Aplisens SGE-25.Modbus User manual

USER’S MANUAL
SMART LEVEL PROBES
SGE-25.Modbus and SGE-25S.Modbus
EN.IO.SGE.25.MODBUS
SEPTEMBER 2021
APLISENS S.A., 03-192 Warsaw, Morelowa 7 St
tel. +48 22 814 07 77; fax +48 22 814 07 78
www.aplisens.com, e-mail: [email protected]
Revision 01.A.001

PRODUCT CODE –see: (➔Probe identification).
The QR code or ID number identifies the probe and provides quick access to the following documentation on the
manufacturer’s website: User’s Manual, Explosion Proof Device Manual, Modbus Manual, declarations of con-
formity and copies of certificates.
SGE-25.Modbus
ID: 0044 0001 0001 0000 0000 0000 0001 77
https://www.aplisens.pl/ID/004400010001000000000000000177/
SGE-25.Modbus (Exi)
ID: 0044 0002 0001 0000 0000 0001 0001 94
https://www.aplisens.pl/ID/004400020001000000000001000194/
SGE-25S.Modbus
ID: 0045 0001 0001 0000 0000 0000 0001 74
https://www.aplisens.pl/ID/004500010001000000000000000174/
SGE-25S.Modbus (Exi)
ID: 0045 0002 0001 0000 0000 0001 0001 91
https://www.aplisens.pl/ID/004500020001000000000001000191/

Symbols used
Symbol
Description
Warning to proceed strictly in accordance with the information contained in the
documentation in order to ensure the safety and full functionality of the device
Information particularly useful during installation and operation of the device.
Information particularly useful during installation and operation of an Ex type device.
Information on disposal of used equipment.
BASIC REQUIREMENTS AND SAFE USE
The manufacturer will not be liable for damage resulting from incorrect installation,
failure to maintain a suitable technical condition of the device or use of the device
other than for its intended purpose.
Installation should be carried out by qualified staff having the required authorizations
to install electrical and I&C equipment. The installer is responsible for performing
the installation in accordance with manual as well as with the electromagnetic
compatibility and safety regulations and standards applicable to the type
of installation.
In systems with I&C equipment, in case of leakage, there is a danger to staff due
to the medium under pressure. All safety and protection requirements
must be observed during installation, operation and inspections.
If a malfunction occurs, the device should be disconnected and handed over to the
manufacturer for repair.
In order to minimize the risk of malfunction and associated risks to staff, the device
is not to be installed or used in particularly unfavourable conditions, where
the following hazards occur:
-possible mechanical impacts, excessive shocks and vibration;
-excessive temperature fluctuation;
-freezing of the medium.
Changes made to the manufacturing of products may be introduced before the paper version of the
manual is updated. The up-to-date manuals are available on the manufacturer’s website:
www.aplisens.com.

EN.IO.SGE.25.MODBUS
4Revision 01.A.001/2021.09
TABLE OF CONTENTS
1. INTRODUCTION..........................................................................................6
1.1. Purpose of the document .......................................................................................................6
2. SAFETY.......................................................................................................6
3. TRANSPORT AND STORAGE....................................................................7
3.1. Delivery check........................................................................................................................7
3.2. Transport................................................................................................................................7
3.3. Storage and use.....................................................................................................................7
4. GUARANTEE ..............................................................................................7
5. IDENTIFICATION.........................................................................................8
5.1. Manufacturer address ............................................................................................................8
5.2. Probe identification.................................................................................................................8
5.3. CE mark, declaration of conformity.........................................................................................8
6. INSTALLATION...........................................................................................9
6.1. General recommendation.......................................................................................................9
7. ELECTRICAL CONNECTION....................................................................10
7.1. Connection, signal output.....................................................................................................10
7.2. Power supply........................................................................................................................10
7.2.1. Power supply voltage....................................................................................................10
7.2.2. Shielding, equipotential bonding...................................................................................10
7.3. Operation mode in MODBUS network..................................................................................11
7.4. Overvoltage protection.........................................................................................................13
7.5. Final Inspection of cabling....................................................................................................13
8. START-UP.................................................................................................13
9. OPERATION..............................................................................................14
9.1. MODBUS register layout in the address space.....................................................................14
9.2. Pressure unit codes..............................................................................................................15
9.3. Modbus status register description.......................................................................................15
9.4. Error codes supported by Modbus........................................................................................15
10.MAINTENANCE.........................................................................................16
10.1. Periodic inspections .............................................................................................................16
10.1.1. External overview .........................................................................................................16
10.1.2. „Zero” check .................................................................................................................16
10.2. Non periodic inspections ......................................................................................................16
10.3. Cleaning/Washing................................................................................................................16
10.4. Diaphragm cleaning .............................................................................................................16
10.5. Spare parts...........................................................................................................................16
10.6. Repair ..................................................................................................................................16
10.7. Return..................................................................................................................................16
11.SCRAPPING, DISPOSAL..........................................................................17
12.HISTORY OF REVISIONS.........................................................................17
Explosion-proof device manual EN.IX.SGE.25.MODBUS ...........................18

