VorTek MT160 User manual

MT160
Ultrasonic Thickness Gauge
Instruction Manual
Document Number 800103
Rev A
8475 W I-25 Frontage Rd
Suite 300
Longmont, CO 80504
(303) 682-9999 (888) 386-7835 Fax (303) 682-4368
http://www.vortekinst.com

MT160 Instruction Manual
800103 1
1 Overview..................................... 3
1.1 Product Specifications .......................................... 3
1.2 Main Functions ..................................................... 4
1.3 Measuring Principle .............................................. 4
1.4 Configuration ........................................................ 5
1.5 Operating Conditions ............................................ 5
2 Features ....................................... 6
2.1 Main Screen .......................................................... 7
2.2 Keypad Definitions ............................................... 8
3 Preparation .................................. 9
3.1 Transducer Selection ............................................. 9
3.2 Condition and Preparation of Surfaces ............... 13
4 Operation................................... 14
4.1 Power On/Off...................................................... 14
4.2 Probe Zero........................................................... 14
4.3 Sound Velocity Calibration ................................. 16
4.4 Making Measurements........................................ 19
4.5 Scan mode........................................................... 23
4.6 Changing Resolution........................................... 25
4.7 Changing Units ................................................... 25
4.8 Memory Management......................................... 25
4.9 Beep Mode .......................................................... 27
4.10 EL Backlight ..................................................... 28
4.11 Battery Information........................................... 28
4.12 Auto Power Off ................................................. 28
4.13 System Reset..................................................... 29

MT160 Instruction Manual
800103 3
1 Overview
The model MT160 is a digital ultrasonic thickness gauge.
Based on the same operating principles as SONAR, the instrument
is capable of measuring the thickness of various materials with
accuracy as high as 0.1mm/0.01 millimeters. It is suitable for a
variety of metallic and non-metallic materials.
1.1 Product Specifications
1) Display: 4.5-digit LCD with EL backlight.
2) Measuring Range: (0.75~300) mm (in Steel)
3) Sound Velocity Range: (1000~9999) m/s
4) Resolution: MT160: 0.1mm/0.01mm
5) Accuracy: ± (0.5% Thickness + 0.04)mm, depends on
material and conditions
6) Units: Metric/Imperial unit selectable
7) Four readings per second for single point measurement, and
ten readings per second in Scan Mode.
8) Memory to store up to 20 files (up to 99 values for each file)
9) Power Source: Two “AA”, 1.5 Volt alkaline batteries.
100 hours typical operating time (EL backlight off).
10) Communication: MT160: USB serial port
11) Outline dimensions: 150mm × 74mm × 32 mm
12) Weight: 245g

MT160 Instruction Manual
800103 4
1.2 Main Functions
1) Capable of performing measurements on a wide range of
material, including: metals, plastic, ceramics, composites,
epoxies, glass and other acoustically conductive materials.
2) Transducer models are available for special applications,
including: high temperature or coarse material applications.
3) Probe-Zero function
4) Sound-Velocity-Calibration function
5) Two-Point Calibration function
6) Two operating modes: Single point and Scan mode
7) Coupling status indicator
8) Battery status indicator
9) Auto sleep and auto power off function to conserve battery
life.
1.3 Measuring Principle
The digital ultrasonic thickness gauge determines the
thickness of a part or structure by accurately measuring the time
required for a short ultrasonic pulse generated by a transducer to
travel through the thickness of the material, reflect from the back
or inside surface, and be returned to the transducer. The measured
two-way transit time is divided by two to account for the down-
and-back travel path, and then multiplied by the velocity of sound
in the material. The result is expressed in the well-known
relationship:

MT160 Instruction Manual
800103 5
2tv
H
=
Where:H-Thickness of the test piece.
v-Sound Velocity in the material.
t-The measured round-trip transit time.
1.4 Configuration
No.
Item
Quantity
Note
Standard
Configuration
1
Main body
1
2
Transducer
1
Model: N05
3
Couplant
1
4
Instrument Case
1
Optional
Configuration
5
Transducer: N02
See Table 3-1
6
Transducer: N07
7
Transducer: HT5
Table 1-1: Product Configuration
1.5 Operating Conditions
Operating Temperature: -20℃~+60℃;
Storage Temperature: -30℃~+70℃
Relative Humidity: ≤ 90%;
The surrounding environment should avoid that of vibration,
strong magnetic fields, corrosive medium and heavy dust.

