ALFAMATIC Press-Right User manual

Issue 2 - October 11, 2021
I N S T A L L A T I O N M A N U A L
PRESS-RIGHT
equipped with a VIO10 board
•Installation manual

2 Press Right installation

Press Right installation 3
1Press-Right Installation......................................................................................... 4
1.1 Important notes for installation ..................................................................................4
1.2 Instrument operation.................................................................................................4
1.3 The internal boards...................................................................................................5
1.4 Electric Wiring...........................................................................................................5
2Particular functions ............................................................................................. 15
2.1 Configure the job automatic selection......................................................................15
2.2 Connecting an external reset ..................................................................................15
2.3 Additional controls...................................................................................................15
3Instructions to install Press-Right........................................................................ 17
4Mounting the transducers ................................................................................... 21

4 Press Right installation
1 Press-Right Installation
This chapter explains the steps required to install and connect Press-Right to the
equipment and make prepare it for operation.
The Press-Right instrument is designed to work on its own or in combination with a PLC
(see important information in paragraph 1.4.1).
For operation, the Press-Right instrument must be connected to a PLC via a number of
input and output signals. In addition to it, the instrument must be connected to a force
transducer (typically a load cell) and a position transducer (incremental encoder,
potentiometer or transducer with analogue output).
The load cell and the encoder or the potentiometer are powered by the instrument. The
instrument also includes also the amplifiers which are necessary to condition signals from
the transducers.
Press-Right is supplied with serial ModbusTCP and it can be ordered with a PROFINET or
EthernetIP interface.
1.1 Important notes for installation
This manual refers only to the instrument equipped with a VIO10 expansion card.
Press-Right must be powered at 24VDC. It is possible to obtain an optional
internal power supply that allows the direct connection to the mains.
This instrument is not (and could not be used as) a safety device: the descent of
the press must be governed by elements which are external to it. The instrument
simply synchronizes the descent of the press to its operation.
It is very important that the end of the unshielded load cell cable is as short as
possible
When the instrument is equipped with motors, motors must be equipped with a
noise reducing filter and it must be operated by semiconductor devices.
Always connect the instrument container to a earth conductor.
1.2 Instrument operation
Caution: Press-right is not (and could not be used as) a safety device: the descent
of the press must be governed by elements which are external to it. The instrument
synchronizes the descent to its operation. Usually, the GO output must be
connected in series to the cylinder descent chain. In a nutshell, if the instrument
activates the GO enabling output, the cylinder must not descent if it is not safe.
The operation takes place in the following way: when the instrument START input is
operated an external command, Press-Right activates the GO cylinder descent output, if it
is ready and all ENABLE inputs are active. When the GO signal is active, the cylinder must
continue until the instrument deactivates the signal.

Press Right installation 5
When the GO output is active and the instrument touches the piece, the instrument
activates the BOOSTER output.
Based on the stop parameters achieved (quota, strength, etc.), Press-Right deactivates
the GO signal.
After deactivating the GO signal, the instrument continues the monitor the curve until either
the force and the quota begin to decrease, and the cylinder retracts. The piece it classified
as either good or scrap.
If the piece is good, the GOOD output is activated. On the other hand, if the piece is scrap,
the REJECTED output is activated.
The proper encoder zeroing occurs using its zero notch and the T.D.C. cylinder retracted
signal
1.3 The internal boards
Press-Right consists of two circuit boards:
front PR1MB1 mounts a display, a keyboard and a main CPU.
input and output VIO10 Input and output signals, and transducers are connected to this
board.
All boards are manufactured by us.
1.4 Electric Wiring
The following information is used to perform the instrument electrical wiring.
1.4.1 Connect an external controller (PLC)
The PLC connected to Press-Right must be a PNP logic type. The instrument inputs and
outputs are isolated and protected, and as a result they do not need any interface relay.
Signals which are essential for operation are START, GO, GOOD and REJECTED.
Remember that, in all cases, it is always necessary to connect the instrument T.D.C. input.
The T.D.C. signal can be taken directly from a limit switch operated when the press is in
rest position. However, almost every time the press rest signal also serves the PLC; in this
case the signal to be transmitted to the instrument can be taken in parallel to the one that
is transmitted to the PLC.
1.4.2 VIO10 board wiring
Note: this information applies only to the VIO10 board. Make sure the board is exactly this
version.