EN.IO.SGE.25.MODBUS
Revision 01.A.001/2021.09 5
LIST OF DRAWINGS
Figure 1. Mounting brackets for probes...................................................................................9
Figure 2. Diaphragm cover for SGE-25S.Modbus probe.........................................................9
Figure 3. Connection in Modbus network..............................................................................12
LIST OF TABLES
Table 1.Symbols appearing on the probe’s nameplate...........................................................8
Table 2. Probe connection.....................................................................................................10
Table 3. Permissible power supply voltage for probes. .........................................................10
Table 4. A binary value assigned to the corresponding pressure unit. ..................................15

EN.IO.SGE.25.MODBUS
6Revision 01.A.001/2021.09
1. INTRODUCTION
1.1. Purpose of the document
The subject of manual are smart level probes: SGE-25.Modbus and SGE-25S.Modbus hereinafter
referred to as probes in the manual. The manual applies to the following versions: standard and intrin-
sically safe Exi.
The manual contains data, guidelines and general recommendations for the safe installation and oper-
ation of the probes, as well as procedures in the event of a possible failure.
It is forbidden to use devices in hazardous areas without appropriate permits.
Data on the hydrostatic level probes SGE-25.Modbus, SG-25S.Modbus and
SGE-25C.Modbus in intrinsically safe version according to IECEx and ATEX
are included in the Explosion-proof Device Manual marked as EN.IX.SGE.25.MODBUS.
2. SAFETY
−The installation and start-up of the device and anyactivities relatedto operation shall
be carried out after thorough examination of the contents of user’s manual and the
instructions related thereto;
−installation and maintenance should be carried out by qualified staff having
the required authorizations to install electrical and measuring devices;
−the device shall be used according to its intendedpurpose in line with the permissible
parameters specified on the nameplate (➔Probe identification);
−the protection elements used by the manufacturer to ensure probes safety may
be less effective if the device is operated in a manner not consistent with its intended
purpose;
−before installing or disassembling the device, it is absolutely necessary
to disconnect; it from the power source;
−no repairs or alterations to the probes electronic system are permitted. Assessment
of damages and possible repair may only be performed by the manufacturer
or authorized representative;
−do not use instruments if damaged. In case of malfunction, the device must be put
out of operation.

EN.IO.SGE.25.MODBUS
Revision 01.A.001/2021.09 7
3. TRANSPORT AND STORAGE
3.1. Delivery check
After receiving the delivery, please refer to the general terms and conditions of contracts available
on the manufacturer website: https://aplisens.com/ogolne_warunki_umow.html.
3.2. Transport
Transport of probes shall be carried out with the use ofcoveredmeans of transport, in original packages
with diaphragm provided with protection. The packaging shall be protected against movement
and direct impact of atmospheric factors.
3.3. Storage and use
Probes shall be stored in a factory packaging, in a room without vapours and aggressive substances,
protected against mechanical impact. The cable should be coiled into a circle with a diameter
of ≥ 30 cm, the coils of the coil should be fixed in relation to each other and the whole should be fixed
in the package. Avoid kinking the cable at the point where it exits the gland.
Permissible medium temperature range:
•SGE-25.MODBUS/ SGE-25S.MODBUS -25 … 40°C (-13 … 104°F);
•Special version - Teflon 0 … 75°C (32 … 167°F);
The medium must not be allowed to freeze in the immediate vicinity of the probe.
4. GUARANTEE
General terms and conditions of guarantee are available on the manufacturer's website:
www.aplisens.com/ogolne_warunki_gwarancji
The guarantee shall be repealed if the device is used against its intended use, failure
to comply with user’s manual or interference with the structure of the device.

EN.IO.SGE.25.MODBUS
8Revision 01.A.001/2021.09
5. IDENTIFICATION
5.1. Manufacturer address
APLISENS S.A.
03-192 Warsaw
Morelowa 7 St.
Poland
5.2. Probe identification
Depending on the version of the probe, the nameplates may differ in the amount of information
and parameters.
Table 1.Symbols appearing on the probe’s nameplate.
5.3. CE mark, declaration of conformity
The device has been designed to meet the highest safety standards, has been tested and has left
the factory in a condition that is safe for operation. The device complies with the applicable standards
and regulations listed in the EU Declaration of Conformity and has CE marking on nameplate.
Logo and name of manufacturer
CE mark
CE mark with number notified body
Manufacturer address
QR code
Probe type
Probe model ID
Probe serial number
Measuring range
Power supply voltage
Output signal
Permissible range of ambient temperature
IP protection rating
Year of production
Note about the obligation of read the manual
//Lower part of
the nameplate//
Special versions

EN.IO.SGE.25.MODBUS
Revision 01.A.001/2021.09 9
6. INSTALLATION
6.1. General recommendation
The probe can be hung on the power cable, e.g. by using from the Aplisens SG cable hanger (item 1
in fig. 1). In the event of frequent removal of the probe or when there is a risk of catching on protruding
elements during pulling up, it is recommended to hang the probe on a steel cord using the carrying eye
(item 2 in Fig. 1.). The probes are immersed in the medium to be measured. A special cable extends
above the level of the medium and can be connected directly to probe or to a junction box. If the probe
is to be placed in the current or in an area of turbulence, it should be installed in a protective tube.
Figure 1. Mounting brackets for probes.
Do not clean or touch the diaphragm with hard or sharp objects. Hang the probe with the additional
Teflon coating on the cable on the suspension cable or on the inner cable (do not grab the Teflon).
Remove the protective cap from the probe's separator immediately before
the SGE-25S.Modbus type probe is inserted into the medium to be measured.
During installation protect the probe from mechanical impacts
Figure 2. Diaphragm cover for SGE-25S.Modbus probe.

