Spirax Sarco MkII Guide




















Other Spirax Sarco Control Unit manuals
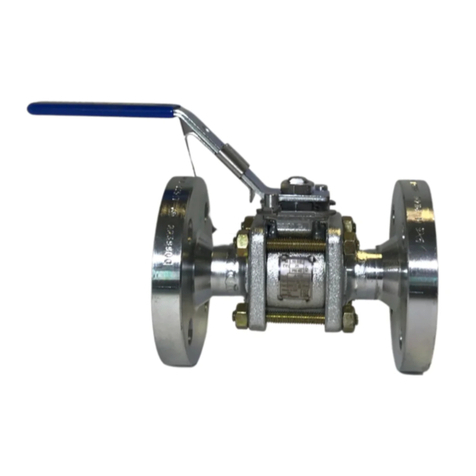
Spirax Sarco
Spirax Sarco M10Si Automation User manual

Spirax Sarco
Spirax Sarco ADV Series User manual

Spirax Sarco
Spirax Sarco PV4 User manual
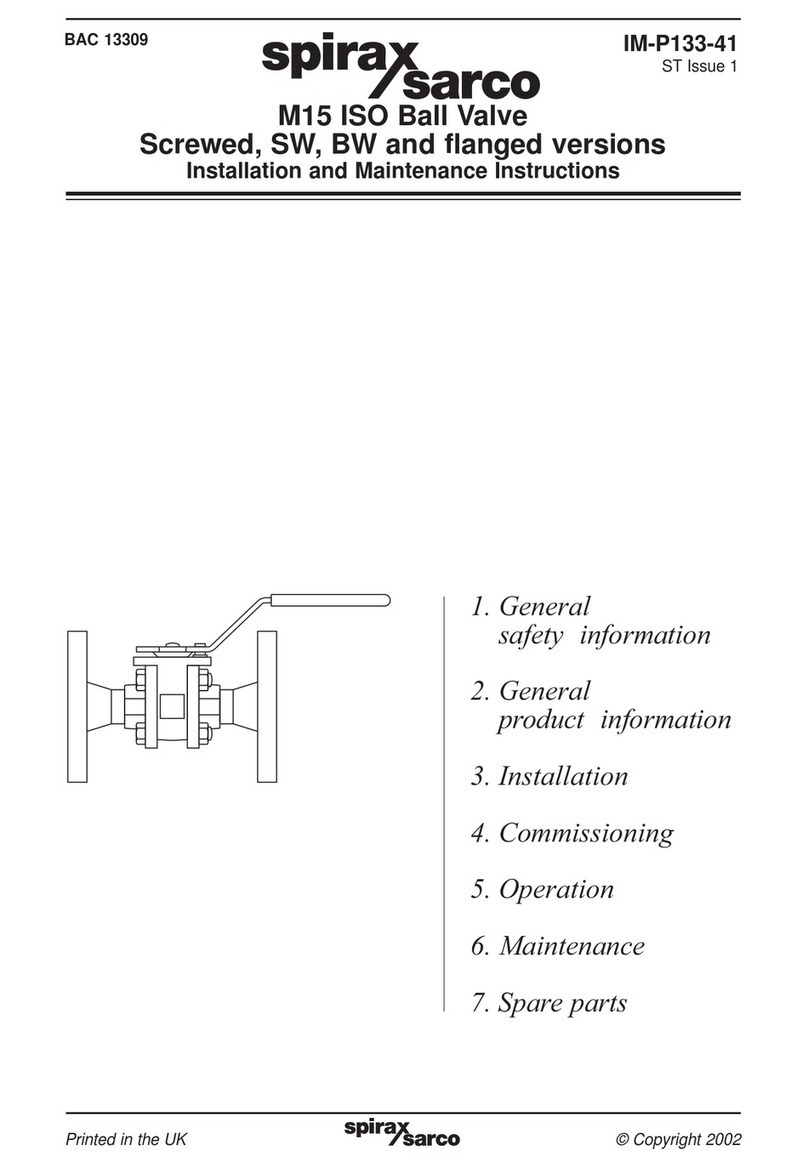
Spirax Sarco
Spirax Sarco M15 Series User manual

Spirax Sarco
Spirax Sarco BSA3HP User manual
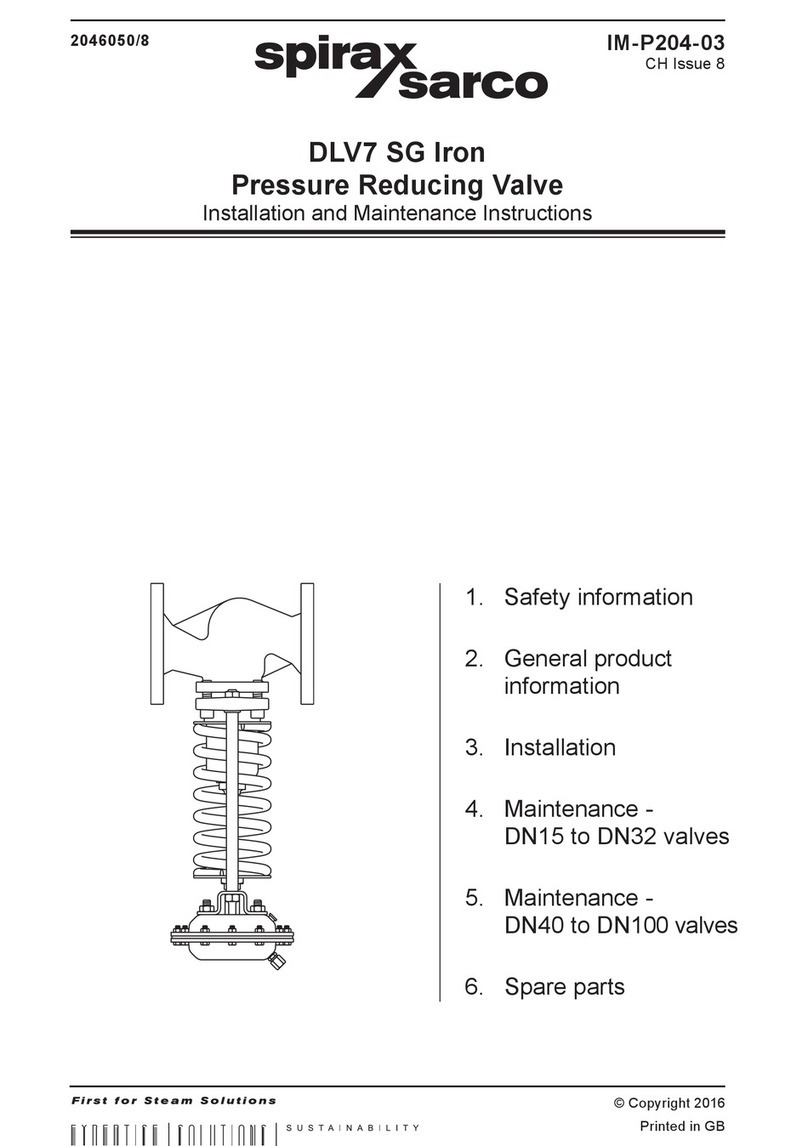
Spirax Sarco
Spirax Sarco DLV7 User manual
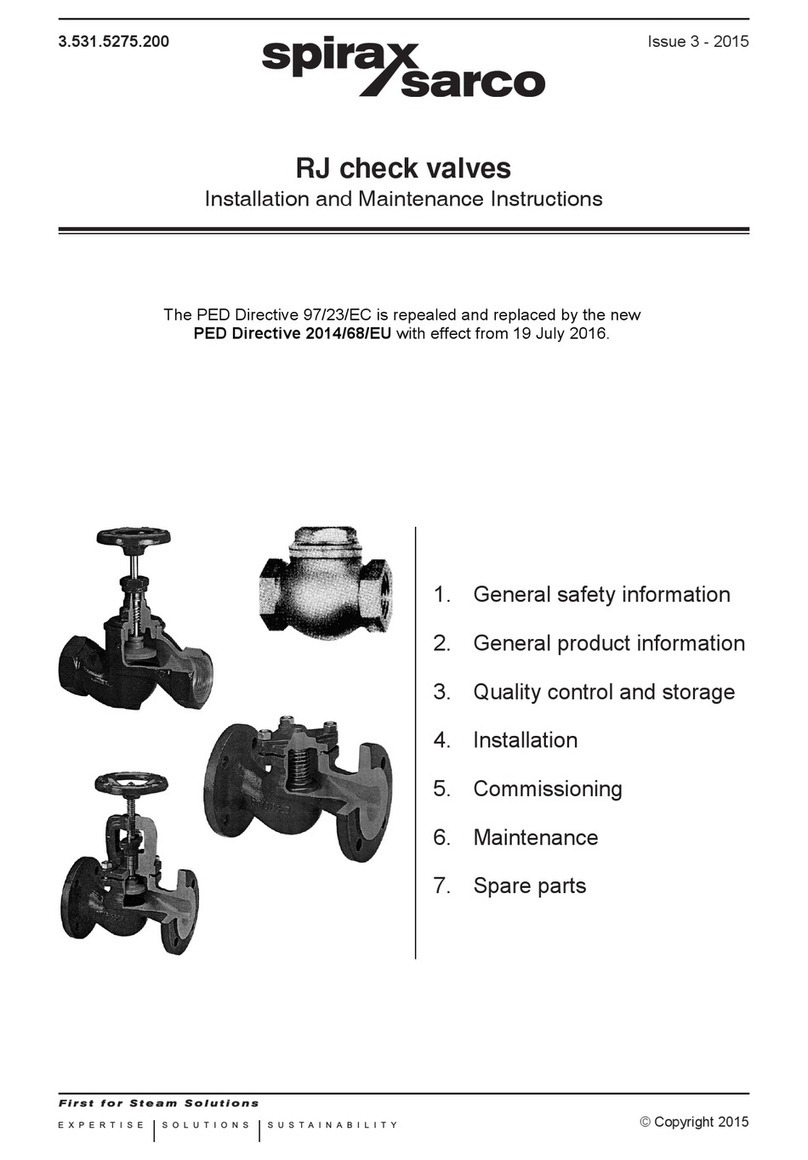
