WIKA FLC-UFL Series User manual

Operating Instructions
ENUltrasonic Flowmeter FLC-UFL Series
Ultrasonic Flowmeter FLC-UFL

2WIKA Operating Instructions - Ultrasonic Flowmeter FLC-UFL
81500908.01 08/2020 EN
EN
Prior to starting any work, read the operating instructions!
Keep for later use!
Ultrasonic Flowmeter FLC-UFL Series Page 3 - 20
Additional languages available on www.wika.com

3WIKA Operating Instructions - Ultrasonic Flowmeter FLC-UFL
81500908.01 08/2020 EN
EN
Contents
Table of contents
1. Introduction 5
2. About this document 5
2.1 Conventions . . . . . . . . . . . . . . . . . . . . . . . . . . . . . . 5
2.2 Related documents . . . . . . . . . . . . . . . . . . . . . . . . . . . . 5
2.3 Abbreviations . . . . . . . . . . . . . . . . . . . . . . . . . . . . . . 5
3. Important information 6
3.1 Main hazards . . . . . . . . . . . . . . . . . . . . . . . . . . . . . . 6
3.2 Intended use . . . . . . . . . . . . . . . . . . . . . . . . . . . . . . 6
3.3 Identification . . . . . . . . . . . . . . . . . . . . . . . . . . . . . . 6
3.4 Operation in explosive atmospheres . . . . . . . . . . . . . . . . . . . . . . 6
3.5 Restrictions for use . . . . . . . . . . . . . . . . . . . . . . . . . . . . 6
3.6 Cleaning . . . . . . . . . . . . . . . . . . . . . . . . . . . . . . . 6
3.7 User responsibility . . . . . . . . . . . . . . . . . . . . . . . . . . . . 5
3.8 Additional documentation. . . . . . . . . . . . . . . . . . . . . . . . . . 6
4. FLC-UFL Series Product Description 7
4.1 Principle of operation . . . . . . . . . . . . . . . . . . . . . . . . . . . 7
4.2 System components . . . . . . . . . . . . . . . . . . . . . . . . . . . 7
4.2.1 Signal Processing Unit . . . . . . . . . . . . . . . . . . . . . . . . . 7
4.2.2 Flowbody . . . . . . . . . . . . . . . . . . . . . . . . . . . . . . 7
4.2.3 Nameplate. . . . . . . . . . . . . . . . . . . . . . . . . . . . . . 8
4.2.4 Flowbody nameplate . . . . . . . . . . . . . . . . . . . . . . . . . . 8
4.2.5 SPU nameplate . . . . . . . . . . . . . . . . . . . . . . . . . . . . 8
4.2.6 Spare parts and accessories . . . . . . . . . . . . . . . . . . . . . . . 8
4.3 Interface . . . . . . . . . . . . . . . . . . . . . . . . . . . . . . . 8
4.3.1 Ground screw . . . . . . . . . . . . . . . . . . . . . . . . . . . . 8
4.3.2 Main board - Power supply . . . . . . . . . . . . . . . . . . . . . . . . 8
4.3.3 Main board - Frequency out . . . . . . . . . . . . . . . . . . . . . . . . 8
4.3.4 SLOT 1 - RS485 Option board terminals (01-0020 / TIP007) . . . . . . . . . . . . . 9
4.3.5 SLOT 1 - RS485 IO 4..20mA Option board terminals (01-0202 / TIP010). . . . . . . . . 9
4.3.6 SLOT 2 - P/T Option Board (01-0022 / TIP008) . . . . . . . . . . . . . . . . . 9
4.3.7 SLOT 2 - 4..20mA Option board (01-0203 / TIP011). . . . . . . . . . . . . . . . 10
4.4 Front interfaces . . . . . . . . . . . . . . . . . . . . . . . . . . . . . 10
4.5 Display and keypad . . . . . . . . . . . . . . . . . . . . . . . . . . . . 10
4.6 LEDs. . . . . . . . . . . . . . . . . . . . . . . . . . . . . . . . . 10
4.7 USB Service interface and lock switch . . . . . . . . . . . . . . . . . . . . . 10
5. Installation 11
5.1 Introduction . . . . . . . . . . . . . . . . . . . . . . . . . . . . . . 11
5.2 Installation in the pipeline . . . . . . . . . . . . . . . . . . . . . . . . . . 11
5.2.1 Installation configurations . . . . . . . . . . . . . . . . . . . . . . . . 11
5.3 Wiring of the FLC-UFL Series . . . . . . . . . . . . . . . . . . . . . . . . 12
5.3.1 Determining installed option boards . . . . . . . . . . . . . . . . . . . . . 12
5.3.2 Main board terminals . . . . . . . . . . . . . . . . . . . . . . . . . . 12
5.3.3 Slot 1, RS485 Option board terminals (01-0020) . . . . . . . . . . . . . . . . . 12
5.3.4 Slot 1, RS485 IO 4..20 mA Option board terminals (01-0202) . . . . . . . . . . . . 12
5.3.5 Slot 2, P/T Option board terminals (01-0022) . . . . . . . . . . . . . . . . . . 12
5.3.6 Slot 2, 4..20 mA option board (01-0203). . . . . . . . . . . . . . . . . . . . 13
5.3.7 Galvanic isolation . . . . . . . . . . . . . . . . . . . . . . . . . . . 13

4WIKA Operating Instructions - Ultrasonic Flowmeter FLC-UFL
81500908.01 08/2020 EN
EN
Contents
6. Start-up and commissioning 13
6.1 Powering up . . . . . . . . . . . . . . . . . . . . . . . . . . . . . . 13
6.2 Connecting to the USB Service port . . . . . . . . . . . . . . . . . . . . . . 13
6.3 Connecting to a flowcomputer or external device on the RS485 port . . . . . . . . . . . 13
6.4 Commissioning . . . . . . . . . . . . . . . . . . . . . . . . . . . . . 13
7. Operation of the local user interface 14
7.1 LED indicators . . . . . . . . . . . . . . . . . . . . . . . . . . . . . 14
7.2 Keypad . . . . . . . . . . . . . . . . . . . . . . . . . . . . . . . . 14
7.3 Normal operating mode screens . . . . . . . . . . . . . . . . . . . . . . . 14
7.3.1 Contrast Control . . . . . . . . . . . . . . . . . . . . . . . . . . . . . . . . . . . . . . . . . . . . . 14
7.4 Main Menu. . . . . . . . . . . . . . . . . . . . . . . . . . . . . . . 15
7.4.1 Available menu options . . . . . . . . . . . . . . . . . . . . . . . . . . . . . . . . . . . . . . . . . 15
7.4.2 System info . . . . . . . . . . . . . . . . . . . . . . . . . . . . . 15
7.4.3 Display Test . . . . . . . . . . . . . . . . . . . . . . . . . . . . . 15
7.4.4 Diagnostic Display . . . . . . . . . . . . . . . . . . . . . . . . . . . 15
7.4.5 USB Service mode . . . . . . . . . . . . . . . . . . . . . . . . . . . 16
7.4.6 Clearing errors . . . . . . . . . . . . . . . . . . . . . . . . . . . . 16
8. Maintenance 16
8.1 Inspection of measurement and diagnostic data . . . . . . . . . . . . . . . . . . 16
8.1.1 Performances . . . . . . . . . . . . . . . . . . . . . . . . . . . . . . . . . . . . . . . . . . . . . . 16
8.1.2 Velocity of Sound (VoS) . . . . . . . . . . . . . . . . . . . . . . . . . . . . . . . . . . . . . . . . . 16
8.1.3 Gas Velocity (VoG) . . . . . . . . . . . . . . . . . . . . . . . . . . . . . . . . . . . . . . . . . . . . 16
8.1.4 Gain (AGC AB and AGC BA) . . . . . . . . . . . . . . . . . . . . . . . . . . . . . . . . . . . . . . 16
8.1.5 Signal to noise ratio (SNR AB and SNR BA). . . . . . . . . . . . . . . . . . . . . . . . . . . . . . 17
8.1.6 Velocity of gas ratio (VOG ratio) and profile factors . . . . . . . . . . . . . . . . . . . . . . . . . . 17
8.1.7 Velocity of sound ratio (VOS ratio) . . . . . . . . . . . . . . . . . . . . . . . . . . . . . . . . . . . 17
8.1.8 Path Status (PathStatus AB and PathStatus BA) . . . . . . . . . . . . . . . . . . . . . . . . . . . 17
9. Sealing, Shipping & Storage 17
9.1 Sealing . . . . . . . . . . . . . . . . . . . . . . . . . . . . . . . . 17
9.2 Shipping & Storage . . . . . . . . . . . . . . . . . . . . . . . . . . . . 17
Appendix A: Diagnostic Codes 18

