ST STM3221G-EVAL User manual

October 2011 Doc ID 018640 Rev 4 1/65
UM1065
User manual
STM3221G-EVAL evaluation board
Introduction
The STM3221G-EVAL evaluation board is a complete demonstration and development
platform for the STM32F2 series and includes an embedded STM32F217IGH6 high-
performance ARM®Cortex™-M3 32-bit microcontroller with a cryptographic acceleration
cell.
The full range of hardware features on the board is provided to help you evaluate all
peripherals (USB OTG HS, USB OTG FS, ethernet, motor control, CAN, MicroSD Card™,
smartcard, USART, Audio DAC, RS-232, IrDA, SRAM, MEMS, EEPROM… etc.) and
develop your own applications. Extension headers make it possible to easily connect a
daughter board or wrapping board for your specific application.
The in-circuit ST-LINK tool can be easily used for JTAG and SWD interface debugging and
programming.
Figure 1. STM3221G-EVAL evaluation board
www.st.com

Contents UM1065
2/65 Doc ID 018640 Rev 4
Contents
1 Overview . . . . . . . . . . . . . . . . . . . . . . . . . . . . . . . . . . . . . . . . . . . . . . . . . . 4
1.1 Features . . . . . . . . . . . . . . . . . . . . . . . . . . . . . . . . . . . . . . . . . . . . . . . . . . . 4
1.2 Demonstration software . . . . . . . . . . . . . . . . . . . . . . . . . . . . . . . . . . . . . . . 4
1.3 Order code . . . . . . . . . . . . . . . . . . . . . . . . . . . . . . . . . . . . . . . . . . . . . . . . . 4
1.4 Delivery recommendations . . . . . . . . . . . . . . . . . . . . . . . . . . . . . . . . . . . . . 5
2 Hardware layout and configuration . . . . . . . . . . . . . . . . . . . . . . . . . . . . . 6
2.1 Power supply . . . . . . . . . . . . . . . . . . . . . . . . . . . . . . . . . . . . . . . . . . . . . . . 9
2.2 Boot option . . . . . . . . . . . . . . . . . . . . . . . . . . . . . . . . . . . . . . . . . . . . . . . . 10
2.3 Clock source . . . . . . . . . . . . . . . . . . . . . . . . . . . . . . . . . . . . . . . . . . . . . . . 11
2.4 Reset source . . . . . . . . . . . . . . . . . . . . . . . . . . . . . . . . . . . . . . . . . . . . . . 11
2.5 Audio . . . . . . . . . . . . . . . . . . . . . . . . . . . . . . . . . . . . . . . . . . . . . . . . . . . . 11
2.6 EEPROM . . . . . . . . . . . . . . . . . . . . . . . . . . . . . . . . . . . . . . . . . . . . . . . . . 12
2.7 CAN . . . . . . . . . . . . . . . . . . . . . . . . . . . . . . . . . . . . . . . . . . . . . . . . . . . . . 12
2.8 RS-232 and IrDA . . . . . . . . . . . . . . . . . . . . . . . . . . . . . . . . . . . . . . . . . . . 13
2.9 Motor control . . . . . . . . . . . . . . . . . . . . . . . . . . . . . . . . . . . . . . . . . . . . . . 14
2.10 Smartcard . . . . . . . . . . . . . . . . . . . . . . . . . . . . . . . . . . . . . . . . . . . . . . . . . 15
2.11 MicroSD Card . . . . . . . . . . . . . . . . . . . . . . . . . . . . . . . . . . . . . . . . . . . . . . 15
2.12 MEMS . . . . . . . . . . . . . . . . . . . . . . . . . . . . . . . . . . . . . . . . . . . . . . . . . . . . 16
2.13 Potentiometer . . . . . . . . . . . . . . . . . . . . . . . . . . . . . . . . . . . . . . . . . . . . . . 16
2.14 ADC . . . . . . . . . . . . . . . . . . . . . . . . . . . . . . . . . . . . . . . . . . . . . . . . . . . . . 16
2.15 USB OTG FS . . . . . . . . . . . . . . . . . . . . . . . . . . . . . . . . . . . . . . . . . . . . . . 16
2.16 Ethernet . . . . . . . . . . . . . . . . . . . . . . . . . . . . . . . . . . . . . . . . . . . . . . . . . . 17
2.17 USB OTG HS . . . . . . . . . . . . . . . . . . . . . . . . . . . . . . . . . . . . . . . . . . . . . . 18
2.18 Camera module . . . . . . . . . . . . . . . . . . . . . . . . . . . . . . . . . . . . . . . . . . . . 18
2.19 SRAM . . . . . . . . . . . . . . . . . . . . . . . . . . . . . . . . . . . . . . . . . . . . . . . . . . . . 19
2.20 Development and debug support . . . . . . . . . . . . . . . . . . . . . . . . . . . . . . . 20
2.21 Display and input devices . . . . . . . . . . . . . . . . . . . . . . . . . . . . . . . . . . . . . 21
3 Connectors . . . . . . . . . . . . . . . . . . . . . . . . . . . . . . . . . . . . . . . . . . . . . . . 22
3.1 Daughter board extension connectors CN1, 2, 3 and 4 . . . . . . . . . . . . . . 22

UM1065 Contents
Doc ID 018640 Rev 4 3/65
3.2 Motor control connector CN5 . . . . . . . . . . . . . . . . . . . . . . . . . . . . . . . . . . 28
3.3 MicroSD connector CN6 . . . . . . . . . . . . . . . . . . . . . . . . . . . . . . . . . . . . . . 29
3.4 Ethernet RJ45 connector CN7 . . . . . . . . . . . . . . . . . . . . . . . . . . . . . . . . . 30
3.5 USB OTG FS Micro-AB connector CN8 . . . . . . . . . . . . . . . . . . . . . . . . . . 30
3.6 USB OTG HS Micro-AB connector CN9 . . . . . . . . . . . . . . . . . . . . . . . . . 31
3.7 CAN D-type 9-pin male connectors CN10 (CAN1 or CAN2) . . . . . . . . . . 31
3.8 Audio connector CN11 . . . . . . . . . . . . . . . . . . . . . . . . . . . . . . . . . . . . . . . 31
3.9 Trace debugging connector CN13 . . . . . . . . . . . . . . . . . . . . . . . . . . . . . . 32
3.10 JTAG debugging connector CN14 . . . . . . . . . . . . . . . . . . . . . . . . . . . . . . 32
3.11 Camera module connector CN15 . . . . . . . . . . . . . . . . . . . . . . . . . . . . . . . 33
3.12 RS-232 connector CN16 . . . . . . . . . . . . . . . . . . . . . . . . . . . . . . . . . . . . . 34
3.13 Power connector CN18 . . . . . . . . . . . . . . . . . . . . . . . . . . . . . . . . . . . . . . 34
3.14 TFT LCD connector CN19 . . . . . . . . . . . . . . . . . . . . . . . . . . . . . . . . . . . . 34
3.15 Smartcard connector CN20 . . . . . . . . . . . . . . . . . . . . . . . . . . . . . . . . . . . 35
3.16 ST-LINK/V2 connector CN21 . . . . . . . . . . . . . . . . . . . . . . . . . . . . . . . . . . 35
3.17 Camera extension connector CN23 . . . . . . . . . . . . . . . . . . . . . . . . . . . . . 36
3.18 STM3221G-EVAL pinout . . . . . . . . . . . . . . . . . . . . . . . . . . . . . . . . . . . . . 36
4 Schematics . . . . . . . . . . . . . . . . . . . . . . . . . . . . . . . . . . . . . . . . . . . . . . . 42
5 Revision history . . . . . . . . . . . . . . . . . . . . . . . . . . . . . . . . . . . . . . . . . . . 64

