VICOR FlatPAC-EN Guide

FlatPAC-EN™ and FlatPAC-EN MI
EN Compliant Autoranging Switchers
FlatPAC-EN/EN MI Design Guide
Design Guide
and
“Quick Install” Instructions
www.vicorpower.com
Rev. 2/2012 Vicor 800-735-6200 Westcor Division 408-522-5280 Applications Engineering 800-927-9474

TABLE OF CONTENT
Overview of Product...........................................................................................................................3
Part Numbering...................................................................................................................................3
Mechanical Considerations.................................................................................................................4
FlatPAC-EN/EN MI Do’s and Don’ts................................................................................................4
Technical Description.........................................................................................................................5
Configuration Layout drawing...........................................................................................................6
Quick Install Instructions....................................................................................................................7
Mechanical Drawings.........................................................................................................................10
Output connector information............................................................................................................11
Connector Kit listing..........................................................................................................................12
Interface Connections.........................................................................................................................13
RS 232 Microcontroller......................................................................................................................14
Specifications.......................................................................................................................... ..........18
Output vs. AC & DC Voltage Graphs . .............................................................................................20
Thermal Curves..................................................................................................................................22
Current Share Boards.........................................................................................................................26
Pg 2 Vicor 800-735-6200 Westcor Division 408-522-5280 Applications Engineering 800-927-9474 Rev. 2/2012
FlatPAC-EN/EN MI Design Guide

FlatPAC-EN™ and FlatPAC-EN MI
EN Compliant Autoranging Switcher
Overview
The FlatPAC-EN/EN MI is an ultra low profile switching power supply that provides up to 500 Watts from up to 4
isolated outputs. It operates on either 115 or 230 Vac nominal (47-63 Hz), or 250-380 Vdc. It can be populated
with either VI-200/VI-J00 or Maxi/Mini/Micro Vicor converters. The use of these converters gives the FlatPAC-
EN/EN MI the inherent power flexibility typical of all Vicor products. With dimensions of 1.4" H (35,6mm) x 5.0"
W (127mm) x 9.2" L (233,7mm), the FlatPAC-EN/EN MI provides a power density greater than 7W/in3.It is facto-
ry configured to meet user output requirements. Note: The FlatPAC-EN/EN MI does not have an internal fan.
The MI version is a rugged chassis designed specifically for COTS and harsh environment applications
Using the PowerBench configurator tool available on vicorpower.com, anybody can now configure a FlatPAC-EN
(and other Westcor power supplies) online.
Standard Features
• Power Factor Correction (passive): Power Factor (Typical) 0.70 (>75% Load)
• Input Voltage: 90-132/180-264 Vac1, 47-63 Hz, or 250-380 Vdc
• Maximum Power Output: 500W (105/190Vac min.)
425W for EN61000-3-2 compliance
• Up to 4 isolated user specifiable outputs
• Conducted EMI: FCC Class A EN 55022 Class A
FCC Class B EN 55022 Class B
Mil-STD 461 may require external filter
• Harmonic Attenuation to EN61000-3-2/A142
• Compliant to EN61000-4-4 (Electrical Fast Transient/Burst) and EN61000-4-5 (Surge Immunity)
• MI version meets Mil-STD 810 for Shock and Vibration with extended temp range
• MI version also available with -40C temp rating
• Efficiency (typical) > 70%
• Autosense3
• RS-232 microcontroller interface
• Output overcurrent protection on all outputs
• Size: 1.4" H (35,6mm) x 5.0" W (127,0mm) x 9.2" L (233,7mm)
• Safety Agency Approvals: cURus, cTUVus, CE Mark
1Derates to 260W@90Vac, 400W @ 180 Vac.
2For output power ≤425W, not to exceed an input current of 3.33 A rms at 230 Vac, 50 Hz.
3 This feature is implemented in all converter slots (except with Micro modules). Autosense allows automatic local sensing
when remote sense connections are not made. The FlatPAC-EN/EN MI will operate in remote sense mode when remote
sense connections are made. Refer to page 16 for more information on Autosense.
Optional Features
• Current Share Board for unit to unit power sharing - See page 26 and page 27
• Connector kits (# 19-130044)
• Conformal coating available on select MI models - contact factory
• -40oC Operation, Mil-STD 810 Shock and Vibration (MI rugged chassis only)
Part Numbering
FlatPAC-EN/EN MI FLx1-x2 x3 -xxxx (-x4)(-x5)x
1Number of outputs
e.g. FL4-13-6544 x2Number of VI-200/VI-J00 modules
x3Number of Maxi/Mini/Micro modules
xxxx Sequential number assigned by Westcor
(-x4) Optional Factory assigned: G - RoHS
(-x5)Optional versions
Note: x5= MI for rugged chassis, = MC for rugged chassis with conformal coating
Rev. 2/2012 Vicor 800-735-6200 Westcor Division 408-522-5280 Applications Engineering 800-927-9474 Pg. 3
FlatPAC-EN/EN MI Design Guide

Mechanical Considerations
The FlatPAC-EN/EN MI is mounted on the bottom surface using standard 8-32 or 4 mm screws (cannot be mount-
ed from the front.)
Maximum allowable torque is 5 in. lbs.,. The maximum penetration for mounting holes A1, A2, A3 and A4 is
0.125 in. (3mm) and for mounting holes B1, B2, C1 and C2 is 0.250 in. (6mm). The minimum recommended
mounting holes are as follows:
1. For standard mounting (forced air cooling), use A1, A2, A3, A4 mounting holes.
2. For standard mounting (conduction cooling), use A1, A2, A3, A4, B1 and B2 mounting holes.
3. For a Vicor 2 Up FlatPAC retrofit replacement, use C1 and C2 as these two are identical to the recommended
mounting holes on the FlatPAC.
For increased ruggedness, additional mounting holes can be used to secure the power supply.
The FlatPAC-EN/EN MI does not have an internal fan. It can be either conduction or convection cooled (same
model).
Avoid excessive bending of output power cables after they are connected to the output terminals. For high-current
outputs, use cable ties to support heavy cables and minimize mechanical stress on connectors. Be careful not to
short-out to neighboring outputs. The maximum torque recommended on output nuts is 10 in. lbs.
For applications that require vibration levels above MIL-STD-810E, minimum integrity test, a shock absorbing
mount design is required.
FlatPAC-EN/EN MI Do’s and Don’ts
• Do not exceed an operating case temperature of 90oC. To prevent an overtemperature condition, an external
fan may be required.
• Run the output (+/–) power cables next to each other to minimize inductance.
• Always turn the power supply off before disconnecting input or output wires.
• When using the remote sense feature, the +Out and -Out load wires should never be disconnected while the
supply is operating. Failing to do so could damage the power supply.
• Do not attempt to repair or modify the power supply in any manner as this action will void the warranty. In
the event of problems, contact Customer Service at 1-800-735-6200.
• Insert proper fault protection at power supply input terminals (i.e., a fuse). Refer pg 13 for more information.
• Use proper size wires to avoid overheating and excessive voltage drop.
• Output voltages over 60Vdc, whether from individual modules or series arrays, are considered as hazardous
secondary outputs under UL 60950. Appropriate care must be taken in design implementation of the supply.
Pg 4 Vicor 800-735-6200 Westcor Division 408-522-5280 Applications Engineering 800-927-9474 Rev. 2/2012
FlatPAC-EN/EN MI Design Guide
Identical mounting
holes (C1 & C2)
to Vicor's
2 UP FlatPAC
C1
C2
A1
A2
B1
B2
A3
A4

Technical Description
The FlatPAC-EN/EN MI consists of an off-line single phase autoranging front end, EMI filter, customer interface,
power supply control circuit, associated housekeeping circuits, a MiniHAM module and a selection of Vicor’s VI-
200/VI-J00 and/or Maxi/Mini/Micro DC-DC converters.
The MiniHAM was specifically designed for EN compliance using passive filtering. Unlike active PFC solutions,
the MiniHAM generates no EMI, greatly simplifying and reducing system noise filtering requirements. It is also
considerably smaller and more efficient than active alternatives and improves the unit’s MTBF. It will provide har-
monic current compliance at 230Vac input up to 425W of output power. Input AC mains voltage is applied to input
connector MBJ1 (see page 7) and the input current is passed through an EMI filter designed to meet conducted
noise limit of EN 55022, Classes A and B specifications (certain configurations meet EN55022 Class B. Consult
Factory.)
At start-up, the microcontroller verifies that the input voltage is within the specified operating range. Once this
occurs, the microcontroller closes the safety relay and puts the autoranging front-end in the correct mode (closing
or opening the Doubler relay). The autoranging front-end has two modes, the doubler mode (90Vac - 132Vac) or
bridge rectifier mode (180Vac-264Vac, 250Vdc-380Vdc). Inrush current is limited by a PTC thermistor. The PTC
is shunted out (by closing the Inrush relay) when the output voltage has charged up the bus capacitors within the
specified range (205Vdc-390Vdc). Approximately 1 second after the application of the input voltage, the bus volt-
age is within operating limits and the AC OK signal asserts to a TTL "1", indicating the input power is OK. After
AC OK is asserted high, the user can now control the power outputs.
Output voltage conversion is achieved by Vicor’s 300Vin family of Zero-Current-Switching (ZCS) DC-DC con-
verters. These are forward converters in which the main switching element switches at zero current. This patented
topology has a number of unique attributes: low switching losses; high frequency operation, resulting in reduced
size for magnetics and capacitors; excellent line and load regulation; wide adjustment range for output; low
EMI/RFI emission and high efficiencies.
At initial power-up, all outputs are disabled to limit the inrush current and to allow the DC bus potential to settle
to the correct operating level. A low-power transformer flyback circuit converts the high voltage DC bus into regu-
lated low voltage to power the internal housekeeping circuits as well as the auxiliary +5Vs located in the interface
connector.
An output Enable/Disable function is provided to control Vicor’s DC-DC converters. If the Enable/Disable control
pin is pulled low, the modules output is disabled. The nominal delay associated for an output to come up when
measured from release of the Enable/Disable pin is 9-12 ms. The General Shutdown function controls all outputs
simultaneously and works in a similar manner.
Rev. 2/2012 Vicor 800-735-6200 Westcor Division 408-522-5280 Applications Engineering 800-927-9474 Pg. 5
FlatPAC-EN/EN MI Design Guide

