ProJet HD3000 User manual

1. Table of Contents . . . . . . . . . . . . . . . . . . . . . . . . . . . . . . . . . . . . . . . . . . . . . . . . . . . . . . . . . . . . . . . . . . . . . . . . . . . . . . . . . . . . . . . . . . . . 3
1.1 01.0 Introduction . . . . . . . . . . . . . . . . . . . . . . . . . . . . . . . . . . . . . . . . . . . . . . . . . . . . . . . . . . . . . . . . . . . . . . . . . . . . . . . . . . . . . . . . 5
1.1.1 1.6 ProJet™ Systems Software . . . . . . . . . . . . . . . . . . . . . . . . . . . . . . . . . . . . . . . . . . . . . . . . . . . . . . . . . . . . . . . . . . . . . . . 5
1.1.2 1.1 About this Guide . . . . . . . . . . . . . . . . . . . . . . . . . . . . . . . . . . . . . . . . . . . . . . . . . . . . . . . . . . . . . . . . . . . . . . . . . . . . . . . . 5
1.1.3 1.2 Copyright . . . . . . . . . . . . . . . . . . . . . . . . . . . . . . . . . . . . . . . . . . . . . . . . . . . . . . . . . . . . . . . . . . . . . . . . . . . . . . . . . . . . . . 5
1.1.4 1.3 Useful Documents . . . . . . . . . . . . . . . . . . . . . . . . . . . . . . . . . . . . . . . . . . . . . . . . . . . . . . . . . . . . . . . . . . . . . . . . . . . . . . . 6
1.1.5 1.4 What's Inside . . . . . . . . . . . . . . . . . . . . . . . . . . . . . . . . . . . . . . . . . . . . . . . . . . . . . . . . . . . . . . . . . . . . . . . . . . . . . . . . . . . 6
1.1.6 1.5 Features and Benefits . . . . . . . . . . . . . . . . . . . . . . . . . . . . . . . . . . . . . . . . . . . . . . . . . . . . . . . . . . . . . . . . . . . . . . . . . . . . 6
1.1.6.1 1.5.1 Description and Definitions . . . . . . . . . . . . . . . . . . . . . . . . . . . . . . . . . . . . . . . . . . . . . . . . . . . . . . . . . . . . . . . . . . 8
1.1.7 1.7 Packaging . . . . . . . . . . . . . . . . . . . . . . . . . . . . . . . . . . . . . . . . . . . . . . . . . . . . . . . . . . . . . . . . . . . . . . . . . . . . . . . . . . . . . 9
1.2 02.0 Safety Symbols & Definitions . . . . . . . . . . . . . . . . . . . . . . . . . . . . . . . . . . . . . . . . . . . . . . . . . . . . . . . . . . . . . . . . . . . . . . . . . . 9
1.3 03.0 Safety Guidelines . . . . . . . . . . . . . . . . . . . . . . . . . . . . . . . . . . . . . . . . . . . . . . . . . . . . . . . . . . . . . . . . . . . . . . . . . . . . . . . . . . . 9
1.3.1 3.1 General . . . . . . . . . . . . . . . . . . . . . . . . . . . . . . . . . . . . . . . . . . . . . . . . . . . . . . . . . . . . . . . . . . . . . . . . . . . . . . . . . . . . . . . 10
1.3.2 3.2 Electrical . . . . . . . . . . . . . . . . . . . . . . . . . . . . . . . . . . . . . . . . . . . . . . . . . . . . . . . . . . . . . . . . . . . . . . . . . . . . . . . . . . . . . . 10
1.3.3 3.3 Ultraviolet (UV) Light . . . . . . . . . . . . . . . . . . . . . . . . . . . . . . . . . . . . . . . . . . . . . . . . . . . . . . . . . . . . . . . . . . . . . . . . . . . . . 10
1.4 04.0 Build Material Safety . . . . . . . . . . . . . . . . . . . . . . . . . . . . . . . . . . . . . . . . . . . . . . . . . . . . . . . . . . . . . . . . . . . . . . . . . . . . . . . . . 11
1.4.1 4.1 Disposal . . . . . . . . . . . . . . . . . . . . . . . . . . . . . . . . . . . . . . . . . . . . . . . . . . . . . . . . . . . . . . . . . . . . . . . . . . . . . . . . . . . . . . . 11
1.4.2 4.2 Health Hazards . . . . . . . . . . . . . . . . . . . . . . . . . . . . . . . . . . . . . . . . . . . . . . . . . . . . . . . . . . . . . . . . . . . . . . . . . . . . . . . . . 12
1.4.3 4.3 Material Handling . . . . . . . . . . . . . . . . . . . . . . . . . . . . . . . . . . . . . . . . . . . . . . . . . . . . . . . . . . . . . . . . . . . . . . . . . . . . . . . 13
1.4.4 4.4 Personal Protection Equipment . . . . . . . . . . . . . . . . . . . . . . . . . . . . . . . . . . . . . . . . . . . . . . . . . . . . . . . . . . . . . . . . . . . . . 13
1.4.5 4.5 Regulatory Information . . . . . . . . . . . . . . . . . . . . . . . . . . . . . . . . . . . . . . . . . . . . . . . . . . . . . . . . . . . . . . . . . . . . . . . . . . . 14
1.4.6 4.6 Spilled VisiJet® Material . . . . . . . . . . . . . . . . . . . . . . . . . . . . . . . . . . . . . . . . . . . . . . . . . . . . . . . . . . . . . . . . . . . . . . . . . . 14
1.4.7 4.7 Waste Removal . . . . . . . . . . . . . . . . . . . . . . . . . . . . . . . . . . . . . . . . . . . . . . . . . . . . . . . . . . . . . . . . . . . . . . . . . . . . . . . . . 14
1.4.8 4.8 Material Storage . . . . . . . . . . . . . . . . . . . . . . . . . . . . . . . . . . . . . . . . . . . . . . . . . . . . . . . . . . . . . . . . . . . . . . . . . . . . . . . . 15
1.5 05.0 System Requirements . . . . . . . . . . . . . . . . . . . . . . . . . . . . . . . . . . . . . . . . . . . . . . . . . . . . . . . . . . . . . . . . . . . . . . . . . . . . . . . . 16
1.6 06.0 Familiarization . . . . . . . . . . . . . . . . . . . . . . . . . . . . . . . . . . . . . . . . . . . . . . . . . . . . . . . . . . . . . . . . . . . . . . . . . . . . . . . . . . . . . . 16
1.6.1 6.1 System Functions . . . . . . . . . . . . . . . . . . . . . . . . . . . . . . . . . . . . . . . . . . . . . . . . . . . . . . . . . . . . . . . . . . . . . . . . . . . . . . . 18
1.7 07.0 Modeler Setup . . . . . . . . . . . . . . . . . . . . . . . . . . . . . . . . . . . . . . . . . . . . . . . . . . . . . . . . . . . . . . . . . . . . . . . . . . . . . . . . . . . . . . 18
1.7.1 7.1 Power on Modeler . . . . . . . . . . . . . . . . . . . . . . . . . . . . . . . . . . . . . . . . . . . . . . . . . . . . . . . . . . . . . . . . . . . . . . . . . . . . . . . 19
1.7.2 7.2 Add Cartridge and Install Build Platform . . . . . . . . . . . . . . . . . . . . . . . . . . . . . . . . . . . . . . . . . . . . . . . . . . . . . . . . . . . . . . 20
1.7.3 7.3 Install and Run ProJet™ 3-D Modeling Client Software . . . . . . . . . . . . . . . . . . . . . . . . . . . . . . . . . . . . . . . . . . . . . . . . . . 21
1.7.4 7.4 Create STL File(s) to Build . . . . . . . . . . . . . . . . . . . . . . . . . . . . . . . . . . . . . . . . . . . . . . . . . . . . . . . . . . . . . . . . . . . . . . . . 23
1.7.5 7.5 Submit Test Build . . . . . . . . . . . . . . . . . . . . . . . . . . . . . . . . . . . . . . . . . . . . . . . . . . . . . . . . . . . . . . . . . . . . . . . . . . . . . . . 24
1.7.6 7.6 Build Demo . . . . . . . . . . . . . . . . . . . . . . . . . . . . . . . . . . . . . . . . . . . . . . . . . . . . . . . . . . . . . . . . . . . . . . . . . . . . . . . . . . . . 25
1.8 08.0 Operations . . . . . . . . . . . . . . . . . . . . . . . . . . . . . . . . . . . . . . . . . . . . . . . . . . . . . . . . . . . . . . . . . . . . . . . . . . . . . . . . . . . . . . . . . 25
1.8.1 8.1 Preview Build Job . . . . . . . . . . . . . . . . . . . . . . . . . . . . . . . . . . . . . . . . . . . . . . . . . . . . . . . . . . . . . . . . . . . . . . . . . . . . . . . 25
1.8.2 8.2 Save a Build Job . . . . . . . . . . . . . . . . . . . . . . . . . . . . . . . . . . . . . . . . . . . . . . . . . . . . . . . . . . . . . . . . . . . . . . . . . . . . . . . . 29
