BIFFI RPS Series User manual

Installation, Operation and Maintenance Manual
MAN 573 Rev. 8
July 2020
Biffi RPS
Spring-Return Pneumatic Actuator
Copyright © Bif. The information in this document is subject to change without notice. Updated data sheets can be obtained from our website www.bif.it or from your nearest Bif Center:
Bif Italia s.r.l. - Strada Bif 165, 29017 Fiorenzuola d'Arda (PC) – Italy PH: +39 0523 944 411 – bif_italia@bif.it

July 2020
Installation, Operation and Maintenance Manual
MAN 573 Rev. 8
Revision Details
Revision Details
Revision Details
Rev. Date Description Prepared Checked Approved
8 July 2020 General update (Migration to new template)
7November 2019 Added Sectional drawings for
MSJ-MHW and DMHW Ermanni Oreci Vigliano
6 March 2018 Updated Data-plate Ermanni Oreci Vigliano
5April 2016 Updated Applicable Regulation (Section 1.1.1) Ermanni Oreci Vigliano
4 April 2014 Updated Section 1.4 Ermanni Stoto Vigliano
3June 2012 Updated Section 1.4 and Section 5.4 Ermanni Stoto Vigliano

i
Installation, Operation and Maintenance Manual
MAN 573 Rev. 8
Table of Contents
July 2020
Table of Contents
Section 1: General Warnings
1.1 Generalities................................................................................................... 1
1.1.1 Applicable Regulation ........................................................................ 1
1.1.2 Terms and Conditions......................................................................... 1
1.2 Identication Plate ........................................................................................ 2
1.3 Introducing the Actuator............................................................................... 2
1.4 Data Sheet .................................................................................................... 5
Section 2: Installation
2.1 Checks upon Actuator Receipt ...................................................................... 6
2.2 Actuator Handling......................................................................................... 6
2.3 Storage ......................................................................................................... 8
2.4 Actuator Assembly on the Valve.................................................................... 9
2.4.1 Types of Assembly.............................................................................. 9
2.4.2 Assembly procedure......................................................................... 11
2.5 Pneumatic Connections .............................................................................. 12
2.6 Electrical Connections (If any) ..................................................................... 12
2.7 Commissioning........................................................................................... 13
Section 3: Operation and Use
3.1 Operation Description................................................................................. 14
3.2 Residual Risks.............................................................................................. 16
3.3 Operations.................................................................................................. 16
3.4 Calibration of the angular stroke ................................................................. 17
3.5 Calibration of Micro-switches (If Foreseen).................................................. 19
3.6 Calibration of the Operation Time............................................................... 19
Section 4: Operational Tests and Inspections
Operational Tests and Inspections......................................................................... 20
Section 5: Maintenance
5.1 Periodic maintenance.................................................................................. 21
5.2 Extraordinary Maintenance ......................................................................... 22
5.2.1 Replacement of Cylinder Seals .......................................................... 22
5.3 Lubrication of Mechanism........................................................................... 26
5.4 Dismantling and Demolition ....................................................................... 27
Table of Contents

ii
Table of Contents
July 2020
Installation, Operation and Maintenance Manual
MAN 573 Rev. 8
Section 6: Troubleshooting
6.1 Failure or Breakdown Research.................................................................... 28
Section 7: Layouts
7.1 Spare Parts Order........................................................................................ 29
7.2 Parts List for Maintenance and Replacing Procedure.................................... 30
Section 8: Date Report for Maintenance Operations
Date Report for Maintenance Operations .............................................................. 35
Table of Contents

Installation, Operation and Maintenance Manual
MAN 573 Rev. 8 July 2020
Section 1: General Warnings
1.1 Generalities
Bif Italia s.r.l. actuators are conceived, manufactured and controlled according to the Quality
Control System in compliance with EN-ISO 9001 international regulation.
1.1.1 Applicable Regulation
EN ISO 12100:2010: Safety of machinery – General principles for design –
Risk assessment and risk reduction
2006/42/EC: Machine directive
2014/68/EU: Directive for pressure PED equipment
2014/35/EU: Directive for low voltage equipment
2014/30/EU: Directive for the electromagnetic compatibility
2014/34/EU: Directive and safety instructions for use in hazardous area
1.1.2 Terms and Conditions
Bif Italia s.r.l. guarantees that all the items produced are free of defects in workmanship and
manufacturing materials and meet relevant current specications, provided they are installed, used
and serviced according to the instructions contained in the present manual. The warranty can last
either one year from the date of installation by the initial user of the product, or eighteen months
from the date of shipment to the initial user, depending on which event occurs rst. All detailed
warranty conditions are specied in the documentation forwarded together with the product.
This warranty does not cover special products or components not warranted by subcontractors, or
materials that were used or installed improperly or were modied or repaired by unauthorized staff.
In the event that a fault condition be caused by improper installation, maintenance or use, or by
irregular working conditions, the repairs will be charged according to applicable fees.
The warranty and Bif Italia s.r.l. liability shall lapse in the event that any modication or
tampering whatsoever be performed on the actuator.
NOTICE
Bif Italia s.r.l. pays the highest attention to collecting and verifying the documentation contained in
this user manual. However Bif Italia s.r.l. is not liable for any mistakes contained in this manual, for
damage or accidents due to the use of the latter. The information contained is of exclusive reserved
ownership of Bif Italia s.r.l. and may be modied without prior notice. All rights reserved.
NOTICE
The manual is an integral part of the machine, it should be carefully read before carrying out any
operation and it should be kept for future references.
General Warnings 1
Section 1: General Warnings

