Arbortech AS200X User manual

ALLSAW AS200X
SERVICE MANUAL
ALL.FG.200240.00
ALL.FG.200240.40
ALL.FG.200240.60
ALL.FG.200110.20
ALL.FG.200110.40
The contents of this manual are confidential and should not be distributed without written approval from
Arbortech Pty Ltd.

Contents
1INTRODUCTION ..............................................................................................................................................1
2SERVICING INFORMATION..............................................................................................................................1
2.1 Diagnosis and Troubleshooting.............................................................................................................1
2.2 Service Time Estimates .........................................................................................................................1
2.3 Torque Settings and Driver Types .........................................................................................................1
2.4 Exploded Diagram and Parts List...........................................................................................................2
2.4.1 Mechanism and Ancillaries ...............................................................................................................2
2.4.2 Motor and Electrical .........................................................................................................................4
3SERVICE PROCEDURES ....................................................................................................................................6
3.1 Head Shells and Ancillaries....................................................................................................................6
3.1.1 Right Hand Head Shell ......................................................................................................................6
3.1.2 Handle Locking Button......................................................................................................................6
3.1.3 Left Hand Head Shell.........................................................................................................................6
3.1.4 Top Handle........................................................................................................................................6
3.1.5 Dust Extraction Bracket ....................................................................................................................7
3.1.6 Wire Guard and Nose Hook ..............................................................................................................7
3.1.7 Retractor...........................................................................................................................................7
3.2 Belt and Pulleys.....................................................................................................................................8
3.2.1 Belt Tensioning .................................................................................................................................8
3.2.2 Belt Inspection and Replacement .....................................................................................................8
3.2.3 Pulleys...............................................................................................................................................8
3.3 Motor ....................................................................................................................................................9
3.3.1 Brushes Inspection & Replacement..................................................................................................9
3.3.2 Mounting Screws Inspection ............................................................................................................9
3.3.3 Motor Separation ...........................................................................................................................10
3.4 Castings and Mechanism.....................................................................................................................11
3.4.1 Top Springs .....................................................................................................................................11
3.4.2 Left Hand Casting............................................................................................................................12
3.4.3 Gearbox inspection.........................................................................................................................13
3.4.4 Conrods Assembly........................................................................................................................... 13
3.4.5 Right Hand Casting..........................................................................................................................13

1
1INTRODUCTION
This manual details the common procedures for maintenance and repair work for the Arbortech AS200X. These procedures may
be required following tool wear or failure from use. The most common maintenance items are drive belt and motor brush
replacement, which will occur from extended use. If the tool is damaged beyond these items, replacement of internal bearings,
mechanism components, castings, head shells or motor components may be necessary.
At all times when performing maintenance or repair tasks, the following safety guidelines must be observed:
•Only properly trained and qualified technicians should complete repairs involving potential hazards
•Use appropriate PPE including, but not limited to, suitable eye and ear protection
•Never attempt any service or repair work with the tool connected to any power source
•Handle electrical components with care and take all necessary precautions to avoid electrical hazards
•Beware of mechanical hazards, such as pinch points between moving parts, and components which may be hot
Procedures are described with accompanying images. Tools are listed (in brackets), for example, the size of hex key required. Refer
to the owner’s manual for operation procedures and general specifications.
2SERVICING INFORMATION
2.1 Diagnosis and Troubleshooting
The most common symptoms of a mechanical or electrical failure are listed below, with the appropriate steps to diagnose and
remedy the fault.
Symptom
Cause
Check/Remedy
Section
Blades frequently jam
and stop during cutting
Insufficient belt tension
Check belt tension
3.2.1
Excessive belt wear
Replace belt if required
3.2.2
Motor runs but blades
do not move
Belt failure
Check tension, replace belt
3.2.2
Gearbox failure
If no pulleys move, inspect gearbox
3.4.3
Motor does not run
when switch is activated
Brush failure
Inspect/replace brushes
3.3.1
Motor failure
Replace motor
3.3.3
Conrod pitching freely
Top spring failure
Replace top spring
3.4.1
Blade does not attach or
stay attached
Incorrectly attaching blades
Refer user manual for correct method
Conrod blade mount damaged
Replace conrod assembly
3.4.4
Motor overheating
and/or running slowly
Blades jammed with debris
Clear any debris
Cooling vents blocked
Clear cooling vents
Brushes worn
Inspect brushes, replace
3.3.1
Motor casing loose
Check motor mount screws
3.3.2
Mechanism failure or jam
Inspect mechanism
Bearing or gearbox failure
Inspect bearings and/or gearbox
3.4.2 - 3.4.4
Motor failure
Replace motor
3.3.3
Excessive gearbox or
bearing noise
Bearing failure
Inspect bearings
3.4.2, 3.4.4
Crown wheel/pinion damage
Inspect gearbox
3.4.3
2.2 Service Time Estimates
Process
Time (mins)
Belt inspection and replacement, brush inspection and replacement, handle washers replacement
10
Crown wheel and pinion inspection or replacement, motor change
20
Camshaft assembly replacement, full bearing inspection and replacement
30
2.3 Torque Settings and Driver Types
Fastener
Torque (Nm)
Driver Type
Motor mount screws
1.5 - 2
Torx T20
Idler screw
8
5 mm hex
Casting screws
10
4 mm hex
Top spring screws (conrods and casting)
18
5 mm hex
Left head shell screws
6
Torx T25
Right head shell screws
6
5 mm hex
Bridging screw
8
5 mm hex
Dust extraction bracket screw
2
3 mm hex

2
2.4 Exploded Diagram and Parts List
2.4.1 Mechanism and Ancillaries
This diagram provides an overview of the AS200X components. Detailed diagrams of assembly positions and alignments are shown
in the Service Procedures section.

