Texas Instruments TLC5924EVM User manual









Other Texas Instruments Motherboard manuals
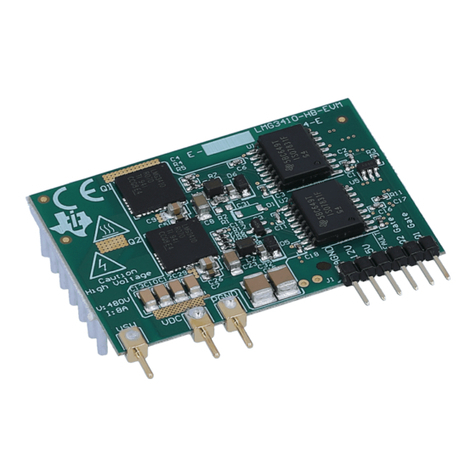
Texas Instruments
Texas Instruments LMG3410-HB-EVM User manual
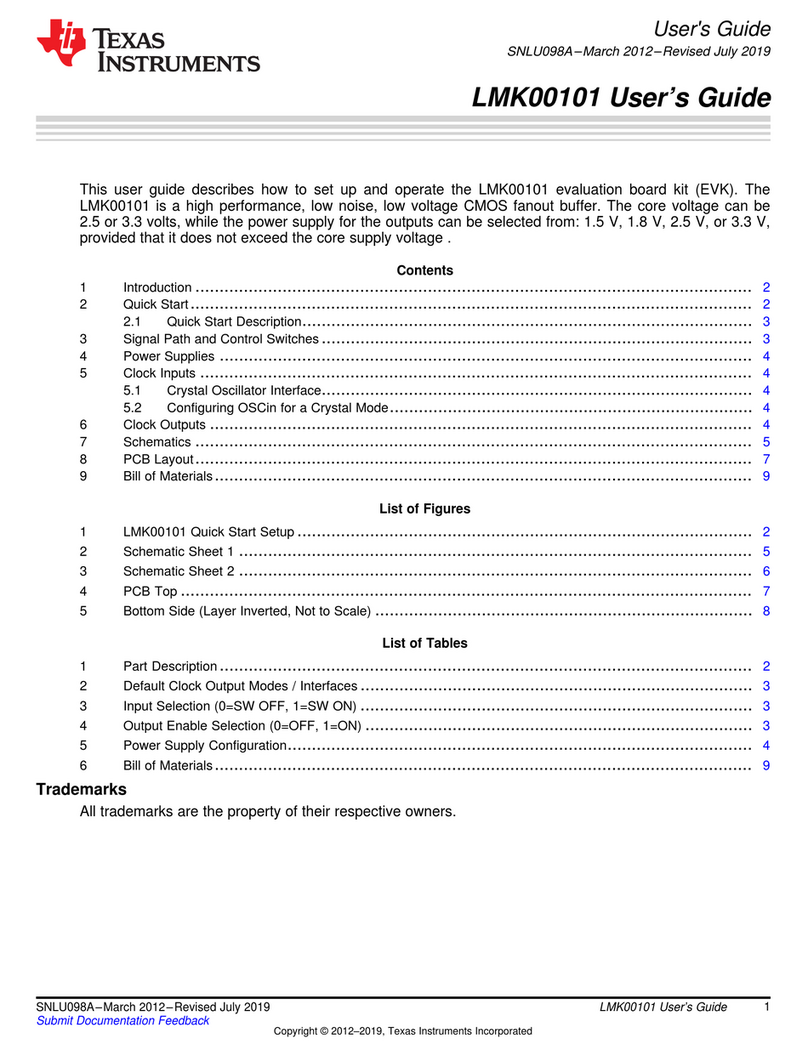
Texas Instruments
