Swegon P.LEMMENS TAC4 DG User manual

TAC4 DG + RC


TAC4 DG + RC
Installation and user’s manual


TABLE OF CONTENTS
1.
FUNCTIONALITIES OF THE REGULATION ........................................................................................... 5
2.
GENERAL MAINTENANCE INSTRUCTIONS ......................................................................................... 7
2.1.
General information......................................................................................................................... 7
2.1.1.
General schematic of the HR units...................................................................7
2.1.2.
Label located inside the cover of the control panel 3 .......................................8
3.
REGULATION: CONFIGURATION – WIRING – OPERATING ............................................................... 9
3.1.
Connecting the RC TAC4 to the CB4 TAC4 DG circuit................................................................ 9
3.1.1.
Open the RC TAC4 casing:..............................................................................9
3.1.2.
Wiring diagram to connect the RC TAC4 REC to the TAC4 DG circuit:.........10
3.2.
Selecting the Master...................................................................................................................... 10
3.3.
Fan control ..................................................................................................................................... 12
3.3.1.
Working modes..............................................................................................12
3.3.2.
CA Mode: setup, operating instructions and wiring diagrams.........................13
3.3.3.
LS Mode: setup, operating instructions and wiring diagrams.........................16
3.3.4.
CPs Mode: setup, operating instructions and wiring diagrams.......................19
3.4.
Time slots schedules .................................................................................................................... 22
3.4.1.
Definition........................................................................................................22
3.4.2.
Configuration..................................................................................................22
3.4.3.
Switching from MANU to AUTO mode (scheduler) ........................................26
3.5.
Alarms............................................................................................................................................. 27
3.5.1.
Alarm types....................................................................................................27
3.5.2.
Alarm table.....................................................................................................30
3.5.3.
Wiring diagrams:............................................................................................31
3.5.4.
Fire alarm.......................................................................................................31
3.6.
BOOST function............................................................................................................................. 32
3.6.1.
Setup..............................................................................................................32
3.6.2.
Wiring diagram...............................................................................................32
3.7.
FREECOOLING Function.............................................................................................................. 32
3.7.1.
Operating description.....................................................................................33
3.7.2.
Additional function..........................................................................................33
3.7.3.
Wiring diagram...............................................................................................33
3.8.
Opening / closing of dampers (CT option) at inlet..................................................................... 34
3.9.
Heat exchanger anti-frost protection system............................................................................. 34
3.9.1.
Anti-frost protection via pulse flow reduction..................................................34
3.9.2.
Anti-frost protection via regulation of the by-pass opening.............................35
3.9.3.
Anti-frost protection with 1 internal electrical pre-heating coil KWin (option)..36
3.9.4.
Anti-frost protection with 1 external hydraulic pre-heating coil BAin (option)..37
3.10.
KWout post heating electrical coil control (HRglobal and HRup option)................................ 37
3.10.1.
Wiring diagrams..........................................................................................38
3.11.
Post heating regulation (HRglobal and HRup NV option)......................................................... 38
3.11.1.
Wiring diagrams..........................................................................................39

3.12.
Regulation for external coil(s) (SAT TAC4 BA/KW option) ....................................................... 41
3.13.
Display on the RC TAC4................................................................................................................ 41
3.14.
Fan failure alarm............................................................................................................................ 42
3.14.1.
Wiring diagram............................................................................................42
3.15.
Actual airflow / pressure output signals..................................................................................... 43
3.16.
Advanced setup............................................................................................................................. 44
Appendix: Installation control datasheet (to be filled in after starting the installation) ........................ 45

5
1. FUNCTIONALITIES OF THE REGULATION
The TAC4 DG controller is mounted in the units of series HRglobal, HRup and HRflat.
This handbook describes the functionalities of the TAC4 DG when using an RC TAC4 display.
The TAC4 DG with RC TAC4 controller provides the following features:
-Monitoring of the fans (exhaust and supply) in chosen working mode: constant airflow (CA),
constant pressure (CPs) or constant airflow linked to 0-10V signal (LS) (e.g. CO2 sensor).
-Management of 4 timeslots.
-Alarms on defects, set points, overpressure.
-Fire alarm airflow management.
-BOOST function, allowing to force a pre-set airflow (supply/exhaust), overriding the assigned
airflow
-Automatic management of the 100% modulating bypass (freecooling function and/or Heat
exchanger antifreeze protection).
-Automatic management of inlet dampers (CT).
-Heat exchanger antifreeze protection system by modulation of airflow or by modulation of the
opening of the modulating bypass or with an intelligent internal pre-heat electrical coil (KWin)
or even by regulating the power of an external hydraulic pre-heat coil (BAin).
-Post heating management of water coil (NV) or electrical coil (KWout) to keep a set
temperature constant.
-Display of the settings and working fans
-Analogical output signals of airflow and pressure
-Advanced setup
The following options can be combined with TAC4 DG controller:
- SAT3 Option :
Circuit with 2 relays for
•Information about the « Pressure alarm » (on O.R.1)
•Information about the « FAN ON » (on O.R.2)
•
Status of NV option circulator
(on O.R.3)
•Information about the status of the « bypass » (on O.R.4)
- SAT TAC4 BA/KW Option :
Regulation of 2 external exchangers (electrical/water, post-hot and/or post-cold).
Regulation of an external hydraulic pre-heat coil (BAin option)
- RC TAC4 Option :
Simple remote control with a LCD display (2x8 digits) to configure, control and visualize the
unit parameters.
- SAT TAC4 MODBUS Option:
Enables the following options:
•GRC – colour touchscreen remote control (more user-friendly).
•TAC4 TCP/IP module – configuration and visualization via webpages.
•TAC4 GPRS module – configuration and visualization via webpages.
•MODBUS RTU communication – configuration and visualization via a centralized technical
management system.
- SAT TAC4 ETHERNET Option: communication with MODBUS TCP/IP protocol on Ethernet
over twisted pair 10 BASE T network.

Installation and user’s manual TAC4 DG + RC
6
- SAT TAC4 WIFI Option: communication with MODBUS TCP/IP protocol on wireless WIFI
network.
- SAT TAC4 KNX Option:
KNX Communication
See separate installation manual for each of these options.

