Physik Instrumente H-850 Series User manual

Physik Instrumente (PI) GmbH & Co. KG, Auf der Roemerstrasse 1, 76228 Karlsruhe, Germany
Phone +49 721 4846-0, Fax +49 721 4846-1019, Email info@pi.ws, www.pi.ws
MS202E
H
-850 Hexapod Microrobot
User Manual
Version: 2.3.0
Date: 03.12.2019
This document describes the following hexapod
microrobots:
H-850.H2
H-850.H2A
H-850.H2I
H-850.H2V
H-850.G2
H-850.G2A
H-850.G2I
H-850.G2V

The following company names and brands are registered trademarks of Physik Instrumente (PI) GmbH & Co.
KG:
PI®, NanoCube®, PICMA®, PILine®, NEXLINE®, PiezoWalk®, NEXACT®, Picoactuator®, PInano®, PIMag®,
Q-Motion®
The patents held by PI are found in our patent list: http://www.physikinstrumente.com/en/about-pi/patents
Notes on brand names and third-party trademarks:
BiSS is a registered trademark of iC-Haus GmbH.
© 2019 Physik Instrumente (PI) GmbH & Co. KG, Karlsruhe, Germany. The text, photographs, and drawings in
this manual are protected by copyright. With regard thereto, Physik Instrumente (PI) GmbH & Co. KG retains
all the rights. The use of any text, images and drawings is permitted only in part and only when indicating the
source.
Original instructions
First printing: 03.12.2019
Document number: MS202E, BRo, Version 2.3.0
Subject to change. This manual is superseded by any new release. The latest respective release is available for
download (p. 3) on our website.

1About this Document 1
1.1 Objective and Target Audience of this User Manual.................................................. 1
1.2 Symbols and Typographic Conventions...................................................................... 1
1.3 Figures ........................................................................................................................ 2
1.4 Other Applicable Documents ..................................................................................... 2
1.5 Downloading Manuals................................................................................................ 3
2Safety 5
2.1 Intended Use .............................................................................................................. 5
2.2 General Safety Instructions ........................................................................................ 5
2.3 Organizational Measures............................................................................................ 5
2.4 Measures for Handling Vacuum-Compatible Products.............................................. 6
3Product Description 7
3.1 Features and Applications .......................................................................................... 7
3.2 Model Overview ......................................................................................................... 7
3.3 Suitable Controllers .................................................................................................... 8
3.4 Product View .............................................................................................................. 9
3.5 Scope of Delivery........................................................................................................ 9
3.6 Accessories ............................................................................................................... 10
3.7 Technical Features.................................................................................................... 12
3.7.1 Struts............................................................................................................ 12
3.7.2 Reference Switch and Limit Switches.......................................................... 13
3.7.3 Control......................................................................................................... 13
3.7.4 Motion ......................................................................................................... 13
3.7.5 ID Chip.......................................................................................................... 17
4Unpacking 19
4.1 Unpacking the Hexapod ........................................................................................... 19
4.2 Removing the Transport Safeguard.......................................................................... 20
4.2.1 Removing the Transport Safeguard for the H-850.x2 and .x2V Models...... 20
4.2.2 Removing the Transport Safeguard for the H-850.x2A and .x2I
Models ......................................................................................................... 21
5Installation 23
5.1 General Notes on Installation................................................................................... 23
5.2 Determining the Permissible Load and Workspace ................................................. 24
5.3 Attaching the Snap-on Ferrite .................................................................................. 25
5.4 Grounding the Hexapod ........................................................................................... 26
Contents

