ST STM32H7B3I-EVAL User manual

Introduction
The STM32H7B3I-EVAL Evaluation board is a complete demonstration and development platform for the Arm® Cortex®-M7-
based STM32H7B3LIH6QU microcontroller. The STM32H7B3I-EVAL Evaluation board provides access to all the STM32
peripherals for user applications, and includes an embedded STLINK-V3E debugger/programmer.
The full range of the STM32H7B3I-EVAL hardware features helps to develop applications and evaluate all the peripherals, such
as USB OTG_HS and FS, CAN FD, USART, ADC and DAC, digital microphones, SRAM, SDRAM, NOR Flash memory, Octo-
SPI Flash memory with OTFDEC, microSD™ 3.0 card, 7" 800x480 WVGA TFT color RGB LCD with capacitive touch panel
(I2C), and DCMI camera.
The expansion connectors provide an easy way to add specialized features, while ETM trace is supported through external
probes.
Figure 1. STM32H7B3I-EVAL Evaluation board (top view)
Picture is not contractual.
Evaluation board with STM32H7B3LI MCU
UM2662
User manual
UM2662 - Rev 1 - February 2020
For further information contact your local STMicroelectronics sales office. www.st.com

1Features
• STM32H7B3LIH6QU Arm® Cortex® microcontroller with 2 Mbytes of Flash memory and 1.4 Mbytes of RAM
in TFBGA225 package
• 7" 800x480 WVGA TFT color LCD module with RGB parallel interface and capacitive touch panel with I2C
interface
• 1/4" color CMOS QSXGA (5 Mpixels) camera module with DCMI and I2C interface
• USB OTG_HS and USB OTG_FS
• On-board current measurement
•I2S / SAI audio codec
• 512-Mbit Octo-SPI NOR Flash, 8 Mx32bit SDRAM, 1 Mx16bit SRAM, and 8 Mx16bit NOR Flash
• 4 color user LEDs
• Reset, Wake Up and Tamper push-buttons
• 4-direction joystick with a selection button
• Potentiometer
• Coin-battery cell holder for power backup
• Power-metering and temperature-monitoring demonstration with 2 dual-channel, sigma-delta modulators
•Wi-Fi® module compliant with 802.11 b/g/n
• Board connectors:
– 2 USB Micro-AB
– 2 microSD™ cards
– OCSPI NOR Flash module connector
– Stereo Line OUT headset jack including analog microphone input
– Stereo Line IN headset jack
– 2xDB9 for external RS-232 port and CAN FD
– JTAG and ETM trace debugger
– Connectors for ADC and DAC
– I/O expansion connectors
– DFSDM microphones daughterboard expansion connector
– Motor-control interface expansion connector
– I2C expansion connector
• Flexible power-supply options: ST-LINK, USB VBUS or external sources
• On-board STLINK-V3E debugger/programmer with USB re-enumeration capability: mass storage, Virtual
COM port, and debug port
• Comprehensive free software libraries and examples available with the STM32Cube MCU Package
• Support of a wide choice of Integrated Development Environments (IDEs) including IAR™, Keil®, and GCC-
based IDEs
Note: Arm is a registered trademark of Arm Limited (or its subsidiaries) in the US and/or elsewhere.
UM2662
Features
UM2662 - Rev 1 page 2/95

2Ordering information
To order the STM32H7B3I-EVAL Evaluation board, refer to Table 1. For a detailed description, refer to its user
manual on the product web page. Additional information is available from the datasheet and reference manual of
the target STM32.
Table 1. List of available products
Order code Board references Target STM32
STM32H7B3I-EVAL
• MB1331
• MB1370(1)
• MB1379(2)
• MB1486(3)
STM32H7B3LIH6QU
1. LCD board
2. Camera module
3. Wi-Fi® module
2.1 Product marking
Evaluation tools marked as “ES” or “E” are not yet qualified and therefore not ready to be used as reference
design or in production. Any consequences deriving from such usage will not be at ST charge. In no event, ST will
be liable for any customer usage of these engineering sample tools as reference designs or in production.
“E” or “ES” marking examples of location:
• On the targeted STM32 that is soldered on the board (For an illustration of STM32 marking, refer to the
STM32 datasheet “Package information” paragraph at the www.st.com website).
• Next to the evaluation tool ordering part number that is stuck or silk-screen printed on the board.
This board features a specific STM32 device version, which allows the operation of any bundled commercial
stack/library available. This STM32 device shows a "U" marking option at the end of the standard part number
and is not available for sales.
In order to use the same commercial stack in his application, a developer may need to purchase a part number
specific to this stack/library. The price of those part numbers includes the stack/library royalties.
2.2 Codification
The meaning of the codification is explained in Table 2. The order code is mentioned on a sticker placed on the
top or bottom side of the board.
Table 2. Codification explanation
STM32TTXXY-EVAL Description Example: STM32H7B3I-EVAL
STM32TT MCU series in STM32 32-bit Arm Cortex MCUs STM32H7 Series
XX MCU product line in the series STM32H7B3
YSTM32 Flash memory size:
• I for 2 Mbytes 2 Mbytes
UM2662
Ordering information
UM2662 - Rev 1 page 3/95

3Development environment
3.1 System requirements
• Windows® OS (7, 8 and 10), Linux® 64-bit, or macOS®
• USB Type-A to Micro-B cable
Note: macOS® is a trademark of Apple Inc. registered in the U.S. and other countries.
All other trademarks are the property of their respective owners.
3.2 Development toolchains
• IAR™ - EWARM (see note)
• Keil® - MDK-ARM (see note)
• GCC-based IDEs
Note: On Windows® only.
3.3 Demonstration software
The demonstration software, included in the STM32Cube MCU Package corresponding to the on-board
microcontroller, is preloaded in the STM32 Flash memory for easy demonstration of the device peripherals in
standalone mode. The latest versions of the demonstration source code and associated documentation can be
downloaded from www.st.com.
UM2662
Development environment
UM2662 - Rev 1 page 4/95

