Allied Systems H5C Series User manual

P/N 599028W Printed in U.S.A. 12/16/2020
Hydraulic Winch
Please check the Allied Systems website
regularly for updates to this manual.
www.alliedsystems.com
A Product of
Sherwood, OR USA
Service Manual
H5C
Applicable to winches with serial numbers H5C***1226*** and later.

Safety Precautions
Read, understand and observe the Safety Summary
on pages i through iii
to prevent injury to personnel and damage to equipment.
Winch serial number _________________________
Date put into service _________________________
NOTE: This publication may be translated to different languages for sole purpose
of easy reference in non-English speaking locations.
Should there be differences in interpretations to the text,
please refer to the English language edition published by Allied Systems Company
as the controlling document.

i
Safety Summary
General Safety Notices
The following pages contain general safety warnings
which supplement specific warnings and cautions
appearing elsewhere in this manual. All electrical and
hydraulic equipment is dangerous. You must thoroughly
review and understand the Safety Summary before
attempting to operate, troubleshoot or service this winch.
The following symbols and terms are used to emphasize
safety precautions and notices in this manual:
The “DANGER” symbol indicates a
hazardous situation which, if not avoided,
will result in serious injury or death.
Carefully read the message that follows
to prevent serious injury or death.
The “WARNING” symbol appears
wherever incorrect operating procedures
or practices could cause serious injury
or death. Carefully read the message that
follows to prevent serious injury or death.
The “CAUTION” symbol appears where a
hazardous situation which, if not avoided,
could result in minor to moderate injury
and equipment damage.
NOTICE
This signal word alerts to a situation that
is not related to personal injury but may
cause equipment damage.
NOTE: …
The term “NOTE” highlights operating
procedures or practices that may improve
equipment reliability and/or personnel
performance.
NOTE: All possible safety hazards cannot
be foreseen so as to be included in this
manual. Therefore, you must always
be alert to potential hazards that could
endanger personnel and/or damage the
equipment.
Safety Regulations
Each country has its own safety legislation. It is in the
operator’s own interest to be conversant with these
regulations and to comply with them in full. This also
applies to local bylaws and regulations in force on a
particular worksite.
Should the recommendations in this manual deviate from
those in the user’ country, the national regulations should
be followed.
Operation, Inspection, and Maintenance Warnings
Obey the following cautions and warnings
before using your winch to avoid equipment
damage, personal injury or death.
• Do not operate the winch unless your are authorized
and trained to do so.
• Do not operate the winch unless the vehicle is
equipped with a screen to protect the operator if
the wire rope breaks.
• Read, understand, and follow the operating,
inspection, and maintenance instructions in this
manual.
• Do not use the control levers for hand holds when
entering or leaving the vehicle.
• Do not permit other people near the control area
when you inspect or repair a machine.
• Never inspect, repair, or perform maintenance on
a machine that is in motion.
Safety Summary

ii
• Inspect the winch before each use:
»Make sure that the controls and instruments
operate correctly.
»Report the need for repairs immediately.
»Do not work with a damaged or worn wire rope.
»Do not use a winch that needs repairs.
»If the wire rope and ferrule must be removed
from the drum, make sure the end of the
wire rope and ferrule are controlled when
the ferrule is released. The end of the wire
rope can suddenly move from the drum like
a compressed spring when the ferrule is
released, and cause an injury.
• Stay in the operator’s seat when operating the
winch.
• Do not stand on the vehicle when operating the
winch.
• Avoid winch operation near people or other
machines.
• Never stand nor permit others to stand in the bight
(loop) of a wire rope.
• Do not stand nor permit others to be near the winch
or wire rope when there is tension on the wire rope.
• Observe jobsite rules.
• Be in complete control at all times.
• Do not use the control levers as hangers for clothes,
water bags, grease guns, lunch pails, etc.
• Do not leave the vehicle when the winch wire rope
is under tension.
• Do not permit riders on the vehicle or load.
• Do not use the winch as an anchor for a double or
two-part line.
• Do not pull the hook through the throat or over the
drum, which will cause damage.
• When the winch is not in use, make sure the control
lever is in BRAKE-ON position and the winch brake
is applied.
• Do not use winch as a hoist. Tractor and skidder
mounted winches are designed for towing.
• Always inspect wire rope, tail chain and other rigging
components for wear, damage, broken strands or
abuse before use.
• Never use wire rope, tail chain or other rigging that
is worn-out, damaged or abused.
• Never overload wire rope, tail chain or rigging.
• Wire rope and tail chain will fail if worn-out,
overloaded, misused, damaged, improperly
maintained or abused. Wire rope or tail chain failure
may cause serious injury or death!
KG
KG
KG
KG
• Do not terminate wire rope to tail chain by the use
of a knot.
• Do not handle wire rope if the hook end is not free.
A load could break away, suddenly tensioning the
wire rope, resulting in serious injury or death.
• Stay clear of wire rope entry areas (fairlead or arch
rollers, winch drum etc).
• Make sure ground personnel are in plain view of the
operator, and at a distance of at least 1½ times the
working length of the wire rope.

