Trox LVC Installation and operation manual

Easy control
component
for VAV terminal units
Installation and commissioning instructions
Read the instructions prior to performing any task!
LVC • TVE • TVR • TVJ • TVT • TZ-/TA-Silenzio • TVZ • TVA
GB/en

A00000073971, 4, GB/en
© TROX GmbH 2018
TROX GmbH
Heinrich-Trox-Platz
47504 Neukirchen-Vluyn, Germany
Germany
Telephone: +49 (0) 2845 202-0
Fax: +49 (0) 2845 202-265
E-mail: [email protected]
Internet: www.trox.de
02/2022
Easy control component for VAV terminal units
2

General information
Information about installation and commissioning
instructions
These installation and commissioning instructions
enable the safe and efficient handling of the Easy type
control components and the associated VAV terminal
unit.
The manual must be kept near the unit to be available
for use at all times.
The personnel performing work on the device must read
and understand this manual carefully before starting any
work. The basic prerequisite for safe working is to
comply with the safety notes and all instructions in this
manual.
In addition, the local health and safety regulations and
general safety regulations apply to the area of applica-
tion of the device.
Illustrations in this manual are mainly for information
and may differ from the actual design.
Other applicable documentation
In addition to these instructions, the following docu-
ments must be observed:
Installation and commissioning instructions of the
VAV terminal unit
Product data sheets
Project-specific wiring documents, if any
TROX Technical Service
To ensure that your request is processed as quickly as
possible, please keep the following information ready:
Product name
TROX order number
Delivery date
Brief description of the fault
Online www.troxtechnik.com
Phone +49 2845 202-400
Safety notes
Symbols are used in this manual to alert readers to
areas of potential hazard. Signal words express the
degree of the hazard.
Comply with all safety instructions and proceed carefully
to avoid accidents, injuries and damage to property.
DANGER!
Imminently hazardous situation which, if not avoided,
will result in death or serious injury.
WARNING!
Potentially hazardous situation which, if not avoided,
may result in death or serious injury.
CAUTION!
Potentially hazardous situation which, if not avoided,
may result in minor or moderate injury.
NOTICE!
Potentially hazardous situation which, if not avoided,
may result in property damage.
ENVIRONMENT!
Environmental pollution hazard.
Tips and recommendations
Useful tips and recommendations as well as informa-
tion for efficient and fault-free operation.
General information
Easy control component for VAV terminal units 3

Safety notes as part of instructions
Safety notes may refer to individual instructions. In this
case, safety notes will be included in the instructions
and hence facilitate following the instructions. The
above listed signal words will be used.
Example:
1. Loosen the screw.
2.
CAUTION!
Danger of finger entrapment when closing
the lid.
Be careful when closing the lid.
3. Tighten the screw.
Specific safety notes
The following symbols are used in safety notes to alert
you to specific hazards:
Warning signs Type of danger
Warning – high-voltage.
Warning – danger zone.
General information
Easy control component for VAV terminal units4

1 Safety ................................................................ 6
1.1 Correct use ................................................ 6
1.2 Safety signs ............................................... 6
1.3 Residual risks ............................................ 6
1.3.1 Electric shock hazards ........................... 7
1.4 System owner's responsibility ................... 7
1.5 Staff ........................................................... 7
1.6 Personal protective equipment .................. 8
1.7 General safety measures .......................... 8
1.8 Repair and replacement parts ................... 8
2 Transport, storage and packaging ................. 9
2.1 Delivery check ........................................... 9
2.2 Transport on site ........................................ 9
2.3 Bearing ...................................................... 9
2.4 Packaging .................................................. 9
3 Structure and functional description ........... 10
3.1 Product overview types LVC, TVR, TVJ,
TVT, TZ-Silenzio, TA-Silenzio, TVZ, TVA
.................................................................. 10
3.2 Product overview TVE type ..................... 11
3.3 Position of the damper blade ................... 11
3.4 Function description ................................ 12
3.5 Operating modes ..................................... 13
3.5.1 Operation with constant volume flow
rate setpoint value ................................ 13
3.5.2 Operation with variable volume flow rate
setpoint value ....................................... 14
3.6 Characteristics ......................................... 16
4 Installation ...................................................... 17
5 Wiring ............................................................. 18
5.1 Installation instructions ............................ 18
5.2 Connection diagrams .............................. 18
6 Commissioning and operation ..................... 21
6.1 Setting of the control component ............. 21
6.1.1 Control ranges of VAV terminal units .... 22
6.1.2 Volume flow rate scale ......................... 22
6.1.3 Setting examples .................................. 23
6.1.4 Default settings qvmin and qvmax ............. 24
6.1.5 Setting constant volume flow control .... 24
6.1.6 Setting variable volume flow control ..... 24
6.2 Functional test ......................................... 25
6.3 Switching the direction of rotation ........... 25
7 Troubleshooting ............................................ 26
7.1 Common faults ........................................ 26
7.1.1 Volume flow rate deviation due to unfav-
ourable installation situation ................. 26
7.1.2 Incorrect wiring ..................................... 26
7.1.3 System pressure too low ...................... 26
7.1.4 Use outside the control range .............. 26
7.1.5 Deviation between setpoint value and
actual value signal ................................ 26
7.2 Systematic troubleshooting ..................... 28
7.3 Further diagnostic options ....................... 29
7.3.1 Use of a voltmeter to control setpoint
values and feedback signals ................ 29
7.3.2 Use of adjustment devices ................... 30
7.3.3 Adjustments sticker .............................. 30
7.3.4 Ordering replacement controllers ......... 30
8 Disposal .......................................................... 31
9 Technical data ................................................ 32
10 Declaration of conformity ............................. 35
Table of contents
Easy control component for VAV terminal units 5

