Reverberi MEDEA Guide

MEDICAL DEVICES SECTOR
USER MANUAL AND MAINTENANCE
Language: ENGLISH Cod. 9991
STEAM STERILIZER
MƎDEA
“THE NEW GENERATION”

MƎDEA GB –Rev. 02 del 06.02.2019
C/Doc/Manuali e doc/Settore dentale/Medea
2/93
IMPORTANT
THE MACHINE IS FOR PROFESSIONAL USE ONLY
THE USE IS PERMITTED ONLY QUALIFIED PERSONNEL TO DO
CONTACT THE QUALIFIED INSTALLER FOR THE IMPLEMENTATION OF THEEQUIPMENT
THE MACHINE CANNOT BE PUT IN WORK IN A ENVIRONMENT AT RISK OF EXPLOSION
Read carefully the instructions when buying the machine and before storing / installing / using it.
This Manual, that provides useful information regarding the safety during the IMPLEMENTATION
OF THE EQUIPMENT, INSTALLATION, USE, etc., is part of the product itself and it must be
delivered to the user, who has to store and carefully read it before starting each step of the service
provided by the machine.
Do not remove, tear or rewrite neither partly this Manual.
Keep the Manual in areas protected from moisture and heat for future reference.
This Manual contains the “CE” Declaration of conformity.
THE MACHINE MUST BE INSTALLED
AND USED ONLY ACCORDING TO THE
RULES LAID DOWN BY THE MANUAL
U.M.M.
NOTE:
Images, designs, and texts included in this manual are producer’s property. All rights reserved. It is forbidden even
partial reproduction of drawings, images and texts. The manufacturer reserves the right to alter without notice the
info in this manual.

MƎDEA GB –Rev. 02 del 06.02.2019
C/Doc/Manuali e doc/Settore dentale/Medea
3/93
1. INTRODUCTION ....................................................................................................................................................6
1.0. PURPOSE OF THE USER MANUAL AND MAINTENANCE..........................................................................6
1.1 USER’S PROFILE...........................................................................................................................................6
1.2 EUROPEAN STANDARDS AND DIRECTIVES APPLICABLE.......................................................................7
1.3 EXPECTED USAGE.......................................................................................................................................7
1.4 SYMBOLS SHOWN ON THE STERILIZER....................................................................................................7
1.5 CAUTIONS, WARNINGS, PROHIBITIONS....................................................................................................8
1.6 WARRANTIES AND LIABILITY ......................................................................................................................9
1.7 WARRANTIES CONDITIONS ......................................................................................................................10
1.8 ENVIRONMENTAL CONDITIONS ALLOWED.............................................................................................11
1.9 ILLUMINATION IN THEWORKPLACE ........................................................................................................11
1.10 USE NOT PERMITTED.................................................................................................................................12
1.11 RECOMMENDATIONS AND GENERAL SAFETY.......................................................................................12
1.12 SAFETY DEVICES .......................................................................................................................................12
1.13 DEVICES FOR PERSONAL PROTECTION.................................................................................................13
1.14 EMERGENCY STOP AUTOCLAVE .............................................................................................................13
1.15 CONDUCT OF MACHINE BY USER ............................................................................................................13
1.16 RESIDUAL DANGERS INFORMATION.......................................................................................................13
1.17 FAILURES, MALFUNCTIONS OR OTHER INCONVENIENCES.................................................................14
2. UNPACKING ........................................................................................................................................................15
2.0. SUPPLIED ACCESSORIES (STANDARD)......................................................................................................15
3. STERILIZER DESCRIPTION ...............................................................................................................................16
3.0. KEYBOARD......................................................................................................................................................16
3.1 FRONTAL SIDE............................................................................................................................................16
3.2 BACK SIDE...................................................................................................................................................17
3.3 VACUUM PUMP...........................................................................................................................................17
3.4 DESCRIPTION OF INTERIORWATER TANKS...........................................................................................18
3.5 QUALITATIVE WATER TABLE..............................................................................................................................19
3.6 CLEAN WATER LOAD.........................................................................................................................................19
3.7 AUTOMATIC LOADING................................................................................................................................19
3.8 DRAINING WATER USED............................................................................................................................22
3.9 DIRECT CHARGEAND DISCHARGEWATER CONNECTIONS...................................................................................23
3.10 TRAYS SUPPORT FOR THE STERILIZATION CHAMBER ..........................................................................................23
4. INSTALLATION....................................................................................................................................................24
4.0. POSITIONING ..............................................................................................................................................24
4.1 POWER SUPPLY .........................................................................................................................................24
4.2 BAROMETRIC ALIGNMENT........................................................................................................................25
4.3 CONNECTION TO THE LABELLER M9006............................................................................................................25
4.4 CONNECTIONS TO DEMINERALIZERS KIARA-TEC.................................................................................25
4.5 COLLEGAMENTO SERBATOIO ESTERNO................................................................................................25
4.6 USING SD CARD..............................................................................................................................................26
5. LOADING PREPARATION..................................................................................................................................27
5.0. CLEANING OF TOOLS.................................................................................................................................27
5.1. PREPARATION OF THE TRAYS...................................................................................................................28
6. START OF STERILIZER......................................................................................................................................29
6.0. EXECUTION OF ASTERILIZATION CYCLE ...............................................................................................31
6.1 AVAILABLE PROGRAMMS..........................................................................................................................34
6.1.1. UNIVERSAL CYCLE TYPE B...................................................................................................................34
6.0.2. SPECIAL CYCLES....................................................................................................................................34
6.1.3. STERILIZATION CYCLES GRAPHS, TEST AND TYPE OF TEST.........................................................35
6.1.4. SPECIAL CYCLE......................................................................................................................................38
6.1.5. TEST CYCLE............................................................................................................................................41
6.1.5.1. VACUUM TEST................................................................................................................................................41
6.1.5.2. B&D/HELIX TEST ............................................................................................................................................41
6.1.5.3. SPORE TEST...................................................................................................................................................41
7. OPTIONS..............................................................................................................................................................42
7.0 PRINT LABELS LAST CYCLES....................................................................................................................42
7.1. DRYING ONLY .............................................................................................................................................42
7.2 EXTRA DRYING ...........................................................................................................................................42
7.3 LABELS EXPIRY DATE................................................................................................................................43
7.4 START PORTPONED CYCLE......................................................................................................................43

