Powers HydroGuard 400 Series How to use
Other Powers Control Unit manuals
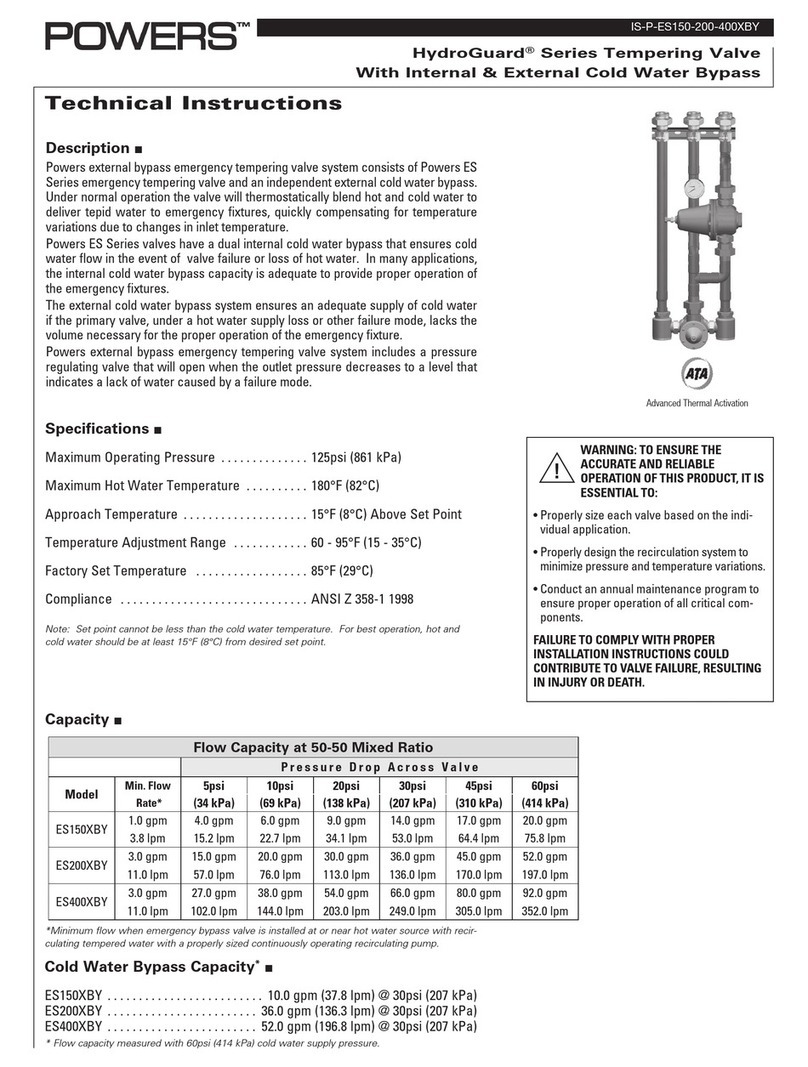
Powers
Powers HydroGuard ES150XBY Owner's manual
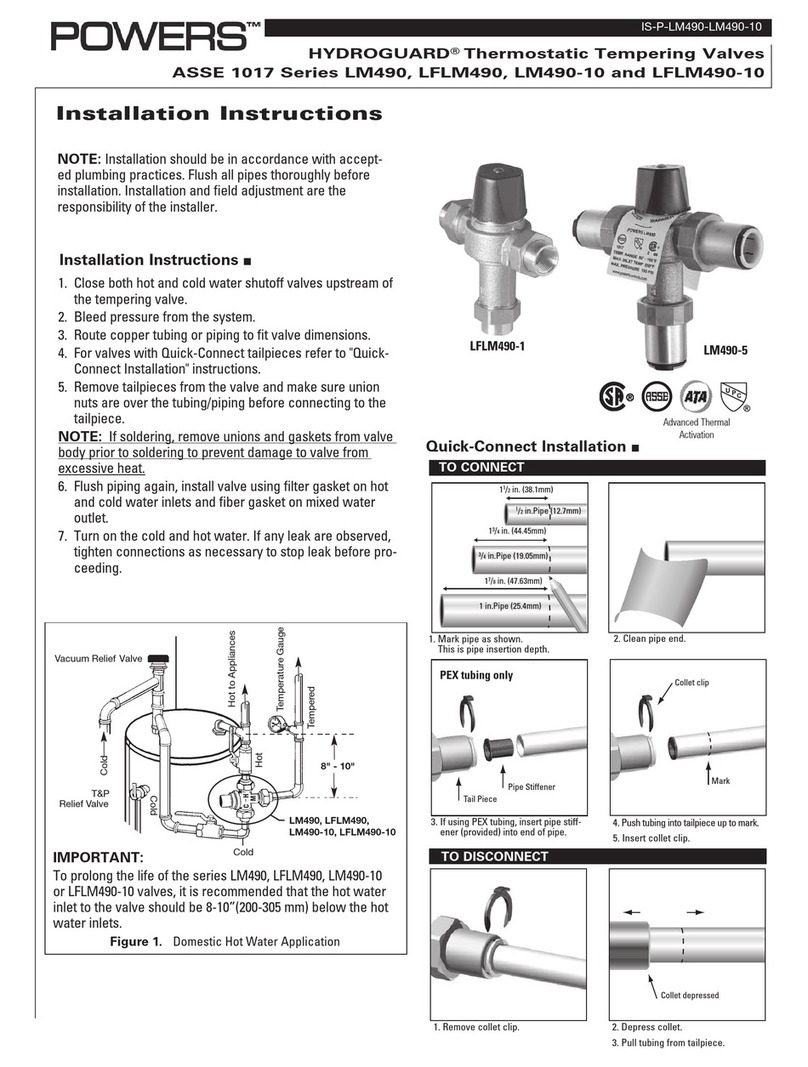
Powers
Powers HydroGuard LFLM490 User manual

