Armstrong EvaPack Series User manual

EvaPack™ Series
Evaporative Pad Adiabatic Humidifier/Cooler
Installation and Operation Manual
For RW and DW configuration
IOM-542-V11

2
Table of Contents
General Safety Information..................................................................................................................................3
Product Information ..............................................................................................................................................5
EvaPack™ humidifier, operation principle........................................................................................................................... 5
Direct Water (DW) configuration......................................................................................................................................... 5
Recirculated Water (RW) configuration ............................................................................................................................. 6
EvaPack™Pad pressure drop ............................................................................................................................................... 6
Droplet separator pressure drop ....................................................................................................................................... 7
Product Installation ...............................................................................................................................................7
General Installation Requirements..................................................................................................................................... 7
Minimum space needed for the cassette extraction/installation............................................................................... 9
One EvaPack™ module assembly....................................................................................................................................... 10
EvaPack™stucture assembly method................................................................................................................................. 11
Cassette installation by the side ........................................................................................................................................ 13
Cassette installation by the front ...................................................................................................................................... 15
EvaPack™ configuration “11” assembly (valid also for configuration “21”) ................................................................ 18
Flangeable unit for duct installation .................................................................................................................................. 18
Supplied water installation................................................................................................................................................... 19
Inlet tap water treatment recommendations................................................................................................................... 21
Inlet water valve installation ................................................................................................................................................ 22
Water distribution headers................................................................................................................................................... 23
Water pump.............................................................................................................................................................................. 23
Irrigation water hoses............................................................................................................................................................ 24
Water level sensor installation ............................................................................................................................................ 25
Water draining installation....................................................................................................................................................26
Maintenance Requirements .................................................................................................................................28
EvaPack™ drying and bleed-o settings to reduce maintenance ............................................................................. 28
To prevent microorganism development......................................................................................................................... 28
Humidifier drying recommendations................................................................................................................................. 29
To prevent salt deposits on EvaPack™ pad: bleed-o................................................................................................... 29
Periodic Maintenance ........................................................................................................................................................... 34
Cassettes dismantling for replacement............................................................................................................................ 37
Cassette Side Extraction ...................................................................................................................................................... 37
Lateral Extraction for droplet separator cassettes and pad........................................................................................ 38
Front Extraction for droplet separator cassettes and pad........................................................................................... 39
Disinfection product recommendations for the EvaPack™ Evaporative Pad........................................................... 42
Troubleshooting.....................................................................................................................................................43
Glossary ..................................................................................................................................................................45

3
General Safety Information
This bulletin should be used by experienced personnel as a guide to the installation of the Armstrong EvaPack™.
Selection or installation of equipment should always be accompanied by competent technical assistance.
Please contact Armstrong International or its local sales representative for additional information.
IMPORTANT
Please read, heed and follow the enclosed safety information and the warning labels inside the humidifier
before installation or maintenance.
EvaPack™ Evaporative Pad Material
The EvaPack™ evaporative pad material should not be cut or crushed as doing so may generate dust.
Emergency Overview:
This product is non-hazardous under ordinary conditions of use.
There is almost no possibility of creating dust. However dust will be created in process of cutting, polishing or
destroying of this product.
Hazard information of generated dust is described as below.
Primary Routes of Entry:
Via respirable dust to the lungs and respiratory system and via coarse dust and particulate to the eyes.
Primary Target Organs: Lungs, respiratory system and eyes.
Potential Health Eects:
Eye Contact: May cause mechanical irritation.
Skin Contact: May cause transitory mechanical dermatitis.
Inhalation: Long term overexposure to airborne dust may cause respiratory disease.
Ingestion: None-hazardous when ingested.
Carcinogenicity: Glass filament is classified as IARC Group 3 (Not classifiable as its carcinogenicity to humans).
FIRST AID MEASURES
Inhalation: Remove from exposure to fresh air.
Ingestion: Ingestion is unlikely. If ingested, drink sucient water and vomit and get medical attention.
Skin Contact: Flush with water or slightly warm water and wash with soap. Get medical attention if pain and
inflammation.
Eye Contact: Flush eyes with water for a least 15 minutes. Abrasive action may cause damage to the outer
surface of the eye. Get medical attention if irritating.
Note to Physician: Treat symptomatically.
TOXICOLOGICAL INFORMATION
Acute Eects: Exposure to glass filament sometimes causes skin irritation and occasionally upper respiratory
tract irritation.
Chronic Eects: A number of epidemiology studies, done over many years of workers employed for up to 40
years in manufacturing of glass filament have shown no eects.
Carcinogenicity: Glass filament is classified as IARC Group 3 (Not classifiable as its carcinogenicity to humans.).
Mutagenicity: No available data.
FIRE FIGHTING MEASURES
Flammable Properties: This product is not flammable.
Extinguishing Media: Not applicable.
Fire Fighting Procedure: Not applicable.
Unusual Fire and Explosion Hazards: None.
Delivery, Lifting, Inspection and Storage
Any loss or damage during delivery should be reported to carrier by registered letter within 3 working days

