Verasys ZEC410 User manual

ZEC410 VAV Controllers Installation Instructions
Refer to the QuickLIT website for the most up-to-date version of this document.
Contents subject to change.
1
ZEC410 VAV Controllers
Installation Instructions
LC-ZEC410-xx Part No. 24-10143-1264, Rev. –
Issued January 2017
Applications
The ZEC410 VAV Controllers are components of the Verasys SMART equipment family. The VAV Zone controllers run
a pre-engineered HVAC zoning sequence and provide the inputs and outputs required for this application.
The ZEC Controller contains multiple features to ensure occupant comfort. Optional occupancy sensing capability
enables the ZEC controller to switch from occupied mode to standby mode based upon zone activity. Standby mode
maximizes energy savings by using setpoints that are higher and lower than occupied mode setpoints.
The ZEC410 controller also uses plug and play technology to detect which network sensor types are connected. See
the Accessories section to determine availability of additional sensing product information.
You use the Verasys Smart Building Hub to set up the ZEC410 controller. The VAV controller commissioning is
performed with either the Smart Building Hub or the VAV Balancing Thermostat.
North American Emissions Compliance
United States
Canada
IMPORTANT: Use this ZEC410 VAV controller only as an operating control. Where failure or malfunction of the
PEAK OEM controller could lead to personal injury or property damage to the controlled equipment or other
property, additional precautions must be designed into the control system. Incorporate and maintain other
devices, such as supervisory or alarm systems or safety or limit controls, intended to warn of or protect against
failure or malfunction of the ZEC410 VAV controller.
IMPORTANT : Utiliser ce ZEC410 VAV Controller uniquement en tant que dispositif de contrôle de
fonctionnement. Lorsqu'une défaillance ou un dysfonctionnement du controller risque de provoquer des
blessures ou d'endommager l'équipement contrôlé ou un autre équipement, la conception du système de
contrôle doit intégrer des dispositifs de protection supplémentaires. Veiller dans ce cas à intégrer de façon
permanente d'autres dispositifs, tels que des systèmes de supervision ou d'alarme, ou des dispositifs de
sécurité ou de limitation, ayant une fonction d'avertissement ou de protection en cas de défaillance ou de
dysfonctionnement du ZEC410 VAV controller.
This equipment has been tested and found to comply with the limits for a Class A digital device pursuant to
Part 15 of the FCC Rules. These limits are designed to provide reasonable protection against harmful
interference when this equipment is operated in a commercial environment. This equipment generates, uses,
and can radiate radio frequency energy and, if not installed and used in accordance with the instruction
manual, may cause harmful interference to radio communications. Operation of this equipment in a residential
area may cause harmful interference, in which case users will be required to correct the interference at their
own expense.
This Class (A) digital apparatus meets all the requirements of the Canadian Interference-Causing Equipment
Regulations.
Cet appareil numérique de la Classe (A) respecte toutes les exigences du Règlement sur le matériel brouilleur
du Canada.

ZEC410 VAV Controllers Installation Instructions
2
Installation
Observe these guidelines when installing a ZEC controller:
• Transport the ZEC controller in the original container to minimize vibration and shock damage to the ZEC
controller.
• Do not drop the ZEC controller or subject it to physical shock.
Parts Included
• one ZEC controller with removable FC and SA buses and power terminal blocks
• one self-drilling No. 10 x 25 mm (1 in.) screw
Materials and Special Tools Needed
• 6 mm (1/4 in.) female spade terminals for input and output wiring and crimping tool or spade mounted terminal
blocks
• small straight-blade screwdriver for securing wires in the terminal blocks
• 8 mm (5/16 in.) wrench or 10 mm (3/8 in.) 12-point socket to tighten the square coupler bolt
• shims or washers to mount the ZEC, if necessary
• power screwdriver, 100 mm (4 in.) extension socket,
or a
punch, drill, and 3.5 mm (9/64 in.) drill bits to mount
the ZEC
• pliers to open and close the damper
• 3.97 mm (5/32 in.) ID poly tubing
Mounting
Observe these guidelines when mounting a ZEC:
• Ensure that the mounting surface can support the ZEC
and any user-supplied enclosure.
• Mount the ZEC on a hard, even surface whenever possible.
• Use shims or washers to mount the ZEC securely and evenly on the mounting surface, if necessary.
• Mount the ZEC in an area free of corrosive vapors that matches the ambient conditions specified in the
Technical Specifications section.
• Provide sufficient space around the ZEC for cable and wire connections and adequate ventilation through the
controller (at least 50 mm [2 in.] on the top, bottom, sides, and front of the controllers).
• Do not mount the ZEC in areas where electromagnetic emissions from other devices or wiring can interfere
with controller communication.
• Avoid mounting the ZEC on surfaces with excessive vibration.
Onpanelorenclosuremountapplications,observethese additional guidelines:
• Do not install the ZEC in an airtight enclosure.
• Mount the ZEC so that the enclosure walls do not obstruct cover removal or ventilation through the controller.
• Mount the ZEC so that the power transformer and other devices do not radiate excessive heat to the controller.
IMPORTANT: WhentheairsupplytotheVAVboxisbelow 10°C (50°F), make sure that any condensation on the
VAV box, particularly on the damper shaft, does not enter the ZEC electronics. Mount the ZEC vertically above
the damper shaft to allow any shaft
condensation to fall away from the ZEC. Additional measures may be
required in some installations.

ZEC410 VAV Controllers Installation Instructions
3
Tomount the ZEC controllers:
1. Ensure that you have the appropriate personal protective equipment (PPE), such as a hard hat, safety glasses,
steel toe boots, and gloves.
2. Disconnect power from the controller transformer as well as the VAV box fan and heater circuits, if applicable.
3. Set all the switches on the field controller to their known settings, and then set the Master-Slave/Token-Passing
(MS/TP) address, and ensure that EOL is set to Off. See Setup and Adjustments.
4. Place the ZEC controller in the proper mounting position on the actuator shaft so that the wiring connections
are easily accessible. Make sure the ZEC controller base is parallel to the VAV box (perpendicular to the
damper shaft). If needed, use a spacer to offset tipping of the ZEC controller caused by the shaft bushings.
Note: Usethealignmentmarkstocenterthecaptive spacer to ensure sufficient ZEC movement in either direction
(Figure 8).
5. Secure the self-drilling No. 10 screw through the captive spacer with a power screwdriver and
100 mm (4 in.)extension socket. Otherwise,use a punch to mark the position of the shoulder washer,
andthen
drilla hole intotheVAVbox usinga 5/16 in. drill bit. Insert the mounting screw and tighten it against the spacer.
6. Locatethe damper position usingthetypicalmarking on the end of the damper shaft.
Table 1: Verasys System Bus Controller Addressing
System Bus
Address/Range Standalone Verasys System Bus
(not integrated into a BACnet BAS
network)
Verasys System Bus
(integrated into a BACnet BAS network)
1May be used for Verasys system controllers Used for BACnet reserved function devices - not
used for Verasys System Bus controllers
2
3Address used by an FC Bus or System Bus - connected to a Smart Building Hub - not used for Verasys
System Bus controllers or BACnet device address
May be used for Verasys System Bus controllers if
there is not an FC Bus or System Bus connected
Smart Building Hub
May be used for Verasys System Bus controllers if
there is not an FC Bus or System Bus connected
4May be used for Verasys System Bus controllers May be used for Verasys System Bus controllers if
there is a not a BACnet device address conflict
117 Address used by the Smart Building Hub - not used for other Verasys System Bus controllers or BACnet
device address
118 through 127 May be used for Verasys System Bus controllers May be used for Verasys System Bus controllers if
there is not a BACnet device address conflict
IMPORTANT: Do not overtighten the screw, or the threads may strip. If you mount the ZEC to the VAV box,
make sure thatthe screws do not interferewithdamperblademovement.
Alignment
Marks
Figure 1: Captive Spacer Alignment Marks

