Siemens GMI Series User manual



















Other manuals for GMI Series
2
This manual suits for next models
6
Other Siemens Circuit Breaker manuals
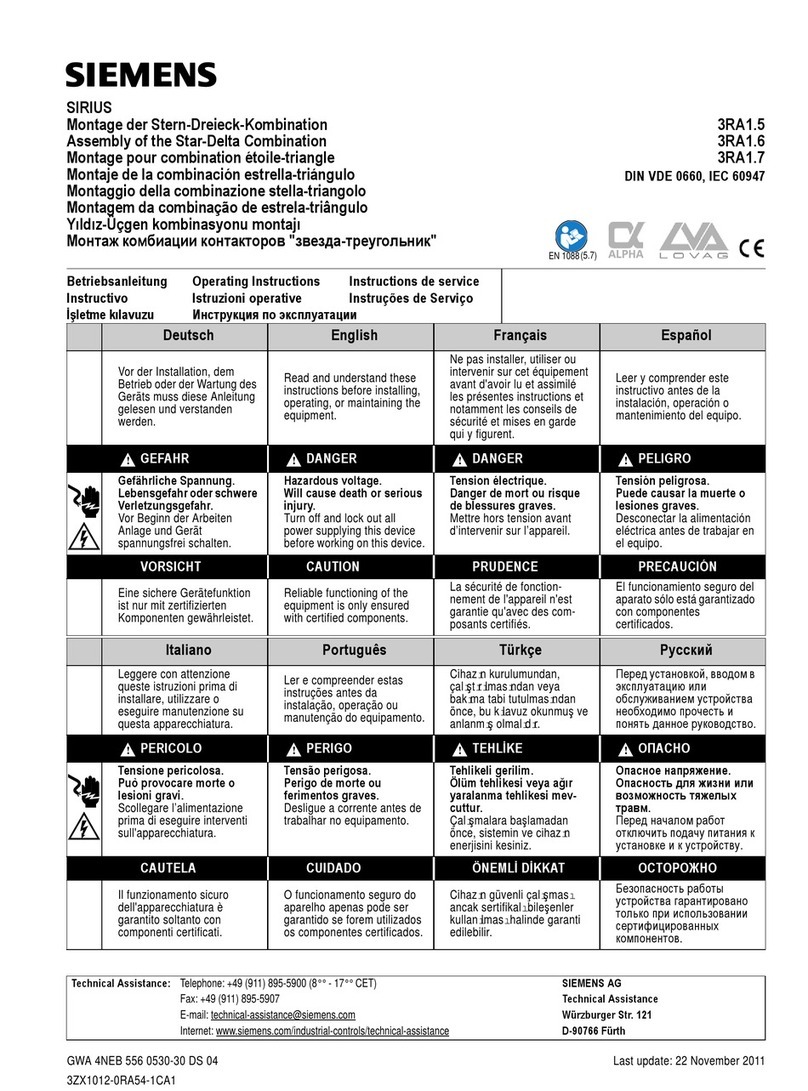
Siemens
Siemens SIRIUS 3RA1.5 User manual
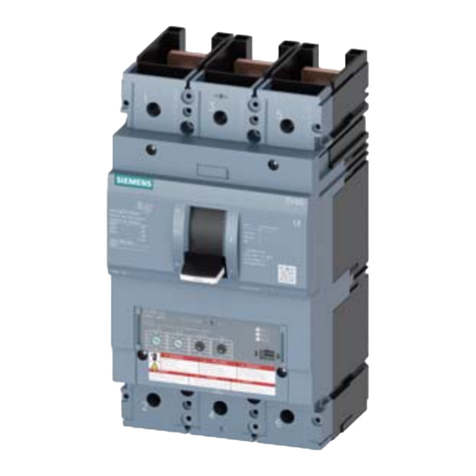