7
2. GENERAL MAINTENANCE INSTRUCTIONS
2.1. General information
2.1.1. General schematic of the HR units
HRflat HRup
HRglobal
1. Main switch for power supply fans and control
2. Main switch for power supply to pre (KWin) and/or post (KWout) heating coils (options)
3. Centralized wiring box of the CB4 TAC4 DG circuit (factory pre-wired)
4. Supply fan(s) (exhaust on HRflat 450)
5. Exhaust fan(s) (supply on HRflat 450)
6. Post-heating water or electrical coil (NV or KWout option)
7. Motorized damper at fresh air inlet (CT option)
8. F7 class filter at fresh air inlet (HRflat: G4 class filter) (exhaust air inlet on HRflat 450)
9. Pre-heating electrical antifreeze coil (KWin option)
10. Drain pan and drain (HRflat: drain pipe out)
11. Air/Air heat exchanger + modulating By-pass 100%
12. G4 filter on exhaust air (supply air inlet on HRflat 450)
13. Motorized damper at exhaust air inlet (option)
14. RC TAC4
All electrical connections made the installer are in 1/2/3.
14
1
4
5
8
10
11
12
2
1
3
4
5
6
7
8 9
10
11
12
13
14
1
2
3
45
6
8
9
10
11
12
14
9
3

Installation and user’s manual TAC4 DG + RC
8
Schematic of the T° sensors positioning in the HRg unit
To allow easier identification of the temperature sensors 4 different wire colours are used:
-T1 : black wire
-T2 : white wire
-T3 : blue wire
-T4 & T5 : green wire
2.1.2. Label located inside the cover of the control panel 3

9
3. REGULATION: CONFIGURATION – WIRING – OPERATING
The regulation is delivered fully factory pre-wired. Nevertheless, the TAC4 RC (remote control) and the I/O signals
if any must still be wired by the installer.
3.1. Connecting the RC TAC4 to the CB4 TAC4 DG circuit
The connection between the various circuits is made by a communication bus.
Follow these steps to connect the RC TAC4 to the CB4 TAC4 DG:
3.1.1. Open the RC TAC4 casing:
Using a small screwdriver unlock the 4 pins
2 pins on each side
Remove the cover
Points for fixation of the casing
(spacing = 88mm).
RC dimensions = 122 x 66mm
RC TAC4 wiring terminals

Installation and user’s manual TAC4 DG + RC
10
Caution:
•The RC box is class IP20 and cannot be installed outdoors as such. If you wish to install it outdoors you need
to fasten inside a proper watertight box.
•The configuration data is stored in the TAC4 DG circuit. Therefore, unlike the previous generation, the RC does
not have to be permanently connected for the regulation to operate properly.
3.1.2. Wiring diagram to connect the RC TAC4 REC to the TAC4 DG circuit:
Cable specifications:
•Recommended cable: category 5 shielded twisted pair (FTP) cable with a section of 0,26 … 0,50 mm ².
Use 1 pair to connect GND and +12V and 1 pair to connect B- and A +
•Maximum cable length: 1000 m.
•Keep this communication cable at distance from power cables.
•If the unit is installed in a location with high electro-mechanical interference levels we strongly advise to
connect the armoured shield of the TAC4 DG – RC cable on one side of the ground only.
•If the HRg unit is installed outside, select a suitable cable for outdoor application (UV light …).
3.2. Selecting the Master
« Selecting the master » means the determination of which module of the I/O and the RC will “control” the fans,
“controlling” the fans means:
-
If CA mode is chosen (cfr § 3.3.2), to be the master means to control the start/stop of the fans as well as to select
the airflow
-
If LS or CPs mode (cfr § 3.3.3 and 3.3.4), to be the master means to control the start/stop of the fans as well as to
activate/deactivate a different assignment (assignment multiplier).
2 setups are possible:
1) Or TAC4 DG circuit is « master »: contact between terminals IN1 and +12Vdc of TAC4 DG circuit is closed.
- The TAC4 DG circuit allows control of the fans through its inputs.
- The RC TAC4 allows to configure and to visualize all the parameters on the display and with the LEDs,
2) Or RC TAC4 is « master »: contact between terminals IN1 and +12Vdc of TAC4 DG circuit is open.
- The TAC4 DG circuit is then in control of the system and serves as a control hub between fans and the RC TAC4.
- The RC TAC4 allows to configure and to visualize all the parameters on the display and with the LEDs,
- The RC TAC4 controls the fans with the OFF / I / II / III keys,

11
TAC4 DG
circuit is
master
Control Visualization
RC
TAC4
is master
Control
Visualization
Wiring diagram
Contact closed = TAC4 DG circuit master
Contact open = RC TAC4 master
Caution: Use gold-plated contact only
.
The use of this contact enables to switch automatically from RC TAC4 master to TAC4 DG master.
Using this you can for instance:
•Work in RC TAC4 master and switch in position TAC4 DG master to stop automatically the fans (attention, in
this case the inputs K1/K2/K3 on the TAC4 DG have to be disconnected from the +12V).
•Work in RC TAC4 master and switch in position TAC4 DG master to activate automatically a sleep value
(attention K1/K2/K3 on the TAC4 DG have to be properly connected to activate this value).

Installation and user’s manual TAC4 DG + RC
12
3.3. Fan control
3.3.1. Working modes
The various working modes give the user the choice on how the airflow must be modulated according to your
application.
In all the working modes the supply fan will operate according to the assigned mode and parameters. The airflow
of the exhaust fan will then equal to a percentage of the actual airflow of the supply fan (noted %EXH / SUP for
ratio between exhaust and supply airflows).
The RC TAC4 allows configuration of one of the following 4 modes:
•CA MODE :
3 constant airflow assignments for the supply fan are determined by the user (m³h K1, m³h K2 and m³h K3).
•LS MODE :
The assigned supply airflow is a function of a 0-10V linear signal. The user defines the link with 4 parameters:
Vmin, Vmax, m³h≡Vmin and m³h≡Vmax, applied to the following diagram:
With m³h≡Vmin < or > m³h≡Vmax (positive or negative link).
Using the advanced setup, it is possible to stop the fans once the input signal
value has reached a certain upper and/or lower limit.
•CPs MODE:
CPs on supply: the airflow of the supply fan(s) is modulated so as to maintain constant a certain pressure value
measured by a pressure sensor properly located in the ducting.
CPs on exhaust: the airflow of the exhaust fan(s) is modulated so as to maintain constant a certain pressure value
measured by a pressure sensor properly located in the ducting.
•MODE OFF:
Is not a real working mode, it is a way to temporarily shortcut the TAC4 DG master setup. It allows, if working in
TAC4 DG master, to stop the fans with the RC TAC4. But then to restart the fans it is required to choose one of the
other 3 working modes.