Powers
Powers HYDROGUARD MM430 Series Owner's manual
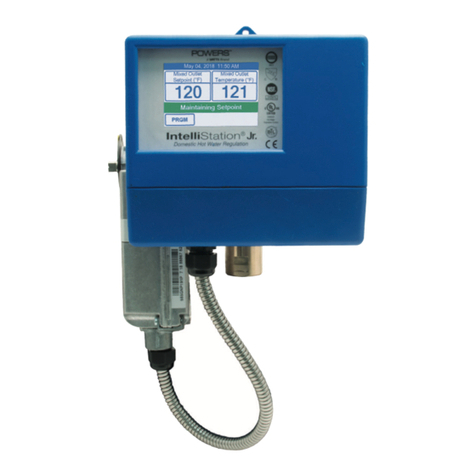
Powers
Powers IntelliStation Jr User manual
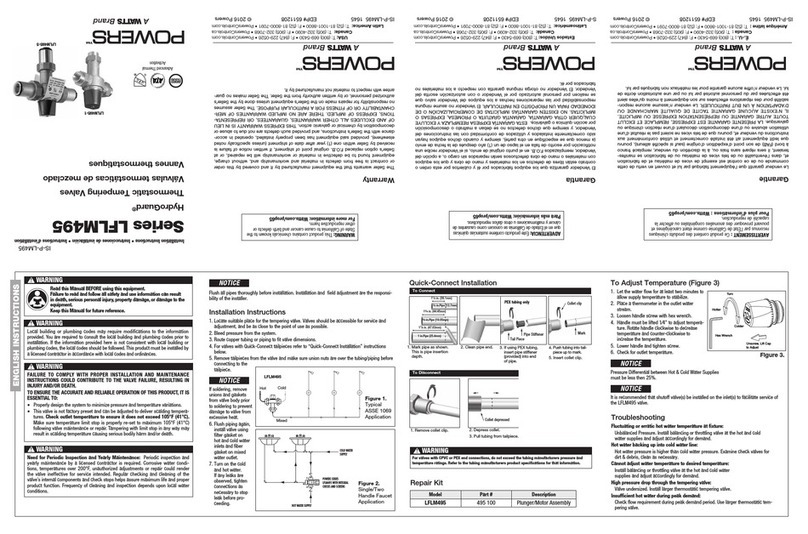
Powers
Powers LFLM49 Series User manual