6 Press Right installation
The wiring relies on several numbered removable terminal boards (X3, X4, X16...). Each
terminal in each terminal board is numbered. The seventh terminal of the X18 terminal
board will be called X18.7. The numbering of the terminal board is also shown on the
board.
Figure 1
Main power supply terminal board (X24)
The electronic part of Press Right and the transducers are powered by 24VDC current via
the three-pole X24 terminal board.
Name
Function
Terminal
0VDC:
Negative power supply cable
X24.1
PE
Grounding
X24.2
+24 Vdc
Positive power supply cable
X24.3
If the internal power supply is present, the switch behind the instrument must interrupt the
phase and the neutral before reaching the transformer. The power supply output is
connected to the X24 terminal board X24.

Press Right installation 7
Input terminal board (X3 and X17)
Inputs are isolated and are compatible with clean contact signals or with 24VDC PNP
transistor output. The X17 input terminal board is optional.
Name
Terminal
Default
Input 0
X3.1
START
Input 8
X3.2
Input 1
X3.3
T.D.C.(1)
Input 9
X3.4
Input 2
X3.5
Input 3
X3.6
Input 4
X3.7
Input 5
X3.8
Input 6
X3.9
Input 7
X3.10
0VDC:
X3.11
Power supply ground
+24 Vdc
X3.12
Positive power supply cable
(1) The T.D.C. input must always be Input 1.
Name
Terminal
Default
Input 10
X17.7
Input 11
X17.8
Input 12
X17.9
Input 13
X17.10
Input 14
X17.11
0VDC
X17.12
.

8 Press Right installation
The function of each input may be set up. Each input can have one of the following
functions:
Name
Preferred
input
Function
START
0
Request to start a new cycle. If removed, the acquisition is interrupted.
T.D.C.(1)
1
The "upper dead point" signal, used as a reset signal for a new cycle and
in "AND" with the encoder zero point for the "zero" of the absolute
dimensions
JOB SELECTOR
These inputs are used to select a job with their binary combination (see
2.1.1).
PHASE SELECTOR
These inputs are used to select a job phase with their binary combination.
BASKET 1
2
Sensor for normal scrap baskets
BASKET 2
3
Sensor for special scrap baskets
BASKET AUTO-CHECK
Sensor for self-test sample baskets
RESET
2
Re-enables the device after a scrap
SESPEND ACQUIRE
It suspends the acquisition of the useful curve on hydraulic or electric
presses, in case of incomplete cycle
ENABLE #
See 2.3
TEST SIGNAL #
#1=4
See 2.3
BOOSTER CYL BACK
Used to repeat a cycle
BOOSTER CYL END
Used to repeat a cycle
MAINTENANCE
5
Disables all commands
TABLE IN POS
Manual slide signal in operating position
IMPULSIVE START
Left=6
Right=7
Request to start a new cycle
NO EMERGENCY
No emergency commands
SAFETY
Safe machine operation (protections closed)
DRIVER ATIVATE
Active Driver (electric press)
IN POSITION
Position reached (electric press)
(1) The T.D.C. input must always be Input 1 and, therefore, clamp X3.3.

Press Right installation 9
Output terminal board (X4 and X17)
Outputs for 24VDC utilities. For inductive loads, such as valves and the relay coils,
mounting a diode in parallel is necessary to prevent surges. All the X17 terminal board and
output 8 of the X4 terminal board are optional.
Name
Terminal
Default
Output 0
X4.1
GOOD
0V
X4.2
Power supply ground
Output 1
X4.3
REJECTED 1
Output 8
X4.4
Output 2
X4.5
GO
Output 3
X4.6
PROTECTION
Output 4
X4.7
Output 5
X4.8
Output 6
X4.9
Output 7
X4.10
Name
Terminal
Default
Output 9
X17.1
Output 10
X17.2
Output 11
X17.3
Output 12
X17.4
Output 13
X17.5
Output 14
X17.6

10 Press Right installation
The function of each output may be set up. Each output can have one of the following
functions:
Name
Default
Function
GOOD
0
Good piece signal Active after the return of the cylinder, until the
following start.
REJECTED 1
1
Normal scrap signal
REJECTED 2
7
Special scrap signal
REJECTED AUTO-CHECK
Sample scrap signal used during self-test
GO
2
Press permission. Active after start, if the device is ready and turned off
when the stop value is reached.
DOOR
3
Protection block command
BUZZER
4
Buzzer command.
TEST OUTPUT
6
Activation signal for TEST SIGNAL 1 See 2.3
CONTACT/BOOSTER
Piece contact signal and start of power phase. Note: this signal is only
activated if the T.D.C. signal is absent
CHECK POINT OUT #
Output activated at a programmable portion (maximum 3 outputs)
PHASE BIT 0
Active during phase 2 and 4
PHASE BIT 1
Active during phase 3 and 4
MANUAL
Active when a job not included in the list of available jobs, is run
BRAKE
Output for shock absorber command
ENABLE RETURN
5
Consents the return of the active cylinder where a good piece is detected
or after reset
ENABLE MANUAL
Command for mechanical press lever electric block
OPEN GREEN BOX
Command to open good piece basket
CLOSE PK TANK
Command to close the tank on PK model thrust units
BLOCK OF THE TABLE
Command to block the manual slide
PULL LEVER
Cylinder command to help cylinder return (for heavy tools)
RESET DRIVER
Driver reset fault (electric press)
ENABLE DRIVER
Enables driver (electric press)
Transducer terminal board (X12)
An incremental encoder, a potentiometer or an analog output encoder may be connected
to the X12 terminal board.
On this terminal board, it is also possible to supply power to the transducers. The encoder
requires a 12VDC (J3A*) or 5VDC (J3B) power supply voltage. The potentiometer requires
a high-precision 10VDC supply voltage.

