WinGD X72 User manual

Maintenance Manual
X72
Issue 002 2019-09
Winterthur Gas & Diesel Ltd. Schützenstrasse 3 Tel. +41 (0)52 264 8844
Winterthur Gas & Diesel AG P.O. Box 414, 8401 Fax +41 (0)52 264 8866
Winterthur Gas & Diesel S.A. Winterthur, Switzerland www.wingd.com

© 2019 Winterthur Gas & Diesel Ltd. – All rights reserved
No part of this publication may be reproduced or copied in any form or by any means (electronic,
mechanical, graphic, photocopying, recording, taping or other information retrieval systems)
without the prior written permission of the copyright holder. Winterthur Gas & Diesel Ltd. makes
no representation, warranty (express or implied) in this publication and assumes no responsibility
for the correctness, errors or omissions of information contained herein. Information in this
publication is subject to change without notice.
NO LIABILITY, WHETHER DIRECT, INDIRECT, SPECIAL, INCIDENTAL OR CONSEQUENTIAL, IS
ASSUMED WITH RESPECT TO THE INFORMATION CONTAINED HEREIN. THIS PUBLICATION IS
INTENDED FOR INFORMATION PURPOSES ONLY.
www.wingd.com

Summary for Maintenance Manual
(MM)
Page No. Title Subject
Date No.
new exch.
2015 Maintenance Manual, Issue 2015 x
Date of publication 2015
3303-2/A2 2015 EAAD085741 Bottom End Bearing New document for engines with ELBA (New Support 94322A) x
3303-3/A 2015 EAAD085741 Top End Bearing New document for engines with ELBA (New Support 94322A) x
Group 3 ToC 2015 EAAD085741 ToC Two Chapters added - 3303-2/A2 and 3303-3/A2 x
9403-5/A1 2015 EAAD085741 Standard Tools Tool 94322A added to page 17 x
Date of publication 2015-03
4325-1/A1 2015-04
Sarting Air Shut-off
Valve
Data changed in pages 3, 5 and 6 x
8447-1/A1 2015-03 EAAD085307 Servo Oil Pipes New pipe grinding tool number. Page 3 Updated x
Date of publication 2015-04
2722-1/A1 (1) 2015-08 Preliminary work added; set cooling to off x
2722-2/A1 2015-06 EAAD085606 Injection Valve Page 8, Step 8 - Torque angle data changed x
8447-1/A1 2015-06 EAAD085307 HP Servo Oil Pipe Page 3, Grinding Tool replaced x
2708/A1 2015-06 EAAD085436
Removal and
Installation of Cylinder
Cover
Page 2 Fig. 2 and Page 5 Fig. 8 replaced (new lifting tool) x
5556-1/A1 (17) 2015-08 RT-180 better describtion of oil flow check x
5562-3/A1 2015-06 Flow Limiting Valve New maintenance work added x
9403-5/A1 2015-06
EAAD085436
new drawing
Standard Tools
Page 10, new lifting tool and pretensioner (94215, 94215A);
New tools 94815 Lifting Tool, 94820 Cover added;
x
0380-1/A1 Maintenance Schedule
Now with component lifetime, New data for main bearings,
engine stays, starting air valve, Relief valve, exhaust valve,
Crankshaft, Piston, Starting air shut off valve, Fuel Pump, Flow
limiting valve, Lubricating pump,
x
9308-1/A1 Relief Valve Relocatet Design-Group: former 2745-1
Date of publication 2015-08-12
0002-1/A1 2016-02 Table of contents
iELBA Maintenance Work added (7758-1/A1, 7762-1/A1)
3303-2/A2 and 3303-3/A2 integrated in A1
x
0330-1/A1
(26,27)
2016-02 Clearance table Clearance for Balancer (iELBA) added. x
0380-1/A1 Major update of maintenance schedule x
2751-1/A1 (1) 2016-02 Exhaust Valve Correction of preliminary tasks and illustration x
2751-2/A1 (6) 2016-02 Exhaust Valve Correction shim table x
2303-1/A1 (1, 8-
11)
2016-02 EAAD086068 Piston Rod Gland New procedure 2 (new tool 94235). x
3303-2/A1 2016-02 EAAD085741
Bottom End Bearing
removal
New tool 94322A for iELBA equipped engines x
3303-3/A1 2016-02 EAAD085741
Top End Bearing
removal
New tool 94322A for iELBA equipped engines x
Group7 2016-02 iELBA instructions added x
7758-1/A1 2016 iELBA drive iELBA Maintenance Work added x
7762-1/A1 2016
iELBA proximity
sensors
iELBA Maintenance Work added x
9403-5/A1 (34) 2016-02 EAAD086068 Tool list New Tool: 94235 x
Date of publication 2016-04-06
Manual
Modification Service
Engine Documentation
X72
Modification
Page or
1/3 02/09/2019

Summary for Maintenance Manual
(MM)
Page No. Title Subject
Date No.
new exch.
Manual
Modification Service
Engine Documentation
X72
Modification
Page or
Maintenance
Manual
2016-11
General
Update
All documents New engine brand WinGD X72 added x
0002-1/A1 2016-11 Update SCR Table of Contents New documents 2708-1/A2; 8155-1/A1 added x
0330-1/A1 2016-11 EAAD086203 Clearance Table Guide shoe nominal dimension changed x
0360-1/A1 2016-11
EAAD086104
EAAD086256
Individual Components
Weights
ABB A275 Turbocharger added;
Weights changed for: thrust bearing pad, piston rod gland box,
piston and piston head;
x
Group 2 ToC 2016-11 EAAD086244
New document added: 2708-1/A2; new procedure. Re: new
tool 94270H
x
2303-1/A1 2016-11
General
Update
Piston Rod Gland -
Replace, Assembling,
Wear Measurement
para 3.1, wrong tool number changed to 94234 in the caution
element
x
2708-1/A2 2016-11 EAAD086244
Removal and
Installation of Cylinder
Cover, Water Guide
Jacket, Exhaust Valve
(with Recommended
Tool)
New document with new procedure. Re: new tool 94270H x
Group 8 2016-11 Update SCR Group TOC New document 8155-1/A1 added; x
8155-1/A1 2016-11 New drawing
SCR Valve - Removal,
Installation
New procedure added x
9223-1/A1 2016-11 Update
Crank Angle Sensor
Unit: Proximity Sensor -
Replace
para 2.1: Procedure updated, tolerance changed x
9403-5/A1 2016-11
EAAD086244;
Update SCR
Tool List New tools: 94270H; 94815 x
Date of publication 2016-12-16
2751-2/A1 2017-02
Update
WinGD
Exhaust Valve:
Disassemble and
Assemble
Page 6, para 3.4. Table removed. Text changed. x
9403-5/A1 2017-12
Update
WinGD
Tools List Page 31: 94844 Lubrication device added x
Date of publication 2017-12-22
0330-1/A1 2018-02 WinGD Input Clearance Table x
2138-1/A1 2018-02 WinGD Input Lubricating Quill
Pge 1: Dismantling tool 94213 added to tool list. Pge2:
Replace procedure added.
x
2722-1/A1 2018-02 WinGD Input
Injection Valve:
Removal and
Installation
Pge 2: Warning about copper paste added x
2722-2/A1 2018-02 WinGD Input
Injection Valve:
Disassemble, Checks,
Assemble
Pge 8: Warning about copper paste added x
Group 5 ToC 2018-02 Wartsila Input
Lubrication of Supply
Unit during
Maintenance
New Titles Added: 5552-5/A1, 5562-1/A2 x
5552-5/A1 2018-02 Wartsila Input
Lubrication of Supply
Unit during
Maintenance
New document added x
5562-1/A2 2018-02 Wartsila Input
Fuel Pressure Control
Valve: Manual relase
Valve - Clean
New document added x
9403-5/A1 2018-02 WinGD Input Tools List
Pge 32: 94929 moved to Special Recommended Tools on Pge
35
x
2/3 02/09/2019

