Sminn BOX L VF1D User manual

BOX L VF1D/EA
UNIVERSAL CONTROL PANEL
For gates with 1 three-phase 230VAC motor with frequency converter
INSTRUCTION MANUAL
innovative in electronics

COMPONENTS SITUATION
8
1
4
5
6
2
1. LED connector panel cover
2. TRSH radio card socket
3. LCD display
4. Options selection keypad
5. TEST Run button
6. Connection terminals
7. Auxiliary output relays
8. AC power input fuse
9. High voltage zone 230VAC
10. Bus capacitors
11. Bus load relays
12. Power transformer
Fig.1
9
12
SMINN
BOX L VF1D
7
3
10
11
INDEX
Description .......................................................... 2
Limitation of use of the panel .................... 2
Warnings .............................................................. 2
Installation ........................................................... 3
Important safety instructions for
installation ........................................................... 3
Important safety instructions for use .... 3
Wiring ................................................................... 4
Conguration .................................................... 6
Manoeuvre programming ........................... 7
Manoeuvre ......................................................... 8
Activation ........................................................... 8
Control modes ................................................. 8
Phases .................................................................. 9
Safety test .......................................................... 9
Unlocking ............................................................ 9
Stroke ................................................................... 9
Lock ...................................................................... 10
Pause ................................................................... 10
Safety ................................................................... 11
Stop ...................................................................... 11
Photocells .......................................................... 11
Safety edges .................................................... 12
Amperometric sensor ................................. 12
Encoder .............................................................. 13
Motor ................................................................... 13
Outputs .............................................................. 16
Display ................................................................ 17
Encoder ............................................................. 17
Electrical connection table ...................... 14
Power supply connection of the
photocells ........................................................ 14
Accessories and peripherals .................. 15
Options ............................................................. 18
Adjustments ................................................... 20
Maintenance ................................................... 22
Error logging .................................................. 23
Brake connection ......................................... 24
Absolute encoder connection ............... 25
Photocell shielding ...................................... 25
Warranty .......................................................... 26
Waste electrical and electronic
equipment ....................................................... 26
Technical data ............................................... 27
Declaration of conformity ....................... 27
Notes ................................................................. 28
Explosion components ............................. 29
INDEX OF FIGURES
Figure 1 ........................................................ 0
Figure 2 ....................................................... 14
Figure 3 ....................................................... 29
Symbols
1
.......................... Encoder pulses
. Relay output (NO contact)
................................. Safety edge
..........Normally open contact
........Normally closed contact
............................................... Earth
..................... High voltage area
ESPAÑOLPORTUGÊSDEUTSCH
NEDERLANDS ITALIANO ENGLISHFRANÇAIS

COMPONENTS SITUATION
8
1
4
5
6
2
1. LED connector panel cover
2. TRSH radio card socket
3. LCD display
4. Options selection keypad
5. TEST Run button
6. Connection terminals
7. Auxiliary output relays
8. AC power input fuse
9. High voltage zone 230VAC
10. Bus capacitors
11. Bus load relays
12. Power transformer
Fig.1
9
12
SMINN
BOX L VF1D
7
3
10
11
INDEX
Description .......................................................... 2
Limitation of use of the panel .................... 2
Warnings .............................................................. 2
Installation ........................................................... 3
Important safety instructions for
installation ........................................................... 3
Important safety instructions for use .... 3
Wiring ................................................................... 4
Conguration .................................................... 6
Manoeuvre programming ........................... 7
Manoeuvre ......................................................... 8
Activation ........................................................... 8
Control modes ................................................. 8
Phases .................................................................. 9
Safety test .......................................................... 9
Unlocking ............................................................ 9
Stroke ................................................................... 9
Lock ...................................................................... 10
Pause ................................................................... 10
Safety ................................................................... 11
Stop ...................................................................... 11
Photocells .......................................................... 11
Safety edges .................................................... 12
Amperometric sensor ................................. 12
Encoder .............................................................. 13
Motor ................................................................... 13
Outputs .............................................................. 16
Display ................................................................ 17
Encoder ............................................................. 17
Electrical connection table ...................... 14
Power supply connection of the
photocells ........................................................ 14
Accessories and peripherals .................. 15
Options ............................................................. 18
Adjustments ................................................... 20
Maintenance ................................................... 22
Error logging .................................................. 23
Brake connection ......................................... 24
Absolute encoder connection ............... 25
Photocell shielding ...................................... 25
Warranty .......................................................... 26
Waste electrical and electronic
equipment ....................................................... 26
Technical data ............................................... 27
Declaration of conformity ....................... 27
Notes ................................................................. 28
Explosion components ............................. 29
INDEX OF FIGURES
Figure 1 ........................................................ 0
Figure 2 ....................................................... 14
Figure 3 ....................................................... 29
Symbols
1
.......................... Encoder pulses
. Relay output (NO contact)
................................. Safety edge
..........Normally open contact
........Normally closed contact
............................................... Earth
..................... High voltage area
ESPAÑOLPORTUGÊSDEUTSCH
NEDERLANDS ITALIANO ENGLISHFRANÇAIS

The BXL-VF1D / BXL-VF1EA universal
control panel is designed to form part of a
230VAC three-phase motor automation
system for high-speed, up-and-over, up-
and-over or sliding gates.
The board has the following features:
wControl of 1 three-phase 230VAC motor
up to 1.5kW (delta connection).
wIntuitive multilingual programming
menu via 4 keys and backlit LCD display.
wSupport of 1-channel or 2-channel
encoder (pulse and direction or quadra-
ture) in the VF1D version and absolute
encoder by RS485 in the VF1EA version.
wIndependent regulation of power and
speed in each phase of the manoeuvre.
wCongurable test of safety devices
before each opening or closing.
wThree independent key inputs for
different activation modes.
wThree programmable potential-free
relays with different functions.
wSocket for SMINN radio card (6 pins).
wIndependent inputs for two strips
(resistive or contact) and two photo-
cells.
wLEDs indicating the status of the inputs
and outputs of the panel.
wVoltage outputs for peripherals of
24VAC (12W) and 15VDC (3.5W),
protected by resettable fuses.
wOptocoupled inputs with high electrical
isolation.
wStorage of number of manoeuvres
(partial and total) and events to facilita-
te maintenance. Congurable mainte-
nance signal on external LED.
wManoeuvre learning system that facilita-
tes start-up and conguration.
wObstacle detection with congurable
sensitivity by amperometric sensor
and/or encoder.
DESCRIPTION
LIMITATIONS ON THE USE OF THE
CONTROLLER
Use is not guaranteed when installed on
equipment other than that specied.
The manufacturer reserves the right to
change the specications of the swit-
chgear and this manual without prior
notice. The switchgear must only be
handled by specialised and/or suitably
instructed personnel.
WARNING
The product must be used for its intended
purpose and any other use is considered
inappropriate. Packaging and containers
must not be disposed of in the environ-
ment. Keep products, packaging, contai-
ners, documentation, etc. out of the reach
of children. Observe applicable local,
national and European regulations. The
information contained in this document
may contain errors which will be corrected
in subsequent editions. The manufacturer
reserves the right to modify the contents
of this document or the product without
prior notice.
THE INSTRUCTIONS FOR USE OF THIS EQUIPMENT MUST BE GIVEN TO THE USER. IN CASE OF
LOSS, THE USER MAY REQUEST A COPY OR DOWNLOAD THEM DIRECTLY FROM THE WEBSITE
WWW.SMINN.COM.
S M I N N C O N T R O L P A N E L S A R E
EQUIPPED WITH AN INDICATOR LIGHT
T H A T L E T S U S K N O W I F T H E
EQUIPMENT IS POWERED
2
The box is xed to the wall with only three
screws, all of them external (see Fig.3).
Drill three holes in the wall according to
the cut-out template printed on the
bottom of the box. Use the screws and
plugs supplied.
Cut out the rubber plugs located at the
bottom of the box and pass the cable
conduit through them into the equipment.
Observe the safety instructions for insta-
llation.
Connect the power, motor and device
cables to the terminals on the terminal
strips as indicated on the printed circuit
board. Refer to the following sections of
the manual for wiring and conguration
specic to each element.
Power the panel and the ON LED will light
up (See Fig.1).For the initial operation
check, connect at least the motor, the
brake (if necessary) and the limit switches
or absolute encoder (VF1EA) and use the
keys -> to open and <- to close in dead
man's mode, checking the operation of the
motor (in slow speed and dead man's
mode).
Connect the rest of the automation
elements a nd carr y out a lear ni ng
manoeuvre to start up the control panel.
After nishing, customise the congura-
tion if necessary.
IMPORTANT SAFETY INSTRUCTIONS
FOR INSTALLATION
Before installing the panel::
wCheck that the door/blind is in good
mechanical condition and properly
counterbalanced.
wRemove everything that is not neces-
sary from the environment and switch
off the AC power.
wInstall the panel at a minimum height of
1.5 m, preferably next to the door.
wUse power and motor cables of suitable
cross-section.
wPower the panel via a circuit brea-
ker/emergency switch that is easily
accessible by the user.
The European door standards EN 12453
and EN 12445 specify the minimum levels
of protection and safety for doors installed
in single-family dwellings and communal
and public facilities. The moving door
must be prevented from making contact
with any object or limiting the contact
force (e.g. safety edge), and in the case of
automatic closing, it is necessary to
supplement it with a presence detector
(e.g. photocell).
Check that the congured photocells and
strips act by means of the LED associated
with each of these inputs. The LEDs of the
strips will not activate if this strip has not
been previously activated in the menu
(See Fig. 1).
Make sure that the safety edge is not
activated when the door is completely
closed.
Once the manoeuvre programming and
conguration have been carried out, test
the manoeuvre using the TEST button
(Fig.1), or using the appropriate key input
to validate that the conguration and
operation are correct.
IMPORTANT SAFETY INSTRUCTIONS
FOR USAGE
Once the mechanism is installed and as a
precaution, the user must:
wKeep the control mechanism out of the
reach of children.
wMonitor the movement of the door,
keeping the area clear of people and
objects.
wExercise caution when operating the
door manually (unlocked) as it may
move uncontrollably due to the weight
of the door, the condition of the xings,
springs and counterweights.
If a malfunction of the system is observed,
the user should IMMEDIATELY contact the
technical support service. The mechanism
must not be used as it may cause damage.
INSTALLATION
3
ESPAÑOLPORTUGÊSDEUTSCH
NEDERLANDS ITALIANO ENGLISHFRANÇAIS