1.8.3 8.3 Submit a Build Job . . . . . . . . . . . . . . . . . . . . . . . . . . . . . . . . . . . . . . . . . . . . . . . . . . . . . . . . . . . . . . . . . . . . . . . . . . . . . . 30
1.8.3.1 8.3.1 Remove Build Platform . . . . . . . . . . . . . . . . . . . . . . . . . . . . . . . . . . . . . . . . . . . . . . . . . . . . . . . . . . . . . . . . . . . . . 35
1.8.4 8.4 Manage Build Jobs . . . . . . . . . . . . . . . . . . . . . . . . . . . . . . . . . . . . . . . . . . . . . . . . . . . . . . . . . . . . . . . . . . . . . . . . . . . . . . 35
1.8.4.1 8.4.1 Delete Build Jobs . . . . . . . . . . . . . . . . . . . . . . . . . . . . . . . . . . . . . . . . . . . . . . . . . . . . . . . . . . . . . . . . . . . . . . . . . 37
1.8.4.2 8.4.2 Pause Build Job . . . . . . . . . . . . . . . . . . . . . . . . . . . . . . . . . . . . . . . . . . . . . . . . . . . . . . . . . . . . . . . . . . . . . . . . . . 38
1.8.4.3 8.4.3 Abort Build Job . . . . . . . . . . . . . . . . . . . . . . . . . . . . . . . . . . . . . . . . . . . . . . . . . . . . . . . . . . . . . . . . . . . . . . . . . . . 39
1.8.4.4 8.4.4 Repeat Build Job . . . . . . . . . . . . . . . . . . . . . . . . . . . . . . . . . . . . . . . . . . . . . . . . . . . . . . . . . . . . . . . . . . . . . . . . . 40
1.8.5 8.5 Modeler Status . . . . . . . . . . . . . . . . . . . . . . . . . . . . . . . . . . . . . . . . . . . . . . . . . . . . . . . . . . . . . . . . . . . . . . . . . . . . . . . . . 41
1.8.6 8.6 Empty Waste Drawer . . . . . . . . . . . . . . . . . . . . . . . . . . . . . . . . . . . . . . . . . . . . . . . . . . . . . . . . . . . . . . . . . . . . . . . . . . . . 41
1.8.7 8.7 Shutdown Modeler . . . . . . . . . . . . . . . . . . . . . . . . . . . . . . . . . . . . . . . . . . . . . . . . . . . . . . . . . . . . . . . . . . . . . . . . . . . . . . 42
1.8.8 8.8 Remove Part from Build Platform . . . . . . . . . . . . . . . . . . . . . . . . . . . . . . . . . . . . . . . . . . . . . . . . . . . . . . . . . . . . . . . . . . . 44
1.8.9 8.9 3D Modeling Batch Submission for Production Environment . . . . . . . . . . . . . . . . . . . . . . . . . . . . . . . . . . . . . . . . . . . . . . 44
1.8.10 8.10 Shrink Compensation for ProJet VisiJet® Materials . . . . . . . . . . . . . . . . . . . . . . . . . . . . . . . . . . . . . . . . . . . . . . . . . . . 50
1.9 09.0 Maintenance . . . . . . . . . . . . . . . . . . . . . . . . . . . . . . . . . . . . . . . . . . . . . . . . . . . . . . . . . . . . . . . . . . . . . . . . . . . . . . . . . . . . . . . 51
1.9.1 9.1 Cleaning Surfaces . . . . . . . . . . . . . . . . . . . . . . . . . . . . . . . . . . . . . . . . . . . . . . . . . . . . . . . . . . . . . . . . . . . . . . . . . . . . . . . 51
1.9.2 9.2 Cleaning the Waste Drawer . . . . . . . . . . . . . . . . . . . . . . . . . . . . . . . . . . . . . . . . . . . . . . . . . . . . . . . . . . . . . . . . . . . . . . . 52
1.9.3 9.3 Preventive Maintenance . . . . . . . . . . . . . . . . . . . . . . . . . . . . . . . . . . . . . . . . . . . . . . . . . . . . . . . . . . . . . . . . . . . . . . . . . . 53
1.9.4 9.4 Return Modeler for Repair . . . . . . . . . . . . . . . . . . . . . . . . . . . . . . . . . . . . . . . . . . . . . . . . . . . . . . . . . . . . . . . . . . . . . . . . . 53
1.10 10.0 Error Messages . . . . . . . . . . . . . . . . . . . . . . . . . . . . . . . . . . . . . . . . . . . . . . . . . . . . . . . . . . . . . . . . . . . . . . . . . . . . . . . . . . . . 53
1.10.1 10.1 Build Messages . . . . . . . . . . . . . . . . . . . . . . . . . . . . . . . . . . . . . . . . . . . . . . . . . . . . . . . . . . . . . . . . . . . . . . . . . . . . . . . 54
1.10.2 10.2 Material Messages . . . . . . . . . . . . . . . . . . . . . . . . . . . . . . . . . . . . . . . . . . . . . . . . . . . . . . . . . . . . . . . . . . . . . . . . . . . . 54
1.10.3 10.3 Status and Message Lines . . . . . . . . . . . . . . . . . . . . . . . . . . . . . . . . . . . . . . . . . . . . . . . . . . . . . . . . . . . . . . . . . . . . . . 55
1.11 11.0 Troubleshooting . . . . . . . . . . . . . . . . . . . . . . . . . . . . . . . . . . . . . . . . . . . . . . . . . . . . . . . . . . . . . . . . . . . . . . . . . . . . . . . . . . . 57
1.11.1 11.1 Communication Errors . . . . . . . . . . . . . . . . . . . . . . . . . . . . . . . . . . . . . . . . . . . . . . . . . . . . . . . . . . . . . . . . . . . . . . . . . . 57
1.11.2 11.2 Head Maintenance Station Errors . . . . . . . . . . . . . . . . . . . . . . . . . . . . . . . . . . . . . . . . . . . . . . . . . . . . . . . . . . . . . . . . . 58
1.11.3 11.3 Material Feed and Waste System Errors . . . . . . . . . . . . . . . . . . . . . . . . . . . . . . . . . . . . . . . . . . . . . . . . . . . . . . . . . . . 58
1.11.4 11.4 Material Quality Guarantee Errors . . . . . . . . . . . . . . . . . . . . . . . . . . . . . . . . . . . . . . . . . . . . . . . . . . . . . . . . . . . . . . . . . 58
1.11.5 11.5 Material Waste Errors . . . . . . . . . . . . . . . . . . . . . . . . . . . . . . . . . . . . . . . . . . . . . . . . . . . . . . . . . . . . . . . . . . . . . . . . . . 59
1.11.6 11.6 Motion System Errors . . . . . . . . . . . . . . . . . . . . . . . . . . . . . . . . . . . . . . . . . . . . . . . . . . . . . . . . . . . . . . . . . . . . . . . . . . 59
1.11.7 11.7 UV Subsystem Errors . . . . . . . . . . . . . . . . . . . . . . . . . . . . . . . . . . . . . . . . . . . . . . . . . . . . . . . . . . . . . . . . . . . . . . . . . . 59
1.11.8 11.8 Vacuum Regulator Errors . . . . . . . . . . . . . . . . . . . . . . . . . . . . . . . . . . . . . . . . . . . . . . . . . . . . . . . . . . . . . . . . . . . . . . . 60
1.11.9 11.9 Power Outage . . . . . . . . . . . . . . . . . . . . . . . . . . . . . . . . . . . . . . . . . . . . . . . . . . . . . . . . . . . . . . . . . . . . . . . . . . . . . . . . 60
1.12 12.0 Finishing . . . . . . . . . . . . . . . . . . . . . . . . . . . . . . . . . . . . . . . . . . . . . . . . . . . . . . . . . . . . . . . . . . . . . . . . . . . . . . . . . . . . . . . . . 61
1.13 13.0 Projet™ Spare Parts List . . . . . . . . . . . . . . . . . . . . . . . . . . . . . . . . . . . . . . . . . . . . . . . . . . . . . . . . . . . . . . . . . . . . . . . . . . . . . 61
1.13.1 13.1 Consumables and Replacement Modules . . . . . . . . . . . . . . . . . . . . . . . . . . . . . . . . . . . . . . . . . . . . . . . . . . . . . . . . . . . 61
1.14 14.0 Other Documents . . . . . . . . . . . . . . . . . . . . . . . . . . . . . . . . . . . . . . . . . . . . . . . . . . . . . . . . . . . . . . . . . . . . . . . . . . . . . . . . . . 61
1.14.1 14.1 Parts Finisher User Guide . . . . . . . . . . . . . . . . . . . . . . . . . . . . . . . . . . . . . . . . . . . . . . . . . . . . . . . . . . . . . . . . . . . . . . . 61
1.14.2 14.2 Material Safety Data Sheets (MSDS) . . . . . . . . . . . . . . . . . . . . . . . . . . . . . . . . . . . . . . . . . . . . . . . . . . . . . . . . . . . . . . 61