5WIKA Operating Instructions - Ultrasonic Flowmeter FLC-UFL
81500908.01 08/2020 EN
EN
1. Introduction / 2. About this document
This manual provides information about the installation,
operation and maintenance of the FLC-UFL series ultrasonic
gas flowmeter. It contains information for correct operation
and maintenance of this product. It also contains important
instructions to prevent accidents and serious damages
before commissioning and during operation. Furthermore,
the information provided ensures trouble free and safe
operation of the equipment. Read and understand this
manual before operating the product. Follow strictly the safety
instructions and warnings.
In the event of questions or need for additional information
regarding specific matters about the FLC-UFL series,
please contact Euromisure via email or telephone.
This instruction manual is based on the latest information at
the time of writing. It is provided subject to changes
and updates.
We reserve the right to change the configuration and/or
construction of our products at any time without obligation
to update previously shipped products.
The warranty provisions stipulated in our Terms and
conditions are applicable to the product.
1. Introduction
Euromisure shall have no obligation if:
■Repair or replacement of equipment or parts has
been required through normal wear and tear, or due to
negligence of the purchaser.
■The equipment, or parts, have been maintained or
repaired by other than an authorized representative of
Euromisure, or have been modified in any manner without
prior express written permission of the manufacturer.
■Non-original parts are used.
■Equipment is used improperly, incorrectly, carelessly
or not in line with its nature and/or purpose.
■Use of this product with unauthorized equipment or
peripherals, including, but not necessarily limited to,
cables, testing equipment, computers, voltage, etc.
Euromisure is not responsible for the incidental or
consequential damages resulting from the breach of any
express or implied warranties, including damage to property,
and to the extent permitted by law, damage for personal
injury.
2. About this document
This manual contains several sections, covering various
aspects of the FLC-UFL series flowmeter.
■Chapter 1: Introduction
■Chapter 2: this chapter
■Chapter 3: Important information
■Chapter 4: FLC-UFL Series Product description
■Chapter 5: Installation
■Chapter 6: Startup and commissioning
■Chapter 7: Operation of the local user interface
■Chapter 8: Maintenance
■Chapter 9: Sealing, Shipping & Storage
■Appendices
2.1 Conventions
The following symbol and indication conventions are used
throughout this manual.
WARNING!
... indicates hazards or unsafe practices that
could result in severe personal injury or death.
ATTENTION!
… indicates potential hazardous or unsafe
operations that could result in minor personal
injury or damage of product or property.
It is also used to indicate operations or practices
that could cause the product to operate in an
unexpected way or provide results outside its
specification.
2.2 Related documents
The last version of the referenced document is leading,
unless otherwise specified.
[1] FLC-UFL Series Safety instructions
Author: Euromisure
Document Code: 81500907 FLC-UFL Series Safety Instructions.
[2] FLC-UFL Series Sealing locations
Author: Euromisure
Document Code: 81500906 FLC-UFL Series Flowmeter Sealing
Locations.
2.3 Abbreviations
Acronym Meaning
ATEX ATmosphère Explosive
CSA Canadian Standards Association
EMC Electromagnetic Compatibility
FM Factory Mutual
IEC International Electrotechnical Commission

6 WIKA Operating Instructions - Ultrasonic Flowmeter FLC-UFL
81500908.01 08/2020 EN
EN
2. About this document / 3. Important information
Acronym Meaning
IECEx International Electrotechnical Commission
certification scheme for Explosive atmospheres
IS Intrinsic Safety
ISO International Organization for Standardization
LCD Liquid Crystal Display
LVD Low Voltage Directive
OIML Organisation Internationale de Métrologie
Légale
PCBA Printed Circuit Board Assembly
PED Pressure Equipment Directive
SPU Signal Processing Unit
USM Ultrasonic Flowmeter
3. Important information
3.1 Main hazards
WARNING!
Pressurized flammable gas flows through
the Flowbody of the FLC-UFL series ultrasonic
gas flowmeter. Do not remove any transducers
or parts from the flowbody whilst the flowmeter
is under pressure. Flammable gas can escape
and parts may blow out.
3.2 Intended use
The FLS-UFL series ultrasonic gas flowmeter primary use
is to measure the volume flow rate and gas velocity of gases
in pipelines.
Optionally the FLC-UFL series can convert the volume
flow at measuring conditions to base conditions as well as
registering data on meter readings, diagnostics and other
data.
3.3 Identification
Each FLC-UFL series flowmeter has two nameplates for
identification, one on the SPU and one on the flowbody.
Refer to chapter 4.2.3 for detailed information about the
nameplates and identification.
3.4 Operation in explosive atmospheres
The FLC-UFL series flowmeters are suitable for use in
potentially explosive atmospheres. Refer to the Safety
instructions [1] (81500907 FLC-UFL Series Safety
Instructions) for detailed information about this.
■ATEX Ex ia IIC T4 Gb
■IECEx Ex ia IIC T4 Gb
3.5 Restrictions for use
The FLC-UFL series flowmeters are suitable for use
in pressurized lines within the design conditions specified
on the flowmeter nameplate.
3.6 Cleaning
Only clean the FLC-UFL series ultrasonic flowmeter with a
damp cloth. Do not use solvents for cleaning.
3.7 User responsibility
The user should read and understand the operating
instructions prior to putting the FLC-UFL series ultrasonic
flowmeter in use. All safety information should be observed.
In case of doubt always contact Euromisure.
3.8 Additional documentation
Additional documentation is delivered with the product.
This contains specific set-up data for the individual flowmeter.
Depending on the configuration, the following documentation
is delivered with the meter:
■
Certificate of conformity / EX certificates
■
Safety instructions
■Material certificates
■Inspection certificate:
▶Meter configuration sheet
▶Factory acceptance test report
Furthermore, product information such as this manual can be
downloaded from the website www.wika.com.

7WIKA Operating Instructions - Ultrasonic Flowmeter FLC-UFL
81500908.01 08/2020 EN
EN
4. FLC-UFL Series description
4. FLC-UFL Series Product description
4.1 Principle of operation
The FLC-UFL series ultrasonic gas flowmeters operate according to the transit time difference measurement.
Measured ultrasonic signal transit times tup and tdn are defined by the sound and gas velocity. Gas velocity V is proportional
to the difference between the signal transit times. Changes in the sound velocity caused by pressure or temperature
fluctuations do not affect the calculated gas velocity with this measurement method.The FLC-UFL series ultrasonic gas
flowmeter calculates the volume flow rate based on the gas velocity and the Flowbody internal diameter.
4.2 System components
4.2.1 Signal Process Unit
The Signal Processing Unit (SPU) consists of a mainboard
that contains all the electronic circuits for operation of the
unit. In addition to the mainboard, two additional boards
can be placed for extra functionality such as pressure and
temperature sensor interfaces and additional Input/Output
interfaces.The mainboard interfaces to the transducers
and controls the complete measuring process. All interfaces
are intrinsically safe, except the USB service port.
4.2.2 Flowbody
The Flowbody is used to install the FLC-UFL series
flowmeter in the pipeline. It is available in various pipe sizes,
pressure ratings and flange types.
2
1
3
4
5
1SPU
2SPU nameplate location
3Meterbody nameplate
4Eyebolt
5Meterbody
The FLC-UFL series comprises of a Signal Processing Unit
(SPU), Flowbody with transducers, nameplate with essential
information and eyebolts for lifting purposes.