Overview UM1065
4/65 Doc ID 018640 Rev 4
1 Overview
1.1 Features
■STM32F217IGH6 microcontroller
■16 Mbit SRAM
■1 Gbyte or more MicroSD Card
■Boot from user Flash, system memory or SRAM
■Both ISO/IEC 14443 type A and B smartcard support
■I2C compatible serial interface 8 Kbytes EEPROM, MEMS and I/O expander
■IEEE 802.3-2002 compliant ethernet connector
■Two CAN 2.0 A/B channels on the same DB connector
■RS-232 communication
■IrDA transceiver
■USB OTG (HS and FS) with Micro-AB connector
■Inductor motor control connector
■I2S Audio DAC, stereo audio jack for headset
■3.2" 240x320 TFT color LCD with touchscreen
■4 color LEDs
■Camera module and extension connector for ST camera plug-in
■Joystick with 4-direction control and selector
■Reset, wakeup, tamper and user button
■RTC with backup battery
■Extension connector for daughterboard or wrapping board
■JTAG, SW and trace debug support
■Embedded ST-LINK/V2
■Five 5V power supply options: Power jack, USB FS connector, USB HS connector,
ST-LINK/V2 or daughterboard
■MCU consumption measurement circuit
1.2 Demonstration software
Demonstration software is preloaded in the board's Flash memory for easy demonstration of
the device peripherals in standalone mode. For more information and to download the latest
version, please refer to STM3221G-EVAL demonstration software available on web:
www.st.com/mcu.
1.3 Order code
To order the STM32F217IGH6 MCU evaluation board, use the order code
STM3221G-EVAL.

UM1065 Overview
Doc ID 018640 Rev 4 5/65
1.4 Delivery recommendations
Several verifications are needed before using the board for the first time to make sure that
nothing has been damaged during shipment and no components are unplugged and lost.
When the board is extracted from its plastic bag, please check that no component remains
in the bag. Main components to verify are:
1. The 25 MHz crytals (X1 and X4) may have been removed by a shock.
2. The camera connected on socket CN15 located on the right side of the board under the
JTAG connector may be unplugged. If this is the case, please refer to the note in
Section 2.18: Camera module to make sure to replug it in the correct position.
3. The MicroSDCard may have been ejected from its connector CN6 (top left corner of the
board).
The plastic protection on the camera should be removed carefully as the connection is very
fragile.

Hardware layout and configuration UM1065
6/65 Doc ID 018640 Rev 4
2 Hardware layout and configuration
The STM3221G-EVAL evaluation board is designed around the STM32F217IGH6
microcontroller with a cryptographic acceleration cell in the UFBGA176 package. The
hardware block diagram Figure 2 illustrates the connection between STM32F217IGH6 and
peripherals (Camera module, LCD, SRAM, EEPROM, MEMS, USART, IrDA, USB OTG HS,
USB OTG FS, Ethernet, Audio, CAN bus, smartcard, MicroSD Card and motor control) and
Figure 3 will help you locate these features on the actual evaluation board.

UM1065 Hardware layout and configuration
Doc ID 018640 Rev 4 7/65
Figure 2. Hardware layout and configuration
069
05[[[[[9
670),*+
56
WUDQVFHLYHU
,U'$
WUDQVFHLYHU
6PDUW&DUG
LQWHUIDFH
9UHJXODWRU
7)7/&'
0LFUR6'
FDUG
$XGLR'$&
0&FRQWURO
FRQQHFWRU
/('V.H\
-7$*
0(06
3RWHQWLRPHWHU
6PDUW&DUG
FRQQHFWRU
,QWHJUDWHG5-
FRQQHFWRU
56
'%FRQQHFWRU
$'&
,6
*3,2
0,,50,,
86$57
,&
([WHQVLRQ
FRQQHFWRUIRU
*3,2V
3+<
86$57
&$1
&$1
WUDQVFHLYHU
&$1
'%FRQQHFWRU
0&
6',2
7UDFH
'HEXJ
27*)6 86%0LFUR$%
FRQQHFWRU
((3520
,2H[SDQGRU
-R\VWLFN
7RXFKVFUHHQ
86%SRZHU
VZLWFK
&$1
9UHJXODWRU
9UHJXODWRU
9UHJXODWRU
'&0,
&DPHUD
PRGXOH
27*+6 86%0LFUR$%
FRQQHFWRU
86%SRZHU
VZLWFK
86%+6
3+<
'$&
)60&
65$0
67/,1.9
&DPHUDH[WHQVLRQ
FRQQHFWRU
0LFURSKRQH
$PSOLILHU
$XGLR-DFN
$'&

Hardware layout and configuration UM1065
8/65 Doc ID 018640 Rev 4
Figure 3. STM3221G-EVAL evaluation board layout
06 9
&1
0RWRUFRQWURO
&1
0LFUR6'FDUG
&1
7UDFH
&1
-7$*
8
,U'$
&1
86%27*)6
&1
86%27*+6
&1
67/,1.9
&1
&RORU/&'
&1
&DPHUDPRGXOH
&1
&DPHUDH[WHQVLRQ
FRQQHFWRU
8
-R\VWLFN
%
8VHUNH\
%
7DPSHU
&1
6PDUWFDUG
%
:DNHXS
%
5HVHW
59
3RWHQWLRPHWHU
&1
9SRZHUMDFN
&1
$XGLRMDFN
&1
86$57
&1
&$1
8
670),*+
&1
5-
FRQQHFWRU
&1&1
([WHQVLRQ
CONNECTOR $4"

UM1065 Hardware layout and configuration
Doc ID 018640 Rev 4 9/65
2.1 Power supply
The STM3221G-EVAL evaluation board is designed to be powered by 5 V DC power supply
and to be protected by PolyZen from a wrong power plug-in event. It is possible to configure
the evaluation board to use any of following five sources for the power supply:
●5 V DC power adapter connected to JP18, the power jack on the board
●5 V DC power with 500 mA limitation from CN8, the USB OTG FS Micro-AB connector
●5 V DC power with 500 mA limitation from CN9, the USB OTG HS Micro-AB connector
●5 V DC power with 500 mA limitation from CN21, the ST-LINK/V2 USB connector
●5 V DC power from both CN1 and CN3, the extension connector for daughterboard
(DTB for daughterboard on silkscreen)
The power supply is configured by setting the related jumpers JP4, JP32, JP18 and JP19 as
described in Table 1.
Table 1. Power related jumpers and solder bridges
Jumper Description
JP4 Jumper reserved for future use (RFU).
Default setting: Fitted
JP32 MCU_VDD is connected to 3.3 V power when JP32 is closed and MCU current
consumption measurement can be done manually by multi-meter when JP32 is open.
Default setting: Fitted
JP18
JP18 selects one of the five possible power supply sources.
Selects the ST-LINK/V2 USB connector (CN21) power supply,
set JP18 as shown:
(Default setting)
To select power supply jack (CN18) power supply, set JP18 as
shown:
To select daughterboard connector (CN1 and CN3)power
supply, set JP18 as shown:
HS
FS
DTB
PSU
STlk
HS
FS
DTB
PSU
STlk
HS
FS
DTB
PSU
STlk

Hardware layout and configuration UM1065
10/65 Doc ID 018640 Rev 4
Note: LED LD9 is lit when the STM3221G-EVAL evaluation board is powered by 5 V correctly.
2.2 Boot option
The STM3221G-EVAL evaluation board is able to boot from:
●Embedded User Flash
●System memory with boot loader for ISP
●Embedded SRAM for debugging
The boot option is configured by setting switch SW1 (BOOT1) and SW2 (BOOT0). The
BOOT0 can be configured also via RS-232 connector CN16.
JP18
(cont.)
To select USB OTG FS (CN8) power supply, set JP18 as shown:
To select USB OTG HS (CN9)power supply, set JP18 as shown:
To select power supply jack (CN18) power supply to both
STM3221G-EVAL and daughterboard connected on CN1 and
CN3, set JP18 as shown (daughterboard must not have its own
power supply connected)
JP19
To connect Vbat to the battery, set JP19 as shown:
To connect Vbat to 3.3 V power, set JP19 as shown: (Default setting)
Table 1. Power related jumpers and solder bridges (continued)
Jumper Description
HS
FS
DTB
PSU
STlk
HS
FS
DTB
PSU
STlk
HS
FS
DTB
PSU
STlk
321
3
21
Table 2. Boot related jumpers
BOOT 0 BOOT 1 Boot source
0 1 or 0 STM3221G-EVAL boots from User Flash (Default setting)
1 1 STM3221G-EVAL boots from Embedded SRAM
1 0 STM3221G-EVAL boots from System Memory