The BXL-VF1D / BXL-VF1EA universal
control panel is designed to form part of a
230VAC three-phase motor automation
system for high-speed, up-and-over, up-
and-over or sliding gates.
The board has the following features:
wControl of 1 three-phase 230VAC motor
up to 1.5kW (delta connection).
wIntuitive multilingual programming
menu via 4 keys and backlit LCD display.
wSupport of 1-channel or 2-channel
encoder (pulse and direction or quadra-
ture) in the VF1D version and absolute
encoder by RS485 in the VF1EA version.
wIndependent regulation of power and
speed in each phase of the manoeuvre.
wCongurable test of safety devices
before each opening or closing.
wThree independent key inputs for
different activation modes.
wThree programmable potential-free
relays with different functions.
wSocket for SMINN radio card (6 pins).
wIndependent inputs for two strips
(resistive or contact) and two photo-
cells.
wLEDs indicating the status of the inputs
and outputs of the panel.
wVoltage outputs for peripherals of
24VAC (12W) and 15VDC (3.5W),
protected by resettable fuses.
wOptocoupled inputs with high electrical
isolation.
wStorage of number of manoeuvres
(partial and total) and events to facilita-
te maintenance. Congurable mainte-
nance signal on external LED.
wManoeuvre learning system that facilita-
tes start-up and conguration.
wObstacle detection with congurable
sensitivity by amperometric sensor
and/or encoder.
DESCRIPTION
LIMITATIONS ON THE USE OF THE
CONTROLLER
Use is not guaranteed when installed on
equipment other than that specied.
The manufacturer reserves the right to
change the specications of the swit-
chgear and this manual without prior
notice. The switchgear must only be
handled by specialised and/or suitably
instructed personnel.
WARNING
The product must be used for its intended
purpose and any other use is considered
inappropriate. Packaging and containers
must not be disposed of in the environ-
ment. Keep products, packaging, contai-
ners, documentation, etc. out of the reach
of children. Observe applicable local,
national and European regulations. The
information contained in this document
may contain errors which will be corrected
in subsequent editions. The manufacturer
reserves the right to modify the contents
of this document or the product without
prior notice.
THE INSTRUCTIONS FOR USE OF THIS EQUIPMENT MUST BE GIVEN TO THE USER. IN CASE OF
LOSS, THE USER MAY REQUEST A COPY OR DOWNLOAD THEM DIRECTLY FROM THE WEBSITE
WWW.SMINN.COM.
S M I N N C O N T R O L P A N E L S A R E
EQUIPPED WITH AN INDICATOR LIGHT
T H A T L E T S U S K N O W I F T H E
EQUIPMENT IS POWERED
2
The box is xed to the wall with only three
screws, all of them external (see Fig.3).
Drill three holes in the wall according to
the cut-out template printed on the
bottom of the box. Use the screws and
plugs supplied.
Cut out the rubber plugs located at the
bottom of the box and pass the cable
conduit through them into the equipment.
Observe the safety instructions for insta-
llation.
Connect the power, motor and device
cables to the terminals on the terminal
strips as indicated on the printed circuit
board. Refer to the following sections of
the manual for wiring and conguration
specic to each element.
Power the panel and the ON LED will light
up (See Fig.1).For the initial operation
check, connect at least the motor, the
brake (if necessary) and the limit switches
or absolute encoder (VF1EA) and use the
keys -> to open and <- to close in dead
man's mode, checking the operation of the
motor (in slow speed and dead man's
mode).
Connect the rest of the automation
elements a nd carr y out a lear ni ng
manoeuvre to start up the control panel.
After nishing, customise the congura-
tion if necessary.
IMPORTANT SAFETY INSTRUCTIONS
FOR INSTALLATION
Before installing the panel::
wCheck that the door/blind is in good
mechanical condition and properly
counterbalanced.
wRemove everything that is not neces-
sary from the environment and switch
off the AC power.
wInstall the panel at a minimum height of
1.5 m, preferably next to the door.
wUse power and motor cables of suitable
cross-section.
wPower the panel via a circuit brea-
ker/emergency switch that is easily
accessible by the user.
The European door standards EN 12453
and EN 12445 specify the minimum levels
of protection and safety for doors installed
in single-family dwellings and communal
and public facilities. The moving door
must be prevented from making contact
with any object or limiting the contact
force (e.g. safety edge), and in the case of
automatic closing, it is necessary to
supplement it with a presence detector
(e.g. photocell).
Check that the congured photocells and
strips act by means of the LED associated
with each of these inputs. The LEDs of the
strips will not activate if this strip has not
been previously activated in the menu
(See Fig. 1).
Make sure that the safety edge is not
activated when the door is completely
closed.
Once the manoeuvre programming and
conguration have been carried out, test
the manoeuvre using the TEST button
(Fig.1), or using the appropriate key input
to validate that the conguration and
operation are correct.
IMPORTANT SAFETY INSTRUCTIONS
FOR USAGE
Once the mechanism is installed and as a
precaution, the user must:
wKeep the control mechanism out of the
reach of children.
wMonitor the movement of the door,
keeping the area clear of people and
objects.
wExercise caution when operating the
door manually (unlocked) as it may
move uncontrollably due to the weight
of the door, the condition of the xings,
springs and counterweights.
If a malfunction of the system is observed,
the user should IMMEDIATELY contact the
technical support service. The mechanism
must not be used as it may cause damage.
INSTALLATION
3
ESPAÑOLPORTUGÊSDEUTSCH
NEDERLANDS ITALIANO ENGLISHFRANÇAIS

WIRING
The panel is supplied with 230VAC 50Hz
via terminals 1 and 2. The earth connection
is made at terminal 3.
The control unit can control a three-phase
230VAC motor. Connect the three phases
to terminals 4, 5 and 6 and connect the
earth terminal 7 to the motor housing. If
the direction of rotation is incorrect, swap
two of the phases.
NOTE: In order to comply with European
standards regarding electromagnetic
interference, it is mandatory to pass the
motor cables back through the ferrite core
included with the product.
The panel has three potential-free relay
contacts normally open to perform
different functions such as control of
lamps, trafc lights, brake, electric lock...
These relays can withstand 16A over
24VDC or 230VAC. See page 24 for
electromechanical brake wiring instruc-
tions.
Terminals 14-15 provide 12W with 24VAC
via a resettable fuse to power external
devices such as lamps or an electric lock.
At terminals 16 and 17, the panel has a
voltage output for peripherals of 15VDC -
3.5VA protected by a resettable fuse for
powering external circuits such as photo-
cells.
Additionally, terminal 18 serves as a
specic negative for photocell testing.
According to standard.
Terminals 20 and 21 allow the connection
of one or two resistive or contact strips.
Terminals 22 and 23 allow the connection
of one or two normally closed safety
circuits (normally photocells). Terminals
24 and 25 are used to manage two limit
switches, the opening limit switch on
terminal 24 and the closing limit switch on
terminal 25.
Terminals 19 and 26 serve as common
terminals for the connection of all the
above elements.
NOTE: The limit switches must be connec-
ted for the correct operation of the
system, except if an absolute encoder is
used in the VF1EA version.
4
VF1D: Terminals 27 and 30 provide an
incremental encoder with 5VDC power
supply. Terminals 28 and 29 are used to
connect the encoder signals, either one-
channel encoder (signal to terminal 28) or
two-channel encoder in quadrature or
direction and signal mode (one signal to
terminal 28 and one signal to terminal 29).
Terminals 31 and 32 are used for the
connection of a normally closed safety
device for emergency stop, such as an
emergency stop mushroom.
The control unit has three independent
key inputs which are congured with
different functions depending on the
selected operating mode.
Normally, input LL1 serves as an opening
command and input LL2 serves as a
closing or pedestrian opening command.
Terminal 36 serves as common for all key
inputs.
The radio card socket allows a SMINN
radio card (6 pins) to be plugged in,
enabling the opening command to be
given via radio transmitters.
WIRING
VF1EA: Terminals 27 and 30 provide an
absolute encoder with 12VDC power
supply. Terminals 28 and 29 are used to
connect the RS485 signals of the encoder.
For correct operation it is necessary to
connect each terminal to the encoder
terminal marked with the same symbol (A
to A and B to B). See page 25 for connec-
tion instructions.
5
AB
ESPAÑOLPORTUGÊSDEUTSCH
NEDERLANDS ITALIANO ENGLISHFRANÇAIS

WIRING
The panel is supplied with 230VAC 50Hz
via terminals 1 and 2. The earth connection
is made at terminal 3.
The control unit can control a three-phase
230VAC motor. Connect the three phases
to terminals 4, 5 and 6 and connect the
earth terminal 7 to the motor housing. If
the direction of rotation is incorrect, swap
two of the phases.
NOTE: In order to comply with European
standards regarding electromagnetic
interference, it is mandatory to pass the
motor cables back through the ferrite core
included with the product.
The panel has three potential-free relay
contacts normally open to perform
different functions such as control of
lamps, trafc lights, brake, electric lock...
These relays can withstand 16A over
24VDC or 230VAC. See page 24 for
electromechanical brake wiring instruc-
tions.
Terminals 14-15 provide 12W with 24VAC
via a resettable fuse to power external
devices such as lamps or an electric lock.
At terminals 16 and 17, the panel has a
voltage output for peripherals of 15VDC -
3.5VA protected by a resettable fuse for
powering external circuits such as photo-
cells.
Additionally, terminal 18 serves as a
specic negative for photocell testing.
According to standard.
Terminals 20 and 21 allow the connection
of one or two resistive or contact strips.
Terminals 22 and 23 allow the connection
of one or two normally closed safety
circuits (normally photocells). Terminals
24 and 25 are used to manage two limit
switches, the opening limit switch on
terminal 24 and the closing limit switch on
terminal 25.
Terminals 19 and 26 serve as common
terminals for the connection of all the
above elements.
NOTE: The limit switches must be connec-
ted for the correct operation of the
system, except if an absolute encoder is
used in the VF1EA version.
4
VF1D: Terminals 27 and 30 provide an
incremental encoder with 5VDC power
supply. Terminals 28 and 29 are used to
connect the encoder signals, either one-
channel encoder (signal to terminal 28) or
two-channel encoder in quadrature or
direction and signal mode (one signal to
terminal 28 and one signal to terminal 29).
Terminals 31 and 32 are used for the
connection of a normally closed safety
device for emergency stop, such as an
emergency stop mushroom.
The control unit has three independent
key inputs which are congured with
different functions depending on the
selected operating mode.
Normally, input LL1 serves as an opening
command and input LL2 serves as a
closing or pedestrian opening command.
Terminal 36 serves as common for all key
inputs.
The radio card socket allows a SMINN
radio card (6 pins) to be plugged in,
enabling the opening command to be
given via radio transmitters.
WIRING
VF1EA: Terminals 27 and 30 provide an
absolute encoder with 12VDC power
supply. Terminals 28 and 29 are used to
connect the RS485 signals of the encoder.
For correct operation it is necessary to
connect each terminal to the encoder
terminal marked with the same symbol (A
to A and B to B). See page 25 for connec-
tion instructions.
5
AB
ESPAÑOLPORTUGÊSDEUTSCH
NEDERLANDS ITALIANO ENGLISHFRANÇAIS

