ACS TC110 Series Guide

TC110 SERIES
WATER TEMPERATURE CONTROL UNITS
Part Number: 882.03888.00
Revision Date: 09.19.2018
OPERATION AND INSTRUCTION MANUAL
TC11O

TC110 Series
Water Temperature Control Units 882.03888.00 •09/19/2018 2
Write down your serial numbers here for future reference:
_________________________ _________________________
_________________________ _________________________
_________________________ _________________________
We are committed to product improvement.
Specifications, appearance, and dimensions described in this manual are subject to change without
notice.
DCN No. ____________
© Copyright 2018 All rights reserved.

TC110 Series
Water Temperature Control Units 882.03888.00 •09/19/2018 3
Shipping Info
Inspecting Packaging and Equipment
Please inspect all packaging for any damage prior to unpacking. If you see any damage to
the packaging, please take pictures of the packaging prior to unpacking the equipment.
Once the pictures are taken of the packaging, take pictures of the equipment as well.
If the packaging is damaged, write Damaged Freight on the delivery receipt. If we find the
equipment is damaged, a claim can be filed.
Thoroughly check the equipment for any damage that might have occurred in transit, such
as broken or loose wiring and components, loose hardware and mounting screws, etc.
Please take pictures of the damage.
In the Event of Shipping Damage
According to the contract terms and conditions of the Carrier, the freight claims are filed by
the terms below.
If the order is prepaid, ACS Group is responsible for the freight payment. ACS will file the
claim with the truck line. We need pictures of the damaged freight and a copy of the
delivery receipt marked Damaged Freight. ACS must be notified within 24 hours of any
damage. The driver should give you a claim number before they leave your facility.
If the order is collect or third party billing to a customer’s account, the customer is
responsible to file the claim with the truck line. You will need pictures of the damaged
freight and a copy of the delivery receipt marked Damaged Freight to file the claim. The
driver should give you a claim number before they leave your facility.
Advise customer service regarding your wish for assistance and to obtain an RMA (Return
Material Authorization) number. If you need assistance contact the shipping supervisor for
assistance at 262-641-8600.
Hold the damaged goods and packing material for the examining agent’s inspection. Do not
return any goods before the transportation company’s inspection and authorization and
you have received your RMA (Return Material Authorization) number from ACS.
A certified copy of our invoice is available upon request. The original Bill of Lading is
attached to our original invoice. If the shipment was prepaid and ACS is responsible for the
freight, we will submit the claim. You will need pictures of the freight, a copy of the delivery
receipt marked damaged freight and the claim number.

TC110 Series
Water Temperature Control Units 882.03888.00 •09/19/2018 4
If the Shipment is Not Complete
Check the packing list as back-ordered items are noted on the packing list. You should
have:
Temperature control unit
Bill of lading
Packing list
Operating and Installation manual
Electrical schematic and panel layout drawings
Re-inspect the container and packing material to see if you missed any smaller items during
unpacking.
If the Shipment is Not Correct
If the shipment is not what you ordered, contact the shipping department immediately.
Please call 262-641-8600: Have the order number and item number available.
Hold the items until you receive shipping instructions. Do not return any goods before
receiving your RMA (Return Material Authorization) number from ACS.
Returns
Do not return any goods before receiving your RMA (Return Material Authorization)
number and shipping instructions from ACS.

TC110 Series
Water Temperature Control Units 882.03888.00 •09/19/2018 5
Table of Contents
CHAPTER 1: SAFETY......................................................................7
1-1 How to Use This Manual ...............................................................................................7
Safety Symbols Used in this Manual......................................................................... 7
1-2 General Safety Regulations............................................................................................8
1-3 Responsibility ..............................................................................................................8
1-4 Warnings and Precautions .....……………………………………………………………..9
CHAPTER 2: FUNCTIONAL DESCRIPTION ......................................12
2-1 Introduction ..............................................................................................................12
2-2 Necessary Documents ................................................................................................12
2-3 Models Covered.........................................................................................................13
2-4 Standard Features......................................................................................................13
2-5 Available Options .......................................................................................................14
CHAPTER 3: INSTALLATION.........................................................16
3-1 Installation Location Considerations.............................................................................16
3-2 Process Approach Temperature Considerations.............................................................16
3-3 External Piping Sizing Considerations............................................................................16
3-4 Piping Considerations for Permanent Installations .........................................................17
3-5 Piping Considerations for High Mobility Installations......................................................17
3-6 Process Water Considerations .....................................................................................18
Raw Water ..........................................................................................................18
3-7 Making Process Water Connections .............................................................................18
TO PROCESS —1½” NPT........................................................................................18
FROM PROCESS —1½” NPT...................................................................................18
3-8 Making Cooling Water Connections..............................................................................19
Water In —¾” .....................................................................................................19
Water Out ...........................................................................................................19
Pressure Relief —¾” ............................................................................................19
3-9 Making System Purge Connections...............................................................................20
3-10 Making Electrical Connections .....................................................................................22
CHAPTER 4: OPERATION.............................................................24
4-1 Introduction ..............................................................................................................24
4-2 Startup Checklist ........................................................................................................24
4-3 Starting the Temperature Control Unit .........................................................................25
4-4 Sequence of Operation ...............................................................................................26
4-5 Identifying Mechanical Controls and Features ...............................................................27
To Process Thermocouple .....................................................................................27
Safety Thermostat ................................................................................................27
Pressure Relief Valve ............................................................................................27