UM1065 Hardware layout and configuration
Doc ID 018640 Rev 4 11/65
2.3 Clock source
Four clock sources are available on STM3221G-EVAL evaluation board for
STM32F217IGH6 and RTC embedded:
●X1, 25 MHz crystal for ethernet PHY with socket. It can be removed when clock is
provided by MCO pin of the MCU
●X2, 26 MHz crystal for USB OTG HS PHY
●X3, 32 kHz crystal for embedded RTC
●X4, 25 MHz crystal with socket for STM32F217IGH6 microcontroller (it can be removed
from socket when internal RC clock is used)
2.4 Reset source
The reset signal of STM3221G-EVAL evaluation board is low active and the reset sources
include:
●Reset button B1
●Debugging tools from JTAG connector CN14 and trace connector CN13
●Daughterboard from CN3
●RS-232 connector CN16 for ISP
●ST-LINK/V2
2.5 Audio
The STM3221G-EVAL evaluation board enables stereo audio play and microphone
recording by an external headset connected on audio jack CN11.
An audio DAC CS43L22 is connected to both the I2S2 port and the DAC channel while a
microphone amplifier is connected to the ADC of the STM32F217IGH6.
The CS43L22 can be configured via I2C1 and the external PLL (U36) can provide an
external clock which is connected to the I2S_CKIN pin (PC9).
Warning: Signal I2S_SD (PI3) is close to signal TCK/SWCLK of the
JTAG/SWD interface, so to avoid possible communication
issues on JTAG/SWD when the I2S interface is used the
recommendations are to:
1) Prefer usage of embedded ST-LINK/V2 to external tool
connected on CN14.
2) Configure PI3 GPIO in low speed (2 MHz or 10 MHz).
Table 3. Audio related jumpers
Jumper Description
JP16 Description of JP16 is in Table 10 on page 15.
JP33 The microphone amplifier can be disabled when JP33 is fitted. Default setting: Not fitted.

Hardware layout and configuration UM1065
12/65 Doc ID 018640 Rev 4
2.6 EEPROM
A 64 Kbit EEPROM is connected to the I2C1 bus of STM32F217IGH6.
2.7 CAN
The STM3221G-EVAL evaluation board enables two channels of CAN2.0A/B compliant
CAN bus communication based on a 3.3 V CAN transceiver on one DB9 connector (CN10).
The two CAN buses can be disconnected by jumpers from the relevant STM32F217IGH6
I/Os which are shared with FSMC and USB OTG HS.
JP3 and JP10 must be refitted to enable CAN1 or CAN2 as listed in Table 5.
High-speed, Standby and Slope Control modes can be selected by setting jumper JP7.
Table 4. EEPROM related jumper and solder bridge
Jumper Description
JP24 EEPROM is in Write Protection mode when JP24 is not fitted.
Default setting: Not fitted.
Table 5. CAN-related jumpers
Jumper Description
JP3
To connect CAN1_TX to CAN transceiver, set JP3 as shown:
To connect CAN2_TX to CAN transceiver, set JP3 as shown:
JP10
To connect CAN1_RX to CAN transceiver, set JP10 as shown:
To connect CAN2_RX to CAN transceiver, set JP10 as shown:
PD0 and PB5 are disconnected from the CAN transceiver and used for FSMC and
USB_OTG_HS when jumper JP10 is not fitted (default setting).
JP7
To enable the selected CAN transceiver to work in Standby mode, set JP7 as
shown:
To enable the selected CAN transceiver to work in High-speed mode, set JP7 as
shown (Default setting):
To enable the selected CAN transceiver to work in Slope Control mode, do not fit JP7.
JP9 To enable the terminal resistor for the selected CAN, fit a jumper on JP9.
(Default setting: Not fitted).
321
3
21
321
3
21
32
1
3
21

UM1065 Hardware layout and configuration
Doc ID 018640 Rev 4 13/65
2.8 RS-232 and IrDA
Both RS-232 and IrDA communication is enabled by D-type 9-pin RS-232 connector (CN16)
and IrDA transceiver U11 which are connected to USART3 of STM32F217IGH6 on the
STM3221G-EVAL evaluation board.
For ISP support, two signals are added on the RS-232 connector CN16:
●Bootloader_RESET (shared with CTS signal)
●Bootloader_BOOT0 (shared with DSR signal)
RS-232 or IrDA can be selected by setting JP22, and ISP can be enabled by setting JP29
and JP34 as shown in Table 6.
Table 6. RS-232 and IrDA related jumper
Jumper Description
JP22
To connect USART3_RX to IrDA transceiver and enable IrDA communication,
set JP22 as shown:
To connect USART3_RX to RS-232 transceiver and enable RS-232
communication, set JP22 as shown (Default setting):
To enable MicroSD Card, which shares same I/Os with RS-232, JP22 is not fitted.
JP29 Bootloader_BOOT0 is managed by pin 6 of CN16 (RS-232 DSR signal) when JP29 is
closed. This configuration is used for boot loader application only.
Default setting: Not fitted.
JP34 Bootloader_RESET is managed by pin 8 of CN16 (RS-232 CTS signal) when JP34 is
fitted. This configuration is used for boot loader application only.
Default setting: Not fitted.
321
3
21

Hardware layout and configuration UM1065
14/65 Doc ID 018640 Rev 4
2.9 Motor control
The STM3221G-EVAL evaluation board enables a three-phase brushless motor control via
a 34-pin connector (CN5), which provides all required control and feedback signals to and
from the motor power-driving board. Available signals on this connector include emergency
stop, motor speed, 3-phase motor current, bus voltage, heatsink temperature (coming from
the motor driving board) and 6 channels of PWM control signal going to the motor driving
circuit.
The solder bridge (SB18) allows to choose two kinds of synchronization methods for PFCs
(Power Factor Correction) while the SB17 can be set for different signals on pin 31 of CN5.
The I/O pins used on motor control connector CN5 are multiplexed with some peripherals on
the board; either motor control connector or multiplexed peripherals can be enabled by the
setting of solder bridges SB10, SB11, SB12, SB14, SB15 and SB16.
Note: 1 Some 0 ohm resistors have to be removed or soldered to enable motor control application
except the solder bridges configurations mentioned above:
– R34, R58 & R51 to be removed
– R66, R204 & R205 to be soldered
2 MicroSD Card must be removed from CN6 for motor control application.
Table 7. Motor control solder bridges
Solder
bridge Description Multiplexed
peripherals
SB18 When closed, SB18 redirects the PFC synchronized signal to timer 3
input capture pin 2 in addition to the timer 3 external trigger input.
Default setting: Open
SB17
For CN5 encoder signal input (pin 31), SB17 must be open.
For CN5 special motor analog signal input (pin 31), SB17 must be
closed.
Default setting: Open
SB16 To connect MC_EmergencySTOP to PI4, close SB16.
Default setting: Open
Camera module
connected to
CN15
SB10 To connect MC_EnIndex to PB8, close SB10.
Default setting: Open
EthernetSB11 To connect MC_CurrentA to PC1, close SB11.
Default setting: Open
SB12 To connect MC_CurrentB to PC2, close SB12.
Default setting: Open
SB14 To connect MC_EnB to PD13, close SB14.
Default setting: Open FSMC
SB15 To connect MC_EnA to PD12 close SB15.
Default setting: Open

