PPI Neuro 102EX User manual

Enhanced
Universal Process Controller
User Manual
Neuro 102EX

CONTENTS
User Manual
neuro 102EX
1. FRONT PANEL LAYOUT 1
2. BASIC OPERATION 3
3. SET-UP MODE ACCESS AND OPERATION 8
4. 10CONTROL PARAMETERS
5. ALARM PARAMETERS 12
6. CONFIGURATION PARAMETERS 14
7. SUPERVISORY PARAMETERS 17
8. 19PROFILE PARAMETERS
9. OP2 & OP3 FUNCTION PARAMETERS 22
10. USER LINEARISATION PARAMETERS 25
11. HARDWARE ASSEMBLY & CONFIGURATIONS 26
12. MECHANICAL INSTALLATION 31
13. ELECTRICAL CONNECTIONS 33
APPENDIX-A : MODBUS COMMUNICATION ADDRESSES 37

1
Figure 1.1
Upper Readout
Lower Readout
Enter Key
Up Key
Down Key
Page Key
Output-1 Status
Output-2 Status
Alarm-1 Status
Alarm-2 Status
PPI
neuro 102 EX
A/M CMD OPR PRF
OP1 OP2 MAN ASP
AL1 AL2 SBY PRF R/S Profile Status
Standby mode
Auxiliary SP mode
Manual control mode
Profile Key
Auto / Man Key
Command Key Operator Key
Ramp / Soak Status
Section 1
The controller front panel comprises of digital readouts, LED indicators and membrane keys as shown in Figure 1.1 below.
READOUTS
The Upper Readout is a 5 digit, 7-segment bright red LED display and usually displays the PV (Process Value). In Set-up
Mode, the Upper Readout displays parameter values/options.
The Lower Readout is a 5 digit, 7-segment bright green LED display and usually displays Setpoint Value. In Program Mode,
the Lower Readout displays the names (identifier tags) for the parameters.
INDICATORS
The front panel comprises 9 LED indicators that show the status related to control, alarm and operation mode. Refer Table 1.1
below for details.
Table 1.1
LED Status
Indicates Control Output-1 ON/OFF Status in Uni or Bi-Directional Control mode.
OP1
PRF
OP2
AL1
AL2
MAN
ASP
R/S
SBY
Indicates Control Output-2 ON/OFF Status in Bi-Directional Control mode.
• Flashes while the Ramp/Soak profile is in progress.
• Glows if profile is in PAUSE/ HOLD state.
• Remains OFF if profile is not in progress.
Flashes while Alarm-1 is active.
Flashes while Alarm-2 is active.
Glows if MANUAL control mode is active.
Glows if the Auxiliary Setpoint is active.
• Flashes while the Ramp (Setpoint changing) segment is in progress .
• Glows continuously while the Soak (Setpoint at rest) segment is in progress.
Flashes if STANDBY mode is active.
User Manual
neuro 102EX
FRONT PANEL LAYOUT

2
KEYS
There are eight tactile keys provided on the front panel for configuring the controller, setting-up the parameter values and
selecting Operation / Display Modes. Refer Table 1.2 below.
Table 1.2
Symbol Key Function
Press to enter or exit set-up mode.
PAGE
PRF
OPR
CMD
A/M
AUTO
MANUAL
(1)
COMMAND
DOWN
UP
ENTER
(1)
OPERATOR
(2)
PROFILE
Press to store the set parameter value and to scroll to the next
parameter on the PAGE.
Press to increase the parameter value. Pressing once increases
the value by one count; keeping pressed speeds up the change.
Press to decrease the parameter value. Pressing once decreases
the value by one count; keeping pressed speeds up the change.
Press to toggle between Auto or Manual Control Mode.
Press to access ‘Profile Run-Time Variables’.
Press to access ‘Operator-Page’ parameters.
Press to access parameters that are used as Commands.
(1) The parameters are listed and described in section 2 : Basic Operations
(2) The parameters are listed and described in section 8 : Profile Parameter
User Manual
neuro 102EX

3
BASIC OPERATION
POWER-UP
Upon power-up, all displays and indicators are lit on for approximately 3 seconds. This is followed by the indication of the
controller model name on the Upper Readout and the firmware version on the Lower Readout, for approx. 1
second.
MAIN DISPLAY MODE
After the Power-up display sequence, the Upper Readout starts showing the measured PV (Process Value) and the Lower
Readout displays the Setpoint Value. This is the MAIN Display Mode that shall be used most often.
% Output Power Indication
In PID control mode, the Lower Readout can be toggled using ENTER key to indicate either % output power or setpoint value
SP. The output power is indicated with the left most digit showing ‘P’, ‘H’ or ‘C’ depending upon uni-directional (Heat or Cool) or
bi-directional (Heat and Cool) control mode. Refer Figure 2.1 below.
Adjusting SP (Control Setpoint)
If permitted at Supervisory Level, the SP value can be directly adjusted on the Lower Readout in the MAIN Display Mode.
While the Lower Readout is showing SP value, step through the following sequence for adjusting the SP value :
1. Press and release UP or DOWN key once. The Lower Readout starts flashing.
2. Use UP/ DOWN keys to adjust the SP value.
3. Press and release ENTER key. The Lower Readout stops flashing and the new set value is registered and stored.
Figure 2.1
Heat or Cool Power
Uni-directional Control Bi-directional Control
Heat Power Cool Power
Tune Mode Indication
The Lower Readout flashes while the controller is Tuning. Do not disturb the process or alter any parameter values
while Tuning is in progress. The “Tune” message automatically disappears upon completion of Tuning procedure.
Profile Mode Indications
While a Profile Cycle is in progress, the front panel indicator ‘PRF’ flashes or glows steadily. The steady glowing indicates that
though the profile is active, it is currently in HOLD state. Also, the Lower Readout shows the Profile Setpoint (Ramping or
Soaking) instead of the control setpoint SP. The % Output Power (if PID Control) can be viewed by toggling the Lower Readout
using ENTER key.
Note :
While Profile Cycle is in progress, the Control Setpoint SP can still be adjusted on Lower Readout. While the Lower Readout shows Profile
Setpoint, use UP/DOWN keys to adjust the control setpoint SP as described earlier.
User Manual
neuro 102EX
Section 2