Texas Instruments LMK00101BEVAL/NOPB User manual
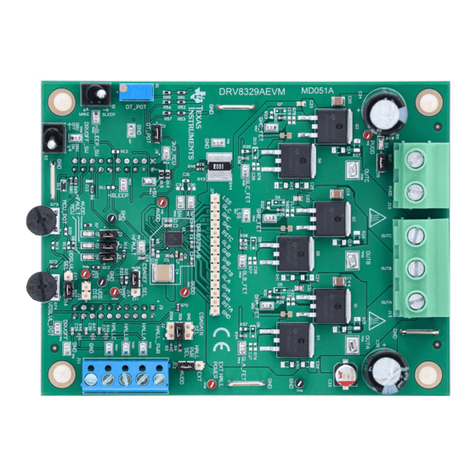
Texas Instruments
Texas Instruments DRV8329AEVM User manual
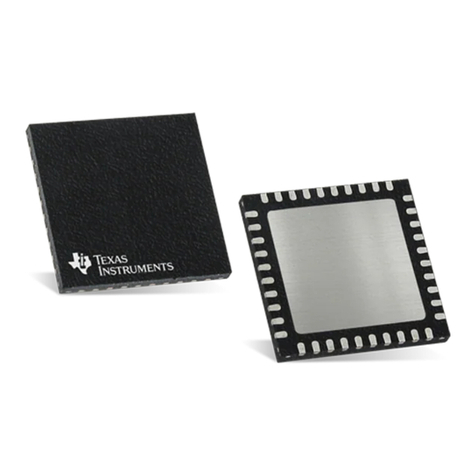
Texas Instruments
Texas Instruments CC2540 User manual