EN.IO.SGE.25.MODBUS
10 Revision 01.A.001/2021.09
7. ELECTRICAL CONNECTION
7.1. Connection, signal output
All connection and assembly activities must be performed with the power supply
disconnected and other external voltages, if used.
Incorrect connection of the probe may endanger safety.
Risk of electric shock and / or ignition in hazardous areas.
The electrical connection should be made according to Table. 2. It is recommended to install
the PP-Modbus connection box manufactured by Aplisens S.A. to connect the probe cable with the rest
of the transmission line. The PP-Modbus junction box is non-hermetic (pressure inside is equal to
atmospheric pressure) due to the use of an air filter, which is required for the probe to operate correctly.
Do not allow the capillary outlet to become contaminated or any liquid to enter the capillary.
Table 2. Probe connection.
Signal output
Type of connector
Wire colour
SHIELD
Green
+
Red
- (GND)
Black
RS-485 A +
Blue
RS-485 B -
Yellow
7.2. Power supply
7.2.1. Power supply voltage
Supply cables may be live.
There is a risk of electric shock and/or explosion.
Installation in potentially explosive atmospheres must comply with local standards
and regulations.
Table 3. Permissible power supply voltage for probes.
Mode
Output signal
MIN. Power supply
voltage
MAX Power supply
voltage
MODBUS mode - standard
version*
MODBUS RTU
4 V DC
28 V DC
MODBUS mode Exi version
MODBUS RTU
4 V DC
10 V DC
Configuration mode –standard
version
4…20 mA
5 V DC
28 V DC
*- power consumption in Modbus mode <3,6 mA.
7.2.2. Shielding, equipotential bonding
A cable shield (green cable) is led out of the probe power supply and measurement cable.
Connect the shield on one side at the probe supply point.

EN.IO.SGE.25.MODBUS
Revision 01.A.001/2021.09 11
7.3. Operation mode in MODBUS network
The SGE-25.Modbus and SGE-25S.Modbus probes have two modes of operation:
-configuration mode;
-Modbus mode.
The configuration mode is used to change the settings and for accurate diagnostics of the probe. In this
mode, in devices with software version at least 14 and electronics version at least 48, the current loop
is also activated, allowing operation with current output 4...20 mA.
The SGE-25.Modbus and SGE-25S.Modbus probes in Exi version have a Modbus RTU
interface without current regulator 4...20 mA.
If the user intends to use the 4...20 mA operating mode, the probe must be left in the configuration
mode after the parameters have been configured with the "Modbus Configurator" program.
Additional settings for the 4...20 mA operating mode beyond the scope of the "Modbus Configurator"
option are possible using the Report 2 program. If the user intends to use the Modbus mode of
operation, the probe must be switched to Modbus mode after the parameters have been configured
with the "Modbus Configurator" program.
The measuring range for 1/100th of an integer unit with sign is between -32767 and 32767 units.
Exceeding this range results in a skewed reading.
In case of pressure readings in binary format "Signed 16-bit int", the basic unit must be selected so that
100 times the pressure value expressed in it does not exceed the above range.
At all transmission speeds (especially at 115200 bps), a 120 Ω matching resistor should be used, which
by default is included via a jumper in the transmission circuit between the "Digital" A and B outputs
(Aplisens PP-Modbus boxes are factory equipped with a 120 Ω resistor).

EN.IO.SGE.25.MODBUS
12 Revision 01.A.001/2021.09
Figure 3. Connection in Modbus network.

EN.IO.SGE.25.MODBUS
Revision 01.A.001/2021.09 13
7.4. Overvoltage protection
Probes can be exposed to switching surges, or other surges, such as those resulting from lightning.
Protection against surges between the wires of the transmission line is provided by surge diodes.
For protection against surges between the transmission line and earth or housing (which are
not protected by diodes connected between the line conductors), the probes are equipped with
additional protection in the form of surge arrestors.
7.5. Final Inspection of cabling
After completing the electrical installation of the probe, it is necessary to check the following:
−that the supply voltage measured at the power supply terminals of the cable connection at the
maximum current is in accordance with the supply voltage range specified on the rating plate;
−is the probe connected according to the information given in section ➔ELECTRICAL
CONNECTION;
−when using a junction box, that the glands are tightened.
8. START-UP
The probe's basic data can be read from the device's rating plate (➔Probe identification).
Description of the communication protocol used in probes with Modbus digital output is available on the
manufacturer's website in “Modbus Configurator” manual.