TC110 Series
Water Temperature Control Units 882.03888.00 •09/19/2018 6
Low Pressure Cutout Switch ..................................................................................27
Pumps.................................................................................................................27
Heaters ...............................................................................................................28
Solenoid Valves....................................................................................................28
Water Hammer Arrestor (Shock Stop)- Optional ......................................................28
Pump Starter .......................................................................................................28
Transformer.........................................................................................................28
Heater Contactor..................................................................................................28
Cooling................................................................................................................28
Electricals ............................................................................................................29
Automatic Vent....................................................................................................29
Pressure Switch....................................................................................................29
4-6 The microprocessor Controller.....................................................................................29
4-7 Controller Display.......................................................................................................30
4-8 Checking Motor Rotation Direction ..............................................................................31
Maintenance........................................................................................................32
4-9 Preventative Maintenance ..........................................................................................33
Every Six Months ..................................................................................................33
4-10 Corrective Maintenance..............................................................................................33
Electrical Connections ...........................................................................................35
4-11 Safety Devices ...........................................................................................................35
Motor Overload ...................................................................................................35
Pressure Switch....................................................................................................35
Safety Thermostat ................................................................................................37
4-12 Cleaning and Storage..................................................................................................38
CHAPTER 5: TROUBLESHOOTING ................................................39
5-1 Introduction ..............................................................................................................39
5-2 Troubleshooting Problem-Solution chart.......................................................................40
CHAPTER 6: APPENDIX ...............................................................43
6-1 Customer Satisfaction Warranty Program .....................................................................43
8-2 Technical Assistance...................................................................................................45

TC110 Series
Water Temperature Control Units 882.03888.00 •09/19/2018 7
Chapter 1: Safety
1-1 How to Use This Manual
Use this manual as a guide and reference for installing, operating, and maintaining your
machine. The purpose is to assist you in applying efficient, proven techniques that enhance
equipment productivity.
This manual covers only light corrective maintenance. No other maintenance should be
undertaken without first contacting a service engineer.
The Functional Description section outlines models covered, standard features, and safety
features. Additional sections within the manual provide instructions for installation, pre-
operational procedures, operation, preventive maintenance, and corrective maintenance.
The Installation chapter includes required data for receiving, unpacking, inspecting, and
setup of the machine. We can also provide the assistance of a factory-trained technician to
help train your operator(s) for a nominal charge. This section includes instructions, checks,
and adjustments that should be followed before commencing with operation of the
machine. These instructions are intended to supplement standard shop procedures
performed at shift, daily, and weekly intervals.
The Operation chapter includes a description of electrical and mechanical controls, in
addition to information for operating the machine safely and efficiently.
The Maintenance chapter is intended to serve as a source of detailed assembly and
disassembly instructions for those areas of the equipment requiring service. Preventive
maintenance sections are included to ensure that your machine provides excellent, long
service.
The Troubleshooting chapter serves as a guide for identification of most common problems.
Potential problems are listed, along with possible causes and related solutions.
The Appendix contains technical specifications, drawings, schematics, parts lists, and
available options. A spare parts list with part numbers specific to your machine is provided
with your shipping paperwork package. Refer to this section for a listing of spare parts for
purchase. Have your serial number and model number ready when ordering.
Safety Symbols Used in this Manual
The following safety alert symbols are used to alert you to potential personal injury hazards.
Obey all safety messages that follow these symbols to avoid possible injury or death.
DANGER! DANGER indicates an imminently hazardous situation that, if not avoided,
will result in death or serious injury.
WARNING! WARNING indicates a potentially hazardous situation or practice that, if
not avoided, could result in death or serious injury.
Caution! CAUTION indicates a potentially hazardous situation or practice that, if not
avoided, may result in minor or moderate injury or in property damage.

TC110 Series
Water Temperature Control Units 882.03888.00 •09/19/2018 8
1-2 General Safety Regulations
These regulations should be read, understood and periodically reviewed by all personnel
involved in any way with this machine.
Never operate or remove any machine components that are secured by mechanical
fasteners unless the motor is electrically locked out and all moving parts are motionless.
Do not circumvent the safety interlocks.
Extreme care should be taken to see that all bolts and threaded pipe connections are
properly tightened at all times during the operation of the machine.
1-3 Responsibility
These machines are constructed for maximum operator safety when used under standard
operating conditions and when recommended instructions are followed in the maintenance
and operation of the machine.
All personnel engaged in the use of the machine should become familiar with its operation
as described in this manual.
Proper operation of the machine promotes safety for the operator and all workers in its
vicinity.
Become familiar with materials, inspection, limitations, maintenance, and total user
responsibility while using or servicing the equipment.
Each individual must take responsibility for observing the prescribed safety rules as outlined.
All caution, warning and danger signs must be observed and obeyed. Any actual or potential
dangerous conditions must be reported to your immediate supervisor.