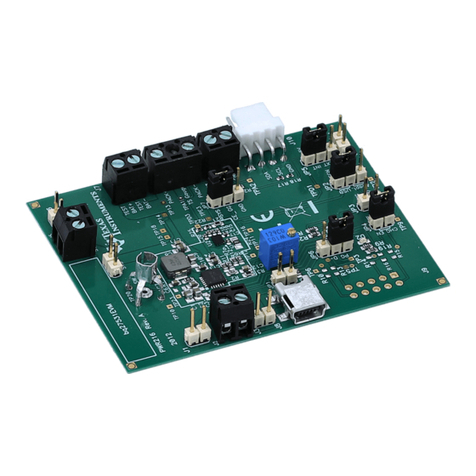
Texas Instruments
Texas Instruments bq27531EVM User manual
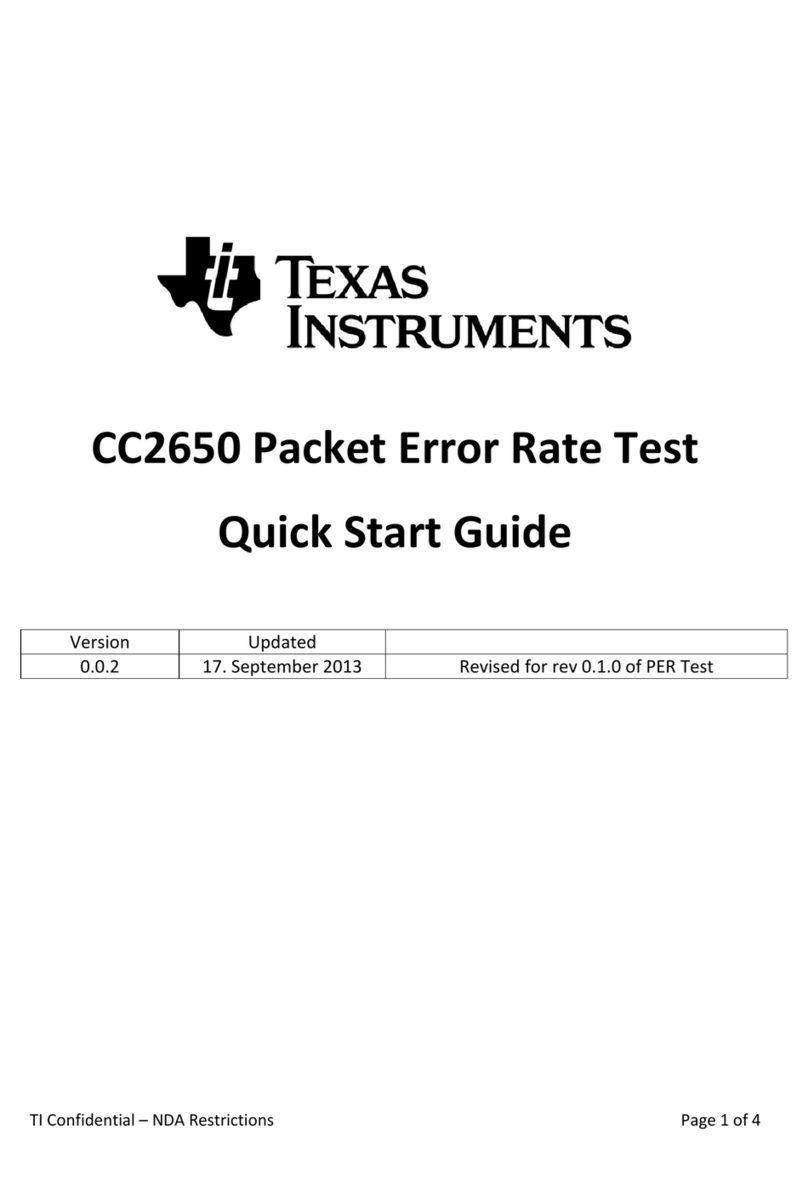
Texas Instruments
Texas Instruments SimpleLink CC2650 User manual
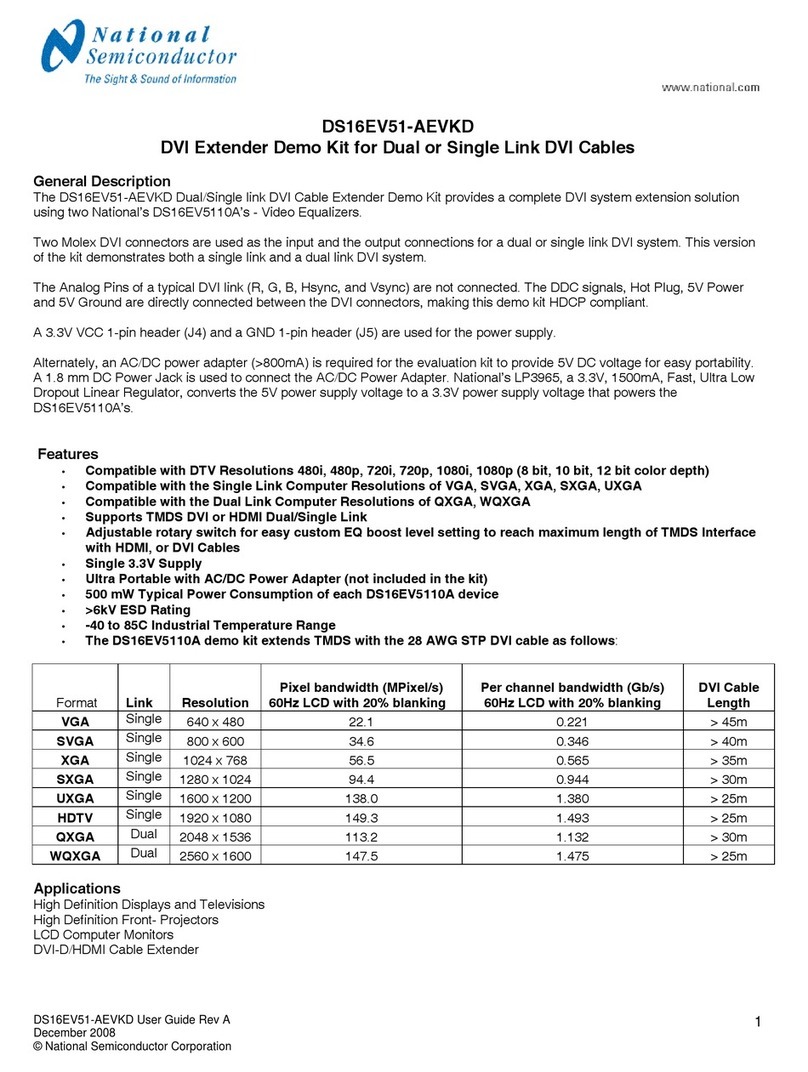
Texas Instruments
