cable.
This
may
be
accomplished
by
inserting
a
series
resistor
equal
to
the
characteristic
impedance
of
the
ca
ble
internally
in
the
module
between
the
actual
ampiifier
output
on
the
etched
board
and
the
output
connector.
It
must
be
remembered
that
this
impedance
is
in
series
with
the
input
impedance
of
the
load
being
driven,
and
in
the
case
where
the
driven
load
is
900
ohms,
a
decrease
in
the
signal
span
of
approximately
10%
will
occur
for
a
93-ohm
transmission
line.
A
more
serious
loss
occurs
when
the
driven
load
is
93ohms
and
the
transmis
sion
system
is
93
ohms.
In
this
case,
a50%
loss
will
occur.
BNC
connec
tors
with
internal
terminators
are
available
from
a
number
of
connector
manufacturers
in
nominal
values
of
50,
100,
and
lOOOohms.
ORTEC
stocks
in
limited
quantity
both
the
50
and
100
ohm
BNC
terminators.
The
BNC
terminators
are
quite
convenient
to
use
in
conjunction
with
a
BNC
tee.

4-1
4.
OPERATING
INSTRUCTIONS
4.1
Front
Panel
Control
Functions
"E"
DISC.
The
function
of
the
"E"
(or
energy)
discriminator
is
the
some
as
with
any
discrimi
nator,
i.e.,
to
prevent
discriminator
triggering
by
those
signals
which
are
below
the
selected
threshold.
The
threshold
range
of
this
discriminator
is
from
approxi
mately
100
millivolts
to
10
volts
direct
reading
on
the
dial.
"AE"
DISC.
The
"AE"
discriminator
forms
the
upper
level
of
the
single
channel
analyzer.
The
dial
of
this
discriminator
reads
the
difference
in
voltage
or
energy
between
the
"E"
discriminator
and
the
upper
level;
therefore,
it
reads
"AE."
Since
this
forms
the
upper
level
of
the
single
channel
analyzer,
the
output
from
this
discriminator
is
placed
in
anticoincidence
with
an
output
from
the
lower
level
or
"E"
discrimi
nator
so
that
when
triggered,
there
is
no
output.
Therefore,
to
obtain
an
output
from
this
unit
a
signal
must
be
bigger
than
the
"E"
setting
but
less
than
"E"
+
"AE."
(When
the
Differential/Integral
(DIFF./INT.)
switch
is
set
to
the
INT
position,
the
"AE"
function
is
disabled,
and
the
unit
becomes
an
integral
dis
criminator
which
is
controlled
by
the
"E"
dial.)
Delay
Control
When
the
bipolar
signal
passes
from
a
positive
to
a
negative
value,
or
when
the
unipolar
signal
recrosses
the
"E"
discriminator
setting
(depending
upon
the
selec
tion
of
unipolar
or
bipolar
operation
by
means
of
switch
SI),
a
logic
signal
to
be
used
for
timing
or
counting
operation
is
generated.
The
delay
control
allows
the
output
logic
signal
to
be
delayed
in
time
from
this
reference
time,
to+
a
constant
propagation
delay,
over
a
range
of
0
to
1000
nanoseconds.
This
delay
is
con
tinuously
variable
by
means
of
a
10-turn
potentiometer.
UNIPOLAR/BIPOLAR
Switch
(SI)
Switch
SI
selects
the
mode
of
operation
of
the
timing
unit,
and
should
be
set
to
correspond
to
unipolar
or
bipolar
signals
at
the
input;
i.e.,
if
the
input
signal
is
a
singly
differentiated
pulse
this
switch
should
be
in
the
UNIPOLAR
position,
and
if
the
input
signal
is
a
bipolar
signal
the
switch
should
be
in
the
BIPOLAR
posi
tion.
Precise
timing
is
available
only
when
the
signal
is
a
bipolar
signal.

4-2
DIFF./INT.
Switch
(32)
Switch
52
determines
whether
the
unit
shall
be
on
integral
timing
discriminator
or
o
timing
single
channel
analyzer.
When
this
switch
is
in
the
DIFF.
position
all
signals
which
trigger
the
AE
discriminator
will
prevent
the
logic
signal
created
by
the
timing
discriminator
from
reaching
the
output,
and
therefore
there
will
be
no
output
from
the
unit.
When
the
switch
is
in
the
INT.
position,
the
AE
discriminator
is
disabled,
and
all
signals
which
exceed
the
lower
level
threshold
will
create
an
output
signal.
WALK
Adj.
Due
to
minor
circuit
differences,
various
amplifiers
will
have
a
true
crossover
at
different
values
of
voltage,
but
very
near
zero.
For
this
reason,
a
WALK
adjust
ment
is
provided
on
the
front
panel.
This
is
a
screwdriver
adjustment
and
is
adjusted
to
an
optimum
value
with
a
Model
410
Amplifier
before
the
unit
leaves
the
factory.
For
information
concerning
the
method
of
adjustment,
refer
to
"Cali
bration
Adjustment,"
Section
6.1
of
this
manual.
4.2
Initial
Testing
and
Observation
of
Waveforms
Refer
to
Section
6.1
for
information
on
testing
performance
and
observing
wave
forms.
4.3
Connector
Data
CN1
—
INPUT
(BNC)
Connector
CN1
has
input
impedance
of
2000
ohms,
oc-coupled,
and
a
maximum
input
of
10
volts.
To
minimize
reflections
when
driving
into
CNl
from
a
low
impedance
voltage
source
such
as
the
output
of
the
Model
410,
etc.,
CNl
should
be
extern
ally
terminated
in
the
characteristic
impedance
of
the
connecting
coaxial
cable.
CN2—OUTPUT
NEG.
(BNC)
Connector
Output
driving
source
impedance
is
less
than
10
ohms.
The
signal
is
dc
coupled
starting
from
zero
volts;
it
is
the
standard
ORTEC
Fast
Negative
logic
signal
and
is
used
for
optimum
timing
resolution.
CN3
—OUTPUT
POS.
(BNC)
Connector
Output
driving
impedance
is
less
than
10
ohms.
The
signal
is
dc
coupled
starting
from
zero
volts;
it
is
the
standard
ORTEC
positive
logic
pulse
whose
application
is
normally
coincidence
timing
and
analyzer
gating.
OUTPUT
Test
Points
Oscilloscope
test
points
for
monitoring
output
signals
are
available
at
each
OUTPUT
BNC.
Each
test
point
has
a
470-ohm
series
resistor
connecting
it
to
the
respective
OUTPUT
BNC
connector.