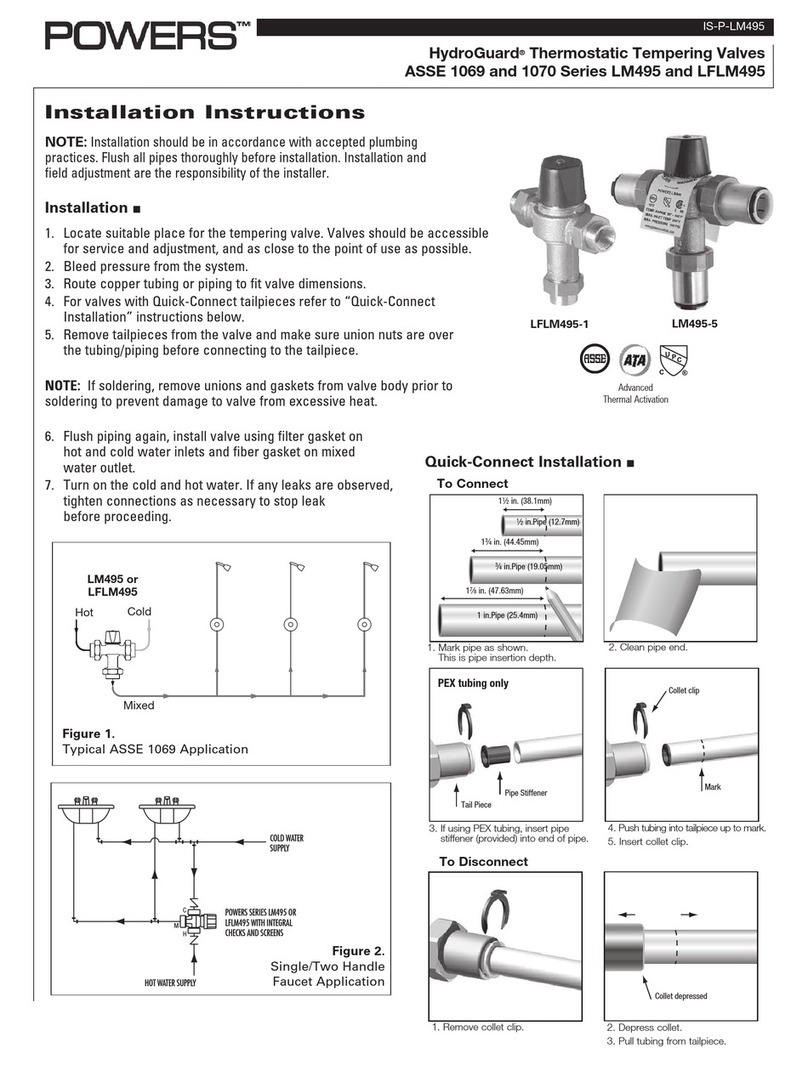
Powers
Powers HydroGuard LM495 Series User manual
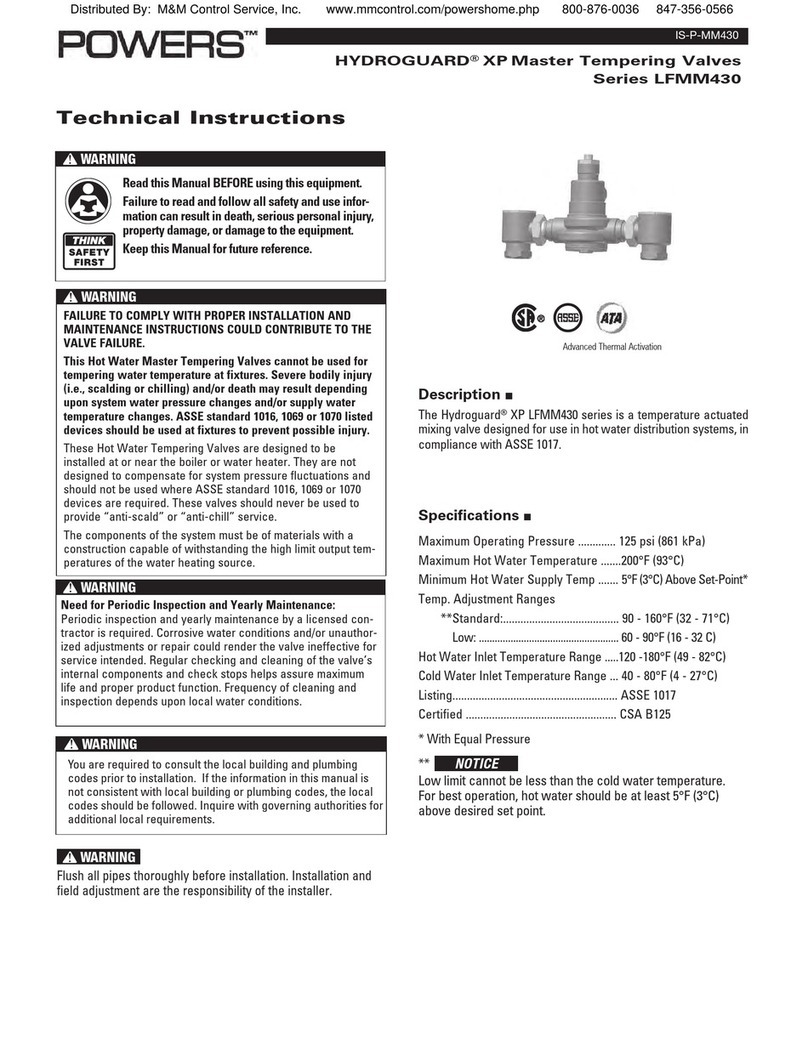
Powers
Powers HYDROGUARD XP LFMM430 Series Owner's manual
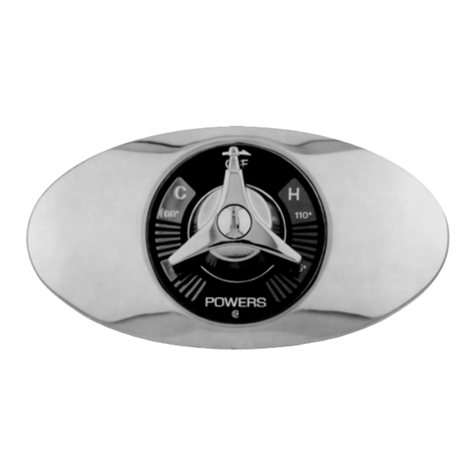
Powers