4
and be advised to Armstrong International or to an authorized dealer.
Lifting or handling must only be carried out by trained and qualified personnel.
It is the customer’s responsibility to ensure that operators are trained in handling heavy goods and to enforce
the relevant lifting regulations.
It is recommended that the EvaPack™ humidifier be kept in its transit packaging for as long as possible
prior to maintenance. If the humidifier is to be put into storage prior to installation, it must be stored under
cover and protected from physical damage, dust, frost, rain and humidity. More than 6 months storage is not
recommended.
GENERAL
This manual contains all details necessary for the planning and installation of the EvaPack™ humidifier. In
addition commissioning and maintenance details are included. The manual is intended for use by engineers
and properly trained technical personnel. Maintenance, servicing or repair work must only be carried out by
suitable skilled and qualified personnel; the customer must be responsible for ensuring their suitability. Any
risks or hazards, especially when working from ladders or towers should be identified by a skilled and Health
and Safety representative and eective control measure put in place. No liability will attach to the Distributor
if any damage, injury or accident is attributable to inattentive, inappropriate, negligent or incorrect operation
of the machinery whether or not caused deliberately. Always isolate all electrical and water supplies before
commencing any maintenance. Every eort has been made to ensure details contained in this manual are
correct, however, in view of the wide range of conditions experienced in air handling systems, the information
provided should only be used as a guide. Please contact your Agent if any doubt.
CORRECT USE
EvaPack™ humidifiers are ONLY intended for use with air handling systems or direct air humidification. ANY
OTHER APPLICATION IS NOT CONSIDERED USE FOR THE INTENDED PURPOSE. THE MANUFACTURER
CANNOT BE MADE LIABLE FOR ANY DAMAGE RESULTING FROM INCORRECT USE.
ELECTRICITY
All work concerned with electrical installation MUST only be performed by skilled and qualified technical
personnel (electricians or technicians with appropriate training). The customer must be responsible for
ensuring their suitability. It is the duty of the installer to ensure that suitable sized cables and MCB protection
is provided. Please observe the local regulations concerning the provision of electrical installations.
DISPOSAL
You must observe local laws and regulations when disposing of your EvaPack™ HUMIDIFIER at the end of
its working life. Use personal protective equipment as recommended in the handling section above when
handling the evaporative material. In addition, respiratory protection should be worn to avoid inhalation of dust
or debris from the air flow which may have accumulated on the material.
NOTE
The manufacturer’s policy is one of continuous researches and development. He therefore reserves the right to
amend without notice the specifications given in this document. The photographs are for illustrating purposes
only.
Manufacturer’s Name and Address - Authorized Representative
Armstrong International - Devatec SAS
185 Boulevard des Frères Rousseau
76550 Oranville - FRANCE
CE conformity declaration
EvaPack™ is CE. EAC, VDI 6022 compliant.
Devatec-Armstrong is ISO 9001, ISO 14001 compliant.
Type of equipment: Humidifier
Model Name (s) & Series: EvaPack™
We the undersigned, hereby declare that the equipment specified above conforms to the above
Directive(s) and Standard(s).

5
Product Information
Hot Dry
Air
Cool Moist
Air
Evaporative
Pad
Water
Reserve
Direct Water configuration
Operation sequences
A. Water enters from the water supply (1) and arrives to the dispersion
manifold (4). The water flow is adjusted with a manual gate valve (3).
B. The calibrated orifices deliver uniformly the water over each
media pad (5).
C. Dry air passes through a corrugated bank of wetted cells
media (5). Air is cooled and humidified.
D. The irrigation piping draining (6) should be installed in order to
avoid any microbiological issues.
E. The excess water washes the EvaPack™evaporative pad and
is eliminated (with minerals) from the water basin (2) through the
draining connection (7).
This configuration is recommended with high hardness supplied
water (to increase the pad life time) or with reverse osmosis water
(to reduce the RO water consumption).
F. Water level switch option (8) could be installed as an alarm system.
4
5
3
1
2
6
4
5
3
7
8
Inlet water valve and
water level sensor
are optional
EvaPack™ humidifier, operation principle
Armstrong EvaPack™ Series converts ordinary tap water into
water vapor by using an adiabatic process. Dry air passes
through a corrugated bank of wetted cells media made from
non-organic fibers. EvaPack™ series uses the sensible air heat
to evaporate the water. The air is cooled and humidified.
All types of water can be used (see page 8 for more details
on water quality).