Summary for Maintenance Manual
(MM)
Page No. Title Subject
Date No.
new exch.
Manual
Modification Service
Engine Documentation
X72
Modification
Page or
Date of publication 2018-02
Group 0 2019-08 WinGD Input ToC Links to 5562-1/A2 and 5552-5/A1 corrected x
Group 5 2019-08 WinGD Input
Supply Unit, Injection
and Exhaust Valve
Control
Links to 5562-1/A2 and 5552-5/A1 corrected x
Date of publication 2019-08
9403-4A1 2019-08 WinDG input
Hydraulic Pre-
tensioning Jacks -
General Instructions
Pge 4: Cylinder cover Reset Jack/Round Nut turns changed. x
Date of publication 2019-09
3/3 02/09/2019

0
1
2
3
4
5
6
7
8
9
MM / X72 / Register
Driving Wheels and Shut-off Valve for Starting Air
Crankshaft, Connecting Rod and Piston
Cylinder Liner and Cylinder Cover
Bedplate and Tie Rod
General Information
Supply Unit, Injection and Exhaust Valve Control
Scavenge Air Receiver and Auxiliary Blower
Cylinder Lubrication
Piping, Exhaust Manifold, SCR
Crank Angle Sensor Unit, Tools

Maintenance Group0
Winterthur Gas & Diesel Ltd. 1/ 1
General Information Group 0
For Particular Attention 0000−1/A1..................................................................
Preface 0001−1/A1.................................................................................
Table of Contents 0002−1/A1.......................................................................
Engine Numbering and Designations 0008−1/A1.....................................................
General Guidelines
for Maintenance: Safety Measures and Warnings 0011−1/A1........................................
for Lifting Tools: Wire Rope Slings, Span-sets, Eye Bolts etc. 0012−1/A1..............................
Clearance Table 0330−1/A1.........................................................................
General Page 1...............................................................................
Crankshaft and Thrust Bearing 2, 3..............................................................
Crankshaft and Main Bearing 4, 5................................................................
Crosshead Guide 6, 7..........................................................................
Cylinder Liner 8, 9.............................................................................
Piston Rod Gland 10, 11........................................................................
Exhaust Valve 12, 13...........................................................................
Top and Bottom End Bearings to Connecting Rod 14, 15............................................
Piston Cooling and Crosshead Lubricating Link 16, 17..............................................
Piston and Piston Rings 18, 19..................................................................
Driving Wheels for Supply Unit 20, 21............................................................
Fuel and Servo Pump Units 22, 23...............................................................
Fuel Pump 24, 25..............................................................................
Tightening Values of Important Screwed Connections 0352−1/A1.....................................
Torque Values and Elastic Stud Replacement −Standard Screws and Elastic Studs 0352−2/A1..........
Masses (Weights): Individual Components per Piece in kg 0360−1/A1.................................
Maintenance Schedule: Inspection and Overhaul Intervals (Guidelines) 0380−1/A1.....................
Engine Cross Section and Longitudinal Section 0803−1/A1...........................................
Winterthur Gas & Diesel Ltd. X72 / MM / 2015

Maintenance 0000−1/A1
Winterthur Gas & Diesel Ltd. 1/ 1
For Your Attention
1. General
This manual is for the operator and is for use only for the related type of diesel engine
(the engine described in this manual). The data in this manual is confidential.
Make sure that you read carefully the Operation Manual before you operate the
engine.
Make sure that you know the Inspection and Overhaul intervals in the Maintenance
Manual before you operate the engine.
Make sure that you read the data in Group 0 in the Maintenance Manual before you
do maintenance work on the engine.
2. Spare Parts
Use only original spare parts and components to make sure that the engine will
continue to operate satisfactorily. All equipment and tools for maintenance and
operation must be serviceable and in good condition.
The extent of all supplies and services is set exclusively to the related supply
contract.
3. Data
The specifications and recommendations of the classification societies, which are
essential for the design, are included in this manual.
The data, instructions, graphics and illustrations etc. in this manual are related to
drawings from WinGD. These data relate to the date of issue of the manual (the year
of the issue is shown on the title page). All instructions, graphics and illustrations etc
can change because of continuous new development and modifications.
4. Personnel
Only qualified personnel that have the applicable knowledge and training must do
work on the engine, its systems and related auxiliary equipment.
Data related to protection against danger and damage to equipment are specified in
this manual as Warnings and Cautions.
2015