To facilitate the conguration and
maintenance of the panel, it has an advan-
ced menu system accessible by means of
an integrated 4-key keypad and data
presentation on a backlit LCD display that
allows the panel to be congured simply,
quickly and intuitively.
Press the BACK + ENTER keys simulta-
neously to access the conguration menu.
The LCD will light up. To move through the
menu, the panel has 4 keys which are:
BACK (exit)
ENTER (accept)
<- (back)
-> (forward)
While using the conguration menu, the
two lines of the screen are normally used;
on one of them, the symbols < and > will
appear at the ends to indicate that the
user is navigating on that line. Navigating
on the top line navigates between menus
and parameters (with the current value, if
applicable, appearing on the bottom line).
Navigating on the bottom line navigates
between the possible values of the selec-
ted parameter, shown on the top line.
Therefore, the <- / -> keys are used to
move between the elements of the current
navigation level, the ENTER key is used to
select an element or validate the selection
of a value, and the BACK key is used to
cancel the modication of a parameter
and, in general, to go backwards.
CONFIGURATION
BACK ENTER
BACK ENTER
Force diagram
Fd: Dynamic force
Fs: Static force
Temporarily and depending on its use, the
installation must be subjected to a
complete operation test by qualied
personnel in order to detect any signs of
wear or deterioration.
If for any reason the panel needs to be
repaired, contact the manufacturer or the
nearest ofcial service centre.
O n c e t h e m a n o e u v r e h a s b e e n
programmed, we must ensure that the
power and soft stop settings are suitable
for compliance with standard EN
1 2 4 5 3 : 2 0 1 8 + A 1 : 2 0 2 2 , t a k i n g t h e
measurements in accordance with the
method described in the standard. See
force graph.
If, due to the characteristics of the
installation, these values are not met,
additional protection elements must be
installed.
The dynamic force Fd must not exceed
the following measurements:
< 400N in spaces between 5-50cm
< 1400N in spaces larger than 50cm
BOX L VF1D
SMINN
6
The control panel has a conguration
wizard that allows you to select the most
important parameters and start up the
control panel quickly.
To start the wizard, with the door closed,
enter the conguration menu by pressing
BACK+ENTER, the parameter GATE TYPE
will appear.
Press ENTER and use the <-/-> keys to
scroll through the options until the desired
type is selected. Press ENTER to validate.
Then press -> and MANIOB MODE will
appear.
Press ENTER to access the submenu and
use the <-/ -> keys to select the desired
mode. Press ENTER to validate. Then
press -> until the MAINTENANCE menu
appears. Press ENTER to access the
submenu. Press -> to select the OPEN
and/or CLOSE commands.
In either command, pressing ENTER will
operate the door (opening or closing) in
deadman mode at soft stop speed and
power. In this way it is checked that the
connections of the phases to the motor
are correctly made and the direction of
rotation of the motor is correct, or not, in
which case the parameter INVERT MOTOR
can be used or any 2 phases can be swap-
ped between them.
Once these steps have been carried out,
press -> until PROG MANEUVER appears on
the screen and accept by pressing ENTER.
After this, the panel will ask one by one for
the vital parameters of the conguration.
Choose the desired value for each option
with the <- and -> keys and press ENTER
to accept and continue or BACK to go
back.
If the door interrupts the photocell insta-
lled at input S1 during its movement, it is
possible to congure the panel to learn the
inhibition interval automatically by setting
the parameter INHIB. SEG1 parameter to
YES.
In the case of the VF1EA version with
absolute encoder enabled, the panel will
instruct you to position the door at the
opening and closing points using the <-
and -> keys to memorise their positions.
After conguring the basic parameters,
MANOEUVER PROG.
the panel will indicate that after pressing
ENTER again, the learning manoeuvre will
begin.
From here you can carry out the following
steps using the ENTER key, the LL1 key
input, or by means of a radio transmitter:
wPress to start opening.
wPress to start soft stop (if the parame-
ter SOFT STOP is activated).
wWait until the opening limit switch is
reached (the door will stop by itself).
wPress to start closing.
wPress to start soft stop (if parameter
SOFT STOP is activated).
wWait until the closing limit switch is
reached (the door will stop by itself).
wThe control panel will record by default
both the opening and closing time
(with a 10% increment) as a safety
measure in case of failure in the limit
switches.
The programming manoeuvre will change
the following parameters:
wTOTAL PULSES
wSOFT STOP AP
wSOFT STOP CR
wM1 SENSIB.
wM1 ENC SENS
wM1 LIM. PRES.
wOPENING TIME (with a 10% increase)
wCLOSING TIME (with a 10% increase)
wPOLARITY ENC
wENC ABS POS I (for the VF1EA model)
wENC ABS POS F (for the VF1EA model)
7
ESPAÑOLPORTUGÊSDEUTSCH
NEDERLANDS ITALIANO ENGLISHFRANÇAIS

To facilitate the conguration and
maintenance of the panel, it has an advan-
ced menu system accessible by means of
an integrated 4-key keypad and data
presentation on a backlit LCD display that
allows the panel to be congured simply,
quickly and intuitively.
Press the BACK + ENTER keys simulta-
neously to access the conguration menu.
The LCD will light up. To move through the
menu, the panel has 4 keys which are:
BACK (exit)
ENTER (accept)
<- (back)
-> (forward)
While using the conguration menu, the
two lines of the screen are normally used;
on one of them, the symbols < and > will
appear at the ends to indicate that the
user is navigating on that line. Navigating
on the top line navigates between menus
and parameters (with the current value, if
applicable, appearing on the bottom line).
Navigating on the bottom line navigates
between the possible values of the selec-
ted parameter, shown on the top line.
Therefore, the <- / -> keys are used to
move between the elements of the current
navigation level, the ENTER key is used to
select an element or validate the selection
of a value, and the BACK key is used to
cancel the modication of a parameter
and, in general, to go backwards.
CONFIGURATION
BACK ENTER
BACK ENTER
Force diagram
Fd: Dynamic force
Fs: Static force
Temporarily and depending on its use, the
installation must be subjected to a
complete operation test by qualied
personnel in order to detect any signs of
wear or deterioration.
If for any reason the panel needs to be
repaired, contact the manufacturer or the
nearest ofcial service centre.
O n c e t h e m a n o e u v r e h a s b e e n
programmed, we must ensure that the
power and soft stop settings are suitable
for compliance with standard EN
1 2 4 5 3 : 2 0 1 8 + A 1 : 2 0 2 2 , t a k i n g t h e
measurements in accordance with the
method described in the standard. See
force graph.
If, due to the characteristics of the
installation, these values are not met,
additional protection elements must be
installed.
The dynamic force Fd must not exceed
the following measurements:
< 400N in spaces between 5-50cm
< 1400N in spaces larger than 50cm
BOX L VF1D
SMINN
6
The control panel has a conguration
wizard that allows you to select the most
important parameters and start up the
control panel quickly.
To start the wizard, with the door closed,
enter the conguration menu by pressing
BACK+ENTER, the parameter GATE TYPE
will appear.
Press ENTER and use the <-/-> keys to
scroll through the options until the desired
type is selected. Press ENTER to validate.
Then press -> and MANIOB MODE will
appear.
Press ENTER to access the submenu and
use the <-/ -> keys to select the desired
mode. Press ENTER to validate. Then
press -> until the MAINTENANCE menu
appears. Press ENTER to access the
submenu. Press -> to select the OPEN
and/or CLOSE commands.
In either command, pressing ENTER will
operate the door (opening or closing) in
deadman mode at soft stop speed and
power. In this way it is checked that the
connections of the phases to the motor
are correctly made and the direction of
rotation of the motor is correct, or not, in
which case the parameter INVERT MOTOR
can be used or any 2 phases can be swap-
ped between them.
Once these steps have been carried out,
press -> until PROG MANEUVER appears on
the screen and accept by pressing ENTER.
After this, the panel will ask one by one for
the vital parameters of the conguration.
Choose the desired value for each option
with the <- and -> keys and press ENTER
to accept and continue or BACK to go
back.
If the door interrupts the photocell insta-
lled at input S1 during its movement, it is
possible to congure the panel to learn the
inhibition interval automatically by setting
the parameter INHIB. SEG1 parameter to
YES.
In the case of the VF1EA version with
absolute encoder enabled, the panel will
instruct you to position the door at the
opening and closing points using the <-
and -> keys to memorise their positions.
After conguring the basic parameters,
MANOEUVER PROG.
the panel will indicate that after pressing
ENTER again, the learning manoeuvre will
begin.
From here you can carry out the following
steps using the ENTER key, the LL1 key
input, or by means of a radio transmitter:
wPress to start opening.
wPress to start soft stop (if the parame-
ter SOFT STOP is activated).
wWait until the opening limit switch is
reached (the door will stop by itself).
wPress to start closing.
wPress to start soft stop (if parameter
SOFT STOP is activated).
wWait until the closing limit switch is
reached (the door will stop by itself).
wThe control panel will record by default
both the opening and closing time
(with a 10% increment) as a safety
measure in case of failure in the limit
switches.
The programming manoeuvre will change
the following parameters:
wTOTAL PULSES
wSOFT STOP AP
wSOFT STOP CR
wM1 SENSIB.
wM1 ENC SENS
wM1 LIM. PRES.
wOPENING TIME (with a 10% increase)
wCLOSING TIME (with a 10% increase)
wPOLARITY ENC
wENC ABS POS I (for the VF1EA model)
wENC ABS POS F (for the VF1EA model)
7
ESPAÑOLPORTUGÊSDEUTSCH
NEDERLANDS ITALIANO ENGLISHFRANÇAIS

