Roger PR402 User manual

PR402EN.doc
1
PR402 v1.0
S
INGLE
D
OOR
A
CCESS
C
ONTROLLER
F
IRMWARE VERSION
117.0
Installation Manual

PR402EN.doc
2
General Description
The PR402 controller is dedicated for use in Access Control and Time & Attendance systems. It may be configured to perform both function
simultaneously or exclusively. Controller is equipped with switched mode power supply circuit adopted for operation with sealed gel type
battery. PR402 offers four NO/OC inputs, two relay outputs and two transistor outputs. Inputs and outputs can be configured to several pre-
defined functions. Two remote PRT series access terminals can be connected to controller. PR402 can register up to 4000 users, every user
can be identify by Card, PIN or both method together (Card+PIN). Controller offers In Circuit Programming feature which enables firmware
downloading into microprocessor memory. PR402 may operate is autonomic mode or in networked system equipped with CPR control panel
or without it. Controller can be programmed from PC only, manual programming is not available, programming from PC requires UT-2
communication interface.
PR402 features
-single door access controller,
-Entry/Exit control,
-autonomic or networked operation,
-Card and/or PIN identification,
-4000 users,
-250 access groups,
-500 access zones.
-99 general purpose time schedules,
-holiday definition,
-non violate 32 000 events buffer,
-real time clock,
-four multipurpose NO/NC inputs,
-two multipurpose, electronically protected 1A transistor outputs,
-two relay output (form C contacts, 1.5A rated),
-inputs and outputs controlled by time schedules,
-four user types: Normal, Swicher full, Switcher limited and Master,
-card usage limit definition,
-Door contact, Exit button, Forced entry, Duress and more function,
-Soft or Hard mode anti-passback with reset schedule,
-Normal, Locked, Unlocked and Conditional Unlocked door modes, each under schedule control,
-Card or PIN or Card+PIN mode, both controlled by schedule,
-special entry modes; Card+Card and Conditional Access, both under schedule control,
-High Security identification mode (requires additional reader e.g. biometric),
-customer defined T&A registration modes,
-T&A registration modes controlled manually from keypad, by external line or by schedule,
-integration with IAS (Intruder Alarm System) through output line,
-Intruder Detector Input with automatic Arming/Disarming feature,
-operation with two remote PRT series access terminal or with one Wiegand 26/34/42/66 bit reader,
-operation with XM-2 remote input/output module,
-operation with PSAM-1 power supply alarm module,
-operation with XM-8 lift control modules,
-operation with biometric reader (Wiegand interface required),
-firmware download mode,
-metal case, metal keypad,
-RS485 interface,
-requires 20VAC/40VA supply,
-switched mode 1.5A power supply circuit,
-Windows 95/98/2K/NT/XP software, free for systems up to 8 doors,
-comply with EN 50133-4,
-CE mark.
Functional Description
Autonomic operation
In autonomic (standalone) mode after configuration procedure controller may continue operation and does not need to communicate with
any other equipment, events are recorded and stored in its internal memory banks, internal clock circuit control time schedules and access
levels.
Networked operation with CPR
When controller operates in networked system together with other controllers and CPR control panel, events are continuously transferred
from all controllers to CPR internal buffer. When connection with CPR is broken controllers automatically move to autonomic mode and store
events in theirs internal memory banks, after communication with CPR is restored controllers return automatically to networked, in both
cases controllers retain theirs full functionality (no functionality is lost or reduced). During normal system operation CPR synchronize real
time clocks of all controllers and stores events which occurred in system. Events stored in CPR and eventually in controllers’ buffers can be
manually downloaded to PC database or will be downloaded automatically anytime monitoring from PC is started. The main advantage of
networked system equipped with CPR is that events which have been occurred on controllers are instantly transferred to remote “secure”
buffer in CPR and that CPR continuously synchronize clocks on all controllers so even after long time period controllers’ clocks have the
same time.
Networked operation without CPR
When computer is connected to access control system and monitoring window of PR Master is active, events are continuously transferred
from controllers to PC database. When PR Master operate with monitoring window deactivated, events are stored in controllers’ internal
buffers and can be later transferred to PC using interactive command or will be downloaded automatically anytime monitoring window is
started.

PR402EN.doc
3
Note: Controller automatically detect CPR control panel or PR Master running in monitoring mode and move automatically to networked
mode and vice verso, when no CPR exist in access network or PR Master is operating without monitoring mode controller move to
autonomic mode.
Single Door Operation
PR402 may operate with two identification access points (access terminals), first located on EXIT side and second located on ENTRY side
of the door. As a default an EXIT terminal has address ID=1 where ENTRY terminal has address ID=0 (this assignments refer to PRT series
readers). A default address assignments for ENTRY and EXIT terminals may be changed by option Terminal ID=1 located on ENTRY, in
this case terminal ID=0 is treated as EXIT point and terminal ID=1 as ENTRY point. Generally ENTRY/EXIT assignments (which were
described above) refer to anti-passback function only, this function determines actual status of each users which may be logged on ENTRY,
EXIT or may have undefined status when controller didn’t register any login of particular user at all. If user made its last identification on
ENTRY terminal he/she has status as “logged inside” controlled premises, when last identification was performed on EXIT terminal user has
status “logged outside”. The User’s Last Login function which is available in RACS software determines the place where actually particular
user attend basing on APB Register, as mentioned above this register show the last entry.
Note: There are at least three cases listed below when ENTRY and EXIT terms are used:
•ENTRY/EXIT terms which refers to entry and exit terminal which control access to premises,
•ENTRY/EXIT terms which refers to entry and exit access points which define Attendance Area used in statistic
calculations,
•ENTRY/EXIT terms which refers to predefined T&A Mode of registration which can be assigned to particular access
point.
In each case listed above ENTRY/EXIT terms refer to another physical or logical matter, for example at the same time an access terminal
may have ENTRY status for anti-passback function, EXIT status for Attendance Area calculation function and may have EXIT mode
assigned for T&A registration.
RS485 Communication interface
Controller is equipped with RS485 serial communication interface which is dedicated for communication with PC computer and optional CPR
control panel, up to 32 controllers may be connected to one RS485 communication bus. Each controller connected to communication bus
must have individual address (ID number) from 00 to 99. The PR Master v4.x supervising program enables up to 10 separate networks to be
connected to one computer. Each network requires UT-2 communication interface which converts RS232 signals into RS485 standard. The
access network or even separate controller can be also connected to PC through computer network, this requires UT-4 communication
interface. The UT-4 acts as communication converter between TCP/IP network and RS485 serial interface.
Clock & Data interface
Controller is equipped with Clock and Data interface which is dedicated for connection with remote reader(s) and/or extension modules.
PR402 may operate with following external readers and/or modules:
-PRT Card/PIN reader,
-PRT User ID reader,
-Wiegand 26/34/42/66 bit PIN reader,
-Wiegand 26/34/42/66 bit Card reader,
-Wiegand 26/34/42/66 bit User ID reader,
-XM-2 input/output remote module,
-XM-8 input/output configured for lift control purpose,
-PSAM-1 power supply alarm module,
-Additional High Security reader (PRT series terminal or Wiegand interface reader).
Each PRT reader or extension module connected to Clock and Data interface must have its individual address (ID number) from 0 to 15. The
following assignments for address are valid:
Address
(ID number) Device Notes
0 PRT reader External reader, logically interpreted as ENTRY reader.
1 PRT reader External reader, logically interpreted as EXIT reader.
2 PRT reader The High Security reader on ENTRY.
3 PRT reader The High Security reader on EXIT.
4 PSAM-1
module Power supply alarm module, optional part of PS20 power supply.
5 XM-2 module The 2 inputs and 2 relay outputs extension module.
6 Reserved
7 Reserved
8 XM-8 module
The 8 inputs and 8 relay outputs extension module, controller allow this
module for operation as elevator control interface (floors 1-8).
9 XM-8 module
The 8 inputs and 8 relay outputs extension module, controller allow this
module for operation as elevator control interface (floors 9-16).
10 Reserved
11 Reserved
12 Reserved
13 Reserved
14 Reserved
15 Reserved
Note: If controller is configured for operation with remote Wiegand type reader instead of PRT terminal no other terminals or extension
modules can be connected to Clock and Data lines simultaneously.