Maintenance 0001−1/A1
Winterthur Gas & Diesel Ltd. 1/ 1
Preface
The instructions contained in this Maintenance Manual are intended to help to ensure
that the maintenance which must be carried out at specific intervals is correctly
carried out.
It is a precondition that the personnel charged with such important work possesses
the necessary training and experience.
Information about the operation of the engine as well as descriptions of the function of
the various systems are part of a separate book, the Operation Manual containing
also under 0010−1 explanations of the layout and structure of the Operation and
Maintenance Manuals as well as of the used symbols, signs and special characters.
More detailed instructions on the operation and maintenance of components from
sub-suppliers can be gathered from the instruction leaflets of the respective
manufacturers. Outside makes are, for example, such engine components, tools or
devices which are not manufactured in accordance with production drawings from
WinGD Ltd.
The ”Maintenance Manual” is divided into the following main chapters:
1) General guidelines for maintenance
2) Clearance tables, tightening values of screwed connections, masses (weights)
3) Maintenance schedule
4) Design groups
5) Tool lists
A few explanations to the above:
1) The General Guidelines for Maintenance contain, in addition to recommendations
on precautionary measures to be taken, also suggestions for carrying out the
work.
2) The above mentioned tables inform about normal and maximum acceptable
clearances, the tightening of important screwed connections, weights of individu-
al engine components as well as the type and use of various sealing rings.
3) The Maintenance Schedule indicates nominal intervals in which various mainte-
nance operations are to be carried out. Please note that the maintenance inter-
vals are based on experience and are subject to operation of the engine under
standard conditions.
4) Detailed instructions are given in the Design Groups on the procedure of mainte-
nance work on certain engine parts.
5) Tools and devices necessary to carry out maintenance are described in the Tool
Lists, and are generally supplied with the engine.
All information contained in the text and illustrations of this manual are valid at the
time of printing.
Modifications will be incorporated in the next edition.
2015

Intentionally blank

Maintenance 0002−1/A1
Table of Contents
Winterthur Gas & Diesel Ltd. 1/ 4 2019−08
General Information Group 0
For Particular Attention 0000−1/A1..................................................................
Preface 0001−1/A1.................................................................................
Engine Numbering and Designations 0008−1/A1.....................................................
General Guidelines
for Maintenance: Safety Measures and Warnings 0011−1/A1........................................
for Lifting Tools: Wire Rope Slings, Span-sets, Eye Bolts etc. 0012−1/A1..............................
Clearance Table 0330−1/A1.........................................................................
General Page 1...............................................................................
Crankshaft and Thrust Bearing 2, 3..............................................................
Crankshaft and Main Bearing 4, 5................................................................
Crosshead Guide 6, 7..........................................................................
Cylinder Liner 8, 9.............................................................................
Piston Rod Gland 10, 11........................................................................
Exhaust Valve 12, 13...........................................................................
Top and Bottom End Bearings to Connecting Rod 14, 15............................................
Piston Cooling and Crosshead Lubricating Link 16, 17..............................................
Piston and Piston Rings 18, 19..................................................................
Driving Wheels for Supply Unit 20, 21............................................................
Fuel and Servo Pump Units 22, 23...............................................................
Fuel Pump 24, 25..............................................................................
Tightening Values of Important Screwed Connections 0352−1/A1.....................................
Torque Values and Elastic Stud Replacement −Standard Screws and Elastic Studs 0352−2/A1..........
Masses (Weights): Individual Components per Piece in kg 0360−1/A1.................................
Maintenance Schedule: Inspection and Overhaul Intervals (Guidelines) 0380−1/A1.....................
Engine Cross Section and Longitudinal Section 0803−1/A1...........................................
Bedplate and Tie Rod Group 1
Bedplate and Thrust Bearing: Foundation Bolts Checks 1112−1/A1...................................
Main Bearing
Elastic Studs −Loosen and Apply Tension 1132−1/A1..............................................
Main Bearing −Removal and Installation 1132−2/A1................................................
Thrust Bearing
Axial Clearance Check 1203−1/A1...............................................................
Thrust Bearing Pads −Removal and Installation 1224−1/A1.........................................
Engine Stays with Friction Shims: Pre-tension Checks 1715−1/A1....................................
Hydraulic Engine Stays: Oil Pressure Checks 1715−1/A2.............................................
Tie Rod: Pre-tension Checks and Tie Rods Replacement 1903−1/A1...................................
Table of Contents

Maintenance0002−1/A1
Table of Contents
Winterthur Gas & Diesel Ltd.
2/ 4
2016-11
Cylinder Liner and Cylinder Cover Group 2
Cylinder Liner
Measure the Bore 2124−1/A1....................................................................
Removal and Installation 2124−2/A1..............................................................
Remove Unwanted Material, Dress the Lubricating Grooves and Scavenge Ports 2124−3/A1............
Lubricating Quill: Removal and Installation 2138−1/A2...............................................
Piston Rod Gland: Replace, Assembling, Wear Measurement 2303−1/A1..............................
Cylinder Cover
Removal and Installation of Cylinder Cover and Water Guide Jacket 2708−1/A1........................
Removal and Installation of Cylinder Cover and Water Guide Jacket (with Recommended Tool) 2708−1/A2
Injection Valve −Sealing Face Machining 2708−3/A1...............................................
Injection Valve: Removal and Installation 2722−1/A1.................................................
Injection Valve: Disassemble, Checks, Assemble (Injection Valve with FAST) 2722−2/A1.............
Starting Valve: Removal, Disassemble, Grinding, Assemble, Installation 2728−1/A1....................
Exhaust Valve
Exhaust Valve −Removal and Installation 2751−1/A1...............................................
Disassemble and Assemble 2751−2/A1...........................................................
Valve Seat −Removal, Grind ans Installation 2751−3/A1............................................
Valve Head −Grind the Seating Surface 2751−4/A1................................................
Crankshaft, Connecting Rod and Piston Group 3
Crankshaft: Measuring Crank Deflection 3103−1/A1.................................................
Vibration Damper
Silicone Fluid Sample 3130−1/A1................................................................
Inspection −GEISLINGER Vibration Damper 3130−2/A1............................................
Axial Damper: Removal and Installation 3140−1/A1..................................................
Turning Gear: Teeth and Screwed Connections −Check 3206−1/A1...................................
Crankcase: Work Platform 3301−1/A1...............................................................
Connecting Rod
Bottom End Bearing −Inspection, Removal and Installation 3303−2/A1...............................
Top End Bearing −Removal, Inspection and Installation 3303−3/A1..................................
Removal and Installation 3303−4/A1..............................................................
Top End Bearing Cover −Removal, Inspection and Installation 3303−5/A1............................
Crosshead
Clearance Checks 3326−1/A1...................................................................
Crosshead Pin −Removal, Installation, Clearance Checks 3326−2/A1................................