6
Recirculated Water configuration
Operation sequences
A. Water enters into the basin passing through the filling valve (1).
The water level sensor (7) controls the basin (2) filling, the pump (3)
starting-up and the fill valve opening.
B. The recirculation water pump (3) supplies water to the dierent
dispersion manifolds (5). The water flow of each cassette (6) is
adjusted with a manual gate valve (4). Calibrated orifices deliver the
water evenly over each media pad (6).
C. Dry air passes through a corrugated bank of wetted cells media
(6), is cooled and humidified.
D. The excess water washes the evaporative pad and falls.
(with minerals) into the water tank.
E. The excess of minerals is drained by the draining valve minimizing
the water consumption and the media scaling. This configuration
is recommended when the available supplied water has a low or
medium hardness.
5
6
4
1 3 7
2
9
8
5
6
4

7
EvaPack™Pad pressure drop
Air Front Velocity in m/s
Air Speed in m/s
Pressure loss in Pa
Droplet separator pressure drop
Pressure drop in Pa
Droplet separator is:
Recommended when net air velocity ≥ 3.2 m/s
Necessary when net air velocity ≥ 3.5 m/s

8
Product Installation
General installation requirements
1. EvaPack™ humidifier must be installed into the Air Handling Unit (AHU) or Duct.
2. AHU / Duct – work floor must be designed with a loading capacity capable of supporting the humidifier
weight when wet.
3. EvaPack™ humidifier must be installed horizontally. Armstrong International recommends using a spirit level
to make sure that the unit is level front to back and across the width when installed. Failure to observe this
point could result in footing of the AHU/Duct, or an incomplete unit emptying.
4. Once EvaPack™ humidifier has been positioned in a section of air handling unit, non-corrosive blanking
plates must be installed to prevent air bypass around the unit in the AHU.
5. EvaPack™ must be cleaned before the initial fan starting-up, the pad must be flushed with water several
times to eliminate remaining dust.
6. Check that there is no water leakage coming from water connection or others.
7. The standards EN 13053 and EN 1886 should be respected and mainly:
7-a. Humidifiers must not be placed directly upstream of filters or attenuator (according to
EN Standards)
7-b. Supply air units to have at least two filter stages (first stage min. ePM1 ≥ 50% or F7 filter).
The humidifier must be placed in-between the filter stages.
7-c. Inspection access: An inspection opening (Clear width not less than 150 mm) and lighting of
EvaPack™ humidifier chamber shall be provided. No external light must enter through the housing
of the lighting. It must be possible to recognize the condition of the lighting (on/o) from outside.
ADDITIONAL FOR HYGIENIC VDI 3803 and VDI-6022 REQUIREMENTS
1. All the non-metallic product used for the installation (seal, etc.) must not absorb moisture or provide a
nutrient substrate for micro-organisms.
2. The relative humidity downstream from the humidifier section must not exceed 90%. It must be ensured that
drops of water could not reach the components installed downstream.
3. Max. number of germs of the circulation water: − relating to the total colony number 1000 cfu/ml. − relating
to Legionella spp. 100 cfu/100 ml.
4. Drainage system must be equipped with a siphon with non-return valve or a siphon disconnected from the
sewage network.
5. Shutdown: In case of shutdown or failure of the ventilating and air-conditioning system, the humidifier shall
be switched o automatically.
OTHER GENERAL INSTALLATION RECOMMENDATIONS
1. ARMSTRONG recommends installation within a waterproof section.
2. EvaPack™ humidifier components should be easily accessible for checking, inspection and cleaning at any
time.
3. It is recommended not to exceed 55 °C in the processed air
temperature when the pad is not wetted.
The non-metallic parts might be damaged over this temperature.
The dry bulb temperature and the wet bulb temperature of the inlet air
must be positive to avoid water freezing on the pad.

9
Minimum space needed for the cassette Extraction/Installation
Side Extraction/ Installation
Minimum free space of 600 mm is needed for the cassette Extraction/ Installation. The cassette can be
extracted from both sides.
600 mm
Front Extraction/ Installation
For inspection, commissioning and maintenance, Armstrong International recommends to always providing an
area of minimum 500 mm(*) rear and 500 mm front of the EvaPack™humidifier.
min. 500 mm min. 500 mm
According to the available service rear distance, a specific cassette dismantling procedure should be followed.
Please see chapter: Cassette dismantling for replacement.
min. 150 mm min. 150 mm
Rear or upstream Front or downstream
Rear or upstream Front or downstream
Air direction Air direction
Air directionAir direction

10
One EvaPack™ module assembly
When the unit has been supplied dismounted for any transport or installation reason, please follow this pro-
cedure to assemble the EvaPack™ module.
INCLUDED WITH STANDARD DELIVERY:
N°
For Standard DW
configuration
1
Water basin (x1)
7
Right Lateral door
9
Roof with assembled
watering system (x1)
10
Evaporative pad cas-
settes
11
Pillars (x4)
12
Left lateral door
13
Water hoses
N°
Additional for
droplet separator
option
8
Droplet separator
cassettes
N°
Additional for RW
2
Water level switch
3
Header (x1)
4
Water pump (x1)
5
Inlet water valve (x1)
6
Drain valve (X1)

11
Screw and nut M4
Screw M4
without nut
Place the pillars to the intended fixing points
on the basin, with the open part towards the
outside of the EvaPack™.
Place the basin on a solid and plane surface.
EvaPack™stucture assembly method

12
Roof assembly
Install the roof carefully on the four pillars by intro-
ducing the welded threaded stud bolts into the four
intended pillar holes.
Vertically : 1 x nut M4 for each
welded threaded stud bolt.
Horizontally : 1 screw + nut M4.
Vertically : 1 x nut M4 for each
welded threaded stud bolt.
Horizontally : 1 screw + nut M4.
Install first the side-door not used for cassettes extraction.
Vertically : 1x screw M4.
Horizontally : 1 screw + nut M4 (x6)
From this stage, please follow the instructions in page 14, if you can install the cassettes from the side, if
not (Cassette installation by the front) please follow the instructions in page 15 (Cassette installation by
the front).