5.5 Mounting the Hexapod on a Surface ....................................................................... 26
5.6 Fixing the Load to the Hexapod................................................................................ 28
5.7 Optional: Removing the Coordinate Cube ............................................................... 29
5.8 Connecting the Hexapod to the Controller .............................................................. 30
6Startup 37
6.1 General Notes on Startup......................................................................................... 37
6.2 Starting Up the Hexapod System ............................................................................. 38
6.3 Baking Out Vacuum-Compatible Models ................................................................. 39
7Maintenance 41
7.1 Performing a Maintenance Run ............................................................................... 41
7.2 Packing the Hexapod for Transport.......................................................................... 41
7.2.1 Attaching the Transport Safeguard ............................................................. 42
7.2.2 Packing the Hexapod ................................................................................... 46
7.3 Cleaning the Hexapod .............................................................................................. 49
8Troubleshooting 51
9Customer Service 53
10 Technical Data 55
10.1 Specifications............................................................................................................ 55
10.1.1 Data Table.................................................................................................... 55
10.1.2 Specifications for Vacuum-Compatible Versions ........................................ 58
10.1.3 Maximum Ratings........................................................................................ 60
10.2 Cable Set Specifications............................................................................................ 60
10.3 Ambient Conditions and Classifications ................................................................... 61
10.4 Dimensions ............................................................................................................... 61
10.5 Pin Assignment ......................................................................................................... 63
10.5.1 Power Supply Connection............................................................................ 63
10.5.2 Data Transmission Connection.................................................................... 63
11 Old Equipment Disposal 67
12 Glossary 69
13 Appendix 73
13.1 Explanations of the Performance Test Sheet........................................................... 73
13.2 EU Declaration of Conformity .................................................................................. 75

1 About this Document
H-850 Hexapod Microrobot MS202E Version: 2.3.0 1
In this Chapter
Objective and Target Audience of this User Manual..................................................................... 1
Symbols and Typographic Conventions......................................................................................... 1
Figures............................................................................................................................................ 2
Other Applicable Documents......................................................................................................... 2
Downloading Manuals ................................................................................................................... 3
1.1 Objective and Target Audience of this User Manual
This manual contains information on using the H-850 as intended.
It assumes that the reader has a fundamental understanding of basic servo systems as well as
motion control concepts and applicable safety procedures.
The latest versions of the user manuals are available for download (p. 3) on our website.
1.2 Symbols and Typographic Conventions
The following symbols and typographic conventions are used in this user manual:
CAUTION
Dangerous situation
Failure to comply could lead to minor injury.
Precautionary measures for avoiding.
NOTICE
Dangerous situation
Failure to comply could cause damage to equipment.
Precautionary measures for avoiding the risk.
INFORMATION
Information for easier handling, tricks, tips, etc.
1
About this Document

1 About this Document
2 Version: 2.3.0 MS202E H-850 Hexapod Microrobot
Symbol/Label Meaning
1.
2.
Action consisting of several steps whose sequential order must be observed
Action consisting of one or several steps whose sequential order is
irrelevant
List item
p. 5 Cross-reference to page 5
RS-232 Labeling of an operating element on the product (example: socket of the
RS-232 interface)
Warning sign on the product which refers to detailed information in this
manual.
1.3 Figures
For better understandability, the colors, proportions, and degree of detail in illustrations can
deviate from the actual circumstances. Photographic illustrations may also differ and must not
be seen as guaranteed properties.
1.4 Other Applicable Documents
The devices and software tools from PI mentioned in this documentation are described in their
own manuals.
Device/program Document
no.
Document content
C-887.5xx controller MS247EK Short instructions for hexapod systems
MS244E User manual
C887T0011 EtherCAT interface of the C-887.53 controller series
C887T0007 Coordinate Systems for Hexapod Microrobots
C887T0021 Motion of the Hexapod. Position and Orientation in
Space, Center of Rotation
PI Hexapod Simulation
Tool
A000T0068 Determining the workspace and the permissible load of
the hexapod
PC software included
in the controller's
scope of delivery
Various For details, see the user manual for the C-887.5xx
controller.

1 About this Document
H-850 Hexapod Microrobot MS202E Version: 2.3.0 3
1.5 Downloading Manuals
INFORMATION
If a manual is missing or problems occur with downloading:
Contact our customer service department (p. 53).
Downloading manuals
1. Open the website www.pi.ws.
2. Search the website for the product number (e.g., P-882) or the product family (e.g.,
PICMA® bender).
3. Click the corresponding product to open the product detail page.
4. Click Downloads.
The manuals are shown under Documentation.
5. Click the desired manual and fill out the inquiry form.
The download link will then be sent to the email address entered.


