RHEONIK RHE21 Installation manual

RHE21 Installation & Startup Guide –Doc. No. 8.2.1.04 –Ver. 1.31
1 / 58
RHE21
Installation & Startup Guide
Documen t No.: 8.2. 1.0 4
Version 1. 31 APR-202 1

RHE21 Installation & Startup Guide –Doc. No. 8.2.1.04 –Ver. 1.31
2 / 58
Table of Contents
1General Information ..........................................................................................................4
1.1 Important Safety Instructions for operating Coriolis Flowmeters......................................4
1.2 Manufacturer’s Liability......................................................................................................4
1.3 Additional Resources ..........................................................................................................4
2Quick Start ........................................................................................................................5
3Installation........................................................................................................................5
3.1 Mechanical Installation ......................................................................................................5
3.2 Electrical Installation ..........................................................................................................6
Interconnecting RHE/RHM..................................................................................................6
3.2.1.1 RHM Electrical Connection Type JM & SM (11 Terminals) .................................................6
3.2.1.2 RHM Electrical Connection Type TM (PTFE Cable) .............................................................7
3.2.1.3 RHM Electrical Connection Type JO (12 Terminals)............................................................8
3.2.1.4 Legacy RHM Sensors (9 Terminals).....................................................................................9
Power Supply, Grounding and I/O Connections Overview ...............................................11
3.2.2.1 Grounding .........................................................................................................................13
3.2.2.2 12V to 24V DC Power Supply ............................................................................................13
3.2.2.3 100V to 240V AC Power Supply ........................................................................................13
3.2.2.4 AC and DC Supply..............................................................................................................14
Control Inputs and Outputs ..............................................................................................14
3.2.3.1 Digital Outputs..................................................................................................................14
3.2.3.2 Analog Outputs.................................................................................................................16
3.2.3.3 Digital Inputs.....................................................................................................................18
3.2.3.4 Analog Input .....................................................................................................................19
4Operation and Configuration ........................................................................................... 20
4.1 Function of the Pushbuttons.............................................................................................20
4.2Passcodes and Menu Selection.........................................................................................21
4.3 Zero Offset Calibration......................................................................................................22
4.4 Change of Positive Flow Direction ....................................................................................22
4.5 Temperature Measurement Configuration ......................................................................23
4.6 Output Configuration........................................................................................................24
Analog Output Configuration ...........................................................................................24
Digital Output Configuration ............................................................................................25
Digital Input Configuration ...............................................................................................28
5Remote Operation ........................................................................................................... 29
5.1 RS485 ................................................................................................................................29

RHE21 Installation & Startup Guide –Doc. No. 8.2.1.04 –Ver. 1.31
3 / 58
5.2 HART .................................................................................................................................30
6Service and Maintenance................................................................................................. 31
6.1 Maintenance and Calibration...........................................................................................31
6.2Troubleshooting................................................................................................................31
6.3 Service...............................................................................................................................32
6.4 WEEE and RoHS ................................................................................................................32
7Ordering Code ................................................................................................................. 32
Appendix A Ex-Safety Instructions................................................................................... 33
A.1 Safety instructions for the installation in a hazardous area:............................................33
A.2 System Description: ..........................................................................................................34
A.3 Electrical Safety Limits ......................................................................................................34
A.4 Thermal Safety Limits .......................................................................................................36
A.5 Grounding and Shielding ..................................................................................................36
A.6 Installation........................................................................................................................36
A.7 Electrical connection of power supply and I/O .................................................................38
A.8 Electrical connection to RHM and pressure sensor ..........................................................38
A.9 Ordering Code...................................................................................................................40
A.10 Technical Data ..................................................................................................................41
A.11 Compliance .......................................................................................................................41
A.12 Service and repair .............................................................................................................42
A.13 Contact address ................................................................................................................42
Appendix B Technical Information .................................................................................. 43
B.1 Technical Data ..................................................................................................................43
B.2 Mechanical Drawings .......................................................................................................45
B.3 Mounting Drawing............................................................................................................51
Appendix C CE Certificates .............................................................................................. 52

RHE21 Installation & Startup Guide –Doc. No. 8.2.1.04 –Ver. 1.31
4 / 58
1General Information
1.1 Important Safety Instructions for operating Coriolis Flowmeters
For RHE21 units requiring 12 to 24V DC power, the use of a properly grounded (PELV)
supply is highly recommended.
The use of shielded cables for all I/O signals is recommended to prevent interference
from high level EMI.
Only the specifically designed shielded cable supplied by Rheonik should be used to
connect RHE Transmitters to RHM Flow Sensors. Do not use other types of cable.
For safety instructions regarding RHM Coriolis Flow Sensors, please refer to the RHM
installation and startup guide manual.
These measuring instruments are not designed for, and should not be installed in, life-
preserving systems used in the medical, motor vehicle, aircraft, water craft or mining
industries.
All national regulations and standards regarding electrical installation must be
observed!
1.2 Manufacturer’s Liability
Rheonik assumes no liability for loss and/or consequential damages stemming from the
use of this product utilized in life-preserving systems in the medical, motor vehicle,
aircraft, water craft or mining industries.
Rheonik accepts no liability for loss or damage resulting from the improper use of any
of its products.
Rheonik assumes no liability for the loss of production and/or consequential damage
from the use of this product unless such liability has been expressly and contractually
agreed.
Rheonik provides a standard one year from shipment warranty on all products for
workmanship and materials. Performance of this warranty will be at the Rheonik
manufacturing facility.
Rheonik assumes no liability for determining the suitability of its products in any specific
application. This is the sole responsibility of the end user.
1.3 Additional Resources
This guide is intended as a quick reference instruction to aid the
installation and startup of an RHE21 Coriolis mass flow transmitter
with an RHM flow sensor and is a supplement to the documentation
found in the RHE2X Desktop Reference. The RHE2X Desktop
Reference and further resources are available for download from the
Rheonik website:
www.rheonik.com