8 WIKA Operating Instructions - Ultrasonic Flowmeter FLC-UFL
81500908.01 08/2020 EN
EN
4. FLC-UFL Series description
4.2.3 Nameplate
Nameplates and labels are fitted on the FLC-UFL Series
flowmeter for identification and providing details on the
specific product as well as safety related information.
Together with the safety instructions and this manual,
it specifies how to use the product and how it is designed
and certified.
The main nameplate is fitted on the Flowbody and provides
information on mechanical design conditions as well as flow
related information such as meter factor and range.
The meter’s serial number is also provided on this nameplate.
The nameplate on the SPU provides the relevant electrical
and hazardous area approval details according to ATEX,
IECEx.
The electronic individual serial number is provided on this
nameplate. Refer to the Safety instructions for an example
of this nameplate.
4.2.4 Flowbody nameplate
The Flowbody nameplate contains information about:
■Company name and address
■Type of Ultrasonic flowmeter
■Model identification
■Flow range information
■Pressure and temperature range
■Mechanical design parameters (design code, design
pressure and temperature)
■Sizing and weight
■Serial numbers
■Year-Month
■Warning: Read instruction manual before operating
device.
4.2.5 SPU nameplate
The SPU nameplate contains information about:
■Company name and address
■Type of Ultrasonic flowmeter Electronics
■Hazardous area approval
■Model identification
■SPU Serial Number
■SPU Power Requirements
■Year of manufacture
■Substitution of components may impair intrinsic safety
■Install per drawing 81500909.
4.2.6 Spare parts and accessories
Please contact Euromisure for spare parts and accessories.
1Main Board Terminal Blocks
2Option Board Terminal Blocks
3Ground Screw
Main Board Terminal Blocks
1
2
3
4.3 Interfaces
The FLC-UFL series flowmeter has several electrical
interfaces.This chapter describes their function, operating
parameters and intrinsic safety relevant information.
4.3.1 Ground screw
A ground screw is provided to connect the FLC-UFL series
flowmeter to ground / earth.
4.3.2 Main board - Power supply
The FLC-UFL series flowmeter requires an external
intrinsically safe power supply.
Signal Function
PWR - Power supply
PWR +
WARNING!
The power supply interfaces of the FLC-UFL
series flowmeter are reverse polarity protected
up to 250 mA max. Always connect via a suited
intrinsically safe isolator or barrier.
Refer to Control drawing 81500909 for detailed
information.
4.3.3 Main board - Frequency out
A frequency out / pulse output is available on the mainboard
(base configuration).The main purpose of this output is
to provide pulses proportional to the volume flowing through
the pipeline.The number of pulses per unit volume (m3or
cubic feet) is printed on the nameplate.
Signal Function
D0_B Frequency output -
D0_A Frequency output +

9WIKA Operating Instructions - Ultrasonic Flowmeter FLC-UFL
81500908.01 08/2020 EN
EN
4. FLC-UFL Series description
4.3.4 SLOT 1 - RS485 Option board terminals (01-0020
/ TIP007)
Optionally the FLC-UFL series flowmeter can be fitted with an
I/O option board, extending the functionality of the system.The
option board requires a separate intrinsically safe power supply.
4.3.5 SLOT 1 - RS485 IO 4..20 mA Option board
terminals (01-0202 / TIP010)
When the FLC-UFL series flowmeter is fitted with the RS485
IO 4..20 mA option board, the option board requires a separate
intrinsically safe power supply.The board’s supply at the same
time will function as a 4..20 mA output.
Signal Function
PWR1 + Option board power supply
PWR1 - Option board power supply
D1_B RS485 B
D1_A RS485 A
D2_B Digital output -
D2_A Digital output +
D3_B Digital output -
D3_A Digital output +
Signal Function
PWR1 + Option board power supply / 4..20 mA loop
PWR1 - Option board power supply / 4..20 mA loop
D1_B RS485 B
D1_A RS485 A
D2_B Digital output -
D2_A Digital output +
D3_B Digital output -
D3_A Digital output +
4.3.6 SLOT 2 - P/T Option Board (01-0022 / TIP008)
In addition, the FLC-UFL series flowmeter can be fitted with
an optional Pressure / Temperature board, extending the
functionality of the system with pressure and temperature
measurement capabilities.This enables the FLC-UFL series
flowmeter to calculate base volume using PTZ conversion.
A pressure and temperature sensor are then supplied by
Euromisure. Refer to the safety instructions for information
on compatible sensors.When wiring the sensors to the
FLC-UFL always use shielded cable and ensure the shield is
connected to ground.
Pressure sensor wiring
Temperature sensor wiring
WARNING!
ONLY CONNECT APPROVED PRESSURE AND
TEMPERATURE SENSORS.
MAXIMUM CABLE LENGTH TO THE SENSORS
MAY NOT EXCEED 2 m (6.7 ft).
ATTENTION!
The interface of the PT option board is
configured for 4 wire PT100 sensors and voltage
mode pressure sensors.

10 WIKA Operating Instructions - Ultrasonic Flowmeter FLC-UFL
81500908.01 08/2020 EN
EN
4. FLC-UFL Series description
4.3.7 SLOT 2 - 4..20 mA Option board (01-0203 / TIP011)
When equipped with this option board, a passive (externally
powered) mA output is available.The output is software
configurable for any parameter required, however normally
it is used for flowrate, gas velocity etc.
Using the PC tool, it can be configured and calibrated.
Figure 4.3.7: Display, keypad, USB and switch
4.4 Front interfaces
1Display
2USB connector
3Keys
4Lock switch
1
2
3
4
4.5 Display and keypad
The front of the FLC-UFL series electronics is equipped with
a graphical 128x128 dot matrix LCD graphic display.
Four navigation keys are located at the corners of the display
for operation of the local user interface.
4.6 LEDs
Two LEDs are provided on the front panel.Their function is
explained in detail in chapter 7.
4.7 USB Service interface and lock switch
A mini USB connector is present for connection of a laptop
on the right side of the display.
ATTENTION!
This interface is not intrinsically safe and
therefore powered by the USB host (laptop
or computer). It may be used in a safe area only
or after taking suitable precautions such as gas
detection. Refer to the Safety instructions [1]
for further details.
The parameter lock switch is located below the USB
connector and provides a way to lock all relevant parameters.
This switch can be protected with a tamper proof sticker.
Refer to chapter 9 (Sealing) for more details on the lock
switch.
Note: the sticker shall also covers one of the display bracket
screws.
LED Function
Green LED Power indication
Red LED Status / Error indication