MƎDEA GB –Rev. 02 del 06.02.2019
C/Doc/Manuali e doc/Settore dentale/Medea
4/93
7.5 OPENING DOOR..........................................................................................................................................43
8. SETTING ..............................................................................................................................................................44
8.0 LANGUAGE..................................................................................................................................................44
8.1 PRE-HEATING .............................................................................................................................................44
8.2 DRYING TEMPERATURE............................................................................................................................44
8.3 DATE FORMAT .................................................................................................................................................45
8.4 DATE/TIME...................................................................................................................................................45
8.5 OPENING DOOR..........................................................................................................................................45
8.6 MAINTENANCE............................................................................................................................................45
8.6.1. BACTERIAL FILTER.................................................................................................................................46
8.6.2. WASHER ..................................................................................................................................................46
8.6.3. WATER FILTER........................................................................................................................................46
8.6.4. HAVE THE AUTOCLAVE SERVICED......................................................................................................46
8.7 TOTAL N° OF CYCLES ................................................................................................................................47
8.7.1. VALID CYCLES ........................................................................................................................................47
8.7.2. CYCLES NOT VALID................................................................................................................................47
8.7.3. VACUUM TEST ........................................................................................................................................47
8.7.4. B&D/HELIX TEST.....................................................................................................................................47
8.7.5. SPORE TEST ...........................................................................................................................................48
8.8 COUNTERS..................................................................................................................................................48
8.8.1. WORKING HOURS ..................................................................................................................................48
8.8.2. N° OF CYCLES PERFOMED...................................................................................................................48
8.8.3. CONFORMABLE WATER LITRES ..........................................................................................................48
8.8.4. UNCONFORMABLE WATER LITRES .....................................................................................................49
8.8.5. PRINTER LABELS....................................................................................................................................49
8.9 CYCLES HISTORY.......................................................................................................................................49
8.10 BAROMETRIC ALIGNMENT........................................................................................................................49
8.11 CONFIGURATION........................................................................................................................................50
9. ALARMS...............................................................................................................................................................51
9.0 ALARM CODES...........................................................................................................................................52
9.1 TABLE OF STERILIZATION PROGRAMS AVAILABLE...............................................................................56
10. MAINTENANCE ...................................................................................................................................................57
10.0 NATURE AND FREQUENCY OF CLEANING, INSPECTION AND MAINTENANCE...................................58
10.0.1 BACTERIOLOGICAL FILTER REPLACEMENT ......................................................................................58
10.0.2 PINS LUBRICATION ................................................................................................................................58
10.0.3 WATER TANK CLEANING.......................................................................................................................58
10.0.4 REPLACEMENT OF THE ELECTROVALVES GROUP ..........................................................................59
10.0.5 MAINTENANCE VACUUM PUMP............................................................................................................59
10.0.6 REPLACEMENT OF THE GASKET.........................................................................................................59
10.0.7 REPLACEMENT OF THE TRASDUCER .................................................................................................59
10.0.8 REPLACEMENT OF THE ELECTRONIC BOARD ..................................................................................60
10.0.9 REPLACEMENT OF THE BATTERY OF THE ELECTRICAL CARD......................................................60
10.0.10 REPLACEMENT OF DISPLAY ...............................................................................................................60
10.0.11 REPLACE PRINTER PAPER ROLL .......................................................................................................61
10.1 SCHEDULED MAINTENANCE SUMMARY TABLE.....................................................................................63
10.2 RECOMMENDED SPARE PARTS LIST.......................................................................................................66
11. EMERGENCY –HOW TO COPE.........................................................................................................................67
11.0 FIRE..............................................................................................................................................................67
12. SOLUTION TO FAILURES ..................................................................................................................................68
13. INTERRUPTION OF THE STERILIZATION CYCLE...........................................................................................69
14. TECHNICAL FEATURES.....................................................................................................................................70
15. APPENDIXES.......................................................................................................................................................71
15.0 HYDRAULIC DIAGRAM................................................................................................................................71
15.1 ELECTRICAL DIAGRAM..............................................................................................................................72
15.1.1 NEW SOFTWARE INSTALLATION –PROCEDURE ..............................................................................73
15.2 LABELLING ......................................................................................................................................................75
15.3 EXPLODED ..................................................................................................................................................75
15.4 TEST...............................................................................................................................................................76
15.5 SCHEDULED MAINTENANCE COUPONS..................................................................................................79
15.6 FORM TO FILL IN FOR THE RETURN OF THE EQUIPMENT.....................................................................86

MƎDEA GB –Rev. 02 del 06.02.2019
C/Doc/Manuali e doc/Settore dentale/Medea
5/93
15.7 CERTIFICATO DI GARANZIA ......................................................................................................................87
15.8 VARIOUS FORMS........................................................................................................................................88
16. DECLARATION OF INSTALLATION ..................................................................................................................91
16. DECLARATION OF INSTALLATION ..................................................................................................................93

MƎDEA GB –Rev. 02 del 06.02.2019
C/Doc/Manuali e doc/Settore dentale/Medea
6/93
1. INTRODUCTION
We thank you for choosing a REVERBERI sterilizer.
The User and Maintenance Manual (U.M.M.) has been realized in order to provide general knowledge of the
machine and to give the transport, use and maintenance instructions and all the necessary details for the installation,
for the correct use and for the proper functioning.
We ask you kindly to CAREFULLY read the manual BEFORE CARRYING OUT ANY OPERATION ON THE
MACHINE.
In case you need another copy of the Use and Maintenance Manual (U.M.M.) you are invited to forward your
motivated request to the CONSTRUCTOR, quoting the serial number on the title of this post or on the name plate on
the back of the machine.
1.0.PURPOSE OF THE USER MANUAL AND MAINTENANCE
The following Manual aims to provide user all the information about MƎDEA sterilizers in order to warrant:
The correct installation and implementation of the MƎDEA steam sterilizer.
The optimal use.
A safe and reliable functioning.
The requirements for proper and regular maintenance and for the periodic replacement operations of the
components.
1.1 USER’S PROFILE
The user, who has the responsibility for operation of the equipment, must be a person previously well trained by the
Employer (or whoever takes his place), that person must MANDATORY read/UNDERSTAND all the instructions in
this U.M.M.
The manufacturer is not liable for any direct or indirect damages caused by people who had used
the device without having received adequate instruction and relevant qualifications to conduct the
same and consequently have made bad use.
Three kinds of profiles can use the sterilizer and have to read carefully this Manual:
The Administrator
The administrator is the responsible for the clinic or doctor's office, or rather the person responsible for the protocol
of hygiene and sterilization process.
The administrator is also responsible for the OPERATORS’ training and for the proper operation and maintenance of
the equipment. Must have adequate training for all operations to be performed and for safe use.
The Operators
The operators are those who use the sterilizer according to the instructions received from the ADMINISTRATOR.
Enabled technicians
All the ordinary and extraordinary maintenance, qualified, controls, cleanings and registrations should be performed
only by authorized personnel and/or instructed to do so and when the equipment is not working (state of zero
energy).
The qualified personnel must have attended a technical training from the manufacturer. At the end of the course will
receive a certificate of training.
The manufacturer shall make available to operators and technical managers, training at the
headquarters of Bibbiano (RE). For information on course dates contact number.
Tel 0522 875 159.