Texas Instruments DS16EV51-AEVKD User manual
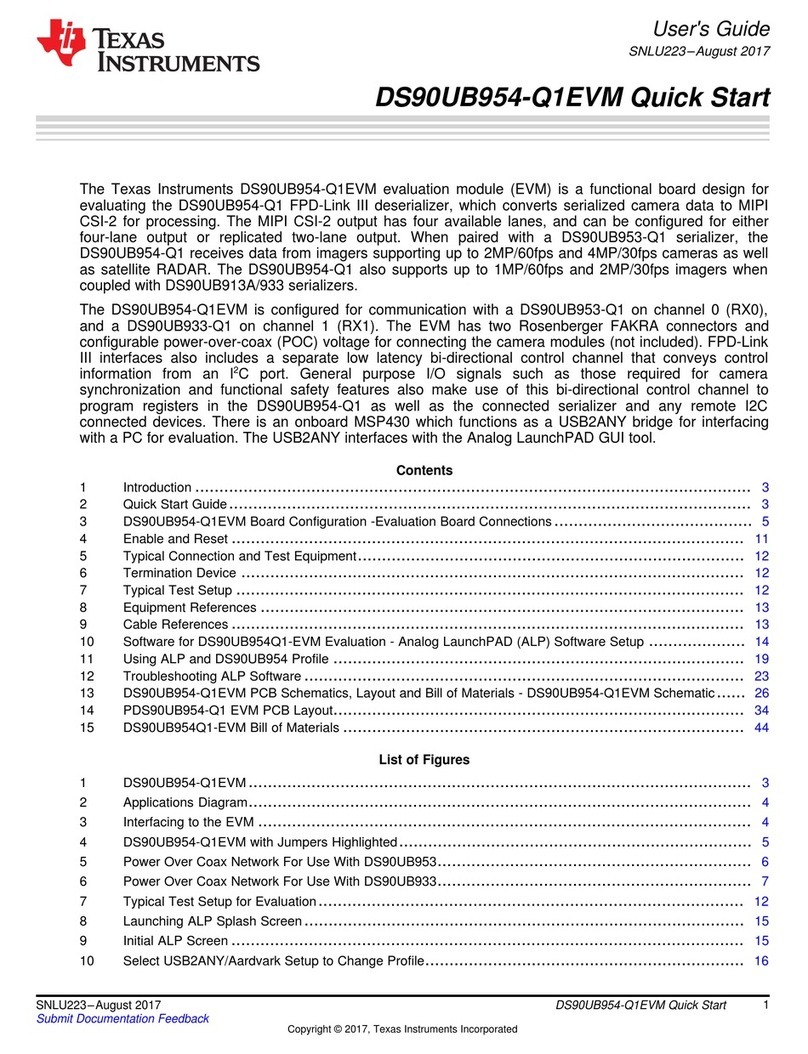
Texas Instruments
Texas Instruments DS90UB954-Q1EVM User manual
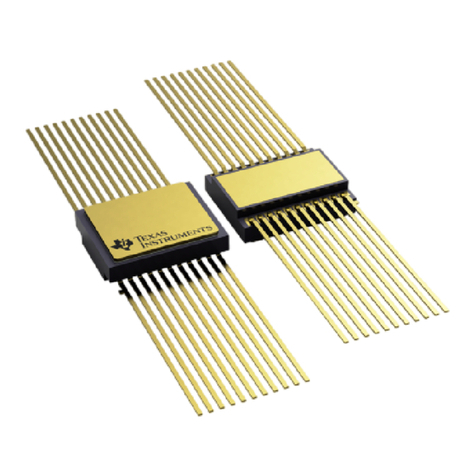
Texas Instruments
Texas Instruments TPS7H500-SP Series User manual