iii
Safety Summary
• Make sure that any hand signals used by ground
personnel are clearly defined and understood by
everyone involved.
• Do not attempt to “jerk” or “shock” a load free. Doing
so can cause loads in excess of the rated capacity
of the wire rope, winch, or mounting hardware.
• Replace any parts only with genuine Allied Winch
parts. Refer to Parts Manual 599048W.
• Maintain a minimum of three (3) complete wraps
of wire rope on the drum for normal operation. It
may help to paint the last five wraps of wire rope
a contrasting color, to serve as a visual indicator.
• Do not handle wire rope with bare hands. Wear
leather gloves at all times.
• Align the tractor with the load to prevent side loading
the winch, and to maintain even spooling of the
wire rope.
• If applying tension to the wire rope manually during
spooling:
»ensure that the operator is winching in slowly,
»keep your hands and clothing well clear of any
rollers or the winch drum,
»do not maintain tension by letting the wire rope
to slip through your hands,
»use a hand-over-hand technique to maintain
tension.
• Be aware of the ground conditions, and make sure
the ground and tractor are stable enough to pull
the intended load.
• Do not attempt to pull loads in excess of the rated
capacity of the winch.
• Keep yourself informed of any applicable codes,
regulations and standards for the job.
• Your winch may have temperature shut-off system
for protection of tractor and winch. Manual override
of high temperature shut-off will cause damage to
tractor and winch.
• This winch is neither intended, designed, nor rated
for any application involved in the lifting or moving
of personnel.
• Use only the lubricants listed in the Recommended
Oil List. See pages 1-4 and 1-5.
• Do not weld on any part of the winch. Contact Allied
Systems if weld repairs are needed.
• The hydraulic system must be kept clean and free
of contamination at all times.
• Be aware of the hazards of pressurized hydraulics:
»Wear personal protective equipment, such as
gloves and safety glasses, whenever servicing
or checking a hydraulic system.
»Assume that all hydraulic hoses and components
are pressurized. Relieve all hydraulic pressure
before disconnecting any hydraulic line.
»Never try to stop or check for a hydraulic leak
with any part of your body; use a piece of
cardboard to check for hydraulic leaks.
»Small hydraulic hose leaks are extremely
dangerous, and can inject hydraulic oil under
the skin, even through gloves.
»Infection and gangrene are possible when
hydraulic oil penetrates the skin. See a doctor
immediately to prevent loss of limb or death.

iv
Ordering Parts:
When ordering replacement parts, give the unit serial number,
part number, name of part and quantity required.
For any further information on parts, service or ordering,
consult your local winch dealer, or contact Allied Systems Company:
Allied Systems Company
21433 SW Oregon Street
Sherwood, OR 97140 USA
Phone: 503-625-2560
Fax: 503-625-5132
E-Mail: par[email protected]
Also see our website, www.alliedsystems.com, where the most current copy of this manual is always available.

v
Contents
Safety Summary .........................................................i
General ....................................................................1-1
Introduction...............................................................1-1
Description ...............................................................1-1
Unit Identification ...............................................1-2
Serial Number Codes.........................................1-3
Nameplate .........................................................1-3
Specifications ...........................................................1-4
Drum Wire Rope Capacities...............................1-4
Hydraulic Specifications.....................................1-4
Oil Specifications ...............................................1-4
Oil Capacity........................................................1-4
Maintenance Decal ............................................1-5
Torque Specifications.........................................1-5
Gear Train ................................................................1-6
FREESPOOL Operation ..........................................1-7
Operation and Control ..............................................1-8
Brake ......................................................................1-10
Motor ......................................................................1-11
Counterbalance Relief Manifold .............................1-12
Control Manifold (without DRAG-BRAKE)..............1-13
Control Manifold (with DRAG-BRAKE)...................1-13
Sequence of Operation - K371 & L39
BRAKE-ON ......................................................1-15
LINE-IN ............................................................1-17
LINE-OUT ........................................................1-19
FREESPOOL ...................................................1-21
Sequence of Operation - C805, R371, R42
BRAKE-ON ......................................................1-23
LINE-IN ............................................................1-25
LINE-OUT ........................................................1-27
FREESPOOL ...................................................1-29
Sequence of Operation - Y46F
BRAKE-ON ......................................................1-31
LINE-IN ............................................................1-33
LINE-OUT ........................................................1-35
FREESPOOL ...................................................1-37
DRAG-BRAKE .................................................1-39
Schematics.............................................................1-41
Troubleshooting......................................................2-1
General.....................................................................2-1
Mechanical/Hydraulic Troubleshooting Charts..........2-1
Service.....................................................................3-1
General ....................................................................3-1
Maintenance.............................................................3-1
Maintenance Points............................................3-1
Maintenance Schedule ......................................3-1
Checks Before Operation...................................3-2
Checks During Operation...................................3-2
FREESPOOL Drag Adjustment .........................3-2
Hydraulic System Pressure Checks .........................3-2
Preparation.........................................................3-2
Pilot Supply Pressure Check..............................3-4
Installations without Optional DRAG-BRAKE:
Motor Supply Pressure Check ...........................3-5
Brake Pressure Check .......................................3-6
Brake Valve Pressure Check & Adjustment .......3-7
FREESPOOL Pressure Check...........................3-8
LINE-IN Pressure Check....................................3-9
LINE-OUT Pressure Check..............................3-10
Installations with Optional DRAG-BRAKE:
Motor Supply Pressure Check .........................3-11
Brake Pressure Check .....................................3-12
Brake Valve Pressure Check & Adjustment .....3-13
FREESPOOL Pressure Check.........................3-14
LINE-IN Pressure Check..................................3-15
LINE-OUT Pressure Check..............................3-16
DRAG-BRAKE Pressure Check.......................3-17
Repairs ...................................................................4-1
General ....................................................................4-1
Winch Removal ........................................................4-1
Winch Disassembly ..................................................4-1
Drum and Drum Shaft ........................................4-2
Intermediate and FREESPOOL Shaft................4-3
Motor Removal
Winches without optional DRAG-BRAKE........4-4
Winches with optional DRAG-BRAKE.............4-5
Motor Disassembly.............................................4-6
Brake Removal.................................................4-10
Brake Disassembly ..........................................4-14
Drag Brake Disassembly..................................4-15
Winch Assembly...............................................4-16
Visual Inspection..............................................4-16
Drag Brake Assembly ......................................4-18
Brake Assembly ...............................................4-19
Brake Installation..............................................4-20
Motor Assembly...............................................4-24
Motor Installation
Winches without optional DRAG-BRAKE....4-28
Winches with optional DRAG-BRAKE ........4-29
Winch Installation.............................................4-30
Contents