Maintenance 0002−1/A1
Table of Contents
Winterthur Gas & Diesel Ltd. 3/ 4 2019−08
Piston
Removal and Installation 3403−1/A1..............................................................
Disassemble and Assemble 3403−3/A1...........................................................
Top Surface Check 3403−4/A1...................................................................
Piston Rings: Wear of Piston Rings and Ring Grooves 3425−1/A1.....................................
Driving Wheels and Shut-off Valve for Starting Air Group 4
Driving Wheels
Running and Backlash Clearances and Tooth Condition 4103−1/A1..................................
Replacing the Gear Wheel on the Crankshaft 4103−2/A1............................................
Shut-off Valve for Starting Air: Cleaning and Function Check 4325−1/A1...............................
Supply Unit, Injection and Exhaust Valve Control Group 5
Fuel Pump
Disassemble and Assemble 5556−1/A1...........................................................
Removal of a Seized Pump Plunger 5556−2/A1....................................................
Fuel Pressure Control Valve: Removal, Check, Installation 5562−1/A1.................................
Fuel Pressure Control Valve: Manual Release Valve −Clean 5562−1/A2................................
Relief Valve: Removal, Check, Installation 5562−2/A1................................................
Flow Limiting Valve: Removal, Inspection, Installation 5562−3/A1.....................................
Fuel Pump Unit
Camshaft and Bearing Shells −Removal and Installation 5581−1/A1.................................
Lubrication of Supply Unit during Maintenance 5552−5/A1...........................................
Fuel Pump Actuator
Connection to Fuel Pump 5583−1/A1.............................................................
Servo Pump Unit
Servo Oil Pump −Removal and Installation (with Hawe SOP) 5591−1/A1.............................
Exhaust Valve Control Unit: Removal, Disassemble, Assemble, Installation 5612−1/A1.................
Scavenge Air Receiver and Auxiliary Blower Group 6
Scavenge Air Receiver −Checks and Cleaning 6420-1/A1...........................................
Auxiliary Blower −Removal and Installation 6545-1/A1..............................................
Scavenge Air Cooler −Removal and Installation 6606-1/A1...........................................
Water Separator −Removal and Installation 6708-1/A1...............................................
Scavenge Air Waste Gate −Disassemble and Assemble 6735-1/A1...................................
Cylinder Lubrication Group 7
Cylinder Lubrication System 7218−1/A1.............................................................
Integrated Electric Balancer (iELBA)
Bearing Replacement and Adjustment 7758−1/A1.................................................
Replacement of Proximity Sensors 7762−1/A1.....................................................

Maintenance0002−1/A1
Table of Contents
Winterthur Gas & Diesel Ltd.
4/ 4
2016-11
Piping Group 8
Exhaust Waste Gate (Low-Load Tuning) 8135−1/A1..................................................
SCR Valve −Removal and Installation 8155−1/A1....................................................
HP Servo Oil Pipe: Removal, Grind the Sealing Faces and Installation (with HAWE SOP) 8447−1/A1.....
Hydraulic Pipe −Exhaust Valve Drive: Removal, Grind the Sealing Faces and Installation 8460−1/A1....
HP Fuel Pipe (Injection Valve): Removal, Grind the Sealing Faces and Installation 8733−1/A1...........
HP Fuel Pipe: Removal, Grind the Sealing Faces and Installation 8752−1/A1...........................
Crank Angle Sensor Unit, Tools Group 9
Crank Angle Sensor Unit: Replacement of Proximity Sensor 9223−1/A1...............................
Relief Valve on Cylinder Cover: Blow-off Pressure Check 9308−1/A1..................................
Tools: Description of Tool Categories 9403−1/A1.....................................................
Hydraulic Pre-tensioning Jacks and Pumps
Configuration and Application 9403−2/A1.........................................................
Overview, Storage, Servicing and Maintenance 9403−3/A1..........................................
General Instructions 9403−4/A1..................................................................
Tool List 9403−5/A1................................................................................
Standard Tools Pages 1 to 35...................................................................
Recommended Special Tools Pages 36 to 38......................................................

Maintenance 0008−1/A1
Winterthur Gas & Diesel Ltd. 1/ 2
Engine Numbering and Designations
2FREE END
DRIVING END
Thrust Bearing Pads
FUEL
SIDE
EXHAUST
SIDE
Rail Unit
Clockwise
Rotation
Counterclockwise
Rotation
Supply Unit
Turbocharger 1
Cylinder
Numbering
WCH01189
Main Bearing
Numbering
Auxiliary
Blower 1
1
1 2 3 4 5
6543 7
6
8
Auxiliary
Blower 2
Turbocharger 2
DRAWN FOR TWO A175 TURBOCHARGERS
Fig. 1
Fig. 2
General
2015

Maintenance 0011−1/A1
Winterthur Gas & Diesel Ltd. 1/ 4
Safety Measures and Warnings
1. General 1..........................................................
2. General safety precautions 1........................................
3. Precautionary measures before beginning of maintenance work 2.....
4. Special safety measures 3..........................................
5. Recommendations for performing work 3............................
1. General
The maintenance work which is required to be carried out on the engine at regular
intervals is described in the Maintenance Schedule 0380−1of this manual and is to
be understood as a general guide. The maintenance intervals are dependent on the
mode of operation, on the power as well as on the quality of the fuel used. Further
details are set out in the maintenance schedule.
Experience will show whether the intervals may be extended or need to be shortened.
Strict compliance with the below mentioned recommendations regarding safety
measures and maintenance work is mandatory; the recommendations are not
exhaustive.
2. General safety precautions
DIt is the operator’s duty to assure that all personnel is familiar with all safety,
health as well as environment protection rules released for operating and
maintaining a diesel engine plant. In particular greatest attention has to be given
to the functioning, handling and dangers of cranes and lifting devices.
DThe safety officer has to make sure that all precautions have been taken in order
to avoid dangerous situations.
DThe operator has to nominate a person responsible for assigning work tasks to
every person who is participating in maintenance work.
DMake sure that fluids or gases draining or escaping cannot cause accidents, fires
or explosions during maintenance work. Keep the engine and the surroundings
clean. Cleanliness increases the quality of the work and helps to prevent
accidents.
Before beginning maintenance work on the diesel engine the corresponding
systems which are influenced by the maintenance work must be relieved of pressure
and/or drained if necessary. A protocol must be established evidencing these
activities.
DCertain media, i.e. fuels etc., are highly inflammable, therefore all precautionary
measures have to be taken that they do not come into in contact with fires,
glowing or hot parts. Smoking in the engine room is strictly forbidden.
Special attention has to be paid to the rules of fire fighting.
Make absolutely sure that in case of fire alarm no fire extinguishing gases can be
released into the engine room while people are still inside. Emergency escapes are
to be marked and personnel is to be instructed of what to do in case of fire.
DOils and other media can cause slippery surfaces. In order to avoid injury all
surfaces which can be stepped on must be kept clean and dry.
CAUTION
Damage Hazard: Do not use water or cleaning fluids to clean the
UNIC electronic components and control boxes on the engine and
rail unit. Damage can occur if water goes into these electronic
components or control boxes.
2015
General Guidelines for Maintenance