MT160 Instruction Manual
800103 6
2 Features
Figure 1: Product Features
1 Main Body 2 Keypad 3 LCD Display 4 Transmitter
Socket 5 Receiver Socket 6 Probe Zero-Disc
7 Communication Port 8 Label 9 Battery Cover
10 Probe
POWER: 2 X 1.5V
SN:
ULTRASONIC
THICKNESS GAUGE
MT160

MT160 Instruction Manual
800103 7
2.1 Main Screen
Figure 2: Main Screen
1. Coupling Status: Indicates the coupling status. While the
gauge is taking a measurement, the coupling status indicator
should be on. If it is not on or not stable, the gauge is having
difficulty achieving a stable measurement, and the thickness value
displayed will most likely be erroneous.
2. Unit: Current unit system. MM or IN for thickness value. M/S
or IN/μS for sound velocity.
3. Battery Information: Indicates the remaining capacity of the
battery.
4. Information Display: Displays the measured thickness value,
the sound velocity, and shows hints of current operation.

MT160 Instruction Manual
800103 8
2.2 Keypad Definitions
Turn the instrument
on/off
Sound velocity
calibration
Turn on/off the EL
backlight
Enter
Probe-Zero operation
Plus;
Turn on/off Scan
Mode
Unit switch between
Metric and Imperial
system
Minus;
Turn on/off Beep
Mode
Data Save or Data
Delete
Figure 3: Keypad Definitions

MT160 Instruction Manual
800103 9
3 Preparation
3.1 Transducer Selection
The gauge is inherently capable of performing measurements
on a wide range of materials, from various metals to glass and
plastics. Different types of material, however, will require the use
of different transducers. Choosing the correct transducer for a job
is critical to being able to easily perform accurate and reliable
measurements. The following paragraphs highlight the important
properties of transducers, which should be considered when
selecting a transducer for a specific job.
Generally speaking, the best transducer for a job is one that
sends sufficient ultrasonic energy into the material being
measured such that a strong, stable echo is received by the gauge.
Several factors affect the strength of ultrasound as it travels. These
are outlined below:
Initial Signal Strength. The stronger a signal is to begin with,
the stronger its return echo will be. Initial signal strength is largely
a factor of the size of the ultrasound emitter in the transducer. A
large emitting area will send more energy into the material being
measured than a small emitting area. Thus, a so-called “1/2 inch”
transducer will emit a stronger signal than a “1/4 inch” transducer.
Absorption and Scattering. As ultrasound travels through any
material, it is partly absorbed. If the material through which the
sound travels has any grain structure, the sound waves will
experience scattering. Both of these effects reduce the strength of
the waves, and thus, the gauge’s ability to detect the returning

MT160 Instruction Manual
800103 10
echo. Higher frequency ultrasound is absorbed and scattered more
than ultrasound of a lower frequency. While it may seem that
using a lower frequency transducer might be better in every
instance, low frequencies are less directional than high
frequencies. Thus, a higher frequency transducer would be a better
choice for detecting the exact location of small pits or flaws in the
material being measured.
Geometry of the transducer. The physical constraints of the
measuring environment sometimes determine a transducer’s
suitability for a given job. Some transducers may simply be too
large to be used in tightly confined areas. Also, the surface area
available for contacting with the transducer may be limited,
requiring the use of a transducer with a small wear face.
Measuring on a curved surface, such as an engine cylinder wall,
may require the use of a transducer with a matching curved wear
face.
Temperature of the material. When it is necessary to measure
on surfaces that are exceedingly hot, high temperature transducers
must be used. These transducers are built using special materials
and techniques that allow them to withstand high temperatures
without damage. Additionally, care must be taken when
performing a “Probe-Zero” or “Calibration to Known Thickness”
with a high temperature transducer.
Selection of the proper transducer is often a matter of
tradeoffs between various characteristics. It may be necessary to
experiment with a variety of transducers in order to find one that
works well for a given job.