4
Table 2.1
PV above Max. Range
PV below Min. Range
Message Error Type Cause
Thermocouple / RTD broken
Sensor Open
Under-range
Over-range
CONTROL / ALARM STATUS UNDER PV ERROR CONDITIONS
a) The tuning, if in progress, is aborted.
b) The Profile Cycle, if in progress, enters in HOLD state.
c) Under Over-range or Under-range error condition, all the control outputs are switched off. However, under Sensor Open
error, the PID control output power depends upon the power - fail strategy and the user set default power value.
d) For Alarm activation, the under-range condition is treated as minimum PV, whereas the over-range and open conditions
are treated as maximum PV. Thus, Process High, positive Deviation Band and Window Band alarms activate under Over-
range/Open error. Similarly, Process Low, negative Deviation Band and Window Band alarms activate under Under-range
error.
• MANUAL MODE OPERATION
This operation mode is available only if the control action is PID and if the manual mode operation is permitted at supervisory
level. In this mode, the controller operates in Open loop mode wherein the % Output Power is manually adjusted by the
operator. This mode is often used for process start-up to make sure that the process equilibrium is achieved before the control
is transferred for subsequent automatic (closed loop) control. The controller ensures a bumpless Auto / Manual transfer.
The Manual mode can be activated or de-activated using A/M key. While in Manual mode, the Upper Readout shows PV while
the Lower Readout shows % Power that can be adjusted using UP/DOWN keys.
Pressing and Releasing A/M key switches the mode from Auto to Manual and vice-a-versa. While the controller is in Manual
mode the front panel indicator MAN glows. Use UP/DOWN keys to adjust the power. In Unidirectional mode, the Output Power
is adjustable between the set Power Low and Power High limits. However, in Bi-directional mode, the Output Power is
adjustable from -100% to +100%.The power range from -100% to 0 is Cool Power (with the leftmost digit indicating C) and 0 to
+100% is Heat Power (with the leftmost digit indicating H).
Notes:
1. If the Manual mode is activated while a Profile Cycle is in progress; the profile segment (Ramp or Soak) continues to run uninterrupted.
However, the % output power is in accordance with the user set value. The PV, thus may not follow the setpoint profile closely.
2. The Manual mode Activation / De-activation is suppressed while the Tuning is in progress. However, the Tuning procedure can be
activated regardless of whether the controller is in Auto or Manual control mode.
3. The Standby Mode (explained later in this section) over-rides the Manual control mode (if active).
4. If the power fails while the Manual Control Mode is active; upon resumption of power the controller continues to remain in Manual control
mode with the last user set power.
• STANDBY MODE
This mode allows the operator to put the controller in ‘indication-only’ mode wherein all the output control signals are forced
OFF while keeping the alarm system enabled. This may be desired prior to the start of a new process batch.
User Manual
neuro 102EX
PV Error Indications
The PV Error type is flashed on the Upper Readout. For different errors and the causes, refer Table 2.1 below.

5
If enabled at supervisory level, the standby mode can be activated or de-activated by setting the parameter ‘Standby’ to ‘Yes’
or ‘No’ respectively. The standby parameter can be accessed using the front panel ‘CMD’ key, explained later in this section.
The front panel indicator SBY flashes while the controller is in Standby mode.
Notes:
1. The Standby and Tuning modes are mutually exclusive. If Tune command is issued while the Standby mode is active, the controller exits
Standby mode and starts Tuning. Similarly, if Standby mode is activated while the controller is tuning, the controller aborts tuning
operation and enters Standby mode.
2. If the Power Supply to the controller is switched-off or a Power-failure occurs while the controller is operating in Standby mode; upon
resumption of power, the controller continues to operate in Standby mode.
OPERATOR PAGE AND PARAMETERS
The parameters that require frequent settings are organized on a separate page, called the Operator Page. The availability of
operator parameters is controlled at supervisory level and the parameter setting cannot be locked by the Master Lock.
Accessing Operator Page & Adjusting Parameters
Step through the following sequence to open the operator page and to adjust the operator parameter values.
1. Press and release ‘OPR’ key. The Lower Readout shows prompt for the first available operator parameter and the Upper
Readout shows value for the parameter.
2. Use UP / DOWN keys to adjust the value and then press ENTER key to store the set value and scroll to next parameter.
The controller automatically reverts to MAIN Display Mode upon scrolling through the last operator parameter. Alternatively,
use PAGE key to return to MAIN Display Mode.
Note:
The Operator Page can also be accessed through PAGE-0. (The pages and parameters are explained in next section).
The operator parameters are described in Table 2.2. Note that the parameters presented on Operator Page depend upon the
functions selected/enabled and supervisory level permissions.
The operator parameter list mainly includes :
a) Control Setpoint (SP) or Auxiliary Control Setpoint value.
b) Alarm-1 Setpoint / Band values.
c) Alarm-2 Setpoint / Band values.
Table 2.2
CONTROL SETPOINT
This is the Setpoint value that the controller respects for the
control purpose while it is not running a profile or not in standby /
tuning mode.
Parameter Description Settings
(Default Value)
Setpoint Low Limit to
Setpoint High Limit
(Default : -200.0)
User Manual
neuro 102EX