4-3
4.4
Typical
Operating
Conditions
The
realization
of
both
optimum
timing
and
optimum
energy
resolution
are
mutu
ally
exclusive
when
using
the
crossover
pickofF
method
of
timing;
however,
a
satisfactory
compromise
of
timing
and
resolution
is
usually
not
difficult
to
obtain.
Optimum
timing
is
realized
with
wide
bandwidth
capabilities
in
the
linear
ampli
fier,
resulting
in
fast
rise
and
fall
times.
Optimum
energy
resolution
is
realized
with
narrow
bandwidth
so
that
the
bypass
of
the
noise
spectrum
can
be
selectively
chosen
at
a
particular
location
in
the
frequency
spectrum.
The
method
of
compromise
is
illustrated
with
reference
to
the
model
410
Amplifier
when
used
in
conjunction
with
the
Model
420
Timing
Single
Channel
Analyzer.
To
optimize
timing,
the
Model
410
would
be
operated:
1)
with
a
minimum
of
integration
and
double
delay
line
differentiation;
or
2)
in
the
double
RC
shaping
mode
with
the
integration
and
differentiation
time
constants
set
on
0.1
microsecond.
The
optimization
of
timing
would
be
at
the
expense
of
energy
resolution.
If
it
is
desired
to
optimize
the
energy
resolution,
the
Model
410
should
be
operated:
1)
with
an
integration
time
constant
of
1
or
2
microseconds
and
double
delay
line
differentiation;
or
2)
in
the
double
RC
shaping
mode
with
the
integration
and
differentiation
time
constants
set
at
1
or
2
microseconds.
In
the
latter
case,
it
is
observed
that
the
rate
of
change
of
voltage
when
the
linear
amplifier
output
crosses
through
zero
is
very
much
less
than
in
the
former
case.
With
the
lower
rote
of
change,
the
noise
modulation
of
the
linear
amplifier
output
signal
causes
a
larger
time
jitter
of
the
timing
output
signal.
In
the
former
cose,
the
rote
of
change
of
voltage
with
respect
to
time
is
quite
high
and
the
jitter
in
the
timing
output
due
to
linear
amplifier
noise
modulation
is
quite
small.
Jj^

5-1
5.
CIRCUIT
DESCRIPTION
(See
Drawings
420-0001-SI
and
420-0002A-B1.)
Resistors
R1
and
R5
form
a
resistive
voltage
divider
v/hich
divides
the
input
signal
from
a
maximum
of
10
volts
to
a
maximum
of
5
volts
at
the
base
of
Q1
and
Q9.
Q1
and
Q2
form
a
long-tail
pair
which
is
the
lower
level
discriminator.
Transistors
Q3
through
Q8
are
necessary
to
obtain
the
control
desired
on
the
hysteresis
of
the
circuit.
Q3
and
Q5
are
normally
on
in
the
absence
of
an
input
signal
and
hold
the
base
of
Q2
at
zero
volts.
When
on
input
signal
exceeds
the
threshold
level
set
by
the
"E"
discriminator,
R2,
the
trigger
pair,
Q1
and
Q2,
regenerates
and
triggers
another
trigger
pair
formed
of
Q7
and
Q8.
Q7
turns
on
and
Q8
turns
off.
When
Q8
turns
off,
this
allows
the
emitter
of
Q4
to
fall
toward
—12
volts
and
it
is
caught
at
—E.
When
the
emitter
of
Q4
and
base
of
Q6
fall
negative,
Q6
turns
on
and
Q5
turns
off,
which
sets
the
base
of
Q2
at
—E.
Since
the
base
of
Q1
has
a
baseline
voltage
equal
to
—E
and
the
base
of
Q2
has
a
baseline
voltage
of
-E
in
the
presence
of
the
signal,
the
trigger
pair
will
reset
when
the
signal
makes
the
transition
from
the
positive
condition
to
the
negative
condition,
i.e.,
zero
crossing
point.
The
signal
at
the
collector
of
Q7
is
differentiated
by
means
of
L3
and
is
fed
to
the
base
of
Q15.
The
negative
portion
of
the
signal
will
cause
Q15
to
conduct
if
the
upper
level
discriminator
has
not
been
triggered.
A
signal
from
the
collector
of
Q6
is
used
to
reset
the
upper
discriminator
when
it
has
been
triggered,
and
this
signal
is
fed
to
the
base
of
Q11.
R14,
the
zero
adjust
trimpot,
is
used
to
zero
the
"E"
pulse
height
dial.
The
adjust
ment
of
the
walk
adjust
potentiometer,
R6,
will
be
explained
in
Section
6.1.
Switch
SI
is
used
to
obtain
operation
in
either
bipolar
or
unipolar
mode.
In
the
bipolar
position,
tran
sistor
Q4
has
the
value
of
—E
imposed
on
its
base
at
all
times;
however,
in
the
unipolar
position
this
base
sees
a
constant
—75
mV
dc
voltage.
This
dc
voltage
is
the
amount
of
hysteresis
on
the
lower
level
discriminator
in
the
unipolar
mode.
The
upper
level
discriminator
is
formed
by
Q9
and
QIO.
The
output
from
QIO
is
differentiated
and
fed
to
the
base
of
Q12.
When
switch
S2
is
in
the
differential
position,
this
signal
is
sufficiently
large
to
trigger
the
multivibrator
composed
of
Q12
and
Q13.
If,
however,
52
is
in
the
integral
mode,
this
pulse
cannot
trigger
the
multivibrator
com
posed
of
Q12
and
Q13.
Once
this
multivibrator
is
triggered,
it
could
recover
with
an
RC
recovery
time
of
approximately
100
microseconds;
however,
it
is
reset
at
essentially
zero
crossing
time
by
means
of
the
reset
pulse
which
is
present
by
way
of
Q11.
Due
to
the
long
time
constant
involved
with
this
multivibrator,
this
circuit
con
handle
pulse
widths
which
are
very
wide,
e.g.,
20
microseconds.
An
output
from
Q13
will
cause
Q14
to
inhibit
any
signal
that
appears
at
the
base
of
Q15;
thus,
the
anticoincidence
function
is
performed
between
the
"AE"
discriminator
and
the
"E"
discriminator.
This
anticoincidence
function
assures
that
the
input
pulsie
must
be
within
the
selected
window
to
obtain
an
output.
Q16,Q17,Q18,
and
Q19
form
a
delay
generator.
The
delay
control,
R46,
will
vary
the
delay
of
the
output
logic
signal