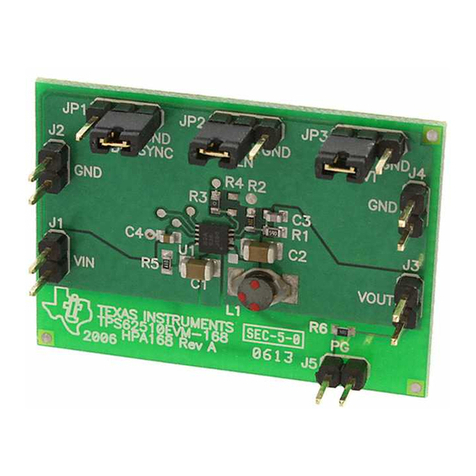
Texas Instruments
Texas Instruments PS62510EVM-168 User manual
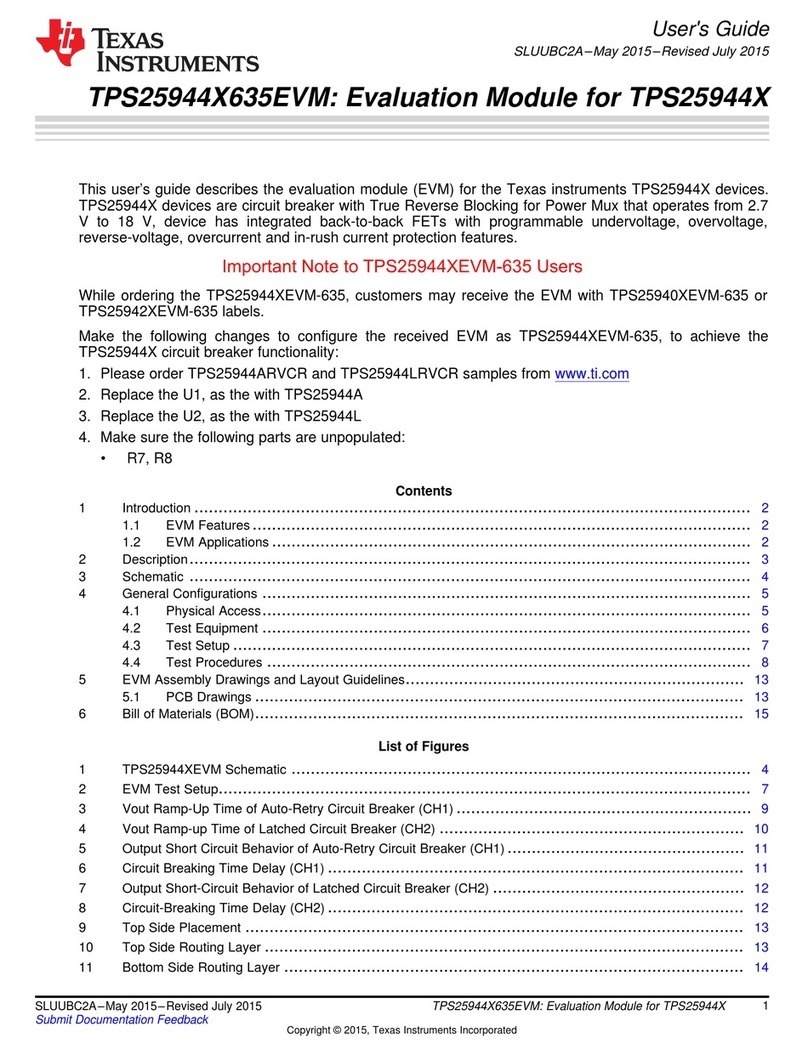
Texas Instruments
Texas Instruments TPS25944X635EVM User manual

Texas Instruments
Texas Instruments bq27750EVM User manual