Spirax Sarco
Spirax Sarco RJ216Z User manual
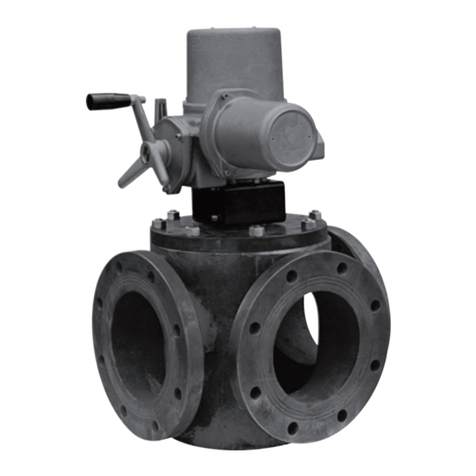
Spirax Sarco
Spirax Sarco RSW User manual
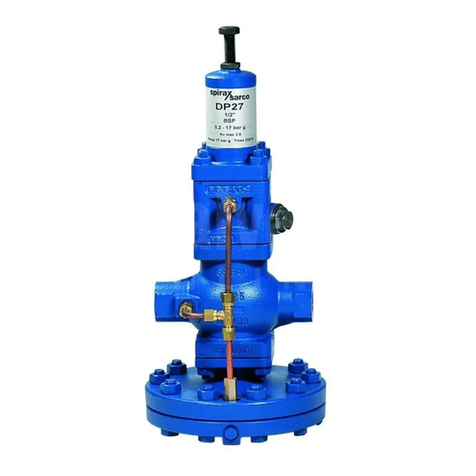
Spirax Sarco
Spirax Sarco DP27 User manual
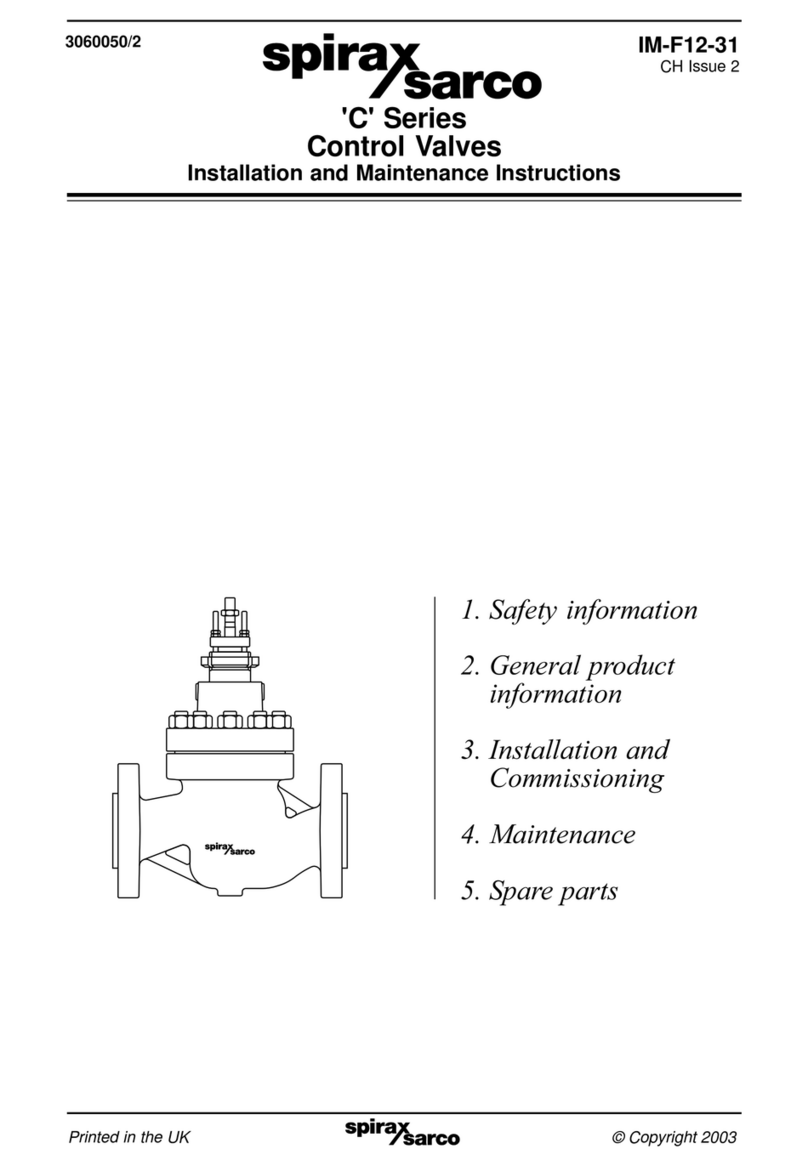