EN.IO.SGE.25.MODBUS
14 Revision 01.A.001/2021.09
9. OPERATION
9.1. MODBUS register layout in the address space
Read-only data
Register
Address
(hex)
Purpose
Comments
Format
Number of bytes (2 bytes
per register)
1
0x0000
User value
% of the set range
IEEE754
4 bytes (2 registers)
3
0x0002
Pressure of sensor 1
Pressure or level process
variable
IEEE754
4 bytes (2 registers)
5
0x0004
Pressure of sensor 2
Constant value 0 ºC
IEEE754
4 bytes (2 registers)
7
0x0006
Temperature of
sensor 1
Sensor 1 temperature
process variable in ºC
IEEE754
4 bytes (2 registers)
9
0x0008
Temperature of
processor
Processor temperature
process variable in ºC
IEEE754
4 bytes (2 registers)
11
0x000A
Temperature of
sensor 2
Constant value 0 ºC
IEEE754
4bytes (2 registers)
13
0x000C
--------------------------
------------------------
-----------------
------
4bytes (2 registers)
15
0x000E
--------------------------
------------------------
-----------------
------
4bytes (2 registers)
17
0x0010
User value
1/100% controlled of
the set range
Signed
16-bit int
2 bytes (1 register)
18
0x0011
Pressure of sensor 1
Integer, 1/100 of pressure
or level unit
Signed
16-bit int
2 bytes (1 register)
19
0x0012
Pressure of sensor 2
Value 0
1/100 of the selected unit.
Signed 16-
bit int
2 bytes (1 register)
20
0x0013
Temperature of
sensor 1
Integer,
1/100 ºC
Signed
16-bit int
2 bytes (1 register)
21
0x0014
Temperature of
processor
Integer,
1/100 ºC
Signed
16-bit int
2 bytes (1 register)
22
0x0015
Temperature sensor 2
Value 0
1/100 w ºC
Signed
16-bit int
2 bytes (1 register)
23
0x0016
Pressure unit
Pressure or level unit
Unsigned
16-bit int
2 bytes (1 register)
➔Table 4
24
0x0017
--------------------------
------------------------
-----------------
------
2 bytes (1 register)
25
0x0018
Upper sensor range
Upper limit of the standard
range
IEEE754
4 bytes (2 registers)
27
0x001A
Lower sensor range
Lower limit of the standard
range
IEEE754
4 bytes (2 registers)
29
0x001C
Damping time
constant [s] second
IEEE754
4 bytes (2 registers)
31
0x001E
Response delay
Millisecond [ms]
Unsigned
16-bit int
2 bytes (1 register)
32
0x001F
Address Modbus
1…247
Unsigned
8-bit int
2 bytes (1 register)
33
0x0020
Identification register
Unsigned
8-bit int
6 bytes (3 registers)
36
0x0023
Status Register
8-bit flags
2 bytes (1 register)
* The shaded fields are not active in the described version of the devices.

EN.IO.SGE.25.MODBUS
Revision 01.A.001/2021.09 15
9.2. Pressure unit codes
Table 4. A binary value assigned to the corresponding pressure unit.
Unit
Value (decimal)
Unit
Value (decimal)
atm
14
mbar
8
bar
7
mmH2O (w 4°C)
239
FtH2O
3
mmH2O
4
g/cm²
9
mH2O (w 4°C)
171
InH2O (w 4°C)
238
mmHg
5
InHg
1
MPa
237
kg/cm²
2
Pa
11
kPa
10
psi
6
mbar
12
torr
13
9.3. Modbus status register description
15
14
13
12
11
10
9
8
7
6
5
4
3
2
1
0
0
0
0
0
0
0
0
0
0
SV,TV,FV out of
limit
PV out of
limit
0
0
0
0
0
9.4. Error codes supported by Modbus
Error
code
Designation
Description
1
Disallowed function code
The error occurs when the function code is unsupported by the de-
vice. Currently the function code with number 3 is implemented -
Read Holding Registers.
2
Disallowed data address
Error occurs for addresses out of the range 0x00 0x23.
3
Incorrect data quantity
Invalid number of read registers declared in frame.
4
Probe failure
Hardware fault detected.
8
Memory error
A RAM or FLASH error has been detected.

EN.IO.SGE.25.MODBUS
16 Revision 01.A.001/2021.09
10. MAINTENANCE
10.1.Periodic inspections
Periodic inspections should be carried out in accordance with the standards applicable to the user.
Check the processing characteristics by following the steps appropriate to the calibration
and configuration procedure described in the EN.IM.PCE.PRE.SGE.MODBUS document available on
the manufacturer's website.
10.1.1. External overview
During the inspection, check the condition of the separating membranes (tarnish, corrosion)
and the electrical connection (check the condition of the cable), as well as the stability of the handle
(if used). Check for signs of mechanical damage in the form of impact marks or dents.
10.1.2. „Zero” check
Every 2 years or in accordance with the user's standards, check the probe's "zero" by pulling the probe
above the liquid mirror and reading the output signal. Make any adjustments using the "Modbus
Configurator" software”.
10.2.Non periodic inspections
If the probe has been subjected to mechanical damage, pressure overload, hydraulic impulses,
electrical surges, deposits, crystallization of the medium, etching of the diaphragm, or if the probe
is found to be working incorrectly, the device should be inspected. Check the condition
of the diaphragm, clean it, check the electrical functionality and processing characteristics.
If the signal is missing in the transmission line or its value is incorrect, check the power
supply line, the state of connections on terminal strips, connections, etc. Check the correct
value of the supply voltage and the resistance of the load.
10.3.Cleaning/Washing
To remove impurities from the external surfaces of the probe wipe it with a cloth dampened
in water.
10.4.Diaphragm cleaning
The only possible method of cleaning the probe diaphragms is to dissolve the sludge produced.
Do not remove deposits and impurities from the probe diaphragms, which are formed
during operation, mechanically using tools, since the diaphragms and the probes
can be damaged.
10.5.Spare parts
Parts of the probe that may be worn or damaged and must be replaced: cable and gland seals.
The cable and seals can only be replaced by the manufacturer.
10.6.Repair
Faulty or non-operational probe shall be provided to the manufacturer or an authorized representative.
10.7.Return
In the following cases the, probe should be returned directly to the manufacturer:
-Need for repair;
-Need for factory calibration;
-Replacement of improperly selected/shipped probe.