vi
Notes

Section 1
1 - 1
General
Introduction
This service manual is for the H5C hydraulic winch. The
following information is included in this manual:
Section 1. General includes operation descriptions of
systems and components as an aid for troubleshooting
and repair.
Section 2. Troubleshooting lists common problems
and the possible causes and corrections.
Section 3. Maintenance provides a guide for periodic
maintenance, checks and adjustments.
Section 4. Repairs describes the removal,
disassembly and assembly of the winch.
Description
The H5C Winch is a Power Forward (LINE-IN) and Power
Reverse (LINE-OUT) winch. The winch is powered by an
internal hydraulic motor connected to the tractor hydraulic
system. Oil flow and pressure are converted to rotational
energy by the winch motor. Motor torque is transmitted
through a holding brake and two gear reductions to the
drum. Hydraulic oil is supplied by the tractor mounted
auxiliary pump circuit or designated winch pump. The
winch utilizes oil, cooling, and sometimes filtration provided
by the tractor circuit. Flow to the winch is controlled by a
control lever and electrical switches located at the tractor’s
control station.
The H5C winch has a maximum rated line pull capacity
of 222,400 N (50,000 lbf) when there is one layer or less
of wire rope on the drum. When there is more than one
layer of wire rope on the drum, the maximum rated line
pull is reduced.
Figure 1-1 H5C Winch
1
2
3
4
5
8
6
7
9
10
11
1. Drum
2. Access Cover for Motor and Hydraulics
3. Plug to Drain Oil
4. Plug to Check Oil Level
5. Serial Number Plate
6. Tie Bar
7. Fill Plug
8. Serial Number Stamp
9. Bearing Retainer for Intermediate Shaft & Freespool Drag
10. Right Side Drum Shaft
11. Breather

General
1 - 2
Unit Identification
Allied Winch S/N Nameplate Data For Tractor Mountings
Figure 1-2 Tractor Identification Codes and Available Gear Ratios for H5C Winch
Tractor Make Model and Starting Tractor Serial Number Where Applicable
H5C T 2 D 1235 K371
Sequence Number
Winch Model
Gear Ratio (Code #)
1 = 44.75:1
2 = 48.00:1
Hydraulic Operation Type
T = Standard
Tractor Direction Valve, Single or 2-Speed
Vehicle Code
See Figure 1-2
Internal Options
D = External Pump, PFR, FS, Overwind,
2-Speed (Rescue)
G = External Pump, PFR, FS, Overwind,
2-Speed (Rescue), DRAG-BRAKE (HI-P)
1. In Addition to the serial number plate, the
serial number is stamped on the top left-
hand side of the frame. (See Figure 1-1
on page 1-1.)
2. Circled numbers in Figure 1-2 indicate
possible gear ratio.
Notes:
C
O
D
E
C
Caterpillar
K
Komatsu
L
Liebherr
R
Case
Y
Tigercat
39 PR716
42 1650M
46F 920
371 D51-24
1150M
805 D6K2 T4f
H5C