Siemens
Siemens 3 Series User manual
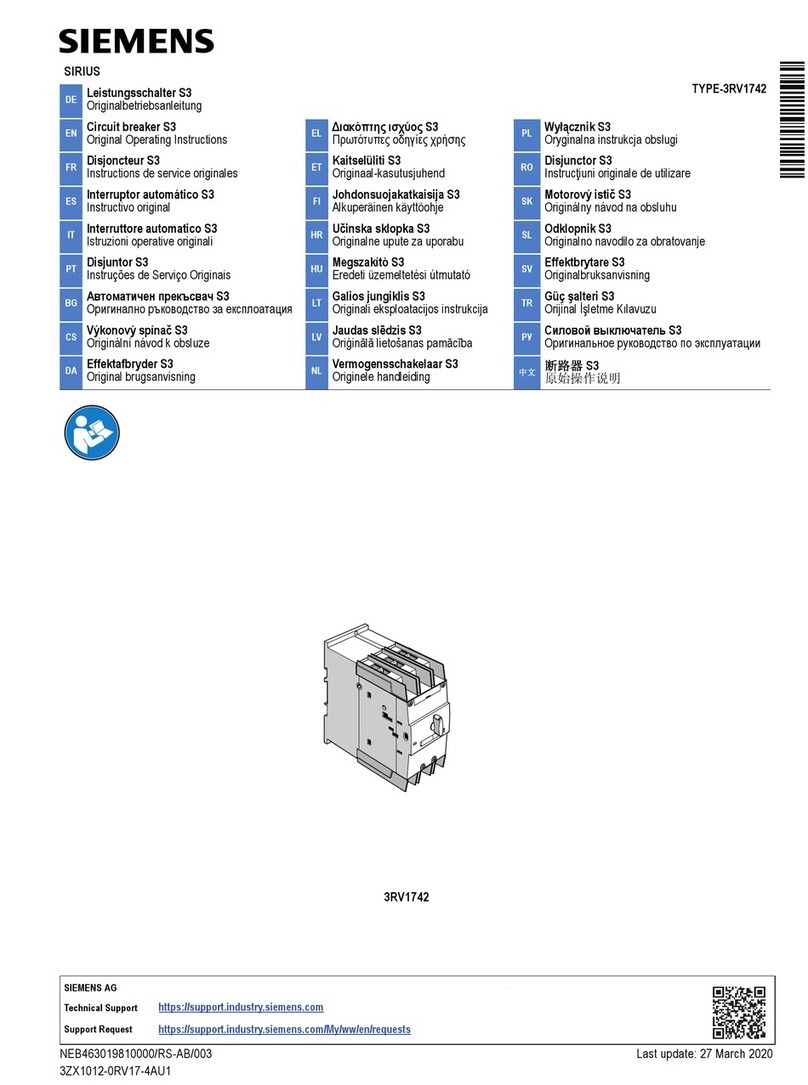
Siemens
Siemens SIRIUS 3RV1742 User manual
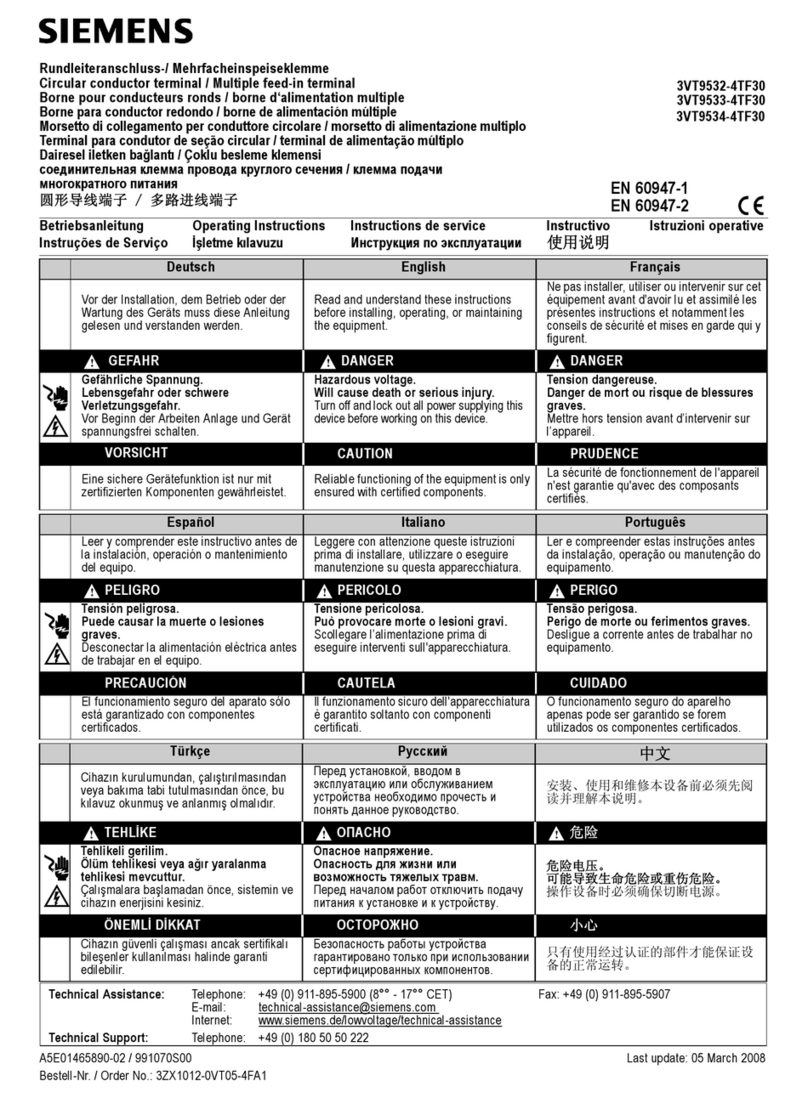
Siemens
Siemens 3VT9532-4TF30 User manual

Siemens
Siemens 3VL41 KN30 Series User manual
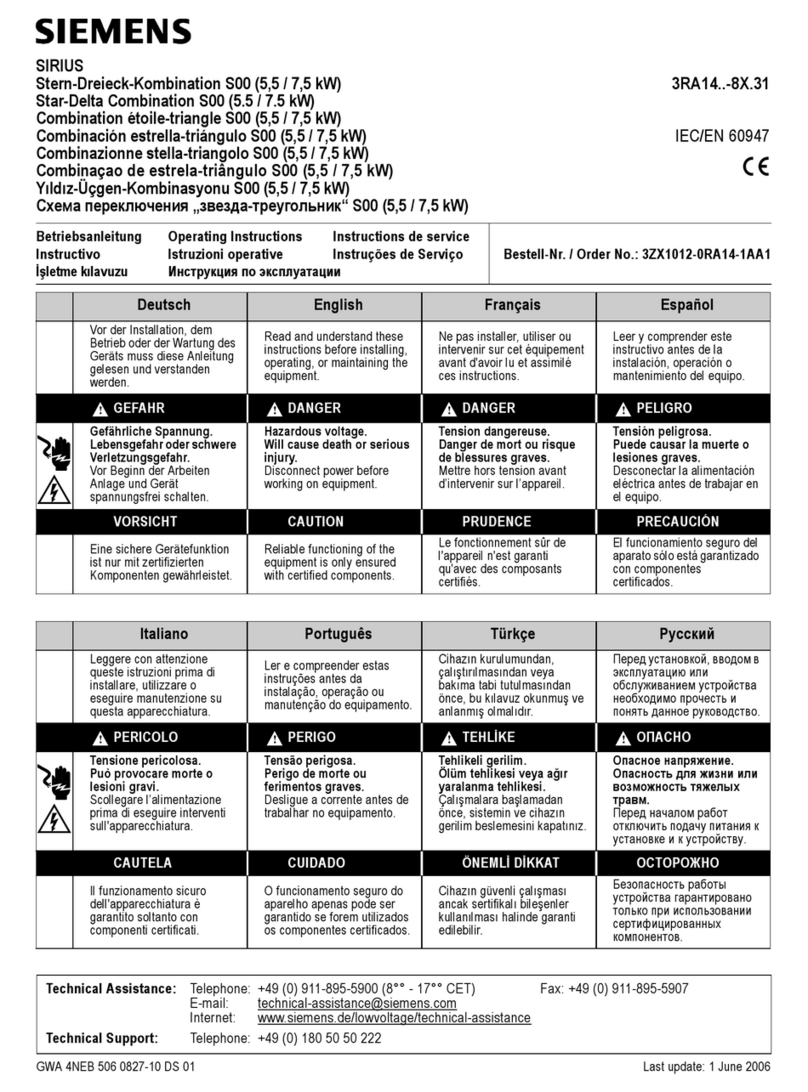