Press Right installation 11
Name
Terminal
Description
Phase Z
X12.1:
Zero notch signal
Phase B
X12.2:
PHASE B signal
Phase A
X12.3:
PHASE A signal
+VDC
X12.4:
Power supply: J3A with 12V or 5V with J3B
0VDC:
X12.5:
Ground wire
AIN-
X12.6:
Negative analog input cable (for convenience, it can be grounded
with J8
+10VDC
X12.7:
Analog transducer power supply
AIN+
X12.8:
Positive analog input cable
Electrical characteristics of a X12.4 terminal with J3A*
Output voltage
12V ±10%
Continuous output current
200mA
Protection
Current, Temperature
Electrical characteristics of a X12.4 terminal with J3B
Output voltage
5V ±10%
Continuous output current
200mA
Protection
Current, Temperature
Electrical characteristics of a X12.7 terminal
Output voltage
10V
Continuous output current
10mA
Protection
Current, Temperature
X12.1, X12.2 and X12.3 input terminal circuit
X12 analog input selection
J4
J9
J11
J12
Input 0-10 V *
OPEN
IN
IN
OPEN
Input 0-5 V
OPEN
OPEN
IN
OPEN
Input 0-20 mA
IN
IN
IN
OPEN
Input 4-20 mA
IN
IN
OPEN
IN
* default
Load cell terminal board (X11)
Input for resistive bridge load cell with a sensitivity of 2 mV/V, or 0-10V or 0-5V differential
analog input. On this terminal board, the transducer power supply is also available.

12 Press Right installation
Name
Terminal
Description
Gefran TU
AEP TC4
IN+
X11.1
Positive input
Yellow
Yellow
IN-
X11.2
Negative input
Red
White
0V
X11.3
Shielded cable sleeve
Stocking
Stocking
0V
X11.4
Power supply ground
Green
Black
+VDC
X11.5
J10A=10V J10B=5V
White
Red
Electrical characteristics of 10V voltage X11.5 terminal
Output voltage
10V ±10%
Continuous output current
60mA
Protection
Current, Temperature
Electrical characteristics of 5V voltage X11.5 terminal
Output voltage
5V ±10%
Continuous output current
100mA
Protection
Current, Temperature
X11 analog input selection
J5
J6
J7
J10
2mV/V 10V load cell Compression operation *
A
A
OPEN
A
2mV/V 10V load cell Compression and Traction *
B
OPEN
OPEN
A
2mV/V 5V load cell Compression and Traction *
A
OPEN
OPEN
B
Input 0-10V
OPEN
B
IN
A
Input 0-5V
OPEN
B
OPEN
B
* default
Optional 422 encoder terminal (X18)
This terminal board is used to connect an encoder with 422 signals.
Name
Terminal
Description
0V
X18.1:
Signal reference Voltage
ENC_C-
X18.2:
Clock signal - towards servo drive CN5
ENC_C+
X18.3:
Direction signal + towards servo drive CN5
ENC_A-
X18.4:
Clock signal + towards servo drive CN5
ENC_A+
X18.5:
Analogue output 1
ENC_B+
X18.6:
Analogue output 2
ENC_B-
X18.7:
Signal reference Voltage
+VDC
X18.8:
Power supply: J3A with 12V or 5V with J3B
0VDC:
X18.9:
Sleeve