PR402EN.doc
4
Input Lines
Controller offer four input lines: IN1, IN2, IN3 and IN4. Each input can be programmed as NO or NC type. The function of each input line can
be assigned during controllers setup. The following input functions are available:
Function Description
Input ignored Selecting this function will disable decoding of this input, function can be used for temporary input
deactivation without disconnecting it from triggering source.
Door Contact
Input is dedicated for contact which will indicate that door is open. Input activation generate [Door
opened] event, input deactivation generate [Door closed] event.
Exit Button
Input is dedicated for operation with button which will be used to open the door without use of any
identifier. Activation of this input will activate door lock for the same time period as after standard
[Access granted] event, function is usually used for Request To Exit (REX) button connection.
Activation/deactivation of input generate [Exit button ON]/[ Exit button OFF event].
[ON/OFF] Mode Control
Input is dedicated for operation with some button, switch or output line which will control actual
[ON/OFF] mode of controller. Activation of this input force controller to [ON] mode, as long as input
is triggered controller will remain in [ON] mode. Only one input on controller can be configured to
this function. When such a function is selected any other methods of [ON/OFF] mode control will be
forbidden.
AC Lost Input
Input is dedicated to be connected to output line or contact which will indicate that AC supply of
power supply unit is lost. Some brands of power supply are equipped with such a output line (e.g.
PS20N from Roger). After input line is triggered controller generate [AC lost alarm ON] event, when
line returns to normal condition controller generates [AC lost alarm OFF] event.
Low Battery Input
Input is dedicated to be connected to output line or contact which will indicate that reserve battery is
in low condition. Some brands of modern power supply are equipped with such a output line (e.g.
PS20N from Roger). After input line is triggered controller generate [Low battery alarm input ON]
event, when line returns to normal condition controller generates [Low battery alarm input OFF]
event.
Bell Button Input
Input is dedicated to be connected to button which will indicate that somebody want to enter
premises. After input is triggered controller generate [BELL button ON] event and optionally may
activate output line if configured as [BELL Output], when line returns to normal condition controller
generates [BELL button OFF] event and clears [BELL Output] line.
Tamper Loop Input
Input is dedicated to be connected to tamper contact which will indicate that unauthorized person
try to open controller/terminal case. After input is triggered controller generates [Tamper loop ON]
event, when line returns to normal condition controller generates [Tamper loop OFF] event.
Intruder Detector Input
Input is dedicated to be connected to some kind of intruder detector (e.g. PIR) which will indicate
intruder’s attendance in premises. After input is triggered controller generates [Intruder detector
ON] event, when line returns to normal condition controller generates [Intruder detector OFF] event.
The intruder detector input line can by bypassed in [ON] mode, this can be achieved selecting
[Disable Intruder detector when controller in ON mode] option.
[ON/OFF] Mode Reversing Input Input is dedicated to be connected to button (or output) which when changes condition will alternate
[ON/OFF] mode of controller to opposite condition (from [ON] to [OFF] or reversely). Each time this
type of input is triggered controller changes [ON/OFF] mode.
Access Disabling Input
Input is dedicated to be connected to switch (or output) which when activated will disable access to
controlled door, activation/deactivation of this input generate [Access disabled input ON]/ [Access
disabled input OFF] event.
Stable T&A Mode Setting Input
Input is dedicated to be connected to some kind of button which when pressed will change the
actual T&A Mode of controller. Each time input is triggered controller move to next predefined T&A
Mode. After new T&A Mode is set controller remains in selected T&A Mode till next time button is
pressed or till [T&A Mode Schedule] will change actual T&A Mode.
Momentary T&A Mode Setting
Input
Input is dedicated to be connected to button which when pressed will change the T&A Mode of
controller. Every time input is triggered controller move to next predefined T&A Mode and then
waits for identifier, as soon as identifier (Card/PIN) is entered controller returns to its previous T&A
Mode, when no identifier is read during 8 seconds period controller returns to its previous T&A
Mode automatically.
Selects Predefined T&A Mode –
Stable Type Selection Input is dedicated to be connected to button which when pressed will turn controller to specified
T&A Mode. The T&A Mode which will be set after input is triggered is declared by installer for every
input line individually. The new T&A Mode is set for undefined time (until next command which will
change T&A Mode of controller).
Selects Predefined T&A Mode –
Momentary Type Selection Input is dedicated to be connected to button which when pressed will turn controller to specified
T&A Mode. The T&A mode which will be set after input is triggered is declared by installer for each
input line individually. The new T&A Mode is active till nearest user identification, if during next 8
seconds no identification was performed controller return to previously selected T&A Mode.
APB Reset Input
Input is dedicated to be connected to button which when pressed will reset APB Register of
controller. Any time input is activated an internal APB Register of controller is initialized (cleared)
and [APB reset] event is generated.
Clears all outputs on XM-8
elevator control module Input is dedicated to be connected to output line (contact) which when triggered will clear all outputs
on XM-8 elevator control module(s).
Sets all outputs on XM-8
elevator control module Input is dedicated to be connected to output line (contact) which when triggered will set all outputs
on XM-8 elevator control module(s).

PR402EN.doc
5
Besides those listed above functions input lines can be configured to customer defined input functions. Using PC software installer may
define new input line functions, definition of input line function consist from function name and function code. Function name can be used to
distinguish purpose of input e.g. [Guard Tour Button], [Alarm Button], [Assistance Request Button], each time input is activated system will
register events which consist from function name and ON or OFF status which specify if the input line was activated or deactivated.
Output lines
Controller offer two transistor outputs (IO1 and IO2) and two relay outputs (REL1 and REL2). The REL1 relay output is dedicated to control
door lock, the functions of REL2, IO1 and IO2 can be assigned during controller’s setup. The following functions are available:
Function Description
Alarm Output Output is activated when at least one alarm situation occur. There are three different alarm situation
which can be signalized on this output: [PREALARM], [DOOR ALARM] and [FORCED ENTRY].
Installer may select which alarm output should output line signalize.
General Purpose Output Output is activated through interactive command which can be send from PC.
Activated when controller in
[ON] mode Output is activated when controller turns to [ON] mode and remain active as long as controller
remain in this mode.
Activated on [Access granted]
event Output is activated after controller grant access and remains in active state until door contact
indicate that door became closed or lock activation time period has elapsed.
Activated on [Door open] event Output is activated after controller detects that door became open and remains active as long as
door is being open.
Activated on [Access denied]
event Output is activated for period abut 2 seconds after controller denies access.
Activated by schedule Output is activated/deactivated according to selected schedule, no other method may change
condition of output line.
Activated by schedule or PC
command Output is activated/deactivated according to selected schedule or interactive command from PC,
both control methods have the same priority.
Activated when identification on
terminal ID=1 Each time a successful identification is made on ENTRY terminal (ID=1) output go to active
condition and remains in this state till successful identification on EXIT terminal (ID=0) is performed.
Usually this option is used when controller operates with TRIPOD type gate where lock must be set
for clockwise or anticlockwise rotation depending on which terminals identification has been
recognized.
BELL Output Output is triggered when controller recognize [BELL Input] activation and remains active as long as
[BELL Input] remains triggered. This output may be also triggered by BELL Button key which is
available on PRT42 and PRT42-BK access terminals.
Alarm Output
In most cases one output line is configured as [Alarm Output] and is dedicated to trigger signaling device when alarm situation on controller
occur. The [Alarm Output] line may signalize the following alarms:
A
LARM
D
ESCRIPTION
P
RIORITY
S
IGNALIZATION METHOD
PREALARM The alarm occurs after three consecutive
attempts of entering an unknown identifier
repeated in a period shorter than 1 minute. Low Single pulse every 2 seconds.
DOOR ALARM The alarm occurs after door remains open in a
period of time defined by “Time for door
closing”. Middle Double pulse every 2 seconds.
FORCED ENTRY The alarm occurs after door opening without
the use of controller. Highest Pulse/Pause 0.8/0.8 sec.
Signalization of the PREALARM, DOOR ALARM and FORCED ENTRY disappears automatically after 3 minutes or can be switched off
earlier by using any valid identifier (Card/PIN) registered in system. Alarm on controller can also be cleared remotely from PC. When the
[ALARM Output] has been programmed to signalize more than one alarm condition, only the highest priority alarm is signalized.
Relay output (REL1)
The REL1 relay output is dedicated to control door lock. Each time controller grants access this output is activated for predefined period
declared in Lock activation time. Lock activation time can be set from 1 to 99 seconds or minutes or for undefined period, in last case
installer must select Bistable mode option. When Bistable mode is selected each time access is granted REL1 output turn to reverse
condition (from ON to OFF or inversely). When Auto-relock option is set, door lock is deactivated as soon as door contact connected to
controller will indicate that door became open. Lock activation can be temporary disabled when controller stay in [OFF] mode, this can be
achieved by option Access disabled in [OFF] mode. This feature is usually used when some of controller output line is dedicated to
Arm/Disarm alarm zone or intruder detector(s). In this case switching controller to [OFF] mode will arm alarm system (or alarm zone) and
thus will automatically disable access to controlled area for all users regardless of actual access settings.