TC110 Series
Water Temperature Control Units 882.03888.00 •09/19/2018 9
1-4 Warnings and Precautions
Our machines are designed to provide safe and reliable operation when installed and operated
within design specifications, and follow national and local safety codes.
To avoid possible personal injury or equipment damage when installing, operating, or
maintaining this machine, use good judgment and follow these safe practices:
LEARN AND OBEY your company’s safety policy regarding mechanical and
electrical equipment.
MOVING OR LIFTING THE MACHINE: Although our equipment is built and
engineered for great ruggedness in operation, care must be taken when moving the
machine along the floor or lifting it. Damage may occur to sheet metal covers,
electrical cabinets, or small brackets if pressure is applied to them when moving the
machine. When lifting the machine, be certain of total machine weight does not
exceed the capability of the lifting equipment.
EQUIPMENT LOCATION: Adequate area for routine maintenance should be
provided in order to open the machine for service. Proper service area clearances also
should allow people who are working on the machine to be clearly visible to others,
thereby reducing the potential safety hazards.
SAFE HOUSEKEEPING: The work area must be kept clean and uncluttered during
periods of operation or maintenance. No hand tools or other metal objects should be
left on or around the machine.
SAFETY GLASSES OR A FACE SHIELD MUST ALWAYS BE WORN
when servicing or operating the machine.
EAR PROTECTION: The Occupational Safety and Health Act of 1970 has
established guidelines for Permissible Noise Exposures (OSHA 1910.95) that should
be followed.
NEVER attempt to operate the machine unless it is fully assembled with all guards
and interlocks in place and functional.
OBSERVE all danger, warning, caution and safety labels on the equipment.
Upon completion of any machine maintenance, be certain ALL SAFETY GUARDS
AND COVERS are securely and properly fastened prior to resuming machine
operation. All fasteners must be in place and properly tightened. ANY
SHORTCUTS MAY RESULT IN INJURY TO PERSONNEL OR DAMAGE
TO EQUIPMENT.
NEVER wear any loose fitting clothes, neckties, or dangling items such as earrings,
belts, or shoestrings. Jewelry, such as wristwatches, bracelets, or rings should
NEVER be worn. Long hair must be tied back or placed in a tight fitting hairnet.
NEVER lean against or rest hands or feet on the equipment when it is in operation or
open for maintenance. NEVER stand on the machine when it is in operation.
ROTATION OF MOTORS: The correct rotating direction for the machine motor is
clearly marked on the machine. Always check for proper rotation of motors. Incorrect
rotation direction can cause severe damage.
ELECTRICAL GROUNDING: All electrical equipment on the machine must be
grounded in accordance to all local codes and Article 250 of the National Electric
Code.

TC110 Series
Water Temperature Control Units 882.03888.00 •09/19/2018 10
ALWAYS DISCONNECT AND LOCKOUT the main electrical power to the
machine before performing any service.
SAFETY INTERLOCKS MUST NOT BE BYPASSED. The mechanical and
electrical safety interlocks ensure the safety of personnel. They should never be
tampered with or removed for ANY reason. They should be checked frequently by a
qualified mechanic for proper operation.
NEVER modify the machine configuration or any individual component without
written notice from the factory.
We have long recognized the importance of safety and have designed and manufactured our
equipment with operator safety as a prime consideration. We expect you, as a user, to abide
by the foregoing recommendations in order to make operator safety a reality.

TC110 Series
Water Temperature Control Units 882.03888.00 •09/19/2018 11
Figure 1: Safety Tags and Warning Labels

TC110 Series
Water Temperature Control Units 882.03888.00 •09/19/2018 12
Chapter 2: Functional Description
2-1 Introduction
TC110 Series water temperature control units are reliable, accurate, and easy-to-use
process temperature control units. They are self-contained, portable, and shipped ready to
use.
The TC110 Series water temperature control unit is designed to circulate water through your
process and to precisely, automatically, and reliably maintain it at a specified temperature.
Standard unit operating range is from 32°F (0°C) to 250°F (121°C). The unit is suited for use
with city water, water from portable or central chillers or towers, or well water.
These units are designed for rapid recirculation of a relatively small amount of water to
provide close and uniform temperature relation between To Process and From Process lines.
This performance, of course, depends on the configuration of your process and any
restrictions within the mold. The recirculation, combined with the large immersion heater
and cooling capability, gives fast and accurate response to bring the water up to
temperature or to changes in the settings when needed.
The TC110 Series water temperature control unit is a self-contained system consisting of a
centrifugal pump, electric immersion heater, cool/vent solenoid valve, and electrical control,
including a PID microprocessor controller and thermocouple. It is designed for use in
process temperature control applications using water or a water/glycol mix. Any other use
or fluid is prohibited.
Some standard safety devices include a mechanical over temperature safety thermostat, a
pressure relief valve, motor overload protection, a low pressure cutout switch and branch
fusing.
A properly installed, operated, and maintained TC110 Series system provides years of
reliable operation. Please read and follow the instructions in this manual to get the most
satisfaction from your TC110 Series system.
2-2 Necessary Documents
The following documents are necessary for the operation, installation, and maintenance of
TC110 Series water temperature control units. Additional copies are available from the
manufacturer.
Familiarize the appropriate personnel with these documents:
This manual.
The controller operation manual.
The electrical schematic and connection diagram placed inside the
control enclosure.