1.14.3 14.3 Projet™ Quick Reference Guide . . . . . . . . . . . . . . . . . . . . . . . . . . . . . . . . . . . . . . . . . . . . . . . . . . . . . . . . . . . . . . . . . . 61
1.14.4 14.4 Facility Requirements Guide . . . . . . . . . . . . . . . . . . . . . . . . . . . . . . . . . . . . . . . . . . . . . . . . . . . . . . . . . . . . . . . . . . . . . 61
1.14.5 14.5 VisiJet® Material Handling and Post-Processing Guide . . . . . . . . . . . . . . . . . . . . . . . . . . . . . . . . . . . . . . . . . . . . . . . . 62
1.15 15.0 Service and Support . . . . . . . . . . . . . . . . . . . . . . . . . . . . . . . . . . . . . . . . . . . . . . . . . . . . . . . . . . . . . . . . . . . . . . . . . . . . . . . . 62
1.15.1 15.1 Contacts . . . . . . . . . . . . . . . . . . . . . . . . . . . . . . . . . . . . . . . . . . . . . . . . . . . . . . . . . . . . . . . . . . . . . . . . . . . . . . . . . . . . 62
1.15.2 15.2 How to Order Parts . . . . . . . . . . . . . . . . . . . . . . . . . . . . . . . . . . . . . . . . . . . . . . . . . . . . . . . . . . . . . . . . . . . . . . . . . . . . 62
1.16 16.0 Online Help . . . . . . . . . . . . . . . . . . . . . . . . . . . . . . . . . . . . . . . . . . . . . . . . . . . . . . . . . . . . . . . . . . . . . . . . . . . . . . . . . . . . . . . 62
1.16.1 16.1 Frequently Asked Questions (FAQ) . . . . . . . . . . . . . . . . . . . . . . . . . . . . . . . . . . . . . . . . . . . . . . . . . . . . . . . . . . . . . . . 62
1.16.2 16.2 Getting Help . . . . . . . . . . . . . . . . . . . . . . . . . . . . . . . . . . . . . . . . . . . . . . . . . . . . . . . . . . . . . . . . . . . . . . . . . . . . . . . . . 64
1.16.3 16.3 Build Material . . . . . . . . . . . . . . . . . . . . . . . . . . . . . . . . . . . . . . . . . . . . . . . . . . . . . . . . . . . . . . . . . . . . . . . . . . . . . . . . . 64
1.16.4 16.4 Modeler Hardware and Installation . . . . . . . . . . . . . . . . . . . . . . . . . . . . . . . . . . . . . . . . . . . . . . . . . . . . . . . . . . . . . . . . 64
1.16.5 16.5 Facility Requirements . . . . . . . . . . . . . . . . . . . . . . . . . . . . . . . . . . . . . . . . . . . . . . . . . . . . . . . . . . . . . . . . . . . . . . . . . . 65
1.17 17.0 Glossary of Terms . . . . . . . . . . . . . . . . . . . . . . . . . . . . . . . . . . . . . . . . . . . . . . . . . . . . . . . . . . . . . . . . . . . . . . . . . . . . . . . . . . 65
1.18 18.0 Index . . . . . . . . . . . . . . . . . . . . . . . . . . . . . . . . . . . . . . . . . . . . . . . . . . . . . . . . . . . . . . . . . . . . . . . . . . . . . . . . . . . . . . . . . . . . 65

Table of Contents
01.0 Introduction
1.1 About this Guide
1.2 Copyright
1.3 Useful Documents
1.4 What's Inside
1.5 Features and Benefits
1.5.1 Description and Definitions
1.6 ProJet™ Systems Software
1.7 Packaging
02.0 Safety Symbols & Definitions
03.0 Safety Guidelines
3.1 General
3.2 Electrical
3.3 Ultraviolet (UV) Light
04.0 Build Material Safety
4.1 Disposal
4.2 Health Hazards
4.3 Material Handling
4.4 Personal Protection Equipment
4.5 Regulatory Information
4.6 Spilled VisiJet® Material
4.7 Waste Removal
4.8 Material Storage
05.0 System Requirements
06.0 Familiarization
6.1 System Functions
07.0 Modeler Setup
7.1 Power on Modeler
7.2 Add Cartridge and Install Build Platform
7.3 Install and Run ProJet™ 3-D Modeling Client Software
7.4 Create STL File(s) to Build
7.5 Submit Test Build
7.6 Build Demo
08.0 Operations
8.10 Shrink Compensation for ProJet VisiJet® Materials
8.1 Preview Build Job
8.2 Save a Build Job
8.3 Submit a Build Job
8.3.1 Remove Build Platform
8.4 Manage Build Jobs
8.4.1 Delete Build Jobs

8.4.2 Pause Build Job
8.4.3 Abort Build Job
8.4.4 Repeat Build Job
8.5 Modeler Status
8.6 Empty Waste Drawer
8.7 Shutdown Modeler
8.8 Remove Part from Build Platform
8.9 3D Modeling Batch Submission for Production Environment
09.0 Maintenance
9.1 Cleaning Surfaces
9.2 Cleaning the Waste Drawer
9.3 Preventive Maintenance
9.4 Return Modeler for Repair
10.0 Error Messages
10.1 Build Messages
10.2 Material Messages
10.3 Status and Message Lines
11.0 Troubleshooting
11.1 Communication Errors
11.2 Head Maintenance Station Errors
11.3 Material Feed and Waste System Errors
11.4 Material Quality Guarantee Errors
11.5 Material Waste Errors
11.6 Motion System Errors
11.7 UV Subsystem Errors
11.8 Vacuum Regulator Errors
11.9 Power Outage
12.0 Finishing
13.0 Projet™ Spare Parts List
13.1 Consumables and Replacement Modules
14.0 Other Documents
14.1 Parts Finisher User Guide
14.2 Material Safety Data Sheets (MSDS)
14.3 Projet™ Quick Reference Guide
14.4 Facility Requirements Guide
14.5 VisiJet® Material Handling and Post-Processing Guide
15.0 Service and Support
15.1 Contacts
15.2 How to Order Parts
16.0 Online Help
16.1 Frequently Asked Questions (FAQ)
16.2 Getting Help
16.3 Build Material
16.4 Modeler Hardware and Installation
16.5 Facility Requirements