MƎDEA GB –Rev. 02 del 06.02.2019
C/Doc/Manuali e doc/Settore dentale/Medea
7/93
1.2 EUROPEAN STANDARDS AND DIRECTIVES APPLICABLE
MƎDEA sterilizer complies with the following European Directives:
93/42/CEE and s.m.i. Medical Devices Directive, IIb Class, in accordance with the rule 15 –Appendix IX of
the above Directive.
2014/68/UE (PED –Pressure Equipment Directive) on the sterilization chambers projected and realized in
accordance with Category I with evaluation form A.
2002/96/CEE (RAEE) on the disposal of shares from electrical or electronic components.
EN13060 current edition concerning performance requirement for small steam sterilizers
EN 61010-1 and 61010-2-40 current edition concerning safety requirements for small steam sterilizers.
EN 62304 Software certification current edition
EN 61326 Electromagnetic Compatibility current edition
1.3 EXPECTED USAGE
Sterilizers MƎDEA are "steam sterilizers" fully automatic, which generate steam by heating elements.
MƎDEA sterilizers are used for the sterilization of surgical instruments
The load types that can be sterilized by the sterilizer MƎDEA are described in Table 1 of the reference technical
standard EN 13060. These loads include solid, porous, hollow type A and B, unwrapped, wrapped in single and
double envelope.. They are also used for materials and tools that can come into contact with blood and / or body
fluids.
Usage environments may be: hospitals, education or medical clinics, dental offices, veterinary.
Sterilizers REVERBERI cannot be used to sterilize liquids or pharmaceutical products.
Do not use the machine for purposes other than those for which it was created.
It is important to ensure that the value of ground resistance is efficient and
well coordinated with the electrical protections of the implant, in order to avoid
electrical interferences to the autoclave.
1.4 SYMBOLS SHOWN ON THE STERILIZER
Consult the following table whenever a symbol below appears on the sterilizer or on the Manual.
WARNING
It shows a notice or a warning about the key functions or about useful
information. Pay close attention to blocks of text indicated by this symbol.
OBSERVATION
The User is required to detect a measure value, to check an alert, etc.
PROHIBITION
Any procedures that staff must not perform because, otherwise, might
endanger his own safety and that of others
OBLIGATION
Any procedures that staff must perform because, otherwise, might endanger
his own safety and that of others
CAUTION, IT IDENTIFIES A SOURCE OF HEAT, THERE MAY BE AN UNSAFE
TEMPERATURE
CAUTION, IT IDENTIFIES A GENERIC DANGER, THERE MAY BE A DANGEROUS
SITUATION
IT IDENTIFIES THE PROTECTIVE EARTH TERMINAL

MƎDEA GB –Rev. 02 del 06.02.2019
C/Doc/Manuali e doc/Settore dentale/Medea
8/93
IT IDENTIFIES THAT THE AUTOCLAVE HAS BEEN CERTIFIED BY THE
NOTIFIED BODY IMQ S.p.a
This symbol indicates that the product is covered by 2002/96/CE European
Directive.
Please inform yourself about the local separate collection system for electrical and
electronic products.
Comply with local rules and do not dispose of your old products with your
normal household waste. Proper disposal of the product will help prevent
potential negative consequences for the man’s health and for the environment.
THE MANUFACTURER DO NOT PROVIDE WARRANTIES ABOUT THE SUITABILITY OF THE TECHNICAL /
LEGAL ROOM WHERE THE EQUIPMENT IS INSTALLED AND ALL THE SUPPORT SERVICES AT THE
SAME, ALTHOUGH THE U.M.M. OFFERS IMPORTANT INFORMATION FOR A PROPER INSTALLATION.
REGARDING THIS ASPECT THE USER IS RECOMMENDED TO USE THE ADVICE OF QUALIFIED
PERSONNEL EXPERT IN THE FIELD, FOR THE RESPECT OF EVENTUAL LAWS AND/OR REGULATIONS
TOO.
DO NOT ALLOW ANYONE TO USE THE INSTRUMENT WITHOUT FIRST:
READ AND UNDERSTAND ALL THE INDICATIONS INCLUDED IN THE U.M.M.
RECEIVE SUITABLE INSTRUCTION FOR THE SAME CONDUCTION BY A PERSON AUTHORIZED.
THE MACHINE IS BUILT IN COMPLIANCE WITH CURRENT STANDARDS. PLEASE BEFORE
PROCEEDING WITH THE INSTALLATION, USE, MAINTENANCE AND REPARATION (AND RELATED),
READ CAREFULLY THIS USER AND MAINTENANCE MANUAL BECAUSE IT CONTAINS ALL THE
NECESSARY INFORMATION FOR A PROPER USE AND OPERATION, DESIGNED TO PREVENT
ACCIDENTS.
THIS U.M.M. MUST BE CONSIDERED PART OF THE PRODUCT ITSELF AND IT MUST REMAIN PART
OF IT FOR ALL THE PRODUCT LIFE.
The frequencies of monitoring and maintenance, prescribed by the U.M.M., refer to the minimum necessary
to ensure efficiency, safety, and duration of the equipment in normal working conditions. Surveillance will still be
constant and will act promptly in cases of anomalies.
All our equipment are subject to continuous technological development. We must therefore, from time to
time, subject to the possibility of making changes regarding the construction and endowment, which can modify the
operating features.
The electrical system, as well as the continuity of the protective circuit, has been tested by REVERBERI at
the factory so it is general and guaranteed perfect and functioning.
Any damage caused by the buyer for incorrect links, automatically excludes any warranty on the unit.
The position of the CE plaque is visible EC.
1.5 CAUTIONS, WARNINGS, PROHIBITIONS
1°. LIQUIDS OR DUSTSHOULD NOT FALL/ENTER INTO THE APPARATUS. SEEK TO MAKE
INSTALLATION THAT AVOID THESE PROBLEMS.
2°. FLAMMABLE LIQUIDS OR POWDERS SHOULD NOT BE USED NEAR THE MACHINERY.
3°. IT IS FORBIDDEN TO EVERYONE AND / OR TO OPERATORSWITH HEART DISORDERS AND
PACEMAKERS,TO APPROACH THE MACHINERY WITHOUT FIRST CONSULTING THE DOCTOR.
4°. BEFORE USING THE DEVICE, IT IS NECESSARY TO KNOW ALL THE OPERATIONS AND CONTROL
DEVICES. LEARNING CONCEPTS OF THIS SHOULD BE MANDATORY BEFORE BEGINNING. PEOPLE
NOT ATTACHED AND WITHOUTTHE APPROPRIATE CONCEPTS ARE NOT ALLOW USING THE
STERILIZER.
5°. READ ALL SAFETY INFORMATION CONTAINED HEREIN AND UNDERSTAND ALL THE PLATES
(REPORTS SECURITY) ON THE UNITS. THE SIGNS ON THE UNIT MUST ALWAYS BE READ WELL,
REPLACE THEM IN CASE THEY GET WORN OR DAMAGED.
6°. NO WARRANTIES PROVIDED ON GOOD FUNCTIONAL OR ON SAFETY OF THE USER AND / OR
ENABLED PERSON AND / OR ANY OTHER PERSON AND / OR THE ENVIRONMENT, IN THE EVENT
THAT:
•THE PROVISION OF ELECTRICITY NOT COMPLY WITH THE REQUIREMENTS OF THIS LAW
AND U.M.M.;