Spirax Sarco
Spirax Sarco C Series User manual
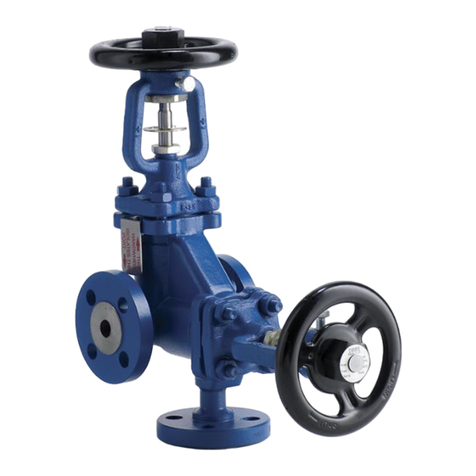
Spirax Sarco
Spirax Sarco SafeBloc DBB3 User manual
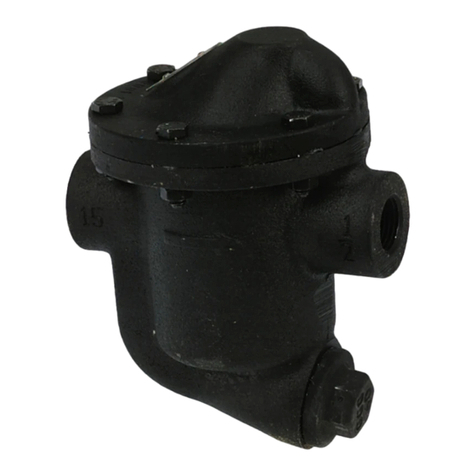
Spirax Sarco
Spirax Sarco HM Series User manual
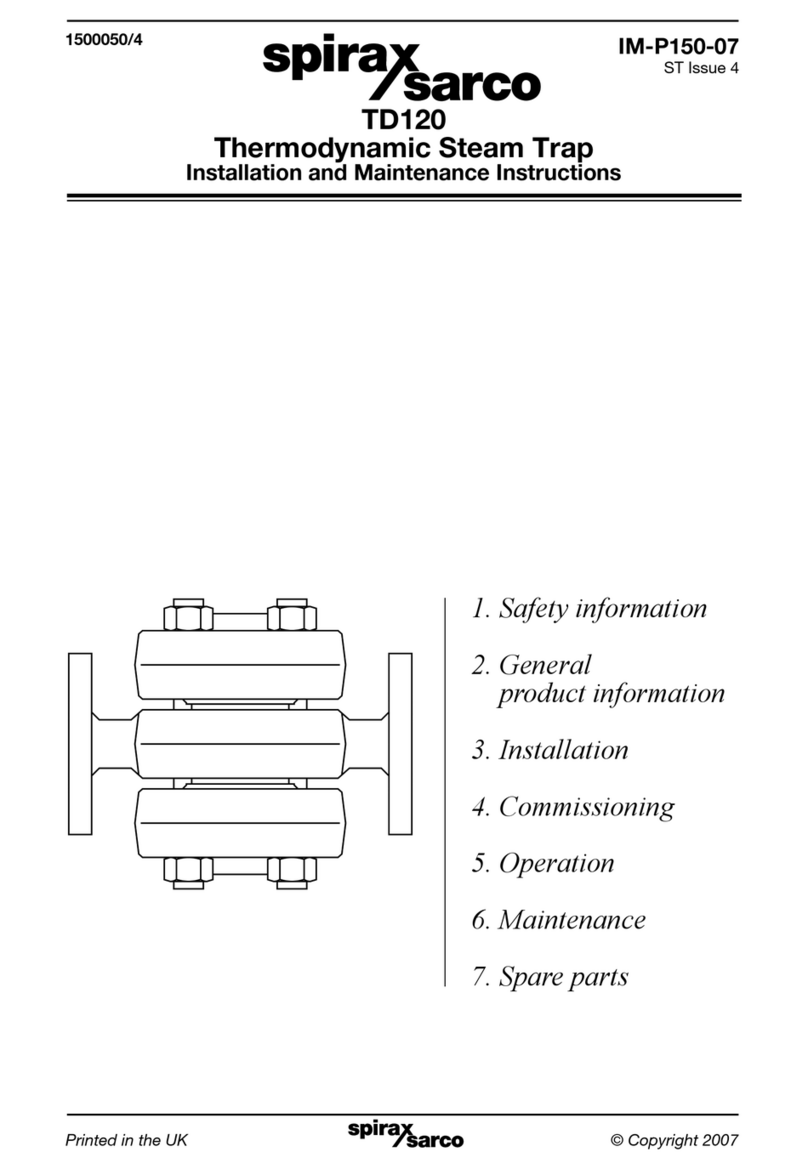