13
Cassette installation by the side
Please respect the minimum space needed for cassette extraction/ installation as described in page 9.
Introduce the cassettes one by one, by sliding them.
Please make sure the watering area is in-between top rails.
Introduce the droplet separator cassettes (if supplied) one at a time, by sliding them.
Attach the union frames with M4 screws at the rear and front cassette sides.
Air direction Air direction
Correct position of the droplet separator :
Attach the union frames with M4 screws at the rear and front cassette sides.

14
For ancillary installation, please review the corresponding chapter.
EvaPack™ final assembly with droplet separator option.
Access side-door assembly.
Vertically : 1 x screw M4.
Horizontally : 1 screw + nut M4 (x6)

15
Cassette installation by the front
Please respect the minimum space needed for cassette Extraction/Installation as described in page 9.
Second side-door assembly.
Extract the middle cassette
support rails.
Extract the manifold support
frames and the cassettes
downstream top rail.
Hexagonal
screws M4.
Vertically : 1 x screw M4.
Horizontally : 1 screw + nut M4 (x6)

16
Reinstall the manifolds and their support
frames.
Install the cassettes one by one, from the center, and by sliding them towards the sides.
Be careful: respect the correct insertion of the watering part into the cassette tops.
Reinstall the cassettes downstream
top rail.
Install the cassettes support rails as shown in the picture.
Hexagonal
screws M4.

17
Correct droplet separa-
tor cassette top posi-
tion.
Air direction Air direction
Correct position of the droplet separator :
Install the droplet separators one by one, from the center, and by sliding them towards the
sides.
Hexagonal
screws M4.
Hexagonal M6 nuts for the
droplet separator top rail.
Hexagonal M4 screws
for the manifold support
frames.
Install the cassette support rail as shown in the pictures below.
The droplet separator can fall down, we recommend at least 2 people for this step.

18
EvaPack™ configuration “11” assembly (valid also for configuration “21”)
Put several self-drilling
screws (upstream and
downstream) to secure the
two EvaPack™assembly.
Be careful : do not drill the
upper water basin.
Flangeable unit for duct installation
Flange the unit to the duct frame and screw it properly.
Do not drill the water basin and use the correct sealant to tight the flange connection.
Inlet water connection

19
Supplied water installation
EvaPack™ can work with dierent types of water: potable water, reverse osmosis or softened water. It is the
responsibility of the user to ensure that the water supply system is part of a managed, hygiene monitored
water system. Water quality must comply with the local regulations and laws.
Reverse osmosis water
Reverse osmosis water is water purified under pressure by a semipermeable membrane. This membrane
retains ions, molecules, and larger particles and allows only the water to pass to the other side. EvaPack™
pad accepts RO water with a conductivity > 1μS/cm at 20º C.
Softened Water
Softened water is hard water treated by ion-exchange resins. The resins remove the calcium, magnesium
cations of the water. It is essential that the salt maintenance of softeners be programmed for the water
volume consumed in order to prevent an excessive salt concentration to humidify once the regeneration
cycle is finished (please refer to the softener’s user manual).
Potable water
EvaPack™ air evaporative humidifier must be connected to a clean, potable (drinking water quality) water
supply.
EvaPack™ air evaporative humidifier must operate within potable tap water specifications (main sources:
Directive 98/83/CE and VDI 6022 requirements).
Organoleptic parameters
Parameter Parametric value Parameter Parametric value
Temperature (*) < 20°C Color Acceptable and no abnor-
mal change
Turbidity ≤ 2,0 NTU Odor Acceptable and no abnor-
mal change
Taste Acceptable and no abnor-
mal change
Microbiological parameters
Enterococci (¹) 0/100ml Pseudomonas aeruginosa 0/250ml
Coliform bacteria 0/100 ml Clostridium perfringens
(including spores) 0/100 ml
Escherichia coli (E. coli) 0/250 ml Legionella spp (2) (3) < 100 CFU/100 ml
Colony count 22ºC (1)
Colony count 37ºC (1)
Total colony number (2)
No variation in a ratio of 10
to the usual value of the inlet
water.
< 1000 CFU/ml
Sulfate-reducing bacteria (1)
(including spores)
0/100 ml
(In the event of non-com-
pliance with this value,
an investigation must be
carried out to ensure that
there is no danger to hu-
man health resulting from
the presence of pathoge-
nic micro-organisms, for
example Crystosporidium.)
(1) Value given by Directive 98/83/CE
(2) Value given by VDI 6022-4.3.7 for recirculating water in air humidifiers.
(3) This value must comply with potable water standards applicable in your country.
(4) EvaPack™ air evaporative humidifier must operate within these specifications.