July 2020
Installation, Operation and Maintenance Manual
MAN 573 Rev. 8
1.2 Identication Plate
! WARNING
It is forbidden to modify the information and the marks without previous written authorization
by Bif Italia s.r.l.
The plate fastened on the actuator contains the following information (see Figure 1).
Figure 1 Data Plate
1.3 Introducing the Actuator
RPS actuators are pneumatic low-pressure Spring-Return, suitable for any quarter-turn application
such as ball, plug, buttery valves or dampers, in both ON-OFF and modulating heavy-duty service.
The actuator is made up of a rack and pinion mechanism, which transforms the linear movement
of the pneumatic cylinder, in one direction, and of the spring, in the opposite direction, into the
rotary movement for the valve operation. An adjustable bronze sliding block supports the
transverse force exerted on the rack by its engagement with the pinion. The rack is nitride
for ensure the minimal friction.
The spring module incorporates one or two springs in series, depending on the model, and is fully
encapsulated. This assures safety to personnel and ease of assembly. External travel stops allow
precise angular stroke adjustment between 80° and 100°.
Totally enclosed, weatherproof housing, made of nodular cast iron for maximum strength and
suitable for use in hostile environments.
The mounting ange is identical on both (upper and lower) faces of the housing; the shaft output
drives have the same dimensions but is positioned at 90°. This allows the actuator to be used as
spring to close or spring to open without modication.
The actuator is assembled onto the valve by connecting the actuator housing ange to the valve
ange by a spool piece and the actuator shaft to the valve stem by a stem extension.
Actuator manual emergency operation in opposition to the spring action, is performed by rotating
the jackscrew by a wrench or by a hand-wheel (available on request).
The mounting ange, on the housing top, can be utilised for the assembly of limit switches, position
transmitter, positioner etc., which are actuated by the actuator output shaft.
General Warnings2
Section 1: General Warnings

Installation, Operation and Maintenance Manual
MAN 573 Rev. 8 July 2020
Figure 2
The actuator housing is provided, on the front face and in the back face (optional), with threaded
holes for the assembly of accessories (control panels, air storage tank, etc.).
RP 13-14-15 49,5 49,5 M8 10 16 21 23 66 30 2,7 140 40 M6 4
RP 30 72,1 72,1 M10 12 22 29 25 92 32 2,7 164 50 M6 4
RP 60 88,4 88,4 M12 15 28 37 34 112 42 3,0 204 60 M6 4
RP 120 99,0 99,0 M16 23 37 49 45 132 55 3,0 270 75 M6 4
Both the actuator anges can be used for valve coupling or the mounting of ancillary equipment
(positioner, limit switch box, etc.).
* UNI 3221
Actuator
Model A± 0,2 B± 0,2 ØC D ØE ØF G ØH K J L ØM ØN* R
0
-0,1 0
-0,5 0
-0,2 +0,1
0
View from X View from Y
№4 threaded
holes
№4 threaded
holes
Threaded hole ØN
Joint detail
Threaded hole ØN
X
Y
A
R
R
R
R
A
KK
=
=
=
=
=
=
=
=
=
=
=
=
B
12
4
B
L
JJ
G
D
ØM
ØF
M6
ØE
ØH
ØC ØC
ØE
+ 0,5
0
Table 1. Dimensions in mm
General Warnings 3
Section 1: General Warnings

July 2020
Installation, Operation and Maintenance Manual
MAN 573 Rev. 8
A±0.2
A ±0.2 B
B ±0.2
M ±0.2
K L
GH
FF
D
ØE
ØE
Front side
Top view
Back side
№4 threaded holes
№4 threaded holes (optional)
Figure 3
Model A B C D ØE F G H K L M
15 55 110 12.5 43 M8 14 17 98 114 67 181
30 70 125 15 56 M10 16 35 120 136 80 216
60 88 160 16 68 M12 19 35 150 160 105 265
120 124 190 18 82 M16 23 50 183 210 124 334
Table 2. Dimensions in mm
The expected lifetime of actuator is approximately 25 years.
General Warnings4
Section 1: General Warnings