4Conventions
Table 3 provides the conventions used for the ON and OFF settings in the present document.
Table 3. ON/OFF convention
Convention Definition
Jumper JPx ON Jumper fitted
Jumper JPx OFF Jumper not fitted
Jumper JPx [1-2] Jumper should be fitted between Pin 1 and Pin 2
Solder bridge SBx ON SBx connections closed by 0 Ω resistor
Solder bridge SBx OFF SBx connections left open
Resistor Rx ON Resistor soldered
Resistor Rx OFF Resistor not soldered
UM2662
Conventions
UM2662 - Rev 1 page 5/95

5Delivery recommendations
Some verifications are needed before using the board for the first time to make sure that nothing was damaged
during shipment and that no components are unplugged or lost. When the board is extracted from its plastic bag,
check that no component remains in the bag. Before starting the demo, take the microSD™ card from the
separated ESD bag and plug it in the connector CN28, on the right side of the board.
Warning:
There is an explosion risk if the battery is replaced by an incorrect one. Make sure to dispose of
used batteries according to the instructions.
UM2662
Delivery recommendations
UM2662 - Rev 1 page 6/95

6Hardware layout and configuration
The STM32H7B3I-EVAL Evaluation board is designed around the STM32H7B3LIH6QU target microcontroller.
Figure 2 illustrates STM32H7B3LIH6QU connections with peripheral components.
Figure 2. Hardware block diagram
3V3 Power Supply
(3V3_AO)
LED, push-button, and wake-up
External USB
HS PHY
MIcro-AB
USB
connector
Wi-Fi® module
GPIOs
OTG HS (ULPI)
OTG FS
UART + SPI +
GPIOs
VCP UART
SWD
VBAT
LSE
LCD
Reset
FMC
SDIO 1
SDIO 2
I2C
SAI1 or I2S6
and / or
differential ADC
GPIO, I2C, INT
Audio codec
CS42L51-CNZ
3 V battery
32 KHz crystal
RK070ER9427L
RGB - 7 INCH –
WVGA
LCD + CTP
MB1370 module
8 Mx32bit SDRAM
8 Mx16bit NOR Flash
microSDTM
card 2.0
(3V3)
microSDTM
card 3.0
(3V3 / 1V8) STM32L152CCT6
MFX GPIO Expander
Stereo jack
(line-out)
STM32F723IEK6
STLINK V3.0
Micro-B
USB
connector
MB1299 Module
1 Mx16bit SRAM
HSE
24 MHz crystal
Reset button
OCSPI 2
OCSPI
connector
OCSPI 1
MX25LM51245GXDI00
OCSPI DFSDM1 and 2
DFSDM
ADC Potentiometer
ADCs, PWMs,
GPIOs,
DFSDM
Motor-control
connector
CAN, CAN FD,
and bootloader
RS-232
DB9
connectors
GPIOs Extension
connectors
DCMI
Camera
module
connector
DFSDM
connector
MB1242
OCSPI module
microSDTM
card
connector
3V3_SW
LDO
3V3_SW
MB1379
camera module
Micro-AB
USB
connector
LCD +
CTP
connector
STM32H7B3LIH6QU
VDDMMC
MFX IO0
VDDMMC 1V8_SW
LDO
1V8_SW
GPIO
MFX IO8
ON/OFF
ON/OFF
SEL
microSDTM
card
connector
Note: Interfaces in blue are partially supplied by VDDMMC. Refer to Section 6.3.5 .
UM2662
Hardware layout and configuration
UM2662 - Rev 1 page 7/95

Figure 3 shows the location of the main components on the top side of the Evaluation board.
Figure 3. STM32H7B3I-EVAL Evaluation board layout
CN9: UART RS-232 connector
CN3: microSD™ connector
CN8: USB HS connector
JP29: 5 V selection
CN17: 5 V DC jack
CN21: ST-LINK USB connector
U21: MCU STLINK-V3
CN24: EXT I2C connector
LD9: ST-LINK COM LED
CN12/CN13: Extension connectors
U11: Octo-SPI Flash
CN5/CN6: Extension connectors
RV1: ADC potentiometer
U12: NOR Flash
U16: SDRAM
U17: SRAM
JPME1: Power meter connector
U5: STM32H7B3LIH6QU
U24: Wi-Fi® module
SW1: BOOT0 switch
CN4: MB1299 DFSDM microphones module connector
B1: Reset button
B2: Wake-up button
CN10/CN11: MB1242 Octo-SPI module connector
CN2: MB1379 camera module connector
CN1: Motor-control connector
CN28: microSD™ connector (bottom)
CN15: ETM trace connector
CN14: JTAG connector
CN16: MIPI-10 connector
U48: Audio codec (bottom)
CN18: Audio stereo output jack
CN20: Audio stereo input jack
CN22: CANFD connector
U25: I/O expander
CN23: MB1370 LCD module RGB connector
CN30: MB1370 LCD module CTP connector
LD1/LD2/LD3/LD4: User LEDs
CN27: USB FS connector
B4: Joystick
B3: Tamper button
CN29: Battery connector (bottom)
UM2662
Hardware layout and configuration
UM2662 - Rev 1 page 8/95