20
Chemical parameters
Acrylamide ≤ 0,1μg/l Epichlorohydrin (1) ≤ 0,1 μg/l
Aluminium <200 μg/l Fluoride (1) ≤ 1,5 mg/l
Ammonium (1) < 0,1 mg/l Iron total (1) ≤ 200 μg/l
Antimony (1) ≤ 5,0μg/l Lead (1) ≤ 10 μg/l
Arsenic (1) ≤ 10μg/l Magnesium (3) ≤ 50 mg
Benzene (1) ≤ 1,0 μg/l Manganese (1) ≤ 50 μg/l
Benzo(a)pyrene (1) ≤ 0,01μg/l Mercury (1) ≤ 1,0 μg/l
Boron (1) ≤ 1,0 mg/l Nickel (1) ≤ 20 μg/l
Bromate (1) ≤ 10 μg/l Nitrate (1) ≤ 50 mg/l
Cadmium (1) ≤ 5,0 μg/l Nitrite (1) ≤ 0,50 mg/l
Calcium (3) ≤ 300 mg/l pH (Hydrogen ion concen-
tration) (1) 6.5 to 9
Total organique carbone
(TOC) (1) ≤ 2,0 mg/l Pesticides total (1) ≤ 0,50 μg/l
Chloride (1) ≤ 250 mg/l Polycyclic aromatic hydro-
carbons (1) ≤ 0,10 μg/l
Chromium (1) ≤ 50 μg/l Selenium (1) ≤10 μg/l
Conductivity (1) (3) ≤ 1000 μS/cm at 20ºC Silicate < 150 mg/l
Copper (1) ≤ 1,0 mg/l Sodium ≤ 200 mg/l
Cyanide (1) ≤ 50 μg/l Sulfate ≤ 250 mg/l
1,2-dichloroethane (1) ≤ 3,0 μg/l Trihalomethane Total (1) ≤ 100 μg/l
Tetra- and tri-chloroethene
(1) ≤ 10 μg/l Vinyl chloride (1) ≤ 0,50 μg/l
Radioactivity
Tritium (1) <100 Bq/l Total indicative dose (1) < 0,1 mSv/year
(1) Value given by Directive 98/83/CE
(2) Value given by VDI 6022-4.3.7 for recirculating water in air humidifiers.
(3) Water hardness range will be confirmed by PSI value (please see EvaPack™ bleed-o chapter)
(4) EvaPack™ air evaporative humidifier must operate within these specifications.
These values are to be taken into account when setting the bleed-o limits.
*A too low water temperature can impact humidification eciency.
Table of contents
Other Armstrong Humidifier manuals
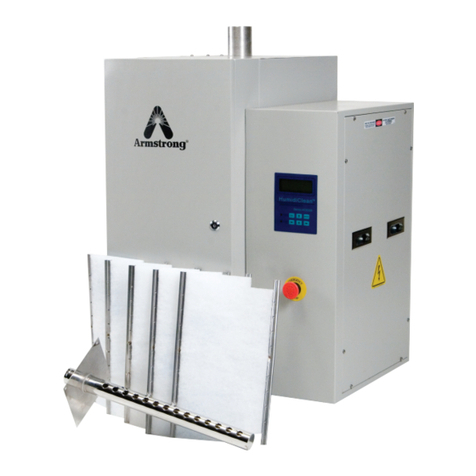
Armstrong
Armstrong Series HC- 6100 Manual