Siemens
Siemens SIRIUS Star-Delta Combination S00 User manual
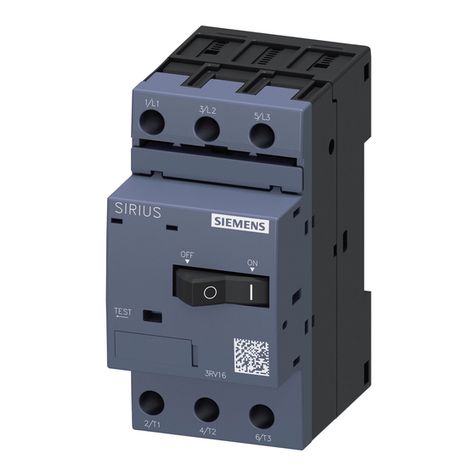
Siemens
Siemens SIRIUS 3RV1611-0BD10 User manual
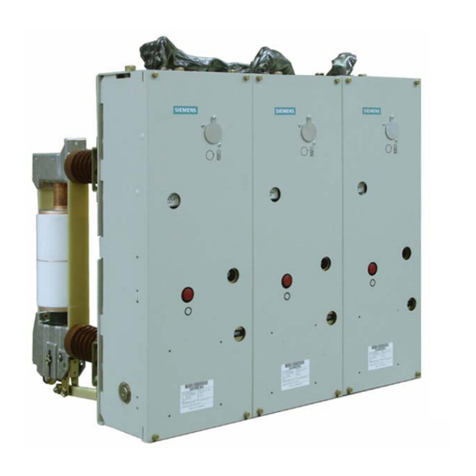
Siemens
Siemens 3AH52 User manual
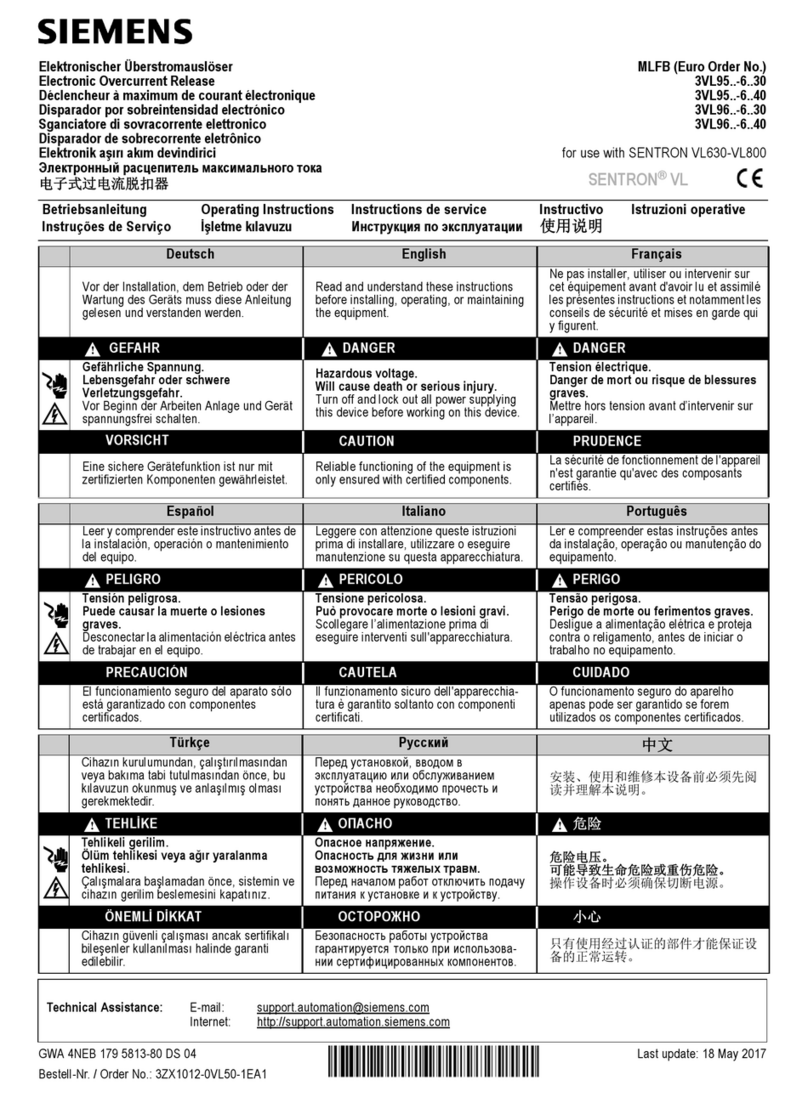
