Penn P32 Series User manual

Figure 1: P32AC Differential Pressure Switch with
U mounting bracket and direct mounted sensing
probe assembled.
Application
This differential pressure switch is used to sense
the flow of air in ducts. When used with electric
strip heaters, the switch can be wired to open the
control circuit and de-energize the heaters when
air flow stops.
Important: P32 Series pressure switches are
intended to control equipment under normal
operating conditions. Where failure or malfunction
of a P32 pressure switch could lead to an abnormal
operating condition that could cause personal
injury or damage to the equipment or other
property, other devices (limit or safety controls) or
systems (alarm or supervisory) intended to warn
of or protect against failure or malfunction of the
P32 pressure switch must be incorporated into and
maintained as part of the control system.
Typical applications include:
• Air flow proving with electric duct heaters
• maximum air flow controller for variable air
Volume systems
• Clogged filter detection
• Detection of icing of air conditioning coils
and initiation of defrost cycle
For a P32 sensitive differential pressure switch
P32 Series Sensitive Differential Pressure Switch
Installation Guide
for combustion air applications, refer to P32
Series Sensitive Differential Pressure Switch For
Combustion Air Applications ( LIT-125430) at
https://docs.johnsoncontrols.com/bas/.
Operation
This differential pressure switch senses a change
in the differential pressure (either velocity pressure
or pressure drop across a fixed restriction in
the duct) as air flow in the duct changes. This
differential pressure, as sensed by the two sensing
ports, is applied to the two sides of a diaphragm in
the pressure switch.
The spring-loaded diaphragm moves and actuates
the switch when the air pressure difference
reaches the setpoint.
This switch can also be used to detect small
positive gauge pressure by using only the high
pressure connection and leaving the low pressure
connector open, or to detect a vacuum by using
only the low pressure connection and leaving the
high pressure connector open to ambient pressure.
Installation
Follow equipment manufacturer’s instructions.
Locating
Select a location on or near the duct where
vibrations are minimal and the terminal screws
and adjusting screw are accessible. Ambient
temperature should be within the range of -40 to
167°F (-40 to 75°C) to avoid physical damage to
the control. The factory setting of the P32 is made
at room temperature. Ensure mounting locations
are as close to room temperature as possible.
Otherwise, for best performance, set switches
in the field in their mounted position and at the
normal ambient temperature for that application.
Mounting
The switch is normally mounted with the
diaphragm in a vertical position. It may be
fastened directly to the duct, heater, or panel as
long as the mounting surface has minimal or no
vibration.
Note: The switch is factory set with the
diaphragm in a vertical position. If it is mounted
in a horizontal position with the steel housing
(high pressure connector) down, the setpoint
will increase by about 0.07 in W.C. (.017 kPa). If
mounted with the steel housing up, the switch
may be inoperative at minimum setting. Adjustable
models can be readjusted for this mounting
position and minimum setpoint as follows:
1. Mount the switch securely.
2. Make sure no pressure is applied to either
connector.
3. Turn the adjusting screw clockwise until the
switch operates and at least an additional 1/3
turn.
Important: When turning the fitting into the
plastic low pressure port, do not overtighten
and crack the threaded boss. Turn fitting in
finger-tight, then an additional 1 to 1 1/2 turns
(approximately 15 to 20 in.lb). Sealing compound
or tape is not required for the plastic low pressure
port.
Figure 2: Interior view of the P32AA Differential
Pressure Switch.
Figure 3: Direct mounting a P32 using the L
bracket as a mounting flange
Figure 4: Typical installation for a P32 Switch on
duct using Part No. BKT229-1R bracket and direct
mounting probe
Mounting for direct duct or heater
1. Cut or drill a 7/8 in. (22 mm) diameter hole.
2. Install tubing in the 1/8 in. NPT high pressure
(metal) connector, if required.
3. Place the metal connector in the hole.
4. Use a 1/2 in. conduit lock nut on the
connector and secure in place.
Part No. 996-100, Rev. F
Issue Date: May 2022

www.penncontrols.com
® Johnson Controls and Penn are registered trademarks of Johnson Controls in the United States of America and/or other countries. All other trademarks used herein are the property of their respective owners.