13
3.3.2. CA Mode: setup, operating instructions and wiring diagrams
3.3.2.1. Setup CA mode
The setup is made by means of the LCD screen and the 4 knobs SETUP,
↑, ↓
and ENTER of the RC.
To start the setup:
- Enter in the setup mode using the left knob on the diagram so that the SETUP LED
lights.
- Press then the SETUP knob until the text ‘SETUP’ appears on the screen.
The idea is to select your choice with the
↑↓
knobs and then to confirm your choice by
pressing ‘ENTER’. The numbers are introduced digit by digit.
1 LANGUAGE Choose your language (English, French, Dutch, German)
2
HEATING
T°? xx°C Only available with post-heating exchanger(s), Select the supply T° to the heating
exchanger which is connected to the SAT BA/KW.
3 COOLING
T°? xx°C Only available with post-cooling exchanger(s), Select the supply T° to the cooling
exchanger which is connected to the SAT BA/KW.
4
FREECOOL
T°? xx°C Only available with setup of modulating bypass in modality «FREECOOL» or
« AF+FREECOOL». See §3.7 for details.
5 WORKING
MODE Select CA from CA, LS, CPs
6 m³h K1? Type in supply airflow 1 (will be activated if contact between K1 and +12V of TAC4 DG
circuit closed or if position I on RC TAC4 is selected)
7 m³h K2? Type in supply airflow 2 (will be activated if contact between K1 and +12V of TAC4 DG
circuit closed or if position II on RC TAC4 is selected)
8 m³h K3? Type in supply airflow 3 (will be activated if contact between K1 and +12V of TAC4 DG
circuit closed or if position III on RC TAC4 is selected)
9 %EXH/SUP Type in ratio between exhaust (EXH) and supply (SUP) airflow to create over, under or
even pressure.
10 TIME
SEGMENT?N
Select Y to activate the time segment scheduling function
11 CONFIG
TIME? N Select ‘Y’ to activate time segment function
12 … For more details see § 3.4
13 PRESSURE
ALARM? The pressure alarm is optional. If you do not wish it select N and skip to step 14.
Otherwise select Y. For more details see §3.5
14 ∆P SUP Type in the pressure increment for the supply airflow.
15 ∆P EXH Type in the pressure increment for the exhaust airflow.
16 INIT Pa
REF? Do you wish to (re-)configure the reference pressure for the supply and the exhaust
airflows? Y or N. (this is optional if it has been done previously)
17 m³h INIT If Y is selected, enter nominal airflow at which you wish to initialize the reference
pressure. (same airflow for exhaust and supply air)
18 Pa REF INIT
xxxx m³h
xxxx Pa
Initializing the reference pressure…
After +/-1 minute, the system will memorize the calculated pressure value of the fan as
the reference pressure. While initializing the airflow and pressure on F1 is displayed.
19 ALARM
RESET? Possibility to reset the alarms. Y or N?
20 END SETUP End

Installation and user’s manual TAC4 DG + RC
14
3.3.2.2. Operating CA mode with RC TAC4 master
•One of the 3 assignment constant airflows (m³h K1, m³h K2 and m³h K3) is selected using the I / II / III knobs of
the RC TAC4. The selection made is highlighted by the corresponding LED on the RC. The exhaust airflow is
equal to (%EXH/SUP) of the supply airflow.
•The OFF touch allows stopping the fans.
3.3.2.3. Operation CA mode with TAC4 DG master
One of the 3 assignment constant airflows (m³h K1, m³h K2 and m³h K3) is selected using the K1/K2/K3 terminals
on TAC4 DG. The selection made is highlighted by the corresponding LED on the RC TAC4). The exhaust airflow
is equal to (%EXH/SUP) of the supply airflow.
Wiring diagrams
a) Wiring 1 circuit to 3 external contacts
b) Wiring 1 circuit to 1 COM4 (PLC 4 positions switch)
K1 closed airflow m
3
h K1
K2 closed airflow m
3
h K2
K3 closed airflow m
3
h K3
K1/K2/K3 open soft stop
Caution K1/K2/K3: Use gold-plated contacts only.

15
c) Wiring several circuits to 3 external contacts
K1 closed airflow m
3
h K1
K2 closed airflow m
3
h K2
K3 closed airflow m
3
h K3
K1/K2/K3 open soft stop
Caution K1/K2/K3: Use gold-plated contacts only.
d) Wiring several circuits to 1 COM4

Installation and user’s manual TAC4 DG + RC
16
3.3.3. LS Mode: setup, operating instructions and wiring diagrams
3.3.3.1. Setup LS mode
The setup is made by means of the LCD screen and the 4 knobs SETUP,
↑, ↓
and ENTER of the RC.
To start the setup:
- Enter in the setup mode using the left knob on the diagram so that the SETUP LED lights.
- Press then the SETUP knob until the text ‘SETUP’ appears on the screen.
The idea is to select your choice with the
↑↓
knobs and then to confirm your choice by
pressing ‘ENTER’. The numbers are introduced digit by digit.
1 LANGUAGE Choose your language (English, French, Dutch, German)
2
HEATING
T°? xx°C Only available with post-heating exchanger(s), Select the supply T° to the heating
exchanger which is connected to the SAT BA/KW.
3 COOLING
T°? xx°C Only available with post-cooling exchanger(s), Select the supply T° to the cooling
exchanger which is connected to the SAT BA/KW.
4
FREECOOL
T°? xx°C Only available with setup of modulating bypass in modality «FREECOOL» or
« AF+FREECOOL». See §3.7 for details.
5 WORKING
MODE Select LS from CA, LS, CPs
6 V min? Select minimum voltage value
7 V max? Select maximum voltage value
8 m³/h≡Vmin Select constant airflow value for minimum voltage Vmin
9 m³/h≡Vmax Select constant airflow value for maximum voltage Vmax
10 % on K3? Select constant airflow multiplier when contact between terminals +12V and K3 in the
TAC4 DG is closed, or if position III is activated on the RC TAC4.
11 %EXH/SUP Type in ratio between exhaust (EXH) and supply (SUP) airflow to create over, under or
even pressure.
12 TIME
SEGMENT?N
Select Y to activate the time segment scheduling function
13 CONFIG
TIME? N Select ‘Y’ to activate time segment function
14 … For more details see § 3.4
15 PRESSURE
ALARM? The pressure alarm is optional. If you do not wish it select N and skip to step 16.
Otherwise select Y. For more details see §3.5
16 ∆P SUP Type in the pressure increment for the supply airflow.
17 ∆P EXH Type in the pressure increment for the exhaust airflow.
18 INIT Pa
REF? Do you wish to (re-)configure the reference pressure for the supply and the exhaust
airflows? Y or N. (this is optional if it has been done previously)
19 m³h INIT If Y is selected, enter nominal airflow at which you wish to initialize the reference
pressure. (same airflow for exhaust and supply air)
20 Pa REF
INIT
xxxx m³h
xxxx Pa
Initializing the reference pressure…
After +/-1 minute, the system will memorize the calculated pressure value of the fan as
the reference pressure. While initializing the airflow and pressure on F1 is displayed.
21 ALARM
RESET? Possibility to reset of the alarms. Y or N?
22 END SETUP End

17
3.3.3.2. Operating LS mode with RC TAC4 master
The assignment value for the supply constant airflow is a function of a 0-10V signal connected to terminals K2 of
the TAC4 DG circuit. The link between voltage and airflow is linear. The exhaust constant airflow is equal to
%EXH/SUP of the supply airflow (except if 2 separate 0-10V signals are used to determine exhaust and supply
constant airflows, see advanced setup).
•Starting/stopping the fan is carried out with knobs I/III and OFF.
•The pressure sensor is connected to entry K2 of the TAC4 DG circuit.
•By pressing knob III of the RC you activate the pre-set multiplier (% on K3).
a) Wiring to 1 circuit
b) Wiring to several circuits connected in parallel
(*) K20-10V signal, maximum impedance allowed: 1500 Ω
(*)
(*)