Siemens
Siemens 3VL95 6 Series User manual
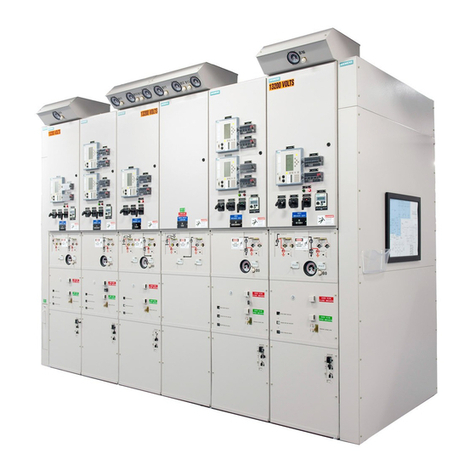
Siemens
Siemens 8DA10 User manual
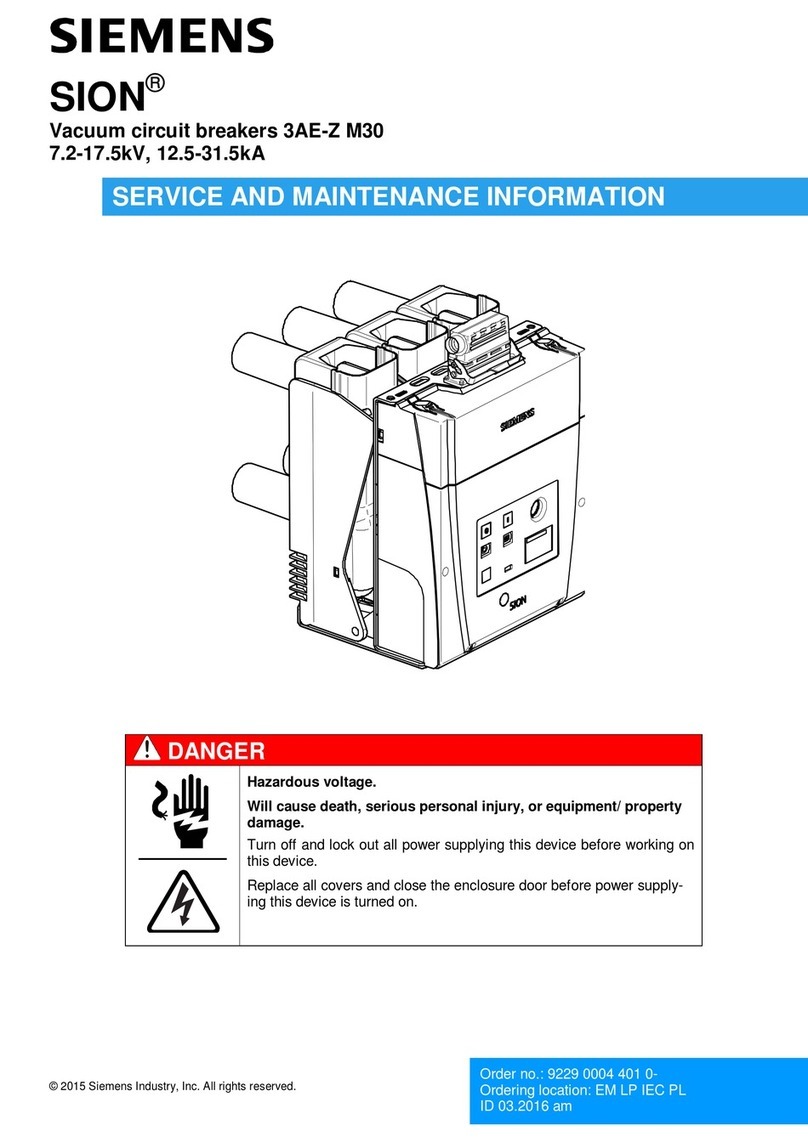
Siemens
Siemens SION 3AE-Z M30 Installation and user guide
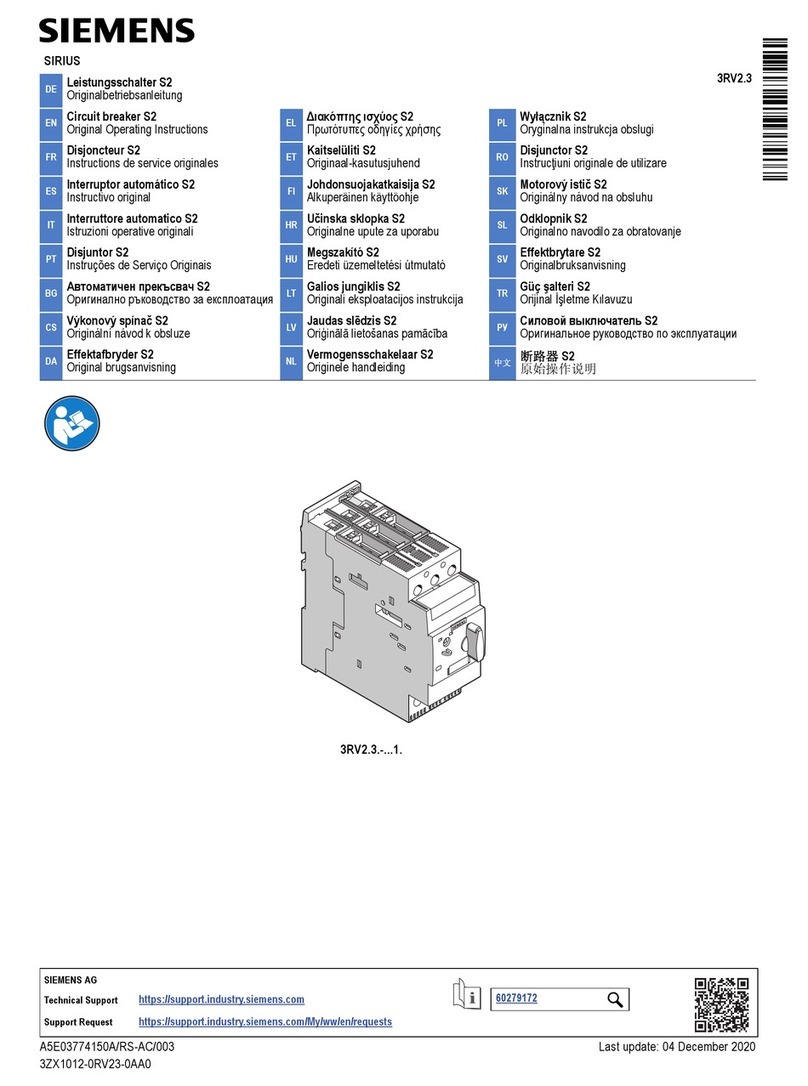
Siemens