3
Description
Part No.
Details
Model
Qty.
1
Handle washer
ALL.FG.WASH030
200
2
2
Handle Pin
ALL.FG.PIN005
10 x 35 mm dowel
200
1
3
Top handle
ALL.FG.HANDLE003
200
1
4
Idler nut
ALL.FG.NUT006
M6 Nyloc
170/175/200
1
5
Idler washer
ALL.FG.WASH024
170/175/200
1
6
Tension idler
ALL.FG.TENSION002
Includes ALL.FG.BEARING003
175/200
1
7
Tension idler bearing
ALL.FG.BEARING003
170/175/200
1
8
Idler screw
ALL.FG.SCREW013A
M6 x 20 grade 12.9
200
1
9
Right hand head shell
ALL.FG.HEADSHELLRH
Includes button ALL.FG.BUTTON001
200
1
10
Handle locking button
ALL.FG.BUTTON001
200
1
11
Right head shell screw
ALL.FG.SCREW025
M6 x 10 grade 12.9
200
3
12
Drive belt
ALL.FG.BELT003
OPTIBELT 3PJ280
175/200
1
13
Power pulley
ALL.FG.PULLEY008
175/200
1
14
Driven pulley
ALL.FG.PULLEY007
175/200
1
15
Nose hook
ALL.FG.HOOK001
200
1
16
Wire guard
ALL.FG.GUARD005
200
1
17
Motor screw
ALL.FG.SCREW028
Includes spring washers
200
4
18
Retractor homing spring
ALL.FG.SPRING005
200
1
19
Retractor
ALL.FG.RETRACTOR001
200
1
20
Dust Boot
ALL.FG.BOOT003
200
1
21
Conrods assembly
ALL.FG.CONROD004
200
1
22
Top spring washer
ALL.FG.WASH027
170/175/200
4
23
Conrod clamp washer
ALL.FG.WASH022
170/175/200
2
24
Top spring conrod screw
ALL.FG.SCREW013
M6 x 20 grade 12.9
170/175/200
2
25
Top springs kit
ALL.FG.SPRINGASS003
200
1
26
Double clamping washer
ALL.FG.WASH025
170/175/200
1
27
Nord-lock washer
ALL.FG.WASH019
M6
170/175/200
4
28
Top spring casting screw
ALL.FG.SCREW026
M6 x 16 grade 12.9
200
2
29
Casting screw, long
ALL.FG.SCREW023
M6 x 35 grade 12.9
200
2
30
Casting screw, short
ALL.FG.SCREW022
M6 x 16 grade 12.9
200
1
31
Left hand head shell
ALL.FG.HEADSHELLLH
200
1
32
Left head shell screw
ALL.FG.SCREW018
M5 x 10 self-tapping
200
3
33
Bridging screw
ALL.FG.SCREW019
M6 x 30 plastic tapping
200
1
34
Handle locking pin e-clip
ALL.FG.CLIP006
6 mm
200
1
35
Handle button spring
ALL.FG.SPRING007
200
1
36
Handle locking pin
ALL.FG.PIN003
200
1
37
Left hand casting
ALL.FG.HOUSE200LH
Includes bearings
200
1
38
Camshaft bearing
ALL.FG.BEARING002
170/175/200
2
39
LH crown shaft bearing
ALL.FG.BEARING011
200
1
40
Crown shaft assembly
ALL.FG.CROWN200
200
1
41
Gearbox O-ring
ALL.FG.SEAL003
54 x 2 mm
200
1
42
RH crown bearing circlip
ALL.FG.CLIP008
200
1
43
RH crown shaft bearing
ALL.FG.BEARING002A
200
1
44
Right hand casting
ALL.FG.HOUSE200RH
Includes bearings, circlips, o-ring
200
1
45
Dust extraction bracket screw
ALL.FG.SCREW024
M4 x 10 grade 12.9
200
1
46
Dust extraction bracket
ALL.FG.BRACKET005
200
1
47
Motor
Australia
ALL.FG.MOTOR175.00
230V
175/200
1
UK
ALL.FG.MOTOR175.40
230V
175/200
UK Industrial
ALL.FG.MOTOR175.41
120V
175/200
Europe
ALL.FG.MOTOR175.60
230V
175/200
USA
ALL.FG.MOTOR175.20
120V
175/200
48
Armature circlip
ALL.FG.CLIP005
22 x 1.2 increased abutment
175/200
1
49
Armature bearing
ALL.FG.BEARING007
175/200
1
50
Spindle O-ring
ALL.FG.SEAL175
BS020
175/200
1
51
Pinion gear
ALL.FG.PINION002
175/200
1
52
Pinion nut
ALL.FG.NUT002
175/200
1

4
2.4.2 Motor and Electrical

5
Description
Part No.
Qty.
11
Bearing Cup
See item 102
12
Rear armature bearing
See item 102
13
Magnet
See item 102
14
Armature
See item 102
31
Baffle fan
N399419
1
32
Plug, rubber
949638-02
2
33
Field
230V
N474622
1
120V
N474963
34
Field case
N548995
1
35
Brush box
See item 107
36
Spring
See item 107
38
Brush cap
N462741
2
39
Brush cap screw, M3
648777-00
2
40
Brush box screw, M3 x 8
593478-00
4
41
Separator
N458066
1
42
Insert
N451017
1
43
Switch
N451612
1
44
Switch screw, M4 x 6
330065-07
1
45
Cord
Australia
562226-85
1
UK
562226-86
UK Industrial
562226-87
Europe
562226-84
USA/CAN
330081-18
46
Protector
N542553
1
47
Cord clamp
N174601
1
48
Cord clamp screw, M3.5 x 16
30019-03
2
51
Field case screw, M4 x 40
N389438
2
52
End handle screw, M4 x 18
330065-08
5
64
Capacitor
Omitted in USA/CAN region
N482574
1
102
Armature assembly
230V
N490496
1
UK Industrial
N474960
USA/CAN
N490499
107
Brush box
N413349
1
108
Brush (pair)
230V
N489059
2
UK Industrial
N421361
USA/CAN
N257540
109
End handle assembly
N548991
1