Installation and user’s manual TAC4 DG + RC
18
3.3.3.3. Operating LS mode with TAC4 DG master
The assignment value for the supply constant airflow is a function of a 0-10V signal connected to terminals K2 of
the TAC4 DG circuit. The link between voltage and airflow is linear. The exhaust constant airflow is equal to
%EXH/SUP of the supply airflow (except if 2 separate 0-10V signals are used to determine exhaust and supply
constant airflows, see advanced setup).
•Starting/stopping the fans is carried out with entry K1 on the TAC4 DG circuit.
•The pressure sensor is connected to entry K2 of the TAC4 DG circuit.
•The K3 entry of the TAC4 DG can be used to activate the pre-set multiplier (% on K3.
Wiring diagrams
a) Wiring to 1 circuit
b) Wiring to several circuits in parallel
(*)
K1 closed soft start
K1 open softstop
K2 0-10V signal, maximum impedance allowed: 1500 Ω
K1+K3 closed % on K3 activated
K3 open % on K3 inactive
Caution: use gold-plated contacts only.
(*)
(*)
Table of contents
Other Swegon Controllers manuals
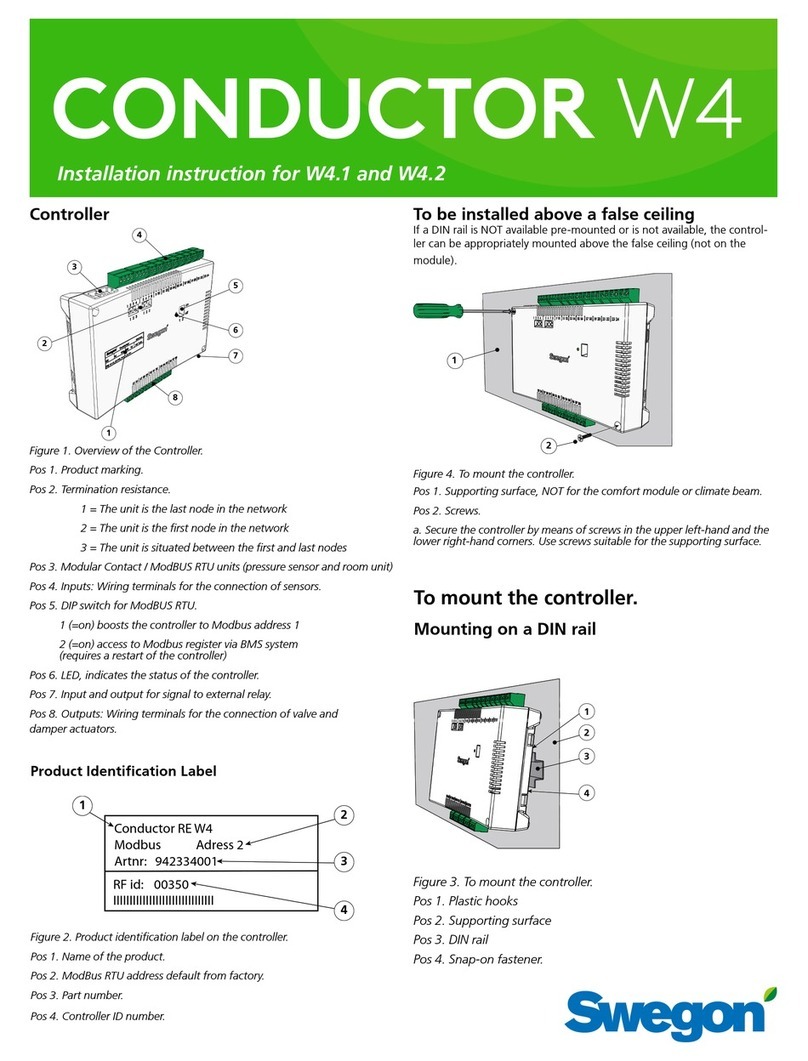
Swegon
Swegon CONDUCTOR W4 Series User manual
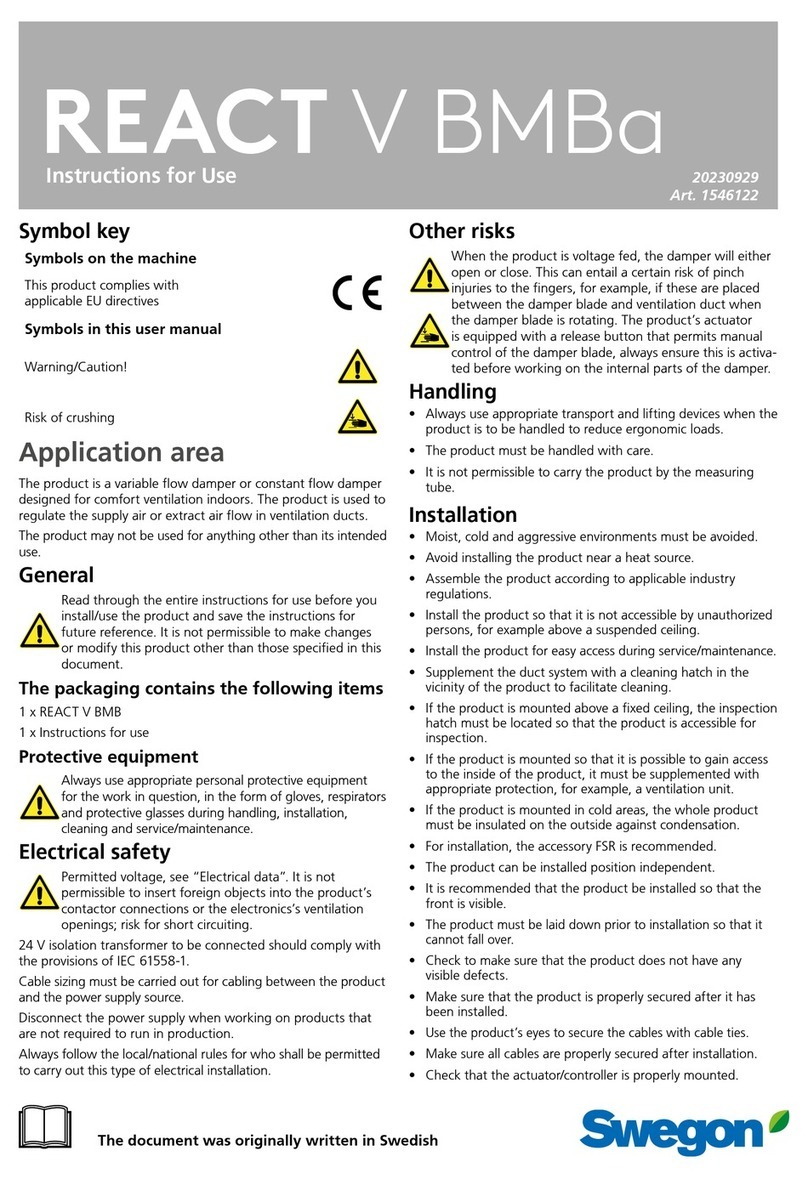
Swegon
Swegon REACT V BMBa User manual
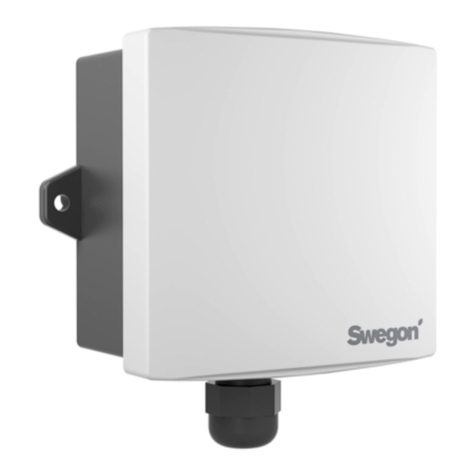
Swegon
Swegon DETECT IAQ a User manual