There are two different ways to program and debug the onboard STM32 MCU:
• Using the embedded STLINK-V3E
• Using an external debug tool
6.1 Embedded STLINK-V3E
6.1.1 Description
The STLINK-V3E programming and debugging tool is integrated into the STM32H7B3I-EVAL Evaluation board.
The embedded STLINK-V3E supports:
• 5 V power supplied by the CN21 USB connector
• USB 2.0 high-speed-compatible interface
• JTAG and serial wire debugging (SWD) specific features:
– 3 to 3.6 V application voltage on the JTAG/SWD interface and 5V tolerant inputs
– JTAG
– SWD and serial viewer (SWV) communication
• Direct firmware update feature (DFU) (CN25)
• MIPI10 compatible connector (CN16)
• Status COM LED (LD9) which blinks during communication with the PC
• Fault red LED (LD8) alerting on USB overcurrent request
• 5 V / 500 mA output power supply capability (U19) with current limitation
• 5 V enabled green LED (LD7)
6.1.2 How to use
It is very easy to use STLINK-V3E to program and debug the on-board STM32.
1. Verify that the jumper JP29 of Power Supply Sources is correctly set. (Refer to Table 9).
2. Connect the board to a PC with a USB Type-A to Micro-B cable through the USB connector CN21.
Note: For more details regarding the STLINK-V3E functionalities, refer to the STLINK-V3E user manual on the
www.st.com website.
UM2662
Embedded STLINK-V3E
UM2662 - Rev 1 page 9/95

6.1.3 Drivers
Before connecting the STM32H7B3I-EVAL board to a Windows PC via USB, the user must install a driver for the
STLINK-V3E (not required for Windows 10). It is available on the www.st.com website.
In case the STM32H7B3I-EVAL board is connected to the PC before the driver is installed, some STM32H7B3I-
EVAL interfaces may be declared as “Unknown” in the PC device manager. In this case, the user must install the
dedicated driver files, and update the driver of the connected device from the device manager as shown in
Figure 4.
Note: Prefer using the USB Composite Device handle for a full recovery.
Figure 4. USB composite device
Note: 37xx:
• 374E for STLINK-V3E without bridges functions
• 374F for STLINK-V3E with bridges functions
6.1.4 STLINK-V3E firmware upgrade
The STLINK-V3E embeds a firmware upgrade mechanism for in-situ upgrades through the USB port. As the
firmware may evolve during the lifetime of the STLINK-V3E product (For example new functionalities, bug fixes,
support for new microcontroller families), it is recommended to visit the www.st.com website before starting to use
the STM32H7B3I-EVAL Evaluation board and periodically, to stay up-to-date with the latest firmware version.
6.1.5 Interface
STLINK-V3E programming connector CN25
The connector CN21 is used only for embedded STLINK-V3E programming during board manufacturing. It is not
populated by default and not for the end-user.
STLINK-V3E USB Type B connector CN21
The USB Micro-B connector CN21 is used to connect embedded STLINK-V3E to PC for debugging of the board.
UM2662
Embedded STLINK-V3E
UM2662 - Rev 1 page 10/95

6.2 External JTAG, SWD, and trace
6.2.1 Description
There are two basics ways to support an external debug tool. If the user encounters any trouble with the first
procedure, then the second one is mandatory.
1. Keep the embedded STLINK-V3E running. Power on the STLINK-V3E at first until the COM LED lights RED.
Then connect the external Debug tool through connector CN14, CN15 or CN16.
2. Set the embedded STLINK-V3E in a high impedance state. When the Jumper CN19 (STLK NRST) is ON,
the embedded STLINK-V3E is in RESET state and all GPIOs are in high impedance; then the user can
connect his external Debug tool on the DEBUG connector CN14, CN15, or CN16 (Refer to Figure 5).
Note: Depending on the design requirement, the embedded STLINK-V3E hardware may be completely disconnected if
that is required early in the project.
Figure 5. External debug tools connectors
Remarks:
• It is possible to power the board via CN21 (Embedded STLINK-V3E USB connector) even if an external tool
is connected to CN15 (ETM trace connector) or CN14 (External JTAG and SWD connector).
• ETM can only work at 50 MHz clock frequency by default because ETM signals are shared with other
peripherals.
UM2662
External JTAG, SWD, and trace
UM2662 - Rev 1 page 11/95

6.2.2 Limitations and hardware configuration - ETM trace (CN15)
Limitations: Wi‑Fi®, LCD, SAI, FMC A19-22 cannot be used at the same time as TRACE.
If the best performance of ETM is required (84 MHz/98 MHz), refer to Table 4. ETM trace hardware configuration.
Table 4. ETM trace hardware configuration
Signal name Pin name Setting JTAG / TRACE(1)
WIFI_SPI4_SCK
PE2
R343 OFF(2)
FMC_A23 R342 OFF(2)
TRACECLK R101 ON
WIFI_SPI4_NSS
PE3
R337 OFF(2)
SAI1_SD_B JP34 OFF(2)
FMC_A19 R97 OFF(2)
JTAG_TDO (PB3) R390 OFF(2)
TRACED0 R93 ON
SAI1_FS_A
PE4
JP26 OFF(2)
FMC_A20 R88 OFF(2)
JTAG_TRST (PB4) R372 OFF(2)
DCMI_D4 R116 OFF(2)
TRACED1 R340 ON
WIFI_SPI4_MISO
PE5
R69 OFF(2)
SAI1_SCK_A JP28 OFF(2)
FMC_A21 R324 OFF(2)
TRACED2 R71 ON
WIFI_SPI4_MOSI
PE6
R334 OFF(2)
SAI1_SD_A JP27 OFF(2)
FMC_A22 R78 OFF(2)
TRACED3 R80 ON
RGB_LCD_G0 PJ7 R315 OFF(2)
TRGIN R64 ON
RGB_LCD_B0 PJ12 R259 OFF(2)
TRGOUT R34 ON
1. Trace configuration is in bold.
2. Remove to avoid stub if necessary.
Remark:
• R69 must be removed to avoid conflict with the WIFI_SPI4_MISO output, but it is also recommended to
remove R343, R337, R116, and R334 to have the best signal quality. With these changes, ETM trace 4-bits
is successfully tested in DDR with the ULINK PRO up to 108MHz (CPU at 280 MHz) but the timing of the
data [3:0] sampling must be adjusted on the ULINK pro: CLK: +0 ns (no change) / D [3:0]: ~ 2.5 ns.
UM2662
External JTAG, SWD, and trace
UM2662 - Rev 1 page 12/95