MƎDEA GB –Rev. 02 del 06.02.2019
C/Doc/Manuali e doc/Settore dentale/Medea
9/93
•THE EQUIPMENT ONCE INSTALLED AND PUT IN SERVICE NOT COMPLY WITH THE
REQUIREMENTS STATED IN THIS U.M.M.;
•THE DEADLINES SET MAINTENANCE ARE NOT RESPECTED
7°. THE OPERATING SAFETY EQUIPMENT ALLOWS IT TO BE INSTALLED AND PUT INTO SERVICE BY
QUALIFIED PERSONNEL RESPONSIBLE TO FOLLOW THE INSTRUCTIONS GIVEN IN THIS U.M.M.
AND RULES.
8°. THOSE WHO ARE NOT ABLE TO INSTALL, START UP OR USE SAFETY ALONE OUR PRODUCT,
BECAUSE OF PHYSICAL, SENSORY OR MENTAL INABILITY, OR THROUGH INEXPERIENCE OR NO
KNOWLEDGE, THEY MAY CARRY OUT THE BUSINESS SPECIAL SUPERVISION ONLY IF
INSTRUCTED BY COMPETENT PEOPLE, WHO TAKE FULL RESPONSIBILITY.
9°. YOU MAY NOT USE WATER TO WASH THE MACHINE PARTS (EXCEPT FOR SOME ACCESSORIES,
NOT EXPRESSLY REPORTED)
10°.IT IS FORBIDDEN TO REMOVE AND / OR TAMPER WITH THE LABELLING AND SYMBOLS FROM
ORIGINALLY AFFIXED REVERBERI.
11°.DO NOT PUT ANY OBJECT OVER EQUIPMENT,
12°.DO NOT TOUCH THE DEVICE WITH BODY PARTS WET AND / OR BARE FEET.
13°.DO NOT PULL THE ELECTRICAL CABLES OR THE SHEATHS OF THE ELECTRICAL INSTALLATION
14°.DO NOT START BEFORE CHECKING DIRECTLY AND VISUALLY THAT IN OR ON THE MACHINERY
THERE IS NO FOREIGN BODY.
15°.IN ANY SPECIFIC CIRCUMSTANCES ALWAYS USE APPROPRIATE PROTECTIVE CLOTHING OR
TOOLS.
16°.NEVER INSERT THE HANDS OR OTHER PARTS OF THE BODY IN COMPONENTS NOT PERFECTLY
FIXED OR IN PARTS NOT COMPLETELY VISIBLE FROM THE PERSON WHO IS OPERATING.
17°.KEEP THIS U.M.M. ALWAYS AT HAND AND AT DISPOSAL OF THE ENABLED USER AND DURING
INSTALLATION AND / OR MORE VISITS AND USE.
18°.THE U.M.M. DUPLICATION IS RECOMMENDED (AUTHORIZED BY THE MANUFACTURER FOR THE
INTERNAL USE ONLY) AND IT IS AVAILABLE FOR THE PERSONAL AND ENABLED USER, KEEP
THEN THE ORIGINAL COPY IN A SAFE AND EASY AVAILABILITY.
DURING THE OPERATION OF THE MACHINE, THE
SURVEILLANCE OPERATOR MUST BE CONTINUED
ANY TOOLS FOR THE OPENING OF ELECTRICAL PANEL OR
PROTECTIONS MUST BE STORED AND / OR ACCESS ONLY TO
AUTHORIZED PERSONS AND EDUCATED.
IT IS OUT OF LAW LEAVE THESE TOOLS AND ACCESSIBLE TO
ALL PACKING
1.6 WARRANTIES AND LIABILITY
THE MANUFACTURER ASSUMES NO LIABILITY FOR DAMAGES CAUSED ON THEMACHINE, ON
THINGS, ANIMALS AND / OR PERSONS, MAKING ANY KIND OFWARRANTY INVALIDATE IMMEDIATELY IF:
THE INSTALLATION OF THE APPLIANCE IS NOT DONE BY QUALIFIED PERSONNEL IN
ACCORDANCE WITH THE RULES AND MAY BE REPORTED ASIN THE DECLARATION OF
CONFORMITY
THE START UP OF THE EQUIPMENT IS NOT PERFORMED BY A QUALIFIED
QUALIFIED PERSONNEL AND / OR USER NOT COMPLY WITH THE INSTRUCTIONS GIVEN IN THIS
USER AND MAINTENANCE MANUAL OR AS RESULT OF ANY OPERATION NO SPECIFICALLY
DESCRIBED.
VERIFY CAREFULLY DURING THE READING OF U.M.M. THE CORRESPONDENCE WITH THE PARTS OF THE
EQUIPMENT, CHECKING:
THE PARTS HAVE NOT BEEN DAMAGED DURING THE TRANSPORTATION AND HAVE BEEN
DELIVERED INTEGRA,
THERE ARE ALL THE SAFETY SYMBOLS.

MƎDEA GB –Rev. 02 del 06.02.2019
C/Doc/Manuali e doc/Settore dentale/Medea
10/93
DO NOT PROCEED TO USE THE STERILIZER IF ALL ITEMS DESCRIBED ABOVE DO NOT EXIST:
THE MANUFACTURER ASSUMES NO RESPONSABILITY FOR DAMAGES CAUSED TO THE SAME
DEVICE ON PEOPLE, ANIMALS AND / OR PROPERTY, IF ANY ANOMALIES IS NOT REPORTED
WITHIN 30 DAYS OF RECEIPT OF GOOD TO MANUFACTURER. IN THESE CASES ANY TYPE OF
WARRANTY BECOME INVALID AUTOMATICALLY.
TO COMPLY WITH THE TRACEABILITY OF THE STERILIZER ANY CHANGE OF ADDRESS OF THE
SAME MACHINE MUST BE COMMUNICATED TO THE MANUFACTURER / DEALER.
ANY CHANGES MADE ON ITS DEVICE or safety devices, WHICH MAY AFFECT THE FUNCTIONS
PROVIDED BY THE MANUFACTURER and the risks of the risk analysis, included in the “Technical
Construction File”,
WILL BE FULL RESPONSIBILITY OF THE RUN. AS CHANGE IS MEANT ALSO THE FAILURE OF THE
INSTRUCTIONS, REPRESENTATIONS AND EFFORT NONCONFORMING AND THE USE OF PARTS
NOT ORIGINAL.
Any change, even if not substantial, must be communicated by registered post and also approved by
the MANUFACTURER, THAT will approve THE CHANGES only if, such amendment, shall not constitute
implementations of risk analysis AND THE risks of the machine.
Any change made without notice to the MANUFACTURER, will constitute CANCELLATION OF the
“CE” Declaration of Conformity, making void any warranty and guarantee by the same.
The manufacturer is not responsible for:
• The placement of a protection mechanisms against overcurrent for power conductors of the
electrical equipment, which must be placed upstream of the apparatus and duly reported.
• The installation of a power plug to be placed between the electrical panel and the electrical
appliance in place of the existing installation.
1.7 WARRANTIES CONDITIONS
This appliance is guaranteed for one year (12 months) from the date of purchase, on the whole territory of
the European Union; the date of the delivery note / invoice will be the authentication.
The device is used for professional use.
During this period, the manufacturer will repair or replace for free those pieces that, at its own sole
discretion, were to be originally defective, with only the reimbursement of travel expenses incurred by the
technicians of the "Service Centre", at doorstep or totally free if the equipment is delivered to BARCO di
Bibbiano (RE).
Defective parts replaced become the property of the manufacturer.
If the defect is not repaired, the manufacturer may avoid the termination of the contract by the customer by
offering free replacement of the property.
Are not covered by the warranty the damaged parts for transport / shock for bad or improper installation / use,
through neglect or misuse, tampering by unauthorized persons, damages weather or other natural events or other
causes not dependent on REVERBERI, supplies and / or subjected to wear / low.
Further or other claims for damages, in addition to those provided by law, are excluded.
The manufacturer will charge the cost of repair if the returned product is not covered under warranty.
Interventions for alleged defects or casual checking shall be borne by the customer.
Any repair of transport to and from the "Technical Assistance Centre" of BARCO di Bibbiano (RE) is done at the
expense and responsibility of the customer.