Swegon
Swegon Conductor W4 User manual
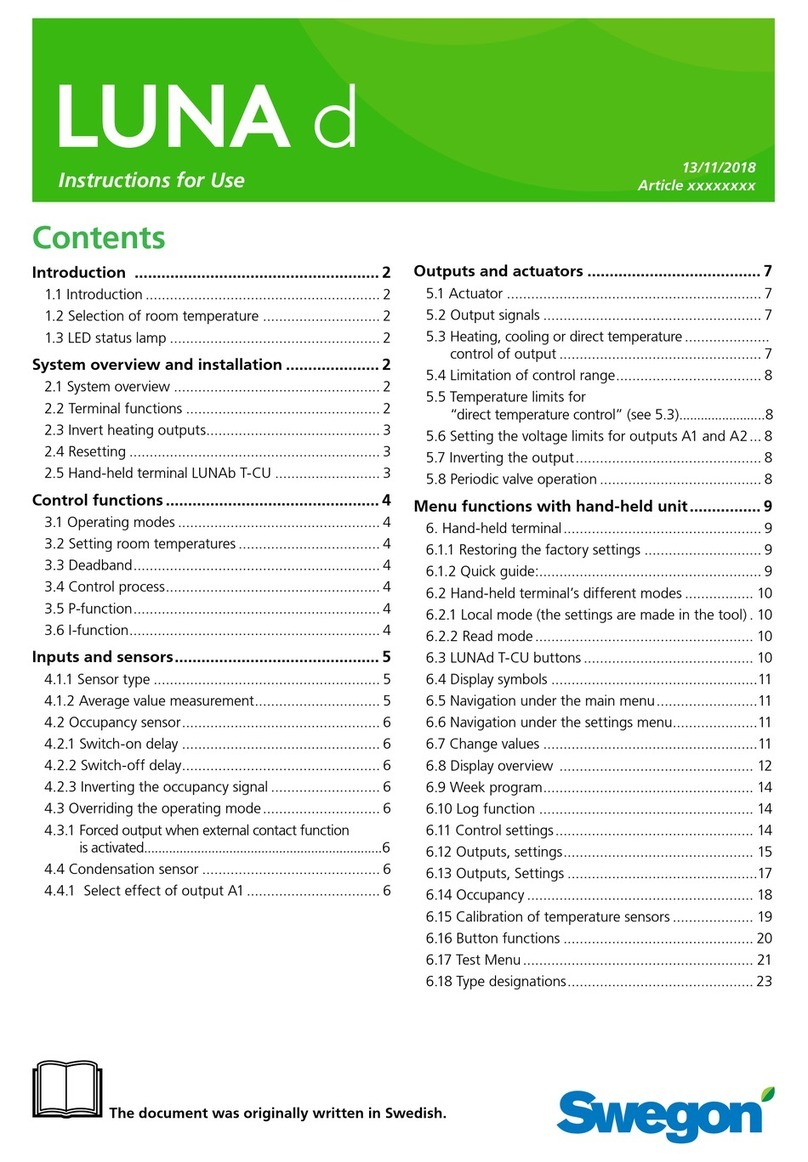
Swegon
Swegon LUNAd User manual