6
Parameter Description Settings
(Default Value)
0.3 to 999.9
(Default : 5.0)
-999.9 to 999.9
(Default : 5.0)
Throughout the range
for the selected Input Type
(Default :
For Process Low : -200.0
For Process High : 1376.0)
0.3 to 999.9
(Default : 5.0)
-999.9 to 999.9
(Default : 5.0)
Throughout the range
for the selected Input Type
(Default :
For Process Low : -200.0
For Process High : 1376.0)
ALARM-2 WINDOW BAND
Same as Alarm-2 Setpoint
ALARM-2 DEVIATION BAND
Same as Alarm-2 Setpoint
ALARM-2 SETPOINT
The setpoint / Band value (depending upon the type of Alarm) for
Alarm-2. This parameter is not available if the selected Alarm type
is ‘None’.
ALARM-1 WINDOW BAND
Same as Alarm-1 Setpoint
ALARM-1 DEVIATION BAND
Same as Alarm-1 Setpoint
ALARM-1 SETPOINT
The setpoint / Band value (depending upon the type of Alarm) for
Alarm-1. This parameter is not available if the selected Alarm type
is ‘None’.
‘COMMAND’ PAGE AND PARAMETERS
The parameters that the operator can use to control the Profile and Standby operation mode are called ‘Operator Commands’
and are accessible using the front panel CMD Key.
Step through the following sequence to access and issue the operator commands.
1. Press and release ‘CMD’ key. The Lower Readout shows prompt for the first available command parameter and the Upper
Readout displays ‘No’ or ‘Yes’.
2. Use UP / DOWN keys to select ‘Yes’ (for issuing/enabling a command) or ‘No’ (for disabling a command) and then press
ENTER key.
The controller reverts to MAIN Display Mode upon :
(a) Issuing a Command
(b) Scrolling through the last command parameter
(c) Pressing PAGE Key
User Manual
neuro 102EX
AUXILIARY CONTROL SETPOINT
The alternate control setpoint that the controller respects for
control purpose when selected through remote input terminals.
This parameter is available only if the parameter Auxiliary
Setpoint is enabled.
Setpoint Low Limit to
Setpoint High Limit
(Default : -200.0)

7
Parameter Description Settings
(Default Value)
Table 2.3
No
Yes
(Default : No)
No
Yes
(Default : No)
No
Yes
(Default : No)
No
Yes
(Default : No)
No
Yes
(Default : No)
No
Yes
(Default : No)
This parameter is available after end of the running Profile, if
Output-2(OP2) and/or Output-3(OP3) Relay/SSR is programmed
as an ‘End-Of-Profile’ signal. Set this parameter to ‘Yes’ to
acknowledge the alarm and to turn OFF the output.
END OF PROFILE ACKNOWLEDGE
These parameters are mutually exclusive. Use Start command to
commence a new Profile Cycle and Abort command to abort /
terminate a running Profile cycle. Set the value to ‘Yes’ to issue the
command. The Abort Command is available if permitted at
supervisory level.
PROFILE START COMMAND
These parameters are mutually exclusive. Use Start command to
commence a new Profile Cycle and Abort command to abort /
terminate a running Profile cycle. Set the value to ‘Yes’ to issue the
command. The Abort Command is available if permitted at
supervisory level.
PROFILE ABORT COMMAND
This parameter is available while a profile cycle is in progress and
can be used to Pause (halt) the profile as long as desired. Set the
command to ‘Yes’ for Pausing and ‘No’ to continue. Under Pause
state, the ramp segment stops ramping while the soak segment
stops counting down the timer. The Pause Command is available
if permitted at supervisory level.
PROFILE PAUSE COMMAND
Use this command to terminate a running profile segment and to
move to the next segment. Skipping the last segment will result in
completion of the current profile cycle. The Skip Command is
available if permitted at supervisory level.
SEGMENT SKIP COMMAND
This parameter is available and applicable only if Standby mode is
enabled at supervisory level. Set the parameter value to ‘Yes or
‘No’ for entering and exiting the Standby mode, respectively.
(DE)ACTIVATE STANDBY MODE
User Manual
neuro 102EX
Note:
The Command Parameters can also be accessed through PAGE-2. (The pages and parameters are explained in next section).
The command parameters are described in Table 2.3. Note that the commands available to the Operator depends upon the
feature selected and supervisory permission.
The command parameter list mainly includes :
a) Profile related commands like Start, Abort, Pause, Skip etc.
b) Standby mode entry / exit.