6.2.3 Limitations and hardware configuration - JTAG (CN14) or MIPI10 (CN16)
Limitations: STM32H7B3LIH6QU JTAG cannot be connected at the same time to STLINK-V3E and to CN14 or
CN16 connector. To be able to use JTAG on CN14 or CN16 connector, it is necessary to disconnect JTAG signals
from STLINK-V3E (JTMS, JTCK, JTDO, and NRST).
• To do so, R409, R401, R399, and R398 must be removed.
6.2.4 Interface
Figure 6. STDC14 / MIPI10 debugging connector CN16
Table 5. STDC14 / MIPI10 debugging connector CN16
Pin number Description Pin number Description
1 (STDC14) NC 2 NC (STDC14)
3 (MIPI10) +3.3V 4 (MIPI10) SWDIO-TMS / PA13
5 (MIPI10) GND 6 (MIPI10) SWCLK-TCK / PA14
7 (MIPI10) GND 8 (MIPI10) SWO-TDO / PB3
9 (MIPI10) KEY (NC) 10 (MIPI10) TDI / PA15
11 (MIPI10) GNDDetect 12 (MIPI10) RESET#
13 (STDC14) VCP_USART_RX / PB14 or PA2 14 (STDC14) VCP_USART_TX / PB15 or PA3
Table 6. STDC14 / MIPI10 debug connector CN16
MIPI10
pin
STDC14
pin CN16 Designation
- 1 NC Reserved
- 2 NC Reserved
1 3 T_VCC Target VCC
2 4 T_SWDIO Target SWDIO using SWD protocol or Target JTMS (T_JTMS) using JTAG protocol
3 5 GND Ground
4 6 T_SWCLK Target SWCLK using SWD protocol or Target JCLK (T_JCLK) using JTAG protocol
5 7 GND Ground
6 8 T_SWO Target SWO using SWD protocol or Target JTDO (T_JTMS) using JTAG protocol
7 9 KEY (NC) KEY (NC)
8 10 T_JTDI Not used by SWD protocol, Target JTDI (T_JTDI) using JTAG protocol, only for
external tools
9 11 GNDDetect GND detect for plug indicator, used on SWD and JTAG neither
10 12 T_NRST Target NRST using SWD protocol or Target JTMS (T_JTMS) using JTAG protocol
UM2662
External JTAG, SWD, and trace
UM2662 - Rev 1 page 13/95

MIPI10
pin
STDC14
pin CN16 Designation
- 13 T_VCP_RX Target RX used for VCP (must be UART dedicated to Bootloader)
- 14 T_VCP_TX Target TX used for VCP (must be UART dedicated to Bootloader)
Figure 7. ETM trace debugging connector CN15
19
20 18
17 15
16
13
14
11
12 10
9
8
7
6
5
4
3 1
2
Table 7. ETM trace debugging connector CN15
Pin number Description Pin number Description
1 +3.3V 2 TMS/PA13
3 GND 4 TCK/PA14
5 GND 6 TDO/PB3
7 KEY (NC) 8 TDI/PA15
9 GND 10 RESET#
11 GND 12 TraceCLK/PE2
13 GND 14 TraceD0/PE3 or SWO / PB3
15 GND 16 TraceD1/PE4 or nTRST / PB4
17 GND 18 TraceD2 / PE5
19 GND 20 TraceD3 / PE6
UM2662
External JTAG, SWD, and trace
UM2662 - Rev 1 page 14/95

Figure 8. JTAG debugging connector CN14
19
20 18
17 15
16
13
14
11
12 10
9
8
7
6
5
4
3 1
2
Table 8. JTAG / SWD debugging connector CN14
Pin number Description Pin number Description
1 +3.3V 2 +3.3V
3 TRST(PB4) 4 GND
5 TDI(PA15) 6 GND
7 TMS/SWDIO(PA13) 8 GND
9 TCK/SWCLK(PA14) 10 GND
11 RTCK 12 GND
13 TDO/SWO(PB3) 14 GND
15 RESET# 16 GND
17 DBGRQ(PJ7) 18 GND
19 DBGACK(PJ12) 20 GND
UM2662
External JTAG, SWD, and trace
UM2662 - Rev 1 page 15/95