Spirax Sarco
Spirax Sarco TD120 User manual
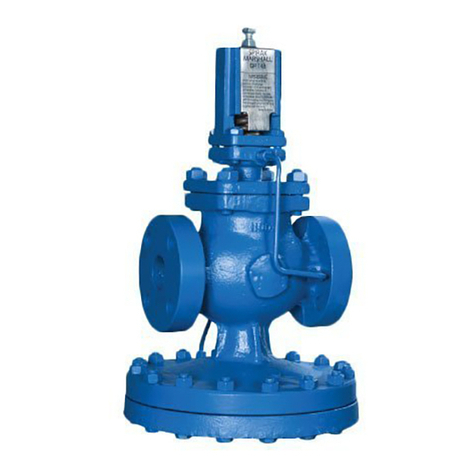
Spirax Sarco
Spirax Sarco DP143 User manual

Spirax Sarco
Spirax Sarco GKE 10 Guide

Spirax Sarco
Spirax Sarco Spira-trol KE73 User manual
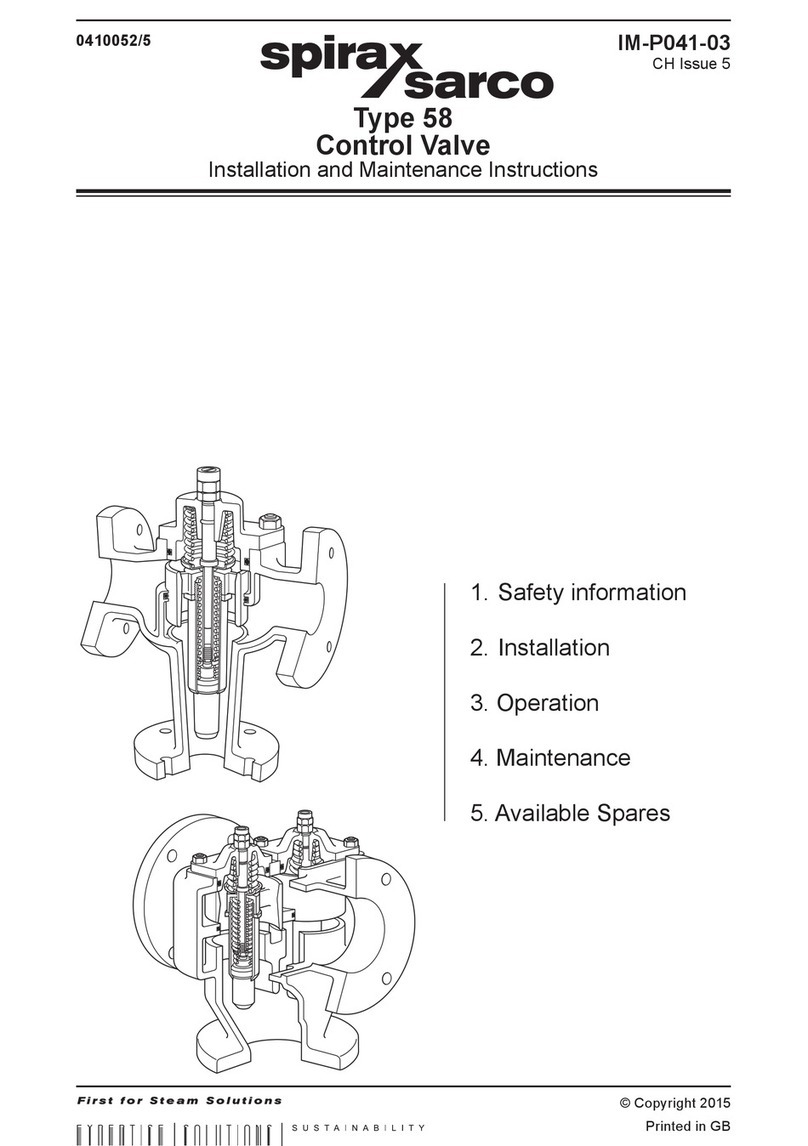