RHE21 Installation & Startup Guide –Doc. No. 8.2.1.04 –Ver. 1.31
5 / 58
2Quick Start
A complete flowmeter system typically consists of a:
RHMxxx Sensor
RHExx Transmitter
Interconnection cable
Carry out the following steps to prepare the flow meter for operation:
1) If not already done, install the RHM sensor in line (refer to the RHM Coriolis Sensor
installation and startup guide for additional information on mechanical installation).
Connect the interconnecting cable to the RHE using the terminating scheme that matches
the RHM electrical connection type (see section 3.2.1 for electrical termination schemes).
2) Connect all signal input, output and communications interface wiring as required (section
3.2.3).
3) Connect power supply (section 3.2.2).
NOTE:
For safety, always connect the protective ground.
For installations in hazardous areas, a protective ground must always be connected.
4) Switch on the power supply. The display backlight will light up and after a power up
sequence, the display will show the flow measurement screen. In case of an error the
backlight will turn red.
5) Flush the RHM flow sensor with process fluid and ensure that it is free of air bubbles (in
case of a liquid process fluid) or liquid droplets (in case of a gaseous process fluid).
6) Wait until the RHM temperature has stabilized and then carry out a zero point calibration
(section 4.3):
Ensure a zero flow condition is present in the flow sensor by closing isolation valves
Initiate zeroing of the sensor and wait for the zeroing procedure to complete
Open isolation valves to allow flow through the sensor
3Installation
3.1 Mechanical Installation
The RHE21 transmitter are designed for wall or pipe bracket mounting in harsh environment. The
enclosure is rated IP66 / type 4X. The RHE21-EP can also be installed behind a panel.
The RHE21 should be mounted with 4 screws M6 or #12 (e.g. UNC12-24) on a metal mounting
plate with minimum thickness of 6mm (1/4”).
Note: The screw must enter the nut by at least 4 full turns!
Alternatively a pipe mounting is possible. A set of 2 pipe brackets is available as accessory.
The mechanical drawings of the different RHE21 as well as the mounting drawing for pipe bracket
mounting can be found in appendix B.

RHE21 Installation & Startup Guide –Doc. No. 8.2.1.04 –Ver. 1.31
6 / 58
3.2 Electrical Installation
Caution, the surface of the connection box may be hot if a hot fluid is running through
the RHM sensor.
Unused cable entries at the RHE21 have to be closed by suitable sealing plugs.
Electrical connections to the transmitter are made either with screw terminals or push-in
connectors. To connect or disconnect a wire to a push-in connector push down the cable release
operator while inserting or drawing out the wire.
Interconnecting RHE/RHM
Except for the RHE21 construction types E5 and H3 all RHE21 are delivered with an integrated
cable for connection with an RHM sensor. They can be directly connected to the RHM sensor
according to Tables 2 to 5.
The RHE21 construction types E5 and H3 have to be connected to an RHM sensor according to
Tables 2 to 5 using the bottom RHE21 terminal box. Only interconnecting cable (ARHE-Cx cable)
supplied by Rheonik should be used to connect an RHE to an RHM. Cable not supplied by
Rheonik may lead to a poor performance of the Coriolis mass flow meter.
Table 1: Overview RHM electrical connection types
RHM electrical
connection type
Junction box / terminals
Section
JM, SM
aluminium, stainless steel / 11
3.1.1.1
TM
- / PTFE cable with 9 wires + shield
3.1.1.2
JO
aluminium / 12
3.1.1.3
legacy type
aluminium, stainless steel / 9
3.1.1.4
3.2.1.1 RHM Electrical Connection Type JM & SM (11 Terminals)
Table 2: RHE21 Wiring Plan for RHM Connection Types JM, SM
RHM Terminal
Cable
RHE21 Terminal 1
No.
Name
Wire
Color
Function
No.
Name
1
DRV H
Brown
Drive Coil high
1
DrvH
2
DRV L
Blue
Drive Coil low
2
DrvL
3
PT P
Red
Temperature Sensor Pipe
3
PtP
4
PT G
Pink
Temperature Sensors GND
4
PtG
5
PT T
Orange
Temperature Sensor Torsion
5
PtT
6
PUA H
Yellow
Pick Up Coil A high
6
PkAH
7
PUA L
Green
Pick Up Coil A low
7
PkAL
8
PUB L
Grey
Pick Up Coil B low
8
PkBL
9
PUB H
White
Pick Up Coil B high
9
PkBH
10 2
PE
(yel/grn)
Shield
10
PE
11 2
PE C
(yel/grn)