© Copyright 2022 by Johnson Controls.
All rights reserved.
Mounting for direct duct with L
bracket No. BKT182-2R where inside
of duct is not accessible for securing
lock nut. See Fig. 3.
1. Cut or drill a 1 1/4 in. (32 mm) diameter hole
in duct.
2. Secure mounting bracket to switch with angle
at side of switch using 1/2 in. conduit lock
nut.
3. Mount to duct using sheet metal screws
through the four holes in large surface of
mounting bracket.
Mounting for direct mounting with
channel U bracket No. BKT229-1R. See
Fig. 4.
1. Drill a 1/4 in. (6 mm) hole in the duct at
sensing location.
2. Install 1/4 in. tube into metal (high pressure)
connector with compression fitting and
coupling.
3. Secure bracket to switch with 1/2 in. conduit
lock nut, if not factory installed.
4. Remove adhesive protection paper from
gasket and slide gasket onto 1/4 in. tube with
adhesive away from switch.
5. Place switch on duct tube in 1/4 in. hole, drill
or punch mounting screw holes.
6. Fasten to duct with the two self-tapping
screws.
7. Press gasket against duct.
Mounting for remote. See Fig. 5.
1. If direct panel mount is required, drill 7/8 in.
(22 mm) diameter hole and secure with lock
nut.
2. When mounting bracket is required, use L
bracket No. BKT182-2R.
3. Use the bracket as a guide and drill or punch
the mounting screw holes.
4. Determine the correct mounting bracket
position and secure it to the switch with
1/2 in. conduit lock nut. There may be
installations where the bracket must be
installed before fastening it to the switch.
5. Use FTG18A-600R remote mounting probe
kits for remote sensing locations. Run plastic
or copper tubing from the high and/or low
pressure connectors to the sensing point. Use
tubing with at least .17in. I.D. (1/4in. O.D.)
Figure 5: The P32 may be mounted on either a vertical or horizontal surface
using an L bracket and two FTG18A-600R remote mounted probe kits.
Wiring
Risk of electrical shock.
Disconnect the electrical power
supply before wiring the switch into circuit to
avoid electrical shock.
Risk of equipment damage.
Disconnect the electrical power
supply before wiring the switch into circuit to
avoid possible damage to equipment.
Make all wiring connections using copper
conductors only, and in accordance with the local,
national, and regional regulations.
Figure 6: Switch action on the P32 control.
Important: Use terminal screws furnished (8-
32 x 1/4in. binder head). Substitution of other
screws may cause problems in making proper
connections.
The single pole double throw (SPDT) models have
color coded terminals. The Red to Yellow circuit
closes on differential pressure increase and the red
to blue circuit opens. See Fig. 6.
Adjustment
The field-adjustable switch has an adjusting screw
located under the cover. Some models have a
scale plate for adjusting convenience.
To adjust, complete the following steps:
1. Remove cover.
2. Turn adjusting screw CW to increase the
differential pressure setpoint.
3. Turn adjusting screw CCW to decrease the
setpoint.
4. If the high or low adjustment stop is reached,
back off the adjusting screw at least 1/6 turn
from the stop.
Checkout procedure
Before leaving the installation, observe at least
three complete operating cycles to ensure that all
components function correctly.
Repairs and replacement
Field repairs must not be made. For a replacement
pressure switch, contact the nearest Johnson
Controls distributor.
APAC Single Point of Contact:
JOHNSON CONTROLS
C/O CONTROLS PRODUCT MANAGEMENT
NO. 32 CHANGJIANG RD NEW DISTRICT
WUXI JIANGSU PROVINCE 214028
CHINA
European Single Point of Contact:
JOHNSON CONTROLS
VOLTAWEG 20
6101 XK ECHT
THE NETHERLANDS
NA/SA Single Point of Contact:
JOHNSON CONTROLS
5757 N GREEN BAY AVE.
GLENDALE, WI 53209
USA
UK Single Point of Contact:
JOHNSON CONTROLS
TYCO PARK
GRIMSHAW LANE
MANCHESTER M40 2WL
UNITED KINGDOM
Other Penn Switch manuals
Popular Switch manuals by other brands
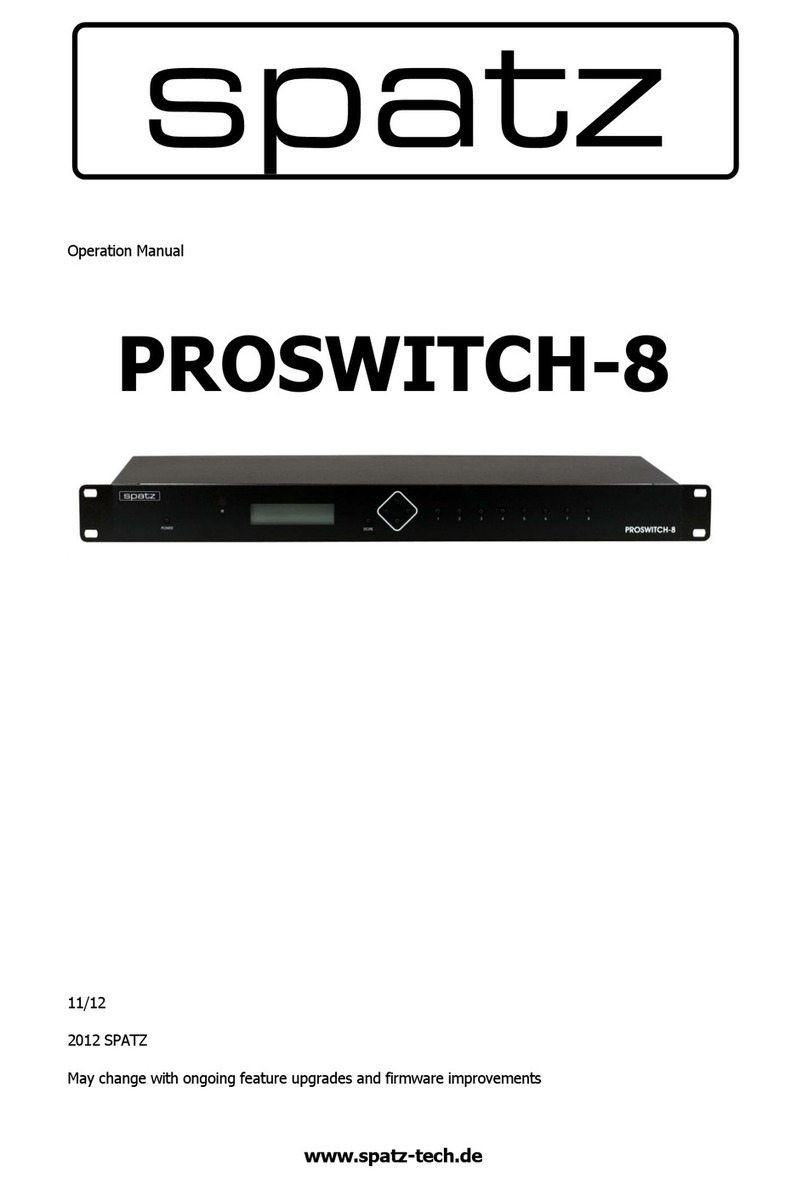
Spatz
Spatz PROSWITCH-8 Operation manual

American Megatrends
American Megatrends MegaRAC K1 user guide

