WinGD WARTSILA RT-flex58T-D User manual

RT-flex58T-D
Maintenance Manual
“Marine” Version 2
Supply Unit Aft End
Vessel:
Type:
Engine No.:
Document ID: DBAC351676
Winterthur Gas & Diesel Ltd. 24hrs Support:
Schützenstrasse 1−3 Wärtsilä Services Switzerland Ltd.
CH-8400 Winterthur Zürcherstrasse 12
Switzerland CH 8400 Winterthur
Switzerland
+41 52 262 80 10

E2014-04 Winterthur Gas & Diesel Ltd., Printed in Switzerland – All rights reserved
No part of this publication may be reproduced or copied in any form or by any means (electron-
ic, mechanical, graphic, photocopying, recording, taping or other information retrieval systems)
without the prior written permission of the copyright holder.
Wärtsilä Services Switzerland Ltd. makes no representation, warranty (express or implied) in
this publication and assumes no responsibility for the correctness, errors or omissions for infor-
mation contained herein. Information in this publication is subject to change without notice.
NO LIABILITY WHETHER DIRECT, INDIRECT, SPECIAL, INCIDENTAL OR CONSEQUEN-
TIAL, IS ASSUMED WITH RESPECT TO THE INFORMATION CONTAINED HEREIN. THIS
PUBLICATION IS CONFIDENTIAL AND INTENDED FOR INFORMATION PURPOSES ONLY.

RT-flex58T-D
Maintenance Manual
“Marine” Version 2
Supply Unit Aft End
Vessel:
Type:
Engine No.:
Document ID: DBAC351676
Winterthur Gas & Diesel Ltd. 24hrs Support:
Schützenstrasse 1−3 Wärtsilä Services Switzerland Ltd.
CH-8400 Winterthur Zürcherstrasse 12
Switzerland CH 8400 Winterthur
Switzerland
+41 52 262 80 10

E2014-04 Winterthur Gas & Diesel Ltd., Printed in Switzerland – All rights reserved
No part of this publication may be reproduced or copied in any form or by any means (electron-
ic, mechanical, graphic, photocopying, recording, taping or other information retrieval systems)
without the prior written permission of the copyright holder.
Wärtsilä Services Switzerland Ltd. makes no representation, warranty (express or implied) in
this publication and assumes no responsibility for the correctness, errors or omissions for infor-
mation contained herein. Information in this publication is subject to change without notice.
NO LIABILITY WHETHER DIRECT, INDIRECT, SPECIAL, INCIDENTAL OR CONSEQUEN-
TIAL, IS ASSUMED WITH RESPECT TO THE INFORMATION CONTAINED HEREIN. THIS
PUBLICATION IS CONFIDENTIAL AND INTENDED FOR INFORMATION PURPOSES ONLY.