17.0 Glossary of Terms
18.0 Index
01.0 Introduction
Thank you for purchasing ProJet™ 3-D modeler system. We pride ourselves in our ability to offer customers three dimensional modeling
solutions. The 3D System team is confident your system will provide many years of service.
1.1 About this Guide
1.2 Copyright
1.3 Useful Documents
1.4 What's Inside
1.5 Features and Benefits
1.5.1 Description and Definitions
1.6 ProJet™ Systems Software
1.7 Packaging
1.6 ProJet™ Systems Software
To install ProJet™ series upgrades, click on to download the software and the software release notes that provideProJet™ Systems Software
detailed installation instructions.
1.1 About this Guide
This guide describes how to create finished parts using the ProJet™ 3-D Modeler. It also provides user's with an understanding of key features,
system requirements, and operating procedures.
Should additional questions arise, consult Section of this guide. If further assistance required, contact 3D Systems11.0 Troubleshooting
or visit Web Site.Technical Support http://www.3dsystems.com/
1.2 Copyright
© 2011 by 3D Systems, Inc. All rights reserved. Subject to change without notice. This document is copyrighted and contains proprietary
information that is the property of 3D Systems, Inc. The licensed user, in the name of whom this document is registered (the "Licensed User")
does not have the right to copy, reproduce, or translate this document in any way or to any media without the prior written consent of 3D Systems,
Inc. No copies of the document may be sold or given to any person or other entity.
ProJet™is a trademark and the 3D logo and VisiJet® are registered trademarks of 3D Systems, Inc.
Improvements
3D Systems may (but shall not be obligated to) make improvements to this document from time to time. However, the Licensed User
acknowledges that at any time after the expiration of the date of issuance, 3D Systems may institute a periodic charge or fee payable by the
Licensed User in return for ongoing receipt of improvements. It is the responsibility of the Licensed User to provide 3D Systems with current
information as to its name and address. The Licensed User also undertakes to notify 3D Systems promptly in the event that it considers any of the
data contained in this document to be incomplete or erroneous in any respect, in connection with Licensed User's particular use or generally.
FCC Notice
This equipment has been tested and found to comply with the limits for a class A digital device, pursuant to Part 15 of the FCC Rules. These limits
are designed to provide reasonable protection against harmful interference when the equipment is operated in a commercial environment. This
equipment generates, uses, and can radiate radio frequency energy and, if not installed and used in accordance with the instruction manual, may
cause harmful interference to radio communications. Operation of this equipment in a residential area is likely to cause harmful interference in
which case the user will be required to correct the interference at his own expense.
Changes or modifications not expressly approved by 3D Systems could void your authority to operate this equipment.
Limitations of Warranty and Liability
This information is provided by 3D Systems for the convenience of its customers. It is believed to be reliable, but NO REPRESENTATIONS,
GUARANTEES, OR WARRANTIES OF ANY KIND ARE MADE AS TO ITS ACCURACY, FITNESS FOR A PARTICULAR USE, OR THE

RESULTS TO BE OBTAINED THEREFROM. The information is based in whole or in large part on laboratory work and does not necessarily
indicate performance in all conditions. Notwithstanding any information provided by 3D Systems or its affiliates, the customer remains fully
responsible for determining which federal, state, or local laws or regulations, or industry practices are relevant to activities in which it engages, as
well as assuring that those laws, regulations, or standards are complied with under actual operating conditions, and 3D Systems undertakes no
responsibility in these areas.
IN NO EVENT WILL 3D Systems BE RESPONSIBLE FOR DAMAGES OF ANY NATURE, INCLUDING SPECIAL OR CONSEQUENTIAL
DAMAGES, RESULTING FROM THE USE OF OR RELIANCE UPON THIS INFORMATION. THE CUSTOMER ASSUMES ALL RISK
RESULTING FROM THE USE OF THIS INFORMATION. Customers use of the materials that follow is an acknowledgment of its agreement to
the foregoing. Any customer not wishing to be bound should return this material to 3D Systems. Nothing contained herein is to be considered as
permission, recommendation, nor as an inducement to practice any patented invention without permission of the patent owner.
1.3 Useful Documents
The documents listed below will help get the most out of your system, To access, click on the document title.
ProJet™ 3-D Modeling Client Online Help: Run the client software, select in the modelers window or in Build Preview windowHelp > Help Topics
to launch the client online help. The online help provide detailed instructions on how to use the client software to setup, run, and manage build
jobs.
PROJET 3-D Modelers Quick_Reference Guide.pdf: Download to have quick reference on the control panel functions, how to load / remove
cartridges, and how to run a test build.
VisiJet® Material Handling and Post-Processing Guide: This document has everything needed to guide you in safely handling and disposing of
VisiJet® material, including relevant regulatory guidelines for material disposal worldwide. It also provides information on how to clean parts once
the build process is completed.
. This guide provides the dimensional data that is required when the 3D System's FieldProjet™ 3-D Modelers Facility Requirements Guide
Service Engineer installs the modeler. Clck on the part number to view a copy for reference.
VisiJet® Material Safety Data Sheets (MSDS's): Ensure everyone who handles VisiJet™ materials is familiar with MSDS's and follows the safety
guidelines. To order extra copies of MSDS's, request the appropriate document part numbers are located on the bottom left-hand corner of the
MSDS.
1.4 What's Inside
Safety: Read prior to handling VisiJet® Materials or operating the modeler system. The safety sections inform you of handling the material
properly and avoid damage and injury when operating the modeler. For more detailed material safety information, refer to VisiJet® Material
Handling Guide.
System Requirements: Provides electrical requirements prior to plugging in your modeler for operation. For more detailed facility requirements
information, see the ProJet™ 3-D Modelers Facility Requirements Guide.
Familiarization: Provides a brief description of the modeler system.
Modeler Setup: Provides information on preparing the 3-D modeler for builds using the software, and how to send test and demo builds to the
modeler from your computer. Also refer to your online help for software instructions.
Operations: Describes loading and running the modeler; start and stop build jobs; monitor and control build jobs; unload build parts; and
disposing waste material.
Error Messges: Defines the error messages you may see on the modeler's LCD and provide the actions to take.
Finishing:Provides information on finishing models.
Maintenance: List modeler maintenance procedures which must be done to ensure high part yield and low modeler down time. Semi-annual
preventive maintenance requires a certified 3D Systems Technical Support Representative.
Troubleshooting: If problems occur with the modeler, look for solutions in this section first. It describes some common problems which can
occur and suggests corrective actions.
Technical Support: List of contact numbers of sale and support personnel for your modeler system.
1.5 Features and Benefits