Maintenance0011−1/A1
Winterthur Gas & Diesel Ltd.
2/ 4
3. Precautionary measures before beginning of
maintenance work
Before starting any maintenance work on the engine (particularly on the running
gear), take the following precautionary measures:
1) Close the shut-off valves on the starting air bottles.
2) Close all the shut-off valves in the control air supply unit, and open the drains on
both air bottles until it is depressurized.
3) Close by hand the (automatic) shut-off valve for starting air and open the vent
and drain valve to the main starting air piping on the engine as well as the vent
valves on the shut-off valve for starting air, and leave them in this position until
maintenance work is completed.
4) Open all indicator cocks on the cylinder covers and leave them in this position
until maintenance work is completed.
5) Engage turning gear (gear pinion must be in engaged position) and lock the lever
(see also 3206−1 and 0750−1 in the Operating Manual).
DWhere the engine has been stopped due to overheated running gear or
bearings, wait at least 20 minutes before opening the crankcase doors.
DThe crankcase doors must always be locked with all the clamps whenever
the engine is running, even if this is only for a short time in order to make
temperature checks (e.g. after changing bearings during an overhaul, etc.).
DIn the case of a fire in the engine having been extinguished by means of CO2, the
spaces affected must be well ventilated before work can be carried out within
them.
CAUTION
Damage Hazard: When you do electric welding near or on the
engine, electromagnetic fields or peak voltage can occur. This
can damage the electronic components of the Engine Control
System UNIC.
Therefore, prior to performing electric welding in the vicinity of the mentioned
components, the following precautions must be taken:
DStop the engine if it is in operation.
DPower off the electronic system and wait one minute.
DIf the welding point is within a radius of two metres from an electronic module
and/or a sensor, disconnect the modules and/or sensors.
DClose the covers of all electric boxes and protect cables, sensors, etc. against
sparking and heat.
DShield the check and control units with a conductive material and connect them
to earth.
DRun the welding cable from the welding apparatus directly to the welding point
without any unnecessary loops; also, avoid leading the welding cable parallel to
cables of the electronic control unit.
2015
Safety Measures and Warnings

Maintenance 0011−1/A1
Winterthur Gas & Diesel Ltd. 3/ 4
4. Special safety measures
DPrior to turning the crankshaft with the turning gear, make sure and take notice:
1) that no person is inside the engine and no loose parts, tools or devices can get
jammed.
2) bear in mind that the coupled propeller turns too (danger in surroundings).
DAt all times when somebody is inside the engine casing another person must
stand by in order that he can give the necessary aid if something unexpected
happens to the person inside the engine. The person who is inside the engine
casing must be equipped with all safety gears which are required to prevent
suffocation within the limited space and atmospheric conditions. Moreover an
anti-fall guard must be carried at dangerous places.
DThe allowed load capacity of the engine room crane, the lifting tools, ropes and
chains must be sufficient for the parts to be lifted (see 0012−1and 0360−1).
Pay also attention to the weight distribution and attachment of the lifting tackle in
order that the part which must be lifted cannot tip over or crash down!
DSharp edges, mating faces etc. as well as ropes are to be protected by wooden
pieces, leather or special edge guards which are placed between the part and the
rope or chain.
DAlways use gloves, a face shield and wear safety goggles when working with
hydraulic tools.
DFor your own safety keep away from under hanging loads, never undersling
hanging parts with your fingers or hands and never embrace lifting ropes with
your hands.
DRemoved parts must be secured in the engine room.
DFor reasons of safety, openings resulting from removed engine components must
be closed!
Note: For further instructions see also Safety Precautions and Warnings
(General Information) 0210−1 in the Operating Manual.
5. Recommendations for performing work
DPay attention to Utilization of Working Platform 3301−1.
DCarry out all work carefully, observing utmost cleanliness!
DFor maintenance work on the engine use the tools and devices intended for the
particular job, which, as a rule, are supplied with the engine (see tool list at the
end of this manual).
1) Tools and devices must be made ready prior to use, make sure they are in
perfect condition.
2) Calibrate gauge tools before using and at periodical intervals.
3) Check hydraulic tools periodically for tightness and perfect functioning.
4) Protect running faces and sealing faces of removed parts by suitable means to
prevent damages.
2015
Safety Measures and Warnings

Maintenance0011−1/A1
Winterthur Gas & Diesel Ltd.
4/ 4
5) Close all openings which form when certain parts are removed e.g. pipes, oil
holes etc. to prevent dirt from entering the engine. (This includes also the pipes
which are removed).
6) Check all repaired, overhauled or replaced parts for perfect functioning before
starting the engine.
7) Check all pipes which have been removed, for tightness after they are refitted.
8) Clearances of moving parts must be checked periodically. Should the maximum
permissible values (see Clearance Table 0330−1) have been reached or even
exceeded, these parts must be replaced.
9) Arrange to replace all parts taken from spares stock. When ordering new parts
refer to the Code Book, mention code numbers and description.
DWhen tightening studs, nuts or screws, take the utmost care not to damage their
thread. They must be screwed in by hand until metal to metal contact is
achieved. Always use the specified lubricants on the threads.
DAdhere to tightening values wherever they are indicated. Use the specified
lubricant on the threads (see 0352−1and 0352−2).
DLocking devices of bolts, nuts, etc. must be fitted correctly and secured properly.
Use locking plates and locking wires only once.
DFor threads of screws and studs which are getting very hot, (i.e. exhaust pipe or
turbocharger fastenings) apply a high temperature resistant lubricant before
assembly, to prevent a heat seizure.
DUsed rubber rings must always be replaced by new ones when an overhaul of
any engine component takes place; they must conform in dimension and quality
to the WinGD specifications.
The fitting of piston seal rings and rod seal rings requires the greatest of care to
prevent damage, over expansion or deformation. Before fitting the rings heat them
first in boiling water.
2015
Safety Measures and Warnings
Other manuals for X72
2
Table of contents
Other WinGD Engine manuals