Armstrong
Armstrong EM-1000 Series Owner's manual
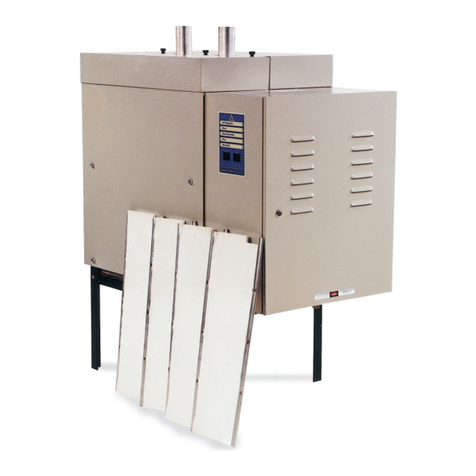
Armstrong
Armstrong Gas Fired HumidiClean Series Manual
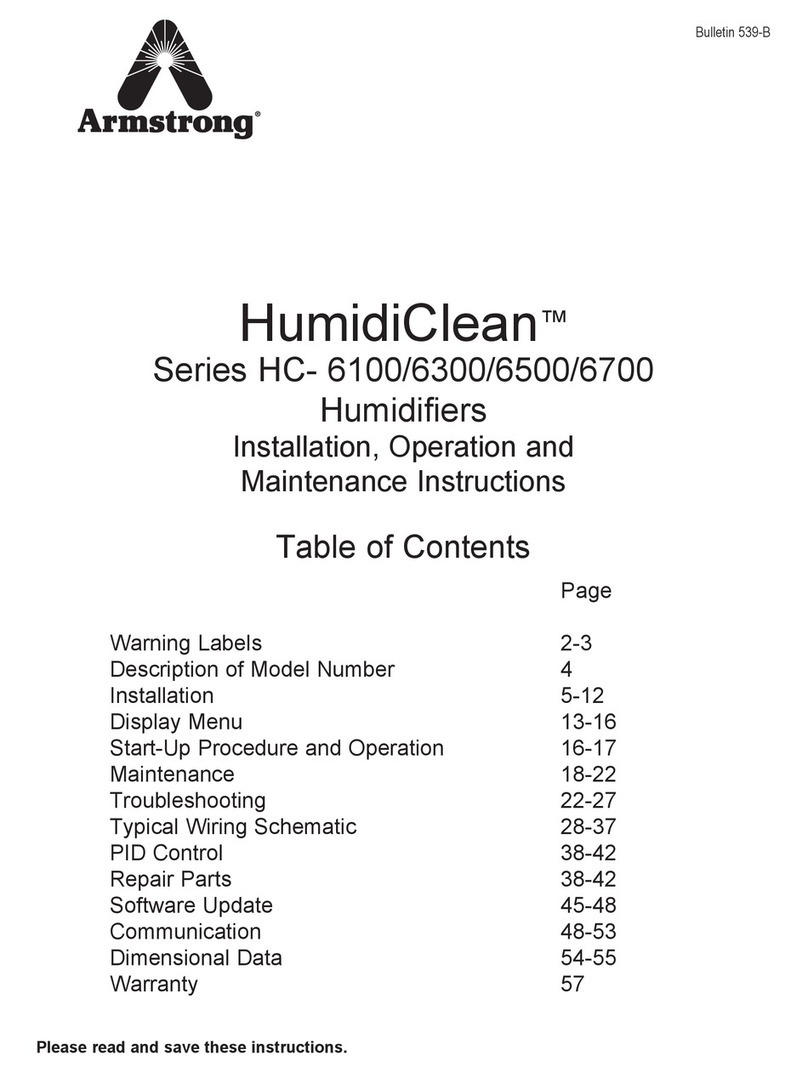
Armstrong
Armstrong 6100 Manual