FlatPAC-EN/EN MI Configuration Layout
Pg 6 Vicor 800-735-6200 Westcor Division 408-522-5280 Applications Engineering 800-927-9474 Rev. 2/2012
FlatPAC-EN/EN MI Design Guide
CBJ1
Interface Conn.
M2
VI-200
Maxi
M1
VI-J00
or
Mini
MBJ1
Input Conn.
MiniHAM
CBJ1
Interface Conn.
MBJ1
Input Conn.
M2
Micro
M1
Micro
M3
Micro
MiniHAM
M4
VI-J00
or
Mini
CBJ1
Interface Conn.
M1
VI-J00
or
Mini
MBJ1
Input Conn.
MiniHAM
M2
VI-J00
or
Mini
M3
VI-J00
or
Mini
Single or Dual Outputs
(Stud Connectors)
Single, Dual orTriple Outputs
(Two 18 pin Molex Connectors)
Single, Dual, Triple or Quadruple Outputs
(Two 18 pin Molex Connectors)
For a single output configuration,
either M1or M2 is used
(assumes either a full brick
and/or half brick is used) (assumes only half bricks are used)
Note:The type of output connector a FlatPAC-EN has depends on which modules are used. E.g. if a two output configuration uses
two half bricks (instead of a full brick and half brick) this two output configuration will have the 18 pin molex connectors,
not stud connectors.
(assumes only half and/or
quarter bricks are used)

FlatPAC-EN/EN MI “Quick Install” Instructions (For mechanical drawings, see page 10)
Mounting the FlatPAC-EN/EN MI
• Mount the FlatPAC-EN on the bottom (cannot be mounted from the front).
• For standard mounting (forced air cooling), use A1, A2, A3, A4 mount-
ing holes.
For standard mounting (conduction cooling), use A1, A2, A3, A4, B and B2
mounting holes.
• For a Vicor 2 Up FlatPAC retrofit replacement, use C1 and C2 as these
two are identical to the mounting holes on the FlatPAC.
• For increased ruggedness, use additional mounting holes to secure the power
supply.
• Use #8-32 or 4mm mounting screws. For mounting holes A1, A2, A3 and
A4, the maximum penetration should not exceed 0.125 in. (3mm). For mount-
ing holes B1, B2, C1 and C2, do not exceed maximum penetration of 0.250 in.
(6 mm).
* The maximum allowable torque is 5 in. lbs.,
Input Connections
Input Power MBJ1
• Apply input AC power connector MBJ1 using a maximum torque of 5 in. lbs
• Place a fuse or circuit breaker in the input line for safety requirements
(9A).
• Use Molex mating receptacle 39-01-4051, terminals 39-00-0090 and crimp
tool Molex # 11-01-0199.
Output Connections (Refer to page 6 for more information on configuration
layout and output connector type)
Note: The type of output connector a FlatPAC-EN has depends on which modules are
used. Also, outputs with molex connectors are limited to 9A/pin (27A per output).
Power Connections
Installing power connectors on outputs with 10-32 stud connectors (only full
and/or half bricks used):
• Install #10 ring lugs on output studs
* The right stud is positive and the left stud is the return when viewed from the
output end.
• Remove the nut and place ring lug over output stud.
• Replace and tighten the nut to a torque of 10 inch pounds. Do Not Over-
Tighten Nuts.
Installing power connectors on outputs with 18 pin Molex connectors (only
half bricks used):
• The output M1 slot accepts either a Mini or a Junior module. J2-7, J2-8, J2-
16 are positive, while pins J2-9, J2-17 and J2-18 are the returns.
• J2-1, J2-2, J2-3, J2-4, J2-5, J2-10, J2-11, J2-12 and J2-14 are not connected.
• The output M2 slot accepts either a Mini or a Junior module. J3-7, J3-8,
and J3-16 are positive while pins J3-9, J3-17 and J3-18 are the returns.
• The output M3 slot accepts either a Mini or a Junior module. J3-1, J3-10,
J11 are positive while pins J3-2, J3-3, J3-12 are the returns.
• For this 18 pin housing, use Molex mating receptacle #39-01-2180 with #39-
00-0039 terminals.
• Attach 18-24 AWG stranded wire using Molex tool #11-01-0197.
• Note: The molex connectors are limited to 9A/pin (27A per output)
Rev. 2/2012 Vicor 800-735-6200 Westcor Division 408-522-5280 Applications Engineering 800-927-9474 Pg. 7
FlatPAC-EN/EN MI Design Guide
Identical mounting
holes (CI & C2) to Vicor's
2 UP FlatPAC
C1 C2
B1 B2
A3 A4
A1 A2
MBJ1
N/C
N/C
L1
L2/N
GND
OUTPUT M1 OUTPUT M2
10-32 STUDS
+
J2
-
M1
-
J1
+
STUD OUTPUT CONNECTORS
OUTPUTS M2 & M3
OUTPUT M1
18 PIN MOLEX OUTPUT CONNECTOR
J2
J3
1
18
9
10
1
9
10
18
PIN DESCRIPTION
1 N/C
2 N/C
3 N/C
4 N/C
5 N/C
6 TRIM M1
7 +V OUT M1
8 +V OUT M1
9 -V OUT M1
PIN DESCRIPTION
10 N/C
11 N/C
12 N/C
13 + SENSE M1
14 N/C
15 - SENSE M1
16 +V OUT M1
17 - V OUT M1
18 - V OUT M1
J2
PIN DESCRIPTION
1 +V OUT M3
2 -V OUT M3
3 -V OUT M3
4 + SENSE M3
5 - SENSE M3
6 TRIM M2
7 +V OUT M2
8 +V OUT M2
9 -V OUT M2
PIN DESCRIPTION
10 +V OUT M3
11 +V OUT M3
12 -V OUT M3
13 + SENSE M2
14 TRIM M3
15 - SENSE M2
16 +V OUT M2
17 - V OUT M2
18 - V OUT M2
J3