Section 1
1 - 3
Serial Number Codes
The serial number codes are described on page 1-2 of
this manual. The nameplate with the serial number code
is found on the top left hand side of the winch case. The
serial number code is also stamped on the left hand side
of the winch frame.
Nameplate
The rated capacity for the winch, as it is equipped, is
shown on the nameplate. Each winch is shipped from the
factory with a nameplate as shown in Figure 1-3. If the
nameplate is missing, or the wire rope does not match the
information on the nameplate, do not operate the winch
until its capacity is known and a new nameplate is installed.
Each winch must be operated within its rated capacity as
shown on the nameplate. Figure 1-3 Nameplate
ALLIED SYSTEMS COMPANY
21433 SW OREGON STREET
SHERWOOD, OREGON 97140 USA
WWW.ALLIEDSYSTEMS.COM
MODEL:
SERIAL NO.:
MAXIMUM LINE PULL*
BARE DRUM:
MAXIMUM WIRE
ROPE DIAMETER:
*LIMITED BY WIRE BREAKING STRENGTH. MAY BE LOWER DUE
TO AVAILABLE POWER FROM WINCH CARRIER. CONTINUOUS
LINE PULLS SHOULD BE LESS THAN WINCH CARRIER GVW.
MADE IN USA 2315005 REV A

General
1 - 4
Specifications
Drum Wire Rope Capacities (Drum: 9 Inch Diameter)
WIRE ROPE DIAMETER Length
(2/3 Drum Capacity*)
Length
(Full Drum Capacity**)
16 mm (5/8 in) 85 m (279 ft.) 129 m (423 ft.)
19 mm (3/4 in) 60 m (197 ft.) 91 m (298 ft.)
22 mm (7/8 in) 43 m (142 ft.) 66 m (215 ft.)
Notes: * Recommended length to fill drum up to 2/3 capacity to leave room for uneven spooling.
** Length to fill drum to full capacity. Will have no room for uneven spooling. Not recommended.
1. Wire Rope: IWRC 6 X 19, extra improved plow steel, with ferrule, tail chain and hook.
2. Loosely or unevenly spooled wire rope will change capacities. Use flexible wire rope with
independent wire rope center.
3. Ferrule: Light (2-1/4” Long X 2” Diameter)
Figure 1-4 Drum Wire Rope Capacities
Hydraulic Specifications
Motor ................... Hydraulic 2-Speed Vane Single Pilot
Brake ............................... Dry multi-disc spring applied
Oil Specifications
The hydraulic winch motor and control system operate off of the tractor implement hydraulic system. The winch gear
case is filled with hydraulic transmission oil and is separate from the tractor hydraulic system. Factory fill for the gear
case is Exxon-Mobil 424. For proper operation, only oils shown in Figure 1-5 should be used in the winch gear case.
Oil Capacity
The oil capacity for H5C winch is approximately 17 quarts (16 liters).
°F °C
ExxonMobil Mobil Fluid 424 (Factory fill) -13 to 104 -25 to 40
05ot52-221ot31-™draG-yHereeDnhoJ
04ot52-401ot31-FHT0001norvehC
Caterpillar Multipurpose Tractor Oil (MTO) -13 to 104 -25 to 40
05ot92-221ot02-artlUnarT-yHesaC
°F °C
03ot04-68ot04-TLdiulFliboMliboMnoxxE
John Deere Low Viscosity Hy-Gard -40 to 86 -40 to 30
03ot04-68ot04-WFHTnorvehC
used only in the winch gear case.
Recommended Oils* - Low Temperature Conditions
Manufacturer Oil Type Ambient Temperature Range
* Note: Use of a non-recommended oil may void warranty.
** For winches using tractor-supplied hydraulics for winch operation, recommended oil is
Recommended Oils* - General Conditions
Manufacturer Oil Type Ambient Temperature Range
Figure 1-5 Recommended Oils

Section 1
1 - 5
Figure 1-6 Maintenance Decal
Torque Specifications
Figure 1-7 Torque Specifications
Maintenance Decal
Recommended Gear Compartment Oil:
Hydraulic Winch Maintenance
Recommended Winch Service Intervals
Hours or
First 250 1 Change
Every 500
Every 2,000
Every 5,000
Every 10,000
John Deere
ExxonMobil
Caterpillar
Chevron -1000 THF
-Multipurpose Tractor Oil (MTO)
2311329 Rev C
-Mobil Fluid 424 (Factory Fill)
-Hy-Gard
3
12
Change
Change
Inspect
** **
**
*
*
*
Evaluate
Evaluate = Service based on average winch use;
Inspect = disassemble and inspect for wear.
Consult service/operating manual for low
temperature oils and other details. Tractor
final drive oils may be used in winch.
- if used more than once a day, perform overhaul.
- if used less than once a day, remove covers and check to determine need.
Follow tractor schedule if using tractor filter.
Service winch using the tractor’s hour meter or the length of time the
winch is mounted to the tractor, whichever occurs first.
*
***
***
Months Filter
Lube rollers and check oil level and filter light weekly.
Winch
Gear Oil
Brake &
Clutch
Major
Overhaul
Hardware Size TORQUE VALUES
ft-lbs. N-m kg-m
3/8-UNC Grade 8 33 - 35 45 - 47 4.6 - 4.8
1/2-UNC Grade 8 80 - 84 108 - 114 11.1 - 11.6
5/8-UNC Grade 8 160 - 168 217 - 228 22.1 - 23.2
3/4-UNF Grade 8 375 - 385 508 - 522 51.8 - 53.2
3/4-UNC Grade 8 285 - 300 386 - 407 39.4 - 41.5

