SRM ORIGIN PowerMeter User manual

EN
USER GUIDE
NOTICE
• Please check that the chain catcher pin of the big chainring aligns with the drive-side crankarm.
• Make sure the chainrings sit at and ght on the 110mm BCD (bolt circle diameter) of the PowerMeter.
• Check chainrings bolts of the SRM ORIGIN PowerMeter are torqued to the correct specicaons:
Shimano chainrings - 12Nm
Other manufacturers - 8Nm (check manufacturer specicaons)
• The drive-side crankarm comes pre-installed at the correct torque specicaon.
WARNING
WARNING
• Ensure frame has a suitable 30mm boom bracket installed when mounng the SRM ORIGIN PowerMeter.
Compable boom brackets can also be purchased from an SRM authorized dealers or our online shop at:
.
• Install Boom Bracket per manufacturers instrucons, ensuring sealing rings are placed properly and bearings
are fully seated and concentric in frame.
• Determine the required spacers for the Drive and Non-Drive side according to your boom bracket type - check
table (Fig. 11).
• Install the corresponding spacers onto the drive side axle (Fig. 1) and apply a small amount of grease to the
contact surfaces of the bearing/axle. Due to ght tolerances the axle/boom bracket can be dicult to install
if not inserted straight. Carefully align the spindle with both bearings and with a slight rocking moon use light
pressure to fully seat crank in the boom bracket. Make sure that the Non-Drive Side boom bracket does not
come loose or even come out of the BB shell.
• Remove the excess grease from the non-drive side of the crank axle and posion the appropriate spacers
according to the table (Fig. 11). When installing the non-drive crank, make sure that the crank is rotated by
180 ° to the drive-side crankarm.
• Apply a light thread locker (violet) to the threads of the axle bolt and slightly ghten with a 10mm allen key
(Fig. 2).
NOTICE
• Unscrew the non drive side crank bolt counterclockwise and place a small drop of light thread locker (violet) on
the threads. Re-torque the bolt to (Fig.3.1).
• Tighten the le axle bolt counterclockwise with a torque of (Fig.3.2).
• Let the thread locker cure for at least 6 hours before use!
• The crank length can get adjusted from 170, 172.5 to 175mm. Make sure you select the correct crank length!
• Degrease and clean the Tri-lobe nut, Tri-lobe washer and the contacng crank surfaces. Dust and/or any other
parcles on the Tri-lobe nut or on the crank could damage the crank or the pedal threads.
• Make sure to use the correct Tri-lobe nut marked with “R“ when installing the Drive-Side pedal (Fig. 5).
• Posion the arrow on the Tri-lobe washer facing the marking of the desired length. Make sure the washer is
aligned correctly and sing ush inside the crank (Fig. 4). Insert the Tri-lobe nut from the backside. Make sure
the holes of the washer and nut are concentric with each other.
• Proceed accordingly with the Tri-lobe nut marked with “L“ on the Non-Drive side crankarm (Fig. 6).
• Tighten the pedals with the recommended torque: (check pedal manufacturer specicaons).
WARNING
PowerMeter
PM-SRM-VAR-AXL-SH4-110-010

Extent of Limited Warranty: SRM warrants to the
end-user customer that the SRM products are free
from defects in materials and workmanship for a
3-year duraon aer the date of purchase by the
customer. The complete SRM warranty can be
found online at www.SRM.de.
CE - The CE mark is used to mark conformity with
the European Union EMC direcves EN 301 489-1
V1.81, EN 301 489-3 V1.41 and EN300 440-2 V1.3.1.
- This device complies with Part
15 of the FCC Rules. Operaon is subject to the
following two condions: (1) this device may not
cause harmful interference, and (2) this device
must accept any interference received, including
interference that may cause undesired operaon.
Repairs should be made by authorized SRM service
personnel. Unauthorized repairs will void warranty.
This product has been tested to comply with FCC
standards and is intended for personal use only.
Dispose of this device according to local and
federal regulaons, treang it as electronic
waste. You may return this device to your
nearest SRM Service Center for proper
disposal.
• The cadence magnet must be installed properly in order for the PowerMeter to turn on and measure cadence.
• The recommended posion for the cadence magnet is on the underside of the boom bracket.
• Make sure the magnet is posioned between 21-51 mm from the center point of the boom bracket shell. (Fig. 7).
• If your frame geometry does not allow for these magnet posions, visit our store at for
integrated chain catcher magnets and addional mounng opons.
• Remove the cable guide bolt and install the magnet under the cable guide (Fig. 8).