1 Safety
1.1 Correct use
The electronic control component type Easy is used in
combination with a TROX air terminal unit for variable
volume flow rate control in ventilation and air condi-
tioning systems.
The Easy control component (controller Easy for short)
is designed for use indoors to control clean indoor air.
Supply air area of application:
–The usual conditioning in ventilation and air con-
ditioning systems allows the use of the Easy
controller in supply air without additional dust
protection measures.
Extract air area of application:
– Extract air with a low content of dust or lint (e.g.
office) allows the use of the Easy controller
without additional dust protection measures.
– For dry extract air with a higher proportion of
dust or lint, a suitable filter must be used in front
of the VAV terminal unit.
– For extract air with a high content of dust, lint or
sticky components, or extract air with aggressive
operating fluids, use a controller with a static dif-
ferential pressure transducer, e.g. TROX Com-
pact controller or universal controller.
– Do not use VAV terminal units in extract air sys-
tems in kitchens unless the extract air has been
cleaned as much as possible with high-effi-
ciency aerosol separators; see VDI 2052.
In unspecified applications, or when combined with pol-
luted air (e.g. dust) and moisture, a controller with static
differential pressure transducer should be used, e.g.
TROX Compact controller or universal controller.
Incorrect use
WARNING!
Danger of injury or risk of damage to property
due to incorrect use!
Misuse of the control component can lead to dan-
gerous situations.
Never use the control component/device:
–in explosion-proof areas
– in aircrafts
– outdoors without sufficient protection against the
effects of weather
– in humid air (even temporarily, e. g. in wet areas,
such as bathrooms with a shower)
– for areas of application that are not described in
this manual
Modifying the unit or using replacement parts that have
not been approved by TROX is not permitted.
1.2 Safety signs
The following symbols and signs are usually found in
the work area. They apply to the very location where
they are found.
WARNING!
Danger due to illegible signage!
Over time, stickers and signs may fade or become
otherwise illegible, meaning that hazards cannot be
identified and necessary operating instructions
cannot be followed. There is then a risk of injury.
– Ensure that all of the safety, warning and oper-
ating information is clearly legible.
–Replace illegible signs or stickers immediately.
Electrical voltage
Only skilled qualified electricians are allowed to work in
areas marked as having electrical voltage.
Unauthorised people must not enter areas, open cabi-
nets or work on components where an electrical voltage
is present and which are hence marked with this
symbol.
1.3 Residual risks
The VAV terminal unit is designed in accordance with
the state of the art and current safety requirements.
Residual risks cannot be excluded, however, and you
should proceed with caution. This section describes the
residual risks that have been identified in a risk assess-
ment.
Always read and comply with the safety notes provided
in the following chapters of this manual to reduce health
hazards and prevent any hazardous situations.
Safety
Residual risks
Easy control component for VAV terminal units6

1.3.1 Electric shock hazards
Electric current
DANGER!
Danger of death due to electric current!
Danger of electric shock! Do not touch any live com-
ponents! Damaged insulation or damaged parts are
a life threatening hazard.
– Have work on the electrical system carried out
only by skilled qualified electricians.
–If the insulation is damaged, disconnect the
power supply immediately and have the insula-
tion repaired.
– Before you start working on electric systems and
equipment, switch off the supply voltage and
secure it against being switched on accidentally.
Comply with the following safety rules:
– Switch off the power supply.
– Secure it against being switched on acciden-
tally.
– Ensure that no voltage is present.
– Connect to the earth; short circuit connection.
– Do not bypass or disable any circuit breakers. Be
sure to maintain the correct current rating when
you replace a circuit breaker.
– Ensure that live parts do not come into contact
with moisture. Moisture can cause a short circuit.
1.4 System owner's responsibility
System owner
The system owner is a natural or legal person who for
commercial or business purposes owns or manages the
ventilation system or component or allows third parties
to use or operate it, but continues to bear legal respon-
sibility for the safety of users, staff or third parties while
the product is in use.
System owner's obligations
The unit is intended for commercial use. The system
owner is therefore subject to the legal obligations of
occupational health and safety regulations.
In addition to the safety notes in this manual, the appli-
cable regulations for safety, accident prevention and
environmental protection must also be complied with.
In particular:
The system owner must be aware of the applicable
occupational health and safety regulations and carry
out a risk assessment to determine any additional
hazards that may exist or result from the specific
working conditions at the installation location. The
system owner has to create operating instructions
for the unit that reflect the results of this risk assess-
ment.
The system owner has to ensure, throughout the
entire operating period of the unit, that these oper-
ating instructions conform to applicable standards
and guidelines; in case of any deviation, the system
owner has to adapt the instructions.
The system owner must secure the unit to prevent
access by unauthorised individuals.
The system owner must clearly define the responsi-
bilities for operation, maintenance, cleaning, trouble-
shooting and removal.
The system owner has to ensure that all individuals
who handle or use the unit have read and under-
stood this manual.
The system owner must provide the employees with
the required personal protective equipment.
The system owner must observe the local fire regu-
lations.
Hygiene requirements
The system owner has to comply with the local regula-
tions and harmonised standards for hygiene require-
ments. These include, among other things, compliance
with the corresponding maintenance and test intervals.
1.5 Staff
Qualification
The work described in this manual has to be carried out
by individuals with the qualification, training, knowledge
and experience described below:
HVAC technician
HVAC technicians are individuals who have sufficient
professional or technical training in the field they are
working in to enable them to carry out their assigned
duties at the level of responsibility allocated to them and
in compliance with the relevant guidelines, safety regu-
lations and instructions. HVAC technicians are individ-
uals who have in-depth knowledge and skills related to
HVAC systems; they are also responsible for the profes-
sional completion of the work under consideration.
HVAC technicians are individuals who have sufficient
professional or technical training, knowledge and actual
experience to enable them to work on HVAC systems,
understand any potential hazards related to the work
under consideration, and recognise and avoid any risks
involved.
Safety
Staff
Easy control component for VAV terminal units 7