TC110 Series
Water Temperature Control Units 882.03888.00 •09/19/2018 13
The operation and installation manuals for accessories and options
selected by the customer.
The Customer Parts List included in the information packet.
2-3 Models Covered
This manual provides operation, installation, and maintenance instructions for the TC110
Series water temperature control unit.
Make sure that you know the model number, serial number, and operating voltage of your
temperature control unit if you contact the manufacturer.
2-4 Standard Features
Compact, rugged cabinet with easy-access side panels
Incoloy™ immersion heaters with IEC contactors
NEMA 1 electrical enclosure
Independent high temperature safety thermostat
Motor Circuit Protector for pump
¼” cooling solenoid valve
EPDM/Carbon-silicon carbide pump seal
Adjustable low supply water pressure switch; factory-set at 16
psig (110 kPa/1.1 bar)
150 psig (1034 kPa/10.3 bar) pressure relief valve
Choice of 230V or 460V operating voltages
3/4” water supply; drain connection size matches valve size; 1-
1/2” process connections
Automatic vent sequence
Operating range of 32°F to 250°F (-0°C to 121°C)
One (1) -year parts and labor warranty at the factory; three (3)
-year controller warranty
Quick Cool
.

TC110 Series
Water Temperature Control Units 882.03888.00 •09/19/2018 14
2-5 Available Options
TC110 Series systems are available with options to tailor the unit to your requirements.
Some are factory installed; some can be retro-fitted in the field. Consult your ACS Group
sales representative for more information. Available options include:
Heaters upgrade available to 12 kW
Manual bypass
Auto system water purge (mold purge)
Y-strainer
Hammer arrestor (water hammer shock stop)
Rubber feet available in lieu of casters
½” or ¾” cooling solenoid valves available on all sizes
Two-zone stack rack with casters, common wiring and piping
available
Electrical operation available in three phase 230 and 460 volts, 60
Hz
Figure 1
Typical Control Unit and Specifications
Direct Injection

TC110 Series
Water Temperature Control Units 882.03888.00 •09/19/2018 15
Model
Dimensions
Shipping
Number
Pump
H
W
D
weight
460 / 230
hp
kW
gpm
lpm
psig
kPa
in.
cm
in.
cm
in.
cm
lbs.
Kg
TC110
9 kW heater
¾
0.56
30
114
25
172
25¾”
65.4
12”
30.5
23”
58.4
210
96
1
0.75
35
133
30
207
2
1.50
50
189
30
207
3
2.24
60
227
35
241
5
3.73
75
284
54
372
240
109
7½
5.60
90
454
63
434
Figure 2: TC110 Series Unit Full-Load Amps
Model
Full-load amps at 460 volts
hp
kW
9 kW heater
12 kW heater
0.75 hp
0.56 kW
12.7 amps
16.5 amps
1.00 hp
0.75 kW
13.1 amps
16.9 amps
2.00 hp
1.50 kW
14.7 amps
18.5 amps
3.00 hp
2.24 kW
16.1 amps
19.9 amps
5.00 hp
3.73 kW
18.9 amps
22.7 amps
7.50 hp
5.60 kW
22.3 amps
26.1 amps

TC110 Series
Water Temperature Control Units 882.03888.00 •09/19/2018 16
Chapter 3: Installation
3-1 Installation Location Considerations
TC110 Series systems are portable and can be installed almost anywhere. As with all
equipment installations, follow all applicable codes and regulations.
The recommended ambient temperature range for TC110 Series installations is from
32°F (0°C) to a maximum operating ambient temperature of 131°F (55°C).
Recommended ambient storage temperature range is from -13°F to 149°F (-25°C to
65°C). If storing the unit below freezing temperatures, make sure the unit has an
antifreeze mixture circulated inside.
Provide a minimum of twelve inches (12” or about 30 cm) clearance on all sides of
the cabinet to allow circulation of cooling air.
Locate the unit as close to the process as is practical.
3-2 Process Approach Temperature Considerations
If the differential () between COOLING WATER IN and TO PROCESS temperatures is less
than 10°F (5.5°C), consult our Sales Department for advice on how to control low approach
applications.
3-3 External Piping Sizing Considerations
All external hose and piping should be adequately sized to assure minimum external
pressure drop.
Low external piping pressure drop is needed for best operation.
Use a backup wrench to support TC110 Series system piping when making process
piping connections.
All external valves, fittings, and hoses must be rated at a minimum of
150 psig and 250°F (1034 kPa/10.3 bar and 121°C).