MT160 Instruction Manual
800103 11
The transducer is the “business end” of the instrument. It
transmits and receives ultrasonic sound waves that the instrument
uses to calculate the thickness of the material being measured. The
transducer connects to the instrument via the attached cable, and
two coaxial connectors. When using transducers, the orientation of
the dual coaxial connectors is not critical: either plug may be
fitted to either socket in the instrument.
The transducer must be used correctly in order for the
instrument to produce accurate, reliable measurements. Below is a
short description of the transducer, followed by instructions for its
use.
Figure 4: View of a Typical Transducer
The left image in Figure 4 is a bottom view of a typical
transducer. The two semicircles of the wear face are visible, as is
the barrier separating them. One of the semicircles is responsible
for conducting ultrasonic sound into the material being measured,
and the other semicircle is responsible for conducting the echoed
sound back into the transducer. When the transducer is placed
against the material being measured, it is the area directly beneath
the center of the wear face that is being measured.
The right image in Figure 4 is a top view of a typical
transducer. Press against the top with the thumb or index finger to

MT160 Instruction Manual
800103 12
hold the transducer in place. Moderate pressure is sufficient, as it
is only necessary to keep the transducer stationary, and the wear
face seated flat against the surface of the material being measured.
Table 3-1: Transducer Selection
Model
Freq
(MHz)
Diam
(mm)
Measuring
Range
Lower
limit
Description
N02
2.5
14
3.0mm~
300.0mm(In
Steel)
40mm (in Gray
Cast Iron
HT200)
20mm
For thick, highly
attenuating, or
highly scattering
materials
N05
5
10
1.2mm~
230.0mm(In
Steel)
Φ20mm×
3.0mm
Normal
Measurement
N07
7
6
0.75mm~
80.0mm
(In Steel)
Φ15mm×
2.0mm
For thin pipe wall
or small curvature
pipe wall
measurement
HT5
5
14
3~200mm
(In Steel)
30mm
For high
temperature
(lower than
300℃)
measurement.

MT160 Instruction Manual
800103 13
3.2 Condition and Preparation of Surfaces
In any ultrasonic measurement scenario, the shape and
roughness of the test surface are of paramount importance. Rough,
uneven surfaces may limit the penetration of ultrasound through
the material, and result in unstable, and therefore unreliable,
measurements. The surface being measured should be clean, and
free of any small particulate matter, rust, or scale. The presence of
such obstructions will prevent the transducer from seating
properly against the surface. Often, a wire brush or scraper will be
necessary to help clean the surface of the material. In more
extreme cases, rotary sanders or grinding wheels may be used,
though care must be taken to prevent surface gouging, which will
inhibit proper transducer coupling.
Extremely rough surfaces, such as the pebble-like finish of
some cast iron, will prove most difficult to measure. These kinds
of surfaces act on the sound beam like frosted glass on light, the
beam becomes diffused and scattered in all directions.
In addition to posing obstacles to measurement, rough
surfaces contribute to excessive wear of the transducer,
particularly in situations where the transducer is “scrubbed” along
the surface. Transducers should be inspected on a regular basis,
for signs of uneven wear of the wear face. If the wear face is worn
on one side more than another, the sound beam penetrating the test
material may no longer be perpendicular to the material surface.
In this case, it will be difficult to exactly locate tiny irregularities
in the material being measured, as the focus of the sound beam no

MT160 Instruction Manual
800103 14
longer lies directly beneath the transducer.
4 Operation
4.1 Power On/Off
The instrument is turned on by pressing the key.
Figure 5: LCD Display with Power Turned On
The gauge can be turned off by pressing the key while it
is on. The instrument has special memory that retains all of its
settings even when the power is off.
4.2 Probe Zero
The key is used to “zero” the instrument in much the
same way that a mechanical micrometer is zeroed. If the gauge is
not zeroed correctly, all the measurements that the gauge makes
may be in error by some fixed value. When the instrument is
“zeroed”, this fixed error value is measured and automatically

MT160 Instruction Manual
800103 15
corrected for in all subsequent measurements. The instrument may
be “zeroed” by performing the following procedure:
1) Plug the transducer into the instrument. Make sure that the
connectors are fully engaged. Check that the wear face of the
transducer is clean and free of any debris.
2) Press the key to activate the probe zero mode.
3) Use the key and the key to scroll to the probe model
currently being used. Be sure to set the right probe model in
the instrument, otherwise, erroneous measurements may
result.
4) Apply a single droplet of ultrasonic couplant to the face of the
metal probe-disc.
5) Press the transducer against the probe disc, making sure that
the transducer sits flat against the surface.
6) Remove the transducer from the probe disc.
At this point, the instrument has successfully calculated its
internal error factor, and will compensate for this value in any
subsequent measurements. When performing a “probe zero”, the
instrument will always use the sound velocity value of the built-in
probe-disc, even if some other velocity value has been entered for
making actual measurements. Though the instrument will
remember the last “probe zero” performed, it is generally a good
idea to perform a “probe zero” whenever the gauge is turned on,
as well as any time a different transducer is used. This will ensure
that the instrument is always correctly zeroed.
Pressing while in probe zero mode will stop current
probe zero operation and return to measurement mode.