Installing power connectors on outputs with 18 pin Molex connectors
(only half and/or quarter bricks used):
• The output M1 slot only accepts a Micro module. J2-7, J2-8, J2-13 and
J2-16 are positive, while pins J2-9, J2-15, J2-17 and J2-18 are the
returns.
• The output M2 slot only accepts a Micro module. J2-1, J2-4, J2-10, J2-
11 are positive, while pins J2-2, J2-3, J2-5 and J2-12 are the returns.
• The output M3 slot only accepts a Micro module. J3-7, J3-8, J3-13
and J3-16 are positive, while pins J3-9, J3-15, J3-17 and J3-18 are the
returns.
• The output M4 slot only accepts either a Mini or a Junior module. J3-1,
J3-10 and J3-11 are positive while pins J3-2, J3-3, and J3-12 are the
returns.
• For this 18 pin housing, use Molex mating receptacle #39-01-2180 with
#39-00-0039 terminals.
• Attach 18-24 AWG stranded wire using Molex tool #11-01-0197
• Note: The molex connectors are limited to 9A/pin (27A per output)
See page 11 for detailed diagrams of output connections.
Sense Connections
The FlatPAC-EN/EN MI is shipped with Autosense installed (For more informa-
tion on Autosense, refer to page 16)
Sense Connections for stud outputs (only full and/or half bricks used):
• For Remote Sense, connect Remote Sense wires to Remote Sense/Trim Pin
Access Connector J1 or J2 for single output and J1/J2 for dual outputs.
*Connector pins J1-2 and J2-2 are the + Senses and J1-3 and J2-3 are
the -Senses.
• Use Molex mating receptacle #50-57-9403 with #16-02-0103 terminals.
• Attach terminals to 24-30 AWG stranded twisted pair wire using Molex tool #
11-01-0208.
• Attach opposite end of sense lines to their respective outputs to point where
regulation is desired. Verify that sense lines are not cross-connected.
Sense Connections on 18 pin molex output connectors (only half bricks used):
• If Remote Sense is desired, connect Remote Sense wires to the sense lines of
Connector J2 for output 1 and J3 for outputs 2 and 3.
* For Output M1, J2-13 is the +Sense and J2-15 is the -Sense.
* For Output M2, J3-13 is the +Sense and J3-15 is the -Sense.
* For Output M3, J3-4 is the +Sense and J3-5 is the -Sense.
• Use Molex mating receptacle #39-01-2180 with #39-00-0039 terminals.
• Attach 18-24 AWG stranded twisted pair wire using Molex tool #11-01-
0197.
Sense Connections on 18 pin output connectors (only half and/or quarter bricks
used):
• If Remote Sense is desired (available only on output M4), connect Remote
Sense wires to sense lines of Connector J3
* Remote Sense is NOT available for Micro modules and hence is not
available on outputs M1, M2 and M3.
* On output M4, J3-4 is the +Sense and J3-5 is the -Sense.
• Use Molex mating receptacle #39-01-2180 with #39-00-0039 terminals.
• Attach 18-24 AWG stranded twisted pair wire using Molex tool #11-01-0197
Pg 8 Vicor 800-735-6200 Westcor Division 408-522-5280 Applications Engineering 800-927-9474 Rev. 2/2012
FlatPAC-EN/EN MI Design Guide
OUTPUTS M1 & M2 OUTPUTS M3 & M4
18 PIN MOLEX OUTPUT CONNECTORS
J2 J3
PIN DESCRIPTION
1 +V OUT M2
2 -V OUT M2
3 -V OUT M2
4 +V OUT M2
5 - VOUT M2
6 TRIM M1
7 +V OUT M1
8 +V OUT M1
9 -V OUT M1
PIN DESCRIPTION
10 +V OUT M2
11 +V OUT M2
12 -V OUT M2
13 + VOUT M1
14 TRIM M2
15 - VOUT M1
16 +V OUT M1
17 - V OUT M1
18 - V OUT M1
PIN DESCRIPTION
1 +V OUT M4
2 -V OUT M4
3 -V OUT M4
4 + SENSE M4
5 - SENSE M4
6 TRIM M3
7 +V OUT M3
8 +V OUT M3
9 -V OUT M3
PIN DESCRIPTION
10 +V OUT M4
11 +V OUT M4
12 -V OUT M4
13 + VOUT M3
14 TRIM M4
15 - VOUT M3
16 +V OUT M3
17 - V OUT M3
18 - V OUT M3
1
9
10
18
1
9
10
18
OUTPUT M1 OUTPUT M2
10-32 STUDS
+
M2
J2
-
M1
-
J1
+
STUD OUTPUT CONNECTORS
1
2
3
1 Trim Pin
2 + Remote Sense
3 - Remote Sense
Pin
OUTPUTS M2 & M3
OUTPUT M1
18 PIN MOLEX OUTPUT CONNECTORS
J2 J3
J2-13 + SENSE M1
J2-15 - SENSE M1
J3-4 + SENSE M3
J3-5 - SENSE M3
J3-13 + SENSE M2
J3-15 - SENSE M2
1
18
9
10
1
9
10
18
+S
-S
+S
-S
+S
-S
OUTPUTS M1 & M2 OUTPUTS M3 & M4
18 PIN OUTPUT CONNECTORS
J2 J3
M4 accepts 1 Mini or 1
Junior
J3-4 + SENSE M4
J3-5 - SENSE M4
1
9
10
18
1
9
10
18
M1, M2, M3 accept Micro modules
No sense connections are available
for Micro modules
+S
-S

Trim Connections
Trim Connections on stud output connectors (when full and/or half brick
used) :
• For output M1, J1-1 provides Trim Access
• For output M2, J2-2 provides Trim Access
• Use Molex mating receptacle #50-57-9403 with #16-02-0103 terminals.
• Attach 24-30 AWG stranded wire using Molex tool #11-01-0208.
Trim Connections for 18 pin Molex output connectors (when half bricks
used):
• For output M1, J2-6 provides Trim access
• For output M2 and M3, J3-6 and J3-14 provides Trim access respectively.
• Use Molex mating receptacle #39-01-2180 with #39-00-0039 terminals.
• Attach 18-24 AWG stranded wire using Molex tool #11-01-0197.
Trim Connections for 18 pin Molex output connectors (when half and/or
quarter bricks used):
• For outputs M1 and M2, J2-6 and J2-14 provide Trim access respectively.
• For outputs M3 and M4, J3-6 and J3-14 provide Trim access respectively.
• Use Molex mating receptacle #39-01-2180 with #39-00-0039 terminals.
• Attach 18-24 AWG stranded wire using Molex tool #11-01-0197.
Interface Connections
• CBJ1-1 is Signal Ground and CBJ1-3 is AC OK.
• CBJ1-4 is the Transmit and CBJ1-5 is the Receive functions for the RS-232
command protocol.+
• CBJ1-4 thru 9 are Enable/Disable,CBJ1-10 is General Shutdown and CBJ3-
12 is +5VS.
• For the FlatPAC-EN, CBJ1-2 and CBJ1-11 are not connected.
• Use Molex mating receptacle #50-57-9412 with #16-02-0097 cinch pins.
• Attach 24-30 AWG stranded wire using Molex tool #11-01-0209.
+ These functions are part of the RS-232 Command Protocols. See page 14 for
detailed information .
Rev. 2/2012 Vicor 800-735-6200 Westcor Division 408-522-5280 Applications Engineering 800-927-9474 Pg. 9
FlatPAC-EN/EN MI Design Guide
1
2
3
1 Trim Pin
2 + Remote Sense
3 - Remote Sense
Pin
OUTPUT M1 OUTPUT M2
10-32 STUDS
+
M2
J2
-
M2
M1
-
J1
+
TRIM: STUD OUTPUT CONNECTORS
OUTPUTS M2 & M3
OUTPUT M1
18 PIN MOLEX OUTPUT CONNECTORS
J2 J3
J2-6 TRIM M1 J3-6 TRIM M2 J3-14 TRIM M3
1
18
9
10
1
9
10
18
TT
T
OUTPUTS M1 & M2 OUTPUTS M3 & M4
18 PIN MOLEX OUTPUT CONNECTORS
J2 J3
J2-6 TRIM M1 J2-14 TRIM M2 J3-6 TRIM M3 J3-14 TRIM M4
1
9
10
18
1
9
10
18
T
T
T
T
PIN DESCRIPTION
CBJ1-1 SGND
CBJ1-2 N/C
CBJ1-3 ACOK
CBJ1-4 TX
CBJ1-5 RX
CBJ1-6 E/D-4
CBJ1-7 E/D-3
CBJ1-8 E/D-2
CBJ1-9 E/D-1
CBJ1-10 GSD
CBJ1-11 N/C
CBJ1-12 +5VS

FlatPAC-EN/EN MI Mechanical Drawings
Pg 10 Vicor 800-735-6200 Westcor Division 408-522-5280 Applications Engineering 800-927-9474 Rev. 2/2012
FlatPAC-EN/EN MI Design Guide
1CB J1 (12 PIN)
MBJ1
1
9.53.38 215.908.500
12.70.50
101.604.000
4X #8-32 x .125 OR M4 x 3mm MAX LG
FROM OUTSIDE OF POWER SUPPLY
CUSTOMER MOUNTING HOLES
138.435.450
147.965.825
5.56.219
115.894.563
AIR
FLOW
CUSTOMER MOUNTING HOLES
4X #8-32 x .250 OR M4 x 6mm MAX LG
FROM OUTSIDE OF POWER SUPPLY
OUTPUTS M1 & M2 OUTPUTS M3 & M4
J2
J3
OUTPUT M2 & M3
OUTPUT M1
J2
J3
OUTPUT M1 OUTPUT M2
+
M2
J2
-
M2
M1
M1
-
J1
+
PIN 1
N/C
N/C
L1
L2/N
GND
0.77.03
35.591.40
233.699.20
C1
C2
MATING CONNECTOR:
HOUSING: MOLEX (50-57-9412)
SOCKET CRIMP 24-30 AWG: MOLEX (16-02-0097)
CRIMP TOOL: MOLEX (11-01-0209)
23
CBJ1 E/D INTERFACE CONNECTOR
4
PIN REF DESCRIPTION
CBJ1-1 SGND SIGNAL GROUND
CBJ1-2 N/C N/C
CBJ1-3 ACOK AC POWER OK
CBJ1-4 TX TRANSMIT
CBJ1- 5 RX RECEIVE
CBJ1-6 E/D-4 ENABLE/DISABLE
CBJ1-7 E/D-3 ENABLE/DISABLE
CBJ1- 8 E/D-2 ENABLE/DISABLE
CBJ1-9 E/D-1 ENABLE/DISABLE
CBJ1-10 GSD GENERAL SHUTDOWN
CBJ1-11 N/C N/C
CBJ1-12 +5VS +5V@300mA
3
2
1REFERENCE DESIGNATION
NOTES: UNLESS OTHERWISE SPECIFIED
MB MOTHER BOARD
CB CONTROL BOARD
CONNECTOR PART NUMBERS SPECIFIED ARE MOLEX OR EQUIVALENT
A COMPLETE SET OF MATING CONNECTORS CAN BE PURCHASED FROM WESTCOR BY SPECIFYING
CONNECTOR KIT P/N 19-130044.
4
CBJ4 AND CBJ5 ARE PART OF THE RS-232 MICROCONTROLLER FUNCTIONS. SEE PAGE 12 INFORMATION.
5
FOR A VICOR 2 UP FLATPAC RETROFIT, USE MOUNTING HOLES C1 AND C2. SEE PAGE 4 OR 7 FOR MOUNTING DETAILS.
5
5
MATING CONNECTOR:
HOUSING: MOLEX (39-01-4051)
SOCKET CRIMP 16 AWG: MOLEX (39-00-0090)
CRIMP TOOL: MOLEX (11-01-0199)
MBJ1 A/C INPUT 23
Measurement tolerances are
Fractions +/- 1/32
Decimals .xx +/- .01
.xxx +/- .005
Angles +/- 1/2o
Note: The type of output connector a FlatPAC-EN has
depends on which modules are used.
See page 11 for detailed
output connection information