ACTIVATION
The key inputs (marked LL1, LL2 and LL3)
and a radio card installed in the radio
socket can be used to start a manoeuvre
when the control panel is idle.
The functions of the key inputs LL1, LL2
and the radio card are determined by the
selected manoeuvre mode, while input
LL3 can be set separately to operate
differently (using the POLARITY and MODE
parameters within the LL3 menu). It is
possible to disable any of the LL1, LL2 or
LL3 inputs using the LL1 BLOCK, LL2
BLOCK or LL3 BLOCK parameters, so that
any stimulus on these inputs will be
ignored.
Each input is assigned a transit direction
to enable the use of discriminating trafc
lights. LL1, LL2, and the radio card are used
for the incoming transit direction and LL3
for the outgoing transit direction.
NOTE: The radio card operates by default
the same as LL1 unless the parameter
RADIO ALT STOP is activated, in which
case it shall operate in alternate stop
(regardless of the general manoeuvre
mode selected).
MANOEUVRE MODES
The MANOEUVER MODE parameter sets the
functions that the key and radio inputs
perform.
STANDARD
In STANDARD mode, Ll1 will give an open
command if the door is closed and a close
command if the door is open and at rest.
LL2 will work in the same way except that
the opening will be in pedestrian mode.
None of the keys perform any function
while the door is moving unless the
parameter INVER ON KEY is activated, in
which case during closing LL1 and LL2 will
cause a soft manoeuvre inversion to be
performed. In this mode, AUTO CLOSING is
activated by default, although in OPTIONS,
by accessing this command, it can be
deactivated by selecting NO.
MANOEUVER
OPEN/CLOSE
The OPEN/CLOSE mode uses LL1 as the
opening command and LL2 as the closing
command. When the door is in motion the
opposite direction input will cause a
smooth reversal of manoeuvre (without
passing through stop). In this mode, AUTO
CLOSE is disabled by default, although in
OPTIONS, by accessing this command it
can be activated by selecting YES.
ALT. STOP
The ALT STOP mode works in the same
way as the STANDARD mode, except that if
LL1 or LL2 is used while the door is moving,
it stops. The next press will make the door
continue the manoeuvre in the opposite
direction to the previous one. In this mode,
the AUTO CLOSE is disabled by default,
although in OPTIONS, by accessing this
command, it can be activated by selecting
YES.
DEADMAN
The DEADMAN mode only allows the door
to move while the LL1 or radio input is
active (opening) or the LL2 input is active
(closing). The manoeuvre is interrupted
when the input in use is deactivated. In this
mode, th e saf et ie s onl y pause the
manoeuvre.
SEMI. DEADMAN
The SEMI DEADMAN mode performs full
opening in the normal way when using LL1
or LL2, but requires using either of the
inputs in deadman mode to close.
AUXILIARY DEADMAN
The parameter AUX DEAD MAN parameter
allows the panel to temporarily operate in
deadman mode when one of the safeties
fails the test, allowing the door to be
opened in case of problems. When this
option is activated, in the event of a failure,
simply press and hold the usual key or
radio input for a few seconds.
8
PHASES
SAFETY TESTS
The safety tests phase is performed in the
beginning of every maneuver before
moving the gate. The controller rst
checks for obstructed safeties (corres-
ponding led off in the board) that are
relevant to the maneuver. If there is any
obstructed safety it waits for them to
enter idle state and will show a message in
the display to this effect. Then the board
checks the resistive values of safety edges
and performs a test procedure on light
barriers removing power from the trans-
mitter to check the system is in order.
UNLOCKING
The unlocking phase performs many
different functions simultaneosly before
starting the movement phase:
wActivates the garage light relay during
the time interval specied by the GARG
LIGHT T parameter. This paremeter can
be set to any time from 1 sec. to 240
sec., thus saving the need to use an
external timer.
wActivates the electrolock relay if any of
the relays is congured as such and the
ELECTROLOCK parameter is set with a
time interval.
wWhen the electrolock is activated and
the maneuver will open the gate the
controler performs a reversing stroke in
soft stop speed ( OP SOFT VEL parame-
ter) with normal power (OP NORMAL POW
parameter) for a duration specied by
the REVERS. STROKE parameter.
wPerforms preashing through a relay
congured for light beacon during the
time interval specied by the PREFLASH
OP T parameter for opening and the
PREFLASH CL T for closing. Preashing
is managed following the mode speci-
ed by the PREFLASH MODE parameter. If
the FLASHING SEM. parameter is set
preashing will be performed through a
relay congured as red semaphore
light.
MANOEUVER
MOVEMENT
The movement phase comprises the
actual gate movement and management
of the safety devices. First the red semap-
hore light is activated if any relay is set as
such and the maneuver counters are
incremented (once per gate movement
direction). The electrolock, if activated in
the previous phase, is held active until the
time specied by the ELECTROLOCK
parameter passes. If there is a relay set up
as a beacon light it will be managed
following the mode set in the FLASH MODE
MOV parameter.
Motor speed and power are adjusted in
different phases:
wAcceleration ramp: The acceleration
ramp is performed at maximum power
and goes from stopped motor to the
transit speed in the time specied by the
OP ACCEL RAMP parameter for opening
and CL ACCEL RAMP for closing. The
shorter the ramp time the more abrupt
the speed change is, and the longer the
r a m p, s of t e r t h e s pe e d c h a ng e .
wTransit: In transit the motor spins with
the the speed and power adequate to
the maneuver. Most maneuvers are
performed in normal speed OP NORMAL (
VEL CL NORMAL VEL for opening and for
closing) ( for and power OP NORMAL POW
opening and for clo-CL NORMAL POW
sing). Deadman maneuvers before the
rst learning maneuver are performed
in soft stop speed OP SOFT VEL( for
opening and for closing) CL SOFT VEL
and power ( for opening OP SOFT POW
and for closing)CL SOFT POW .
continues on next page -->
9
ESPAÑOLPORTUGÊSDEUTSCH
NEDERLANDS ITALIANO ENGLISHFRANÇAIS

ACTIVATION
The key inputs (marked LL1, LL2 and LL3)
and a radio card installed in the radio
socket can be used to start a manoeuvre
when the control panel is idle.
The functions of the key inputs LL1, LL2
and the radio card are determined by the
selected manoeuvre mode, while input
LL3 can be set separately to operate
differently (using the POLARITY and MODE
parameters within the LL3 menu). It is
possible to disable any of the LL1, LL2 or
LL3 inputs using the LL1 BLOCK, LL2
BLOCK or LL3 BLOCK parameters, so that
any stimulus on these inputs will be
ignored.
Each input is assigned a transit direction
to enable the use of discriminating trafc
lights. LL1, LL2, and the radio card are used
for the incoming transit direction and LL3
for the outgoing transit direction.
NOTE: The radio card operates by default
the same as LL1 unless the parameter
RADIO ALT STOP is activated, in which
case it shall operate in alternate stop
(regardless of the general manoeuvre
mode selected).
MANOEUVRE MODES
The MANOEUVER MODE parameter sets the
functions that the key and radio inputs
perform.
STANDARD
In STANDARD mode, Ll1 will give an open
command if the door is closed and a close
command if the door is open and at rest.
LL2 will work in the same way except that
the opening will be in pedestrian mode.
None of the keys perform any function
while the door is moving unless the
parameter INVER ON KEY is activated, in
which case during closing LL1 and LL2 will
cause a soft manoeuvre inversion to be
performed. In this mode, AUTO CLOSING is
activated by default, although in OPTIONS,
by accessing this command, it can be
deactivated by selecting NO.
MANOEUVER
OPEN/CLOSE
The OPEN/CLOSE mode uses LL1 as the
opening command and LL2 as the closing
command. When the door is in motion the
opposite direction input will cause a
smooth reversal of manoeuvre (without
passing through stop). In this mode, AUTO
CLOSE is disabled by default, although in
OPTIONS, by accessing this command it
can be activated by selecting YES.
ALT. STOP
The ALT STOP mode works in the same
way as the STANDARD mode, except that if
LL1 or LL2 is used while the door is moving,
it stops. The next press will make the door
continue the manoeuvre in the opposite
direction to the previous one. In this mode,
the AUTO CLOSE is disabled by default,
although in OPTIONS, by accessing this
command, it can be activated by selecting
YES.
DEADMAN
The DEADMAN mode only allows the door
to move while the LL1 or radio input is
active (opening) or the LL2 input is active
(closing). The manoeuvre is interrupted
when the input in use is deactivated. In this
mode, th e saf et ie s onl y pause the
manoeuvre.
SEMI. DEADMAN
The SEMI DEADMAN mode performs full
opening in the normal way when using LL1
or LL2, but requires using either of the
inputs in deadman mode to close.
AUXILIARY DEADMAN
The parameter AUX DEAD MAN parameter
allows the panel to temporarily operate in
deadman mode when one of the safeties
fails the test, allowing the door to be
opened in case of problems. When this
option is activated, in the event of a failure,
simply press and hold the usual key or
radio input for a few seconds.
8
PHASES
SAFETY TESTS
The safety tests phase is performed in the
beginning of every maneuver before
moving the gate. The controller rst
checks for obstructed safeties (corres-
ponding led off in the board) that are
relevant to the maneuver. If there is any
obstructed safety it waits for them to
enter idle state and will show a message in
the display to this effect. Then the board
checks the resistive values of safety edges
and performs a test procedure on light
barriers removing power from the trans-
mitter to check the system is in order.
UNLOCKING
The unlocking phase performs many
different functions simultaneosly before
starting the movement phase:
wActivates the garage light relay during
the time interval specied by the GARG
LIGHT T parameter. This paremeter can
be set to any time from 1 sec. to 240
sec., thus saving the need to use an
external timer.
wActivates the electrolock relay if any of
the relays is congured as such and the
ELECTROLOCK parameter is set with a
time interval.
wWhen the electrolock is activated and
the maneuver will open the gate the
controler performs a reversing stroke in
soft stop speed ( OP SOFT VEL parame-
ter) with normal power (OP NORMAL POW
parameter) for a duration specied by
the REVERS. STROKE parameter.
wPerforms preashing through a relay
congured for light beacon during the
time interval specied by the PREFLASH
OP T parameter for opening and the
PREFLASH CL T for closing. Preashing
is managed following the mode speci-
ed by the PREFLASH MODE parameter. If
the FLASHING SEM. parameter is set
preashing will be performed through a
relay congured as red semaphore
light.
MANOEUVER
MOVEMENT
The movement phase comprises the
actual gate movement and management
of the safety devices. First the red semap-
hore light is activated if any relay is set as
such and the maneuver counters are
incremented (once per gate movement
direction). The electrolock, if activated in
the previous phase, is held active until the
time specied by the ELECTROLOCK
parameter passes. If there is a relay set up
as a beacon light it will be managed
following the mode set in the FLASH MODE
MOV parameter.
Motor speed and power are adjusted in
different phases:
wAcceleration ramp: The acceleration
ramp is performed at maximum power
and goes from stopped motor to the
transit speed in the time specied by the
OP ACCEL RAMP parameter for opening
and CL ACCEL RAMP for closing. The
shorter the ramp time the more abrupt
the speed change is, and the longer the
r a m p, s of t e r t h e s pe e d c h a ng e .
wTransit: In transit the motor spins with
the the speed and power adequate to
the maneuver. Most maneuvers are
performed in normal speed OP NORMAL (
VEL CL NORMAL VEL for opening and for
closing) ( for and power OP NORMAL POW
opening and for clo-CL NORMAL POW
sing). Deadman maneuvers before the
rst learning maneuver are performed
in soft stop speed OP SOFT VEL( for
opening and for closing) CL SOFT VEL
and power ( for opening OP SOFT POW
and for closing)CL SOFT POW .
continues on next page -->
9
ESPAÑOLPORTUGÊSDEUTSCH
NEDERLANDS ITALIANO ENGLISHFRANÇAIS