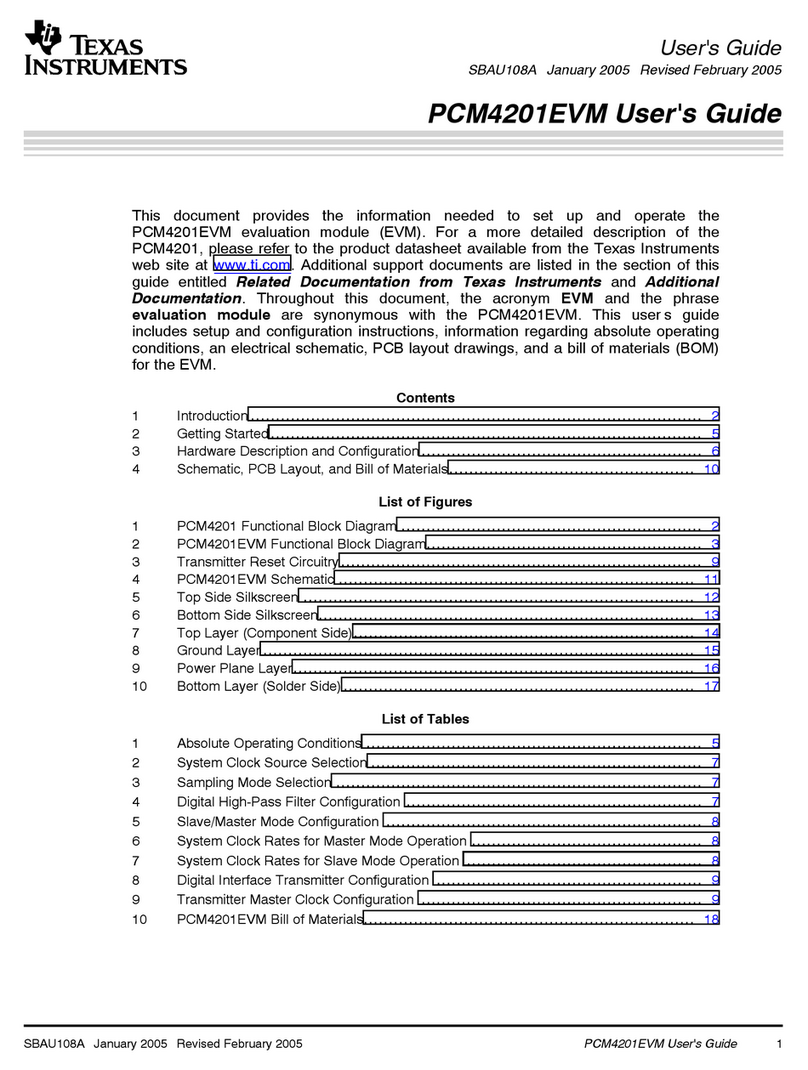
Texas Instruments
Texas Instruments PCM4201EVM User manual
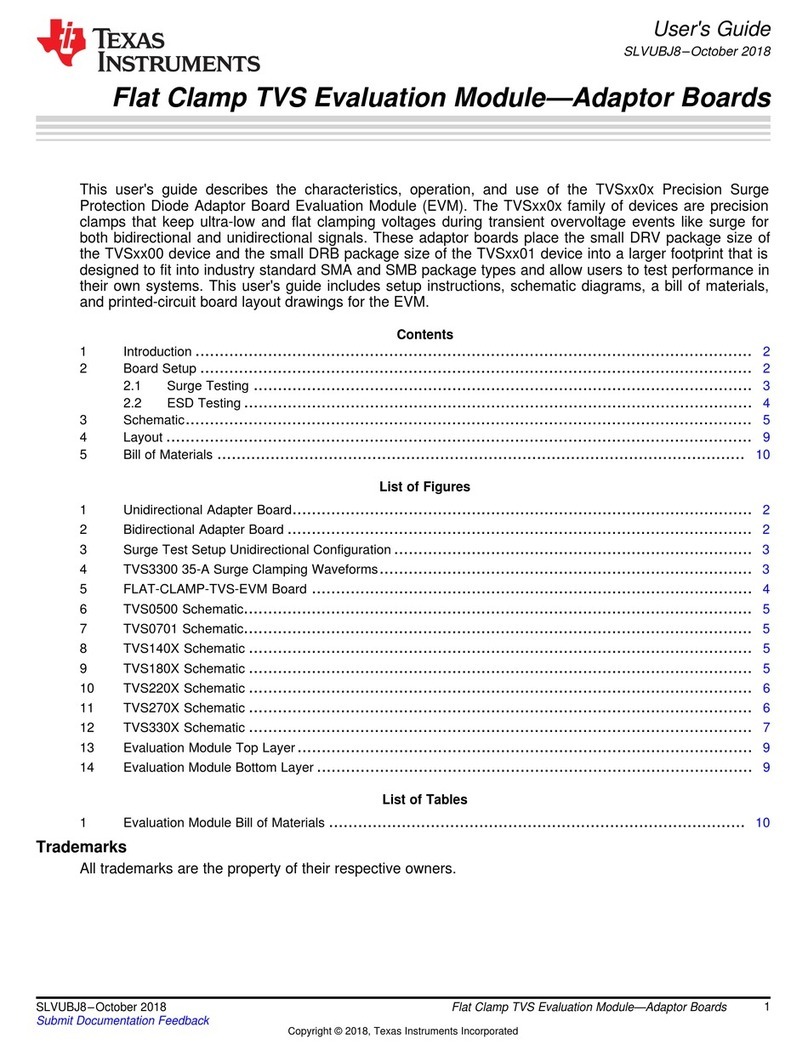
Texas Instruments
Texas Instruments TVS 0 Series User manual
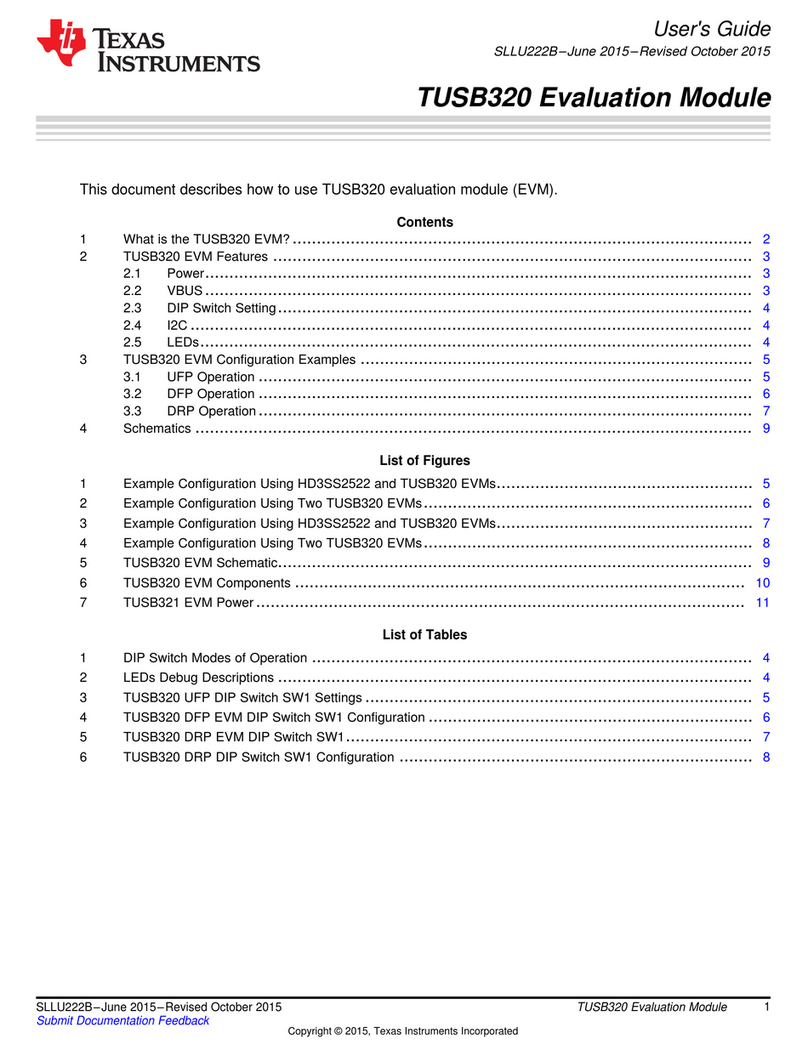