ZEC410 VAV Controllers Installation Instructions
4
7. Note the direction, clockwise (CW) or counterclockwise (CCW), required to close the damper. The actuator
setup depends on the necessary amount of rotation required for the damper to go from full-open to full-closed.
For 90° rotation, install the damper full-closed. For 45° or 60° rotation, install the damper full-open.
8. Push down and hold the Manual Override button and turn the ZEC controller coupler until it contacts the
mechanical end-stop at either the full-closed or full-open position.
9. If the damper for a 45° or 60° box closes CCW, rotate the coupler to the CW mechanical limit. If the damper for
a 45° or 60° box closes CW,rotate the coupler to the CCW mechanical limit. This action sets the open end-
stop; the closed end-stop is set by the closed damper.
For 45° and 60° boxes, hard stopsmust be provided at both full-closed and full-open damper positions. By
installing the ZEC controller at the full-open position, the ZEC controller provides the open stop for 45° and 60°
boxes. The closed damper seal provides the full-closed stop.
10. Tighten the square coupler bolt to the shaft using an8 mm (5/16 in.) wrench or 10 mm (3/8 in.) 12-point socket.
Tighten to 10.5 to 11.5 N·m (95 to 105 lb·in).
11. Put a loop in the poly tubing, to trap condensation, when you attach the poly tubing to the ZEC pressure
transducer ports. Loop the poly tubing before you make the final connections.
12. Push the Manual Override button, and turn the actuator coupling manually to ensure that the actuator can
rotate from full-closed to full-open positions without binding.
13. Complete the mounting by rotating the damper to
the full-open position.
Figure 2: Manual Override and Coupler

ZEC410 VAV Controllers Installation Instructions
5
Wiring
Observe the following guidelines when wiring a ZEC controller.
Input and Output Terminals
See Figure 8 for an example of the staged control wiring. See Figure 9 for an example of the incremental control
wiring.
Sensor Actuator (SA) Bus Terminal Block
The SA Bus terminal block is a brown, removable 4-terminal plug, that is keyed to only fit into the board-mounted
brown SA bus.
Risk of Electric Shock.
Disconnect power from the controller before making any adjustments. Do not touch any part of the printed circuit
board while power is applied. Failure to follow these precautions can result in personal injury or death.
Risque de décharge électrique.
Déconnecter l'alimentation du controller avant toute opération de réglage. Veiller à ne toucher aucune partie du
circuit imprimé lorsque celui-ci est sous tension. Le non-respect de ces précautions peut provoquer des blessures
graves, voire mortelles.
IMPORTANT: Make all wiring connections in accordance with the National Electrical Code and local
regulations. Use proper electrostatic discharge (ESD) precautions during installation and servicing to avoid
damaging the electronic circuits of the controller.
IMPORTANT: Do not exceed the controller electrical ratings. Exceeding controller electrical ratings can result in
permanent damage to the controller and void any warranty.
IMPORTANT: Do not connect supply power to the controller before finishing wiring and checking all wiring
connections. Short circuits or improperly connected wires can result in damage to the controller and void any
warranty.
IMPORTANT: Use copper conductors only. Make all wiring in accordance with local, national, and regional
regulations.

ZEC410 VAV Controllers Installation Instructions
6
Wire the removable SA Bus terminal block plugs on the ZEC and other field devices in a daisy-chain configuration
using 4-wire twisted, shielded cable as shown in Figure 3.
Field Controller (FC) Bus Terminal Block
The FC Bus terminal block is a blue, removable, 4-terminal plug that is keyed to only fit in to the board-mounted,
blue FC Bus jack.
Wire the removable FC Bus terminal block plugs on the ZEC and other FC Bus controllers in a daisy-chain
configuration using 3-wire twisted, shielded cable, as shown in Figure 4.
Modular Ports
The modular SA Bus and FCBus ports on the face of the ZEC are RJ-12 (6-position) modular jacks.
The modular SA Bus ports provide a connection for the VAV
Balancing Tool. The FC Bus port is not used in ZEC
installations.
Figure 3: SA Bus Terminal Block Wiring
Stranded, 4-Wire (2 Twisted Pair) Shielded Cable
(One twisted pair is the and leads.
The second pair is COM and SA PWR.)
+ -
Cable Shield
Connection
To Next
Device on
the SABus
FIG:sa_bus_spade
SA Bus
Spade Lugs
Terminating Device
on SABus
Daisy Chained Device
on SABus
To Next
Device on
the SABus
+
COM
PWR
+
CO
M
PW
R
Figure 4: FC Bus Terminal Block Wiring
SHIELD
CO M
-
+
Cable Shield
Connection
To Next
Device on
the FC Bus
FIG:sa_bus_spade
FC Bus
Spade Lugs
Terminating Device
on FC Bus Daisy Chained Device
on FC Bus
To Next
Device on
the FC Bus
SHIELD
COM
-
+
Figure 5: Pin Number Assignments
SA and FC Bus Ports
Power
(15 VDC)
SA or FC Bus +
SA or FC Bus
-
Bus and Power Common
Power
(15 VDC)
Bus and Power Common
FIG:rj12_pinout
2
3
4
5
6
1

ZEC410 VAV Controllers Installation Instructions
7
Supply Power Terminal Block
The 24 VACsupply power terminal block is a gray,
removable,2-terminalplugthatfitsintoaboard-mounted jack on
the upper left of the ZEC controller.
Wirethe 24VACsupplypower wires fromthetransformer to the HOT and COM terminals on the terminal plug.
To wire the ZEC410 controller:
1. Terminate wiring according to Figure 8 if you are using staged outputs for the heating control. See Figure 9 if
you are using incremental outputs for the heating control.
2. Wire the network temperature sensor and CO2sensor to the ZEC’s SA Bus.
3. Wire the FC Bus in a daisy chain.
4. Ensure that the ZEC’s device address DIP switches are set to the appropriate device address. (See Setup and
Adjustments.) Also, activate the end-of-line (EOL) switch if necessary.
IMPORTANT: The 24 VAC power should not be shared with other network devices. Sharing power with other
network devices may cause noise, interference, and ground loop problems. You may damage the controller by
sharing power with other devices.
Figure 6: VAC Supply Power
Terminal Block Wiring
ZEC410
Supply Power
Terminal Block
Wires from
24 VAC, Class 2
Power Transformer
COM 24 VAC

ZEC410 VAV Controllers Installation Instructions
8
5. Connect the ZEC controller to 24 VAC, Class 2 power.
Figure 7: ZEC410-1 Controller - VAV with Staged Reheat Control Wiring Example
VAV with No Fan
HTG2-C
(Optional)
E
C
HTG1-C
(Optional)
ZEC410-1
SUPHTG1-C
(Optional)
ZN-T
SA DA
ZN-CO2
(Optional)
OCC-S
(Optional)
DA-T
(Optional)
HTG3-C
(Optional)
HTG2-C
(Optional)
E
C
HTG1-C
(Optional)
SF-C
SUPHTG1-C
(Optional)
ZN-T
SA
RA
DA
ZN-CO2
(Optional)
OCC-S
(Optional)
DA-T
(Optional)
ZEC410-1
VAV with Parallel Fan
HTG3-C
(Optional)
VAV with Series Fan
HTG2-C
(Optional)
E
C
HTG1-C
(Optional)
SF-C
SUPHTG1-C
(Optional)
ZN-T
SA DA
RA
ZN-CO2
(Optional)
OCC-S
(Optional)
DA-T
(Optional)
ZEC410-1
HTG3-C
(Optional)