NETGEAR
NETGEAR GS724TPv3 Hardware installation guide
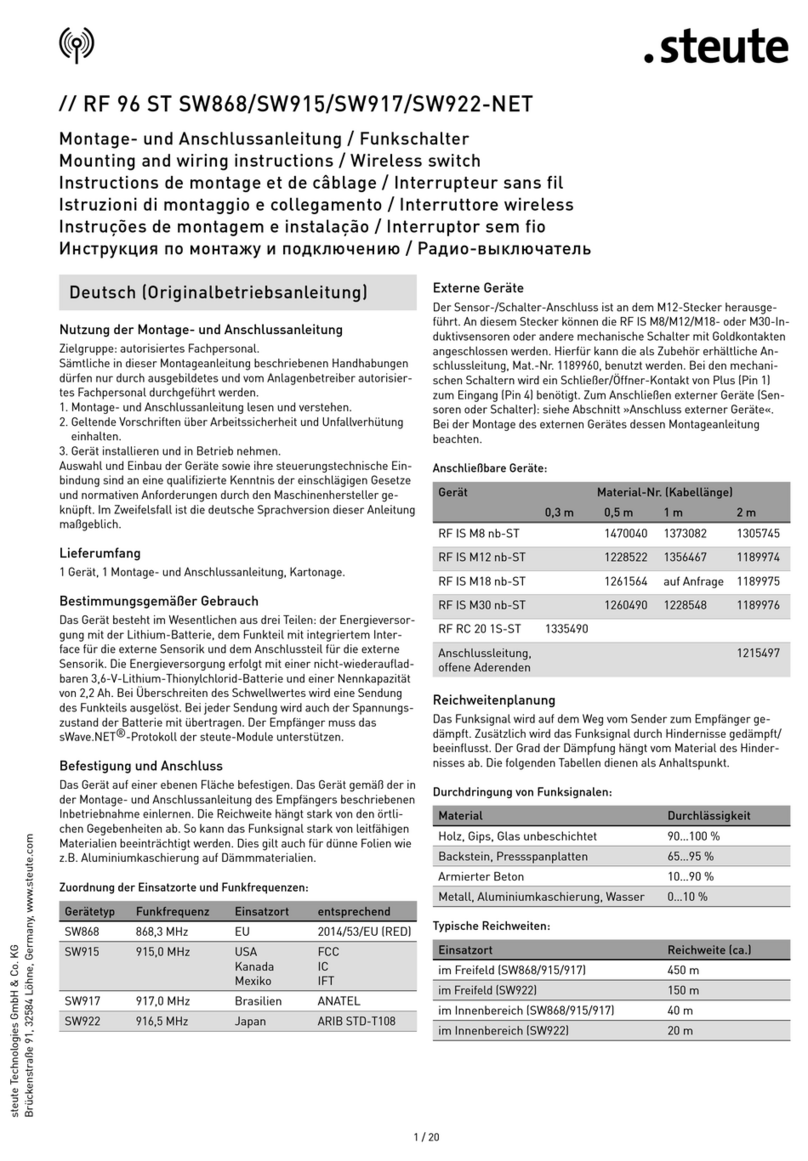
steute
steute RF 96 ST SW868-NET Mounting and wiring instructions
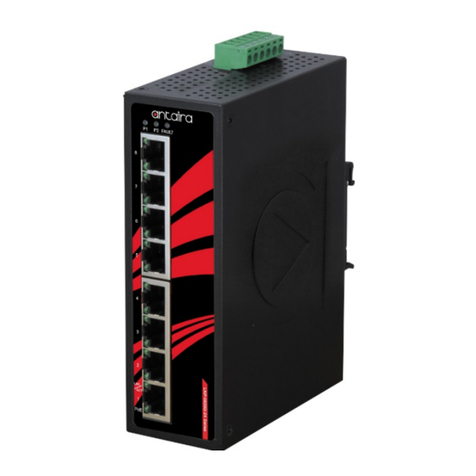
ANTAIRA
ANTAIRA LNP-0800G-24 Series Quick installation guide
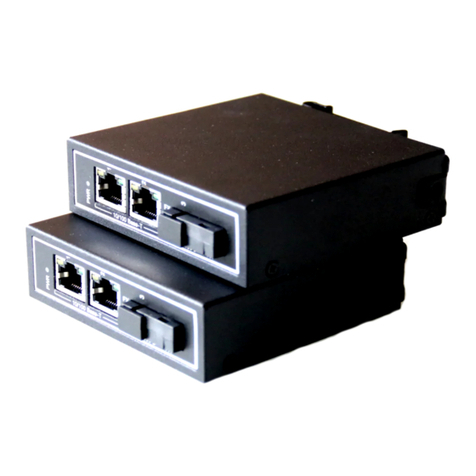
Wiwav
Wiwav WDH-2ET1FX-DC user manual