prints precision, durable plastic parts ideal for functional testing, design communication,ProJet™ HD3000
rapid manufacturing, rapid tooling and more. It features selectable resolution choices for speed and quality.
High Definition(HD), Ultra High Definition (UHD)Printing Mode: : 298 x 185 x 203mm (11.75 x 7.3 x 8 inches); 127 x 178 xNet Build Volume (xyz): HD Mode UHD Mode:
152mm (5 x 7 x 6 inches) : 328 x 328 x 606 DPI (xyz); 40µ layers; : 656 x 656 x 800 DPI (xyz); 32µResolution (xyz): *HD Mode UHD Mode
layers : EX200, SR200, HR200; : S100VisiJet® Materials: Part Materials Support Material
features part stacking and nesting capability in both build modes. The user canPart Stacking and Nesting:
now utilize the entire build volume by stacking parts vertically in the z-direction to fill up the entire build envelop
with parts. The user can control the space between layers to minimize support material usage and build time.
Now, hours can be saved by stacking parts and submitting single, long builds overnight and weekends.
ProJet™ HD3000plus features a 60% expanded high definition build envelope and advanced print detail
output. A new 16 micron print resolution delivers exceptional hard plastic parts with unmatched micro-detail and
surface quality. High Definition (HD), Ultra High Definition (UHD), Xtreme High Definition (XHD)Printing Mode: : 298 x 185 x 203mm (11.75 x 7.3 x 8 inches); : 203 x 178 xNet Build Volume (xyz): HD Mode UHD Mode
152mm (8 x 7 x 6 inches);
: 203 x 178 x 152mm (8 x 7 x 6 inches)XHD Mode : 328 x 328 x 606 DPI; 40µ layers; : 656 x 656 x 800 DPI; 32µ layers;Resolution (xyz): HD Mode UHD Mode
: 656 x 656 x 1600 DPI ; 16µ layersXHD Mode : EX200, SR200, HR200; : S100VisiJet® Materials: Part Materials Support Material
Provides email notification to the user when their job begins, completes, aborts and if theEmail Notification:
system is low on material at any time during their build. Users can set their defaults and make changes as to
what emails they will receive via the Job Options window.
mass produces 100% wax patterns with unmatched surface quality, extreme fine detail andProJet™ CPX3000
exceptional precision. RealWax patterns are ideal for casting jewelry, apparel, micro-detail medical instruments
and devices, medical implants, electrical components, figurines, replicas, collectables and more.
High Definition(HD), Xtreme High Definition (XHD)Printing Mode: 298 x 185 x 203mm (11.75 x 7.3 x 8 inches); 127 x 178 xNet Build Volume (xyz): HD Mode: XHD Mode:
152mm (5 x 7 x 6 inches) : 328 x 328 x 700 DPI (xyz); 36µ layers; : 656 x 656 x 1600 DPI (xyz);Resolution (xyz): *HD Mode XHD Mode
16µ layers : CPX200 Wax; : S200VisiJet® Materials: Part Materials Support Material
features part stacking and nesting capability in both build modes. The user canPart Stacking and Nesting:
now utilize the entire build volume by stacking parts vertically in the z-direction to fill up the entire build envelop
with parts. The user can control the space between layers to minimize support material usage and build time.
Now, hours can be saved by stacking parts and submitting single, long builds overnight and weekends.
ProJet™ CPX3000plus features a 60% expanded high definition build envelope with up to 20% increased print
speed. A new 20 micron high resolution option delivers exceptional wax patterns with smooth surface quality
and fine feature detail in less time.
High Definition (HD), Ultra High Definition (UHD), Xtreme High Definition (XHD)Printing Mode: : 298 x 185 x 203 (11.75 x 7.3 x 8 inches); : 203 x 178 x 152mmNet Build Volume (xyz): HD Mode UHD Mode
(8 x 7 x 6 inches);
: 203 x 178 x 152mm (8 x 7 x 6 inches)XHD Mode : 328 x 328 x 700 DPI (xyz); 36µ layers; : 656 x 656 x 1300 DPI; 20µResolution (xyz): HD Mode UHD Mode
layers; : 656 x 656 x 1600 DPI, 16µ layersXHD Mode : CPX200 Wax; : S200VisiJet® Materials: Part Materials Support Material
Provides email notification to the user when their job begins, completes, aborts and if theEmail Notification:
system is low on material at any time during their build. Users can set their defaults and make changes as to
what emails they will receive via the Job Options window.
ProJet™ CP3000 mass produces 100% wax patterns with smooth surface quality and exceptional precision,
supporting almost unlimited applications capabilities. RealWax patterns are ideal for general foundry casting
applications such as medium-sized to large mechanical parts for engines, pneumatics, aerospace, energy
production and delivery, custom manufacturing equipment, restorations and other heavy equipment.
298 x 185 x 203mm (11.75 x 7.3 x 8 inches)Net Build Volume (xyz):
328 x 328 x 700 DPI; 36µ layersResolution (xyz): : CP200 Wax; : S200VisiJet® Materials: Part Materials Support Material
features part stacking and nesting capability in both build modes. The user canPart Stacking and Nesting:
now utilize the entire build volume by stacking parts vertically in the z-direction to fill up the entire build envelop
with parts. The user can control the space between layers to minimize support material usage and build time.
Now, hours can be saved by stacking parts and submitting single, long builds overnight and weekends.

ProJet™ SD3000 prints high definition, durable plastic parts for engineering and mechanical design
applications including functional testing, form and fit verification, rapid prototyping, design communication, rapid
tooling and more. 298 x 185 x 203mm (11.75 x 7.3 x 8 inches)Net Build Volume (xyz):
328 x 328 x 606 DPI (xyz)Resolution (xyz): : EX200 (natural) & SR200 (Blue, Natural & Gray); : S100VisiJet® Materials: Part Materials Support Material
ProJet™ DP3000 accurately, consistently and economically manufactures precision wax-ups for dental
professionals. The system can generate hundreds of units each cycle. The wax-ups have a smooth surface
finish and can be cast or pressed with conventional techniques. The large build volume and optional part
stacking and nesting capabilities enable unattended operation ideal for high-volume production.
High Definition (HD); Ultra High Definition (UHD)Printing Mode: 298 x 185 x 203mm (11.75 x 7.3 x 8 inches); 203 x 178 xNet Build Volume (xyz): HD Mode: UHD Mode:
152mm (8 x 7 x 6 inches) : 328 x 328 x 606 DPI; :328 x 328 x 606 DPIResolution (xyz): *HD Mode UHD Mode
: DP200; : S100VisiJet® Materials: Part Materials Support Material
Provides email notification to the user when their job begins, completes, aborts and if theEmail Notification:
system is low on material at any time during their build. Users can set their defaults and make changes as to
what emails they will receive via the Job Options window.
ProJet™ MP3000 can produce any size model with smooth surfaces. Multiple models can be built at one time.
Works with any compatible intraoral, plaster or impression scanner. This Printing System is designed for use in
laboratories with extended unattended operation, same day processing - helps you reduce time and cost.
High Definition (HDX); Ultra High Definition (UHD)Printing Mode: 298 x 185 x 203mm (11.75 x 7.3 x 8 inches); 127 x 178 xNet Build Volume (xyz): HDX Mode: UHD Mode:
152mm (5 x 7 x 6 inches) : 328 x 328 x 606 DPI; : 656 x 656 x 800 DPIResolution (xyz): *HDX Mode UHD Mode
: MP200; : S100VisiJet® Materials: Part Materials Support Material
1.5.1 Description and Definitions
1.5.1 Description and Definitions
Depending on the model of the ProJet 3000 3-D Production System, your system features different types of build styles to meet a variety of model
making applications. Please refer to Features and Benefits that will describe your extended choices for your particular system.
Description and Definitions
The High Definition (HD) Mode allows the user rapid model making capability on a full platform. This mode produces high quality parts
for concept models, verification designs and patterns for casting.
The Ultra High Definition (UHD) Mode allows the users to build extremely high resolution parts with exceptional surface finish and
superior accuracy. Models build in UHD mode are typically used for show models, fit testing and direct manufacturing using patterns for
investment casting of jewelry and small components.
Expanded UHD Mode: Provides the user with an Expanded Ultra High Definition (UHD) mode build envelope.
Expanded XHD Mode: Provides the user access to the new Extreme High Definition (XHD) Mode that features a new print resolution
with the same expanded build envelope available in UHD.
Email Notification: Provides email notification to the user when their job begins, completes, aborts and if the system is low on material
at any time during their build. Users can set their defaults and make changes as to what emails they will receive via the Job Options
window.
Part Stacking and Nesting
The new ProJet 3-D Production System, features part stacking and nesting capability in both build modes. The user can now utilize the entire
build volume by stacking parts vertically in the z-direction to fill up the entire build envelop with parts. The user can control the space between
layers to minimize support material usage and build time. Now, hours can be saved by stacking parts and submitting single, long builds overnight
and weekends.
Bounding Box Display Added to Print Preview
A few new features have been added to Print Preview to allow it to handle up to two gigabytes of part data on a single build.
The has been added to Print Preview to allow file sizes that were previously too large for Print Preview to loadBounding Box Display
successfully. The Bounding Box Display only displays the bounding extents of a given geometry and does not try to resolve the triangles
required to display an entire geometry. See .Section 8.1 Preview Build Job