2 Safety
H-850 Hexapod Microrobot MS202E Version: 2.3.0 5
In this Chapter
Intended Use.................................................................................................................................. 5
General Safety Instructions............................................................................................................ 5
Organizational Measures............................................................................................................... 5
Measures for Handling Vacuum-Compatible Products ................................................................. 6
2.1 Intended Use
The hexapod microrobot (short "hexapod") is a laboratory device as defined by DIN EN 61010-1.
It is built for indoor use and use in an environment which is free of dirt, oil, and lubricants.
In accordance with its design, the hexapod is intended for positioning, adjusting, and shifting of
loads on six axes at various velocities.
The hexapod can only be used as intended in conjunction with a suitable controller available
from PI (p. 8), which coordinates all motion of the hexapod.
2.2 General Safety Instructions
The H-850 is built according to state-of-the-art technology and recognized safety standards.
Improper use can result in personal injury and/or damage to the H-850.
Use the H-850 for its intended purpose only, and only when it is in perfect technical
condition.
Read the user manual.
Eliminate any malfunctions that may affect safety immediately.
The operator is responsible for the correct installation and operation of the H-850.
2.3 Organizational Measures
User manual
Always keep this user manual together with the H-850.
The latest versions of the user manuals are available for download (p. 3) on our
website.
2
Safety

2 Safety
6 Version: 2.3.0 MS202E H-850 Hexapod Microrobot
Add all information from the manufacturer to the user manual, for example
supplements or technical notes.
If you give the H-850 to a third party, include this user manual as well as other relevant
information provided by the manufacturer.
Do the work only if the user manual is complete. Missing information due to an
incomplete user manual can result in minor injury and damage to equipment.
Install and operate the H-850 only after you have read and understood this user
manual.
Personnel qualification
The H-850 may only be installed, started, operated, maintained, and cleaned by authorized and
appropriately qualified personnel.
2.4 Measures for Handling Vacuum-Compatible Products
When handling the vacuum version of the hexapod, attention must be paid to appropriate
cleanliness. At PI, all parts are cleaned before assembly. During assembly and measurement,
powder-free gloves are worn. Afterwards, the hexapod is cleaned once again by wiping and
shrink-wrapped twice in vacuum-compatible film.
Touch the hexapod only with powder-free gloves.
If necessary, wipe the hexapod clean after unpacking.

3 Product Description
H-850 Hexapod Microrobot MS202E Version: 2.3.0 7
In this Chapter
Features and Applications ............................................................................................................. 7
Model Overview............................................................................................................................. 7
Suitable Controllers ....................................................................................................................... 8
Product View.................................................................................................................................. 9
Scope of Delivery ........................................................................................................................... 9
Accessories................................................................................................................................... 10
Technical Features ....................................................................................................................... 12
3.1 Features and Applications
The various models (p. 7) of H-850 hexapod that are offered differ with respect to the sensor
type, the maximum velocity, and load capacity as well as suitability for use in a vacuum.
The parallel-kinematic design of the hexapod offers the following advantages:
Positioning operations in six independent axes (three translational axes, three
rotational axes) with short settling times
The center of rotation moves together with the motion platform
High accuracy and step resolution in all axes
No accumulation of errors of individual axes
No friction and torques from moving cables
The hexapod is controlled with a controller that can be ordered separately from PI (p. 8). The
position commands to the controller are entered as Cartesian coordinates.
3.2 Model Overview
Model Designation
H-850.H2 Precision Hexapod microrobot, DC gear motor, rotary encoder, 250 kg load
capacity, 0.5 mm/s velocity, including 3 m cable
H-850.H2A Precision Hexapod microrobot, brushless DC gear motor, absolute encoder,
250 kg load capacity, 0.5 mm/s velocity, including 3 m cable
H-850.H2I Precision Hexapod microrobot, brushless DC gear motor, incremental encoder,
250 kg load capacity, 0.5 mm/s velocity, including 3 m cable
3
Product Description