Siemens SIRIUS 3RV2 3 Series User manual

Siemens
Siemens Sentron 3VA9157-0FK Series User manual
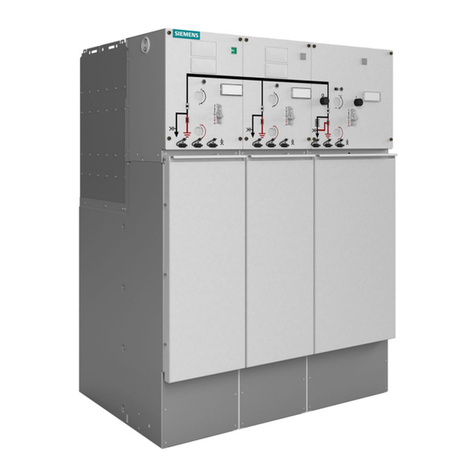
Siemens
Siemens 8DJH Manual

Siemens
Siemens SIPLUS HCS POM4320 Highend Administrator guide
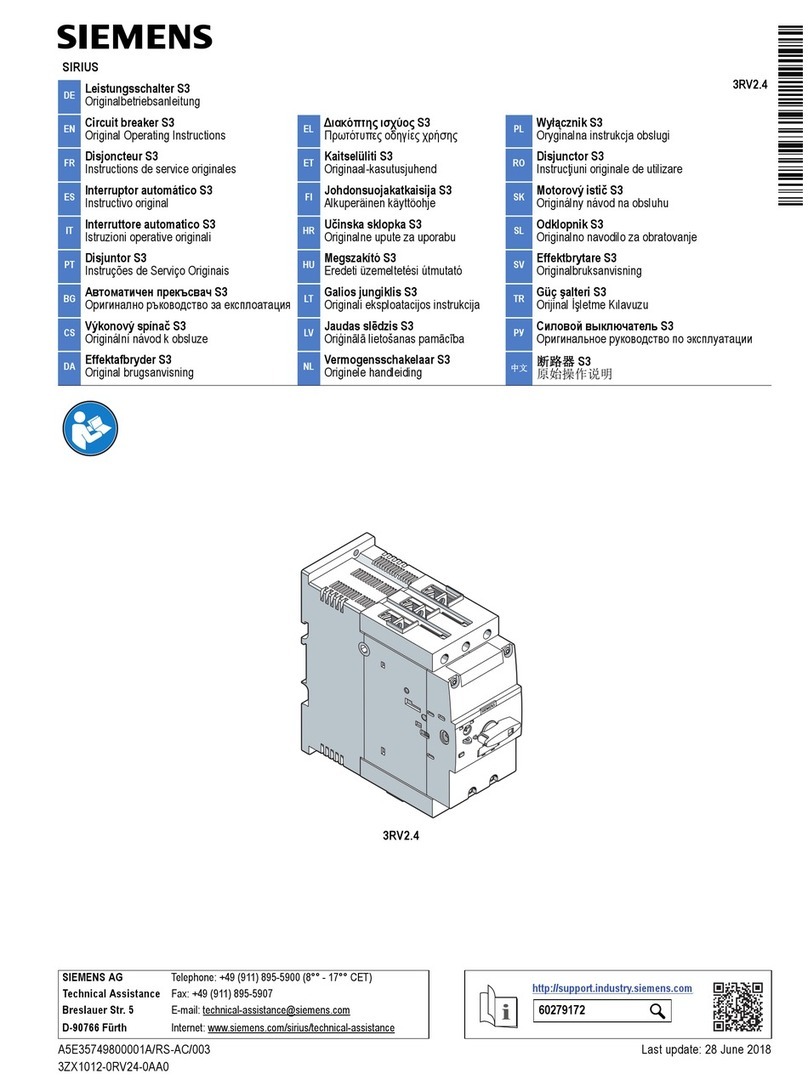
Siemens