11WIKA Operating Instructions - Ultrasonic Flowmeter FLC-UFL
81500908.01 08/2020 EN
EN
5. Installation
5. Installation
5.1 Introduction
It is very important to check the shipment of your ultrasonic
flowmeter equipment. By means of a visual inspection
of surfaces, paint, flange sealing faces and electronics
housing should be performed. In case of damage, contact
Euromisure immediately. In addition verify all the necessary
documentation is available as well:
■Safety instructions [1]
■Installation, operation and maintenance manual (this
document).
In addition to this additional documentation may be required
based on project specifications. In the event documentation
is missing contact Euromisure or your local representative
immediately.
5.2.1 Installation configurations
The recommended installation configurations are shown in the below figure. Refer to your specific type approval for approved
installation configurations OIMLR137 and MID 2014/32/EU.
5.2 Installation in the pipeline
The FLC-UFL series ultrasonic flowmeter is shipped in a
wooden crate.To open the crate remove the top panel nails
or screws and disassemble the box. Remove the transport
fixtures and then move the flowmeter (using the lifting lugs
provided on the flow cell) to the installation site. Install the
meter according to end-user’s company regulations and
applicable local and national requirements. To ensure optimal
performance of the flowmeter, comply with the up- and
downstream spool requirements specified for your particular
application.
WARNING!
To avoid possible strain, ensure your lifting
equipment is suitable for the weight of the
FLC-UFL series flowmeter. Always use the
eyebolts provided on the flowbody and make
sure to use approved lifting equipment and
the equipment shows no damage or wear.
1Configuration 1 - Recommended configuration without
flow conditioner
2Configuration 2 - Recommended configuration with flow
conditioner
3Configuration 3 - Conservative configuration with flow
conditioner
1
2
3
For bi-directional flow:
■The upstream piping spools and flow conditioner as applicable from configurations 1, 2 and 3 can be used on both ends of
the metering package.
■Any thermowell should be positioned 3 – 5 diameters away from meter flanges.
ATTENTION!
The installation orientation of the FLC-UFL series flowmeter is expected to be horizontal. Always consult with
Euromisure for vertical installation requirements.

12 WIKA Operating Instructions - Ultrasonic Flowmeter FLC-UFL
81500908.01 08/2020 EN
EN
5. Installation
5.3 Wiring of the FLC-UFL series
This chapter provides information for correct wiring of the
FLC-UFL series flowmeter. The electronics enclosure is
provided with up to four cable gland entries with metric
(M20x1.5) or imperial (1/2” NPT) thread. Suitable shielded
cables must be used (for signal and communication cables
the use of twisted pair cables is recommended) whereby
the cables are protected from mechanical damages as
well as electrical interference. In addition, ensure length,
diameter, core are suitable for the length required in the field.
As a minimum 0.75 mm² core cross sectional area should
be used. All terminal connections use the Phoenix contact
MK3DSH series terminal blocks, suitable for wires with a
core cross sectional area up to 2.5 mm².
ATTENTION!
For a reliable connection always use insulated
wire end terminals compatible with the cable
core cross sectional area.
WARNING!
REFER TO CONTROL DRAWING 81500909
FOR THE INTRINSIC SAFETY PARAMETERS.
5.3.1 Determining installed option boards
In order to determine which option boards are installed
in your FLC-UFL series flowmeter, locate the FLC-UFL
Electronics model number on the nameplate of the SPU.
Using the table on the control drawing (drawing 81500909)
determine which option boards are installed.
5.3.2 Main board terminals
Signal Function Operating
parameters
PWR -
Power supply
Rated input voltage
12...29 VDC (After safety
barrier)
PWR +
D0_B Frequency output - 0...5 kHz Passive open
drain, not electrically
isolated from system
ground
D0_A Frequency output +
WARNING!
The power supply interfaces of the FLC-UFL
series flowmeter are reverse polarity protected
up to 250 mA max. Always connect via a suited
intrinsically safe isolator or barrier.
Refer to Control drawing 81500909 for detailed
information.
5.3.3 Slot 1, RS485 Option board terminals (01-0020)
5.3.4 Slot 1, RS485 IO 4..20 mA Option board terminals
(01-0202)
5.3.5 Slot 2, P/T Option board terminals (01-0022)
Signal Function Operating
parameters
PWR1 + Option board power
supply Power supply for the
I/O option board (10-29
VDC) (After safety
barrier)
PWR1 - Option board power
supply
D1_B RS485 B Differential RS485 two
wire communications
port, galvanically
isolated
D1_A RS485 A
D2_B Digital output - Passive, optically
isolated open collector
D2_A Digital output +
D3_B Digital output - Passive, optically
isolated open collector
D3_A Digital output +
Signal Function Operating
parameters
PWR1 + 4..20 mA Loop / power
supply Power supply for the I/O
option board and the
4..20 mA loop. (10-29
VDC, after safety barrier)
PWR1 - 4..20 mA Loop / Loop
power supply
D1_B RS485 B Differential RS485 two
wire communications
port, galvanically
isolated
D1_A RS485 A
D2_B Digital output - Passive, optically
isolated open collector
D2_A Digital output +
D3_B Digital output - Passive, optically
isolated open collector
D3_A Digital output +
Signal Function Operating
parameters
PRESS1 Bridge + Connections to the
resistive bridge type
pressure sensor (factory
default = voltage mode
sensor). Refer to Safety
instructions for approved
pressure sensors, or
contact Euromisure for
more information
PRESS2 Signal +
PRESS3 Signal -
PRESS4 Bridge -
TEMP1 Supply + Connections to the RTD
sensor (factory default
= 4 wire PT100). Refer
to Safety instructions
for approved pressure
sensors, or contact
Euromisure for more
information
TEMP2 Signal +
TEMP3 Signal -
TEMP4 Supply -

13WIKA Operating Instructions - Ultrasonic Flowmeter FLC-UFL
81500908.01 08/2020 EN
EN
5.3.6 Slot 2, 4..20 mA option board (01-0203)
Signal Function Operating
parameters
LPWR2+ Loop power supply
LPWR2- Loop power supply
5.3.7 Galvanic isolation
In case galvanic isolation is required, the use of an external
isolator on frequency output D0 is required.
5. Installation / 6. Start-up and commissioning
6. Start-up and commissioning
6.1 Powering up
After the SPU has been wired and powered up it is advisable
to read out a complete list of parameters. In case of a flow
calibrated meter, it is recommended to verify the parameters
as found with the calibration parameters.
The parameters can be read with the dedicated software tool
(consult Euromisure to obtain tool).
A serial connection can be made via the USB interface.
WARNING!
When connecting a PC or laptop in the
hazardous area, ensure the rules and
regulations to work with non EX equipment
are met.
A flow calibrated meter should have the parameter lock
switch closed and tamper proof sealing sticker in place.
Make sure this is in place. Refer to chapter 9 for more details
about sealing.
6.2 Connecting to the USB Service port
To connect to the FLC-UFL series via the USB Service port
it may be necessary to put the FLC-UFL series flowmeter
in USB Service mode. When the communication mode is
set to the RS485 port, the USB Service mode enables to
temporarily interface via the USB port. Refer to chapter 7.4
for details how to enable the USB service mode.
ATTENTION!
When USB Service mode is enabled it will
temporarily disable the RS485 option board.
When there is no activity for 60 seconds on the
USB port the FLC-UFL series resumes normal
operation again.
The default USB communication port settings are:
Baudrate 115400
Parity None
Databits 8
Stopbits 1
Modbus address 1
6.3 Connecting to a flowcomputer or external device on
the RS485 port
When fitted with an option board for RS485 communications
the FLC-UFL series flowmeter can be connected to a
flowcomputer or external device using the MODBUS RTU
protocol.The default communication protocol and serial port
settings are provided in below:
The Modbus address map can be provided on request.
The FLC-UFL series flowmeter has a built in 120 ohm
termination resistor in case the RS485 network needs to be
terminated at this position. The switch shown in the following
figure can be used for this.
6.4 Commissioning
When possible verify operation of the flowmeter at (near)
zero flow at known gas composition. Zero flow readings and
diagnostics per path should be recorded and assessed. After
this zero flow check, start the gas flow and monitor per path
readings and diagnostics for proper operation of the device.
Ensure that the frequency signal provided by the meter
match the volume flow reading on the local LCD.
It is recommended to log meter readings and diagnostics
using the dedicated software tool during startup conditions.
Baudrate 38400
Parity None
Databits 8
Stopbits 1
Modbus address 1