UM1065 Hardware layout and configuration
Doc ID 018640 Rev 4 15/65
2.10 Smartcard
STMicroelectronics smartcard interface chip ST8024 is used on STM3221G-EVAL board for
asynchronous 3 V and 5 V smartcards. It performs all supply protection and control
functions based on the connections with STM32F217IGH6 listed in Table 8:
Smartcard shares some I/Os with I2S bus for Audio. Some jumper settings need to be
reconfigured to enable smartcard as indicated below:
2.11 MicroSD Card
The 1 GByte or more MicroSD Card connected to SDIO of STM32F217IGH6 is available on
the board. MicroSD Card detection is managed by the standard I/O port PH13. MicroSD
Card shares I/Os with motor control, RS-232 and audio. The jumpers JP22 and JP16 must
be refit and motor control connector (CN5) must be disconnected for MicroSD Card function.
Table 8. Connection between ST8024 and STM32F217IGH6
ST8024 signals Description Connect to
STM32F217IGH6
5V/3V Smartcard power supply selection pin PH15
I/OUC MCU data I/O line PC6
XTAL1 Crystal or external clock input PG7
OFF Detect presence of a card, MCU interrupt, share same
pin with motor controller PF6
RSTIN Card reset input from MCU PF7
CMDVCC Start activation sequence input (Active Low), share
same pin with I2S DAC and Motor control PG12
Table 9. Smartcard related jumper
Jumper Description
JP21 To connect Smartcard_IO to PC6, JP21must be fitted.
JP21 must not be fitted for Audio DAC connection to I2S.
Default setting: Not fitted.
Table 10. MicroSD Card related jumpers
Jumper Description
JP22 Description of JP22 is in Section 2.8: RS-232 and IrDA
JP16
PC9 is connected to MicroSDCard_D1 when JP16 is set as shown to the right:
(Default setting):
PC9 is connected to I2S_CKIN when JP16 is set as show to the right:
3
21
321

Hardware layout and configuration UM1065
16/65 Doc ID 018640 Rev 4
2.12 MEMS
A ST MEMS device LIS302DL is connected to I2C1 bus of STM32F217IGH6 on the board.
2.13 Potentiometer
There is one 10 Kohm potentiometer RV1 connected to PF9 of STM32F217IGH6 on the
board.
2.14 ADC
Two test points (TP3 AIN-) and (TP4 AIN+) are placed close to port PC1 of the MCU
allowing precise measurements on ADC1, ADC2 or ADC3 channel 11. As PC1 is also used
as current A input on the motor control connector it is recommended to remove R219 to
optimize noise immunity on this input.
A potentiometer RV1 is connected to PF9 of STM32F217IGH6. If needed, a low pass filter
(R74 and C59) can be placed on this input to reduce the bandwidth of the analog input PF9.
It is also possible to place the Ethernet PHY (U5) in low power mode in order to reduce the
noise induced by this high frequency peripheral. Power down pin (MII_INT in the schematic)
is connected to PB14 of the MCU, so this I/O can be to be configured as output low during
analog precision measurement.
2.15 USB OTG FS
The STM3221G-EVAL evaluation board enables USB OTG full speed communication via a
USB micro-AB connector (CN8) and USB power switch (U1) connected to VBUS. The
evaluation board can be powered by this USB connection at 5 V DC with a 500 mA current
limitation.
LED LD6 indicates that either:
●Power switch (U1) is ON and the STM3221G-EVAL functions as a USB host or
●VBUS is powered by another USB host while the STM3221G-EVAL functions as a USB
device.
LED LD5 indicates an over-current.

UM1065 Hardware layout and configuration
Doc ID 018640 Rev 4 17/65
2.16 Ethernet
The STM3221G-EVAL evaluation board enables 10/100M ethernet communication by a
PHY DP83848CVV (U5) and integrated RJ45 connector (CN7). Both MII and RMII interface
modes can be selected by setting jumpers JP5, JP6 and JP8 as listed below:
Note: 1 A test point (TP2) is available on the board for the PTP_PPS feature test.
2 The Ethernet PHY, U5, can be powered down by regulating PB14.
3 In RMII mode it is not possible to use MCO to output the 50 MHz clock to PHY due to the
PLL limitation explained in chapter 2.6.5 of STM32F20x & STM32F21x Errata sheet
(ES0005). In such a case it is possible to provide the 50 MHz clock by soldering a 50 MHz
oscillator (ref SM7745HEV-50.0M or equivalent) on the U3 footprint located under CN3 and
also removing jumper on JP5. This oscillator is not provided with the board.
Table 11. Ethernet related jumpers and solder bridges
Jumper Description
JP8
JP8 selects MII or RMII interface mode.
To enable MII, JP8 is not fitted.
To enable RMII interface mode, JP8 is fitted.
Default setting: Not fitted.
JP6
To enable MII interface mode, set JP6 as shown (Default setting):
To enable RMII interface mode, set JP6 as shown:
JP5
To provide 25 MHz clock for MII or 50 MHz clock for RMII by MCO at PA8, set
JP5 as shown (Default setting):
To provide 25 MHz clock by external crystal X1 (for MII interface mode only) set
JP5 as shown:
When clock is provided by external oscillator U3, JP5 must not be fitted (Default setting).
SB1
SB1 selects clock source only for RMII mode.
To connect the clock from MCO to RMII_REF_CLK, close SB1.
The resistor R212 has to be removed in this case.
Default setting: Open.
321
3
21
321
3
21

Hardware layout and configuration UM1065
18/65 Doc ID 018640 Rev 4
2.17 USB OTG HS
The STM3221G-EVAL evaluation board enables USB OTG high speed communication via a
USB micro-AB connector (CN9), USB high speed PHY (U8) and USB power switch (U4)
connected to VBUS. The evaluation board can be powered by this USB connector (CN9) at
5 V DC with a 500 mA current limitation.
LED LD7 indicates that power switch (U4) is ON and the STM3221G-EVAL is working as a
USB host or that VBUS is powered by another USB host when the STM3221G-EVAL is
working as a USB device. LD8 indicates an over-current.
The USB ULPI bus is shared with CAN2 bus, JP10 and JP3 must be kept open for USB
OTG HS.
Note: On boards MB786 prior to version B03 it is possible that after a board RESET the MCU is no
longer able to control communication with the OTG PHY (U8). When this issue occurs the
only way to recover OTG PHY control is to power the board OFF and ON. This issue is fixed
on MB786 version B03 or newer.
2.18 Camera module
A camera module is connected to DCMI bus of STM32F217IGH6 and shares the same I/Os
with the motor control connector. SB16 must be kept open (default setting) for camera
module application.
There are two possible modules and omnivision cameras populated on the CN15 connector
of the board:
●1.3 Megapixel: Module CN01302H1045-C: Camera OV9655
●2 Megapixel: Module CN020VAH2554-C: Camera OV2640
Note: 1 When the camera demo loaded in Flash is executed, some green pixels may appear in high
contrast zones, depending on the image captured.
2 The camera is not firmly restricted on its connector (CN15). It is possible that during
shipment the camera could be unplugged. In such case you need to plug it into the right
position as shown on the picture below (pin 1 dot on top left corner of the socket).
It is not recommended to remove it in order to avoid false contact later.
Table 12. MicroSD Card related jumper
Jumper Description
JP31 To disable USB OTG PHY U8, JP31 is not fitted.
Default setting: Fitted.
Table 13. Camera module related jumpers
Jumper Description
JP26 To set power down mode for the camera module, JP26 is fitted.
Default setting: Not fitted.
SB16 Description of SB16 is in Section 2.9: Motor control.