Job Submission Checking has also been added. Both the 3-D Modeling Client and Print Preview now check to make sure that the
maximum allowable accumulated build file size on the machine is not exceeded during job submission. The maximum threshold for job
submission is roughly two gigabytes or 40,000,000 triangles. See Section 8.3 Submit a Build Job
The new production system introduces new enhancements including an expanded build envelope for the UHDProJet™ HD 3000plus
build mode, the new XHD build mode and email notification.
1.7 Packaging
Packaging
damage or discard any packaging materials or carton(s). If the modeler needs to be returned to the manufacturer, it should be shipped inDo not
it's original packaging. If other packaging is used, the customer will be responsible for any shipping damages that may occur.
Only Certified/Qualifed Service Personnel can install the 3-D modeler.
02.0 Safety Symbols & Definitions
UV Radiation Hazard: Invisible UV radiation is accessible in the vicinity of this sign or behind the panel. Radiation can cause eye injury.
Access panels are for service only and should be opened only by certified service personnel.
High voltage electricity is accessible in the vicinity of this sign or behind the access panel. HighElectrical Shock Hazard:
voltage can cause severe burns or death. Access panels are for service only and should be opened only by certified service
personnel or trained maintenance personnel.
A hot surface is accessible in the vicinity of this sign or behind the access panel. Avoid contact. Hot surfaces canHot Surface Hazard:
cause severe burns. Access panels are for service only and should be opened only by certified service personnel or trained
maintenance personnel.
: Indicates that skin or eye irritation could result while exposed to aHarmful Irritant Warning
chemical composition.
Caution: Indicates something may happen that could cause loss of data, damage to equipment, or personal injury.
03.0 Safety Guidelines

Before using the modeler, your company should have a safety program in place. The safety program should:
Label and point out hazardous equipment, materials, and procedures.
Explain what to do in case of an emergency.
Provide information about hazards of equipment and materials in the form of Material Safety Data Sheets (MSDSs). The MSDSs are
provided with all materials supplied by 3D Systems.
3.1 General
3.2 Electrical
3.3 Ultraviolet (UV) Light
3.1 General
The modeler is designed with built in safety features, improper use and malfunctions can cause injury to personnel. To prevent unsafe operation,
the modeler will automatically shut down if unsafe conditions are detected.
Follow these safety guidelines when operating the modeler:
Read and follow all modeler instructions.
Follow all safety rules and heed all cautions and warnings in this guide.
Do not attempt to open chamber door while build in progress.
Do not use any material without reviewing the Material Safety Data Sheets (MSDS).
Dress power and communication cables behind modeler to prevent tripping.
Do not attempt to access, service, or adjust modeler components. Do not attempt to perform any maintenance procedures unless
specifically trained to do so.
Operators are trained to operate system and perform all necessary tasks to create a part.
Certified service personnel are those who completed the 3D Systems service training package and certified to perform service tasks. Certification
may occur at different levels, and service providers should only perform tasks they are authorized and certified to complete.
Do not ignore warning signs posted during modeler service operations.
If an error message appears on the modeler's LCD refer to Section within this guide before resuming operation.10.0 Error Messages
To prevent potential skin-irritation and sensitization due to contact with waste material, follow all guidelines within .Build Material Safety
To prevent pinch and crush injuries to the hand, use caution when replacing platform inside the build chamber.
3.2 Electrical
DANGERHazardous voltage exists inside the modeler. Injury or death from electrical shock can result if you remove the printer's
external panels. Panels should only be removed for service by trained and certified 3D Systems Technical Support
personnel.
To prevent electrical shock, the modeler will not operate unless external panels are installed. service ratingVerify facility's electrical before you
connect power to the modeler.
3.3 Ultraviolet (UV) Light
CAUTION
Hazardous UV radiation exists inside the modeler build chamber during build job. Eye injury or blindness can result if
chamber door is opened while a build job is in progress. If a build job is running, abort build job before attempting to open
chamber door.

To prevent eye injury, ultraviolet (UV) light inside the chamber will not operate when chamber door is open. When closed, the chamber door
keeps UV radiation from escaping. The chamber door remains locked if build job is paused.
04.0 Build Material Safety
Users of the modeler should be informed of potential hazards of part material prior to working with a modeler, or performing duties which may
result in exposure to uncured part material, such as removal and disposal of bin liners and empty cartridges, or waste bag.
4.1 Disposal
4.2 Health Hazards
4.3 Material Handling
4.4 Personal Protection Equipment
4.5 Regulatory Information
4.6 Spilled VisiJet® Material
4.7 Waste Removal
4.8 Material Storage
4.1 Disposal
Disposal of parts produced are not subject to regulations of any known agency worldwide. VisiJet® support material and cartridgesfully cured
may be disposed of in ordinary office trash.
Uncured part material waste is classified as regulated, and in some areas hazardous, requiring special packaging, transportation, and disposal.
The disposal of partially cured or uncured model material must comply with all local, state, and federal environmental safety regulations.
Applicable part "waste" includes cartridges (empty or full) and waste bag. Any materials used cleaning up uncured part material should be
disposed of as uncured part material.

To find out facility disposal requirements, contact a local waste disposal provider. (Local environmental regulatory agency should have a list of
qualified providers.) You will need to give disposal service provider a copy of the part material MSDS / SDS, and possibly other forms included in
the Appendix of your , such as Waste Profile Worksheet and SNUR (Significant New Use Regulation - U.S.VisiJet® Material Handling Guide
only). A report will be provided, indicating disposal requirements, as well as a quotation for regularly scheduled pickups. If assistance lis needed
locating a waste disposal provider, or completing a waste disposal form, contact local 3D Systems Hotline.Technical Support
3D Systems assumes no liability or responsibility for proper disposal of uncured part material. Proper disposal of uncured part material is the sole
responsibility of the user.
4.2 Health Hazards
Health Hazards
Uncured VisiJet® model material is a sensitizer. Skin or eye irritation could occur when exposed to the chemical composition of the
material.
Any chemical may exert harmful effects if contacts or enters the body. VisiJet® part material is a sensitizer and irritant.
Skin Sensitization
CAUTION: Uncured VisiJet® part material is a sensitizer. Skin or eye irritation could occur when exposed to the chemical composition
of the material.
Uncured material is a sensitizer, and can cause allergic reactions if contacts skin without protective gloves. Refer to personal protection
for more information. To avoid sensitization, do not allow uncured material to contact skin. Consult the MSDS for specific informationequipment
about the sensitization potential.
Inhalation
Under normal operation, inhalation is not an expected route of entry.
Ingestion
CAUTION: Uncured VisiJet® model material is toxic if ingested.
Uncured material is toxic if ingested. Uncured material must not be present where food and drink are stored, prepared, or consumed and not
ingested. After handling modeler materials, wash hands with soap and water before consuming or preparing food.
Handling Finished Parts
Finished (cured) parts can be handled or disposed of the same as standard household plastic products. VisiJet® parts are not recyclable. VisiJet®
materials are not intended for, and cannot be used for medical implant, or food or drink handling applications.

Exposure control
The modeler has a variety of built-in engineering controls which are designed to prevent operator exposure. Do not try to change or disable these
controls.
Appropriate hygienic practices should be followed, including washing with soap and water before meals, breaks, smoking, applying cosmetics,
using toilet facilities, and after work.
Employees should be alerted to the need to clean and rinse off any contacted surface promptly in order to prevent
further contamination. Ensure a convenient washroom location is provided with access to soap, water, and
disposable paper towels.
4.3 Material Handling
Emergency (MSDS)
Chemtrec USA ; Europe(800) 424-9300 +1-703-527-3887
Packaging Inspection
VisiJet® material is packaged in cartridges. Eight cartridges are packaged in polybags, and placed in shipping
cartons. Upon receipt of material shipments, inspect cardboard carton exterior for signs of damage and leakage. If leakage is observed, DO
NOT open carton, and contact 3D Systems' Hotline. If no leakage is observed, store materials in cartons until material is used.Technical Support
Part Building
If uncured material is observed on the part or platform after build, this is an abnormal condition, and is an indication the modeler requires servicing
by 3D Systems. Assume any liquid or paste-like material is part material. Do not directly touch uncured part material without protective gloves.
Discontinue use of the modeler, pending service by a 3D Systems Technical Support Representative.
Flammability and Combustibility
Do not expose materials to heat at or above 230°F (110°C), flames, sparks, or any source of ignition. (Though the U.S. Department of
Transportation does not consider VisiJet materials a "flammability hazard," they do classify them "combustible" based on flash points.) For more
information on VisiJet material flash points and combustibility, see VisiJet® Material Handling and Post Processing Guide.
4.4 Personal Protection Equipment
Exposure to uncured model material may occur; when removing and disposing of the bin liners containing spent
model material cartridges and waste bag. To prevent contact, wear chemically resistant protective gloves - nitrile
or neoprene gloves are recommended. Do not use Latex gloves.
In the event of a leak or spill of uncured part material, wear safety glasses with side shields to provide eye
protection