Swegon
Swegon TACTouch TAC5 User manual
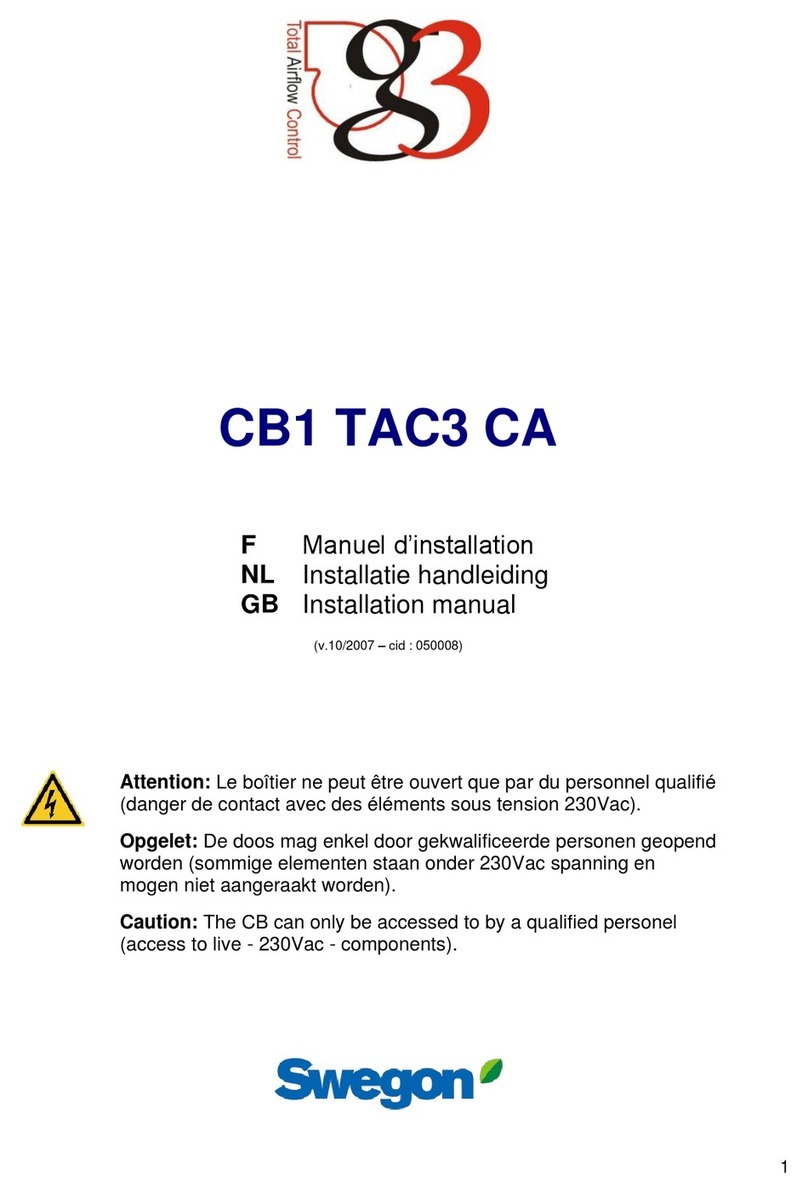
Swegon
Swegon CB1 TAC3 CA User manual
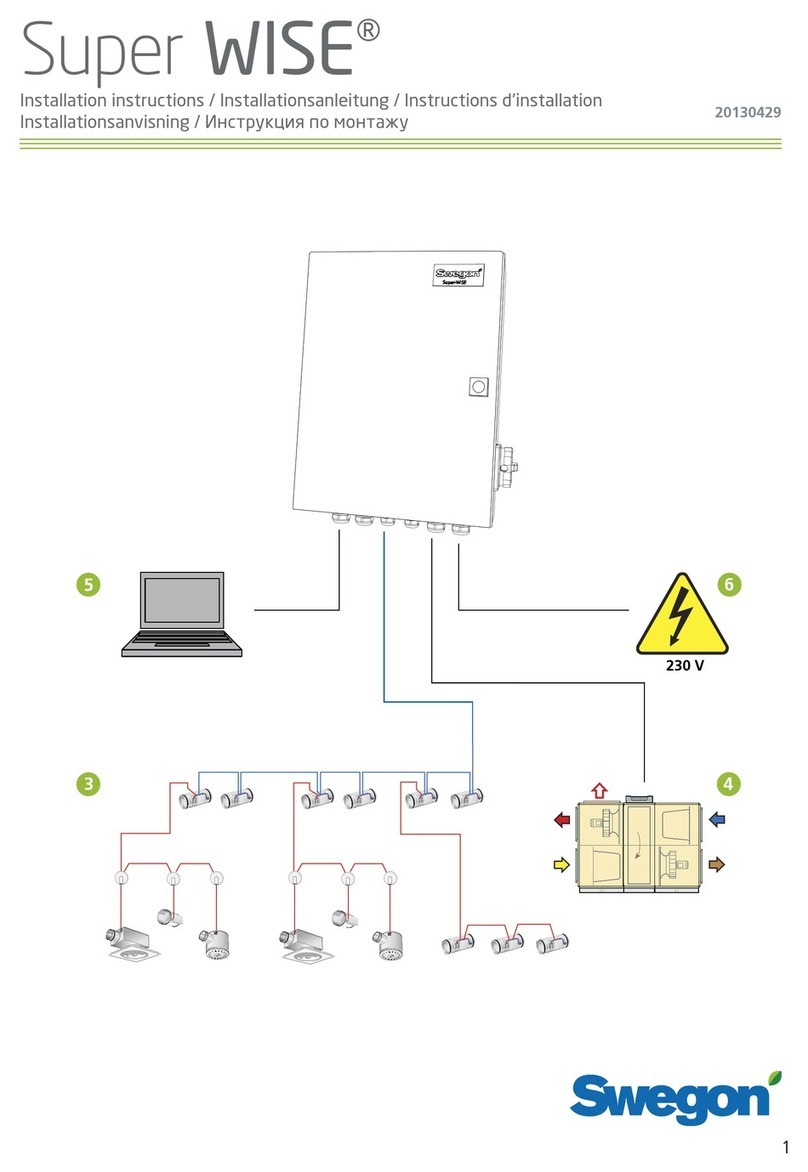
Swegon
Swegon Super WISE User manual
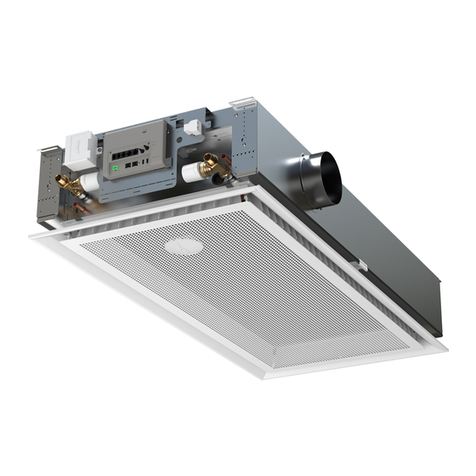
Swegon
Swegon Super WISE User manual
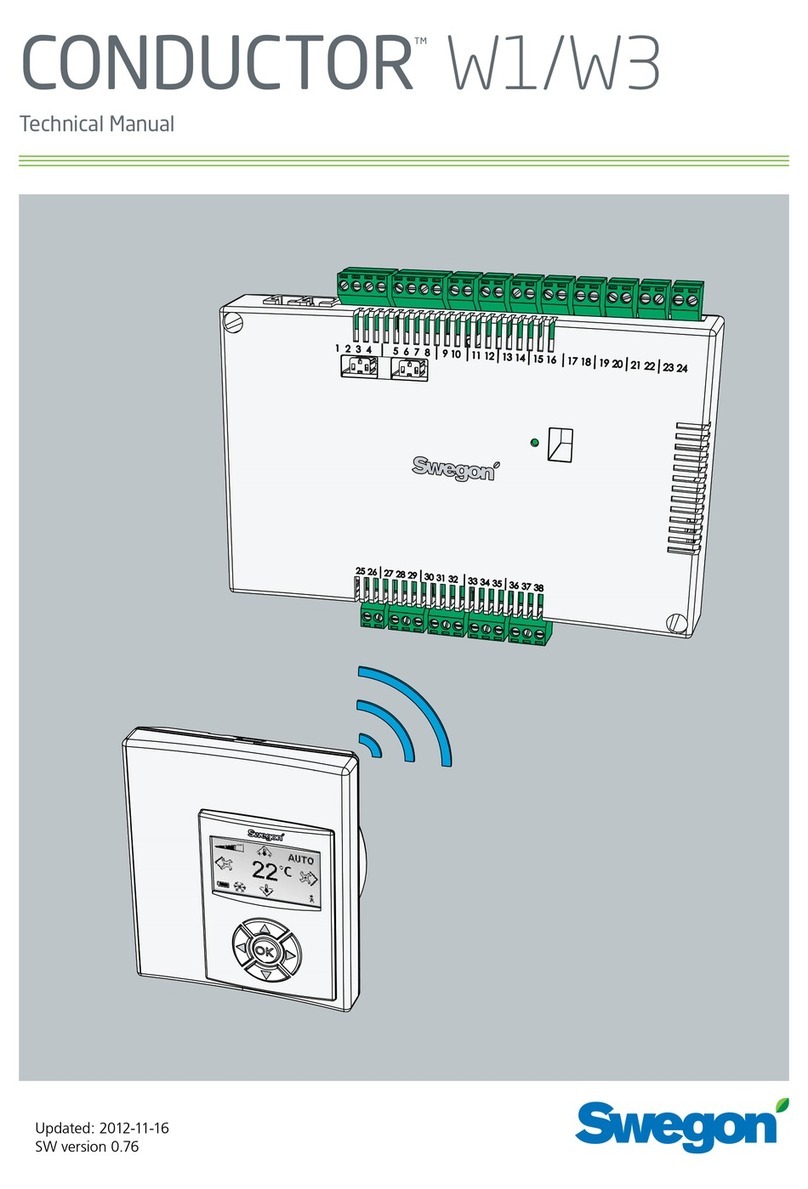
Swegon