Skilled qualified electrician
Skilled qualified electricians are individuals who have
sufficient professional or technical training, knowledge
and actual experience to enable them to work on elec-
trical systems, understand any potential hazards related
to the work under consideration, and recognise and
avoid any risks involved.
TROX Technical Service
Staff of TROX Technical Service or of service partner
companies approved and assigned by TROX GmbH.
1.6 Personal protective equipment
Personal protective equipment is equipment that pro-
tects the user against health or safety risks at work.
Personal protective equipment must be worn for various
types of work; the protective equipment required is
listed in this manual together with the description of
each type of work.
Description of personal protective equipment
Industrial safety helmet
Industrial safety helmets protect the head from falling
objects, suspended loads, and the effects of striking the
head against stationary objects.
Protective gloves
Protective gloves protect hands from friction, abrasions,
punctures, deep cuts, and direct contact with hot sur-
faces.
Safety shoes
Safety shoes protect the feet from crushing, falling parts
and prevent slipping on a slippery floor.
1.7 General safety measures
NOTICE!
Risk of damage to property due to large tempera-
ture differences
If any electronic components have been kept in an
unheated area, condensation may form and damage
the electronic components beyond repair.
– Before you start commissioning, make sure that
all devices have warmed up to the ambient tem-
perature. Only after about 2 hours will the system
have reached ambient temperature.
Foreign matter and liquids
NOTICE!
Risk of damage to property due to foreign matter
and liquids!
Foreign matter and liquids that get into the unit may
damage the electronic parts.
– Do not use any liquids for cleaning.
– Remove foreign matter, if any.
– If the device emits a smell or smoke, have it
checked by the manufacturer.
– If liquid gets into the module, let the module com-
pletely dry before commissioning.
1.8 Repair and replacement parts
The devices must be repaired by qualified personnel
using genuine replacement parts only. This particularly
applies to work on the electrical equipment. For safety
reasons, defective devices should therefore be repaired
by the TROX Technical Service,
Ä
‘TROX Technical
Service’ on page 3 .
Safety
Repair and replacement parts
Easy control component for VAV terminal units8

2 Transport, storage and
packaging
Sharp edges and sheet metal parts
CAUTION!
Danger of injury from sharp edges and sheet
metal parts.
– Always wear protective gloves when handling the
unit.
Damage to the VAV terminal unit
NOTICE!
Risk of damage to the VAV terminal unit!
– Handle the unit with care.
– Do not lift the VAV terminal unit by its control
components, the damper blade or differential
pressure sensor.
– Lift the unit only by lifting the entire casing.
2.1 Delivery check
Check delivered items immediately after arrival for
transport damage and completeness. In case of any
damage or an incomplete shipment, contact the ship-
ping company and your supplier immediately.
The product is typically delivered mounted on a VAV ter-
minal unit.
Check the following items on delivery:
Easy controller
– Transparent protective cap, or rubber terminal
covers for TVE type.
– Mounted on the VAV terminal unit and fixed with
anti-rotation lock
– Measuring hoses without kinks connected to the
VAV terminal unit (not on TVE type)
VAV terminal unit:
– Scale sticker for setting qvmin / qvmax in place
– Adjustment sticker in place
– Cable ties for wire clamping bracket in place
(not for TVE type)
2.2 Transport on site
If possible, transport the VAV terminal unit to the
installation location in the shipping container.
Do not remove the protective wrapping until just
before installation.
2.3 Bearing
If the product has to be stored temporarily:
Moisture and lack of ventilation can lead to oxida-
tion, even on galvanised components. Remove any
plastic wrapping in order to avoid oxidation.
Protect the product from dust and contamination.
Store the product in a dry place and away from
direct sunlight.
Do not store the product below -10 °C or above +50
°C.
2.4 Packaging
Properly dispose of packaging material.
Transport, storage and packaging
Packaging
Easy control component for VAV terminal units 9

3 Structure and functional description
3.1 Product overview types LVC, TVR, TVJ, TVT, TZ-Silenzio, TA-Silenzio, TVZ, TVA
Fig. 1: Easy controller mounted on the control unit e.g. TVR
1 Easy controller
2 Measuring hoses
3 VAV terminal unit
4 Sensor tubes of the control unit
5 Wire clamping bracket
6 Scale sticker for setting qvmin/qvmax (Vmin / Vmax)
7 Terminals
8 'Test' push button
9 LED for displaying the operating states, see table
10 qvmin potentiometer (Vmin)
11 qvmax potentiometer (Vmax)
12 Axle mounting (positive connection or clamping
device)
13 Travel stops
14 Protective cap
15 Tube connection transducer
– Adjustments sticker on VAV terminal unit (not pic-
tured)
16 Service socket, not functional on Easy
Detection of operating states (LED)
LED Operating status
ON Target volume flow rate reached
Off Test push button pressed
No supply voltage
Easy controller faulty
Flashes (slowly 0.5 Hz) Actual value ≠ setpoint value, controller tries to control to the setpoint
value
Test operation started
Synchronisation process active
Flashes (rapidly 2.5 Hz) Direction of rotation change confirmation
Ä
Chapter 6.3 ‘Switching the
direction of rotation’ on page 25 );
Then slowly flashing until the synchronisation process is completed.
Structure and functional description
Product overview types LVC, TVR, TVJ, TVT, TZ-Si...
Easy control component for VAV terminal units10

3.2 Product overview TVE type
Fig. 2: TVE basic unit with Easy controller
1 Easy controller
2 Damper blade
3 VAV terminal unit
4 Lip seal
5 Scale sticker for setting qvmin/qvmax (Vmin / Vmax)
6 Release button and damper blade position indicator
7 qvmin potentiometer (Vmin)
8 qvmax potentiometer (Vmax)
9 Test push button and LED to display the operating
states, see table
10 Terminals
11 Service socket, not functional on Easy
12 Cover of the terminals
– Adjustments sticker on VAV terminal unit (not pic-
tured)
Detection of operating states (LED) TVE type
LED flashing frequency Meaning
Keine Spannungsversor-
gung
Controller not pre-set
Actuator overload
detected (block)
Positive pressure detected
on effective pressure
sensor
Synchronisation or test
mode activated
LED flashing frequency Meaning
Setpoint value or override
control position not yet
reached (0.5 Hz flashes)
Control mode setpoint
value corrected
3.3 Position of the damper blade
The position of the damper blade corresponds to the
mark on the shaft and is thus recognisable from the out-
side.
Structure and functional description
Position of the damper blade
Easy control component for VAV terminal units 11