EN.IO.SGE.25.MODBUS
Revision 01.A.001/2021.09 17
11. SCRAPPING, DISPOSAL
Worn or damaged devices shall be scrapped in accordance with WEEE Directive
(2012/19/EU) on waste electrical and electronic equipment or returned to the manufacturer.
12. HISTORY OF REVISIONS
Revision
No.
Document revision
Description of changes
1
D1/2018.12
The electrical parameters in point 2.3 of Part 1 have been completed.
2
D2/2019.05
The content of the comment in point 1 of Part 1 has been changed.
3
01.D.011/2020.06
The figure in point 5 and figure 1.5 in appendix Ex.04 has been
changed.
4
01.A.001/2021.09
New version of the document. Replaces the revision
01_01.D.011_2020-01. Change of software, power supply, figures.
Editorial changes. Prepared by DBFD.

EN.IO.SGE.25.MODBUS
EN.IX.SGE.25.MODBUS
18 Revision 01.A.001/2021.09
Explosion-proof Device Manual EN.IX.SGE.25.MODBUS
LEVEL PROBES:
SGE-25.Modbus, SGE-25C.Modbus, SGE-25S.Modbus
INTRINSICALLY SAFE acc. to ATEX
1. Introduction
Explosion-proof Device Manual EN.IX.SGE.25.MODBUS only applies to probes SGE-25.Modbus,
SGE–25S.Modbus, SGE–25C.Modbus in intrinsically safe version acc. to ATEX marked as in point 2
and the Ex information in the Product Certificate. During installation and useof Ex probes it is necessary
to use User’s Manual EN.IO.SGE.25.MODBUS with „Explosion-proof Device Manual
EN.IX.SGE.25.MODBUS”.
2. Using probes in hazardous area.
The probes are produced in accordance with the requirements of the following standards:
EN 60079-0:2018-09, EN 60079-11:2012, EN 50303:2004
The probes may operate in areas where there is a risk of explosion, in accordance with the rating of the
explosion protection design:
I M1 Ex ia I Ma
II 1G Ex ia IIB T4/T5/T6 Ga
FTZÚ 18 ATEX 0077X
3. Permissible input parameters (based on data from the FTZÚ 18 ATEX 0077X)
For the connection of the power supply line and the RS485 data transmission signal line, use
devices that have the relevant intrinsic safety certificates, whose parameters must not exceed
the permissible input-output parameters given in points a) and b).
The probes should be powered from devices with galvanically separated power supply.
Minimum probe supply voltage 4 V DC.
The probe is an intrinsically safe device with protection level "ia" when the power supply circuit
has protection level "ia"
a) Permissible input parameters for power supply (red “+”, black “-“)
- for power supply with linear characteristics:
Ui ≤ 10 V, Ii ≤ 0.4 A,
- for power supply with rectangular and trapezoidal characteristics:
Ui ≤ 5 V, Ii ≤ 0.4 A
b) Permissible input and output parameters for RS485 transmission (blue VA, yellow VB):
Ui ≤ 10 V, Ii ≤ 0.2 A, Uo ≤ 10V*, Io ≤ 0.4 A*
* the output parameters of the probes Uo, Io are equal to the output parameters Uo, Io of the power supply used.
Dependence of temperature class of probes on ambient temperature (including temperature of
measured medium) Ta [°C] and sum of power Pi [W] in power supply circuit and in RS485 transmission
circuit is given in Table Z1.
Min. ambient temperature Ta = -40°C (special version from -50°C).
c) The internal capacitance and inductance of the probe in the power supply circuit and in the RS485
transmission circuit is: Li= 0 µH, Ci≈ 2.5 µF **
d) The maximum capacitance and inductance that can be connected to the probe in the transmission
circuit is for the subgroup:
- IIC Lo= 0.2 mH, Co = 0.5 µF;
- IIB Lo= 0.7 mH, Co = 15 µF;
- IIA and group I Lo= 1.7 mH, Co = 80 µF.
** Consider the cable capacitance and inductance, which for a permanently connected cable are:
Ck = 0,2 nF/m i Lk = 1 µH/m

EN.IO.SGE.25.MODBUS
EN.IX.SGE.25.MODBUS
Revision 01.A.001/2021.09 19
Table Z1. Temperature class dependence on ambient temperature Ta and total amount of input power Pi.
Pi [W]
Total input power of
485 power and
transmission
circuits
Ta
[ºC]
Class
temp.
Pi [W]
Total input power of
485 power and
transmission
circuits
Ta
[ºC]
Class
temp.
Pi [W]
Total input power of
485 power and
transmission
circuits
Ta
[ºC]
Class
temp.
0.25
65
T6
0.75
55
T6
1.5
65
T5
80
T5
80
T5
80
T4
0.5
60
T6
1.2
70
T5
1.75
60
T5
80
T5
80
T4
80
T4
4. Connection of probes in Ex version
Connections of the probe and devices in the probe measuring loop must be made in accordance with
intrinsic safety and explosion protection standards and conditions of use in hazardous areas. Failure to
observe the intrinsic safety rules may result in an explosion and resultant danger to people.
Fig. I.1