WinGD
WinGD X92DF User manual
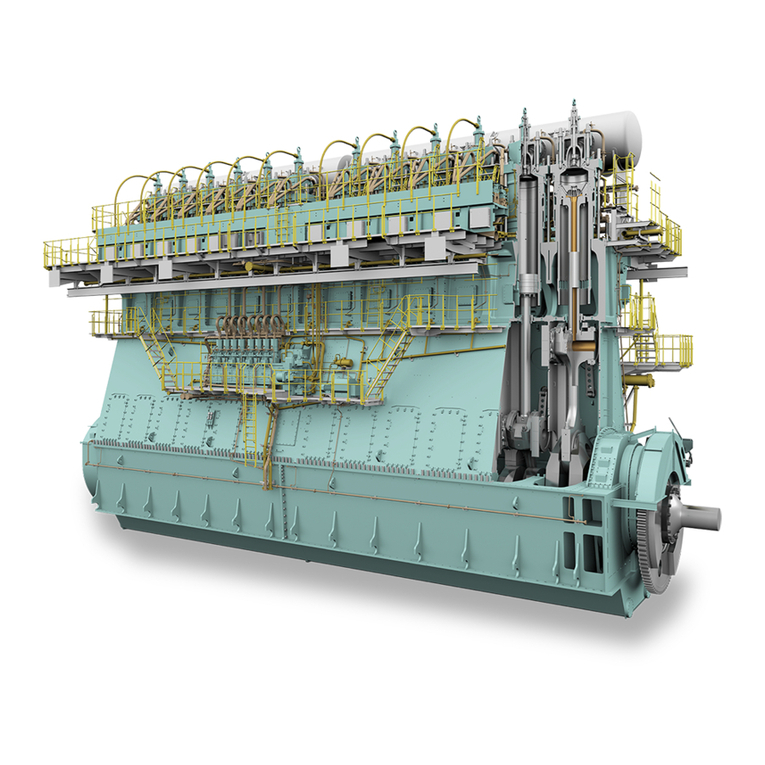
WinGD
WinGD X72 User manual
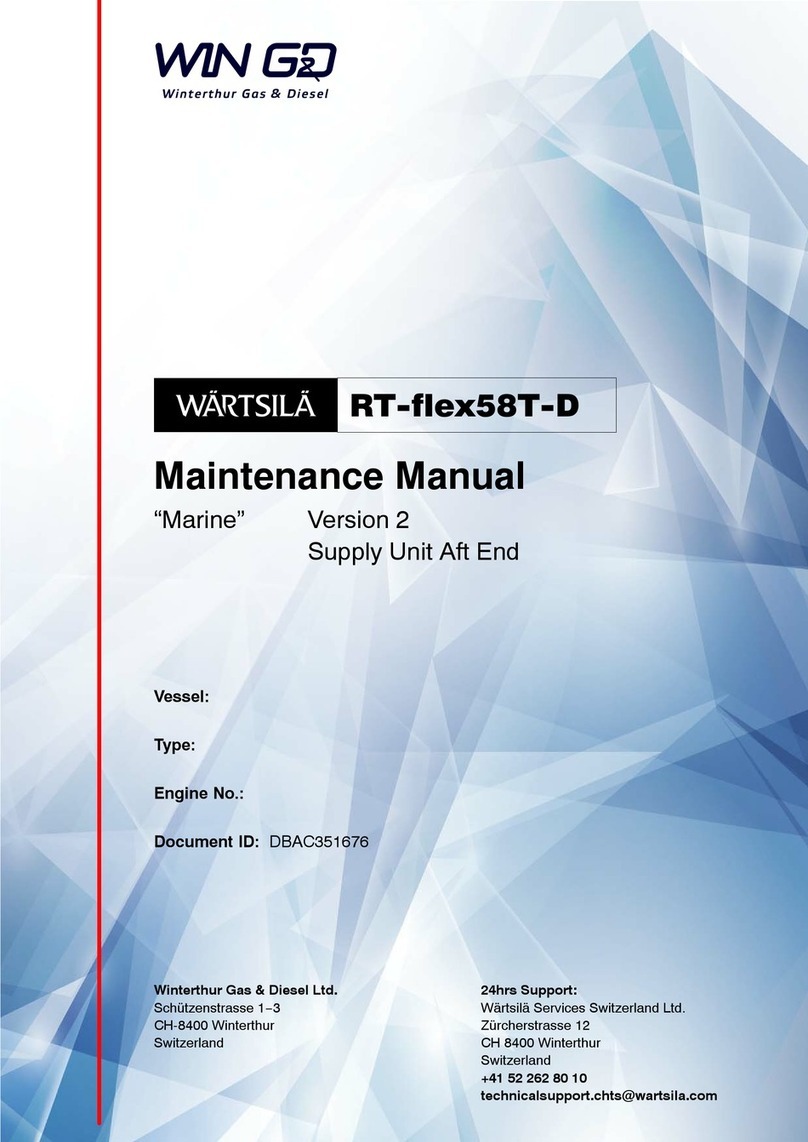
WinGD
WinGD WARTSILA RT-flex58T-D User manual

WinGD
WinGD W-X82 User manual
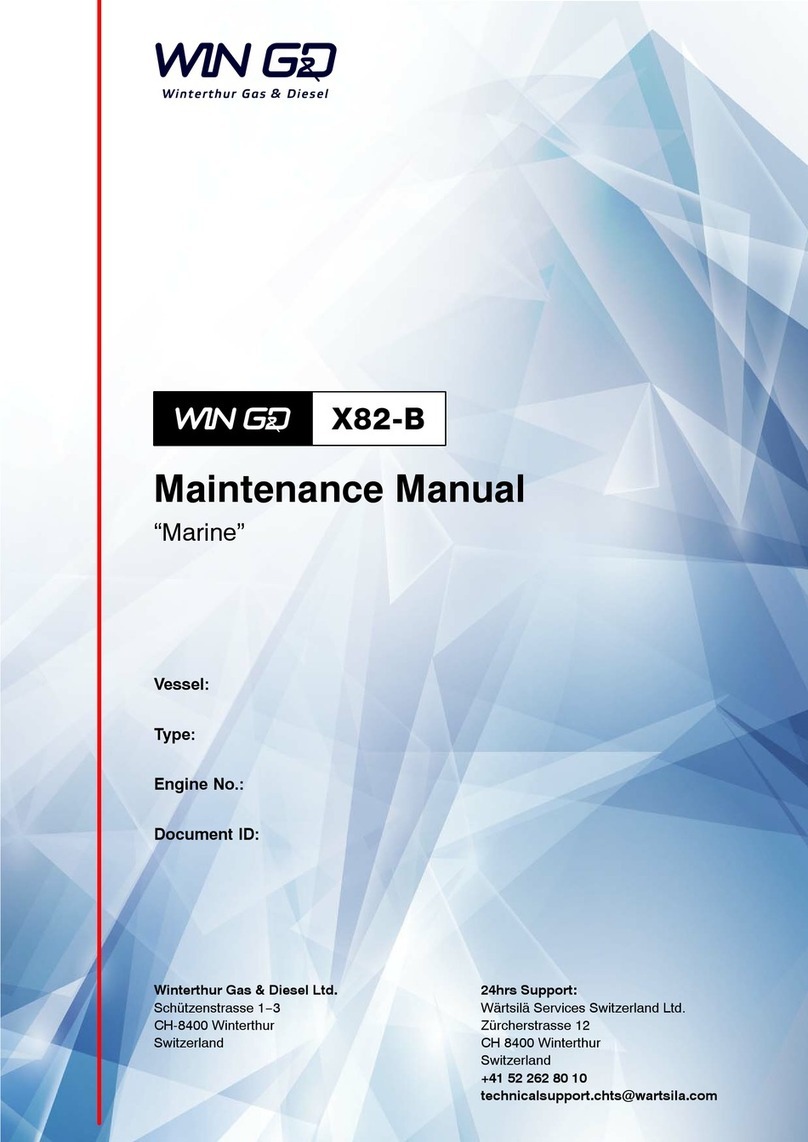
WinGD
WinGD X82-B User manual