Summary for Maintenance Manual
(MM)
Page No. Title Subject
Date No.
new exch.
2013 Issue 2013 x
Date of publication 2013-01-30
0380-1/A1 (2) 2013-02 TB RT-143 Maintenance Schedule 2728-1: Monthly check of nut to solenoid added x
2728-1/A1 Starting Air Valve
Check concerning venting of starting air manifold and
tightening of nut (18) to solenoild (17) added
x
2124-1/A1 Cylinder Liner x
2124-3/A1 (2) Cylinder Liner x
2708-1/A1 Cylinder Cover Cyliner liner with upper and lower water guide jacket adapted x
2722-1/A1 (6) Injection Valve Sec. 7: Remark added concerning replacing of a nozzle tip x
6420-1/A1 Scavenge Air Receiver Arrangement of air flaps standardized to those in OM x
9403-4/A1 (2) Hydr. Pre-tens. Jacks 1132-1: Comparison value in (°) deleted x
Date of publication 2013-02-20
0002-1/A1 x
Index 3, 9 x
0008-1/A1 (2) EAAD084591
Engine Numbering and
Designations
Crank angle sensor unit at gear wheel added x
0011-1/A1 (1)
Safety Measures and
Warnings
Attention concerning clean areas (no water or cleaning fluids)
added
x
0330-1/A1
(18, 19)
Clearance Table Key No. 6 and 7: points A and B added x
0380-1/A1 (2) Maintenance Schedule
3103-1: Interval changed "according to classification society"
x
(3)
3403-1: Intervals changed to 18 000-36 000 operating hours
3403-4: Intervals changed to 500-1000 operating hours
3425-1: Work to be carried out and intervals changed
x
2303-1/A1
(1, 7)
EAAD084619 Piston Rod Gland Recess applied on clamping ring 94345b as shown in Fig. 'G' x
2722-1/A1
(1, 3, 4-6, 8)
Injection Valve
Sec. 11 added; system oil as test media mentioned; Sec. 3:
keeping opening pressure changed from 10 to 30 seconds;
Sec. 5 revised; Remark concerning IMO technical file and
detail of nozzle type added
x
3103-1/A1
Measuring Crank
Deflection
1. General aspects; 2. Condition of measuring and 4. Crank
deflection limits revised
x
3425-1/A1
Piston Rings
(Four Piston Rings)
Determination of wear rate of chrome-ceramic piston rings and
measuring piston ring grooves introduced
x
3425-1/A2
Piston Rings
(Three Piston Rings)
Determination of wear rate of chrome-ceramic piston rings and
measuring piston ring grooves introduced
x
4103-3/A1 (5)
Replacing Gear Wheel
on Crankshaft
Stud side (thread) to be applied with MOLYKOTE and
LOCTITE 262 corrected
x
5801-1/A2 (1) Regulating Linkage
(with Woodward ProAct II Analog Actuator): 2nd sentence
about configuration and setting procedure added
x
8733-1/A1
(1, 2)
EAAD084136
HP Pipe to Injection
Valve
Special spanner 94874 and detail concerned in Fig. 'B' added x
9223-1/A2 2013 EAAD084591
Crank Angle Sensor
Unit
Assembly and replacement of proximity sensor (pickup) at
gear wheel introduced
x
9403-5/A1
(30, 33, 34)
2013-08 Tool List
Tools 94874, 94291A, 94356 (only figure modified) and 94357
added
x
Date of publication 2013-08-23
9403-5/A1
(3,4,10,21,26,
27,28,29,35)
2014-01 Tool List
94012 changed to 94012C, GF94020 changed to 94020D,
94022 changed to 94022B,94142 changed to 94142-L and -R,
94345F changed to 94345F/94345G,94651 changed to
94651C, 94662 deleted, 94481 deleted,94870E,F,G changed
to 94870K,94870A,B,C changed to 94870J
x
Modification Service
Engine Documentation
RT-flex58T-D Version 2
Supply Unit Aft End
Modification
Page or
2013-08
Table of Contents
3425-1/A1, A2: checking wear of … ring grooves and new
group 9223-1/A2 added
Execution cylinder liner / supporing ring replaced with cylinder
liner / water guide jacket
Manual
1/2 09/04/2018

Summary for Maintenance Manual
(MM)
Page No. Title Subject
Date No.
new exch.
Modification Service
Engine Documentation
RT-flex58T-D Version 2
Supply Unit Aft End
Modification
Page or
Manual
Date of publication 2014-01-09
9403-5/A1 (36) 2014-04 Tool List Tools: 94211, 94212 deleted x
Date of publication 2014-04-02
0352-1/A1 (1) 2015-08 EAAD086016 Tightening Values
New tightening values for elastic studs of cylinder cover (new
pre-tensioning jack)
x
2708-2/A1 2015-08 EAAD086016
tensioning of cyl.
Cover studs
new pretensioning jack for cyl. Cover GF94215A x
9403-3/A1 (1, 5) 2015-08 EAAD086016 Pre-Tesnioning jacks New jack for Cyl. Cover studs x
9403-5/A1 (30) 2015-08 EAAD085234 Tool List
Tool numbers 94871 and 94871A added, new cyl. Cover press
GF94215A
x
Date of publication 2016-02-17
2751-2/A1 2018 WinGD Input
Exhaust Valve:
Disassemble and
Assemble
Pge: 7. Paragraph 3.4 - Procedure changed. x
5552-5/A1 2018-02 Wartsila Input
Lubrication of Supply
Unit during
Maintenance
Procedure changed x
Group 5 ToC 2018 WinGD Input ToC Analog Actuator replaced with Digital Actuator x
5801-1/A2 2018 WinGD Input
Regulating Linkage -
Woodward ProAct II -
Digital Actuator
Procedure changed. Analog actuator replace with digital
actuator
x
9403-5/A1 2018-01 DAAD083068 Tools List Page 36: 94844 Lubrication device added. x
Date of publication 2018-02
2/2 09/04/2018