RHE21 Installation & Startup Guide –Doc. No. 8.2.1.04 –Ver. 1.31
7 / 58
Figure 2: RHE21 Wiring
with RHM Connection
Type TM
1 Connection only necessary for RHE21 construction types E5 and H3 without integrated sensor cable.
2The RHM has 2 terminals for the connection of the cable shield. One is connected directly to PE, the other via a
1nF capacitor (PE C).
The best protection against RF EMI is achieved if the cable shield is connected at both ends. In installations with a
long interconnecting cable between RHE and RHM, significant potential difference between the PE at the RHE and
the PE at the RHM may occur. Connecting the shield to PE at both ends might lead to undesirable current flow in
the shield. In situations where a high potential difference is present between the RHE and RHM, we recommend
grounding via the PE C terminal on the RHM side.
Figure 1: RHE21 Wiring with RHM Connection Types JM, SM
Upon power up, if the RHE indicates an error and the temperature measurement on the bottom
right of the display shows “ -.--°C/°F ” please check the temperature measurement configuration
setting in the RHE (section 4.5).
The correct temperature measurement configuration setting for an RHM with connection type
JM or SM is “7”.
3.2.1.2 RHM Electrical Connection Type TM (PTFE Cable)
Table 3: RHE21 Wiring Plan for RHM Connection Type TM
1The shield of the cable is connected internally to the housing of the RHM. If there is a
risk of a significant potential difference between the housing of the RHM and the PE
terminal of the RHE, the shield should be connected to the RHE PE connection via a 1nF
Cable
RHE21 Terminal
No.
Wire Color
Function
No.
Name
1
Brown
Drive Coil high
1
DrvH
2
Blue
Drive Coil low
2
DrvL
3
Red
Temp. Sensor Pipe
3
PtP
4
Pink
Temp. Sensors GND
4
PtG
5
Orange
Temp. Sensor Torsion
5
PtT
6
Yellow
Pick Up Coil A high
6
PkAH
7
Green
Pick Up Coil A low
7
PkAL
8
Grey
Pick Up Coil B low
8
PkBL
9
White
Pick Up Coil B high
9
PkBH
10 1
(yel/grn)
Shield
10
PE

RHE21 Installation & Startup Guide –Doc. No. 8.2.1.04 –Ver. 1.31
8 / 58
capacitor. Alternatively, a separate cable can be run for potential equalization between
the RHM case and the RHE and the shield left both unconnected and isolated at the RHE
or terminated to the PE connection via a 1nF capacitor.
Upon power up, if the RHE indicates an error and the temperature measurement on the bottom
right of the display shows “ -.--°C/°F ” please check the temperature measurement configuration
setting in the RHE (section 4.5).
The correct temperature measurement configuration setting for an RHM with connection type
TM is “7”.
3.2.1.3 RHM Electrical Connection Type JO (12 Terminals)
Table 4: RHE21 Wiring Plan for RHM Connection Types JO
RHM Terminal
Cable
RHE21 Terminal 1
No.
Name
Wire Color
Function
No.
Name
1
DRIVE +
Brown
Drive Coil high
1
DrvH
2
DRIVE -
Blue
Drive Coil low
2
DrvL
3
PT1 Pipe Supply
Red
Temperature Sensor Pipe
3
PtP
4
PT1 Pipe Sense
Pink
Temperature Sensors GND
4
PtG
5
PT 1/2 Common
-
-
-
-
6
Pick-Up left+
Yellow
Pick Up Coil A high
6
PkAH
7
Pick-Up left -
Green
Pick Up Coil A low
7
PkAL
8
Pick-Up right-
Grey
Pick Up Coil B low
8
PkBL
9
Pick-Up right+
White
Pick Up Coil B high
9
PkBH
10 2
GND
(yel/grn)
Shield
10
PE
11
PT2 Tor. Supply
Orange
Temperature Sensor Torsion
5
PtT
12
PT2 Tor. Sense
-
-
-
-
1 Connection only necessary for RHE21 construction types E5 and H3 without integrated sensor cable.
2The shield of the cable is connected through terminal 10 to the housing of the RHM. If there is a risk of a significant
potential difference between the housing of the RHM and the PE terminal of the RHE, the shield should be connected
to the RHE PE connection via a 1nF capacitor. Alternatively, a separate cable can be run for potential equalization
between the RHM case and the RHE and the shield left both unconnected and isolated at the RHE or terminated to
the PE connection via a 1nF capacitor.