Because of the modeler's built in engineering controls, respiratory protection is not necessary during normal
operation. A NIOSH-approved (or equivalent) dust mask is recommended when dry sanding cured material parts.
4.5 Regulatory Information
Support material has no known regulatory requirements.
In the U.S., material is subject to special EPA disposal regulations and record-keeping requirements. "Uncured VisiJet® material"uncured
includes any model material cartridge (empty or full), and waste bag---about half of which is uncured model material. For complete disposal
regulation details, see Appendix in your Material Handling Guide.
In the U.S., you must keep the following disposal records for five years after the date of disposal:
The quantity of model material received (new or "virgin").
The name and address of the shipping location (the "responsible party" - generally your waste disposal service provider).
The quantity of model material shipped (disposed). For further information, see your .Material Handling Guide
For assistance, contact 3D Systems .Technical Support
4.6 Spilled VisiJet® Material
Spills of material are HIGHLY UNLIKELY, and should NOT occur in normal operation of the modeler. If a leak occurs, it is an indication of a
serious modeler malfunction.
The first priority is to protect users from inadvertently touching material. Spills of support material can be cleaned without use of protective gear,
and disposed of as office trash. Handling uncured part material requires use of gloves and other to ensure nopersonnel protective equipment
direct contact with uncured model material. If you don't know which material it is, assume it to be uncured model material, and handle accordingly
- with the recommended personal protective equipment.
Promptly remove spilled material, dispose of waste material, and cleanup materials per local regulatory requirements. Discontinue use of the
modeler, and contact 3D Systems for a service visit to determine and repair the source of leakage.Technical Support
Small spills of uncured liquid part material can be cleaned up using disposable towels, non-reusable rags, or absorbing materials such as
sawdust, clay, diatomaceous earth, or activated charcoal. If spilled material is hot (liquid), wait until cools and gels before wiping up. After wiping
up the spill, wipe surface with denatured or isopropyl alcohol and clean thoroughly with soap and water.
Consider avoiding placement of the modeler over carpeting, or consider use of barriers to avoid the possibility of carpet damage if spills were to
occur.
Advise service provider involved, of the spilled material, and provide MSDS and other material information prior to contact with the material.
Advise them of disposal requirements for model material and clean-up products if model material (uncured) is the spilled material. Use of heat
above 65°C (149°F) may prove helpful in removing spilled model material from carpet.
Tools contaminated with model material should be cleaned prior to reuse. Solvents such as denatured alcohol or Iso-Propyl Alcohol (IPA), are
normally required to clean equipment and tools. Wash with soap and water to remove any traces of excess model material or solvent. Contact
solvent suppliers for information on proper handling of solvents if used for clean-up.
4.7 Waste Removal
CAUTION: Uncured model material is a sensitizer. Skin or eye irritation could occur when exposed to the chemical composition of the
material.
Wear protective gloves before removing any waste product from the modeler. Be careful not to spill, drop, or expose others to these materials -
particularly part material cartridges or waste bag. Dispose of all waste material appropriately per local regulatory requirements.
Remove support and modeling cartridges from the waste bins. if liners are contaminated with uncured modeling material, replace the liners.
Dispose of waste bag containing both support and uncured model material. Replace with new waste bag.

4.8 Material Storage
BUILD MATERIAL SUPPORT MATERIAL
Shelf life for HR200, SR200,MP200, DP200- 2 yr Shelf life for S100- 5 yr
Shelf Life for CP200, CPX200- 5 yr Shelf Life for S200- 5 yr
Climate - Cool, dry area with adequate ventilation Climate - Cool, dry area with adequate ventilation
Temperature Range - 60°F (16°C) to 80°F (27°C) Temperature Range- 60°F (16°C)to 80°F (27°C)
Maximum Storage Temp - 95°F (35°C) Maximum Storage Temp - 95°F (35°C)
Environmental Conditions - No direct sunlight, heat, flames, or UV
energy. Environmental Conditions - No direct sunlight, heat, flames, or UV
energy.
NOTE: For optimal results, keep stored cartons closed and sealed, and do not open polybags until cartridge is ready for use.
Always check material "Best used by" date before loading cartridge. Do not load cartridges into modeler if about to expire. When modeler detects
an expired cartridge, it aborts the build and ejects the cartridge if date is past expiration date for support material or more than one year past the
expiration date for model material.

Support ( ) cartridges must be loaded in the left side feed slot. VisiJet part ( ) cartridges must be loaded in the side feed slot.white black right
Before removing a cartridge from protective polybag and before loading into modeler, inspect the cartridge for signs of damage or leakage. Do not
load a damaged or leaking cartridge. Dispose of it according to local regulations.
05.0 System Requirements
Power Rating
Country Voltage Frequency Amps (A) Phase Power Cord
USA 100-127 VAC 60 Hz 15 A 1 P/N 23417-802-XX
France 200-240 VAC 50 Hz 15 A 1 P/N 23417-802-XX
Germany 200-240 VAC 50 Hz 15 A 1 P/N 23417-802-XX
Hong Kong 200-240 VAC 50 Hz 15 A 1 P/N 23417-802-XX
Italy 200-240 VAC 50 Hz 15 A 1 P/N 23417-802-XX
Japan 100-127 VAC 60 Hz 15 A 1 P/N 23417-802-XX
Switzerland 200-240 VAC 50 Hz 15 A 1 P/N 23417-802-XX
United Kingdom 200-240 VAC 50 Hz 15 A 1 P/N 23417-802-XX
If connecting the modeler to a 200-240 VAC facility power outlet, connect the power cord (located
inside modeler's country kit)to the external transformer. Connect the transformer's power supply to the
facility's outlet.
06.0 Familiarization
The 3-D modeler system is a Multi-Jet-Modeling (MJM) line of modelers. The solid imaging modeler produces plastic prototype models from 3D
solid Computer-Aided Design (CAD) models and through the modeler client software. The models are generated in a rapid prototyping (RP)
environment. The primary features of the 3-D modeler are the user interface, build chamber, material feed slots, and waste material drawer. The
back of the modeler houses the power switch, internet and the power cord connections.

The three dimensional solid models built by the modeler consist of two materials (support material and part material). The support material is a
wax based material providing adhesion to build platform, as well as, providing material used to produce supports required to build the model.
The part material used to build the models is an ultraviolet (UV) curable material. After a layer of material is deposited in the build chamber, the
part is exposed to a UV flashlamp. The UV energy is absorbed by the material converting a liquid model material to a solid polymer. When the
build is complete the model (consisting of the two materials) is adhered to the build platform by means of the support material.
The material delivery system consists of two vertical stacks referred to as "magazines." The magazine on the left side of the machine holds nine
support material (white) cartridges. The right side of the machine holds up to nine part material (black) cartridges. The magazine system feeds
the cartridges to the modeler using a clamp feed system. As the cartridges are emptied, the clamp feed system releases the empty cartridge(s)
into the waste drawer. Material waste is generated by two processes; cleaning the printhead array plate and planarization. The cleaning process
involves purging jets and wiping the printhead array plate. Gravity pulls the waste material from the Head Maintenance Station (HMS) trough into
the waste umbilical. The combined waste material is then purged. The printhead cleaning process is invoked automatically prior to test print and
build jobs.

After the build is complete, the platform and the model is then removed from the modeler. A secondary operation, knows as finishing, is required
to provide a finished/cleaned model. Refer to your ProJet™ Finisher's Guide for more information.
6.1 System Functions
. Menu names and menu options are capitalized in boldface text. Instructions for selecting menu options look like this: "Select Menus: ." This means "select (click or highlight) the , then select on the menu."Menu>Option Menu Option
Keys: Keyboard key names are capitalized; for example, "Press the Enter key."
Buttons: Command buttons on the modeler's user interface are in boldface upper case text; for example, "Press the button." TheONLINE
command buttons are: , , , , , , and . MENU LIGHT PAUSE ONLINE YES NO ABORT
Display Text: Text on the modeler's display appears in uppercase in this guide; for example, "When the display shows ? , pressPAUSE JOB Y/N
."YES
07.0 Modeler Setup
To prepare and build part files, connect your PC and modeler to the network. For additional information refer to Facility Requirements Guide.
Component Type Software Requirements
PC Microsoft ® Windows® 98, Millennium Edition (Me), New Technology (NT) 4 (SP 3+), 2000, or XP.