UM1065 Hardware layout and configuration
Doc ID 018640 Rev 4 19/65
Figure 4. Pin 1 camera plug
The camera extension connector CN23 is available on the boards to connect the ST camera
plug-in board.
2.19 SRAM
The 16 Mbit SRAM is connected to FSMC bus of the STM32F217IGH6 which shares the
same I/Os with CAN1 bus. JP3 and JP10 must not be fitted for SRAM and LCD application.
Table 14. SRAM related jumpers
Jumper Description
JP1
Connect PE4 to SRAM as A20 by setting JP1 as shown (Default setting):
Connect PE4 to trace connector CN13 as TRACE_D1 by setting JP1 as shown:
JP2
Connect PE3 to SRAM as A19 by settiing JP2 as shown (Default setting):
Connect PE3 to trace connector CN13 as TRACE_D0 by setting JP2 as shown:
321
3
21
321
3
21

Hardware layout and configuration UM1065
20/65 Doc ID 018640 Rev 4
2.20 Development and debug support
Version 2 of the ST-LINK, called ST-LINK/V2, is embedded on the board. This tool allows
onboard program loading and debugging of the STM32F using the JTAG or SWD interface.
Third-party debug tools are also supported by the JTAG (CN14) or Trace (CN13)
connectors.
To communicate with the embedded ST-LINK/V2, a specific driver needs to be installed on
your PC. To download and install this driver, refer to the software and development tools
page for the STM32F family available on www.st.com (the install shield is called
ST-LINK_V2_USBdriver.exe).
Third-party toolchains, Atollic TrueSTUDIO, KEIL ARM-MDK, IAR EWARM and Tasking VX-
Toolset support ST-LINK/V2 according to the following table:
The embedded ST-LINK/V2 connects to the PC via a standard USB cable from connector