General
1 - 6
Figure 1-9 Rotation Torque Transfer
Figure 1-8 Gear Train
Motor Shaft
Idler Shaft
Intermediate
Shaft
Drum
Shaft
Hydraulic
Motor
Brake
Freespool Fork
BRAKE-ON LINE-IN LINE-OUT
Oil Supply (A)
Oil Return (B)
Oil Return (A)
Oil Supply (B)
Gear Train (See Fig. 1-8)
The tractor pump or designated winch pump drives the
hydraulic motor with hydraulic oil supply. The amount of
pressure in the motor is dependent on the size of the load.
The motor shaft rotates to give LINE-IN or LINE-OUT.
Return oil is directed back to the tractor reservoir in open
loop systems and back to the pump in hydrostatic closed
loop systems. The motor is attached to a spring applied
multi-disc brake that holds the winch drum in a fixed posi-
tion.When oil is supplied to the hydraulic motor, the brake
is simultaneously released with pilot control pressure.
The hydraulic motor can operate at half displacement
when the operator selects the HI-SPEED switch. At half
displacement the gear train rotates at roughly twice the
speed.
An intermediate gear assembly gives further gear reduc-
tion to increase torque at the winch drum. A spring-loaded
dental clutch with splines engages the drum pinion gear
and the intermediate gear. The operator can disengage
the dental clutch with an electric switch to activate the
FREESPOOL feature.
A drum gear engages the drum pinion gear and is con-
nected to the drum adapter (which connects the drum to
the drum gear). When power is applied to the gear train,
the drum will rotate in the forward or reverse direction.The
other side of the drum runs on roller bearings held by the
drum shaft.The drum shaft is connected to the winch case.

Section 1
1 - 7
1 Bearing Cone
2 Bearing Cup
3 Intermediate Gear
4 Dental Clutch
5 Drum Pinion Gear
6 Bearing Cone
7 Bearing Cup
8 O-Ring
9 Freespool Adjust Piston
10 Flangescrew
11 Lockwasher
12 Freespool Adjust Retainer
13 Nut
14 Setscrew
15 Shaft
16 Shifter Fork
17 Fitting
18 Spring
19 O-Ring
20 Capscrew
23 O-Ring
INTERMEDIATE
GEAR
DENTAL COLLAR
INTERMEDIATE
SHAFT
DRUM PINION
GEAR
FREESPOOL Operation (See Fig. 1-10 & 1-11)
The FREESPOOL arrangement allows mechanical dis-
engagement of the drum gear from the remainder of the
gear train.When FREESPOOL is selected, a hydraulically-
actuated sleeve disengages the dental clutch from the
intermediate shaft. The drum is now disconnected from
the brake and the winch cannot support a load.
FREESPOOL should not be used if there is a
load on the wire rope. An uncontrolled release
of the load will occur. Loss of the load can
result in equipment damage, personal injury
or death.
The yellow indicator panel on the selector switch lights
when the winch is in FREESPOOL.
NOTE: The dental clutch may not disengage if there
is a load on the wire rope. Remove the load from the
wire rope to activate the FREESPOOL function.
Figure 1-11 FREESPOOL Arrangement
Figure 1-10 FREESPOOL Operation

General
1 - 8
Operation & Control (See Fig 1-12, 1-13)
The H5C winch is designed to operate with a pilot oper-
ated hydraulic system. Hydraulic tractor power supplies
include variable displacement with load sensing control,
fixed displacement, and variable displacement hydrostatic.
When the tractor is running, the winch is ready to operate
but no oil is flowing to the winch. Control (pilot) pressure is
present at the winch.
The control lever and electrical switches are used to select
the following operations (not all winches are equipped with
all options):
BRAKE-ON (spring-centered position)
LINE-IN
LINE-OUT
FREESPOOL
HI-SPEED (either LINE-IN or LINE-OUT) (optional)
DRAG-BRAKE (optional)
The tractor must be running and the auxiliary hydraulic func-
tion switch, if equipped, must be on. LINE-IN, LINE-OUT
and BRAKE-ON are controlled by a control lever.
When the control lever is in the BRAKE-ON or centered
position, the holding brake is automatically applied. Push-
ing the lever away from the operator releases the brake
and reels cable off the drum (LINE-OUT). Pulling the lever
towards the operator releases the brake and reels wire rope
onto the drum (LINE-IN). Releasing the lever causes it to
return to the BRAKE-ON position, which stops the drum
rotation and applies the holding brake. By moving the lever
a small amount, slow wire rope movement is achieved for
inching control. Line speed increases proportionally as the
lever is moved farther.
The switch panel may contain three rocker switches that
control FREESPOOL, HI-SPEED and DRAG-BRAKE.
The tractor must be running to supply hydraulic power to
operate these functions. The switch light illuminates when
the switch is on.
The FREESPOOL switch has a lock to prevent inadvertent
actuation.The slide lock must be released before the switch
can be turned on.
Before operating the winch in LINE-IN or LINE-
OUT mode, ensure the FREESPOOL and DRAG-
BRAKE lights are not illuminated. Doing so may
result in loss of load.
HI-SPEED is selected with a dual-action momentary switch.
A green light in the speed selector switch indicates HI-
SPEED operation. For heavy loads or when better control
is desired, the winch should be operated in low speed. For
light loads and faster wire rope speed, operate the winch
in HI-SPEED mode.
When the DRAG-BRAKE (optional) switch is selected,
FREESPOOL is engaged, and a drag brake is engaged
on the drum shaft, allowing the tractor to move slowly away
from a towed load while keeping the wire rope taut. The
tractor must be operated at low speed or the load may
still be dragged.