MƎDEA GB –Rev. 02 del 06.02.2019
C/Doc/Manuali e doc/Settore dentale/Medea
11/93
The technical staff, when called to repair, will be sent in time only compatible with the business needs of the
manufacturer.
Any use bans imposed by the Health Authority or by other competent bodies, do not entitle the buyer to demand
the surrender or to ask for damages.
Any difference on the exterior colour or colour effects of the various parts making up the unit are not considered
defects: the differences may be e.g. due to the manual workers.
The inability to ensure substitutability of parts that make up the set with pieces from standard / freshmen /
supplies purchased specifically different and not as a replacement is not considered a defect.
In case of repair / replacement of defective parts or replacement of the equipment during the warranty period,
the warranty remains unchanged: it always starts from the original date of purchase of the unit.
As no there reported The Terms and Conditions listed on the commercial documentation / sales catalogue in
force at the time of purchase remain valid.
1.8 ENVIRONMENTAL CONDITIONS ALLOWED
TEMPERATURE, HUMIDITY AND ALTITUDE
See Paragraph in particular
ELECTROMAGNETIC COMPATIBILITY
Install the unit where electromagnetic interference comply with the limits permitted by the rules and with the
presence of electric and electronic equipment.
RADIATION EXPOSURE
The appliance is not intended to be used to direct exposure to:
- Non-ionizing radiation of the sun, being the same to be placed indoor and / or repaired
- X-ray radiation, microwave radiation, laser radiation, etc…
In the event that, in the environment where the unit is placed, there is a risk of radiation directly on it, specific
measures to protect exposed areas must be taken by the purchaser.
USE IN EXPLOSIVE ENVIRONMENT
The device cannot be used in any way in the environment where there is a risk of explosion or in a potentially
explosive environment
1.9 ILLUMINATION IN THE WORKPLACE
The environment in which the sterilizer is installed must meet the requirements listed on the Directive
89/654/EEC concerning the workplace and the requirements of the RULES FORCE THE INSTALLATION SITE.
Proper lighting can, in some cases, avoid or limit an injury to the operator.
REQUIREMENTS OF THE LOCAL WHERE THE EQUIPMENT IS INSTALLED. THE LOCAL SHOULD:
Be free of debris and / or residues of various kinds of flammable or potentially dangerous operation;
Provide a specific room for sterilization, away from the patient.
Have doors (accesses) appropriate to the size of the machine, ensure a suitable floor for the mass flow of
the machine, ensure a perfectly level floor, be free, at the area of installation, strong drafts or substantial
temperature changes;
Ensure good ventilation and air exchange with the provision of specific natural ventilation openings.
IT IS FORBIDDEN TO USE THE EQUIPMENT IN EXPLOSIVE ENVIRONMENTS SUCH
OR CONSIDERED.

MƎDEA GB –Rev. 02 del 06.02.2019
C/Doc/Manuali e doc/Settore dentale/Medea
12/93
1.10 USE NOT PERMITTED
It is not allowed:
•THE USE of the machine if you have not INSTALLED in accordance with APPLICABLE RULES and BY
AUTHORIZED PERSONNEL,
•The use of the appliance by USERS not authorized by the superior role (or employer),
•The use of the appliance by USERS not trained to manage it,
•The use the equipment for purposes other than those expected and stated in the Declaration of Conformity,
•The use the equipment in environments with explosive atmosphere or where there are similar risks,
•Elaborate or otherwise alter the unit cycles and performance
•Use or use accessories other than the original operation,
•Use replacement parts other than original
•Alter the electrical system and safety devices connected to them,
•NOT TO COMPLY WITH THE INSTRUCTIONS, THE OBLIGATIONS AND PROHIBITIONS CONTAINED
IN THIS MANUAL AND ON THE UNIT ITSELF.
1.11 RECOMMENDATIONS AND GENERAL SAFETY
• The user is responsible for installation, proper use and maintenance of the sterilizer in accordance with the
instructions in this manual. If necessary, contact your local Technical Support.
• The sterilizer is not designed for the sterilization of liquids.
• The sterilizer should not be used with flammable gases or vapors.
• For the sterilization of materials, carefully follow the instructions provided by the manufacturer of the materials.
• For the preservation of sterilized materials, we recommend the use of special cabinets equipped with ultraviolet
lamps, which are perfect for this specific use.
• The support trays and trays must be always present In the room
• At the end of the cycle, the load will be hot. Use the appropriate key for the extraction of the trays or cassettes.
• Do not exceed load limits specified in this manual
• Do not remove the identification number or any other labels from the serial number or other sterilizer.
• To prevent electrical short circuits, do not spill water or other liquids on the sterilizer.
• Turn off the sterilizer and unplug the power cord before inspecting, make operations, maintenance or repairs of the
sterilizer.
• Never turn off the machine with the door closed.
• Keep the original packaging carefully for any transport.
• The repairs should be made by individuals authorized by the manufacturer and
Using only original parts.
1.12 SAFETY DEVICES
oSAFETY VALVE 2.5 bar
oFUSE 15 A security
o1 Manual reset safety THERMOSTAT calibrated 230° for internal resistance.
o1 Automatic reset safety THERMOSTAT calibrated 230 ° for external resistance
In case of transport:
• Fully discharge both water tanks.
• Leave to cool the sterilization chamber.
• Use the original packaging or other suitable packaging.
• Use a reliable transporter
Any intervention on, determined by a malfunction, must mandatory be performed
by qualified personnel to do so.
In case of replacements of equipment parts, use original spare parts, to avoid
causing variations in performance and / or reduce the level of safety.
Each cleaning, checking and / or maintenance must be performed by authorized
personnel and authorized to do so in accordance with the requirements
described in this U.M.M.
Failure to follow the instructions in this manual may cause danger to the user.

MƎDEA GB –Rev. 02 del 06.02.2019
C/Doc/Manuali e doc/Settore dentale/Medea
13/93
1.13 DEVICES FOR PERSONAL PROTECTION
TO BE USED TO PREVENT THE ONSET OF RESIDUAL RISKS
According to legal requirements dictated by the regulations on this subject it is the duty of Head of Hygiene and
Safety to analyses the potential risks people are exposed to and to wear appropriate Personal Protective Equipment
(P.P.E.) in the Studio where the equipment is installed. Regardless of the risk analysis of Hygiene and Safety
Manager, in all cases mentioned in this Section are shown the MANDATORY P.P.E. that the exposed personnel
must use while approaching the machine. The use of additional D.P.I. is at the discretion of the Head of the Hygiene
and Safety in the Studio where the equipment is installed.
Use:
1. Safety shoes to ensure a sufficient level of electrical / mechanical isolation /
2. Flame retardant protective clothing.
3. Appropriate gloves
IN NORMAL CONDITION OPERATIONS NEVER STOP THE DEVICE REMOVING
THE POWER SUPPLY DIRECTLY FROM THE GENERAL SWITCH BUT STOP THE
CONTROL PANEL FIRST.
1.14 EMERGENCY STOP AUTOCLAVE
In case of emergency there is a need to stop THE equipment the operator must take prompt action on the
connection socket / plug off, grabbing the plug WITHOUT pulling the cable. In this regard it should be noted that the
plug must always be free of any material or furniture and always visible.
1.15 CONDUCT OF MACHINE BY USER
The user's tasks are:
• Monitor the operation of the appliance, acting promptly in case of malfunctions;
• Check the constancy of performance and integrity of the devices used and promptly shut down the device in case
of malfunctions.
It is FORBIDDEN to leave the unit without first having switched it off at the end of
the work
The intervention of the user will always be subject to compliance with the
symbols placed on the machine and the requirements dictated by this U.M.M.
1.16 RESIDUAL DANGERS INFORMATION
RESIDUAL DANGERS AND SIGNALS
To highlight to the user, to those exposed and to the authorized personnel all the residual risks to which attention
must be paid, it was decided to affix to the machine standardized symbols highlighted in the following pages.
The dangers to which it could not apply a total protection, because it would make the machine difficult to use,
inhibiting their intended use, are as follows:
1
Electrical dangers inside the control panel or any derivations of the unit.
2
Thermal dangers resulting from the contact of the user's arms when the respective
electrical resistance is operating.