Rev. 2/2012 Vicor 800-735-6200 Westcor Division 408-522-5280 Applications Engineering 800-927-9474 Pg. 11
FlatPAC-EN/EN MI Design Guide
Output Connectors for FlatPAC-EN/EN MI
2
3
4
5
6
7
8
11
12
13
14
15
16
17
110
918
MATING CONNECTOR:
18 PIN HOUSING: MOLEX (39-01-2180)
TERMINAL FEM CRIMP 18-24 AWG: MOLEX (39-00-0039)
USE CRIMP TOOL: MOLEX (11-01-0197)
10-32 OUTPUT STUDS
- SENSE
3
SxJ2 REMOTE SENSE/TRIM
PIN CONNECTOR
1
2
TRIM
+ SENSE
MATING CONNECTOR:
HOUSING: MOLEX (50-57-9403)
TERMINAL FEM CRIMP 24-30 AWG: MOLEX (16-02-0103)
USE CRIMP TOOL: MOLEX (11-01-0208)
B. 18 PIN MOLEX CONNECTORS - when configured only with half bricks
A. STUD OUTPUT CONNECTOR - when configured with full brick and/or half brick
-V OUT
+V OUT
C. 18 PIN MOLEX CONNECTORS - when configured with half and/or quarter bricks
Refer to page 6 to review configuration layout of FlatPAC-EN
MATING CONNECTOR:
18 PIN HOUSING: MOLEX (39-01-2180)
TERMINAL FEM CRIMP 18-24 AWG: MOLEX (39-00-0039)
USE CRIMP TOOL: MOLEX (11-01-0197)
2
3
4
5
6
7
8
11
12
13
14
15
16
17
110
918
10 N/C
11 N/C
12 N/C
13 + SENSE M1
14 N/C
15 - SENSE M1
16 +V OUT M1
17 -V OUT M1
18 -V OUT M1
PIN DESCRIPTION
1 N/C
2 N/C
3 N/C
4 N/C
5 N/C
6 TRIM M1
7 +V OUT M1
8 +V OUT M1
9 -V OUT M1
Outputs M1
10 +V OUT M3
11 +V OUT M3
12 -V OUT M3
13 + SENSE M2
14 TRIM M3
15 - SENSE M2
16 +V OUT M2
17 -V OUT M2
18 -V OUT M2
PIN DESCRIPTION
1 +V OUT M3
2 -V OUT M3
3 -V OUT M3
4 + SENSE M3
5 - SENSE M3
6 TRIM M2
7 +V OUT M2
8 +V OUT M2
9 -V OUT M2
Outputs M2 and M3
OUTPUT M2 & M3
OUTPUT M1
J2
3
1 +V OUT M2
2 -V OUT M2
3 -V OUT M2
4 +V OUT M2
5 -V OUT M2
6 TRIM M1
7 +V OUT M1
8 +V OUT M1
9 -V OUT M1
Outputs M1 and M2
10 +V OUT M2
11 +V OUT M2
12 -V OUT M2
13 +V OUT M1
14 TRIM M2
15 -V OUT M1
16 +V OUT M1
17 - V OUT M1
18 - V OUT M1
1 +V OUT M4
2 -V OUT M4
3 -V OUT M4
4 +SENSE M4
5 -SENSE M4
6 TRIM M3
7 +V OUT M3
8 +V OUT M3
9 -V OUT M3
Outputs M3 and M4
10 +V OUT M4
11 +V OUT M4
12 -V OUT M4
13 +V OUT M3
14 TRIM M4
15 -V OUT M3
16 +V OUT M3
17 - V OUT M3
18 - V OUT M3
OUTPUTS M1 & M2 OUTPUTS M3 & M4
J2
J3
Note: The type of output connector a FlatPAC-EN has depends on which modules are used. E.g. if a two output configuration uses two half bricks
(instead of a full brick and half brick) this two output configuration will have the 18 pin molex connectors, not stud connectors.
(Note: The Molex connectors are limited to 9A/pin (27A/output)
(Note: The Molex connectors are limited to 9A/pin (27A/output)

FlatPAC-EN - Connector Kit listing
Connector Kit 19-130044 - Available for purchase from Westcor
Pg 12 Vicor 800-735-6200 Westcor Division 408-522-5280 Applications Engineering 800-927-9474 Rev. 2/2012
FlatPAC-EN/EN MI Design Guide

Rev. 2/2012 Vicor 800-735-6200 Westcor Division 408-522-5280 Applications Engineering 800-927-9474 Pg. 13
FlatPAC-EN/EN MI Design Guide
Interface Connections
Chassis Input Power Terminals (MBJ1)
Input AC power is applied through connector MBJ1 using Molex mating connector 39-01-4051. Use 16 AWG
wire with Molex Socket Pin 39-00-0090 and Crimp Tool 11-01-0199.
A fault clearing device, such as a fuse or circuit breaker, with a maximum 9A rating at the power supply input is
required for safety agency compliance. It should be sized to handle the start-up inrush current of 14Apk rms at
either 115 Vac or 230 Vac.
Output Power Connections
There are two types of output power terminals available in the FlatPAC-EN. Each slot has one of the following
configurations: either 10-32 plated steel bolts or an 18 pin Molex connector (The type of output connector a
FlatPAC-EN has depends on which modules are used. See page 6 and 11. Molex connectors are limited to 9A/pin,
27A per output) The positive polarity of the stud output termination is the right bolt when viewed from the output
end. Each power output is isolated, so outputs of positive or negative polarity can be configured through proper
selection of the output reference terminal.
In order to minimize parasitic cable inductance and reduce EMI, the output power cables should be routed in close
proximity to one another, and large current loops should be avoided. To avoid excessive voltage drop, do not
undersize power cables, especially for high current outputs. Do not bulk input AC wires with the output wires
because this can couple output noise into the input wires which can increase EMI. Excessive cable inductance
coupled with large capacitive loading can introduce instability in switching power supplies. This problem can be
avoided with proper system design. Consult Vicor’s Applications Engineering Department for assistance with
applications that use long cable lengths and excessive load capacitance.
User Interface Connections
Signal Ground (CBJ1-1)
Signal Ground on CBJ1-1 is an isolated secondary ground reference for all CBJ1 interfacing signals. This is not
the same as Earth Ground on input power connector MBJ1.
MATING CONNECTOR:
HOUSING: MOLEX (39-01-4051)
SOCKET CRIMP 16 AWG: MOLEX (39-00-0090)
CRIMP TOOL: MOLEX (11-01-0199)
MBJ1 A/C INPUT MBJ1
N/C
N/C
L1
L2/N
GND
Figure 2: Input Power Terminal MBJ1
2
3
4
5
6
7
8
11
12
13
14
15
16
17
110
918
1 N/C
2 N/C
3 N/C
4 N/C
5 N/C
6 TRIM M1
7 +V OUT M1
8 +V OUT M1
9 -V OUT M1
10 N/C
11 N/C
12 N/C
13 + SENSE M1
14 N/C
15 - SENSE M1
16 +V OUT M1
17 - V OUT M1
18 - V OUT M1
PIN DESCRIPTION PIN DESCRIPTION
10-32 OUTPUT STUDS
TRIM
1
J1/J2 SENSE/TRIM
PIN CONNECTOR
3
2
- SENSE
+ SENSE
B. 18 PIN MOLEX OUTPUT CONNECTOR
A. STUD OUTPUT
J2 (18 PIN OUTPUT, SENSE
AND TRIM PIN CONNECTOR)
-V OUT
+V OUT
Outputs M2 and M3 (Using 2 Minis or 2 Juniors)
1 +V OUT M3
2 -V OUT M3
3 -V OUT M3
4 + SENSE M3
5 - SENSE M3
6 TRIM M2
7 +V OUT M2
8 +V OUT M2
9 -V OUT M2
10 +V OUT M3
11 +V OUT M3
12 -V OUT M3
13 + SENSE M2
14 TRIM M3
15 - SENSE M2
16 +V OUT M2
17 - V OUT M2
18 - V OUT M2
PIN DESCRIPTION PIN DESCRIPTION
J3 (18 PIN OUTPUT, SENSE
AND TRIM PIN CONNECTOR)
J2/J3
2
3
4
5
6
7
8
11
12
13
14
15
16
17
110
918
Outputs M3 and M4 (Using 1 Micro
and 1 Mini or 1 Junior)
1 +V OUT M4
2 -V OUT M4
3 -V OUT M4
4 + SENSE M4
5 - SENSE M4
6 TRIM M3
7 +V OUT M3
8 +V OUT M3
9 -V OUT M3
10 +V OUT M4
11 +V OUT M4
12 -V OUT M4
13 + VOUT M3
14 TRIM M4
15 - VOUT M3
16 +V OUT M3
17 - V OUT M3
18 - V OUT M3
PIN DESCRIPTION PIN DESCRIPTION
J3 (18 PIN OUTPUT, SENSE
AND TRIM PIN CONNECTOR)
1 +V OUT M2
2 -V OUT M2
3 -V OUT M2
4 +V OUT M2
5 - VOUT M2
6 TRIM M1
7 +V OUT M1
8 +V OUT M1
9 -V OUT M1
10 +V OUT M2
11 +V OUT M2
12 -V OUT M2
13 + VOUT M1
14 TRIM M2
15 - VOUT M1
16 +V OUT M1
17 - V OUT M1
18 - V OUT M1
PIN DESCRIPTION PIN DESCRIPTION
J2 (18 PIN OUTPUT, SENSE
AND TRIM PIN CONNECTOR)
J2/J3
Output M1 (Using 1 Mini or 1 Junior)
Outputs M1 and M2 (Using 2 Micros)
B. 18 PIN MOLEX OUTPUT CONNECTOR
(Note: The Molex connectors are limited to 9A/pin (27A/output)
Figure 3: Output Power Connections