5-2
over
a
range
of
approximately
1000
nanoseconds.
This
delay
should
be
quite
linear.
The
delay
generator
triggers
with
an
input
pulse
from
Q15
and
then
resets
when
the
signal
at
the
base
of
Q17
recovers
to
the
zero
voltage
level.
The
recovery
time
constant
is
set
by
capacitor
C19
and
the
constant
current
generator,
Q19.
The
pulse
from
the
col
lector
of
Q17
is
differentiated
and
the
negative
portion
is
fed
out
through
Q20
as
a
fast
output
signal.
An
inversion
of
this
some
signal
appears
at
the
collector
of
Q20
and
triggers
the
multivibrator
composed
of
Q21
and
Q22.
The
signal
from
the
collector
of
Q22
is
emitter-follower
buffered
to
the
output
as
a
positive
5-volt
signal,
0.5
micro
second
wide.
(
'■

6-1
6.
MAINTENANCE
INSTRUCTONS
6.1
Testing
Performance
6.1.1
Introduction
The
following
paragraphs
are
intended
as
an
aid
in
the
installation
and
checkout
of
the
Model
420.
These
instructions
present
information
on
front
panel
controls,
waveforms
and
test
points,
and
output
connectors.
6.1.2
Test
Equipment
The
following
or
equivalent
test
equipment
is
needed:
(1)
ORTEC
Model
419
Pulse
Generator
(2)
Tektronix
Model
545
Series
Oscilloscope
(3)
100-ohm
BNC
terminators
(4)
ORTEC
Model
410
Amplifier
(5)
Schematics
and
Block
Diagrams
for
the
Model
420
Timing
Single
Channel
Analyzer
6.1.3
Preliminary
Procedures
(1)
Visually
check
module
for
possible
damage
due
to
shipment.
(2)
Connect
ac
power
to
Nuclear
Standard
Bin,
e.g.,
ORTEC
Model
401/402.
(3)
Plug
module
into
Bin
and
check
for
proper
mechanical
alignment.
(4)
Switch
on
ac
power
and
check
the
dc
power
voltages
at
the
test
points
on
the
Model
401
Power
Supply
control
panel.
t
r
6.1.4
Testing
the
Single
Channel
Function
(1)
Connect
the
direct
output
of
the
pulse
generator
to
the
scope
trigger.
Connect
the
attenuated
output
of
the
pulse
generator
to
the
input
of
the
Model
410
Amplifier.
Place
all
attenuator
switches
on
the
pulse
I
generator
to
the
out
position
except
one
switch,
which
should
be
an
XI0
switch.
Set
the
Model
410
Amplifier
DIFFERENTIATION
control
to
double
delay
line.
Set
the
INTEGRATION
control
to
the
.1
fisec
posi-
i
tion.
Adjust
the
pulse
generator
output
and/or
amplifier
gain
control
to
achieve
an
amplifier
output
pulse
height
of
approximately
10
volts.
<
]
(2)
Connect
the
amplifier
output
to
the
single
channel
analyzer
input.
Set
the
Model
420
DIFF./INT.
switch
to
the
INT.
position,
and
set
the
BIPOLAR/UNIPOLAR
switch
to
the
BIPOLAR
position.
Adjust
the
"AE"
dial
to
read
500/1000
divisions.
There
should
now
be
on
output
from
both
fast
and
slow
outputs
of
the
single
channel
analyzer.
Turn
the
I
"E"
dial
to
read
1000,
then
adjust
the
pulse
height
dial
on
the
pulse

6-2
generator
so
that
the
single
channel
half-triggers.
Now
set
the
X2
attenuator
switch
on
the
pulse
generator.
The
single
channel
should
again
half-trigger
at
500
dial
divisions.
Next,
set
the
DIFF./INT.
switch
to
the
DIFF.
position,
and
turn
the
"E"
dial
to
400
divisions.
Turn
the
"AE"
dial
toward
zero
and
observe
when
the
single
channel
again
begins
to
half-trigger.
This
should
be
approximately
100
dial
divisions
on
the
"AE"
dial.
We
are
now
certain
that
the
single
channel
analyzer
is
operating
as
a
single
channel
in
the
bipolar
mode.
These
same
steps
may
be
repeated
for
the
unipolar
mode
if
desired,
and
other
points
on
the
pulse
height
vs
dial
curves
may
be
observed.
6.1.5
Testing
the
Timing
Function
(1)
It
is
assumed
for
this
test
that
the
steps
in
6.1.4
have
been
performed
and
that
switch
SI
is
in
the
BIPOLAR
position.
Connect
the
direct
output
of
the
pulse
generator
to
the
trigger
input
to
the
"B"
sweep
on
the
scope
and
set
the
scope
for
"A"
triggered
by
"B."
Obtain
such
trig
gering
of
the
"A"
sweep
that
the
delay
control
in
the
"B"
sweep
section
may
be
used.
(2)
Turn
the
DELAY
control
on
the
Model
420
to
0
and
observe
the
output
pulse
either
at
TP1
or
at
TP2,
then
adjust
the
scope
sweep
speed
and
"B"
sweep
delay
to
observe
the
leading
edge
of
this
pulse
with
a
sweep
speed
of
20
nanoseconds/cm
or
less.
Set
the
DIFF./INT.
switch
to
the
INT.
position
on
the
Model
420.
Set
the
pulse
generator
switches
as
described
in
Section
6.1.4,
step
(4).
Place
the
"E"
discriminator
at
10
divisions.
Attenuate
the
pulse
height
by
factors
of
2,
5,
and
10
by
means
of
the
attenuator
switches
on
the
pulse
generator,
and
observe
the
time
shift
of
the
output
pulse;
the
time
shift
should
be
less
than
4
nanoseconds
over
this
pulse
height
range.
It
may
be
necessary
to
trim
the
time
shift
by
means
of
the
WALK
Adj.
screwdriver
adjustment
(R69)
on
the
front
panel.
For
those
users
who
have
critical
dynamic
range
problems,
the
single
channel
may
be
checked
and
adjusted
to
achieve
less
than
±10
nanoseconds
time
shift
over
a
dynamic
range
of
50:1,
i.e.,
from
200
mV
to
10
volts.
Operation
with
this
wide
a
range
becomes
quite
critical
and
R69
may
have
to
be
slightly
readjusted
to
achieve
this
characteristic.
Of
course,
at
very
low
pulse
heights
the
amount
of
jitter
observed
will
be
large;
this
is
due
to
the
amplifier
noise
modulation
of
the
crossover
point.
(3)
Set
the
scope
sweep
speed
at
50
nanoseconds/cm.
Observe
the
out
put
signal
and
turn
the
DELAY
control
(R46)
through
its
range.
The
output
should
shift
approximately
1000
nanoseconds.