0
1
2
3
4
5
6
7
8
9
MM / RT−flex / Register
Driving Wheels and Shut-off Valve for Starting Air
Crankshaft, Connecting Rod and Piston
Cylinder Liner and Cylinder Cover
Bedplate and Tie Rod
General Information
Supply Unit, Injection and Exhaust Valve Control
Scavenge Air Receiver and Auxiliary Blower
Cylinder Lubrication
Piping
Crank Angle Sensor Unit, Tools

Intentionally blank

Maintenance Group0
RT-flex58T-D
Winterthur Gas & Diesel Ltd. 1/ 1
For Particular Attention 0000−1/A1..................................................
Preface 0001−1/A1...............................................................
Table of Contents 0002−1/A1.......................................................
Engine Numbering and Designations 0008−1/A1......................................
oGeneral Guidelines
−for Maintenance: Safety Measures and Warnings 0011−1/A1........................
−for Lifting Tools: Wire Rope Slings, Span-Sets, Eye Bolts etc. 0012−1/A1..............
oClearance Table 0330−1/A1....................................................................
−General Page 1...............................................................
−Crankshaft and Thrust Bearing 2, 3..............................................
−Crankshaft and Main Bearing 4, 5................................................
−Crosshead Guide 6, 7..........................................................
−Cylinder Liner 8, 9.............................................................
−Piston Rod Gland 10, 11........................................................
−Exhaust Valve 12, 13...........................................................
−Top and Bottom End Bearings to Connecting Rod 14, 15............................
−Piston Cooling and Crosshead Lubricating Link 16, 17..............................
−Piston and Piston Rings 18, 19..................................................
−Driving Wheels for Supply Unit 20, 21............................................
−Supply Unit 22, 23.............................................................
−Fuel Pump 24, 25..............................................................
oTightening Values
−of Important Screwed Connections 0352−1/A1.....................................
−of Standard Screwed Connections 0352−2/A1.....................................
Masses (Weights): Individual Components per Piece in kg 0360−1/A1...................
Maintenance Schedule: Inspection and Overhaul Intervals (Guidelines) 0380−1/A1........
Engine Cross Section and Longitudinal Section 0803−1/A1.............................
General Information Grou
p
0
Winterthur Gas & Diesel Ltd. RT−flex58T−D / V2 / MM / 2013