6.3 Power supply
6.3.1 Board power supply description
The STM32H7B3I-EVAL Evaluation board is designed to be powered from 5 V DC power source. It incorporates a
precise polymer Zener diode (Poly-Zen) protecting the board from damage due to the wrong power supply. One of
the following six 5 V DC power inputs can be used, upon an appropriate board configuration:
•5V DC power adapter connected to CN17, the power jack on the board (EXT on the JP29 silkscreen).
This is the default configuration.
• 5V DC power with 500 mA limitation from CN21, the Micro-B USB connector of STLINK-V3E (STLK on the
JP29 silkscreen). As explained below, if the USB enumeration succeeds, the ST-LINK U5V power is
enabled, by asserting the PWR_EN pin. This pin is connected to a power switch U22, which powers the
board. This power switch features also a current limitation to protect the PC in case of short-circuit on board.
If overcurrent (More than 600 mA) happens onboard, the LED LD11 is lit.
• 5V DC power with 500 mA limitation from CN14, the USB OTG HS Micro-AB connector (HS on the HJP29
silkscreen)
• 5V DC power with 500 mA limitation from CN27, the USB OTG FS Micro-AB connector (FS on the JP29
silkscreen)
• 5V DC power from CN5 and CN6, the extension connectors for daughterboard (D on the JP29 silkscreen)
• 5V DC power without limitation from CN21, the Micro-B USB connector of STLINK-V3E (CHGR on the JP29
silkscreen)
The STM32H7B3I-EVAL Evaluation board can be powered from ST-LINK USB connector CN21 (“STLK”), but only
the ST-LINK circuit has the power before USB enumeration, for the host PC only provides 100 mA to the boards
at that time. During the USB enumeration, the STM32H7B3I-EVAL board asks for the 500 mA power to the Host
PC.
• If the host is able to provide the required power, the enumeration succeeds, the power transistor U22 is
switched ON, the green LED LD7 is turned ON, thus the STM32H7B3I-EVAL board is powered and can
consume a maximum current of 500 mA current, but not more.
• If the host is not able to provide the requested current, the enumeration fails. Therefore, the power switch
(U22) remains OFF, so consequently, 3.3 V domain of the board and MCU are not powered. As a
consequence, the green LED LD7 remains turned OFF. In this case, it is mandatory to use an external
power supply as an extra power supply.
“EXT” from PSU or “D” can be used as an external power supply in case current consumption of the
STM32H7B3I-EVAL board exceeds the allowed current on USB. In this condition, it is still possible to use USB for
communication for programming or debugging only, but it is mandatory to power the board first using E5V or D5V,
and then connecting the USB cable to the PC. Proceeding this way ensures that the enumeration succeeds
thanks to the external power source.
The following power sequence procedure must be respected:
1. Connect jumper JP29 to EXT or D side.
2. Connect the external power source to EXT or D (With mounted daughterboard).
3. Check green LED LD7 is turned ON.
4. Connect the PC to USB connector CN21.
If this order is not respected, the board may be powered by VBUS first then “EXT” or “D”, and the following risks
may be encountered:
1. If more than 500 mA current is needed by the board, the PC may be damaged or current can be limited by
PC. As a consequence, the board is not powered correctly.
2. 500 mA is requested at enumeration, so there is a risk that request is rejected and enumeration does not
succeed if PC cannot provide such current. Consequently, the board is not powered and LED LD7 remains
OFF.
UM2662
Power supply
UM2662 - Rev 1 page 16/95

6.3.2 Board power supply - Hardware configuration
The power supply is configured by setting the related jumpers JP3, JP29 and JP37 as described in Table 9.
Table 9. Power related jumpers
Jumper Description(1)
JP3 JP3 is used to measure current consumption manually with a multimeter.
ON
JP29
JP29 is used to select one of the six possible power supply resources:
For power supply from USB connector of STLINK-V3E (CN21) to
STM32H7B3I-EVAL, JP29 is set as shown on the right.
For power supply jack(CN17) to the STM32H7B3I-EVAL,
JP29 is set as shown on the right.
For power supply from USB OTG HS (CN14) to STM32H7B3I-EVAL,
JP29 is set as shown on the right.
For power supply from USB OTG FS (CN27) to STM32H7B3I-EVAL,
JP29 is set as shown on the right.
For power supply from the daughterboard connectors (CN5 and CN6)
to STM32H7B3I-EVAL, JP29 is set as shown on the right.
For power supply from a USB wall charger plugged to CN21
to STM32H7B3I-EVAL, JP29 is set as shown on the right.
UM2662
Power supply
UM2662 - Rev 1 page 17/95

Jumper Description(1)
JP29
For power supply from power supply jack (CN17) to both STM32H7B3I-EVAL and the
daughterboard connected on CN5 and CN6, JP29 is set as shown on the right.
The daughterboard must not have its own power supply connected.
JP37
Vbat is connected to +3.3V when JP37 is set as shown on the right.
Vbat is connected to the battery when JP37 is set as shown on the right.
1. The default setting is in bold.
The LED LD7 is lit when the STM32H7B3I-EVAL Evaluation board is powered by the 5V correctly.
Note: In order to avoid the impact of USB PHY and get precise results of current consumption on JP3, the following
caution must be taken into account.
1. Configure USB HS PHY into Low Power Mode (Register Address=04, bit 6 in USB PHY).
The STM32H7B3I-EVAL Evaluation board can be powered from a DC 5V power supply via the external power
supply jack (CN17) shown in Figure 9. The central pin of CN17 must be positive.
Figure 9. Power supply connector CN17
DC +5V
GND
UM2662
Power supply
UM2662 - Rev 1 page 18/95