Installation, Operation and Maintenance Manual
MAN 573 Rev. 8 July 2020
1.4 Data Sheet
Supply uid: Air, Nitrogen or sweet gas
Operating temperature: Standard: from –30 °C to +100 °C
Optional: from –60 °C to +140 °C
Design pressure: 12 bar maximum
Supply pressure: Please refer to technical document: “actuator data sheet”
Output torque: up to 3,700 Nm
General Warnings 5
Section 1: General Warnings

July 2020
Installation, Operation and Maintenance Manual
MAN 573 Rev. 8
Section 2: Installation
2.1 Checks upon Actuator Receipt
• Check that the model, the serial number of the actuator and the technical data reported on
the identication plate correspond with those of order conrmation (Section 1.2).
• Check that the actuator is equipped with the ttings as provided for by order conrmation.
• Check that the actuator was not damaged during transportation: if necessary renovate the
painting according to the specication reported on the order conrmation.
• If the actuator is received already assembled with the valve, its settings have already been
made at the factory.
• If the actuator is delivered separately from the valve, it is necessary to check, and, if
required, to adjust, the settings of the mechanical stops (Section 3.4) and of micro-switches
(if any) (Section 3.5).
2.2 Actuator Handling
A. Valve stem with vertical axis:
NOTICE
The lifting and handling should be made by qualied staff and in compliance with the laws and
provisions in force.
! WARNING
The fastening points are appropriate for the lifting of the actuator alone and not for the
valve + actuator assembly. Avoid that during the handling, the actuator passes above the staff.
The actuator should be handled with appropriate lifting means. The weight of the actuator is
reported on the delivery bill.
For a correct lifting procedure, please refer to following Figures :
Figure 4
1 - 2 = Lifting eyelets
Installation
6
Section 2: Installation

Installation, Operation and Maintenance Manual
MAN 573 Rev. 8 July 2020
B. Valve stem with horizontal axis:
The actuator can also be lifted to assemble directly onto the valve with stem with horizontal
axis. To make easier this operation, Bif suggest to move the lifting eyelet from its standard
position, and place it in this suggested position:
Figure 5
A
B
A
A
A
BACK SIDE VIEW
Lifting eyelets (horizontal stem valve mounting position)
Lifting point to balance weight (suitable for slings)
(horizontal stem valve mounting position)
A = Lifting eyelets
B = Lifting point (balancing)
FRONT VIEW SIDE VIEW
TOP VIEW
Lifting eyelets suitable for vertical stem
valve mounting position (standard)
Lifting eyelets (standard position)
Installation 7
Section 2: Installation

July 2020
Installation, Operation and Maintenance Manual
MAN 573 Rev. 8
Figure 6 Actuator Models: RPS
When it's necessary to lift the actuator, in order to stabilize the RPS actuator during the transport in
horizontal position, it's recommendable to x the actuator by the "stabilizing eyelets" placed on the
top of the control cabinet.
! WARNING
Never use the "stabilizing eyelets" to lift actuator.
Stabilizing eyelet (DON'T USE FOR LIFT)
Lifting eyelets Lifting eyelet Lifting eyelet
Rack and Pinion
Stabilizing eyelet (DON'T USE FOR LIFT)
2.3 Storage
If the actuator needs storage before installation, follow these steps:
• Place it on a wood surface in order not to deteriorate the area of valve coupling.
• Make sure that plastic plugs are present on the hydraulic and electrical connections
(if present).
• Check that the protection of the control system and of the limit switch box (if any) are
properly closed.
If the storage is long-term or outdoor:
• Keep the actuator protected from direct weather conditions.
• Replace plastic plugs of hydraulic and electrical connections (if any) with metal plugs that
guarantee perfect tightness.
• Coat with oil, grease or protection disc, the valve coupling area.
• Periodically operate the actuator (Section 3.3).
Installation
8
Section 2: Installation

Installation, Operation and Maintenance Manual
MAN 573 Rev. 8 July 2020
! WARNING
Don't lay the actuator on accessories (manual handpump, manual jackscrew, pneumatic control
system etc.).
Figure 7
1 = Points of support
2 = Do not lay the actuator on tie-rods
2.4 Actuator Assembly on the Valve
2.4.1 Types of Assembly
For coupling to the valve, the housing is provided with a ange with threaded holes according to Bif
standard tables (TN1182N attached). The number, dimensions and diameter of the holes are made
in accordance with ISO 5211. The actuator is provided with a spool piece and a stem extension for
coupling to the valve. The assembly position of the actuator, with reference to the valve, must comply
with the plant requirements (cylinder axis parallel or perpendicular to the pipeline axis).
NOTICE
To x the actuator to the valve ange must be used the stud bolts and nuts supplied by Bif.
In case the actuator is supplied without stud bolts and nuts, the following materials must be
used as a minimum:
• ASTM A 193 Grade L7 for Stud Bolts
• ASTM A 194 Grade 4 for Nuts
Installation 9
Section 2: Installation