EN.IO.SGE.25.MODBUS
EN.IX.SGE.25.MODBUS
20 Revision 01.A.001/2021.09
Fig. I.2
5. Special conditions for safe use
1. The probes do not meet the insulation test (500 V rms) required by EN 60079 11:2012.
This must be taken into account during installation of the device.
2. For the ambient temperature range –see Table Z1 as well as the information on the probe's
rating plate.
3. The process (medium) temperature at the diaphragm must be within the ambient temperature
range.
Other manuals for SGE-25.Modbus
1
This manual suits for next models
1
Table of contents
Other Aplisens Measuring Instrument manuals
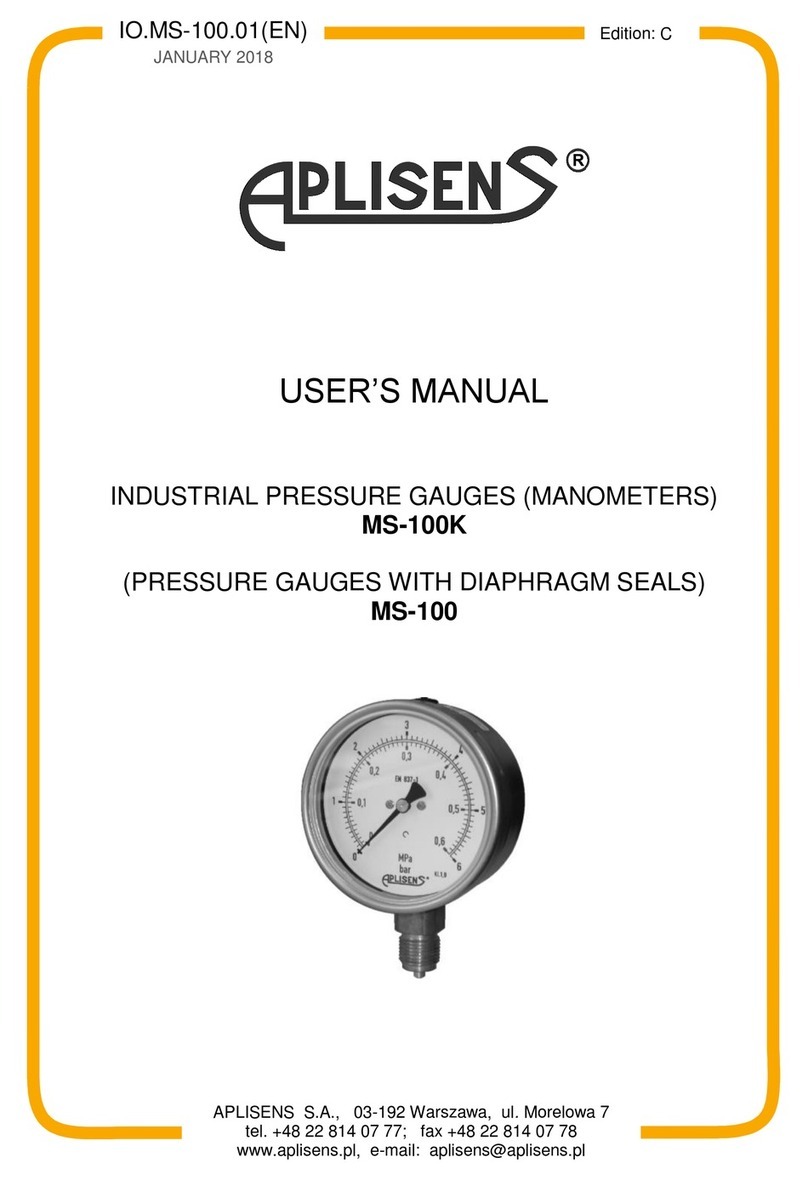
Aplisens
Aplisens MS-100K User manual
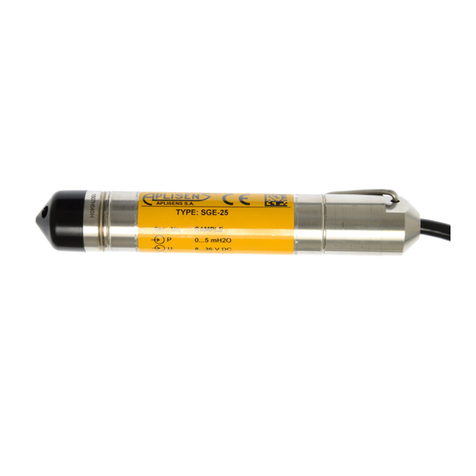
Aplisens
Aplisens SGE-25.SMART User manual

Aplisens
Aplisens WW-30Pt User manual
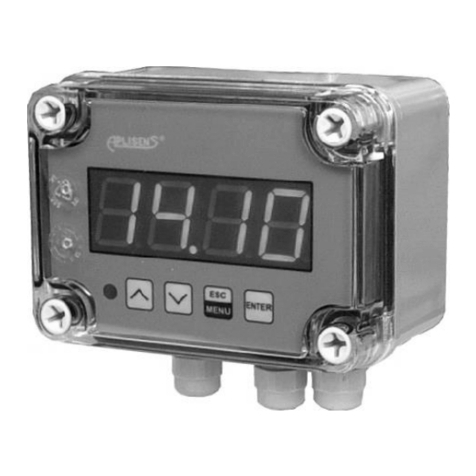
Aplisens
Aplisens PMS-620N User manual