Texas Instruments
Texas Instruments TUSB320 User manual
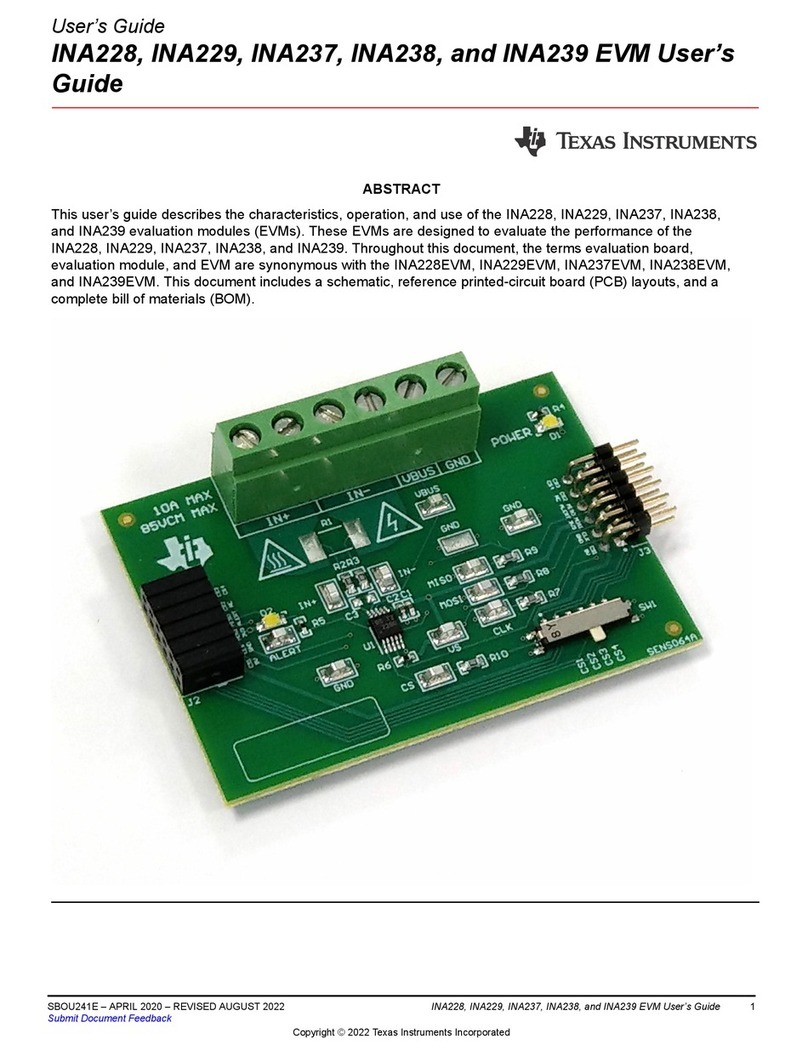
Texas Instruments
Texas Instruments INA228 EVM User manual
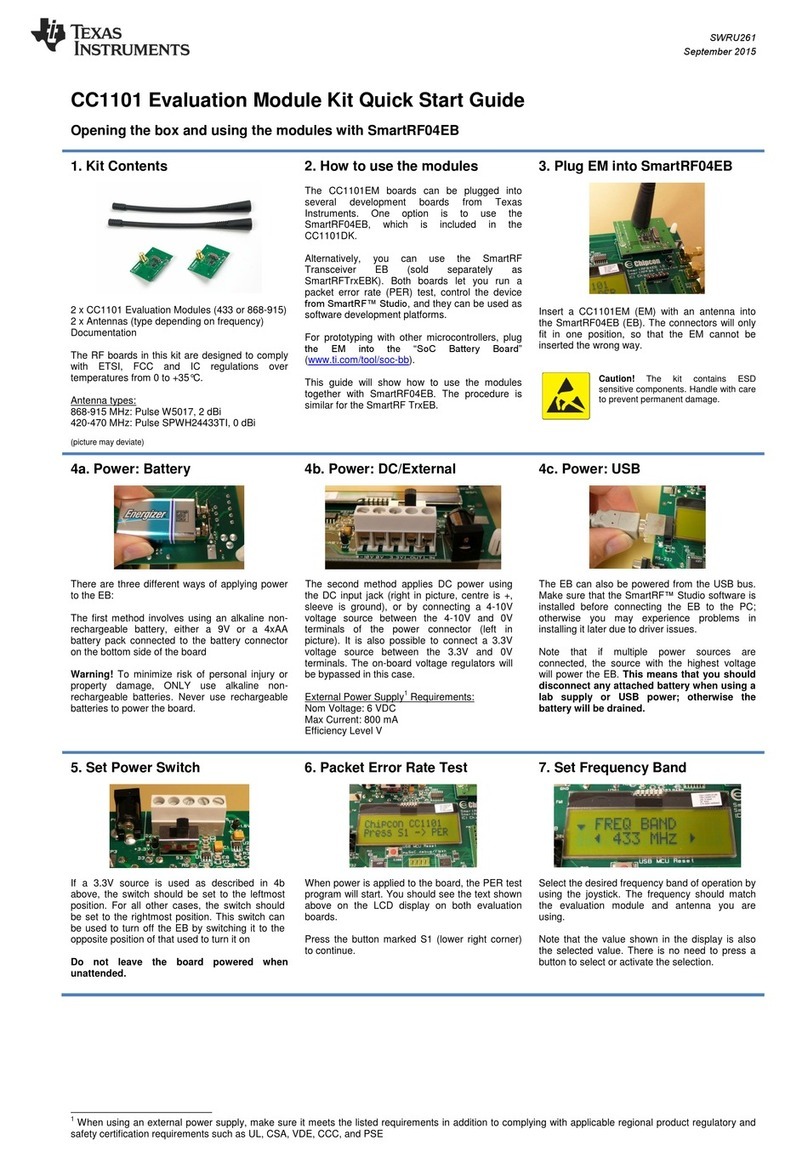
Texas Instruments
Texas Instruments CC1101 User manual