Spirax Sarco
Spirax Sarco 58 User manual
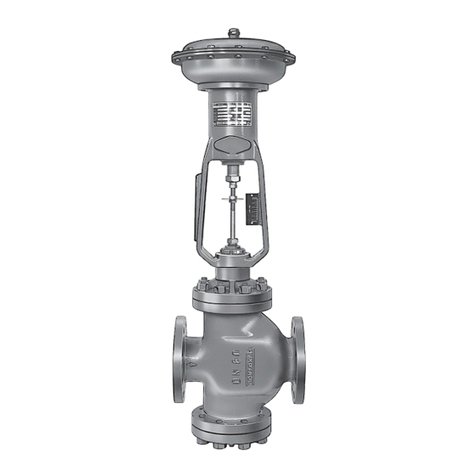
Spirax Sarco
Spirax Sarco 5953 Series User manual
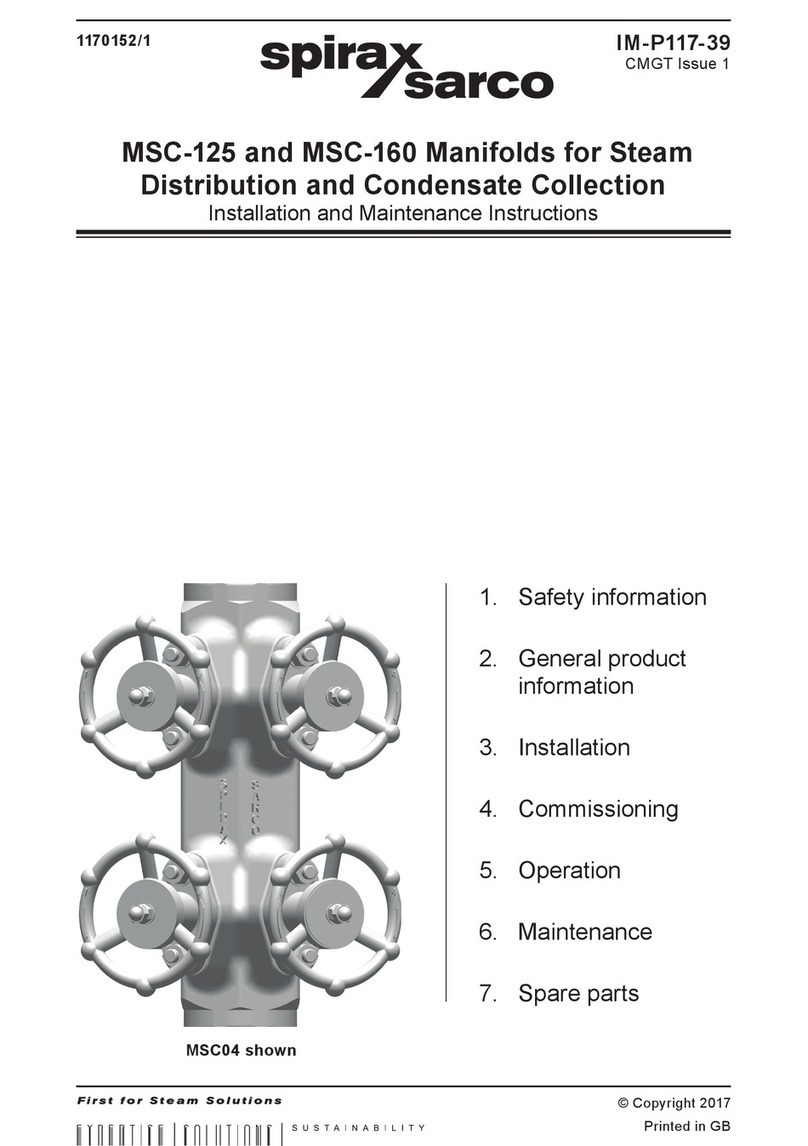
Spirax Sarco
Spirax Sarco MSC-125 User manual
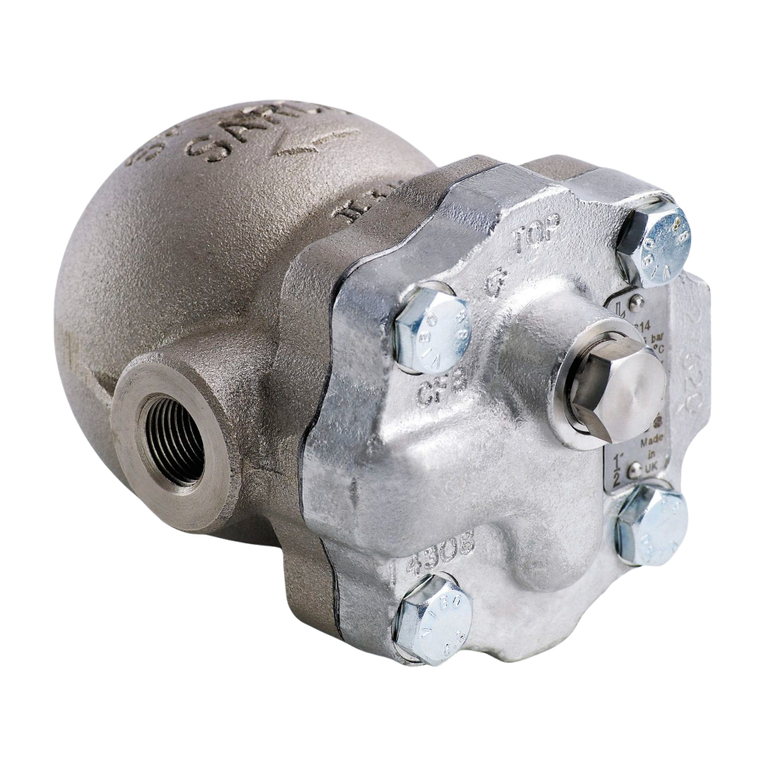