wSoft stop ramp: If the SOFT STOP
parameter is set, when the gate reaches
the position set as a percentage of the
gate limits (OP SOFT STOP for opening
or CL SOFT STOP for closing), the
controller starts the soft stop phase.
The soft stop ramp regulates the speed
and power from the ones used in transit
to the the ones set for the soft stop
phase (OP SOFT VEL and OP SOFT POW
for opening or CL SOFT VEL and CL SOFT
POW for closing) and lasts the time set in
the OP SOFT RAMP parameter for ope-
ning or the CL SOFT RAMP parameter for
closing.
wSoft stop: if the SOFT STOP parameter is
set the motor will spin using the soft
stop speed and power (OP SOFT VEL
and OP SOFT POW for opening or CL SOFT
VEL and CL SOFT POW for closing).
wDecceleration before limit: if the DCEL
OP MARGIN parameter when closing or
the DCEL CL MARGIN when closing are
greater than zero the controller will
progressively deccelerate when the
remaining gate movement reaches the
margin specied by the corresponding
parameter, reaching the end with the
speed specied by the DCEL OP VEL
parameter when opening or the DCEL
CL VEL parameter when closing.
wDecceleration ramp: when the gate
reaches its end position (PEDEST LIM.
parameter for pedestrian opening
maneuvers) or the maneuver time runs
out a nal decceleration ramp to stop
the motor is performed. The ramp lasts
the time specied by the OP DECC RAMP
parameter when opening or the CL
DECC RAMP parameter whenclosing. If
the motor must be stopped immedia-
tely the ramp time should be set to zero
seconds.
The movement phase nishes either
because the maneuver time runs out, a
limit switch has been reached, the pro-
grammed encoder position has been
reached (VF1EA, ABS ENC I POS and ABS
ENC F POS parameters) or, in pedestrian
mode, the gate reaches the congured
position (PEDEST LIM parameter). The
maneuver time is set in the OPEN TIME
parameter for opening and CLOSE TIME
MANOEUVER
parameter for closing. When the maneu-
ver is inverted the controller calculates the
needed time using the current gate
position as reference, If the gate does not
reach its end point in this situation it is
possible to apply some extra time (EXTRA
TIME parameter).
Safeties can alter maneuvers (inversion,
safety stop...). Ending a maneuver becau-
se of a safety is considered a cancellation
and can be followed automatically by
another maneuver (inversions).
When the opening movement phase ends
succesfully, the red semaphore light is
deactivated and the green semaphore
light is activated.
LOCKING
The locking phase when closing, if an
electrolock is installed, performs a nal
stroke in soft stop speed (CL SOFT VEL)
and in normal power (CL NORMAL POW
parameter) lasting the time specied by
the FINAL STROKE parameter.
PAUSE
The pause phase is performed after
opening if the AUTO CLOSE parameter is set.
This phase lasts the time specied by the
AUTO CLOSE T parameter for normal
maneuvers, the AUTO C PED T parameter
for pedestrian maneuvers and the FAST
PHOTO CLOSE parameter for light barrier
inversions. If a light beacon relay is con-
gured it will follow the conguration set in
the FLASH MODE PAUS parameter. When the
pause ends a new closing maneuver starts.
If the OPTIONAL AUTO parameter is set, any
key switch activation will terminate the
pause phase. If OPTIONAL AUTO is not set
but KEY RES. AUTO is set, key switch inputs
will restart the pause timer, also when
held.
If the CLOSE ON BEAM parameter is set with
an specic time, a light barrier obstruction
during pause will reset the timer to the
value set in the parameter.
10
MANOEUVER
SAFETIES
The controller supports many safety
devices that can affect the maneuver:
STOP, light barriers, safety edges, current
sensor and encoder.
STOP
The STOP input supports a normally
closed contact for emergency stop. In
case no device is installed the terminals
should be bridged (led off) for the contro-
ller to work.
Opening the stop contact will make the
motor stop immediately and will cancel
the current maneuver no matter in which
phase it is currently in.
LIGHT BARRIERS
The controller has two separate inputs for
light barrier use that can be independtly
enabled and congured. These inputs
work as normally closed contacts, so in
case of more than two light barriers they
should be connected in series. If more than
one light barrier share the same board
input the same conguration will apply to
all of them.
To enable a light barrier input rst the
input needs to be enabled using the BEAM
1 parameter or the BEAM 2 parameter. Once
the input is enabled it is possible to con-
gure the safety test and the behavior both
when opening and when closing.
To activate the safety test the TEST BEAM 1
parameter or the TEST BEAM 2 parameter
must be used. Once set, the default testing
strategy is to test both before opening
and closing. It is possible to adjust this
strategy using the TEST BEAM 1 OP, TEST
BEAM 1 CL, TEST BEAM 2 OP and TEST BEAM
2 CL parameters.
To perform the safety test it is neccesary
to interrupt the power line to the periphe-
ral or, in some cases, provide a test impul-
se. For maximum exibility the controller
provides two ways of performing the test:
terminal 18 can be used as DC negative
supply for testable devices or one of the
dry relay contacts can be used using the
TEST function.
Below all possible values for BEAM 1 OPEN,
BEAM 1 CLOSE, BEAM 2 OPEN and BEAM 2
CLOSE are detailed.
NO
The light barrier is ignored.
PAUSE
The light barrier pauses the maneuver while obstructed. When unobstruc-
ted, the controller waits for three seconds and resumes the maneuver.
INVERT
The light barrier inverts the maneuver direction.
STOP
The light barrier stops and cancels the maneuver.
SHORT INV.
The light barrier inverts the maneuver direction during the time set in the
SHORT INV. T. parameter and then stops and cancels the maneuver.
DELAYED INV.
When the light barrier is unobstructed the gatye stops, waits during the
time set in the DEL. INV. T. parameter and then inverts the maneuver.
11
ESPAÑOLPORTUGÊSDEUTSCH
NEDERLANDS ITALIANO ENGLISHFRANÇAIS

wSoft stop ramp: If the SOFT STOP
parameter is set, when the gate reaches
the position set as a percentage of the
gate limits (OP SOFT STOP for opening
or CL SOFT STOP for closing), the
controller starts the soft stop phase.
The soft stop ramp regulates the speed
and power from the ones used in transit
to the the ones set for the soft stop
phase (OP SOFT VEL and OP SOFT POW
for opening or CL SOFT VEL and CL SOFT
POW for closing) and lasts the time set in
the OP SOFT RAMP parameter for ope-
ning or the CL SOFT RAMP parameter for
closing.
wSoft stop: if the SOFT STOP parameter is
set the motor will spin using the soft
stop speed and power (OP SOFT VEL
and OP SOFT POW for opening or CL SOFT
VEL and CL SOFT POW for closing).
wDecceleration before limit: if the DCEL
OP MARGIN parameter when closing or
the DCEL CL MARGIN when closing are
greater than zero the controller will
progressively deccelerate when the
remaining gate movement reaches the
margin specied by the corresponding
parameter, reaching the end with the
speed specied by the DCEL OP VEL
parameter when opening or the DCEL
CL VEL parameter when closing.
wDecceleration ramp: when the gate
reaches its end position (PEDEST LIM.
parameter for pedestrian opening
maneuvers) or the maneuver time runs
out a nal decceleration ramp to stop
the motor is performed. The ramp lasts
the time specied by the OP DECC RAMP
parameter when opening or the CL
DECC RAMP parameter whenclosing. If
the motor must be stopped immedia-
tely the ramp time should be set to zero
seconds.
The movement phase nishes either
because the maneuver time runs out, a
limit switch has been reached, the pro-
grammed encoder position has been
reached (VF1EA, ABS ENC I POS and ABS
ENC F POS parameters) or, in pedestrian
mode, the gate reaches the congured
position (PEDEST LIM parameter). The
maneuver time is set in the OPEN TIME
parameter for opening and CLOSE TIME
MANOEUVER
parameter for closing. When the maneu-
ver is inverted the controller calculates the
needed time using the current gate
position as reference, If the gate does not
reach its end point in this situation it is
possible to apply some extra time (EXTRA
TIME parameter).
Safeties can alter maneuvers (inversion,
safety stop...). Ending a maneuver becau-
se of a safety is considered a cancellation
and can be followed automatically by
another maneuver (inversions).
When the opening movement phase ends
succesfully, the red semaphore light is
deactivated and the green semaphore
light is activated.
LOCKING
The locking phase when closing, if an
electrolock is installed, performs a nal
stroke in soft stop speed (CL SOFT VEL)
and in normal power (CL NORMAL POW
parameter) lasting the time specied by
the FINAL STROKE parameter.
PAUSE
The pause phase is performed after
opening if the AUTO CLOSE parameter is set.
This phase lasts the time specied by the
AUTO CLOSE T parameter for normal
maneuvers, the AUTO C PED T parameter
for pedestrian maneuvers and the FAST
PHOTO CLOSE parameter for light barrier
inversions. If a light beacon relay is con-
gured it will follow the conguration set in
the FLASH MODE PAUS parameter. When the
pause ends a new closing maneuver starts.
If the OPTIONAL AUTO parameter is set, any
key switch activation will terminate the
pause phase. If OPTIONAL AUTO is not set
but KEY RES. AUTO is set, key switch inputs
will restart the pause timer, also when
held.
If the CLOSE ON BEAM parameter is set with
an specic time, a light barrier obstruction
during pause will reset the timer to the
value set in the parameter.
10
MANOEUVER
SAFETIES
The controller supports many safety
devices that can affect the maneuver:
STOP, light barriers, safety edges, current
sensor and encoder.
STOP
The STOP input supports a normally
closed contact for emergency stop. In
case no device is installed the terminals
should be bridged (led off) for the contro-
ller to work.
Opening the stop contact will make the
motor stop immediately and will cancel
the current maneuver no matter in which
phase it is currently in.
LIGHT BARRIERS
The controller has two separate inputs for
light barrier use that can be independtly
enabled and congured. These inputs
work as normally closed contacts, so in
case of more than two light barriers they
should be connected in series. If more than
one light barrier share the same board
input the same conguration will apply to
all of them.
To enable a light barrier input rst the
input needs to be enabled using the BEAM
1 parameter or the BEAM 2 parameter. Once
the input is enabled it is possible to con-
gure the safety test and the behavior both
when opening and when closing.
To activate the safety test the TEST BEAM 1
parameter or the TEST BEAM 2 parameter
must be used. Once set, the default testing
strategy is to test both before opening
and closing. It is possible to adjust this
strategy using the TEST BEAM 1 OP, TEST
BEAM 1 CL, TEST BEAM 2 OP and TEST BEAM
2 CL parameters.
To perform the safety test it is neccesary
to interrupt the power line to the periphe-
ral or, in some cases, provide a test impul-
se. For maximum exibility the controller
provides two ways of performing the test:
terminal 18 can be used as DC negative
supply for testable devices or one of the
dry relay contacts can be used using the
TEST function.
Below all possible values for BEAM 1 OPEN,
BEAM 1 CLOSE, BEAM 2 OPEN and BEAM 2
CLOSE are detailed.
NO
The light barrier is ignored.
PAUSE
The light barrier pauses the maneuver while obstructed. When unobstruc-
ted, the controller waits for three seconds and resumes the maneuver.
INVERT
The light barrier inverts the maneuver direction.
STOP
The light barrier stops and cancels the maneuver.
SHORT INV.
The light barrier inverts the maneuver direction during the time set in the
SHORT INV. T. parameter and then stops and cancels the maneuver.
DELAYED INV.
When the light barrier is unobstructed the gatye stops, waits during the
time set in the DEL. INV. T. parameter and then inverts the maneuver.
11
ESPAÑOLPORTUGÊSDEUTSCH
NEDERLANDS ITALIANO ENGLISHFRANÇAIS