• To assist with cable guide removal, shi the chain into the largest cog in the rear and the largest chainring in
the front. Next, without turning the cranks, shi both derailleurs to the smallest cog. This will remove tension
from both cables.
• Posion the magnet 4-6 mm from the backside of the PowerMeter (Fig. 9).
• Install the bolt and ghten it to the torque specied by the frame manufacturer - you may need a longer screw
to securely hold the cable guide and magnet in place.
NOTICE
• Clean both the magnet and the mounng surface of the frame with the isopropanol alcohol.
• Posion the magnet 4-6 mm from the backside of the PowerMeter (Fig. 10).
NOTICE
• Use the double sided tape to install the cadence magnet to the frame. Remove the protecve lm on each side
of the tape. Avoid touching the adhesive surfaces. Glue the magnet in the correct posion.
• To achieve opmal magnet posion, the cadence magnet and double sided tape can be cut with scissors to t
your desired locaon.
• For informaon on connecng the SRM ORIGIN PowerMeter to your SRM PowerControl or other third party
ANT+ devices, please refer to the device manual.
NOTICE
• The SRM ORIGIN PowerMeter broadcasts the baery status to the SRM PowerControl or other compable
ANT+ devices. You will get noed if the baery is running low!
• See our authorized dealers or us directly at for a baery replacement.
WARNING
NOTICE
Non-Drive Drive-Side
BSA (68mm) 68 mm ±0,2 45,25 45,25 30mm 134mm 1mm 1mm
ITA (70mm) 70 mm ±0,2 45,25 45,25 30mm 134mm 1mm 1mm
BB30 68 mm ±0,2 (Ø42) 34 34 30mm 134mm 9mm + 2x 2mm 9mm + 1,5mm
PF30
68 mm ±0,2 (Ø46) 34 34 30mm 134mm 9mm + 2x 2mm 9mm + 1,5mm
BB 30A 73 mm ±0,2 (Ø42) 39 34 30mm 134mm 2x 3mm + 2mm 9mm + 1,5mm
PF 30A 73 mm ±0,2 (Ø46) 39 34 30mm 134mm 2x 3mm + 2mm 9mm + 1,5mm
OSBB 61 61,5 mm ±0,2 (Ø46) 30,75 30,75 30mm 134mm N/A N/A
BBRight™ Direct 79 mm ±0,2 (Ø42) 45 34 30mm 134mm 2mm 9mm + 1mm
BBRight™ Press 79 mm ±0,2 (Ø46) 45 34 30mm 134mm 2mm 9mm + 1mm
BB86 86,5 mm ±0,2 (Ø41) 43,25 43,25 30mm 134mm 2x 2mm 1,5mm
BB386 EVO 86,5 mm ±0,2 (Ø46) 43,25 43,25 30mm 134mm 2x 2mm 1,5mm