8
The various parameters are arranged in different groups, called PAGES, depending upon the functions they represent. Each
group is assigned a unique numeric value, called PAGE NUMBER, for its access.
The parameters are always presented in a fixed format: The Lower Readout displays the parameter prompt (Identification
Name) and the Upper Readout displays the set value. The parameters appear in the same sequence as listed in their
respective sections.
SET-UP MODE
The Set-up Mode allows the user to view and modify the parameter values. Follow the steps below for setting the parameter
values:
1. Press and release PAGE key. The Lower Readout shows PAGE and the Upper Readout shows page number 0. Refer
Figure 3.1.
2. Use UP / DOWN keys to set the desired PAGE NUMBER.
3. Press and release ENTER key. The Lower Readout shows the prompt for the first parameter listed in the set PAGE and the
Upper Readout shows its current value. If the entered PAGE NUMBER is invalid (contains no parameter list or any
associated function), the controller reverts to the MAIN Display Mode.
4. Press and release the ENTER key until the prompt for the required parameter appears on the Lower Readout. (The last
parameter in the list rolls back to the first parameter).
5. Use UP / DOWN keys to adjust the parameter value. (The display flashes if UP key is pressed after reaching the maximum
value or DOWN key is pressed after reaching the minimum value).
6. Press and release the ENTER key. The new value gets stored in the controller’s non-volatile memory and the next
parameter in the list is displayed.
SET-UP MODE : ACCESS AND OPERATION
The Figure 3.1 illustrates the example of altering the value for the parameter ‘Control Output’.
Notes
1. Each page contains a fixed list of parameters that are presented in a pre-determined sequence. Note however that
availability of a few parameters, called Conditional Parameters, depend upon the settings for some other parameters. For
example, the parameter ‘Control Hysteresis’ for Output-1 is available only if, the set value for the parameter ‘Control
Action’ is ‘On-Off’.
2. To exit the set-up mode and return to the MAIN Display Mode, press and release PAGE key.
3. If no key is pressed for approximately 30 seconds, the set-up mode times out and reverts to the MAIN Display Mode.
User Manual
neuro 102EX
Section 3
Press PAGE
key to enter
Set-up mode
Press ENTER
key to open
the Page
Use UP/DOWN
keys to set the
Page Number
MAIN Display
Mode
Default Page Page Number
Use UP/DOWN
keys to change
the value
Press ENTER key
to store the value &
move to next parameter
First Parameter
on PAGE-12
Next Parameter
on PAGE-12
New Parameter
value
Figure 3.1
or or

9
UnLocking
Repeat the Locking procedure twice for unlocking.
MASTER LOCKING
The controller facilitates locking all the PAGES (except Operator PAGE) by applying Master Lock Code. Under Locking, the
parameters are available for view only and cannot be adjusted. The Master Lock, however, does not lock the operator
parameters. This feature allows protecting the rather less frequently used parameters against any inadvertent changes while
making the frequently used operator parameters still available for any editing.
For enabling / disabling the Lock, step through the following sequence:
Locking
1. Press and release PAGE key while the controller is in the MAIN Display Mode. The Lower Readout shows PAGE and the
Upper Readout shows 0.
2. Use UP / DOWN keys to set the Page Number to 123 on the Upper Readout.
3. Press and release ENTER key. The controller returns to the MAIN Display Mode with the Lock enabled.
The Figure 3.2 below illustrates the Locking procedure.
User Manual
neuro 102EX
Figure 3.2
Press PAGE
key to enter
Set-up mode
Use UP/DOWN
keys to set the
‘Locking’ Code
Press ENTER key
to Lock & Return to
MAIN Mode
MAIN Mode
MAIN Mode
Default Page Locking Code
or

10
CONTROL PARAMETERS
Visit www.ppiindia.net for technical notes on CONTROL and TUNING for detailed understanding of the parameters /
terminologies used for describing control parameters in this section.
The parameters presented on PAGE-10 depend upon the type of algorithm selected for the control purpose, viz., On-Off,
Pulsed On-Off and PID. The parameter list further extends if the selected control mode is bi-directional (that is, heat-cool
control). Refer Table 4.1 for the parameter descriptions and settings.
Table 4.1
COOL CYCLE TIME
(Available for PID Control with bi-directional, that is, Heat-
Cool mode)
Sets the On + Off cycle time in seconds for time proportional
power output through Relay / SSR for OP2.
RELATIVE COOL GAIN
(Available for PID Control with bi-directional, that is, Heat-
Cool mode)
Sets the ratio of cooling power to the heating power.
CYCLE TIME
(Available for PID Control only)
Sets the total ‘On + Off’ time in seconds for time proportional
power output through Relay / SSR for OP1.
DERIVATIVE TIME
(Available for PID Control only)
Sets derivative time constant in seconds. Setting the value to 0,
cuts-off the derivative action.
INTEGRAL TIME
(Available for PID Control only)
Sets integral time constant in Seconds. Setting the value to 0,
cuts-off the integral action.
PROPORTIONAL BAND
(Available for PID Control only)
Sets proportional gain (% power per unit error). Defined in same
units and resolution as that for PV.
Parameter Description Settings
(Default Value)
0 to 600 Seconds
(Default : 16 sec.)
0 to 3600 Seconds
(Default : 100 sec.)
0.1 to 999.9 Units
(Default : 50.0)
0.5 to 100.0 Seconds
(in steps of 0.5 secs.)
(Default : 10.0 sec.)
0.1 to 10.0
(Default : 1.0)
0.5 to 100.0 Seconds
(in steps of 0.5 secs.)
(Default : 10.0 sec.)
1 to 999
or
0.1 to 999.9
(Default : 2.0)
HYSTERESIS
(Available for On-Off or Pulsed On-Off Control only)
Sets differential (dead) band between On-Off switching for OP1.
Pulse ON Time
to 120.0 Seconds
(Default : 2.0 sec.)
PULSE TIME
(Available for Pulsed On-Off Control only)
Sets the total ‘On + Off’ pulse time in seconds for Relay / SSR
output for OP1.
User Manual
neuro 102EX
Section 4