Armstrong
Armstrong C-1801 User manual
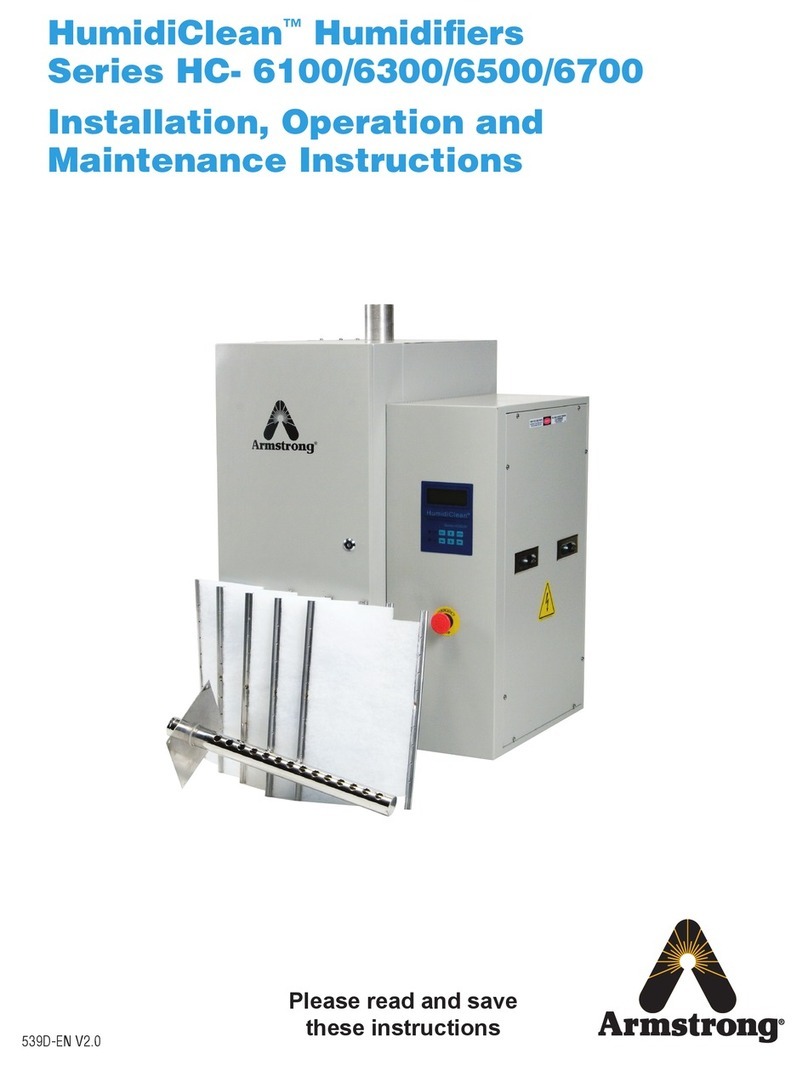
Armstrong
Armstrong HumidiClean HC-6000 Series Manual
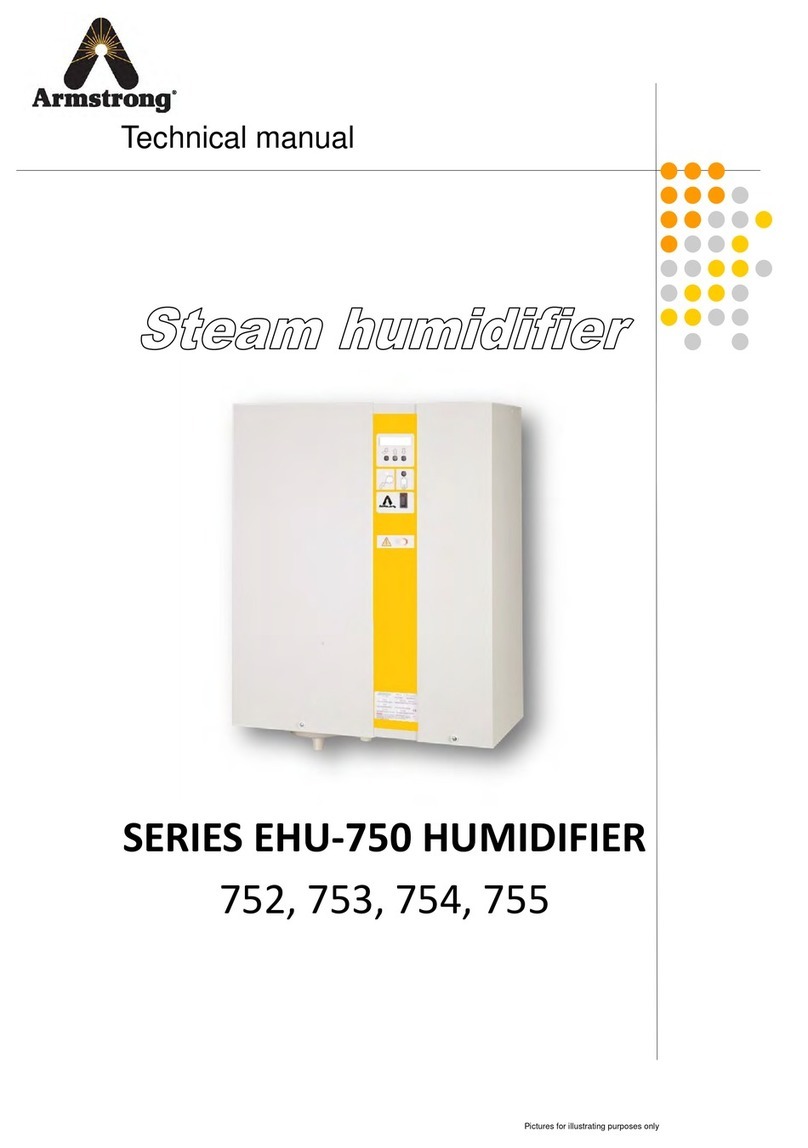
Armstrong
Armstrong EHU-750 Series User manual
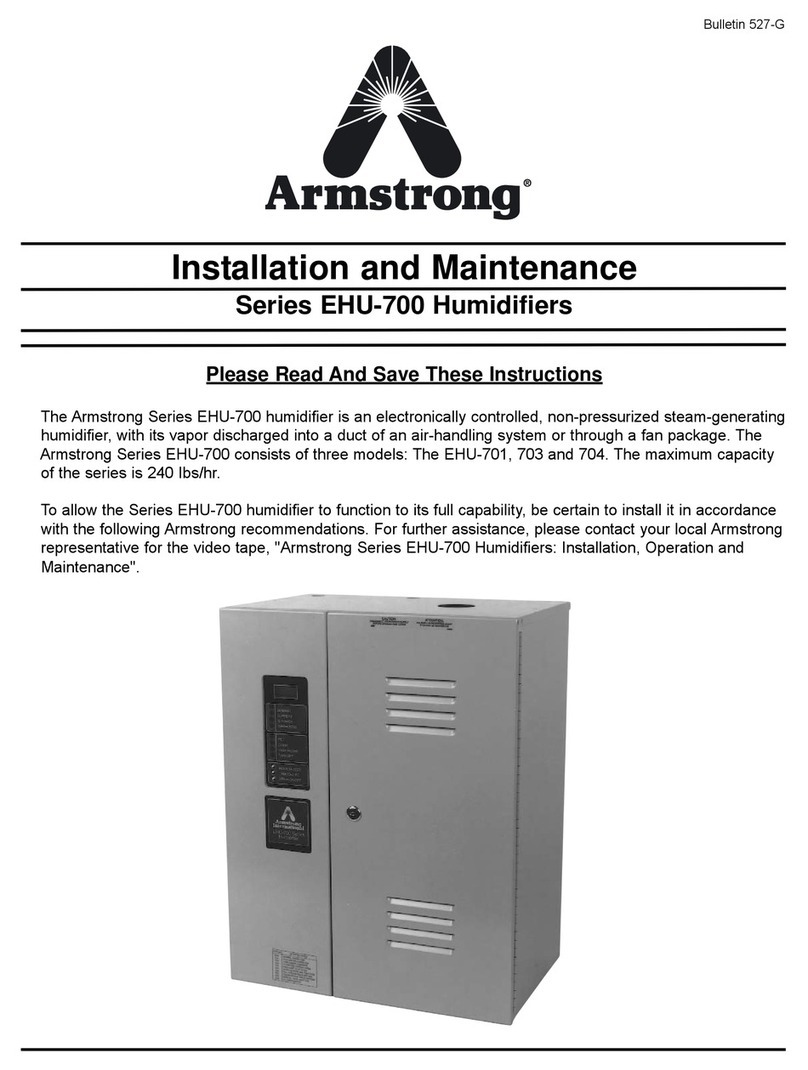