6.3.3 Board power supply - SMPS / LDO configuration
Figure 10. MCU Power : SMPS / LDO
STM32H7B3I-EVAL supports four “SMPS / LDO” configurations of the STM32H7B3LIH6QU microcontroller
described in Table 10:
1. LDO supply only
2. SMPS supply only (Default configuration)
3. SMPS and LDO supplies cascaded
4. SMPS and LDO supplies (SMPS supplies 1V8 to board as well)
Some PCB reworks are needed to change power configuration as shown in Table 10:
Table 10. Internal SMPS / LDO and board configuration
Signal name Setting Supply config 1:
LDD only
Supply config 2:
SMPS only(1)
Supply config 3:
SMPS and LDO
cascaded
Supply config 4:
external SMPS
-Figure 11 Figure 12 Figure 13 Figure 14
SMPS OFF ON ON ON
LDO ON OFF ON ON
3V3_MCU = VDD_LDO SB37 X - - -
VFBSD = GND R251 X - - -
3V3_SMPS_IN = GND SB10 X - - -
3V3_MCU = 3V3_SMPS_IN R22 X XX X
VDD_SMPS_IND_OUT = VDD_LDO SB3 - XX X
VDD_SMPS_IND_OUT = VCAP SB5 - X- -
VCAP capacitor C121 2.2 uF 100 nF 2.2 uF 2.2 uF
VCAP capacitor C126 2.2 uF 100 nF 2.2 uF 2.2 uF
VFBSD = VCAP R263 - X- -
VFBSD = VDD_LDO R262 - - X X
VDD_SMPS_IND_OUT = 1V8_AO SB4 - - - X
1V8_AO capacitor C21 - - - X
1. The default setting is in bold.
UM2662
Power supply
UM2662 - Rev 1 page 19/95

Figure 11. Config1 - LDO only
Figure 12. Config2 - SMPS only (Default configuration)
UM2662
Power supply
UM2662 - Rev 1 page 20/95
Table of contents
Other ST Motherboard manuals
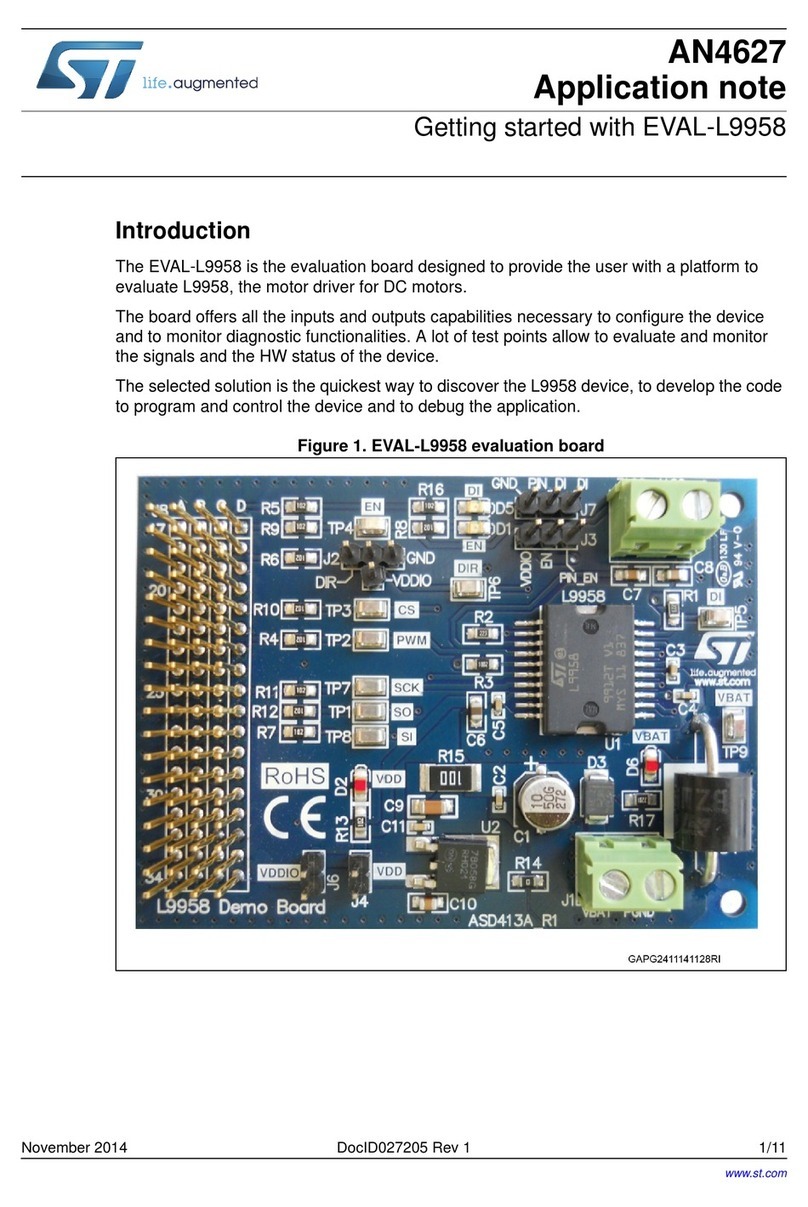
ST
ST EVAL-L9958 User manual
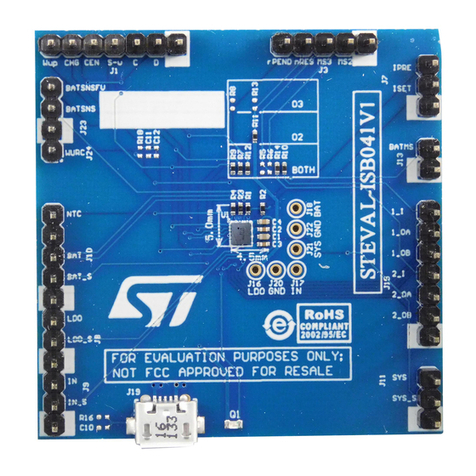
ST
ST STEVAL-ISB041V1 User manual
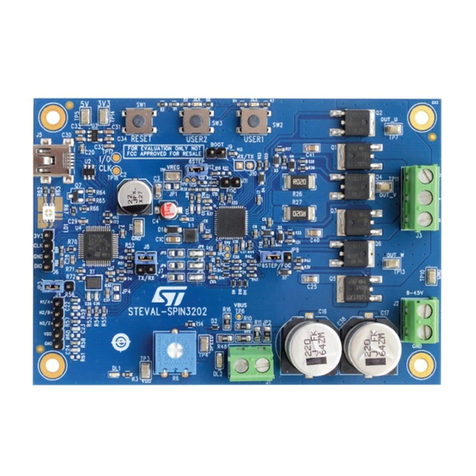
ST
ST STEVAL-SPIN3202 User manual