RHE21 Installation & Startup Guide –Doc. No. 8.2.1.04 –Ver. 1.31
9 / 58
Figure 3: RHE21 Wiring with RHM Connection Types J6 & JO
Upon power up, if the RHE indicates an error and the temperature measurement on the bottom
right of the display shows “ -.--°C/°F ” please check the temperature measurement configuration
setting in the RHE (section 4.5).
The correct temperature measurement configuration setting for an RHM with connection type
JO is “3”.
3.2.1.4 Legacy RHM Sensors (9 Terminals)
Table 5: RHE21 Wiring Plan for RHM legacy version
RHM Terminal
Cable
RHE21 Terminal 1
No.
Wire Color
Function
No.
Name
1
Brown
Drive Coil high
1
DrvH
2
Blue
Drive Coil low
2
DrvL
3
Red
Temperature Sensor Pipe Supply
3
PtP
4
Pink
Temperature Sensor Pipe Sense
4
PtG
5
Orange
Temperature Sensors Common
5
PtT
6
Yellow
Pick Up Coil A high
6
PkAH
7
Green
Pick Up Coil A low
7
PkAL
8
Grey
Pick Up Coil B low
8
PkBL
9
White
Pick Up Coil B high
9
PkBH
Screw Term 2
(yel/grn)
Shield
10
PE
1 Connection only necessary for RHE21 construction types E5 and H3 without integrated sensor cable.
2The shield of the cable is connected to the housing of the RHM using a screw terminal in the junction box. If there
is a risk of a significant potential difference between the housing of the RHM and the PE terminal of the RHE, the
shield should be connected to the RHE PE connection via a 1nF capacitor. Alternatively, a separate cable can be run
for potential equalization between the RHM case and the RHE and the shield left both unconnected and isolated at
the RHE or terminated to the PE connection via a 1nF capacitor.

RHE21 Installation & Startup Guide –Doc. No. 8.2.1.04 –Ver. 1.31
10 / 58
Upon power up, if the RHE indicates an error and the temperature measurement on the bottom
right of the display shows “ -.--°C/°F ” please check the temperature measurement configuration
setting in the RHE (section 4.5).
The correct temperature measurement configuration setting for an RHM legacy sensor is “1”.
Figure 4: RHE21 Wiring with RHM legacy Sensors

RHE21 Installation & Startup Guide –Doc. No. 8.2.1.04 –Ver. 1.31
11 / 58
Power Supply, Grounding and I/O Connections Overview
For connections longer than 0.5m shielded cables should be used. For connections longer than
3m, additional ferrite filter beads close to the RHE are recommended for avoiding RF EMI.
The power supply input is protected by a fuse. As a protection against fire in case of a short in
the cable, the supply side of the cable should be protected by a fuse (see figure 7, SI1) with a
rating not higher than the current carrying capacity of the cable.
For RHE21 constructions types E* the power supply and I/O connections are located in the
terminal box shown in Figure 5. The available I/O connections depend on the I/O configuration
option of the RHE21.
Figure 5: RHE21 Types E* with Terminal Box for Power Supply, I/O Connection and optional Layout
For RHE21 constructions types H* the power supply and I/O connections are located in the
housing of the transmitter as shown in Figure 6. The upper part of the housing has to be screwed
off for connection and the wires must be put through the two cable entries using suitable cable
glands.
Figure 6: RHE21 Types H* with integrated Connectors for Power Supply and I/O Connection
I/O
power
supply

RHE21 Installation & Startup Guide –Doc. No. 8.2.1.04 –Ver. 1.31
12 / 58
Depending on the I/O configuration (please see section 7 for further information) of the RHE21
only a limited number of I/O and power supply connections are available. Table 6 lists all I/O and
power supply connections.
Table 6: I/O and Power Supply Connections
Terminal
No.
Function
Availability
20
Power Supply
+24V
RHE21-**D1,U1-****-****-***
21
GND
RHE21-**D1,U1-****-****-***
22
PE
all versions
23
L
RHE21-**A1,U1-****-****-***
24
N
RHE21-**A1,U1-****-****-***
31
Digital I/O
DO1
all versions (except i* versions)
32
DO2
RHE21-****-**S1,P1-****-***
40
DO1 C
RHE21-****-**i1,i2,i3,iH-****-***
41
DO1 E
RHE21-****-**i1,i2,i3,iH-****-***
42
DO2 C
RHE21-****-**i1,i3-****-***
43
DO2 E
RHE21-****-**i1,i3-****-***
35
DI1
all versions (except i* versions)
37
GND
all versions (except i* versions)
50
Analog 4-20mA
Output
+24Vo
RHE21-E***-**P1-****-***
RHE21-H***-****-****-***
51
AO1H
RHE21-****-**P2,PH,CH,i1,i2,i3,iH-****-***
52
AO1L
RHE21-****-**P2,PH,CH,i1,i2,i3,iH-****-***
RHE21-H***-**S2,SH-****-***
53
AO2H
RHE21-****-**P1,P2,PH,CH,i2,iH-****-***
54
AO2L
RHE21-****-**P1,P2,PH,CH,i2,iH-****-***
RHE21-H***-**S1,S2,SH-****-***
55
AO1
RHE21-E***-**S2,SH-****-***
56
AO2
RHE21-E***-**S1,S2,SH-****-***
57
GND
RHE21-****-**S1,S2,P1,SH-****-***
RHE21-H***-****-****-***
60
Analog 4-20mA
Input
AI+
RHE21-E5,H3**-**CH-****-***
61
AIG
RHE21-E5,H3**-**CH-****-***
68
PE
RHE21-E5,H3**-**CH-****-***
70
RS485 Interface
RS485A
all versions
71
RS485B
all versions
The cables used for power supply and grounding must comply with the national
requirements. If required, certified cables must be used. The minimum cross section is
0.35mm² (AWG 22) for DC supply cables and 0.5mm² (AWG 20) for mains supply cables.
The RHE21 do not contain a mains switch. A switch or circuit breaker close to the RHE21
must be included in the supply line. The switch must be marked correspondingly.