Press Right installation 13
Typical transducer connection

14 Press Right installation
Optional internal serial port terminal board (X23)
If an internal serial connection or a RS485 port must be used, it is possible to connect to
the X15 terminal board via the D-Sub connector. Press Right automatically recognizes and
selects the RS232 or RS485 port; however, two serial ports may not be used at the same
time. The RS485 serial port can be used only to connect to a PLC.
Name
Terminal
Description
0V
X23.1
GND Serial Reference
A+485
X23.2
RS485 interface signal
B-485:
X23.3
RS485 interface signal
Optional analog output terminal board (X16)
On the X16 terminal board, there are two analog outputs. Analog output 1 can be used to
operate a proportional valve to adjust the cylinder operating pressure.
Name
Terminal
Description
CLK+
X16.1
Do not connect
CLK-
X16.2
Do not connect
DIR+
X16.3
Do not connect
DIR-
X16.4
Do not connect
ANA2:
X16.5
Analogue output 2
ANA1:
X16.6
Analogue output 1
0V
X16.7
Signal reference Voltage

Press Right installation 15
2 Particular functions
This chapter describes the particular functions of inputs and outputs.
2.1 Configure the job automatic selection
Press Right supports the automatic selection of jobs by combining inputs or via a bar-code
scanner.
The selection via inputs may be useful to automatically recognize the piece or the tool
mounted.
To enable the automatic selection of jobs, enter in the instrument the maximum number of
selectable jobs and how to select them.
To do this, select from the menu TOOLS > ADVANCED OPTIONS > MACHINE TYPE > CHANNEL
PHASE JOBS and change the value Number of selectable jobs; then, indicate the selection
mode by changing the Automatic Selection Code.
After changing the configuration, the instrument will create the selected jobs, initially
empty; to make an empty job available, use the command JOB MANAGEMENT > CHANGE WORK
and press Enter on the desired job; then, choose the name of the work. The item CREATE
NEW JOB in the JOB MANAGEMENT menu, allows the creation of extra jobs that can be used
regardless of the automatically selected job; to create a extra job and use a job selected
automatically, the unlock password is required.
2.1.1 Selection via inputs
When the selection is made via the inputs, the instrument changes the input status. The
device ignores the job change command when the start signal is active.
The job number depends on the binary combination of inputs. The first job has a zero
binary code, i.e. no active input. The maximum number of selectable jobs is 64 (with a
binary code from 0 to 63), if sufficient inputs are available.
To enable the job selection must:
enter the maximum number of selectable jobs can in the CHANNEL PHASE JOB menu.
Define the function of the inputs used as JOB SELECTOR.
The wiring of the inputs leans on the X3 terminal board.
2.2 Connecting an external reset
When a deviation is detected, the instrument freezes, preventing the execution of other
pieces. To resume operation, reset the scrap. To normally reset the scrap, use the front
button. You can disable this button from the instrument configuration menu.
To reset the scrap, it is possible to use the RESET input.
2.3 Additional controls
Up to six additional controls can be connected to the instrument.
Three of them are used to start of the press while the other three are used to sort the good
pieces from the scrap, or other consents to start.
The first three are called ENABLE, the second three are called TEST SIGNAL. Additional
controls can be renamed from the instrument setup menu.
Additional controls may be excluded from each job.

16 Press Right installation
The TEST SIGNAL 1 control may also be associated with a useful output signal to activate
the control system.
To use additional controls, the instrument should be set up to select which inputs are
connected to the signals.
After the input configuration, a name may be set for each of the six signals.
The enabling signals are checked when the START signal is activated: if an enabling
signal is missing, the instrument displays the message "No enabling signal".
Test signals affect the good or scrap result: if a test signal is not activated, the piece is
rejected.
The moment when the presence or absence of each test input is verified, may be
individually set up.
The moment when the test signals are checked, can be selected in the job options. Note
that only Test input 1 includes all the options.
at the start the signal is checked when the start input is activated
at the stop the signal is checked when the stop input is activated
at the end the signal is checked when the cylinder returns
at the quota the signal is checked at a certain quota
up to a quota the signal is checked from start to a certain quota
from a quota the signal is checked from a certain quota to a stop
continuous the signal is checked from start to stop
enabling the signal is used as a start enabling signal

Press Right installation 17
3 Instructions to install Press-Right
The Press-Right instrument is supplied in a metal case which can be attached to an
support arm.
It is possible to request the version with pre-assembled support arm. The support arm can
be rotated.

18 Press Right installation
3.1 Dimensions
The overall dimensions of the cable glands and cables must be added to the depth
indicated in the following drawing (about 55 mm).

Press Right installation 19
3.2 Montaggio strumento
Always disconnect the instrument from the power supply before opening it.
Open the instrument by unscrewing the four screws at the corners of the front panel
(Figure 2).
Figure 2
Remove the internal boards by a few centimeters (Figure 3). Then release the boards from
the front panel.
Figure 3
Remove all the boards from the container and remove the terminal assemblies.
To fasten the instrument, it is possible to drill a hole on the sides or above or a central
lower position of the container (first, remove all boards).
Mount conduits and plugs.
Insert the cables in the conduits and start wiring.
It is very important that the end of the unshielded load cell cable is as short as
possible
Once the wiring is completed, mount the boards
Finally, mount the terminal assemblies, paying attention to mount them in the correct
direction.
Make sure that the cables are not be pressed onto the bottom of the instrument.