ZEC410 VAV Controllers Installation Instructions
9
Figure 8: ZEC410-1 Controller - VAV with Staged Reheat Control Wiring Example
TO REDWIRE
OCCUPANCY SWITCH
TO BLACKWIRE
OCCUPANCY SWITCH
1
2
4
8
16
32
64
128
ON
Addres
s:
See Riser
Diagram
+15
IN3
ICOM3
UNIVERSA
L
SA PWR
COM
-
+
FC EOL
SA BUS
IN
COM
SHLD
-
+
FC BUS
HOT
COM
24~
ZEC410-1
SA BUS FC BUS
IN2
ICOM2
IN1
ICOM1
+15 COM
MANUAL
OVERRIDE
OCOM3
OUT3
OCOM2
OUT2
BINARY
OCOM1
OUT1
OCOM5
OUT5
OCOM4
OUT4
CONFIGURABLE
CONNECTOR ON BACK
OF SENSOR
ZONE SENSOR ZN-T (IF
NETSTAT IS SELECTED)
24V COM
24V HOT
SA PWR
COM
-
+
TO NEXT
DEVICE
FROM LAST
DEVICE
MS/TP
MS/TP
Occupancy Sensor
(OLS-2100-1)
CONNECTOR ON BACK
OF SENSOR
ZONE SENSOR ZN-CO2
24V HOT
-
COM
SA PWR
24V COM
SEE RISER SCHEDULE FOR
WHICH DEVICES TO SET EOL
TO ON.
SEE RISER FOR POWER
SOURCE
24V Hot
24V Com
(OPTIONAL)
(OPTIONAL)
+
ZONE BUS
WIRINGSEE
RISER DETAIL
CONNECT TO AIR FLOW PROBE
(POLARITY IS NOTIMPORTANT)
-
+
SF-C
(OPTIONAL)
+
-
HTG2-C
(OPTIONAL)
-
+
HTG1-C
(OPTIONAL)
DA-T
DISCHARGE AIR TEMP
(OPTIONAL)
-
+
SUPHTG1-C
(OPTIONAL)
24V Com
24VHot
HEATING AND/OR FAN CONTACTORS IN
VAV BOX. NOTE THE VAV CONTROLLER
BINARY OUTPUTS SWITCH THE COMMON.
OUT1, OUT2, AND OUT3 ARE 24V HOT
CONTINUOSLY.
ELECTRIC HEAT
SAFETIES
-
+
HTG3-C
(OPTIONAL)
24V Com

ZEC410 VAV Controllers Installation Instructions
10
Sequence of Operation for Staged with Reheat Control
Occupied Mode: When the zone temperature is between the occupied heating and cooling setpoints (inside of the
bias), the primary air damper is at the Minimum CFM and no mechanical heating runs. When the zone temperature
rises above the cooling setpoint, the primary air damper increases the cfm and no mechanical heating runs. If a
drop in zone temperature below the heating setpoint occurs, the supplemental heating coil is fully used before the
reheat heat coil enables, and the damper opens to provide to minimum cfm.
Note: The box reheat and supplemental reheat is a box option. You have a cooling only box if you do not select
either reheat or supplemental reheat.
Unoccupied Mode: In unoccupied mode, when the zone temperature is between the unoccupied heating and
cooling setpoints (inside of the bias), the primary air damper is at the minimum cfm and no mechanical heating
runs. When the zone temperature rises above the unoccupied cooling setpoint, the primary air damper increases
the cfm (if available), and no mechanical heating runs. When the zone temperature drops below the unoccupied
heating setpoint, the supplemental heating coil is fully used before the reheat heat coil enables. The damper is at
the minimum cfm.
Unit Enable: A network unit enable signal controls the mode of the box.
Fan Control (Optional): With parallel fans, when a call for heat occurs, the fan cycles on. In all other states the fan
remains off. With series fans, in occupied mode, the fan runs continuously. In unoccupied mode, the fan cycles on
with a call for heating or cooling.
Occupancy Lighting Switch (Optional): You can add an occupancy lighting switch to the box, temporarily setting
the VAV box to Standby mode when the occupancy is not sensed. When the box senses occupancy, the zone
switches back to occupied. Standby mode uses standby temperature setpoints that are slightly highter or lower
than the occupied cooling or heating setpoints, respectively. The VAV box also uses unoccupied flow setpoints in
addition to the low temperatures.
Demand Control Ventilation (Optional): When zone CO2sensors are wired to the boxes to sense the air quality
in the zone, the minimum damper flows are proportionally reset based on an air quality setpoint (CO2). The reset of
the damper minimum flows do not exceed the maximum value that you set. the CO2 sensor with the highest value
determines the reset, if more than one is wired.

ZEC410 VAV Controllers Installation Instructions
11
Figure 9: ZEC410-2 Controller - VAV with Incremental Reheat Control Wiring Example
ZEC410-2
ZN-T
SA DA
ZN-CO2
(Optional)
OCC-S
(Optional)
DA-T
(Optional)
VAV with No Fan
SUPPLY
RETURN
SUPHTG-O
(Optional)
SUPPLY
RETURN
HC
SEEHEATING
VALVEDETAILS
BELOW
(OPTIONAL)
SF-C
ZN-T
SA
RA
DA
ZN-CO2
(Optional)
OCC-S
(Optional)
DA-T
(Optional)
ZEC410-2
VAV with Parallel Fan
SUPPLY
RETURN
SUPHTG-O
(Optional)
SUPPLY
RETURN
HC
SEE HEATING
VALVE DETAILS
BELOW
(OPTIONAL)
VAV with Series Fan
SF-C
ZN-T
SA DA
RA
ZN-CO2
(Optional)
OCC-S
(Optional)
DA-T
(Optional)
ZZEC410-2
SUPPLY
RETURN
SUPHTG-O
(Optional)
SUPPLY
RETURN
HC
SEEHEATING
VALVE DETAILS
BELOW
(OPTIONAL)
1
2
4
8
16
32
64
128
ON
Address:
See Riser Diagram
+15
IN3
ICOM3
UNIVERSAL
SA PWR
COM
-
+
FC EOL
SA BUS
IN
COM
SHLD
-
+
FC BUS
HOT
COM
24~
ZEC410-1
SA BUS FC BUS
IN2
ICOM2
IN1
ICOM1
+15 COM
MANUAL
OVERRIDE
OCOM3
OUT3
OCOM2
OUT2
BINARY
OCOM1
OUT1
OCOM5
OUT5
OCOM4
OUT4
CONFIGURABLE
CONNECTOR ON BACK
OF SENSOR
ZONE SENSOR ZN -T (IF
NETSTAT IS SELECTED )
24V COM
24V HOT
SA PWR
COM
-
+
TO NEXT
DEVICE
FROM LAST
DEVICE
MS/TP
MS/TP
TO RED WIRE
OCCUPANCY SWITCH
TOBLACK WIRE
OCCUPANCY SWITCH
Occupancy Sensor
(OLS-2100-1)
CONNECTOR ON BACK
OF SENSOR
ZONE SENSOR ZN -CO2
24V HOT
-
COM
SA PWR
24V COM
24V Hot
24V Com
(OPTIONAL)
(OPTIONAL)
+
ZONE BUS
WIRING SEE
RISER DETAIL
-
+
SF-C
(OPTIONAL)
DA-T
DISCHARGE AIR TEMP
(OPTIONAL)
24V Hot
24V Com
NOTE: BOTH HEATING VALVES DEFAULT TO A 60
SECOND INCREMENTAL ACTUATOR . THIS IS
ADJUSTABLE IN VERASYS
TERMINATIONSFOR
2 WAY / 3 WAY COIL-A
VALVECONFIGURATIONS
(SHOWN CCW TO OPEN)
HTG-O
(OPTIONAL )
TERMINATIONSFOR
3 WAY COIL-B VALVE
CONFIGURATION
(SHOWN CCW TO
CLOSE)
CW
CCW
COM
CCW
CW
COM
PIPING DETAILS SHOWN FOR VALVE CONFIGURATIONS:
SEE THE VALVE SCHEDULE FOR THE SPECIFIC CONFIGURATION
SEE THE WIRING DETAIL BELOW FOR TERMINATIONS FOR SPECIFIC APPLICATION
C
B
A
HTG-O
SUPPLY
RETURN
HC
C
B
A
HC
HTG-O
SUPPLY
RETURN HTG-O
RETURN
HC
3WAY
COIL-A 3WAY
COIL-B 2WAY
SUPPLY
SUPHTG-O
(OPTIONAL )
CW
CCW
COM
24V Hot
(SHOWN CCW TO OPEN)
HTG-O
(OPTIONAL )
POWER FROM 24V AC
TRANSFORMER
CONNECT TO AIR FLOW PROBE
(POLARITY IS NOT IMPORTANT )