3 Product Description
8 Version: 2.3.0 MS202E H-850 Hexapod Microrobot
Model Designation
H-850.H2V Precision Hexapod microrobot, DC gear motor, rotary encoder, 80 kg load
capacity, 0.15 mm/s velocity, vacuum compatible to 10-6 hPa, including 3 m
cable set on the air side and 2 m cable set on the vacuum side
H-850.G2 Precision Hexapod microrobot, DC gear motor, rotary encoder, 50 kg load
capacity, 8 mm/s velocity, including 3 m cable
H-850.G2A Precision Hexapod microrobot, brushless DC gear motor, absolute encoder,
50 kg load capacity, 8 mm/s velocity, including 3 m cable
H-850.G2I Precision Hexapod microrobot, brushless DC gear motor, incremental encoder,
50 kg load capacity, 8 mm/s velocity, including 3 m cable
H-850.G2V Precision Hexapod microrobot, DC gear motor, rotary encoder, 25 kg load
capacity, 2.5 mm/s velocity, vacuum compatible to 10-6 hPa, including 3 m
cable set on the air side and 2 m cable set on the vacuum side
3.3 Suitable Controllers
Model Description
C-887.52 6-axis controller for hexapods, TCP/IP, RS-232, benchtop device, incl. control of
two additional axes
C-887.521
6-axis controller for hexapods, TCP/IP, RS-232, benchtop device, incl. control of
two additional axes, analog inputs
C-887.522
6-axis controller for hexapods, TCP/IP, RS-232, benchtop device, incl. control of
two additional axes, motion stop
C-887.523
6-axis controller for hexapods, TCP/IP, RS-232, benchtop device, incl. control of
two additional axes, motion stop, analog inputs
C-887.53
6-axis controller for hexapods, TCP/IP, RS-232, benchtop device, incl. control of
two additional axes, EtherCAT interface
C-887.531 6-axis controller for hexapods, TCP/IP, RS-232, benchtop device, incl. control of
two additional axes, EtherCAT interface, analog inputs
C-887.532 6-axis controller for hexapods, TCP/IP, RS-232, benchtop device, incl. control of
two additional axes, EtherCAT interface, motion stop
C-887.533 6-axis controller for hexapods, TCP/IP, RS-232, benchtop device, incl. control of
two additional axes, EtherCAT interface, motion stop, analog inputs
To order, contact our customer service department (p. 53).

3 Product Description
H-850 Hexapod Microrobot MS202E Version: 2.3.0 9
3.4 Product View
Figure 1: Product view, here: H-850.G2A
1
Panel plug for data transmission cable
2Panel plug for power supply cable
3Motion platform
4Strut
5Coordinate cube
6Base plate
3.5 Scope of Delivery
Order number Components
H-850 Hexapod according to your order (p. 7)
000015165 Snap-on ferrite
Cable set for all H-850 models:
K040B0478
or
K040B0241
Data transmission cable, HD D-sub 78 f/m, 1:1, 3 m
The K040B0478 drag chain-compatible cable is supplied with the H-
850.G2A, .G2I, .H2A, and .H2I models.
The K040B0241 cable is supplied with the H-850.G2, .H2, .H2V, and .G2V
models and is not drag chain-compatible.
K060B0111
Power supply cable, M12m 180° to M12f 90°, 3 m