7.1 Power on Modeler
7.2 Add Cartridge and Install Build Platform
7.3 Install and Run ProJet™ 3-D Modeling Client Software
7.4 Create STL File(s) to Build
7.5 Submit Test Build
7.6 Build Demo
7.1 Power on Modeler
WARNING: Read and follow safety guidelines in Ignoring these guidelines could result in death, bodily injury, orElectrical Safety.
modeler damage due to electrical shock or fire.
CAUTION: Verify modeler's rear panel power switch is OFF. Connecting power with switch on can damage modeler and cause
bodily injury or death due to sudden, unexpected mechanical motion.
1. Plug modeler power cord P/N 23417-802-XX into modeler's rear panel socket. Plug modeler power cord into a grounded power outlet.
2. If 200-240 VAC required, connect modeler power cord to external transformer in kit P/N 23418-801-XX, then plug transformer power cord into
a grounded power outlet.
3. Place switch on the rear of modeler to the ON position.
4. Wait 4 hours for modeler to warm up before pressing to start a build job.ONLINE
NOTE: You can submit jobs to modeler while it is warming up.

1.
2.
3.
7.2 Add Cartridge and Install Build Platform
Add Cartridge
Add material to feed slot when it has 3 cartridges or less. When a feed slot has 3 cartridges or less,
the operator panel displays and/or . Add 9 cartridges maximum per slot. ADD SUPPORT ADD PART
5 cartridges are visible when magazine feed slot is full.
NOTE: Before handling build material cartridges. Read Material Safety Data Sheet (MSDS).
Unpack cartridge and MSDS/SDS Sheet. Remove cartridge's from poly bag.
Open left and/or right magazine feed slot doors. Insert support material (white)
cartridges in left magazine feed slot. Insert model marterial (black) cartridges
in right magazine feed slot.
Lower each cartridge into slot. Ensure flat of cartridge and label on cartridge
is facing upward. Add eight cartridges maximum to each slot.
Close both magazine feed doors.
NOTE: For proper operation of the feed system, a minimum of three (3) support and three (3)
build cartridges must be present.
Table of contents
Other ProJet 3D Printer manuals

ProJet
ProJet MJP 5600 User manual

ProJet
ProJet 60 Series User manual

ProJet
ProJet PJ 5000 User manual
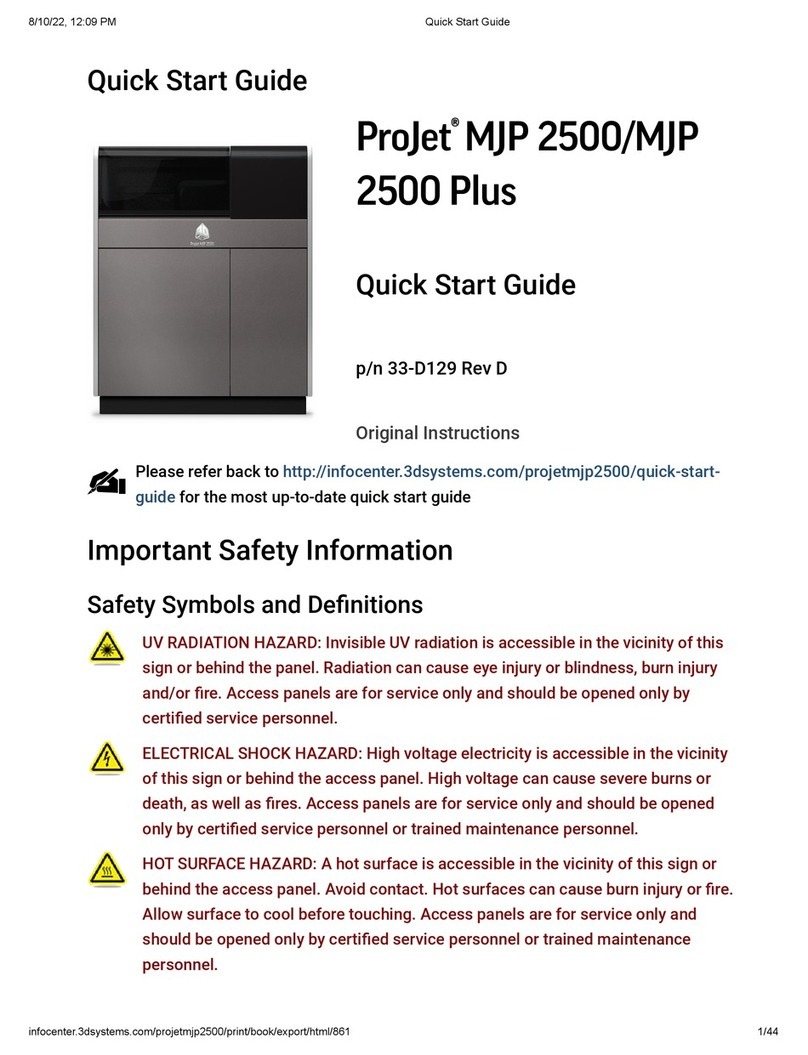
ProJet
ProJet MJP 2500 User manual

ProJet
ProJet 5500X User manual
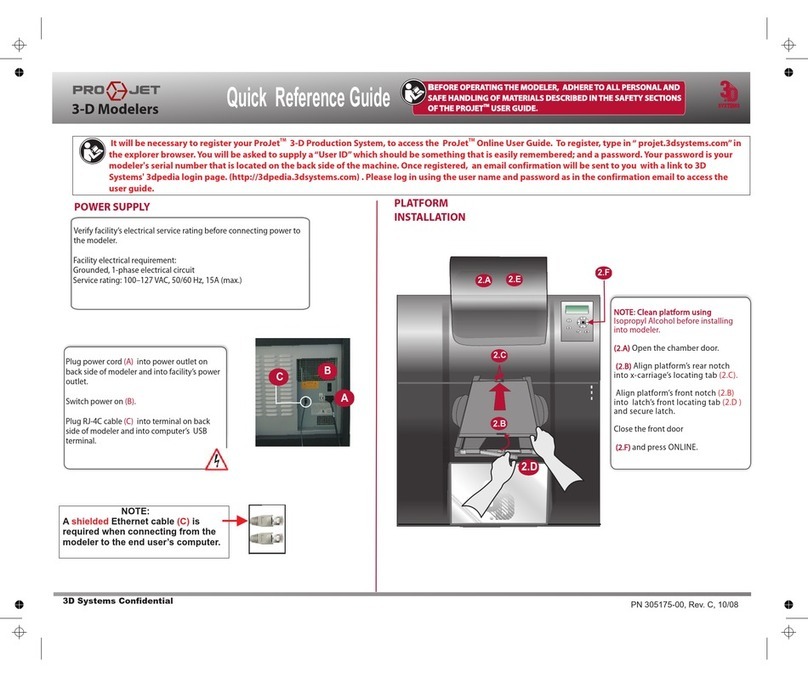
ProJet
ProJet 3-D Modelers User manual

ProJet
ProJet 1000 User manual
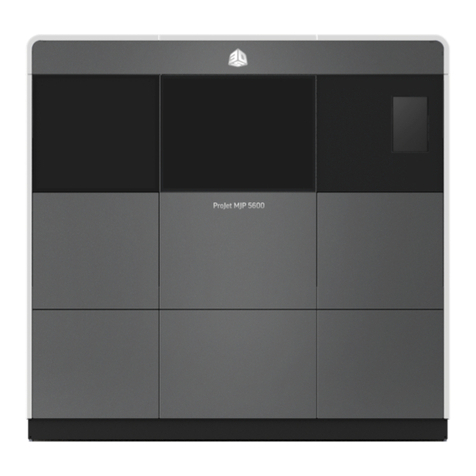
ProJet
ProJet MJP 5600 User manual

ProJet
ProJet MJP 5600 Installation manual

ProJet
ProJet MJP 2500W User manual