Spirax Sarco
Spirax Sarco FTS14 User manual
Popular Control Unit manuals by other brands

IRT Communications
IRT Communications DDT-4638 user manual
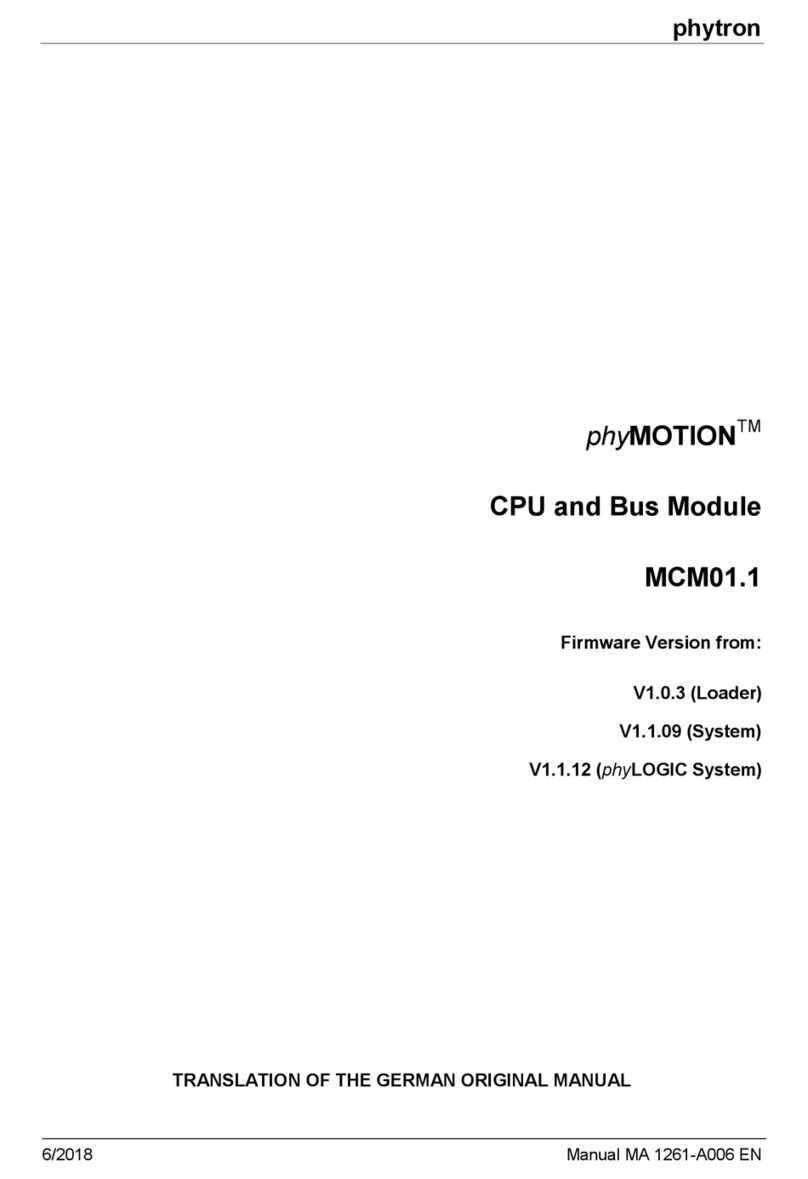
phytron
phytron phyMOTION MCM01.1 TRANSLATION OF THE GERMAN ORIGINAL MANUAL