ZEC410 VAV Controllers Installation Instructions
12
Sequence of Operation for Incremental Control Wiring Example
Occupied Mode: When the zone temperature is between the occupied heating and cooling setpoints (inside of the
bias), the primary air damper is at the minimum cfm and mechanical heating is unavailable. When the zone
temperature rises above the cooling setpoint, the primary air damper increases the cfm and mechanical heating is
unavailable. When the zone temperature drops below the heating setpoint, the supplemental heating coil is fully
used before the reheat coil enables. The damper is controlled to provide a minimum cfm.
Note: The box reheat and supplemental reheat is a box option. If you select neither, you have a cooling only box.
Unoccupied Mode: When in unoccupied mode, if the zone temperature is between the unoccupied heating and
cooling setpoints (inside of the bias), the primary air damper is at the minimum cfm and mechanical heating is
unavailable. When the zone temperature rises above the unoccupied cooling setpoint, the primary air damper
increases the cfm, if available, and mechanical heating is unavailable. When the zone temperature drops below the
unoccupied heating setpoint, the supplemental heating coil is fully used before the reheat heat coil enables. The
damper is at the minimum cfm.
Unit Enable: A network unit enable sign controls the box mode.
Fan Control (Optional): For parallel fans, upon a call for heat, the fan cycles on. For all other states, the fan is off.
For Series fan, during the occupied mode the fan runs continuously. During the unoccupied mode, the fan cycles
on with a call for heating or cooling.
Occupancy Lighting Switch (Optional): You can add an occupancy lighting switch to the box. This temporarily
sets the VAV box to Standby mode when the occupancy is not sensed. When the box senses occupancy, the zone
switches back to occupied. Standby mode uses standby temperature setpoints that are slightly higher or lower than
the occupied cooling or heating setpoints, respectively. The VAV Box also uses unoccupied flow setpoints in
addition to the low standby temperatures.
Demand Control Ventilation (Optional): When Zone CO2sensors are wired to the boxes to sense the air quality
in the zone, the minimum damper flows are proportionally reset based on the air quality (CO2) setpoint. The reset
of damper minimum flows does not exceed the maximum value you set. The CO2sensor with the highest value
determines the reset if more than one sensor is wired.

ZEC410 VAV Controllers Installation Instructions
13
Figure 10: MULTIZONE UNIT VAV WITH PROPORTIONAL REHEAT CONTROL
HI
(Red)
LO
1
2
4
8
16
32
64
128
ON
Address:
SeeRiser Diagram
+15
IN3
ICOM3
UNIVERSAL
SA PWR
COM
-
+
FC EOL
SA BUS
IN
COM
SHLD
-
+
FC BUS
HOT
COM
24~
ZEC410-3
SA BUS FC BUS
IN2
ICOM2
IN1
ICOM1
+15 COM
MANUAL
OVERRIDE
OCOM3
OUT3
OCOM2
OUT2
BINARY
OCOM1
OUT1
OCOM5
OUT5
OCOM4
OUT4
CONFIGURABLE
CONNECTOR ON BACK
OF SENSOR
ZONESENSOR ZN -T (IF
NETSTAT ISSELECTED )
24V COM
24V HOT
SA PWR
COM
-
+
TO NEXT
DEVICE
FROM LAST
DEVICE
MS/TP
MS/TP
TORED WIRE
OCCUPANCYSWITCH
TOBLACKWIRE
OCCUPANCYSWITCH
Occupancy Sensor
(OLS-2100 -1)
CONNECTOR ON BACK
OF SENSOR
ZONESENSORZN -CO2
24V HOT
-
COM
SA PWR
24V COM
24V Hot
24V Com
(OPTIONAL)
(OPTIONAL)
+
ZONE BUS
WIRING SEE
RISER DETAIL
CONNECT TOAIR
FLOW PROBE
-
+
SF-C
(OPTIONAL ) DA-T
DISCHARGE AIR TEMP
(OPTIONAL)
24V Hot
24V Com
NOTE: SUPPLEMENTAL VALVES DEFAULT TO A 60
SECOND INCREMENTALACTUATOR . THISIS
ADJUSTABLE IN VERASYS
SUPHTG-O
(OPTIONAL )
CW
CCW
COM
-
+
HTG-C
(OPTIONAL )
-
+
HTG-O
(OPTIONAL )
NOTE: THE DRAWING SHOWS A CONNECTION TO AN
ELECTRIC SCR REHEAT COIL WHICH IS
PROPORTIONALLY CONTROLLED . THE HTG-O
SIGNAL IS 0-10V WHICH COULD CONTROLA
PROPORTIONAL WATER VALVE . THE APPLICATION
IS SETUP TO SUPPORT EITHER .
POWER FROM 24V AC
TRANSFORMER
ZEC410-1
ZN-T
SA DA
ZN-CO2
(Optional)
OCC-S
(Optional)
DA-T
(Optional)
VAV with No Fan
SUPPLY
RETURN
SUPHTG-O
(Optional)
EC
SCR
HTG-O
(Optional)
HTG-C
(Optional)
SF-C
ZN-T
SA
RA
DA
ZN-CO2
(Optional)
OCC-S
(Optional)
DA-T
(Optional)
ZEC410-1
VAV with Parallel Fan
SUPPLY
RETURN
SUPHTG-O
(Optional)
EC
SCR
HTG-O
(Optional)
HTG-C
(Optional)
VAV with Series Fan
SF-C
ZN-T
SA DA
RA
ZN-CO2
(Optional)
OCC-S
(Optional)
DA-T
(Optional)
ZEC410-1
SUPPLY
RETURN
SUPHTG-O
(Optional)
EC
SCR
HTG-O
(Optional)
HTG-C
(Optional)