6
3SERVICE PROCEDURES
3.1 Head Shells and Ancillaries
3.1.1 Right Hand Head Shell
To disassemble:
1. Unscrew the bridging screw (5 mm hex)
2. Unscrew the three right hand head shell screws (5
mm hex)
3. Remove the shell. Most resistance will be around
the base of the top handle.
Assembly is the reverse procedure, taking care to align the
handle pivot pin, handle locking pin and retractor pivot into
their corresponding holes. Torque the right head shell
screws to 6 Nm and the bridging screw to 8 Nm.
3.1.2 Handle Locking Button
Warning: detaching the button from the right hand head
shell permanently damages the button. It should only be
removed if it requires replacement.
1. Remove the right hand head shell as per 3.1.1. From
the inside of the shell, use a sharp probe to bend or
snap the button retaining hooks until the button
can be removed. Take care not to damage the
surrounding hole surface.
2. Align the new button with the head shell hole and
press firmly to engage the hooks through the hole.
3.1.3 Left Hand Head Shell
To disassemble:
1. Remove the right hand head shell as per 3.1.1
2. Unscrew the three left head shell screws (Torx T25)
3. Rotate the head shell around the retractor as
shown until the shell is inverted then unhook the
retractor from the conrods and the wire guard.
Rotating either forwards or rearwards may be
easier depending on the conrods position.
Assembly is the reverse process, taking care to correctly
hook the retractor through the conrods and the wire guard.
When starting the three screws take care to correctly find
the hole threads since they are easily damaged. Torque the
left head shell screws to 6 Nm.
3.1.4 Top Handle
To service the top handle and handle adjustment
mechanism, first remove the right hand head shell as per
3.1.1.
The top handle, handle washers and pivot pin can then be
inspected and replaced if necessary. A small amount of
movement between the handle and the pivot pin is
acceptable and is part of the vibration isolation system.
When installing a new top handle ensure it is facing forwards
with one handle washer on each side.
To remove the handle locking pin, pry off the e-clip with a
small flat blade screwdriver. The pin will be partly ejected by
the spring. When assembling the locking pin do not apply oil
or grease to the mechanism as they may attract dust.

7
3.1.5 Dust Extraction Bracket
To remove the bracket, unscrew the dust extraction bracket
screw (3 mm hex). The bracket can then be pivoted
downwards and unhooked from the right hand casting. Note
the wire guard may spring out of place by several mm.
When assembling the dust extraction bracket, hook it into
the casting then pivot upwards to trap the wire guard.
Ensure the bracket is seated squarely then tighten the screw
carefully to the required torque (2 Nm).
3.1.6 Wire Guard and Nose Hook
To disassemble:
1. Remove the head shells as per 3.1.1 & 3.1.3 and the
dust extraction bracket as per 3.1.5
2. Unwind the three casting screws by 4 turns each (4
mm hex)
3. Using a soft-face hammer, separate the left hand
casting from the right hand casting until it reaches
the limit of the casting screws or the nose hook is
released.
4. Remove the nose hook
5. To also remove the wire guard, pinch together the
front ends until they are released from the castings.
Assembly is the reverse procedure, with the following notes:
•Use a soft-face hammer to tap the left hand casting
back to its original position. Do not use the casting
screws to pull the castings together.
•As the left hand casting is assembled check the
gearbox o-ring is still correctly seated inside the
gearbox.
•Once the left hand casting is assembled, tighten the
three casting screws to hand tight, then torque to
10 Nm.
3.1.7 Retractor
Shallow marking or grooving of the retractor can occur as
part of normal operation. Severe grooving may indicate a
malfunction in one or both conrods. If the retractor is
damaged or no longer allows blades to be installed or
removed, it must be replaced. If the retractor does not
return to the home position after use, the retractor homing
spring should be inspected and may need replacing.
To disassemble:
1. Remove the head shells as per 3.1.1 & 3.1.3. The
retractor should rotate smoothly in the left hand
head shell and the homing spring should force the
retractor to its home position.
2. Unhook the retractor homing spring from the left
hand head shell post.
3. Slide the retractor out of the head shell hole.
4. If replacing the homing spring, unhook it from the
retractor.
Assembly is the reverse process, taking care to ensure the
homing spring is oriented correctly and is hooked onto the
left hand head shell post.

8
3.2 Belt and Pulleys
3.2.1 Belt Tensioning
To tension the belt without disassembly:
1. Loosen the idler screw (5 mm hex) until the screw
can be moved along the slot (approximately 1 turn).
Do not loosen further.
2. Using the hex key, push the screw upwards towards
the handle to tension the belt. While the screw is
being pushed, tighten it to hand tight.
3. Torque the idler screw to 8 Nm.
4. Check belt tension is sufficient to prevent slipping
during use.
If belt tension cannot be achieved remove the right hand
head shell as per 3.1.1 and inspect the belt as per 3.2.2
3.2.2 Belt Inspection and Replacement
Remove the right hand head shell as per 3.1.1.
The belt can be tensioned as per 3.2.1 if required.
If sufficient tension to prevent slipping during use cannot be
achieved within the travel of the idler, the belt is worn and
should be replaced:
1. Loosen the idler screw (5 mm hex) until the idler can
be moved along the slot (approximately 1 turn). Do
not loosen further.
2. Move the idler down the slot away from the handle.
3. Remove the belt.
4. Install the new belt. Avoid rolling the belt during
installation. Check to ensure it is correctly seated on
all three pulleys.
5. Tension as per 3.2.1
3.2.3 Pulleys
Before servicing the pulleys, both head shells must be
removed as per 3.1.1 and 3.1.3 and the belt must be
removed as per 3.2.2.
Remove the power pulley by locking the opposite end of the
shaft with a flat blade screwdriver and unwinding the pulley
with a pin spanner. Note it is a left-hand (reversed) thread.
Warning: never activate the motor when the power pulley is
disassembled. Doing so may cause permanent damage to
the gears.
Remove the driven pulley by locking the near end of the
shaft with a flat blade screwdriver and unwinding the pulley
with a pin spanner. It uses a right-hand (standard) thread.
When installing the driven pulley apply a drop of Loctite 243
to the camshaft thread. Tighten both pulleys thoroughly.
Before removing the tension idler, move it to its highest
position and hold the idler nut in place so it does not fall into
the mechanism. Fully unwind the screw to remove the
pulley. During assembly ensure:
•The idler washer’s largest face is towards the casting
•The tension idler’s open side is away from the casting
Reassemble the belt and tension as per 3.2.2.