MANOEUVER
ENCODER
When the encoder is enabled it can be
used as a safety measure too. The contro-
ller monitors the time lapse between
position changes and implements two
protections::
wObstacle detection: If the controller
detects an abrupt rise in time between
position changes the obstacle detec-
tion safety activates. This safety only
works if the M1 ENC SENS. parameter is 1
or greater; this parameter set the
sensitivity to rises in current draw,
being 1 the lowest and 9 the highest. If
this safety is activated the controller
will log an error for future reference..
NOTE: This safety does not work during
speed ramps.
wLocking detection: If the controller tries
to make the motor spin but no signica-
tive position change is detected the
maneuver is cancelled to avoid damage
and an error is logged for future refe-
rence.
MOTOR
The BOX L VF1D allows independent
control of speed and power for a 230VAC
three-phase motor (delta wiring). Speed
can be set between 10Hz (Hertz) and
100Hz (OP NORMAL VEL, CL NORMAL VEL, OP
SOFT VEL and CL SOFT VEL parameters)
and power can be set from 30% to 100%
(OP NORMAL POW, CL NORMAL POW, OP SOFT
POW and CL SOFT POW).
It is important to consider that three-
phase motors are usually designed with
50Hz and 100% power in mind. Using
these values is equivalent to powering the
motor with direct three-phase power.
Frequency modication, specially close to
the limits, can make the motor spin badly,
cause higher power drain and general
malfunction. Also, reducing the delivered
power can make the motor spin slower
than intended or general malfunction. It is
recommended to test thoroughly the
selected parameter values.
The controller has two complementary
brake systems: electrical brake and
electromechanical brake. The electrical
brake is performed by applying DC power
in the motor phases and practicaly locks
the motor in place, eliminating inertia and
relieving the electromechanical brake
from unneeded friction. The electrome-
chanical brake is activated through one of
the output relays and primarily serves the
function of locking the motor in place
when the gate is idle.
The electrical brake strength can be
regulated using the BRAKE POW OP and
BRAKE POW CL parameters. This parame-
ters accepet any value from 0 to 4, 0 being
electrical brake disabled and 4 being the
highest power setting. NOTE: It is not
recommended to change the brake
strength if not actually needed, specially
setting level 4 as it can damage the motor.
13
SAFETY EDGES
The panel has two inputs for safety edges
that can be enabled and congured
independently. These inputs work by
monitoring the connected resistive value
and support 8K2 or 4K1 resistive edges
and contact edges, either normally open
or normally closed. If you want to connect
several strips to the same input, it is
necessary to connect them in series if they
are normally closed contact, and in parallel
if they are normally open contact or
resistive. In the case of resistive strips, the
panel only supports two connected in
parallel on the same input, conguring the
MANOEUVER
input for 4K1.
In order to use a band input, it is necessary
to congure the input by modifying
parameter EDGE 1 or parameter EDGE 2.
The possible options for the parameters
EDGE 1 APER, EDGE 1 CLOSE, EDGE 2
APER and EDGE 2 CLOSE are detailed
below, with the selected action being
applied when the safety is activated in the
chosen direction.
NO
The safety edge is ignored.
INVERT
The safety edge inverts the maneuver.
STOP
The safety edge stops and cancels the maneuver.
SHORT INV.
The safety edge inverts the maneuver direction during the time set in the
SHORT INV. T. parameter and then stops and cancels the maneuver.
CURRENT SENSOR
The BOX L VF1D controller
monitors the current draw on
each motor phase in real time so
it can be displayed in the LCD
screen and to implement three
different protections :
wObstacle detection: When the contro-
ller detects an abrupt rise in motor
current draw or detects that it is higher
than a congurable limit (M1 OBST.
LIM) during a short span of time the
obstacle detection safety activates.
This safety only works if the M1 SENSIB.
parameter is 1 or greater; this parame-
ter set the sensitivity to rises in current
draw, being 1 the lowest and 9 the
highest. If this safety is activated the
controller will log an error for future
reference. NOTE: This safety does not
work during speed ramps and performs
best when the motor spins with redu-
ced power.
wOvercurrent protection: If the contro-
ller detects that the motor current draw
rises above a limit set in the OC LIMIT
parameter for a brief span of time the
maneuver will be cancelled immedia-
tely and an error will be logged for
future reference.
wShortcircuit protection: If the controller
detects that the motor current draw
rises above an internal limit close to the
maximum supported by the board the
maneuver is cancelled immediately and
an error is logged for future reference.
OBSTACLE DETECTION
The controller has many means to detect
an obstacle. The behaviour of the gate
when one is encountered is set by the
PUSH SEC. OPEN and PUSH SEC. CLOSE
parameters in a similar fashion to safety
edges (see table above).
12
ESPAÑOLPORTUGÊSDEUTSCH
NEDERLANDS ITALIANO ENGLISHFRANÇAIS

MANOEUVER
ENCODER
When the encoder is enabled it can be
used as a safety measure too. The contro-
ller monitors the time lapse between
position changes and implements two
protections::
wObstacle detection: If the controller
detects an abrupt rise in time between
position changes the obstacle detec-
tion safety activates. This safety only
works if the M1 ENC SENS. parameter is 1
or greater; this parameter set the
sensitivity to rises in current draw,
being 1 the lowest and 9 the highest. If
this safety is activated the controller
will log an error for future reference..
NOTE: This safety does not work during
speed ramps.
wLocking detection: If the controller tries
to make the motor spin but no signica-
tive position change is detected the
maneuver is cancelled to avoid damage
and an error is logged for future refe-
rence.
MOTOR
The BOX L VF1D allows independent
control of speed and power for a 230VAC
three-phase motor (delta wiring). Speed
can be set between 10Hz (Hertz) and
100Hz (OP NORMAL VEL, CL NORMAL VEL, OP
SOFT VEL and CL SOFT VEL parameters)
and power can be set from 30% to 100%
(OP NORMAL POW, CL NORMAL POW, OP SOFT
POW and CL SOFT POW).
It is important to consider that three-
phase motors are usually designed with
50Hz and 100% power in mind. Using
these values is equivalent to powering the
motor with direct three-phase power.
Frequency modication, specially close to
the limits, can make the motor spin badly,
cause higher power drain and general
malfunction. Also, reducing the delivered
power can make the motor spin slower
than intended or general malfunction. It is
recommended to test thoroughly the
selected parameter values.
The controller has two complementary
brake systems: electrical brake and
electromechanical brake. The electrical
brake is performed by applying DC power
in the motor phases and practicaly locks
the motor in place, eliminating inertia and
relieving the electromechanical brake
from unneeded friction. The electrome-
chanical brake is activated through one of
the output relays and primarily serves the
function of locking the motor in place
when the gate is idle.
The electrical brake strength can be
regulated using the BRAKE POW OP and
BRAKE POW CL parameters. This parame-
ters accepet any value from 0 to 4, 0 being
electrical brake disabled and 4 being the
highest power setting. NOTE: It is not
recommended to change the brake
strength if not actually needed, specially
setting level 4 as it can damage the motor.
13
SAFETY EDGES
The panel has two inputs for safety edges
that can be enabled and congured
independently. These inputs work by
monitoring the connected resistive value
and support 8K2 or 4K1 resistive edges
and contact edges, either normally open
or normally closed. If you want to connect
several strips to the same input, it is
necessary to connect them in series if they
are normally closed contact, and in parallel
if they are normally open contact or
resistive. In the case of resistive strips, the
panel only supports two connected in
parallel on the same input, conguring the
MANOEUVER
input for 4K1.
In order to use a band input, it is necessary
to congure the input by modifying
parameter EDGE 1 or parameter EDGE 2.
The possible options for the parameters
EDGE 1 APER, EDGE 1 CLOSE, EDGE 2
APER and EDGE 2 CLOSE are detailed
below, with the selected action being
applied when the safety is activated in the
chosen direction.
NO
The safety edge is ignored.
INVERT
The safety edge inverts the maneuver.
STOP
The safety edge stops and cancels the maneuver.
SHORT INV.
The safety edge inverts the maneuver direction during the time set in the
SHORT INV. T. parameter and then stops and cancels the maneuver.
CURRENT SENSOR
The BOX L VF1D controller
monitors the current draw on
each motor phase in real time so
it can be displayed in the LCD
screen and to implement three
different protections :
wObstacle detection: When the contro-
ller detects an abrupt rise in motor
current draw or detects that it is higher
than a congurable limit (M1 OBST.
LIM) during a short span of time the
obstacle detection safety activates.
This safety only works if the M1 SENSIB.
parameter is 1 or greater; this parame-
ter set the sensitivity to rises in current
draw, being 1 the lowest and 9 the
highest. If this safety is activated the
controller will log an error for future
reference. NOTE: This safety does not
work during speed ramps and performs
best when the motor spins with redu-
ced power.
wOvercurrent protection: If the contro-
ller detects that the motor current draw
rises above a limit set in the OC LIMIT
parameter for a brief span of time the
maneuver will be cancelled immedia-
tely and an error will be logged for
future reference.
wShortcircuit protection: If the controller
detects that the motor current draw
rises above an internal limit close to the
maximum supported by the board the
maneuver is cancelled immediately and
an error is logged for future reference.
OBSTACLE DETECTION
The controller has many means to detect
an obstacle. The behaviour of the gate
when one is encountered is set by the
PUSH SEC. OPEN and PUSH SEC. CLOSE
parameters in a similar fashion to safety
edges (see table above).
12
ESPAÑOLPORTUGÊSDEUTSCH
NEDERLANDS ITALIANO ENGLISHFRANÇAIS

14
ELECTRICAL WIRING
DIAGRAM
LIGHT BARRIER POWER
DIAGRAM
RX
-
+
Fig.2
SMINN
BOX L VF1D
See page 25
for correct
shielding
of the receiver
The negative of the light barrier transmitter must be connected to pin 18 of the terminal block
to facilitate the light barrier test function.
1
230VAC phase
2
230VAC neutral
3
Earth terminal
4
U motor phase
5
V motor phase
6
W motor phase
7
Motor earth terminal
8
RL1 output relay
9
10
RL2 output relay
11
12
RL3 output relay
13
14
24VAC 12W power output
15
16
Negative
15VDC power output for
light barriers and others
17
Positive
18
Power negative for light barrier
transmitter with autotest function
19
Input electrical common
20
Safety edge 1- R8K2 / NC
21
Safety edge 2 - R8K2 / NC
22
Light barrier 1 NC
23
Light barrier 2 NC
24
Opening limit switch
25
Closing limit switch
26
Input electrical common
27
Encoder power negative
28
ENC1 encoder input
29
ENC2 encoder input
30
Encoder power positive
31
STOP (NO contact)
32
33
LL1 Input
34
LL2 Input
35
LL3 Input
36
Input common
ACCESORIES
AND PERIPHERALS
Radio card
Transmitter-receiver light barrier set
Beacon light and light barrier stand
15
ESPAÑOLPORTUGÊSDEUTSCH
NEDERLANDS ITALIANO ENGLISHFRANÇAIS

14
ELECTRICAL WIRING
DIAGRAM
LIGHT BARRIER POWER
DIAGRAM
RX
-
+
Fig.2
SMINN
BOX L VF1D
See page 25
for correct
shielding
of the receiver
The negative of the light barrier transmitter must be connected to pin 18 of the terminal block
to facilitate the light barrier test function.
1
230VAC phase
2
230VAC neutral
3
Earth terminal
4
U motor phase
5
V motor phase
6
W motor phase
7
Motor earth terminal
8
RL1 output relay
9
10
RL2 output relay
11
12
RL3 output relay
13
14
24VAC 12W power output
15
16
Negative
15VDC power output for
light barriers and others
17
Positive
18
Power negative for light barrier
transmitter with autotest function
19
Input electrical common
20
Safety edge 1- R8K2 / NC
21
Safety edge 2 - R8K2 / NC
22
Light barrier 1 NC
23
Light barrier 2 NC
24
Opening limit switch
25
Closing limit switch
26
Input electrical common
27
Encoder power negative
28
ENC1 encoder input
29
ENC2 encoder input
30
Encoder power positive
31
STOP (NO contact)
32
33
LL1 Input
34
LL2 Input
35
LL3 Input
36
Input common
ACCESORIES
AND PERIPHERALS
Radio card
Transmitter-receiver light barrier set
Beacon light and light barrier stand
15
ESPAÑOLPORTUGÊSDEUTSCH
NEDERLANDS ITALIANO ENGLISHFRANÇAIS