CN21. The bicolor LED LD10 (COM) indicates the status of the communication as follows:
●Slow blinking Red/Off: At power-on before USB initialization
●Fast blinking Red/Off: After the first correct communication between PC and
ST-LINK/V2 (enumeration)
●Red LED On: When initialization between PC and ST-LINK/V2 is successfully finished
●Green LED On: After successful target communication initialization
●Blinking Red/Green: During communication with target
●Green On: Communication finished and OK
●Orange On: Communication failure
Note: 1 It is possible to power the board via CN21 (embedded ST-LINK/V2 USB connector) even if
an external tool is connected to CN13 (trace) or CN14 (external JTAG and SWD).
2 If the I2S interface is used, refer to the warning in Chapter 2.5.
Table 15. Third-party toolchain support
Manufacturer Toolchain Version
Atollic TrueSTUDIO 2.1
IAR EWARM 6.20.4
Keil MDK-ARM 4.20
Tasking VX-Toolset ARM Cortex-M 4.0.1
Other manuals for STM3221G-EVAL
2
Table of contents
Other ST Motherboard manuals
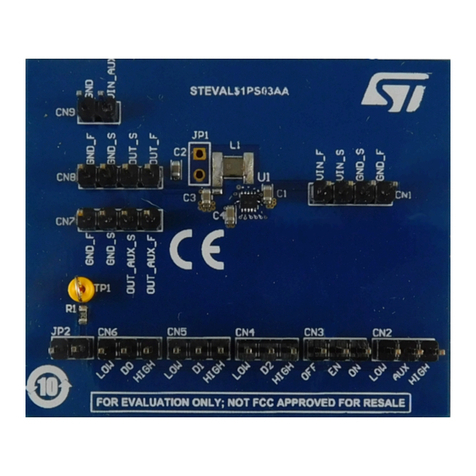
ST
ST STEVAL-1PS03A User manual
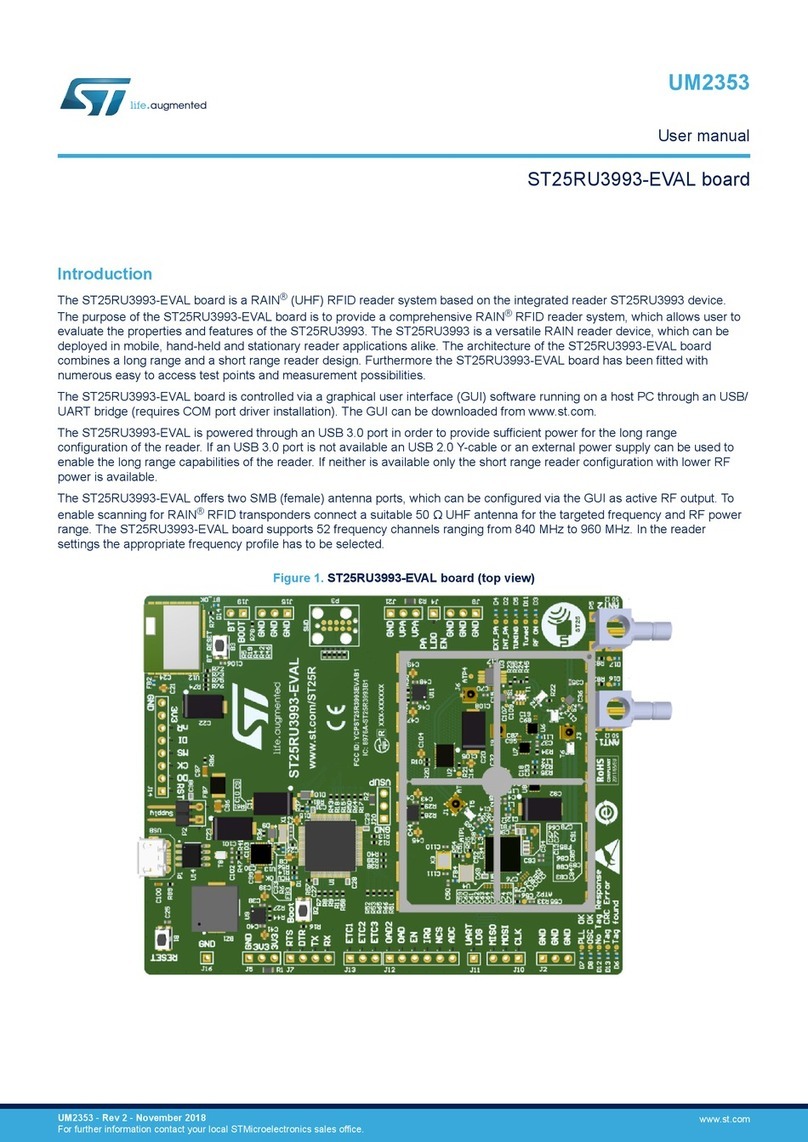
ST
ST ST25RU3993-EVAL User manual
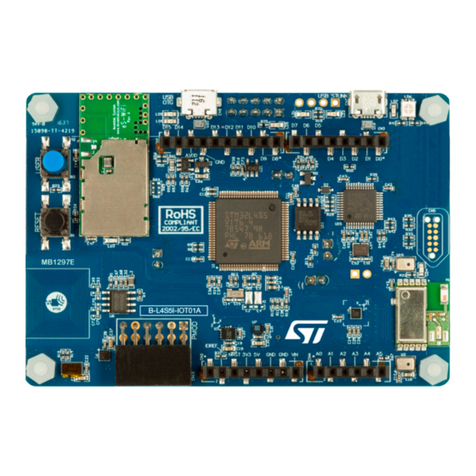
ST
ST B-L4S5I-IOT01A User manual
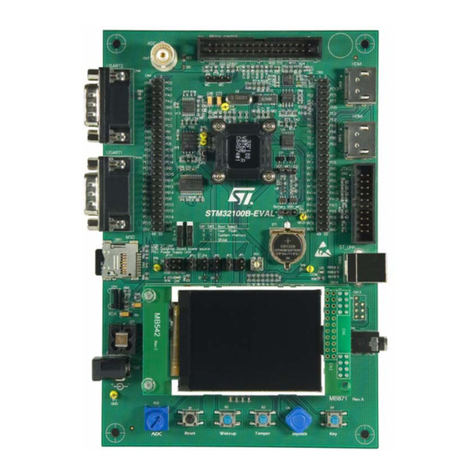
ST
ST STM32100B-EVAL User manual
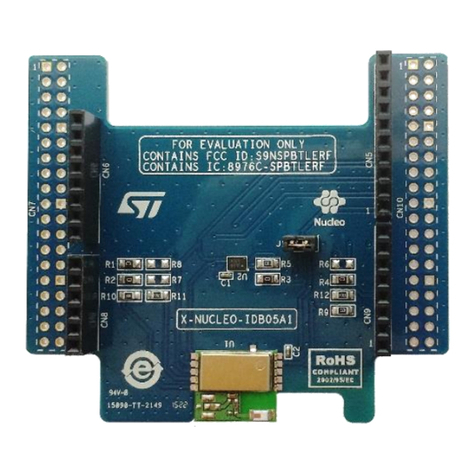
ST
ST X-NUCLEO-IDB05A1 User manual
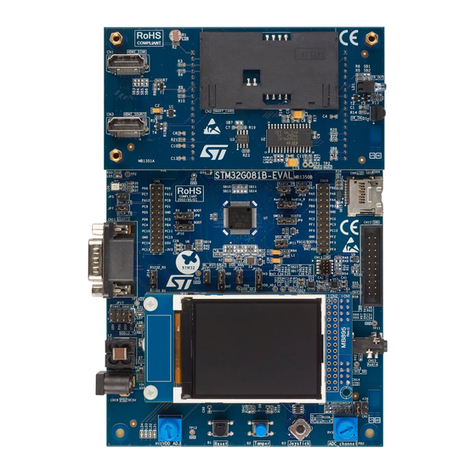
ST
ST STM32G081B-EVAL User manual
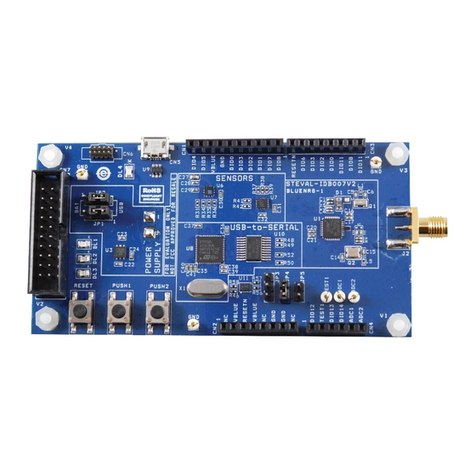
ST
ST STEVAL-IDB007V Series User manual
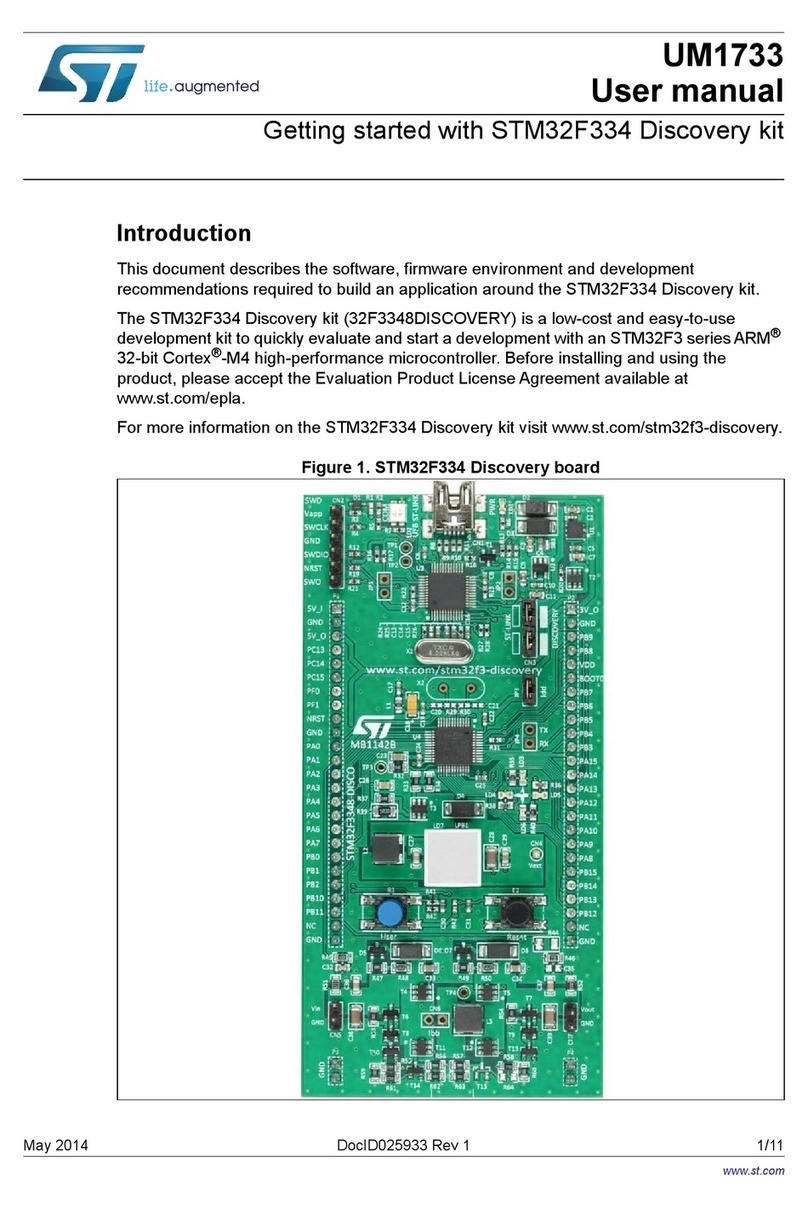
ST
ST STM32F334 User manual
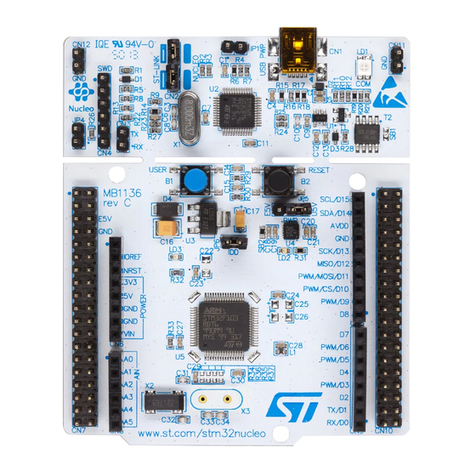
ST
ST Nucleo STM32F302R8 User manual