ZEC410 VAV Controllers Installation Instructions
14
Sequence of Operation - Multizone Unit VAV with Proportional Reheat Control
Occupied Mode: When the zone temperature is between the occupied heating and cooling setpoints (inside of the
bias), the primary air damper is at the minimum cfm and mechanical heating is unavailable. When the zone
temperature rises above the cooling setpoint, the primary air damper increases the cfm and mechanical heating is
unavailable. When the zone temperature drops below the heating setpoint, the supplemental heating coil is fully
used before the reheat coil enables. The damper is controlled to provide a minimum cfm.
Note: The box reheat and supplemental reheat is a box option. If you select neither, you have a cooling only box.
Unoccupied Mode: When in unoccupied mode, if the zone temperature is between the unoccupied heating and
cooling setpoints (inside of the bias), the primary air damper is at the minimum cfm and mechanical heating is
unavailable. When the zone temperature rises above the unoccupied cooling setpoint, the primary air damper
increases the cfm, if available, and mechanical heating is unavailable. When the zone temperature drops below the
unoccupied heating setpoint, the supplemental heating coil is fully used before the reheat heat coil enables. The
damper is at the minimum cfm.
Unit Enable: A network unit enable sign controls the box mode.
Fan Control (Optional): For parallel fans, upon a call for heat, the fan cycles on. For all other states, the fan is off.
For Series fan, during the occupied mode the fan runs continuously. During the unoccupied mode, the fan cycles
on with a call for heating or cooling.
Occupancy Lighting Switch (Optional): You can add an occupancy lighting switch to the box. This temporarily
sets the VAV box to Standby mode when the occupancy is not sensed. When the box senses occupancy, the zone
switches back to occupied. Standby mode uses standby temperature setpoints that are slightly higher or lower than
the occupied cooling or heating setpoints, respectively. The VAV Box alos uses unoccupied flow setpoints in
addition to the low standby temperatures.
Demand Control Ventilation (Optional): When Zone CO2sensors are wired to the boxes to sense the air quality
in the zone, the minimum damper flows are proportionally reset based on the air quality (CO2) setpoint. The reset
of damper minimum flows does not exceed the maximum value you set. The CO2sensor with the highest value
determines the reset if more than one sensor is wired.
ZEC Terminal Functions, Ratings, Requirements, and Wiring Guidelines
Input and Output Wiring Guidelines
Table 2 provides information about the functions, ratings, and requirements for the ZEC input and output terminals.
In addition to the wiring guidelines Table 2, observe these guidelines when wiring ZEC inputs and outputs:
• Run all low-voltage wiring and cables separate from high-voltage wiring.
• All input and output cables, regardless of wire size or number of wires, should consist of twisted, insulated, and
stranded copper wires.
• Shielded cable is not required for input or output cables.
• Shielded cable is recommended for input and output cables that are exposed to high electromagnetic or radio
frequency noise.
System and Zone Bus Supply Power Wiring Guidelines
Table 2 provides information about terminal block functions, ratings, and requirements.
In addition to the guidelines in Table 2, observe these guidelines when wiring the System/Zone Buses and supply
power:
• Run all low-voltage wiring and cables separate from high-voltage wiring.
• All FC and SA Bus cables, regardless of wire size, should be twisted, insulated, stranded copper wire.
• Shielded cable is strongly recommended for all FC and SA Bus cables.

ZEC410 VAV Controllers Installation Instructions
15
• Refer to the MS/TP Communications Bus Technical Bulletin (LIT-12011670) for detailed information regarding
wire size and cable length requirements for the Zone Bus.
Wire Gauges and Lengths
Table 2 outlines the VAV controller wiring details.
Setup and Adjustments
Setting the Device Address
ZEC controllers are master devices on BACnet® MS/TP (SA or FC) Buses. Before operating field controllerson a
bus, you must seta valid and unique device address for each controller on the bus.
Youset a field controller’s device address by setting the positions of the switcheson the Device Address DIP
switch
blockat the topofthe controller. Device addresses 4 through 127 are the valid addresses for
the ZEC controller.
Note: ZEC controllers ship with all address switches set to ON. Set a valid and unique device address on the field
controller before applying power to the controlleron the bus.
The DIP switch block has eight switches numbered 128, 64, 32, 16, 8, 4, 2, and 1.
Toset the deviceaddresses on a ZEC field controller:
1. Set all of the switches on the field controller’s device address DIP switch block (128 through 1) to OFF.
2. Set one or more of the six address switches (32 through 1) to ON, so that the sum of the switch numbers set to
ON equals the intended device address.
Set the highest number switch that is less than or equal to the intended device address to ON. Then continue
setting lower numbered switches until the totalequalstheintendedaddress.Forexample,ifthe intended device
address is 21, set Switch 16 to ON first, then set Switch 4 ON, followed by Switch 1 (16+4+1=21).
3. Set a unique and sequential device address for each of the field controllers connected on the System Bus or
Zone Bus, starting with device address 6.
Table 2: ZEC Controller Wiring
Terminal Terminal Labels Function and Electrical Ratings/
Requirements Recommended Cable Type
and Length
Analog Input
(AI) IN1 Provides an AI connection for discharge
air (DA-T) sensor 0.6 mm (22 AWG) stranded,
2-wire twisted cable
recommended for runs of <30 m
(90 ft).
IN2 Provides a BI connection for occupancy
sensor dry contact (optional) N/A
Binary Output
(BO) (Integrated) Provides a BO connection for clockwise
(CW) rotation to (Open) of actuator, 24
VAC triac output.
N/A
(Integrated) Provides a BO connection for
counterclockwise (CCW) rotation to
(Close) of actuator, 24 VAC triac output.
N/A
Sensor Actuator
(SA) Bus
Terminal Block
+, -, COM, PWR Sources 15 VDC power for SA Bus
devices; supports 5 NS Series Network
Zone Temperature Sensors and up to 5
NS Series Network CO2Sensors.
0.6 mm (22 AWG) stranded,
4-wire twisted cable
recommended for runs of <30 m
(99 ft)
FCBus Terminal
Block + - Com Provides communication network 0.65 mm (22 AWG) stranded,
twisted shielded cable
recommended for runs of 1,000
feet maximum
24 VAC Power Hot AC supply input supply 20–30 VAC
(Nominal 24 VAC) 0.8 mm to 1.5 mm
(20 to 16 AWG) 2-wire
Com 24 VAC power common

ZEC410 VAV Controllers Installation Instructions
16
To ensure the best bus performance, set sequential device addresses with no gaps in the device address range
(4,5,6,andsoon).The fieldcontrollers do not need to be physically connected on the bus in their numerical
device address order.
4. Write each field controller’s device address on the white label below the DIP switch block on the controller’s
cover.
Refer to the MS/TP Communications Bus Technical Bulletin (LIT-12011034) for more information on field controller
device addresses and how to set them on MS/TP Bus devices.
Accessories
Table 3 lists the ZEC controller accessories.
Operation
The ZEC controller is pre-programmed for the VAV box operating sequence as ordered. You do not need to
program the controller; however, you need to provide configuration information using either the Balancing Sensor
or the Zone Setup screen on the Verasys System Smart Building Hub.
For detailed information on Verasys System, including dehumidification capability, DCV, occupancy sensing, and
general operating modes, refer to the Verasys System Operation Overview Technical Bulletin (LIT-12012370).
Table 3: Zone Controller Accessories
Product Code
Number Description
Zone Temperature Sensors (Hardwired)
TE-68NT-0N00S Wall temperature sensor, 1k ohm, nickel with temperature occupancy button.
TE-68NT-1N00S Wall temperature sensor, 1k ohm, nickel with warmer/cooler (W/C) adjustment and temperature
occupancy pushbutton.
Zone CO2Sensor
NS-BCN7004-0 BACnet network CO2sensor designed to function directly with Johnson Controls BACnet MS/TP digital
controllers, in a 80 mm x 120 mm (3 in. x 4.5 in.) enclosure with terminal block and modular jack wiring
connections.
Only addresses 212 to 214 are supported.
Second Zone Damper Actuator1
1. You must purchase the actuator and add it to a damper without a ZEC310 controller.
M9106-GGA-2 6 n•m torque non-spring return damper actuator
Network Sensors for Zone Temperature
NS-BTB7003-0 Network sensor, 120 x 80 mm (4.7 x 3.1 in.), Johnson Controls® logo, local setpoint, terminals
NS-BTB7003-2 Network sensor, 120 x 80 mm (4.7 x 3.1 in.), no logo, local setpoint, terminals
NS-BTN7003-0 Network sensor, 120 x 80 mm (4.7 x 3.1 in.), no logo, no setpoint, terminals
NS-BTN7003-2 Network sensor, 120 x 80 mm (4.7 x 3.1 in.), no logo, no setpoint, terminals.
NS-BTP7002-0 Network sensor, 120 x 80 mm (4.7 x 3.1 in.), Johnson Controls logo, Warmer/Cooler adjustment,
terminals
NS-BTP7002-2 Network sensor, 120 x 80 mm (4.7 x 3.1 in.), no logo, warmer/cooler adjustment, terminals
Occupancy Lighting Switch
NS-BCN7004 Occupancy sensing light switch for control of indoor incandescent and fluorescent lights
RIBU1C Enclosed relay for OLS-2100-1 sensor
Balancing Tool
NS-ATV7003-0 Handheld VAV balancing tool