Powers HydroGuard e427 Series Owner's manual

Powers
Powers HydroGuard XP Series LFSH1430 Owner's manual
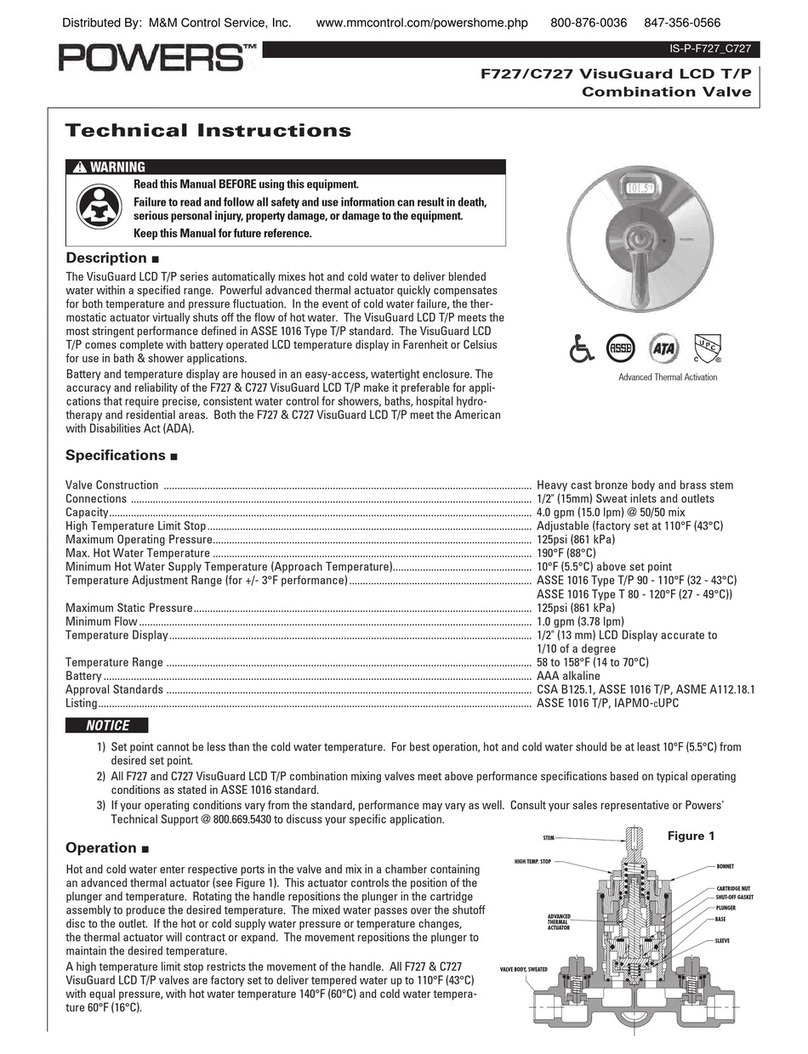
Powers
Powers F727 Owner's manual
Popular Control Unit manuals by other brands
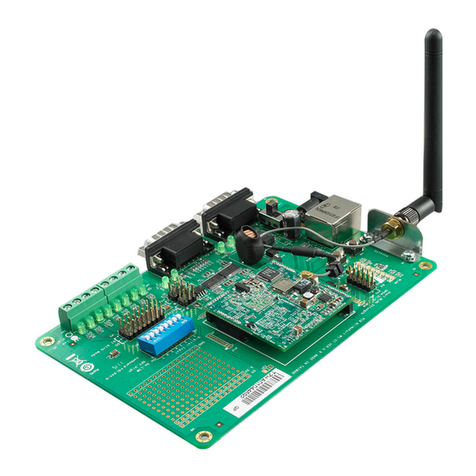