MT160 Instruction Manual
800103 16
4.3 Sound Velocity Calibration
In order for the gauge to make accurate measurements, it
must be set to the correct sound velocity for the material being
measured. Different types of material have different inherent
sound velocities. If the gauge is not set to the correct sound
velocity, all of the measurements the gauge makes will be
erroneous by some fixed percentage. The One-Point calibration is
the simplest and most commonly used calibration procedure,
optimizing linearity over large ranges. The Two-Point calibration
allows for greater accuracy over small ranges by calculating the
probe zero and velocity.
Note: One and Two-Point calibrations must be performed on
material with the paint or coating removed. Failure to remove the
paint or coating prior to calibration will result in a multi material
velocity calculation that may be different from the actual material
velocity intended to be measured.
4.3.1 Calibration to a known thickness
Note: This procedure requires a sample piece of the specific
material to be measured, the exact thickness of which is known
(e.g. from having been measured by some other means).
1) Perform a Probe-Zero.
2) Apply couplant to the sample piece.
3) Press the transducer against the sample piece, making sure
that the transducer sits flat against the surface of the sample.
The display should show some thickness value, and the

MT160 Instruction Manual
800103 17
coupling status indicator should appear steady.
4) Having achieved a stable reading, remove the transducer. If
the displayed thickness changes from the value shown while
the transducer was coupled, repeat step 3.
5) Press the key to activate the calibration mode. The MM
(or IN) symbol should begin flashing.
6) Use the key and the key to adjust the displayed
thickness up or down, until it matches the thickness of the
sample piece.
7) Press the key again. The M/S (or IN/μS) symbols should
begin flashing. The gauge is now displaying the sound
velocity value it has calculated based on the thickness value
that was entered.
8) Press the key once again to exit the calibration mode and
return to the measurement mode. The gauge is now ready to
perform measurements.
4.3.2 Calibration to a known velocity
Note: This procedure requires that the operator know the sound
velocity of the longitudinal wave of the material to be measured.
Using the sound velocity of the transverse (shear) wave will result
in inaccurate measurements. A table of common materials and
their longitudinal wave sound velocities can be found in Appendix
A of this manual.
1) Press the key to activate the calibration mode. The MM
(or IN) symbol should begin flashing.
2) Press the key again, so that the M/S (or IN/μS) symbols

MT160 Instruction Manual
800103 18
are flashing.
3) Use the key and the key to adjust the sound velocity
value up or down, until it matches the sound velocity of the
material to be measured. You can also press the key to
switch among the predefined velocities that are most
commonly used.
4) Press the key to exit from the calibration mode. The
gauge is now ready to perform measurements.
To achieve the most accurate measurements possible, it is
generally advisable to always calibrate the gauge to a sample
piece of known thickness. Material composition (and thus, its
sound velocity) sometimes varies from lot to lot and from
manufacturer to manufacturer. Calibration to a sample of known
thickness will ensure that the gauge is set as closely as possible to
the sound velocity of the material to be measured.
4.3.3 Two Point Calibration
Note: This procedure requires that the operator has two known
thickness points on the test piece that are representative of the
range to be measured.
1) Perform a Probe-Zero.
2) Apply couplant to the sample piece.
3) Press the transducer against the sample piece, at the
first/second calibration point, making sure that the transducer
sits flat against the surface of the sample. The display should
show some (probably incorrect) thickness value, and the
coupling status indicator should appear steady.