OUTPUTS
The controller has three congurable
outputs that support many different
functions in order to adapt to different
installations, Each output has its own
submenu (called RL1, RL2 y RL3) with two
associated parameters, POLARITY and
RELAY MODE.
POLARITY: Allows conguring the output
polarity between NO CONTACT (normally
open) and NC CONTACT (normally closed).
It is important to consider that the physical
relay contact available in the terminal strip
is normally open, so if the board is unpo-
wered the relay will always open the
contact no matter the conguration..
RELAY MODE: Allows selecting the function
each relay will perform.
RELAY – GARAGE LIGHT
The GARAGE LIGHT mode uses the relay to
deliver power or a signal to a device each
time a maneuver begins during the time
span specied by GARG LIGHT T parame-
ter.
RELAY – FLASH LAMP
The FLASH LAMP mode uses the relay to
deliver power to a beacon light during the
unlocking phase (preashing), the
movement phase and during pause. It is
possible to modify the behavior of the
output in each phase (off, intermitent or
on) using the PREFLASH MODE, FLASH MODE
MOV and FLASH MODE PAUS parameters.
RELAY - BRAKE
The BRAKE mode uses the relay to unlock
or lock the electromechanical brake of the
motor. The brake is released just before
spinning the motor and is lock immedia-
tely after stopping it.
RELAY - MAINTENANCE
The MAINTENANCE mode uses a relay to
signal or power an external device when
the maneuver partial counter rises above
the limit set in the MAINT. LIM. parameter.
MANOEUVER
RELAY - SAFETY TEST
The SEC. TEST mode performs a safety
test on devices that are powered exter-
nally or that need a test signal. The contro-
ller will activate the relay to perform the
test and deactivate it when the safety
switches state.
RELAY – ELECTROLOCK
The ELECTROLOCK mode activates an
electrolock before opening the gate.
Setting this mode for a relay enables other
parameters related to the electrolock
function (ELECTROLOCK, REVERS. STROKE,
FINAL STROKE).
RELAY – RED SEMAPH
The RED LIGHT IN and RED LIGHT OUT
modes use a relay to activate a red semap-
hore light for a given transit direction. If
the FLASHING SEM. parameter is set
preashing will be performed in this relay
too.
RELAY – GREEN SEMAPH
The GREEN LIGHT IN and GREEN LIG. OUT
modes use a relay to activate a green
semaphore light for a given transit direc-
tion.
RELAY – GATE STATE
The GATE CLOSED mode activates the relay
while the gate is completely closed.
The GATE OPENED mode activates the
relay while the gate is completely open.
The GATE OPENING mode activates the
relay while the gate is opening.
The GATE CLOSING mode activates the
relay while the gate is closing.
RELAY – IN PAUSE
The IN PAUSE mode activates the relay
while the maneuver is in the pause phase.
16
DISPLAY
The LCD display shows during maneuver
many useful runtime values easing mainte-
nance and initial installation.
MANOEUVER
ENCODER (VF1D)
It is possible to use an incremental enco-
der (ENCODER parameter) to enhance the
precision of the gate position manage-
ment and have some additional safety
measures. The controller supports both
one channel encoders (1 CHANNEL) and
two channel encoders (2 CHANNELS).
NOTE: Two channel encoders are more
precise since they indicate rotation
direction and double the quantity of
pulses..
If a two channel encoder is used the
learning maneuver automatically establis-
hes the correct encoder polarity.
For more information on safety related
encoder settigns check page 13.
ENCODER (VF1EA)
It is possible to use an absolute encoder
via RS485 bus (ENCODER parameter) to
control the gate position. The controller
supports the most widely available motors
with included absolute encoder in Europe.
The learning maneuver automatically
detects the correct encoder polarity.
Before the actual learning maneuver the
instaler is prompted to move the gate to
the opening and closing positions to learn
their encoder values. These positions can
be adjusted after the learning maneuver
using the ABS ENC I POS and ABS ENC F POS
parameters.
For more information on safety related
encoder settigns check page 13.
1.82A 89 2.00A
OPEN 22C I 318V
1 2 4
5 6 7
1. Current phase
2. Controller temperature
3. Input inhibition indication
4. Bus voltage
5. Real-time current draw
6. Percentage-based gate position /
Remaining pause time.
7. Maneuver maximum current draw.
When idle, the controller might show four
E in the display borders to indicate there
are one or more logged errors. When
entering the menu the controller will show
one by one the logged error, waiting for
ENTER to be pressed n between. NOTE:
The controller will still work normally even
if there are logged errors.
E BXL-VF1D E
E SMINN E
3
17
ESPAÑOLPORTUGÊSDEUTSCH
NEDERLANDS ITALIANO ENGLISHFRANÇAIS

OUTPUTS
The controller has three congurable
outputs that support many different
functions in order to adapt to different
installations, Each output has its own
submenu (called RL1, RL2 y RL3) with two
associated parameters, POLARITY and
RELAY MODE.
POLARITY: Allows conguring the output
polarity between NO CONTACT (normally
open) and NC CONTACT (normally closed).
It is important to consider that the physical
relay contact available in the terminal strip
is normally open, so if the board is unpo-
wered the relay will always open the
contact no matter the conguration..
RELAY MODE: Allows selecting the function
each relay will perform.
RELAY – GARAGE LIGHT
The GARAGE LIGHT mode uses the relay to
deliver power or a signal to a device each
time a maneuver begins during the time
span specied by GARG LIGHT T parame-
ter.
RELAY – FLASH LAMP
The FLASH LAMP mode uses the relay to
deliver power to a beacon light during the
unlocking phase (preashing), the
movement phase and during pause. It is
possible to modify the behavior of the
output in each phase (off, intermitent or
on) using the PREFLASH MODE, FLASH MODE
MOV and FLASH MODE PAUS parameters.
RELAY - BRAKE
The BRAKE mode uses the relay to unlock
or lock the electromechanical brake of the
motor. The brake is released just before
spinning the motor and is lock immedia-
tely after stopping it.
RELAY - MAINTENANCE
The MAINTENANCE mode uses a relay to
signal or power an external device when
the maneuver partial counter rises above
the limit set in the MAINT. LIM. parameter.
MANOEUVER
RELAY - SAFETY TEST
The SEC. TEST mode performs a safety
test on devices that are powered exter-
nally or that need a test signal. The contro-
ller will activate the relay to perform the
test and deactivate it when the safety
switches state.
RELAY – ELECTROLOCK
The ELECTROLOCK mode activates an
electrolock before opening the gate.
Setting this mode for a relay enables other
parameters related to the electrolock
function (ELECTROLOCK, REVERS. STROKE,
FINAL STROKE).
RELAY – RED SEMAPH
The RED LIGHT IN and RED LIGHT OUT
modes use a relay to activate a red semap-
hore light for a given transit direction. If
the FLASHING SEM. parameter is set
preashing will be performed in this relay
too.
RELAY – GREEN SEMAPH
The GREEN LIGHT IN and GREEN LIG. OUT
modes use a relay to activate a green
semaphore light for a given transit direc-
tion.
RELAY – GATE STATE
The GATE CLOSED mode activates the relay
while the gate is completely closed.
The GATE OPENED mode activates the
relay while the gate is completely open.
The GATE OPENING mode activates the
relay while the gate is opening.
The GATE CLOSING mode activates the
relay while the gate is closing.
RELAY – IN PAUSE
The IN PAUSE mode activates the relay
while the maneuver is in the pause phase.
16
DISPLAY
The LCD display shows during maneuver
many useful runtime values easing mainte-
nance and initial installation.
MANOEUVER
ENCODER (VF1D)
It is possible to use an incremental enco-
der (ENCODER parameter) to enhance the
precision of the gate position manage-
ment and have some additional safety
measures. The controller supports both
one channel encoders (1 CHANNEL) and
two channel encoders (2 CHANNELS).
NOTE: Two channel encoders are more
precise since they indicate rotation
direction and double the quantity of
pulses..
If a two channel encoder is used the
learning maneuver automatically establis-
hes the correct encoder polarity.
For more information on safety related
encoder settigns check page 13.
ENCODER (VF1EA)
It is possible to use an absolute encoder
via RS485 bus (ENCODER parameter) to
control the gate position. The controller
supports the most widely available motors
with included absolute encoder in Europe.
The learning maneuver automatically
detects the correct encoder polarity.
Before the actual learning maneuver the
instaler is prompted to move the gate to
the opening and closing positions to learn
their encoder values. These positions can
be adjusted after the learning maneuver
using the ABS ENC I POS and ABS ENC F POS
parameters.
For more information on safety related
encoder settigns check page 13.
1.82A 89 2.00A
OPEN 22C I 318V
1 2 4
5 6 7
1. Current phase
2. Controller temperature
3. Input inhibition indication
4. Bus voltage
5. Real-time current draw
6. Percentage-based gate position /
Remaining pause time.
7. Maneuver maximum current draw.
When idle, the controller might show four
E in the display borders to indicate there
are one or more logged errors. When
entering the menu the controller will show
one by one the logged error, waiting for
ENTER to be pressed n between. NOTE:
The controller will still work normally even
if there are logged errors.
E BXL-VF1D E
E SMINN E
3
17
ESPAÑOLPORTUGÊSDEUTSCH
NEDERLANDS ITALIANO ENGLISHFRANÇAIS