Moxa Technologies
Moxa Technologies MiiNePort W1 Series user manual

Eaton
Eaton CMA user manual
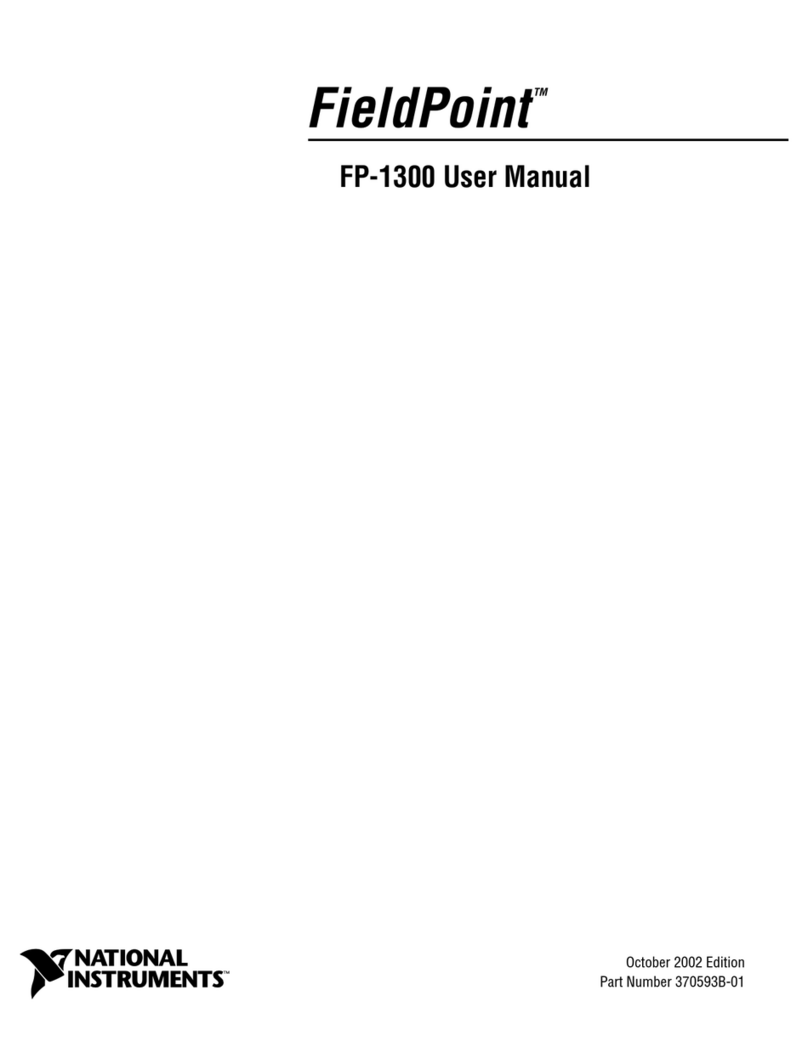
National Instruments
National Instruments FieldPoint FP-1300 user manual
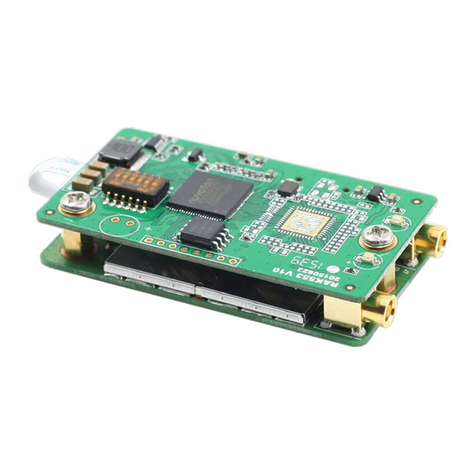