BB90
90 mm ±0,2 (Ø37) 45 45 24mm N/A N/A N/A
Spacer Drive-
Side
Spacer Non-
Drive
Recommended
axle length
BB Type
BB width
Shell width
(diameter)
Max. spindle
diameter
Version: V2.0 / March 2017 © 2017 SRM GmbH All copyrights and trademarks are the property of their respecve owners
www.SRM.de
SRM Training System
@srmtraining
srmpower
This manual suits for next models
1
Table of contents
Other SRM Measuring Instrument manuals
Popular Measuring Instrument manuals by other brands
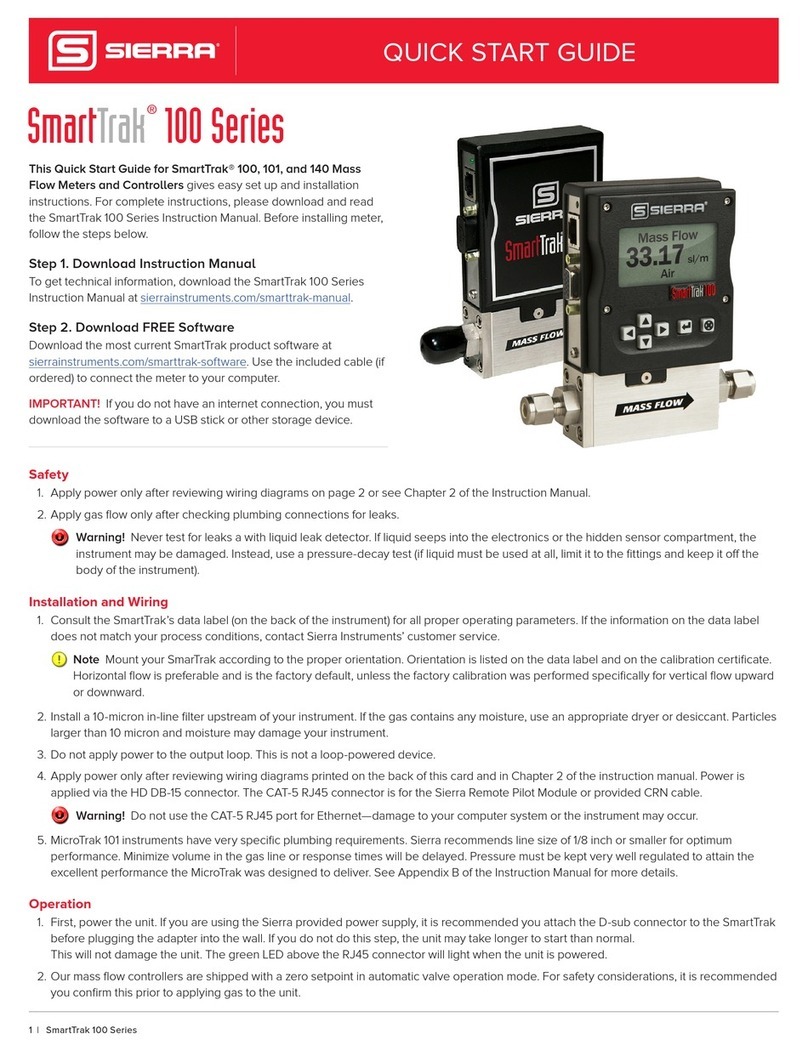
Sierra
Sierra Smart-Trak 100 series quick start guide

EIJKELKAMP
EIJKELKAMP QUICK DRAW 2900F1 operating instructions
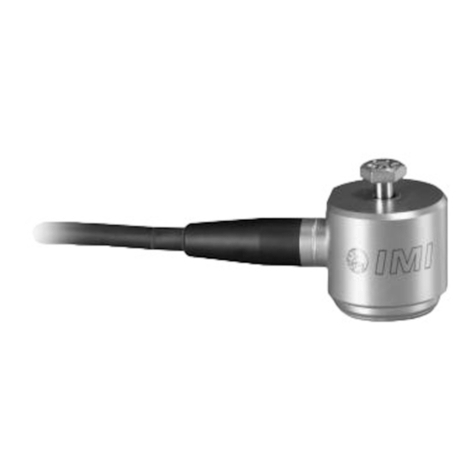
PCB Piezotronics
PCB Piezotronics IMI SENSORS ICP 625B11 Installation and operating manual
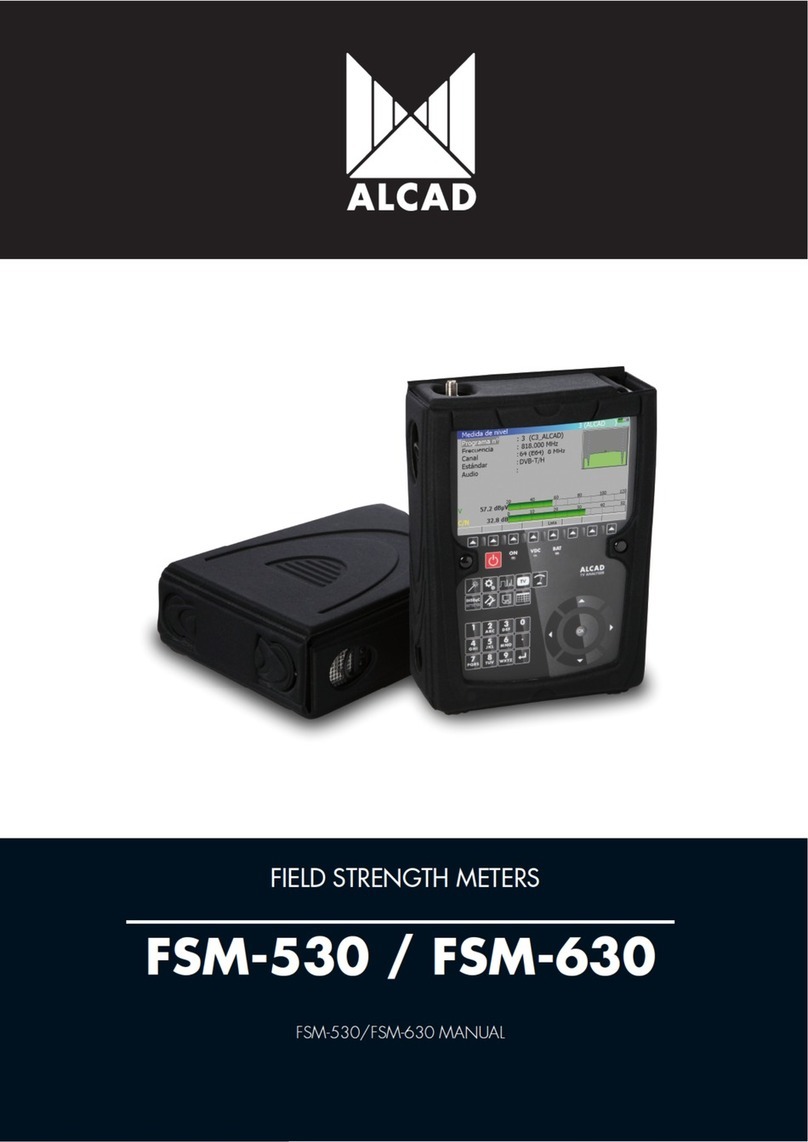
Alcad
Alcad FSM-530 manual
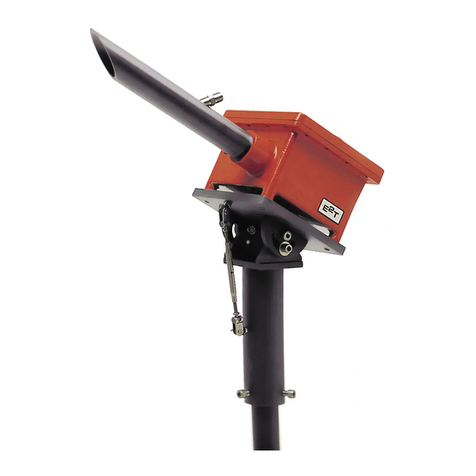
Advanced Energy
Advanced Energy LumaSense Technologies E2T QUASAR Series Operation manual
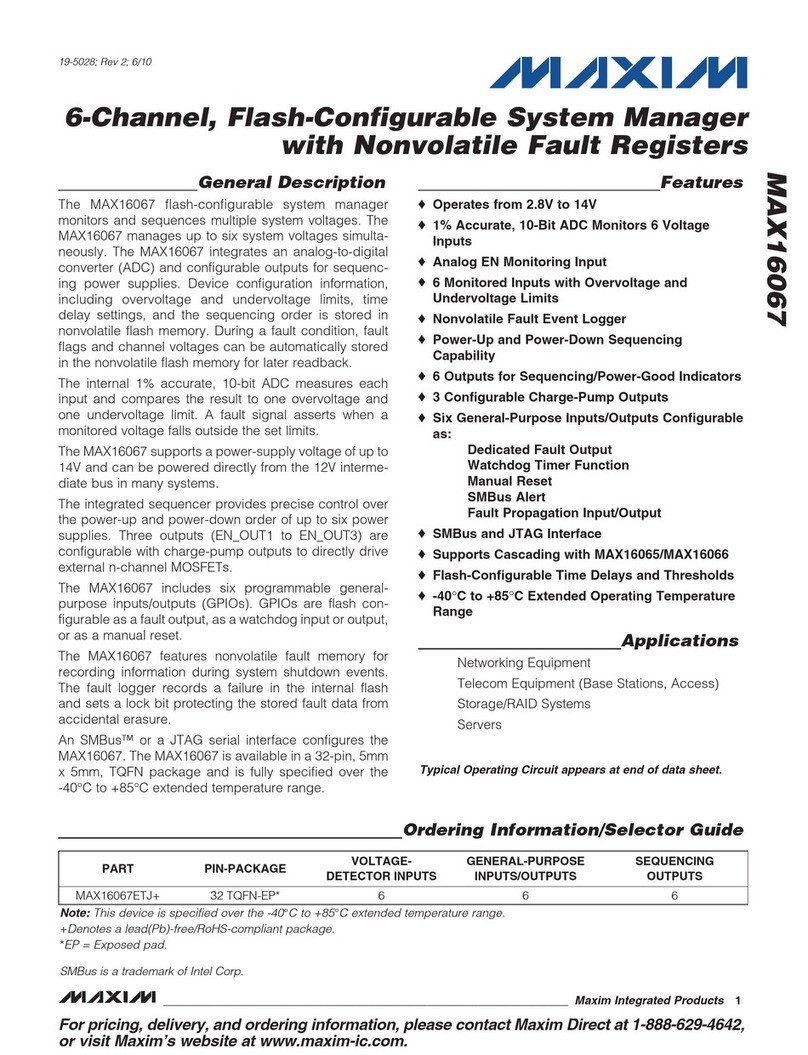
Maxim
Maxim MAX16067 manual