Siemens SIRIUS 3RV2.4 User manual
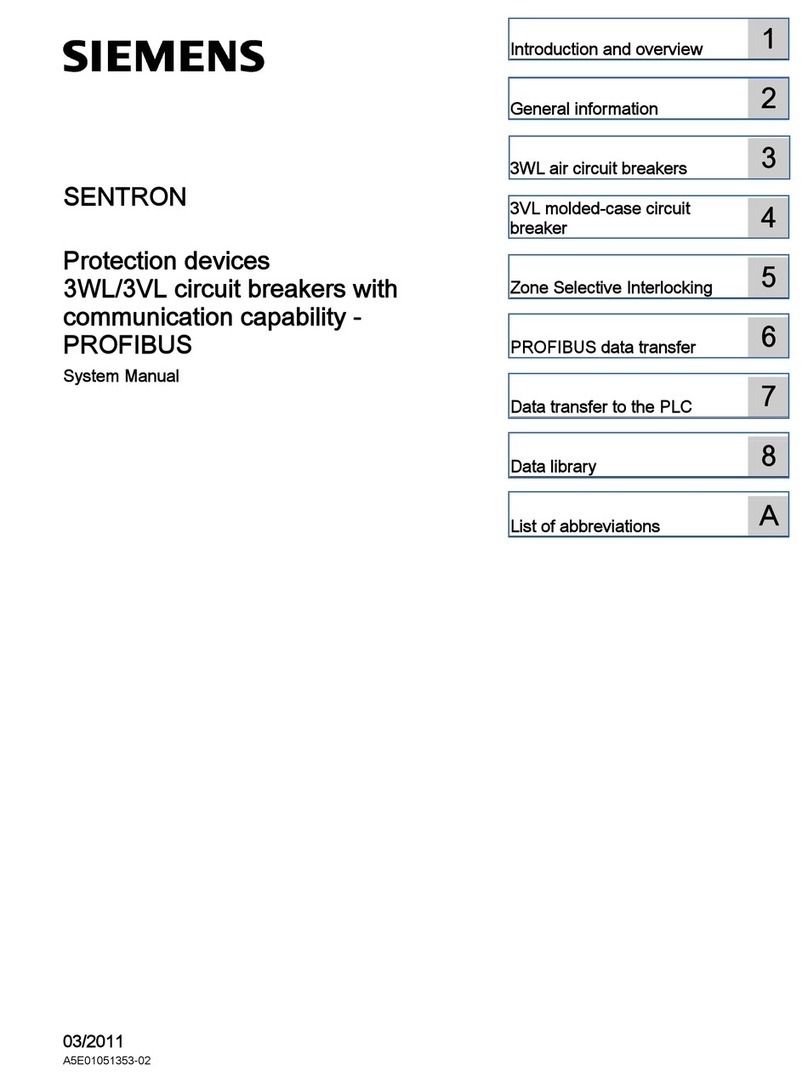
Siemens
Siemens SENTRON VL Series User guide
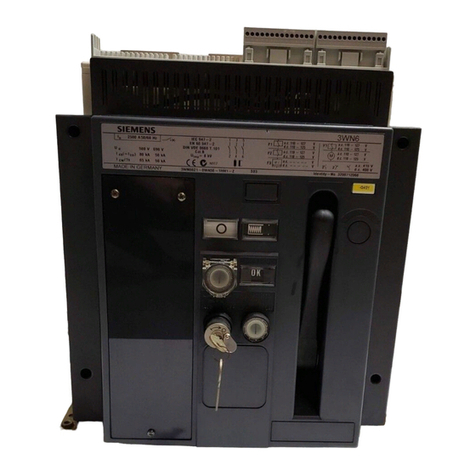
Siemens
Siemens 3WN6 User manual

Siemens
Siemens 3AH6 User manual
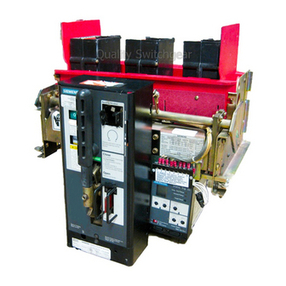
Siemens
Siemens RL Series User manual