6-3
6.1.6
Timing
in
the
Unipolar
Mode
When
switch
SI
is
set
in
the
UNIPOLAR
position,
the
lower
level
discrimi
nator
is
forced
to
fire
and
reset
at
essentially
the
same
voltage;
thus,
the
time
of
the
output
pulse
will
vary
directly
with
the
signal
amplitude
and
fall
time
of
the
input
pulse.
This
means
that
timing
in
the
unipolar
mode
con
be
no
better
than
the
fall
of
the
pulse
times
the
proportion
of
the
dynamic
range
used.
6.2
Calibration
Adjustment
It
is
assumed
for
this
adjustment
that
all
the
steps
outlined
in
Section
6.1
have
been
completed.
To
force
the
lower
lever,
i.e.,
the
"E"
discriminator,
to
extrap
olate
to
zero,
on
adjustment
is
provided
on
the
printed
circuit
board.
To
perform
this
adjustment,
set
the
pulse
generator
controls
as
given
in
Section
6.1.4,
step
(3).
Set
the
Model
420
DIFF./INT.
switch
to
the
INT.
position.
Adjust
the
pulser
to
achieve
half-triggering
with
the
"E"
dial
placed
at
1000,
then,
adjust
the
pulse
height
dial
of
the
pulse
generator
to
100
and
set
the
Model
420
"E"
dial
to
100,
adjusting
the
zero
potentiometer
(R14)
to
achieve
half-triggering.
Other
points
at
lower
pulse
heights
may
be
checked
if
desired.
6.3
Troubleshooting
Suggestions
In
situations
where
the
Model
420
is
suspected
of
malfunction,
it
is
essential
to
verify
such
malfunction
in
terms
of
simple
pulse
generator
pulses
at
the
input
and
output.
For
this
reason,
the
Model
420
must
be
disconnected
from
its
position
in
any
system,
and
routine
diagnostic
analysis
performed
with
a
test
pulse
generator
and
oscilloscope.
It
is
imperative
that
testing
not
be
performed
with
a
source
and
detector
until
the
amplifier
and
single
channel
analyzer
system
perform
satisfac
torily
with
a
test
pulse
generator.
The
testing
instructions
in
Section
6.1
of
this
manual
and
the
circuit
descriptions
in
Section
5
should
provide
assistance
in
locating
the
region
of
trouble
and
repairing
the
malfunction.
The
guide
plate
and
shield
cover
may
be
completely
removed
from
the
module
to
enable
oscilloscope
and
voltmeter
observation
with
a
minimal
chance
of
accidentally
short-circuiting
portions
of
the
etched
board.
The
Model
420
may
be
returned
to
ORTEC
for
repair
service
at
nominal
cost;
our
standardized
procedure
requires
that
each
repaired
instrument
receive
the
same
extensive
quality
control
tests
that
a
new
instrument
receives.
6.4
Tabulated
Test
Point
Voltages
on
Etched
Boards
The
following
voltages
are
intended
to
indicate
typical
dc
voltages
measured
on
the
etched
circuit
board.
In
some
instances
the
circuit
will
perform
satisfactorily
even
though,
due
to
component
variations,
some
voltages
measure
outside
the
given
limits;
therefore,
the
voltages
given
here
should
not
be
taken
as
absolute
values,
but
rather
are
intended
to
serve
as
an
aid
in
troubleshooting.

6-4
Table
6.1
Typical
DC
Voltages
NOTES:
].
All
voltages
ore
measured
from
ground
with
vtvm
having
Impedance
of
10
megohms
or
greater.
2.
All
voltages
ore
dc
values
with
no
input
signals.
3.
Set
all
dials
to
read
ICQ
divisions.
4.
Set
DIFF./INT.
switch
to
DIFF.,
and
BIPOLAR/UNIPOLAR
switch
to
BIPOLAR.
Pin
No.
Location
Minimum
Maximum
A
+
24
bus
+
23.6
+
24.0
B
+
1
2
bus
+
11.5
+
12.0
C
-
12
bus
-
11.5
—
12.0
D
—
24
bus
—
23.6
—
24.0
E
Junction
of
R2
&
R3
—
4.9
-5.1
F
Junction
of
R30
&
R31
+
4.9
+
5.1
G
Ql-C
+
11.4
+
11.9
H
Q4-E
MM
7^/4
0
mm
V
1
Junction
of
R21
&
R22
-0.060 -0.080
J
Q9-C
+
11.3
+
11.8
K
Q12-C
+
11.3
+
11.8
L
Q15-C
0
0
M
Q16-C
+
11.3
+
11.8
N
Q19-B
+
1
7.2
+
18.2
O
Q21-C
0
0
P
Q22-C
+
0.37
+
0.50
Q
Q23-E
0 0
C
—
Collector
B
—
Base
E
—
Emitter