11
User Manual
neuro 102EX
COOL POWER HIGH
(Available for PID Control with bi-directional, that is, Heat-
Cool mode)
Sets the maximum % output power limit for OP2.
COOL POWER LOW
(Available for PID Control with bi-directional, that is, Heat-
Cool mode)
Sets the minimum % output power limit for OP2.
HEAT POWER HIGH
(Available for PID Control only)
Sets the maximum % output power limit for OP1 .
HEAT POWER LOW
(Available for PID Control only)
Sets the minimum % output power limit for OP1.
COOL (PULSE) ON TIME
(Available for On-Off or Pulsed On-Off Control with bi-
directional mode)
Sets the ON pulse time in seconds for Relay/SSR output for OP2.
COOL PULSE TIME
(Available for On-Off or Pulsed On-Off Control with bi-
directional mode)
Sets the total ‘On + Off’ pulse time in seconds for Relay / SSR
output for OP2.
COOL HYSTERESIS
(Available for On-Off or Pulsed On-Off Control with bi-
directional mode)
Sets differential (dead) band between On-Off switching for OP2.
(PULSE) ON TIME
(Available for Pulsed On-Off Control only)
Sets the ON pulse time in seconds for Relay/SSR output for OP1.
Parameter Description Settings
(Default Value)
1 to 999
or
0.1 to 999.9
(Default : 2.0)
Cool ON Time
to 120.0 Seconds
(Default : 2.0)
0.1 to Value set for
Cool Pulse Time
(Default : 1.0)
0 to Heat Power High
(Default : 0.0)
0.1 to Value set
for Pulse Time
(Default : 1.0)
Heat Power Low
to 100.0%
(Default : 100.0)
0 to Cool Power High
(Default : 0.0)
Cool Power Low
to 100.0%
(Default : 100.0)

12
ALARM PARAMETERS
Visit www.ppiindia.net for technical notes on ALARM for detailed understanding of the parameters / terminologies
used for describing the Alarm parameters in this section.
The parameters required for configuring Alarm-1 and Alarm-2 are grouped on PAGE-11. The configuration includes selecting
the type of Alarm, setting the hysteresis value, enabling / disabling start-up Alarm suppression, etc. Refer Table 5.1 for
parameter description & settings.
Table 5.1
ALARM-1 INHIBIT
Set to Yes to suppress Alarm-1 activation upon power-up or
process start-up.
ALARM-1 HYSTERESIS
Sets differential (dead) band between Alarm-1 switching ON and
OFF states.
ALARM-1 WINDOW BAND
(Available for Window Band Alarm-1 Type)
Sets symmetrical positive and negative deviation (offset) limits
from control setpoint for both High and Low Alarm-1 activation.
None
Process Low
Process High
Deviation Band
Window Band
(Default : None)
ALARM-1 TYPE
Select the Alarm-1 activation type. Selecting ‘None’ will disable
the alarm and suppress all the related parameters for Alarm-1.
ALARM-1 SETPOINT
(Available for Process High or Process Low Alarm-1 Type)
Sets Alarm limit independent of control setpoint.
ALARM-1 DEVIATION BAND
(Available for Deviation Band Alarm-1 Type)
Sets positive or negative deviation (offset) limit from control
setpoint for High or Low Alarm-1 activation, respectively.
Min. to Max. Range
specified for the
selected Input Type
(Default : Min or Max
Range)
Parameter Description Settings
(Default Value)
-999 to 999
or
-999.9 to 999.9
(Default : 5.0)
3 to 999
or
0.3 to 999.9
(Default : 5.0)
1 to 999
or
0.1 to 999.9
(Default : 2.0)
No
Yes
(Default : Yes)
User Manual
neuro 102EX
Section 5

13
User Manual
neuro 102EX
ALARM-2 INHIBIT
ALARM-2 HYSTERESIS
ALARM-2 WINDOW BAND
ALARM-2 DEVIATION BAND
Set to Yes to suppress Alarm-2 activation upon power-up or
process start-up.
Sets differential (dead) band between Alarm-2 switching ON and
OFF states.
(Available for Window Band Alarm-1 Type)
Sets symmetrical positive and negative deviation (offset) limits
from control setpoint for both High and Low Alarm-2 activation.
None
Process Low
Process High
Deviation Band
Window Band
(Default : None)
Select the Alarm-2 activation type. Selecting ‘None’ will disable
the alarm and suppress all the related parameters for Alarm-2.
(Available for Process High or Process Low Alarm-2 Type)
Sets Alarm limit independent of control setpoint.
(Available for Deviation Band Alarm-2 Type)
Sets positive or negative deviation (offset) limit from control
setpoint for High or Low Alarm-2 activation, respectively.
Min. to Max. Range
specified for the
selected Input Type
(Default : Min or Max
Range)
Parameter Description Settings
(Default Value)
-999 to 999
or
-999.9 to 999.9
(Default : 5.0)
3 to 999
or
0.3 to 999.9
(Default : 5.0)
1 to 999
or
0.1 to 999.9
(Default : 2.0)
No
Yes
(Default : Yes)
ALARM-2 SETPOINT
ALARM-2 TYPE