ST
ST STEVAL-PTOOL2V1 User manual
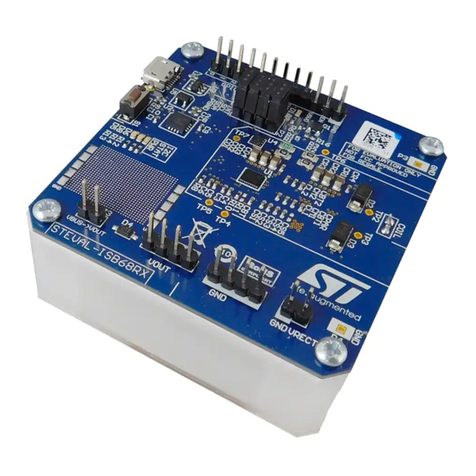
ST
ST STEVAL-ISB68RX User manual
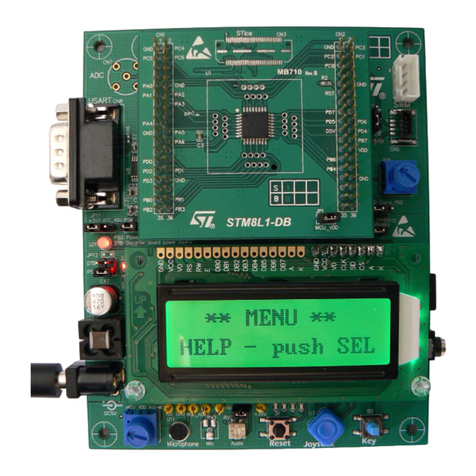
ST
ST STM8L101-EVAL User manual
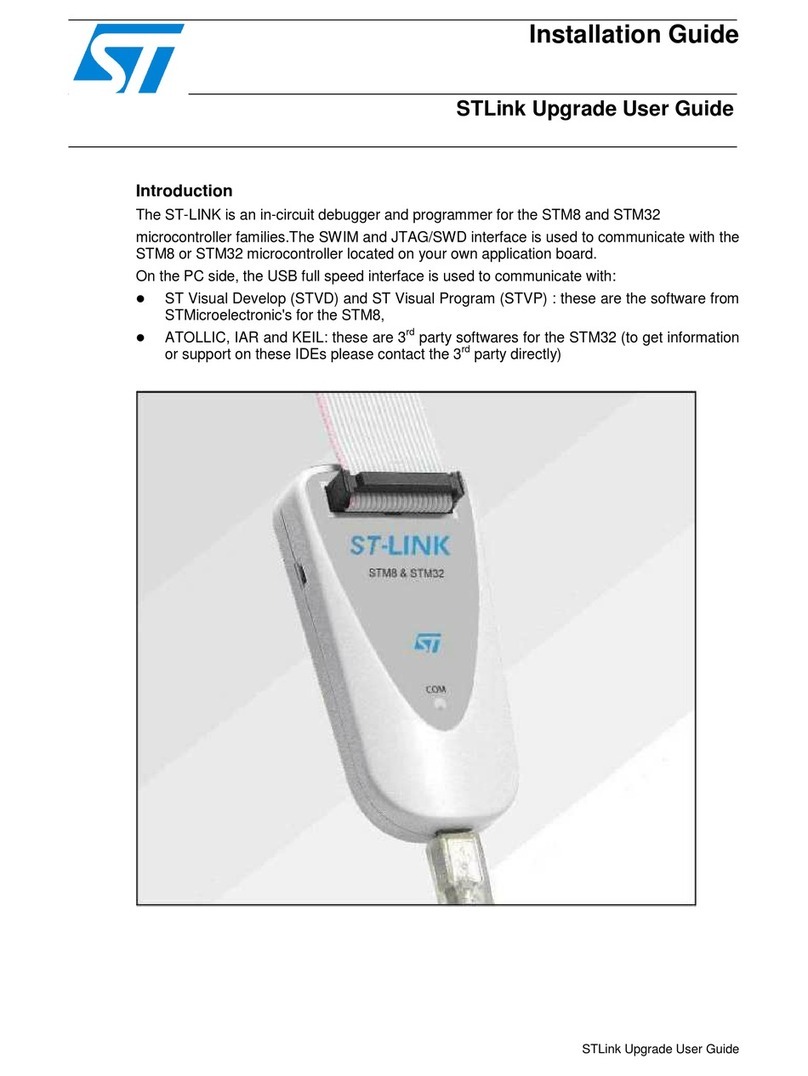