Intentionally blank

Maintenance 0000−1/A1
RT-flex58T-D
Winterthur Gas & Diesel Ltd. 1/ 1
This manual is put at the disposal of the recipient solely for use in connection with
the corresponding type of diesel engine.
It has always to be treated as confidential.
The intellectual property regarding any and all of the contents of this manual, par-
ticularly the copyright, remains with Wärtsilä Switzerland Ltd. This document
and parts thereof must not be reproduced or copied without their written permis-
sion, and the contents thereof must not be imparted to a third party nor be used for
any unauthorized purpose.
Before the operator intends to use the engine or before maintenance work is un-
dertaken, the Operating Instructions or the Maintenance Manual respectively is to
be read carefully.
To ensure the best efficiency, reliability and lifetime of the engine and its compo-
nents, only original spare parts should be used.
It is to be ensured as well that all equipment and tools for maintenance are in good
condition.
The extent of any supplies and services is determined exclusively by the relevant
supply contract.
The data, instructions and graphical illustrations etc. in this manual are based on
drawings made by Wärtsilä Switzerland Ltd and correspond to the actual stan-
dard at the time of printing (year of printing is indicated on title page).
Those specifications and recommendations of the classification societies which
are essential for the design have been considered therein. It must be recognized
that such data, instructions and graphical illustrations may be subject to changes
due to further development, widened experience or any other reason.
This manual is primarily intended for use by the engine operating and maintenance
personnel. It must be ensured that it will always be at the disposal of such person-
nel for the operation of the engines and/or for the required maintenance work.
This manual has been prepared on the assumption that operation and mainte-
nance of the engines concerned will always be carried out by qualified personnel
having the special knowledge, training and qualifications needed to handle in a
workman-like manner diesel engines of the corresponding size, the associated
auxiliary equipment, as well as fuel and other operating media.
Therefore, generally applicable rules, which may also concern such items as
protection against danger, are specified in this manual in exceptional cases only.
It must be made sure that the operating and maintenance personnel are familiar
with the rules concerned.
This manual has been prepared to the best knowledge and ability of its au-
thors. However, neither Wärtsilä Switzerland Ltd nor their employees as-
sume any liability −under any legal aspect whatsoever, including possible
negligence −in connection with this manual, its contents, or modifications
to it or in connection with its use.
Claims relating to any damage whatsoever or claims of other nature such as,
but not limited to, demands for additional spares supplies, service or others
are expressly excluded.
Wärtsilä Switzerland Ltd
Winterthur
Switzerland
For Particular Attention
2013

Intentionally blank

Maintenance 0001−1/A1
RT-flex58T-D
Winterthur Gas & Diesel Ltd. 1/ 1
The instructions contained in this ”Maintenance Manual” are intended to help to
ensure that the maintenance which must be carried out at specific intervals is cor-
rectly carried out.
It is a precondition that the personnel charged with such important work possesses
the necessary training and experience.
Information about the operation of the engine as well as descriptions of the func-
tion of the various systems are part of a separate book, the ”Operating Manual”
containing also under 0010−1 explanations of the layout and structure of the Oper-
ating and Maintenance Manuals as well as of the used symbols, signs and special
characters.
More detailed instructions on the operation and maintenance of components from
sub-suppliers can be gathered from the instruction leaflets of the respective
manufacturers. Outside makes are, for example, such engine components, tools
or devices which are not manufactured in accordance with production drawings
from Wärtsilä Switzerland Ltd.
The ”Maintenance Manual” is divided into the following main chapters:
−General guidelines for maintenance
−Clearance tables, tightening values of screwed connections, masses
(weights), seal rings
−Maintenance schedule
−Design groups
−Tool lists
A few explanations to the above:
−The ’General Guidelines for Maintenance’ contain, in addition to recommen-
dations on precautionary measures to be taken, also suggestions for carrying
out the work.
−The above mentioned tables inform about normal and maximum acceptable
clearances, the tightening of important screwed connections, weights of indi-
vidual engine components as well as the type and use of various sealing rings.
−The ’Maintenance Schedule’ indicates nominal intervals in which various
maintenance operations are to be carried out. Please note that the mainte-
nance intervals are based on experience and are subject to operation of the
engine under standard conditions.
−Detailed instructions are given in the ’Design Groups’ on the procedure of
maintenance work on certain engine parts.
−Tools and devices necessary to carry out maintenance are described in the
’Tool Lists’, and are generally supplied with the engine.
All information contained in the text and illustrations of this manual are valid at the
time of printing.
Modifications will be incorporated in the next edition!
Preface
2013