Swegon CONDUCTOR W1 User manual
Popular Controllers manuals by other brands
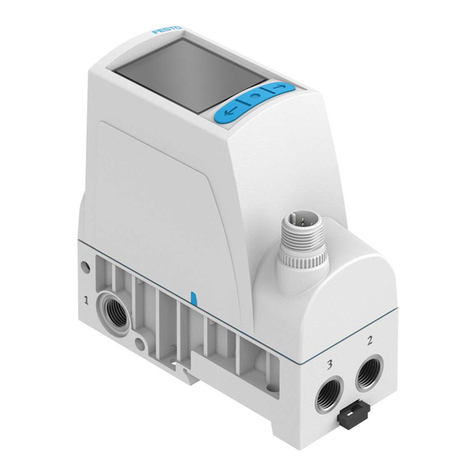
Festo
Festo VPPI S1D Series operating instructions
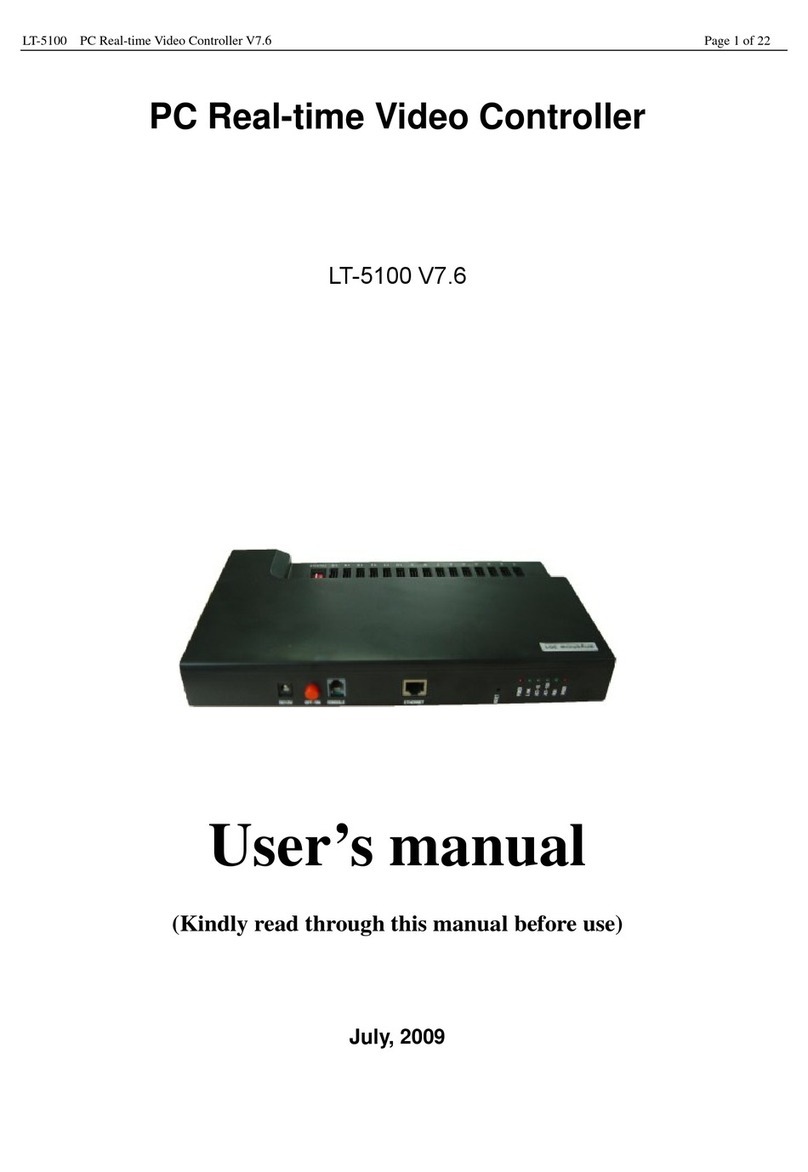
Brother
Brother LT-5100 user manual
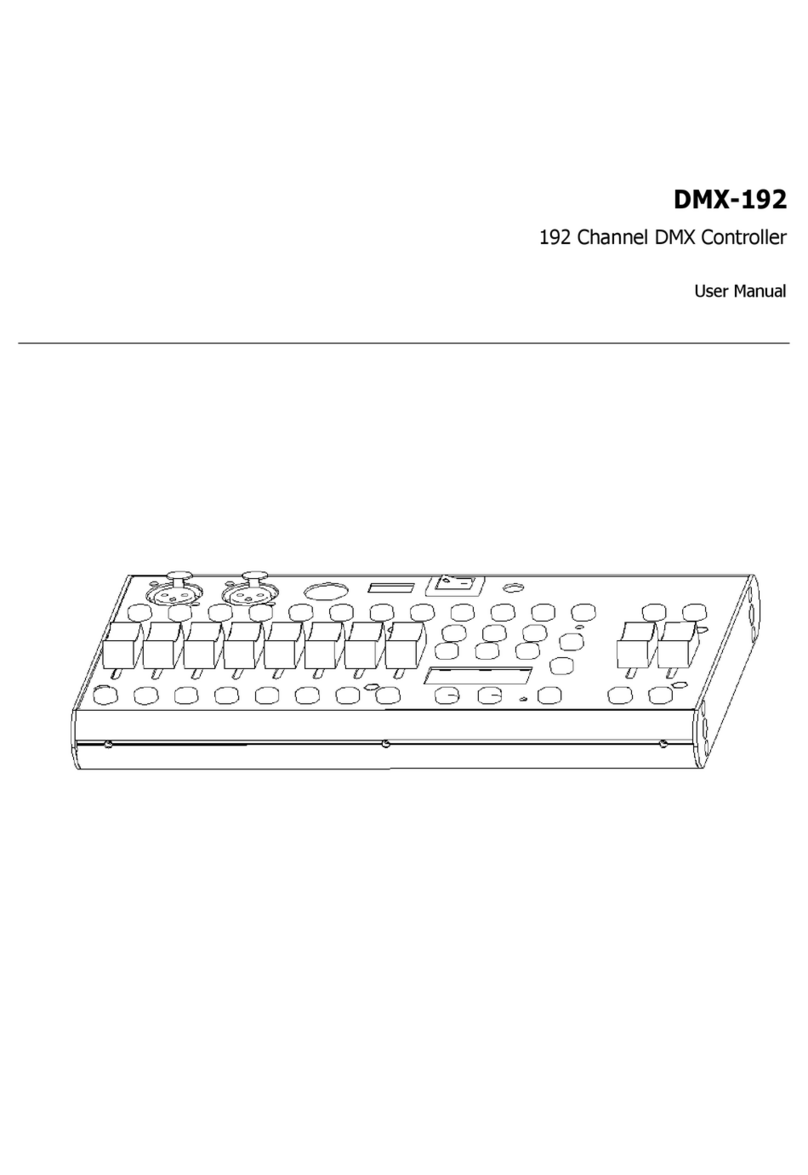
Showlight
Showlight DESK 192B MINI user manual