14 WIKA Operating Instructions - Ultrasonic Flowmeter FLC-UFL
81500908.01 08/2020 EN
EN
7. Operation of the local user interface
7. Operation of the local user interface
7.1 LED indicators
The FLC-UFL series flowmeter has two LED indicators,
located underneath the LC Display.
Their function is described in following tables.
7.2 Keypad
The keypad has four function keys which correspond with a
function shown in the corners of the LCD. Each key will have
a function depending on the operating mode of the interface.
Power LED - GREEN
LED status Interval Description
Off -- Power off
Green, flashing 2 sec Power on, system running
Status LED - RED
LED status Interval Description
Off -- Status OK
Red, flashing 1 sec Warning
Red, flashing 0.5 sec Error
Red, flashing 2 sec
Status OK,
unacknowledged
transient Error present
7.3 Normal operating mode screens
During normal operation the FLC-UFL series flowmeter
provide the essential information on areas on the LCD.
The following parameters can be displayed on both the upper
and lower section of the LCD. Different parameters can be
selected Using the keys on the keypad.
The upper display is “static” - that is only the selected
parameter is displayed.The parameter may be changed
manually using the ◀ <left> and ▶ <right> scroll keys.
The lower display will automatically scroll through the
remaining parameters. The full list of parameters is shown
below.
The following parameters can be viewed.
■Totalized volume forward (TotalFwd)
■Totalized volume reverse (TotalRev)
■Totalized volume forward in alarm conditions
(TotalFwdAlrm)
■Totalized volume reverse in alarm conditions
(TotalRevAlrm)
■Volumetric flowrate (Qline)
■Velocity of Gas (VoGCor)
■Velocity of Sound (VoSAvg)
■Meter status (MeasStatus). For a list of status codes refer
to Appendix A.
7.3.1 Contrast Control
The bottom two keys are used for contrast control. Use
the <-contrast> and <+contrast> keys to adjust the
contrast of the LCD.
2
13
4
1KEY 1
2KEY 2
3KEY 3
4KEY 4

15WIKA Operating Instructions - Ultrasonic Flowmeter FLC-UFL
81500908.01 08/2020 EN
EN
7.4 Main Menu
Pressing the upper left key while in normal operating
mode for 3 to 5 seconds will bring up the main menu of the
FLC-UFL series flowmeter.
The four function keys have now changed into <up>,
<down>, Escape <ESC> and Enter <ENT>.
Using the up and down arrow keys a menu option can be
selected, pressing <ENT> will show the highlighted menu
or function. To go back one step, press <ESC>.
7.4.1 Available menu options
■1 - System Info
■2 - Display Test
■3 - Diagnostic Menus
■4 - Clear error
■5 - USB Service mode (unavailable in “console” mode)
7.4.2 System Info
The System Info Menu provides information about the FLC-UFL
Meter software and hardware. After a few seconds the display
will exit to the Operating Mode.
7.4.3 Display Test
When Display Test is highlighted and selected using
the <down>, and then <ENT> a pattern will be
scanned across the display to test all pixels.
After the test the display will revert to the Operation Mode.
7.4.4 Diagnostic Display
When Diagnostic Display is highlighted and selected,
the following screen will be displayed.
This screen shows diagnostic information for all enabled paths.
Scroll to the next diagnostic value using the ▶ <right> scroll
key.
The following diagnostic values may be displayed using
the ◀ <left> and ▶ <right> scroll keys:
■Performance (DemodPerf)
■Velocity of Sound (VOSRaw)
■Gas Velocity (VoG)
■Gain AB (AGC AB)
■Gain BA (AGC BA)
■Signal to noise ratio AB (SNR AB)
■Signal to noise ratio AB (SNR BA)
■Velocity of gas ratios (VoG ratio)
■Velocity of sound ratio (VoS ratio)
■Path Status AB (Status AB)
■Path Status BA (Status BA)
The diagnostic values and interpretation is discussed further
in section 8: Maintenance.
Pressing <ESC> will return to the normal operating
display.
7. Operation of the local user interface

16 WIKA Operating Instructions - Ultrasonic Flowmeter FLC-UFL
81500908.01 08/2020 EN
EN
7. Operation of the local user interface / 8. Maintenance
7.4.5 USB Service mode
When USB Serv. Mode is highlighted and selected using
the <down> and then <ENT>, the FLC-UFL series
flowmeter will enter the USB service mode, enabling
communications via the USB port.
A message “USB Service Mode” will be shown on the
display.
When pressing <ENT> again the FLC-UFL series
flowmeter will revert to the normal operation mode.
The dedicated software can be used to communicate via
the USB port when in USB service mode.
7.4.6 Clearing errors
In the event an alarm or warning condition is active,
the diagnostic code (refer to appendix A) is shown on the
lower part of the LCD display until it is acknowledged by
the user. Acknowledging alarms or warnings can be done via
the main menu option 4 – Clear Alarms. If the error condition
is still active the alarm or warning cannot be cleared.
8. Maintenance
The FLC-UFL series ultrasonic flowmeter contains no moving
parts.The sensors and electronics are virtually maintenance
free, however periodic inspection is recommended at regular
intervals.
By collecting a short log file of measurement and diagnostic
data at known and repeatable conditions the meter’s health
status can be observed.
8.1 Inspection of measurement and diagnostic data
By comparing diagnostic data with previously collected
data a good indication of the flowmeter’s condition can
be observed. Below chapters outline the most significant
diagnostic indicators.
The display of diagnostic data is described in section 6.4.3
or may downloaded from the USB port or RS485 optional I/O
port using a Modbus protocol.
For the Modbus map or the dedicated software PC tool
to download diagnostic and flow information contact
Euromisure.
8.1.1 Performance
This diagnostic indicates the percentage of accepted
ultrasonic signals per path.The lower limit is set to 20% by
default. At high flows or very turbulent flows, some rejection
of ultrasonic signals may occur.The performance indicator
is available for each path.
8.1.2 Velocity of Sound (VoS)
The FLC-UFL series flowmeter calculates the average
velocity of sound (VoS) based on the individual measuring
paths.The average VoS is simply the average of the paths.
Individual VoS for each path is also provided. Under normal
conditions the individual path velocities should be reading
very close.When possible the theoretical velocity of sound
using AGA-10 calculations based on temperature, pressure
and gas composition may be compared to the measured
average VoS.
8.1.3 Gas Velocity (VoG)
When possible the meter can be isolated from flowing
conditions (using block valves). In this condition the meter
should read less than 0.01 m/s.This is however extremely
difficult to check due to natural convection inside the pipe
and Flowbody as a result of slight temperature differences,
causing the gas to circulate in the blocked pipe section.
8.1.4 Gain (AGC AB and AGC BA)
For each transducer the required gain in the receiver is