Aplisens
Aplisens PEM-1000 User manual
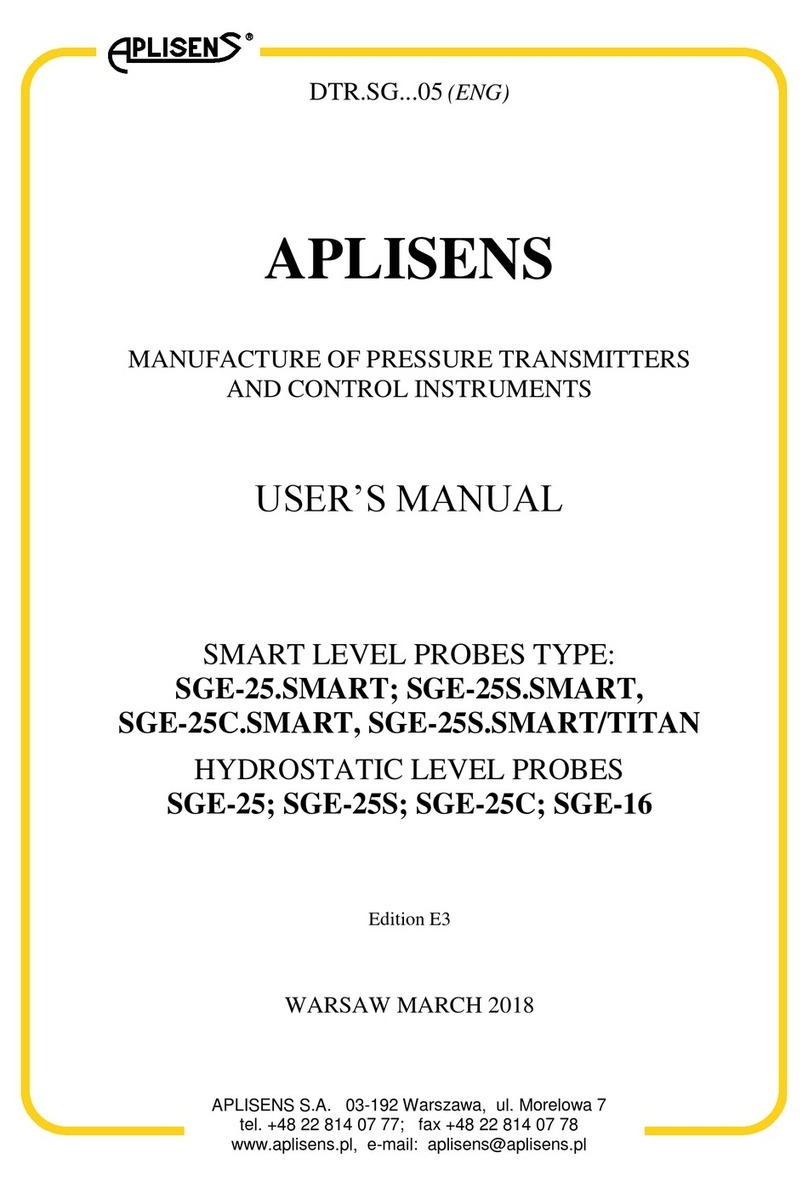
Aplisens
Aplisens SGE-25.SMART User manual