Positive lock connection
Fig. 3: Controller with lock connection
1 Shaft with marking for position indication
2 Damper blade
Clamping device (frictional connection)
Fig. 4: Controller with clamping device
1 Shaft with marking for position indication
2 Damper blade
TVE
Fig. 5: TVE controller
1 Shaft with marking for position indication
2 Damper blade
3.4 Function description
Basic function
The Easy controller is an electronic control component
for variable volume flow control for various TROX VAV
terminal units. Its functional units consist of a dynamic
differential pressure transducer, the controller elec-
tronics and the actuator.
Closed control circuit
The controller operates in a closed control circuit:
measure – compare – control.
The determination of the current volume flow rate takes
place by measuring a differential pressure (effective
pressure). For this purpose, the air terminal unit has a
differential pressure sensor. The effective pressure is
forwarded through the measuring hoses or, in the case
of TVE, through the damper blade shaft to the differen-
tial pressure transducer integrated in the control compo-
nent where it is converted into a voltage signal.
The volume flow rate actual value is thus the internal
control loop as well as an external use, e.g. BMS or
master-slave sequential circuit, available as analogue
voltage signal 0‑10 V. Due to the factory adjustment, the
maximum output value of 10 V DC always corresponds
to the nominal volume flow rate (qvnom) which can be
taken from the scale sticker and the adjustments sticker
on the VAV terminal unit.
The nominal volume flow rate is either set as a constant
value or specified by an analogue voltage signal at the
setpoint value input. The definition of the constant
volume flow rates or of the working range for variable
operation is carried out by the customer via the potenti-
ometers qvmin and qvmax.
Structure and functional description
Function description
Easy control component for VAV terminal units12

In regular operation, the integrated actuator is controlled
by permanent evaluation of the offset (setpoint value-
actual) that adjusts the damper blade of the air terminal
unit via the axle mounting and thus regulates the
volume flow rate to the setpoint value.
Setpoint value adjustment independent of the duct
pressure
Fig. 6: Pressure independent control characteristics
The controller detects and corrects changes of the duct
pressure that may occur, for example, due to volume
flow rate changes from other units. The Easy controller
thus operates independent of duct pressure and pres-
sure fluctuations result in no permanent changes to the
volume flow rate.
In order to prevent the volume flow control from
becoming unstable, the controller maintains a dead
band (hysteresis) within which the damper blade is not
moved. This dead band and the tolerances of the meas-
urement location lead to a volume flow rate deviation
Δqv in accordance with the product data sheets of the
VAV terminal units. If the conditions specified in the
product data sheets (e.g. minimum differential pressure,
upstream conditions) are not met, greater deviations are
to be expected.
Diagnostic options
A functional test is possible using the test push button
( Fig. 1 /8) and LED indicator light ( Fig. 1 /9). The LED
makes it possible to distinguish between operating and
fault states.
The diagnosis of setpoint value and actual value signals
is possible via voltmeter,
Ä
Chapter 7.3.1 ‘Use of a
voltmeter to control setpoint values and feedback sig-
nals’ on page 29 .
Adjustment devices cannot be used for Easy controllers,
Ä
Chapter 7.3.2 ‘Use of adjustment devices’
on page 30 .
3.5 Operating modes
3.5.1 Operation with constant volume flow
rate setpoint value
Operation with a fixed setpoint value
Fig. 7: Constant control
1 Volume flow rate setpoint value specification (qvmin)
2 Actual value volume flow rate as 0–10 V DC signal,
e.g. to the central BMS
In the simplest case, the controller is operated with a
constant volume flow rate setpoint value specification.
During commissioning, the setpoint value is set directly
on the rotary potentiometer (qvmin) on the Easy controller
(qvmax = 0%).
A control signal at terminal w is not required in this
case.
Structure and functional description
Operating modes > Operation with constant volume flow rate setpo...
Easy control component for VAV terminal units 13

Operation with two setpoint values (min./max.
switching)
Fig. 8: Min./max. switching
1 Volume flow rate setpoint value specification (qvmin
and qvmax)
2 Switch or relay for switching between qvmin and qvmax
3 Actual value volume flow rate as 0–10 V DC signal,
e.g. to the central BMS
The constant values (vmin and vmax) set on the rotary
potentiometer can be activated alternately via volt-free
switch contacts. Switching is accomplished by switches
or relays, e. g., day/night switching.
3.5.2 Operation with variable volume flow
rate setpoint value
Fig. 9: Variable volume flow control
1 Volume flow rate limit specification (qvmin and qvmax)
2 Control signal 0–10 V DC at terminal w as setpoint
value input, e.g. from room temperature controller or
DCC outstation or similar
3 Actual value volume flow rate as 0–10 V DC signal,
e.g. to the central BMS
For the use of variable volume flow rate setpoint values,
the specification of an electrical control signal must be
made by a higher-level controller (e.g. room temperature
controller, air quality controller, central building manage-
ment system, etc.). If the input signal is changed, the
controller adjusts the volume flow rate to the new set-
point. The variable volume flow rate is limited to a min-
imum and maximum volume flow rate value,
Ä
Chapter
3.6 ‘Characteristics’ on page 16 .
Override control
The constant or variable control can be disabled by
override controls, e.g. when the window is open, a
window switch stops ventilation of the room by closing
the damper blade.
Further application examples:
Circuits for quick ventilation (qvmax)
Opening the damper blade
Structure and functional description
Operating modes > Operation with variable volume flow rate setpo...
Easy control component for VAV terminal units14