3 Product Description
10 Version: 2.3.0 MS202E H-850 Hexapod Microrobot
Order number Components
Additional cable set for all vacuum-compatible models (H-850.H2V, H-850.G2V):
K040B0254
Data transmission cable on the vacuum side, HD D-sub 78 m/f, 1:1, 2 m
4668
Vacuum feedthrough for data transmission, HD D-sub 78 m/f
K060B0132 Power supply cable on the vacuum side, LEMO 2-pin (m) 180° to 2-
pin (f) 90°, 2 m
C887B0002 Vacuum feedthrough for power supply, LEMO 2-pin (f) to M12 (m)
Packaging, consisting of:
Transport safeguard with mounting kit
Inner and outer box
Foam and corrugated cardboard cushions
Pallet
Documentation, consisting of:
H850T0001
Printed technical note on unpacking the hexapod
MS247EK
Short instructions for hexapod systems
Screw sets and tools:
000034605
Mounting kit:
6 socket head screws, M6×30 ISO 4762
1 hex key 5.0 DIN 911
000077312 Double open-end wrench, 10 x 13 mm DIN 895
000036450 Accessories for connecting to the grounding system:
1 flat-head screw with cross recess, M4x8 ISO 7045
2 flat washers, form A-4.3 DIN 7090
2 safety washers, Schnorr Ø 4 mm N0110
3.6 Accessories
Order number Description*
C-887.5A03 Hexapod cable set 3 m, consisting of:
Description
Length
Item number
Data transmission cable, HD D-sub 78 f/m, 1:1
3 m
K040B0490
Power supply cable, M12 m/f, 1:1 3 m K060B0262
C-887.5B03 Hexapod cable set 3 m, drag chain compatible, consisting of:
Designation
Length
Item number
Data transmission cable, HD D-sub 78 f/m, 1:1
3 m
K040B0270
Power supply cable, M12 m/f, 1:1 3 m K060B0262

3 Product Description
H-850 Hexapod Microrobot MS202E Version: 2.3.0 11
Order number Description*
C-887.5A05
Hexapod cable set 5 m, consisting of:
Designation Length Item number
Data transmission cable, HD D-sub 78 f/m, 1:1 5 m K040B0243
Power supply cable, M12 m/f, 1:1 5 m K060B0222
C-887.5B05
Hexapod cable set 5 m, drag chain compatible, consisting of:
Designation Length Item number
Data transmission cable, HD D-sub 78 f/m, 1:1 5 m K040B0271
Power supply cable, M12 m/f, 1:1 5 m K060B0222
C-887.5A07 Hexapod cable set 7.5 m, consisting of:
Designation Length Item number
Data transmission cable, HD D-sub 78 f/m, 1:1
7.5 m
K040B0244
Power supply cable, M12 m/f, 1:1
7.5 m
K060B0223
C-887.5B07 Hexapod cable set 7.5 m, drag chain compatible, consisting of:
Designation Length Item number
Data transmission cable, HD D-sub 78 f/m, 1:1 7.5 m K040B0295
Power supply cable, M12 m/f, 1:1 7.5 m K060B0223
C-887.5A10
Hexapod cable set 10 m, consisting of:
Designation Length Item number
Data transmission cable, HD D-sub 78 f/m, 1:1 10 m K040B0245
Power supply cable, M12 m/f, 1:1 10 m K060B0224
C-887.5B10 Hexapod cable set 10 m, drag chain compatible, consisting of:
Designation
Length
Item number
Data transmission cable, HD D-sub 78 f/m, 1:1 10 m K040B0296
Power supply cable, M12 m/f, 1:1 10 m K060B0224
C-887.5A20
Hexapod cable set 20 m, consisting of:
Designation Length Item number
Data transmission cable, HD D-sub 78 f/m, 1:1 20 m K040B0251
Power supply cable, M12 m/f, 1:1 20 m K060B0225
C-887.5B20 Hexapod cable set 20 m, drag chain compatible, consisting of:
Designation
Length
Item number
Data transmission cable, HD D-sub 78 f/m, 1:1 20 m K040B0297
Power supply cable, M12 m/f, 1:1 20 m K060B0225