July 2020
Installation, Operation and Maintenance Manual
MAN 573 Rev. 8
Figure 8 "RP" Pneumatic Actuators Coupling Dimensions - Overall Dimensions
Table 3. Dimensions in mm
RP 13-14-15 49,5 49,5 M8 10 16 21 23 66 30 2,7 140 40 M6 4
RP 30 72,1 72,1 M10 12 22 29 25 92 32 2,7 164 50 M6 4
RP 60 88,4 88,4 M12 15 28 37 34 112 42 3,0 204 60 M6 4
RP 120 99,0 99,0 M16 23 37 49 45 132 55 3,0 270 75 M6 4
Both the actuator anges can be used for valve coupling or the mounting of ancillary equipment
(positioner, limit switch box, etc.).
* UNI 3221
Actuator
Model A± 0,2 B± 0,2 ØC D ØE ØF G ØH K J L ØM ØN* R
0
-0,1 0
-0,5 0
-0,2 +0,1
0
View from X View from Y
№4 threaded
holes
№4 threaded
holes
Threaded hole ØN
Joint detail
Threaded hole ØN
X
Y
A
R
R
R
R
A
KK
=
=
=
=
=
=
=
=
=
=
=
=
B
12
4
B
L
JJ
G
D
ØM
ØF
M6
ØE
ØH
ØC ØC
ØE
+ 0,5
0
Installation
10
Section 2: Installation

Installation, Operation and Maintenance Manual
MAN 573 Rev. 8 July 2020
2.4.2 Assembly procedure
NOTICE
Failure to comply with the following procedures may impair product warranty.
For actuator assembly on the valve:
NOTICE
Check that the assembly position, as shown on the documentation, complies with system’s geom-
etry. Check the consistency of the parts of actuator-valve coupling.
• Operate the actuator so that it reaches the matching valve position (Section 3.3).
• Lubricate valve stem with oil or grease.
• Properly clean and remove grease from valve coupling ange surfaces.
• Connect, if supplied separately, the stem extension onto the valve stem and fasten it with
the special fastening pins.
• Lift the actuator using the special lifting points (Section 2.2).
• Install the actuator so that valve stem inserts in the coupling area. This coupling should be
made without forcing.
• Fasten the two parts with the threaded connections (screws, tie rods, nuts). If holes of
coupling anges are not aligned, adequately operate the actuator if necessary, move the
mechanical stops backwards (Section 3.4).
• Fasten threaded connections. Please refer to Table 4.
! WARNING
Installation, commissioning and maintenance and repair works should be carried out by qualied staff.
A non-conforming assembly could be the source of serious accidents.
Table 4. Nuts tightening torque
Threading Tightening torque (Nm)
M8 20
M10 40
M12 70
M16 160
The screwing values in Table 4 were calculated considering the materials ASTM A320 L7 for screws or
tie rods and ASTM A194 gr.2H for the nuts.
Installation 11
Section 2: Installation

July 2020
Installation, Operation and Maintenance Manual
MAN 573 Rev. 8
2.5 Pneumatic Connections
Connect the actuator to the pneumatic feed line with ttings and pipes in accordance to the plant
specications. They must be sized correctly in order to guarantee the necessary air ow for the
operation of the actuator, with pressure drops not exceeding the maximum allowable value.
The shape of the connecting piping must not cause excessive stress to the inlets of the actuator.
The piping must be suitably fastened so as not to cause excessive stress or loosening of threaded
connections, if the system undergoes strong vibrations.
Every precaution must be taken to ensure that any solid or liquid contaminants which may be present
in the pneumatic pipe-work to the actuator are removed to avoid possible damages to the unit or loss
of performance. The inside of the pipes used for the connections must be well cleaned before use:
wash them with suitable substances and blow through them with air or nitrogen.
The ends of the tubes must be well deburred and cleaned. Once the connections are completed,
operate the actuator and check that it functions correctly, that the operation times meet the plant
requirements and that there are no leakages in the pneumatic connections.
2.6 Electrical Connections (If any)
! WARNING
The connections should be made by qualied staff. Before carrying out any operation, cut line power
off. Safety provisions as per CEI 64-8 regulation should be complied with (same as IEC 60364).
Connect the electrical feed, control and signal lines to the actuator, by linking them up with the
terminal blocks of the electrical components. In order to do this, the housing covers must be
removed without damaging the coupling surfaces, the O-rings or the gaskets. Remove the plugs
from the cable entries. For electrical connections use components (cable glands, cables, hoses,
conduits) which meet the requirements and codes applicable to the plant specications (mechanical
protection and/or explosion-proof protection). Screw the cable glands tightly into the threaded
inlets, so as to guarantee the weatherproof and explosion-proof protection (when applicable).
Insert the connection cables into the electrical enclosures through the cable glands and connect
the cable wires to the terminals according to the applicable wiring diagram. If conduits are used,
it is advisable to carry out the connection to the electrical enclosures by inserting hoses so as not
to cause anomalous stress on the housing cable entries. Replace the plastic plugs of the unused
enclosure entries by metal ones, to guarantee perfect weatherproof tightness and to comply with
the explosion-proof protection codes (where applicable). Once the connections are completed,
check that the controls and signals work properly.
Installation
12
Section 2: Installation