BIN/MODULE
CONNECTOR
PIN
ASSIGNMENTS
FOR
AEC
STANDARD
NUCLEAR
INSTRUMENT
MODULES
PER
TID-20893
Pin
Function
Pin
Function
1
+3
volts
23
Reserved
2
—3
volts
24
Reserved
3
Spare
Bus
25
Reserved
4
Reserved
Bus
26
Spare
5
Coaxial
27
Spare
6
Coaxial
*28
+24
volts
7
Coaxial
*29
—24
volts
8
200
volts
dc
30
Spare
Bus
9
Spore
31
Carry
No.
2
♦
10
+6
volts
32
Spare
*11
—6
volts
*33
115
volts
acC^®'")
12
Reserved
Bus
*34
Power
Return
Ground,
13
Carry
No.
1
35
Reset
14
Spare
36
Gate
15
Reserved
37
Spare
*16
+12
volts
38
Coaxial
*17
—12
volts
39
Coaxial
18
Spare
Bus
40
Coaxial
19
Reserved
Bus
*41
115
volts
ac(Neut.)
20
Spare
*42
High
Quality
Ground
21
Spare
G
Ground
Guide
Pin
22
Reserved
These
pins
are
installed
and
wired
in
parallel
in
the
ORTEC
Model
401
Modular
System
Bin.

The
transistor
types
instalted
in
your
instrument
may
differ
from
those
shown
in
the
schematic
diagram.
In
such
cases,
necessary
replace
ments
can
be
made
with
either
the
type
shown
in
the
diagram
or
the
type
actually
used
in
the
instrument.
Table of contents
Other ORTEC Measuring Instrument manuals
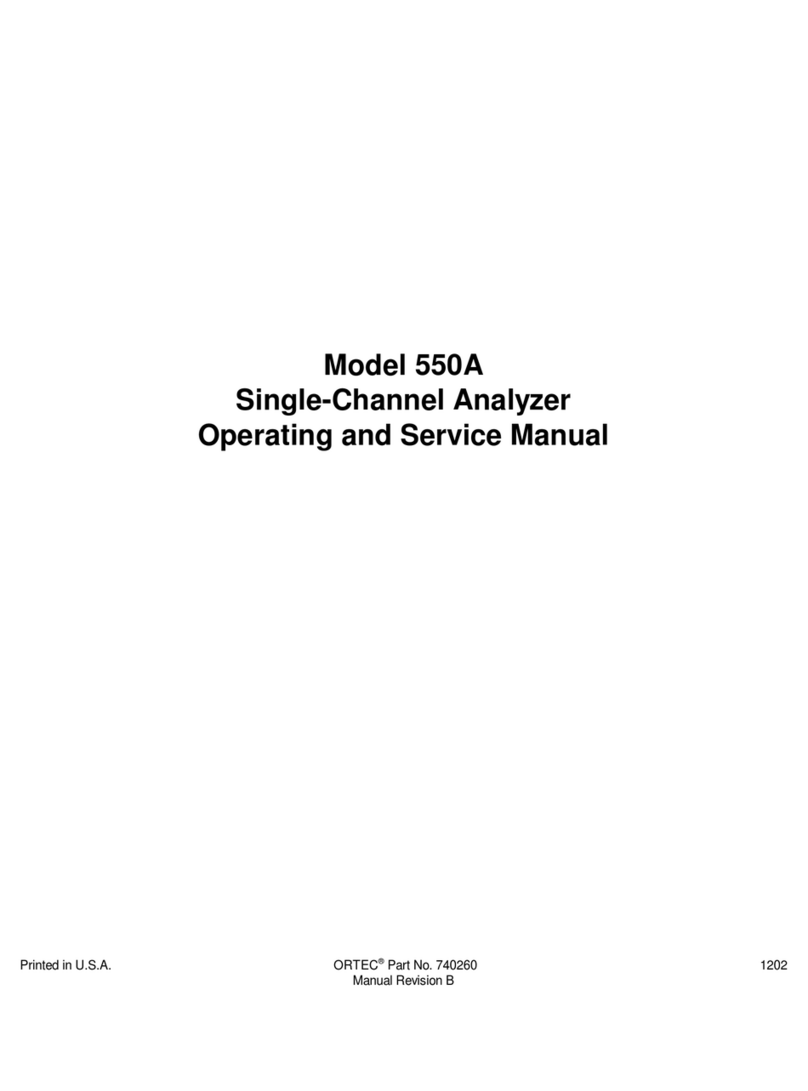
ORTEC
ORTEC 550A Service manual