3 Product Description
12 Version: 2.3.0 MS202E H-850 Hexapod Microrobot
Order number Description*
C-887.5A50
Hexapod cable set 50 m, consisting of:
Designation Length Item number
Line driver box for data transmission cable,
controller-side
– C887B0057
Line driver box for data transmission cable,
hexapod-side
–
C887B0058
Short data transmission cable, HD D-sub 78 f/m,
1:1
3 m
K040B0241
Long data transmission cable, HD D-sub 44 f/m,
1:1, three pieces
44 m K040B0277
Power supply cable for hexapod-side line driver
box, with M12 connector (m)/M-12 connector (f)
47 m K060B0228
Power adapter for hexapod, with M12 connector
(f) and power cord
1.5 m** C-
501.24180M12
Snap-on ferrite, for hexapod power adapter
–
000012097
* See "Cable Set Specifications" (p. 60) for more information.
**The length refers to the cable between the power adapter and the hexapod.
To order, contact our customer service department (p. 53).
3.7 Technical Features
3.7.1 Struts
The hexapod has six adjustable-length struts. Each strut carries out linear motion. Each set of
settings of the six struts defines a position of the motion platform in six degrees of freedom
(three translational axes and three rotational axes).
Each strut is equipped with the following components:
One actuator
Reference and limit switches
Joints for connecting to the base plate and motion platform
The actuator contains the following components:
H-850.G2, .G2V, .H2, .H2V: DC motor with incremental rotary encoder
H-850.G2A, .H2A: Brushless DC motor, absolute-measuring encoder
H-850.G2I, .H2I: Brushless DC motor, incremental encoder
Gearhead
Drive screw

3 Product Description
H-850 Hexapod Microrobot MS202E Version: 2.3.0 13
3.7.2 Reference Switch and Limit Switches
The reference switch of a strut functions independently of the angular positions of the strut
ends and the lengths of the other struts.
When a limit switch is activated, the power source of the motor is switched off to protect the
hexapod against damage from malfunctions.
3.7.3 Control
Der hexapod is intended for operation with a suitable controller from PI (p. 8). The controller
makes it possible to command motion of individual axes, combinations of axes or all six axes at
the same time in a single motion command.
The controller calculates the settings for the individual struts from the target positions given for
the translational and rotational axes. The velocities and accelerations of the struts are
calculated so that all struts start and stop at the same time.
Every time the controller of a hexapod equipped with incremental encoders is switched on or
rebooted, the hexapod must complete a reference move, in which each strut moves to its
reference switch. After the reference move, the motion platform is in the reference position
and can be commanded to move to absolute target positions.
A reference move is not required for a hexapod with absolute-measuring sensors.
For further information, see the user manual for the controller.
3.7.4 Motion
The platform moves along the translational axes X, Y, and Z and around the rotational axes U, V,
and W.
Using the controller, custom coordinate systems can be defined and used instead of the default
coordinate system.
Default and user-defined coordinate systems are always right-handed systems. It is not possible
to convert a right-handed system to a left-handed system.

3 Product Description
14 Version: 2.3.0 MS202E H-850 Hexapod Microrobot
The following is a description of how the hexapod behaves with the default coordinate system.
Work with user-defined coordinate systems is described in the C887T0007 technical note.
Figure 2: Coordinate system and rotations to the rotational coordinates U, V, and W. The coordinate
system is depicted above the platform for better clarity.
Translation
Translations are described in the spatially-fixed coordinate system. The translational axes X, Y,
and Z meet at the origin of the coordinate system (0,0,0). For further information, see the
glossary (p. 69).
Rotation
Rotations take place around the rotational axes U, V, and W. The rotational axes meet at the
center of rotation (also referred to as "pivot point"). The rotational axes and therefore also the
center of rotation always move together with the platform of the hexapod (see also the
example below for consecutive rotations).
A given rotation in space is calculated from the individual rotations in the order U -> V- > W.
For further information on the center of rotation, see the glossary (p. 69).
INFORMATION
The dimensional drawing (p. 61) contains the following:
Orientation of the default coordinate system
Position of the default center of rotation

3 Product Description
H-850 Hexapod Microrobot MS202E Version: 2.3.0 15
Example: Consecutive rotations
INFORMATION
For a clearer view, the figures have been adapted as follows:
Round platform replaced by T-shaped platform
Coordinate system shown shifted
Center of rotation in the top left corner of the platform
1. The U axis is commanded to move to position 10.
The rotation around the U axis tilts the rotational axes V and W.
Figure 3: Rotation around the U axis
Platform in reference position
Platform position: U = 10 (U parallel to spatially-fixed X axis)