Popular Circuit Breaker manuals by other brands
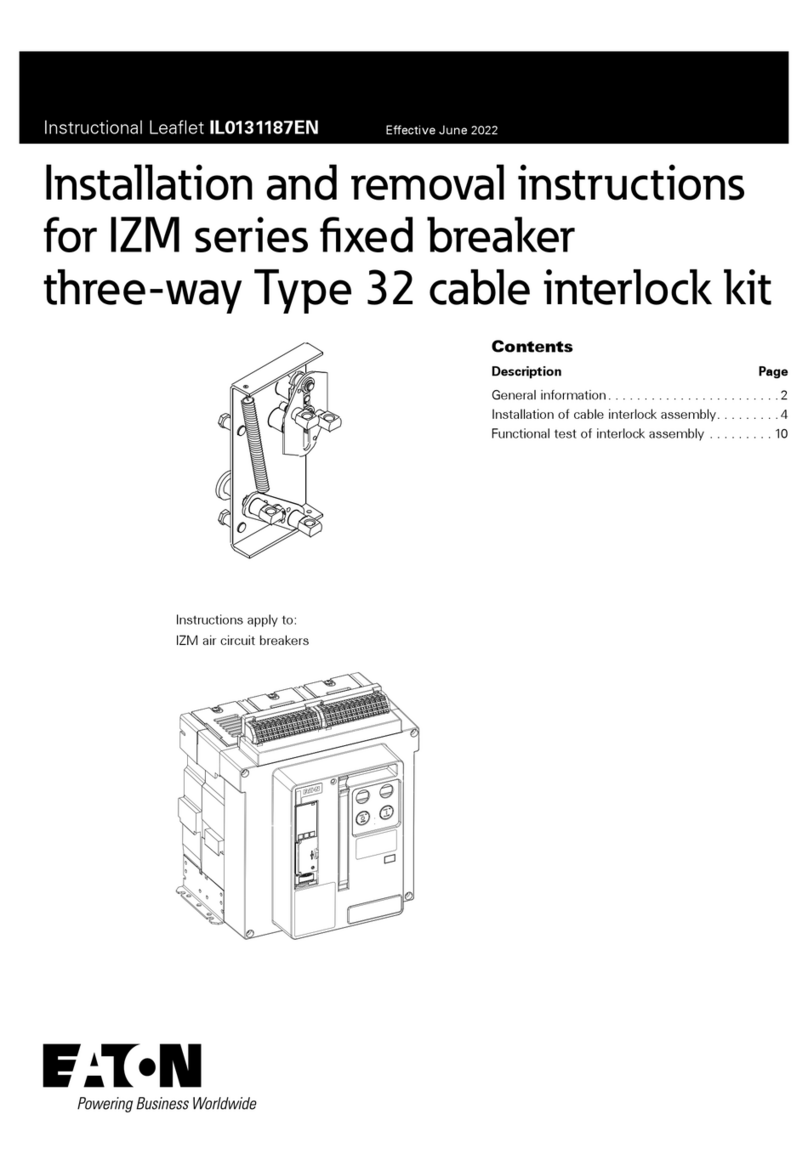
Eaton
Eaton IZM Series Installation and Removal Instructions

ABB
ABB SACE Emax 2 manual
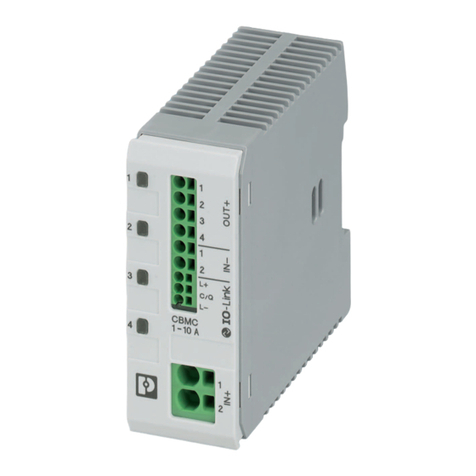
Phoenix Contact
Phoenix Contact CBMC E4 24DC/1-10A IOL user manual