ORTEC
ORTEC Fission Meter FM-P3 User manual
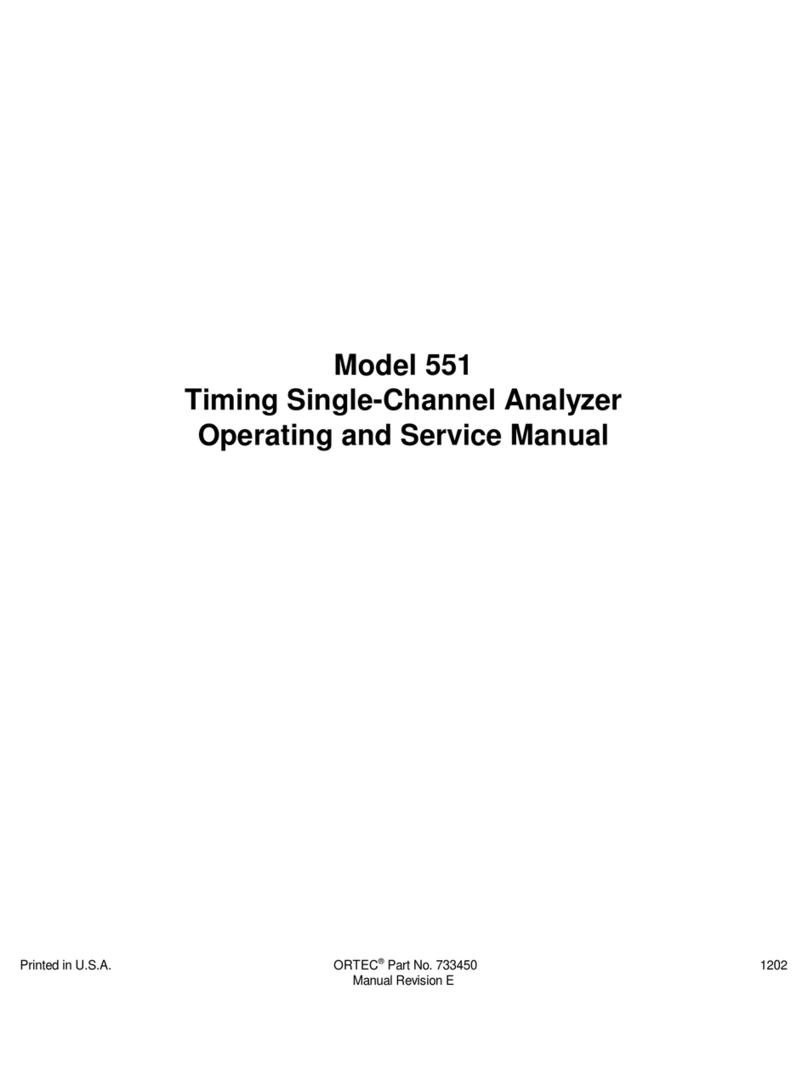
ORTEC
ORTEC 551 Service manual
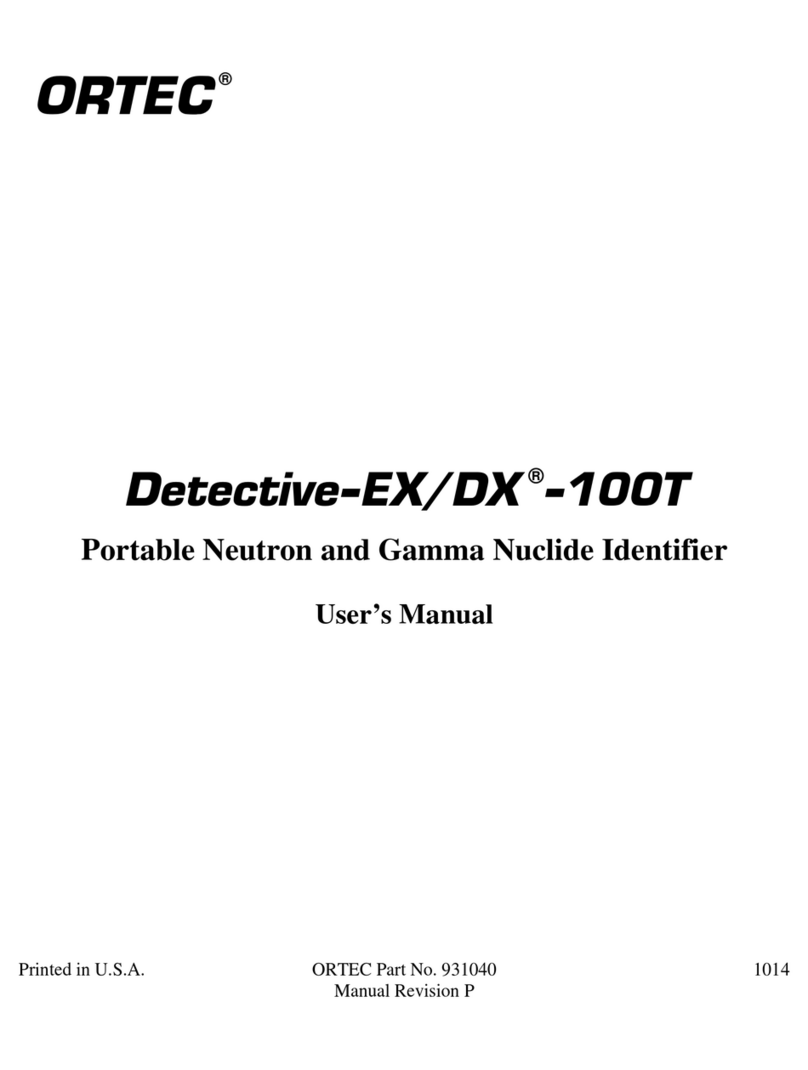
ORTEC
ORTEC Detective-EX-100T User manual

ORTEC
ORTEC EASY-MCA-8K User manual

ORTEC
ORTEC 418A Service manual
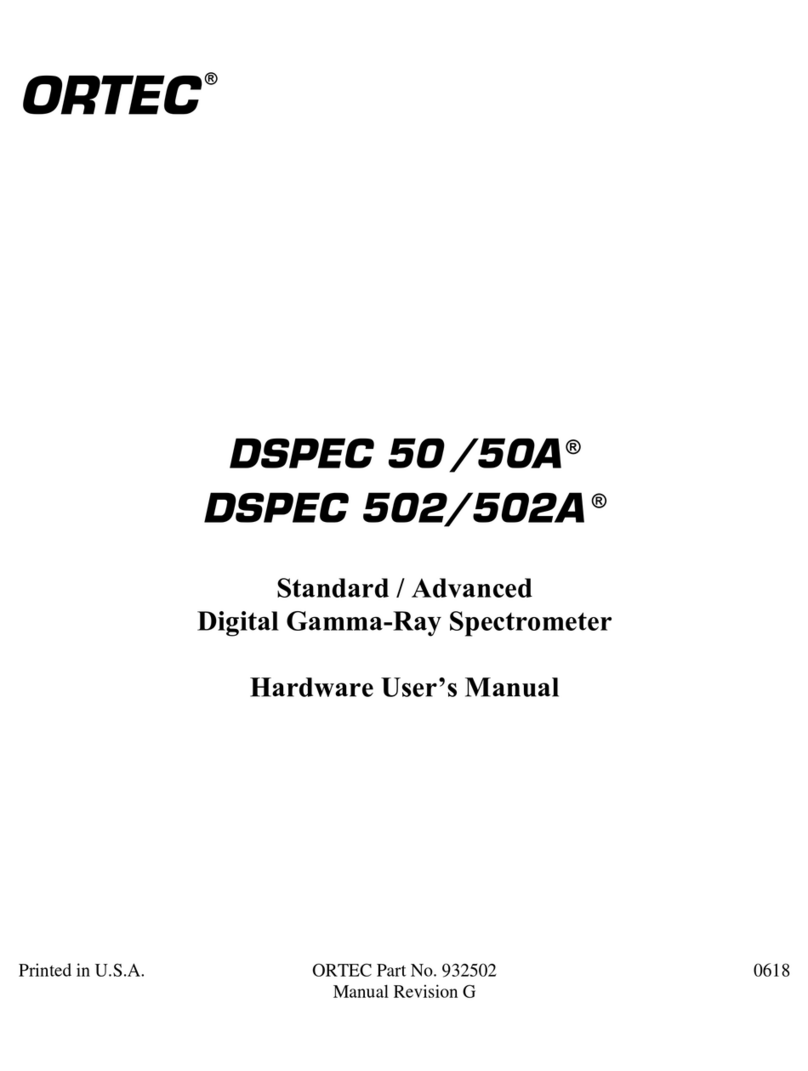
ORTEC
ORTEC DSPEC 50 Instructions for use
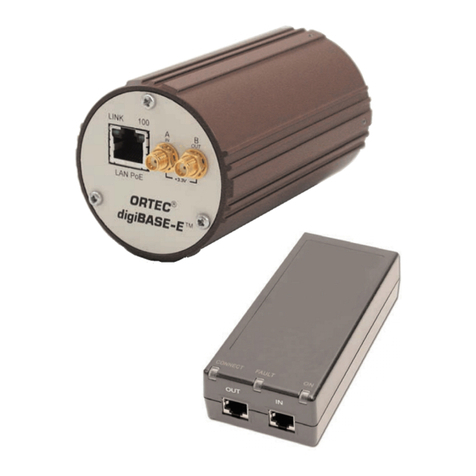
ORTEC
ORTEC digiBASE-E User manual