3 Product Description
16 Version: 2.3.0 MS202E H-850 Hexapod Microrobot
2. The V axis is commanded to move to position –10.
The rotation takes place around rotational axis V, which was tilted during the previous
rotation.
The rotation around the V axis tilts the rotational axes U and W.
Figure 4: Rotation around the V axis
Platform in reference position
Platform position: U = 10, V = –10 (U and V parallel to the platform level)
This manual suits for next models
8
Table of contents
Popular Robotics manuals by other brands
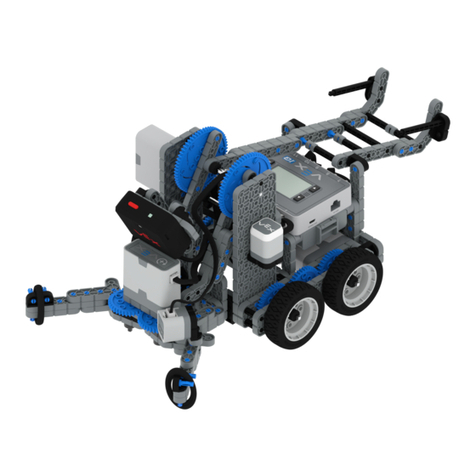
Vex
Vex Clawbot IQ Build instructions
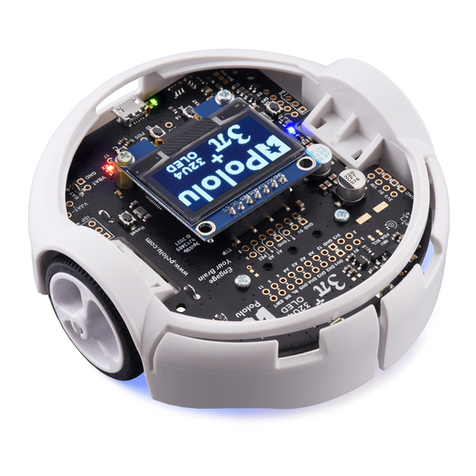
Pololu
Pololu 3pi+ 32U4 user guide
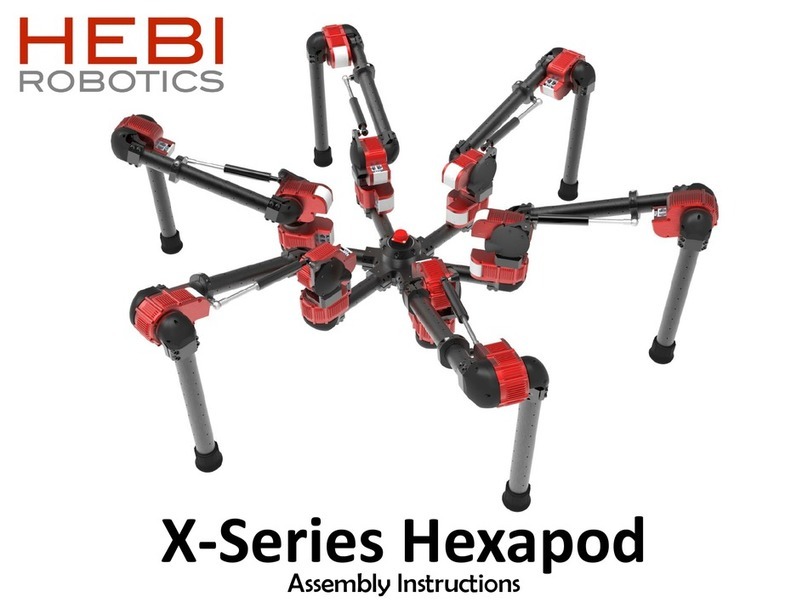
HEBI Robotics
HEBI Robotics X-Series Hexapod Assembly instructions