17WIKA Operating Instructions - Ultrasonic Flowmeter FLC-UFL
81500908.01 08/2020 EN
EN
controlled. Gain values should be in the normal operating
range for all transducers.
Gain values depend on gas pressure, composition and
velocity, therefore, gain values may differ between events.
Gain Condition
>70 Very weak or no signal
10 - 70 Good
< 10 Very strong or saturated signal
8.1.5 Signal to noise ratio (SNR AB and SNR BA)
The SNR is calculated in dB for each received signal
transducer. SNR values depend on gas pressure,
composition and velocity.
The below table provide information on Signal to noise ratio
conditions.
SNR Condition
>50 Very good
25 - 50 Good
10 - 25 Poor – fair
<10 Bad
8. Maintenance / 9. Sealing, Shipping & Storage
8.1.6 Velocity of gas ratio (VOG ratio) and profile factors
The velocity of gas ratio is calculated between paths and
provides a good indicator of the flow profile in the meter
(determined by upstream piping). Profile factors are
calculated from the velocity of gas ratios. Profile factors are
an easy way to “understand” the flow profile in the flowmeter.
8.1.7 Velocity of sound ratio (VOS ratio)
The velocity of sound ratio is a good indicator of problems,
either in the process or in the FLC-UFL series signal
detection. During normal condition the ratios should be very
close to 1.0.
8.1.8 Path Status (PathStatus AB and PathStatus BA)
The Path Status diagnostic values provide a more detailed
indication of the health of each path in each direction
of transmission using an 8 digit number. A zero value
(0x00000000) indicates that all parameters are within limits
and no errors are present.
The error codes are tabulated in Appendix A.
9. Sealing, Shipping & Storage
9.1 Sealing
For sealing locations refer to document [2] FLC-UFL Series
Flowmeter Sealing Locations.
9.2 Shipping & Storage
Use suitable means for transportation, loading and unloading
of the packed FLC-UFL Series flowmeter. The packing is not
suitable for the use of strap belts and lifting by a crane.
If the flowmeter has been removed from its packaging, lifting
and moving may only be carried out using suitable, properly
fitted lifting lugs.
Take care that the meter will be installed on a vibration
free location. Continuous vibration or shocks may have an
adverse effect on the construction of the flow meter.
The dimensions and weight of the package depend on the
type and size of the ultrasonic gas flow meter and are to be
specified on the packing list.
If the FLC-UFL series flowmeter needs to be stored for a
certain period of time before installation, the following storage
conditions do apply:
■Never stack the (packaged) flowmeters.
■It is recommended to use a corrosion preventative coating
(oil, WD40, tectyl) on all bare metal parts of the flowcell
(e.g. inside, flange surfaces,...).
■Be aware to remove the corrosion preventative coating
prior to putting the flowmeter in service.
■Storage temperature: -30 °C to 60 °C.
■Storage relative humidity: 5 – 95% RH, non-condensing
■Use moisture absorbing bags (silica gel) inside the SPU to
protect the electronics from moisture.
■Inspect the stored flowmeter on a regular basis to ensure
no condensation is present which may cause corrosion
and /or damage to the electronics.
■When other piping components and/or flow conditioners
are provided with the meter, also apply a corrosion
preventative coating to any uncoated surfaces.
ATTENTION! - LONG TERM STORAGE
When the meter is stored for longer time, ensure
that the meter is stored in a sheltered condition
with a temperature between 0 °C and + 60 °C.
The inside of the Flowbody should be protected
from corrosion using a suitable corrosion
preventive coating.

18 WIKA Operating Instructions - Ultrasonic Flowmeter FLC-UFL
81500908.01 08/2020 EN
EN
Appendix A: Diagnostic Codes
Measurement Status / TransientErr
Diagnostic Status Bits Set
both
AB/BA
Affects WARNING ERROR
Hex Value Decimal
Value
Enum / Short Description Long Description
MeasStatus
Values set for Meter Values
0x00000000 0No_error No Error
0x00000001 1Warning Measurement Warning X
0x00000002 2Error Measurement Error X
0x00000004 4CalSwitch_unlock Calibration lock open X
0x00000008 8System_error Inconsistency in system
parameters
X
0x00000010 16 FPGA_error Inconsistency in FPGA
parameters
X
0x00000020 32 Flash_mem_error Error accessing internal flash
memory
X
0x00000040 64 RTCBattFail RTC clock battery failure X
0x00000080 128 Ispare Not enough power X
0x00000100 256 Firmware_error Firmware checksum error X
0x00000200 512 Factory_defaults Started from factory defaults X
0x00000400 1024 ParamCRC_Error Parameter checksum error X
0x00000800 2048 Optionboard_timeout Option board does not respond X
0x00001000 4096 TestMode Meter is in test mode X
0x00002000 8192 DigOutOverflow LF pulse output overflow X
0x00004000 16384 TotalStorageInitError Totalizer storage error - no valid
flash record found on startup
X
0x00008000 32768 TotalPersistError Totalizer persistence error -
totalizer storage verification failed
X
0x00010000 65536 PTError PTZ module error X
PTZStatus
Diagnostic Status Bits Set both
AB/BA
Affects WARNING ERROR
Hex Value Decimal
Value
Enum / Short Description Long Description
PTZStatus
0x00000000 0 PTStatusGood PTZ No errors
0x00000001 1PTStatusWarning PTZ Warning X
0x00000002 2PTStatusError PTZ Error X
0x00000004 4Spare Spare
0x00000008 8Spare Spare
0x00000010 16 TemperatureOutofRangeError Temperature sensor error or value
out of range
X
0x00000020 32 PressureOutofRangeError Pressure sensor error or value out
of range
X
0x00000040 64 PTReadTimeOutError No response from PT option
board
X
0x00000080 128 PTZInputsOutofRangeError PTZ inputs out of range X

19WIKA Operating Instructions - Ultrasonic Flowmeter FLC-UFL
81500908.01 08/2020 EN
EN
Appendix A: Diagnostic Codes
Path / Transducer diagnostics
Diagnostic Status Bits Set
both
AB/BA
Affects WARNING ERROR
Hex Value Decimal
Value
Enum / Short Description Long Description
Path/ Transducer Status
Values set per transducer AB or BA
0x00000000 0No error No Error
0x00000001 1Performance_bad Performance too low
0x00000002 2No_Correlation MaxAmp and/or MinAmp below
low limit
YES
0x00000004 4SNR_Range Signal to noise ratio too low YES
0x00000008 8Signal_overflow Signal too large YES
0x00000010 16 MinMaxZoom_Range Min and Max indices of raw signal
too far away
NO
0x00000020 32 Envelope_slope_range Signal signature out of range YES
0x00000040 64 Envelope_slope_dev % deviation filter on Signal
signature
YES
0x00000080 128 DetPoint_Range Zero Cross out of range YES
0x00000100 256 ZC_DETPT_Filter Detectionpoint corrected by
ZC_DETPT_filter
NO
0x00000200 512 DeltaT_error ABS((DetPTCorrBA -
DetPtCorrAB) - (ZeroCrossBA
- ZeroCrossAB))
YES
0x00000400 1024 DemodTransittimeAccel Transittime accelleration too high
(cycle skip)
YES
0x00000800 2048 EnvPeakSkip Envelope peak skip (packet) NO
0x00001000 4096 SPARE
0x00002000 8192 SPARE
0x00004000 16348 SPARE
0x00008000 32786 SPARE
0x00010000 65536 VOSRange Velocity of sound out of range YES X
0x00020000 131072 VOGRange Velocity of gas out of range YES X
0x00040000 262144 WetGasVOS Wetgas filter triggered substitution
based on VOS
YES X
0x00080000 524288 WetGasVOG Wetgas filter triggered substitution
based on VOG
YES X
0x00100000 1048576 Substitution Path being substituted based on
historical data
YES X
0x00200000 2097152 SPARE