Section 1
1 - 9
Figure 1-12 Winch Controls (Installation on Komatsu D51-24 shown. Your controls may vary.)
LINE IN
LINE OUT
Figure 1-13 Winch Controls (Installation on CAT D6K2 shown.Your controls may vary.)

General
1 - 10
Brake (See Fig. 1-14)
The brake is a dry multi-disc spring applied design. The
springs push against a piston that applies force to the
friction discs and separator plates.The brake valve directs
pressurized oil to the piston and pushes back on the brake
springs to release the brake. The separator plates have
teeth that engage the splines inside the brake housing and
are held stationary. Teeth in the friction discs engage the
splines on the motor shaft and rotate with the hub.
Figure 1-14 Brake
1. Brake Mounting Plate
2. Brake Housing
3. Capscrew
4. Sleeve
5. Snap Ring
6. O-Ring
7. Pipe Plug
8. O-Ring
9. O-Ring
10. Brake Piston
11. Ball Bearing
14. Rotary Seal
15. Capscrew
16. Snap Ring
17. Belleville Spring
18. Snap Ring, External
19. Pressure Plate
20. Friction Disc
21. Separator Plate
23. Flangescrew
28. Fitting
29. Magnet
30. Capscrew
Note:
Minimum pack height of
service items #20 and #21
is 1.397”.
- ID Towards
Piston (#10)

Section 1
1 - 11
Figure 1-15 Motor, 2-Speed Vane
1. Seal Plate Snap Ring
2. Seal
4. Steel Plate
5. Seal Plate O-Ring
6. Bearing Snap Ring
7. Ball Bearing
8. Shaft
9. Bolt
10. Front Housing, Internal
11. Dowel Pins, Front
12. O-Ring
13. Ball Checks
14. Screw
15. Timing Plate
16. Stator
17. Rotor
18. Rotor Vane
19. Rotor Vane Spring, Outer
20. Rotor Vane Spring, Inner
21. Stator Vane
22. Stator Vane Spring
23. Needle Bearing
24. Rear Housing
25. Dowel Pins, Rear
Motor (See Fig. 1-15)
The hydraulic motor is a dual displacement vane-type (see
Figure 1-15).Winch speed is proportionally varied by input
flow from the pump and/or the displacement of the motor.