AC OK (CBJ1-3)
AC OK is an active high TTL compatible signal and provides a status indication of the AC input power. It is on pin
CBJ1-3 and is capable of sinking 16 mA maximum. This signal switches to a TTL "1" when the high voltage bus
exceeds low-line condition during turn-on. Upon loss of input power, the bus voltage will drop, causing the AC
OK signal to go low. Typically, a 2.5ms holdup time is provided for a 500W load following the loss of the AC OK
signal.
TRANSMIT/RECEIVE RS-232 Command Protocol (CBJ1-4 and CBJ1-5)
The FlatPAC-EN/EN MI incorporates a microprocessor for communicating status and allowing user control. A
suitable Terminal Emulator must be used to communicate with this circuit. A free emulator can be downloaded
from the vicor website at www.vicorpower.com (FlatPAC-EN page). Operation in the remote mode requires com-
manding the Power Supply to be a slave via the RS-232 interface.
Operating Modes
The FlatPAC-EN has two operating modes, Remote and Manual, which can be set using the RS-232 interface fea-
ture. The operating mode setting is stored in a non-volatile EEPROM and requires an REON or REOFF command
in order to switch modes. The default mode setting from the factory is in Manual mode. The FlatPAC-EN has an
operating mode indicator LED, which is viewable through the left side vent hole nearest the CBJ1 E/D Interface
Connector. When this LED is ON, the power supply is operating in Remote Mode.
Communications Protocol
The protocol is an ASCII character stream that will be sent back and forth between the power supply and the user.
The FlatPAC-EN/EN MI in the remote mode will be considered a slave in that it will only respond to commands
and requests and will not initiate conversations. Communications are half-duplex in that only the FlatPAC-EN/EN
MI receiver or transmitter may be active at one time. The unit will reply to all commands or requests with a
defined response followed by a carriage return and line feed character pair (CR/LF). The user must wait for the
reply from the FlatPAC-EN before issuing the next command or request. The data bytes will have a format of 1
start bit, 8 data bits, 1 stop bit and no parity at 9600 Baud.
Commands, Status Requests and Module Replies
All commands and requests will have a reply. The reply will be one of the following character strings followed by
a CR/LF character pair. "OK"- Issued when a command has been received and acted upon and the command has no
return data associated with it. "Inv Command"- Issued when an unrecognized command has been received or a
command cannot be executed at this time. "Inv Range"- Issued when a command argument is not within a valid
range.
The following is the list of commands and their definitions. All commands must be followed with a CR/LF charac-
ter pair.
PUP - Power Up
This command starts the automatic turn on timed sequence for the modules. If a Power Down sequence is active at
the time this command is received, a reply of "Inv Command" is returned; otherwise "OK" is returned.
PDN - Power Down
This command starts the automatic turn off timed sequence for the modules. This command can be given at any
time and will cancel any uncompleted automatic power up sequences. "OK" is returned.
EMO - Emergency Off
This command turns all modules off. If either a Power Up or Power Down sequence is active at the time, it will be
terminated immediately. A response of "OK" is returned.
Pg 14 Vicor 800-735-6200 Westcor Division 408-522-5280 Applications Engineering 800-927-9474 Rev. 2/2012
FlatPAC-EN/EN MI Design Guide
LED Indicator inside
CBJ1
Interface
Connector
Output
Connections
Figure 4: LED Indicator

TON1, TON2, TON3, TON4 - Turn On commands for modules 1, 2, 3, or 4.
These commands turn on the module identified by the trailing digit. If an automatic sequence is in effect at the
time this command is received, a reply of "Inv Command" is returned; otherwise "OK" is returned.
TOFF1, TOFF2, TOFF3, TOFF4 - Turn Off commands for modules 1, 2, 3, or 4.
These commands turn off the module identified by the trailing digit. If an automatic sequence is in effect at the
time this command is received, a reply of "Inv Command" is returned; otherwise "OK" is returned.
SDON1, SDON2, SDON3, SDON4 - Set Delay On Time for modules 1, 2, 3 or 4.
These commands set the associated time delays for the DC-DC converters to be activated via "PC" pin release.
There is an additional delay of up to 7ms inherent in the DC-DC converters. These commands are entered with a
trailing argument. The valid range of the argument is from 1 to 255 and is in 10 millisecond increments. The effec-
tive range of delay then becomes 10 to 2550 milliseconds or 0.01 to 2.55 seconds. Out of range arguments are
replied to with an "Inv Range" message; otherwise "OK" is returned. The delay times are effective and run concur-
rent from either power up of the unit or from receipt of the Power Up command. If these commands are entered
without an argument then the unit will report the present settings of these variables.
SDOFF1, SDOFF2, SDOFF3, SDOFF4 - Set Delay Off Time for modules 1, 2, 3, or 4.
These commands set the associated time delays for the DC-DC converters to be deactivated via "PC"pin release.
These commands are entered with a trailing argument. The valid range of the argument is from 1 to 255 and is in
10 millisecond increments. The effective range of delay then becomes 10 to 2550 milliseconds or 0.01 to 2.55 sec-
onds. Out of range arguments are replied to with an "Inv Range" message; otherwise "OK" is returned. The delay
times are effective and run concurrent from either receipt of the Power Down command or from an error condition
with the unit. If these commands are entered without an argument then the unit will report the present settings of
these variables.
BV - Bus Voltage Readback
This command returns the current Bus Voltage reading.
MS - Module Status
This command returns the module status as shown: MS=X1 X2 X3 X4 X5
X1 indicates the status of module output 1.
X2 indicates the status of module output 2.
X3 indicates the status of module output 3.
X4 indicates the status of module output 4.
A "1" indicates the output is up/on and ok and a "0" indicates the output is down/off.
X5 indicates the status of the power supply Bus. A "1" indicates BUS OK and a "0" indicates BUS NOT OK.
SN - Serial Number
This command returns the serial number as set by factory (available only on request.)
REON - Remote Mode ON
This command put the power supply into the slave mode. In this mode the power supply will only respond when
commanded.
REOFF - Remote Mode OFF
This command put the power supply into the manual mode. In this mode the power supply will only respond to the
following commands via the RS-232 interface: REON, SN, SDON1, SDON2, SDON3, SDON4, BV, MS, HST.
HST - Heat Sink Temperature
This command returns Temperature of the Heat Sink in degrees Celsius. Heat Sink Temperature is measured fre-
quently and stored into EEPROM memory. Upon loss of power last measured value in stored in EEPROM.
Rev. 2/2012 Vicor 800-735-6200 Westcor Division 408-522-5280 Applications Engineering 800-927-9474 Pg. 15
FlatPAC-EN/EN MI Design Guide

Pg 16 Vicor 800-735-6200 Westcor Division 408-522-5280 Applications Engineering 800-927-9474 Rev. 2/2012
FlatPAC-EN/EN MI Design Guide
Enable/Disable Mode (CBJ1-8 and CBJ1-9)
The Enable/Disable control pins allow outputs to be sequenced either on or off. CBJ1-4 through CBJ1-9 are the
control pins for outputs 1 through 4. The Enable/Disable pins should be pulled low to less than 0.7V with respect
to Signal Ground to disable the outputs. They will source 9mA maximum. These pins should be open circuited or
allowed to exceed 4.5V when enabled. Do not apply more than 5V to these inputs.
The correspondence between a module and its E/D line as seen from the output end of the power supply goes from
left to right.
General Shutdown /GSD (CBJ1-10)
The GSD control pin on CBJ1-10 allows simultaneous shutdown of all outputs. This pin must be pulled down to
less than 0.7V, and will source 9mA maximum to shut down all outputs. The GSD pin should be open circuited or
allowed to exceed 4.5V when not in use, or when the outputs are to be enabled. Do not apply more than 5V to this
input at any time. Normal open circuit voltage is 1.5 to 4V with respect to Signal Ground.
Auxiliary Vcc +5V/300mA (CBJ1-12)
The Vcc on CBJ1-12 is an auxiliary 5V regulated power source. It is +5 Vdc +/–5% with respect to Signal Ground
and can supply 300 mA maximum. It is capable of withstanding a short, but shorted user interface functionality
will be lost.
+Sense/–Sense ( J2) (Not applicable when using BatMod current source.)
The sense lines for the outputs are shipped from the factory with Autosense. Autosense provides the user with
automatic sensing of the outputs. With Autosense, the FlatPAC-EN/EN MI will automatically operate in a Remote
Sense mode when the Remote Sense connections are made. But in the event that the Remote Sense is not connect-
ed or needed, no Local Sense selection is necessary - simply hook up the outputs and the FlatPAC-EN will auto-
matically operate in Local Sense mode. To check if an output has the Autosense feature, measure the impedance
from the + Out to + Sense and - Out to - Sense pins. If the impedance is 5 ohms, then the output has Autosense
and does not require local sense jumpers. When using the remote sense feature, the +Out and -Out load wires
should never be disconnected while the supply is operating. Failing to do so could damage the power supply.
In the local sense mode (Remote Sense lines not connected), the power supply will regulate the output at the output
terminals. The voltage appearing at the load may drop slightly due to voltage drop in the power cables. If it is nec-
essary to compensate for voltage drop along the output power cables, the output can be trimmed up or configured
for Remote Sense. Use stranded twisted pair 24-30 AWG wire for the Remote Sense lines. Remote Sense can com-
pensate for a voltage drop of up to 0.5V, or 0.25V on each leg.
The Sense connector for outputs with stud connectors is a 3 pin connector providing the +Sense connection on J1/
J2-2 and the - Sense connection on J1/J2-3. The Sense connector for outputs with 18 pin Molex connectors is pro-
vided on the 18 pin output connector that also provides the output and trim connections. See page 11 for details.
Note: Remote sense is not available for output configurations using the Micro modules.
FlatPAC-EN
4
7
Signal Ground
General Shutdown
Enable/Disable Output 1
J1
1
0
TTL "1" (OFF)
TTL "0" (ON)
A TTL "1" applied to the base of the transistor turns
output OFF. Pin 1 (or Pin 7 for GSD) is pulled Low
with respect to Signal Ground.
5Vcc
1
Enable/Disable Control
Figure 5: Enable/Disable Mode
78M05
Auxiliary Vcc
CBJ1-12
0.1 µF
Signal Ground
CBJ1
CBJ1-1
+5V/300 mA
Figure 6: Auxiliary Vcc