RAK
RAK RAK566 quick start guide
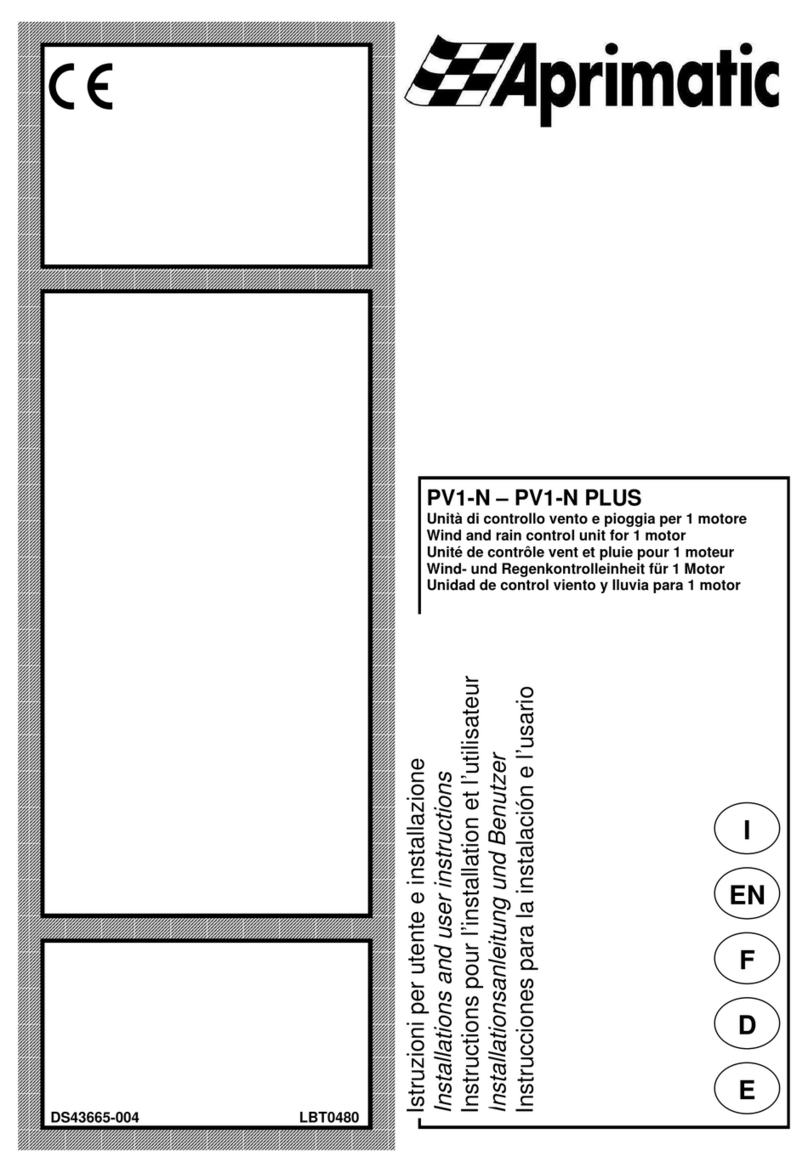
Aprimatic
Aprimatic PV1-N Installation and user instructions

Kessel
Kessel Comfort PLUS original operation manual
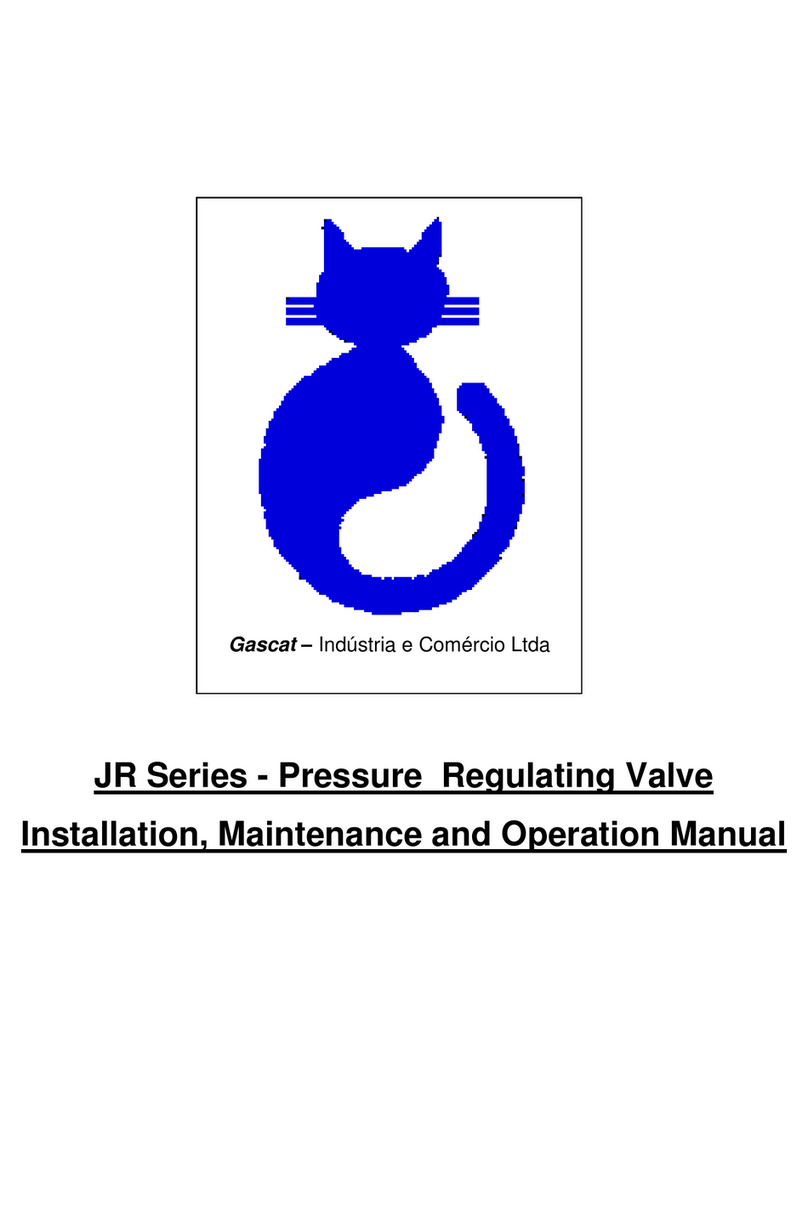