Installation, Operation and Maintenance Manual
MAN 573 Rev. 8 July 2020
2.7 Commissioning
! WARNING
Installation, commissioning and maintenance and repair works should be made by qualied staff.
Any calibration relative to functional aspects of the actuator are preset at the factory, except the
angular stroke setting because for this setting operation, the actuator must be placed on to the valve
(see Section 3.4). Before any modications please contact Bif Italia s.r.l.
Upon actuator commissioning please carry out the following checks:
• Check that the pressure and quality of the air supply (ltering degree, dehydration) are as
prescribed. Check that the feed voltage values of the electrical components (solenoid valve
coils, micro-switches, pressure switches, etc.) are as prescribed.
• Check that the actuator controls work properly (remote control, local control, emergency
controls, etc.).
• Check that the required remote signals (valve position, air pressure, etc.) are correct.
• Check that the setting of the components of the actuator control unit (pressure regulator,
pressure switches, ow control valves, etc.) meet the plant requirements.
• Check there are no leakages in the pneumatic connections. If necessary, tighten the nuts of
the pipe ttings.
• Remove all rust and, in accordance with the applicable painting specications,
repair paint-coat that has been damaged during transport, storage or assembly.
Installation 13
Section 2: Installation

July 2020
Installation, Operation and Maintenance Manual
MAN 573 Rev. 8
Section 3: Operation and Use
3.1 Operation Description
The air pressurizes the cylinder chamber and this pressure starts the linear motion of the piston
and the consequent rotation motion of the rack and pinion mechanism, to which the valve stem is
coupled, in one direction. The operation in the opposite direction is made by the linear movement
generated from the spring releasing, when the opposition of pneumatic supply is discharged from
the cylinder.
Figure 9
For local or remote operations related to the actuator, please refer to technical documentation
furnished with actuators.
Typical schematics for various applications are follow attached for information only.
Manual Override for RPS Spring-Return Pneumatic Actuator
Actuator manual emergency operation in opposition to the spring action, is performed by rotating
the jackscrew by a handwheel (available on request) until valve completely open (or close – it depend
to actuator fail action).
Figure 10
NOTICE
The jackscrew must be completely unscrewed to allow pneumatic remote control.
Operation and Use14
Section 3: Operation and Use

Installation, Operation and Maintenance Manual
MAN 573 Rev. 8 July 2020
Figure 11 ON-OFF Service: Three way control valve
The Figure shows the simplest ON-OFF control. The control valve (2) has two positions. In one
position, the gas supply pressure is connected to the cylinder chamber, and the actuator performs
the “pneumatic” operation. In the other position the cylinder is connected to the exhaust and
the actuator moves under the operation of the spring. The control valve can have many types of
actuating devices (solenoid, manual control, pneumatic pilot, spring, etc.). Spring-Return control
valves allow “fail safe” operation.
1
2
Pressurized air
Atmospheric pressure air
Manual control
Pneumatic pilot
control
Solenoid
control
Figure 12 ON-OFF Service: Quick spring operation
When fast action is required under spring operation, a quick exhaust valve (3) is installed in the
cylinder directly port to exhaust the gas from the cylinder directly to the atmosphere. When the
control valve (2) opens to the atmosphere a differential pressure is created across the quick exhaust
valve (3) causing it to open. The resultant high ow capacity from cylinder to atmosphere allows
quick spring operation of the actuator.
1
3
2
Pressurized air
Atmospheric pressure air
Operation and Use 15
Section 3: Operation and Use