MƎDEA GB –Rev. 02 del 06.02.2019
C/Doc/Manuali e doc/Settore dentale/Medea
14/93
1.17 FAILURES, MALFUNCTIONS OR OTHER INCONVENIENCES
In case of failures, malfunctions or other problems not covered in this U.M.M., call the manufacturer directly.
The address is as follows.
REVERBERI ARNALDO S.R.L.
Via Don L. Sturzo, 6 –42021 BARCO di Bibbiano (RE) –ITALIA
Tel. +39 (0) 522 875159 Fax.+39 (0) 522 875579 e-mail: reverberisrl@gmail.com
Any work on the machine, determined by a malfunction, must necessarily be
performed by qualified personnel.
In case of replacements of equipment parts, use original spare parts, to avoid
causing variations in performance and / or reduce the level of safety
Each cleaning, checking and / or maintenance must be performed by authorized
personnel and authorized to do so in compliance with the requirements given in
this U.M.M.

MƎDEA GB –Rev. 02 del 06.02.2019
C/Doc/Manuali e doc/Settore dentale/Medea
15/93
2. UNPACKING
UNPACKING OF THE
STERILIZER
If the sterilizer has been
kept in temperature and
humidity conditions
different from those of the
installation, wait for an
appropriate period of time
before installing it and
turn it on. The sterilizer
that comes from a cold
place could accumulate
inside moisture an
condensation which could
cause a danger if turned
on immediately.
The sterilizer should be
removed from the
packing box and
transported by two
people.
TOTAL WEIGHT DRY:
MƎDEA 62 Kg
NOTES:
Check the external condition of the carton
box and of the sterilizer. In case of
damage, contact the retailer, the shipper
and the carrier that have delivered the
product.
2.0.SUPPLIED ACCESSORIES (STANDARD)
4 Trays made of anodized aluminium
Support for 4 aluminum trays
Tray extrication glove
Water supply hose
Exhaust hose
Support phials for spores
SD Card
2 Sterilization indicators
Sponge for cleaning
User manual and maintenance
CE Declaration of Conformity

MƎDEA GB –Rev. 02 del 06.02.2019
C/Doc/Manuali e doc/Settore dentale/Medea
16/93
3. STERILIZER DESCRIPTION
3.0. KEYBOARD
1- Info / Esc
2- Start / Stop
3- Reduction / Menu
4- Increase / Menu
3.1 FRONTAL SIDE
5- Keyboard
6- Switch
7- SD card
8- Printer
9- Info display

MƎDEA GB –Rev. 02 del 06.02.2019
C/Doc/Manuali e doc/Settore dentale/Medea
17/93
10- Drainage used water
11- Bacterial filter
12- Door switch
13- Drainage clean water
24 - Door switch
3.2 BACK SIDE
14- Labeller connection
15- Safety valve
16- 230v/50Hz 10A Power outlet
for connection to the clean water
17- Power cord
18- CE plate
19- Drainage used water
20- Drainage clean water
21- Double safety thermostat
22-Manual reset thermostat for
chamber resistance
23- Safety thermostat
3.3 VACUUM PUMP

MƎDEA GB –Rev. 02 del 06.02.2019
C/Doc/Manuali e doc/Settore dentale/Medea
18/93
3.4 DESCRIPTION OF INTERIOR WATER TANKS
The autoclave is equipped with two independent water tanks, respectively, for pure water and that used ( each tank
has a usable capacity of 3.5 litres). The drainage port for the water used is black.
The lower tank (12) is called “clean water tank” and must be filled with distilled or demineralized water required for
the sterilization process. Please find below the quality table of the water to be used.
The tank has a minimum (0.8 litres) and maximum level sensor (3.5 litres). When the water level falls below the
minimum threshold and you are choosing a sterilization cycle, the display shows a message of request for water.
Filling can be:
- By connecting to the KIARA TEC connected to the quick attack (20)
- By EXTERNAL TANK complete with WATER ENTRY DEVICE connected to the quick attack (20)
Use the quick port (13) for drain the clean water tank.
The upper tank (21) is called "water tank used" and contains the used water collected at the end of each cycle. The
tank is equipped with a sensor-level maximum (3.5 litres).
If it is connected to KIARA TEC the drain is automatic
If it is connect to EXTERNAL TANK the drain will be drainage into sewerage system or into a external tank.
Water consumption per cycle varies depending on the type and weight of the
load. The clean water tank capacity is enough for 2 to 3 cycles of sterilization.
Never reuse the water used!
The length of the exhaust pipe should not exceed 5 mt.
The discharge point must be at least 30 cm below the autoclave floor

MƎDEA GB –Rev. 02 del 06.02.2019
C/Doc/Manuali e doc/Settore dentale/Medea
19/93
3.5 QUALITATIVE WATER TABLE
CEN STANDARD DIN EN 285
MAXIMUM VALUE
Evaporation residue
10mg/l
Silicon oxide (SiO2)
1mg/l
Iron
0,2mg/l
Cadmium
0,005mg/l
Lead
0,05mg/l
Remains heavy metal (excluded iron cadmium and lead)
0,01mg/l
Chloride
2mg/l
Phosphate
0,5mg/l
Conductivity (at 20° C)
15μs/cm
Ph value
rom 5 t 7
Aspect
colourless, clan and free of sediment
Hardness
0,02 mmol/l
NOTE: the use of feed water containing concentrations higher than those indicated in the table above may significantly reduce
the life of the device causing serious damages to its components and determining the loss of the warranty.
3.6 CLEAN WATER LOAD
FILLING THE TANK WITH CLEAN WATER
Use only distilled water of high quality! Follow the qualitative water table!
3.7 AUTOMATIC LOADING
In the SETTINGS choose time of loading water:
AUTOMATIC
LOADING
40 min.
It is recommended to set about 20-40 minutes if the water supply system has no less than 2 atmospheres.
The valve of the water purifier starts working for the set minutes pressing the START button.
t.o. LOADING
000
T.O. LOADING means TIME OUT LOADING. It’s a valve opening timer of the purifier with sufficient time for refilling
the tank with clean water to a minimum. The three zeros indicate that no passage of water has been found therefore
the quality has not been checked. In case of normal water passage numbers instead of zeros attest to the quality of
the water.
Loading…
010

MƎDEA GB –Rev. 02 del 06.02.2019
C/Doc/Manuali e doc/Settore dentale/Medea
20/93
t.o. LOADING
000
CONNECTION TO KIARA-TEC:
1. Make sure the tap of the depurator is opened.
2. The technician must verify the correct operation of the filling device present in the autoclave.
3. For the detailed calibration, refer to the instruction manual of our depurator.
Insert the depurator’s attack to the rear of the sterilizer (20).
Connect the plug of the depurator into the plug to the back of the sterilizer (16).
CONNECTION CLEAN WATER TO EXTERNAL TANK:
1. Mount the tank support (29) to the cover (there are 4 cuts in which to insert it)
2. Fix the electrovalve (27) on the rear side of the machine (see photo below):
Unscrew the rear panel screw
Position the electrovalve support (see arrow)
Screw everything with the screw previously
unscrewed
For the first functioning of purifier, check the pressure gauge. The pressure must be at least 2 bars.
Otherwise, extend the filling T.O.
After replacing the cartridges, turn off and then switch on the sterilizer.
Just in case use depurator, it is the task manager, to provide the sterilizer a check valve
conforms to IEC 61770.
Table of contents
Other Reverberi Laboratory Equipment manuals