TC110 Series
Water Temperature Control Units 882.03888.00 •09/19/2018 17
3-4 Piping Considerations for Permanent Installations
An optional (or customer-installed) strainer on the COOLING WATER IN inlet is
recommended
The unit must have at least 16 psig (110 kPa/1.1 bar) water supply pressure to prevent
pump cavitation that can be caused by the water “flashing” to steam. To avoid damage to
the pump or other components, make sure that maximum supply pressure does not exceed
75 psig (517 kPa/5.2 bar).
Keep restrictions to a minimum by using proper inlet pipe sizing. If the water supply piping is
larger than ¾”, reduce the size at the unit. The table below contains the pipe sizes that are
used in the unit.
Pipe sizes for ¾ hp to 7.5 hp (0.56 kW to 5.59 kW) units
Location
Size in inches NPT
To Process
1½”
From Process
1½”
Cooling Water In
¾”
Cooling Water Out
- depends on solenoid valve used -
Common black pipe is recommended for permanent installations. TC110 Series water circuit
piping is primarily ferrous (iron) and reacts electro-chemically with non-ferrous metallic
materials such as copper. Some water contains dissolved minerals that greatly accelerate
the reaction between dissimilar metals.
Ferrous piping is recommended to minimize galvanic action. If piping must be copper, use
dielectric unions at the unit.
3-5 Piping Considerations for High Mobility Installations
Mobile TC110 Series systems must use high quality hose rated for at least 150 psig and
250°F (1034 kPa/10.3 bar and 121°C).
Quick disconnects may be used for mobility, although they cause a drop in pressure. If used,
they must be sized carefully to minimize pressure drop. Don’t use quick disconnects with
check valves unless absolutely necessary.
Non-relieving quick connect fittings or check valves on the water supply must have a
pressure relief piped to the drain.
Failure to do so could result in a dangerous over-pressure condition!

TC110 Series
Water Temperature Control Units 882.03888.00 •09/19/2018 18
3-6 Process Water Considerations
Raw Water
Water treatment is vital in any piping system. In some cases, raw water may be used in the
system without problems; in other cases, it can result in large deposits of scale and
corrosion.
The ACS Group offers a complete line of water treatment equipment. Contact your sales
representative for water testing and treatment options.
3-7 Making Process Water Connections
On the back of each unit, the connections are labeled appropriately. Connect the TO
PROCESS hookup to the entrance of the process and the FROM PROCESS hookup to the exit
of the process. Connect the COOLING WATER
IN to your plant water supply. Connect the COOLING WATER OUT line to an open drain, or
to the return line of your central water system.
Make sure you carefully select the connecting lines and connectors between the
temperature control unit and the process to suit the needs and requirements of your
application.
If your unit has a maximum operating temperature of 250°F (121°C), the connecting lines
and connectors should have a service rating of at least 250°F (121°C) and 150 psig (1034
kPa/10 bar).
TO PROCESS —1½” NPT
This is the outlet for the tempered water leading to the process being controlled.
FROM PROCESS —1½” NPT
Water from the process re-enters the TC110 Series system to be tempered and re-circulated
back into the process.

TC110 Series
Water Temperature Control Units 882.03888.00 •09/19/2018 19
3-8 Making Cooling Water Connections
Water In —¾”
The cooling water supply inlet from a cooling tower, a chiller, or a city water supply.
If a non-relieving device such as a regulator, ball valve,
or check valve is installed on the WATER IN line,
you MUST install an expansion tank
of at least ½ gallon (about 2 liters) capacity.
Failure to do so can result in system overpressure from thermal expansion.
Install the tank configured as shown below:
Check the expansion tank frequently to make sure it is not flooded.
Water Out
Size Depends on Solenoid Valve Used
The cooling water outlet leading back to the cooling tower, chiller, or drain.
Net supply pressure should be between 25 psig and 55 psig (172 kPa/1.7 bar and 379
kPa/3.8 bar). Net supply below 15 psig (103 kPa/1.10 bar) may allow water to flash to
steam, cavitate the impeller, and damage the pump, which prevents the unit from cooling
properly. Operation above 55 psig (379 kPa/3.8 bar) may cause premature opening of the
relief valve from pump pressure and pressure surges.
Pressure Relief —¾”
The pressure relief valve, located at the back of the unit.