Gascat
Gascat JR Series Installation, maintenance and operation manual
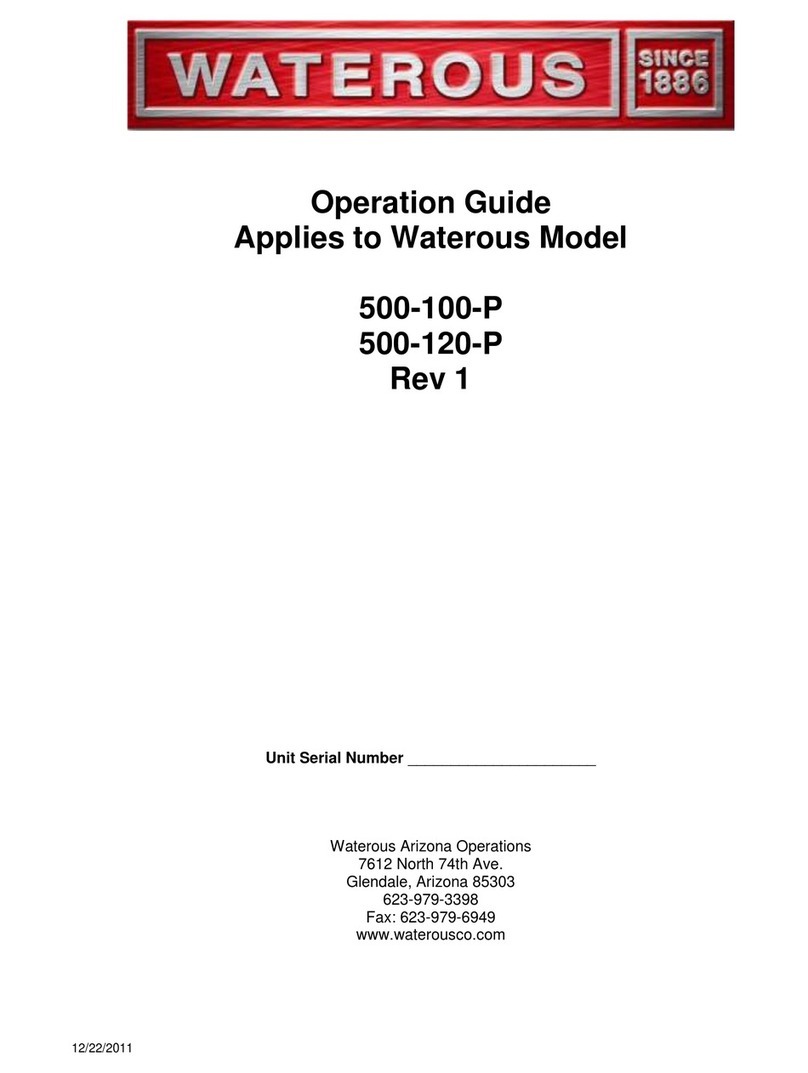
Waterous
Waterous 500-100-P Operation guide
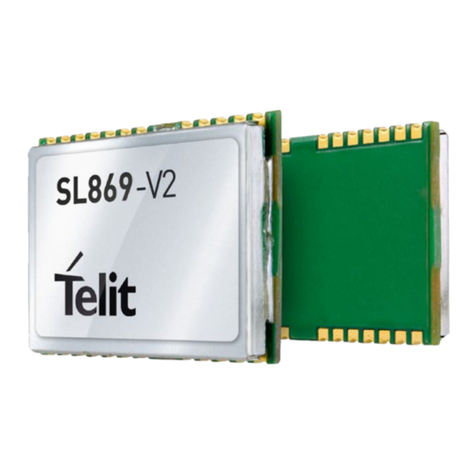
Telit Wireless Solutions