Reverberi
Reverberi SERENA 18 Guide

Reverberi
Reverberi SERENA 9046 User manual

Reverberi
Reverberi STERILIX 2 PLUS User manual
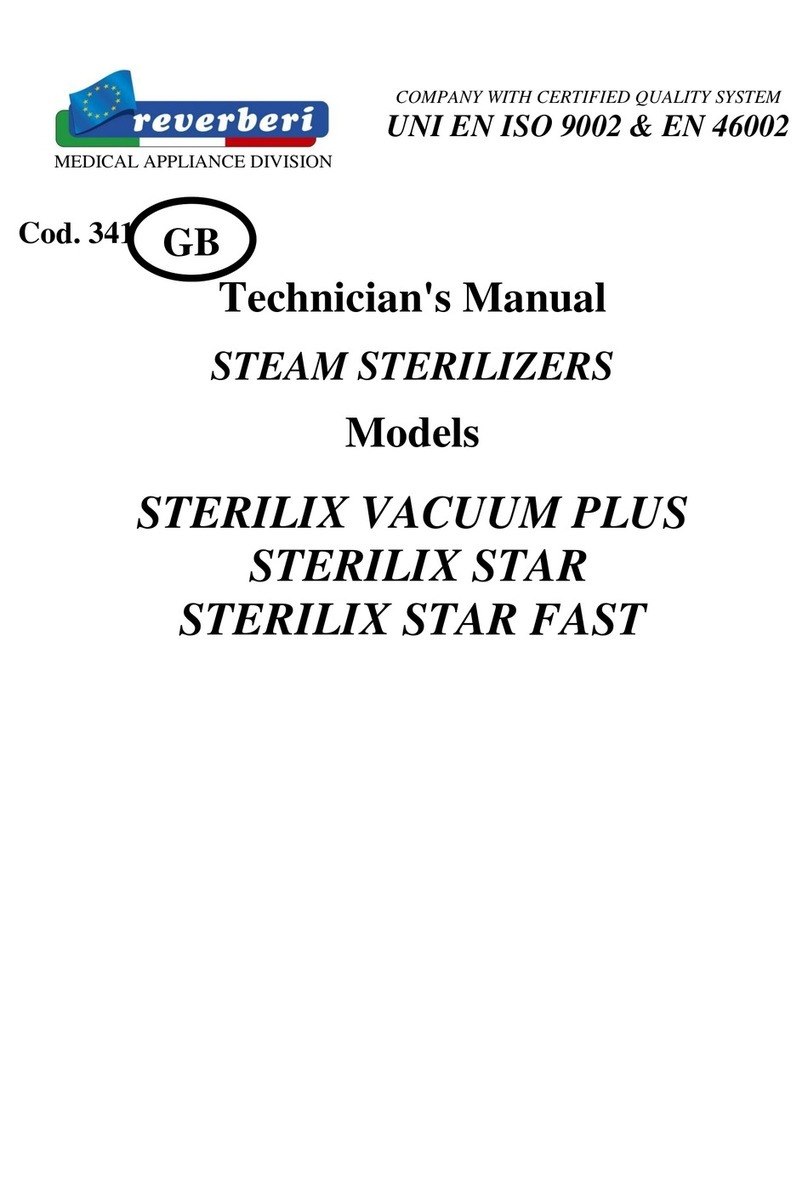
Reverberi
Reverberi STERILIX VACUUM PLUS User manual
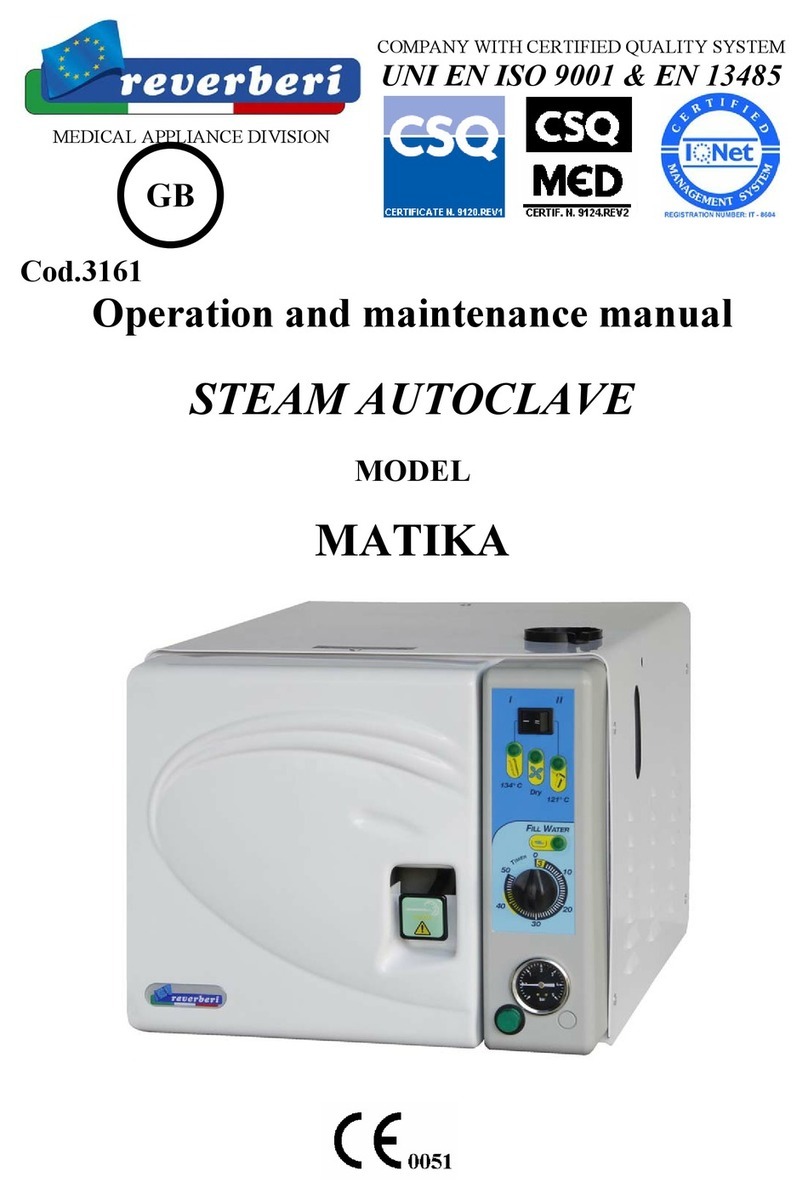
Reverberi
Reverberi MATIKA User manual
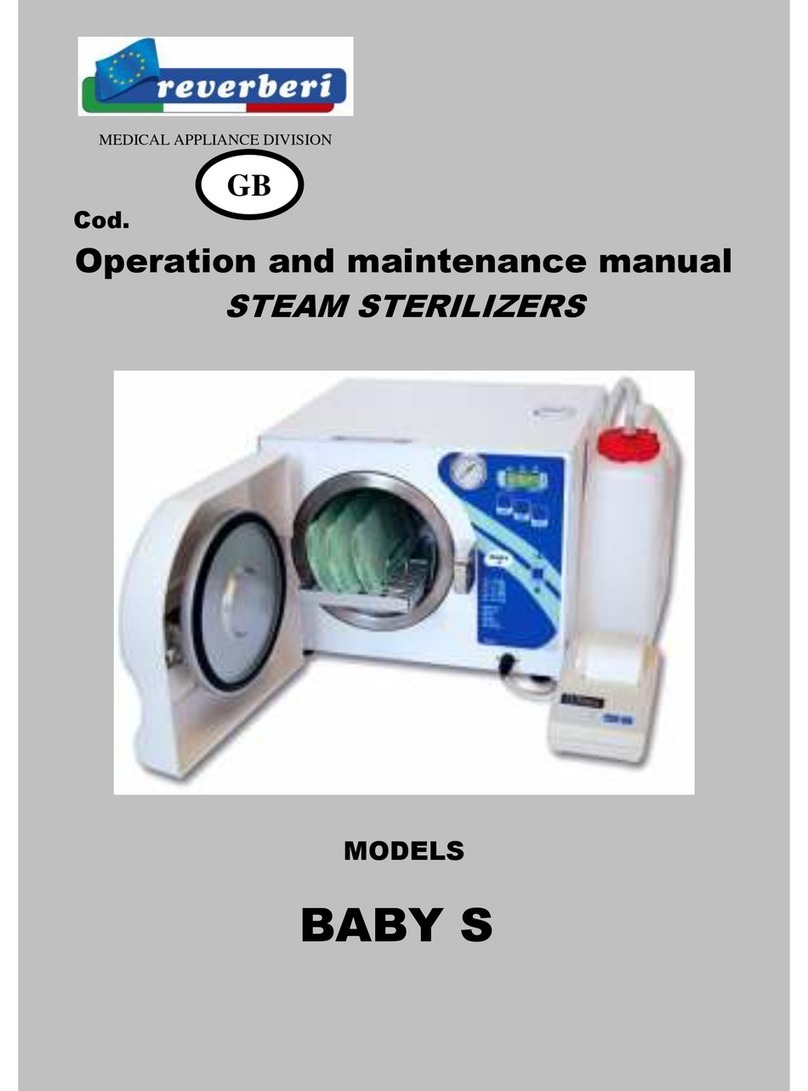