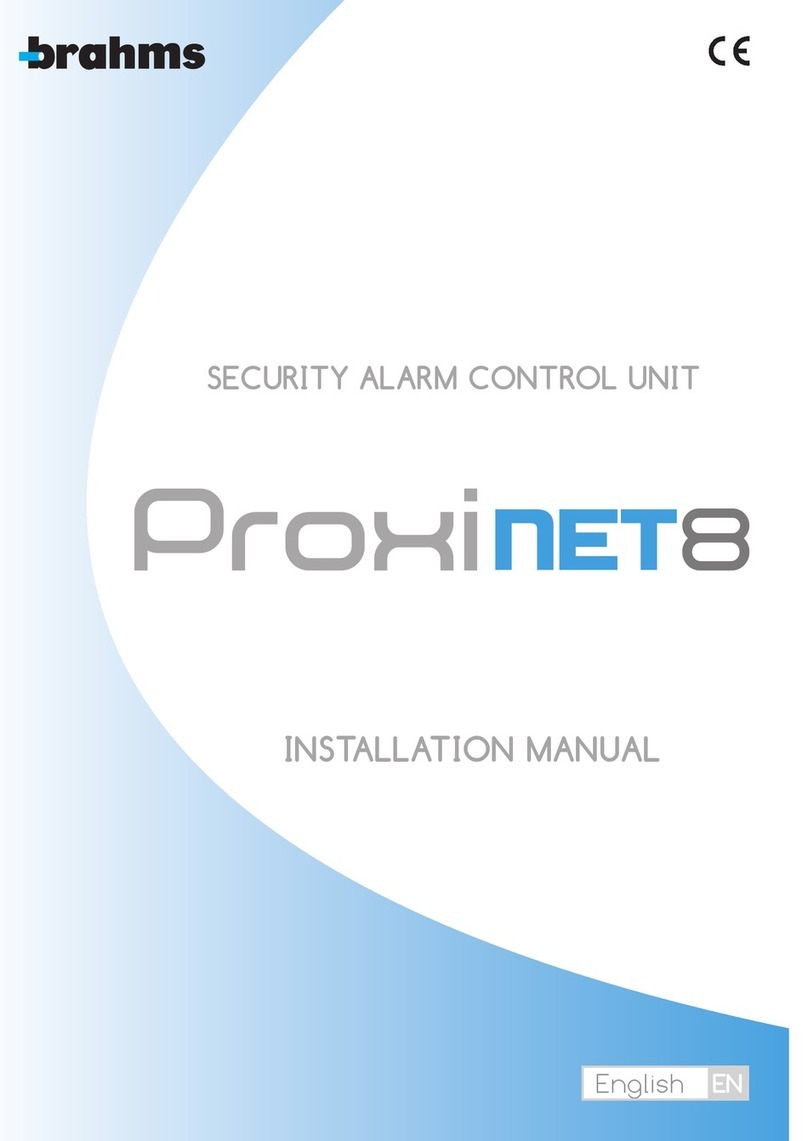
Brahms
Brahms proxinet8 installation manual
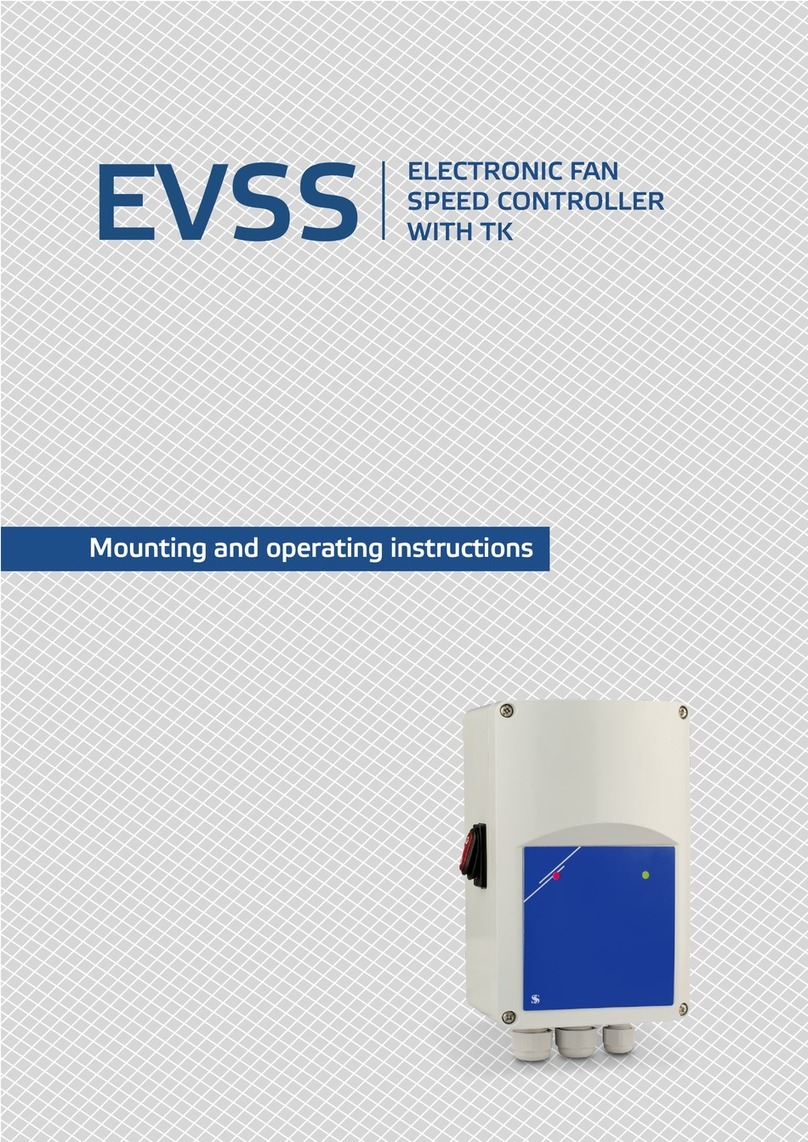
Sentera Controls
Sentera Controls EVSS1 Series Mounting and operating instructions
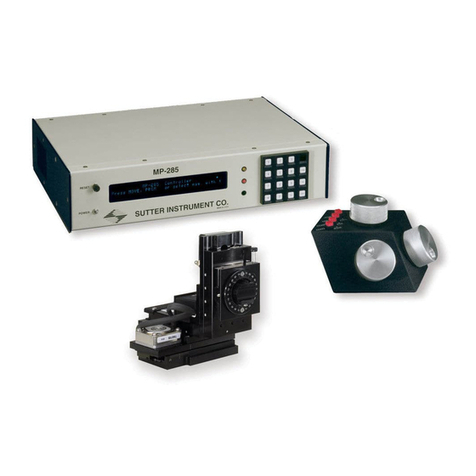
Sutter Instrument
Sutter Instrument MP-285A Basic operations