9
3.3 Motor
3.3.1 Brushes Inspection & Replacement
The AS200 motor uses two brushes (top and bottom), one of
which is fitted with an auto cut-off system. If the brush fitted
with the system has reached the auto cut-off, or if either
brush has worn to limit, replace both.
To disassemble:
1. Unscrew the two screws retaining the brush covers
(flat blade screwdriver or Torx T10)
2. Remove both brush covers (see diagram for pry
point)
3. Lift both brush springs to the side
4. The brushes can be lifted from their holders for
inspection without disconnecting
5. If replacing the brushes, disconnect the connector
at the end of the brush wire and remove the old
brush
Assembly is the reverse process, taking care to:
•fit the brush wire into the slot in the brush holder
•seat the brush spring in the slot in the brush holder
and in the groove on top of the brush.
Warning: confirm the brush springs have been
seated. Failure to do so can cause rapid damage to
brushes and commutator.
3.3.2 Mounting Screws Inspection
The motor is attached to the right hand casting with four
dedicated plastic tapping screws with spring washers. If the
motor is loose on the casting, remove the head shells as per
3.1.1 & 3.1.3 and tighten the screws (Torx T20) to 2 Nm. If
they cannot be tightened to the specified torque, the plastic
motor housing has stripped and should be replaced as per
3.3.3. Do not substitute alternate screws. Take care when
removing and installing screws to avoid stripping the thread.

10
3.3.3 Motor Separation
If the armature requires replacement, the LH casting and
crown shaft should be disassembled first as per 3.4.2 and
3.4.3 before separating the motor. Most other tasks
requiring motor separation (such as replacing the field,
replacing the field case, or inspecting the armature) can be
performed with the LH casting in place.
To disassemble:
1. Remove the head shells as per 3.1.1 & 3.1.3
2. Lift the brushes as per 3.3.1
3. Unscrew the four motor mount screws (Torx T20)
4. Pull the motor away from the casting. There should
be a slight resistance as the armature separates
from the motor. Pull straight without bending or
twisting. Take care not to damage the armature,
which will remain attached to the right hand
casting.
If the left hand casting and crown shaft have already
been disassembled, the armature can be separated
from the right hand casting:
5. Hold the armature using a soft-jaw vice at the
location indicated
6. Undo the pinion nut (10 mm)
7. Pull the armature out of the armature bearing
8. If the bearing requires replacement, remove the
circlip, bearing and o-ring.
Inspection points:
Check the motor commutator, armature and field for visible
damage or significant wear.
Check the armature bearing (in right hand casting). Replace
if it does not rotate smoothly or is visibly damaged. Replace
the o-ring if it is damaged.
To assemble
1. Fit the replacement o-ring and bearing if required,
and fit the circlip with rounded face away from the
bearing (tabs pressing towards the bearing)
2. Check the armature spindle is clean then align and
push the spindle into the bearing
3. Fit the pinion onto the armature spindle inside the
gearbox
4. Apply a small drop of Loctite 243 to the thread for
the pinion nut then thread the nut on with the small
serrations towards the pinion.
5. Hold the armature and tighten the pinion nut to
firm hand tight
6. Check the brushes are outside the motor body then
carefully feed the armature into the motor.
7. Once the motor seats against the casting, check the
motor and casting are oriented correctly (trigger
opposite to top springs).
8. Carefully thread in the four motor screws, locating
the existing threads if possible. Tighten the screws
to 2 Nm, taking care not to strip the threads.
9. Re-fit the brushes as per 3.3.1

11
3.4 Castings and Mechanism
The aluminium castings (left hand and right hand) form the
gearbox and provide mounting points for the mechanism,
head shells and ancillaries. The left hand casting must be
disassembled to access the gearbox, remove the armature
or to remove the mechanism. The left hand casting must be
assembled when removing or installing the top springs.
3.4.1 Top Springs
If a top spring has failed, both springs should be replaced
using the top springs kit. Warning: a top spring failure can
damage other components such as the head shells, which
should be inspected thoroughly. Replace all existing washers
and screws with the new washers and screws supplied in the
kit. Note: the conrods assembly kit and top springs kit
include several duplicate washers and screws.
To disassemble:
1. Remove the head shells as per 3.1.1 & 3.1.3
2. Unscrew the four top spring screws (5 mm hex)
(two at the casting and two at the conrods).
Inspect the casting spring seat and the tops of the conrods
for any damage caused by a broken spring. If any damage is
visible, replacement is required.
Note the left hand casting must be in place before
assembling new top springs.
To assemble:
1. Check the spring seat, the tops of the conrods,
the threaded holes in the casting, the springs and
all washers are clean.
2. Do not scrape or abrade the springs to remove
residue or debris. If a spring is scratched it must
be replaced.
3. Assemble the screws and washers as shown,
taking care to orient each washer correctly
(top/bottom and front/back).
4. Include a small drop of Loctite 243 on the last
thread of each screw and wind them into the
casting and conrods. Note the shorter (16 mm)
screws fasten into the casting and the longer (20
mm) screws fasten into the conrods. Do not
tighten any screws until all four are in place.
5. Gradually tighten the four screws, ensuring the
washers at the conrods remain square to the top
springs. Tighten all four screws to 18 Nm. Pay
special attention to the conrod screws which
may give a false tight feeling while the screws
and washers settle (approx 1 turn before fully
tightening).
Do not allow the tool to sit for more than 10 mins
with Loctite applied before tightening fully.