Supply/extract air tracking control
Fig. 10: Supply/extract air tracking control
1 Volume flow rate limit specification (qvmin and qvmax)
2 Room temperature controller (control signal for
supply air controller)
3 Actual value volume flow rate as 0–10 V DC signal
to the extract air controller
4 Actual value volume flow rate as 0–10 V DC signal,
e.g. to the central BMS
In individual rooms and closed-off office areas, where the balance between supply and extract air flow rate has to be
maintained. Otherwise, annoying whistling noises can occur at door gaps, and the doors can be difficult to open. For
this reason, the extract air should also have variable control in a VAV system.
The control signal from the room temperature controller is switched to the supply air controller in this example. The
actual value signal of the Easy controller for the supply air is then applied as a setpoint signal for the Easy controller
on the extract air (slave controller). As a consequence, the extract air always follows the supply air.
Setting for the slave controller in the simplest case (same VAV terminal units and dimensions):
qvmin 0%
qvmax100%
When using different air terminal unit types or dimensions for tracking control, special setting instructions for qvmin
and qvmax of the slave controller must be observed due to the different nominal volume flow rates.
Alternatively, the control signal of the room temperature controller can also be connected in parallel to the supply air
and the extract air controller. The limitation due to the technical data of the controller outputs (current) and the con-
troller inputs (input resistances) must be observed.
Structure and functional description
Operating modes > Operation with variable volume flow rate setpo...
Easy control component for VAV terminal units 15

3.6 Characteristics
Actual value signal
Fig. 11: Characteristic of the actual value signal 0–10 V
The actual value volume flow rate can be tapped as a
voltage signal at the terminal (U). The measuring range
is factory-set to the size of the VAV terminal unit, so that
the respectively rated nominal flow rate (qvnom) always
corresponds to an actual value signal of 10 V DC. The
current actual value volume flow rate can be calculated
from the measured voltage at the output (U) using the
formula below.
Setpoint value signal
Fig. 12: Characteristic of the reference signal 0–10 V
In order to specify a volume flow rate setpoint value to
the Easy controller, a DC voltage signal in the range of
0–10 V DC must be applied to the terminal (w).
The relationship between the nominal volume flow rate
and the associated voltage signal can be calculated
using the formula below. The setting of the potentiome-
ters qvmin and qvmax must be taken into account.
The default settings of the working range qvmin = 40 %
and qvmax = 80 % can be easily changed by the cus-
tomer.
Calculation example:
qvnom of the VAV terminal
unit:
- 800 m³/h
qvmin - should be 200 m³/h
qvmax - should be 600 m³/h
At a setting of qvmin = 0 % and qvmax = 100 %, the control-
ling unit can specify the entire nominal volume flow rate
range of the VAV terminal unit as a setpoint value.
If qvmin and qvmax are set to only a partial range of the
nominal volume flow rate range, a higher resolution for
the control input signal is available for this work area. In
the first case, the limitation of the setpoint signal to the
work area must be taken into account by the superordi-
nate rule instance,
Ä
Chapter 6.1.1 ‘Control ranges of
VAV terminal units’ on page 22 .
Structure and functional description
Characteristics
Easy control component for VAV terminal units16

4 Installation
Personnel:
HVAC technician
Protective equipment:
Protective gloves
Safety shoes
Industrial safety helmet
Only specialist personnel are allowed to perform the
described work on the VAV terminal unit.
Only skilled qualified electricians are allowed to work on
the electrical system.
CAUTION!
Danger of injury from sharp edges and sheet
metal parts.
– Always wear protective gloves when handling the
unit.
The Easy controller is delivered mounted on the VAV
terminal unit, so that the work is limited to electrical
wiring
Ä
Chapter 5 ‘Wiring’ on page 18 and setting
of the Easy controller
Ä
6.1 ‘Setting of the control
component’ on page 21 .
When installing the VAV terminal unit, take particular
note of the following points:
Upstream section
Direction of airflow
Fixing/suspension
Accessibility for service work
Information on this can be found in the VAV terminal unit
installation and commissioning instructions.
Installation orientation
The installation orientation of the VAV terminal unit is
arbitrary due to the dynamic differential pressure trans-
ducer in the Easy controller. The Easy controller must
be located on, under or to the side of the ductwork.
Installation
Easy control component for VAV terminal units 17

5 Wiring
Safety instructions
DANGER!
Danger of electric shock! Do not touch any live com-
ponents! Electrical equipment carries a dangerous
electrical voltage.
– Only skilled qualified electricians are allowed to
work on the electrical system.
–Switch off the power supply before working on
any electrical equipment.
5.1 Installation instructions
The VAV terminal unit was manufactured and configured
on a project-specific basis. The control components are
factory-mounted and balanced. For installation, the
supply voltage and, if necessary, signal lines, must be
connected for electrical control components.
The connection is established based on the information
specified on the control components or connection dia-
grams in this manual. Project-specific wiring diagrams
must be observed. The voltage ranges and terminal
connections specified on the control components must
be observed!
Personnel:
Skilled qualified electrician
Observe the following during installation:
Legal and official regulations, in particular VDE
guidelines.
Consideration of the technical connection rules
(TCR) of the local network operators.
Wiring work for supply voltage and signal lines on
site.
The rating and manufacture of customer-side con-
nections and wiring must be carried out in accord-
ance with the recognised rules of electrical engi-
neering.
Observe wiring guidelines and project-specific circuit
diagrams of the control components.
The electrical connection to the terminal unit may
only be established if the installation has been car-
ried out correctly.
The 24 V supply voltage must only be supplied with
a safety transformer.
To protect against overload, the supply voltage for a
maximum of three Easy controllers may be through-
wired.
If multiple volume flow rate controllers are con-
nected to a 24 V network, it must be ensured that a
common neutral or ground line is defined and not
interchanged.
The control component contains no parts that can
be replaced or repaired by the user and may only be
opened by the manufacturer.
Remove the transparent protective cap of the Easy
controller only temporarily for wiring and commis-
sioning, not available for TVE.
For TVE type only: to ensure IP protection, use the
rubber cover to insert the connection cables.
Lay connecting cables in such a way that they
cannot be accidentally damaged by mechanical
impact or by heat.
Electrical safety
The control component complies with all relevant stand-
ards and guidelines, see declaration of conformity.
Open terminals
According to the electro-technical regulations, contact
protection insulation is only required for active parts.
Because Easy controllers are operated with protective
extra-low voltage (PELV), the screw terminals are not
considered active parts.
Wire clamping bracket
Devices that are permanently installed in buildings are
stationary electrical equipment for which no wire
clamping bracket on the connecting cables is pre-
scribed.
Some VAV terminal units come with a wire clamping
bracket (cable tie) that can be used to secure the con-
necting cable as part of electrical installation work.
5.2 Connection diagrams
Terminals
Fig. 13: Terminals
1 Ground
2 24 V AC / DC supply voltage
3 Setpoint value signal (w) 0 – 10 V DC
4 Actual signal (U) 0 – 10 V DC
The connection terminals for the supply voltage (1 and
2) are doubled for easy rewiring.
Caution: to protect against overload, the supply voltage
for a maximum of three Easy controllers must be
through-wired.
Terminals for 0.5 to 2.5 mm² cables, rigid and flexible.
Wiring
Connection diagrams
Easy control component for VAV terminal units18