RHE21 Installation & Startup Guide –Doc. No. 8.2.1.04 –Ver. 1.31
13 / 58
3.2.2.1 Grounding
RHE21 transmitters must be grounded. Ground the RHE by either connecting a ground to
terminal 22 (PE) or to the M4 screw type terminal on the left lower mounting flange. The cross
sectional area of the grounding wire must be equal to or larger than the conductors used for any
supply or I/O connection.
Note: National and Local electrical code requirements may contain additional grounding
requirements. Please ensure that all grounding to carried out to these [legal] requirements.
3.2.2.2 12V to 24V DC Power Supply
Units for use with a DC power supply (order
code options D1 and U1) require a regulated DC
supply voltage of 12V or 24V. They will operate
with a power supply in the range 10V to 28V.
Connect the positive supply to terminal 20 and
0V to terminal 21.
Terminals 21 (0V) and 22 (PE) are connected via
a 1kΩ resistor. The resistor can withstand a
potential difference of up to 30V between 0V
and PE, but voltage differences above 5V should
be avoided.
3.2.2.3 100V to 240V AC Power Supply
Units for use with an AC power supply (options
A1 and U1) will operate with any AC supply with
nominal 100V to 240V, 50H to 60Hz. Voltage
limits are 90V to 264V.
Connect the live or hot wire (L) to terminal 23
and the neutral wire (N) to terminal 24.
The AC supply terminals are completely
isolated from PE (terminals 10, 22, 68) and GND
(terminals 21, 37, 57).
Figure 7: DC Power Supply
Figure 8: AC Power Supply

RHE21 Installation & Startup Guide –Doc. No. 8.2.1.04 –Ver. 1.31
14 / 58
3.2.2.4 AC and DC Supply
Units with power supply option U1 (only available for construction type H*) can be operated from
both DC and AC power supplies. Both can be connected simultaneously and the RHE will be
powered up as long as one of the supplies is present and within operating tolerance.
The U1 power supply option is designed
to be used where, for instance, battery
backup of the flow meter is required.
Connect an AC supply to terminal 23 and
24 (see section 3.2.2.3) and a DC supply
to terminals 20 and 21 (see section
3.2.2.2).
If both power supply options are
connected, avoid a DC supply voltage
higher than 23V to ensure that the AC
power supply is used. If the AC supply is
disconnected, the DC supply will be used
to power the RHE until the Voltage
present drops below 10V.
An RHE/RHM flow meter has a typical
power consumption of around 3W. If a
12V / 100Ahr battery is used as the DC
input to the RHE, the unit would operate for more than 10 days after the AC supply had been
disconnected.
Control Inputs and Outputs
In general, shielded cables should be used for cable connections longer than 0.5m. For cable
connections longer than 3m, it is recommended that ferrite filter beads are installed close to the
RHE terminations to help avoid RF EMI.
3.2.3.1 Digital Outputs
3.2.3.1.1 Non intrinsically safe Digital Outputs
The RHE21 can be supplied with up to two digital outputs.
Outputs DO1 and DO2 are universal outputs and can be used as frequency, pulse or
control/status outputs.
Outputs DO3 and DO4 are control/status outputs only.
Digital outputs are push-pull outputs compliant to IEC 60946. They can drive loads connected to
ground and loads connected to +24V.
Figure 9: Universal Power Supply

RHE21 Installation & Startup Guide –Doc. No. 8.2.1.04 –Ver. 1.31
15 / 58
Figure 10: Digital Outputs
Connect the output of the RHE to the load. Connect the other side of the load to either GND or
to the positive supply rail. With a grounded load, the output current should be limited to 20mA
(480mW at 24V). With a load connected to the positive supply rail the output can drive up to
100mA (2.4W at 24V).
The output can drive relays directly as well. Relays should be connected between the output and
the positive supply rail.
3.2.3.1.2 Intrinsically safe Digital Outputs
NOTE: Intrinsically safe I/O circuits must only be operated with certified barriers or isolating
amplifiers
The RHE21 can be supplied with up to two intrinsically safe digital outputs.
Outputs DO1 and DO2 are universal outputs and can be used as frequency, pulse or
control/status outputs.
As a standard the outputs are floating open collector outputs.
Figure 11: Digital Output with Relays

RHE21 Installation & Startup Guide –Doc. No. 8.2.1.04 –Ver. 1.31
16 / 58
Figure 12: Intrinsically Safe Digital Outputs
Connect the output of the RHE to the isolating switching amplifier.
If an open collector output of the RHE21 is connected to a NAMUR isolating switching amplifier,
it might be recommended to disable the short / open supervision of the amplifier.
3.2.3.2 Analog Outputs
3.2.3.2.1 Non intrinsically safe Analog Outputs
RHE21-H*:
An RHE21-H* transmitter can be supplied with up to two 4-20 mA analog outputs. The outputs
can be connected in a passive/floating configuration or as active outputs for ground referenced
loads.
Output 1 can optionally be equipped with a HART digital communications interface.
For a floating output connect terminal 51 (53 for output 2) to the positive supply rail and terminal
52 (54 for output 2) to the input of local display/PLC/supervisory control system etc.
DOn C
DOn E