Rev. 2/2012 Vicor 800-735-6200 Westcor Division 408-522-5280 Applications Engineering 800-927-9474 Pg. 17
FlatPAC-EN/EN MI Design Guide
External Trim (Not applicable when using BatMod current source)
The Trim pin can be used for external control of the output voltage. Trim connections on single and dual output
connector for output M1 is J1-1 while for output M2 is J2-2. Trim connections on triple output connectors for out-
put M1 is J2-6, for output M2 is J3-6, and for output M3 is J3-14. Trim connections for quadruple output connec-
tors on outputs M1 and M2 is J2-6 and J2-14 respectively, and for outputs M3 and M4 is J3-6 and J3-14 respec-
tively. A 10% increase to the trim pin voltage will result in a 10% increase in output voltage. Reducing the trim
pin voltage by 10% will result in a 10% decrease in output voltage.
OUTPUT MODULE Vref RTH
VI-200/VI-J00 ≥3.3V 2.5V 10kΩ
VI-200/VI-J00 <3.3V 0.97V 3.88kΩ
Maxi/Mini/Micro (Predefined) 1.23V 1kΩ
Maxi/Mini/Micro (Userdefined) 1.23V Consult Factory
Table 1. Module Internal Reference Voltages and Thevenin Resistances.
Example:
±10% trim adjust on a 12V nominal output.
Figure 8 shows a typical variable trim circuit. Using a 10k trimpot (R7), the resistor values for R6 and R8 can be
calculated as follows:
V1= Vref + 10% = 2.75V Given: Vref = 2.5V (see Table 1)
IR5 = (2.75V - Vref)/RTH = (2.75V - 2.5V)/10kΩ= 25μA Given: RTH = 10kΩ(see Table 1)
Setting the bottom limit:
VR6 = 2.5V - 10% = 2.25V
And since IR5 = IR6 = 25μA,
R6 = VR6/IR6= 2.25V/25μA = 90kΩ
V2= V1+ VR6 = 2.75V + 2.25V = 5V
IR7 = V2/R7 = 5V/10kΩ= 500μA
IR8 = IR7 + IR6 = 525μA
VR8 = (Vnom +10%) - V2= 13.2V - 5V = 8.2V Given: Vnom = 12V
R8 = VR8/IR8 = 8.2V/525μA = 15.62kΩ
Consult Applications Engineering when trimming outputs below 5V.
(Remote Sense)
Load
+Out
+Sense
-Sense
-Out
Use 24-30 AWG
Twisted Pair Wires
R5
V Ref
Trim
R6
R8
R7
To Error
Amplifier
R4
R3
R2
R1
+
+
V2
V1
-
-
RTH
Use 24-30 AWG
Twisted Pair Wires
Load
+Out
+Sense
-Sense
-Out
Use 24-30 AWG
Twisted Pair Wires
Figure 7: Remote Sense
Figure 8: External Trim
Note: Trimming up by more than 15%
may induce over voltage protection.

Specifications (Typical at 25°C, nominal line and 75% load, unless otherwise specified)
GENERAL
Number of Outputs 1-4
Modules VI-200/VI-J00, VE-200/VE-J00: Maxi/Mini/Micro
Efficiency Typically > 70%
Safety Agency Approvals cURus – UL 60950-1, CSA 60950-1
cTUVus – EN 60950-1, UL 60950-1, CSA 60950-1
CE Mark – Low Voltage Directive, 73/23/EEC amended by 93/68/EEC
Vibration Mil-STD 810 Minimum Integrity (MI chassis only)
Shock Mil-STD 810 40G Functional Shock (MI chassis only)
Maximum Output Power Up to 500 Watts; 425 Watts for EN 61000-3-2/A14 compliance
(not to exceed input current of 9A) (105/190 Vac minimum input)
INPUT
Input 90-132/180-264 Vac 47-63Hz
250-380 Vdc
Inrush Current 14 A pk @ 115 Vac and 230 Vac
Line/Load Regulation VI200/VI-J00:± 0.2% max.10% to full load; ± 0.5% max. No load to 10% load
Line Regulation* Maxi/Mini/Micro:± 0.20% max. to 0.3% max LL to HL, Full Load
Ride Through Time 500W 400W
@ 115Vac (typical) 12ms 15ms
@ 230Vac (typical) 16ms 18ms
Harmonic Distortion EN61000-3-2 A/14 (For output power ≤425W or input current not
in excess of 3.33 A rms at 230 Vac, 50 Hz.)
Conducted EMI FCC and EN 55022 Class A(certain configurations meet EN 55022 Class B)
Mil-STD 461 may require external filter - contact factory
Power Factor >.70
Transient Burst Immunity EN61000-4-4
Surge Immunity EN61000-4-5
Voltage Dips EN61000-4-11
Dielectric Withstand Primary to Chassis GND = 1,500 VRMS
Primary to Secondary = 3,000 VRMS
Secondary to Chassis GND = 500 VRMS
* See Vicor module specifications. A preload may be necessary for modules trimmed down below 90% of normal output voltage.
OUTPUT
VI-200/VI-J00 Modules
Parameter MIN. TYP. MAX. UNITS NOTES
Setpoint Accuracy* 0.5 1 % of Vnom
Load/line Regulation ±0.2 % 10% to Full Load
Load/line Regulation ±0.5 % Load to 10%
Temperature Regulation 0.01 0.02 %/°C Over rated temp.
Long Term Drift 0.02 %/K hours
Output Ripple & Noise:
VI/E-200 100 mV p-p See module design guide
VI/E-J00 100 mV p-p for exact specifications
Voltage Trim Range
VI-200/VI-J00 Slots 50-110 % V out ± 10% on 10-15 Vout
Total Remote Sense Compensation 0.5 Volts Autosense. See pg.14
OVP Set Point1115 125 135 %Vout Recycle Power
Current Limit 105 115 125 % of I max Auto Recovery
Short Circuit Current 20 (1052) 130 %
Overtemperature Limiting Not available on VI-J00
*For special and adjustable voltages, maximum setpoint accuracy is 2% of Vnom.
1131% Nominal for Booster Modules. No OVP for VI-J00
2 VI-J00 modules only.
Pg 18 Vicor 800-735-6200 Westcor Division 408-522-5280 Applications Engineering 800-927-9474 Rev. 2/2012
FlatPAC-EN/EN MI Design Guide

Rev. 2/2012 Vicor 800-735-6200 Westcor Division 408-522-5280 Applications Engineering 800-927-9474 Pg. 19
FlatPAC-EN/EN MI Design Guide
OUTPUT (CONT’D.)
Maxi/Mini/Micro Modules
Parameter MIN. TYP. MAX. UNITS NOTES
Setpoint Accuracy* ±0.5 ±1 % of VNOM
Load Regulation ±0.01 % of VNOM See module design guide for e
exact specifications.
Temperature Regulation 0.002 0.005 %/°C -20 to 100°C
Long Term Drift 0.02 %/K hours
Output Ripple and noise:
Maxi 75 mV p-p See module design guide
Mini 100 mV p-p for exact output ripple
Micro 125 mV p-p specifications.
Voltage Trim Range
Maxi/Mini/Micro Slots 10-110 % Vout Preload may be required.
Total Remote Sense Compensation 0.5 Volts Autosense. See pg 14
OVP Set Point 112 135 % of Vout Recycle power
Current Limit 102 115 135 % of I max Auto Recovery
Overtemperature Limiting Not available
* For special, adjustable voltages and 48Vdc outputs, maximum setpoint accuracy is 2% of Vnom.
Note: See individual module datasheets for specific module specifications.
ENVIRONMENTAL
Storage Temperature -40°C to +100°C
Operating Temperature
Ambient air (see derating curves) -20°C to +70°C (MI -40°C to +70°C)
Case Temperature -20°C to +90°C (MI -40°C to +90°C)
(75° for full size VI-200 module)
Specific temperature data on all module configurations can be obtained by contacting Applications Engineering.
Altitude Derate 2.6% total output power for each 1,000 ft to a maximum
operating altitude of 15,000 ft. Non-operating storage maximum
altitude is 40K.
Humidity 0 to 95% non condensing
Product Weight 3.4 lbs. (1,5 kg)
Dimensions 1.4" H (35,6mm) x 5.0" W (127,0mm) x 9.20" L (233,7mm)
Warranty** 2 years limited warranty. See vicorpower.com for complete warranty
statement.
** Opening, repairing or modifying the unit will void the warranty. If you have any problem with the power supply, please
contact Customer Service at 1-800-735-6200. If the unit needs to be returned for inspection/analysis, an RMA number will
be issued. All units must have a RMA number prior to return.