WinGD
WinGD X35-B User manual
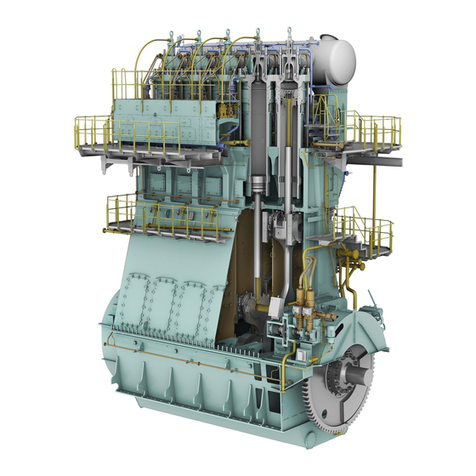
WinGD
WinGD X72DF User manual
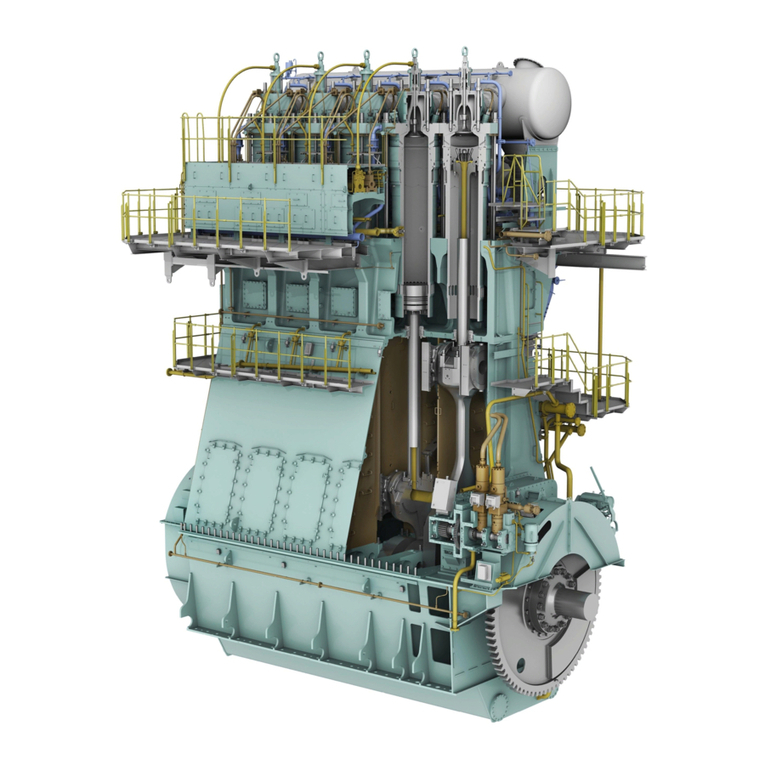
WinGD
WinGD X72 User manual
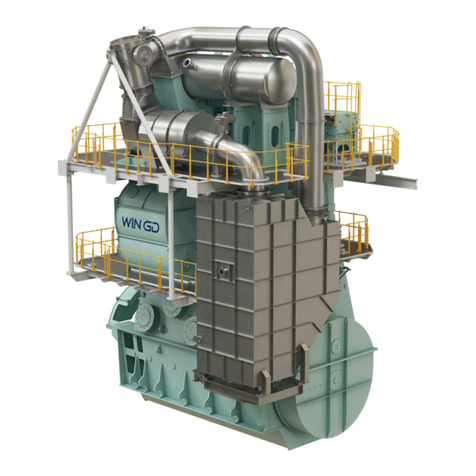
WinGD
WinGD WARTSILA RT-flex58T-E User manual

WinGD
WinGD X92-B User manual
Popular Engine manuals by other brands
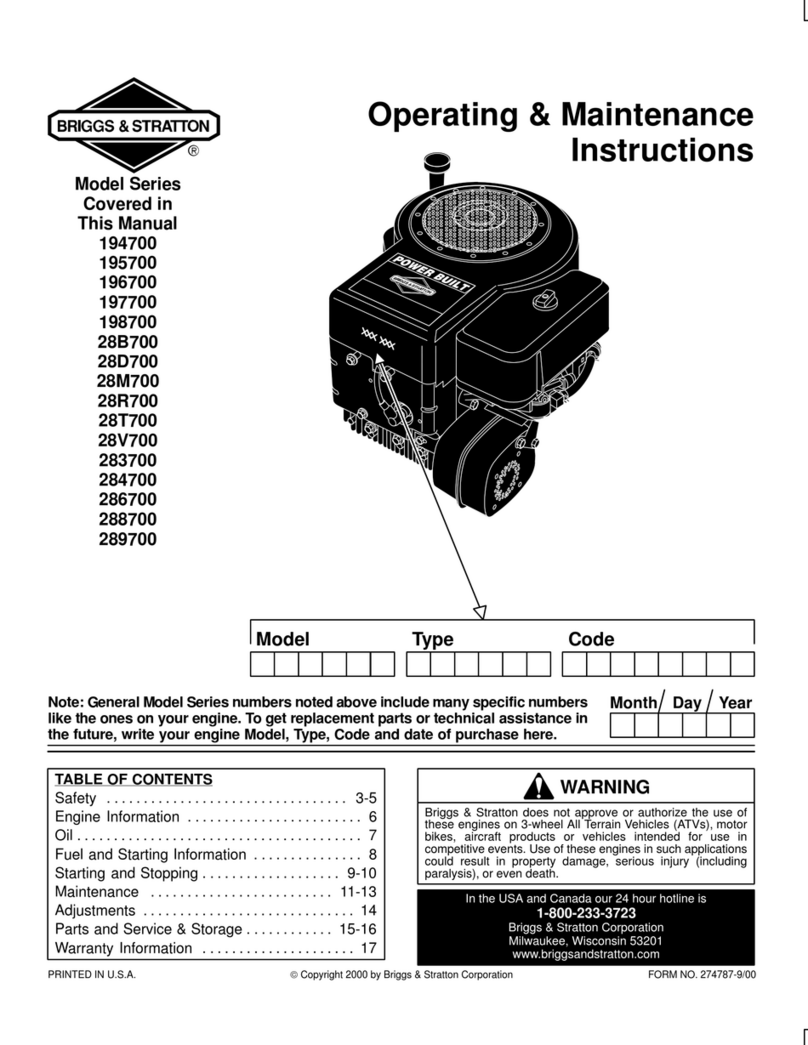
Briggs & Stratton
Briggs & Stratton 194700 Series Operating & maintenance instructions