TC110 Series
Water Temperature Control Units 882.03888.00 •09/19/2018 20
3-9 Making System Purge Connections
TC110 Series systems equipped with the System Purge option have a compressed air inlet
marked MOLD PURGE. Connect to a clean, dry 100 psig (690 kPa/6.9 bar) air line. Install
your own shutoff valve to prevent process liquid from backing up into the plant air piping if
the compressed air is turned off and the check valve fails. Don’t depend on the solenoid
valve to hold water pressure in the temperature control unit.
Figure 3: Typical Piping Schematic
This manual suits for next models
1
Table of contents
Other ACS Control Unit manuals
Popular Control Unit manuals by other brands

Emhart Teknologies
Emhart Teknologies Tucker TMP Series Programming manual
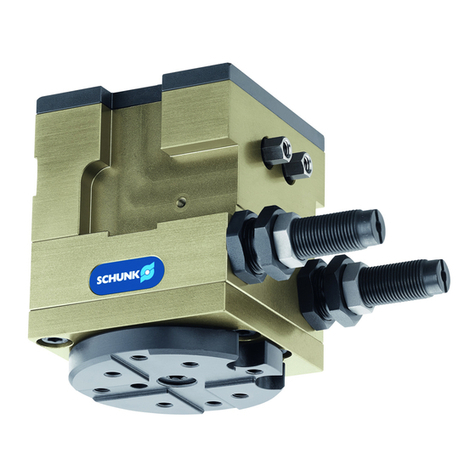
SCHUNK
SCHUNK RM-W Series Assembly and operating manual