Aplisens
Aplisens CS-27/W User manual
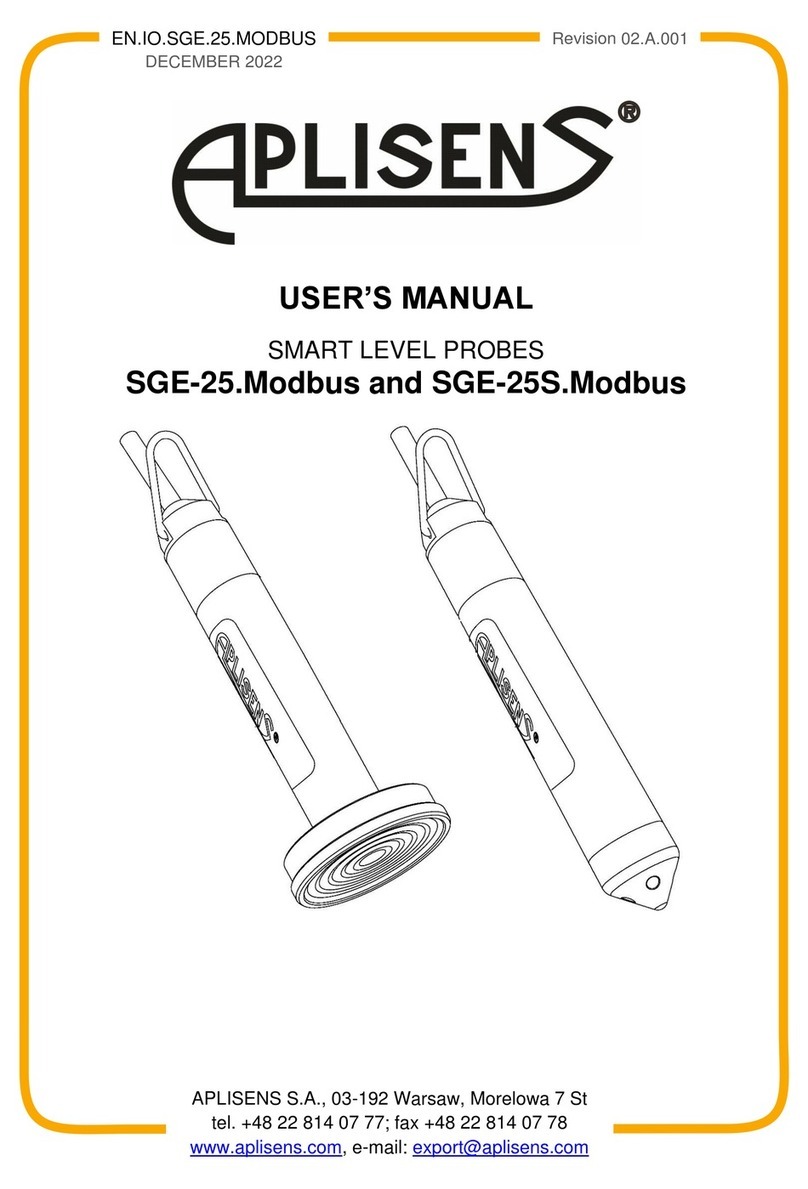
Aplisens
Aplisens SGE-25.Modbus User manual
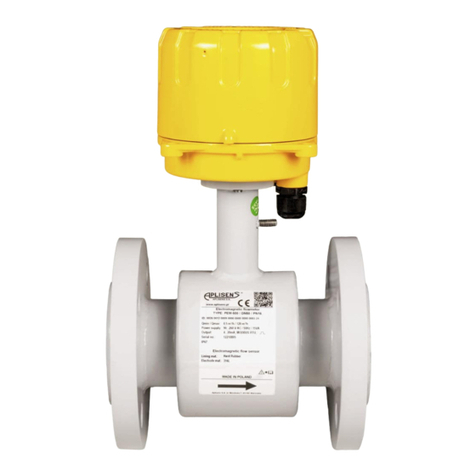
Aplisens
Aplisens PEM-500 User manual
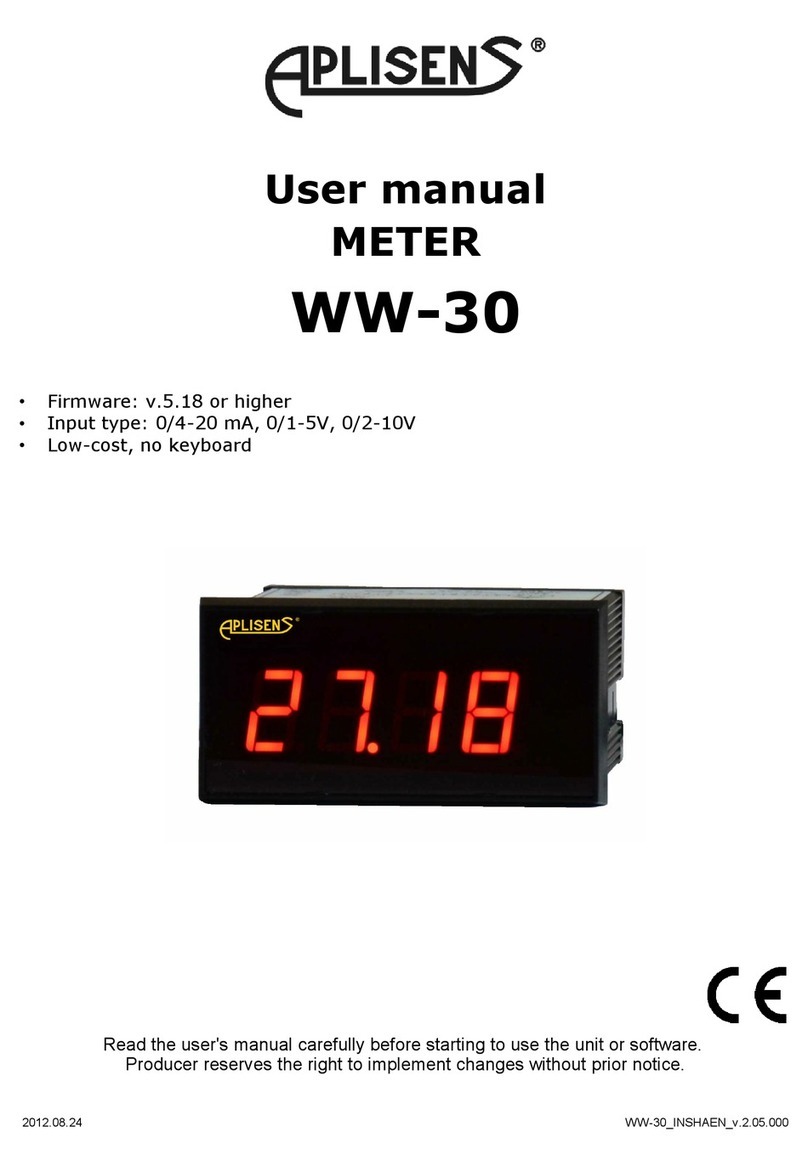
Aplisens
Aplisens WW-30 User manual