PR402EN.doc
6
Users
Controller distinguish the following four types of users:
U
SER
T
YPE
ID
N
UMBER
A
UTHORIZATION
INSTALLER NONE Authorization for entry to the installer programming mode, it does not have an identification number.
MASTER 0 Authorization for entry to the user programming mode, opening the door and switching the reader
between the ON and OFF mode, he has identification number is 000.
SWITCHER
Full 001..049 Users with ID = 001..049 have authorization for door opening and switching controller between the
ON an OFF mode.
SWITCHER Limited 050..099 Users with ID = 050..099 have authorization for switching controller between the ON and OFF mode
only, have no authorization for door opening.
NORMAL 100..3999 Authorization only for door opening, users of this type have ID numbers from 100 to 3900. Optionally
users with ID 1000-3900 can be individually set as SWITCHER type on particular controller(s).
Note: Installer may define some users from ID=1000 to ID=3999 as Local SWITCHER type, such a setting can be done individually on
particular controller(s). As a result some user may be a SWITCHER type on some particular controller but the NORMAL type on other ones.
PR402 identifies users by his/her identifier, each user has his/her own identification number (ID = 0000…3999). Identifier can be a PIN or
Card . In case the Card+PIN mode is active, controller requires use of both forms of identification (PIN and Card) in any sequence (Card
then PIN or reverse sequence). PR402 accepts PINs consisting from 3 up to 6 digits and Cards (proximity transponders). The type of card is
not determined it depend of type of reader connected to controller’s Clock & Data lines. When terminal or reader is operating as User ID
controller interpret data incoming from device as User ID.
Note: The term "identifier" or "Ident." means the operation which consist from Card reading and/or PIN entry (sequence no matter).
Examples:
1. [Identifier] = [PIN][#]+[Card] or
2. [Identifier] = [Card]+[PIN][#] or
3. [Identifier] = [PIN] [#] or
4. [Identifier] = [Card]
5. [Identifier] = [User ID]
Examples [1] and [2] refer to situation when option Card+PIN is active, example [5] refer to situation when reader deliver User ID.
Duress entry.
If the user enters his/her PIN code, which differs from its original form by “one” (plus or minus), controller interprets it as a duress code entry.
When duress entry is recognized the DURESS event is generated and FORCED ENTRY alarm signalization might occur on output line.
Example
The original code is [4569], entering [4568][#] or [4560][#] is treated as a duress entry.
Note: For proper recognition of duress entry, the PIN codes of individual users should differ one from each other at least by a value of +/- [2]
on the last significant digit.
The detection of duress codes can be disabled from managing software.
ON/OFF Mode of Controller
PR402 controller may stay in ON or OFF mode, both modes are signalized on bi-color LED marked ON/OFF. The actual mode (ON or OFF)
may be optionally signalized on dedicated output line (output option: Activated when controller in [ON] mode), when controller is switched
from ON to OFF mode (or in reverse direction) output line will follow this changes. Generally the ON/OFF modes are dedicated for auxiliary
control purposes e.g. light control, copy machine control etc. but in most cases they are used for integration with Intruder Alarm System
(IAS). Connecting controller’s output line which follows ON/OFF mode to adequate input line of Intruder Alarm Panel user may arm or disarm
entire alarm system or particular alarm zone, in this case when controller goes to OFF mode (ON/OFF LED set to red) this will automatically
arm adequate alarm zone and vice verso when controller goes to ON mode (ON/OFF LED set to green) this will automatically disarm
adequate alarm zone. The access to premises/zone can be temporary blocked when controller stay in OFF mode, this can be achieved by
option Access disabled in OFF mode.
An ON/OFF mode of controller can be controlled in few listed below ways:
•manually by SWITCHER or MASTER user,
•by external input line configured as ON/OFF Mode Control Input or ON/OFF Mode Reversing Input,
•automatically by ON/OFF Mode Schedule,
•remotely by interactive command from PC (Set controller to ON (OFF) mode).
Note: When ON/OFF mode is controlled by ON/OFF Mode Control Input all other methods of ON/OFF mode control is forbidden.
Manual method of ON/OFF mode control
Controller can be manually switched between ON and OFF modes by SWITCHER or MASTER type users. The manual switching between
ON and OFF modes can be performed only when adequate time schedule (SWITCHER Schedule) enables this type of operation.
The following ON/OFF mode manual switching procedures are allowed:
Procedure for MASTER or SWITCHER FULL users: enter MASTER or SWITCHER FULL identifier first time (Card and/or PIN depending on
actual valid identification mode), wait till LED SYSTEM starts flashing, when LED SYSTEM is flashing enter the same identifier second time,
controller will change ON/OFF mode. After first use of MASTER or SWITCHER identifier controller may or may not activate door relay, it

PR402EN.doc
7
depends on actual access settings. When option If access denied SWITCHER disabled is active controller will not change ON/OFF mode
when MASTER or SWITCHER user which performed identification has not access authorization at that particular moment.
Procedure for SWITCHER LIMITED users: enter SWITCHER LIMITED identifier once (Card and/or PIN depending on actual valid
identification mode) controller will change ON/OFF mode immediately, door lock will not be activated.
Anti-passback (APB)
When anti-passback function is activated users are obliged to perform identification alternatively on ENTRY and EXIT access points. The
anti-passback can be used in two variants:
•APB Hard (anti-passback hard)
•APB Soft (anti-passback soft)
When APB Hard is selected, the attempt to use the same identifier two consecutive times on the same ENTRY or EXIT point will be
rejected, access will be denied and Anti-passback violation event will occur, when APB Soft is selected an attempt to use the same
identifier on the same ENTRY/EXIT point will be accepted but Anti-passback violation event will be generated. The activity of anti-
passback can be reset (initialized) periodically according to APB Reset Schedule or manually triggering APB Reset Input line. After APB
Reset the first use of each identifier can be performed on ENTRY or EXIT terminal, but after this first identification user must use its identifier
alternatively on ENTRY and EXIT terminal.
Identification Modes
Controller enables identification of users in two different modes:
Identification
Mode Description
Card/PIN Controller require Card or PIN to be entered for successful identification.
Card+PIN Controller require Card and PIN to be entered for successful identification, no matter what sequence Card then PIN
or PIN then Card.
Installer may define Default Identification Mode of controller which specify identification method which will be required for each type of
users (Master, Switcher and Normal), Default Identification Mode is set separately for each type of users. In some periods of day or week
controller can be switched to Card+PIN mode according to Card+PIN Schedule. This schedule specify time periods when all types of users
must use its Card and PIN. There are two predefined schedules which can be set for Card+PIN Schedule: Always and Never. When Always
schedule is selected controller will always require Card and PIN (for all type of users), when Never schedule is selected, controller will
always stay in Default Identification Mode.
Card+Card Mode
When this mode is active controller requires two users two perform successful identification then access might be granted. This mode can be
controlled by Card+Card Schedule, selecting schedule Never will permanently disable this mode where schedule Always will permanently
activate it. When together with this Card+Card option the Card+PIN mode is active both users must read his/her Cards and enter his/her
PINs otherwise identification will not be successful.
High Security Mode
When this mode is active users must perform two steps identification procedure, a standard identification (Card/PIN or Card+PIN depending
on actual valid identification mode) plus an additional identification on High Security reader. The High Security reader can be connected to
the same Clock & Data lines which are used for communication with ENTRY/EXIT access terminal and/or extension modules. Controller
accept few types of High Security readers including Wiegand Card/PIN and WIegand User ID. The Wiegand Card/PIN sends the code of
entered PIN or Card, the Wiegand User ID sends ID number of user which has made identification. The High Security option can be
activated separately for each side of the door and can be controlled by time schedule. Generally, the High Security option is dedicated for
those doors which have to be protected with advanced identification method (e.g. biometric identification) .
Door Modes
Door Mode determines how the controller will energize and de-energize electric lock. Door can be set to few listed below modes of
operation:
Door Mode Description
Normal Door lock is activated after each successful identification.
Unlocked Door lock is continuously energized, door can be opened by unauthorized person.
Conditional Unlocked Initially door lock is not energized, but when first authorized person come and use its identifier lock became
energized and remain in this state until new door mode is set.
Locked Activation of door lock is permanently forbidden, no matter if some user has authorization for access or not,
every attempt to open the lock will be rejected.
As a default door stay in Normal Mode but it can be switch to another mode by Door Mode Schedule or by remote command from PC
software.
Operation with XM-8 module
The PR402 may operate with one or two remote XM-8 I/O modules connected to controller via Clock and Data lines. PR402 enable
operation with XM-8 as elevator control interface. The first XM-8 module (address ID=8) is dedicated to control access to floor 1-8, the
second one (address ID=9) controls access to floors 9-16. Each time a successful identification is made controller determine to which floors
has access particular user then activate some of XM-8’s relays, relays remain active until input line assigned to option Clears all outputs on
XM-8 elevator control module(s) is triggered or until next identification is accomplished and new set of outputs is activated. The operation
with XM-8 module(s) is activated through option: Enable XM-8 elevator control module(s). All outputs of XM-8 can be alternatively
activated by input line programmed to option: Sets all outputs on XM-8 elevator control module(s).