Intentionally blank

RT-flex58T-D Maintenance 0002−1/A1
Table of Contents
Winterthur Gas & Diesel Ltd. 1/ 5 V2 / 2013-08
General Information Group 0
For Particular Attention 0000−1/A1..................................................
Preface 0001−1/A1...............................................................
Engine Numbering and Designations 0008−1/A1......................................
oGeneral Guidelines
−for Maintenance: Safety Measures and Warnings 0011−1/A1........................
−for Lifting Tools: Wire Rope Slings, Span-Sets, Eye Bolts etc. 0012−1/A1..............
oClearance Table 0330−1/A1....................................................................
−General Page 1...............................................................
−Crankshaft and Thrust Bearing 2, 3..............................................
−Crankshaft and Main Bearing 4, 5................................................
−Crosshead Guide 6, 7..........................................................
−Cylinder Liner 8, 9.............................................................
−Piston Rod Gland 10, 11........................................................
−Exhaust Valve 12, 13...........................................................
−Top and Bottom End Bearings to Connecting Rod 14, 15............................
−Piston Cooling and Crosshead Lubricating Link 16, 17..............................
−Piston and Piston Rings 18, 19..................................................
−Driving Wheels for Supply Unit 20, 21............................................
−Supply Unit 22, 23.............................................................
−Fuel Pump 24, 25..............................................................
oTightening Values
−of Important Screwed Connections 0352−1/A1.....................................
−of Standard Screwed Connections 0352−2/A1.....................................
Masses (Weights): Individual Components per Piece in kg 0360−1/A1...................
Maintenance Schedule: Inspection and Overhaul Intervals (Guidelines) 0380−1/A1........
Engine Cross Section and Longitudinal Section 0803−1/A1.............................
Table of Contents

RT-flex58T-D
Maintenance0002−1/A1
Table of Contents
2/ 5 Winterthur Gas & Diesel Ltd.
2013-08 / V2
Bedplate and Tie Rod Group 1
Bedplate and Thrust Bearing: Checking the Foundation Bolts 1112−1/A1.................
oMain Bearing
−Loosening and Tensioning of Elastic Studs 1132−1/A1..............................
−Removal and Fitting of a Main Bearing 1132−2/A1.................................
oThrust Bearing
−Checking the Axial Clearance 1203−1/A1.........................................
−Removal and Fitting the Thrust Bearing Pads 1224−1/A1............................
Engine Stays with Friction Shims: Checking the Pre-tension 1715−1/A1..................
Tie Rod: Checking the Pre-tension and Tensioning the Tie Rods 1903−1/A2..............
Cylinder Liner and Cylinder Cover Group 2
oCylinder Liner
−Measuring Bore Wear 2124−1/A1................................................
−Removal and Fitting 2124−2/A1..................................................
−Removing the Wear Ridge, Re-dressing Lubricating Grooves
and Scavenge Ports 2124−3/A1..................................................
Lubricating Quill with Pulse Jet Lubrication: Removal and Fitting 2138−1/A2..............
Piston Rod Gland: Dismantling and Assembling, Measuring the Wear 2303−1/A1.........
oCylinder Cover
−Removal and Fitting of Cylinder Cover and Water Guide Jacket 2708−1/A1............
−Loosening and Tensioning of Cylinder Cover Elastic Studs 2708−2/A1................
−Machining of Sealing Face for Injection Valve 2708−3/A1............................
Injection Valve: Checking, Dismantling, Assembling and Adjusting 2722−1/A1............
Starting Air Valve: Removal, Fitting and Dismantling, Grinding-in and Assembling2728−1/A1
Relief Valve for Cylinder Cover 2745−1/A1...........................................
oExhaust Valve
−Removal and Fitting of Exhaust Valve, Replacing of Elastic Studs 2751−1/A1..........
−Dismantling and Assembling 2751−2/A1..........................................
−Replacing and Grinding the Valve Seat 2751−3/A1.................................
−Grinding the Seating Surface on the Valve Head 2751−4/A1.........................