12
3.4.2 Left Hand Casting
To disassemble:
1. Remove the head shells as per 3.1.1 & 3.1.3 and the
drive belt as per 3.2.2. Remove the dust extraction
bracket as per 3.1.5 can improve access but is not
essential.
2. Remove the top spring conrod screws (5 mm hex)
and washers
3. Remove the three casting screws (4 mm hex)
4. Use a soft-face hammer to gently tap the left hand
casting away from the right hand casting. A rod-
type punch with a soft end (e.g. plastic) can be used
with care at the locations indicated.
Inspection points:
Check both the bearings which mount in the left hand casting
(they may remain attached to their shafts after disassembly).
Replace if they do not rotate smoothly or are visibly
damaged. Check the o-ring for cracks or tears and replace if
any defects are found. If possible, replace the o-ring each
time the left hand casting is disassembled.
To assemble:
1. Seat the o-ring into the right hand casting, flush
with the opening face of the gearbox.
2. Align the left hand casting on the crown shaft and
cam shaft, and gently tap with a soft-face hammer
to begin fitting
3. Check the two dowel bushes are aligned with the
corresponding holes (see diagram) and the o-ring
remains seated inside the gearbox.
4. Ensure the wire guard and nose hook are fitted as
per 3.1.6. They cannot be added after the casting is
assembled.
5. Continue tapping the casting into position with a
soft-face hammer until it is fully seated (no gaps at
the contact surfaces).
6. Install the three casting screws to hand tight. Note
the short screw (16 mm) fastens at the upper hole
near the top springs, and the two longer screws (35
mm) fasten at the front and lower holes.
7. Torque the three casting screws to 10 Nm.
8. Reassemble the top spring conrod screws, washers
and Loctite 243 as per 3.4.1. Torque to 18 Nm.

13
3.4.3 Gearbox inspection
To disassemble:
1. Remove the head shells as per 3.1.1 & 3.1.3, the
drive belt as per 3.2.2, the power pulley as per 3.2.3
and the left hand casting as per 3.4.2.
2. Use a soft-face hammer to tap the threaded end of
the crown shaft until it releases from the gearbox.
Inspection points:
Check crown wheel and pinion for worn or broken teeth, and
replace the crown shaft assembly if necessary. To replace the
pinion, the motor must be separated as per 3.4.2.
Check the pinion is tightly locked to the armature. If the
pinion can rotate on the armature, separate the motor and
tighten the pinion nut as per 3.4.2.
Check the grease condition and replace if any debris is found.
Check the right hand crown shaft bearing rotates smoothly.
If not, or if it is visibly damaged, it must be replaced (first
remove the retaining circlip which may be hidden by grease).
To assemble:
1. Start the crown shaft into the right hand bearing
2. Push the shaft into place, ensuring it meshes
correctly with the pinion and seats against the
bearing.
3. Assemble the left hand casting as per 3.4.2
3.4.4 Conrods Assembly
To disassemble:
1. Remove the head shells as per 3.1.1 & 3.1.3, the
drive belt as per 3.2.2 and the driven pulley as per
3.2.3
2. Remove the top spring conrod screws (5 mm hex)
3. Disassemble the left hand casting as per 3.4.2
4. Use a soft-face hammer to tap the threaded end of
the camshaft until it releases from the right hand
casting (the bearing may stay attached to the
camshaft). Take care not to bend the casting.
Inspection points:
Check the right hand camshaft bearing and replace if it does
not rotate smoothly or is visibly damaged.
Replace the conrods assembly if the conrod bearings do not
rotate freely, the conrods are cracked or the conrod blade
attachment mechanisms are damaged or excessively worn.
Warning: individual conrods are not serviceable and
attempts to remove them from the camshaft or disassemble
the conrods can cause permanent damage. If a conrod or
component requires replacement the entire conrods
assembly must be replaced.
Note: the conrods assembly kit and top springs kit include
several duplicate washers and screws.
To assemble:
1. Press the conrods assembly into the right hand
camshaft bearing (threaded end first), ensuring the
camshaft seats fully against the bearing. Avoid
collision with the top springs and right hand casting.
2. Assemble the left hand casting as per 3.4.2
3. Assemble the top spring conrod screws, washers
and Loctite 243 as per 3.4.1. Torque to 18 Nm.
4. Assemble the driven pulley, drive belt and head
shells.
3.4.5 Right Hand Casting
If the right hand casting becomes deformed, cracked or
otherwise damaged during use it must be replaced.
Replacing the right hand casting requires removal of the
head shells, ancillaries, top springs, left hand casting,
drivetrain, conrods assembly and motor including armature.
The tension idler must also be removed as per 3.2.3.
Notes for assembly:
•Assemble the tension idler to the right hand casting
first as per 3.2.3 before any other assembly steps.
•Do not tighten any top spring screws until the
castings are fully assembled.