14
CONFIGURATION PARAMETERS
The controller is provided with a variety of hardware options and software features to cater to a host of applications. The
controller thus needs to be appropriately configured in terms of inputs / outputs and other features like control algorithm, digital
filter etc.
The PAGE-12 presents configuration parameters that are listed below in Table 6.1 .
Table 6.1
°C
°F
(Default : C)°
PV UNITS
(Available for Thermocouple / RTD Inputs)
Selects temperature measurement units in °C or °F.
Refer Table 6.2
(Default : 1)
PV RESOLUTION
(Not Available for Thermocouple Inputs)
Sets the process value indication resolution (decimal point). All
the resolution based parameters (control setpoint, hysteresis,
alarm setpoints etc.) then follow this resolution setting.
INPUT TYPE
Select Input type in accordance with the type of Thermocouple or
RTD, sensor or transducer output connected for process value
measurement. Ensure proper hardware jumper settings, if
required.
Direct
Reverse
(Default : Reverse)
On-Off
Pulse
PID
(Default : PID)
Relay
SSR
0 - 20mA
4 - 20mA
0 - 5V
0 - 10V
(Default : Relay)
CONTROL LOGIC
Select Reverse (heat logic) or Direct (cool logic).
CONTROL ACTION
Select appropriate Control Algorithm suited for process
requirement.
CONTROL OUTPUT (OP1) TYPE
Select the output type in accordance with the hardware
configuration for Output-1 (OP1).
Parameter Description Settings
(Default Value)
Refer Table 6.2
(Default : Type K)
User Manual
neuro 102EX
Section 6

15
SETPOINT LOW LIMIT
Sets minimum permissible control setpoint value.
(Default : -200.0)
Min. Range to
Setpoint High for the
selected Input Type
OFFSET FOR PV
This value is algebraically added to the measured PV to derive the
final PV that is displayed and compared for alarm / control.
Final PV = Measured PV + Offset
-1999 to 9999 or
-1999.9 to 9999.9
(Default : 0)
0.5 to 60.0 Seconds
(in steps of 0.5 Seconds)
(Default : 2.0 sec.)
SENSOR BREAK OUTPUT POWER
(Available for PID control only)
In case of Thermocouple / RTD broken or disconnected, the
controller outputs this power value under open loop condition.
0.0 to 100.0 or
-100.0 to 100.0
(Default : 0.0)
DIGITAL FILTER TIME CONSTANT
Sets the time constant, in seconds, for the low-pass digital filter
applied to the measured PV. The filter helps smoothing/averaging
the signal input and removing the undesired noise.
SETPOINT HIGH LIMIT
Sets maximum permissible control setpoint value.
Setpoint Low to
Max. Range for the
selected Input Type
(Default : 1376.0)
Parameter Description Settings
(Default Value)
-19999 to
PV Range High
(Default : 0.0)
PV Range Low to
99999
(Default : 100.0)
PV RANGE HIGH
(Available for DC Linear Inputs)
Sets process value corresponding to maximum DC Linear signal
input (e.g., 5V, 10V, 20mA, etc.)
PV RANGE LOW
(Available for DC Linear Inputs)
Sets process value corresponding to minimum DC Linear signal
input (e.g., 0V, 0mA, 4mA, etc.)
User Manual
neuro 102EX

16
User Manual
neuro 102EX
Resolution
Option What it means Range (Min. to Max. )
Type J Thermocouple
Type K Thermocouple
Type T Thermocouple
0.0 to +960°C / +32.0 0 to +1760.0°F
-200.0 to +1376.0°C / -328.0 to +2508.0°F
-200.0 to +385.0°C / -328.0 to +725.0°F
Type R Thermocouple
Type S Thermocouple
Type B Thermocouple
Type N Thermocouple
0.0 to +1770.0°C / +32.0 to +3218.0°F
0.0 to +1765.0°C / +32.0 to +3209.0°F
0.0 to +1825.0°C / +32.0 to +3092.0°F
0.0 to +1300.0°C / +32.0 to +2372.0°F
1 °C/°F
or
0.1 °C/°F
0 to 20mA DC current
4 to 20mA DC current
0 to 50mV DC voltage
0 to 200mV DC voltage
0 to 1.25V DC voltage
0 to 5.0V DC voltage
0 to 10.0V DC voltage
1 to 5.0V DC voltage
3-wire, RTD Pt100
-19999 to 30000 units
-199 to +600°C / -3280 to +1112°F
-199.9 to +600.0°C / -3280.0 to +1112.0°F
or
1 °C/°F
or
0.1 °C/°F
1
0.1
0.01
0.001
units
Table 6.2
Reserved for customer specific Thermocouple type not
listed above. The type shall be specified in accordance with
the ordered (optional on request) Thermocouple type.

17
SUPERVISORY PARAMETERS
The supervisory level responsibilities include exercising control over operator, making process related decisions and
controlling the availability of process data for remote use. The PAGE-13 parameters allow implementation of supervisory level
decisions. The Table 7.1 below list supervisory parameters.
Table 7.1
(Available for PID control with Overshoot Inhibit enabled )
This value governs the effectiveness of Overshoot inhibit feature
by controlling the brake applied to the PV rise or fall. Increase the
value if overshoot persist. Decrease the value if PV rise / fall has
slowed down considerably.
OVERSHOOT INHIBIT FACTOR
OVERSHOOT INHIBIT
(Available for PID control only)
Enabling this feature controls the PV rise or fall upon process
start-up in order to reach the control setpoint with as minimum
overshoot as possible.
SELF-TUNE COMMAND
Set to ‘Yes’ to initiate a new tuning cycle or set to ‘No’ to abort a
tuning operation in progress.
Parameter Description Settings
(Default Value)
Disable
Enable
(Default : Disable)
No
Yes
(Default : No)
1.0 to 2.0
(Default : 1.0)
RECORDER (RETRANSMISSION) OUTPUT
Supervisory permission for enabling recorder (retransmission)
output.
AUXILIARY SETPOINT
Supervisory permission for change-over from Main to Auxiliary
Setpoint and vice-a-versa.
Disable
Enable
(Default : Disable)
Disable
Enable
(Default : Disable)
SP ADJUSTMENT ON OPERATOR PAGE
Supervisory permission for control setpoint editing on Operator
Page. Set to ‘Enable’ for permission.
SP ADJUSTMENT ON LOWER READOUT
Supervisory permission for control setpoint editing on Lower
Readout. Set to ‘Enable’ for permission.
Disable
Enable
(Default : Enable)
Disable
Enable
(Default : Enable)
User Manual
neuro 102EX
Section 7