Output Power Derating
Pg 20 Vicor 800-735-6200 Westcor Division 408-522-5280 Applications Engineering 800-927-9474 Rev. 2/2012
FlatPAC-EN/EN MI Design Guide
Other manuals for FlatPAC-EN
1
This manual suits for next models
1
Table of contents
Other VICOR Switch manuals
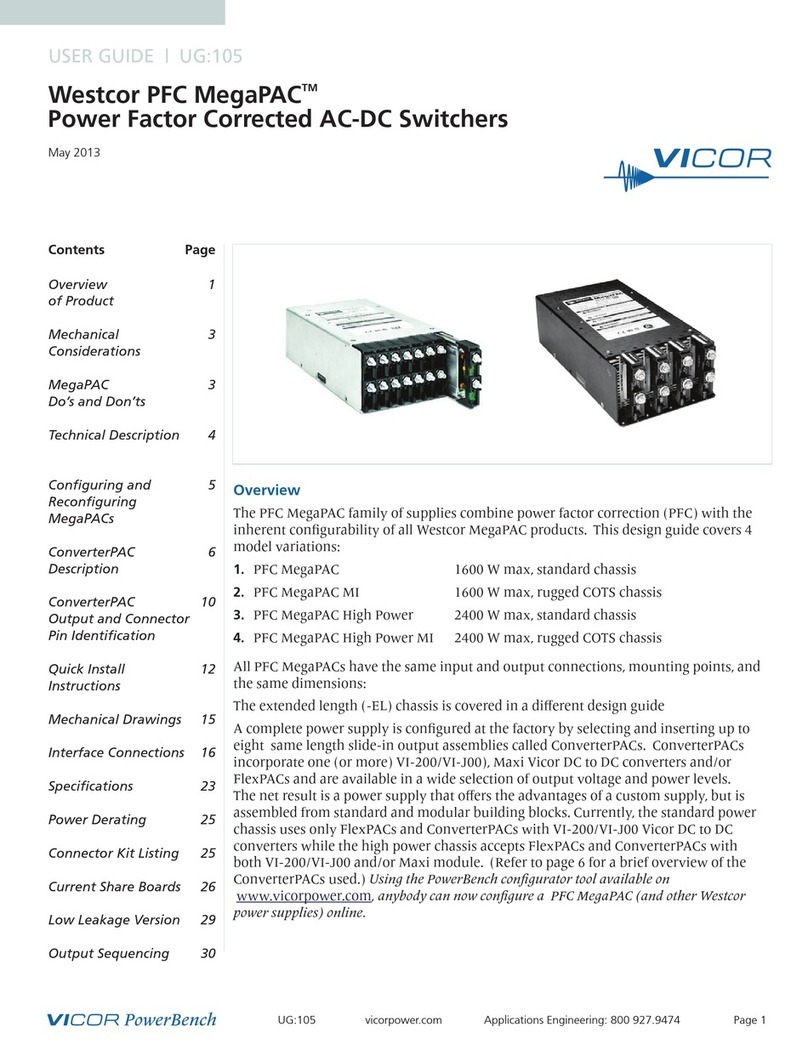
VICOR
VICOR PFC MegaPAC User manual

VICOR
VICOR FlatPAC Family AC Supplement
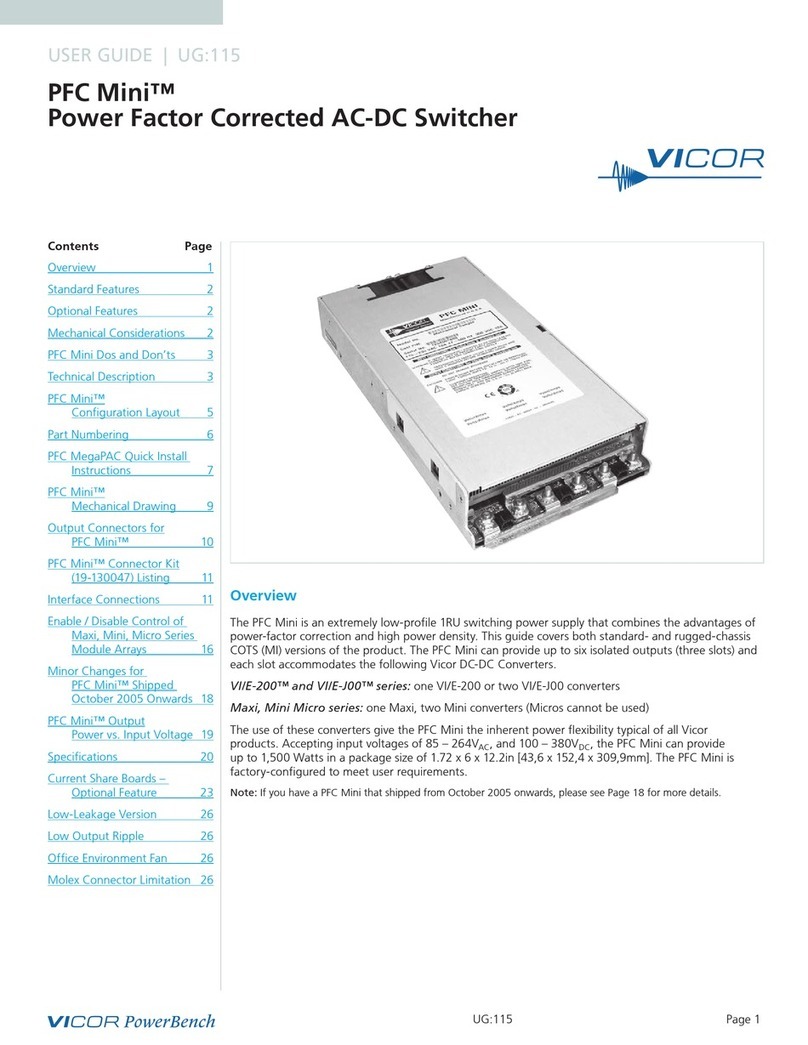
VICOR
VICOR PFC Mini User manual
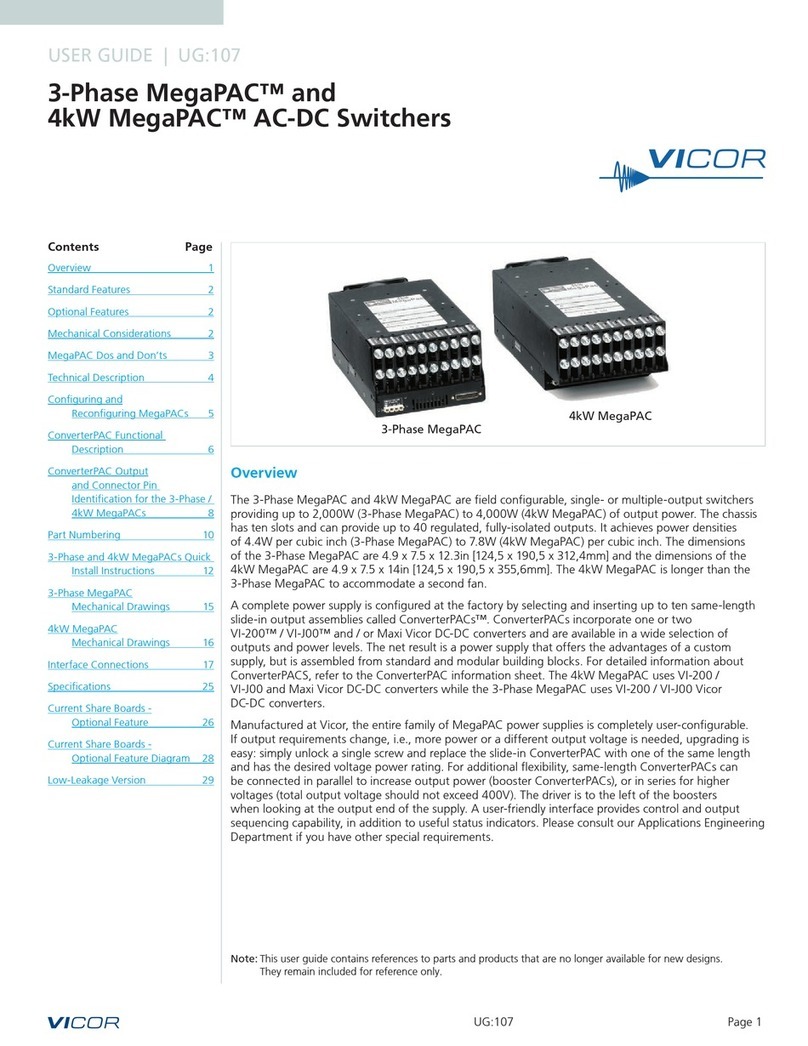
VICOR
VICOR MegaPAC 3-Phase User manual