WIKA Operating Instructions - Ultrasonic Flowmeter FLC-UFL
81500908.01 08/2020 EN
Euromisure s.a.s di WIKA Italia S.r.l
via Borghisani 4
26035 Pieve San Giacomo (CR) - Italy
Telefon (+39) 0375 6404
Telefax (+39) 0372 640490
E-Mail salesow[email protected]
www.wika.com
20
For WIKA branches worldwide, visit our website www.wika.com.
Ultrasonic Flowmeter FLC-UFL Series
Table of contents
Other WIKA Measuring Instrument manuals
Popular Measuring Instrument manuals by other brands
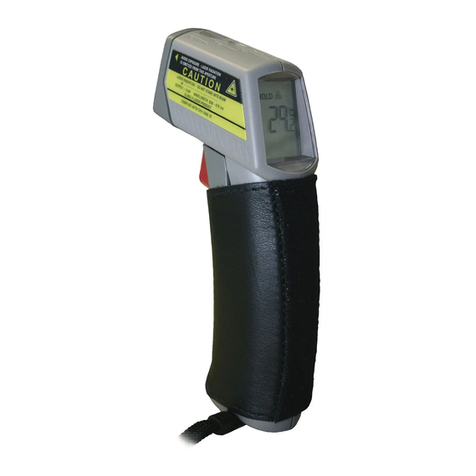
Ecom
Ecom Ex-MP4 a operating instructions
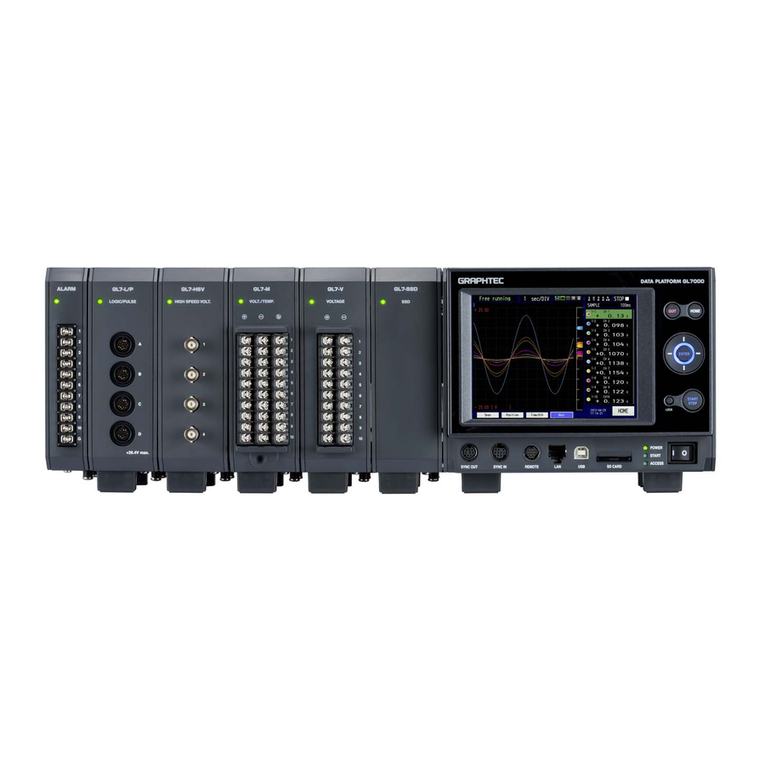
GRAPHTEC
GRAPHTEC Data Platform GL7000 Study guide

Omntec
Omntec PROTEUS OEL8000III Series manual
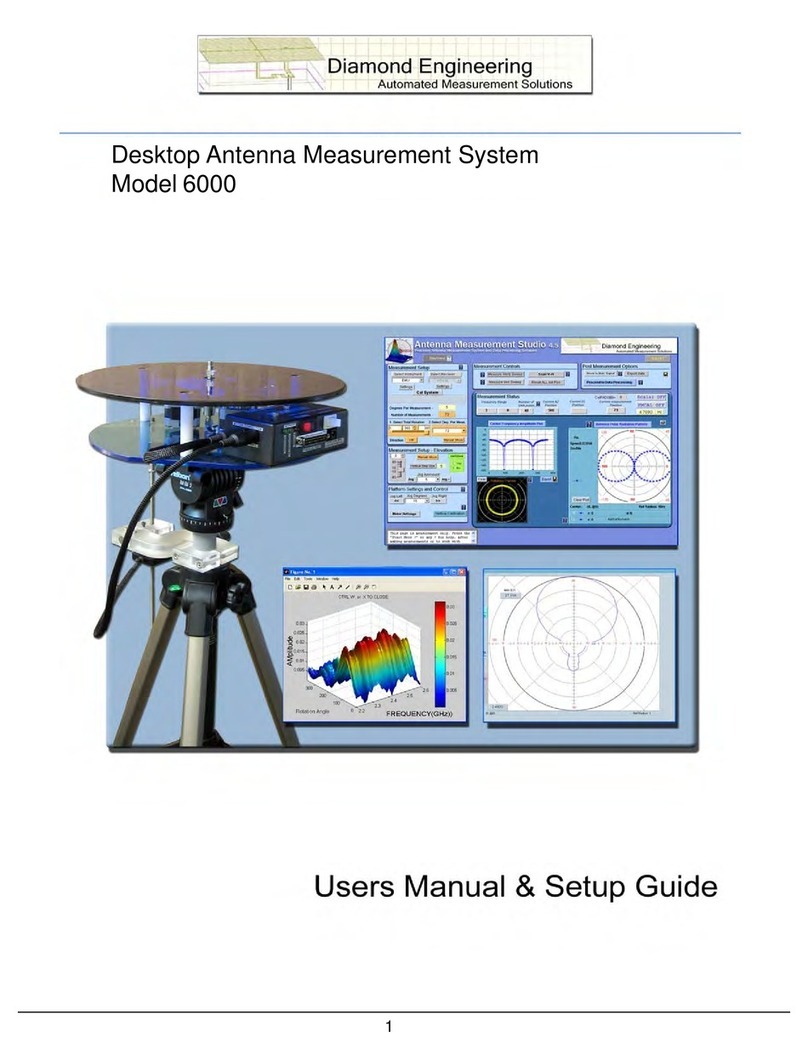
Diamond Engineering
Diamond Engineering Officejet 6000 User manual & setup guide
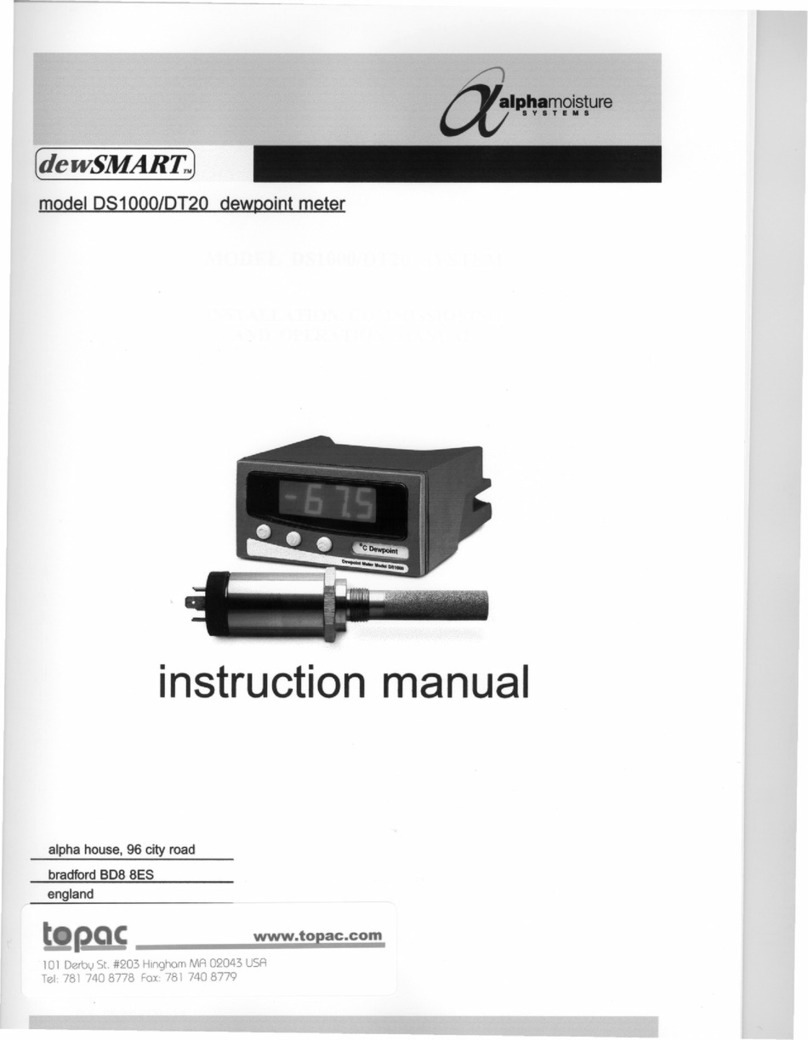
Alpha Moisture Systems
Alpha Moisture Systems dewSMART DS1000 instruction manual
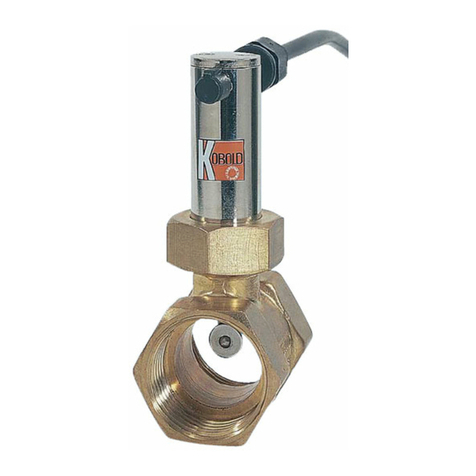
Kobold
Kobold PSR series operating instructions