July 2020
Installation, Operation and Maintenance Manual
MAN 573 Rev. 8
Figure 13 Modulating service
2
P
3
4
5
1
P
Pneumatic
positioner
Pneumatic
control signal Electric
control signal
Electropneumatic positioner
Pressurized air (supply)
Reduced pressure air
3.2 Residual Risks
When modulating control is required as a function of a pneumatic or electric control signal, a
positioner (5) is used, which controls the supply to the actuator cylinder to keep the valve in the
required angular position. The positioner has a mechanical linkage to the actuator, for a feedback of
the valve position.
3.3 Operations
The operations are carried out sending the proper signal through the control system in compliance
with Customer specications.
Please refer to applicable “operating diagram” and to Bif technical documentation supplied.
! WARNING
The actuator has parts under pressure. Use the due caution. Use individual protections provided for
by the laws and provisions in force.
Operation and Use16
Section 3: Operation and Use
This manual suits for next models
17
Table of contents
Other BIFFI Controllers manuals
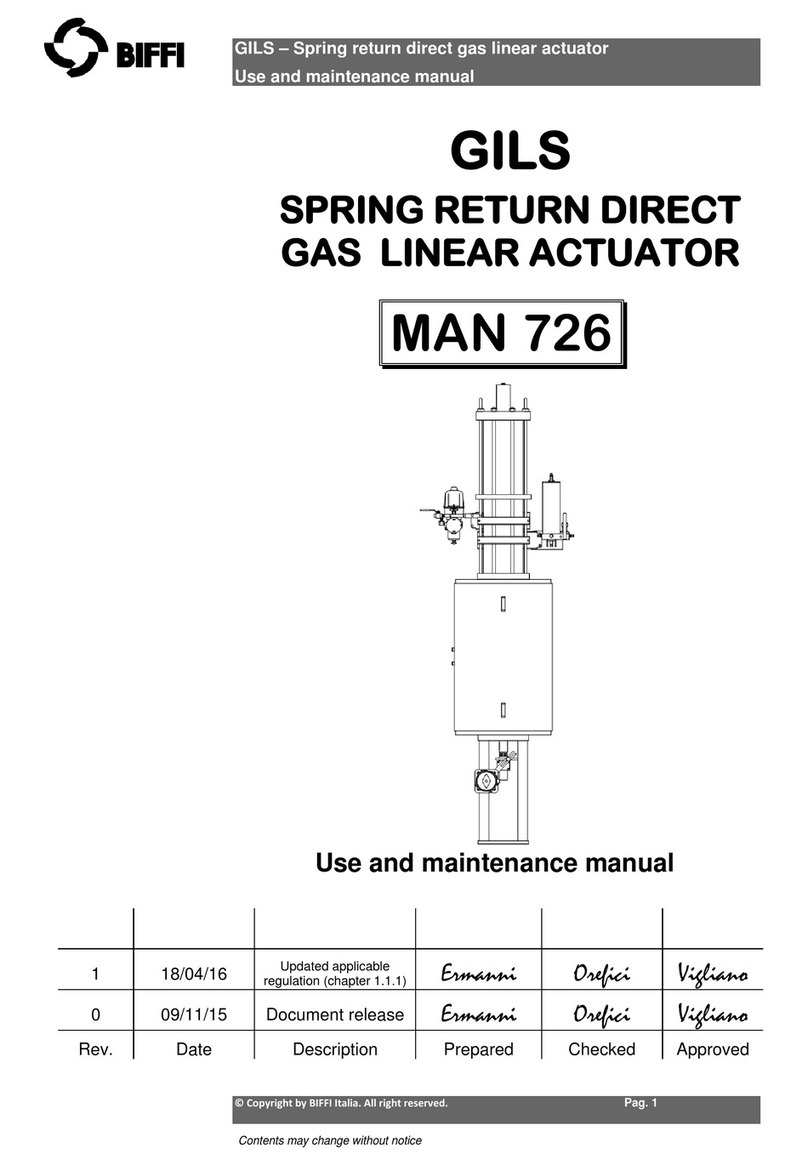
BIFFI
BIFFI GILS User manual