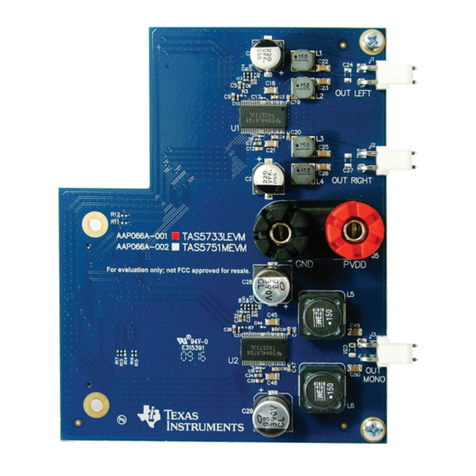
Texas Instruments
Texas Instruments TAS5733LEVM Troubleshooting guide
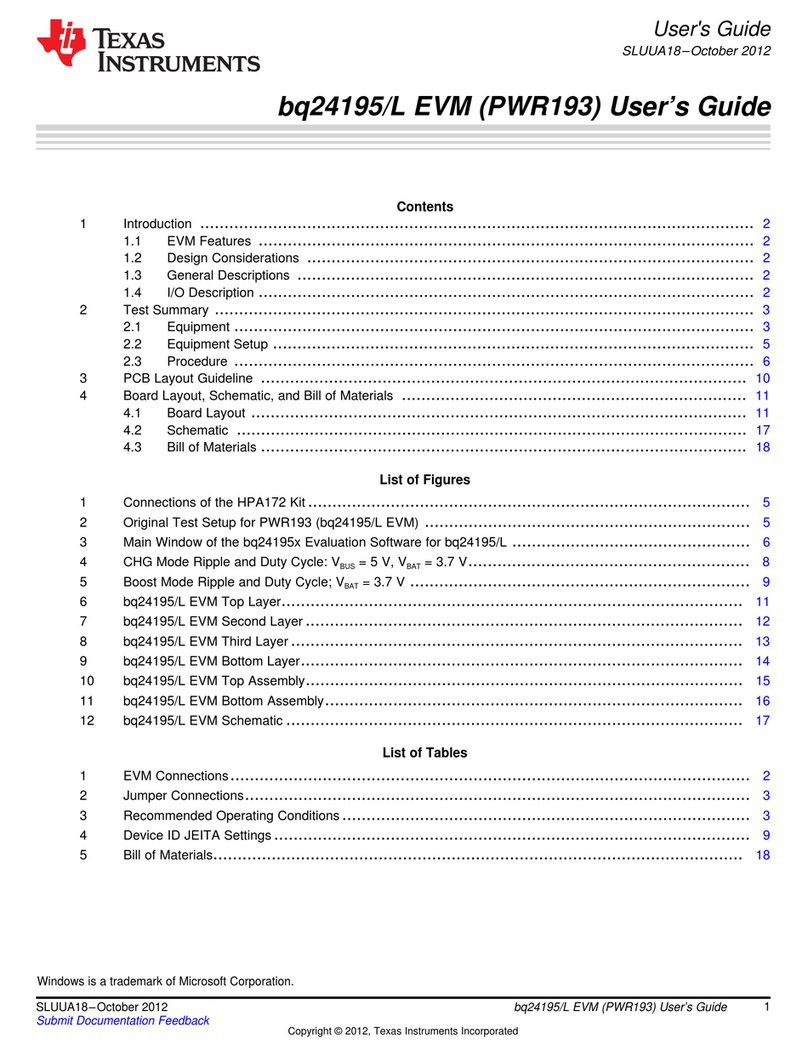
Texas Instruments
Texas Instruments bq24195/L User manual

Texas Instruments
Texas Instruments TPS65132S User manual