PR402EN.doc
8
Operation with XM-2 module
Controller may operate with one external XM-2 I/O module (address=5) connected to controller via Clock and Data lines. The XM-2 offers
two relay outputs (REL1 and REL2) and two NO/NC inputs (IN1 and IN2). The REL1 output on XM-2 is activated/deactivated simultaneously
with REL1 output of controller, the second XM-2’s output (REL2) is activated/deactivated simultaneously with controller’s IO2 output. The
XM-2’s inputs are normally ignored but when allowed during controller’s setup they can be used instead of IN1/IN2 inputs located on
controller board. Installer may select which input(s) (local or remote) should be interpreted by controller. Generally XM-2 module is dedicated
for PR302/PR302LCD controllers which normally activate door lock through internal relay, this relay can be easy accessed by non
authorized person. When XM-2 is used, door lock may be activated not by internal controller’s relay but by remote relay output located in
secure location, this increase overall controller’s security level significantly. The operation with XM-2 module is activated through option:
Enable XM-2 remote I/O expander module. The are two additional XM-2 options:
•Ignore IN1 on controller, enable IN1 on XM-2 – controller will use remote (on XM-2) IN1 input instead of local (on controller) IN1,
remote IN1 input will have the same function as assigned previously for local IN1 input, the electrical signals on controller’s IN1
line will be ignored.
•Ignore IN2 on controller, enable IN2 on XM-2 – controller will use remote (on XM-2) IN2 input instead of local (on controller) IN2,
remote IN2 input will have the same function as assigned previously for local IN2 input, the electrical signals on controller’s IN2
line will be ignored.
Operation with PSAM-1 module
Controller may operate with one PSAM-1 power supply alarm module (address ID=4) connected to controller through Clock and Data lines.
The PSAM-1 is an optional part of power supplys offered by Roger, it delivers following data:
•actual DC output level
•low battery alert
•battery failure alert
Note: PSAM-1 may operate in autonomic or networked mode, when connected to controller’s Clock and Data lines it should be configured to
networked mode with address ID=4.
The operation with PSAM-1 module is activated through option: Enable PSAM-1 power supply alarm module.
Operation with Wiegand readers
Controller may operate with one Wiegand interface reader connected to Clock and Data lines instead of standard PRT terminal(s). Controller
accept 26, 34, 42 and 66 bit Wiegand transmissions. The transmission of Wiegand reader can be interpret by controller as PIN, Card or
User ID number. When controller is configured for operation with Wiegand User ID reader it interprets transmitted digits as ID number of
user which has performed identification, when is set to Wiegand PIN reader controller interprets transmitted digits as PIN number, when is
set to Wiegand Card reader controller interprets transmitted digits as Card number. The Wiegand User ID mode is generally dedicated for
biometric type readers which does not transmits PINs nor Cards codes but deliver ID number of user which has made successful
identification. When controller is configured to Wiegand type reader no other extensions modules (XM-2, XM-8 or PSAM1) nor standard PRT
reader can be connected simultaneously to controller’s Clock and Data lines. By default Wiegand reader connected to Clock and Data lines
is treated by controller as an ENTRY terminal.
T&A Registration
The PR402 offers T&A registration which further can be used for calculation of total job hours. Each [Access granted] event which occur on
controller have a T&A Mark (T&A status) which specifies what kind of entry/exit has been registered. The actual type of registration for T&A
purposes is determined by controller’s T&A Mode. PR402 offers few predefined T&A Modes (Entry, Exit, On Duty Exit or Ignored for T&A)
as well as customer defined. Each T&A Mode has its individual ID number from 0 to 255, numbers between 0 and 50 are reserved for
predefined T&A Modes which can not be modified or changed. When controller stay in Ignored for T&A mode it means that events which
will occur during this mode will not play any rule in T&A reports or calculations. The customer defined modes can be useful when new types
of entry/exit are requested for detailed statistics of users attendance. In RACS system each access point (controller/terminal) may have its
own Default T&A Mode. The T&A Mode of terminal ID=0 can not by dynamically changed during system activity except situation when
option [Terminals ID=0 and ID=1 have the same T&A Mode] is set, the T&A Mode of controller(s) can be dynamically changed in few
manners which are listed below:
•by adequate Time Schedule (T&A Mode Schedule),
•by activation of input line.
If option [Terminals ID=0 and ID=1 have the same T&A Mode] is active events registered on terminal ID=0 have the same T&A status a as
events registered on terminal ID=1 (no matter if event was registered on terminal ID=1 or ID=0 they have assigned the same T&A status
which is actually assigned for terminal ID=1). Generally, this option is dedicated to situation when controller is integrated into system which
utilize another card standard (e.g. Mifare), in such a configuration T&A Mode might be changed on controller (using input line or time
schedule) but identification will be performed on remote Wiegand interface reader connected to Clock and Data lines.
Setting T&A Mode from input
Installer may define one or more input line to be used for setting required T&A Mode of controller. The input line can be used to set specified
T&A Mode or to switch controller between different T&A modes. The input line which dynamically change T&A Mode is very useful especially
when an external button(s) is required to select specified T&A Mode. There are following input function which enable setting of T&A mode
from external button:
Stable T&A Mode setting input
When this type of input line is triggered controller move to next predefined T&A Mode and remain in this mode until next command comes
and change it again.
Momentary T&A Mode setting input
When this type of input line is triggered controller move to next predefined T&A Mode and remain in this mode until next Card/PIN is entered,
after this controller returns to previous T&A Mode. When no Car/PIN is entered during 8 seconds period controller will restore previous T&A
Mode automatically.

PR402EN.doc
9
Predefined T&A Mode setting input
When this type of input line is triggered controller move to dedicated T&A Mode and remain in that mode until next command comes and
change it again. Each input line can be used for setting individual T&A Mode. For example IN1 can be used to set “Exit”, IN2 can be used to
set “Entry” and IN3 to set “On Duty Exit”.
T&A Mode controlled by schedule
The T&A Mode Schedule enables automatic change of controller T&A Mode according to defined time schedule details. The T&A Mode
Schedule specifies what T&A Mode will be set on controller in particular moments of day, week or holydays.
Note: All listed previously methods of T&A Mode control may be used simultaneously.
Holidays
Holidays definition specify some days during year period in which controller behavior is different as usual. Installer can define some special
rules for holidays, PR Master software enables four types of holidays settings to be defined, H1, H2, H3 and H4. The holiday definition
consist from:
-name of holiday day, (e.g. Easter)
-date of holiday, (e.g. 12 of April)
-detail settings of holiday (e.g. H1)
Signalization
Optical signalization
Controller perform two methods of optical signalization, first on internal SMD LEDs located on printed circuit board and second on LEDs
located on remote PRT terminals. The table below describes optical signalization.
LED F
UNCTION
N
OTES
CHARGE When set on it signalize that reserve batter is under
charging phase, when off it signalize that battery is fully
charged.
ON Signalize ON mode of controller.
OFF Signalize OFF mode of controller. The PRT terminal offer one bi-color LEDs marked
as ON/OFF, when this LED is set to RED it
signalize OFF mode, when is set to green it
signalize ON mode.
OPEN Signalize that door lock is energized. The LED OPEN on terminal signalize that door
lock is energized.
SYSTEM When blinks it signalize that controller stands by for next
part of command. This LED is momentary activated
each time the Card/PIN is entered.
The LED SYSTEM located on PRT terminal is
momentary activated each time the Card or PIN is
entered.
ERROR Memory contents corrupted, controller should be
reprogrammed. Non available on terminal.
LED SYSTEM is blinking when controller waits for next card or PIN entry, such a situation occurs when controller recognized SWITCHER
Full or MASTER identifier. If during period when LED SYSTEM is blinking a SWITCHER or MASTER Card/PIN is used again controller will
move from ON to OFF mode or in reverse direction.
Installation
Locate the controller in a dry area, all electrical connections must be made with power supply off. Once wiring is complete, power up the
control panel. The controller should be mounted using four mounting screws. Originally the new controller is delivered with preprogrammed
MASTER Card (included in carton box), preprogrammed MASTER PIN code (1234) and ID address set to “00“.
!When controller and external terminals are supplied from separate power sources, both minuses (terminal’s and controller’s) must
be connected together.
!Roger recommend to ground power supply minus.
!PR402 can not be mounted in external location, it hasn’t any protection against moisture, rain or cold, only indoor location are
acceptable.
Note: You must complete all wiring before applying AC supply to controller.
Connection Terminals Descriptions
Battery Connection: RED and BLACK wires
A 12V 7Ah rechargeable battery is used as a backup source of power in the event of an AC power failure. The battery also provides
additional current when the equipment connected to panel demands exceed the power output of the transformer, such as when door strike
energizing or activating signaling device (e.g. alarm siren). Electronic circuit monitors reserve battery voltage level, when it falls below ~12V
the Low Battery alarm is signalized, when it falls below ~11.5V the Battery Failure alarm is signalized, when battery level drop below ∼10V
electronic circuit automatically disconnect battery, entire system goes down. Automatic disconnection of battery protects it from deep
discharge and access system from operation below minimum acceptable supply voltage. CPR charges battery with stable current, this
method guarantee relatively quick and safe battery charging process. The supply output voltage is factory set to 13.8V but it can vary from
11.0 to 13.8V, this depends on actual battery charging phase. When output level is above 13.5V it means that battery is nearly charged,
when levels drop below 12.0V it indicates that battery is on beginning phase of charging.
Note: Do not connect the battery until all other wiring is complete. Connect the battery before connecting AC.
Connect the RED battery lead to the positive battery terminal; connect the black lead to negative.