BIFFI
BIFFI GIGS 0.3 User manual

BIFFI
BIFFI RPS User manual
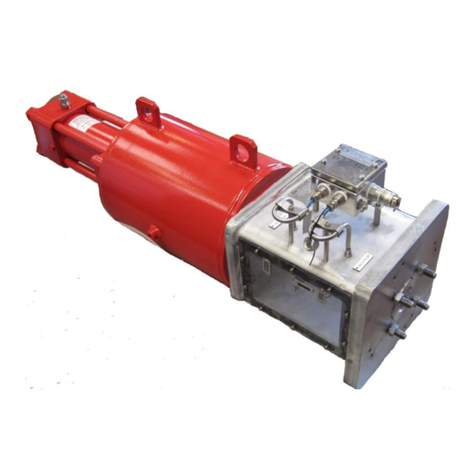
BIFFI
BIFFI HLAS User manual
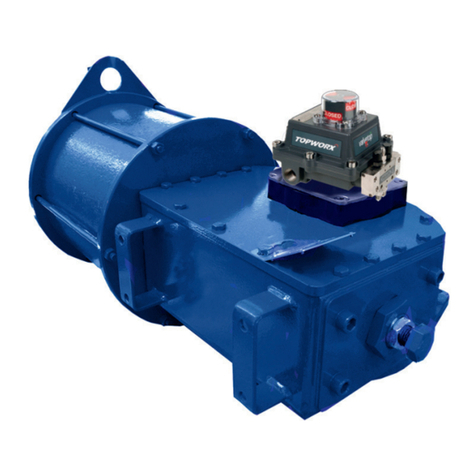
BIFFI
BIFFI ALGA-EAC Series User manual
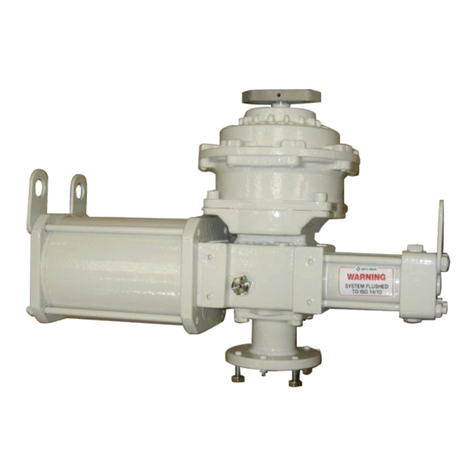
BIFFI
BIFFI RPHD-10 User manual