RHE21 Installation & Startup Guide –Doc. No. 8.2.1.04 –Ver. 1.31
17 / 58
Figure 123: RHE21-H* Analog Outputs
For an active output connect terminal 51 (53 for output 2) to terminal 50 and connect the load
between terminal 52 (54 for output 2) and terminal 57.
A protective resistor can be connected in series with the transmitter output and the load. Please
note, with a 24Vdc supply, the maximum total load resistance is 600 Ω.
For analog outputs with HART communication, a load resistance of 250 Ω is recommended.
RHE21-E*:
The RHE21-E***-**S* have 1 or 2 active, grounded analog
outputs according to Figure 14. Units with I/O version S1
have output AO2, terminal 56. Units with I/O version S2 or
SH have 2 outputs, output AO1 (terminal 55) and AO2
(terminal 56). Connect the load as shown between
terminal 55 and 57 or 56 and 57.
The RHE21-E***-**P1 have 1 passive floating analog
output AO2 (terminals 53 and 54) which also can be wired
as active grounded output according to Figure 13, as
described above.
The RHE21-E***-**P2, -**PH and -**CH have 2 passive
floating analog outputs AO1 (Terminals 51 and 52) and
AO2 (terminals 53 and 54). Connect the outputs according
to Figure 13, left drawing. A connection for active
operation according to the right drawing is not possible as
those RHE21 do not provide terminal 50.
A protective resistor can be connected in series with the transmitter output and the load. Please
note, with a 24Vdc supply, the maximum total load resistance is 600 Ω.
For analog outputs with HART communication, a load resistance of 250 Ω is recommended.
Figure 134: RHE21-E*, active
Analog Output

RHE21 Installation & Startup Guide –Doc. No. 8.2.1.04 –Ver. 1.31
18 / 58
3.2.3.2.2 Intrinsically safe Analog Outputs
NOTE: Intrinsically safe I/O circuits must only be operated with certified barriers or isolating
amplifiers
An RHE21 transmitter can be supplied with up to two passive floating 4-20 mA analog outputs.
Output 1 can optionally be equipped with a HART digital communications interface.
Figure 15: RHE42 Intrinsically Safe Analog Outputs
Connect the output of the RHE to the isolating switching amplifier.
For analog outputs with HART communication, a HART transparent isolating amplifier must be
used.
3.2.3.3 Digital Inputs
RHE21 transmitters are equipped with one IEC60946 compliant digital input.
NOTE: Unless advised in advance of delivery, all digital inputs are configured by default for
active high operation at the factory. Units with active low operational inputs are available upon
request.
The digital input has an input resistance of 24 kΩ and when operated, will draw approx. 1mA
when connected to a 24Vdc supply.
AOn H
AOn L

RHE21 Installation & Startup Guide –Doc. No. 8.2.1.04 –Ver. 1.31
19 / 58
Figure 146: Digital Inputs
The digital input can be operated with an active DC signal instead of a switch. The maximum
input voltage must not exceed 30V DC. Note that inputs require a switching current of 0.6mA;
the minimum input voltage for a high reading is 14.4V DC.
3.2.3.4 Analog Input
The RHE21-E5 or RHE21-H3 can be equipped with a 4-20 mA analog input for connecting an
external transmitter (such as a pressure sensor) with a passive 4-20 mA output. The RHE21
transmitter provides power to the connected devices’ output.
The 4 –20mA analog input is connected to terminal 60 (positive) and terminal 61 (negative) in
the bottom terminal box. It is highly recommended to use a shielded cable and that the shield is
connected to terminal 68 (PE) at the transmitter.
The analog input in RHE21 transmitters is certified for use with an external transmitter in a
hazardous area which includes a certified barrier circuitry for connection with an intrinsically safe
device.
The negative (AIG) terminal of the input is internally connected to PE, so it is important to connect
only devices that are floating.
Figure 17: Analog Input