18
User Manual
neuro 102EX
4800
9600
19200
38400
57600
(Default : 9.6 )
None
Even
Odd
(Default : Even)
Parameter Description Settings
(Default Value)
ALARM SP ADJUSTMENT
ON OPERATOR PAGE
Supervisory permission for Alarm setpoint adjustments on
Operator Page. Set to ‘Enable’ for permission.
MANUAL MODE
Supervisory permission for Manual mode operation. Set to
‘Enable’ for permission.
Disable
Enable
(Default : Disable)
Disable
Enable
(Default : Disable)
PROFILE ABORT COMMAND
ON OPERATOR PAGE
Supervisory control over availability of Profile Abort command on
Operator Page. ‘Enable’ for availability.
STANDBY MODE
Supervisory control over availability of Standby command on
Operator Page. ‘Enable’ for availability.
Disable
Enable
(Default : Disable)
Disable
Enable
(Default : Disable)
1 to 127
(Default : 1)
COMMUNICATION WRITE ENABLE
Setting to ‘No’ disallows the host to set / modify any parameter
value. The host, however, can read the value.
CONTROLLER ID NUMBER
Unique numeric code assigned to the controller for identification
by the host. Set the value as required by the host.
COMMUNICATION PARITY
One of the communication error trapping features. Select the data
packet parity as implemented by the host protocol.
BAUD RATE
Communication speed in ‘Bits per Second’. Set the value to match
with the host baud rate.
No
Yes
(Default : No)
Table of contents
Other PPI Controllers manuals
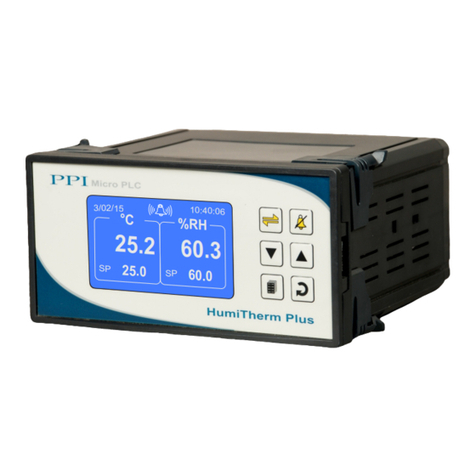
PPI
PPI HumiTherm Plus User manual
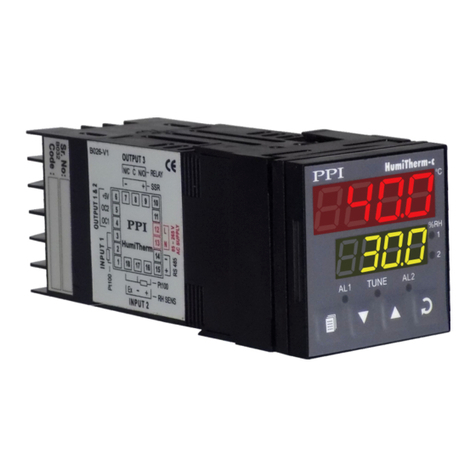
PPI
PPI HumiTherm-c Series User manual