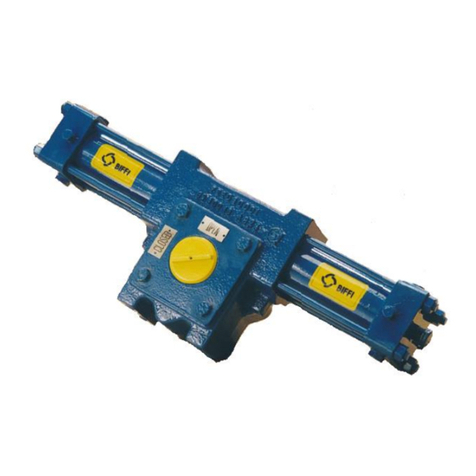
BIFFI
BIFFI RPHD User manual
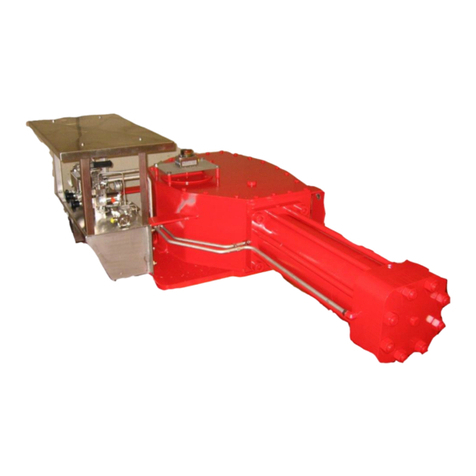
BIFFI
BIFFI OLGA-H User manual
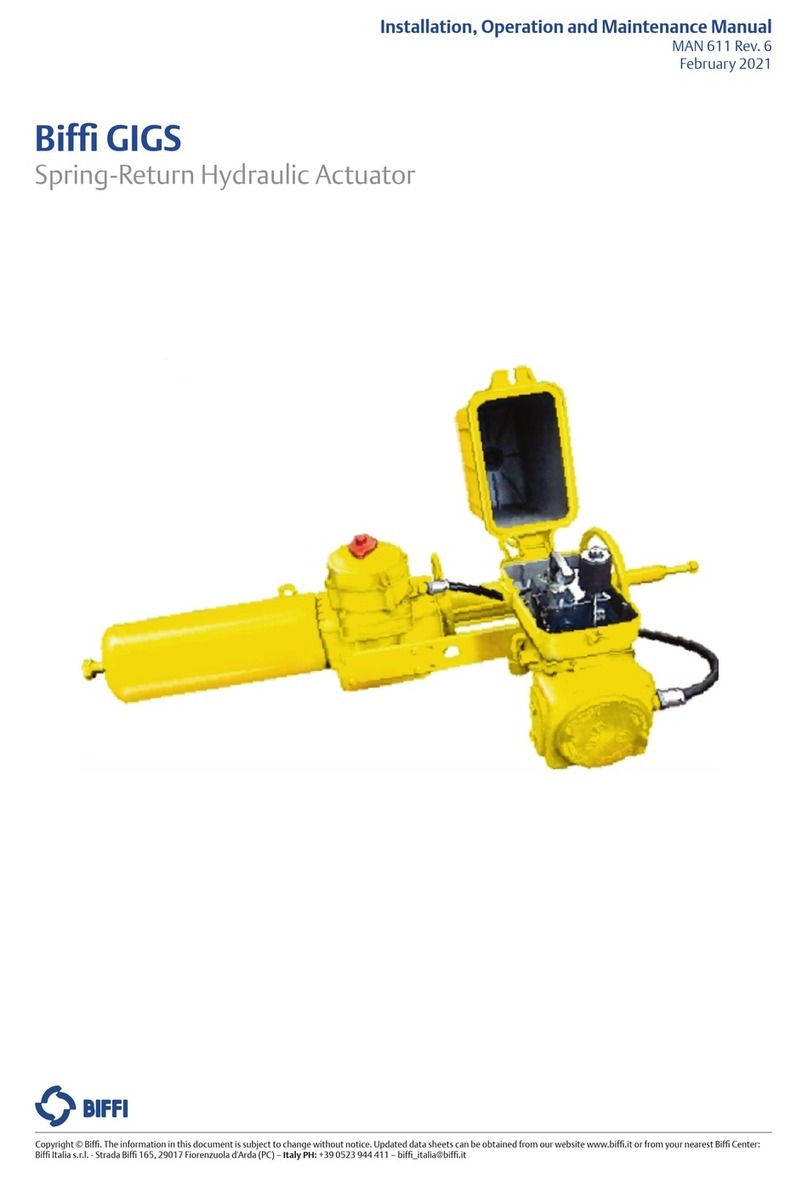
BIFFI
BIFFI GIGS Series User manual
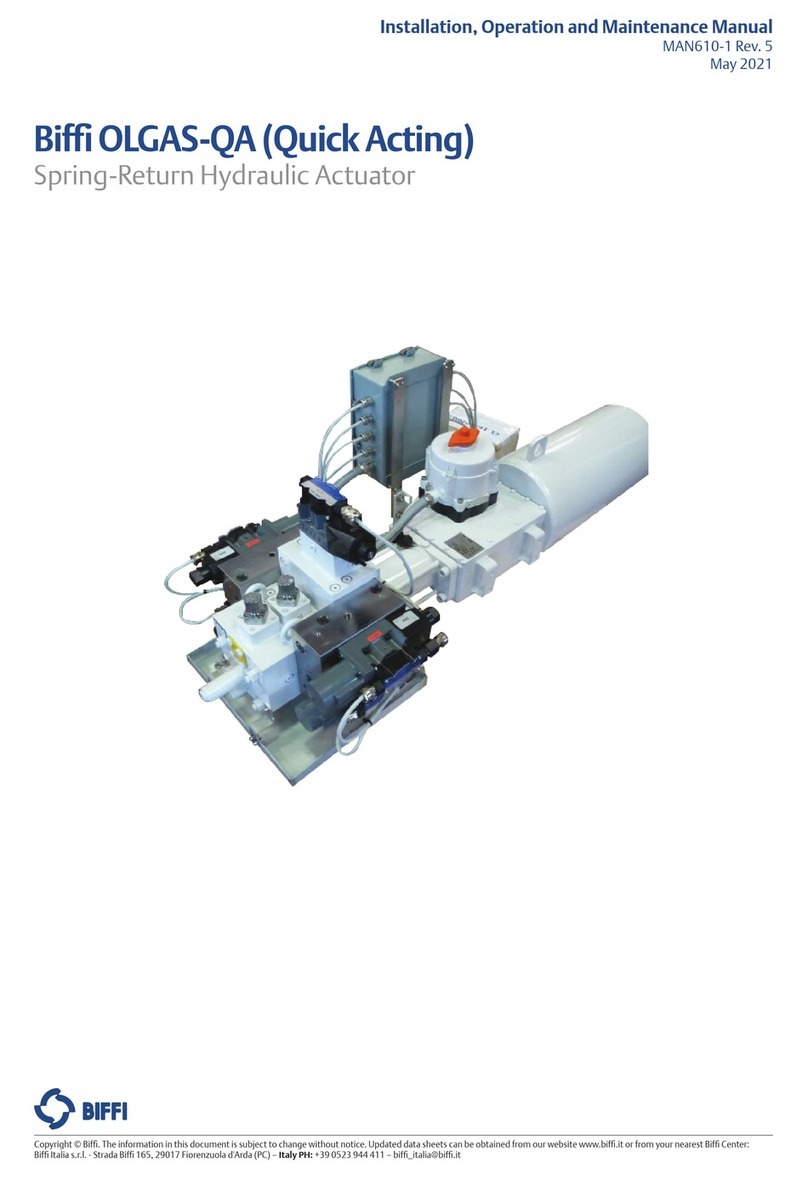
BIFFI
BIFFI OLGAS-QA User manual