PR402EN.doc
10
AC input, terminals: AC
The panel requires 18-22V 30VA transformer. Connect the primary side of transformer to unswitched AC source and secondary side to AC
terminals.
Note: Do not connect transformer until all other wiring is complete.
Auxiliary Power Output, terminals: +AUX-
These terminals provide up to 1A of additional current at 12V DC for devices requiring power. Connect the positive side of any device
requiring power to AUX+ terminal, the negative side to AUX- (GND-ground). The AUX output is protected, when too much current is drawn
from these terminals AUX output will be temporarily shut off until the problem is corrected.
DC output, terminals: +TML-
These terminals provide up to 200mA of additional current at 12V DC for devices requiring power. Connect the positive side of any device
requiring power to TMS+ terminal, the negative side to TMS-- (GND-ground). The TMS output is protected, when too much current is drawn
from these terminals TMS output will be temporarily shut off until the problem is corrected. The TMS output is dedicated to supply remote
access terminals and/or extension modules connected to Clock & Data lines.
Input lines, terminals: IN1, IN2, IN3 and IN4
Each controller input (IN1, IN2, IN3 and IN4) have the identical electrical structure. All inputs are NO/NC type with 5,6 kΩresistor pulled up
to supply plus. During setup process installer may configure each input independent as NO or NC. The NO type input is triggered when
connecting it to supply minus. The NC input is normally shorted with supply minus, when disconnecting it from supply minus it became
triggered. Controller ignore triggering impulses if they are shorter then 200 ms and accept signals that are longer then 500 ms. Detection of
signals between 200 and 500 ms is not guaranteed. Each controller input can be programmed to different function and may be under control
of time schedule.
RS485 communication interface, terminals: A, B and SHLD
The RS485 interface consist from two signal lines (A and B) and optional cable shield terminal (SHLD). Installer may use arbitrary
communication bus topology (star, three or any combination of both), no terminating resistors are required. In most cases communication
runs satisfactory on almost each types of cables (twisted/untwisted, shielded/unshielded) but it is not guaranteed in each case. Generally
unshielded, twisted type cables are preferred and guarantee best performance of communication. Each communication line (A and B) is
protected from voltage surges and from supply minus and plus. RS485 standard of transmission guarantee up to 1200 meters
communication distance with high immunity against interferences. When longer communication distances are required the UT-3 or UT-4
interfaces might be used. The one pair of UT-3 interfaces extend communication distance by 1200m, the UT-4 enables communication
trough computer network (LAN or WAN) witch utilize TCP/IP protocol.
Clock & Data interface, terminals: CLK and DTA
Each reader or module connected to Clock & Data lines must have its individual ID address which can be set on programming jumpers.
There are no restrictions for types of cables used for Clock & Data lines except that the maximum cable length may not exceed 150 meters
(500Ft.). The terminals or modules connected to Clock & Data lines should be supplied from the same supply source as controller, if not
supply minus of controller should be shorted with supply minus of other equipment which is connected to Clock & Data lines.
Tamper contact, terminals: TAMPER
Controller is equipped with switch which is dedicated to detect attempt to open controller case. Normally tamper contacts are closed, they
became open when device is open. Tamper contacts are rating for 50 mA only, they can be connected in series with tamper contacts of
another controller(s) and supervised together by CPR Tamper Input line or they can be connected to controller’s input which is configured as
TAMPER Input. When TAMPER contact are connected to controller input a [Tamper On] or [Tamper Off] event is registered and transmitted
to monitoring computer when TAMPER contacts are open/close.
IO1 and IO2 output lines, terminals: IO1 and IO2
Both lines are open drain N-MOS transistor outputs. Each output can sink up to 1A DC current for unlimited time. In normal (not triggered)
condition both outputs remain in high impedance state, when triggered they move to low resistance state which results that supply minus is
observed on output. Both inputs are electronically protected from excessive currents and over-voltage. Each transistor output can be
programmed to different function and can be controlled by individual time schedule.
REL1 Relay output, terminals: NO1, NC1 and COM1
The relay output is dedicated to control electric door lock, it offers normally open and normally closed contacts rating for 1.5A/24V DC or AC.
Both pair of relay contact are protected with over-voltage elements (MOV) which reduce sparks during switching inductive loads such
electronic locks and thus extends relay contacts life significantly.
Note: Using relay contact to switch voltages above 30V may damage relay protection elements (MOV) which can result in unintended
connections between relay contacts.
A relay output can be set to momentary or Bi-stable mode. When output is setup for momentary mode it becomes activated for limited period
(from 1 second to 255 minutes) and after it returns to its normal condition. When output is set to Bi-stable mode relay output changes its
state to opposite each time the triggering occurs.
REL2 Relay output, terminals: NO2, NC2 and COM2
This relay output can be assigned to different function, it offers normally open and normally closed contacts rating for 1.5A/24V DC or AC.
Both pair of relay contact are protected with over-voltage elements (MOV) which reduce sparks during switching inductive loads such
electronic locks and thus extends relay contacts life significantly.
Note: Using relay contact to switch voltages above 30V may damage relay protection elements (MOV) which can result in unintended
connections between relay contacts.

PR402EN.doc
11
Memory Reset Procedure
The MEMORY RESET procedure clears all existing data in memory and restores default settings. During MEMORY RESET procedure
operator must program new MASTER identifier (PIN and/or Card) and new ID number of controller. The MEMORY RESET procedure can be
carried out on Terminal ID=1 and requires following steps to be done:
!open controller case,
!press MEMORY RESET button until LED OPEN starts blink (approx. 6..8 seconds) then release MEMORY RESET button,
!enter new Master PIN code (up to 6 digits) then press [#],
!read new Master card,
!enter new ID number (two digits from 00 to 99 range) then press [#], controller will save new setting and return to normal mode.
Note: After Memory Reset the newly programmed PIN and Card became MASTER type identifiers.
Firmware upgrade
During manufacturing process controller microprocessor is programmed with most actual firmware version but it can be upgraded later with
new ones. Roger team constantly working on functionality enhancements so new firmware versions are released quite often (every new
firmware version is published on www.roger.pl). Our customers are advised to register at web site so Roger will let inform when new
versions are ready for download. The new firmware can be downloaded without controller removal from live installation. The detailed
description of firmware upgrade procedure can be found in Firmware upgrade manual on www.roger.pl
Ordering information
PR402 PR402 electronic module with metal case and 30VA transformer.
PR402-MOD PR402 electronic module (without casings).
Technical Specification
Power supply 220..230V AC
Power consumption: 30W
Supply Output (nominal) 13.8 V dc
Battery Charging Current ∼300 mA
Battery Cut Off Level ∼10.0 V
Operating temp. range 0...+55º C.
Cable distance between CPR and
controller or PC computer Max. 1200 meters (4000 ft)
Operating humidity 10 to 95% (non condensing)
Dimensions (mm): 280 x 290 x 80
Weight (grams): ~3.5 kG
Connection terminals assignment
AC AC supply input, 30VA 18-22VAC transformer
+ AUX - Supply output 12V/1A
NO1 REL1 output, normally open contact
COM1 REL1 output, common contact
NC1 REL1 output, normally closed contact
REL1 relay output, 1.5A/24V DC or
AC
NO2 REL2 output, normally open contact
COM2 REL2 output, common contact
NC2 REL2 output, normally closed contact
REL2 relay output, 1.5A/24V DC or
AC
IO1 Transistor output, 1A/16V DC max.
IO2 Transistor output, 1A/16V DC max.
IN1 IN1 input line
COM IN1 and IN2 common terminal, internally connected with supply minus
IN2 IN2 input line
IN3 IN3 input line
COM IN3 and IN4 common terminal, internally connected with supply minus
IN4 IN4 input line
A RS485 communication bus, terminal “A”
B RS485 communication bus, terminal “B”
SHLD RS485 communication bus, cable shield
CLK Clock & Data interface, Clock line
DATA Clock & Data interface, Data line
+ TML - DC supply output, max. 200mA

AC + AUX - NO1 NC1 COM2 IO1 IN1 IN2 COM SHLD DATARS485 +TS-COM1 NO2 NC2 IO2 COM IN3 IN4 A B CLOCK
Communication Bus
TRANSFORMER
30VA, 18-22VAC
230VAC
Sealed Gel Battery
12 V
Memory
Reset
uP
Reset
S1 S2
Output
Voltage
Regulation
POT2
Battery Charge
Regulation
POT1 POT1
+ACC-
uP
Firmware
Download
Mode
CHARGE
ON
OFF
OPEN
SYSTEM
ERROR
12V
DATA
CLOCK
12V
DATA
1
4
7
*
2
5
8
0
3
6
9
#
CLOCK
TAMPER
12V
DATA
1
4
7
*
2
5
8
0
3
6
9
#
CLOCK
TAMPER
Expander Module
e.g. XM-2 / XM-8
Access Terminal
(PRT series reader address ID=1)
Twisted pair of wires
is recommended.
Shielded cables should be used
only if strong interferences exists.
Tamper Loop
16,5 … 22 VAC
Installation notes:
1. Tamper contacts may be connected to Tamper Input of CPR control panel or to some
controller’s input defined as Tamper Input. When connected to controller input when
Tamper occur this will be registered in events history and will be transmitted to monitoring
computer.
2. Each device connected to controller’s Clock & Data lines must have its individual
address. This demand is not valid for Wiegand type readers.
3. Do not adjust potentiometers located on electronic circuit board.
4. Terminals [+ TS -] are dedicated to supply access terminals. Do not use them for other
purposes.
5. It is recommended to supply Door Lock from separate supply source. When Door Lock is
supplied from controller’s AUX terminals use separate pair of wires for Door Lock supply.
Alarm Signalling
Device
Door Lock
Exit Button
BELL Button
Door Contact
Auxiliary control line
e.g. Alarm System, Light control, Heating control etc.
CHARGE Battery during charge
ON
OFF
OPEN Door Lock energized
SYSTEM When pulsing controller wait for SWITCHER type identifier
ERROR Memory Error
LED ASSIGNMENTS
Controller in ON mode
Controller in OFF mode
Cdr109EN
Typical wiring diagram of PR402
DATA
CLOCK
A/D Conv.
Calibration
Tamper Loop
Access Terminal
(PRT series reader address ID=0)