www.arbortechtools.com
ARBORTECH PTY LTD
67 Westchester Rd, Malaga,
WA, Australia, 6090
Ph: +61 8 9249 1944
Fax: +61 8 9249 2936
ARBORTECH EUROPE GMBH
Esloher Str. 188,
57413 Finnentrop, Germany
(Germany) +49 2724 2880474
USA
30 Corporate Park Dr, Suite 210
Pembroke, MA 02359
(USA) Toll Free: (866) 517 7869
CANADA
120 Saunders Rd, Unit 4
Barrie, Ontario L4N 9A8
(CAN) Toll Free: (855) 939-8665
Email
Facebook
www.facebook.com/ArbortechTools
REV 230823
Other manuals for AS200X
2
This manual suits for next models
5
Table of contents
Other Arbortech Power Tools manuals
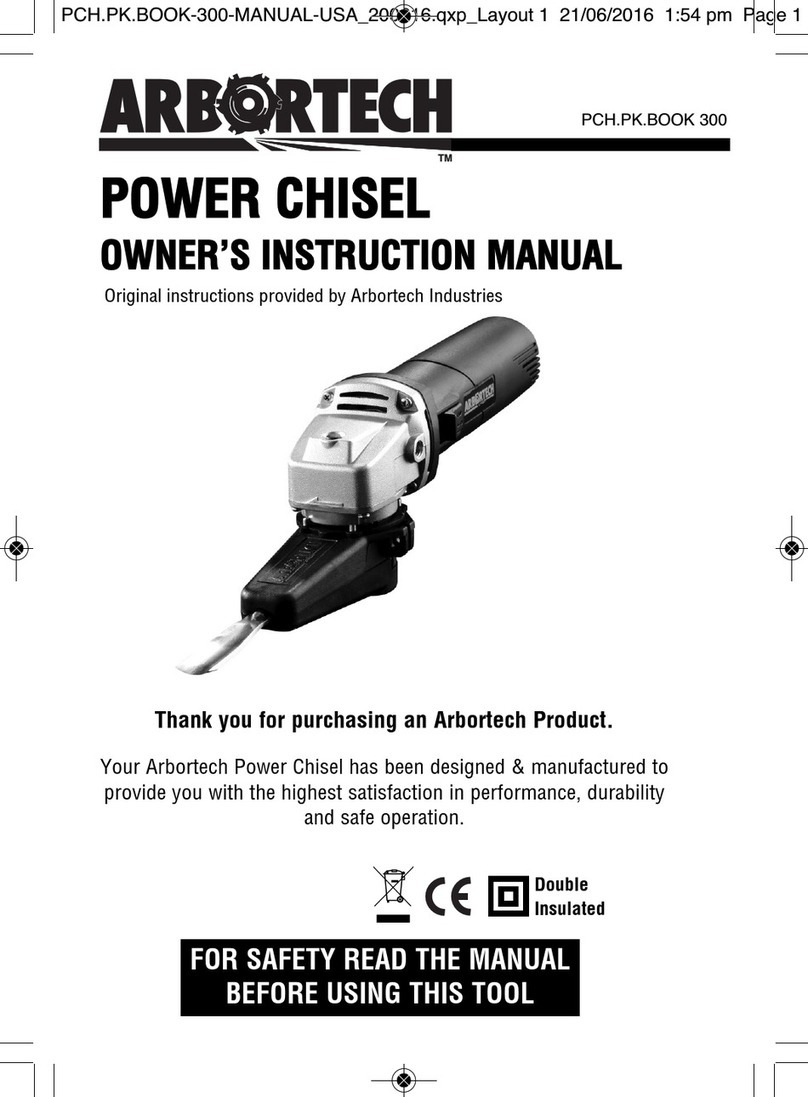
Arbortech
Arbortech POWER CHISEL Setup guide
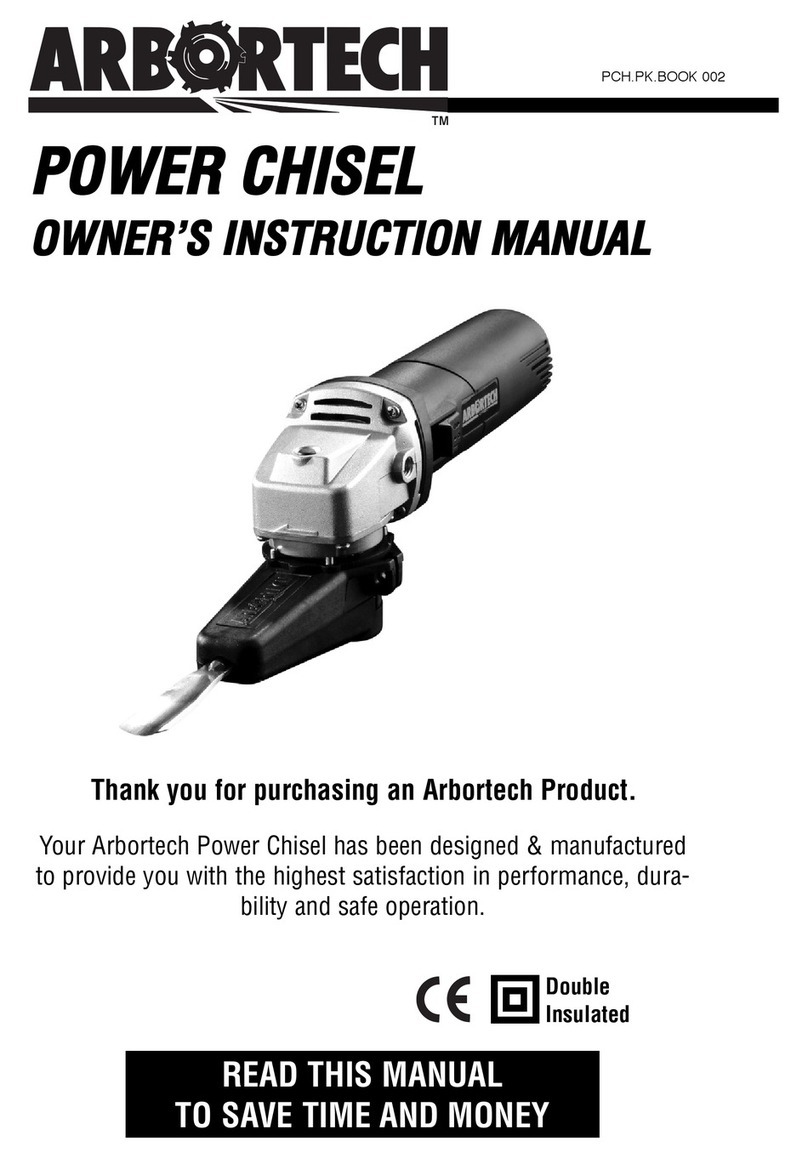
Arbortech
Arbortech POWER CHISEL Setup guide
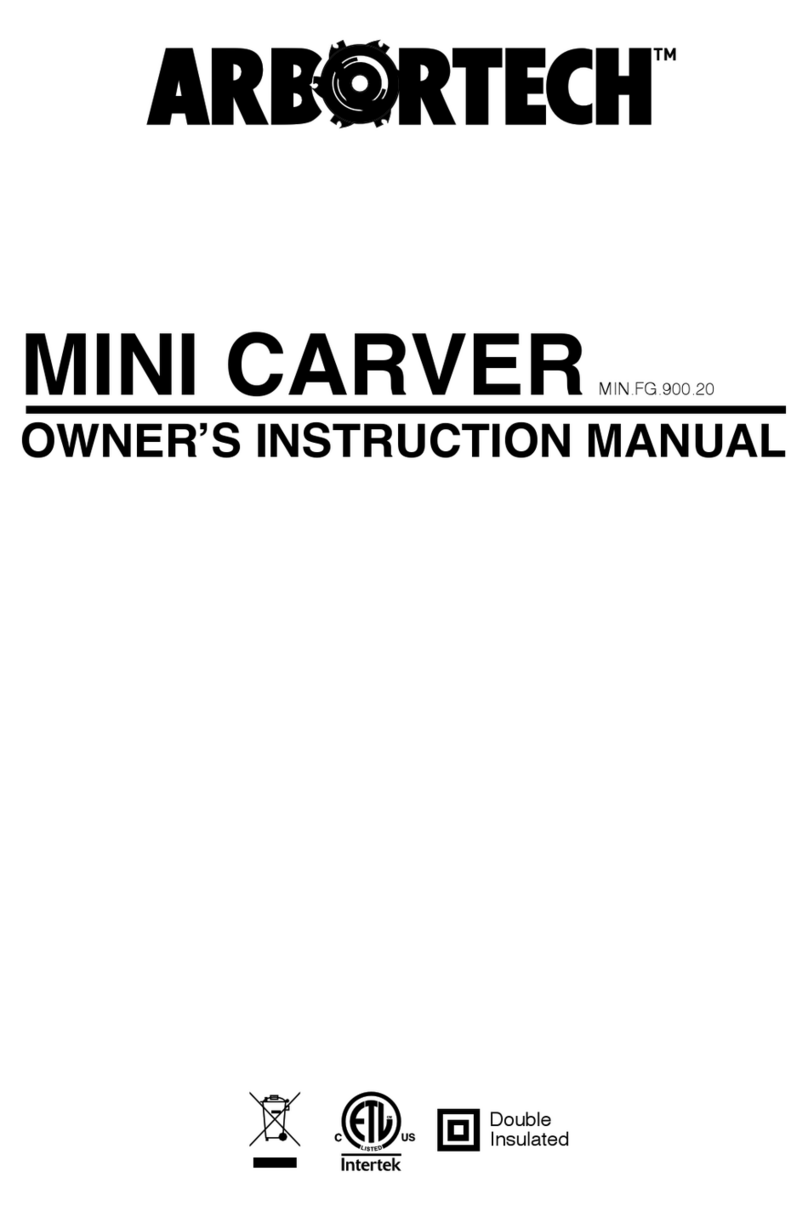
Arbortech
Arbortech MIN.FG.900.20 Setup guide
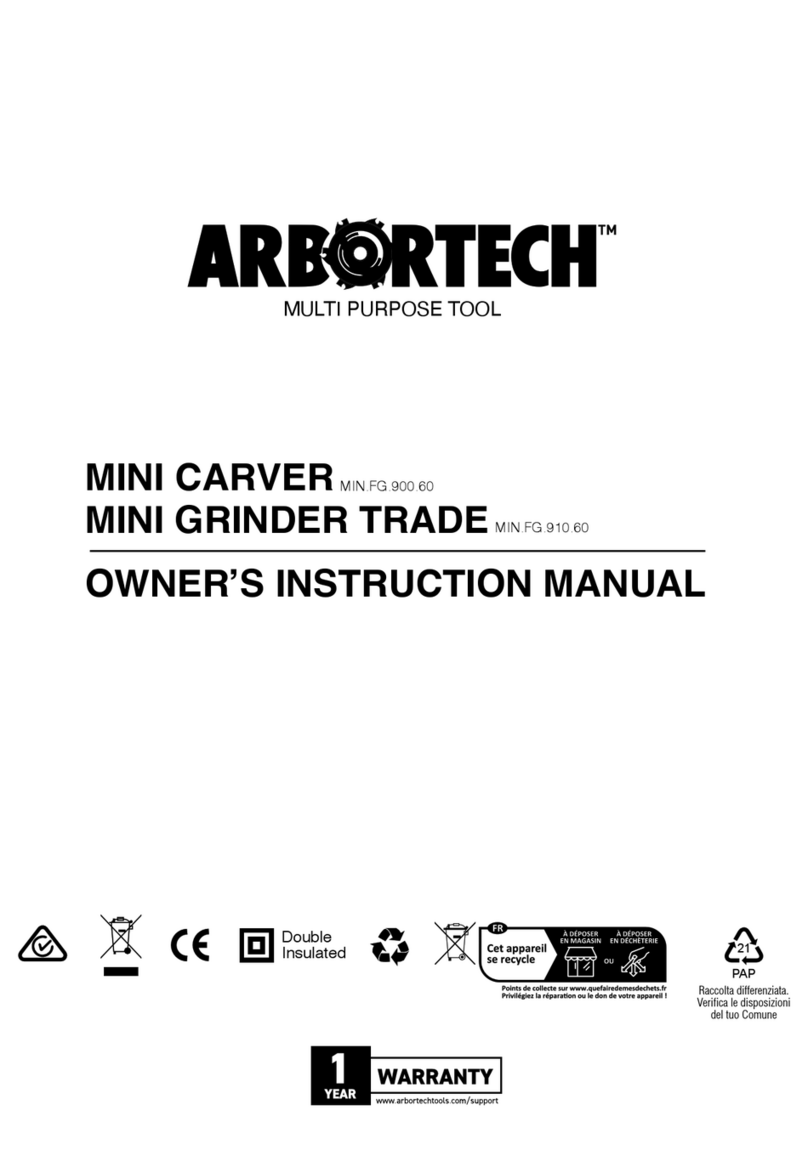
Arbortech
Arbortech MIN.FG.900.60 Setup guide
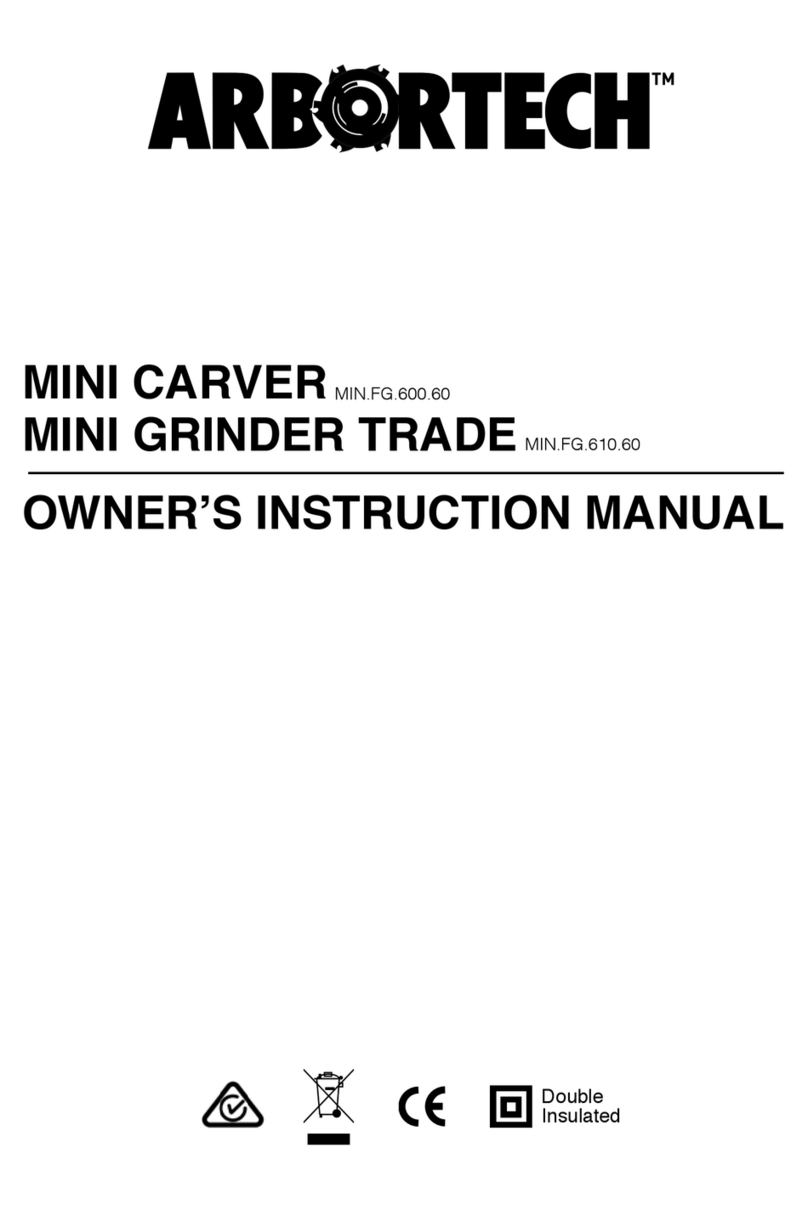
Arbortech
Arbortech MINI CARVER MIN.FG.600.60 Setup guide