M.J. MALLIS GROUP
M.J. MALLIS GROUP SIAT WR100 Instruction manual and spare parts list
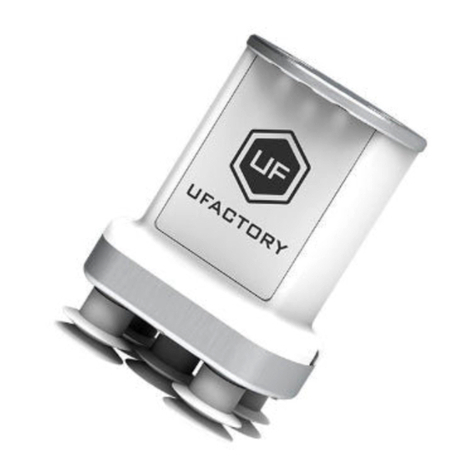
UFactory
UFactory xARM VACUJM GRIPPER user manual
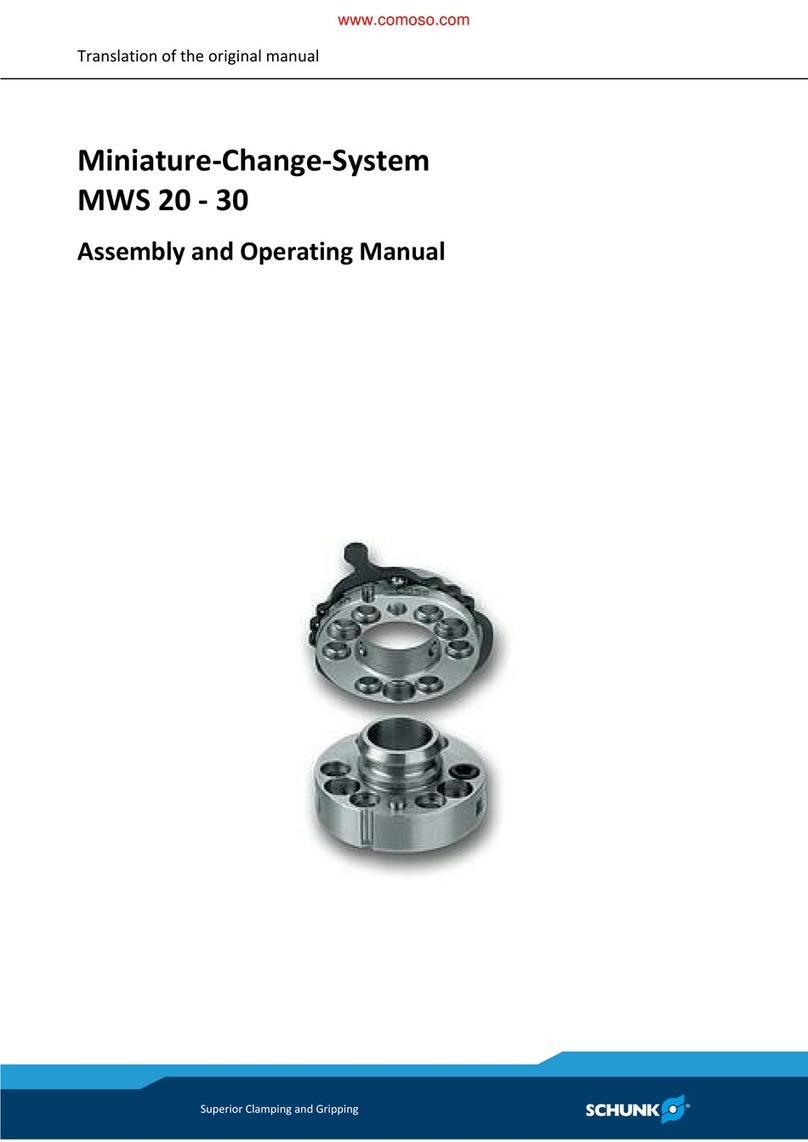
SCHUNK
SCHUNK MWS 20 Assembly and operating manual