ZEC410 VAV Controllers Installation Instructions
17
Occupancy Sensor
All zone controllers support an occupancy sensor. The occupancy sensor enables the controller to switch to
standby mode from occupied mode when local activity is absent during a set time period in a normally occupied
zone. When in standby mode, the zone controller uses standby temperature setpoints that are higher and lower
than the occupied cooling and occupied heating temperature setpoints, respectively. These standby setpoints help
save energy by reducing the demand for heating and cooling in an unoccupied zone. For VAV zone dampers, the
sensor uses unoccupied flow setpoints in addition to standby temperature setpoints. You can enable the occupancy
sensor in the Zone Setup screen of the System Manager or Zone Coordinator. You can set occupancy sensitivity
and time delay until standby locally at the sensor. Refer to the Verasys System User’s Guide (LIT-12012371) for
more information.
CO2 Demand Controlled Ventilation (DCV)
CO2DCV ensures high Indoor Air Quality (IAQ) for the zone by using up to four wall-mounted CO2sensors to
monitor CO2levels. The sensor measures CO2levels on a scale of 0 to 2,000 parts per million (ppm). When the
CO2sensor with the highest CO2reading detects that CO2levels in the zone are above the setpoint (such as
caused by a high number of occupants within the zone), the zone damper opens, to allow more outside air into the
zone. Enable CO2DCV in the Zone Setup screen of the System Manager or Zone Coordinator. Refer to the
Verasys System User’s Guide (LIT-12012371) for more information.
Troubleshooting
Use the following information to troubleshoot the ZEC controllers.
Power Status LED
A green LED shows the power supply status to the VAV zone damper controller. See Table 4 for a description of the
modes.
Table 4: Status LED for Power (PWR)
Mode Description
Off No Power
On Power is supplied by Primary Voltage (Normal operation)

ZEC410 VAV Controllers Installation Instructions
18
Communication Bus Problems
Several factors may influence the behavior of the Zone Communication bus.
I/O Wiring
The ZEC controller must be wired properly. If the ZEC controller is wired incorrectly, communication problems may
occur. These problems include devices going online and offline, to devices not coming online at all.
Incomplete Address
The VAV controller must have the address switch set to a range between 6–37.
Duplicate Addresses
Two or more devices on a communication bus cannot have the same address. Two controllers on the Zone
Communication bus cannot both have an address of 18, for example. If two devices on the same bus have the
same address, performance can degrade or serious communication problems may occur. These problems include
the devices not coming online and all communication stopping completely.
Check for duplicate addresses in the following ways:
• If a specific device is not communicating, remove the device with communication problems and check if device
address remains online at the Smart Building Hub to determine if the device address remains online.
• If the bus communication problems are severe and no communication is present, or you cannot determine
where communication is unreliable, partition (disconnect and isolate a portion of the bus for testing purposes)
and test the bus portion connected to the Zone Coordinator.
Correcting Physical Communication Bus Problems
The communication bus is subject to a number of physical factors that can affect performance. Consider the
following list of common physical problems that affect the communications bus:
• Check status LED to verify power at the controller
• Check wires
- Verify that the wire is a 22 AWG (0.6 mm) three-conductor, twisted, shielded cable.
- Verify that the shield is continuous and hard-grounded at one end.
• Check wiring
- Check for and eliminate T-Taps (wire configurations that create a T shape) and star configurations.
- Ensure that the bus is wired in a daisy-chain fashion.
- Verify that appropriate devices have three wires entering and exiting each terminal (devices at the ends of
the trunk do not have this wiring).
• Check EOL switch settings
- Verify that the zone bus EOL switch on the Zone Coordinator is set to ON and the Zone Coordinator is
located at the end of the zone bus trunk.
- Verify that only the EOL switch at the end of the Zone bus is set to ON and all other Zone bus EOL
switches are set to OFF.
• Check connections, polarity, and lengths
- Verify that communications loops are less than 1,000 ft (304 m) total in length.
- If you are using one transformer to power multiple devices, verify that the device 24 VAC power connection
follows the polarity of the common and 24 V terminations (see System and Zone Bus Supply Power Wiring
Guidelines).
• Check for opens and shorts
• Check terminations

Published in U.S.A. www.johnsoncontrols.com
ZEC410 VAV Controllers Installation Instructions
Verasys™ and Johnson Controls® are registered trademarks of Johnson Controls
All other marks herein are the marks of their respective owners. © 2017 Johnson Controls
Building Technologies and Solutions
507 E. Michigan Street, Milwaukee, WI 53202
19
• Check addresses
- Check for duplicate addresses.
- Verify that the address range is sequential.
• Check for sources of interference
• Check bus voltages:
- (+) to COM must be within 2.0 to 3.0 VDC
- (-) to COM must be within 1.5 to 2.54 VDC
- (+) to (-) must be within 0.3 to 1.0 VDC
Note: Values may fluctuate due to ongoing communications; this operation is normal provided the voltage is
within the defined range.
Repair Information
If the ZEC410 controller fails to operator within its specifications, replace the unit. For a replacement unit, contact
the nearest Verasys representative.
Technical Specifications
ZEC410 VAV Controller
Product Code Number LC-ZEC410-xx
Power Supply Requirement 20–30 VAC at 50 to 60 Hz, Class 2 power supply or Safety Extra-Low Voltage (SELV) at
50/60 Hz (20 VAC minimum)
Power Consumption 10 VA, 14 VA maximum
Ambient Conditions Ambient Operating Conditions: 0 to 50°C (32 to 122°F); 10 to 90% RH condensing
Ambient Storage Conditions: -40 to 85°C (-40 to 185°F); 10 to 90% RH
Processor 20 MHz Renesas® H8S2398 processor
Memory 1 MB flash nonvolatile memory for operating system, configuration data, and operations
data storage and backup
512k Synchronous Random Access Memory (SRAM) for operations data dynamic
memory
Mounting On a flat surface with screws
Dimensions
(Height x Width x Depth) 140 x 140 x 25 mm (5-1/2 x 5-1/2 x 1 in.)
Shipping Weight 0.30 lb (0.14 kg)
Compliance United States
UL Listed, File E107041, CCN PAZX, UL 916
FCC Compliant to CFR47, Part 15, Subpart B, Class A
Canada
UL Listed, File E107041, CCN PAZX7, CAN/CSA C22.2 No. 205, Signal Equipment
Industry Canada Compliant, ICES-003
European Single Point of Contact: NA/SA Single Point of Contact: APAC Single Point of Contact:
JOHNSON CONTROLS
WESTENDHOF 3
45143 ESSEN
GERMANY
JOHNSON CONTROLS
507 E MICHIGAN ST
MILWAUKEE WI 53202
USA
JOHNSON CONTROLS
C/O CONTROLS PRODUCT MANAGEMENT
NO. 22 BLOCK D NEW DISTRICT
WUXI JIANGSU PROVINCE 214142
CHINA
Table of contents
Other Verasys Controllers manuals
Popular Controllers manuals by other brands
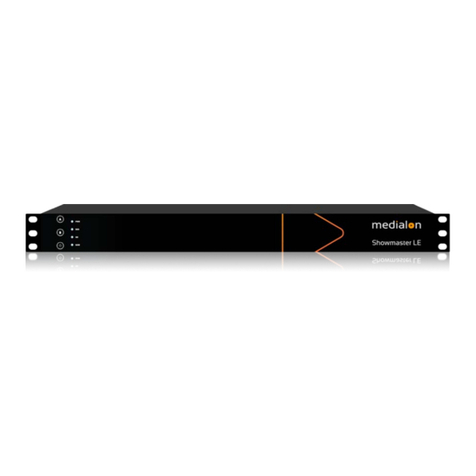
Medialon
Medialon Showmaster Series Hardware manual