Reverberi
Reverberi BABY S User manual
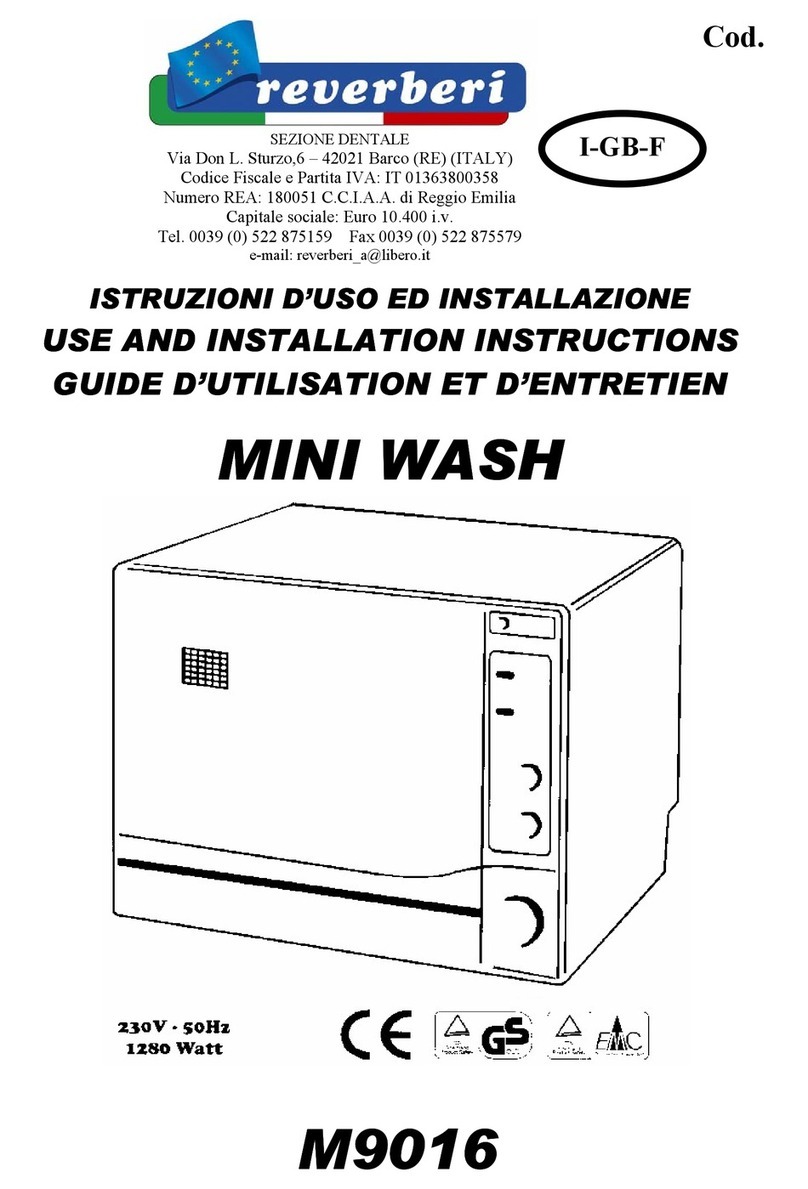
Reverberi
Reverberi MINI WASH Technical manual
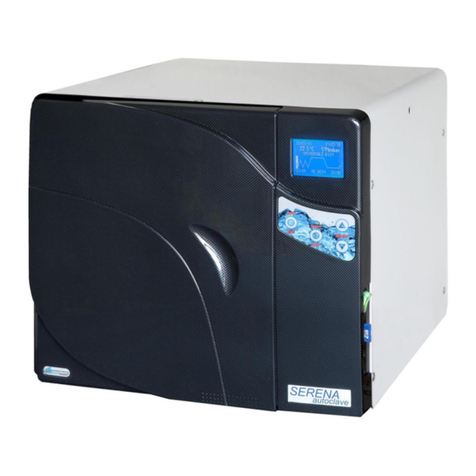
Reverberi
Reverberi SERENA User guide
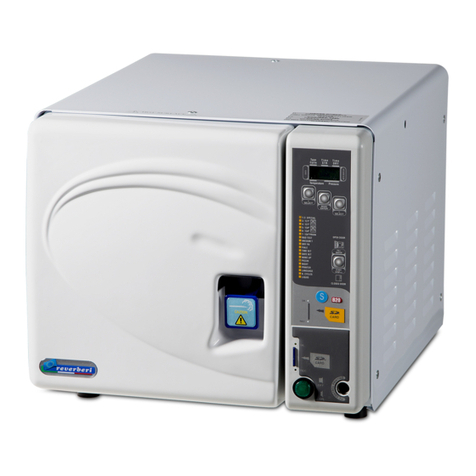
Reverberi
Reverberi PRATIKA S16 User manual

Reverberi
Reverberi Full Clave B 20 User manual