RHE21 Installation & Startup Guide –Doc. No. 8.2.1.04 –Ver. 1.31
20 / 58
4Operation and Configuration
RHE2X transmitters can be interrogated and configured in one of three ways:
1) Manually through the front panel user interface
Each RHE2X transmitter has a user operation interface consisting of a color LCD screen
and three pushbuttons. The screen and pushbuttons are used to navigate through a
hierarchical menu structure that logically and intuitively organizes the various features
and functions available within the programming set supplied with the instrument. This
chapter gives a short introduction into operation of the RHE21 through the front panel
user interface. For more detailed information, please refer to the RHE2X Desktop
Reference Manual.
2) By RHECom PC software through the RS485 serial port
See Chapter 5 for details
3) Through Modbus commands via the RS485 serial port
See Chapter 5 for details
4.1 Function of the Pushbuttons
RHE2X transmitters are operated through three front panel pushbuttons. These are labeled
“ESC” [X], “NEXT” [>], and “ENTER” []. The function of these pushbuttons depends upon the
currently displayed screen.
The following table details button function in specific situations.
Table 7: Functions of the Pushbuttons
Button
Situation
Function
ESC
Menu Navigation
Navigates to the menu one level up
Number Input
Exits number input field and returns to the associated menu window without
saving any changes
NEXT
Menu Navigation
Selects the next menu item
During Number Input
Increments the number at the cursor position by one. Number increment is
circular: a ‘9’ increments to ‘0’ for decimal numbers, ‘F’ increments to ‘0’ for
hexadecimal numbers (used for service password)
Number Sign Change
Changes ‘+’ to ‘-’and vice versa. When entering a number with a sign