ORTEC
ORTEC RADEAGLET User manual
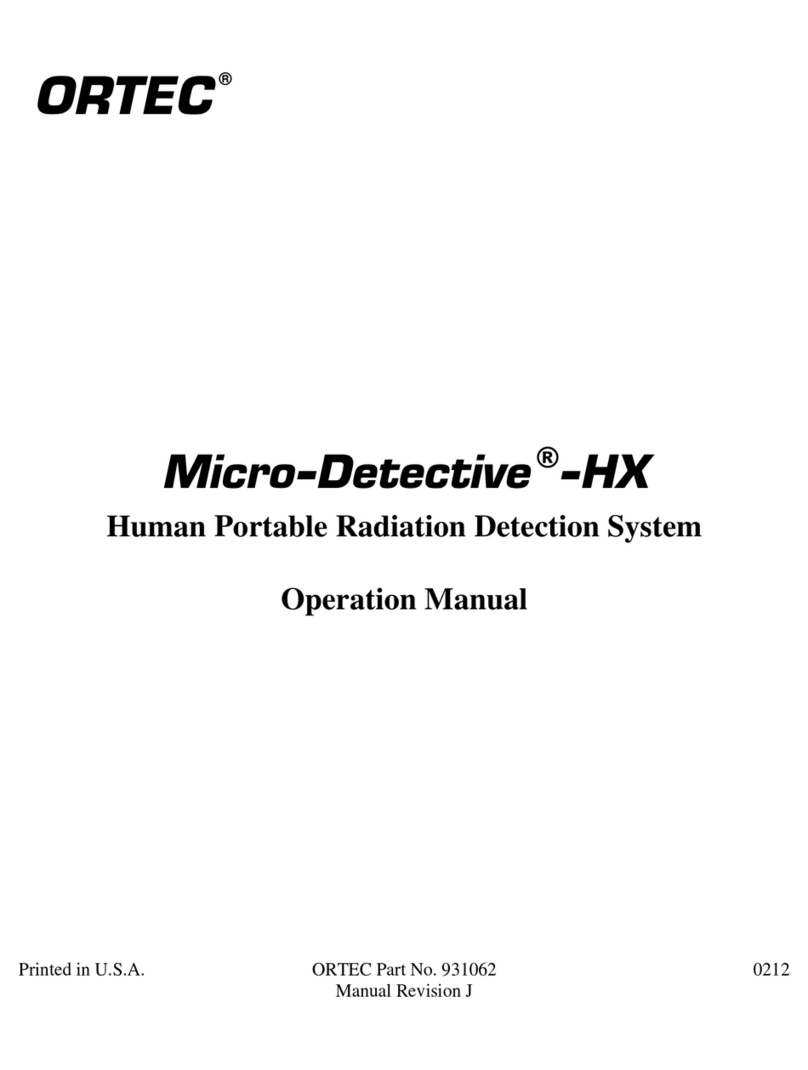
ORTEC
ORTEC Micro-Detective-HX User manual
Popular Measuring Instrument manuals by other brands