Control constant volume flow rate qvmin
Fig. 14: Constant volume flow rate qvmin
After applying the 24 V supply voltage, the controller
throttles the volume flow rate to the value set on the
qvmin potentiometer. A setpoint value signal is not
required. The current actual value volume flow rate can
be tapped at the terminal (U).
Variable volume flow control qvmin…qvmax
Fig. 15: Variable volume flow control
If the volume flow rate is to be specified by a higher-
level controller (e. g. for room temperature, air quality or
a DDC outstation), its 0–10 V DC output must be con-
nected by at least 2 wires (terminals 1 and 3) to the ter-
minals for the control signal (w) of the Easy controller in
accordance with the connection diagram. With a
common 24 V supply voltage, it should be noted that
terminal 1 on the Easy controller is also the ground for
the control signal.
Switching between volume flow rates qvmin and qvmax
Fig. 16: Switching between volume flow rates qvmin and
qvmax
If the volume flow rate between two constant values can
be switched (e. g., day/night switching), it is possible to
switch over between the volume flow rate setpoint
values specified by the qvmin and qvmax potentiometers
using an on-site volt-free switch contact.
Switch S1 open - qvmin
Switch S1 closed - qvmax
Parallel connection
Fig. 17: Parallel connection
If multiple Easy controllers are to be switched simulta-
neously with a switch contact between qvmin and qvmax,
the S1 switch must be designed as a changeover
switch, and the contact for qvmin operation must be con-
nected to the ground (terminal 1)
Wiring
Connection diagrams
Easy control component for VAV terminal units 19

Override control on/off
Fig. 18: Override control
When using a 24 V AC supply voltage, special operating
states, so-called override controls, can alternatively be
activated.
For this purpose, it is necessary to have a different cir-
cuit with a diode circuit and volt-free switch contacts,
provided by others.
Switch S2 closed - CLOSED (closed position)
Switch S3 closed - OPEN (open position)
Note: this functionality is only available with AC supply
voltage.
All override controls can be combined both with each
other and with the different switching options. When
combining several override controls the switches must
be interlocked to prevent short-circuits.
With activation of the override control "damper blade
CLOSED", the VAV terminal unit is put into the closed
position. Depending on the design of the VAV terminal
unit, residual leaks may remain, or an air-tight shut-off
can be achieved. For more detailed information, see
technical data of the VAV terminal unit.
Control qvmin ... qvmax with 20 mA control signal
Fig. 19: Variable volume flow
Connection of a reference signal from 0 to 20 mA is also
possible. For this purpose, a resistance of 500 Ω is
placed between the ground and input (w). The actual
value output (U) is always available as voltage signal
0–10 V DC.
Wiring
Connection diagrams
Easy control component for VAV terminal units20
This manual suits for next models
22
Table of contents
Popular Touch Terminal manuals by other brands
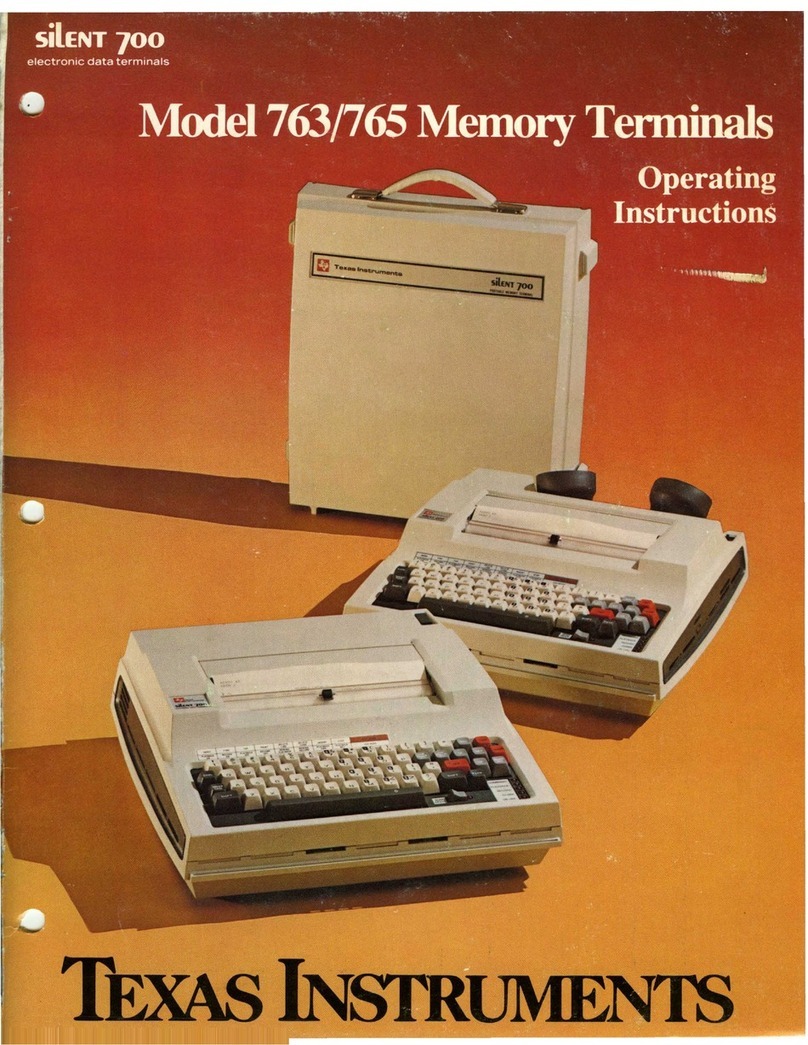
Texas Instruments
Texas Instruments Silent 700 763 operating instructions