Penn
Penn TC3B21 installation guide
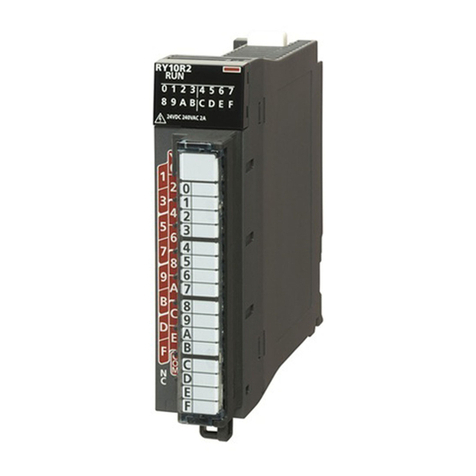
Mitsubishi Electric
Mitsubishi Electric MELSEC iQ-R Series Safety function block reference
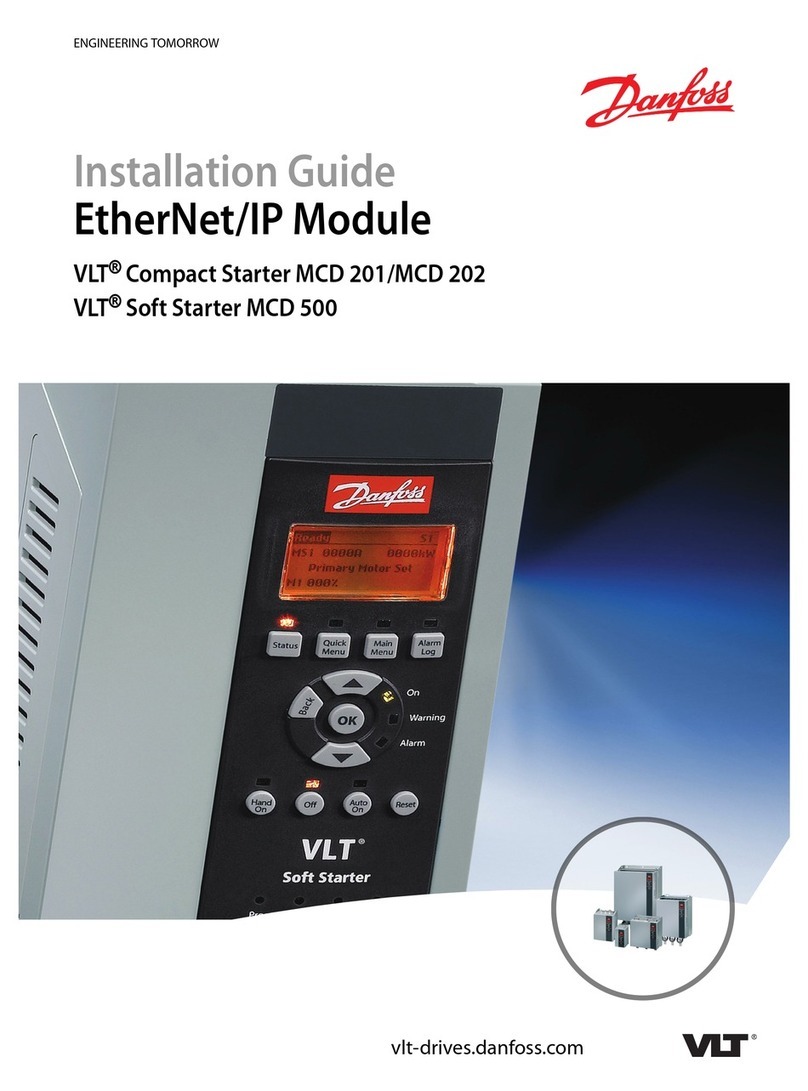
Danfoss
Danfoss VLT Compact Starter MCD 201 installation guide
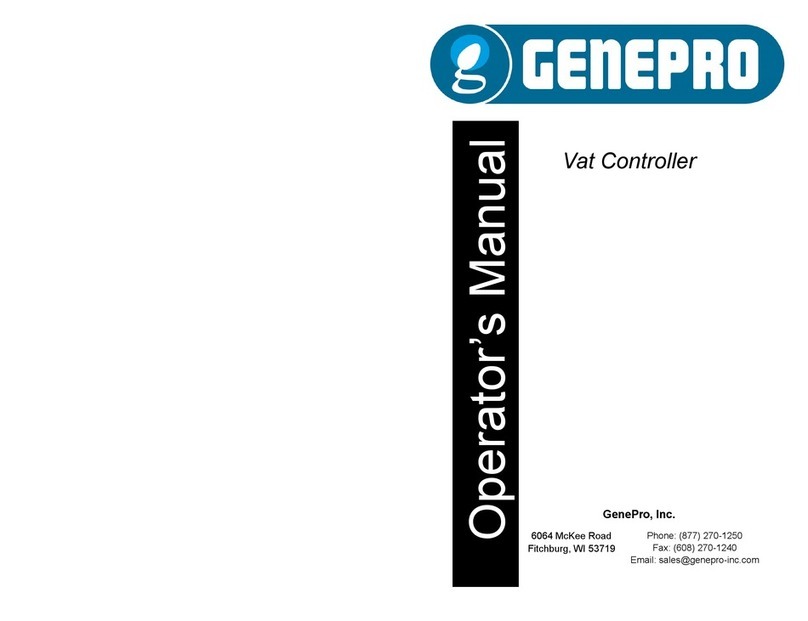
GenePro
GenePro Vat Controller Operator's manual
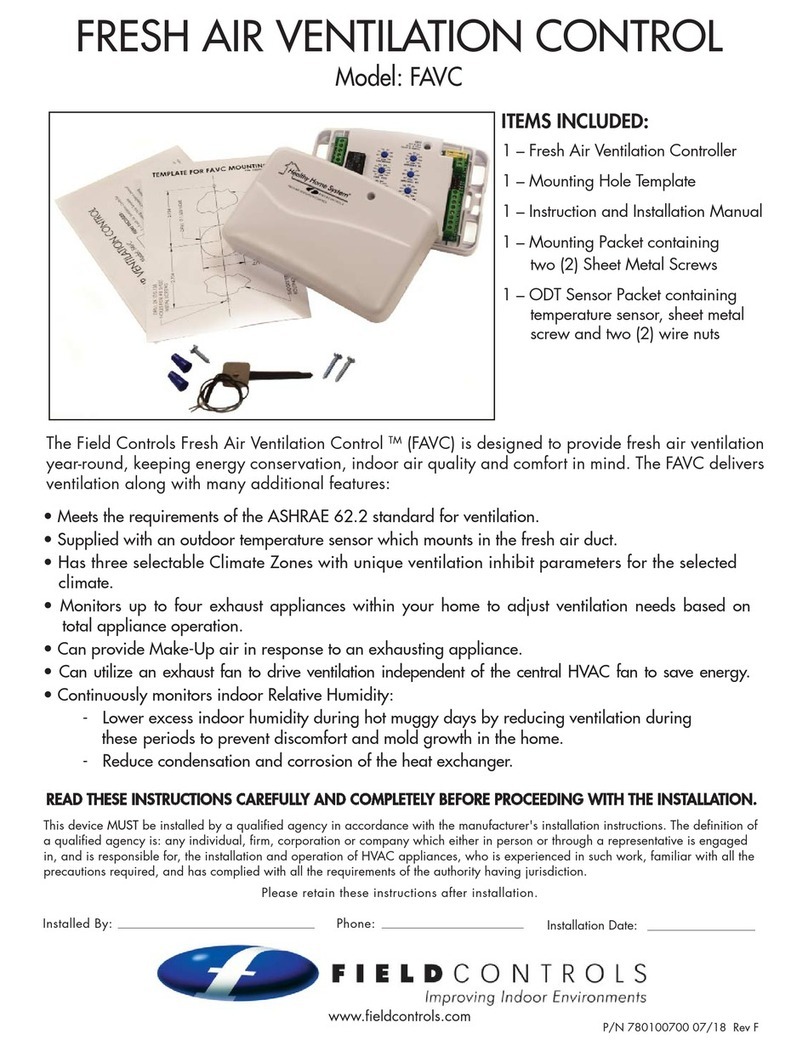
Field Controls
Field Controls FAVC installation manual