Arbortech
Arbortech PCH.FG.900.20 User manual

Arbortech
Arbortech PCH.FG.900.00 User manual
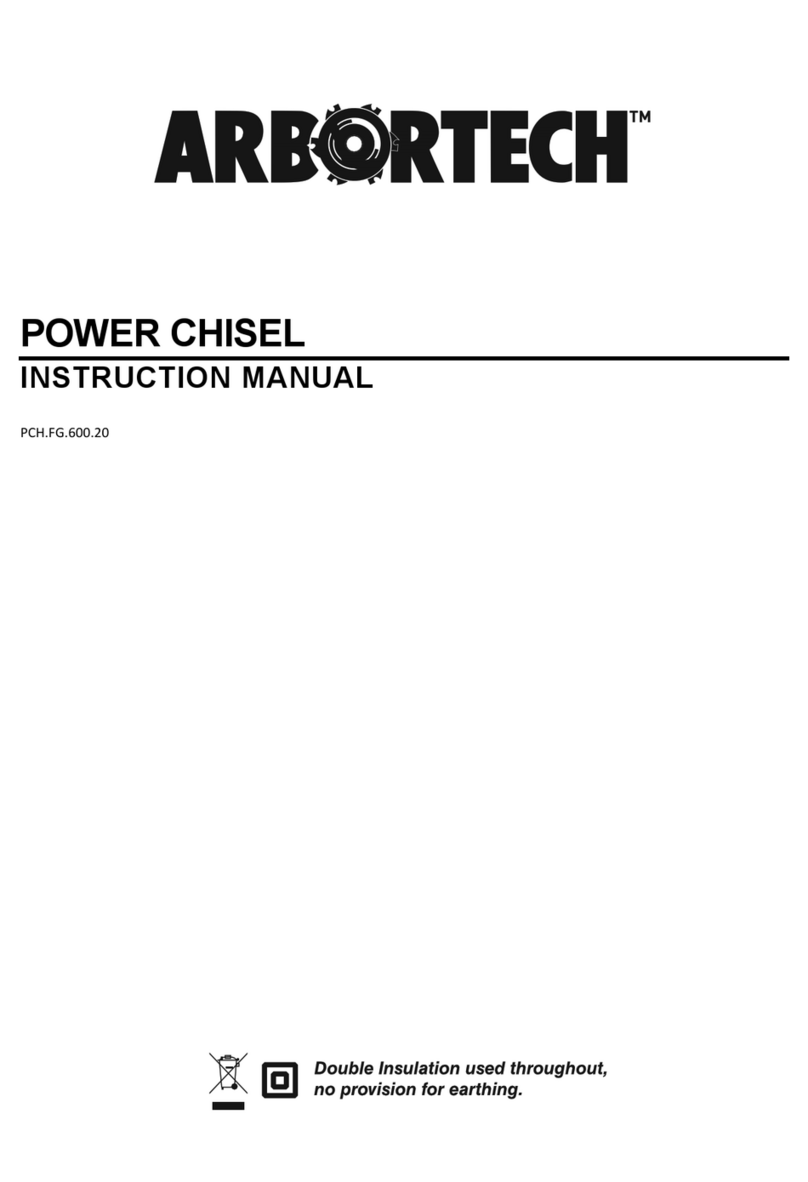
Arbortech
Arbortech PCH.FG.600.20 User manual
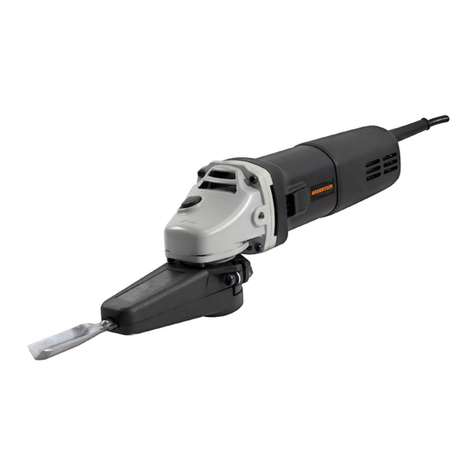
Arbortech
Arbortech POWER CHISEL User manual