TP-Link
TP-Link Agilent XGZ030 Quick installation guide
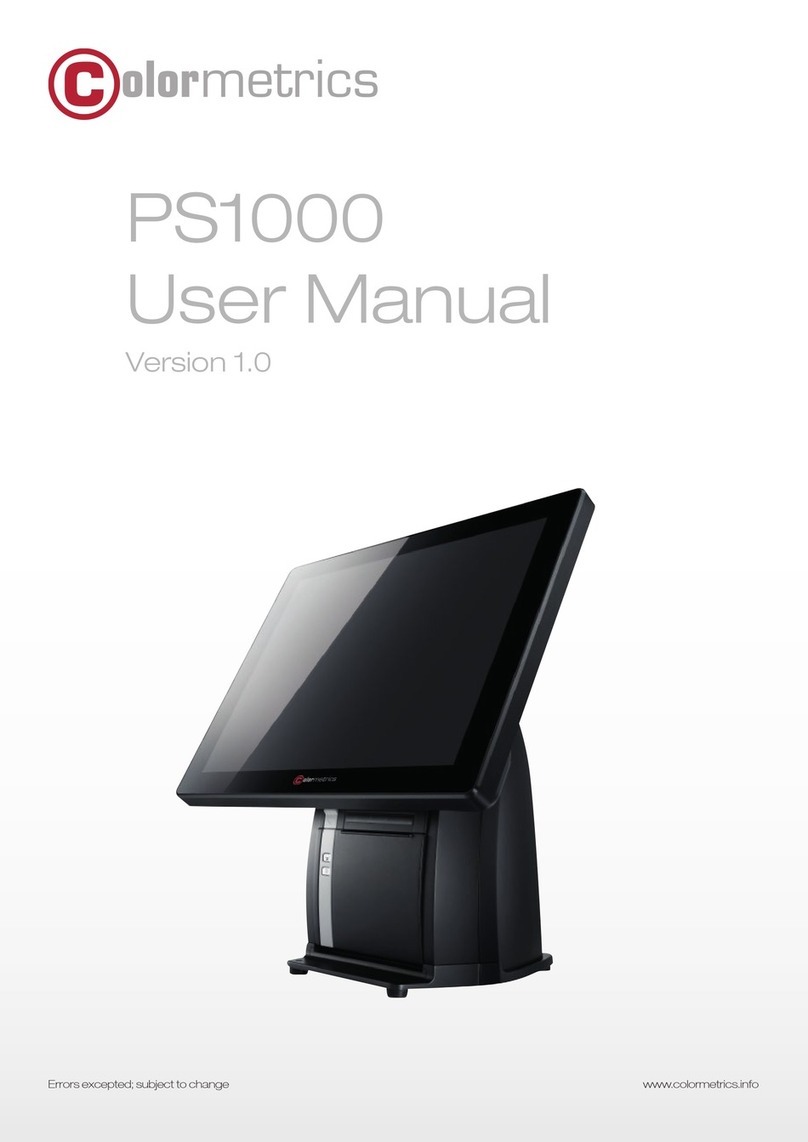
Colormetrics
Colormetrics PS1000 user manual
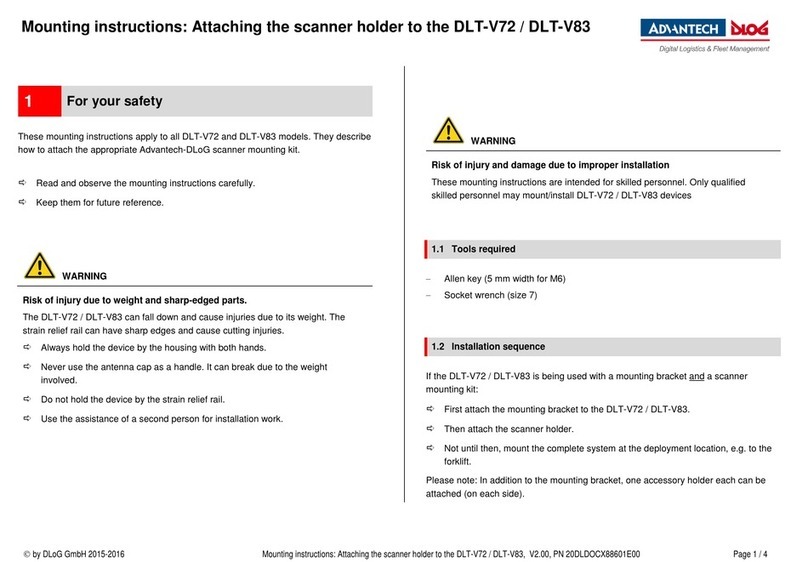
Advantech-DLoG