ST
ST EVAL-L99H02QF User manual
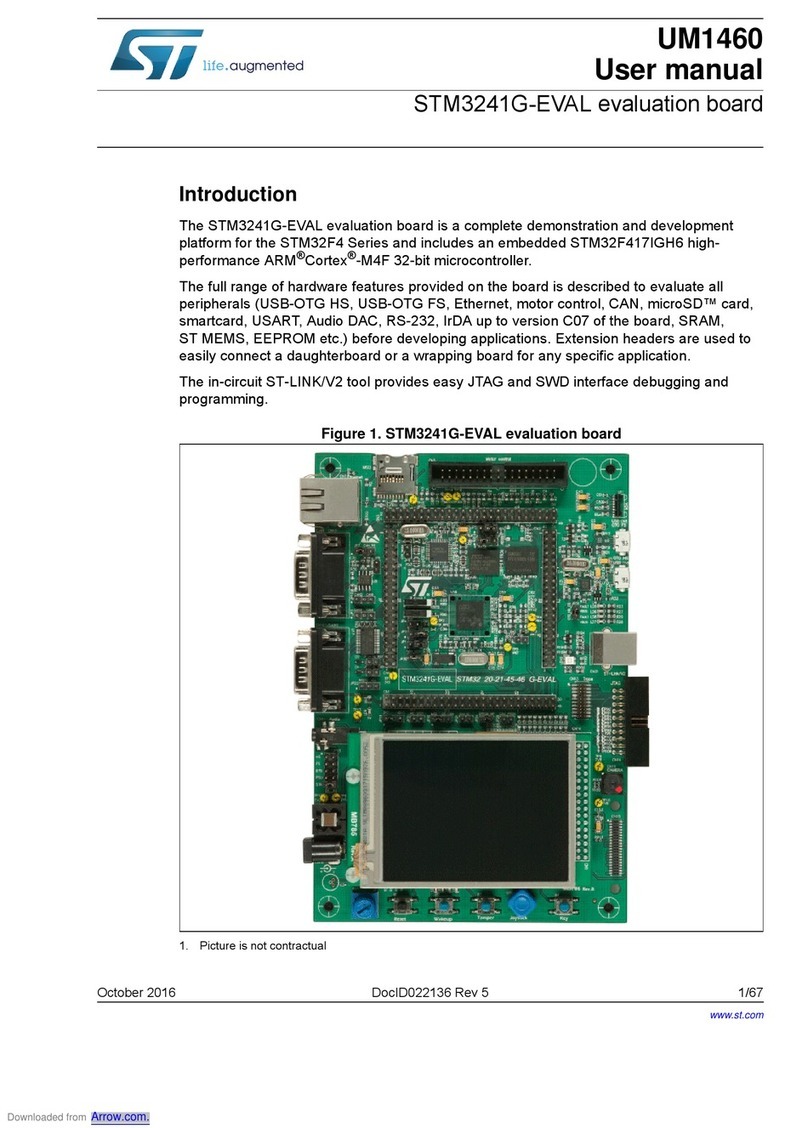
ST
ST STM3241G-EVAL User manual
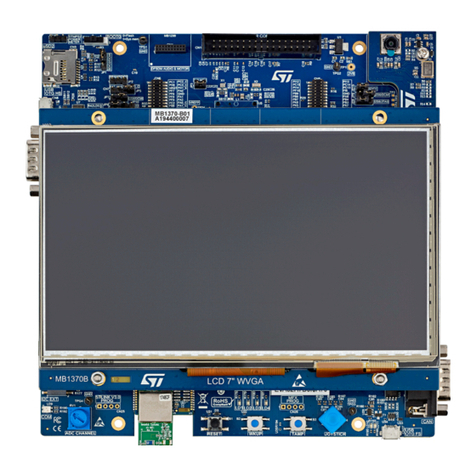
ST
ST STM32H7B3I-EVAL User manual
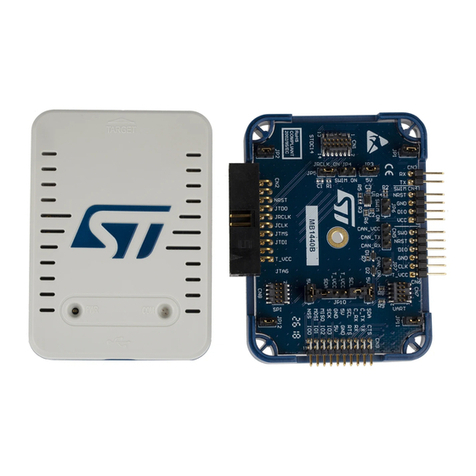
ST
ST STLINK-V3SET User manual
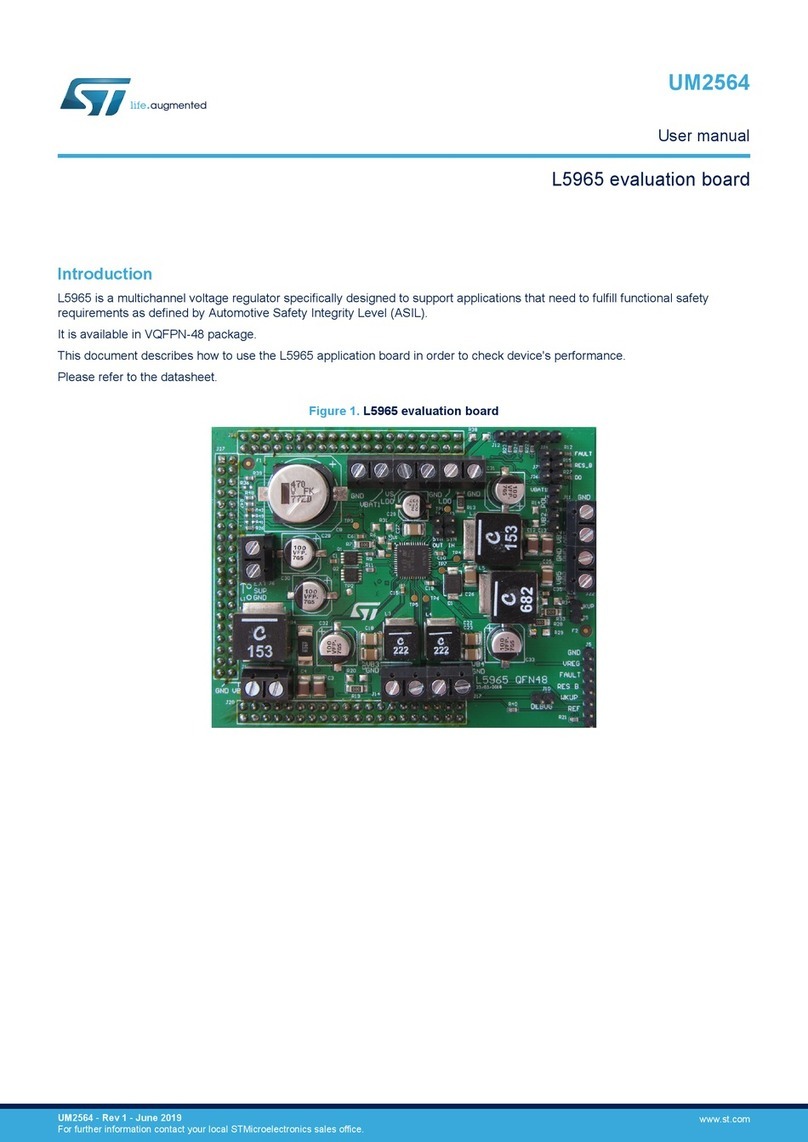
ST
ST L5965 User manual
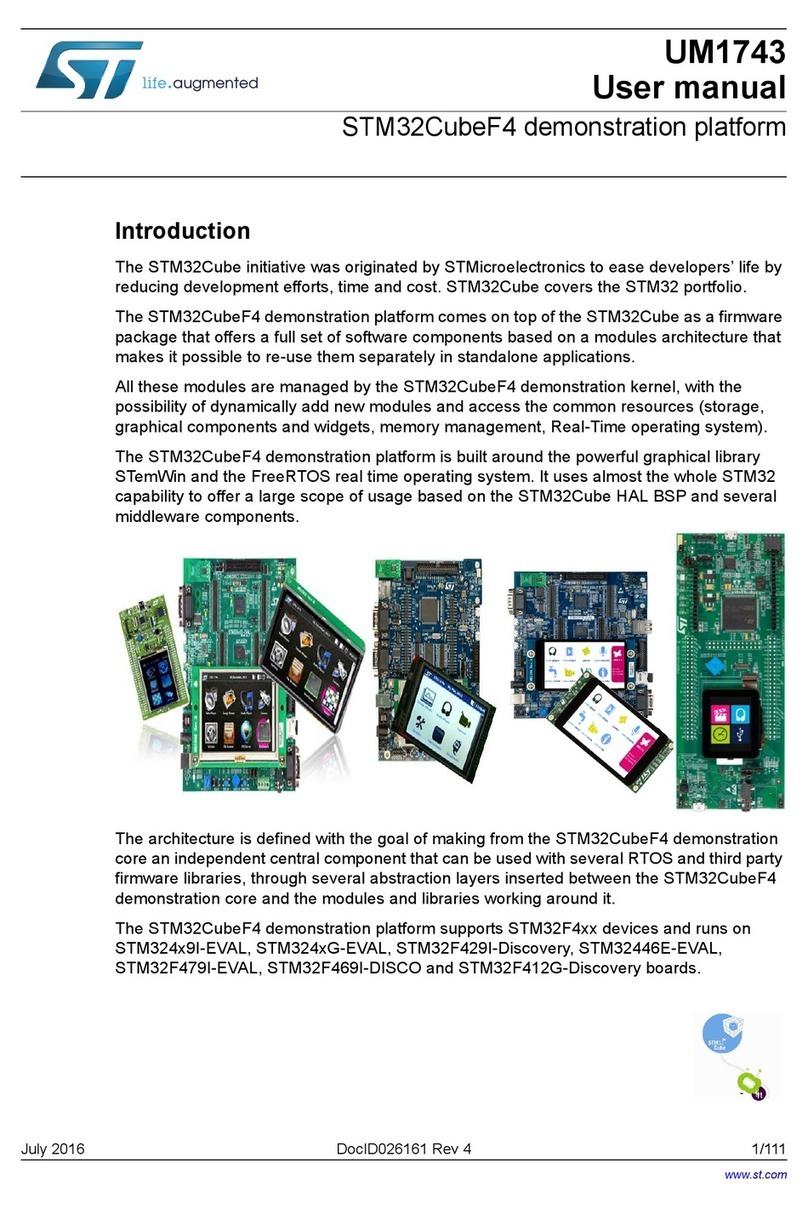
ST
ST STM32CubeF4 User manual
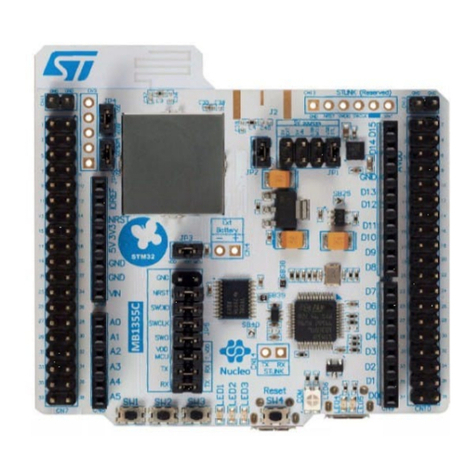
ST
ST ST25DV-I2C User manual