ST
ST STLink User manual
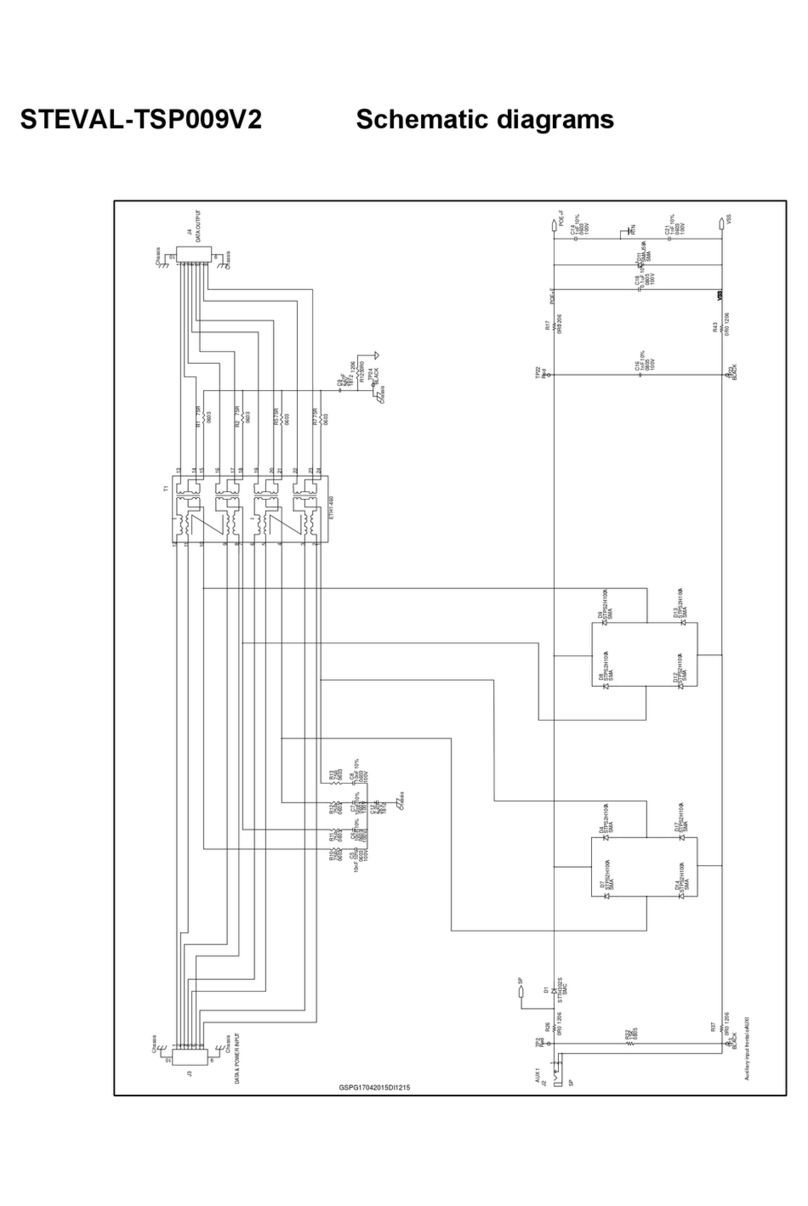
ST
ST STEVAL-TSP009V2 Administrator Guide
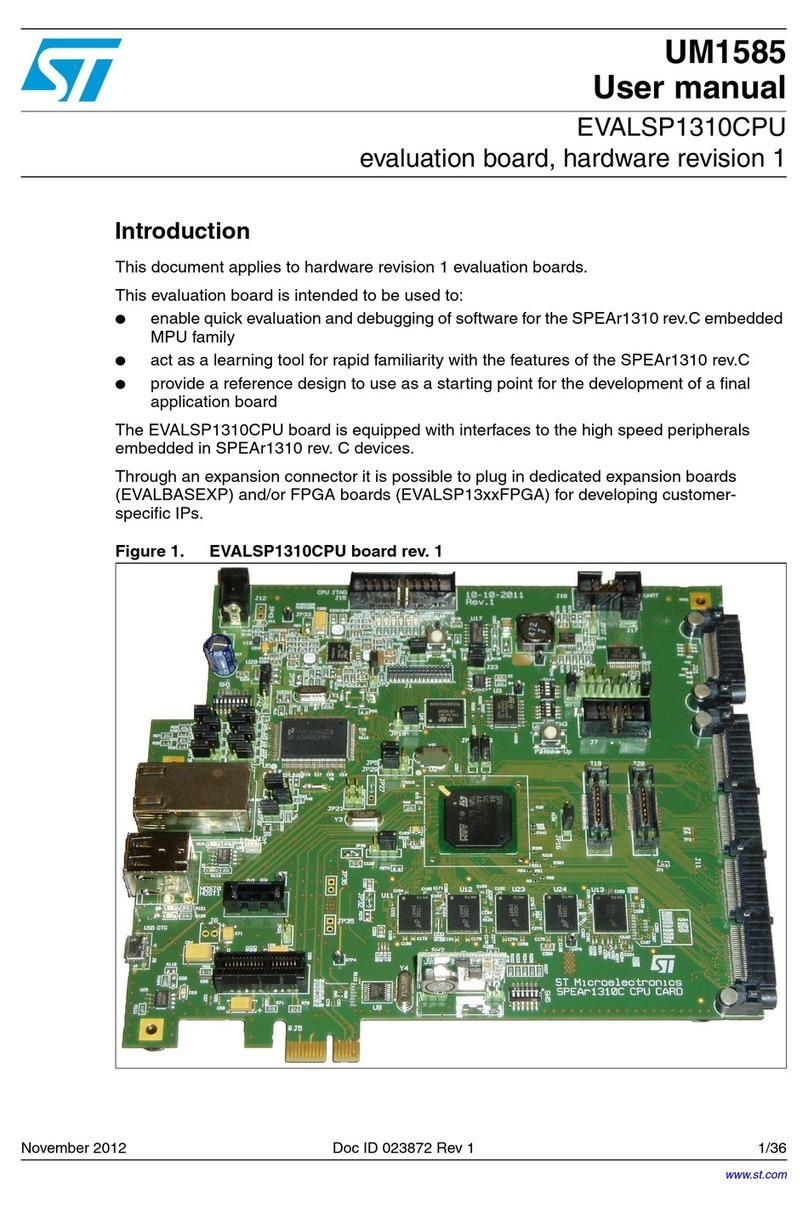
ST
ST EVALSP1310CPU User manual

ST
ST EnFilm EFL1K0AF39 User manual