Advantech-DLoG DLT-V72 Series Mounting instructions
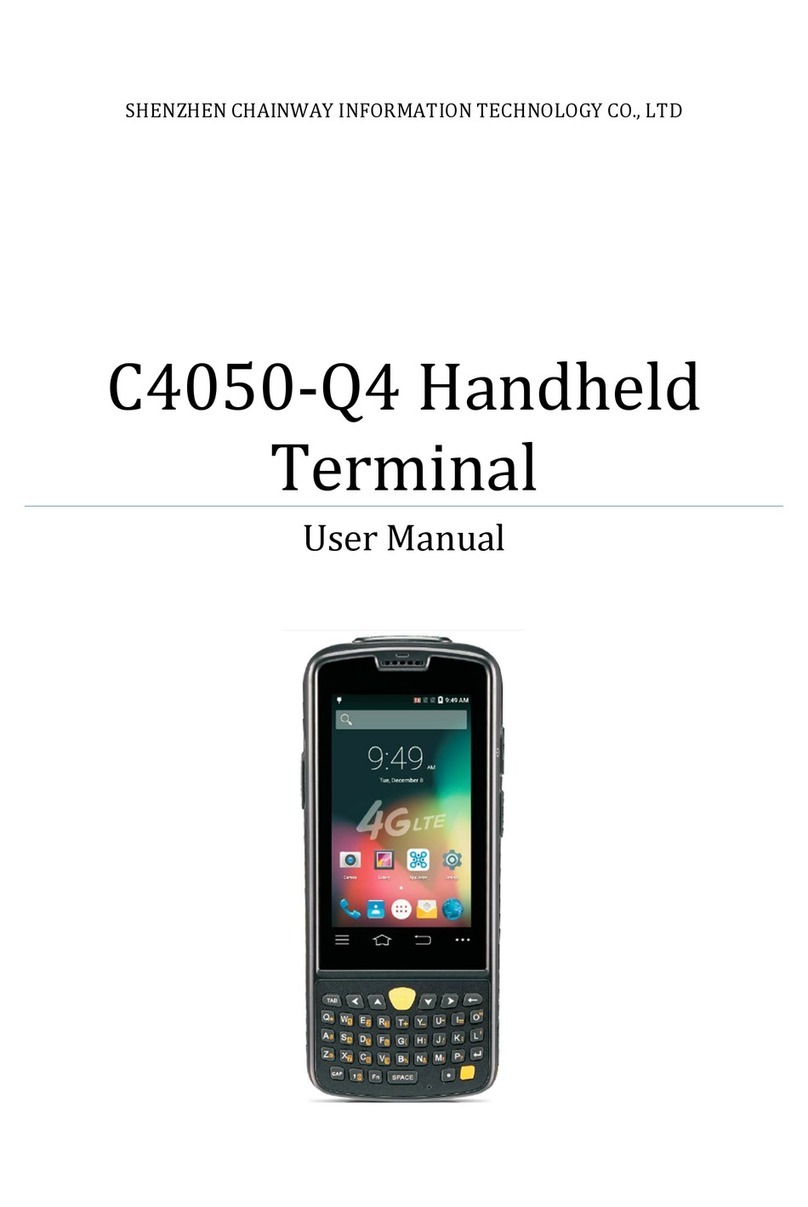
Shenzhen Chainway ITS Co.
Shenzhen Chainway ITS Co. C4050-Q4 user manual
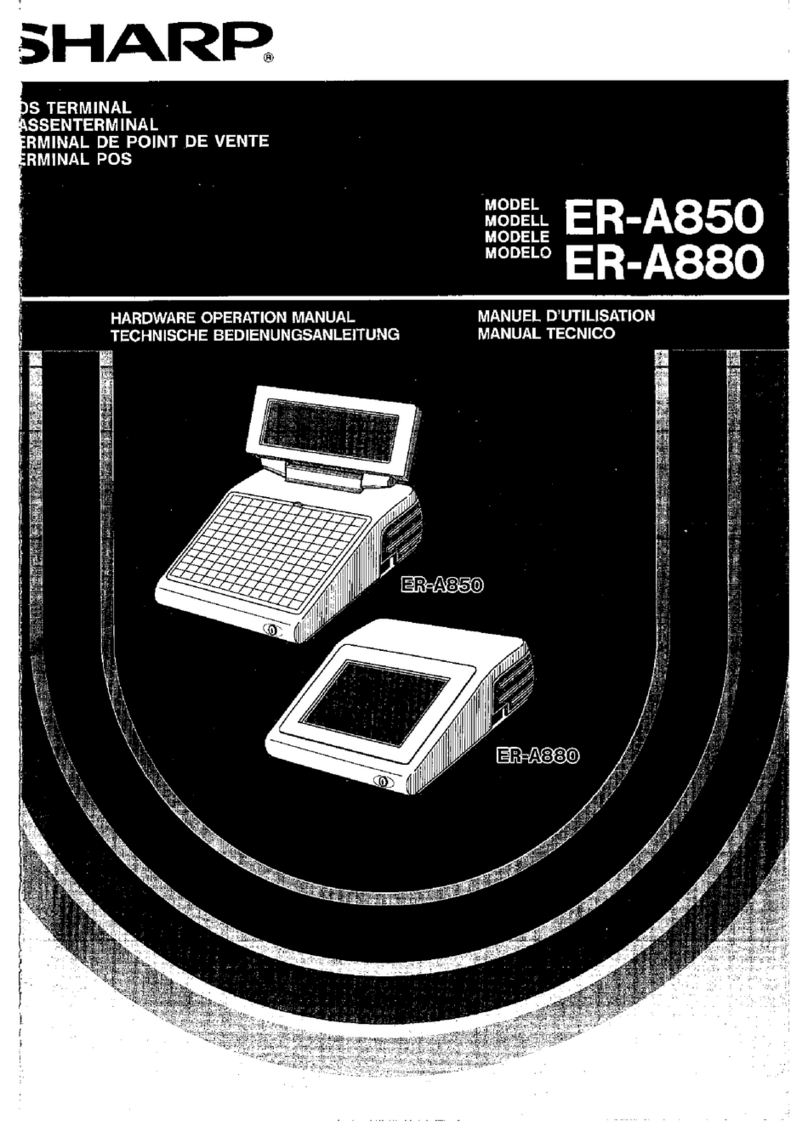
Sharp
Sharp ER-A850 Operation manual