Weco
Weco 14K3-XP Installation and user manual

Samson
Samson 2412 Series Mounting and operating instructions

Sony
Sony DSBK-100 operating instructions
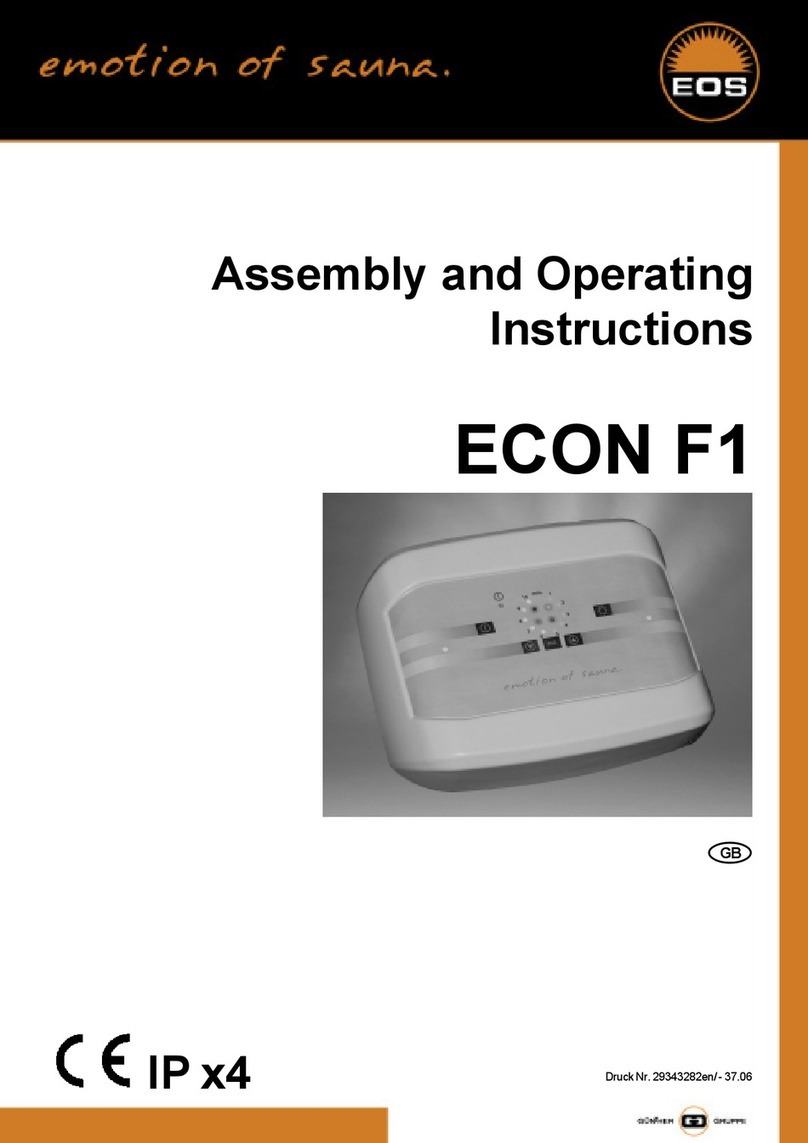
EOS
EOS ECON F1 Assembly and operating instructions
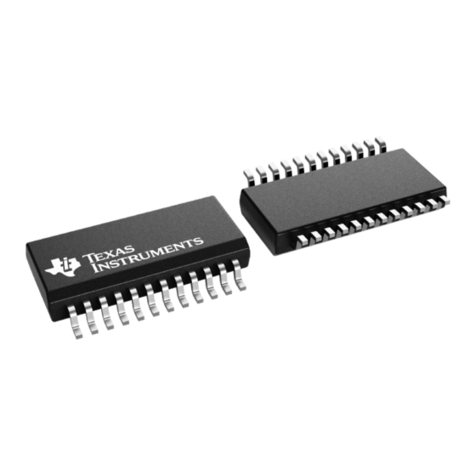
Texas Instruments
Texas Instruments TLC694 Series Technical reference manual