20 Press Right installation
Once the wiring is completed, it is possible to power the instrument and follow the steps
below:
•Set up the instrument.
•Check the operation of inputs and outputs, using the commands from the DIAGNOSTICS
menu.
•Calibrate the transducers.
Other manuals for Press-Right
5
Table of contents
Other ALFAMATIC Measuring Instrument manuals

ALFAMATIC
ALFAMATIC Press-Right User manual
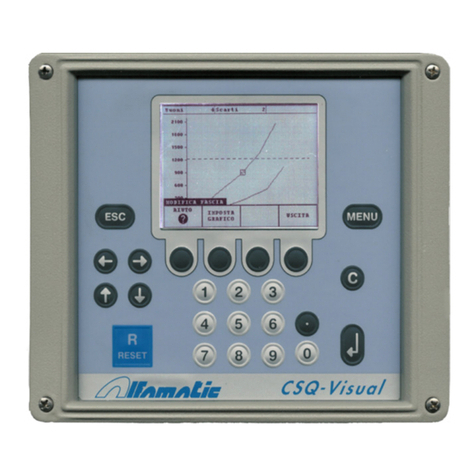
ALFAMATIC
ALFAMATIC CSQ-Visual User manual
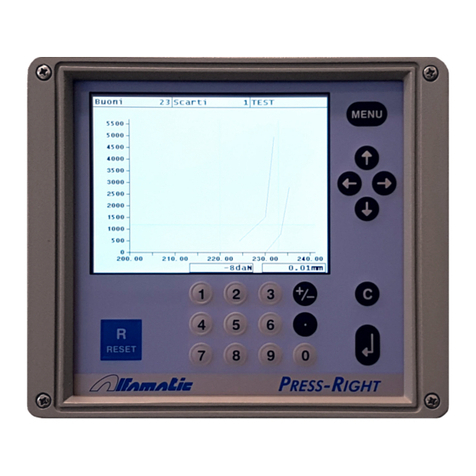
ALFAMATIC
ALFAMATIC Press-Right User manual
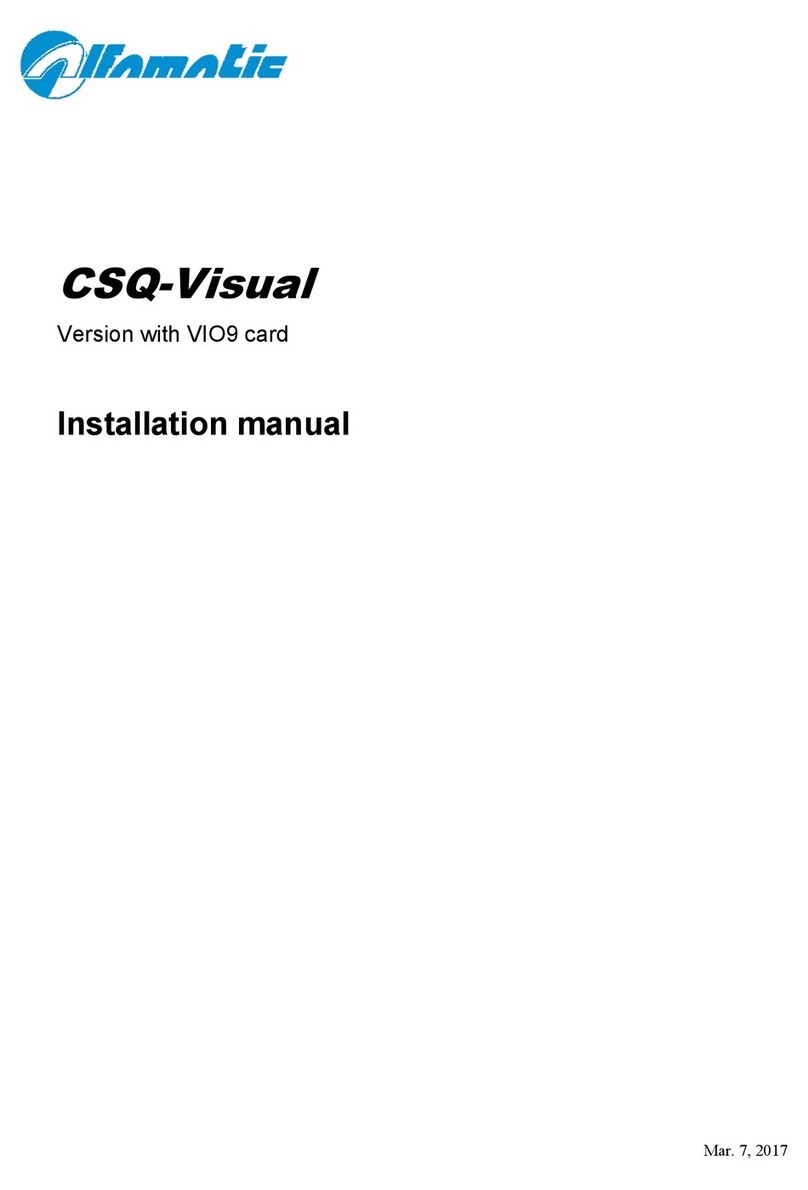
ALFAMATIC
ALFAMATIC CSQ-Visual User manual
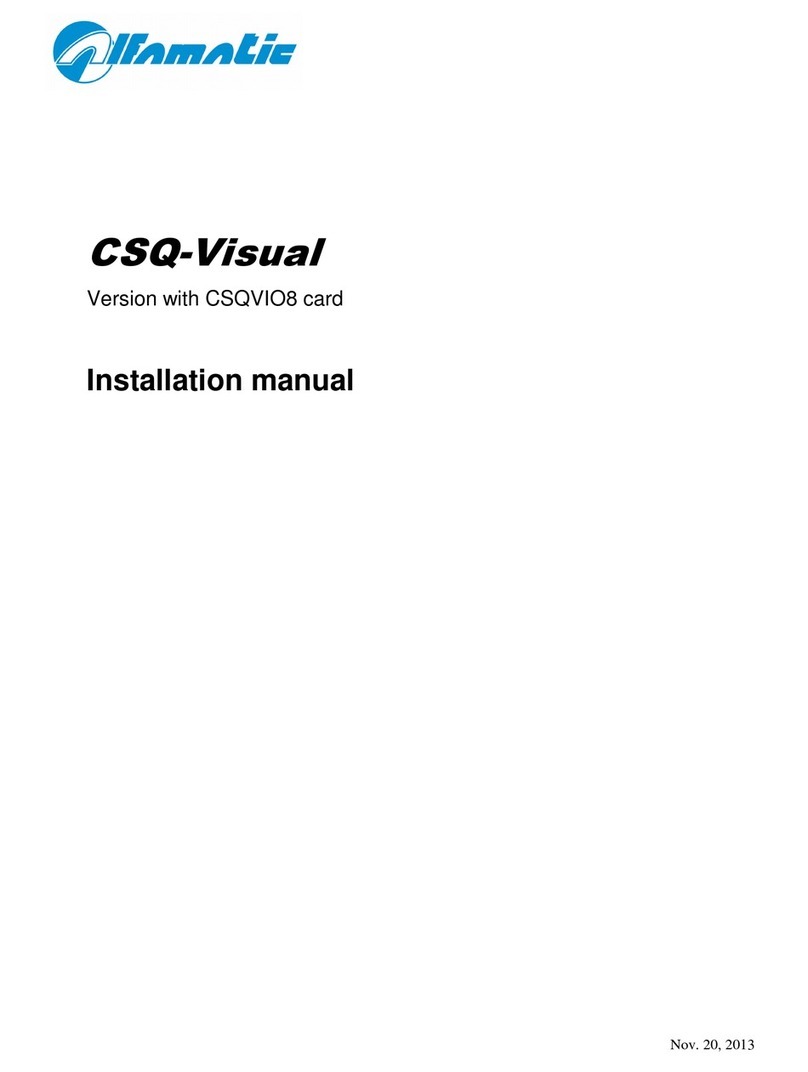