MT160 Instruction Manual
800103 19
4) Having achieved a stable reading, remove the transducer. If
the displayed thickness changes from the value shown while
the transducer was coupled, repeat step 3.
5) Press the key. The MM (or IN) symbol should begin
flashing.
6) Use the key and the key to adjust the displayed
thickness up or down, until it matches the thickness of the
sample piece.
7) Press the key. The display will flash 1OF2. Repeat steps 3
through 6 on the first/second calibration point.
8) Press the key, so that the M/S (or IN/μS) symbols are
flashing. The gauge will now display the sound velocity value
it has calculated based on the thickness values that were
entered in step 6.
9) Press the key once more to exit the calibration mode. The
gauge is now ready to perform measurements within this
range.
4.4 Making Measurements
When the tool is displaying thickness measurements, the
display will hold the last value measured, until a new
measurement is made. See Figure 6 for a visual representation of
this behavior.
In order for the transducer to do its job, there must be no air
gaps between the wear face and the surface of the material being
measured. This is accomplished with the use of a “coupling” fluid,
Table of contents
Other VorTek Measuring Instrument manuals
Popular Measuring Instrument manuals by other brands
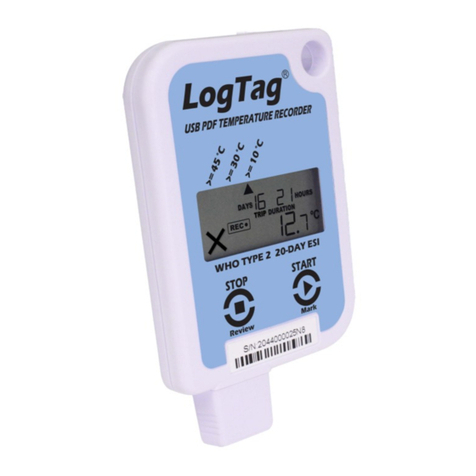
LogTag Recorders
LogTag Recorders USRID-16W Product user guide
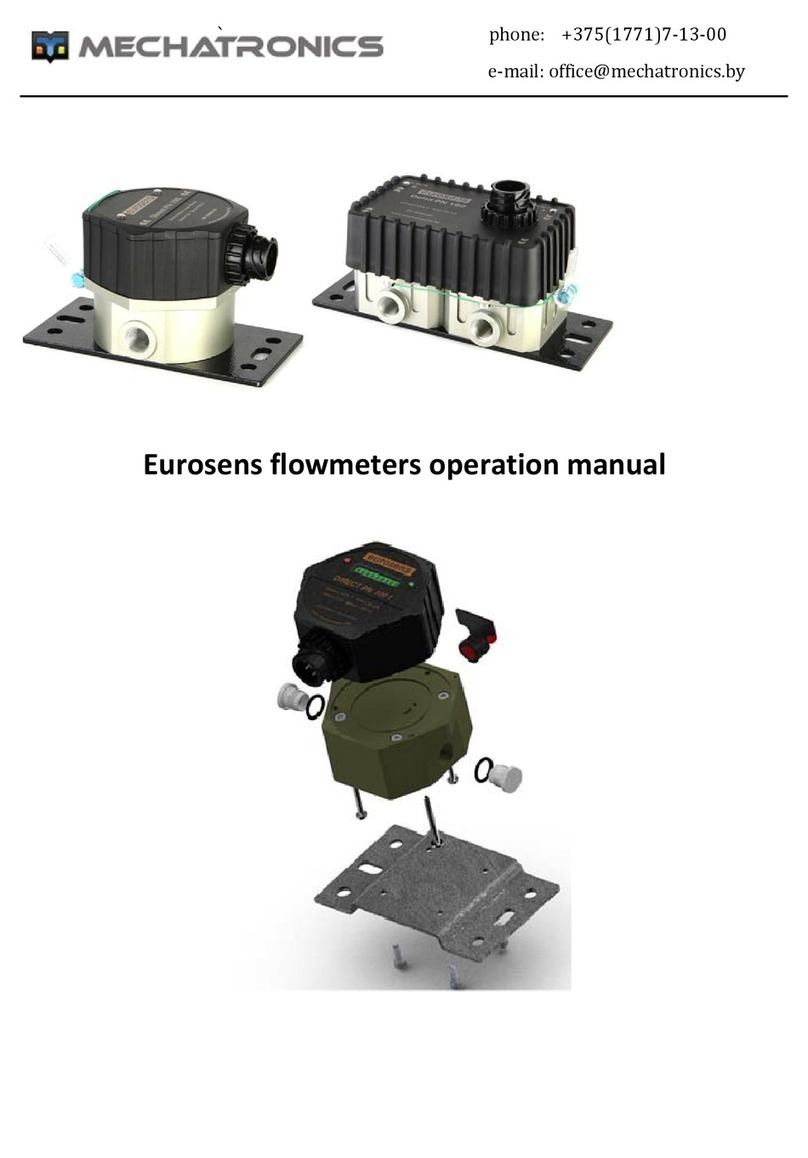
Mechatronics
Mechatronics Eurosens Direct PH 100 Operation manual
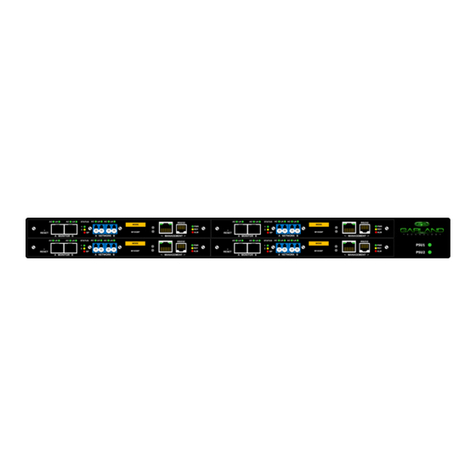
Garland
Garland M10G BP Series installation guide
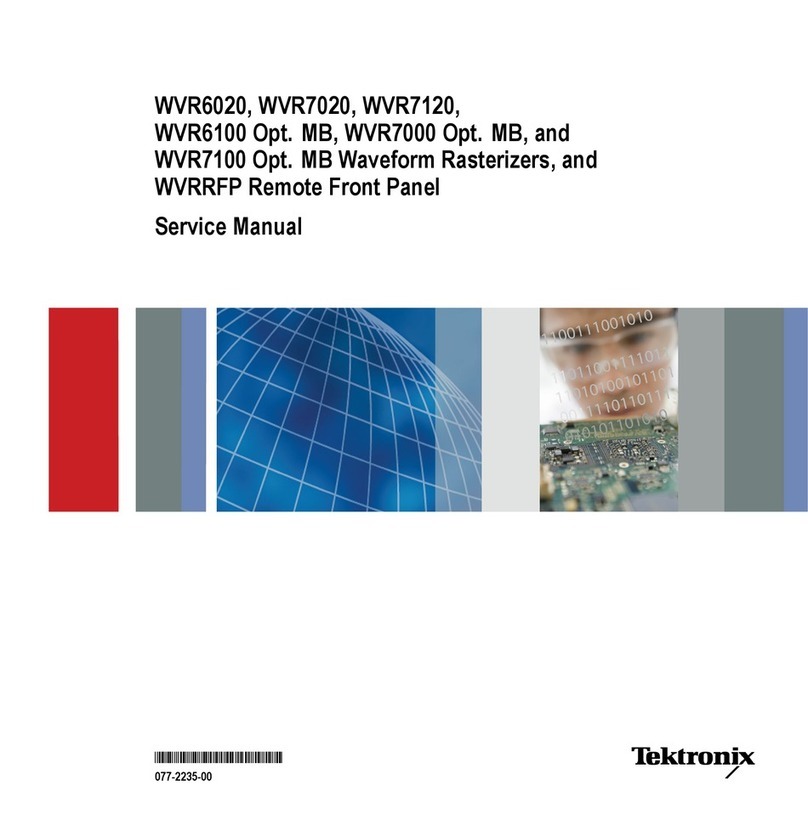
Tektronix
Tektronix WVR6020 Service manual

ESTERS ELEKTRONIK
ESTERS ELEKTRONIK GDR 1530-0000-0000 instruction manual
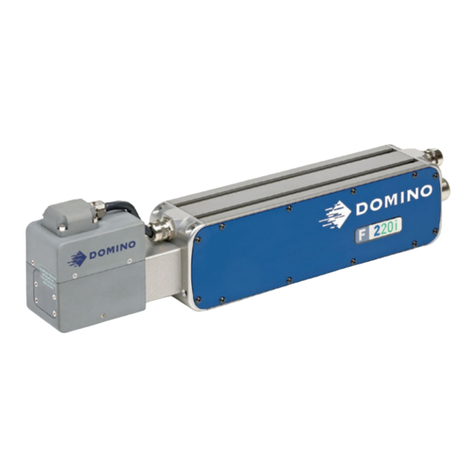
Domino
Domino F Series product manual