General
1 - 12
Figure 1-16 Counterbalance Relief Manifold
Counterbalance Relief Manifold (See Fig. 1-16)
The counterbalance relief (CBR) manifold houses the
counterbalance valve and the high pressure relief valves.
The counterbalance valve is a load holding valve that
blocks return oil flow from the motor in the event supply
pressure drops below a set point in LINE-OUT mode.The
counterbalance valve allows oil to free flow in the LINE-
IN mode through a check valve. The high pressure relief
valves act as an overload relief when supply pressure
exceeds the setting of the valve.
Port A
Port B
Port A1
Port B
Relief Valve
Relief Valve
Counterbalance Valve
Solenoid Valves
Brake Valve
Port PP
Port PD
Port BRAKE
Port RO
Port BO
Port
TP-BRAKE
Port FS
Port X1
Port RI
Figure 1-17 Control Manifold (Installations without DRAG-BRAKE)
This manual suits for next models
6
Table of contents
Other Allied Systems Winch manuals
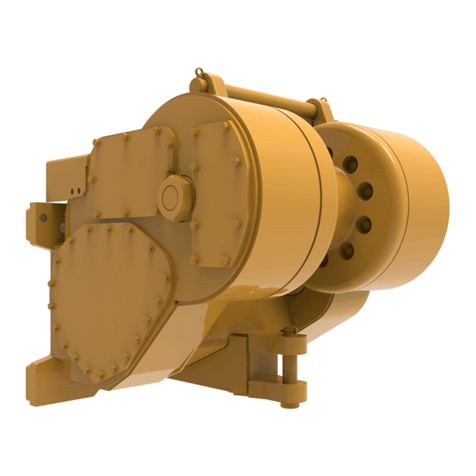
Allied Systems
Allied Systems W6G User manual
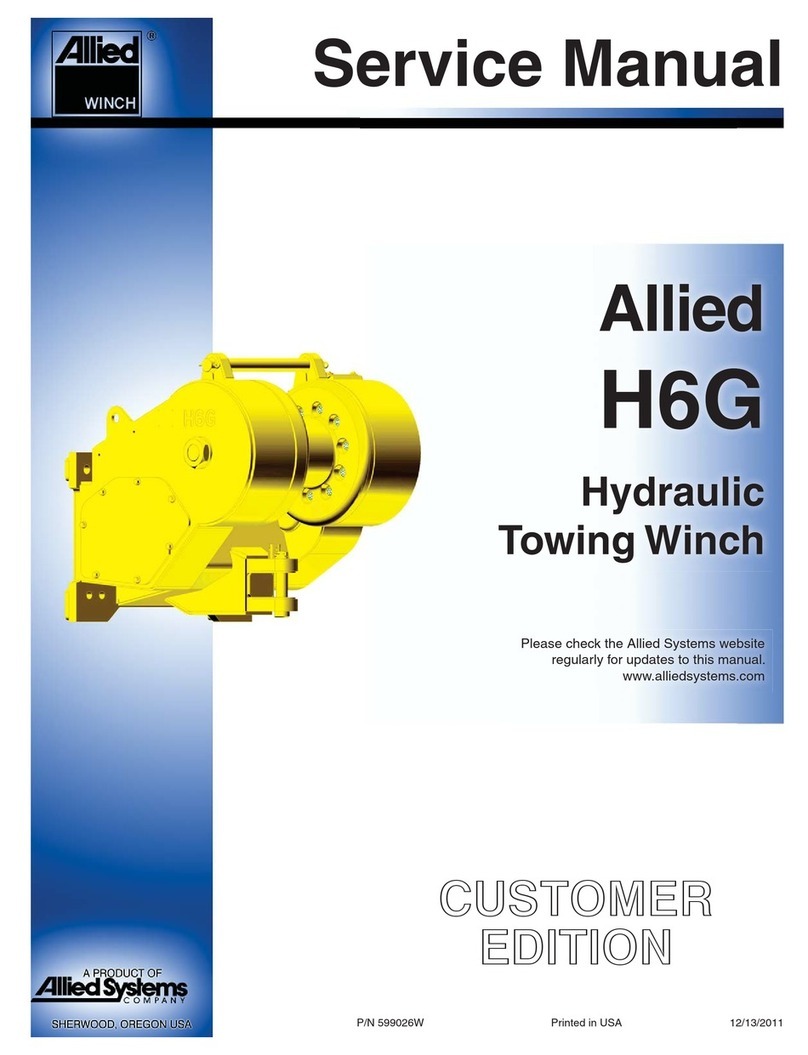
Allied Systems
Allied Systems Allied H6G Series User manual
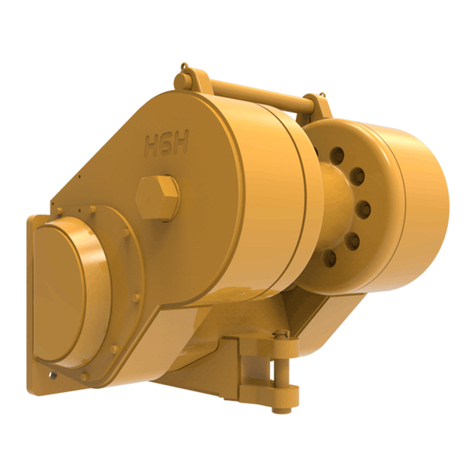
Allied Systems
Allied Systems H6H User manual
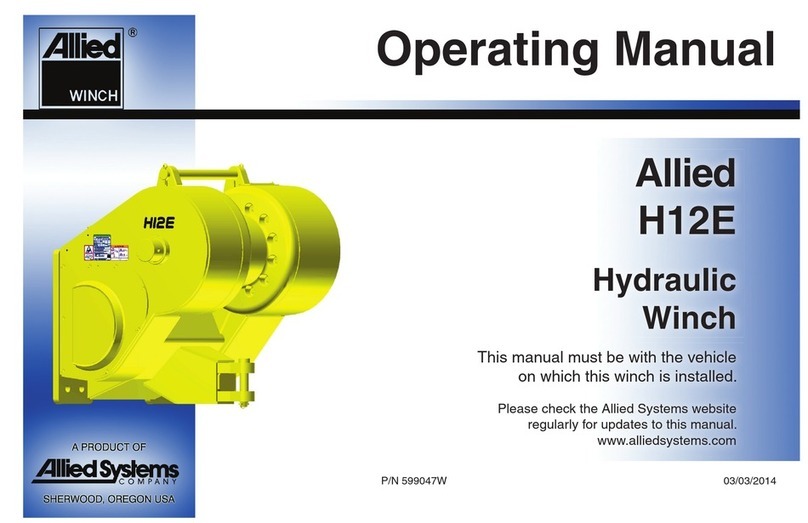
Allied Systems
Allied Systems H12E User manual
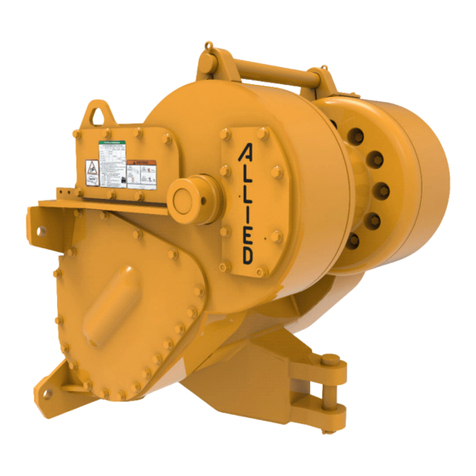
Allied Systems
Allied Systems W8L User manual