Universal Motors
Universal Motors M-12 owner's manual
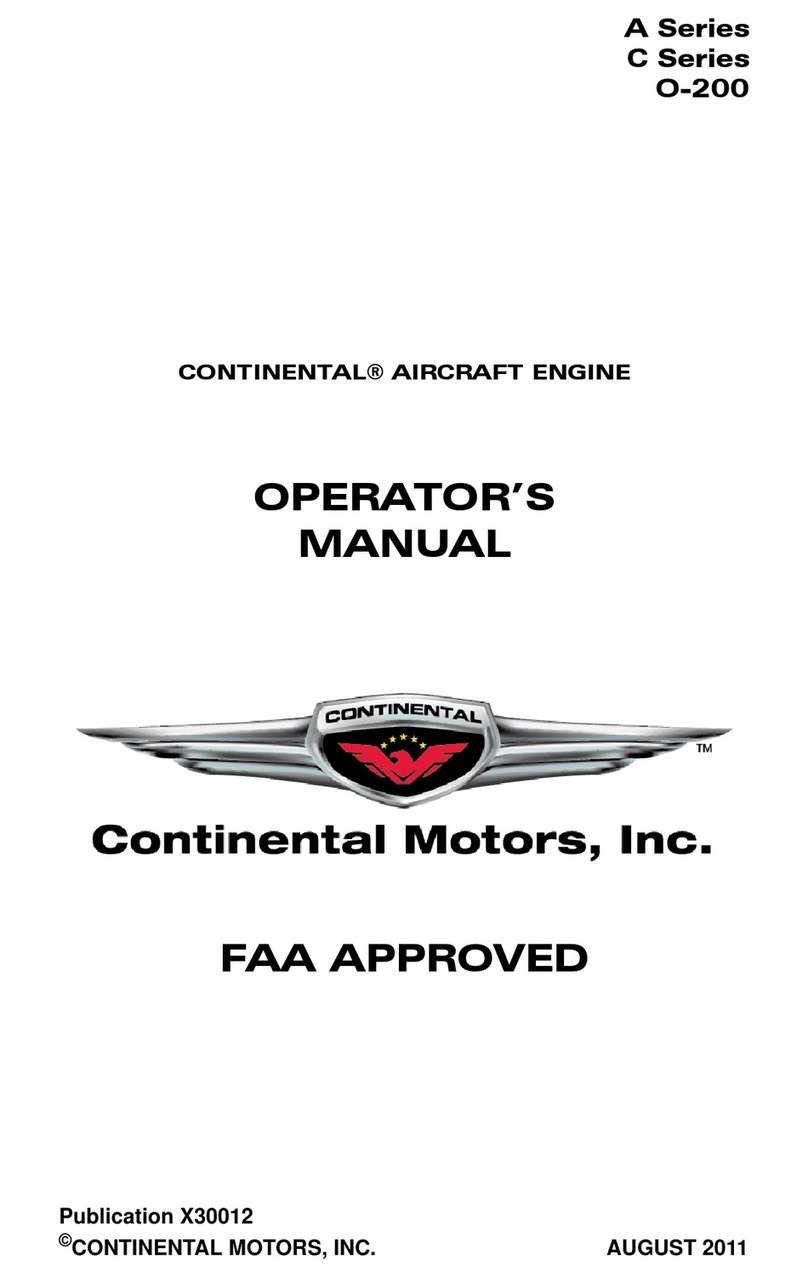
Continental Motors
Continental Motors A Series Operator's manual
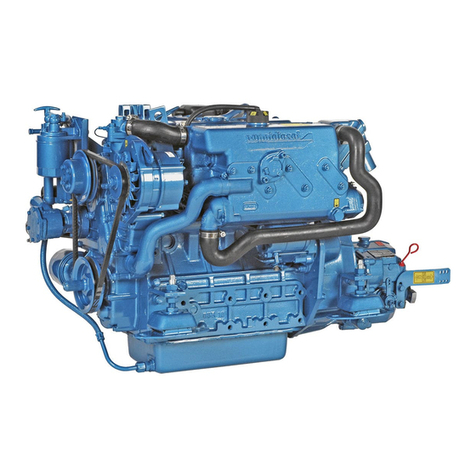
Nanni
Nanni N4.40 Workshop manual
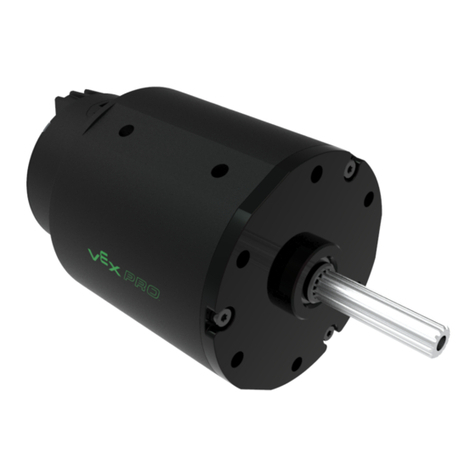
CTR Electronics
CTR Electronics TALON FX VEX.PRO FALCON 500 manual
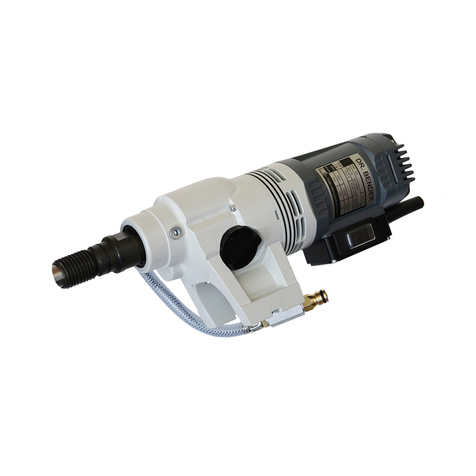
DR. BENDER
DR. BENDER EBL 33L manual