VICOR
VICOR 3 Phase MegaPAC-ELTM User manual

VICOR
VICOR 3 Phase MegaPAC User manual
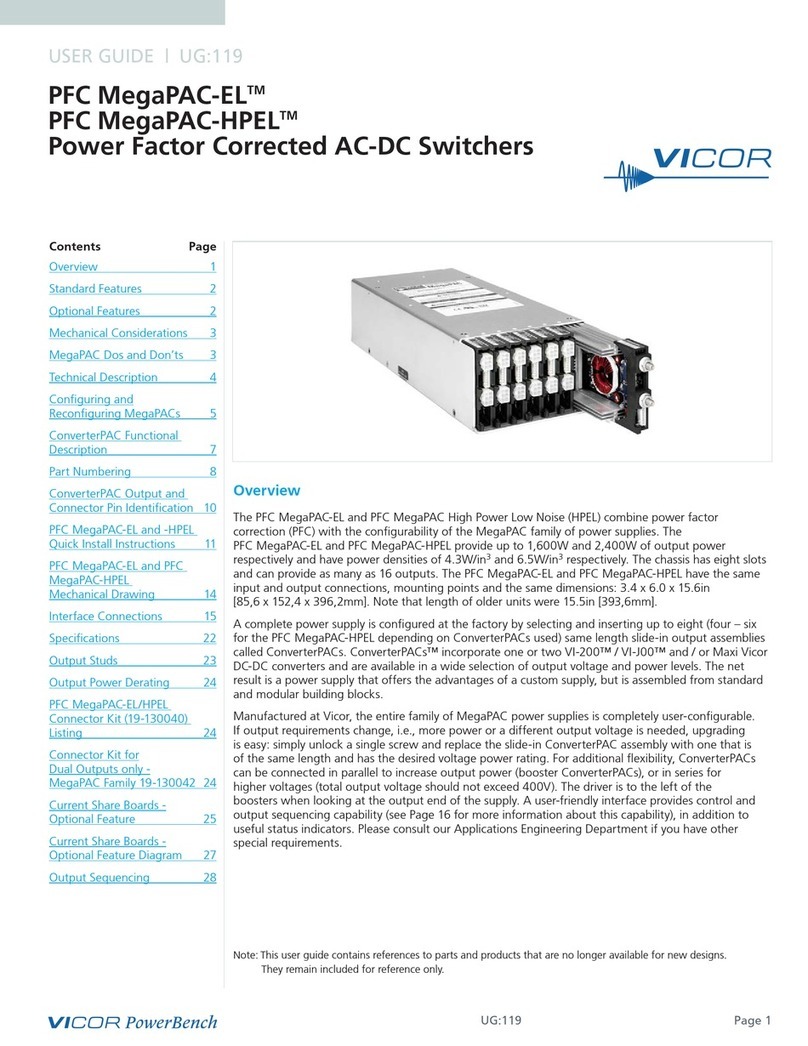
VICOR
VICOR PFC MegaPAC-EL User manual
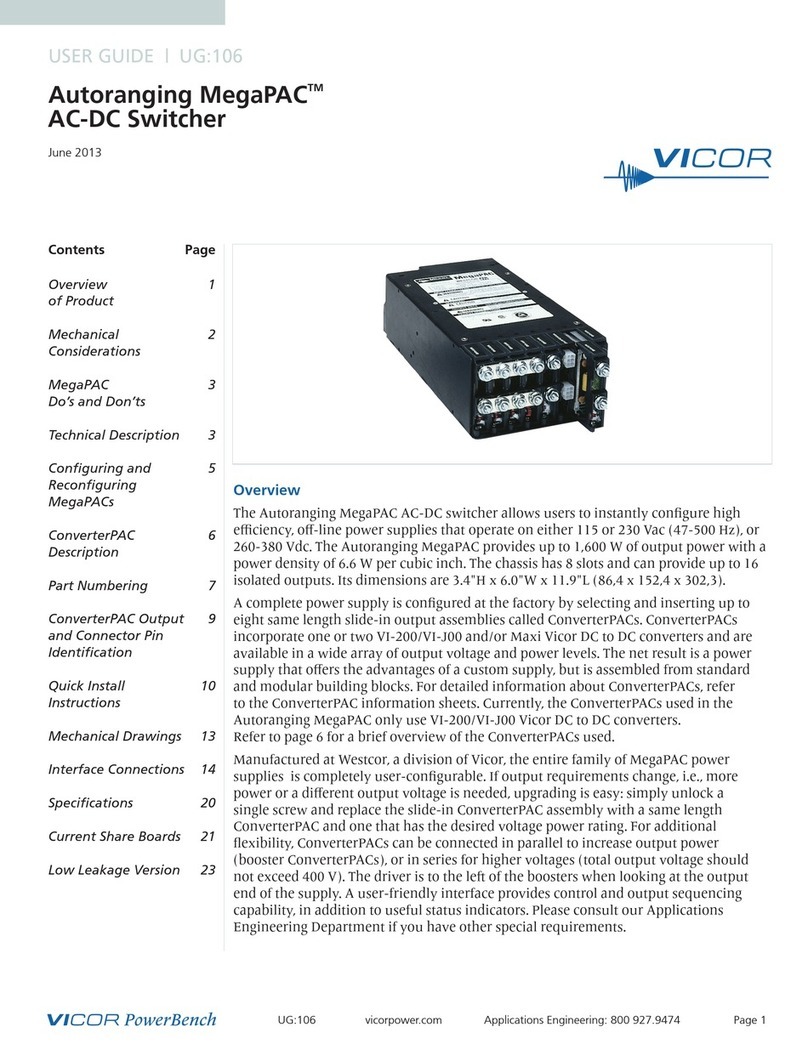
VICOR
VICOR UG:106 User manual
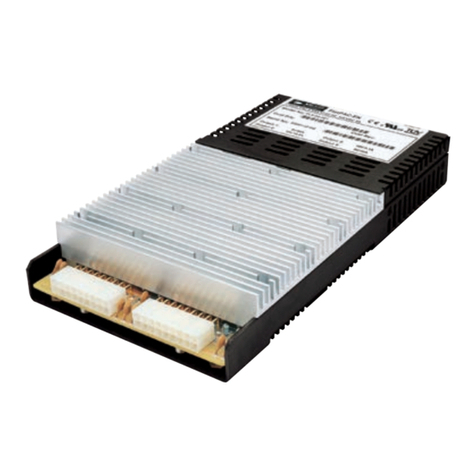
VICOR
VICOR FlatPAC-EN User manual
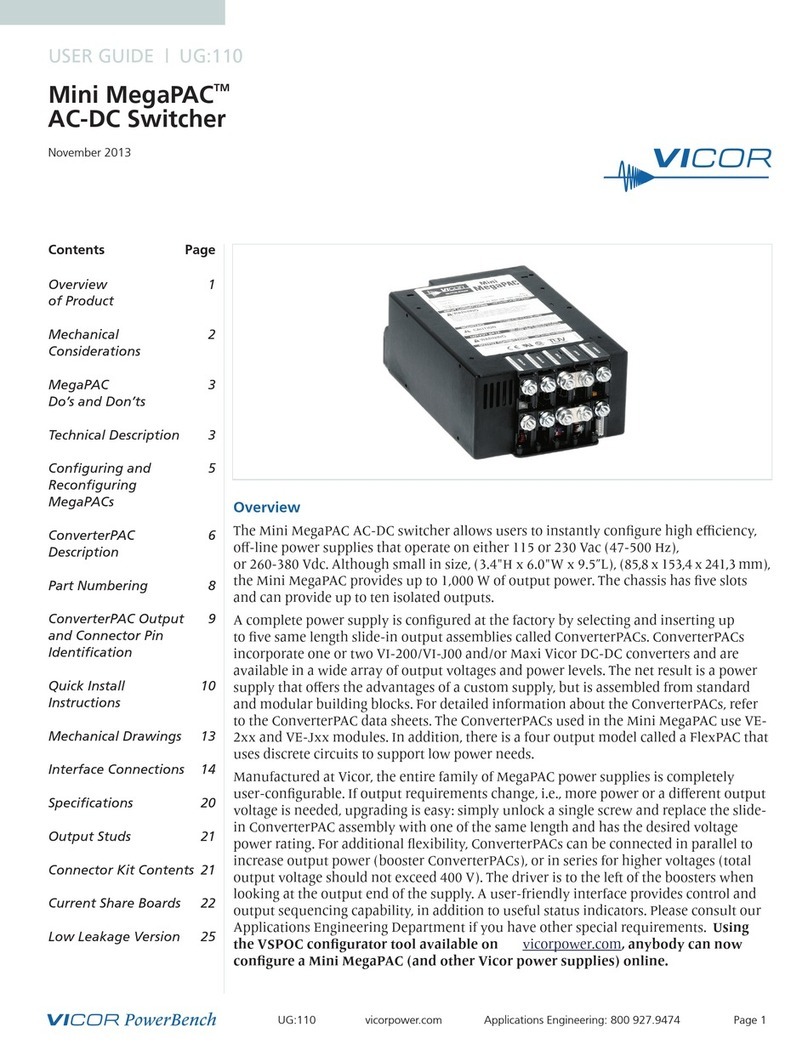
VICOR
VICOR Mini MegaPAC User manual