Lawler
Lawler 801 SEA Basic Installation & maintenance manual
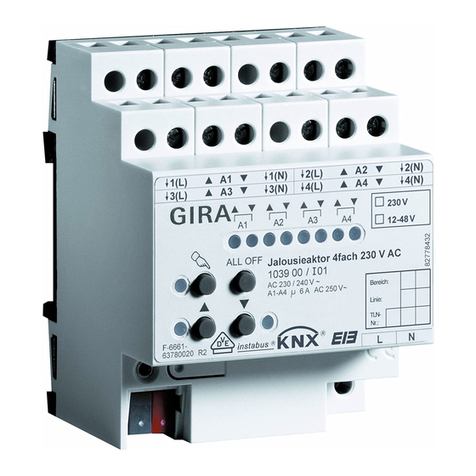
Gira
Gira 1039 00 installation instructions
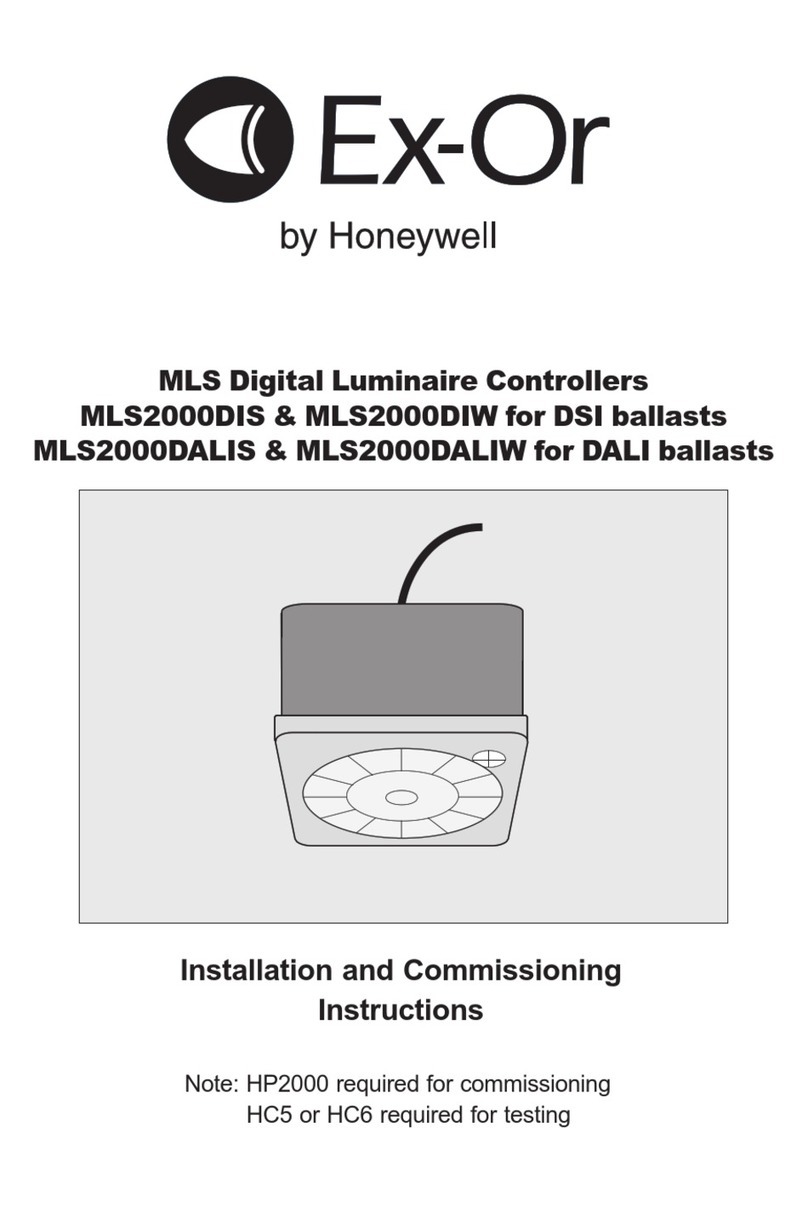
Honeywell
Honeywell Ex-Or MLS Installation and commissioning instructions
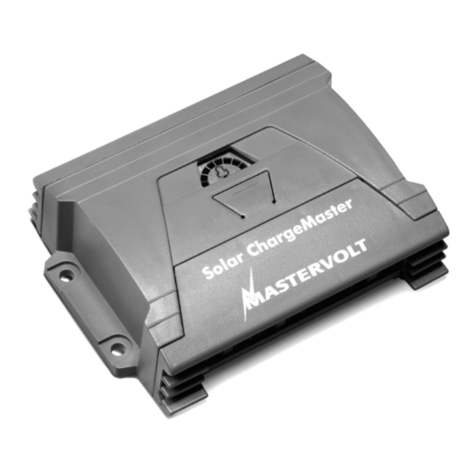
Mastervolt
Mastervolt Solar ChargeMaster SCM-N 20 user manual
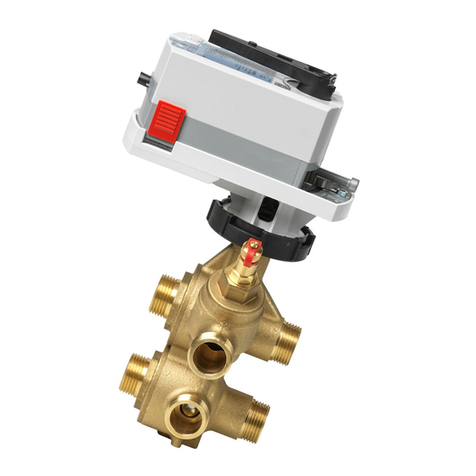
Siemens
Siemens VWPG51 Q Series Mounting instructions
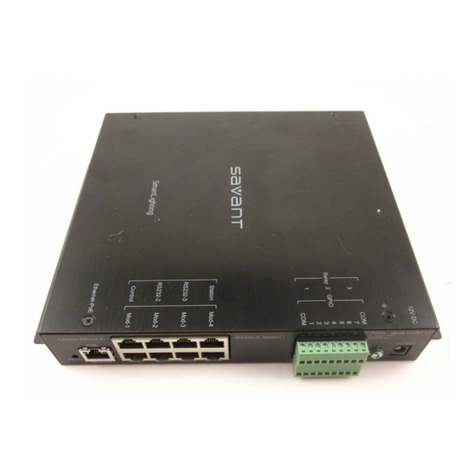
Savant
Savant SmartLighting SSL-P018 Quick reference guide