AC + AUX - NO1 NC1 COM2 IO1 IN1 IN2 COM SHLD DATARS485 +TS-COM1 NO2 NC2 IO2 COM IN3 IN4 A B CLOCK
Communication Bus
TRANSFORMER
30VA, 18-22VAC
230VAC
Sealed Gel Battery
12 V
Memory
Reset
uP
Reset
S1 S2
Output
Voltage
Regulation
POT2
Battery Charge
Regulation
POT1 POT1
+ACC-
uP
Firmware
Download
Mode
CHARGE
ON
OFF
OPEN
SYSTEM
ERROR
12V
DATA
CLOCK
12V
DATA
1
4
7
*
2
5
8
0
3
6
9
#
CLOCK
TAMPER
12V
DATA
1
4
7
*
2
5
8
0
3
6
9
#
CLOCK
TAMPER
Additional Modules
e.g. XM-2/XM-8/PSAM-1
Wiegand ENTRY reader
(Terminal ID=0)
Twisted pair of wires
is recommended.
Shielded cables should be used
only if strong interferences exists.
Tamper Loop
18 … 22 VAC
Installation notes:
1. Tamper contacts may be connected to Tamper Input of CPR control panel or to some
controller’s input defined as Tamper Input. When connected to controller input when
Tamper occur this will be registered in events history and will be transmitted to monitoring
computer.
2. Each device connected to controller’s Clock & Data lines must have its individual
address. This demand is not valid for Wiegand type readers.
3. Do not adjust potentiometers located on electronic circuit board.
4. Terminals [+ TS -] are dedicated to supply access terminals. Do not use them for other
purposes.
5. It is recommended to supply Door Lock from separate supply source. When Door Lock is
supplied from controller’s AUX terminals use separate pair of wires for Door Lock supply.
Alarm Signalling
Device
Door Lock
Exit Button
BELL Button
Door Contact
Auxiliary control line
e.g. Alarm System Arm/Disarm, Light control, Heating control etc.
CHARGE Battery during charge
ON
OFF
OPEN Door Lock energized
SYSTEM When pulsing controller wait for SWITCHER type identifier
ERROR Memory Error
LED ASSIGNMENTS
Controller in ON mode
Controller in OFF mode
Cdr142EN
Typical wiring diagram of PR402 when operating with Wiegand type readers
DATA
CLOCK
A/D Conv.
Calibration
Tamper Loop
Wiegand EXIT reader
(Terminal ID=1)
D1
D1 - General purpose diode (1N4001...1N4007)
Note: When controller operates with two Wiegand
interface readers the IN4 input line is reserved for
communication purpose with mentioned readers
and can not be use for other purposes.

Cdr141EN
PR402: Wiring diagram for INTERLOCK configuration (when door “A” became open access on controller “B” is disabled and vice verso).
AUX
IN1...IN4
IN1...IN4
NC
COM
NO
AUX
IN1..IN4
IN1..IN4
NC
COM
NO
“AUX -” of both controllers must be connected with additional wire
Door contact
(NC type)
Door Lock
Input must be configured as:
“Access Disabling Input” NC type
Controller “A”
NOTES
It is recommended to supply door lock using
separate pair of wires connected to
AUX supply output.
Input line must be configured as:
“Door contact” NC type
DOOR “B”
Door contact
(NC type)
Controller “B”
DOOR “A”
PR402
PR402
Door Lock

cdr139EN
NO1
NO2
COM1
COM2
NC1
NC2
CLK
DTA
REL1 REL2
AUX
PR402 Access Controller
TML
The REL2 relay output apply supply minus to ENTRY or
EXIT Door Lock depending on which reader (entry or
exit) identification was performed.
The REL2 output must be configured as:
“Activated when identification on terminal ID=0”
Using PR402 for separate Entry/Exit door control.
The same method can be implemented for rotary gate control .(TRIPOD)
DOOR LOCK
DOOR LOCK
ENTRY TERMINAL
ADDRESS ID=0
1
3
5
7
9
*
2
4
6
8
0
#
1
3
5
7
9
*
2
4
6
8
0
#
AUX - Door lock supply
REL1 - Activates door lock
REL2 - Selects Entry or Exit door lock
TML - Access terminal supply
CLK/DTA - Communication interface
ENTRYEXIT
EXIT TERMINAL
ADDRESS ID=1

Cdr127EN
Access
Controller
Control Panel
CPR32SE
COM ...
Power Supply
( e.g. PS20N)
12V
12V
12V
12V
Transformer
230VAC
230VAC
230VAC
230VAC
Reserve Battery
12 V
AKUMULATOR
12 V
AKUMULATOR
12 V
AKUMULATOR
12 V
ACC
ACC
ACC
ACC
SECTION “ A”
Power Supply “ A”
Note !
When system is supplied from more then one
supply source, all minuses of all supplies
should be connected together.
Communication Bus - max. 1200m
It is recommended to use twisted, unshielded wires.
Shielded cables should be used only when strong
electric interferences exists.
It is recommended to ground all minuses.
Ground
UT-2
Roger Access Control System
An example of RACS system which incorporate 15 access controllers, CPR control panel and 3 power supplies.
Access
Controller
Access
Controller
Access
Controller
Access
Controller
Access
Controller
Access
Controller
Access
Controller
Access
Controller
Access
Controller
Access
Controller
Access
Controller
Access
Controller
Access
Controller
Access
Controller
Power Supply
( e.g. PS20N) Power Supply “ B”
Power Supply
( e.g. PS20N) Power Supply “ C”
Transformer
Transformer
Transformer
SECTION “ B”
SECTION “ C”SECTION “ CPR”

Cdr126EN
NETWORK C NETWORK DNETWORK B
1. Each access Network requires separate COM port or can be connected via TCP network.
2. The maximum cable length between UT-2 interface and PC COM must not exceed 15m.
3
4. The maximum cable distance between UT-2 interface and any other device connected to communication bus must not exceed 1200m.
5
6. System requires supervising software.
7. PC computer may operate in ON-LINE or OFF-LINE mode.
. The UT-2 interface can be connected to communication bus in any arbitrary selected location.
. The installation of CPR control panel is optional in access Network.
RACS
RACS 4
Roger Access Control System
The structure of RACS v.4
Max. 320 access controllers
Local (LAN) or wide (WAN)
computer network with TCP/IP protocal
RACS Communication Bus
max. 1200m
COM ...
Telephone Line
COM ...
COM ...
UT- 2
MODEM
MODEM
UT- 2
UT- 2
UT- 4
NETWORK A
UT- 4
CPR32
Control
Panel
(optional)
Each Network may have
up to 32 controllers
NETWORK E
Access
Controller
COM ...
UT- 2
Max. 10 access networks
Max. 15m
Access
Controller
Access
Controller
Access
Controller
Access
Controller
Access
Controller
Access
Controller
Access
Controller
Access
Controller
Access
Controller
Access
Controller
Access
Controller
Access
Controller
Access
Controller
Access
Controller
Access
Controller
Access
Controller
Access
Controller
Access
Controller
Access
Controller
Access
Controller
Access
Controller
Access
Controller
CPR32
Control
Panel
(optional)
CPR32
Control
Panel
(optional)
CPR32
Control
Panel
(optional) CPR32
Control
Panel
(optional)
CPR32
Control
Panel
(optional)
NETWORK J .............
Other manuals for PR402
1
Table of contents
Other Roger Controllers manuals
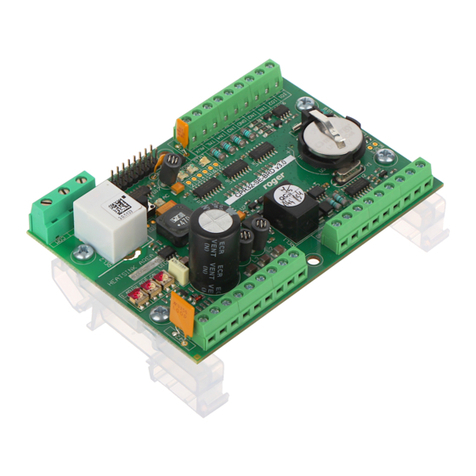
Roger
Roger CPR32-SE v3.0 User manual