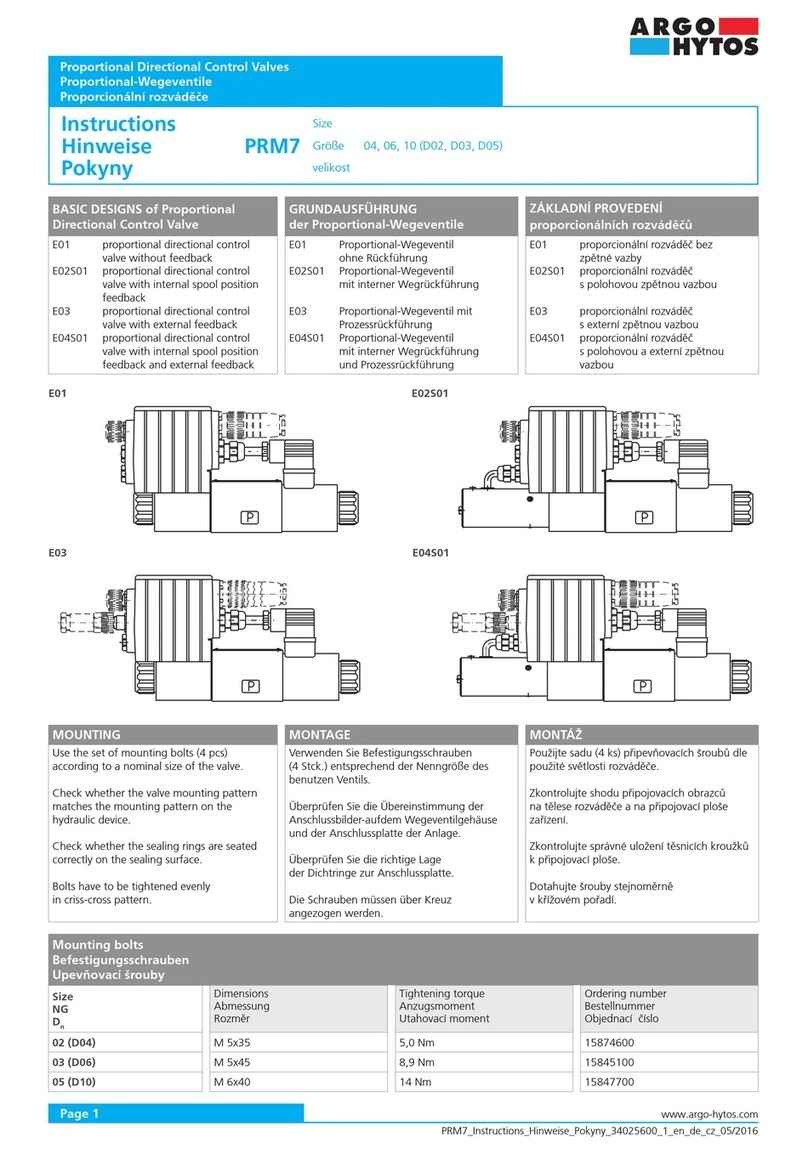
Argo-Hytos
Argo-Hytos PRM7 Series instructions
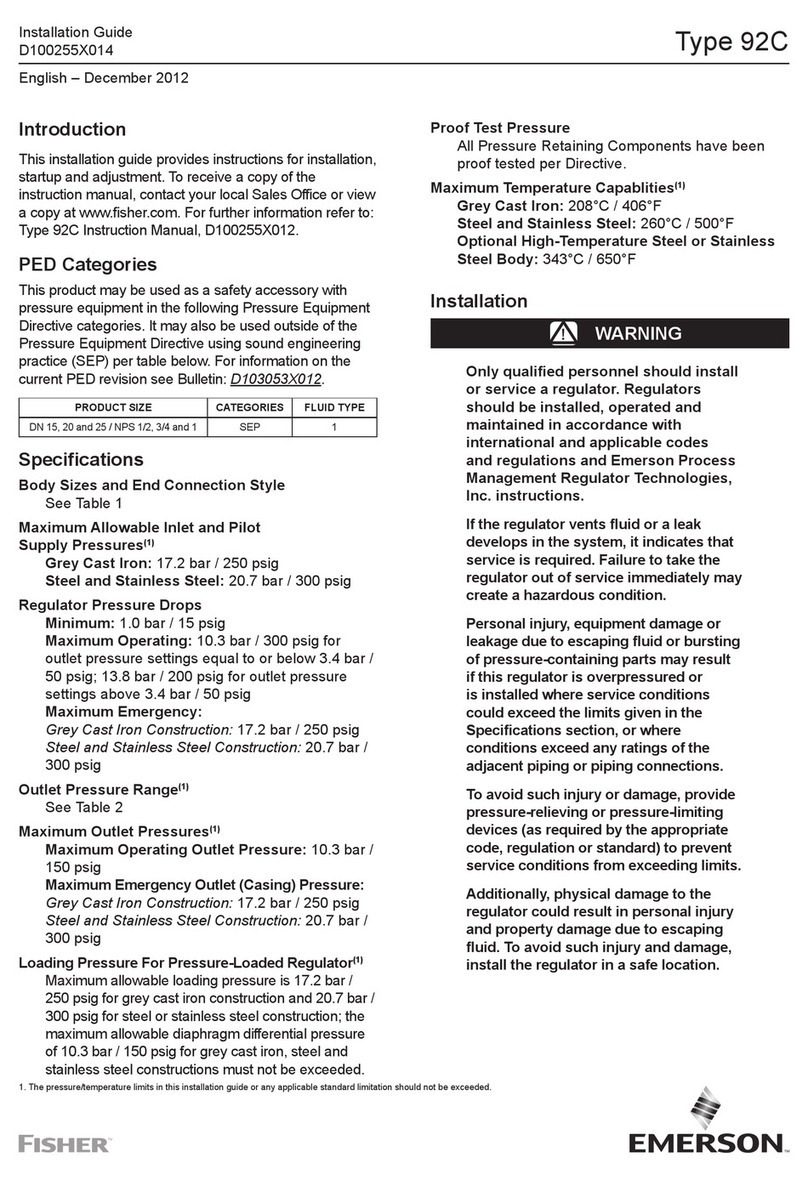
Emerson
Emerson Fisher 92C installation guide
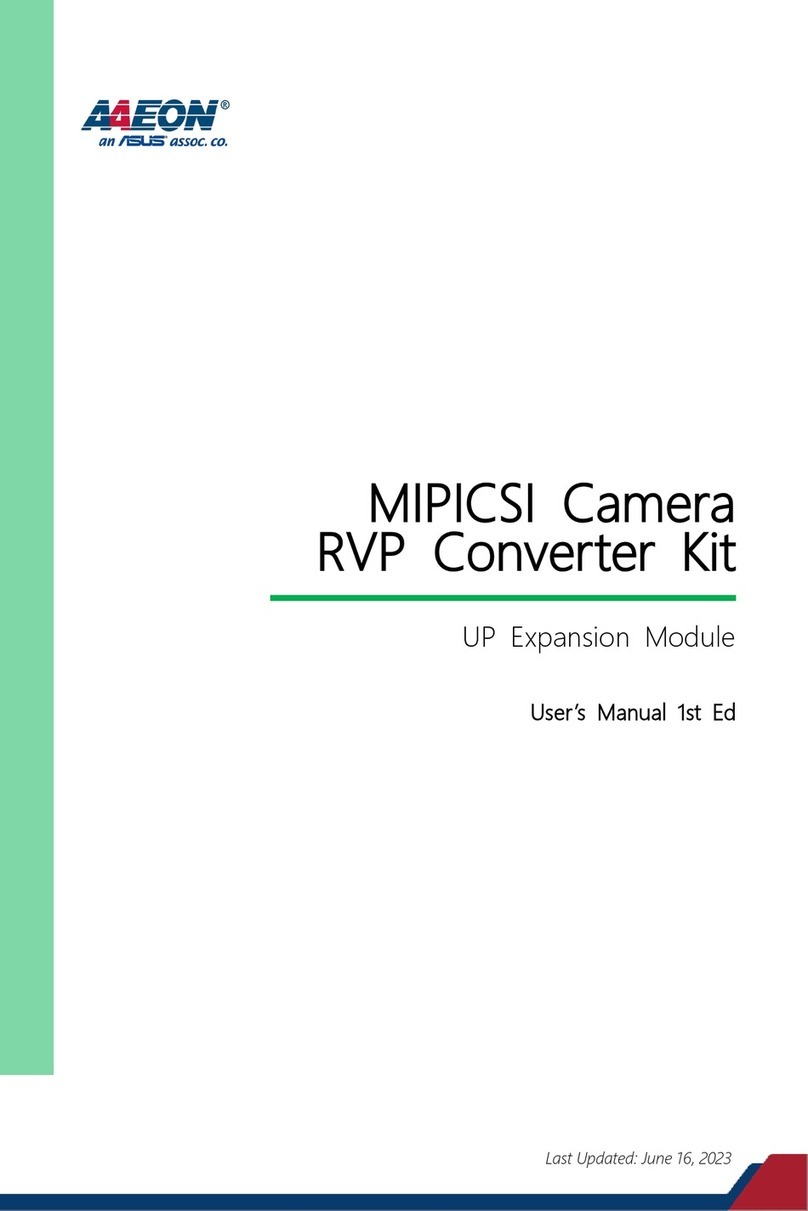
Asus
Asus AAEON MIPICSI Camera RVP Converter Kit user manual

Ebyte
Ebyte E31-400M17S manual

Fibocom
Fibocom L610 MiniPCIe Series Hardware guide