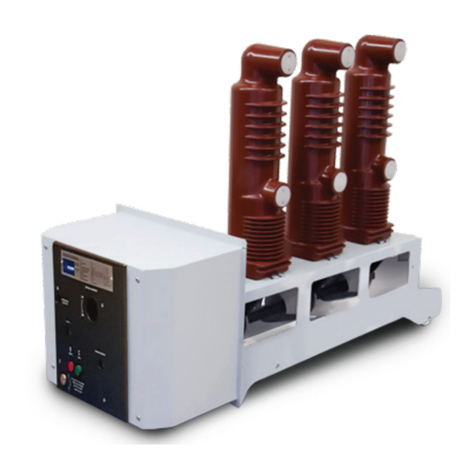
Eaton
Eaton RVU Series operating instructions

Leuze electronic
Leuze electronic MSI-SR-LC21 Series Original operating instructions
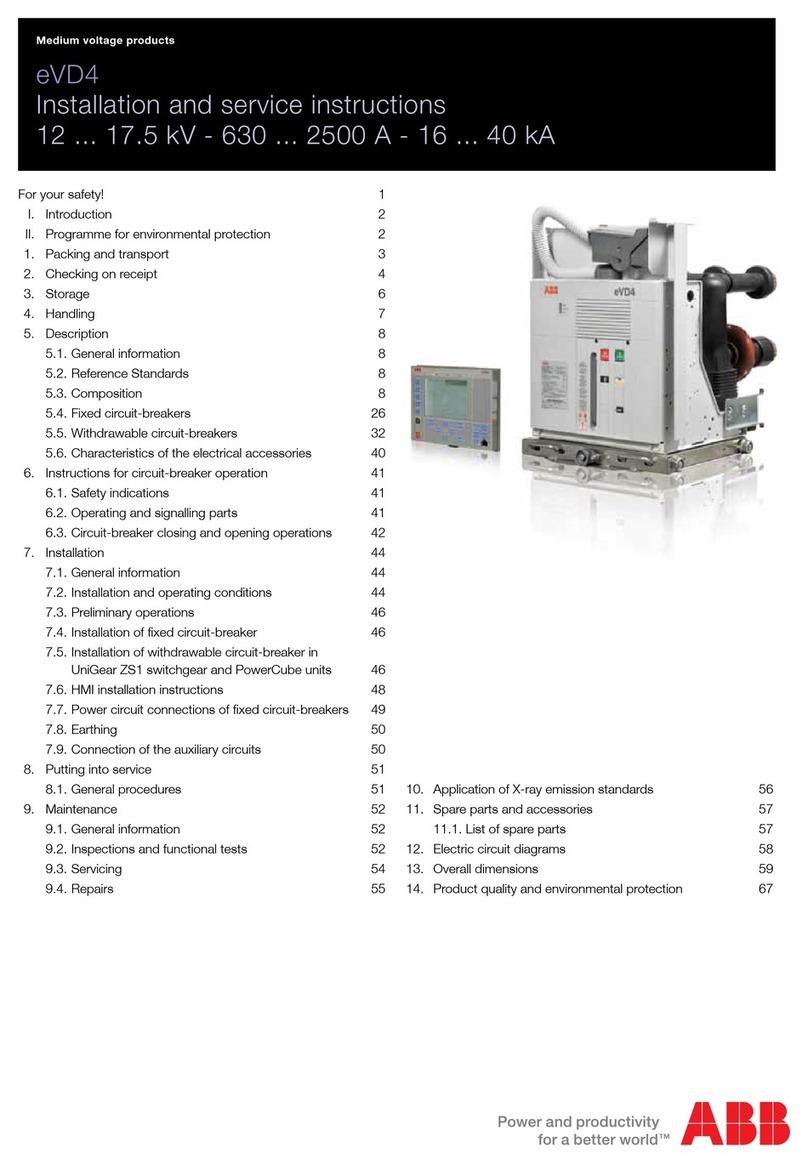
ABB
ABB eVD4 Installation and service instructions