ALFAMATIC
ALFAMATIC CSQVIO8 User manual
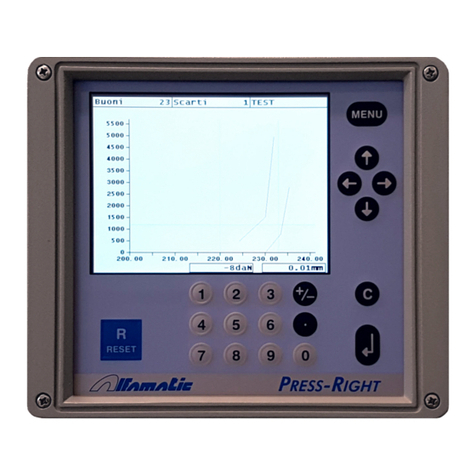
ALFAMATIC
ALFAMATIC Press-Right User manual
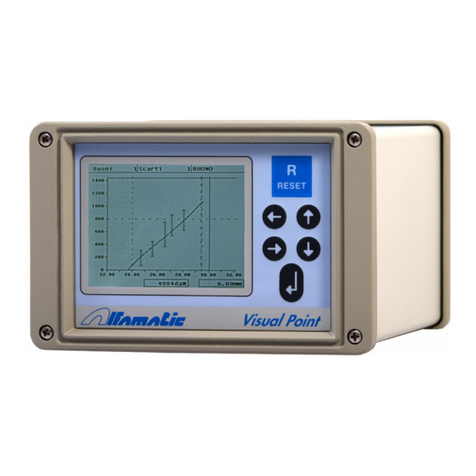
ALFAMATIC
ALFAMATIC Visual Point User manual
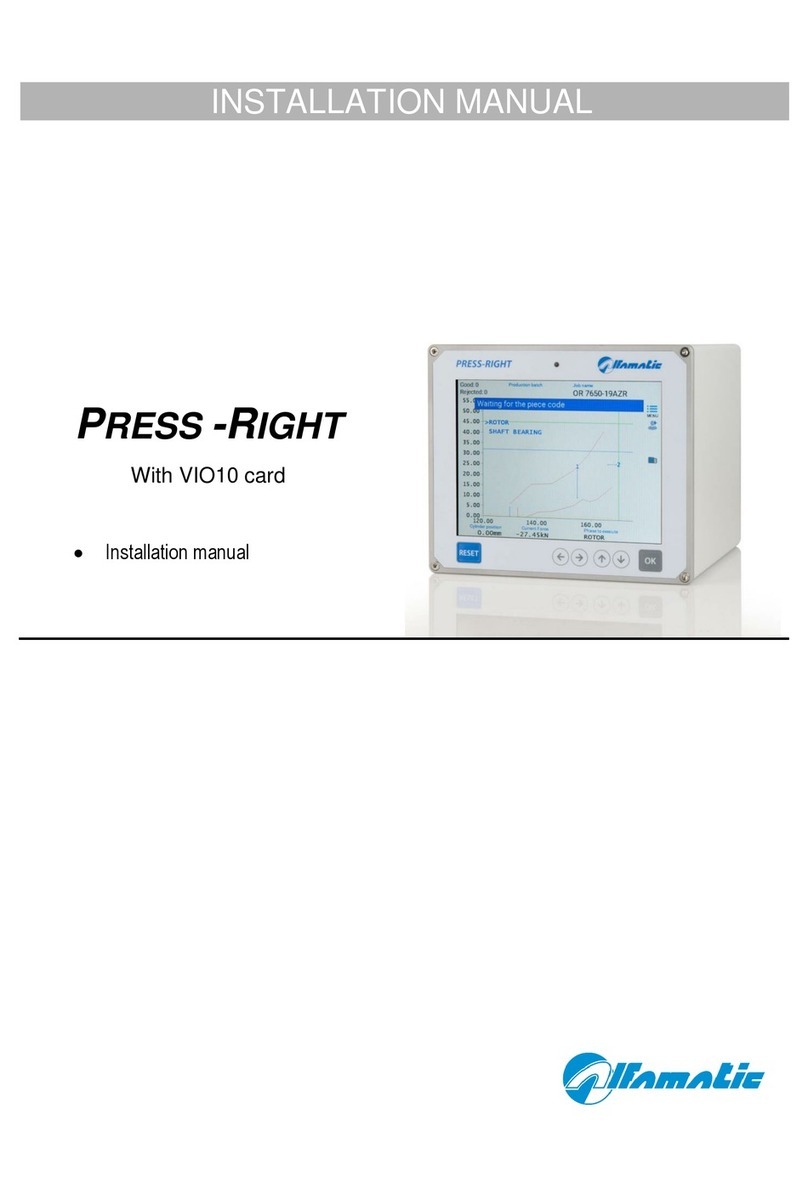
ALFAMATIC
ALFAMATIC PRESS -RIGHT User manual
Popular Measuring Instrument manuals by other brands