Roger
Roger H70/200AC Product manual
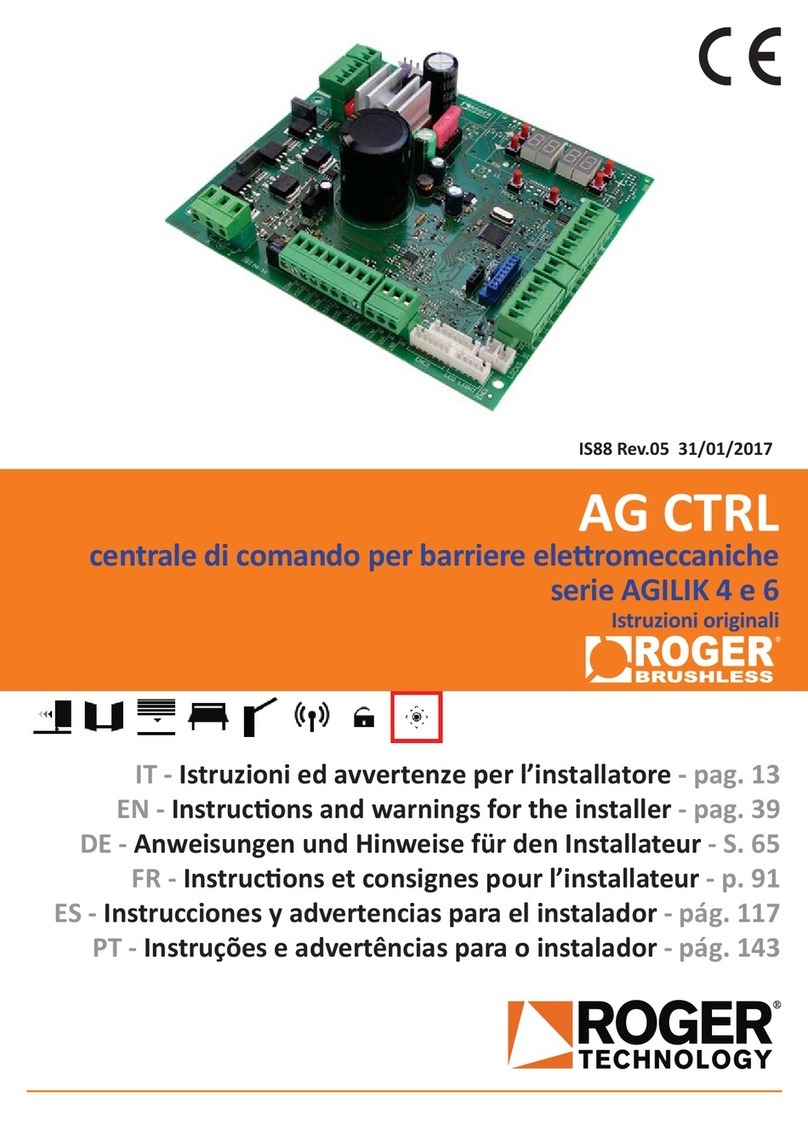
Roger
Roger AG CTRL Product manual