PPI
PPI neuro 102Plus User manual
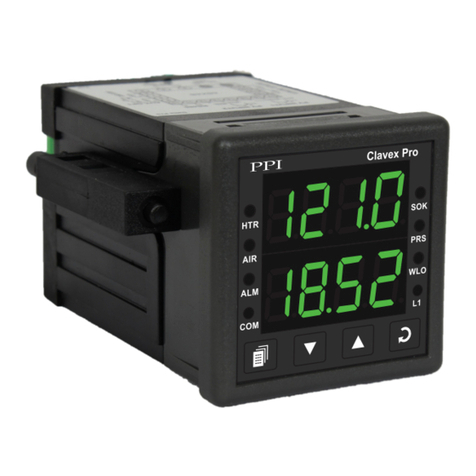
PPI
PPI Clavex Pro User manual
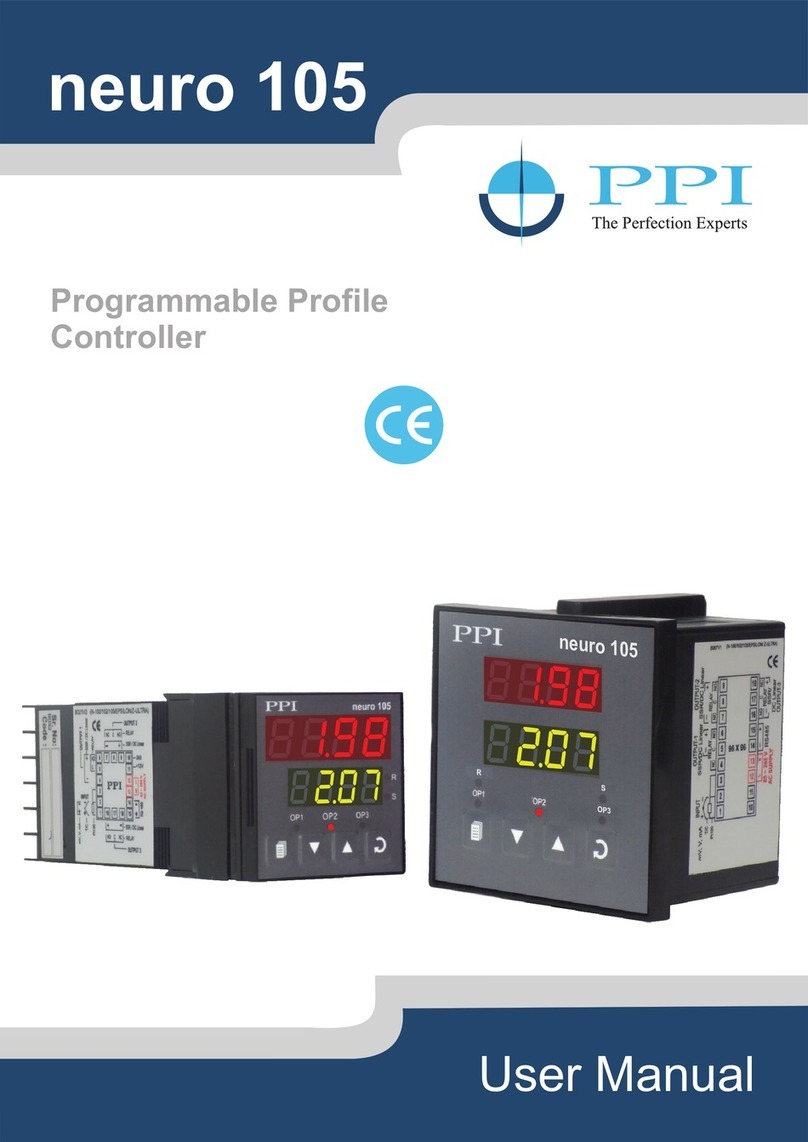
PPI
PPI neuro 105 User manual

PPI
PPI neuro 102 EX User manual
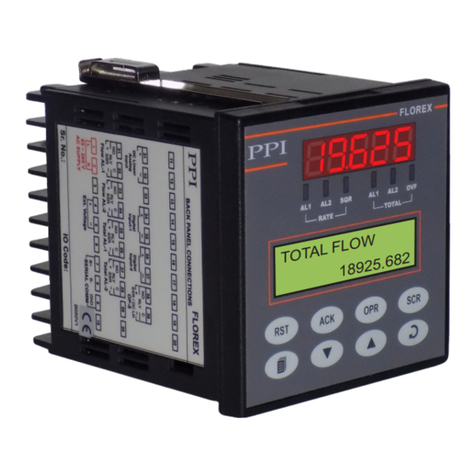
PPI
PPI FLOREX User manual
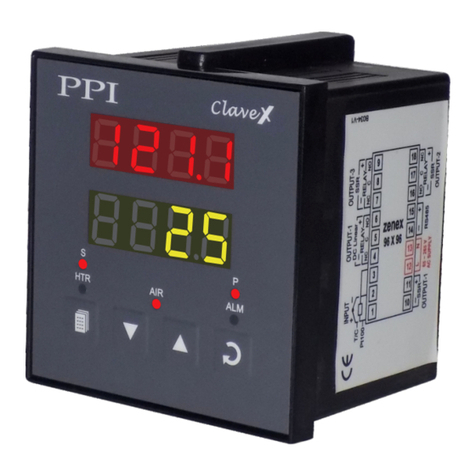
PPI
PPI claveX Series User manual
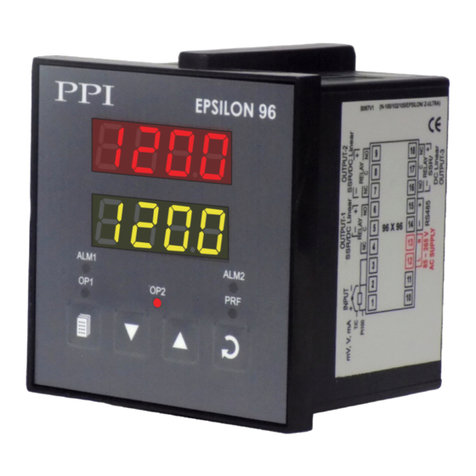
PPI
PPI Epsilon 48 User manual
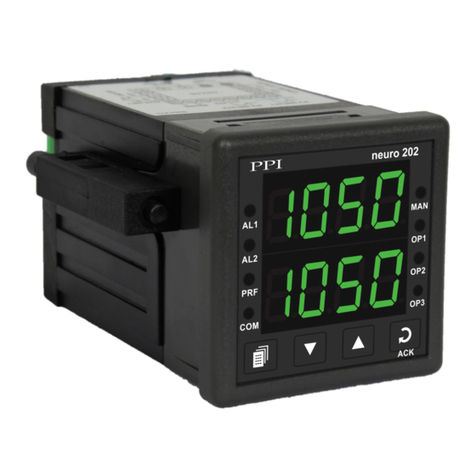
PPI
PPI neuro 202 User manual