Telit Wireless Solutions SL869x-V2 Series Product user guide

elero
elero Aero-868 installation instructions
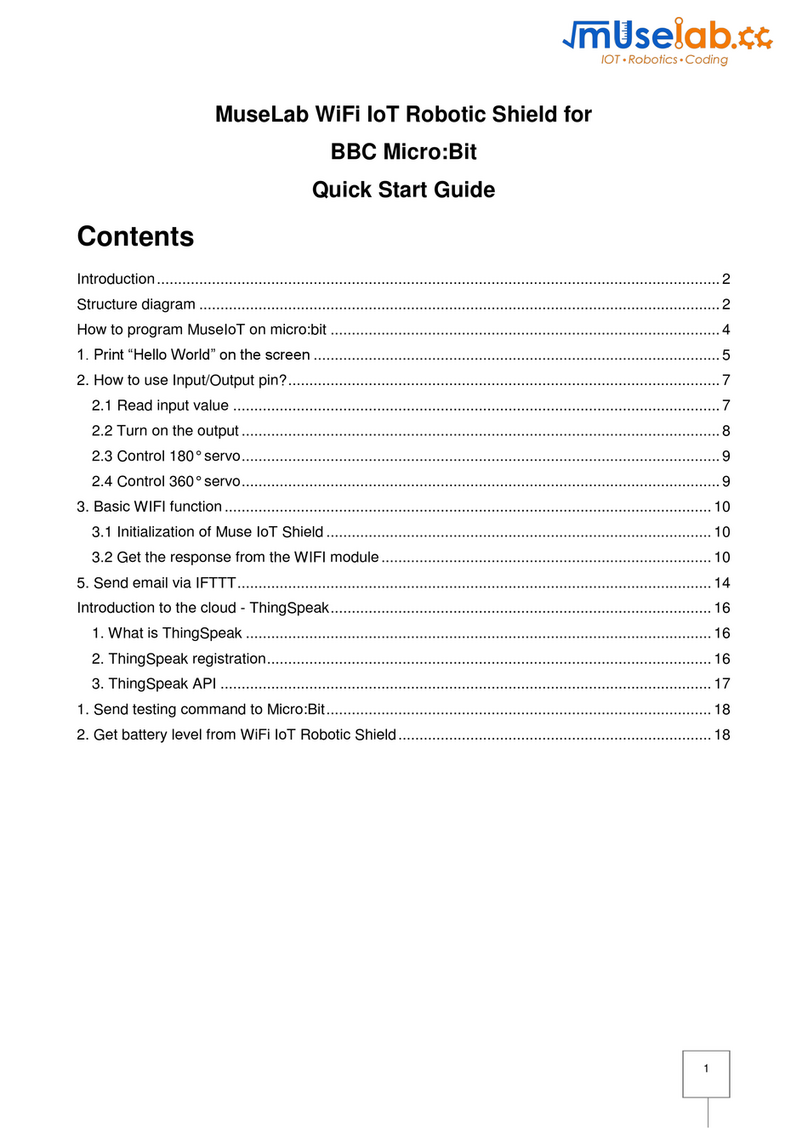
MuseLab
MuseLab WiFi IoT Robotic Shield quick start guide

Invacare
Invacare HomeFill HF2E540M9 Operator's manual