character, the cursor will start at the first number character to the right of
the sign character in the field. In order to reach the sign character, it is
necessary to traverse all the way to the rightmost character and then start
at the beginning of the input field again
Decimal Point Position
Change
Shifts the decimal point and cursor position one place to the right
End of input line
The entire number will flash upon pressing ENTER at the rightmost character
in an input field. Pressing NEXT when the field is flashing will return the
cursor to the start of the input line
ENTER
Menu Navigation
Navigates to the menu one level down or enters an input screen
During Number, Sign or
Decimal Point entry/
change
Moves the cursor one character to the right in an input field. Note that when
a number is entered that is not in the parameters’ acceptable range, the field
will change to inverse colors (light on dark instead of dark on light). When a
number is not within an acceptable range, pressing ENTER at the rightmost
character in the field will return the cursor to the leftmost position in the
field for re-editing.
Table of contents
Other RHEONIK Transmitter manuals
Popular Transmitter manuals by other brands
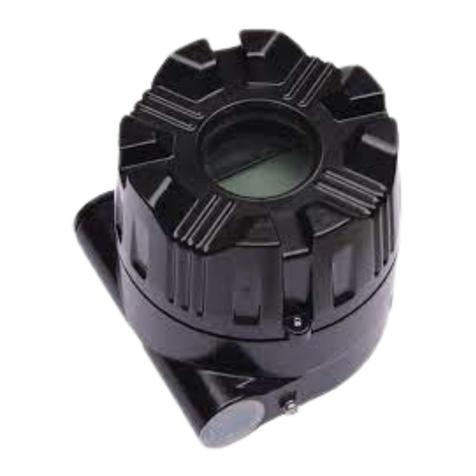
Ytc
Ytc SPTM-6V Series user manual
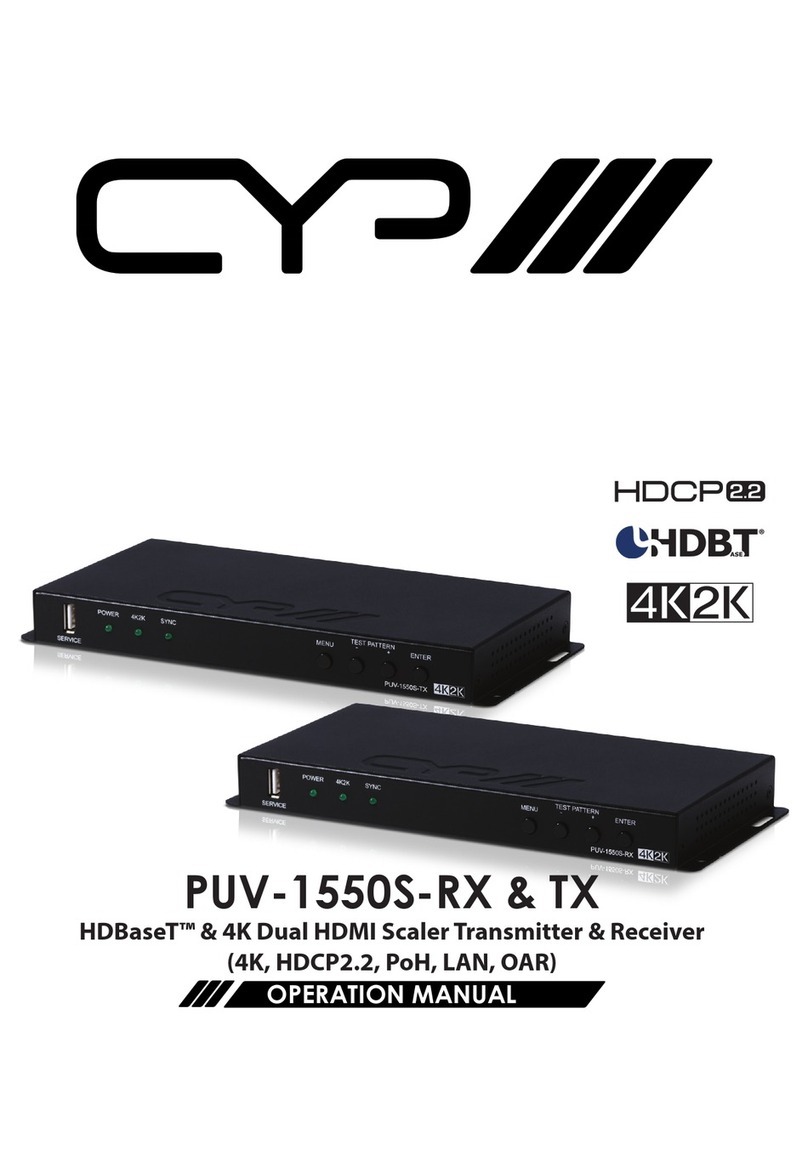
CYP
CYP PUV-1550S-RX Operation manual
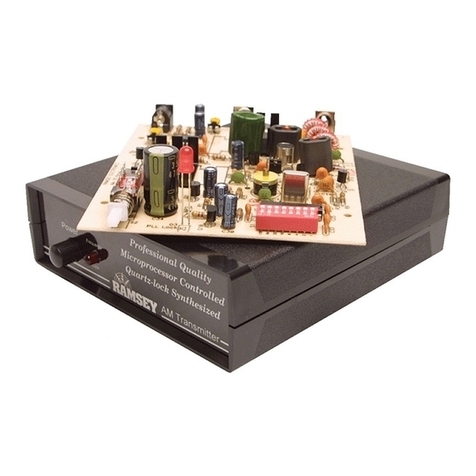
Ramsey Electronics
Ramsey Electronics AM25 Assembly and instruction manual
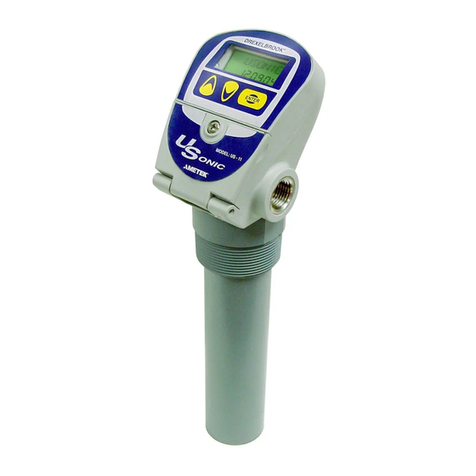
Ametek Drexelbrook
Ametek Drexelbrook USonic Series Installation and operating instructions
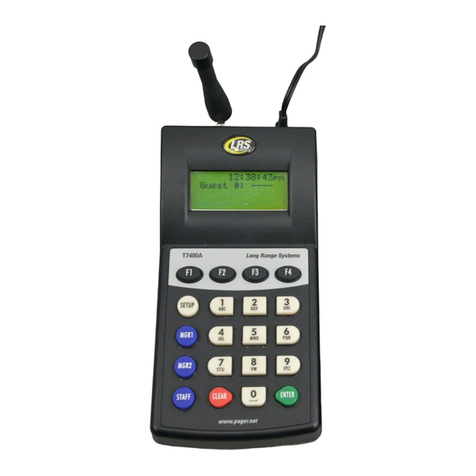
LRS
LRS T7400A Setup guide
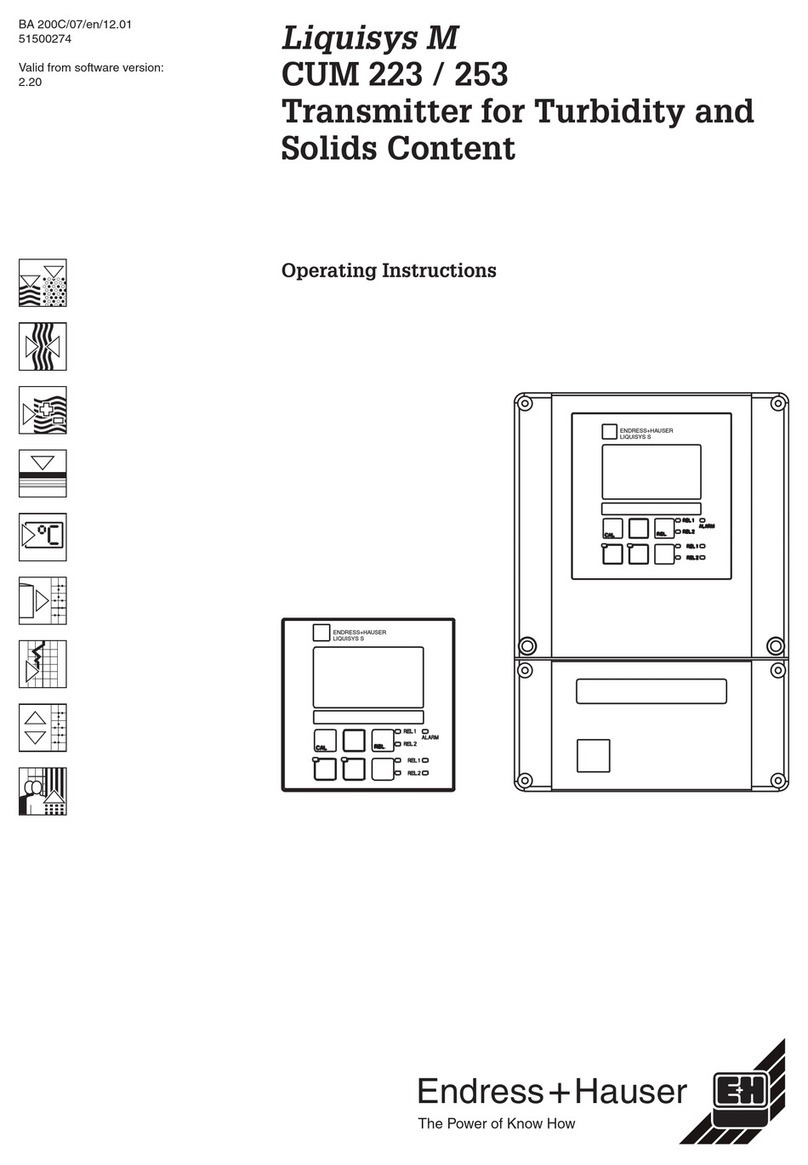
Endress+Hauser
Endress+Hauser Liquisys M CUM 223 operating instructions