RT-flex58T-D Maintenance 0002−1/A1
Table of Contents
Winterthur Gas & Diesel Ltd. 3/ 5 V2 / 2013-08
Crankshaft, Connecting Rod and Piston Group 3
Crankshaft: Measuring Crank Deflection 3103−1/A1..................................
oVibration Damper
−Taking a Silicone Fluid Sample 3130−1/A1........................................
−Inspection (GEISLINGER Vibration Damper) 3130−2/A1............................
Axial Damper: Dismantling and Assembling 3140−1/A1................................
Turning Gear: Checking the Toothing 3206−1/A1......................................
Crankcase: Utilization of Working Platform 3301−1/A1................................
oConnecting Rod
−Loosening and Tensioning the Connecting Rod Studs 3303−1/A1....................
−Inspection, Removal and Fitting of Bottom End Bearing 3303−2/A1...................
−Inspection, Removal and Fitting of Top End Bearing 3303−3/A1......................
−Removal and Fitting 3303−4/A1..................................................
−Removal of Bearing Cover to Top End Bearing 3303−5/A1..........................
oCrosshead
−Checking the Clearances and Fitting the Guide Shoes 3326−1/A1....................
−Removal and Fitting of a Crosshead Pin 3326−2/A1................................
oPiston
−Removal and Fitting 3403−1/A1..................................................
−Changing the Compression Shims 3403−2/A1.....................................
−Dismantling and Assembling 3403−3/A1..........................................
−Checking Piston Top Surface 3403−4/A1..........................................
oPiston Rings
−Checking Piston Ring Wear (Piston with four Piston Rings) 3425−1/A1................
−Checking Piston Ring Wear (Piston with three Piston Rings) 3425−1/A2...............
Driving Wheels and Shut-off Valve for Starting Air Group 4
oDriving Wheels
−Checking the Running and Backlash Clearances and Condition of Teeth 4103−1/A1....
−Replacing the Gear Wheel on Crankshaft 4103−3/A1...............................
Shut-off Valve for Starting Air: Cleaning and Function Check 4325−1/A1.................

RT-flex58T-D
Maintenance0002−1/A1
Table of Contents
4/ 5 Winterthur Gas & Diesel Ltd.
2013-08 / V2
Supply Unit, Injection and Exhaust Valve Control Group 5
oSupply Unit
−Removal and Fitting of Servo Oil Pump and Servo Oil Pump Drive 5552−1/A1.........
−Removal and Fitting of Camshaft and Bearing Shells 5552−2/A1.....................
−Removing and Fitting the Gear Wheel on Camshaft 5552−3/A1......................
−Removal and Fitting 5552−4/A1..................................................
−Lubrication of Supply Unit During Maintenance Works 5552−5/A1....................
Fuel Pump: Dismantling and Assembling 5556−1/A1..................................
Fuel Pressure Control Valve: Removal, Fitting, Dismantling and Assembling 5562−1/A1....
Fuel Overpressure Safety Valve: Checking and Setting 5562−2/A1......................
Injection Control Unit: Removal and Fitting 5564−1/A1.................................
Pressure Reducing Valve 8.11−1: Checking the Gas Pre-charge Pressure 5610−1/A1.....
Exhaust Valve Control Unit:
Removal, Fitting, Dismantling and Assembling 5612−1/A1..............................
oRegulating Linkage
−Adjusting: with Heinzmann StG 10-01 Actuator 5801−1/A1..........................
−Adjusting:with Woodward ProAct II −Analog Actuator 5801−1/A2....................
Scavenge Air Receiver and Auxiliary Blower Group 6
Scavenge Air Receiver: Checking the Air Flaps
and Cleaning the Scavenge Air Receiver 6420−1/A1..................................
Auxiliary Blower: Maintenance 6545−1/A1............................................
oScavenge Air Cooler
−Cleaning (Water Side) on Engine at Standstill 6606−1/A1...........................
−Removal and Fitting of Tube Stack 6606−2/A1.....................................
oWater Separator
−Maintenance of Water Separator (1-part Water Separator) 6708−1/A1................
−Maintenance of Water Separator (2-part Water Separator) 6708−1/A2................
Cylinder Lubrication Group 7
Lubrication Pump CLU4−C: Checking the Gas Pre-charge Pressure 7218−1/A2...........
Piping Group 8
Exhaust Waste Gate (Low-Load Tuning) 8135−1/A1...................................
HP Servo Oil Pipe: Removing, Fitting and Regrinding 8447−1/A1.......................
Hydraulic Pipe for Exhaust Valve Drive: Removing, Fitting and Regrinding 8460−1/A1.....
HP Pipe to Injection Valve: Removing, Fitting and Regrinding 8733−1/A1.................
HP Fuel Pipe: Removing, Fitting and Regrinding 8752−1/A1............................