Armstrong
Armstrong EHU-700 Series Instruction Manual
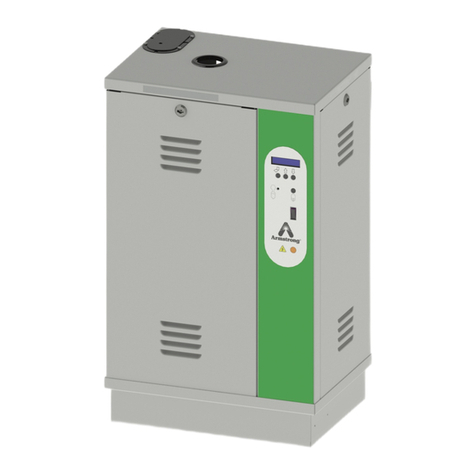
Armstrong
Armstrong EHU-800 Series User manual
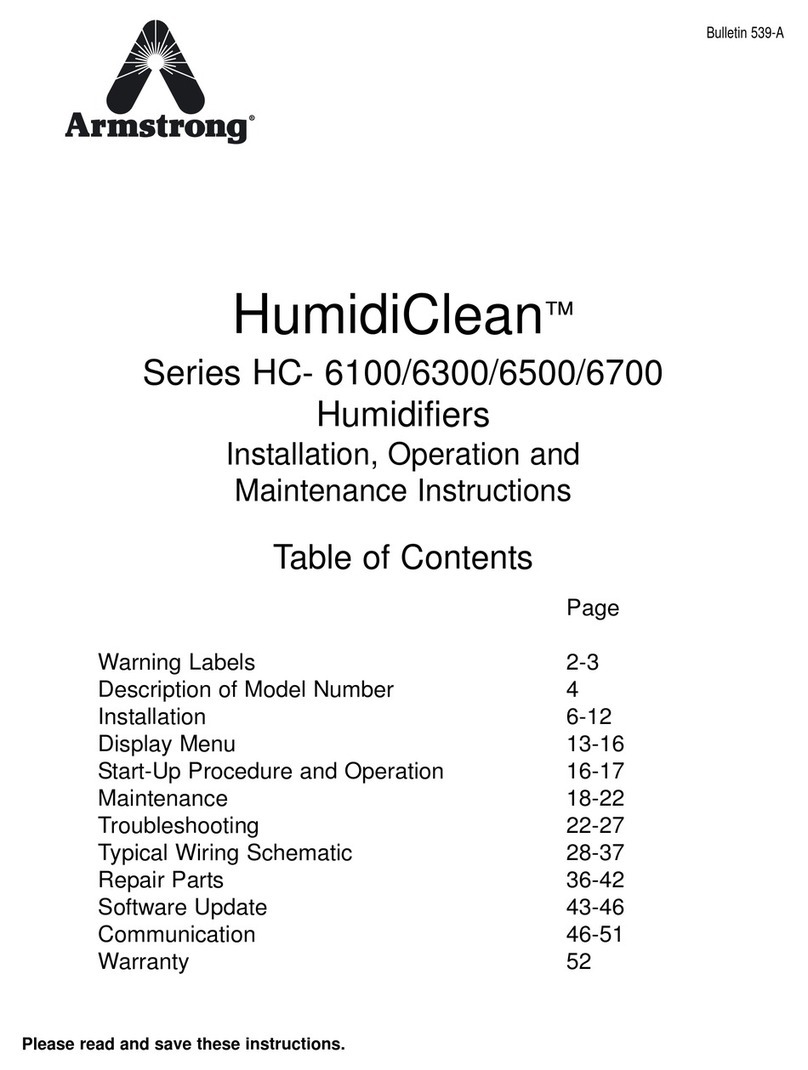
Armstrong
Armstrong HumidiClean HC-6700 Series Manual