BYK-Gardner
BYK-Gardner Haze-gard plus manual
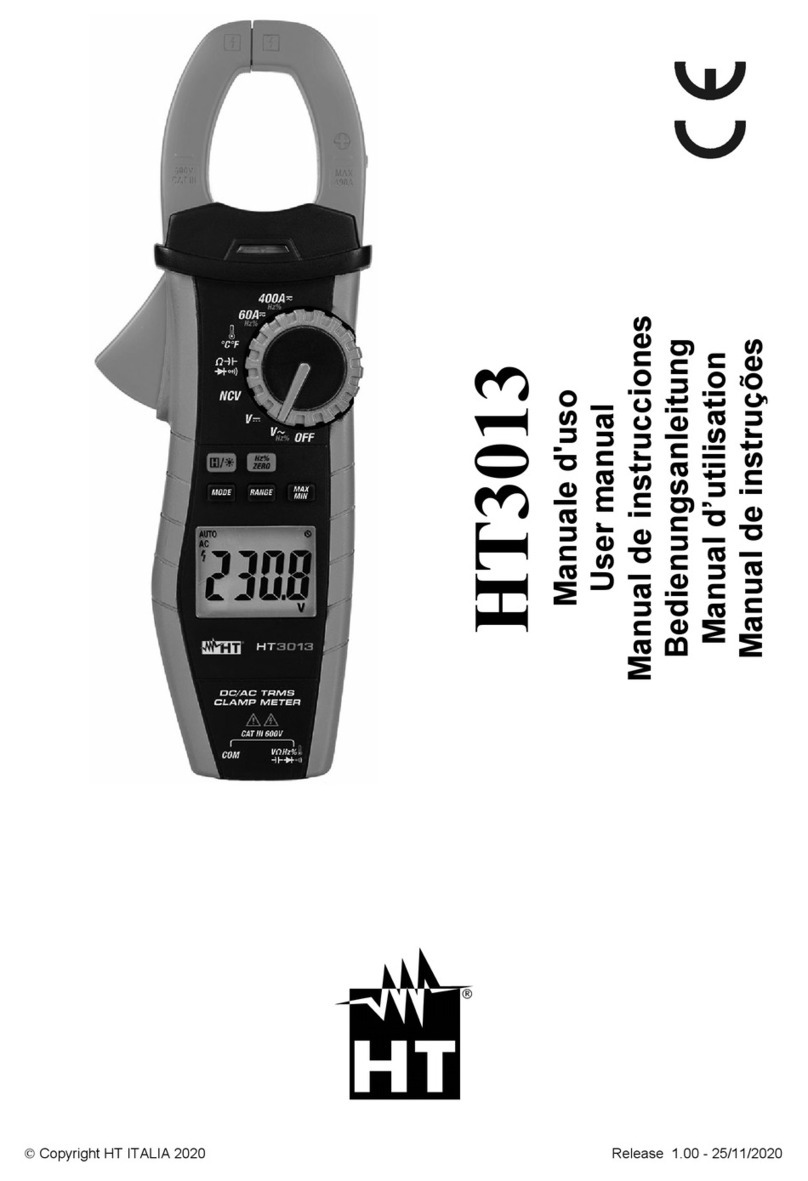
HT
HT HT3013 user manual

smart-me
smart-me 202063 quick start guide
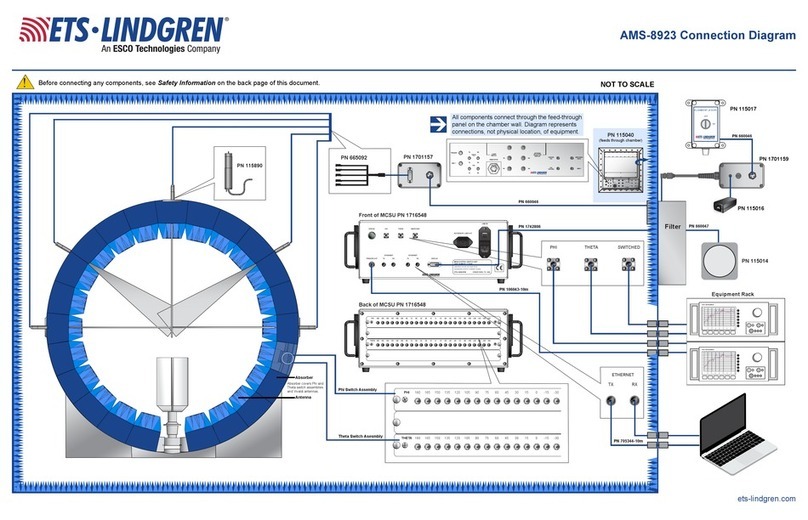
Esco
Esco ETS-Lindgren AMS-8923 Connection diagram
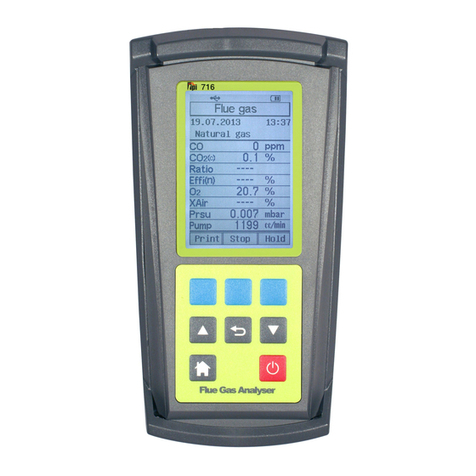
TPI
TPI The Value Leader 716N manual
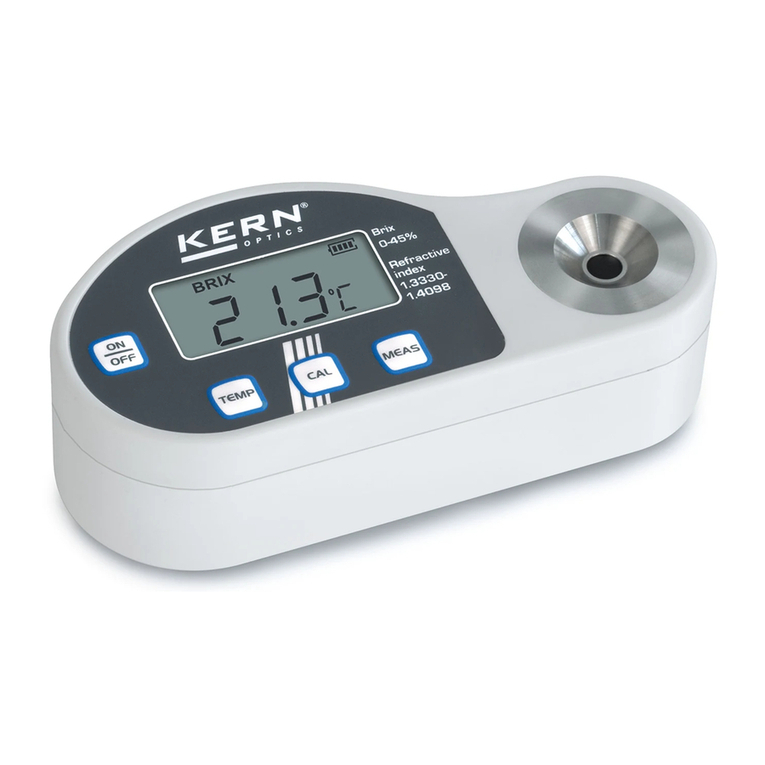
KERN
KERN ORD 45BM, ORD 92BM, ORD 85BM, ORD 92HM, ORD 1SM, ORD 3SM, ORD 2WM, ORD 1PM, ORD 2UM, ORD 5UM, ORD 6 US, ORD... operating instructions