TPS
TPS Aqua-D manual

PCE Health and Fitness
PCE Health and Fitness PCE-NDL 10 Operation manual
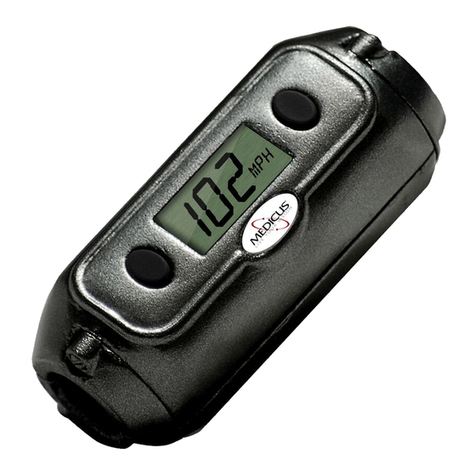
Medicus
Medicus POWER METER INSTRUCTIONAL MANUAL INSTRUCTIONAL MANUAL
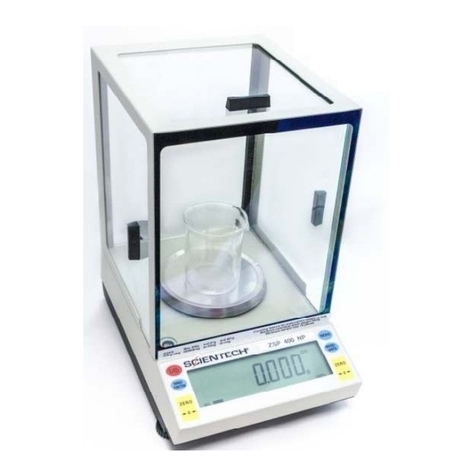
ScienTECH
ScienTECH NTEP quick start guide
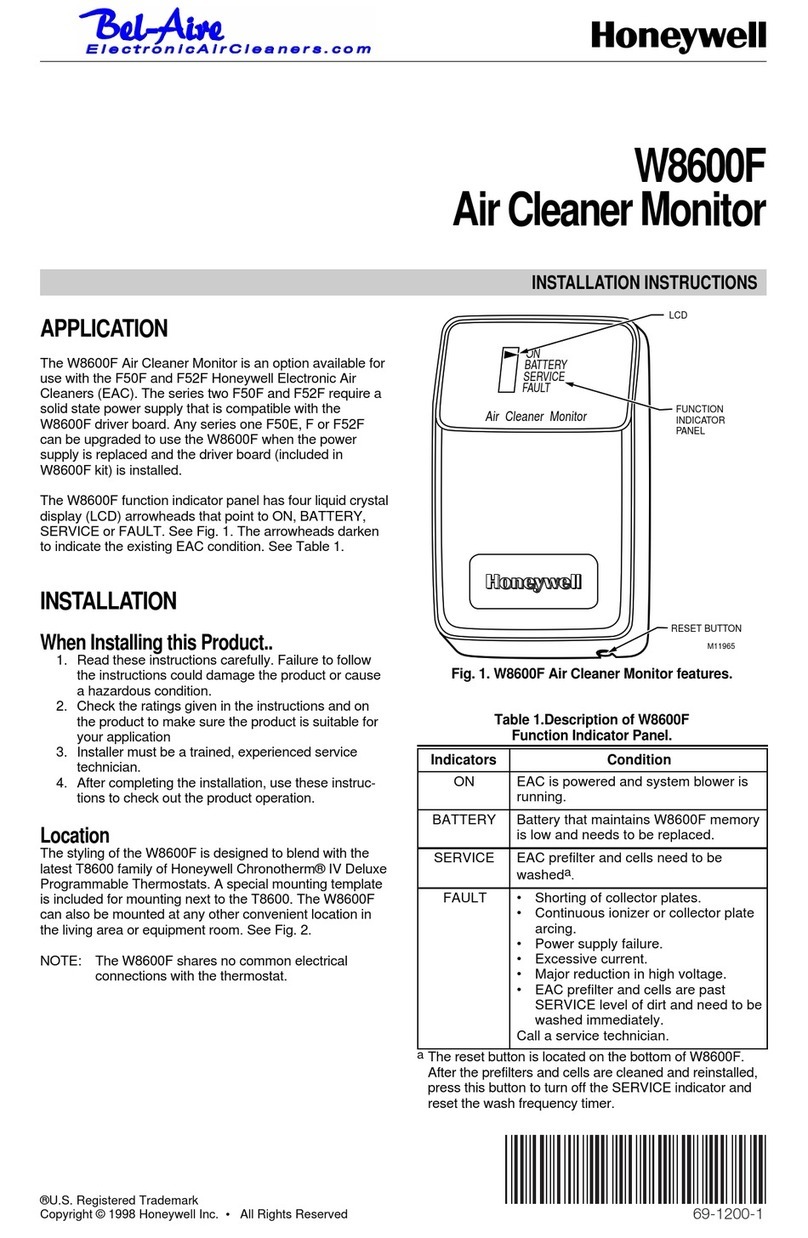
Honeywell
Honeywell W8600B installation instructions

Test Equipment Depot
Test Equipment Depot gom-802 user manual