Allied Systems
Allied Systems H6H User manual
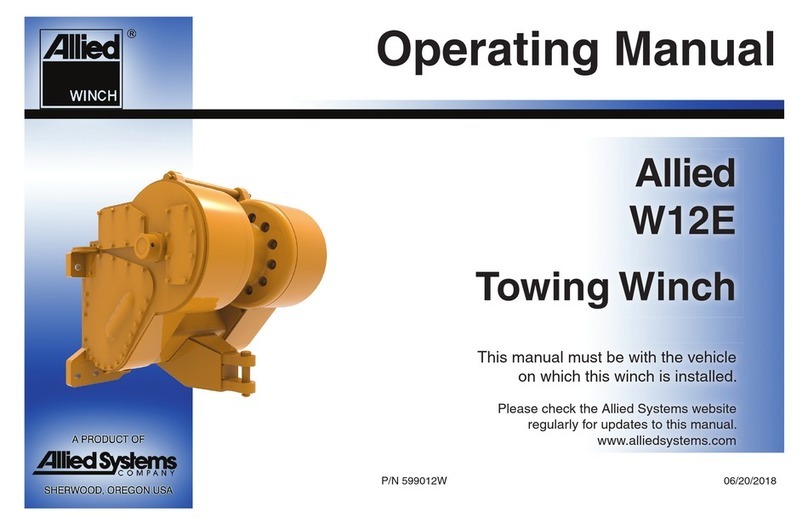
Allied Systems
Allied Systems W12E User manual

Allied Systems
Allied Systems W6G User manual
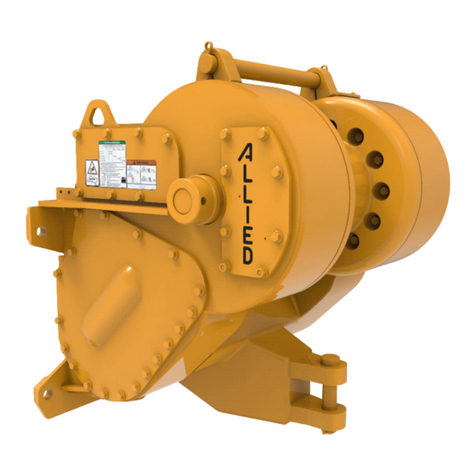
Allied Systems
Allied Systems W8L User manual
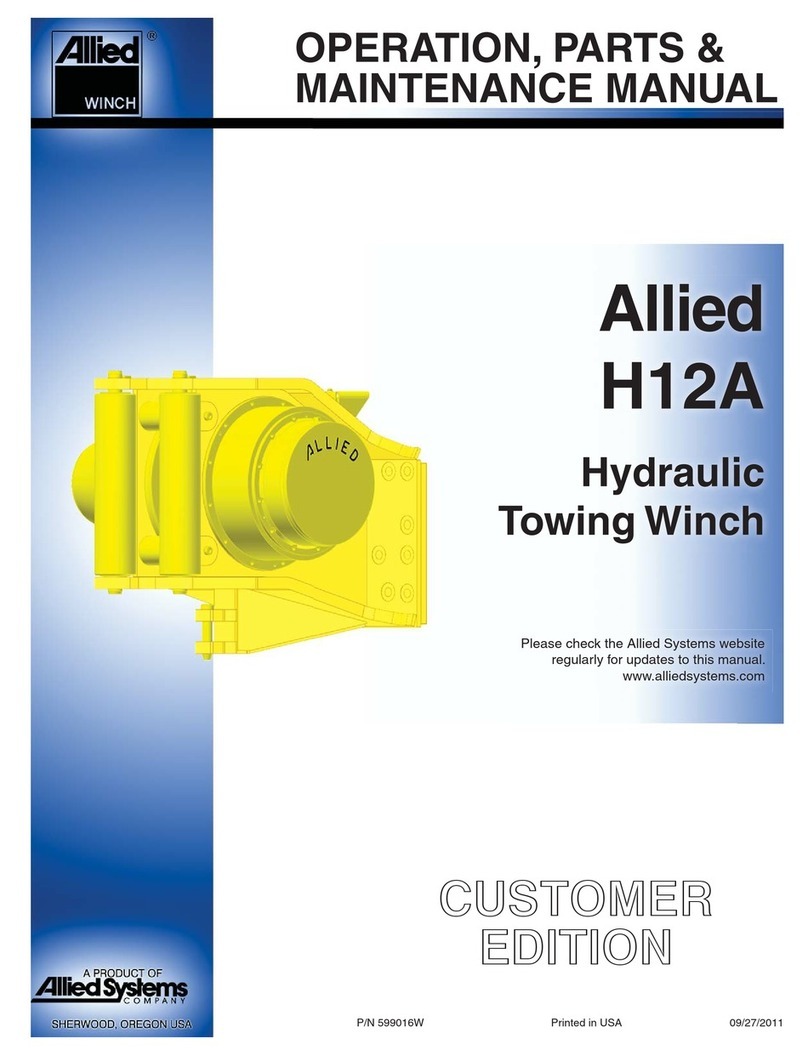
Allied Systems
Allied Systems H12A Guide