RT-flex58T-D Maintenance 0002−1/A1
Table of Contents
Winterthur Gas & Diesel Ltd. 5/ 5 V2 / 2013-08
Crank Angle Sensor Unit, Tools Group 9
Crank Angle Sensor Unit: Dismantling, Assembling and Adjusting 9223−1/A1.............
Tools: Explanation 9403−1/A1......................................................
Hydraulic Jacks and Pumps: Arrangement and Application 9403−2/A1...................
oHydraulic Pre-tensioning Jacks
−Storing, Servicing and Maintenance 9403−3/A1....................................
−General Application Instructions 9403−4/A1.......................................
oTool List 9403−5/A1...........................................................................
−Standard Tools Pages 1 −32..................................................
−Recommended Special Tools Pages 33 −35......................................
−Special Tools Obtainable on Loan Pages 36 & 37..................................

Intentionally blank
Table of contents
Other WinGD Engine manuals
Popular Engine manuals by other brands
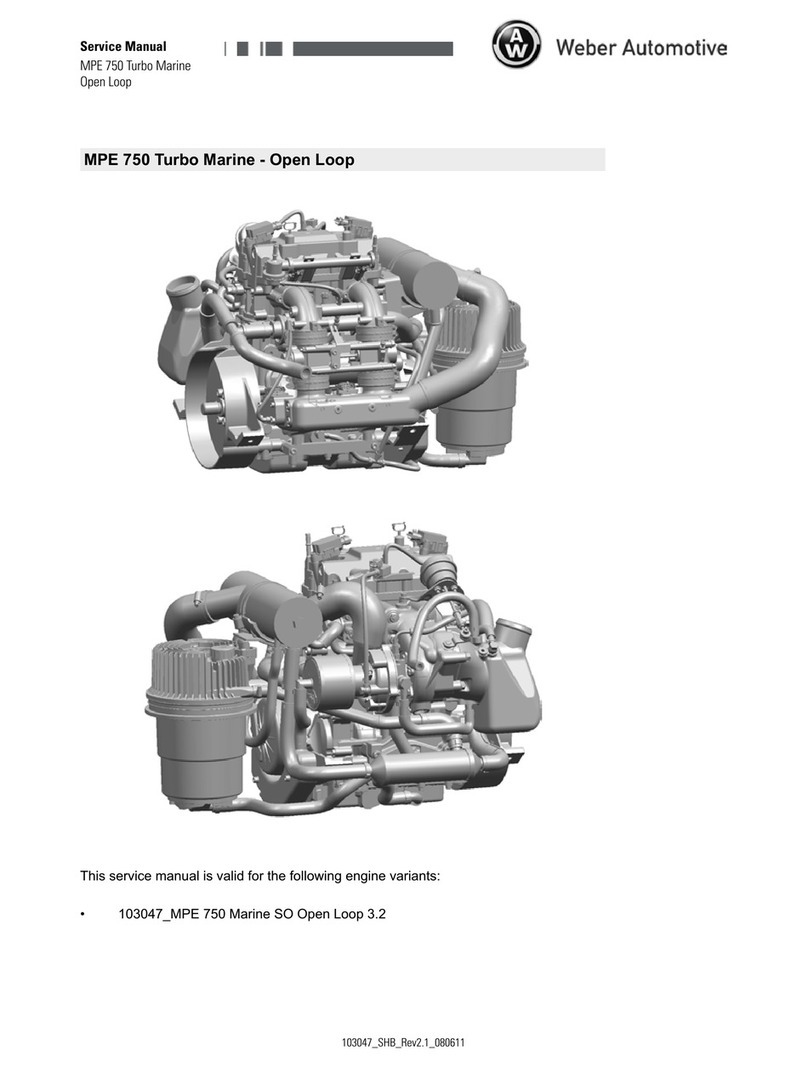
Weber
Weber MPE 750 Turbo Marine Service manual
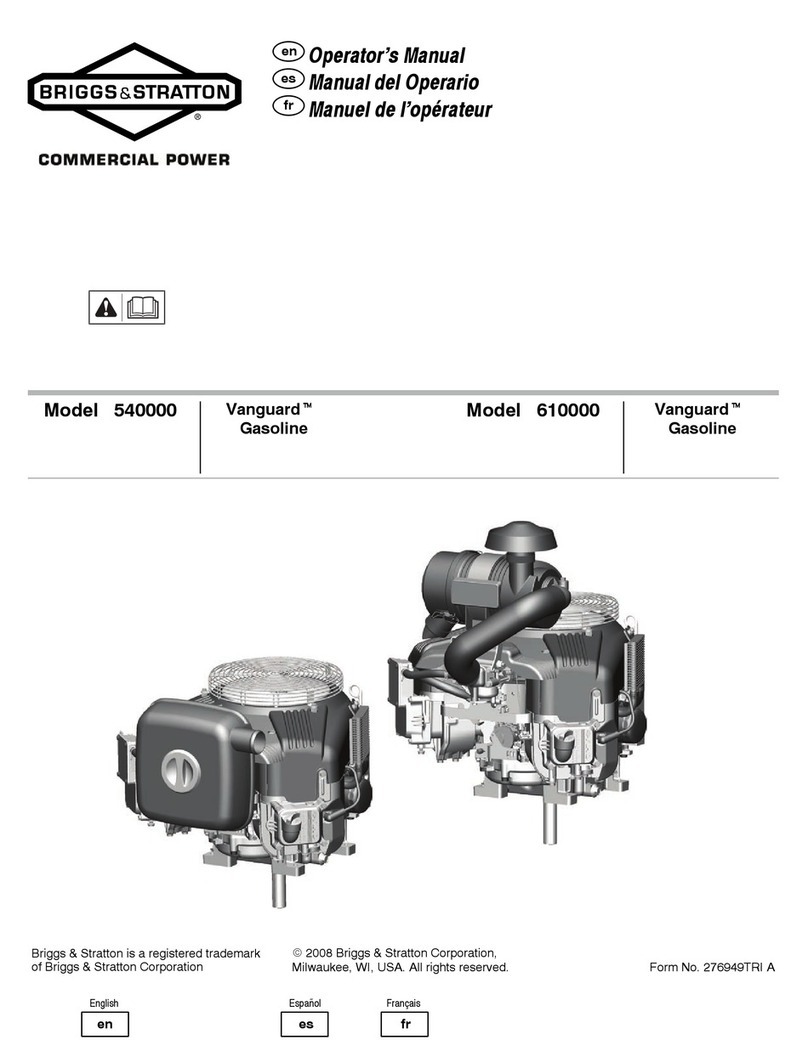
Briggs & Stratton
Briggs & Stratton Vanguard 540000 Series Operator's manual
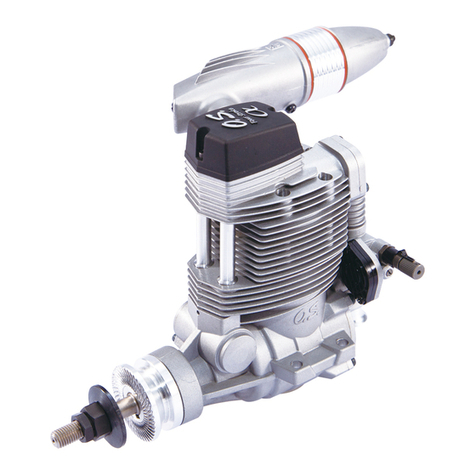
O.S. engine
O.S. engine FSa-155-P Owner's instruction manual

MTU
MTU V 4000 M70 operating instructions

Magnetic
Magnetic BR Series Operation and maintenance manual
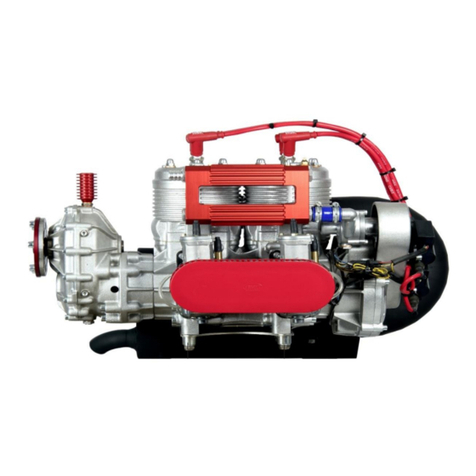
SIMONINI
SIMONINI Victor 2 Plus Operator's manual