ST
ST VIPower VIPer22A-E Installation and operating instructions
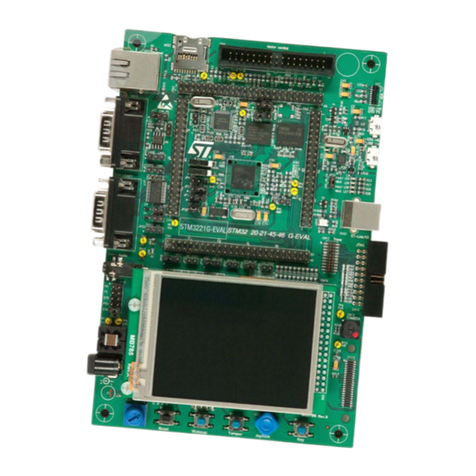
ST
ST STM3221G-EVAL User manual
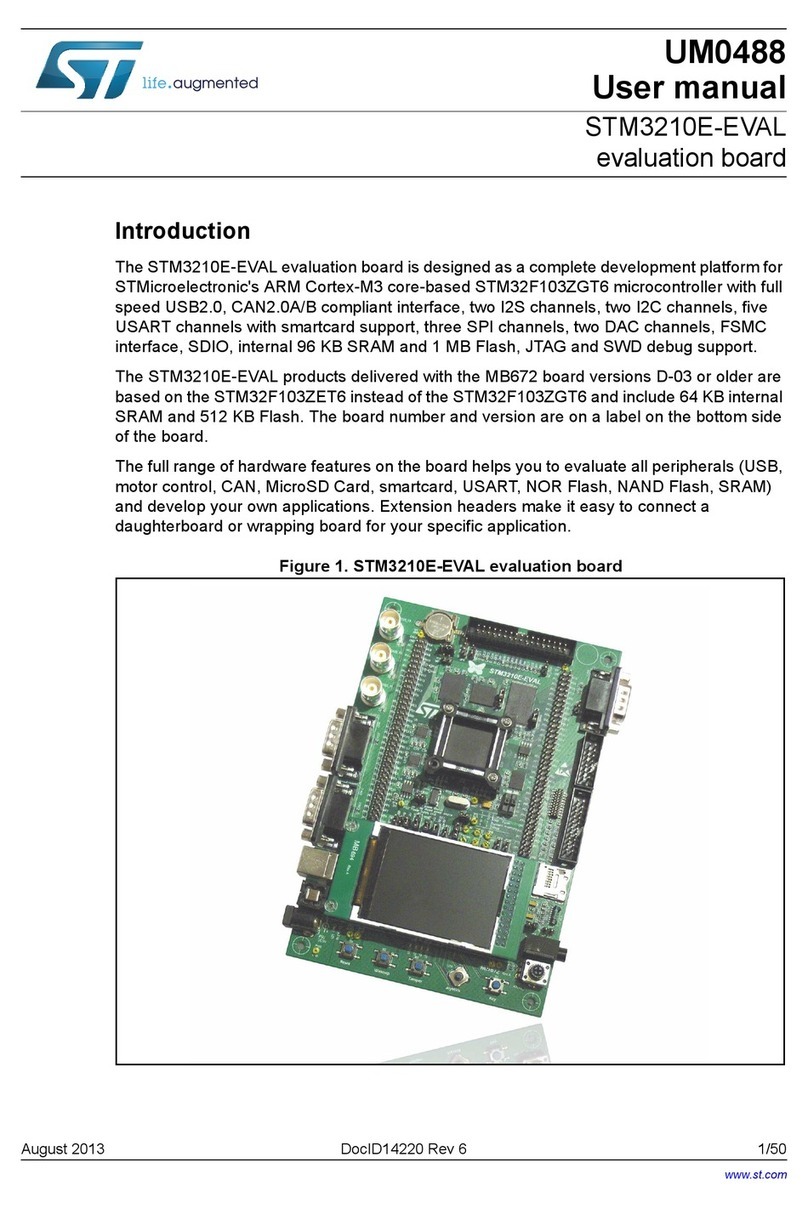
ST
ST STM3210E-EVAL User manual
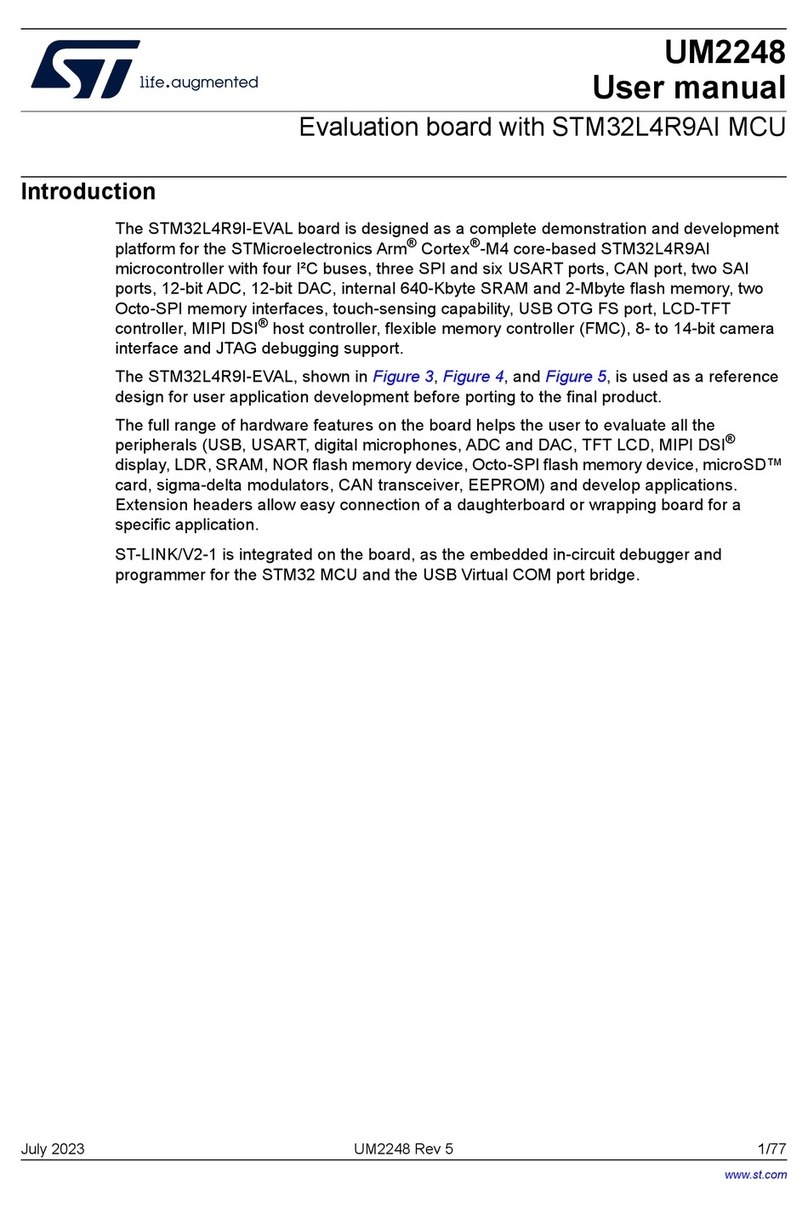
ST
ST STM32L4R9I User manual