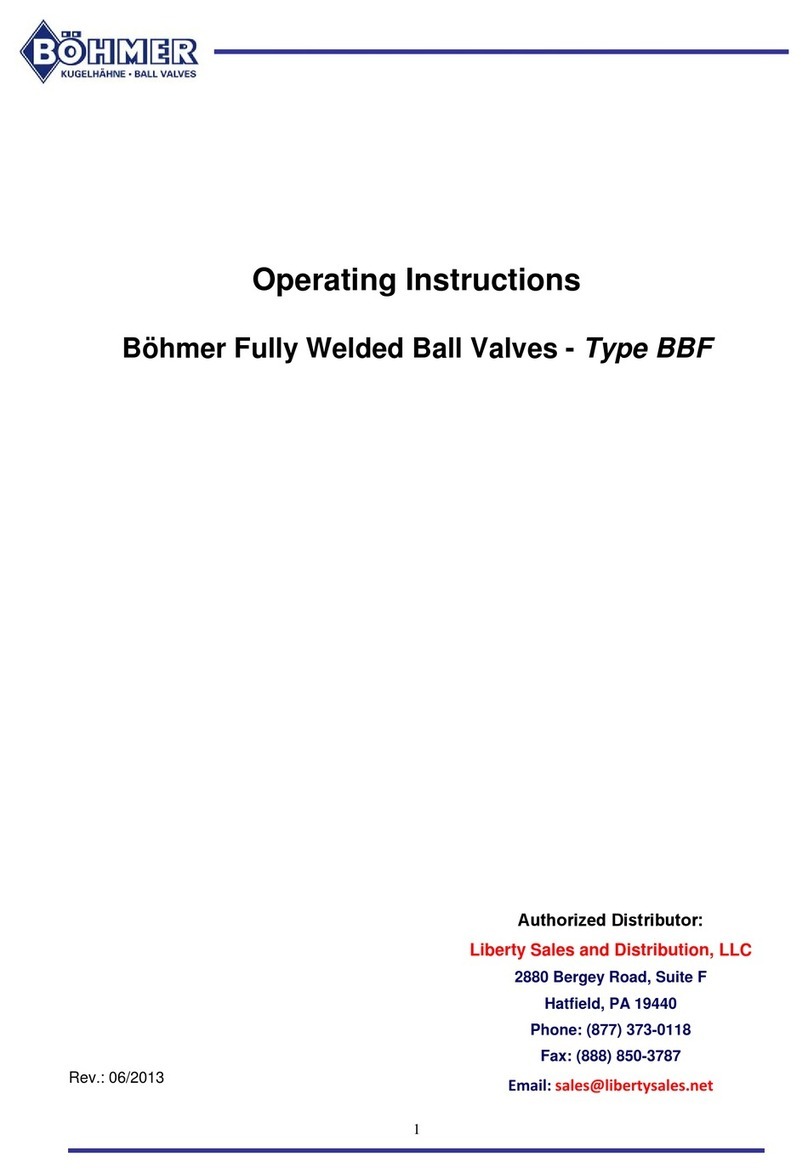
Böhmer
Böhmer BBF operating instructions

Exodraft
Exodraft EFC16 instructions
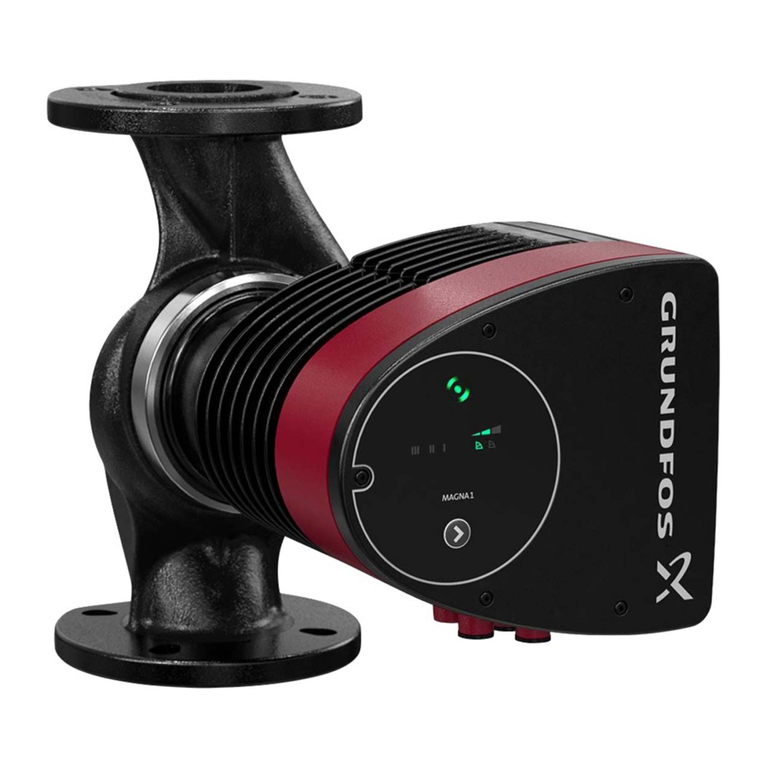
Grundfos
Grundfos MAGNA1 D manual

Genebre
Genebre 2528AV Installation, operation and maintenance manual