PCB Piezotronics
PCB Piezotronics 357A95 manual
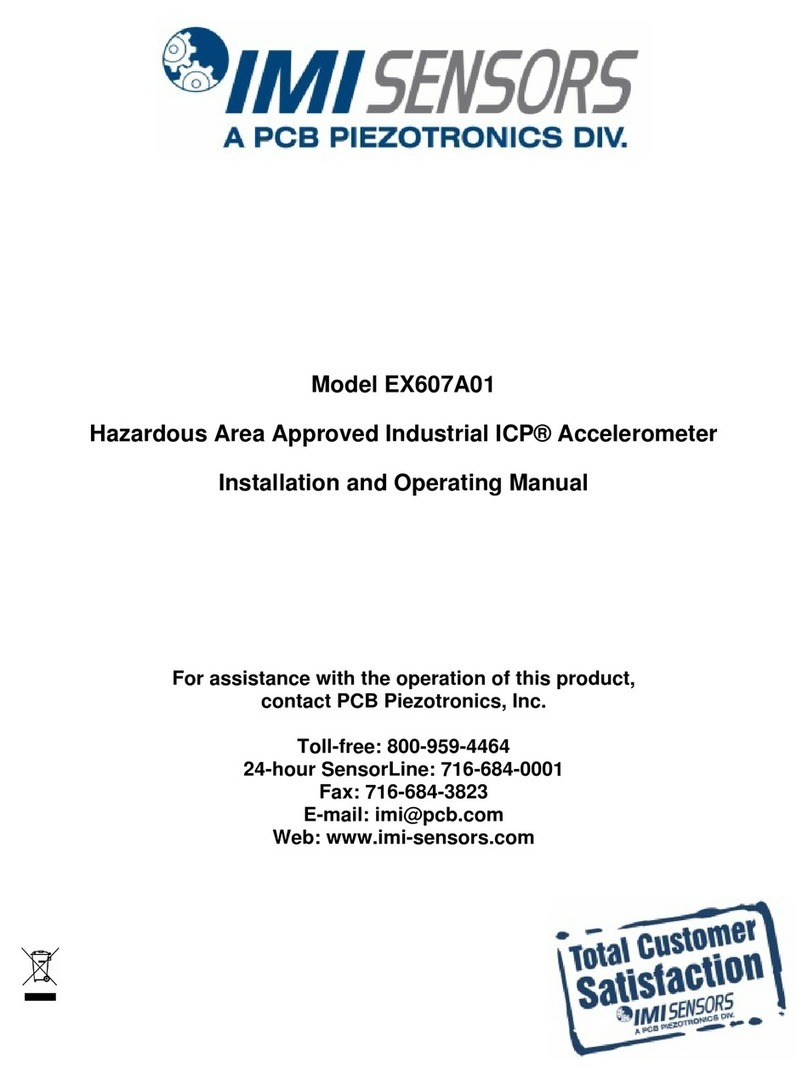
PCB Piezotronics
PCB Piezotronics IMI SENSORS EX607A01 Installation and operating manual

Global Industrial
Global Industrial 412587 instruction manual
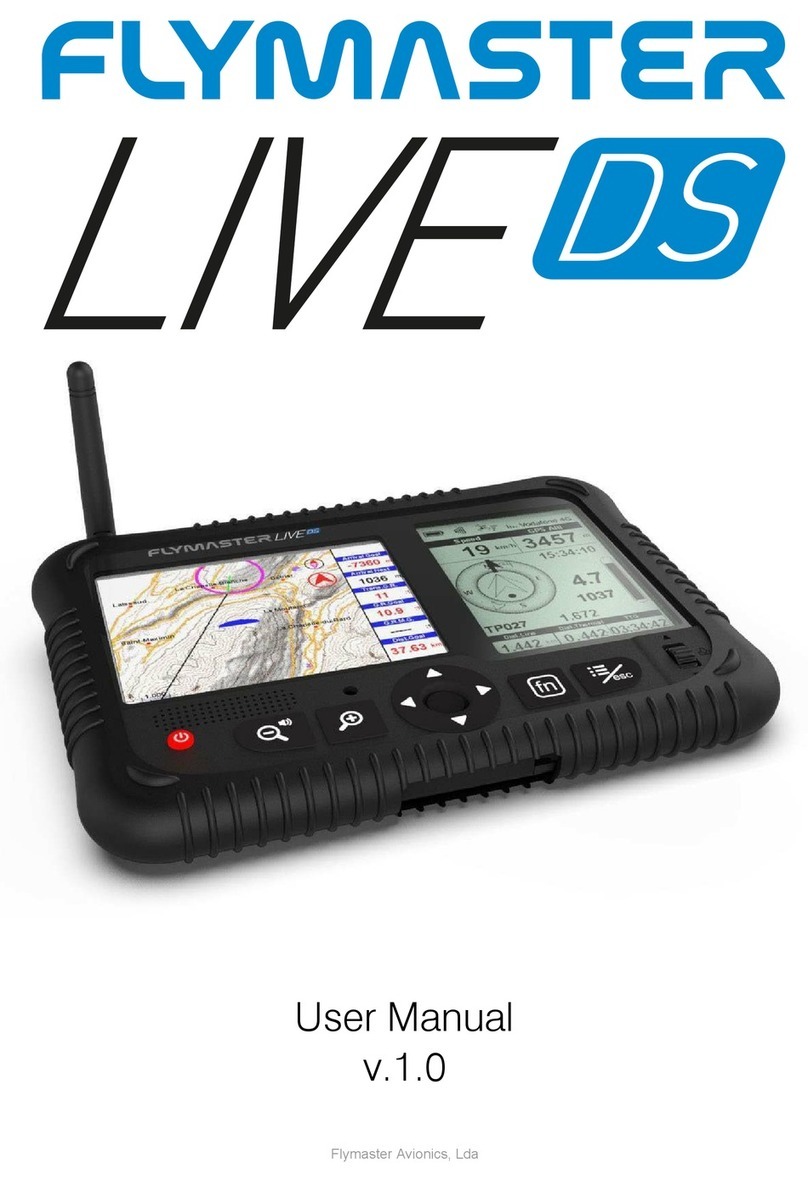
Flymaster
Flymaster LIVE DS manual

DeWalt
DeWalt DW065E user manual
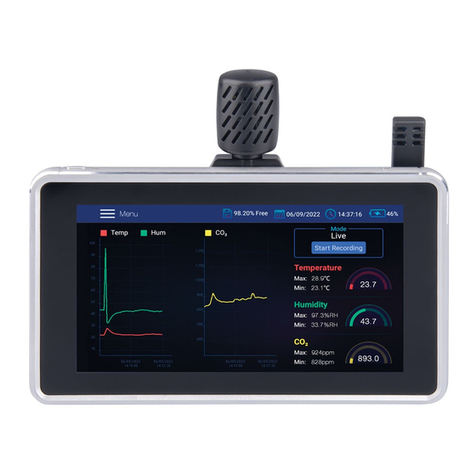
Reed Instruments
Reed Instruments R9920 instruction manual