OPTIONS
AUTOMATIC CLOSING
Enables automatic closing after the pause phase
AUTO CLOSE
YES
8, 10
FAST LIGHT BARRIER CLOSING
The pause after a photocell reversal lasts for the
time set as photocell closure.Only visible if CLOSE
ON BEAM is not NO
FAST PHOTO CLS
NO
10
OPTIONAL AUTO
Terminates the pause phase with an impulse..
Only visible if AUTO CLOSE is enabled
OPTIONAL AUTO
NO
10
AUTO DELAY ON KEY
Restarts the pause phase with each comand
impulse. Only visible if OPTIONAL AUTO is
disabled and AUTO CLOSE is enabled
KEY RES. AUTO
YES
10
INVERT ON KEY
Inverts the maneuver with an impulse. Only
visible in STANDARD mode
INVER TECLA
YES
8
BEAM 1 / 2
Enables control of each of the light barrier inputs.
BEAM 1
BEAM 2
NO
NO
11
TEST BEAM 1 / 2
Enables safety test on the connected light barrier
TEST BEAM 1
TEST BEAM 2
NO
NO
11
TEST BEAM 1 / 2 OPENING/CLOSING
Enables the light barrier safety test before a
maneuver in the corresponding direction.
TEST BEAM1 AP
TEST BEAM1 CR
TEST BEAM2 AP
TEST BEAM2 CR
NO
NO
NO
NO
11
LIGHT BARRIER 1 / 2 MODE
Establishes the behaviour of the light barrier
when opening or closing.
Options.: NO / PAUSE / INVERT / STOP /
SHORT INV. / DELAYED INV.
BEAM 1 OPEN
BEAM 1 CLOSE
BEAM 2 OPEN
BEAM 2 CLOSE
NO
INVERT
NO
INVERT
11
EDGE 1 / 2
Enables control of each safety edge input.
Supports resistive and contact safety edges.
Options: NO / 8K2 / 4K1 / NO CONTACT / NC
CONTACT
EDGE 1
EDGE 2
NO
NO
12
EDGE 1 / 2 MODE OPEN / CLOSE
Establishes the behaviour of the safety edge
when opening or closing.
Options: NO / STOP / SHORT INV. / INVERT
EDGE 1 OPEN
EDGE 1 CLOSE
EDGE 2 OPEN
EDGE 2 CLOSE
NO
INVERT
NO
INVERT
12
OBSTACLE DETECTION OPEN / CLOSE
Establishes the behaviour of the obstacle detec-
tion system when opening or closing.
Options: NO / STOP / SHORT INV. / INVERT
PUSH SEC. OPEN
PUSH SEC.CLOSE
STOP
SHORT INV.
12
SOFT STOP
Enables soft stop
SOFT STOP
YES
7, 10
TEXTO LCD VALOR
POR DEFECTO PAGINAS
18
OPTIONS
CLOSE ON BOOT
After a power failure it causes the door to close if it is not
closed.
CLOSE ON BOOT
NO
PREFLASH MODE
Establishes the behaviour of the light beacon during the
unlocking phase.
Options: NO / INTERMITTENCE / ON
PREFLASH MODE
INTERMITTENCE
9,14
FLASH MODE MOVEMENT
Establishes the behaviour of the light beacon during the
movement phase.
Options: NO / INTERMITTENCE / ON
FLASH MODE MOV
INTERMITTENCE
9,14
FLASH MODE PAUSE
Establishes the behaviour of the light beacon during the
pause phase.
Options: NO / INTERMITTENCE / ON
FLASH MODE PAUS
NO
10,14
FLASHING SEMAPHORE
Uses the red semaphore light for preashing.
FLASHING SEM.
NO
9,14
AUXILIARY DEAD MAN
If the safety test phase detects any failure the mode
swtiches to dead man temporally.
AUX DEAD MAN
NO
8
ENCODER
Enables maneuver control via encoder.
Options: NO / 1 CHANNEL / 2 CHANNELS
Options (VF1EA): NO / KOSTAL / GFA
ENCODER
NO
15
ENCODER POLARITY
Establishes the spin direction interpreted by the encoder.
Options : NORMAL / INVERTED
ENC POLARITY
NORMAL
7
OPENING LIMIT SWITCH (VF1EA)
Enables the opening limit switch input when encoder is
selected.
OPEN LS
NO
CLOSING LIMIT SWITCH (VF1EA)
Enables the closinglimit switch input when encoder is
selected.
CLOSE LS
NO
LL1/LL2/LL3 BLOCK
Blocks any signal in the LL1 / LL2 /LL3 keyswitch inputs.
Only visible with enabled password.
LL1 BLOCK
LL2 BLOCK
LL3 BLOCK
NO
NO
NO
8
RADIO ALTERNATING STOP
Makes the radio card input work in alternating stop mode.
RADIO ALT STOP
NO
8
RL1/RL2/RL3 POLARITY
Establishes the polarity of each relay output.
Options: NO CONTACT / NC CONTACT
RL1/POLARITY
RL2/POLARITY
RL3/POLARITY
NO CONTACT
NO CONTACT
NO CONTACT
14
RL1/RL2/RL3 RELAY MODE
Establishes the function of each relay.
Options: See page 14
RL1/RELAY MODE
RL2/RELAY MODE
RL3/RELAY MODE
GARAGE LIGHT
FLASH LAMP
BRAKE
14
LL3 POLARITY
Establishes the polarity of the LL3 input
Options: NA CONTACT / NC CONTACT
LL3/POLARITY
NO CONTACT
8
LL3 MODE
Establishes the function of the LL3 input.
Options: STANDARD / ALT STOP / SEMI. DEADMAN
LL3/MODE
ALT STOP
8
INVERT MOTOR
Establishes the spin direction of the motor.
INVERT MOTOR
NO
7
TEXTO LCD VALOR
POR DEFECTO PAGINAS
19
ESPAÑOLPORTUGÊSDEUTSCH
NEDERLANDS ITALIANO ENGLISHFRANÇAIS
This manual suits for next models
1
Table of contents
Other Sminn Control Panel manuals
Popular Control Panel manuals by other brands
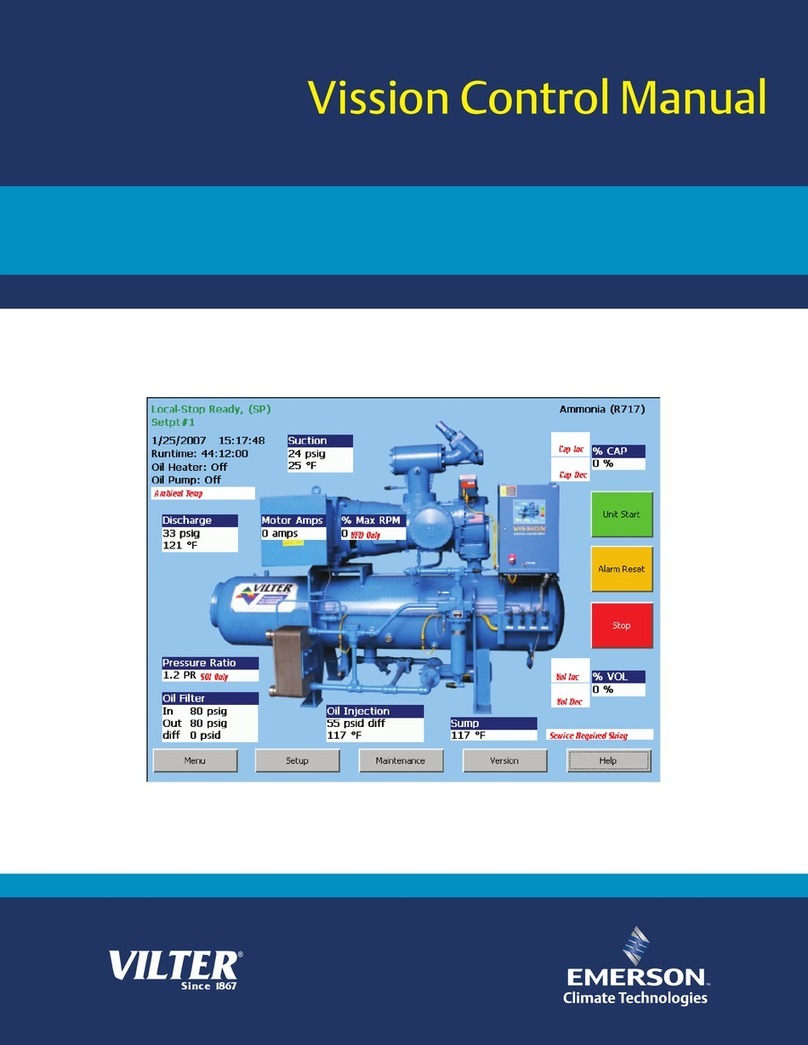
Emerson
Emerson Vission Control manual
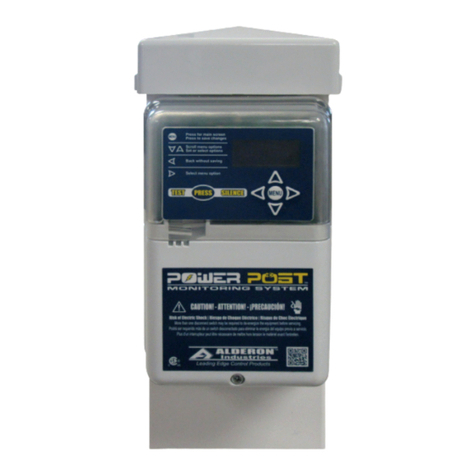
Alderon Industries
Alderon Industries Power Post PPCP Series quick start guide
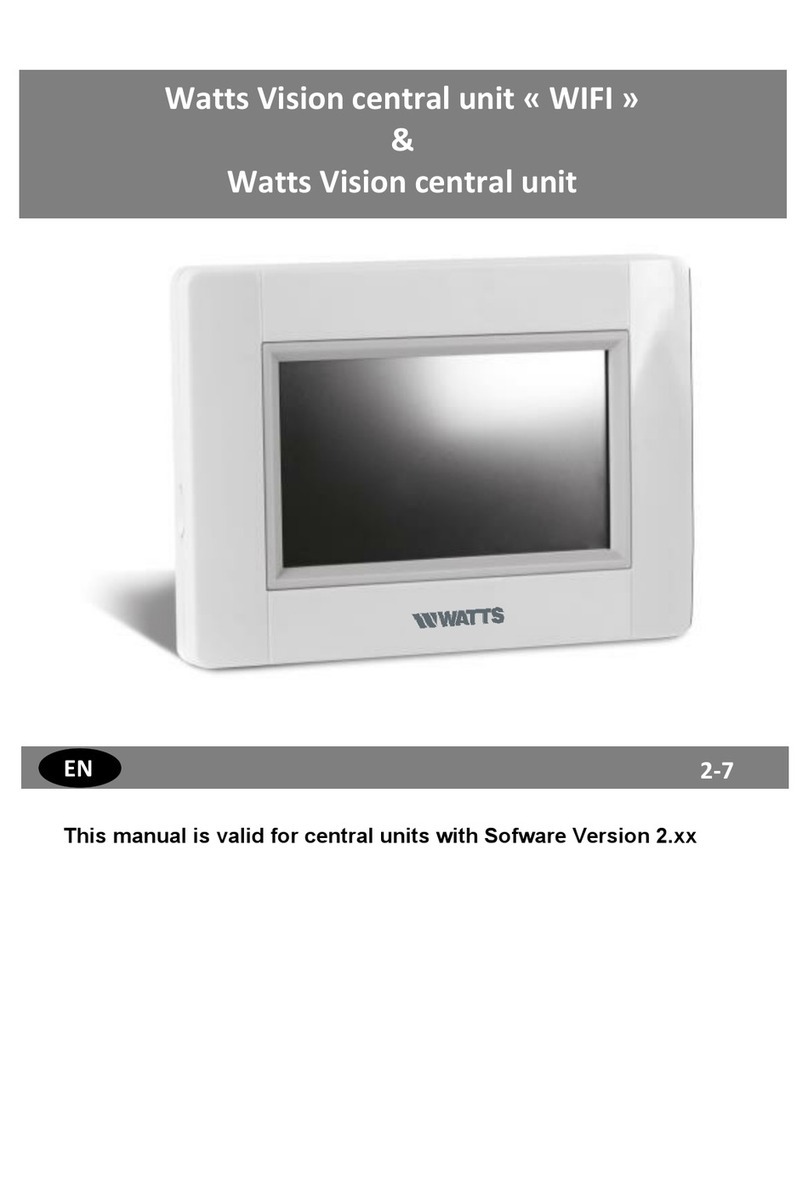
Watts
Watts Vision BT-CT02-RF manual

LynTec
LynTec RPC Sereis quick start guide

Nederman
Nederman HV Control Panel EX Series Original installation and service manual
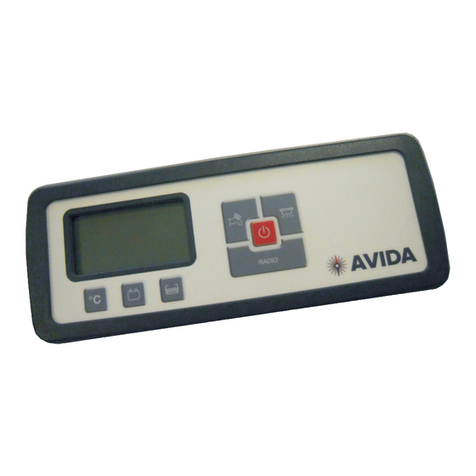
CBE
CBE Avida PC220-KT user manual