Roger
Roger PR311SE Instruction and safety manual
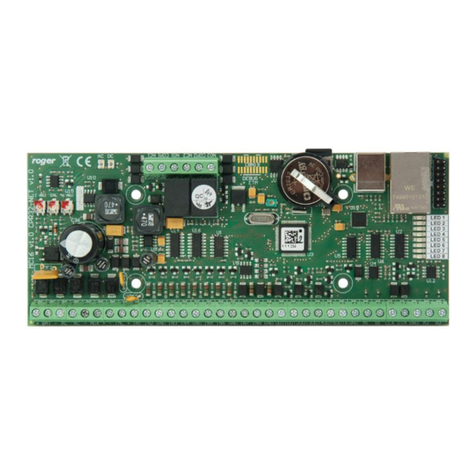
Roger
Roger MC16 User manual
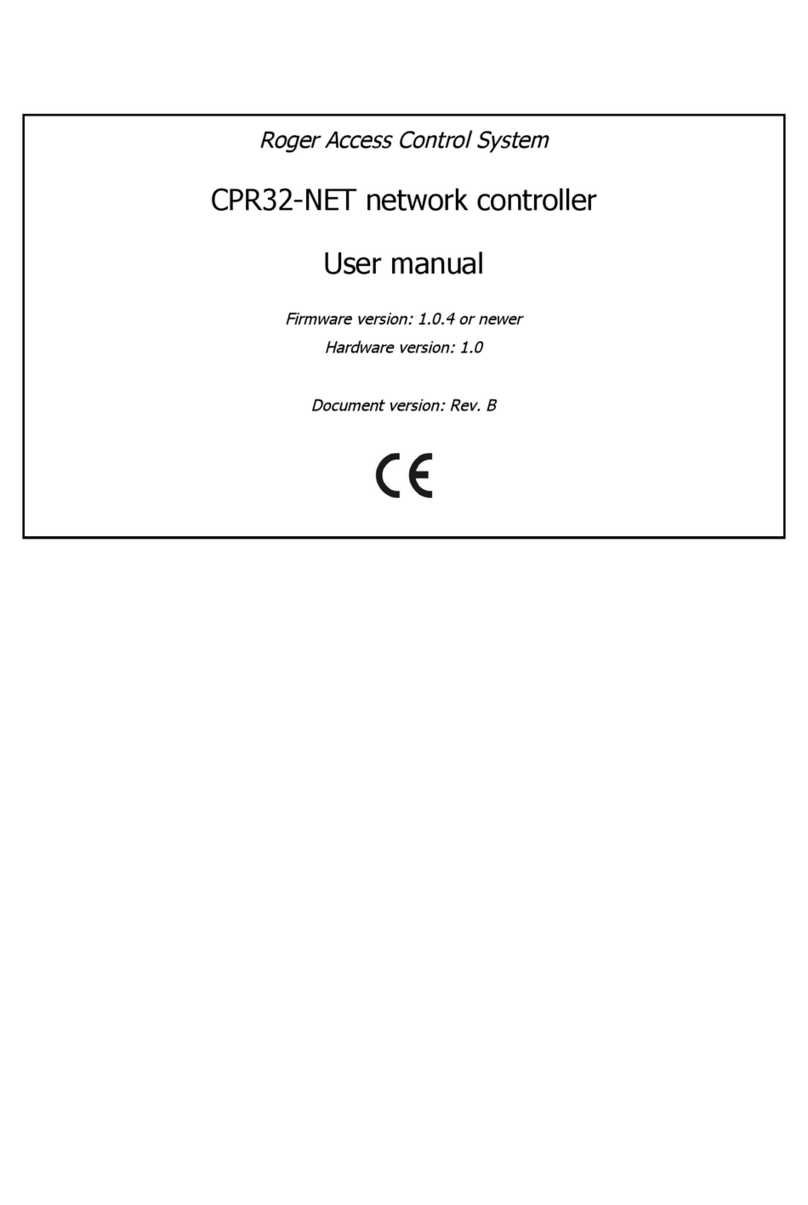
Roger
Roger CPR32-NET User manual
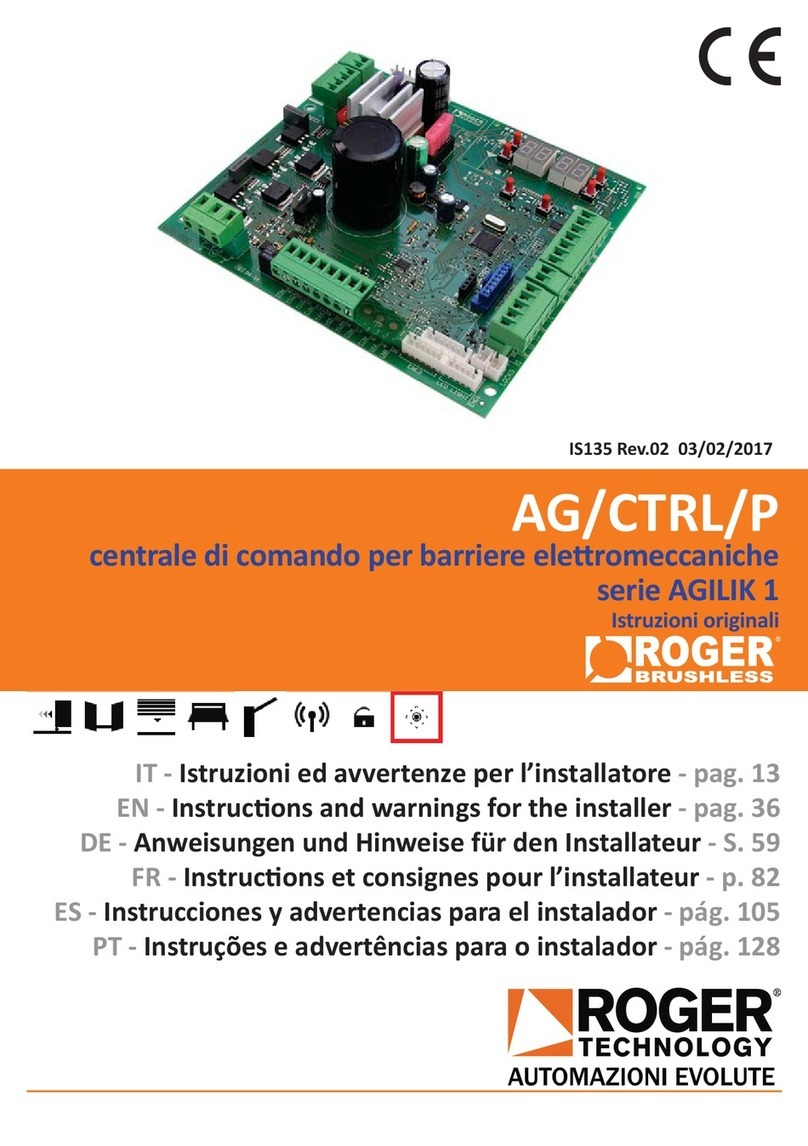
Roger
Roger AG/CTRL/P Product manual
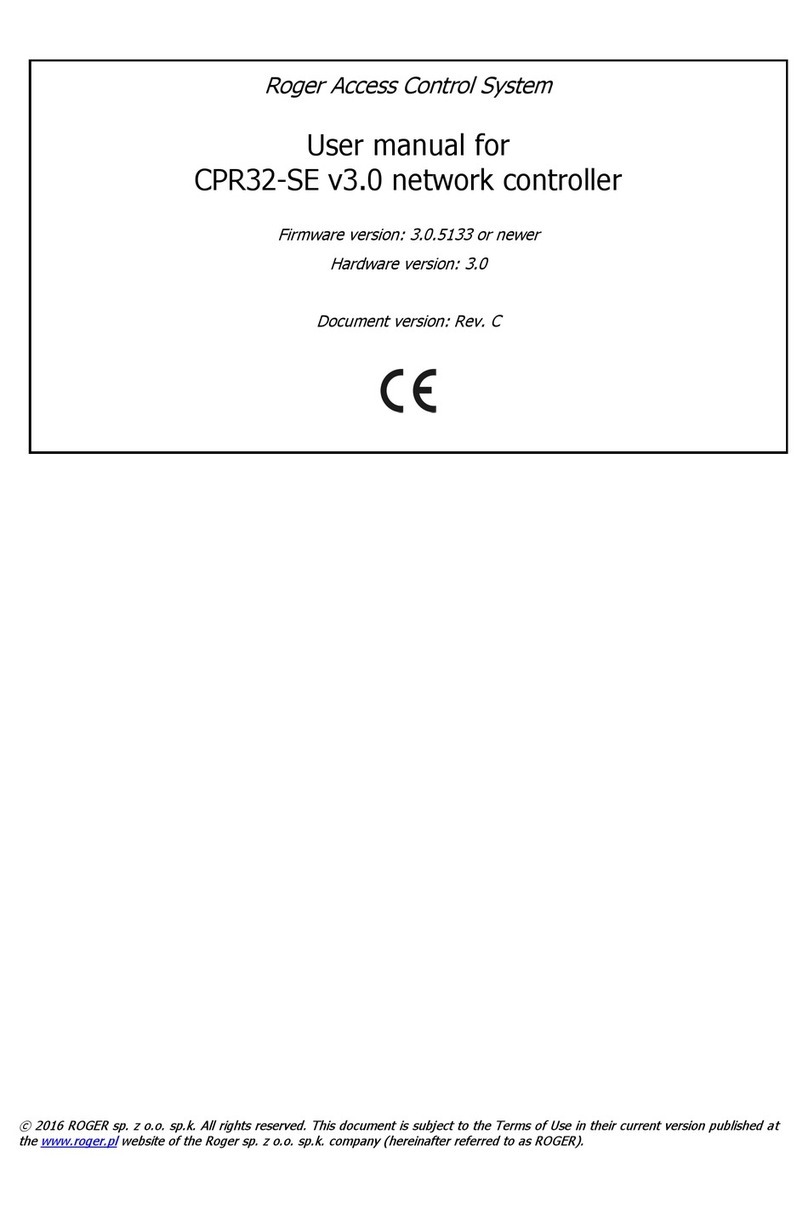
Roger
Roger CPR32-SE User manual
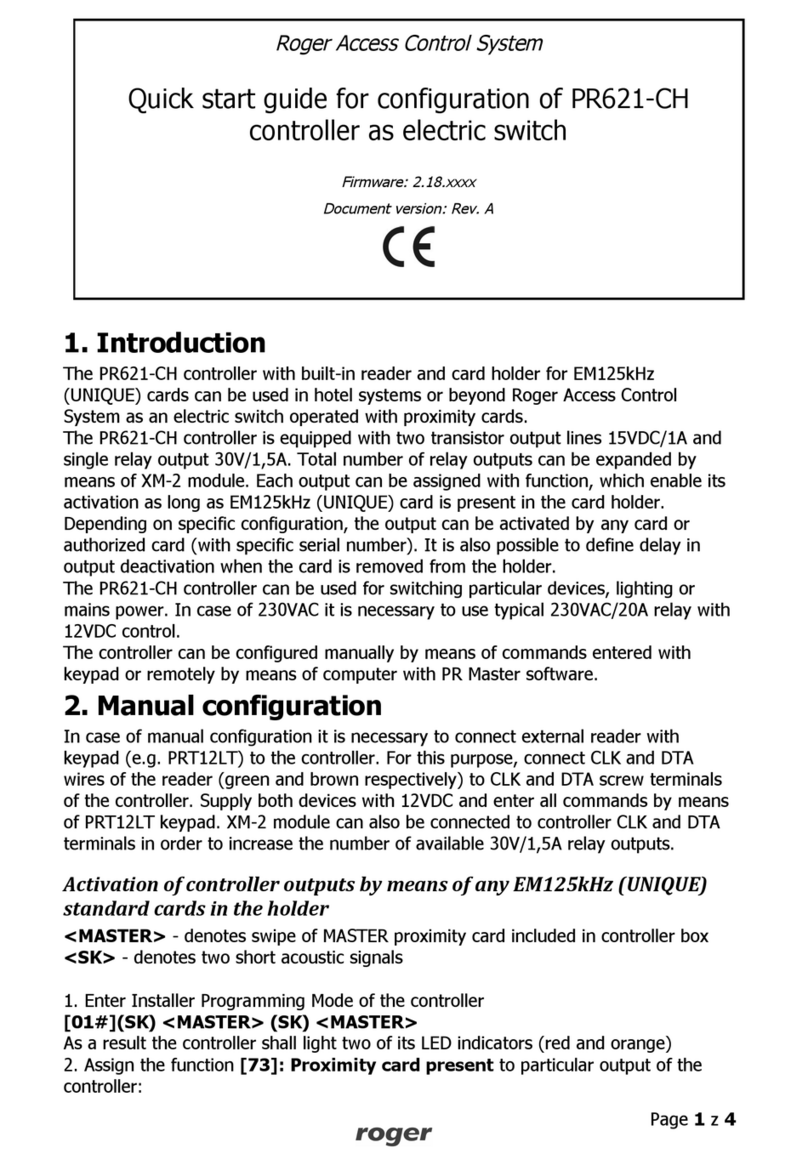
Roger
Roger PR621-CH User manual
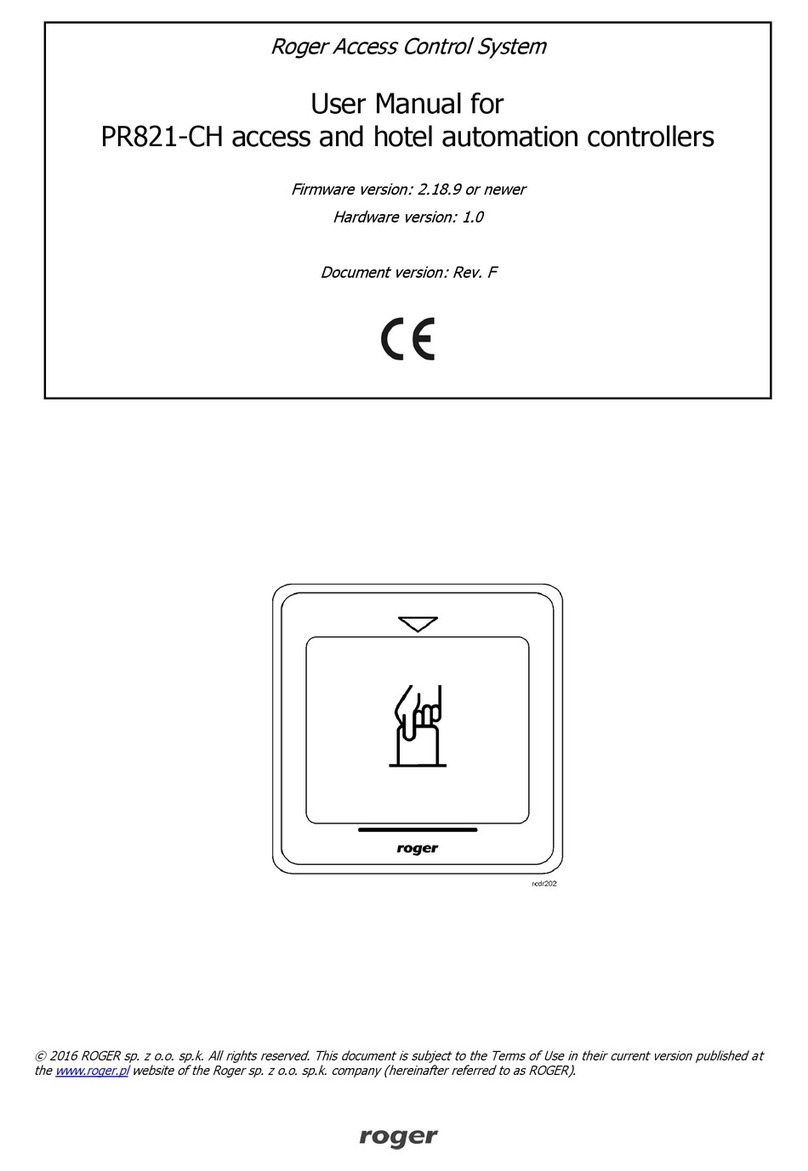
Roger
Roger PR821-CH User manual